Glas
Glas (von germanisch glasa „das Glänzende, Schimmernde“, auch für „Bernstein“) ist ein Sammelbegriff für eine Gruppe amorpher Feststoffe. Die meisten Gläser bestehen hauptsächlich aus Siliciumdioxid, wie Trink- oder Fenstergläser; diese – meist lichtdurchlässigen – Silikat-Gläser haben wirtschaftlich die weitaus größte Bedeutung aller Gläser. Auch amorph erstarrte Metalle sind Gläser. Gläser aus organischen Materialien sind beispielsweise der natürliche Bernstein oder viele Kunststoffe wie Acrylglas. Durch sehr schnelles Abkühlen aus dem flüssigen oder gasförmigen Zustand kann nahezu jeder Stoff in ein (metastabiles) Glas überführt werden.[1] Es gibt eine sehr große Anzahl von Gläsern verschiedener Zusammensetzungen, die aufgrund ihrer Eigenschaften von wirtschaftlichem oder wissenschaftlichem Interesse sind. Wegen der breiten Palette von Anwendungen für Gläser gibt es auch vielfältige Techniken zu deren Erzeugung und Formgebung. Viele dieser Techniken sind bereits sehr alt und werden – von ihrem Grundprinzip her unverändert – auch heute noch industriell umgesetzt.
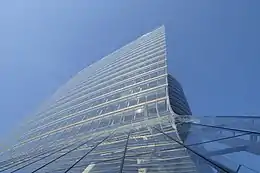
.jpg.webp)
Definition
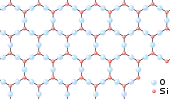
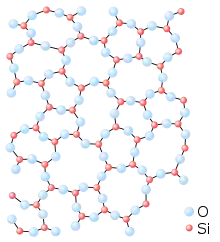
Glas ist eine amorphe Substanz, die durch Schmelzen erzeugt wird. Die Herstellung von Glas ist auch durch die Erwärmung von Sol-Gel und durch Stoßwellen möglich. Thermodynamisch wird Glas als gefrorene, unterkühlte Flüssigkeit bezeichnet. Diese Definition gilt für alle Substanzen, die geschmolzen und entsprechend schnell abgekühlt werden. Das bedeutet, dass sich bei der Erstarrung der Schmelze zum Glas zwar Kristallkeime bilden, für den Kristallisationsprozess jedoch nicht genügend Zeit bleibt. Vereinfachend dargestellt ist der atomare Aufbau eines Glases dem einer hochviskosen Flüssigkeit vergleichbar.[2]:3 Auch nach Jahrzehnten fließt Glas jedoch nicht in dem Maße, dass dies zu der an historischen Gläsern häufig zu beobachtenden Schlierenbildung führen würde. Diese sind vielmehr auf die damaligen Herstellungsprozesse wie den Fourcault-Prozess zurückzuführen.
Der Transformationsbereich, das ist der Übergangsbereich zwischen Schmelze und Feststoff, liegt bei vielen Glasarten um 600 °C. Trotz des nicht definierten Schmelzpunkts sind Gläser Festkörper. Allerdings werden sie in der Fachterminologie als „nichtergodisch“ bezeichnet. Das heißt, ihre Struktur befindet sich nicht im thermodynamischen Gleichgewicht. Viele Kunststoffe, wie zum Beispiel Plexiglas, fallen wegen ihres amorphen Aufbaus und eines Glasübergangs ebenfalls in die Kategorie Gläser, obwohl sie eine völlig andere chemische Zusammensetzung aufweisen als Silikatgläser. Sie werden daher oft als organisches Glas bezeichnet.
Der Unterschied zwischen Gläsern und anderen amorphen Feststoffen liegt darin, dass Gläser beim Erhitzen im Bereich der Glasübergangstemperatur in den flüssigen Zustand übergehen, während nicht glasartige amorphe Substanzen dabei kristallisieren.[3]
Aus der Beobachtung der Eigenschaften der Gläser und ihrer Struktur wurden viele Versuche angestrengt, eine umfassende Definition für den Begriff Glas zu geben. Der anerkannte Glaswissenschaftler Horst Scholze führte eine Auswertung der gängigsten Definitionsversuche des Begriffs Glas durch. In seiner Monographie „Der Glaszustand“ (1933) formierte Gustav Tammann folgende Definition: „Im Glaszustand befinden sich die festen, nicht kristallisierten Stoffe.“, während die ASTM 1945 als Definition „Glas ist ein anorganisches Schmelzprodukt, das im wesentlichen ohne Kristallisation erstarrt.“ vorschlug. Franz Eugen Simon gab bereits 1930 eine Definition aus thermodynamischer Sicht: „Im physikochemischen Sinn ist Glas eine eingefrorene unterkühlte Flüssigkeit.“. Nach Scholze haben alle dieser Definitionen ihre Berechtigungen, jedoch auch ihre Schwächen. So ist die Definition nach Tammann zu allgemein und schließt Kieselgel, das ebenfalls ein nichtkristalliner Festkörper ist, nicht als Glas aus. Die Beschränkung der ASTM-Definition auf anorganische Substanzen wurde von Scholze als bedenklich bewertet, da mittlerweile einige organische Gläser bekannt sind.[4]:3 ff.[5]:27 ff. Eine umfassende Definition wurde von der Kommission für Terminologie der UdSSR gegeben: „Als Gläser werden alle amorphen Körper bezeichnet, die man durch Unterkühlung einer Schmelze erhält, unabhängig von ihrer chemischen Zusammensetzung und dem Temperaturbereich ihrer Verfestigung und die infolge der allmählichen Zunahme der Viskosität die mechanischen Eigenschaften der fester Körper annehmen. Der Übergang aus dem flüssigen in den Glaszustand muß dabei reversibel sein.“[6] Die Beschränkung der Gläser auf Festkörper, die aus einer Schmelzphase erhalten wurden, ist aus heutiger Sicht ebenfalls bedenklich, da auch der Sol-Gel-Prozess amorphe Festkörper bzw. Gläser hervorbringen kann.[4]:76 f. Die Besonderheit des Glaszustandes der Materie geht so weit, dass einige Forscher ihn als „vierten Aggregatzustand zwischen Festkörper und Flüssigkeit“ ansahen.[2]:3
Einteilung der Gläser
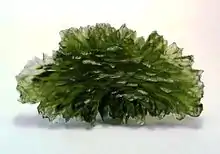
- Nach Art der Genese
- Neben künstlichen finden sich auch natürliche Gläser: Obsidian und Bimsstein sind vulkanischen Ursprungs,[7] Impaktgläser und Tektite entstehen durch Meteoriteneinschlag,[8] Fulgurite bei Blitzeinschlag,[9] Trinitit durch Atombombenexplosion und der Friktionit Köfelsit durch Bergstürze.[10] Diese Gläser entstehen aus dem Schmelzen von Sanden. Durch Einwirkung einer Stoßwelle kann ein Kristallgitter seine geregelte Struktur verlieren und sich so in einen amorphen Festkörper umwandeln. So entstandene Gläser werden als diaplektisch bezeichnet.[11] Hierzu zählt Maskelynit, das aus Feldspat entstanden ist.[12] Künstliche Gläser werden hauptsächlich durch Schmelzen von Rohstoffen in verschiedensten Schmelzaggregaten erzeugt. Ein weiterer Syntheseweg zur Herstellung von Gläsern ist der Sol-Gel-Prozess, mit dem dünne Schichten oder Aerogele erzeugt werden können.[13][4]:3 ff., 76 f.[5]:226 ff.
- Nach Art des „Chemismus“
- Der größte Teil der heute hergestellten Gläser sind Kalk-Natron-Gläser, welche zur Gruppe der Silikatischen Gläser gehören. Alle Gläser dieser Gruppe haben gemeinsam, dass ihr Netzwerk hauptsächlich aus Siliziumdioxid (SiO2) gebildet wird. Durch Zugabe weiterer Oxide wie beispielsweise Aluminiumoxid oder verschiedener Alkalioxide entstehen die Alumo- oder Alkali-Silikatgläser. Für die Einordnung entscheidend ist, welches Oxid mengenmäßig das zweithäufigste im silikatischen Grundglas ist. Ein Silikatglas ohne weitere Bestandteile – also reines SiO2 – wird als Kiesel- oder Quarzglas bezeichnet.[5]:141–150 Aufgrund seiner hohen chemischen Beständigkeit und thermischen Belastbarkeit sowie des geringen Wärmeausdehnungskoeffizienten wird es oft in technischen Spezialanwendungen genutzt. Treten als Hauptnetzwerkbildner eines Glases Phosphorpentoxid oder Bortrioxid auf, spricht man von Phosphat- bzw. Boratgläsern, deren Eigenschaften ebenfalls durch Zugabe weiterer Oxide eingestellt werden können.[5]:164, 185 ff. Alle zuvor genannten Gläser bestehen größtenteils aus Oxiden, weshalb man sie zusammenfassend als Oxidische Gläser bezeichnet. Ist das Anion eines Glases ein Halogenidion spricht man von Halogenidglas[5]:200–207[4]:140 f. oder von einem Chalkogenidglas, wenn es sich hauptsächlich um Schwefel, Selen oder Tellur als Anion im Glasnetzwerk handelt.[4]:142 f.[5]:189 ff. Diese Gläser zeichnen sich durch eine hohe Transparenz, weit über den sichtbaren Bereich des Lichtes hinaus, aus und werden deshalb in der Infrarotoptik eingesetzt. Neben diesen anorganisch-nichtmetallischen Gläsern existieren noch organische Gläser[4]:144 f., beispielsweise amorphe Kunststoffe, welche mit den zuvor genannten als nichtmetallische Gläser zusammengefasst werden können und den metallischen Gläsern gegenüberstehen.[5]:226 Die Grenzen zwischen den einzelnen Glastypen sind fließend und es gibt zahlreiche Untertypen. Ein Beispiel hierfür sind die Oxy-Nitridgläser, in denen ein Teil der Sauerstoffionen durch Stickstoff ersetzt wurde, um gezielt Eigenschaften zu erzeugen.[4]:139 f. Dadurch ist dieses Glas als ein Hybrid zwischen oxidischen und nichtoxidischen Gläsern aufzufassen. Gläser, welche nur aus einem Bestandteil, also dem Netzwerkbildner, bestehen, werden als Einkomponentengläser bezeichnet. Das typische Beispiel hierfür ist das Quarzglas. Durch Zugabe weiterer Bestandteile erhält man die sogenannten Zweikomponentengläser wie das Alkaliboratglas oder die Dreikomponentengläser wie das Kalk-Natron-Glas. In der Regel enthalten Gläser mehr als nur drei Bestandteile, jedoch werden nur die Hauptbestandteile genannt, da sich die Gläser dieser Zusammensetzungen in ihren Eigenschaften und Einsatzgebieten weitestgehend ähneln.[4]:121 ff. Die hierarchische Beziehung der Gläser untereinander ist in der untenstehenden Abbildung dargestellt.[14][4]:120–146[5]:177 f.
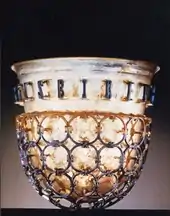
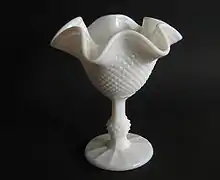
- Nach der Grundform des Produkts und dem Produktionsverfahren
- Die Glasindustrie wird gewöhnlich in Hohlglas-, Flachglas- und Spezialglasherstellung gegliedert, auch wenn diese einfache Gliederung nicht alle Bereiche der Glasindustrie erfasst. Hohlglas bezeichnet in der Regel Behältnisse für Lebensmittel, wie beispielsweise Flaschen und Konservengläser. Diese Massenprodukte werden maschinell im Press-Blas- oder Blas-Blas-Prozess gefertigt. Glasbausteine und Trinkgläser werden nur durch einen Pressvorgang geformt. Höherwertige Produkte wie Weingläser, werden als sogenanntes Tableware bezeichnet und meist in einem aufwendigen mehrstufigen Prozess hergestellt. Im Gegensatz zu den Glasflaschen werden sie nicht mit Hilfe von IS-Maschinen, sondern sogenannten Rotationsblasmaschinen produziert. Für Glühlampen ist ein besonderes Verfahren notwendig, welches sich besonders durch die hohen Produktionsgeschwindigkeiten der Ribbonmaschine auszeichnet. Rohrglas kann nach verschiedenen Verfahren hergestellt werden, welche sich durch die unterschiedlichen Abmessungen des herzustellenden Halbzeugs unterscheiden. Flachglas wird je nach Produktionsverfahren Floatglas oder Walzglas genannt. Das Grundprodukt ist eine Glasscheibe. Endprodukte sind z. B. Automobilglas, Spiegel, Temperglas oder Verbundglas, welche auf verschiedenste Weise nachbearbeitet wurden. Anwendungen in Form von Fasern umfassen Lichtwellenleiter, Glaswolle und glasfaserverstärkten Kunststoff sowie Textilglas. Mundgeblasene Gläser existieren praktisch nur noch im Kunstgewerbe sowie bei kostspieligen Vasen und Weingläsern.[15][16][17]
- Nach ihren hergebrachten Handelsnamen
- Antikglas, Diatretglas, optische Gläser wie Kronglas und Flintglas (Bleiglas), Hyalithglas (opakes Glas, im 19. Jahrhundert benutzt für Tafel- und Pharmaglas), Kryolithglas (opakes, weißes Fluoridglas).[18]
- Nach ihren Markennamen als Gattungsbegriff
- Häufig hat sich der Markenname eines Glasherstellers als Sammelbegriff für verschiedene Produkte eines oder sogar mehrerer Glashersteller eingebürgert. Ceran wird sehr oft als Synonym für Glaskeramiken oder Kochfelder verwandt. Jenaer Glas steht umgangssprachlich oft für alle Varianten von hitzefestem Borosilikatglas. Im angelsächsischen Raum hat sich der Markenname Pyrex von Corning für diese Sorte von Gläsern eingebürgert.[19]
- Nach ihrer Verwendung
- Die wichtigsten optischen Gläser zur Herstellung von Linsen, Prismen, Spiegeln und anderen optischen Bauteilen für Mikroskope, Ferngläser, Objektive usw. sind Quarzglas, Kronglas, Flintglas und Borosilikatglas.[20][21] Als Substratmaterial für optische Elemente in der Astronomie und Raumfahrt kommt der glaskeramische Werkstoff Zerodur (Schott) zum Einsatz. Dieser weist einen äußerst geringen Ausdehnungskoeffizienten auf und eignet sich somit z. B. hervorragend als Spiegelträger für große astronomische Teleskope.[22] Ein weiteres Beispiel ist Geräteglas als Oberbegriff für alle Sorten von Gläsern im Bereich der technischen Laborgläser.[23] Ein ähnlicher Oberbegriff für verschiedene weiterverarbeitete Gläser ist Architektur- oder Bauglas.[24]
Eigenschaften
Struktur
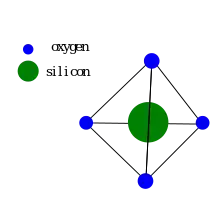
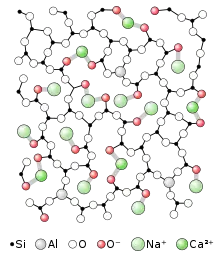
Obwohl Glas zu den ältesten Werkstoffen der Menschheit gehört, besteht noch Unklarheit in vielen Fragen des atomaren Aufbaus und seiner Struktur. Die mittlerweile allgemein anerkannte Deutung der Struktur ist die Netzwerkhypothese, die 1932 von W. H. Zachariasen aufgestellt und B. E. Warren 1933 experimentell bekräftigt wurde. Diese besagt, dass im Glas grundsätzlich dieselben Bindungszustände oder Grundbausteine wie in einem Kristall vorliegen müssen. Im Falle silikatischen Glases also die SiO4-Tetraeder, welche aber im Gegensatz zu einem Quarzkristall ein regelloses Netzwerk bilden. Um die Glasbildung weiterer chemischer Verbindungen vorhersagen zu können, stellte Zachariasen weitere Regeln in seiner Netzwerkhypothese auf. Unter anderem muss ein Kation in einer Verbindung relativ klein im Verhältnis zum Anion sein. Die sich bildenden Polyeder aus den Anionen und Kationen dürfen nur über deren Ecken verbunden sein. Werden die betrachteten Verbindungen auf Oxide beschränkt, so erfüllen unter anderen Phosphorpentoxid (P2O5), Siliziumdioxid (SiO2) und Bortrioxid (B2O3) diese Bedingungen zur Netzwerkbildung und werden daher als Netzwerkbildner bezeichnet.[4]:5 ff.
Wie die zweidimensionalen Abbildungen des Quarzes und des Quarzglases zeigen, liegt der Unterschied in der Regelmäßigkeit des atomaren Aufbaus. Beim Quarz, welcher ein Kristall ist, liegt ein Gitteraufbau vor – beim Quarzglas hingegen ein regelloses Netzwerk von aneinandergereihten SiO4-Tetraedern. Zur besseren Anschaulichkeit ist die vierte Oxidbindung, die aus der Zeichenebene hinaus ragen würde, nicht dargestellt. Die Bindungswinkel und Abstände im Glas sind nicht regelmäßig und die Tetraeder sind ebenfalls verzerrt. Der Vergleich zeigt, dass Glas ausschließlich über eine Nahordnung in Form der Tetraeder verfügt, jedoch keine kristalline Fernordnung aufweist. Diese fehlende Fernordnung hat die sehr schwierige Analyse der Glasstruktur zur Folge. Insbesondere die Analyse in mittlerer Reichweite, also die Verbindungen mehrerer Grundformen (hier den Tetraedern), ist Gegenstand der Forschung und wird zu den heutigen größten Problemen der Physik gezählt.[4]:90 ff. Das liegt zum einen daran, dass Gläser röntgenographischen Untersuchungen nur sehr schwer zugänglich sind und zum anderen daran, dass die strukturbildenden Prozesse teilweise bereits in der Schmelze beginnen, wobei die vorliegenden Temperaturen eine genaue Untersuchung zusätzlich erschweren.[5]:68
Das Material, das diese Grundstruktur des Glases bestimmt, heißt Netzwerkbildner. Neben dem erwähnten Siliciumoxid können auch andere Stoffe Netzwerkbildner sein, wie Bortrioxid und auch nichtoxidische wie Arsensulfid. Einkomponentengläser sind jedoch sehr selten. Das trifft auch auf reines Quarzglas zu, das als einziges Einkomponentenglas wirtschaftliche Bedeutung hat. Die Ursache hierfür sind die enorm hohen Temperaturen (über 2000 °C) welche zu dessen Erzeugung notwendig sind.[4]:154[25]
Weitere Stoffe binden sich anders in das Glasnetzwerk der Netzwerkbildner ein. Hier werden Netzwerkwandler und Stabilisatoren (oder auch Zwischenoxide) unterschieden.[4]:5 ff.[5]:51 f.
Netzwerkwandler werden in das vom Netzwerkbildner gebildete Gerüst eingebaut. Für gewöhnliches Gebrauchsglas – Kalk-Alkali-Glas (gebräuchlicher ist allerdings der engere Terminus Kalk-Natron-Glas) – sind dies Natrium- bzw. Kaliumoxid und Calciumoxid. Diese Netzwerkwandler reißen die Netzwerkstruktur auf. Dabei werden Bindungen des Brückensauerstoffs in den Siliciumoxid-Tetraedern aufgebrochen. Anstelle der Atombindung mit dem Silicium geht der Sauerstoff eine deutlich schwächere Ionenbindung mit einem Alkaliion ein.[4]:5 ff.[5]:51 f.
Zwischenoxide wie Aluminiumoxid können als Netzwerkbildner und -wandler fungieren, das heißt, sie können ein Glasnetzwerk verfestigen (stabilisieren) oder genau wie die Netzwerkwandler die Strukturen schwächen. Ihre jeweilige Wirkung in einem Glas ist stets abhängig von einer Reihe von Faktoren. Allerdings sind Zwischenoxide allein nicht zur Glasbildung fähig.[4]:5 ff.[5]:51 f.
Übergang von der Schmelze zum festen Glas
Während bei kristallinen Materialien der Übergang von der Schmelze zum Kristall durch langsame Abkühlung erfolgt, ist dieser Vorgang bei Gläsern so rasch, dass sich keine Kristallstruktur bilden kann. Der Übergangsbereich von einer Schmelze zum Glas wird Transformationsbereich genannt.[5]:29 f. Im Laufe der Abkühlung nimmt die Viskosität des Materials stark zu. Dies ist das äußere Zeichen für eine zunehmende innere Struktur. Da diese Struktur kein regelmäßiges Muster aufweist, heißt der Zustand der Schmelze im Transformationsbereich, wie auch des erstarrten Glases, amorph. Am kühlen Ende des Transformationsbereichs liegt ein thermodynamischer Übergang, der für Glas charakteristisch ist und daher den Namen Glasübergang trägt. An ihm wandelt sich die Schmelze in den festen, glasartigen Zustand, den das Glas auch bei weiterer Abkühlung beibehält. Der Glasübergang zeichnet sich durch eine sprunghafte Änderung des Wärmeausdehnungskoeffizienten sowie eine Abnahme der spezifischen Wärme aus.[5]:36 ff.[4]:3 ff. Diese Abfolge von Transformationsbereich und Glasübergang ist charakteristisch für alle Gläser, auch solche, die wie Plexiglas aus Kohlenwasserstoffen bestehen. Der amorphe, viskose Zustand der Schmelze im Transformationsbereich wird für die Bearbeitung von Glas durch Glasbläser ausgenutzt. Er erlaubt eine beliebige Verformung, ohne dass Oberflächenspannung und Gravitation das Werkstück sofort zerfließen lassen.[2]:7 f.
Physikalische Eigenschaften
Eigenschaft | Wert | Einheit |
---|---|---|
Dichte eines Kalk-Natron-Glas | 2500 | kg/m³ |
Dichte eines Schwerflintglases (SF59)[26] | 6260 | kg/m³ |
Wärmeleitfähigkeit Kalk-Natron-Glas | 0,80 | W/(K·m) |
Wärmeleitfähigkeit Quarzglas[27] | 1,38 | W/(K·m) |
Wärmeleitfähigkeit Zerodur | 1,46 | W/(K·m) |
Elektrische Leitfähigkeit | bis ca. 600 °C Isolator | |
Thermische Ausdehnung Kalk-Natron-Glas[28] | 9,0·10−6 | 1/K |
Thermische Ausdehnung Borosilikatglas 3.3[28] | 3,3·10−6 | 1/K |
Thermische Ausdehnung Quarzglas[28] | 0,57·10−6 | 1/K |
Thermische Ausdehnung Zerodur | < 0,1·10−6 | 1/K |
Zugfestigkeit | 30 | MPa |
Druckfestigkeit | 900 | MPa |
E-Modul | 70.000 | MPa |
Wärmekapazität | 0,8 | kJ/(kg·K) |
Transmission (Physik) | 0–100 | % |
Brechungsindex (siehe Optisches Glas) | 1,47 bis 1,95 | |
Die im allgemeinen Sprachgebrauch tragende Eigenschaft von Glas ist die optische Durchsichtigkeit. Die optischen Eigenschaften sind so vielfältig, wie die Anzahl der Gläser. Neben klaren Gläsern, die in einem breiten Band für Licht durchlässig sind, kann die Zugabe von speziellen Materialien zur Schmelze die Durchlässigkeit blockieren. Zum Beispiel werden damit optisch klare Gläser für infrarotes Licht undurchdringbar, die Wärmestrahlung ist blockiert. Die bekannteste Steuerung der Durchlässigkeit ist die Färbung. Die verschiedensten Farben können erzielt werden. Andererseits gibt es undurchsichtiges Glas, das schon aufgrund seiner Hauptkomponenten oder der Zugabe von Trübungsmitteln opak ist.[5]:149, 286 f., 304 ff.
Gebrauchsglas hat eine Dichte von ca. 2500 kg/m³ (Kalk-Natron-Glas).[29] Die mechanischen Eigenschaften variieren sehr stark. Die Zerbrechlichkeit von Glas ist sprichwörtlich. Die Bruchfestigkeit wird stark von der Qualität der Oberfläche bestimmt.[4]:240 Glas ist weitgehend resistent gegen Chemikalien. Eine Ausnahme ist Flusssäure; sie löst das Siliciumdioxid und wandelt es zu Hexafluorokieselsäure.[4]:305 f. Durch Verwitterung, bspw. jahrzehntelange Lagerung im Erdreich, entstehen mikroskopisch feine Risse an der Glasoberfläche, die sogenannte Glaskrankheit. Klarglas erscheint dann für das menschliche Auge trüb.[4]:310 ff.[30] Bei Raumtemperatur hat Kalk-Natron-Glas einen hohen elektrischen Widerstand, der allerdings mit steigender Temperatur stark abfällt. Quarzglas (glasartig erstarrtes reines Siliciumdioxid) ist auch noch bei deutlich höheren Temperaturen ein Isolator.[4]:272 ff. Neben den Silikatgläsern gibt es aber auch sog. metallische Gläser wie Fe80B20, die bereits bei Raumtemperatur höhere Leitfähigkeiten besitzen, weil sie sich ähnlich wie eingefrorene flüssige Metalle verhalten.[5]:226
Wegen seiner Natur als unterkühlte Schmelze kann Glas auch in sehr begrenztem Umfang fließen. Dieser Effekt macht sich aber erst bei höheren Temperaturen bemerkbar. Die häufige Behauptung, dass Kirchenfenster unten dicker seien, weil das Glas im Laufe der Jahrhunderte durch die Schwerkraft nach unten geflossen sei, ist falsch, derartige Fließvorgänge hätten bei Raumtemperatur Jahrmillionen benötigt. Die Verdickung ist auf das damalige Produktionsverfahren (Zylinderblasen) zurückzuführen.[31]
Produktionsprozesse
Gemenge
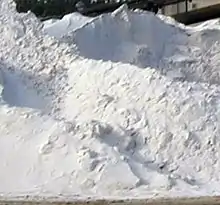
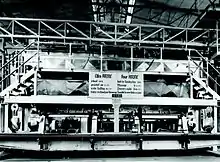
Das Kalk-Natron-Glas ist das vorherrschende Massenglas und macht circa 90 % des weltweit produzierten Glases aus.[32] Grundsätzlich besteht dieses Glas aus Siliziumdioxid (SiO2), Natriumoxid (Na2O) und Calciumoxid (CaO). Im alltäglichen Gebrauchsglas, welches nach wie vor zur Familie der Kalk-Natron-Gläser gehört, werden aber verschiedene weitere Bestandteile zugegeben, um die Gebrauchseigenschaften und Herstellungsbedingungen zu optimieren. Geringfügige Verunreinigungen der Rohstoffe, die mit den normalen Qualitätsanforderungen an das Gebrauchsglas vereinbar sind, stellen ebenfalls Quellen für weitere (unbeabsichtigte) Glasbestandteile dar. In normalem Glas, wie es zur Fertigung von farblosen Behältern oder Flachglas verwendet wird, finden sich oft gewisse Mengen Aluminiumoxid, Magnesiumoxid und Kaliumoxid, welche bewusst zugegeben werden. Durch Verunreinigungen finden sich weiterhin kleinere Mengen von Eisenoxiden, Titanoxid und beispielsweise Chrom(III)-oxid im Glas wieder.[33] Die häufigsten Rohstoffe in der Massenglasproduktion können der nachfolgenden Liste entnommen werden:
- Quarzsand ist ein fast reiner SiO2-Träger zur Netzwerkbildung. Wichtig ist, dass der Sand nur einen geringen Anteil an Fe2O3 besitzen darf (< 0,05 %), da sonst bei Weißglas störende Grünfärbungen auftreten.[34][33] Dieser Rohstoff macht mit über 70 % massenmäßig den größten Teil des Gemenges aus, und ist eine der Hauptquellen für Verunreinigungen.[35]
- Soda (Na2CO3) dient als Natriumoxidträger, das als Netzwerkwandler und als Flussmittel dient und den Schmelzpunkt des SiO2 senkt. In der Schmelze wird Kohlenstoffdioxid frei und löst sich als Gas aus dem Glas.[36] Soda ist im Bereich der Massengläser der teuerste Rohstoff, da er kaum als natürlich vorkommendes Mineral verfügbar ist. Natrium kann der Schmelze auch als Nitrat oder Sulfat zugeführt werden (Natriumsulfat ist Läutermittel zur Reduzierung des Blasengehaltes).[37][35]
- Pottasche (K2CO3) liefert Kaliumoxid für die Schmelze, das wie Natriumoxid als Netzwerkwandler und Flussmittel dient.[35][36]
- Feldspat (NaAlSi3O8) trägt neben SiO2 und Na2O auch Tonerde (Al2O3) in das Gemenge ein. Diese führt zu einer Erhöhung der chemischen Beständigkeit gegenüber Wasser, Nahrungsmitteln und Umwelteinflüssen.[4]:318 ff.[38]
- Kalk dient als Netzwerkwandler. Während der Schmelze zersetzt er sich zu Kohlendioxid und Calciumoxid. CaO erhöht in mäßiger Zugabe (10–15 %) die Härte und chemische Beständigkeit des Endproduktes.[39][4]:318 ff., 273
- Dolomit ist ein Träger für CaO und MgO. Magnesiumoxid wirkt auf die Schmelze ähnlich wie Calciumoxid. Ein zu hoher MgO-Gehalt im Glas kann jedoch die Liquidustemperatur unerwünscht erhöhen und zu Entglasungen führen.[40]
- Altglas oder Eigenscherben aus dem Produktionsbruch werden ebenfalls dem Gemenge wieder zugegeben. Altglas aus dem Glasrecycling geht vor allem in die Behälterglasindustrie, denn Glasflaschen bestehen heute im Schnitt zu rund 60 % aus Altglas, grüne Flaschen aus bis zu 95 %,[41][42] und in die Herstellung von Glaswolle, wo ihr Anteil bis zu 80 % beträgt.[43] Dies spart Rohstoff und Energie, da Scherben leichter schmelzen als das Gemenge und die chemischen Reaktionen wie beispielsweise die Dekarbonatisierung von Soda, Kalk und Dolomit nicht mehr stattfinden müssen.[41] Recycelte Scherben sind eine weitere Hauptquelle für Verunreinigungen, da die Farbsortierung bei Altglasrecycling Probleme bereitet und weitere unerwünschte Fremdstoffe wie Metalle, Keramik oder Spezialgläser nur ungenügend ausgelesen worden sein können. Die Fremdstoffe verursachen Glasfehler durch nicht vollständiges Aufschmelzen oder ungewollte Färbungen des Glases und Schäden in der Glasschmelzwanne, da sich Metalle in den feuerfesten Boden einfressen.[41][2]:366 ff.
Für Spezialgläser kommen auch Mennige, Borax, Bariumcarbonat und seltene Erden zum Einsatz.[44][45][46][47]
Schmelze
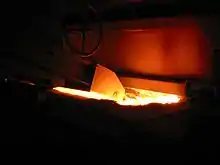
Die Glasschmelze lässt sich in drei Phasen unterteilen:
- Sie beginnt mit der Rauschmelze, die das Erschmelzen des Gemenges und seine Homogenisierung umfasst.
- Im Anschluss erfolgt die Läuterung, in der die Gase ausgetrieben werden.
- Zuletzt wird die geläuterte Schmelze auf die gewünschte Formgebungstemperatur abgekühlt („Abstehen des Glases“).[48]
Bei chargenweise arbeitenden Tageswannen und Hafenöfen geschehen diese Schritte nacheinander in demselben Becken.[49][50] Dieses historische Produktionsverfahren findet heute nur noch bei kunsthandwerklicher Produktion und speziellen, optischen Gläsern in geringen Mengen statt. Im industriellen Maßstab finden ausschließlich kontinuierlich arbeitende Öfen Verwendung.[51] Hier ist die Abfolge obiger Schritte nicht zeitlich, sondern räumlich getrennt, auch wenn die einzelnen Abschnitte fließend ineinander übergehen.[49] Die Menge des zugeführten Gemenges muss derjenigen der Glasentnahme entsprechen. Die notwendige Energie zum Erschmelzen des Glases kann durch fossile Brennstoffe oder elektrische Energie, mittels Stromdurchgang durch die Schmelze, erbracht werden.
Das Gemenge wird der Schmelzwanne mit einer Einlegemaschine am Einlegevorbau, dem Doghouse, aufgegeben. Da das Gemenge eine geringere Dichte als die Glasschmelze besitzt, schwimmt dieses auf der Schmelze und bildet den sogenannten Gemengeteppich.[52][48] Bei Temperaturen von ca. 1400 °C und mehr schmelzen die verschiedenen Bestandteile langsam auf. Einige der Gemengebestandteile können zusammen Eutektika bilden und bereits bei wesentlich geringeren Temperaturen erste Schmelzphasen bilden.[53][54] Die Konvektion im Glasbad bewirkt einen kontinuierlichen Abtransport von Material, das sich vom Gemengeteppich löst. Gleichzeitig bewirkt sie eine Erwärmung des Gemenges. Somit erzeugt sie sowohl eine thermische, als auch eine chemische Homogenität der Schmelze.[55] Diese kann durch ein Bubbling, die Eindüsung von Luft oder Gasen in die Schmelze, unterstützt werden.[56]
Im Läuterbereich, der dem Schmelzbereich unmittelbar folgt, und häufig auch durch einen Wall in der Schmelze von diesem getrennt ist, werden in der Schmelze verbliebene Gase ausgetrieben.[57] Zu diesem Zweck wird dem Gemenge zuvor ein sogenanntes Läutermittel zugegeben. Dieses Läutermittel zersetzt sich bei einer bestimmten Temperatur unter Gasbildung. Aufgrund von Partialdruckdifferenzen diffundieren nun Gase aus der Schmelze in die Läutermittel-Gasblasen ein, welche dadurch anwachsen und aufsteigen. Um diesen Prozess in wirtschaftlich vertretbaren Zeiten durchführen zu können, herrschen im Läuterteil einer Glasschmelzwanne ähnlich hohe Temperaturen wie im Schmelzteil, weil eine zu hohe Viskosität der Schmelze das Aufsteigen der Gasblasen stark verlangsamen würde. Da die Läuterung bestimmend für die Glasqualität ist, gibt es vielfältige unterstützende Maßnahmen.[57][58]
Dem Läuterbereich schließt sich die baulich klar getrennte Arbeitswanne an. Da für die Formgebung niedrigere Temperaturen als zur Schmelze und Läuterung nötig sind, muss das Glas vorher abstehen, das Gefäß heißt daher auch Abstehwanne. Der Kanal, der Schmelzwanne und Arbeitswanne verbindet, wird Durchlass genannt und arbeitet nach dem Siphonprinzip. Bei Flachglaswannen sind Schmelz- und Arbeitswanne nur durch eine Einschnürung getrennt, da ein Durchlass eine optische Unruhe im Fertigprodukt entstehen ließe.[59]
Von der Arbeitswanne fließt das Glas weiter zum Entnahmepunkt, wo dann die Formgebung stattfindet. Bei der Produktion von Hohlglas sind dieses die Speiser oder Feeder. Hier werden Tropfen erzeugt, die über ein Rinnensystem in darunter stehende Glasmaschinen geleitet werden. Bei der Flachglasherstellung nach dem Floatglasverfahren fließt das Glas über einen Lippstein in das Floatbad.[60][61]
Formgebung
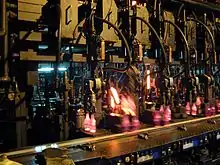
Je nach Produkt wird Glas unterschiedlich geformt. Die Formung erfolgt durch Pressen, Blasen, Schleudern, Spinnen, Walzen oder Ziehen:
- Hohlglas wird in mehreren Verfahren durch Pressen, Blasen, Saugen und Kombinationen dieser Techniken hergestellt. Hier dominiert die IS-Maschine, die im Blas-Blas- oder Press-Blas-Verfahren arbeitet. Für höherwertige Tafelware kommen Press-Blas-Verfahren zum Einsatz, die karussellförmig arbeiten und als Rundläufer oder Rotationsblasmaschine bezeichnet werden.[62]
- kontinuierliche Glasfasern werden durch Spinnen im so genannten TEL-Verfahren produziert[63]
- Glasfasern für beispielsweise Glaswolle werden erzeugt, indem sie durch ein Sieb geschleudert werden[64]
- Flachglas wird hauptsächlich im Floatverfahren hergestellt, kann aber auch nach verschiedenen älteren Verfahren gezogen, gewalzt oder gegossen werden. Manufakturen bieten seit einiger Zeit auch wieder vermehrt handgeblasenes Flachglas an, das Antikglas (oder in Anlehnung an seine Herstellungsmethode auch Zylinderglas) genannt wird.[65][66][67]
- Rohrglas wird durch verschiedene kontinuierliche Ziehverfahren hergestellt, großformatige Glasrohre werden in einem speziellen Schleuderverfahren erzeugt.[68]
Kühlung
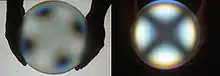
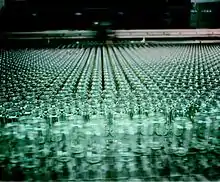
In jedem Glasgegenstand entstehen bei der Formgebung mechanische Spannungen als Folge einer Zwangsformgebung oder Dehnungsunterschiede im Material aufgrund von Temperaturgradienten.[2]:46 Diese Spannungen lassen sich mit optischen Spannungsprüfern unter polarisiertem Licht geometrisch messen (Spannungsdoppelbrechung). Die Spannungsanfälligkeit hängt vom Ausdehnungskoeffizienten des jeweiligen Glases ab und muss thermisch ausgeglichen werden.[2]:107 ff.
Für jedes Glas lässt sich ein Kühlbereich festlegen, welcher von der sogenannten oberen und unteren Kühltemperatur begrenzt wird. Die Lage dieser Temperaturen definiert sich nach der Viskosität, so ist die obere Kühltemperatur diejenige Temperatur bei der das Glas eine Viskosität von 1012 Pa·s besitzt. Bei der unteren Kühltemperatur liegt eine Viskosität 1013,5 Pa·s vor. In der Regel erstreckt sich der Kühlbereich, für die meisten kommerziell genutzten Gläser, zwischen 590 °C und 450 °C. Die Spannungen werden durch Tempern verringert, also durch definiertes langsames Abkühlen, da bei den hier vorherrschenden Viskositäten eine Spannungsrelaxation gerade noch möglich ist und bleibende Spannungen im Glaskörper vermieden werden.[2]:7-10
Die Zeit, in der ein Glasgegenstand den Kühlbereich durchlaufen kann, hängt maßgeblich von der je nach Glasart zu überbrückenden Temperatur und der Stärke (Dicke) des Gegenstands ab. Im Hohlglasbereich sind dies zwischen 30 und 100 Minuten, bei großen optischen Linsen mit 1 m Durchmesser und mehr kann eine langsame Abkühlung von einem Jahr notwendig sein, um sichtbare Spannungen und somit Bildverzeichnungen der Linse zu vermeiden.[2]:46 ff. Die Kühlrate ist bei optischen Gläsern, nach der chemischen Zusammensetzung, der zweite wichtige Parameter zur Einstellung von Brechungsindex bzw. Dispersion und deshalb generell von besonderer Bedeutung im Produktionsprozess.[69]
Es gibt zwei Arten von Kühlaggregaten, die zum Entspannungskühlen von Glasgegenständen genutzt werden können: die periodisch arbeitenden Kühlöfen und kontinuierlich betriebene Kühlbahnen. In der Praxis geschieht jedoch zumeist keine klare Abgrenzung zwischen diesen beiden Fällen, so wird beispielsweise das kontinuierlich betriebene Kühlaggregat in der Flachglasindustrie häufig als Rollenkühlofen bezeichnet.[70]
Kühlöfen eignen sich nur für Sonderfertigungen und Kleinstchargen, da nach jeder Entnahme der Werkstücke der Ofen wieder auf Temperatur gebracht werden muss. Industriell werden Kühlbahnen genutzt. In der Hohlglasindustrie erfolgt der Transport der Glasgegenstände auf Stahlmatten oder Kettenbändern durch die Kühlbahn, während das kontinuierliche Glasband in der Flachglasindustrie mittels Rollen durch die Kühlbahn transportiert wird. Vor den Kühlbahnen (regional auch Kühlbänder genannt) wurden für mittlere Sortimente sogenannte Zugöfen verwendet. Nachdem der Zug im Ofen mit Gläsern gefüllt war, wurde der eine Wagen aus dem Ofen heraus- und ein leerer Wagen hereingefahren. Der heiße Wagen wurde mit isolierten Blechen verhängt und konnte langsam abkühlen, bevor er entleert wurde. Pro Schicht wurden meist drei Wagenwechsel durchgeführt.[71][72][73]
Die bisher geschilderten Vorgänge lassen sich unter dem Begriff des Entspannungskühlen, also dem Kühlen eines Glaskörpers mit dem Zweck bleibende Spannungen zu vermeiden, zusammenfassen. Als einen umgekehrten Fall kann das thermische Vorspannen von Glas zur Herstellung von beispielsweise Einscheibensicherheitsglas betrachtet werden. Dabei wird das Glas von einer Temperatur oberhalb seiner Transformationstemperatur so schnell abgekühlt, dass die thermisch erzeugten Spannungen nicht mehr abgebaut werden können. Infolgedessen entstehen im Glasvolumen Zugspannungen und in der Glasoberfläche Druckspannungen, die ursächlich für eine gesteigerte Festigkeit und Temperaturwechselbeständigkeit des Glaskörpers sind.[74]
Oberflächenveredelung
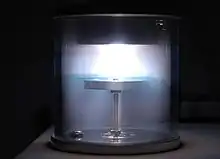
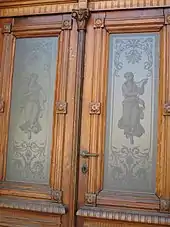
Eine Oberflächenveredelung entsteht durch das Aufbringen von Schichten oder das Abtragen von Schichten, sowie das Modifizieren der Struktur oder der Chemie der Glasoberfläche. Sinn und Zweck solcher Maßnahmen ist die Verbesserung der bestehenden Gebrauchseigenschaften eines Glasgegenstandes oder die Erzeugung neuer Anwendungsgebiete für einen Glasgegenstand.[75]
- Durch chemische und physikalische Gasphasenabscheidung können feinste Metallbeschichtungen aufgebracht werden. Die meisten Fenster- und Autogläser werden auf diese Weise mit für Infrarotlicht undurchlässigen Beschichtungen versehen. Die Wärmestrahlung wird reflektiert und Innenräume heizen durch Sonneneinstrahlung weniger auf. Gleichzeitig werden die Wärmeverluste im Winter reduziert, ohne dabei die Durchsichtigkeit wesentlich zu beeinträchtigen.[76][77]
- Die Beschichtung mit dielektrischem Material, das selbst durchsichtig ist, aber einen vom Glasträger abweichenden Brechungsindex aufweist, ermöglicht sowohl Verspiegelungen als auch eine Entspiegelung. Dies wird bei der Herstellung von Brillengläsern und Linsen für Fotoapparate eingesetzt, um störende Reflexionen zu vermindern. Für wissenschaftliche Zwecke werden Schichten hergestellt, die mehr als 99,9999 % des einfallenden Lichts einer bestimmten Wellenlänge reflektieren. Umgekehrt kann auch erreicht werden, dass 99,999 % des Lichts die Oberfläche passieren.[76][78][79][80]
- Durch Sandstrahlen oder mit Flusssäure kann die Oberfläche so weit aufgeraut werden, dass das Licht stark gestreut wird. Es erscheint dann milchig und nicht mehr durchsichtig, jedoch wird weiterhin nur sehr wenig Licht absorbiert. Daher wird diese Technik häufig für Lampenschirme oder blickdichte Fenster angewandt (siehe auch Satinieren).[81]
- Ebenfalls mit Flusssäure lässt sich die Oberfläche eines Glases säurepolieren. Dabei werden die beschädigten Oberflächenschichten abgetragen was zu defektfreien Oberfläche und somit einer erhöhten Festigkeit des Glasgegenstandes führt.[81]
- Eine weitere häufig eingesetzte Oberflächenveredelungsmethode ist die Entalkalisierung der Glasoberfläche. Durch Reaktion der heißen Glasoberfläche mit aggressiven Gasen (z. B. HCl oder SO2) bilden sich mit den Alkalien aus dem Glas Salze, welche sich auf der Glasoberfläche abscheiden. Das an Alkalien verarmte Glas zeigt infolgedessen eine erhöhte chemische Beständigkeit.[82]
- Während der Hohlglasproduktion wird dem Glas in zwei Schritten eine sogenannte Heiß- und Kaltendvergütung aufgebracht. Diese beiden Vergütungen sollen verhindern, dass sich die Glasflaschen während der Produktion und späteren Befüllung gegenseitig beschädigen, indem ihr Reibkoeffizient verringert wird und sie so im Falle eines Kontaktes aneinander vorbeigleiten, statt sich gegenseitig zu zerkratzen. Hierfür werden verschiedene Zinn- und Titanverbindungen als Schichten verwendet.[83]
Qualitätskontrolle
Um die Qualität des Glases sicherzustellen, müssen regelmäßig umfangreiche Untersuchungen durchgeführt werden, hierzu zählen:
- Online-Kontrolle in der Glashütte (optische Prüfungen aller einzelnen Glaserzeugnisse auf Maßhaltigkeit, Risse, Relikten, Verunreinigungen etc.)
- tägliche oder wöchentliche chemische Glasanalyse mit der ICP-OES, um u. a. auch die Schwermetalle im Verpackungsglas zu überwachen (Forderung der Verpackungsverordnung)
- wöchentliche oder monatliche Fe2+-Analyse und Analyse des Redoxzustandes, um so das Schmelzaggregat und die Qualität der verwendeten Recyclingglasqualitäten zu beurteilen[84]
- tägliche Spannungsprüfungen mit Rotlicht 1. Ordnung unter dem Mikroskop um Bruchprobleme zu reduzieren
- bei Bedarf Bruchanalysen mit der REM-EDX
Glasfärbung und Entfärbung
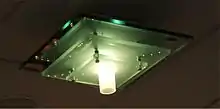
Grundsätze
Die meisten Glassorten werden mit weiteren Zusatzstoffen produziert, um bestimmte Eigenschaften, wie ihre Färbung, zu beeinflussen. Grundsätzlich werden bei Gläsern drei Farbgebungsmechanismen unterschieden, die Ionenfärbung, die kolloidale Färbung und die Anlauffärbung. Während die erstgenannte Möglichkeit hauptsächlich auf der Wechselwirkung des Lichtes mit den Elektronenhüllen der farbgebenden Elemente beruht, treten bei den letzten beiden unterschiedlichste Beugungs-, Reflexions- und Brechungserscheinungen des Lichts auf, die stark abhängig von dispergierten Phasen sind. Im Falle der Anlauffärbung handelt es sich um eine Elektronenanregung im Kristallgitter des Chromophors.[5] :275 ff.[85]
Ionenfärbung
Als färbende Substanzen in Gläsern werden Metalloxide, sehr häufig 3d-Elemente, eingesetzt. Die Entstehung der Farbwirkung beruht auf der Interaktion der äußeren Elektronen mit elektromagnetischen Wellen. Dabei kann es zur Absorption bestimmter Wellenlängen und zur Emission anderer Wellenlängen kommen. Werden Wellenlängen des sichtbaren Lichtes absorbiert, entsteht eine Farbwirkung, da das übriggebliebene Wellenlängenspektrum kein weißes Licht mehr ergibt. Die Färbung kann also als eine selektive Transmission betrachtet werden.[5]:255 ff. Die tatsächliche Färbung eines Glases ist von einer Vielzahl von Parametern abhängig. Neben der Konzentration der farbgebenden Ionen ist auch deren Koordination und die umgebende Glasstruktur von entscheidender Bedeutung. Beispielsweise ergibt Cobalt(II)-oxid in einem Silikatglas einen anderen Blauton als in einem Phosphatglas.[5]:251 ff.[85] Um einen speziellen Farbton zu erhalten, können die verschiedenen farbgebenden Oxide miteinander kombiniert werden, jedoch müssen dabei eventuell auftretende Wechselwirkungen beachtet werden.[5]:264 f.
Anlauffärbung
Zu den Anlaufgläsern gehören die durch Chalkogenide gefärbten Gläser, die hauptsächlich in silikatischen Gläsern mit hohen Zink- und Kaliumoxidgehalten Anwendung finden. Am häufigsten werden hierfür Cadmiumsulfid oder Cadmiumselenid in geringen Prozentbereichen zugegeben, aber auch andere Metallchalkogenide sind denkbar.[5]:266 Das Glas wird unter reduzierenden Bedingungen erschmolzen, wobei zunächst farbloses Glas entsteht. Erst eine anschließende Temperung bewirkt, dass die Gläser farbig werden – sie laufen an. Mit zunehmender Dauer wandert die UV-Kante des Glases immer mehr in den sichtbaren Bereich hinein. Durch eine gezielte Temperung können somit unterschiedliche Farbwirkungen erzielt werden. Ursache für dieses Verhalten sind mikroskopische (Cadmium-)Chalkogenidkristalle, die sich während des Temperns bilden und mit andauernder Temperzeit weiter wachsen.[5]:267 Es handelt sich also um eine gesteuerte Entglasung. Untersuchungen zeigten, dass sich mit zunehmender Kristallisation des Chalkogenids die Verbotene Zone zwischen Valenz- und Leitungsband vergrößert, was die Ursache für die Verschiebung der UV-Kante in den sichtbaren Bereich ist.[5]:275 ff. Aufgrund ihrer scharfen Farbkante werden diese Gläser häufig als Filtergläser eingesetzt.[5]:268
Kolloidale Färbung
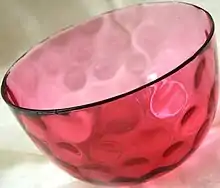
Kolloidalgefärbte Gläser werden oft auch als (echte) Rubingläser bezeichnet. Bei diesen Gläsern werden Metallsalze der Schmelze zugegeben. Zunächst ergibt sich ebenfalls ein farbloses Glas. Durch eine anschließende Temperaturbehandlung werden Metalltröpfchen aus der Glasmatrix ausgeschieden und wachsen an. Die Farbwirkung der Kolloide beruht sowohl auf der Absorption des Lichtes durch die Teilchen als auch der Rayleigh-Streuung des Lichtes an ihnen. Je größer die erzeugten Kolloide werden, umso mehr nimmt ihre Extinktion zu. Gleichzeitig verschiebt sich die Wellenlänge ihrer maximalen Absorption zu langwelligerem Licht hin. Außerdem nimmt mit zunehmender Kolloidgröße der Effekt der Streuung zu, jedoch muss hierfür die Größe des Kolloids sehr viel kleiner als die Wellenlänge des zu streuenden Lichtes sein.[5]:281 ff.
Farbwirkung einzelner Bestandteile (Auswahl)
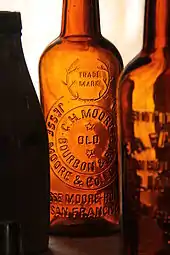
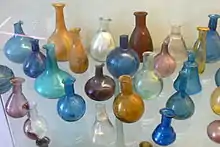
Die nachfolgende Liste enthält einige der häufigeren zur Färbung genutzten Rohstoffe, unabhängig von deren Farbgebungsmechanismus.[5]:226, 284[86][85]
- Eisenoxide: färben je nach Wertigkeit des Eisenions grün-blaugrün (Weinflaschengrün) oder gelb und in Verbindung mit Braunstein gelb sowie braun-schwarz in Verbindung mit Schwefel bei reduzierenden Schmelzbedingungen.
- Kupferoxide: Zweiwertiges Kupfer färbt blau; einwertiges färbt rot, daraus ergibt sich das Kupferrubinglas.
- Chrom(III)-oxid: wird in Verbindung mit Eisenoxid oder allein für die Grünfärbung verwendet.
- Uranoxid: ergibt eine sehr feine Gelb- oder Grünfärbung. (Annagelbglas oder Annagrünglas) mit grüner Fluoreszenz unter Ultraviolettstrahlung. Solche Gläser wurden vor allem in der Zeit des Jugendstils hergestellt. In England und Amerika ist diese Glassorte auch als uranium glass oder vaseline glass bekannt. Aufgrund der Radioaktivität des Urans wird es heutzutage nicht mehr verwendet.
- Cobalt(II)-oxid: färbt intensiv blau und wird auch für die Entfärbung verwendet. Das Cobaltoxid wurde früher in einem aus den Cobalterzen hergestelltem Gemisch zugegeben, das Zaffer oder Safflor genannt wird.
- Nickeloxid: violett, rötlich; es dient auch für die Graufärbung und zur Entfärbung.
- Mangan(IV)-oxid (Braunstein): Es wird als Glasmacherseife zur Entfernung des Grünstichs (durch Absorption der Komplementärfarben) verwendet.
- Selenoxid: färbt rosa und rot. Die rosa Färbung wird als Rosalin bezeichnet, die rote als Selenrubin.
- Silber: ergibt feines Silbergelb.
- Indiumoxid: Es erzeugt gelb bis bernsteinorange Farben.
- Neodym: rosa bis purpur, lila
- Praseodym: grün
- Samarium: gelb
- Europium: intensiv rosa
- Gold: wird erst in Königswasser aufgelöst und färbt rubinrot, eine der teuersten Glasfärbungen (Goldpurpur).
Entfärbung von Gläsern
Die Entfärbung eines Glases ist dann notwendig, wenn durch Verunreinigungen der Rohstoffe größere Mengen an farbgebenden Bestandteilen im Glas vorhanden sind (ungewollter Farbeffekt), oder falls in der regulären Glasproduktion ein Erzeugnis anderer Farbe hergestellt werden soll. Die Entfärbung eines Glases kann sowohl chemisch, als auch physikalisch geschehen.[86] Unter der chemischen Entfärbung werden Änderungen an der Chemie des Glases verstanden, die zur Folge haben, dass die Färbung reduziert wird. Dies kann im einfachsten Fall durch eine Veränderung der Glaszusammensetzung geschehen. Sollten polyvalente Elemente in der Schmelze vorliegen, entscheidet neben deren Konzentration auch deren Oxidationszustand über die Farbwirkung. In diesem Fall kann ein veränderter Redoxzustand einer Glasschmelze die Farbwirkung des fertigen Produktes ebenfalls beeinflussen. Sofern eine Färbung des Glases durch Chalkogenide (Anlauffärbung) verursacht ist, kann der Schmelze Oxidationsmittel zugegeben werden. Diese bewirken eine Zersetzung der Chalkogenide in der Glasschmelze.[5]:267 Eine weitere Möglichkeit, Fehlfarben in einem Glas zu kompensieren, stellt die physikalische Entfärbung dar. Dazu werden kleinste Mengen farbgebender Bestandteile der Schmelze zugegeben. Grundsätzlich dient die komplementäre Farbe zur Beseitigung von Farbstichen. Dadurch entsteht der Effekt eines farblosen Glases. Mit steigender Intensität der ursprünglichen Fehlfärbung werden auch höhere Mengen an Entfärbungsmitteln notwendig, wodurch das Glas zwar farblos, aber zunehmend dunkler wirkt. Entfärbemittel werden Glasmacherseifen (auch Glasseifen) genannt.[86]
Phototropie und Elektrotropie
Hierbei handelt es sich um Färbungen und Entfärbungen, die unter dem Einfluss von mehr oder weniger Sonnenlicht zustande kommen; sie eignen sich für bei starkem Sonnenlicht automatisch dunkel werdende Brillengläser.
Ein ähnlicher Effekt ist mit einem veränderlichen elektrischen Feld erzielbar; er wird u. a. für verdunkelbare Windschutzscheiben verwendet.
Einstellung der Glaseigenschaften allgemein
Glaseigenschaften können mittels statistischer Analyse von Glasdatenbanken ermittelt und optimiert werden. Sofern die gewünschte Glaseigenschaft nicht mit Kristallisation (z. B. Liquidustemperatur) oder Phasentrennung in Zusammenhang steht, ist einfache lineare Regressionsanalyse anwendbar, unter Zuhilfenahme algebraischer Gleichungen der ersten bis zur dritten Ordnung. Viele Verfahren zur Vorausberechnung von Glaseigenschaften sind hauptsächlich empirischer Natur.[4]:162
Die nachstehende Gleichung zweiter Ordnung ist ein Beispiel, wobei C die Konzentrationen der Glaskomponenten wie Na2O oder CaO darstellen. Die b-Werte sind variable Koeffizienten, und n ist die Anzahl aller Glaskomponenten. Der Glas-Hauptbestandteil SiO2 ist in der dargestellten Gleichung ausgeschlossen und wird mit der Konstante bo berücksichtigt. Der Großteil der Glieder in der Beispielgleichung kann aufgrund von Korrelations- und Signifikanzanalyse vernachlässigt werden. Weitere Einzelheiten und Anwendungen siehe.[88]
Oft ist es erforderlich, mehrere Glaseigenschaften sowie die Produktionskosten gleichzeitig zu optimieren. Dies geschieht mit der Methode der kleinsten Quadrate, wodurch der Abstand zwischen den gewünschten Eigenschaften und den vorausberechneten einer fiktiven Glassorte durch Variation der Zusammensetzung minimiert wird. Es ist möglich, die gewünschten Eigenschaften unterschiedlich zu wichten.[89]
Glasart | SiO2 | Al2O3 | Na2O | K2O | MgO | CaO | B2O3 | PbO | TiO2 | F | As | Se | Ge | Te | SO3 |
---|---|---|---|---|---|---|---|---|---|---|---|---|---|---|---|
Quarzglas | ≥99 | – | – | – | – | – | – | – | – | – | – | – | – | – | – |
Borosilikatglas | 70–79 | 1–4,5 | 2–6 | 0–4,4 | 0–0,3 | 0–0,5 | 14–17 | – | – | – | – | – | – | – | – |
Kronglas | 73 | 2 | 5 | 17 | – | 3 | – | – | – | – | – | – | – | – | – |
Kalk-Natron-Glas | 71–73 | 1–2,4 | 14–17 | 0,2–1,6 | 2,6–3,8 | 4,2–6,6 | – | – | – | – | – | – | – | – | – |
Floatglas[92] | 72–72,6 | 0,1–1,1 | 13,5–14 | ≤ 0,7 | 4–4,1 | 8,4–8,8 | – | – | ≤ 0,2 | – | – | – | – | – | 0,2 |
Flintglas | 62 | – | 6 | 8 | – | – | – | 24 | – | – | – | – | – | – | – |
Bleikristallglas | 58 | – | 4 | 9 | – | – | 2 | 24 | – | – | – | – | – | – | – |
Glasfaser | 54 | 14 | – | – | 4,5 | 17,5 | 10 | – | – | – | – | – | – | – | – |
40 | 1,5 | 9 | 6 | 1 | – | 10 | 4 | 15 | 13 | – | – | – | – | – | |
Chalkogenidglas 1 | – | – | – | – | – | – | – | – | – | – | 12 | 55 | 33 | – | – |
Chalkogenidglas 2 | – | – | – | – | – | – | – | – | – | – | 13 | 32 | 30 | 25 | – |
Glasart | SiO2 | Al2O3 | Fe2O3 | Na2O | K2O | MgO | CaO | H2O |
---|---|---|---|---|---|---|---|---|
Kalknatron-Silicatgläser | ||||||||
Behälterglas (weiß) | 73 | 2 | – | 13 | 1 | – | 11 | – |
Floatglas | 72 | 0,5 | – | 14 | – | 4,5 | 9 | – |
Historische Gläser | ||||||||
mesopotamisches Glas | 68 | 1 | 0,5 | 14,5 | 3 | 5 | 8 | – |
römisches Glas | 70 | 2 | 0,5 | 18 | 1 | 1 | 7,5 | – |
mittelalterliches Kirchenfensterglas | 49 | 2 | 0,5 + 1 P2O5 | 0,5 | 20 | 4 | 23 | – |
Natürliche Gläser | ||||||||
Obsidian | 75 | 14 | 0,5 | 4 | 5 | – | 1 | 0,5 |
Tektite | 79 | 10 | 3 | 0,5 | 2,5 | 2 | 3 | – |
Libysches Wüstenglas | 98 + 0,2 TiO2 | 1,3 | 0,3 | – | – | – | – | 0,2 |
Glas-Zuschlagstoffe sind unter anderem:
- andere Flussmittel zur Herabsetzung des Schmelzpunkts[4]:156 ff.
- zur Veränderung des Brechungsindex[4]:204 ff.
- Bariumoxid
- Bleioxid (absorbiert auch Röntgenstrahlung)
- Trübungsmittel:[5]:299 ff.
- Cer wird verwendet, um Glas gegen radioaktive und Röntgenstrahlung zu stabilisieren.[94]
- Boroxid als Zusatz verändert die thermischen und elektrischen Eigenschaften.[4]:173 f., 279
- Aluminiumoxid erhöht die Bruchfestigkeit.[4]:252 f.
Geschichte der Glasherstellung
Frühzeit
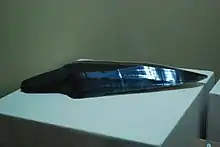
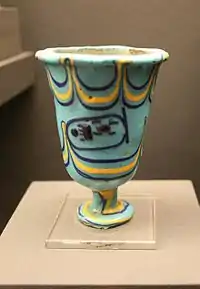
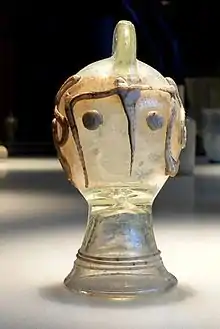
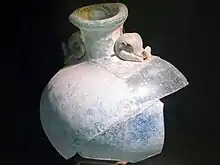
Natürliches Glas wie Obsidian wurde wegen seiner großen Härte und des scharfen Bruchs seit frühester Zeit für Werkzeuge wie Keile, Klingen, Schaber und Bohrer benutzt. Obsidian konnte jedoch – anders als künstlich hergestelltes Glas – mit antiken Mitteln nicht geschmolzen oder gefärbt werden.
Auch die natürlich vorkommenden transluzenten und spaltbaren Minerale Glimmer und Marienglas wurden als Fensterglas verwendet, bevor man in der Lage war, entsprechend große und gleichmäßig dicke Scheiben künstlich herzustellen. Die Römer nannten Marienglas Lapis specularis. Der römische Geschichtsschreiber Plinius der Ältere (23/24–79) beschrieb in seiner Enzyklopädie Naturalis historia den Abbau und die Verarbeitung von Lapis specularis zu Fensterscheiben und Lampen.
Ob die Glasherstellung in Mesopotamien, im alten Ägypten oder an der Levanteküste erfunden wurde, lässt sich nicht mit letzter Gewissheit sagen. Die ältesten Glasfunde stammen aus Mesopotamien; altägyptische Quellen deuten für die Anfangsphase der Glasnutzung in Ägypten auf einen Import aus dem Osten hin. Die älteste textliche Erwähnung stammt aus Ugarit und wird auf etwa 1600 v. Chr. datiert. Als älteste Funde gelten die Nuzi-Perlen. Das älteste sicher zu datierende Glasgefäß ist ein Kelch, der den Thronnamen von Pharao Thutmosis III. trägt und um 1450 v. Chr. entstand. Der Kelch befindet sich seit dem 20. Jahrhundert im Staatlichen Museum Ägyptischer Kunst in München.
Glas wurde in Ägypten seit etwa 1450 v. Chr. zu Gefäßen verarbeitet (siehe unten). Der Herstellungsort dieses frühesten Glases ist allerdings unbekannt, er wird in Theben vermutet, gegenüber dem heutigen Luxor. Die bekannteste Verarbeitungstechnik beruht auf dem Herstellen von Hohlgefäßen durch das Wickeln von erweichten Glasstäbchen um einen porösen Keramikkern, der anschließend herausgekratzt wurde. Die besten Funde hierzu liegen aus den Grabungen von Flinders Petrie aus Amarna vor. Die bislang einzige bekannte bronzezeitliche Glashütte, in der Glas aus seinen Rohstoffen hergestellt wurde, datiert in die Ramessidenzeit und wurde Ende der 1990er Jahre bei Grabungen des Roemer- und Pelizaeus-Museums (Hildesheim) unter der Leitung von Edgar Pusch im östlichen Nil-Delta in Qantir-Piramesse gefunden. Untersuchungen gaben Aufschluss über das Schmelzverfahren. So wurde Quarzgestein zerkleinert, mit sodahaltiger Pflanzenasche vermengt, in einen Krug gefüllt und bei vielleicht 800 °C zu einer Fritte geschmolzen. Diese Fritte wurde nach dem Abkühlen vermutlich zerkleinert und in einer zweiten Schmelze in speziell hergestellten Tiegeln bei 900 bis 1100 °C zu einem 8 bis 10 cm hohen Barren mit 10 bis 14 cm Durchmesser geschmolzen. Das Glas wurde dabei durch Beimischen von Metall-Oxiden schwarz, violett, blau, grün, rot, gelb oder weiß gefärbt. Ein konkreter Zusammenhang von Glasherstellung und Metallgewinnung ist trotz der ähnlichen Temperaturen nicht nachzuweisen. Das gefärbte Rohglas wurde in Barrenform an die weiterverarbeitenden Werkstätten geliefert, die daraus monochrome und polychrome Objekte herstellten. Solche Glasbarren wurden im Schiffswrack von Uluburun nahe dem türkischen Bodrum gefunden, das auf das 14. Jahrhundert v. Chr. datiert ist. Die erste bekannte Rezeptur ist aus der Bibliothek des assyrischen Königs Assurbanipal überliefert, die auf ca. 650 v. Chr. datiert wird: Nimm 60 Teile Sand, 180 Teile Asche aus Meerespflanzen und 5 Teile Kreide und du erhältst Glas. Zu dieser Zeit wurde schon wesentlich mehr Glas verarbeitet, und es entwickelte sich eine neue Glasschmelztechnik.
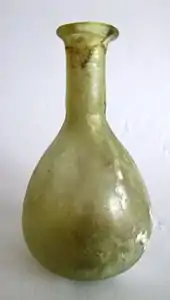
Antike
Plinius der Ältere beschreibt in der Naturalis historia die Herstellung des Glases. Chemische Analysen und Erkenntnisse der experimentellen Archäologie haben Plinius in vielen Fragen bestätigt. Zur Römerzeit wurde Glas (lateinisch vitrum) mit Flusssand und Natron aus Ägypten geschmolzen. Das ägyptische Natron wurde am Wadi Natrun, einem natürlichen Natronsee in Nord-Ägypten, abgebaut und über Alexandria von den Phöniziern in den Mittelmeerraum exportiert. Dieses war verhältnismäßig rein und enthielt mehr als 40 Prozent Natriumoxid (die Angabe wurde wie in der Petrologie üblich auf das Oxid bezogen, faktisch liegt aber Natriumcarbonat vor) und bis zu 4 Prozent Kalk. Die Zusammensetzung machte es zu einem idealen Schmelzmittel. Plinius schreibt weiter von Glassandlagern in Italien, Hispanien und Gallien, aber an keiner dieser Stätten entwickelte sich eine so bedeutende Glasherstellung wie an der palästinischen Küste zwischen Akkon und Tyros sowie in den ägyptischen Glashütten rund um den Wadi Natrun bei Alexandria.
Kaiser Diokletian legte im Jahr 301 die Preise für eine ganze Reihe von Produkten fest, unter anderem für Rohglas. Unterschieden wurde judaicum und alexandrium, wobei Letzteres teurer und wahrscheinlich entfärbtes Glas war. Zu dieser Zeit war die Glasproduktion im Wesentlichen noch immer in Primär- und Sekundärwerkstätten gegliedert. In den Primärwerkstätten wurde in großen Schmelzwannen Rohglas geschmolzen, das dann an die Sekundärwerkstätten geliefert wurde, wo es in Tiegeln eingeschmolzen und verarbeitet wurde. In Bet Eli’ezer im heutigen Israel wurden 17 Glasschmelzwannen freigelegt, die jeweils 2 × 4 m groß sind. Nachdem das Gemenge in die Wanne eingelegt worden war, wurde der Ofen zugemauert und 10 bis 15 Tage lang befeuert. Acht bis neun Tonnen blaues bzw. grünes Rohglas wurden so in nur einem Arbeitsgang erschmolzen. Nach dem Feuerungsstopp und dem Abkühlen wurde das Gewölbe des Ofens abgetragen, der Glasblock herausgestemmt und das Rohglas zur weiteren Verarbeitung versandt. Ein Schiffswrack aus dem 3. Jahrhundert, das an der südfranzösischen Küste gefunden wurde, hatte mehr als drei Tonnen Rohglas geladen.[95] In Ägypten wurden Rohglashütten gefunden, die bis ins 10. Jahrhundert reichten. Die Ägypter benutzten Antimon zur Entfärbung, konnten also farbloses, durchsichtiges Glas herstellen.
Die Sekundärglashütten waren im ganzen Römischen Reich verbreitet und stellten Hohlglas, Flachglas und Mosaiksteine her. Das Rohglas wurde in einem Tiegel eingeschmolzen und mit der Pfeife im zähflüssigen Zustand aus dem Ofen genommen und verarbeitet. An der Pfeife konnte das Glas aufgeblasen werden, was die Herstellung von größeren Gefäßen und neuen Formen ermöglichte. Wurde bis dahin Glas für Perlen, Parfümfläschchen und Trinkschalen verwendet, verbreitete sich im Römischen Reich vor allem Behälterglas – im Gegensatz zu den üblichen Ton-, Holz-, Metall- oder Lederbehältnissen ist Glas geschmacksneutral – sowie Karaffen zum Kredenzen und in der Spätantike auch Trinkgläser. Erste Fenstergläser fanden sich in Aix-en-Provence und Herculaneum. Die Funde haben Größen von bis zu 80 cm × 80 cm. Allerdings erwähnt keine schriftliche Überlieferung das Herstellungsverfahren. Für das frühe, dickwandige und einseitig matte Fensterglas gibt es in der Fachwelt unterschiedliche Auffassungen zu dessen Herstellung. Einerseits wird eine manuelle Strecktechnik[96] in Betracht gezogen, zum Anderen wird von einem Gussverfahren[97] für dessen Herstellung ausgegangen. Für das ab dem 2. Jh. n. Chr. aufkommende, dünnwandige und beidseitig klare Fensterglas ist das Zylinderblasverfahren wahrscheinlich.
Glasarmringe sind eine typische Schmuckform, die neben gläsernen Fingerringen und Ringperlen zur mittleren La-Tène-Zeit im keltischen Mitteleuropa als Frauenschmuck aufkommt und als Grabbeigabe gefunden wird.
Mittelalter und Neuzeit
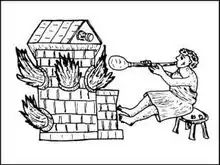
Im frühen Mittelalter stellten die Germanen überall dort, wo die Römer sich zurückgezogen hatten, Glas her, das nahtlos an die schon germanisierte spätantike Formensprache anschließt. Man geht heute davon aus, dass für das fränkische Glas noch vorhandene römische Gläser wiederverwertet wurden.
Waldglas
Mit De diversis artibus des Benediktinermönches Theophilus Presbyter steht erstmals eine längere schriftliche Quelle zur Verfügung, die die Glasherstellung, das Blasen von Flachglas und Hohlglas sowie die Ofentechnologie beschreibt. Theophilus, der wahrscheinlich in Konstantinopel war, vermischte Asche von getrocknetem Buchenholz mit gesiebtem Flusssand im Verhältnis 2:1 und trocknete dieses Gemenge im Ofen unter ständigem Rühren, so dass es nicht schmelzen oder verkleben konnte, einen Tag und eine Nacht. Danach wurde diese Fritte in einen Tiegel gefüllt und in einer Nacht unter starker Hitze zu Glas geschmolzen.
Dieser am Anfang des 12. Jahrhunderts wohl in Köln entstandene Text bildet wahrscheinlich die Grundlage für die Kirchenfenster der Gotik und auch für das Waldglas. Die Pflanzenasche mit allen Verunreinigungen lieferte auch einen Teil des Kalks, der für die Herstellung guten Glases nötig war. Um die enorme Menge an Holz, die für die Befeuerung der Öfen und für die Aschegewinnung nötig war, nicht über lange Wege befördern zu müssen, wurden die Glashütten in abgelegenen Waldgebieten angelegt. Diese Waldglashütten stellten überwiegend Glas her, welches durch Eisenoxid (aus verunreinigtem Sand) grünlich verfärbt war.
Im 15. Jahrhundert wurde auch Blei zur Herstellung von Glas verwendet.[99]
In Georgius Agricolas De re metallica gibt es eine kurze Beschreibung der Glaskunst. Er hat von 1524 bis 1527 in Venedig gelebt und wohl die Insel Murano besuchen dürfen, was die detaillierten Beschreibungen der Öfen vermuten lassen.
Als Rohstoff sind durchsichtige Steine genannt, also Bergkristall und „weiße Steine“, also Marmor, die im Feuer gebrannt, im Pochwerk zu grobem Grieß zerstoßen und danach gesiebt werden. Weiter führt er Kochsalz, Magnetstein und Soda an. Kochsalz und Magnetstein werden von späteren Autoren als unnütz verworfen. Marmor und Soda gab es in Altare und in Mailand; sie sind in Deutschland nicht zu erhalten. Einzig eine Andeutung „salz das aus laugen dargestellt wird“ weist auf ein venezianisches Geheimnis hin.
Die Glasschmelzöfen der Waldglashütten und Venedigs waren eiförmige Konstruktionen mit 3 Meter Durchmesser und bis zu 3 Meter Höhe, gemauert aus mit gebrannter Schamotte versetzten Lehmziegeln. Im unteren Stock lag der Befeuerungsraum mit ein oder zwei halbrunden Öffnungen für den Holzeinwurf. In der Mitte schlugen die Flammen durch eine große runde Öffnung in den zweiten Stock, in dem die Hafenöfen standen. Dieser etwa 1,20 Meter hohe Raum war rundum mit 20 × 20 cm großen Ofentoren versehen, durch die das Gemenge eingelegt und das Glas entnommen werden konnte. Im Obergeschoss, das durch eine kleine Öffnung mit dem Schmelzraum verbunden war, lag der Kühlofen, der nur 400 °C heiß war. Der Kühlofen war mit einer kleinen Öffnung versehen, durch die fertige Werkstücke eingetragen wurden. Am Abend wurde das Loch zwischen Schmelzraum und Kühlraum mit einem Stein verschlossen, so dass das Glas über Nacht abkühlen konnte.
Venedig
Am Anfang der venezianischen Glastradition steht wohl der Handel mit byzantinischen Glaserzeugnissen, die schon im 10. Jahrhundert importiert und nach ganz Europa exportiert wurden. Erste Glasmacher finden sich in den Registern des 11. Jahrhunderts. Sie werden phiolarius („Flaschner“) genannt. Ein an der Südküste der Türkei havariertes Handelsschiff, das um 1025 gesunken ist, transportierte nicht weniger als drei Tonnen Rohglas, das aus Caesarea in Palästina stammte. Ob es für Venedig bestimmt war, lässt sich nicht mit Gewissheit sagen, ist aber naheliegend. Bis 1295 werden alle Glasmacher auf der Insel Murano angesiedelt und ihre Reisefreiheit per Gesetz eingeschränkt. Auf dieser von der Welt abgeschnittenen Insel konnte Angelo Barovier Mitte des 15. Jahrhunderts das Geheimnis der Glasentfärbung lüften und erstmals ungetrübtes, klar durchsichtiges Glas in Europa herstellen. Das crystallo, ein Soda-Kalk-Glas, das mit Manganoxid entfärbt war, sollte den Weltruhm des venezianischen Glases begründen. Die Soda wurde aus der Levante oder Alexandria importiert, ausgelaugt und versotten, bis ein reines Salz entstand. Als Sand wurde ein reiner Glassand aus dem Ticino oder gebrannter Marmor verwendet. Die Manganerze wurden wahrscheinlich von reisenden Erzsuchern aus Deutschland beschafft, die dort als Walen oder Venediger bekannt waren. Eine weitere venezianische Wiederentdeckung ist das lattimo (Milchglas), ein opakes weißes Glas, das mit Zinndioxid und Knochenasche getrübt war und das chinesische Porzellan nachahmte.
Viele neue Techniken wurden entwickelt, insbesondere im 19. und 20. Jahrhundert. Den Höhepunkt erreichte die Branche in den 1950er und 1960er Jahren. Berühmte Techniken aus dieser Zeit sind zum Beispiel: Anse Volante, Battuto, Canna, Colorazione a caldo senza fusione, Fenicio, Incamiciato, Murrina, Oriente, Pezzato, Pulegoso, Scavo, Siderale, Sommerso, Tessuto. Muranoglas gilt heute als begehrtes Sammlerobjekt. Es werden teilweise sehr hohe Summen für seltene und besondere Stücke bezahlt. Berühmte historische Glasmanufakturen sind zum Beispiel Venini & C., Pauly & C., Barovier & Toso, Seguso Vetri d’Arte. Einige dieser Manufakturen bestehen noch heute.
- Kelch von Angelo Barovier (?), Mitte 15. Jahrhundert
- Glasschale mit Vergoldungen, ca. 1510
- Glaskännchen oder -vase, Venedig, ca. 1550–1600
- Vase aus blauem Glas, Murano, um 1600
- Glasteller in reticello-Technik
- Schale aus vetro calcedonio mit Einlagen von vetro aventurino, Murano, um 1700
- Venezianische Gläser, 1880–1890
- Vase in millefiori-Technik, Fratelli Toso, ca. 1900–1910
- Moderne Glasgefäße aus Venedig
- Murano Glas Aschenbecher mit Luftblasen, 1960er Jahre
Glasperlen
Die Glasperlen wurden zu einer begehrten Handelsware und breiteten sich schnell über ganz Europa aus. Über Jahrhunderte waren Glasperlen ein beliebtes Zahlungsmittel im Tauschhandel mit Gold, Elfenbein, Seide und Gewürzen. Seit einigen Jahren sind die bunten Kunstwerke begehrte Objekte für Sammler.
Glasperlen aus Venedig sind die bekanntesten und begehrtesten Perlen der Welt. Venezianische Glaskünstler haben während mehrerer Jahrhunderte Perlenhersteller auf der ganzen Welt beeinflusst. Dort werden die Glasperlen über offener Flamme hergestellt. Es ist ein sehr zeitaufwendiges Verfahren, da jede Perle einzeln gefertigt wird.
Ein Glasstab wird unter der Verwendung einer Lötlampe bis zum Schmelzen erhitzt und um einen Metallstab gewickelt, bis die gewünschte Perlenform erreicht wird. Auf diese Grundperle können nach und nach weitere Glasfarben aufgeschmolzen werden und unterschiedliche Dekorationselemente, wie dünne Glasfäden oder hauchdünne Glasplättchen (Confettis), aufgebracht werden. Dann wird die Perle sehr langsam abgekühlt und von der Stange entfernt, wodurch ein Loch entsteht, durch das die Perle später aufgefädelt werden kann. Diese Perlen heißen Wickelperlen.
Fensterglas
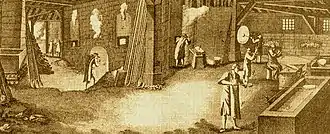
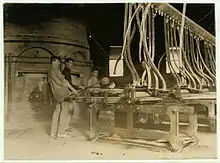
Funde von Fensterglas in Pompeji belegen, dass die Römer bereits im 1. Jahrhundert Fensterglas kannten, das beispielsweise in Thermen oder Villen zum Einsatz kam. Es gibt sogar vereinzelte Berichte von gläsernen Gewächshäusern. Meist handelte es sich um rechteckige Platten von ca. 20 cm × 30 cm bis zu 80 cm × 80 cm Größe und einer Stärke von 3 bis 5 mm, die eine glatte Seite und eine raue Seite aufweisen. Ab dem 2. Jh. n. Chr. scheint beidseitig glattes, dünnwandiges Fensterglas das dickwandige und aufgrund seiner rauen Seite nur mäßig transparente Fensterglas zu verdrängen, welches im archäologischen Befund oftmals schwer von Gefäßglas und rezentem Glas zu unterscheiden ist. Dieses dünnwandige Fensterglas ist wahrscheinlich im Zylinderblasverfahren entstanden.[97][100] Zu einer breiteren Verwendung kommt es mit der aufkommenden Gotik im 12. Jahrhundert.[101]
Bei dem Mondglasverfahren, das bereits im vierten Jahrhundert im vorderen Orient belegt ist und später breite Anwendung in Frankreich fand, wird ein Glastropfen mit der Glasmacherpfeife zu einer Kugel vorgeblasen. Die heiße Glaskugel wird auf der gegenüberliegenden Seite an einem Metallstab befestigt, und die Glasmacherpfeife abgesprengt. Die Kugel hat nun ein Loch, dessen Ränder nach außen gestülpt werden. Zur weiteren Verarbeitung wurde die Kugel wieder auf Temperatur gebracht. Bei ca. 1000 °C war das Glas weich genug, um mittels Zentrifugalkraft in Tellerform geschleudert zu werden. Die Kugel öffnete sich um das Loch, an dem vorher die Pfeife befestigt war. Durch diese Technik wurden Glasplatten von ca. 1,20 m Durchmesser erzeugt. Anschließend wurde der äußere Rand zu Rechtecken geschnitten. Diese fanden Verwendung als z. B. Kirchenglas mit Bleieinfassungen. Das Mittelstück mit der Anschlussstelle des Schleuderstabs heißt Butze und wurde für Butzenscheiben von 10 bis 15 cm Durchmesser verwendet.[102]
Das Walzglasverfahren wurde zum ersten Mal 1688 in Saint-Gobain, der Keimzelle des heutigen gleichnamigen Weltkonzerns, dokumentiert. Geschmolzenes Glas wird auf den Walztisch gegossen, verteilt und schließlich gewalzt. Im Gegensatz zu den vorher genannten Verfahren wurde hier eine gleichmäßige Dicke erreicht. Auch waren erstmals Scheibengrößen von 40 × 60 Zoll möglich, was für die Produktion von Spiegeln genutzt wurde. Probleme bereitet jedoch die ungleichmäßige Oberfläche. Fensterglas dieses Herstellungsverfahrens ist oft blind und Spiegelglas nur durch aufwendiges kaltes Polieren zu erzielen.[102]
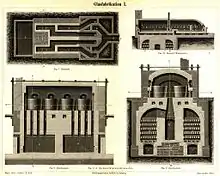
Industrialisierung und Automatisierung
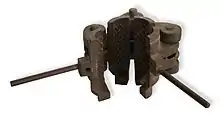
Die Industrialisierung und Automatisierung der Glaserzeugung setzte schrittweise im 19. Jahrhundert ein. Zunächst wurden einzelne Verfahrensabschnitte optimiert. So wurden 1847 durch Joseph Magoun Metallformen in der Hohlglasproduktion eingeführt, welche die bis dahin hauptsächlich genutzten Holzformen ersetzten.[103] 1856 entwickelte Friedrich Siemens den ersten Glasofen mit Regenerativfeuerung, was 1867 zum ersten kontinuierlichen Wannenofen ebenfalls durch Friedrich Siemens führte. Die regenerative Befeuerung ermöglichte erhebliche Energieeinsparungen und zugleich eine verbesserte Temperaturführung in der Glasschmelzwanne. Wenig später, im Jahr 1884, gründeten Ernst Abbe und Otto Schott in Jena ein Glaswerk für optische Spezialgläser.[104][105]
Flachglas
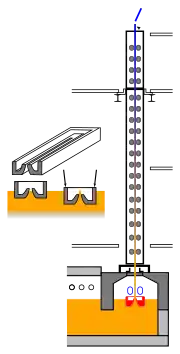
Im Jahr 1905 entwickelte der Amerikaner John H. Lubbers ein Verfahren zur Flachglasherstellung, wobei er den manuellen Prozess des Zylinderblasverfahrens im industriellen Maßstab umzusetzen versuchte. Dabei wurden Zylinder direkt aus der Schmelz gezogen, diese konnten einen Durchmesser von 80 cm erreichen und waren bis zu 12 m hoch. Der Zylinder wurde anschließend aufgeschnitten und geplättet. Das Verfahren war jedoch sehr umständlich, insbesondere das Umlegen der Zylinder in die Horizontale bereitete Schwierigkeiten.[104]
Ein Patent zur verbesserten Flachglasproduktion sollte 1902 von Émile Fourcault folgen. Das nach ihm benannte Fourcault-Verfahren zur Ziehglasherstellung. Das Glas wird dabei kontinuierlich als Glastafel durch eine Düse aus der Schmelze senkrecht nach oben gezogen. Das Flachglas wurde somit ohne Umweg über einen Zylinder erzeugt. Nach dem Hochziehen durch einen senkrechten Kühlkanal auf ca. 8 m Höhe kann gekühltes Flachglas am oberen Ende zugeschnitten werden. Durch Variation der Ziehgeschwindigkeit konnte die Glasdicke eingestellt werden. Das Fourcault-Verfahren kam ab 1913 zum Einsatz und bedeutete eine große Verbesserung.[106]
Ein ähnliches Verfahren ließ der Amerikaner Irving Wightman Colburn 1904 patentieren. Das Glasband wurde ebenfalls senkrecht aus der Schmelz gezogen, aber zur besseren Handhabung über eine Umlenkrolle in einen horizontalen Kühlkanal umgeleitet. Mit einer eigenen Fabrik wurde bis 1912 versucht, das Verfahren zu beherrschen, blieb aber letztlich erfolglos, so dass Insolvenz angemeldet wurde. Das Patent ging an die Toledo Glass Company. 1917 kam das nunmehr sogenannte Libbeys-Owens-Verfahren zur industriellen Anwendung. Die Vorteile gegenüber dem Fourcault-Verfahren lagen in der einfacheren Kühlung. Hingegen konnten bei jenem mehrere Ziehmaschinen an einer Glasschmelzwanne arbeiten. Da der Kühlofen beliebig lang sein konnte, erreichte dieses Verfahren etwa die doppelte Produktionsgeschwindigkeit. In der Folgezeit existierten beide Verfahren parallel. 1925 verbesserte die Plate Glass Company die Vorteile der Verfahren von Fourcault und Colburn; sie erzielte mit dem Pittsburg-Verfahren dadurch eine deutliche Steigerung der Produktionsgeschwindigkeit.[107][108]
Dem Deutschen Max Bicheroux gelang 1919 der entscheidende Schritt bei der Gussglasherstellung. Im Gegensatz zu den bisher genannten Verfahren wurde hier keine Glastafel aus der Schmelze gezogen, sondern die flüssige Glasmasse wurde dabei zwischen gekühlten Walzen zu einem Glasband geformt. Im noch erwärmten Zustand wurde das Glasband zu Tafeln geschnitten und in Öfen abgekühlt. Mit diesem Verfahren konnten Scheiben bis zu 4,5 m Breite hergestellt werden. Ein ähnliches Verfahren wurde 1921 von Pilkington und dem Fahrzeugfabrikanten Ford zur kontinuierlichen Herstellung von Automobilglas als Walzglas entwickelt. Dieses Verfahren lieferte allerdings geringere Breiten als das von Bicheroux.[109]
Die Firma Pilkington bewältigte in den 1960er Jahren als erste die technischen Probleme der Floatglasfertigung, wobei die Glasschmelze auf ein Bad aus flüssigem Zinn gegossen wurde. Dieses Prinzip revolutionierte die Flachglasfertigung, da es eine sehr hohe Produktivität aufwies und die Spiegelglasherstellung ohne weitere Nachbearbeitungsschritte ermöglichte. In den 1970er Jahren wurde dieses Verfahren allgemeiner Standard und verdrängte die Übrigen nahezu vollkommen. Das Verfahren basiert auf einer Idee von Henry Bessemer, die William E. Heal bereits 1902 zum Patent angemeldet hatte.[110]
Hohlglas

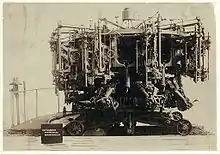
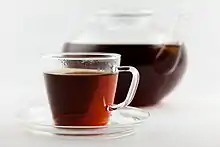
Im frühen 19. Jahrhundert wurden neue mechanische Hilfsmittel zum Blasen der Gläser benutzt. Es wurden Formen benutzt, die ein zu erzeugendes Relief als Negativ aufwiesen. Durch den Blasdruck wird das Glas an die Form gedrückt und das Werkstück erhält so seine Gestalt. Allerdings ist die Lungenkraft des Glasmachers nicht ausreichend hoch für tiefere Reliefs, so dass mechanische Hilfsmittel eingeführt wurden. Durch den Einsatz von Luftpumpen wurde genügend Druck erzielt.[111]
Eine weitere Neuerung in der Mitte des 19. Jahrhunderts war die Einführung von Metallformen. Erstmals 1847 ersetzten die von Joseph Magoun entwickelten Formen die alten aus Holz, was deren Haltbarkeit beträchtlich erhöhte.
Die erste halbautomatische Flaschenblasmaschine entwickelten die Briten Alexander Mein und Howard M. Ashley in Pittsburg im Jahr 1859. Doch noch immer waren manuelle Arbeitsschritte vonnöten.[112]
Ein Meilenstein war die 1903 von Michael Joseph Owens eingeführte Owens-Maschine als erste vollautomatische Glasmaschine überhaupt. In einem in der Schmelze eingetauchten Speiser wird ein Vakuum erzeugt und so die benötigte schmelzflüssige Glasmenge exakt aufgenommen. Der Arm des Speisers schwenkt zurück und drückt den Tropfen in die Form. Mit Pressluft wird der Tropfen in die Metallform geblasen und das Werkstück erhält seine endgültige Gestalt. Diese Technik heißt Saug-Blas-Verfahren. Damit war es möglich, die zu dieser Zeit enorme Menge von vier Flaschen pro Minute zu produzieren.[113]
Trotz dieser Errungenschaft blieben maschinell geblasene Flaschen noch viele Jahre schwerer als mundgeblasene. Um die Glasmacher zu übertreffen, mussten die Maschinen noch sehr viel genauer arbeiten. So ist auch zu erklären, dass die verschiedenen Produktionsverfahren noch lange parallel betrieben wurden.
Wesentliche Verbesserungen der Tropfenentnahme durch den Tropfenspeiser von Karl E. Pfeiffer im Jahre 1911 führten ebenfalls zu einer Steigerung der Produktivität. Die Portionierung der Glasmasse erfolgte nicht mehr durch Abschöpfen oder Saugen einer Menge Glas von der blanken Schmelzoberfläche, sondern indem ein Tropfen durch eine Öffnung am Ende des Feeders (Speiserkanals) abläuft. Durch die genauer mögliche Dosierung der Glasmenge konnten gleichmäßigere Flaschen gefertigt werden.
1924 wurde die IS-Maschine von den Namensgebern Ingle und Smith patentiert, die erste industrielle Anwendung folgte wenige Jahre später. Diese Maschine, die die Vorteile des Tropfen-Verfahrens erst richtig nutzt, arbeitet nach dem Blas-Blas-Verfahren. Ein Tropfen wird in eine Metallform geleitet und vorgeblasen. Der vorgeformte Tropfen wird in eine zweite Form geschwenkt, in der das Werkstück fertig geblasen wird.
Erste Anwendungen des neuen Verfahrens folgten wenige Jahre später. Die erste Maschine von 1927 hatte vier Stationen: Ein Feeder beschickte eine Maschine und diese konnte parallel vier Flaschen fertigen.[114] Das Prinzip des Blas-Blas-Verfahrens ist auch heute noch in der Massenfabrikation gültig.
Rohrglas
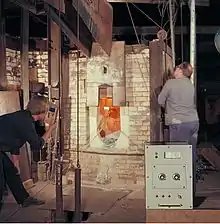
Glasrohre wurden bis ins 19. Jahrhundert ebenfalls (mundgeblasen) ausschließlich diskontinuierlich aus einer Charge oder einem Glasposten hergestellt. Die industriellen Prozesse zur Glasrohrerzeugung werden in Verfahren mit rotierender Pfeife und Ziehverfahren mit Düsen unterteilt. Letztere können weiter unterteilt werden in Varianten, bei denen das Glasrohr senkrecht nach unten oder oben aus der Schmelze gezogen wird. 1912 entwickelte E. Danner (Libbey Glass Company) in den USA das erste kontinuierliche Röhrenziehverfahren, worauf 1917 ein Patent erteilt wurde.[115]
Beim Danner-Verfahren fließt eine Glasschmelze als Band auf einen schräg nach unten geneigten, rotierenden keramischen Hohlzylinder – die Dannerpfeife. Nach Zuführung von Druckluft über das Innere der Pfeife gelingt das Abziehen des sich bildenden Glasrohres in Richtung der Pfeifenachse. Die Ziehgeschwindigkeit des Rohrs sowie Höhe des Drucks der zugeführten Luft bestimmen hierbei die Rohrdimension.[115]
In Frankreich wurde 1929 von L. Sanches-Vello ein vertikales Ziehverfahren ausgearbeitet. Dabei handelt es sich um ein senkrechtes Rohrziehverfahren. Die Schmelze wird durch eine Düse im Boden der Schmelzwanne nach unten gezogen und kurz darauf in die Horizontale umgeleitet.[116][117]
Für die Produktion von Rohrglas existieren eine Reihe weiterer Verfahren, die aber alle nach sehr ähnlichen Prinzipien arbeiten.[68][118]
Märkte für Glas
Glas ist ein vielseitiges Material, das in vielen Bereichen des täglichen Lebens zum Einsatz kommt. So spielt Glas eine wichtige Rolle in Forschung und Wissenschaft, in der modernen Architektur sowie in Zukunftsbranchen. Kernbereiche, in denen Glas eingesetzt wird, sind:[119] Bauindustrie, Ernährungs- und Getränkeindustrie, Kraftfahrzeugindustrie, Elektro(nik)industrie, Haushalt und Gastronomie, Medizin, Forschung und Wissenschaft, Chemie, Pharmazie, Kosmetik, Möbelindustrie und Innenausbau, Kunststoff- und Textilindustrie.
Kunsthandwerk und Glaskunst
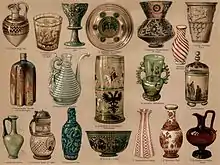
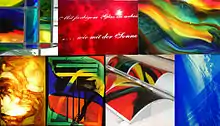
Ägypten
Das Glashandwerk im pharaonischen Ägypten lässt sich bis an den Beginn der 18. Dynastie zurückverfolgen; zunächst handelt es sich dabei um Kleinfunde wie Perlen, Amulette oder Kettenglieder sowie farbigen Einlagen in den typischen ägyptischen Schmuckobjekten (z. B. Pektorale). Diese sind meist in Türkis oder Dunkelblau gehalten, da sie solche Objekte aus Lapislazuli oder Türkis imitieren sollten;[120] dies galt nicht als billiger Schmuck, sondern die Imitation dieser edlen, hoch machtgeladenen Steine galt als besondere Kunst. Das Verfahren war für die damalige Zeit sehr aufwändig und man arbeitete solche Kleinfunde aus Rohglasstücken, ganz und gar vergleichbar mit solchen aus Stein. Dafür spricht auch, dass ein ägyptisches Wort für „Glas“ so nicht existierte; es hieß künstliches Lapislazuli bzw. künstliches Türkis im Gegensatz zum wahren/echten Türkis bzw. Lapislazuli. In der Ersten ägyptischen Glaskunstblüte (18. bis 20. Dynastie) traten stabgeformte Gefäße auf (die auch kerngeformt genannt werden, nach der Sandkerntechnik). Sie gehen auf Vorbilder zeitgenössischer Gefäße, insbesondere solchen aus Stein, zurück.[121] Typische Formen ägyptischer Glasgefäße sind Lotoskelchbecher, Granatapfelgefäße, Krateriskoi und Schminkgefäße wie Kohltöpfe und Kohlpalmsäulchen (für schwarze Augenschminke, sprich „kochel“). Seit Thutmosis III., aus dessen Regierungszeit auch die ältesten Hohlglasfunde stammen, treten auch Importgefäßformen aus dem Mittelmeergebiet hinzu (z. B. Amphoriskoi, Linsenflasche, Henkelflasche, Bilbils und andere Sonderformen); diese werden allgemein in das Spektrum der Gefäßformen eingeführt und betreffen somit auch Gefäßformen aus Keramik und Fayence beispielsweise. Die älteren kerngeformten Gefäße (etwa in der Zeit Thutmosis' III. bis Amenophis III.) sind meistens türkis bis kräftig blau (wie der echte Türkis und Lapislazuli, denn Glas galt als Imitation dieser edlen Steine). Später, besonders in der Ramessidenzeit, wurden Gläser in hellen, kräftigen Farben wie Gelb und Grün, Weiß aber auch Braun beliebt.[122] Als Dekor entstanden Fadenverzierungen in Zickzack- oder Girlandenform in Gelb, Weiß, und Hellblau sowie tordierte Fäden im Hell-Dunkel-Kontrast, manchmal wurden sie auch monochrom belassen und nur die Henkel oder Schulterumbrüche durch Fadenzier betont. Die ägyptischen Glasgefäße dienten der Aufbewahrung von Kosmetika wie Salben, Ölen, Parfümen und Augenschminke. Das stark gefärbte, undurchsichtige Glas wirkte konservierend.
In der Spätzeit (ab der 3. Zwischenzeit bis zur Griechischen Epoche) blieb das Hohlglashandwerk unterrepräsentiert, nur gelegentlich kamen Hohlgläser vor, weiterhin in Form von kleinen meist unverzierten Salbgefäßen. Dagegen waren Glaseinlagen in Schmuck oder Figuren nicht selten und wurden wie zuvor den Edelsteinen gleichrangig behandelt. In der hellenistischen Zeit gewann die Glasproduktion wieder an Bedeutung, auch in Ägypten. Zusammen mit neuen Herstellungstechniken trat eine völlig neue Formenwelt auf, ist aber nicht für Ägypten, sondern eher zeittypisch. Bereits im 5. Jahrhundert v. Chr. hatte sich Rhodos als wichtiges Zentrum der Glasherstellung etabliert. Neben Intarsien und Perlen fanden sich nun vielfarbige Mosaikschalen und die Gefäße der Canossa-Gruppe.
Römisches Reich
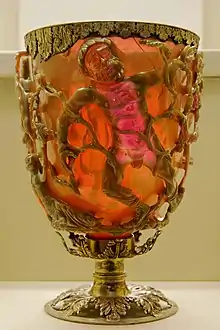
Im 1. Jahrhundert stieg die Glasproduktion derart, dass das vormals rare und teure Material für weite Kreise erschwinglich wurde. Eine umfangreiche Produktion von Trinkgefäßen, Krügen, Schalen und Tellern setzte ein, anfangs meist manuell geformt oder abgesenkt, dann zunehmend mundgeblasen. Eine Vielzahl hochwertiger Spezialgläser beweist handwerkliche Meisterschaft, so die Mosaik-Fadengläser, Kameogläser, Goldfoliengläser, Gläser mit Emailmalerei und besonders die Diatretgläser, meist glockenförmige, prunkvolle Leuchtgefäße in Netzglastechnik, die bis heute wegen ihrer künstlerischen Qualität bewundert werden. Eines der berühmtesten römischen Gläser ist der im Besitz des Britischen Museums befindliche Lykurgosbecher[123] aus dem 4. Jahrhundert, an dem eine dreidimensionale figurative Darstellung angebracht ist, die im Gegenlicht rot und im Auflicht opak-gelbgrün erscheint.
Venezianisches Glas
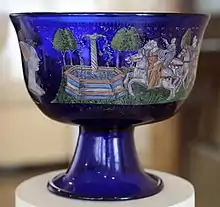
Venedig etablierte ab der Hälfte des 15. Jahrhunderts seinen internationalen Ruf als exquisiter Glashersteller mit der "Erfindung" des cristallo. Diese Neuerung beruht auf der Einführung eines vorgelagerten Prozesses bei der Herstellung des vitrum blanchum, bei dem aus der Levantine-Asche unerwünschte Stoffe wie Eisen, die das Glas verunreinigten, entfernt wurden. Diese Weiterentwicklung geht auf den Muraneser maestro Angelo Barovier zurück.[124] Um diese Zeit entstand beispielsweise die in ausnahmslosem Zustand erhaltene Coppa Barovier und die Flasche mit den Wappen der Familie Bentivoglio und Sforza, heute im Museo Civico in Bologna[125] (2. Hälfte 15. Jahrhundert). Zu den aus dem 16. Jahrhundert erhaltenen Meisterwerken gehören ein emaillierter Kelch (ca. 1510),[126] der 1902 unter dem eingestürzten Turm von San Marco gefunden wurde (heute im Museo del Vetro, Murano) und Handwaschgefäße in Form eines Schiffes aus durchsichtigem und blauem Glas (heute im Museo del Vetro, Murano).[127] Über die Variationsbreite der venezianischen Renaissance-Gläser, ihre Formen und Dekore geben vor allem Gemälde aus naher Umgebung Venedigs, aber auch niederländische und flämische Stillleben Auskunft. Es handelt sich größtenteils um Becher, Schalen, Kannen und Flaschen, die aus hohl geblasenen Balustern zusammengesetzte Schäfte mit flachen Füßen hatten. Diese Schäfte wurden an dem späten 17. Jahrhundert immer ausgeklügelter, Flügel wurden in phantasievollen Ornamenten und figürlichen Dekorationen angesetzt, manchmal war auch der Schaft in figürlicher, beispielsweise in Tiergestalt ausgeführt.
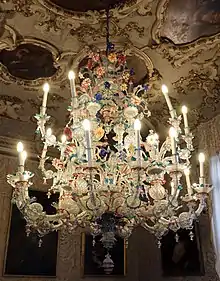
Für die Wandung gab es besondere Veredelungstechniken. Beim Eisglas (ital. ghiaccio) hergestellt durch Abschrecken in eiskaltem Wasser oder durch Rollen über kleine Splitter, wird auf der Oberfläche ein Effekt wie bei einem durch Eisblumen überzogenen Fensterglas erzielt. Beim Faden- oder Netzglas (italienisch latticinio / vetro a filigrano / reticello) – wurden Milchglas-Fäden in die klare Glasmasse eingeschmolzen und die so erhaltenen Glasstäbe durch Applizieren auf einen geblasenen Glaskörper so verwoben, dass ein faden- bzw. netzartiges Muster entstand. Diese Technik war in Ansätzen schon in der Antike bekannt, erlebte jedoch während des 17. und 18. Jahrhunderts ein Revival in Venedig, mit dem die Republik mit starken Konkurrenten aus Frankreich, England und Böhmen konkurrieren sollte. Dem Gusto des Barock entsprechend, wurde mit üppiger Transparenz gearbeitet – weniger mit Farben, stattdessen aber auf vielfältige Texturen (z. B. battuto) gesetzt und vor allem pflanzliche Motive in Glas nachgeahmt (Blumen, Bäume etc.). Einer der herausragendsten Künstler dieser Zeit war Giuseppe Briarti, der eine Reihe bemerkenswert aufwendiger Lüster sowie Tischaufsätze schuf. Nach der Auflösung der Gilden um 1800 durch Napoleon, beeinflusst durch die starke ausländische Konkurrenz, erlebte die Glaskunst einen Untergang in Venedig. Um 1850 wurde sie durch Nachkommen der berühmten Glasmacher-Familien wieder zum Leben gebracht. Alte Rezepte wurden wiederentdeckt und verbessert. Die Skills der alten Meister übte man vorrangig durch Kopieren der eigenen Produktion aus der Frühen Neuzeit (es entstanden beispielsweise einige Kopien der Flasche der Bentivoglio, der Coppa Barovier und des Klechs von San Marco bei Venice and Murano Company/ Salviati & Co.). Aber auch antike Glasformen wurden vielfach nachgeahmt, beflügelt durch neuste archäologische Entdeckungen. Dabei wurden nicht nur Gefäßtypen und Dekorationen/Techniken wie z. B. das Cameo nachgeahmt, sondern auch der Zustand der Funde. Mit avventurina-Glas imitierte man z. B. die Oxidation und Anlagerung von Sediment auf antiker Keramik.[128]
Als Glas à la façon de Venise fand der venezianische Stil trotz aller Versuche der Republik Venedig, ihre Kunst geheim zu halten, Zugang in die Länder nördlich der Alpen.
Schmucktechniken im Barock und Rokoko
Barockes Schnittglas (und Rokoko-Glas) vornehmlich aus Böhmen und Schlesien, aber auch Nürnberg, Brandenburg und Sachsen, seltener Thüringen, Hessen, Norddeutschland und den Niederlanden lief ab dem 18. Jahrhundert venezianischem Glas den Rang ab, da deren Glas für den Glasschnitt und Glasschliff aufgrund seiner Dünnwandigkeit nicht geeignet war.
Die Formen mit Fuß, Baluster-Schaft und dünnwandiger Kuppa ähnelten dem farblosen venezianischen Glas, jedoch ohne Flügel und wiesen eine stärkere Wandung auf. In Potsdam, Schlesien, Böhmen, Kassel und anderen Gebieten experimentierte man mit den Rezepten von Glas, um eine Masse herzustellen, die den Schliff und Schnitt erlaubte. Die Themen des Schnittes waren vielseitig. Jagdszenen waren häufig, Landschaften, aber auch allegorische Figuren mit Beischriften, Blumen- und Blattornamente sowie zeitgenössische Persönlichkeiten und Schlachtenszenen.
Bereits im 17. Jahrhundert signierten Glasschneider vereinzelt ihre Werke und auch aus dem 18. Jahrhundert sind Glasschneider bekannt, etwa: Christian Gottfried Schneider und Friedrich Winter prägten den Glasschnitt Schlesiens wie Martin Winter und Gottfried Spiller denjenigen von Potsdam, Johann Christoph Kießling arbeitete für August den Starken, Franz Gondelach stand im Dienst des Landgrafen Carl von Hessen und David Wolff arbeitete in den Niederlanden.
Gelegentlich weisen die barocken Schnittgläser Vergoldungen an Fuß, Schaft oder am Lippenrand auf. Im 18. Jahrhundert waren auch die Zwischengoldgläser beliebt. Für deren Herstellung wurden zwei Gläser verwendet, wobei eines passgenau in das Zweite, daher größere Glas, passte. Auf die Außenwand des inneren Glases wurde eine Goldfolie aufgelegt und mit einer Radiernadel Motive darin eingeritzt. Dann wurde es in das zweite Glas eingepasst und weiterverarbeitet.
Von der Porzellanmalerei her kam die Technik der Schwarzlotmalerei, die in anderem Zusammenhang bereits im Mittelalter bekannt war. Johann Schaper und Ignaz Preissler prägten diese Kunst in Nürnberg und Schlesien, Böhmen und Sachsen.
Eine rurale Veredelungstechnik barocken Glases ist die Emailmalerei. Sie findet sich vor allem an Gebrauchsglas in ländlichen Gegenden (z. B. Bierhumpen der Schützenvereine und Schnapsflaschen). Passend zur Provenienz sind die Motive: Bauer mit Vieh und Ackergerät, Wirtshausszenen, Spielkarten, Sinnsprüche. In Böhmen entsteht die Emailmalerei auch auf opakem Milchglas, was diese Technik in die Nähe der Porzellanmalerei rückt.
Biedermeierglas
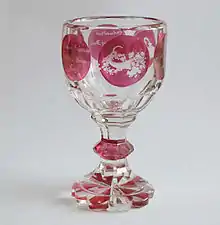
Die Engländer übernahmen im 18. Jahrhundert die Arten und Formen der böhmischen Gläser und beherrschten mit Hilfe der Reinheit ihres Bleikristalls, dessen hervorragende lichtbrechende Eigenschaften durch den Brillantschliff wirkungsvoll zur Geltung kamen, Anfang des 19. Jahrhunderts schließlich den zu der Zeit von klassizistischen Geschmacksvorstellungen geprägten Markt. Um den Vorsprung der Engländer wettzumachen, bemühten sich die böhmischen Glasfabrikanten um größere Reinheit ihres bleifreien Kristallglases. Zugleich nutzten sie alle Möglichkeiten des Musterschliffes für abwechslungsreiche Dekore und versuchten vor allem auch, billiger zu produzieren. Das Ergebnis dieser Anstrengungen lässt sich an den meisterlich geschliffenen Biedermeiergläsern ablesen, die als bewundernswerte Beispiele kunsthandwerklichen Glasschliffs gelten.
In den 1830ern erreichte der Biedermeierstil seinen Höhepunkt. Um Produktion und Absatz auszuweiten, bereicherten die Glashütten nach 1840 ihr Angebot mit dem neuentwickelten Farbglas und verdrängten damit das farblose Glas mehr und mehr vom Markt. Besonders die nordböhmischen Glashütten gestalteten ihre Gläser in immer wirkungsvollerer Farbigkeit. Im Zuge dieser Entwicklung verlor jedoch der Glasschliff gegenüber der Buntheit der Dekore an Bedeutung, Form und Schliff wurden nicht zuletzt aus Kostengründen zunehmend einfacher.
Die Mannigfaltigkeit der aus Farbglas und überfangenem bzw. gebeiztem (siehe Rotbeize) Kristallglas mit Schnittdekor sowie aus Steinglas (Lithyalinglas und Hyalithglas, das mit Gold, Email- und Transparentfarben bemalt wurde) hergestellten Produkte erreichte schließlich ein bis dahin nicht gekanntes Ausmaß. Gängig waren zum Beispiel Trinkgläser und Karaffen aus buntem Glas, ganze Likör- und Dessertservice, Garnituren für Kommoden und Waschtische, Schreibzeuge und Parfümflakons, Schalen, Teller, Tafelaufsätze, und vor allem Vasen. Hinzu kamen die unzähligen Andenken- und Freundschaftsgläser, Dekorations- und Ehrenpokale, außerdem Exportartikel wie Wasserpfeifen und Sprenggefäße für Rosenwasser.
Jugendstilglas
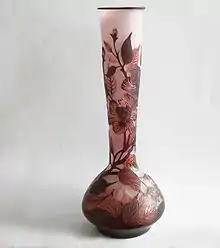
Um 1900 waren sich die Gestalter der jungen Generation einig in ihrer Abkehr vom überkommenen Historismus. Für das daraus resultierende kunstgewerbliche Streben nach neuen, frischen, originellen Ausdrucksformen auf der Basis alter handwerklicher Techniken bürgerte sich im deutschsprachigen Raum, den Niederlanden und den Nordischen Ländern der Begriff Jugendstil ein, während sonst die Bezeichnung Art nouveau gebräuchlich ist. Die Fantasie der Jugendstil-Künstler wurde vor allem von der Farben- und Formenwelt des fernen Ostens beflügelt. So sind die wesentlichen Teile oder Elemente des Jugendstils durch dekorativ geschwungene Linien sowie flächenhafte florale Ornamente und Asymmetrie gekennzeichnet.
Glas nahm in der Entwicklung des Jugendstils eine zentrale Rolle ein. Der Grund dafür ist in den gestalterischen Möglichkeiten zu suchen, die dem angestrebten organischen Wesen der Formgebung entgegenkamen. Die Zusammenarbeit von Designern und Handwerkern brachte fantasievolles, in limitierten Auflagen von Hand hergestelltes Atelierglas hervor, das durch die Vielfalt der Farbeffekte besticht. Französische Glasmacher wie Emile Gallé und die Daum Frères schufen geschnittenes und geätztes Überfangglas in kräftigen Farben. Das böhmische Jugendstilglas hat seinen guten Ruf vor allem Max Ritter von Spaun, Besitzer der Firma Joh. Loetz Witwe in Klostermühle in Böhmen, zu verdanken. Von jenseits des Großen Teiches, aus New York, kamen das irisierende Glas und die berühmten, in Europa als beispielhaft angesehenen Kreationen von Louis Comfort Tiffany.
Der konstruktive Stil, der bestrebt war, alle Formen mit Hilfe einfachster Gebilde wie Quadrat, Rechteck, Kreis und Ellipse zu gestalten und starke Farbgegensätze zu verwenden, wurde am konsequentesten von der Wiener Schule verfolgt. Ihre führenden Repräsentanten waren Josef Hoffmann und Koloman Moser.
Mit den wachsenden wirtschaftlichen Schwierigkeiten in der Zeit des Ersten Weltkrieges ging die Ära des Jugendstils zu Ende. Sie währte knapp zwanzig Jahre, ihre Auswirkungen sind jedoch weiterhin spürbar.
Fusing
Beim Fusing (dt. Verschmelzung) oder Fusen (neudeutsch für Glasverschmelzung) werden verschiedene (weiße oder farbige, eventuell mit Glasschmelzfarbe bemalte) Glasstücke bei 780–900 °C miteinander verschmolzen. Die Schmelztemperatur ist von Zusammensetzung und Dicke der Gläser abhängig. Temperaturbeständige Gegenstände, wie etwa Metalle, können mit eingeschmolzen werden.
Fusing ist in seinen Grundlagen, nach bisherigem archäologischem Wissensstand, ein mindestens 2200 Jahre altes Glasverarbeitungsverfahren. In den letzten Jahrzehnten wurde es zu einer der vielseitigsten und technisch anspruchsvollsten Glasverarbeitungstechniken weiterentwickelt. Viele Glasereien und künstlerische Glasstudios können Glas nach der Fusing-Technik verarbeiten. Das Verfahren wird in großer Variationsbreite eingesetzt: Von Modeschmuck und der Dekoration von Gegenständen bis hin zu Kunstobjekten (z. B. in Murrine- und Millefiori-Technik), großen künstlerisch gestalteten Fenstern und anderen Glaselementen in Architektur und Innenarchitektur.
Folgende Grundvarianten des Fusing werden unterschieden:
- Relief (engl. tack fuse)
- Vollverschmelzung (engl. full fuse)
- Glasfluss (franz. Pâte de verre), Glaspaste wird in Form geschmolzen.
Konventionell handwerklich kann Fusing folgendermaßen ablaufen: Aus verschiedenfarbigen Glasplatten werden passende Teile mit einer besonderen Zange abgezwickt oder mit einem Glasschneider abgeschnitten. Die Glasstücke setzt der Glaskünstler dem Entwurf entsprechend zusammen, beispielsweise als Muster für den Rahmen eines Spiegels oder für die Herstellung einer Glasschüssel. Zwischenräume werden oft mit Glaspulver aus zerstampften Glasplatten ausgefüllt. Nun werden die Stücke in einem Glasfusingofen verschmolzen. Die Temperaturen werden so gewählt, dass das Glas noch nicht als Flüssigkeit verläuft, alle Glasteile und Partikel aber eine dauerhafte Verbindung eingehen. Bei entsprechender Temperaturführung kann ein vollkommen geschlossener und harter Glaskörper hergestellt werden. Dieser Brennvorgang dauert, abhängig von Dicke und Durchmesser des Glases, etwa 18 bis 22 Stunden.
Der Glaskörper wird zunächst zu einer flachen Platte verschmolzen, die bei Bedarf in einem zweiten Arbeitsgang in einem Glasschmelzofen weiter geformt wird, z. B. wenn daraus eine Glasschüssel entstehen soll. Dazu werden Trägerformen oder Modelle verwendet, die oft aus Ton oder unglasierter Keramik bestehen. In konkave Modelle kann sich die erhitzte Glasplatte absenken und über konvexe Modelle kann sie sich aufbiegen. Die Form muss etwas größer als die Glasplatte sein, da Glas sich bei Erwärmung ausdehnt und beim Abkühlen zusammenzieht. Auf die entstandenen Objekte können nach dem Abkühlen Glasveredelungstechniken angewendet werden: Gravieren, Glasmalen, Schleifen, Sandstrahlen oder Ätzen.
.jpg.webp)
Eine fortgeschrittene Anwendung des Verfahrens ist die Herstellung großer selbsttragender Glasscheiben oder Glasobjekte, die beispielsweise als Gegenwartskunst oder als Kirchenkunst künstlerisch kontrolliert gestaltet werden können. Dafür werden auch industriell hergestellte Glasbruchstücke (Fritten) und Glaspulver aus farblosen und farbigen Gläsern verwendet. Beispiele für Fusingtechnik in der Glaskunst schafft die Künstlerin Ulrike Umlauf-Orrom.[129]
Die Herstellung derartiger Fusing-Stücke setzt künstlerisches Talent und die Kenntnis der Verfahrenstricks voraus. So müssen die zusammengeschmolzenen Gläser den gleichen Ausdehnungskoeffizienten (AKW) haben und die Erhitzung und Abkühlung des Glases muss genau kontrolliert bestimmten Temperaturkurven folgen. Andernfalls können im Glas mechanische Spannungen entstehen, die es zerreißen oder zerspringen lassen. Große Fusing-Stücke können daher nur in einem Flachbett in digital gesteuerten Brennöfen hergestellt werden.
Besonders fortgeschrittene Glaskünstler verwenden Glasöfen der Bauart Glory Hole, weil sie es gestatten, kleinere Glasmassen direkt in verschiedenen angeschmolzenen oder nahezu flüssigen Zuständen künstlerisch zu bearbeiten. Glas wird dabei immer wieder für einen neuen Arbeitsgang durch das Loch in der Ofenwand gehalten und aufgeheizt, um es dann außerhalb des Ofens bearbeiten zu können.
Zur ebenso direkten Bearbeitung dienen Öfen mit ausziehbarem Flachbett. Das im Flachbett liegende Glas wird auf Bearbeitungstemperatur gebracht und dann für kurze Zeit aus dem Ofen hervorgezogen. Unter Beachtung der richtigen Verfahren und Vorsichtsmaßnahmen werden dann beispielsweise Chemikalien, Metallstaub oder farbige Glaspulver auf das angeschmolzene oder geschmolzene Glas gebracht. Besondere Kenntnisse setzt es voraus, mit Werkzeugen direkt gestalterisch in diese Glasmasse einzugreifen.
Eine weitere neue Variante ist die Pàte-de-Verre-Herstellung großformatiger Glasplastiken.
Siehe auch
Glasarten und Verwandtes
Herstellung
Medizin
In der Medizin werden Implantate mit einer Glasbeschichtung versehen um eine Abstoßung vom Organismus zu unterdrücken. Je nach Zusammensetzung kann die Biokompatibilität angepasst werden. Bioglas mit der Bezeichnung 45S5 steht für 45 gewichts % SiO2 und einem molaren Verhältnis von 5:1 von Calcium zu Phosphor.[130]
Spezifika
Sonstiges
- Passauer Glasmuseum
- Corning Museum of Glass
- Glasmuseum Frauenau
- Europäisches Flakonglasmuseum am Rennsteig
- Glasarchitektur
- Glasmodelle der Blaschkas
- Glasreich
- Tiffany-Glaskunst
- Islamische Glaskunst
- Meerglas
Literatur
Glaschemie
- G. H. Frischat: Glas – Struktur und Eigenschaften. In: Chemie in unserer Zeit. 11. Jahrg., Nr. 3, 1977, S. 65–74, ISSN 0009-2851
- Werner Vogel: Glaschemie. 3. Auflage. Springer-Verlag, Berlin 1992, ISBN 3-540-55171-9.
- Horst Scholze: Glas. Natur, Struktur und Eigenschaften. 3. Auflage. Springer-Verlag, Berlin 1988, ISBN 3-540-18977-7.
Glasherstellung und Glastechnik
- Joachim Lange: Rohstoffe der Glasindustrie. 3., überarb. Auflage. Wiley-VCH, Leipzig 1993, ISBN 3-342-00663-3.
- Günther Nölle: Technik der Glasherstellung. Deutscher Verlag für Grundstoffindustrie, Stuttgart 1997, ISBN 3-342-00539-4.
- Wolfgang Trier: Glasschmelzöfen, Konstruktion und Betriebsverhalten (Reprint). 1. Auflage. Springer, Berlin 1984, ISBN 3-642-82068-9.
- Günther, Rudolf: Glasschmelzwannenöfen. Verlag der Deutschen Glastechnischen Gesellschaft, Frankfurt am Main. 1954.
- Alexis G. Pincus: Combustion Melting in the Glass Industry (Zusammenstellung von Artikeln aus Magazines for Industry Inc.). 1980.
- I. I. Kitaigorodski: Technologie des Glases. 2., verb. und erw. Auflage. VEB Verlag Technik, Berlin 1957.
- Hans Jebsen-Marwedel (Hrsg.): Glastechnische Fabrikationsfehler. 4. Auflage. Springer, Berlin 2011, ISBN 978-3-642-16432-3.
- W. Giegerich, W. Trier: Glasmaschinen, Aufbau und Betrieb der Maschinen zur Formgebung des heißen Glases. Springer, Berlin 1964.
- Siegfried Rech: Glastechnik 1. 1. Auflage. VEB Deutscher Verlag für Grundstoffindustrie, Leipzig 1978.
- Jürgen Dispan: Glasindustrie in Deutschland. Branchenreport 2013. Stuttgart (= IMU-Informationsdienst. Nr. 3-2013). Link zur Branchenstudie
Geschichte der Glasherstellung
- Birgit Nolte: Die Glasgefässe im alten Ägypten. Hessling, Berlin 1968.
- Daniele Foy, Marie-Dominique Nenna: Tout feu tout sable. Aix-en-Provence 2001, ISBN 2-7449-0264-0.
- Rita Hannig: Glaschronologie Nordostbayerns vom 14. bis zum frühen 17. Jahrhundert. Greiner, Remshalden 2009, ISBN 978-3-86705-027-2.
- Anton Kisa: Das Glas im Altertum. 3 Bände. Hiersemann, Leipzig 1908 (Digitalisat Band 1, Band 2, Band 3).
- Heinrich Maurach: Glas als Wort und Begriff. In: Glastechnische Berichte. Band 25, 1952, S. 1–12.
- Frank Schweizer: Glas des 2. Jahrtausends v. Chr. im Ostmittelmeerraum. Greiner, Remshalden 2003, ISBN 3-935383-08-8.
- Heike Wilde: Technologische Innovationen im zweiten Jahrtausend vor Christus. Zur Verwendung und Verbreitung neuer Werkstoffe im ostmediterranen Raum. Harrassowitz, Wiesbaden 2003, ISBN 3-447-04781-X.
- Lukas Clemens, Peter Steppuhn (Hrsg.): Glasproduktion. Archäologie und Geschichte. Beiträge zum 4. Internationalen Symposium zur Erforschung mittelalterlicher und frühneuzeitlicher Glashütten in Europa. Kliomedia, Trier 2012, ISBN 978-3-89890-162-8.
- Heidi Amrein: L’atelier de verriers d’Avenches. L’artisanat du verre au milieu du Ier siècle après J.-C. In: Cahiers d’archéologie romande. Band 87. Lausanne 2001, ISBN 2-88028-087-7 (französisch).
- Axel von Saldern: Antikes Glas. Beck, München 2004, ISBN 3-406-51994-6.
- Helmut A. Schaeffer (Hrsg.): Glastechnik. Band 1: Werkstoff Glas. Deutsches Museum Verlag, 2012, ISBN 978-3-940396-35-8.
- Helmut A. Schaeffer (Hrsg.): Glastechnik. Band 2: Hohlglas, 2010, ISBN 978-3-940396-16-7.
- Margareta Benz-Zauner, Helmut A. Schaeffer (Hrsg.): Glastechnik. Band 3: Flachglas, 2007, ISBN 978-3-940396-01-3.
- Margareta Benz-Zauner, Helmut A. Schaeffer (Hrsg.): Glastechnik. Band 4: Spezialglas, 2003, ISBN 3-940396-07-9.
Kunsthandwerk und Glaskunst
- Walter Spiegl: Glas. Battenberg Verlag, München 1979, ISBN 3-87045-155-6.
- Judith Miller: Art nouveau. Die Welt des Jugendstils. Dorling Kindersley Verlag, Starnberg 2005, ISBN 3-8310-0767-5.
Restaurierungen historischen Glases
- Glas. In: Hans-Herbert Möller (Hrsg.): Restaurierung von Kulturdenkmalen. Beispiele aus der niedersächsischen Denkmalpflege (= Berichte zur Denkmalpflege. Beiheft 2). Niedersächsisches Landesverwaltungsamt – Institut für Denkmalpflege. Niemeyer, Hameln 1989, ISBN 3-87585-152-8, S. 405–424.
Weblinks
- Wie wurde das Glas erfunden? (PDF; 60 kB) Originaltext von Plinius d. Ä. zur Entdeckung des Glases (mit deutscher Übersetzung von Wolfgang Kilb).
- Werkstoffe – Glas. In: Planet Wissen. Abgerufen am 1. Juli 2010 (Artikel und Videos zu den Themen: Geschichte und Herstellung von Glas).
- glasrepliken.de speziell über römisches Glas und seine Herstellung in Antike und Replik. Abgerufen am 6. Mai 2009
- Martin Weiß (Hrsg.): vitrum – das Glas der Antike. Abgerufen am 8. März 2012.
- Mathias Hennies: Glashandel an der Seidenstraße. Gemeinsames Forschungsprojekt von deutschen und chinesischen Archäologen. In: Studiozeit. Aus Kultur- und Sozialwissenschaften. Deutschlandfunk, 26. Feb. 2009, Abgerufen am 26. Feb. 2009.
- Rudolf Bergmann: Historische Glaserzeugung in Westfalen. In: Geographische Kommission für Westfalen (Hrsg.): Westfalen regional – die landeskundliche Online-Dokumentation über Westfalen. Münster 2009
- Beste verfügbare Techniken (BVT-Merkblatt) der Glasherstellung (Memento vom 17. Juli 2013 im Internet Archive) Umweltbundesamt, Dessau
- Auswahl von Videos aus der Fernsehsendung Kunst und Krempel des Bayerischen Rundfunks mit ausführlichen Beschreibungen von Glas-Objekten
Anmerkungen
- Eintrag zu Glas. In: Römpp Online. Georg Thieme Verlag, abgerufen am 21. Januar 2013.
- Hans Jebsen-Marwedel: Glastechnische Fabrikationsfehler. 4. Auflage.
- Wissenschaft-Online-Lexika: Eintrag zu „Glas“ im Lexikon der Physik, abgerufen am 21. Januar 2013.
- Horst Scholze: Glas. Natur, Struktur und Eigenschaften. 3. Auflage.
- Werner Vogel: Glaschemie. 3. Auflage.
- Manfred Flemming: Faserverbundbauweisen. Springer-Verlag, Berlin 1995, ISBN 3-540-58645-8, S. 52.
- Helmut A. Schaeffer: Glastechnik. Band 1: Werkstoff Glas. 2012, S. 198 f.
- Helmut A. Schaeffer: Glastechnik. Band 1: Werkstoff Glas. 2012, S. 204 ff.
- Helmut A. Schaeffer: Glastechnik. Band 1: Werkstoff Glas. 2012, S. 208 f.
- Th. Erismann, H. Heuberger, Ekkehard Preuss: Der Bimsstein von Köfels (Tirol), ein Bergsturz-“Friktionit”. In: Mineralogy and Petrology. Band 24, Nr. 1–2. Springer, März 1977, ISSN 0930-0708, S. 67–119, doi:10.1007/BF01081746.
- Roland Vinx: Gesteinsbestimmung im Gelände. München (Elesevier) 2005, ISBN 3-8274-2748-7, S. 33.
- Stefan Weiß: Das große Lapis Mineralienverzeichnis. 5. Auflage. Christian Weise Verlag, München 2008, ISBN 3-921656-17-6.
- Helmut A. Schaeffer: Glastechnik. Band 1: Werkstoff Glas. 2012, S. 212 ff.
- Helmut A. Schaeffer: Glastechnik. Band 1: Werkstoff Glas. 2012, S. 60–68.
- Helmut A. Schaeffer: Glastechnik. Band 2: Hohlglas. 2010, S. 13–20.
- Helmut A. Schaeffer: Glastechnik. Band 3: Flachglas. 2007, S. 11–32 ff.
- Helmut A. Schaeffer: Glastechnik. Band 4: Spezialglas. 2003, S. 13–18.
- Helmut A. Schaeffer: Glastechnik. Band 2: Hohlglas. 2010, S. 22–32.
- Helmut A. Schaeffer: Glastechnik. Band 2: Hohlglas. 2010, S. 13–32.
- Helmut A. Schaeffer: Glastechnik. Band 4: Spezialglas. 2003, S. 70 ff.
- Helmut A. Schaeffer: Glastechnik. Band 4: Spezialglas. 2003, S. 120–162.
- Helmut A. Schaeffer: Glastechnik. Band 4: Spezialglas. 2003, S. 168 ff.
- Helmut A. Schaeffer: Glastechnik. Band 4: Spezialglas. 2003, S. 20 ff.
- Helmut A. Schaeffer: Glastechnik. Band 3: Flachglas. 2007, S. 140.
- Helmut A. Schaeffer: Glastechnik. Band 4: Spezialglas. 2003, S. 238 f.
- Helmut A. Schaeffer: Glastechnik. Band 1: Werkstoff Glas. 2012, S. 171.
- Stoffdaten zu Quarzglas auf der Website des Herstellers Heraeus. Abgerufen am 25. März 2013.
- Helmut A. Schaeffer: Glastechnik. Band 1: Werkstoff Glas. 2012, S. 122.
- Mechanische und physikalische Eigenschaften von Kalk-Natron-Silikatglas und von Borosilikatglas nach EN 572-1 [64] und EN 1748-1 [61]. (PDF; 53 kB) In: Baunetzwissen.de. Abgerufen am 20. März 2016.
- Helmut A. Schaeffer: Glastechnik. Band 1: Werkstoff Glas. 2012, S. 96.
- Verena Schulte-Frohlinde: Dicker Irrtum bei alten Fenstern – Ein Physiker räumt mit einer zählebigen Touristenführer-Legende auf: Fensterglas fließt nicht, nicht einmal ganz langsam. In: www.berliner-zeitung.de. 17. Juni 1998, abgerufen am 5. Juli 2013.
- Helmut A. Schaeffer: Glastechnik. Band 1: Werkstoff Glas. 2012, S. 38.
- Joachim Lange: Rohstoffe der Glasindustrie. 3. Auflage. 1993, S. 82.
- Joachim Lange: Rohstoffe der Glasindustrie. 3. Auflage. 1993, S. 94.
- Helmut A. Schaeffer: Glastechnik. Band 1: Werkstoff Glas. 2012, S. 195 f.
- Joachim Lange: Rohstoffe der Glasindustrie. 3. Auflage. 1993, S. 111 ff.
- Joachim Lange: Rohstoffe der Glasindustrie. 3. Auflage. 1993, S. 173.
- Joachim Lange: Rohstoffe der Glasindustrie. 3. Auflage. 1993, S. 156.
- Joachim Lange: Rohstoffe der Glasindustrie. 3. Auflage. 1993, S. 133 ff.
- Joachim Lange: Rohstoffe der Glasindustrie. 3. Auflage. 1993, S. 136.
- Helmut A. Schaeffer: Glastechnik. Band 1: Werkstoff Glas. 2012, S. 218 f.
- Glas & Nachhaltigkeit. (Nicht mehr online verfügbar.) Aktionsforum Glasverpackung im Bundesverband Glasindustrie e. V., archiviert vom Original am 20. Januar 2012; abgerufen am 6. Januar 2012.
- FMI Fachverband Mineralwolleindustrie e. V.: In zunehmendem Umfang wird bei der Herstellung von Glaswolle Altglas in Form von Fensterscheiben, Autofenstern oder Flaschenglas verwendet, wobei der Anteil von Recycling-Material mittlerweile 30 % bis 60 % der eingesetzten Rohstoffe ausmacht. In Einzelfällen erreicht dieser Anteil sogar 80 %. (abgerufen 3/2013)
- Joachim Lange: Rohstoffe der Glasindustrie. 3. Auflage. 1993, S. 99 ff.
- Joachim Lange: Rohstoffe der Glasindustrie. 3. Auflage. 1993, S. 121 f.
- Joachim Lange: Rohstoffe der Glasindustrie. 3. Auflage. 1993, S. 126 ff.
- Joachim Lange: Rohstoffe der Glasindustrie. 3. Auflage. 1993, S. 140 ff.
- I. I. Kitaigorodski: Technologie des Glases. 2. Auflage. 1957, S. 119 ff.
- Wolfgang Trier: Glasschmelzöfen. 1984, S. 240.
- Wolfgang Trier: Glasschmelzöfen. 1984, S. 244.
- Wolfgang Trier: Glasschmelzöfen. 1984, S. 1.
- Wolfgang Trier: Glasschmelzöfen. 1984, S. 150 f.
- I. I. Kitaigorodski: Technologie des Glases. 2. Auflage. 1957, S. 124 ff.
- I. I. Kitaigorodski: Technologie des Glases. 2. Auflage. 1957, S. 141 ff.
- Wolfgang Trier: Glasschmelzöfen. 1984, S. 151, S. 156 ff.
- Wolfgang Trier: Glasschmelzöfen. 1984, S. 164.
- I. I. Kitaigorodski: Technologie des Glases. 2. Auflage. 1957, S. 144 ff.
- Joachim Lange: Rohstoffe der Glasindustrie. 3. Auflage. 1993, S. 166 ff.
- Wolfgang Trier: Glasschmelzöfen. 1984, S. 7 ff.
- Wolfgang Trier: Glasschmelzöfen. 1984, S. 3 ff.
- Helmut A. Schaeffer: Glastechnik. Band 2: Hohlglas. 2010, S. 72 ff.
- Helmut A. Schaeffer: Glastechnik. Band 2: Hohlglas. 2010, S. 88 ff.
- W. Giegerich, W. Trier: Glasmaschinen. 1964, S. 394 f.
- W. Giegerich, W. Trier: Glasmaschinen. 1964, S. 89 ff.
- W. Giegerich, W. Trier: Glasmaschinen. 1964, S. 139 ff.
- Helmut A. Schaeffer: Glastechnik. Band 3: Flachglas. 2007, S. 14.
- Helmut A. Schaeffer: Glastechnik. Band 3: Flachglas. 2007, S. 51 f.
- W. Giegerich, W. Trier: Glasmaschinen. 1964, S. 341.
- H. Bach, N. Neuroth: The Properties of Optical Glass. 2. Auflage. Springer Verlag, 1998, S. 99ff.
- Siegfried Rech: Glastechnik 1. 1. Auflage, S. 122 ff.
- Siegfried Rech: Glastechnik 1. 1. Auflage, S. 122–130 ff.
- Helmut A. Schaeffer: Glastechnik. Band 4: Spezialglas. 2003, S. 172.
- Helmut A. Schaeffer: Glastechnik. Band 4: Spezialglas. 2003, S. 263.
- Helmut A. Schaeffer: Glastechnik. Band 3: Flachglas. 2007, S. 82 ff.
- Hans Joachim Gläser: Dünnfilmtechnologie auf Flachglas. Verlag Karl Hofmann. 1999, ISBN 3-7780-1041-7, S. 23 ff.
- Helmut A. Schaeffer: Glastechnik. Band 3: Flachglas. 2007, S. 102 ff.
- Hans Joachim Gläser: Dünnfilmtechnologie auf Flachglas. Verlag Karl Hofmann. 1999, ISBN 3-7780-1041-7, S. 174 ff.
- Helmut A. Schaeffer: Glastechnik. Band 3: Flachglas. 2007, S. 110 ff.
- Hans Joachim Gläser: Dünnfilmtechnologie auf Flachglas. Verlag Karl Hofmann. 1999, ISBN 3-7780-1041-7, S. 239–245.
- Hans Joachim Gläser: Dünnfilmtechnologie auf Flachglas. Verlag Karl Hofmann. 1999, ISBN 3-7780-1041-7, S. 228.
- Helmut A. Schaeffer:. Glastechnik. Band 2: Hohlglas. 2010, S. 209 ff.
- Helmut A. Schaeffer: Veränderung der Glasoberfläche während des Herstellungs- und Verarbeitungsprozesses. S. II/5 ff. In: HVG-Fortbildungskurs 1989 – Veränderung und Veredelung von Glasoberflächen.
- Helmut A. Schaeffer: Glastechnik. Band 2: Hohlglas. 2010, S. 230 ff.
- Beurteilung des Redoxzustandes von Glasschmelzaggregaten nach IGR
- Joachim Lange: Rohstoffe der Glasindustrie. 3. Auflage. Springer-Verlag, S. 184 ff.
- Joachim Lange: Rohstoffe der Glasindustrie. 3. Auflage. Springer-Verlag, S. 180 ff.
- Glassproperties.com Calculation of the Chemical Durability (Hydrolytic Class, Corrosion) of Glasses
- Glassproperties.com.
- Norman T. Huff, A. D. Call: Computerized prediction of glass compositions from properties. In: Journal of the American Ceramic Society. Band 56, Nr. 2, 1973, S. 55–57, doi:10.1111/j.1151-2916.1973.tb12356.x.
- Helmut A. Schaeffer: Glastechnik. Band 4: Spezialglas. 2003, S. 201.
- Helmut A. Schaeffer: Glastechnik. Band 1: Werkstoff Glas. 2012, S. 63.
- Eintrag zu Floatglas. In: Römpp Online. Georg Thieme Verlag, abgerufen am 29. April 2012.
- Werkstoff Glas: Alter Werkstoff mit großer Zukunft (Technik im Fokus) S. 31.
- Eintrag zu Cer. In: Römpp Online. Georg Thieme Verlag, abgerufen am 7. März 2013.
- Zum Schiffsfund Ouest-Embiez 1 (französisch)
- glasrepliken.de: Artikel über römisches Fensterglas.
- Helmut A. Schaeffer: Glastechnik. Band 3: Flachglas. 2007, S. 34.
- Axel von Saldern, Ulrich Hausmann, Reinhard Herbig, Walter Otto: Antikes Glas. C. H. Beck, München 2004, ISBN 3-406-51994-6.
- Wilhelm Hassenstein, Hermann Virl: Das Feuerwerkbuch von 1420. 600 Jahre deutsche Pulverwaffen und Büchsenmeisterei. Neudruck des Erstdruckes aus dem Jahr 1529 mit Übertragung ins Hochdeutsche und Erläuterungen von Wilhelm Hassenstein. Verlag der Deutschen Technik, München 1941, S. 108 (Glas, vitrum: „Man macht Glas von Blei und subtiler Erden“).
- Helmut A. Schaeffer: Glastechnik. Band 3: Flachglas. 2007, S. 16.
- Helmut A. Schaeffer: Glastechnik. Band 3: Flachglas. 2007, S. 17 f.
- Helmut A. Schaeffer: Glastechnik. Band 3: Flachglas. 2007, S. 44 f.
- Agr Europe (Memento vom 29. April 2013 im Webarchiv archive.today)
- Helmut A. Schaeffer: Glastechnik. Band 3: Hohlglas. 2007, S. 52.
- Geschichte der Schott AG. Abgerufen: 03/2013
- Helmut A. Schaeffer: Glastechnik. Band 3: Flachglas. 2007, S. 54 ff.
- Helmut A. Schaeffer: Glastechnik. Band 3: Flachglas. 2007, S. 60 ff.
- Siegfried Rech: Glastechnik . S. 158 ff.
- Helmut A. Schaeffer: Glastechnik. Band 3: Flachglas. 2007, S. 40 f.
- Helmut A. Schaeffer: Glastechnik. Band 3: Flachglas. 2007, S. 64 ff.
- Walter Spiegl: Maschinell gepresste und druckgeblasene Gläser (PDF; 391 kB).
- Frank Andrews: Moncrieff’s Monish Bottle-making Machines. 1947 (englisch).
- The American Society of Mechanical Engineers: Owens AR Bottle Machine (1912). 1983 (englisch).
- Emhart Glass – An Industry Leader for more than 90 Years. Emhart Glass, 2008, abgerufen am 6. Juni 2009 (englisch, Zusammenfassung der Geschichte der Firma Emhart Glass).
- W. Giegerich, W. Trier: Glasmaschinen. 1964, S. 341ff.
- Geschichte des Glases. Teil 2. (Nicht mehr online verfügbar.) In: petzi-kristall.de. Archiviert vom Original am 25. März 2016; abgerufen am 20. März 2016.
- W. Giegerich, W. Trier: Glasmaschinen. 1964, S. 353 ff.
- W. Giegerich, W. Trier: Glasmaschinen. 1964, S. 341–356.
- Die Glasbranche. Bundesverband Glasindustrie e. V., abgerufen am 6. Januar 2012.
- zur frühen Glasherstellung und ältesten Funden s. H. Wilde: Technologische Innovationen. 2003, S. 21–23, siehe Literatur.
- H. Wilde: Technologische Innovationen. 2003, S. 33–39.
- zur Gestaltung von Glasgefäßen des späten Neuen Reiches vgl. H. Wilde: Technologische Innovationen. 2003, S. 53ff.
- Lykurgosbecher
- Marco Verità: "Secrets and innovations of Venetian Glass between the 15th and the 17th Centuries. Raw Materials, Glass Melting and Artefacts". In: Rosa Barovier Mentasti/ Cristina Tonini (Hrsg.): Study Day on Venetian Glass. Approximetly 1600’s. Venedig 2013, S. 53–68, hier 57 f.
- Percorsi collezionistici / Online / I Bentivoglio al Museo Civico Medievale, auf /museibologna.it
- https://www.carltongrandcanal.com/content/uploads/2014/10/Calice-antico2.jpg
- Attila Dorigato: L’arte del vetro a Murano. San Giovanni Lupatoto 2002.
- Carol Margot Osborne: Venetian glass of the 1890s : Salviati at Stanford University. Philip Wilson Publishers in association with Iris & B. Gerald Cantor Center for Visual Arts at Stanford University, London 2002, ISBN 0-85667-545-8.
- Arbeiten ab 2010 | Glas – Ulrike Umlauf-Orrom. Abgerufen am 7. Juni 2020.
- Qizhi Z. Chen, Ian D. Thompson, Aldo R. Boccaccini: 45S5 Bioglass®-derived glass–ceramic scaffolds for bone tissue engineering. In: Biomaterials. Band 27, Nr. 11, 1. April 2006, ISSN 0142-9612, S. 2414–2425, doi:10.1016/j.biomaterials.2005.11.025 (sciencedirect.com [abgerufen am 4. Oktober 2020]).