Glasschmelzwanne
Die Glasschmelzwanne (Wanne) wird zum Herstellen der Glasschmelze bei der Herstellung von Glas benötigt.
_Illustrationsseite_245a.jpg.webp)
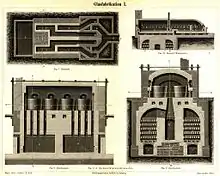
Die Glasrohstoffe werden chargenweise oder kontinuierlich der Glasschmelzwanne zugeführt. Die Bestandteile (das Gemenge) werden dabei zu einer flüssigen Glasschmelze aufgeschmolzen. Das Gemenge enthält neben den Grundkomponenten auch Scherben aus Recycling-Glas zur Energieeinsparung. Der Scherbenanteil kann je nach Anforderung der gewünschten Glasfarbe bis zu ca. 85 % – 90 % (Grünglas) betragen. Beim Wechsel der Glasfarbe (Umfärben) dauert der gesamte Vorgang in großen Glasschmelzwannen oft mehrere Tage. Für einen wirtschaftlichen Betrieb werden die Glasschmelzwannen bei sogenanntem Massenglas (Hohlglas, Flachglas) rund um die Uhr das ganze Jahr hindurch betrieben. Von einer bis max. zwei kleineren geplanten Zwischenreparaturen, bei denen die Wanne außer Betrieb genommen wird, abgesehen, kann eine sogenannte Ofenreise (Kampagne) bis zur Generalreparatur (Neuaufbau) bis zu 16 Jahre und mehr betragen (je nach Produktgruppe).
Abhängig vom Verwendungszweck gibt es verschiedene Bauformen von Glasschmelzwannen.[1]
Das Fassungsvermögen kann von ca. einer Tonne bis über 2000 Tonnen und der tägliche Durchsatz kann von einigen Kilogramm bis über 1000 Tonnen betragen. Die Betriebstemperatur im Inneren der Wanne, beträgt oberhalb des sogenannten Glasbades ca. 1500 °C. Diese Temperatur wird bestimmt durch die Zusammensetzung des Gemenges und wird von der benötigten Menge erschmolzenen Glases – der Tagesproduktion – sowie den konstruktionsbedingten Energieverlusten bestimmt.
Glasschmelzwannen werden zur Energieeffizienzsteigerung mit einem Abgas-Wärmerückgewinnungssystem betrieben.[2]
Die aus Klimaschutzgründen erforderlich Reduzierung CO2-Emission führte zu verschiedenen Konzepten, den Einsatz fossiler Energieträger zu verringern oder zu ersetzen sowie durch einen erhöhten Recycling-Anteil auch das CO2 zu vermeiden, das beim Erschmelzen des Gemenges freigesetzt wird.[3][4]
Tageswannen
Diese historische Bauart von Glasschmelzwannen produziert chargenweise (diskontinuierlich); damit werden Gläser geschmolzen, die nur in geringen Mengen benötigt werden. Die Schmelzfläche von Tageswannen liegt bei maximal 10 m2, die Schmelzleistung zwischen 0,4 und 0,8 t/m2 Schmelzfläche.
Der Hafenofen ist eine Bauart hiervon. Der Ofen besteht aus einem feuerfest gemauerten Bassin von 40 bis 60 cm Tiefe (Unterofen), das mit einem Gewölbe von 70 bis 80 cm Durchmesser übermauert ist (Oberofen).
Anfang des 21. Jh. existierten Tageswannen noch in einigen Mundglashütten und kunsthandwerklichen Ateliers sowie bei einigen Spezialglasherstellern, bei denen kleine Mengen hochqualitativen Glases erschmolzen werden, z. B. Optisches Glas.
Die Tageswannen werden am Ende eines Tages nicht außer Betrieb genommen, sondern die Temperatur wird lediglich über Nacht abgesenkt. Da das feuerfeste Material typischerweise große Temperaturwechsel nicht erträgt und dies zu verstärkter Korrosion (Verbrauch) desselben führt, kann ohnehin keine derart schnelle Abkühlung erfolgen. Wird die Tageswanne z. B. zur Wartung außer Betrieb genommen, müssen auf das feuerfeste Material abgestimmte Abkühl/Aufheiz-Zeiten (zwei bis mehrere Tage), eingehalten werden. Ausgenommen sind kleinere Öfen (Studioöfen) in kunsthandwerklichen Ateliers. Dort ist die feuerfeste Zustellung entsprechend ausgeführt.
Kontinuierlich betriebene Glasschmelzwannen
Die kontinuierlich betriebenen Wannen bestehen aus zwei Teilbereichen, der Schmelzwanne und der Arbeitswanne. Getrennt sind diese durch einen Durchlass oder eine Einschnürung (Floatglas). In der Schmelzwanne wird das aufgegebene Gemenge erschmolzen und geläutert. Anschließend gelangt die Schmelze durch den Durchlass in die Arbeitswanne und von dort in die Feeder (Vorherd). Dort erfolgt die Entnahme des Glases. Bei der Hohlglasfertigung (Hohlglas) wird die darunter stehende Glasmaschine mit Glastropfen beschickt. Bei der Flachglasfertigung (Floatglas) wird das Glas an speziellen breiten Ausläufen als Glasband über ein sogenanntes Floatbad aus flüssigen Zinn (bei Flachglas ohne Struktur : z. B. Fensterglas, Autoglas) oder für Flachglas mit Struktur über eine profilierte Walze geführt. Für die Flachglasfertigung sind auch alternative Verfahren im Einsatz. Darüber hinaus werden Glasschmelzwannen auch zur Herstellung von Mineralwolle verwendet.
Die Schmelzwannen sind aus feuerfesten Materialien erstellt und bestehen aus den Gruppen Tonerden (Al2O3), Silika (SiO2), Magnesia (MgO), Zirkonia (ZrO2) sowie aus Kombinationen davon zur Erzeugung der notwendigen feuerfesten keramischen Werkstoffe. Bei der Erstellungen von Glasschmelzöfen (Schmelzwanne inklusive Regenerativkammern) können für den Hohlglasbereich bis zu 2000 t und für den Flachglasbereich bis zu 9000 t feuerfestes Material aufgewendet werden.
Als Wärmequelle dient im Jahre 2021 typischerweise Erdgas, Schwer- und Leichtöl sowie elektrischer Strom, der mittels Elektroden direkt ins Glasbad geleitet wird. Die Beheizung mit fossilen Energieträgern wird oftmals mit einer elektrischen Zusatzbeheizung kombiniert. Es werden auch ausschließlich elektrisch beheizte Glasschmelzwannen verwendet.
Wird statt Luft reiner Sauerstoff zur Verbrennung von fossilem Brennstoff (vorzugsweise Gas) verwendet, treten Energieeinsparung und im günstigsten Fall auch geringere Betriebskosten auf. Die Verbrennungstemperatur und damit der Wärmeübergang sind höher, das aufzuheizende Gasvolumen hingegen ist geringer. Mit Sauerstoff betriebene Glasschmelzwannen rechnen sich jedoch, wegen der teuren Sauerstofferzeugung, bei der Produktion von sogenanntem Massenglas wie Hohlglas und Flachglas zur Zeit meist nicht. Es sind viele verschiedene Konstruktionen von Glasschmelzwannen bekannt.[5]
Zur Energieeinsparung beim Glasschmelzprozess dient, neben einem möglichst hohen Anteil von Recyclingglas (je 10 % Scherben ca. 2 % Energieeinsparung), das Erwärmen der Verbrennungsluft auf ein möglichst hohes Temperaturniveau durch ein Regenerativ- oder ein Rekuperatorsystem. Eine weitere technische Entwicklung besteht darin, das Gemenge über einen Wärmetauscher, der mit dem Abgas beheizt wird, auf ca. 250 °C vorzuwärmen.
Regenerator
Dieses Verfahren wurde vom Siemens-Martin-Ofen, welcher Mitte des 19. Jh. zur Stahlerzeugung entwickelt wurde, abgeleitet und ist das heute meist gebräuchliche Verfahren. Hier werden die heißen Abgase (1300 °C – 1400 °C) in Kammern (Regenerator) diskontinuierlich durch ein Gitterwerk aus feuerfesten, rechteckigen oder speziellen Formsteinen geleitet. Diese sogenannte Gitterung wird dabei erhitzt. Nach dieser Aufwärmperiode (Speicherung der Wärmeenergie des Abgases durch die Gitterung) wird die Richtung des Gasstroms umgekehrt und es strömt nun die frische, kalte, zur Verbrennung notwendige Luft durch das zuvor aufgeheizte Gitterwerk der Kammer. Die Verbrennungsluft wird dabei auf ca. 1200 °C – 1300 °C vorgewärmt. Die Abgase wiederum treten nach der Verbrennung in die Gitterung einer anderen Kammer ein und heizen dort die nun mehr zuvor abgekühlte Gitterung wieder auf. Der Vorgang wiederholt sich periodisch in Intervallen von 20 bis 30 Minuten. Die Kammern werden somit diskontinuierlich betrieben. Durch dieses Prinzip wird eine erhebliche Energieeinsparung erreicht. Der Rückgewinnungsgrad beträgt ca. 65 %[6].
Rekuperator
Rekuperatoren arbeiten kontinuierlich und bestehen aus einem metallischem Wärmetauscher zwischen Abgas und frischer Verbrennungsluft. Wegen der metallischen Austauscherfläche (warmfeste hochlegierten Stahlrohre in Kombination mit einem metallischen Doppelmantel) können Rekuperatoren nur bei geringeren Abgastemperaturen betrieben werden und arbeiten daher weniger effektiv (40 %). Somit werden hier nur relativ geringere Vorwärmtemperaturen ( max. 800 °C) erreicht.
Rekuperatoren sind weniger aufwändig zu errichten und haben einen geringeren Platz- und Investitionsbedarf als Regenaratoren. Dadurch ergeben sich bei den Investitutionskosten Kostenvorteile, welche allerdings durch die geringere Effektivität erheblich reduziert werden oder sogar für einen langen Betriebszeitraum negativ belastend ausfallen können.
Bei baulichen Einschränkungen für die Installation eines Regenerators wurden, um einen möglichst energiesparenden bzw. effizienten Betrieb der Anlage zu erreichen, auch Kombinationen von Regenerator und Rekuperator entwickelt und realisiert.[6]
Als weitere Maßnahme ist im Anschluss, zur Ausnutzung des Wärmeinhaltes des Abgases (Temperatur > 700 °C), eine nachgeschaltete Wärme/Kraft Kopplung technisch möglich bzw. bereits real im großen Maßstab erprobt worden. Allerdings ist der notwendige Wartungsaufwand eines derartigen Systems mit erheblichen Kosten verbunden und ist deshalb, hinsichtlich der damit verbundenen Betriebskosten, als kritisch zu bewerten. Daher wird dieses besondere Konzept der nachgeschalteten Energierückgewinnung zur Zeit i.a. nicht weiter verfolgt. Innovative Überarbeitungen diese Konzepts müssen mit hohem Aufwand in der Praxis im produktiven Umfeld in Langzeit getestet werden. Dies setzt allerdings eine gewisse Risikobereitschaft der Unternehmen voraus, welche wegen des harten Wettbewerbs in dieser Branche, i.a. nicht eingegangen wird.
Zukünftige Entwicklung
Ausgelöst durch die Klimadiskussion sind mittlerweile mehrere Entwicklungen und Forschungsvorhaben gestartet worden, um das klimaschädliche CO2 bei der Produktion deutlich zu reduzieren. Dazu wurde unter anderen eine Initiative gegründet, um einen neuen Glasschmelzofentyp zu etablieren. An diesem Projekt arbeiten die verschiedensten Glashersteller gemeinsam mit Technologielieferarten zum Zweck, eine entsprechende Anlage im industriellen Maßstab zu realisieren. Es ist beabsichtigt, die Anlage im Jahr 2022 mit einer Schmelzleistung von 350 Tagestonnen in Betrieb zu nehmen.[7][8] Diese Glasschmelzwanne soll mit 80 % Strom aus erneuerbaren Energien betrieben werden und soll eine Reduzierung des CO2 um 50 % ermöglichen.[9]
Des Weiteren bestehen Forschungsvorhaben, Glasschmelzwannen alternativ mit sogenanntem grünen Wasserstoff zu beheizen.[10] Bei der Verbrennung von Wasserstoff entsteht lediglich Wasserdampf. Allerdings hat der Wasserdampf einen Einfluss auf auf den Schmelzprozess und die Glaszusammensetzung sowie die Eigenschaften des produzierten Glases. Auf welche Weise dieser Einfluss gesteuert und korrigiert werden kann, ist Gegenstand weiterer Untersuchungen. Ein industrieller Großversuch wurde im August 2021 erfolgreich durchgeführt.[11]
Wasserstoff hat allerdings im Vergleich zu Erdgas einen erheblichen niedrigeren Brennwert je Kubikmeter. Dieser beträgt nur ca. ein Drittel von dem des Erdgases. Dadurch ergeben sich neue Anforderungen an Gasleitungen zum Transport von Wasserstoff.[12] Das z. Zt. bestehende Erdgasnetz ist dafür nicht ohne weiteres ausgelegt. Um die gleiche Energiemenge zur Verfügung zu stellen, müssen die Leitungen entweder um ca. 70 % größer oder für einen höheren Druck ausgelegt werden oder aber bei gleichem Druck muss eine 3fach höhere Fließgeschwindigkeit realisiert werden. Letztere Maßnahme ließe sich in existierenden Leitungsnetzen anwenden. Damit verbunden, können allerdings vermehrt Vibrationen, ausgelöst vornehmlich durch die vorhandenen Einbauten in der Leitung, auftreten, welche die Rissbildung fördern und somit längerfristig größere Schadensereignisse auslösen. Es ist bekannt, dass 100 % Wasserstoff unter gewissen Bedingungen den Werkstoff an dieser Stelle versprödet und die tiefere Rissbildung dadurch beschleunigt wird. Eine zunächst partielle Zumischung des Wasserstoffes zum Erdgas ist allerdings möglich und wurde bereits umgesetzt.[13] Zur Zeit wird eine breite wissenschaftliche Diskussion, sowie auch von Rohrlieferanten, darüber geführt.[14] Die Ergebnisse sollen dann in ein zukünftig noch zu erstellendes detailliertes Regelwerk einfließen.[15]
Literatur
- Heinz G. Pfänder: Schott-Glaslexikon. Überarbeitet und ergänzt von Hubert Schröder. mvg, München 1980, ISBN 3-478-05240-8.
Einzelnachweise
- Wolfgang Trier: Glasschmelzöfen. Konstruktion und Betriebsverhalten. Springer, Berlin u. a. 1984, ISBN 0-387-12494-2.
- B. Fleischmann: Welches Potential zur Energeieinsparung ist bei modernen Glasschmelzwannen noch vorhanden? Hüttentechnische Vereinigung der Deutschen Glasindustrie e.V.
- Energiewende in der Industrie. Chancen und Herausforderungen durch die Energiewende. BUNDESMINISTERIUM FÜR WIRTSCHAFT UND ENERGIE
- Behälterglasindustrie auf dem Weg zu 50 Prozent CO2-Reduktion. Bundesverband Glasindustrie e. V.
- SCHMELZWANNEN. HORN® Glass Industries AG (Produktbeschreibung).
- The new reality for Glass furnace enhanced heat recovery. (PDF) STARA GLASS S.P.A. (englisch, Produktbeschreibung).
- The Furnace for the Future. A Fundamental Milestone Towards Climate-Neutral Glass Packaging. (englisch).
- FEVE provides update on Furnace of the Future glass decarbonisation… Abgerufen am 13. Dezember 2021 (englisch).
- Die Schmelzwanne der Zukunft: Behälterglasindustrie auf dem Weg zu 50 Prozent CO2-Reduktion. Aktionsforum Glasverpackung, 16. März 2020 .
- Glasherstellung mit Grünem Wasserstoff erstmals erfolgreich getestet. Bundesministerium für Bildung und Forschung, 30. März 2021 .
- Architectural Glass Production Powered by Hydrogen in World First. (PDF) 3. September 2021 (englisch, Firmenmitteilung): „The trial proved that hydrogen was as capable as natural gas in achieving excellent melting performance“
- Nationaler Wasserstoffrat: Wasserstofftransport. (PDF) 16. Juli 2021, S. 7 .
- Gasunie hydrogen pipeline from Dow to Yara brought into operation. (englisch).
- Energiewende mit Wasserstoffrohren „H2Ready“ und Umstellung existierender Erdgasnetze. (PDF)
- EIN ERSTER SCHRITT ZUM EUROPÄISCHEN WASSERSTOFF-NETZ. (PDF) 31. August 2021, S. 11 (Präsentation bei TÜV SÜD : Forum H2): „Aktuell noch kein detailliertes technisches Regelwerk für Wasserstoff verfügbar:“