Statischer Mischer
Ein statischer Mischer oder Statikmischer ist eine Vorrichtung zum Mischen von Fluiden, in der allein die Strömungsbewegung die Vermischung bewirkt und die nicht über bewegte Elemente verfügt. Er besteht aus strömungsbeeinflussenden Elementen in einem Rohr. Diese teilen abwechselnd den Stoffstrom auf und führen ihn dann wieder zusammen, wodurch die Vermischung erreicht wird. Statische Mischer eignen sich für die Kombinationen flüssig/flüssig, gasförmig/gasförmig und flüssig/gasförmig, unter Umständen auch für Schüttgüter. Ein weiterer Anwendungszweck ist die Homogenisierung nur eines Stoffes bezüglich Zusammensetzung und Temperatur.[1][2]
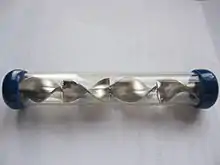

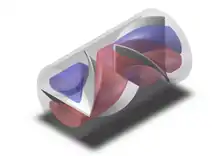
Aufbau und Funktionsweise
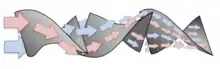
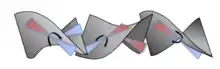
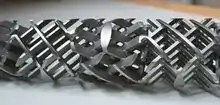
Der statische Mischer besteht aus aneinandergereihten Elementen, die meist schrauben-, lamellen- oder auch gitterförmig sind. Die zu vermischenden Fluide werden gemeinsam und im gewünschten Mischungsverhältnis in den Mischer gedrückt. Die Elemente teilen den Stoffstrom, verdrehen die Ströme und führen sie wieder zusammen. Teilt das erste Element das hineingepumpte zweischichtige Stoffgemisch auf, so ergeben sich nach dem Zusammenführen nach dem Element mindestens vier Schichten. Nach dem nächsten sind es acht Schichten, dann 16 usw. Mit jeder Stufe wird so eine bessere Vermischung erreicht. Allgemein gilt für die Anzahl der Schichten
ist die Anzahl der Schichten am Anfang, die Anzahl der Kanäle, in der Regel zwei, die Anzahl der Mischerelemente.[1]
Neben diesem Effekt, der allein durch laminare Strömung auftritt, gibt es auch eine radiale Mischung der einzelnen Schichten untereinander, insbesondere wenn turbulente Strömungen auftreten.[1]
Es existieren mehrere Dutzend verschiedene Mischertypen, einige Beispiele sind:[1][3]
- Kenics-Mischer: Er besteht aus um 180° verdrillten Blechen. Jede Wendel ist um 90° zur vorigen versetzt und weist den gegensätzlichen Drehsinn auf.
- Sulzer SMV-Mischer: Geriffelte Lamellen leiten die Ströme so, dass sie sich kreuzen.
- Sulzer SMX-Mischer: Dieser Mischer weist eine Vielzahl von gerüstartigen, kreuzweise angeordneten Stegen auf.
- Fluitec CSE-X/6-12 Mischer:[4] Dieser Mischer weist sechs taillierte, kreuzweise angeordneten Stege auf und besitzt Öffnungen in den Randzonen. Dies führt zu einer hohen Mischleistung bei deutlich reduziertem Druckverlust.
- Fluitec CSE-XR Mischer-Wärmetauscher: Dieser statische Mischer weist zusätzlich zu den Mischelemente ein integriertes Rohrbündel für den Wärmeaustausch auf.
- Ross-ISG-Mischer: Der Mischer ist durch Module in Segmente aufgeteilt. Das Material kann nur durch Bohrungen in den Modulen von einem Segment in das andere gelangen. Anfang und Ende der Bohrungen sind so angeordnet, dass eine Durchmischung stattfindet. Die Anzahl der Kanäle (Bohrungen) beträgt vier.[1]
Die Mischer sind entweder aus für die Medien geeignetem Metall oder aus Kunststoff, dann in der Regel als Einwegprodukte, gefertigt.
Auslegung
Die Auswahl des geeigneten Mischertyps und die optimale Geometrie wird in erster Linie bestimmt von:
- den Eigenschaften der zu mischenden Fluide, insbesondere der Viskosität und der Dichte
- der angestrebten Mischgüte
- der zur Verfügung stehenden Einbaulänge und dem Rohrdurchmesser
- den gewünschten Betriebsdrücken
- der Durchflussmenge
- der Verweilzeit im Mischer bei reaktiven Gemischen.
Als Maß für die Mischgüte wird meist der Variationskoeffizient zugrunde gelegt, wobei die mittlere Konzentration einer Komponente ist und deren Standardabweichung. Eine ideale Durchmischung würde also bei vorliegen. Der Variationskoeffizient nimmt mit steigender bezogener Mischerlänge , dem Verhältnis zwischen absoluter Mischerlänge und Durchmesser des Mischers, exponentiell ab. D. h. je länger der Mischer und umso kleiner der Durchmesser, desto besser ist die Mischwirkung. Ist die Strömungsgeschwindigkeit so groß, dass die Reynoldszahl den für diese Mischer kritischen Wert 100–200 erreicht, treten turbulente Strömungen auf. Diese verbessern die Mischgüte weiter.[3][5]
Für Kenics- und Sulzer SMV-Mischer sind folgende Messwerte verfügbar:[3]
für Kenics | für Sulzer SMV | |
---|---|---|
, laminare Strömung | 17 | 9 |
, turbulente Strömung | 3,7 | 1,1 |
, laminare Strömung | 29 | 18 |
, turbulente Strömung | 7,3 | 1,9 |
Eine Verbesserung der Mischgüte durch Verringerung des Durchmessers findet ihre Grenzen im dadurch bedingten Anstieg des Druckverlustes im Mischer. Mit dem Druckverlust steigen auch die notwendigen Förder- und Betriebsdrücke. Im laminaren Bereich gilt
wobei die mittlere Strömungsgeschwindigkeit, die dynamische Viskosität des Fluids und den Druckverlustbeiwert darstellt. Eine Halbierung des Durchmessers bedeutet also eine Vervierfachung des Druckverlustes, bzw. gar eine Versechzehnfachung, wenn der Volumenstrom durch eine Erhöhung der Strömungsgeschwindigkeit gleich bleiben soll.
Das Produkt ist im laminaren Bereich konstant und abhängig vom Mischertypen:[3]
Kenics | Sulzer SMV | Sulzer SMX | Ross-ISG | leeres Rohr | |
---|---|---|---|---|---|
450 | 5600 | 4000 | 12000 | 64 |
Aus den Zusammenhängen ergibt sich, dass man z. B. einen X-Mischer und Sulzer SMV als sehr kompakten Mischer bauen kann. Der Sulzer SMV Mischer zeigt im Vergleich aber einen hohen Druckverlust. Für hochviskose Medien eignen sich eher X- und Kenics-Mischer mit den niedrigeren Druckverlusten.
Vor- und Nachteile
Gegenüber dynamischen Mischern wie z. B. Rührwerken weisen statische Mischer einige Vorteile auf. Sie sind kostengünstig, nehmen nicht viel Raum ein, sind bauartbedingt wartungsfrei, benötigen keine Energieversorgung und lassen sich direkt in Förderleitungen integrieren. Mit ihnen ist es vor allem möglich, kontinuierlich und mit kurzer, wenig variierender Verweilzeit Komponenten über einen großen Viskositätsbereich zu mischen.[6] Beim Rühren in separaten Mischbehältern sind dagegen nur chargenweise Abläufe möglich: die Behälter müssen erst gefüllt werden, darauf erfolgt der eigentliche Mischvorgang und erst dann steht die fertige Mischung zur Verfügung. Insbesondere bei der Verarbeitung von härtbaren Stoffen mit begrenzter Topfzeit wie z. B. Gießharz sind statische Mischer von Vorteil. Das Material wird dabei direkt aus dem Mischer in die Form gefüllt oder aufgetragen, die Komponenten kommen also erst unmittelbar vor der Verarbeitung miteinander in Kontakt, ein Ansetzen auf Vorrat entfällt.
Nachteilig ist, dass normalerweise keine Beeinflussung der Vermischungsintensität möglich ist, während bei Rührern die Drehzahl verändert werden kann. Bei der Verarbeitung aushärtender Stoffe können sich statische Mischer während Fertigungsunterbrechungen zusetzen. Sie müssen deswegen gespült oder aber als Einwegprodukte ausgeführt werden.
Entstehungsgeschichte und Anwendungen
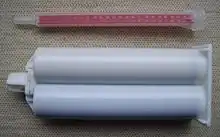
Bereits 1924 wurde eine Wendel in einem Rohr zu Mischzwecken eingesetzt.[7] Die erste Patentanmeldung für einen statischen Mischer nach dem Kenics-Prinzip erfolgte 1965 durch das Unternehmen Arthur D. Little.[8] Der Anwendungszweck war das Vermischen von Kunstharzen in Kleinmengen z. B. für Reparaturarbeiten. Die Kenics Corporation stellte daraufhin diese Mischer in Lizenz aus Edelstahl her. Ab den 1970er Jahren konnten sie auch als Einwegprodukte aus Kunststoff gefertigt werden.[9]
Neben dem Verarbeiten von Harzen, Klebstoffen, Abdichtmassen usw. umfasst das Anwendungsspektrum statischer Mischer heute alle verfahrenstechnische Bereiche mit Mischvorgängen z. B. in der chemischen Industrie, Lebensmittelindustrie, Wasser- und Abwasseraufbereitung (z. B. Anreichern von Wasser mit Sauerstoff), Öl- und Gasindustrie. In der Kunststofftechnik finden statische Mischer Einsatz in Vergussanlagen und zum Mischen von Polymerschmelzen[10].
Literatur
- F. A. Streiff: Statisches Mischen. In: Matthias Kraume (Hrsg.): Mischen und Rühren: Grundlagen und Moderne Verfahren. Wiley-VCH, Weinheim 2003, ISBN 978-3-527-30709-8 (eingeschränkte Vorschau in der Google-Buchsuche)
- Alain Georg und Martin B. Däscher: Chemische Reaktionen in Rohrreaktoren und statischen Mischern – Homogenität, Verweilzeitverhalten, Wärmeabfuhr, Auslegung, Anwendungsbeispiele. Chemie Ingenieur Technik, Volume 77, Issue 6, pages 681–693, June, 2005 Auflage. WILEY-VCH Verlag GmbH & Co. KGaA, Weinheim 2005.
Weblinks
Einzelnachweise
- F. A. Streiff: Statisches Mischen. In: Matthias Kraume (Hrsg.): Mischen und Rühren: Grundlagen und Moderne Verfahren. Wiley-VCH, Weinheim 2003, ISBN 978-3-527-30709-8 (eingeschränkte Vorschau in der Google-Buchsuche)
- Hans Günther Hirschberg: Handbuch Verfahrenstechnik und Anlagenbau: Chemie, Technik und Wirtschaftlichkeit. Springer, Berlin/Heidelberg/New York/Barcelona/Hong Kong/London/Mailand/Singapur/Tokio 1999, ISBN 3-540-60623-8, S. 863–867 (eingeschränkte Vorschau in der Google-Buchsuche)
- Marko Zlokarnik: Rührtechnik: Theorie und Praxis. Springer, Berlin/Heidelberg/New York/Barcelona/Hong Kong/London/Mailand/Singapur/Tokio 1999, ISBN 978-3-540-64639-6, S. 286–291 (eingeschränkte Vorschau in der Google-Buchsuche)
- Patentanmeldung EP2286904A1: Statische Mischvorrichtung für fliessfähige Stoffe. Angemeldet am 12. August 2009, veröffentlicht am 23. Februar 2011, Anmelder: Fluitec Invest AG, Erfinder: Alain Georg et Al.
- Matthias Kraume: Transportvorgänge in der Verfahrenstechnik: Grundlagen und apparative Umsetzungen. Springer, Berlin/Heidelberg/New York, 2003, ISBN 978-3-540-40105-6, S. 529–533 (eingeschränkte Vorschau in der Google-Buchsuche)
- Manfred H. Pahl, Edgar Muschelknautz: Einsatz und Auslegung statischer Mischer. In: Chemie Ingenieur Technik. Band 51, Nr. 5, Mai 1979, Wiley-VCH, S. 347–364
- Patent US1626487A: Emulsifier. Angemeldet am 10. Januar 1924, veröffentlicht am 26. April 1927, Erfinder: David Warren.
- Patent US3286992A: Mixing Device. Angemeldet am 29. November 1965, veröffentlicht am 22. November 1966, Anmelder: Arthur D. Little Inc, Erfinder: Constantine D. Armeniades, Wiliam C. Johnson und Thomas Raphael.
- Irving J. Arons: The Disposable "Motionless Mixer". In: ADL Chronicles – A presentation of the products and inventions that came out of the laboratories of Arthur D. Little, Inc. ADL Chronicles, 23. Juli 2008, abgerufen am 7. Mai 2012 (englisch).
- Friedrich Johannaber, Walter Michaeli: Handbuch Spritzgießen. 2. Auflage. Hanser, München 2004, ISBN 3-446-22966-3, S. 820–822 (eingeschränkte Vorschau in der Google-Buchsuche)