Physikalische Gasphasenabscheidung
Der Begriff physikalische Gasphasenabscheidung (englisch physical vapour deposition, kurz PVD), selten auch physikalische Dampfphasenabscheidung, bezeichnet eine Gruppe von vakuumbasierten Beschichtungsverfahren bzw. Dünnschichttechnologien. Anders als bei Verfahren der chemischen Gasphasenabscheidung wird mithilfe physikalischer Verfahren das Ausgangsmaterial in die Gasphase überführt. Das gasförmige Material wird anschließend zum zu beschichtenden Substrat geführt, wo es kondensiert und die Zielschicht bildet.
Verfahren
Zur Gruppe der Verfahren der physikalischen Gasphasenabscheidung zählen die unten aufgeführten Technologien sowie reaktive Varianten dieser Prozesse.
- Verdampfungsverfahren
- Thermisches Verdampfen (auch Bedampfen genannt)
- Elektronenstrahlverdampfen (engl. electron beam evaporation)
- Laserstrahlverdampfen (engl. pulsed laser deposition, pulsed laser ablation): Atome und Ionen werden durch einen kurzen intensiven Laserpuls verdampft.
- Lichtbogenverdampfen (engl. arc evaporation, Arc-PVD): Atome und Ionen werden durch einen starken Strom, der bei einer elektrischen Entladung zwischen zwei Elektroden fließt (wie bei einem Blitz), aus dem Ausgangsmaterial herausgelöst und in die Gasphase überführt.
- Molekularstrahlepitaxie (engl. molecular beam epitaxy)
- Sputtern (Sputterdeposition, Kathodenzerstäubung): Das Ausgangsmaterial wird durch Ionenbeschuß zerstäubt und in die Gasphase überführt.
- Ionenstrahlgestützte Deposition (engl. ion beam assisted deposition, IBAD)
- Ionenplattieren
- ICB-Technik (engl. ionized cluster beam deposition, ICBD)
Allgemeine Prozessbeschreibung
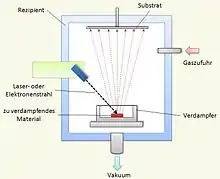
Allen diesen Verfahren ist gemein, dass das abzuscheidende Material in fester Form in der meist evakuierten Beschichtungskammer vorliegt. Durch den Beschuss mit Laserstrahlen, magnetisch abgelenkten Ionen oder Elektronen sowie durch Lichtbogenentladung wird das Material, das als Target bezeichnet wird, verdampft. Wie hoch der Anteil an Atomen, Ionen oder größeren Clustern im Dampf ist, ist von Verfahren zu Verfahren unterschiedlich. Das verdampfte Material bewegt sich entweder ballistisch oder durch elektrische Felder geführt durch die Kammer und trifft dabei auf die zu beschichtenden Teile, wo es zur Schichtbildung kommt.
Damit die Dampfteilchen die Bauteile auch erreichen, und nicht durch Streuung an den Gasteilchen verloren gehen, muss im Unterdruck gearbeitet werden. Typische Arbeitsdrucke liegen im Bereich von 10−4 Pa bis ca. 10 Pa. Da sich die Dampfteilchen geradlinig ausbreiten, werden Flächen, die vom Ort der Dampfquelle aus gesehen nicht sichtbar sind, mit einer geringeren Beschichtungsrate beschichtet. Sollen alle Flächen möglichst homogen beschichtet werden, müssen die Teile während der Beschichtung in geeigneter Weise bewegt werden. Dies geschieht meist durch Rotation des Substrats.
Treffen die Dampfteilchen nun auf das Substrat, beginnen sie sich durch Kondensation an der Oberfläche abzulagern. Die Teilchen bleiben dabei nicht an Ort und Stelle, an der sie auf das Substrat treffen, sondern bewegen sich, je nachdem wie hoch ihre Energie ist, an der Oberfläche entlang (Oberflächendiffusion), um einen energetisch günstigeren Platz zu finden. Dies sind Stellen an der Kristalloberfläche mit möglichst vielen Nachbarn (höhere Bindungsenergie).
Um die Beschichtungsrate und Schichthomogenität zu steigern, werden abhängig vom Beschichtungsprozess und dem abzuscheidenden Material die Anlagen leicht variiert. So wird beispielsweise beim thermischen Verdampfen an die zu bedampfenden Teile eine negative Spannung (Bias-Spannung) angelegt. Diese beschleunigt die positiv geladenen Dampfteilchen bzw. Metallionen (siehe entsprechende Artikel).
Da Verfahren zur physikalischen Gasphasenabscheidung Vakuumbeschichtungen sind, werden sie in der Produktion zumeist im Stapelbetrieb (Batch-Betrieb) betrieben: Chargieren (Befüllen) der Vakuumkammer, Evakuieren, Beschichten, Belüften, Öffnen und Entnahme der beschichteten Teile. Für bestimmte Anwendungen (Beschichtung von Blechen, Fasern oder Drähten und Architekturglas) gibt es jedoch Durchlaufanlagen, bei denen der Unterdruck über ein Schleusensystem erreicht wird und das zu beschichtende Gut kontinuierlich zugeführt wird.
Mit einigen PVD-Verfahren (Magnetronsputtern, Laserstrahlverdampfen, thermische Bedampfung etc.) können sehr niedrige Prozesstemperaturen verwirklicht werden. Dadurch ist es möglich, selbst niedrigschmelzende Kunststoffe zu beschichten. Der früher bei der Beschichtung von Kunststoffen gefürchtete „Eierschaleneffekt“, d. h. Rissbildung und Ablösung der Schicht aufgrund der zu großen Nachgiebigkeit des Substrats bei punktueller Belastung, konnte zudem durch gezielten Einfluss auf den Schichtaufbau mit Viellagen-Beschichtungen mit biomimetischem Aufbau ähnlich jenem von Muschelschalen minimiert werden.
Schichten
Mit den verschiedenen PVD-Varianten können fast alle Metalle und auch Kohlenstoff in sehr reiner Form abgeschieden werden. Führt man dem Prozess Reaktivgase wie Sauerstoff, Stickstoff oder Kohlenwasserstoffe zu, lassen sich auch Oxide, Nitride oder Carbide abscheiden.
Verfahren zur physikalischen Gasphasenabscheidung werden vorwiegend zur Abscheidung dünner Schichten im Bereich einiger Nanometer bis hin zu einigen Mikrometern verwendet. Mit der Schichtdicke nehmen auch die Eigenspannungen innerhalb der Schichten zu, was zur Ablösung vom Substrat (Delamination) führen kann. Dies ist einer der Gründe, weshalb sich mit PVD-Verfahren nicht ohne Weiteres beliebig dicke Schichten herstellen lassen. Forschungsergebnisse des Fraunhofer-Instituts IWS in Dresden zeigen Möglichkeiten auf, Schichtdicken von > 20 µm mit PVD-Verfahren aufzubringen. Dabei werden viele Schichten im nm-Bereich übereinander aufgebracht.[1]
Anwendungen
Schichten der physikalischen Gasphasenabscheidung finden in vielen Bereichen der Industrie Verwendung.
Oberflächenverstärkung
Vor allem im Bereich der spanenden Bearbeitung werden inzwischen größtenteils Werkzeuge aus beschichteten Schneidstoffen eingesetzt. Als Beschichtungen kommen heute vor allem Hartstoffschichten auf Basis von Titannitrid (TiN), Titancarbonitrid (TiCN) oder Titanaluminiumnitrid (TiAlN) zum Einsatz.[2] Bereits Anfang der 1990er Jahre wurden durch verschiedene Forschungseinrichtungen weitere Einsatzmöglichkeiten im Bereich der Werkzeugbeschichtungen für den Druckguss von Aluminium und Magnesium untersucht. Bei diesen Anwendungen kommen vor allem chrombasierende Schichtsysteme wie Chromnitrid (CrN), Chromvanadiumnitrid (CrVN) und Chromaluminiumnitrid (CrAlN) zum Einsatz. Beschichtungen aus CrN finden vielfach auch im Korrosionsschutz Verwendung.
Mikroelektronik
PVD-Schichten werden in der Mikroelektronik z. B. zum Erzeugen von Metall- oder (organischen) Halbleiterschichten eingesetzt. Im Bereich der Unterhaltungselektronik werden Datenträger wie Festplatten, CDs und DVDs mit PVD-Verfahren beschichtet.
Oberflächenschutz
Polyethylen-Folien in der Lebensmittelindustrie (z. B. Kartoffelchipstüten) erhalten von innen eine dünne PVD-Schicht als Dampfsperre. In vielen anderen Anwendungen von Kunststoffen (wie. z. B. zum Verschleißschutz, für optische und dekorative Zwecke) finden PVD-Beschichtungsverfahren bei niedrigen Temperaturen (Raumtemperatur) vermehrt Verwendung. Auch Architekturgläser oder Displays werden mit Schutzschichten im PVD-Verfahren überzogen.
Brennstoffzellen
Bei Brennstoffzellen, im Speziellen Festoxidbrennstoffzellen, können die Elektrolyte durch PVD erzeugt werden, um so möglichst dünne Elektrolyte zu erhalten, die die elektrische Leistungsfähigkeit einer Zelle steigern.
Brennelemente
Eine jüngere Anwendung findet sich in der Fertigung von Nuklear-Brennelementen. Hier wird vor dem Cladding mittels PVD eine Sperrschicht aus z. B. Zirkonium auf die Uran-Molybdän-Folien (U-Mo) aufgedampft. Damit wird im Betrieb die unerwünschte Diffusion zwischen Brennstoff (U-Mo) und der Brennelemente-Hülle (Aluminium) verhindert.[3]
Literatur
- Gerhard Kienel, Klaus Röll: Vakuumbeschichtung: Band 2 Verfahren und Anlagen. Springer, 1997, ISBN 3-540-62266-7.
- Donald M. Mattox: Handbook of Physical Vapor Deposition (PVD) Processing. 2. Auflage. William Andrew, 2010, ISBN 978-0-8155-2037-5 (englisch).
- K. S. Sree Harsha: Principles of Physical Vapor Deposition of Thin Films. Elsevier Science & Technology, 2006, ISBN 0-08-044699-X (englisch).
- Christoph Eisenmenger-Sittner: Physik und Technologie Dünner Schichten; Beschichtungsverfahren. (PDF; 942 kB) TU Wien; Institut für Festkörperphysik, S. 1 - 38, abgerufen am 6. Januar 2020.
Einzelnachweise
- Dr. Ottmar Zimmer: Harte Schichten > 20 μm - neue Möglichkeiten für die Dünnschichttechnik. (PDF; 107 kB) IWS Fraunhofer, 2008, abgerufen am 6. Januar 2020.
- PVD-Beschichtung. Abgerufen am 6. Januar 2020.
- Technische Universität München: Brennstoff-Fertigung für den FRM II. Abgerufen am 6. Januar 2020.