Klebstoff
Ein Klebstoff ist ein nichtmetallischer Stoff, der in der Lage ist, Werkstoffe durch Oberflächenhaftung (Adhäsion) und seine innere Festigkeit (Kohäsion) zu verbinden.[1] Es handelt sich also um einen Prozesswerkstoff, der beim Fügeverfahren Kleben zum Verbinden verschiedener Werkstoffe verwendet wird. Zusätzlich zu der lastübertragenden Wirkung können Klebstoffe in den Verbindungen weitere Funktionen übernehmen, wie z. B. Schwingungsdämpfung, Abdichten gegen Flüssigkeiten und Gase, Ausgleich unterschiedlicher Fügeteildynamiken, Korrosionsschutz, thermische und elektrische Isolation oder Leitfähigkeit.
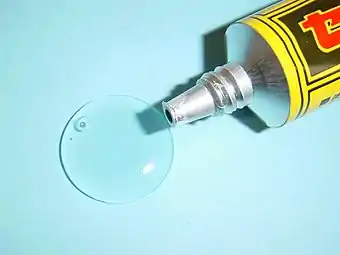
Aufgrund der vielfältigen Vorteile des Fügeverfahrens Kleben sind Klebstoffe aus dem alltäglichen Leben nicht mehr wegzudenken. Mit ihren zahlreichen Anwendungen in den verschiedensten Industriezweigen sind sie für das heutige, moderne Leben praktisch unverzichtbar geworden. Viele Produkte, wie z. B. Bücher, Mobiltelefone, Laminat-Fußböden, Autos und unzählige mehr, wären in ihrer heutigen Form ohne Klebstoffe nicht realisierbar.
Geschichte
Das Kleben ist eine der ältesten und wichtigsten Kulturtechniken der Menschheit. Klebstoffe ermöglichten die Herstellung von Waffen und Werkzeugen und halfen den Frühmenschen, sich gegen eine feindliche Umwelt durchzusetzen. Materielle Beweise sind allerdings rar, da die meisten damaligen organischen Werkstoffe wenig feuchtebeständig sind und von Bakterien und Pilzen zersetzt werden.
Das älteste von Menschen eingesetzte Bindemittel war wohl tonhaltige Erde, die als Putz- und Mauermörtel verwendet wurde.
Jungsteinzeitmenschen nutzten die Klebkraft von Asphalt (Erdpech), Baumharzen und Holzteer. In Sachsen-Anhalt wurde Birkenpech als Klebemittel von Klingeneinsätzen bei Schäftungen (Messer, Speere) gefunden, das mindestens 115.000 Jahre alt war. In Süditalien stießen Wissenschaftler auf Birkenpech, das an einem mindestens 180.000 Jahre alten Steinwerkzeug haftete. Auch Ötzi hatte die Klinge seiner Axt aus Eibenholz vor über 5000 Jahren mit Birkenpech und Lederriemen befestigt.[2] Dieser frühe Klebstoff wurde aus Birkenrinde durch Trockendestillation hergestellt.[3] Untersuchungen aus dem Jahre 2019 kamen zu dem Schluss, dass brauchbare Mengen an Birkenpech schon durch das reine Verbrennen von Birkenrinde nahe Stein- oder Knochenoberflächen hergestellt werden können. Das Birkenpech kann im Anschluss an die Verbrennung von den Oberflächen abgekratzt werden.[4] Der antike Geschichtsschreiber Herodot berichtet, dass die Mauern Babylons mit Erdpech geklebt wurden.
3500 vor Christus wurde das Eiweiß im Tierblut als Bindemittel bei Höhlenmalereien verwendet. 2000 vor Christus begannen die Menschen in Vorderasien Gelatineleime beim Bau von Möbeln zu verwenden.[2] Die Sumerer stellten Leim aus ausgekochten Tierhäuten her.
Spätestens seit etwa 1500 v. Chr. verwendeten die Ägypter einen Sud aus Sehnen, Knorpel und anderen tierischen Abfällen als Klebstoff für furnierte Schreinerarbeiten. Der so entstandene Klebstoff wurde warm aufgetragen und hat teils mehr als drei Jahrtausende überdauert, wie eine Tafel aus dem Grab Tutanchamuns beweist. Die Ägypter nutzten Bienenwachs für handwerkliche Klebungen, indem sie es mit pulverisiertem Steinmehl vermischten und damit z. B. Metallklingen von Rasiermessern mit ihrem Stiel verbanden.
Im antiken Griechenland gab es den Berufsstand des Leimsieders, der einen „Kolla“ genannten eiweißhaltigen Leim herstellte. Die Römer bezeichneten ihre aus Mehlkleister, gesäuertem Brot oder Käse-Kalk-Mischungen hergestellten Leime als „Glutinum“. Angeblich stellten die Römer rund 1000 Jahre vor den Germanen aus Schwimmblasen gewonnenen Fischleim her.
In der nachfolgenden Zeit ist bei Klebstoffen vorerst keine große Entwicklung zu verzeichnen. Erst im Spätmittelalter bildeten sich in Europa nach und nach die ersten eigenständigen Leimsiedereien, da sich die Papierverarbeitung nach der Erfindung des Buchdrucks durch Gutenberg zum Wachstumsmarkt entwickelte. Die immer zahlreicheren Bücher mussten gebunden und mit stabilen Deckeln und Rücken verklebt werden. Die Herstellung von Leimen war teilweise eine eintönige Arbeit und die Bezeichnung „Leimsieder“ galt lange Zeit als Schimpfwort für stumpfsinnige Menschen.
Im Zuge der Industrialisierung erfuhr der Berufsstand einen Aufschwung, der sich Hand in Hand mit der Möbel- und Tapetenindustrie vollzog. Rationellere Herstellungsmethoden ermöglichten es auch einfachen Leuten, sich aufwändiger gefertigtes Mobiliar und vornehm gestaltete Wände zu leisten. Die erste handwerkliche Leimfabrik wurde 1690 in Holland gegründet. 1754 wurde in England das erste Patent auf einen Fischleim für die Tischlerei erteilt und 1789 eröffnete die erste Tapetendruckerei Deutschlands in Kassel.
Nachdem 1880 Otto Ring einen gebrauchsfertigen Fischleim „Syndetikon“ und Ferdinand Sichel 1889 einen ebensolchen Pflanzenleim entwickelt hatte, brach 1909, mit dem Patent zur Phenolharz-Härtung von Leo Hendrik Baekeland, das Zeitalter der Klebstoffe auf Basis synthetisch hergestellter Rohstoffe an. Chemiker, Physiker und Ingenieure setzten sich mit den Wirkungen von Adhäsions- und Kohäsionskräften auseinander, erforschten den makromolekularen Aufbau der Klebstoffe, vervollkommneten die bekannten Rohstoffe und fanden schließlich in den Kunstharzen die Ausgangsbasis für immer leistungsfähigere synthetische Klebstoffe.
Der bis heute für die Klebstoffherstellung meist verwendete synthetische Rohstoff, das Polyvinylacetat, wurde 1914 von Rollet und Klatte patentiert. 1928 fand in den USA die erstmalige Produktion von Polyvinylchlorid (PVC) und Polymethylmethacrylat (Plexiglas) statt. 1929 wurde ein Verfahren zur Härtung des 1919 entdeckten Harnstoffharzes entwickelt und machte es somit einsetzbar für Leime.
In den 30er Jahren des letzten Jahrhunderts gelang die erste technische Herstellung von Polyvinylacetat, Polystyrol und Polyacrylnitril sowie der ersten stabilen Kunststoff-Dispersion auf Basis von Acrylsäureestern und Vinylacetat. Der Schweizer Pierre Castan benutzte die Polyaddition zum Aufbau von Kunststoffen und erfand Epoxidharze, die ihm 1939 patentiert wurden. Neben der Entwicklung des ersten transparenten Klebebandes sind die Herstellung des Rohstoffes Polychlorbutadien und die von Bayer patentierten Polyurethane von enormer Marktbedeutung für die Klebstoffbranche.
Durch die Verwendung von Phenolharz-Polyvinylacetaten und Epoxidharz-Formulierungen hielt der Klebstoff 1943 Einzug in den Flugzeugbau. Als dann 1960 die Produktion von anaeroben und Cyanacrylat-Klebstoffen aufgenommen wurde, gelang der Klebstoffindustrie ein entscheidender Durchbruch im Bereich der Metall- und Kunststoffverbindungen.
Mit der Entdeckung der ersten temperaturfesten Polyimid-Klebstoffe und feuchtigkeitshärtenden Polyurethane erfolgte in den 70er Jahren eine rasche Weiterentwicklung der Polyurethan-Chemie mit vielfältigen 1- und 2-Komponenten-Formulierungen, UV-lichthärtende Acrylat-Formulierungen sowie die Entwicklung von MS-Polymeren. Reaktive Schmelzklebstoffe und anisotrop leitfähige Klebstoffe bezeichnen die größten Errungenschaften der 80er Jahre.
Ab 1990 beginnt die Entwicklung von Klebstoffen mit multiplen Härtungsmechanismen (z. B. UV-Bestrahlung, Luftfeuchtigkeit, Sauerstoffzutritt). Die 1995 entwickelten silanvernetzenden Polyurethan-Prepolymeren (S-PUR) zeigen eine verbesserte Balance zwischen Reaktivität und Lagerstabilität, ein Ausbleiben der Blasenbildung bei der Härtung und besitzen keinen isocyanatbasierten Reaktionsmechanismus mehr. Im Jahre 2000 begann die Entwicklung wiederlösbarer Klebstoffsysteme für Reparatur und Recycling, basierend auf den Methoden Temperatur-, Spannung-, Strom- und pH-Wert-Änderung.
Für die Zukunft kann man weitere Wachstumsopportunitäten erkennen. Gründe hierfür sind die Übernahme zusätzlicher Funktionen, die bisher von anderen Materialien übernommen wurden, der zunehmende Leichtbau und nicht zuletzt die Miniaturisierung elektronischer Bauteile.
Wirtschaftliche Bedeutung
In Deutschland werden jährlich ca. 1,5 Millionen Tonnen Kleb-, Dicht- und zementäre Bauklebstoffe sowie 1 Milliarde Quadratmeter trägergebundene Klebstoffe (Klebebänder/Klebefolien) produziert und damit ein Gesamtbranchenumsatz von 3,7 Milliarden Euro erzielt. Die durch den Einsatz von Klebtechnik generierte Wertschöpfung beträgt – konservativ gerechnet – deutlich über 360 Milliarden Euro. Dieser Betrag entspricht rund 50 % des Beitrages des produzierenden Gewerbes und der Bauwirtschaft zum deutschen Bruttoinlandprodukt (BIP). Somit stehen rund 50 % der in Deutschland produzierten Waren und Baudienstleistungen mit Klebstoffen in Verbindung.[5]
Interessant ist eine vergleichende Betrachtung der Entwicklung des Bruttoinlandprodukts und des Wachstums der Klebstoffindustrie. Über die letzten zehn Jahre ist deutlich zu beobachten, dass auch die Klebstoffindustrie den gesamtwirtschaftlichen Konjunkturzyklen unterliegt – allerdings mit Wachstumsraten, die im Durchschnitt 2,5–5 % über den Wachstumsraten des BIP liegen.[5]
Das globale Marktvolumen für Klebstoffe für 2016 wird auf 49,5 Milliarden USD geschätzt. Papier und Verpackung war 2015 das größte Anwendungssegment des Marktes für Kleb- und Dichtstoffe. Von den verschiedenen Klebstofftechnologien stellten die wasserbasierten Klebstoffe 2015 sowohl wert- als auch mengenmäßig das größte Segment. Wachsende Bevölkerungszahlen und die steigende Nachfrage nach Konsumgütern in mehreren Ländern rund um den Globus sind ein Schlüsselfaktor, der das Wachstum der Klebstoffindustrie in den kommenden Jahren weiter vorantreiben wird. Länder wie China, Japan und Indien werden weiter an Bedeutung gewinnen. Für 2021 wird erwartet, dass der globale Umsatz an Kleb- und Dichtstoffen gut 63 Milliarden USD betragen wird.[6]
Einteilung
Aufgrund der vielfältigen Einsatzgebiete für Klebstoffe und der damit verbundenen verschiedenen Anforderungen ist es nicht verwunderlich, dass eine schier unübersehbare Zahl Klebstoffen angeboten wird. Daher ist es sinnvoll, Klebstoffe zu klassifizieren, um so Gemeinsamkeiten, aber auch Unterschiede besser erkennen und verstehen zu können. Eine erste Einteilung kann entsprechend ihrer chemischen Basis erfolgen.
So wird zwischen Klebstoffen, hergestellt auf Basis organischer Substanzen und solchen basierend auf anorganischer Substanzen unterschieden. Dazwischen stehen die Silikone, die sowohl organische als auch anorganische Bestandteile enthalten. Zusätzlich kann zwischen Klebstoffen, die eine natürliche oder eine synthetische organische Basis haben, unterschieden werden. Letzteres ist häufig nicht eindeutig zu erkennen, da viele Klebstoffe sowohl synthetische als auch natürliche Rohstoffe enthalten. Solche auf rein natürlicher Basis, wie z. B. Bienenwachs oder Baumharz sind wegen der für die meisten Anwendungen nicht ausreichenden Eigenschaften recht selten. Seit einigen Jahren beobachtet man, nicht zuletzt als Folge eines zunehmenden Umweltbewusstseins, der Forderung nach mehr Nachhaltigkeit und der Verringerung des Carbon Footprint einen zunehmenden Einsatz von auf nachwachsenden Rohstoffen basierenden Klebstoffbestandteilen.
Eine weitere, mehr ins Detail gehende Einteilung ist die nach dem Mechanismus der Verfestigung. Hierbei wird zwischen einer Verfestigung durch einen physikalischen Vorgang und der durch eine chemische Reaktion unterschieden. Weiterhin gibt es die Gruppe der Klebstoffe, die keinem Verfestigungsmechanismus unterliegen. Diese drei, in der Tabelle 1 zusammengestellten Klebstoffarten werden im Anschluss näher erläutert.
Die weitere Unterteilung der Einteilung in Duroplaste, Thermoplaste und Elastomere, wie sie bei Kunststoffen üblich ist, gibt dem Anwender wertvolle Hinweise zu den Eigenschaften des jeweiligen Klebstoffs in seinem verfestigten Zustand. Es muss jedoch berücksichtigt werden, dass Klebstoffe ein und derselben Polymerart, in Abhängigkeit von den beigefügten Additiven oder Komponenten sowohl zu Duroplasten, als auch zu Elastomeren oder Thermoplasten härten bzw. als solche vorliegen können. Ein gutes Beispiel hierfür sind die Polyurethanklebstoffe.
KLEBSTOFFE | |||
---|---|---|---|
chemisch härtend | physikalisch abbindend | Klebstoffe mit kombinierten Verfestigungsmechanismen | Klebebänder |
Härtung durch Polymerisation
|
Verfestigung durch Trocknen
|
Kombination von verschiedenen chemischen Mechanismen
|
Keine Verfestigung
|
Härtung durch Polyaddition
|
Verfestigung durch Abkühlen
|
Kombination eines physikalisch und eines chemischen Verfestigungsmechanismus
|
|
Härtung durch Polykondensation
|
Verfestigung durch Gel-Bildung
|
Physikalisch abbindende Klebstoffe
Hierunter versteht man solche Klebstoffe, bei denen die Polymerketten in dem vom Klebstoffhersteller ausgelieferten Klebstoff bereits in ihrer endgültigen Zusammensetzung und Größe vorliegen. Das heißt, das Polymer an sich unterliegt bei der Verfestigung des Klebstoffs keiner chemischen Veränderung. Da Klebstoffe um überhaupt auf einem Fügeteil haften, d. h. Adhäsion aufbauen zu können in flüssiger Form vorliegen müssen, sind für diese Klebstoffklasse nur solche Polymere geeignet, die sich verflüssigen lassen. So lassen sich Thermoplaste durch Erwärmung verflüssigen, um durch Erkalten wieder zu erstarren. Weitere Möglichkeiten sind in Lösemittel lösliche Thermoplaste und die Überführung in eine Dispersion. Die Verfestigung des Klebstoffs erfolgt also durch einen physikalischen Vorgang, dem Erstarren bzw. dem Verdampfen des Lösemittels bzw. des Dispersionsmedium Wasser. Das Abkühlen eines Schmelzklebstoffs hat zur Folge, dass die Beweglichkeit der Polymerketten eingeschränkt wird und sich zwischen den Polymerketten physikalische Wechselwirkungen, wohlgemerkt keine chemischen Bindungen ausbilden, die in ihrer Art und ihrem Ausmaß im Endeffekt die innere Festigkeit, d. h. die Kohäsion des Klebstoffs im verfestigten Zustand bestimmen. Bei Klebstoffen, bei denen der flüssige Zustand schon bei der Herstellung durch Lösen eines Polymers in einem Lösemittel oder die Überführung in eine Dispersion erfolgte, kommt es durch Verdampfen des Lösemittels bzw. des Dispersionsmediums zur Verfestigung. Das Verdampfen des Lösemittels, bzw. des Dispersionsmediums hat zur Folge, dass sich die Polymerketten einander annähern und es dadurch zur Ausbildung von physikalischen Wechselwirkungen kommt. Bildlich dargestellt können die Polymerketten mit Spaghetti verglichen werden. Solange sie sich im heißen Wasser befinden, sind sie relativ leicht beweglich. Verdampft jedoch das Wasser, kommen sie sich näher, bilden Wechselwirkungen untereinander aus und erhalten damit eine gewisse innere Festigkeit.
Im Folgenden werden die wichtigsten Arten der sich physikalisch verfestigenden Klebstoffe charakterisiert und hinsichtlich ihrer typischen Eigenschaften und Anwendungsgebiete beschrieben.
Lösemittelhaltige Nassklebstoffe
Bei lösemittelhaltigen Nassklebstoffen liegt das Polymer in organischen Lösemitteln gelöst vor. Der Klebstoff wird meist auf eines der Fügeteile aufgetragen und das Fügen findet zu einem Zeitpunkt statt, zu dem noch ein Großteil des Lösemittels im Klebstoff vorhanden ist. Dies gewährleistet eine ausreichende Benetzung der zweiten Fügeteiloberfläche. Durch Verdunsten der Lösemittel bindet der Klebstoff ab, das heißt, er wird zunächst zäher und verfestigt sich schließlich durch die Ausbildung physikalischer Wechselwirkungen zwischen den Polymerketten. Während bei einigen dieser Klebstoffe der Fügevorgang unmittelbar nach dem Klebstoffauftrag erfolgen kann, ist für andere die Einhaltung einer produktabhängigen Mindesttrockenzeit erforderlich, d. h. vor dem Fügen muss eine gewisse Ablüftezeit eingehalten werden um ein Teil des Lösemittels verdunsten zu lassen. Dieser Mindestrockenzeit schließt sich die Nassklebzeit an. Dies ist der Zeitraum innerhalb dessen der Klebstoff noch ausreichend Lösemittel enthält, somit ausreichend flüssig ist und das zweite Fügeteil gut zu benetzen. Wird die Nassklebzeit überschritten ist dies in der Regel mit Qualitätseinbußen hinsichtlich Klebfestigkeit verbunden. Der Zeitraum aus Mindesttrockenzeit und Nassklebzeit wird häufig als offene Wartezeit bezeichnet. Die sich anschließende sogenannte geschlossene Wartezeit beschreibt den Zeitraum innerhalb dessen der Klebstoff soweit abbindet, dass eine, die weitere Handhabung der Klebung erlaubende Anfangsfestigkeit erreicht wird. In diesem Zeitraum darf die Klebung nicht belastet werden, was in der Regel eine Fixierung erfordert. Während die offene Wartezeit und die Nassklebezeit im Wesentlichen vom jeweiligen Klebstoff und den Umgebungsbedingungen abhängen ist die geschlossene Wartezeit zusätzlich von den Fügeteilwerkstoffen, d. h. deren Vermögen, das Lösemittel aus der Klebfuge entweichen zu lassen und den Anforderungen an die Höhe der Anfangsfestigkeit abhängig.
Als Polymere werden z. B. Polyurethane, Polyvinylacetat, Synthese- oder Naturkautschuk sowie Acrylate verwendet. Die Art des Lösemittels, wobei häufig auch Gemische verwendet werden, richtet sich nach dem jeweiligen Polymer und dessen Löslichkeit. Typische Lösemittel sind unter anderem Ester (z. B. Ethylacetat), Ketone (z. B. 2-Butanon) oder auch Tetrahydrofuran.
Lösemittelhaltige Nassklebstoffe können auch zum Diffusionskleben (Kaltverschweißen) thermoplastischer Kunststoffe verwendet werden. Dabei werden beide Klebflächen mit dem Klebstoff bestrichen, der ein Lösemittel enthält, welches imstande ist, die Oberfläche der Fügeteile anzulösen. Nach kurzer Einwirkzeit werden die beiden Fügeteile unter Druck gefügt, wodurch sich die durch das Lösemittel freigelegten Polymerketten der angelösten Oberfläche – ähnlich wie die Borsten zweier Bürsten, die ineinander gedrückt werden – durchdringen und miteinander verschlaufen. Nach Entweichen des Lösemittels entsteht so nach einiger Zeit eine Verbindung, die rein auf Kohäsionskräften beruht. Umgangssprachlich wird dieses Verfahren auch als Kaltschweißen oder Quellschweißen bezeichnet.
Anwendungsgebiete
Beispiele für lösemittelhaltige Nassklebstoffe waren lange Zeit die sogenannten „Alleskleber“. Hierzu sei angemerkt, dass es eigentlich „Allesklebstoff“ heißen müsste, es einen solchen im engeren Sinne aber wohl nie gegeben hat. Ähnlich wie beispielsweise eine "Universalschraube" eine Schraube mit vielfältigen Anwendungsgebieten bezeichnet, ist ein "Allesklebstoff" zum Kleben verschiedenster Materialien, wenn auch nicht aller Materialien, geeignet.
Während in der Vergangenheit vielfach Lösemittelklebstoffe u. a. auch im Bereich Hobby und Haushalt verwendet wurden, sind diese aus ökologischen und Arbeitssicherheitsgründen hier und in vielen Anwendungsgebieten durch andere Systeme, die keine brennbaren und/oder gesundheitsschädlichen Lösemittel enthalten ersetzt worden. Heute kommen sie insbesondere zum Kleben von Papier und Pappe sowie zum Diffusionskleben, insbesondere von PVC zum Einsatz.
Beim Einsatz von lösemittelhaltigen Nassklebstoffen sind neben deren Entzündlichkeit und/oder gesundheitsschädlichen Wirkung zu beachten, dass
- insbesondere bei großflächigen Klebungen mindestens ein Substrat lösemitteldurchlässig sein muss, da ansonsten das zum Abbinden erforderliche vollständige Entweichen des Lösemittels aus der Klebfuge sehr lange dauern kann (bis zu einigen Tagen oder Wochen).
- die Eignung lösemittelhaltiger Nassklebstoffe zur Klebung spannungsrissempfindlicher Materialien wie Polycarbonat kritisch betrachtet werden muss, da die enthaltenen Lösemittel Spannungsrisse auslösen können.
Lösemittelhaltige Nassklebstoffe ermöglichen klebstoffabhängig Festigkeiten bis hin zu etwa 10 MPa bei Bruchdehnung im Bereich von ca. 5 bis 400 %. Da es sich bei den als Klebrohstoffen eingesetzten Polymeren um Thermoplaste handelt, weisen die Klebungen eine begrenzte Wärmeformbeständigkeit auf, zeigen unter Belastung eine Neigung zum Kriechen und sind empfindlich gegenüber Lösemitteln.
Kontaktklebstoffe
Bei Kontaktklebstoffen handelt es sich um in Lösemitteln gelöste Polymere (insbesondere Polychloropren und Polyurethane) oder als umweltfreundlichere Alternative um Dispersionen in Wasser. Sie unterscheiden sich jedoch in ihrer Verarbeitung dahingehend, dass Kontaktklebstoffe auf beide Fügeteile aufgetragen werden. Erst nachdem ein Großteil des Lösemittels bzw. Wassers verdunstet ist, d. h. der Klebstofffilm quasi trocken ist, werden die Bauteile gefügt. Hierbei ist der Anpressdruck, er sollte mindestens 0,5 MPa betragen, von ausschlaggebender, die Anpressdauer von untergeordneter Bedeutung. Durch das Zusammenpressen fließen die beiden im amorphen Zustand vorliegenden Klebstoffschichten ineinander, um sich anschließend weiter, unter Ausbildung kristalliner Strukturen zu verfestigen. Die Klebung ist nach dem Fügen sofort belastbar, die Einhaltung einer geschlossenen Wartezeit ist also für typische Kontaktklebstoffe nicht erforderlich.
Die Mindesttrockenzeit bezeichnet hier den Zeitraum, den der Klebfilm benötigt, bis er beim Berühren mit der Fingerkuppe zwar noch eine gewisse Restklebrigkeit aufweist, aber keine Fäden mehr zieht und somit das Fügen erfolgen kann. Um Hautkontakt mit den Restlösemitteln zu vermeiden, sollten bei diesem sogenannten Fingertest geeignete Handschuhe getragen werden. In den technischen Datenblättern der Kontaktklebstoffe wird in der Regel die Kontaktklebzeit, d. h. der Zeitraum nach Ende der Mindesttrockenzeit, innerhalb derer gefügt werden muss, angegeben. Wird erst nach Überschreiten der Kontaktklebzeit gefügt, ist mit Einbußen bei der Festigkeit der Klebung zu rechnen. Bei vielen Kontaktklebstoffen ist, sollte die Kontaktklebzeit überschritten sein, eine Reaktivierung des Klebfilms durch Wärme möglich. Angaben hierzu finden sich ebenfalls in den technischen Datenblättern der jeweiligen Klebstoffe.
Zur Verwendung der lösemittelfreien, wasserbasierten Kontaktklebstoffe muss jedoch angemerkt werden, dass insbesondere die langen Mindesttrockenzeiten und die häufig nur begrenzte Feuchtigkeitsbeständigkeit ihrer Verwendung entgegenstehen. Die Trocknung kann durch einen entsprechenden Wärmeeintrag in Trockenkanälen beschleunigt und die mangelnde Feuchtigkeitsbeständigkeit durch ein zwei-komponentiges Arbeiten, d. h. der Zugabe eines Vernetzers vor der Verwendung (siehe Klebstoffe mit kombinierten Verfestigungsmechanismen) kompensiert werden.
Anwendungsgebiete
Kontaktklebstoffe werden z. B. zum Kleben von Bodenbelägen, bei der Herstellung von Matratzen und Schuhen und zum Anbringen von Zier- und Scheuerleisten eingesetzt. Da das Lösemittel bereits vor dem Fügen nahezu vollständig aus dem Klebfilm entwichen ist, eignen sich Kontaktklebstoffe auch für das Kleben zweier lösemittelundurchlässiger Fügeteile.
Beim Einsatz von Kontaktklebstoffen ist zu beachten, dass
- die produktspezifischen Prozesszeiten, Mindesttrockenzeit und Kontaktklebzeit eingehalten werden
- beim Fügen der erforderliche Anpressdruck gewährleistet ist
Kommen lösemittelhaltige Kontaktklebstoffe zum Einsatz ist neben deren Entzündlichkeit und/oder gesundheitsschädlichen Wirkung zu berücksichtigen,
- dass die enthaltenen Lösemittel bei Kunststoffen Spannungsrisskorrosion auslösen können.
Dispersionsklebstoffe
Bei Dispersionsklebstoffen wird in der Regel Wasser verwendet, um die Klebstoffpolymere in den fürs Kleben erforderlichen flüssigen Zustand zu überführen. Jedoch liegen die Polymere nicht, wie bei Lösemittelklebstoffen gelöst, sondern in Form einer Dispersion vor. Die Polymerteilchen liegen in Form kleinster Teilchen vor und schweben sozusagen in dem (als mobile Phase bezeichneten) Wasser. Bei einem Dispersionsklebstoff handelt es sich also um einen Klebstoff, bei dem die Klebstoffmoleküle unter Zuhilfenahme von Emulgatoren und anderen Hilfsstoffen durch die sie umgebenden Wassermoleküle auseinandergehalten werden, also nicht zu größeren Agglomeraten zusammenlagern können.
Dispersionsklebstoffe können sowohl für die Verarbeitung als Nassklebstoff, analog der oben beschriebenen lösemittelhaltigen Nassklebstoffe, als auch als Kontaktklebstoff formuliert werden. Bei beiden Formen erfolgt das Abbinden durch das Entfernen der mobilen Phase, dem Wasser. Dies kann entweder durch Verdunsten oder durch Aufnahme ins Fügeteil erfolgen. Hierbei erhöht sich die Konzentration der Polymerpartikel und die der sie auseinanderhaltenden Wassermoleküle nimmt ab. Als Folge nähern sich die Polymerpartikel immer weiter an, bis sie schließlich miteinander verfließen. Bei diesem als Filmbildung bezeichneten Vorgang kommt es zur Ausbildung von Wechselwirkungen untereinander (Ausbildung von Kohäsion) und zur Fügeteiloberfläche (Ausbildung von Adhäsion).
Ebenfalls für beide Formen gilt, dass Dispersionsklebstoffe in der Regel frostempfindlich sind, d. h. die Dispersion durch Frosteinwirkung zerstört werden kann, wodurch es zum sogenannten Brechen der Dispersion kommt, die Polymerteilchen koagulieren zu Agglomeraten, sodass kein einheitlicher Klebstofffilm mehr aufgetragen werden kann. Dies hat auch einen nachteiligen Einfluss auf die Ausbildung von Adhäsion zum Fügeteil. Die bei Förderung des Klebstoffs durch Schlauch- oder Rohrleitungen, bzw. in den dafür verwendeten Pumpen auftretenden Scherkräfte können ebenfalls zum Brechen der Dispersion führen. Weiterhin sind Dispersionsklebstoffe für Schimmelbefall im Lagerbehälter anfällig. Meist werden deshalb durch den Klebstoffhersteller Konservierungsstoffe zugegeben, trotzdem muss jedoch, insbesondere bei Lagerung in Tanks auf Sauberkeit geachtet und ggf. Nachkonserviert werden.
Bei Nassklebstoffen ist wiederum deren offene Zeit, d. h. der Zeitraum, beginnend mit dem Klebstoffauftrag, innerhalb dessen der Fügeprozess erfolgen muss, einzuhalten. Sie wird durch Temperatur, relative Feuchte der Umgebungsluft, Klebschichtdicke und dem Wasseraufnahmevermögen des Fügeteils bestimmt. Zum Fügen werden die Fügeteile miteinander verpresst. Die Presszeit ist wiederum von der Temperatur und dem Wasseraufnahmevermögen der Fügeteile abhängig. Bei Kontaktklebstoffen sind entsprechend die Mindestablüftezeit, die wiederum von der Temperatur, der relativen Feuchte der Umgebungsluft, der Klebschichtdicke und dem Wasseraufnahmevermögen des Fügeteils abhängig ist und die Kontaktklebzeit einzuhalten sowie beim Fügen ein ausreichend hoher Anpressdruck anzuwenden.
Allgemein sind die mit Dispersionsklebstoffen erreichbaren Festigkeiten begrenzt, ebenso die Wärmeformbeständigkeit aufgrund des thermoplastischen Charakters der verwendeten Polymere. Aufgrund der zur Stabilisierung der Dispersion erforderlichen Emulgatoren zeigen sie – wenn auch die Filmbildung nicht reversibel ist – eine nur eingeschränkte Feuchtigkeitsbeständigkeit. Sowohl Wärmeform- als auch Feuchtigkeitsbeständigkeit lassen sich durch Zugabe eines Vernetzers, also durch zweikomponentiges Arbeiten deutlich verbessern (siehe auch Klebstoffe mit kombinierten Verfestigungsmechanismen).
Dispersionsklebstoffe für die Verwendung als Nassklebstoff eignen sich besonders gut für großflächige Klebungen von wasserdurchlässigen Werkstoffen, wie Holz, Papier und Pappe. Demgemäß werden sie vielfach in der Papierverarbeitung, bei der Herstellung von Verpackungen und in der Möbelindustrie verwendet. Als Kontaktklebstoff werden Dispersionsklebstoffe vielfach in der Automobilindustrie für die Kaschierung von Innenausstattungsteilen mit Dekorfolien, Textil oder Leder verwendet. Wegen der für die Anwendung erforderlichen guten Temperatur- und Feuchtebeständigkeit erfolgt die Verarbeitung meist als 2K-System (siehe auch Klebstoffe mit kombinierten Verfestigungsmechanismen).
Schmelzklebstoffe
Schmelzklebstoffe – oft auch als Hotmelts bezeichnet – sind bei Raumtemperatur fest und werden durch Aufschmelzen verarbeitbar. Die heiße Klebstoffschmelze wird auf das zu verklebende Teil aufgebracht und sofort mit dem zweiten Teil innerhalb der Offenzeit gefügt. Unmittelbar nach dem Abkühlen und Erstarren des Klebstoffs ist die Verbindung fest und funktionsfähig. Dies ermöglicht in Produktionsprozessen sehr schnelle Taktzeiten und unmittelbares Weiterverarbeiten.
Für den Hobby- und Kleinanwender kommen Schmelzklebstoffe in Form von Klebekerzen (Klebesticks) in den Handel, die mit Schmelzklebepistolen verarbeitet werden können. Bei technischen Anwendungen werden sie auch in Form von Folien, Granulaten oder Blöcken mit Hilfe von Schmelzgeräten und nachgeschalteten Auftragköpfen verarbeitet.
Schmelzklebstoffe sind lösemittelfrei, jedoch ist ihr Einsatz wegen der hohen Verarbeitungstemperaturen auf temperaturresistente Werkstoffe beschränkt. Andererseits verhält sich der Klebstoff reversibel, das heißt, bei Temperaturerhöhung wird er wieder weich und besitzt daher nur eine eingeschränkte Wärmebeständigkeit (siehe auch Reaktiver Schmelzklebstoff).
Plastisole
Unter dem Begriff Plastisol versteht man Dispersionen, also zweiphasige Systeme bestehend aus einem pulverförmigen thermoplastischen Polymer in einer hochsiedenden organischen Flüssigkeit (Weichmacher). Weitere Rezepturbestandteile sind Füllstoffe, Pigmente sowie Additive wie z. B. Haftvermittler.[7] Als Polymere kommen hauptsächlich PVC und Acrylate, als Weichmacher meist Phthalsäureester zum Einsatz.
Bei der Auswahl des Polymers und des Weichmachers muss berücksichtigt werden, dass das Polymer in dem Weichmacher zwar löslich, die Lösungsgeschwindigkeit bei Raumtemperatur aber verschwindend klein sein muss. Erst bei höheren Temperaturen diffundiert der Weichmacher in das Polymer und das zunächst zweiphasige System wandelt sich in ein einphasiges Gel um, das Plastisol geliert. Hierfür sind Temperaturen von 150–180 °C erforderlich. Beim Abkühlen erstarrt dieses aus einem plastifizierten Polymer bestehende Gel, wodurch eine Masse von extrem hochviskoser Konsistenz entsteht, die bei Raumtemperatur nicht mehr fließfähig ist. Die als Kleb- oder Dichtstoff verwendeten Plastisole verfügen über eine hohe Flexibilität und gute Schälfestigkeiten, weisen jedoch den Nachteil auf, dass sie unter Belastung eine Neigung zum Kriechen zeigen. Ferner weisen sie als Thermoplaste nur eine begrenzte Temperaturbeständigkeit auf.
Plastisole als Kleb- und Dichtstoffe
Die Verwendung von Plastisolen in der Klebtechnik ist naturgemäß auf Prozesse beschränkt bei denen die, für die Gelierung erforderlichen Temperaturen angewendet werden können. Das Hauptanwendungsgebiet ist der Karosseriebau im Automobilbau, wobei meist PVC-Plastisole eingesetzt werden. Hier stehen mit den Ofenprozessen zur Lackhärtung entsprechende Temperaturen zur Verfügung. Die Plastisole übernehmen neben einer fügenden Funktion, oft verbunden mit einer Steifigkeitserhöhung der Karosse auch das Abdichten von Fugen gegen Feuchtigkeitseintritt (Vermeidung von Korrosion), sowie eine dämpfende Funktion. Die Fähigkeit der Plastisole bei der Gelierung auf der Blechoberflächen befindliche Korrosionsschutz- und Ziehöle in sich aufzunehmen stellt einen weiteren Vorteil dar. Somit müssen diese Öle erst unmittelbar vor dem Lackierprozess entfernt werden, sodass die Karosse während ihrer aus einer Vielzahl von Einzelschritten bestehenden Herstellung vor Korrosion geschützt ist.
Ein weiterer Vorteil ist, dass der Prozess der Gelierung stufenweise erfolgen kann. So kann durch eine, bei geringerer Temperatur erfolgenden Vorgelierung das pastöse Plastisol soweit verfestigt werden, dass es bei den vor der Lackierung zwingend erforderlichen Waschprozessen zur Entfernung u. a. der Korrosionsschutz- und Ziehölen nicht mit ausgewaschen wird.
Nachteile liegen z. B. in der schon erwähnten begrenzten Temperaturbeständigkeit, einer begrenzten Festigkeit, der Freisetzung von korrosiver Salzsäure bei Überhitzung z. B. beim Punktschweißen durch das PVC-Plastisol oder in seiner unmittelbaren Nähe, der Gefahr des langsamen Ausschwitzens der Weichmacher während der Lebensdauer des Fahrzeugs, was zu einer gewissen Versprödung des Plastisols führt und auch zu einer Innenraumbelastung des Fahrzeuginnenraums mit als gesundheitlich bedenklich eingestuften Weichmachern führen kann sowie in der allgemeinen „PVC-Problematik“[8] beim Fahrzeugrecycling. Nichtsdestotrotz konnten PVC-freie Alternativen, sofern sie keine weiteren Vorteile zeigen, die PVC-Plastisole aufgrund ihrer deutlich höheren Materialkosten nicht verdrängen. Die in den Achtzigerjahren des letzten Jahrhunderts begonnene Entwicklung von chemisch durch Wärmebeaufschlagung härtenden Klebstoffen hat neue Anwendungsgebiete für das Kleben im Karosseriebau eröffnet. Zum Teil haben diese Klebstoffe auch aufgrund ihres verbesserten Eigenschaftsprofils die meist preisgünstigeren Plastisole in einigen Anwendungen ersetzt. Diese Systeme und ihre Anwendungen werden weiter unten bei der Beschreibung der chemisch härtenden Klebstoffe näher beschrieben.
Chemisch härtende Klebstoffe
Im Gegensatz zu den oben beschriebenen physikalisch abbindenden Klebstoffen, bei denen die Polymerketten in dem vom Klebstoffhersteller gelieferten Klebstoff bereits in ihrer endgültigen Zusammensetzung und Größe vorliegen, ist dies bei den chemisch härtenden Klebstoffen nicht der Fall. Das den gehärteten Klebstoffen ausmachende Polymer wird erst bei der Härtung durch eine chemische Reaktion aus kleineren Bausteinen, den sogenannten Monomeren oder Präpolymeren gebildet.
Durch geeignete Maßnahmen muss sichergestellt werden, dass die Härtung erst in der Klebfuge und nicht schon vorzeitig im Liefergebinde erfolgt. Im Fall der Zweikomponenten-Klebstoffe, kurz als 2K-Klebstoffe bezeichnet erfolgt dies, indem sich die Grundkomponenten (häufig als Harz und Härter bezeichnet) in zwei getrennten Behältern befinden und erst kurz vor dem Auftrag auf das zu klebende Bauteil im korrekten Verhältnis miteinander vermischt werden. Durch die fortschreitende Reaktion nimmt die Viskosität der Mischung stetig zu und führt nach Überschreiten der „Topfzeit“, die auch als „offene Zeit“ bezeichnet wird dazu, dass die zu verbindenden Oberflächen nicht mehr ausreichend benetzt werden. Dies bedingt, dass bei der Verwendung von 2K-Klebstoffe, das Dosieren und Mischen der Klebstoffkomponenten, das Applizieren auf das Bauteil und das Fügen innerhalb der Topfzeit erfolgen muss. Nach dem Fügen der miteinander zu verklebenden Bauteile folgt die Aushärtezeit, in der sich die Endfestigkeit der Klebung aufbaut. Sowohl die Topfzeit, als auch die Aushärtezeit wird stark von äußeren Einflüssen, besonders der Temperatur, beeinflusst. Eine Temperaturerhöhung führt zu einer beschleunigten Härtung und oft auch zu einer höheren Festigkeit, während niedrigere Temperaturen die Topfzeit, aber auch die Härtezeit verlängern oder die Härtungsreaktion sogar stoppen. In diesem Zusammenhang sei darauf hingewiesen, dass die von den jeweiligen Klebstoffherstellern in den Datenblättern gegebenen Hinweise zum Mischungsverhältnis und den Verarbeitungs- und Härtungsbedingungen unbedingt einzuhalten sind. Abweichungen können zu Fehlverklebungen führen. Auch an die Qualität der Mischung werden hohe Anforderungen gestellt. Häufig werden die 2K-Klebstoffe aus speziellen Doppelkartuschen mit statischen Mischern verarbeitet. Die Doppelkartusche stellt sicher, dass das Mischungsverhältnis eingehalten wird und der statische Mischer gewährleistet die homogene Durchmischung. Bei Serienanwendungen mit einem entsprechend hohen Klebstoffbedarf kommen spezielle Dosier- und Mischanlagen, die eine Verarbeitung aus Großgebinden ermöglichen zum Einsatz.
Im Gegensatz dazu liegen die Einkomponenten-Klebstoffe, kurz 1K-Klebstoffe bereits gebrauchsfertig gemischt vor und der Klebstoff kann direkt verwendet werden. Hier verhindert eine chemische Blockierung die vorzeitige Härtung oder die Härtungsreaktion erfordert die Zuführung von weiteren Stoffen. Durch besondere Bedingungen, z. B. Einwirkung von Wärme, Licht einer bestimmten Wellenlänge, dem Zutritt von Luftfeuchtigkeit oder von Metallionen in Kombination mit der Abwesenheit von Sauerstoff, wird die Blockierung aufgehoben und die Verfestigungsreaktion gestartet. Um eine Vorzeitige Verfestigung im Liefergebinde zu verhindern werden entsprechende Bedingungen an die Verpackung aber auch an Transport und Lagerung gestellt.
Unabhängig davon, ob es sich um 2K- oder 1K-Klebstoffe handelt, ist die Härtungsreaktion exotherm, d. h. mit der Freisetzung von Wärme verbunden. Daher sollten bei 2K-Klebstoffen die vom Hersteller im technischen Datenblatt angegebenen Klebstoffmengen unter keinen Umständen überschritten werden. Zu große Mengen verkürzen die Topfzeit und können zu einer Überhitzung, verbunden mit der Freisetzung von gasförmigen Gefahrstoffen bis hin zur Selbstentzündung führen. Entsprechend gilt dies auch für 1K-Klebstoffe. Vor dem Hintergrund, dass gehärtete Klebstoffe in der Regel keine Gefahrstoffe darstellen, also nicht als gefährlicher Abfall zu entsorgen sind, kam es in der Vergangenheit bei der Härtung von größeren Restmengen auch von heißhärtenden 1K-Klebstoffen zu Überhitzungen bis hin zu Bränden mit Gefahrstofffreisetzung.
Auch wenn die Unterscheidung nach der Art der chemischen Reaktion – Polymerisation, Polykondensation oder Polyaddition – für den Anwender auf den ersten Blick meist nur von geringerer Bedeutung erscheint, gibt deren Kenntnis doch einige wichtige Hinweise. So sind die bei Härtung von Polyadditionsklebstoffen entstehenden Polymere durch eine abwechselnde Anordnung von Harz- und Härterbausteinen gekennzeichnet, wobei das stöchiometrische Verhältnis der reaktiven Gruppen in den Ausgangsmonomeren oder -prepolymeren das Mischungsverhältnis bestimmt. Es muss für jede reaktive Gruppe des Harzes nicht nur genau eine des Härters zur Verfügung stehen, sondern diese müssen auch miteinander reagieren können, d. h. sich nahe genug zueinander befinden. Das Mischungsverhältnis muss exakt eingehalten werden und genauso ist eine gute, homogene Durchmischung erforderlich. Eventuell nicht in das Klebstoffpolymer eingebaute überschüssige Harz- oder Härterbausteine wirken wie ein Weichmacher und haben einen nachteiligen Einfluss auf die mechanischen Eigenschaften des gehärteten Klebstoffs.
Bei Polykondensationsklebstoff ist, wie auch bei den Polyadditionsklebstoffen für jede reaktive Gruppe der Harzbausteine eine des Härters erforderlich, sodass auch hier Mischungsverhältnis und Mischgüte von hoher Bedeutung sind. Hinzu kommt, dass bei der Härtung Nebenprodukte freigesetzt werden. Diese können je nach ihrer Art die Fügeteiloberflächen angreifen oder zum Aufschäumen der Klebstoffschicht führen.
Anders als bei den Polyadditions- oder Polykondensationsklebstoffen wird bei Polymerisationsklebstoffen die Härtung durch Härtermoleküle gestartet und läuft dann ohne weiteren Härterbedarf in Form einer Kettenreaktion ab. Somit sind die an die Einhaltung des Mischungsverhältnisses und die Mischqualität gestellten Anforderungen geringer. So sind spezielle, als No-Mix-Systeme bezeichnete 2K-Polymerisationsklebstoffe auf dem Markt, die ohne Durchmischung der Komponenten verarbeitet werden können. Die Harzkomponente wird auf das eine und die Härterkomponente auf das andere Fügeteil aufgetragen. Die beim Fügen erfolgende Durchmischung ist ausreichend die Härtungsreaktion zu starten und reproduzierbare Ergebnisse zu erzielen.
Polyadditionsklebstoffe
Wichtige Vertreter aus der Gruppe der durch eine Polyadditionsreaktion härtenden Klebstoffe sind die Epoxidharz-Klebstoffe (kurz Epoxi-Klebstoffe), die Polyurethan-Klebstoffe sowie einige Silikon-Klebstoffe
Epoxidharz-Klebstoffe

Die Fähigkeit von Stoffen mit reaktiven Wasserstoffatomen, hierzu zählen z. B. Amine, Amide, Carbonsäureanhydride und Merkaptane mit der Epoxidgruppe von Epoxidharzen unter Öffnung des gespannten 3-Rings zu reagieren ist die Basis der Epoxidklebstoffchemie. In den meisten Fällen werden auf Bisphenol-A basierende Epoxidharze, die sog. Bisphenol-A-diglycidylether eingesetzt. Bei einer geringen Zahl von sich wiederholenden Moleküleinheiten (n = 0 bis 2) handelt es sich um eine viskose, klare Flüssigkeit (Flüssigharz) bei mehr Moleküleinheiten (n = 2 bis 30) um farblose Feststoffe (Festharz). Ein bei Epoxidharz-Klebstoffen weit verbreitetes flüssiges Bisphenol A Harz hat ein mittleres n von 0,1. Der Reaktionsverlauf eines 2K-Epoxidharz-Klebstoff ist auf der Folie 23 der Informationsserie des Fonds der Chemischen Industrie – Kleben/Klebstoffe beschrieben[9][10]
Bei gehärteten Epoxidharz-Klebstoffen handelt es sich immer um Duromere, was ihre hohen Festigkeiten ihre eher geringe Flexibilität, sowie ihre relativ gute Beständigkeit gegen Feuchtigkeit, viele Chemikalien und Umwelteinflüsse erklärt.
Die Eigenschaften von Epoxidharz-Klebstoffen werden im Wesentlichen durch die verwendeten Härter bestimmt. Durch Ersatz zumindest eines Teils des Bisphenol-A-basierenden Harzes durch andere Epoxidharze können zusätzlich Eigenschaften des gehärteten Klebstoffs, wie z. B. die Beständigkeit gegen hohe Temperaturen und gegen Chemikalien, die Flexibilität und ihre elektrische Eigenschaften weiter an die jeweiligen Anforderungen angepasst werden. Als weitere Rezepturbestandteile kommen verschiedene
· Füllstoffe zur Einstellung des Fließverhaltens bei der Anwendung, zur Verringerung des Härtungsschrumpfs, zur Erhöhung der Wärme- oder elektrischen Leitfähigkeit,
· Haftvermittler zur Verbesserung der Haftung zu bestimmten Werkstoffen und
· reaktive oder nicht reaktive Verdünner zur Reduktion der Viskosität
zum Einsatz. Eine Verringerung des spröden Charakters kann durch den Einsatz von elastifizierenden Härtern, entsprechend modifizierter Epoxidharze oder durch den Zusatz flexibilisierend wirkende Bestandteile erreicht werden. Eine weitere Verbesserung, die es erlaubt den Klebstoff sogar in crashgefährdeten Bereichen in Automobilkarosserien einzusetzen wird durch ein zweistufiges System erreicht. Kleine zähelastische Partikel in der Größe von etwa 500–2000 nm sind meist reaktiv in den Klebstoff eingebunden. Bei Einwirken einer schlagartigen Belastung werden die Energiedichte und das Risswachstum verringert und Energie absorbiert. Im Crashfall kommt es somit nicht zu einem schlagartigen Versagen der Klebung, sondern es wird die Energieaufnahme durch Blechverformung unterstützt, was letztendlich zur Sicherheit der Fahrzeuginsassen beiträgt.[11][12]
Epoxidharz-Klebstoffe sind sowohl als 2K- als auch als 1K-Systeme erhältlich. Einige 2K-Systeme härten bei Raumtemperatur relativ schnell in wenig Minuten vollständig aus, andere benötigen hierfür mehrere Stunden bis hin zu einigen Tagen. Eine Beschleunigung der Härtung bei meist gleichzeitiger Erhöhung der Festigkeit wird durch Erwärmung erreicht, wobei jedoch die Vorgaben des jeweiligen Herstellers unbedingt einzuhalten sind. Bei 1K-Klebstoffen werden Härter verwendet, die bei Raumtemperatur nicht oder nur äußerst langsam mit den Epoxidgruppen des Harzes reagieren. Ein weit verbreiteter Härter ist das Dicyandiamid. Hierbei handelt es sich um einen bei Raumtemperatur in Epoxidharzen praktisch unlöslichen Feststoff. Erst bei erhöhter Temperatur oberhalb von gut 100 °C beginnt er sich im Epoxidharz zu lösen und die Härtungsreaktion beginnt. Übliche Härtungstemperaturen liegen bei 160–200 °C. Durch spezielle Additive kann die Härtungstemperatur reduziert werden. Zu beachten ist hierbei jedoch die damit verbundene Verringerung der Lagerfähigkeit bei Raumtemperatur, sodass ggf. eine gekühlte Lagerung erforderlich wird.
Anwendungsgebiete Epoxidharz-Klebstoffe mit ihren durchweg hohen Festigkeiten, relativ hohen Glasübergangstemperaturen und der sehr guten Dauerbeständigkeit werden häufig für sogenannte strukturelle Klebungen, z. B. im Fahrzeugbau, bei der Herstellung von Rotorblätter von Windkraftanlagen aber u. a. auch für Anwendungen in der Elektronikindustrie verwendet. Je nach Formulierung sind Epoxidharz-Klebstoffe sowohl für Klebverbindungen an sehr großen Bauteilen, wie z. B. bei der Verklebung der zwei Halbschalen von Rotorblättern für Windkraftanlagen – hier werden abhängig von der Rotorblattlänge mehrere hundert Kilogramm Klebstoff pro Rotorblatt benötigt – als auch an kleinsten Bauteilen mit einem Klebstoffbedarf von wenigen Milli- oder Mikrogramm, wie z. B. der Chipkartenherstellung, oder dem Kleben von Ferriten bei der Herstellung von Elektromotoren in der Elektronikindustrie geeignet. Es können sowohl hochautomatisierte Großserienanwendungen mit kurzen Taktzeiten, als auch manuelle Kleinserien mit langen Taktzeiten realisiert werden. Im modernen Automobilbau haben Epoxidharz-Klebstoffe wesentlich dazu beigetragen, dass die gesetzlichen Vorgaben zur Verringerung der CO2-Emission eingehalten erreicht werden konnten. So werden die hohen Spannungsspitzen einer reinen Punktschweißverbindung beim Punktschweißkleben durch den, zwischen den Schweißpunkten befindlichen zusätzlichen Klebstoff nivelliert, was die Verwendung von dünneren Blechen erlaubt. Allgemein wird durch Kleben die Bauteilsteifigkeit erhöht, was ebenfalls die Verwendung dünnerer Bleche, wie weiter oben bereits erwähnt auch von crashgefährdeten Bauteilen ermöglicht. Ebenso sind Verbindungen zwischen verschiedenartigen Metallen oder Stahlsorten, die aufgrund ihres Gefügeaufbaus nicht geschweißt werden können durch Kleben realisierbar. Der heutige automobile Leichtbau wäre ohne die Verwendung von Klebstoffen und insbesondere der Epoxidharz-Klebstoffe nicht möglich.[12]
Arbeitssicherheit Bei der Verwendung von Epoxidharz-Klebstoffen ist zu berücksichtigen, dass diese Systeme im nicht gehärteten Zustand in der Regel Gefahrstoffe gemäß der Europäischen CLP-Verordnung (EG) Nr. 1272/2008 und die von den jeweiligen Klebstoffherstellern in den Sicherheitsdatenblättern beschriebenen Arbeits- und Umweltschutzmaßnahmen beachtet werden müssen. Aufgrund seiner augen- und hautreizenden sowie sensibilisierenden Epoxidharz Wirkung ist jeder Hautkontakt grundsätzlich zu vermeiden und die langfristige, schädliche Wirkung auf Wasserorganismen erfordert einen entsprechenden umweltbewussten Umgang. Auch wenn krebserregende Amine heute durch andere Härter ersetzt worden sind, verursachen die meisten als Härter verwendeten Amine bei Augenkontakt schwere Augenreizungen und können ebenfalls bei Hautkontakt entsprechende Reizungen verursachen und sensibilisierend wirken.
Polyurethan-Klebstoffe (PUR)
Auf Basis der Polyurethanchemie lassen sich sowohl 1K- als 2K-Klebstoffe herstellen. Die Grundlage der zur Härtung der Klebstoffe führenden Reaktion ist die Fähigkeit von Isocyanaten, also Stoffen, die durch die –NCO Gruppe gekennzeichnet sind, mit wasserstoffaktiven Verbindungen, dies sind im Wesentlichen Stoffe mit Hydroxy- (-OH) oder Amingruppen (NH-), oder mit sich selbst zu reagieren.
Zu der Gruppe der 1K-Polyurethan-Klebstoffe gehören, wie auch bei den 1K-Epoxidharz-Klebstoffen, solche, die Wärme zur Härtung, also zur Aktivierung des im Klebstoff bereits enthaltenen blockierten Härters benötigen. Diese enthalten als reaktive Bestandteile Präpolymere mit endständigen OH-Gruppen und blockierte Isocyanate. Nachdem durch Wärmezufuhr die Blockierung der Isocyanatgruppen aufgehoben wurde erfolgt deren Reaktion mit den OH-Gruppen des Präpolymers.
Darüber hinaus gibt es feuchtigkeitsvernetzende 1K-Systeme, die als reaktiven Bestandteil ein nicht flüchtiges Polyurethan-Präpolymer mit Isocyanat-Endgruppen enthalten. Die Härtung erfolgt durch eine Reaktion der Isocyanatgruppen mit Feuchtigkeit, d. h. Wasser aus der Luft oder den Fügeteilen. Um eine vorzeitige Härtung zu verhindern müssen diese Produkte bei der Lagerung durch eine entsprechende Verpackung vor dem Zutritt von Feuchtigkeit geschützt werden. Nach dem Auftrag des Klebstoffs auf das Fügeteil reagiert in einem ersten Schritt Feuchtigkeit aus der Umgebungsluft oder den Fügeteilen in einer Polykondensationsreaktion unter Abspaltung von geringen Mengen an CO2 zu einem Amin. Erst im zweiten Schritt führt die Polyadditionsreaktion des entstandenen Amins mit weiterem Isocyanatgruppen unter Bildung von Harnstoffgruppen zur Härtung des Klebstoffs.
Die Härtung dieser Systeme läuft im Temperaturbereich von etwa 5 bis 40 °C ab, wobei eine relative Luftfeuchtigkeit von 40 bis 70 % erforderlich ist. Da die Härtung von außen nach innen erfolgt, d. h. es bildet sich zunächst an der Klebstoffoberfläche eine Haut, wird der Zeitraum, innerhalb der der Fügevorgang abgeschlossen sein muss, durch die sogenannte Hautbildezeit beschränkt. Erfolgt das Fügen später, ist die zur Ausbildung einer guten Haftung erforderliche Benetzung des zweiten Fügeteils nicht mehr gegeben. Weiterhin ist zu beachten, dass die Geschwindigkeit der Härtung von anfangs einigen Millimetern pro Tag mit zunehmender Dicke der Haut abnimmt und gegebenenfalls sogar zum Stillstand kommt. Um trotzdem großflächige Klebungen von feuchtigkeitsundurchlässigen Fügeteilen zu ermöglichen oder Klebungen bei zu geringer relative Luftfeuchtigkeit durchführen zu können, sind sogenannte „Booster-Systeme“ auf dem Markt. Hier wird, sozusagen als zweite Komponente ein feuchtigkeitshaltiges Gel zugeführt und über einen statischen Mischer mit dem eigentlichen Klebstoff vermischt. Die Härtung erfolgt dann gleichmäßig über den gesamten Querschnitt der Klebschicht.
Diese Klebstoffe sind nach der Härtung gummielastisch-flexibel und kommen zum Einsatz, wenn Materialien mit stark unterschiedlichem Last-Temperaturausdehnungsverhalten miteinander verbunden werden müssen. Beispiele sind das Einkleben der Scheiben im Automobilbau oder die Verbindung von glasfaserverstärkten Kunststoffen auf Metallträger z. B. bei der Herstellung von Thermo-LKW.
Bei einer dritten Variante, den reaktiven Polyurethan-Schmelzklebstoffen, wird die Vernetzung von Isocyanatgruppen enthaltenden, bei Raumtemperatur festen, thermoplastischen Präpolymeren mit Luftfeuchtigkeit genutzt um über die nach dem Fügen, des zunächst verflüssigten und nach dem Fügen erstarrenden Klebstoffs diesen in einen nicht mehr schmelzbaren Elastomeren oder Duroplasten zu überführen. Durch diese Nachvernetzung wird die Beständigkeit der Klebung gegen höhere Temperaturen und verschiedene Medien deutlich verbessert. Diese Klebstoffe zeigen also den Vorteil einer schnellen Anfangsfestigkeit der Schmelzklebstoffe, eliminieren aber den Nachteil, der durch den Erweichungsbereich der Klebstoffe begrenzten Wärmebeständigkeit.
Wie bei 2K-Klebstoffen allgemein üblich wird auch bei den 2K-Polyurethan-Klebstoffen die Härtung durch das Zusammengeben der beiden Komponenten, dem Harz (Gemisch verschiedener Polyole oder Polyurethan-Präpolymerer mit endständigen OH-Gruppen) und dem Härter (Isocyanat), gestartet. Neben den jeweils reaktiven Bestandteilen können die beiden Komponenten
· Füllstoffe zur Einstellung des Fließverhaltens bei der Applikation, Verringerung des Härtungsschrumpfs, Erhöhung der Wärmeleitfähigkeit oder elektrischen Leitfähigkeit,
· Haftvermittler zur Verbesserung der Haftung zu bestimmten Werkstoffen und
· Katalysatoren zur Einstellung der Härtungsgeschwindigkeit enthalten. Aufgrund der Vielfalt an für die Formulierung von 2K-Polyurethan-Klebstoffen geeigneten Rohstoffen und hier insbesondere der Polyole sind Klebstoffe mit unterschiedlichen mechanischen Eigenschaften, von niedrigmodulig, hoch elastisch bis hin zu hochmodulig aber trotzdem zähelastisch verfügbar.
Anwendungsgebiete
Aufgrund der in weiten Bereichen durch die Klebstoffrezeptur bestimmten mechanischen Eigenschaften der Polyurethan-Klebstoffe werden Vertreter dieser Klebstoffklasse in den verschiedensten Industrien für unterschiedliche Anwendungen eingesetzt. Die elastischen feuchtigkeitshärtenden Systeme werden vielfach als Dichtmassen eingesetzt, ein Vorteil gegenüber den Silikondichtmassen besteht darin, dass sie überstreichbar sind. Ein weiteres sehr weites Einsatzgebiet, sowohl für die feuchtigkeitshärtenden 1K-Klebstoffe, als auch für die niedrigmoduligen, elastische 2K-Systeme ist das sogenannte elastische Kleben.[13][14][15]
Die elastischen Eigenschaften dieser Klebstoffe werden zur Schwingungsdämpfung oder zum Ausgleich von erzwungenen Relativbewegungen der Fügeteile zueinander, zum Beispiel aufgrund eines unterschiedlichen thermischen Ausdehnungsverhaltens oder wechselnder mechanischer Belastungen in einer Vielzahl von Anwendungen genutzt. So wurde schon 1969 im VW-Porsche 914 Front- und Heckscheiben nicht mehr über eine Gummidichtung befestigt, sondern in die Karosserie eingeklebt und liefert so einen signifikanten Beitrag zu Steifigkeit; heute ist dies Stand der Technik. Nur ausreichend elastische Klebstoffe sind in der Lage die im Fahrbetrieb auftretenden mechanischen und auch die aufgrund des unterschiedlichen thermischen Ausdehnungsverhaltens von Scheibe und Karosserie auftretenden Belastungen zu kompensieren und somit Glasbruch zu verhindern. Weitere Anwendungen findet man im Bus-, Boots- und Schienenfahrzeugbau, bei der Herstellung von Kühlcontainern, in der Bauindustrie und der Herstellung „weißer Ware“, wie zum Beispiel Waschmaschinen, Kühlschränken und Herde.[13] Im Tiefbau werden feuchtigkeitshärtende Systeme zur Stabilisierung von brüchigen Gesteinsformationen durch Bohrlöcher in die betroffenen Gesteinsschichten injiziert.
Feuchtigkeitsnachvernetzende Polyurethan Schmelzklebstoffe werden unter anderen
- im graphischen Gewerbe zum Binden von Büchern,
- in der Verpackungsindustrie zur Herstellung von Faltschachteln,
- in der Textilindustrie zur Herstellung von Funktionstextilien,
- bei der Möbelherstellung für Kantenklebungen, die Herstellung von 3D-Möbelfronten und zur, Fußbodenherstellung,
- in der Automobilindustrie zur Flächenkaschierung von Innenausstattungsteilen,
- in der Bauindustrie zur Ummantelung von Fensterprofilen und der Herstellung von Sandwichelementen
verwendet.
2K-Polyurethan-Klebstoffe kommen überall dort zum Einsatz wo elastische, aber im Vergleich zu den 1K-feuchtigkeitshärtenden Polyurethan-Klebstoffe eine schnellere Härtung erforderlich ist, oder wo höhere Festigkeiten bei gleichzeitig einer im Vergleich zu den Epoxidklebstoffen höheren Dehnfähigkeit gefordert ist. Beispiele findet man im Automobilbau bei der Herstellung von Kunststoff-Anbauteilen wie Heckdeckel, Kotflügeln, Stoßfängern und Spoilern[16] sowie mit dem Aufkleben der Streuscheibe auf das Gehäuse bei der Herstellung von Automobil-Scheinwerfern. Auch in der Elektronikindustrie, bei der Herstellung von Filtern und in der Hausgeräteindustrie werden 2K-Polyurethan-Klebstoffe verwendet.
Arbeitssicherheit
Aus Gründen der Arbeitssicherheit wird für die Herstellung von Polyurethan-Klebstoffen als Isocyanat meist Methylendiphenylisocyanat (MDI) oder Präpolymere auf Basis MDI verwendet. MDI hat wie auch andere monomere Isocyanate aufgrund seines nicht zu unterschätzenden gesundheitsgefährdenden Potentials mit derzeit 0,005 ppm einen sehr geringen Arbeitsplatzgrenzwert. Aufgrund seines im Vergleich zu anderen monomeren Isocyanaten, wie Isophorondiisocyanat (IPDI), Toluylendiisocyanat (TDI) oder Hexamethylendiisocyanat (HDI) deutlich geringeren Dampfdrucks kann der Arbeitsplatzgrenzwert, sofern der Klebstoff nicht erwärmt wird, weder erreicht noch überschritten werden. Wird der Klebstoff jedoch, wie bei reaktiven Polyurethan-Schmelzklebstoffen warm oder im Sprühverfahren verarbeitet ist unbedingt eine effektive Absaugung vorzusehen.[17][18][19][20]
Polykondensationsklebstoffe
Wichtige Vertreter aus der Gruppe der durch eine Polykondensationsreaktion härtenden Klebstoffe sind die Phenolharz-Klebstoffe, die feuchtigkeitsvernetzenden Silikon-Klebstoffe sowie die recht neue Gruppe der Klebstoffe aus Basis von silan-modifizierten Polymeren, wie z. B. die MS-Polymeren Klebstoffe
Phenol-Formaldehydharz-Klebstoffe[21][22]
Bei den Phenolharzen handelt es sich um Polymere, die auf den vielfältigen Polykondensationsreaktionen zwischen Phenolen und Aldehyden, insbesondere Formaldehyd aufbauen. Von technischer Bedeutung sind die Phenol-Formaldehydharze, die je nach dem molaren Verhältnis von Aldehyd/Phenol bei der Vorkondensation als Resolharze (>1) oder Novolakharze (<1) bezeichnet werden. Resolharze sind anfangs schmelzbare und lösliche Polymere, die durch Erwärmung zeit- temperatur- und pH-Wertabhängig zu Duromeren vernetzt werden können. Novolokharze sind ebenfalls schmelzbar und löslich, benötigen zu einer weiteren Vernetzung jedoch neben Temperatur zusätzliches Formaldehyd und einen Vernetzer. Häufig wird hierfür Paraformaldehyd und Hexamethylentetramin (das sog. „Hexa“) verwendet. Reine Phenol-Formaldehydharze sind durch eine hohe Sprödigkeit gekennzeichnet und mit ihnen hergestellte Klebungen sind somit gegen Schälbelastungen recht empfindlich. Daher werden sie häufig durch Co- bzw. Mischpolymerisation mit thermoplastische Polymere ergebenden Monomeren modifiziert. Andererseits bieten sie aufgrund der hohen Vernetzungsdichte eine hohe Temperatur- und eine gute Chemikalienbeständigkeit.
Als Klebstoff werden Resol- und Novolakharze als Lösung, Pulver oder Folie verwendet. In der Klebfuge wird die quasi unterbrochene Kondensationsreaktion zum unlöslichen und nicht mehr schmelzbaren, hochvernetzen Polymer durch Temperaturerhöhung auf ca. 140 bis 180 °C fortgesetzt. Das bei der Härtung freigesetzte Wasser liegt aufgrund der hohen Härtungstemperatur gasförmig vor. Um ein Aufschäumen des Klebstoffs zu verhindern erfolgt die Härtung von Phenolharzklebstoffen üblicherweise unter Druck.
Anwendungsgebiete
Die Klebstoffe haben eine gute Temperaturbeständigkeit, weshalb sie besonders für temperaturbelastete Metall-Klebungen genutzt werden. Der gute Ruf der Phenol-Formaldehyd Klebstoffe für Metallklebungen geht auf ihre Verwendung im Flugzeugbau schon in den 1940er Jahren zurück. Trotz des vergleichbar hohen Fertigungsaufwands (Fixieren der Fügeteile bis zur Härtung, Härtung unter Druck im Autoklaven etc.) wird diese Klebstoffgruppe bis heute u. a. wegen ihrer guten Langzeitbeständigkeit, auch gegen korrosive Einflüsse im Flugzeugbau für Metallklebungen verwendet.
Weitere große Einsatzgebiete sind die Herstellung von Schleifpapieren und Reibbelägen, z. B. für die Verwendung in Automatikgetrieben. Als Bindemittel für die Fixierung der Schleifpartikel bzw. der Reibmittel auf einem Träger werden häufig Phenol-Formaldehyd-Harze verwendet. Die Reibbeläge werden bei der Fertigung von Kupplungen, Automatikgetrieben und Bremsbelägen mit Phenol-Formaldehyd Klebstoffen auf Metallträger geklebt. Die metallischen Träger bestehen heute, zur Vermeidung von Quietschgeräuschen beim Bremsen aus mehreren dünnen, mittels Phenolharzklebstoff miteinander verbundenen Blechen. Der Klebstoff bewirkt über seine dämpfende Wirkung eine akustische Entkopplung, sodass Schwingungen nicht mehr zu einem Quietschen führen.
Phenol-Formaldehydharz Klebstoffe werden auch zur verstärkenden Imprägnation von Filterpapieren z. B. für die Verwendung in Ölfiltern eingesetzt und verhindern ein Reißen der Filterpapiere unter den im Betrieb auftretenden hohen Temperaturen und Drücken. In der Elektronik werden Phenol-Formaldehyd Klebstoffe u. a. zum Kaschieren bei der Leiterplattenherstellung und zum Kaschieren des Trägermaterials mit Kupferfolien verwendet. Hohe Ansprüche werden an die sogenannten Haftvermittlerklebstoffe gestellt. Einerseits müssen sie neben den guten klebtechnischen auch gute elektrische Eigenschaften aufweisen und andererseits durch einen oxidativen Angriff einer Mikroaufrauhung zugänglich sein, die wiederum eine deutliche Verbesserung der Haftfestigkeit der abgeschiedenen Kupferschicht auf dem Träger zur Folge hat.[23]
Arbeitssicherheit Aus Sicht der Arbeitssicherheit ist neben den jeweiligen Lösemitteln, hier wird neben dem unkritischen Lösemittel Wasser auch Ethanol auch häufig Methanol verwendet der Gehalt freiem Phenol und Formaldehyd von Bedeutung und führen zu entsprechenden Kennzeichnungen der Klebstoffe gemäß Verordnung (EG) Nr. 1272/2008 (CLP). Für die geklebten Produkte, insbesondere aus der Möbelindustrie sind zudem die Restmengen an monomeren Formaldehyd im gehärteten Klebstoff von Bedeutung. Um Belastungen der Kunden durch Formaldehydausdunstungen zu vermeiden gelten hier strenge Grenzwerte.
Silikone[24][25]
Silikon-Polymere nehmen eine gewisse Sonderstellung ein, da ihr Molekülgerüst im Gegensatz zu den anderen hier beschriebenen Klebstoffen nicht aus Kohlenstoffketten aufgebaut ist, sondern sich in der Hauptkette Silicium- und Sauerstoff-Atome abwechseln. Nur in den Seitenketten tragen diese Polymere aus Kohlenstoffketten aufgebaute organische Strukturen. Hierauf beruhen die besonderen Eigenschaften der Silikone. So bewirkt die hohe Kettenbeweglichkeit der Silikonpolymere die hohe Elastizität der Silikone die bis hinab zu −70 bis −90 °C erhalten bleibt. Aufgrund der im Vergleich zur Kohlenstoff-Kohlenstoff-Bindung höheren Bindungsenergie der Silizium-Sauerstoff-Bindung weisen Silikone eine hohe Temperaturbeständigkeit auf. So sind Silikone dauerhaft bis zu ca. 200 °C beständig, kurzfristig sogar bis zu 300 °C. Ein weiterer Vorteil ist die hohe Beständigkeit gegen UV-Strahlung. Unter dem Einfluss von UV-Strahlung entsteht aus Luftsauerstoff (O2) partiell aktiver Sauerstoff, d. h. Ozon (O3) und radikalischer Sauerstoff (O), die die Kohlenstoffketten organischer Klebstoffe an Fehlstellen angreift, den Kohlenstoff oxidiert und so die Kette zerstört. Ein derartiger Angriff ist bei den Silicium-Sauerstoff-Ketten der Silikone nicht möglich, da das Silizium bereits oxidiert vorliegt. Auch gegenüber anderen chemisch aggressiven Stoffen sind Silikone recht stabil und zeigen eine gute Feuchtigkeits- und Witterungsbeständigkeit.
Begrenzt ist jedoch die mit Silikonen erreichbare mechanische Belastbarkeit, so liegen die mit Silikonklebstoffen erreichbaren Zugscherfestigkeiten[26] in der Regel bei maximal 1 MPa. Ein weiterer Nachteil ist, dass sie sich aufgrund ihrer sehr geringen Oberflächenspannung weder lackieren oder beschichten lassen und nachfolgende Klebungen in ihrem Umfeld deutlich erschweren bzw. unmöglich machen. Außerdem sind sie, abhängig vom bei Härtung freiwerdenden Kondensationsprodukt, anfällig gegen Schimmelbefall.
Silikonklebstoffe werden sowohl als 1K-, als auch als 2K-Systeme angeboten. Beide Systeme beruhen auf Polyorgano-, meist Polydimethylsiloxanen und härten durch eine Polykondensation aus, die 1K-Systeme durch Feuchtigkeitszutritt, die 2K-Systeme durch Reaktion mit Kieselsäureestern.
Bei den gebrauchsfertigen 1K-feuchtigkeitshärtenden Silikonen (RTV-1) sind die endständigen Hydroxygruppen der Polydimethylsiloxane durch einen sogenannten Vernetzer blockiert. Bei Zutritt von Feuchtigkeit wird diese Blockierung durch Hydrolyse unter Abspaltung eines Kondensationsproduktes aufgehoben, was die weitere Vernetzung der Siloxanketten untereinander ermöglicht. Je nach der Art des zur Blockierung der Hydroxygruppen verwendeten Vernetzers spricht man von sauer, alkalisch oder neutral vernetzenden Systemen.
Am bekanntesten sind die sauer-vernetzenden Acetatsysteme, die beim Aushärten Essigsäure abspalten. Sie zeichnen sich durch eine gute Haftung zu mineralischen Untergründen wie Glas, Email, Porzellan und auch eloxiertem Aluminium aus und werden für Klebungen und Abdichtungen dieser Werkstoffe z. B. beim Innenausbau von Häusern und insbesondere im Sanitärbereich zur Herstellung von Silikonfugen verwendet.
Bei der Verwendung dieser Systeme für Metallklebungen ist die mögliche Gefahr einer Säurekorrosion, für Kunststoffklebungen die der Spannungsrisskorrosion durch die entstehende Essigsäure zu berücksichtigen.
Für Klebungen von Beton, Putz, Mauerwerk und Metallen eignen sich die alkalisch vernetzenden Systeme. Die bei der Härtung frei werdenden aminischen Verbindungen sind für den bei der Härtung auftretenden charakteristischen, fischartigen Geruch und die Gefahr einer Verfärbung verantwortlich. Obwohl Amin- bzw. Aminoxysysteme auch bei kalter Witterung noch nennenswert durchhärten und zu äußerst stabilen Produkten führen, haben sie, nicht zuletzt aufgrund des unangenehmen Geruchs an Bedeutung verloren.
Korrosion oder Probleme durch Verfärbung treten bei den neutral vernetzenden Systemen nicht auf. Oximsysteme waren lange der Begriff für neutral vernetzende Silikone. Auf Grund der Toxizität der während der Aushärtung frei werdenden Abspaltungsprodukte (2-Butanonoxim (MEKO), 2-Propanonoxim (DMKO) und/oder 2-Pentanonoxim (MPKO)) ist die Verwendung von Oximsilikonen inzwischen als kritisch anzusehen. Unter anderem seitens der Berufsgenossenschaft der Bauwirtschaft (BG BAU) wird daher empfohlen auf andere Silikonsysteme oder andere Technologien zurückzugreifen und die Verwendung von Oximsilikonen zu vermeiden.[27] Estersysteme sind eine der jüngeren Entwicklungen auf dem Gebiet der neutral vernetzenden Silikone. Estersilikone setzen im Gegensatz zu Oximsilikonen keine toxischen Abspaltungsprodukte frei, sondern spalten während der Aushärtung Estermoleküle ab, die wie bei den anderen Silikonsystemen einen charakteristischen Geruch aufweisen. Sie sind für empfindliche Substrate geeignet und zeigen ein breites Haftungsspektrum auf vielen Materialien.
Alkoxysysteme sind ebenfalls neutral vernetzende Silikone und sind bereits seit vielen Jahren im Markt. Alkoxysilikone spalten während der Aushärtung niedere Alkohole ab (Methanol und/oder Ethanol) und riechen daher beim Aushärten kaum wahrnehmbar. Sie sind für empfindliche Substrate geeignet, zeigen ein breites Haftungsspektrum auf vielen Werkstoffen, einschließlich diverser Kunststoffe, Lacke und Beschichtungen.
Die Basis der 2K-kondensationsvernetzenden Silikone (RTV-2) ist die durch Katalysatoren, z. B. eines Zinn-Katalysators beschleunigte Vernetzungsreaktion von Hydroxypolysiloxanen mit Kieselsäureestern. Hierbei wird ein, dem Kieselsäureester entsprechender Alkohol abgespalten. Als 2K-System härten diese Klebstoffe unabhängig von der Umgebungsfeuchtigkeit und werden somit eingesetzt wenn es darum geht großflächige Klebungen, feuchtigkeitsundurchlässiger Werkstoffe oder Klebungen mit hohen Klebschichtdicken durchzuführen. Wie bei 2K-System üblich müssen die Komponenten im korrekten Verhältnis zueinander homogen vermischt und es darf keine den Härtungsprozess behindernde Luft eingerührt werden.
Anwendungsgebiete
Silikone kommen überall dort zum Einsatz, wo ihre besonderen Eigenschaften, hohe Kälteelastizität, hohe Temperatur-, Chemikalien-, Witterungs- und UV-Beständigkeit erforderlich ist und die relativ geringe Festigkeit nicht von Nachteil ist oder durch eine entsprechend vergrößerte Klebfläche ausgeglichen werden kann. Auch wenn es sich bei Silikonanwendungen häufig um Abdichtungen handelt werden sie auch für Klebungen in verschiedenen Anwendungsgebieten eingesetzt. Beispiele findet man im Bau z. B. bei der Herstellung von Mehrfach-Isolierglasscheiben, im Glasfassadenbau oder der Herstellung von Trennwand-Elementen für den Innenausbau. Indem Randprofile durch Silikonfugen ersetzt werden, lassen sich annähernd oberflächenbündige Glasflächen realisieren.
In der Klima- und Lüftungstechnik werden Silikonklebstoffe eingesetzt, um Bauteile aus Werkstoffen mit unterschiedlichem thermischem Ausdehnungsverhalten miteinander zu verbinden. Bei der Herstellung von Photovoltaikmodulen werden Silikone aufgrund ihrer Witterungs- und UV-Beständigkeit für die Klebung des Modulrahmens und das Aufklebens der Anschlussdose verwendet. In der Hausgeräteindustrie sind auch Temperaturbeständigkeit und Elastizität von Vorteil. Bei nahezu allen Klebungen in diesem Bereich, z. B. dem Einkleben von Sichtfenstern in Backofentüren werden Materialien mit unterschiedlichen thermischen Ausdehnungskoeffizienten wie Glas, Metalle und Kunststoffe miteinander verbunden.
Arbeitssicherheit In der Regel sind die durch eine Polykondensation vernetzenden Silikonklebstoffe keine Gefahrstoffe im Sinne der Verordnung (EG) Nr. 1272/2008 (CLP). Die bei der Vernetzung von Oximsystemen frei werdenden Ketoxim-Abspaltungsprodukte (2-Butanonoxim (MEKO), 2-Propanonoxim (DMKO) und/oder 2-Pentanonoxim (MPKO))[28] werden aufgrund des Verdachts auf krebserzeugende Wirkung inzwischen als kritisch angesehen.[29] Die in den 2K-kondensationsvernetzenden Silikone (RTV-2) vielfach verwendeten zinnorganischen Katalysatoren werden aufgrund ihrer fortpflanzungsgefährdenden und fruchtschädigenden Wirkung als kritisch betrachtet und sind mittlerweile vielfach durch alternative Katalysatoren ersetzt.
Klebstoffe auf Basis silanmodifizierter Polymere (SMP-Klebstoffe)
Ende der 80er Jahre kam mit den Kleb- und Dichtstoffen auf Basis von silanmodifizierten Polymeren eine neue Gruppe feuchtigkeitsvernetzender Systeme auf den Markt. Sie kombinieren die positiven Eigenschaften von feuchtigkeitsvernetzenden Silikonen mit denen der Polyurethane. So zeigen sie eine gute Haftung zu vielen Substraten, haben eine gute Witterungs- und UV-Beständigkeit, eine hohe Elastizität, sind im Temperaturbereich von −40 bis 100 °C verwendbar, im noch nicht gehärteten Zustand überstreichbar und stellen meist keine Gefahrstoffe im Sinne der Verordnung (EG) Nr. 1272/2008 (CLP) dar.
Die für die Herstellung der SMP-Klebstoffe verwendeten silanmodifizierten Polymere basieren meist auf einem hochmolekularen Polypropylenglykol (PPG)-Rückgrat, das an seinen Enden entweder direkt oder über eine Urethangruppe mit Silangruppen terminiert ist. Die Härtung erfolgt wie auch bei den RTV1 Silikonen und den feuchtigkeitsvernetzenden Polyurethanen bei Raumtemperatur durch Zutritt von Luftfeuchtigkeit. Es gelten also für deren Verarbeitung die gleichen diesbezüglichen Voraussetzungen. Als Abspaltprodukt der Polykondensationsreaktion wird meist Methanol freigesetzt.
Um ihre Anwendung auch bei einem nicht ausreichenden Feuchtigkeitsangebot (geringe Luftfeuchtigkeit, Dickschichtklebung oder großflächige Verklebung von feuchtigkeitsundurchlässigen Fügeteilen) zu ermöglichen, gibt es diese Klebstoffe auch als 2K-Systeme, wobei die zweite Komponente im Wesentlichen als Feuchtigkeitsquelle dient.
Ein neues Verfahren ermöglicht es, das Polymerrückgrat gezielt anzupassen. So ist man nicht mehr auf eine reine PPG-Struktur beschränkt, der Einbau von z. B. Polyestern oder Polycarbonaten ist möglich, es können zusätzliche Funktionalitäten in das Polymerrückgrat eingebaut und das Molekulargewicht des Polymerrückgrats über einen weiten Bereich eingestellt werden. Durch die Möglichkeit diese neuen Polymere so aufzubauen, dass sie bei der Vernetzung ohne Einbußen bei der Härtungsgeschwindigkeit ausschließlich Ethanol abspalten, können Klebstoffe formuliert werden, die bei der Härtung nicht das gesundheitsschädliche Methanol freisetzen. Da die für die Vernetzung ausschlaggebende Silanfunktionalität nicht, wie bei den bisherigen Systemen ausschließlich endständig, sondern gezielt seitenständig verteilt über die Polymerkette möglich ist, kann die durch die Härtung erreichte Vernetzungsdichte und die Polarität der Struktur gezielt angepasst werden. So ist mit diesen neuen Polymeren ein verbessertes Rückstellvermögen, eine verbesserte Tiefenhärtung, d. h. einer verbesserte Durchhärtung dickerer Schichten, eine verbesserte Anfangsklebrigkeit und eine höhere Endfestigkeiten, wie sie bisher nur von Polyurethanklebdichtstoffen, nicht aber von Silikonen erreicht wurden, möglich.[30][31]
Anwendungsgebiete
Das Anwendungsgebiet, in denen SMP-Klebstoffe eingesetzt werden, ist im Großen und Ganzen mit dem der feuchtigkeitsvernetzenden Polyurethanen und Silkonen deckungsgleich und wird eigentlich nur durch den im Vergleich zu den Silikonen begrenzten Temperatureinsatzbereich und in gewissem Maß durch die etwas geringere Witterungs-, UV- und Chemikalienbeständigkeit eingeschränkt. Das bedeutet aber nicht, dass ein eins-zu-eins Austausch möglich ist. Es handelt sich um unterschiedliche Systeme mit z. T. voneinander abweichenden Eigenschaften und es muss jeweils das gesamte Spektrum der an die Klebung gestellten Anforderungen berücksichtigt werden. Dies schließt die Verarbeitungseigenschaften und somit die Anforderungen durch den Klebprozess mit ein.
An dieser Stelle sollte ein weiterer Nachteil der SMP-Klebstoffe nicht unerwähnt bleiben. Eine Verwendung der feuchtigkeitsvernetzenden SMP-Klebstoffe für das Einkleben der Scheiben im Automobilbau ist zwar prinzipiell möglich, aber aufgrund der geforderten Reparaturmöglichkeit problematisch. So ist die bei den Polyurethansystemen gegebene Möglichkeit, nach einer Aktivierung auf Resten des alten Klebstoffs zu Kleben, bei den SMP-Klebstoffen bisher nicht möglich. Im Reparaturfall müsste der alte Klebstoff vollständig vom Klebflansch entfernt werden, wobei eine Beschädigung der Lackschicht aus Korrosionsschutzgründen nicht zulässig wäre.
Arbeitssicherheit In der Regel sind die SMP-Klebstoffe keine Gefahrstoffe im Sinne der Verordnung (EG) Nr. 1272/2008 (CLP). Aufgrund der bei der Härtung erfolgenden Freisetzung des gesundheitsschädlichen Methanols sollte jedoch bei der Härtung eine entsprechende Lüftung vorgesehen werden. Da für SMP-Klebstoffe häufig wie bei den kondensationsvernetzenden RTV-2 Silikonen ebenfalls zinnorganische Katalysatoren verwendet werden, gelten die dort gemachten Hinweise auch für SMP-Klebstoffe.
Polymerisationsklebstoffe
Zu dieser Gruppe von Klebstoffen, die durch eine als Kettenreaktion ablaufende Polymerisation härten gehören z. B. die, unter ihrer umgangssprachlichen Bezeichnung Sekundenklebstoff oder Super Glue (eingedeutscht Superkleber) bekannten Cyanacrylatklebstoffe (CA-Kleber). Weitere Beispiele sind die unter Luftsauerstoffausschluss härtenden anaeroben Klebstoffe, die z. B. zur Sicherung von Schrauben vor ungewollten Losdrehen verwendet werden, sowie die strahlenhärtenden Klebstoffe bei denen die Polymerisation durch eine Aktivierung der Härtermoleküle durch Strahlung gestartet wird (meist Licht einer bestimmten Wellenlänge). In der Zahnmedizin werden diese als Füllmaterial für kariöse Zähne verwendet.
Cyanacrylat-Klebstoffe
Ihren in der Umgangssprache üblichen Namen „Sekundenklebstoff“ verdankt diese Klebstoffklasse der Möglichkeit, innerhalb von Sekunden handfeste Klebungen zu erreichen. Es ist allerdings zu beachten, dass die Endfestigkeit erst nach mehreren Stunden erreicht wird.
Bei den Cyanacrylat-Klebstoffen handelt es sich um 1K-Reaktionsklebstoffe auf Basis von Cyanacrylsäureestern mit unterschiedlich langen Alkylketten. Häufig werden 2-Cyanacrylsäuremethylester, n-Butylcyanacrylat und 2-Octylcyanacrylat als Rezepturbestandteile verwendet. Die zur Härtung führende Polymerisationsreaktion wird schon durch geringe Mengen von Hydroxid-Ionen gestartet. So reicht bereits die durch die Autoprotolyse unbehandelten Wassers vorliegende Hydroxidkonzentration von 10−7 mol·l−1 aus, die in einer anionischen Polymerisation verlaufende Härtungsreaktion (siehe Abbildung) zum Poly(alkylcyanacrylat) zu starten. Hierzu greift das Hydroxid-Ion an der aufgrund der elektronenziehenden Wirkung der Cyan- und Estergruppen positiv polarisierten Kohlenstoffatom der C-C-Doppelbindung an. Das gebildete Carbanion greift wiederum als Nucleophil das nächste Cyanacrylatmonomer usw.
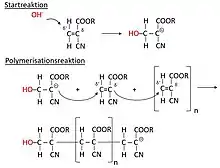
Die Härtung der Cyanacrylate wird also durch die natürliche Luftfeuchtigkeit bzw. die aus der Umgebungsluft auf den Fügeteiloberflächen adsorbierten Wassermoleküle gestartet. Da die Polymerisation der Cyanacrylsäureester-Monomere nur über eine geringe Reichweite ungestört verläuft, können Cyanacrylatklebstoffe nur in Schichtdicken bis zu ca. 0,2 mm voll durchpolymerisiert werden. Bei dickeren Klebschichten wird keine vollständige Vernetzung erreicht, was zu einer verringerten Festigkeit führt.
Basische Oberflächen können die Polymerisation ebenfalls starten bzw. beschleunigen, während saure Oberflächen aufgrund der geringen Konzentration an Hydroxid-Ionen die Polymerisation verlangsamen. Starke Säuren führen zur Protonierung der Carbanionen und somit zum Abbruch der Kettenreaktion.
In einer neutralen oder basischen Umgebung läuft die stark exotherme Reaktion so lange, bis alle Monomere verbraucht sind. Bei einem zu hohen Angebot an Hydroxid-Ionen, sei es als Folge einer zu hohen Feuchtigkeit oder einer stark alkalischen Oberfläche, kann es zur sogenannten Schockhärtung mit einer in der Folge verringerten Klebfestigkeit kommen.
Dem Vorteil einer fast sofort gegebenen Handhabungsfestigkeit stehen einige Nachteile gegenüber:
- Cyanacrylatklebstoffe sind im gehärteten Zustand meist recht spröde und nur wenig flexibel.
- Die erreichbaren Klebschichtdicken sind aufgrund der mangelnden Durchhärtung dickerer Schichten sowie der niedrigen Viskosität, die den Klebstoffen ansonsten eine gute Kapillarwirkung verleiht, begrenzt.
- Als Thermoplast besitzen sie zudem nur eine begrenzte Wärmebeständigkeit.
- Auch wenn sie Wasser zur Härtung benötigen, so weisen die gehärteten Klebstoffe doch eine gewisse Empfindlichkeit gegenüber hoher Feuchtigkeit auf.
- Rezepturabhängig können Cyanacrylatklebstoffe Spannungsrisskorrosion an den Fügeteilen auslösen
Neuere Entwicklungen führten zu teilflexibilisierten Cyanacrylatklebstoffen, die Spannungsspitzen besser abbauen können und häufig auch eine gegenüber den Standardsystemen verbesserte Wärmebeständigkeit aufweisen. Auch konnte die Wasserbeständigkeit verbessert werden.
Anwendungsgebiete
Aufgrund der schnellen Härtung werden die Cyanacrylatklebstoffe insbesondere für das Kleben von Kleinteilen bei dünnen Klebschichten z. B. im Bereich der Optik, der Mikroelektronik, der Medizin- und der Fahrzeugtechnik verwendet. So werden sie z. B. für das Einkleben von Gläsern verwendet, wobei beachtet werden muss, dass stark alkalische Gläser die Polymerisation stark beschleunigen und es zu der bereits erwähnten Schockhärtung kommen kann. Eingesetzt werden diese Klebstoffe auch zum Kleben von Schwingungsdämpfern bei HiFi-Anlagen, dem Aufkleben der Membran bei der Herstellung von Lautsprechern, dem Einkleben der Libellen in Wasserwaagen, bei der Spulendrahtfixierung, der Fixierung von Abdeckklappen und dem Kleben von Elastomerdichtungen. Durch die Stoßverklebung von Elastomer-Rundprofilen können so z. B. O-Ringe hergestellt werden.[32]
Spezielle Cyanacrylatklebstoffe mit medizinischer Zulassung werden als Nahtersatz in der Medizin zum Wundverschluss verwendet. Durch die feucht-warmen Umgebungsbedingungen lösen sich diese Verklebungen langsam wieder auf, nachdem die Wunde verheilt ist.
Arbeitssicherheit
Durch die schnelle Härtung der Cyanacrylatklebstoffe können ungewollt Hautflächen miteinander verkleben. Sollte es trotz der obligatorischen Verwendung von persönlicher Schutzausrüstung wie Handschuhen und Schutzbrille zu einem Hautkontakt mit Cyanacrylatklebstoff gekommen sein, gibt das vom Industrieverband Klebstoffe e.V. herausgegebenen Merkblatt Erste Hilfe bei Unfällen mit Sekundenklebstoffen[33] wichtige Hinweise. Es sollte nicht versucht werden, den Klebstoff gewaltsam von der Haut abzuziehen.
Methylmethacrylat-Klebstoffe
Bei den Methylmethacrylat-Klebstoffen (MMA-Klebstoffe) handelt es sich um 2K-Reaktionsklebstoffe, bei denen das eingesetzte Monomer (typischerweise der Methylester der Methacrylsäure, ggf. in Abmischung mit weiteren polymerisationsfähigen Acrylat- und/oder Methacrylatmonomeren) in einer radikalischen Kettenreaktion polymerisiert wird. Zum Start der Polymerisationsreaktion wird ein reaktives Radikal benötigt, das meist aus einem Peroxid entsteht, wenn man dieses mit einem geeigneten Beschleuniger in Kontakt kommt.
Um eine entsprechend gute Lagerfähigkeit der Klebstoffe zu erzielen, wird das Peroxid im Methylmethacrylat-Monomer als eine Komponente und der Beschleuniger gelöst im Basis-Monomer als zweite Komponente in den Handel gebracht. Durch Zugabe von Füllstoffen, Pigmenten etc. können die Verarbeitungseigenschaften, die Farbe und durch zähelastifizierende Polymere die mechanischen Eigenschaften des gehärteten Klebstoffs an die jeweiligen Anforderungen angepasst und das Mischungsverhältnis in Grenzen variiert werden. So sind Mischungsverhältnisse von 10 : 1 oder 1 : 1 üblich. Durch Mischen beider Komponenten wird die Radikalkettenreaktion initiiert und der Klebstoff härtet. Natürlich ist auch hier die produktspezifische Topfzeit zu beachten
Ebenso können das gesamte Monomer und das Peroxid in eine Komponente vorliegen, die zweite enthält dann lediglich den Beschleuniger. Hierdurch kann das vorangehende Mischen der beiden Komponenten (und die damit verbundene Topfzeit) entfallen. Bei diesem sogenannten No-Mix- oder A/B-Verfahren wird eine Komponente des Klebstoffs auf ein Fügeteil und die zweite auf das andere Fügeteil aufgetragen. Durch Zusammenfügen der Flächen kommen die beiden Komponenten in Kontakt und die Härtungsreaktion startet. Naturgemäß ist dieses Verfahren auf Klebungen mit geringen Klebschichtdicken begrenzt.
Die wesentlichen typischen Eigenschaften der MMA-Klebstoffe sind:
- hohe Festigkeiten (bis zu 25 N/mm²),
- hohe Elastizitäten (bis zu 120 % Dehnung),
- schnelle Härtung (im Vergleich zu polyadditionsvernetzenden 2K-Polyurethan- oder 2K-Epoxidklebstoffen zeigen die MMA-Klebstoffe bei gleicher Topfzeit einen schnelleren Festigkeitsaufbau, d. h. die Handhabungs- und die Endfestigkeit wird schneller erreicht).
- gutes Haftungsspektrum und vergleichsweise bessere Toleranz gegenüber leicht verschmutzten Fügeteiloberflächen
- gute Witterungsbeständigkeit
- temperaturbeständig im Bereich von −40 bis 120 °C
- die MMA-Klebstoffe zeigen den für Acrylate typischen, vielfach als unangenehm beurteilten Geruch.
- die exotherm, d. h. unter Erwärmung ablaufende Härtungsreaktion führt bei einigen 2K-MMA-Klebstoffen zu einer starken Erwärmung, sodass es bei dicken Klebschichten zu einem „Aufkochen“ des Klebstoffs kommen kann. Hierbei verdampfen noch nicht umgesetzte Monomere unter Blasenbildung im Klebstoff. Dies führt nicht nur zu einer blasigen Klebschicht mit einem entsprechenden Festigkeitsverlust, sondern auch zu einer Gesundheitsgefährdung bei der Verarbeitung durch die freigesetzten Monomere und kann im Extremfall zur Selbstentzündung führen.
Anwendungsgebiete
Typische Anwendungen finden sich u. a. in der Fahrzeugindustrie z. B. bei der Herstellung von Kunststoffanbauteilen für Personenwagen, bei der Herstellung von Nutzfahrzeugen, Bussen, Landmaschinen und Eisenbahnwaggons, im Bootsbau z. B. mit der Verklebung von Rumpf und Deck sowie bei der Herstellung von Verkehrsschildern mit dem Aufkleben von Verstärkungsprofilen.
Anaerob härtende Klebstoffe
Ähnlich wie die MMA-Klebstoffe härten die anaeroben Klebstoffe über durch radikalische Polymerisation. Jedoch handelt es sich hierbei um 1K-Klebstoffe, wobei man sich die Tatsache, dass Sauerstoff über Radikale ablaufende Reaktion inhibiert zu Nutze macht, um eine Härtung im Liefergebinde zu verhindern. Neben den polymerisationsfähigen Methacrylatmonomeren (z. B. Tetraethylenglykoldimetharylat, TEGMA) enthalten diese Klebstoffe ein komplexes Härtersystem, bestehend aus Radikalbildnern (z. B. Cumolhydroperoxid), Beschleunigern (z. B. N,N-Dimethyl-p-toluidin) und Saccarin, das als Metallkomplexbildner und Reduktionsmittel für Metallionen dient. Das Härtersystem bewirkt, dass nach dem Aufbringen des Klebstoffs und dem Fügen der im Klebstoff enthaltene Sauerstoff chemisch entfernt wird. Gleichzeitig werden durch das dabei gebildete Reaktionsprodukt Metallionen aus den Fügeteilen herausgelöst und zu einer niedrigen Oxidationsstufe reduziert, die wiederum den Zerfall des Radikalbildners in reaktive Radikale katalysiert. Die reaktiven Radikale initiieren dann die als radikalische Polymerisation ablaufende Härtung des Klebstoffs.[34]
Aus dem Härtungsprozess ergeben sich also die folgenden Randbedingungen für die Anwendung von anaeroben Klebstoffen:
- Um eine vorzeitige Härtung im Liefergebinde zu verhindern, muss der Klebstoff im Liefergebinde Kontakt mit Sauerstoff haben. Dies wird durch die Verwendung von luftdurchlässigen Kunststoffflaschen, die vor dem Befüllen mit Sauerstoff durchspült und nur etwa zur Hälfte gefüllt werden, erreicht.
- Im Klebspalt muss ein Sauerstoffzutritt verhindert werden, so dass die Anwendung auf enge Klebspalte von maximal 0,3 mm begrenzt ist.
- Je enger der Klebspalt, umso schneller erfolgt die Härtung.
- Es ist ein Metallkontakt (Eisen, Kupfer) des Klebstoffs erforderlich. Ist dieser nicht gegeben, kann man die Fügeteiloberflächen vor dem Kleben mittels spezieller, Eisen- oder Kupferionen enthaltender Beschleuniger aktivieren. Die Verwendung des Beschleunigers empfiehlt sich auch bei Metallen mit hoch passiven Eigenschaften wie Chrom- und Edelstählen.
Im gehärteten Zustand sind diese Klebstoffe Duromere und können demnach hohe und temperaturbeständige (−60 bis 200 °C) Festigkeiten aufweisen. Allerdings sind die hochtemperaturbeständigen Systeme recht spröde und eignen sich somit nicht für flexible Fügeteile.
Anwendungsgebiete
Ein Hauptanwendungsgebiet der anaeroben Klebstoffe ist die Schraubensicherung, also das Vermeiden eines ungewollten Lösens der Schraube, z. B. durch Vibration. Diese Schraubensicherungen werden in unterschiedlichen Festigkeiten angeboten, so dass durch Auswahl eines Klebstoffs mit einer an den Schraubendurchmesser angepassten Festigkeit eine Wiederlösbarkeit sichergestellt werden kann. Daneben werden anaerobe Klebstoffe zum Verbinden rotationssymmetrischer Fügeteile (Welle-Nabe-Verbindungen) z. B. in Elektromotoren eingesetzt. Aufgrund der guten Öl-, Lösemittel- und Feuchtigkeitsbeständigkeit wird häufig neben der fügenden auch die dichtende Funktion dieser Klebstoffe genutzt. Beispiele hierfür findet man u. a. in der Motoren- und Getriebemontage.
Strahlenhärtende Klebstoffe
Ebenfalls durch Polymerisation härten diese 1K-Klebstoffe zu festen Polymeren aus, indem die Härtungsreaktion durch Bestrahlung mit UV-Licht, wobei auch teilweise auch Licht aus dem sichtbaren Bereich mit Wellenlängen um die 400 nm verwendet wird oder, wesentlich seltener, durch andere Strahlenquellen wie Elektronenstrahler initiiert wird. Das durch den zur Härtung verwendeten Strahler emittierte Licht muss hinsichtlich seiner Wellenlänge mit dem Absorptionsbereich des jeweils im Klebstoff eingesetzten Initiators möglichst gut übereinstimmen. Übliche zur Härtung verwendete Wellenlängen sind 365, 400 und 460 nm. Elektronenstrahlhärtung hat sich, wohl nicht zuletzt wegen des hohen apparativen Aufwands, nicht durchgesetzt.
Prinzipiell unterscheidet man bei den UV-härtenden Klebstoffen zwischen denen, die durch eine radikalische und denen, die durch eine kationische Polymerisation vernetzen. In beiden Fällen handelt es sich um 1K-Klebstoffe die nur kurze Belichtungszeiten zur Härtung benötigen. Die radikalisch vernetzenden Systeme härten nur während der Belichtung. Diese muss also nach dem Fügen bis zur vollständigen Vernetzung erfolgen, mindestens ein Fügeteil muss also für das verwendete Licht durchlässig ausreichend transparent sein. Dagegen bleiben einige kationisch härtende Systeme nach der Belichtung noch für eine kurze Zeit ausreichend flüssig und härten auch nach Ende der Belichtung weiter. Diese Systeme können also vor dem Fügen durch Belichtung aktiviert werden und sind somit auch für das Kleben von nicht UV-transparenten Fügeteilen geeignet. Natürlich muss hier die offene Zeit, also das Zeitfenster innerhalb dessen die Viskosität noch eine Benetzung des zweiten Fügeteils erlaubt eingehalten werden.
Die radikalisch vernetzenden Systeme basieren auf Acrylatmonomeren, die kationisch härtenden auf Epoxidharzen. In beiden Fällen werden entsprechende Photoinitiatoren benötigt, die im Fall der radikalisch vernetzenden Systeme entweder bei Belichtung direkt die, die Polymerisation startenden Radikale bilden oder aber ein Wasserstoffatom von einem benachbarten Molekül abstrahieren, das dann die Polymerisation auslöst. Die kationischen Photoinitiatoren erzeugen bei Zerfall eine Brönsted- oder Lewis-Säure die im nächsten Schritt die Polymerisation startet.
Anwendungsgebiete
Bekannte Beispiele für UV-härtende Klebstoff sind etwa das Ankleben künstlicher Fingernägel oder das Einkleben von Kunststoff-Zahnfüllungen. In der industriellen Fertigung UV-härtende Klebstoffe insbesondere dort eingesetzt wo eine schnelle Härtung erforderlich ist. Man findet diese Klebstoffe in verschiedenen Bereichen wie z. B.:
- der Consumerelektronik wo z. B. die Minilautsprecher für Mobiltelefone aber auch die Gehäuse der Telefone mit UV-härtenden Klebstoffen geklebt werden
- der Möbelindustrie bei der Herstellung von Glasmöbeln sowie dem Ankleben von Scharnieren an die Glastüren von Schränken oder Duschkabinen
- der Elektronik für verschiedene Vergussaufgaben (Schalter, Stecker, Relais etc.) zum Schutz der Komponenten vor Witterungseinflüssen, zur Spulendrahtfixierung und der Gehäuseverklebung
- der Automobilindustrie z. B. bei der Herstellung von Kamerasystemen und verschiedenen Sensoren
- der Herstellung von LED-Lampen
Daneben gibt es Klebstoffe, die neben der Härtung durch UV-Licht auch durch den Einfluss von Luftfeuchtigkeit oder durch Wärme härten. Diese Systeme sind geeignet für Anwendungen bei denen aufgrund vorhandener Geometrien und daraus resultierender Schattenzonen nicht alle Bereiche der Klebung dem UV-Licht zugänglich sind. Die Lichthärtung im zugänglichen Bereich bietet den Vorteil des schnellen Festigkeitsaufbaus und somit der Realisierung kurzer Taktzeiten. Die Härtung in den Schattenbereichen erfolgt dann zu einem späteren Zeitpunkt entweder durch Luftfeuchtigkeit oder durch Wärme.[32]
Klebebänder (Haftklebstoffsysteme)
Obwohl Klebebänder, insbesondere die sogenannten doppelseitigen Klebebänder, zum Verbinden von Fügeteilen verwendet werden, stellen sie im eigentlichen Sinne keine Klebstoffe dar. Haftklebstoffsysteme, wie z. B. Klebebänder, Etiketten, selbstklebende Stanzteile etc. bestehen meistens aus einem funktionalen Träger, der ein- oder beidseitig mit einem Haftklebstoff beschichtet ist. Der funktionale Träger dient u. a. der mechanischen Stabilität und Festigkeit der Klebstoff-Masse und kann innerhalb einer Klebung zusätzlich verschiedene Aufgaben, wie z. B. mechanische Dämpfung, den Ausgleich von unterschiedlichen Materialausdehnungen, thermische oder elektrische Isolation bzw. Leitfähigkeit usw., übernehmen. Typische Materialien sind Papier, Polymerschäume und -folien, Metallfolien, Metall- und Kunststoffhalbzeuge. Die sogenannten Transferklebebänder sind eine weitere Anwendungsform und bestehen lediglich aus dem Haftklebstoff-Film, sind also trägerlos. Ein wesentlicher Bestandteil der Haftklebstoffsysteme ist der sogenannte Haftklebstoff, also die Substanz, die die klebende Wirkung zeigt.
Da die Klebebänder in einem eigenen Artikel behandelt werden, beschränkt sich dieser Abschnitt auf die für die Herstellung von Klebebändern verwendeten Haftklebstoffe.
Haftklebstoffe[35]
Haftklebstoffe sind Klebstoffe, die bei Raumtemperatur eine mehr oder weniger stark ausgeprägte Dauerklebrigkeit aufweisen und unter leichten Druck eine gute Haftung (Adhäsion) zu verschiedenen Oberflächen ausbilden. Physikalisch betrachtet handelt es sich um extrem hochviskose elastische Flüssigkeiten mit einer Glasübergangstemperatur von < −10 °C. Um Haftung zu der zu klebenden Oberfläche auszubilden, muss der Haftklebstoff diese Oberfläche schnell und vollständig benetzen. Die Qualität der Benetzung hängt dabei u. a. vom viskoelastischen Verhalten des Haftklebstoffs ab. Er muss eine ausreichende Fließfähigkeit aufweisen, um sich der Oberflächenstruktur des Fügeteils anpassen zu können. Dies wird durch einen leichten Druck bei der Anwendung unterstützt. Aufgrund dieser Eigenschaft ist die innere Festigkeit (Kohäsion) der Haftklebstoffe relativ gering und somit liegen die mit Klebebändern erreichbaren Festigkeiten deutlich unter denen anderer Klebstoffsysteme. Typisch für Haftklebstoffe ist ein dynamischer Adhäsionsaufbau; so dauert es je nach Haftklebstofftyp, Temperatur, Anpressdruck und -dauer einige Minuten bis mehrere Tage, bis die Endfestigkeit erreicht wird.
Lange Zeit war Naturkautschuk (1,4-cis-Polyisopren) zusammen mit klebrigmachenden Harzen der dominierende Rohstoff für Haftklebstoffe. Heute werden neben Naturkautschuk vielfach synthetisch hergestellte Elastomere, wie Blockcopolymere aus Isopren und Styrol (den sog. SIS-Blockcopolymeren) und aus Butadien mit Styrol (den sog. SBS-Blockcopolymeren) in Abmischung mit Naturharzen (z. B. Kolophonium), modifizierten Naturharzen (Kolophoniumharzester) oder Syntheseharzen für die Herstellung von Haftklebstoffen verwendet. Es werden meist Harze mit einer niedrigen Molekülmasse und einer Glasübergangstemperatur von −20 °C bis +70 °C eingesetzt. Eine weitere wichtige Gruppe ist die der Acrylatcopolymere. Derartige Haftklebstoffe werden bevorzugt aus 2-Ethylhexylacrylat und Isooctylacrylat unter Zusatz von Acrylsäure und ggf. weiteren Acrylatmonomeren hergestellt. Acrylatbasierte Haftklebstoffe benötigen nur dann eine Zugabe von klebrigmachenden Harzen, wenn Adhäsion zu niedrigenergetischen Oberflächen wie z. B. Polyethylen oder Polypropylen gefordert ist. Wie auch die naturkautschukbasierten Systeme müssen Acrylatsysteme chemisch vernetzt werden, um eine gewisse innere Festigkeit (Kohäsion) zu erreichen. Diese Vernetzung erfolgt meist bei der Herstellung des Klebebandes, d. h. nach dem Aufbringen der Haftklebstoffschicht auf den Träger. Im Gegensatz dazu ist dies bei den SIS- und SBS-basierten Haftklebstoffen nicht erforderlich.
Neben den genannten Haftklebestoffen auf Basis von Natur- oder Synthesekautschuk und Acrylaten gibt es ebenfalls solche auf Basis von Polyurethanen und Silikonen, diese Systeme sind aber Mengenmäßig von untergeordneter Bedeutung und werden nur dann verwendet wenn besondere Eigenschaften erforderlich sind. So werden polyurethanbasierte Haftklebstoffe z. B. in der Wundabdeckung und Silikonsysteme für Hochtemperatur-Anwendungen oder wenn eine hohe Chemikalienbeständigkeit erforderlich ist verwendet.
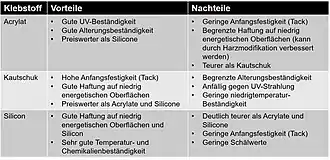
Das Ziel der Formulierung von Haftklebstoffen ist es, durch eine entsprechende Rohstoffauswahl und dem Polymerdesign ein der jeweiligen Anwendung entsprechendes Verhältnis von Anfangsklebrigkeit (Tack), Schälfestigkeit und innerer Festigkeit d. h. Scher- und Kriechfestigkeit (Kohäsion) zu erzielen.
Um eine höhere Verbundfestigkeit zu erlangen sind relativ neue Haftklebstoffe verfügbar, die durch eine nachfolgende chemische Härtung in eine feste, höhere Kräfte übertragende, Klebmasse überführt werden. Diese stellen dann chemisch härtende Klebstoffe dar. Somit ist es auch nicht verwunderlich, dass hier die schon von den chemisch härtenden Klebstoffen bekannten Technologien, wie z. B. Polyurethan, Epoxidharz, Cyanacrylat genutzt werden.
Anwendungsgebiete[36]
Neben der Anwendung als Klebschicht für die Herstellung von doppel- und einseitigen Klebebändern und Etiketten finden die Haftklebstoffe Anwendung
- als Transferklebstoff (doppelseitiges, trägerfreies Klebeband);
- als Sprühklebstoff
- als Haftkitt (z. B. Blu-Tack);
- als Klebstoffstreifen an rückstandsfrei abziehbaren Klebezetteln;
- als Haftmittel für Zahnprothesen
Nach der Anwendungsart kann man folgende Produkttypen unterscheiden:
- wiederverklebbare Produkte:
- geringe Klebkraft,
- das Klebstoff-System wird beim Ablösen nicht beschädigt,
- z. B. Haftnotizzettel, Verschluss-Klebungen (z. B. bei Papiertaschentuch-Verpackungen) etc.
- lösbare Produkte:
- mittlere bis hohe Klebkraft,
- lassen sich rückstandsfrei entfernen,
- meistens einmaliger Gebrauch,
- Haken- und Poster-Befestigungssysteme,
- Wundpflaster und Transdermale Therapeutische Systeme (z. B. Nikotinpflaster),
- Aufkleber,
- Etiketten,
- selbstklebende Folien,
- Verpackungsbänder usw.
- permanent klebende Produkte:
- Klebkraft ist für semistrukturelle Anwendungen
- Anwendungsbeispiele:
- KFZ-Außenspiegel,
- KFZ-Schutz- und Zierleisten,
- Dämpfungs-Versteifungselemente im Fahrzeugbau,
- Spiegelklebungen,
- Anwendungen im Fenster- und Fassadenbau,
- Mobiltelefone
- selbstklebende Produkte, die beim Ablösen bewusst sichtbar verändert oder zerstört werden sollen, wie z. B. Typenschilder, TÜV-Plaketten etc.
Klebstoffe für Lebensmittel
Bei der Herstellung/Zubereitung von Lebensmitteln spielen oft Klebprozesse eine Rolle. Bei der Dekoration von Gebäck kommt Eiklar zum Einsatz, das auf den Teigling gepinselt wird, um dann darauf gestreuten Körnerzucker (Hagelzucker), Salzkörner, Sonnenblumenkerne, Mohn, Nuss- oder Zuckerstreusel anhaften zu lassen. Das Eiklar benetzt dabei das Streugut und gerinnt später beim Backen.
Bei der Dekoration von Süßspeisen wird Glukosesirup als Klebstoff eingesetzt. Verdickt mit Agar-Agar und/oder Pektin bekommt die Masse Volumen und Elastizität und kann dabei auch selbst als Dekorationselement ("Kristall-Tropfen") eingesetzt werden.[37]
Transparente Gelees aus Pektin oder Gelatine können heiß als Sol aufgegossen werden und erstarren zum Gel. Auf Obsttorten oder Gabelbissen werden auf diese Weise Auflagen fixiert, abgeschlossen und feucht gehalten.
Klebstoffauswahl – Prüfung von Klebstoffen

Am Anfang einer Klebstoffauswahl, das gilt sowohl für die industrielle Anwendung als auch für den Hand- und Heimwerker, sollte jeweils die Erstellung eines Anforderungsprofils stehen, auf dessen Basis dann potentiell geeignete Klebstofftechnologien identifiziert werden. Im weiteren Verlauf sollten dann Hersteller oder Händler derartiger Klebstoffe angesprochen werden, um konkrete Produktempfehlungen zu erhalten und daraus Klebstoffe für erste Versuche auszuwählen. In der nebenstehenden Abbildung sind, ohne Anspruch auf Vollständigkeit, die verschiedenen bei der Klebstoffauswahl zu berücksichtigenden Kriterien zusammengestellt. Am Ende steht dann die Nachweisführung, aus der hervorgehen muss, dass die Beanspruchbarkeit der Klebverbindung über die gesamte vorgesehene Lebensdauer stets größer ist als die zu erwartenden Beanspruchungen. Weitere Hinweise hierzu siehe[38][39].
Alle Klebstoffe zeichnen sich durch unterschiedliche physikalisch-chemische Eigenschaften aus. Um eine Vergleichbarkeit zwischen verschiedenen Klebstoffen zu ermöglichen, wurden standardisierte Prüfverfahren und Prüfkörper entwickelt und in Normen beschrieben. Die Normenliste des Industrieverband Klebstoffe e.V.[40] gibt eine Zusammenstellung einer Vielzahl von klebtechnisch relevanten Normen und Richtlinien und soll die Anwender von Klebstoffen u. a. bei der Auswahl von Methoden zur Prüfung von Klebstoffen und Klebverbindungen unterstützen.
Missbrauch als Droge
Flüchtige Bestandteile bestimmter lösemittelhaltige Klebstoffe können auch als Schnüffelstoff inhaliert werden. Die organischen Lösemittel haben eine psychoaktive Wirkung. Es besteht die Gefahr von körperlichen Langzeitschäden bis hin zum Tod. Klebstoffe werden als billiger und leicht zugänglicher Ersatz für illegale Drogen vor allem von Kindern und Jugendlichen missbraucht.[41]
Literatur
- Industrieverband Klebstoffe e.V.: Leitfaden Kleben – aber richtig, https://leitfaden.klebstoffe.com/
- Marlene Doobe: Kunststoffe erfolgreich kleben – Grundlagen, Klebstofftechnologien, Best-Practice-Beispiele. 1. Auflage. Springer Vieweg Verlag, Wiesbaden 2018, ISBN 978-3-658-18444-5.
- Hermann Onusseit: Adhesive Technology – Basic Principles. 1. Auflage. Beuth Verlag, Berlin 2012
- Hermann Onusseit: Klebstoffe der Natur. Anwendung und Perspektiven für die Technik. In: Biologie in unserer Zeit. 5/34/2004, ISSN 0045-205X, S. 307–314.
- Manfred Rasche: Handbuch Klebtechnik. 1. Auflage. Carl Hanser Verlag München Wien 2012, ISBN 978-3-446-42402-9.
- Wilhelm Endlich: Kleb- und Dichtstoffe in der modernen Technik. Ein Praxishandbuch der Kleb- und Dichtstoffanwendung. Vulkan-Verlag, Essen 1998, ISBN 3-8027-2183-7.
- Gerhard Gierenz, F. Röhmer: Arbeitsbuch Kleben und Klebstoffe. Cornelsen und Schwann, Düsseldorf 1989, ISBN 3-590-12939-5.
- Klebstoffe. Theorien und Experimente. In: Praxis der Naturwissenschaften – Chemie. 7/38/1989, Aulis-Verlag, Köln, ISSN 0177-9516.
- Eckehardt Wistuba: Kleben und Klebstoffe. In: Chemie in unserer Zeit. 14. Jahrg. 1980, Nr. 4, ISSN 0009-2851, S. 124–133.
- Gerd Habenicht: Kleben. Leitfaden für die praktische Anwendung und Ausbildung. Vieweg-Verlag, Wiesbaden 1995, ISBN 3-528-04969-3.
- Gerd Habenicht: Kleben. Grundlagen, Technologie, Anwendungen. 3. Auflage. Springer-Verlag, Heidelberg 1997, ISBN 3-540-62445-7.
- Gerhard Fauner, Wilhelm Endlich: Angewandte Klebtechnik. München/ Wien 1979, ISBN 3-446-12767-4.
- Eduardo H. Schindel-Bidinelli: Grundlagen des strukturellen Klebens und Dichtens, Klebstoffarten, Kleb- und Dichttechnik. Hinterwaldner, München 1988, ISBN 3-927235-01-6. (Strukturelles Kleben und Dichten, Band 1)
- Irving Skeist (Hrsg.): Handbook of Adhesives. 3. Auflage. Van Nostrand Reinhold, New York 1990, ISBN 0-442-28013-0.
- Autorenkollektiv: Klebstoffe und Dichtungsmassen. In: Ullmanns-Encyklopädie der technischen Chemie. 4. Auflage. Band 14 1977, ISBN 3-527-20014-2, S. 227–268.
- Bodo Müller, Walter Rath: Formulierung von Kleb- und Dichtstoffen. 2. Auflage. Hannover 2009, ISBN 978-3-86630-862-6.
- Bodo Müller, Walter Rath: Formulating Adhesives and Sealants – Chemistry, Physics and Applications. Hannover 2010, ISBN 978-3-86630-858-9.
- Thomas Stotten, Martin Majolo: Montageklebstoffe in der Praxis. DRW-Verlag, Leinfelden-Echterdingen, 1. Auflage 2010, ISBN 978-3-87181-785-4.
- Industrieverband Klebstoffe e. V.: Handbuch Klebtechnik 2016. ISBN 978-3-658-14529-3.
- Katrin Cura: Vom Hautleim zum Universalklebstoff. Zur Entwicklung der Klebstoffe. GNT-Verlag, Diepholz/Stuttgart/Berlin 2010, ISBN 978-3-928186-91-9
Rundfunkberichte
- Martina Preiner: Kleben – was das Zeug hält, SWR2 – „Wissen“ vom 17. Dezember 2014 (Manuskript)
Weblinks
- Ausbildung, Beratung, Forschung und Entwicklung in der Klebtechnik auf den Seiten des Fraunhofer-Institut für Fertigungstechnik und Angewandte Materialforschung – „Klebtechnik und Oberflächen“
- Kleben & mechanisches Fügen beim Institut für Füge- und Schweißtechnik der TU Braunschweig
Einzelnachweise
- DIN EN 923:2016-03 Klebstoffe – Benennungen und Definitionen; Deutsche Fassung EN 923:2015. Beuth Verlag, Berlin.
- Unterrichtsmaterial Klebstoffe - Die Kunst des Klebens, Seite 10, Fonds der Chemischen Industrie im Verband der Chemischen Industrie e. V., November 2015
- Industrieverband Klebstoffe e.V.: Geschichte des Klebens. Abgerufen am 16. Februar 2018.
- Schmidt, P., Blessing, M., Rageot, M., Iovita, R., Pfleging, J., Nickel, K. G.; Righetti, L. & Tennie, C.: Birch tar extraction does not prove Neanderthal behavioral complexity. In: PNAS. 19. August 2019, doi:10.1073/pnas.1911137116.
- Industrieverband Klebstoffe e.V.: Konjunkturdaten. Abgerufen am 16. Februar 2018.
- MarketsandMarkets: Adhesives & Sealants Market worth 63.50 Billion USD by 2021. In: MarketsandMarkets (Hrsg.): Newsletter. 22. Dezember 2017.
- Eintrag zu Plastisole. In: Römpp Online. Georg Thieme Verlag, abgerufen am 19. März 2018.
- Problematisches Polyvinylchlorid. umwelthaushalt.de. Abgerufen am 11. Juni 2019.
- N. Banduhn u. a.: Kleben/Klebstoff. In: Fonds der Chemischen Industrie/Industrieverband Klebstoffe e.V. (Hrsg.): Informationsserie des Fonds der Chemischen Industrie. Band 27. Frankfurt 2001, S. 39.
- Kleben/Klebstoffe. (PDF) In: Informationsserie des Fonds der Chemischen Industrie. Fonds der Chemischen Industrie/Industrieverband Klebstoffe e.V., abgerufen am 7. Juli 2018.
- D. Symitz, A. Lutz: Strukturkleben im Fahrzeugbau. Verlag moderne Industrie, München 2006.
- H. Stepanski: Punktschweißkleben im Automobilbau – Wie es begann. In: adhäsion – Kleben und Dichten. Nr. 5/210. Springer Verlag, 2010.
- M. Pröbster: Elastisch Kleben aus der Praxis für die Praxis. Springer Fachmedien, Wiesbaden.
- B. Burchard et al.: Elastisches Kleben. Verlag moderne industrie, München 2005.
- R. Heinzmann, S. Koch, H.-C. Thielemann, J. Wolf: Elastisches Kleben im Bauwesen. Verlag moderne Industrie, München 2001.
- Hartwig Lohse: Thermoplastische Systemlösungen im Automobilbau. In: Marlene Doobe (Hrsg.): Kunststoffe erfolgreich kleben. Springer Vieweg, Wiesbaden 2018, ISBN 978-3-658-18444-5, S. 289 ff.
- Technische Regeln für Gefahrstoffe, Isocyanate – Gefährdungsbeurteilung und Schutzmaßnahmen, TRGS 430. BAUA, 2009, abgerufen am 7. Juli 2018.
- GISCHEM: Datenblatt 4,4'-MDI. Abgerufen am 7. Juli 2018.
- GISCHEM: Datenblatt P-MDI. Abgerufen am 7. Juli 2018.
- M. Wirts, R. Lüschen, O. D. Hennemann: Emissionen bei der Verarbeitung von Polyurethanklebstoffen. In: adhäsion – Kleben und Dichten. Nr. 6/2001. Springer Fachmedien, Wiesbaden 2001.
- N. Banduhn u. a.: Kleben/Klebstoffe. In: Fonds der Chemischen Industrie/Industrieverband Klebstoffe e.V. (Hrsg.): Informationsserie des Fonds der chemischen Industrie. Band 27. Frankfurt 2001, S. 33 ff.
- Gert Habenicht: Kleben. Springer Verlag, Berlin 2002, S. 103 ff.
- J. Kramer: Handbuch Fertigungstechnologie Kleben. Hrsg.: O. Hennemann. Carl Hanser Verlag, München / Wien 1992, S. 48 ff.
- N. Banduhn u. a.: Kleben/Klebstoffe. In: Fonds der chemischen Industrie/Industrieverband Klebstoffe e.V. (Hrsg.): Informationsserie des Fonds der chemischen Industrie. Nr. 27. Frankfurt 2001, S. 35 ff.
- B. Brede u. a.: Die Kunst des Klebens. Fonds der chemischen Industrie / Industrieverband Klebstoffe e.V., abgerufen am 7. August 2018.
- Leitfaden Kleben – aber richtig. Industrieverband Klebstoffe, abgerufen am 23. April 2020.
- bgbau.de (Memento des Originals vom 20. Oktober 2018 im Internet Archive) Info: Der Archivlink wurde automatisch eingesetzt und noch nicht geprüft. Bitte prüfe Original- und Archivlink gemäß Anleitung und entferne dann diesen Hinweis.
- bgbau.de (Memento des Originals vom 20. Oktober 2018 im Internet Archive) Info: Der Archivlink wurde automatisch eingesetzt und noch nicht geprüft. Bitte prüfe Original- und Archivlink gemäß Anleitung und entferne dann diesen Hinweis.
- wingisonline.de
- M. Roessing, B. Brugger: Silanmodifizierte Kleb- und Dichtstoffe-Neue Polymere. In: adhäsion – Kleben und Dichten. Nr. 3/2011. Springer Fachmedien, Wiesbaden 2011.
- M. Roessing, B. Brugger: Neue silanmodifizierte Polymere - Flexibles Design für Kleb- und Dichtstoffe. In: adhäsion Kleben und Dichten. Nr. 4/2012. Springer Fachmedien, Wiesbaden.
- Delo Industrieklebstoffe (Hrsg.): Delo Bond it – Nachschlagewerk zur Klebtechnik. 2015.
- Merkblatt Erste Hilfe bei Unfällen mit Sekundenklebstoffen. (PDF) Industrieverband Klebstoffe e.V., abgerufen am 15. Juni 2021.
- N. Banduhn: Kleben/Klebstoffe. In: Fonds der chemischen Industrie, Industrieverband Klebstoffe e.V. (Hrsg.): Informationsserie des Fonds der chemischen Industrie. Band 27. Frankfurt 2001, S. 30 ff.
- W. Brockmann u. a.: Klebtechnik – Klebstoffe, Anwendungen und Verfahren. Wiley-VCH, Weinheim 2005, ISBN 978-3-527-31091-3, S. 41 ff.
- Industrieverband Klebstoffe e.V.: Haftkleben. Abgerufen am 8. Juli 2018.
- bella Lebensmittel Ess-Kleber und Kristall-Tropfen. EAN 4061459457384.
- Andreas Groß, Hartwig Lohse: Qualitätssicherung in der Klebtechnik. In: Marlene Doobe (Hrsg.): Kunststoffe erfolgreich kleben -Grundlagen, Klebstofftechnologien, Best-Practice-Beispiee. Springer Vieweg, Wiesbaden 2018, ISBN 978-3-658-18444-5, S. 141 ff.
- Henning Gleich, Hartwig Lohse: Lebensdauervorhersage – Alterungseffekte im Zeitraffertest. In: Marlene Doobe (Hrsg.): Kunststoffe erfolgreich kleben – Grundlagen, Klebstofftechnologien – Best Practice-Beispiele. Springer Vieweg, Wiesbaden 2018, ISBN 978-3-658-18444-5, S. 153 ff.
- Industrieverband Klebstoffe e.V.: Normenliste. Abgerufen am 8. Juli 2018.
- Drogenprofil „Flüchtige Substanzen“ der Europäischen Beobachtungsstelle für Drogen und Drogensucht, abgerufen am 10. Februar 2019.