Phenoplast
Phenoplaste (DIN-Kurzzeichen: PF für Phenol-Formaldehyd) sind duroplastische Kunststoffe, die auf Basis von Phenolharzen durch Aushärtung hergestellt werden. Phenolharze (PF-Harze, Phenol-Formaldehyd-Harze) sind Kunstharze (Kondensationsharze), die durch Polykondensation aus Phenolen und Aldehyden hergestellt werden.[1] Wichtige Ausgangsstoffe zur Herstellung der Harze sind Phenol und Formaldehyd.
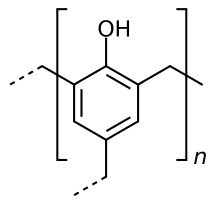
Geschichte
Phenoplaste zählen zu den ersten industriell erzeugten Kunststoffen. Der erste im großen Maßstab produzierte Phenoplast ist das 1907 von Leo Hendrik Baekeland erfundene Phenol-Formaldehyd-Kondensationsharz, das unter dem Warenzeichen Bakelit vermarktet und jahrzehntelang in vielen Bereichen eingesetzt wurde. Phenoplaste sind wegen ihrer Temperaturbeständigkeit, Oberflächenhärte und dem günstigen Preis auch heute die wichtigsten Duroplaste[1] und werden unter anderem zur Herstellung von Bremsbelägen verwendet.
Herstellung
Phenoplaste bestehen aus ausgehärteten Phenolharzen, die man durch die Synthese von Phenolen mit Aldehyden erhält.[2] Neben Phenol werden auch Verbindungen wie 3-Cresol, 3,5-Xylenol oder Resorcin verwendet.[3]
Durch eine elektrophile Substitution von Phenol werden säurekatalysiert Vorprodukte gebildet, die abhängig von der eingesetzten Formaldehydmenge ein bis drei Hydroxymethylgruppen (–CH2–OH) tragen. Als saure Katalysatoren werden u. a. Salzsäure oder Oxalsäure eingesetzt.[4] Die Substitution erfolgt nur in ortho- oder para-Stellung des Phenols:
Es bildet sich o-Hydroxymethylphenol (1) und p-Hydroxymethylphenol (2). Bei einem Überschuss an Formaldehyd und unter basischen Bedingungen können sich Verbindungen mit bis zu drei Hydroxymethylgruppen bilden. Durch katalysierte Polykondensation dieser Phenol-Derivate bilden sich die Harze. Je nach gewünschtem Ergebnis werden die Vorkondensate dann mit sauren oder basischen Kondensationsmitteln versetzt.
Novolake: In saurer Umgebung bilden sich aus den Phenylalkoholen durch Kondensation über Methylengruppe (–CH2–) verknüpfte Oligomere, die sogenannten Novolake. Formaldehyd und Phenole werden im Verhältnis 4:5 oder weniger Formaldehyd umgesetzt:
Novolake sind halbflüssig oder noch schmelzbar. Sie sind lagerstabil, also nicht selbsthärtend. Zusammen mit Formaldehydspendern wie Hexamethylentetramin härten Novolake bei Temperaturen oberhalb von 120 °C zu unschmelzbaren, duroplastischen Massen aus.
Resole: Mit basischen Kondensationsmitteln bilden sich dagegen schmelzbare und in vielen Lösemitteln lösliche Harze, die Resole. Durch die meist eingesetzten größeren Formaldehydmengen (bis 2,5:1) werden neben Methylengruppen auch Ethergruppen gebildet.
Allgemeine Struktur von Resol
Resole neigen zur Selbsthärtung durch weitere Kondensation und bilden die Zwischenstufe Resitol. Werden die Vorkondensate erhitzt, erhält man unter weiterer Abspaltung von Wasser vernetzte Polymere, die unschmelzbare und unlösliche Endstufe, das Resit.
Nach einer Aushärtung eines Harzes bilden sich engmaschig vernetzte Polymere, da die Phenolgruppen mit bis zu drei Methylengruppen untereinander verbunden sind.
Mögliche Struktur eines Phenoplast. Gestrichelte Linien deuten die Fortsetzung des Makromoleküls an.
Eigenschaften
- Dichte: 1,30 … 1,45 g/cm³
- hart, sehr bruchfest
- gelb bis braun; dunkelt unter Lichteinwirkung nach
- nur spanabhebende Bearbeitung möglich
- Brennprobe: meist flammwidrig; gelbliche Flamme; sprüht leicht Funken; Material reißt und platzt knackend und verkohlt; Geruch nach Phenol und Formaldehyd
Verwendung

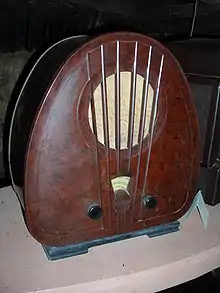
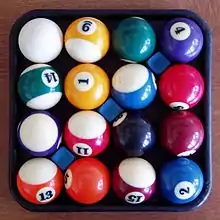
- Harzformteile
- Durch Füllstoffe wie Holzmehl, Ruß, Graphit, Quarzsand, Glasstaub oder Textilfasern erhalten die Phenoplaste mehr Substanz und eine größere Festigkeit. Die Harze bilden zusammen mit den Zusatzstoffen Pressmassen und werden im Pressverfahren zur Produktion von stabilen, hitzeresistenten und relativ schweren Kunststoffteilen verwendet. Bei geringen Mengen von Zusatzstoffen sind auch Spritzgussverfahren möglich. Mit Füllstoffen werden formgepresste Produkte wie Griffe und Gehäuseteile wärmebeanspruchter Haushalts- und Elektrogeräte, Billardkugeln und Kegelkugeln hergestellt.
- Schichtpressstoffe
- Zur Herstellung von Faserverbundwerkstoffen werden Holz-, Papier- oder Gewebebahnen in mehreren Bahnen übereinandergelegt, mit dünnflüssigem Phenolharz getränkt und gepresst. Bei Temperaturen ab 150 °C härtet der Werkstoff aus. Daraus entstehende Produkte sind beispielsweise Hartpapier und daraus gefertigte Leiterplatten, Hartgewebe für Maschinenteile und Isolierstoffe, Kunstharzpressholz (imprägniertes Holz). Phenolharz-Faserverbundwerkstoffe mit Kohlenstofffasern dienen als Hitzeschutzschilde mit Hochtemperaturbeständigkeit für Flugzeug- und Raketenbau. Auch PKW-Karosserieteile, zum Beispiel des Trabant, bestanden aus diesem Faserverbund (Phenoplast und Baumwollfasern).
Reine Phenolharze werden u. a. für die Herstellung von Lacken, Klebstoffen, Spachtelmassen und Schaumstoffen verwendet.
Umweltrelevanz
Während die ausgehärteten Produkte weitgehend frei von Schadstoffabgaben sind, wird bei Erhitzung (Bearbeitung, Brandfall, Versagen von Isolierstoffen) unter anderem Phenol und Formaldehyd frei, also die beiden giftigen Ausgangsstoffe.[5]
Bekannt ist auch die allmähliche Formaldehyd-Ausgasung von Spanplatten, Sperrholz, OSB-Platten und MDF-Platten des Möbel- und Innenausbaus aufgrund nicht vollständig chemisch abgebundenen Klebers. Hier wird teilweise mit Phenolharz-Klebstoffen gearbeitet. Der Harzanteil beträgt bis etwa 12 %.[6] Aus diesem Grund sind diese Stoffe auch problematisch im Hausbrand. Das Verbrennen im eigenen Ofen oder im Garten gilt als Unerlaubter Umgang mit Abfällen (Strafgesetzbuch § 326).
Handelsnamen
Aramith, Bakelit, Erinoplast, Catalin, Kerit, Pertinax, Plastacart, Plastaflex, Prestofol, Resitex, Sprelacart, GESADUR, Linax, Novotex, Resinol, Supraplast, Ruwatex, Prefere, Vyncolit, Phenodur, Uravar
Normen
- EN 13166 Wärmedämmstoffe für Gebäude – Werkmäßig hergestellte Produkte aus Phenolharzschaum (PF) – Spezifikation.
Derivate
Ein Copolymer aus Phenol, Formaldehyd und Harnstoff, das anschließend sulfonyliert wird, findet medizinische Anwendung als topischer Gerbstoff bei Intertrigo unter dem Handelsnamen Tannolact.
Weblinks
Einzelnachweise
- Wolfgang Kaiser: Kunststoffchemie für Ingenieure. Von der Synthese bis zur Anwendung. 3. Auflage. Carl Hanser, München 2011, ISBN 978-3-446-43047-1, S. 411 ff.
- Manfred D. Lechner, Klaus Gehrke, Eckhard H. Nordmeier (Hrsg.): Makromolekulare Chemie. Ein Lehrbuch für Chemiker, Physiker, Materialwissenschaftler und Verfahrenstechniker. 4., überarbeitete und erweiterte Auflage. Birkhäuser, Basel u. a. 2010, ISBN 978-3-7643-8890-4, S. 130–132.
- Hans-Dieter Jakubke, Ruth Karcher (Hrsg.): Lexikon der Chemie. A bis Z. Spektrum – Akademischer Verlag, Heidelberg u. a. 2001, ISBN 3-8274-1152-1.
- Karlheinz Biederbick: Kunststoffe. 4., neubearbeitete und erweiterte Auflage. Vogel, Würzburg 1977, ISBN 3-8023-0010-6, S. 136.
- Information des Ingenieur- und Sachverständigenbüros Wolfgang Gabler zu Brandrauch verschiedener Plastwerkstoffe, abgerufen am 8. Juni 2020
- Gerhard Holzmann, Matthias Wangelin, Rainer Bruns: Natürliche und pflanzliche Baustoffe, Springer-Verlag 2012, 394 Seiten, Seite 32