Widerstandsschweißen
Widerstandsschweißen ist ein Schweißverfahren für elektrisch leitfähige Werkstoffe auf Basis der jouleschen Stromwärme eines durch die Verbindungsstelle fließenden elektrischen Stromes.
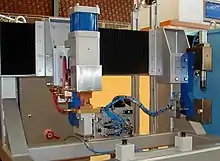
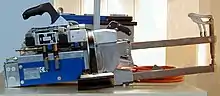
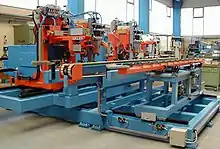
Die Verbindungspartner werden bis zum Erreichen der Schweißtemperatur erhitzt und an der Berührungsstelle unter der Wirkung einer Kraft durch Erstarren von Schmelze, durch Diffusion oder auch in fester Phase verschweißt.
Verfahrensvarianten beim Widerstandsschweißen
Alle Varianten des Widerstandsschweißverfahrens nutzen die Wärme, die vom konzentrierten lokalen Stromfluss durch die zu verbindenden Kontaktstelle erzeugt wird. Die an der oder den Kontaktstellen entstehende Wärme berechnet sich nach:
mit
- Schweißenergie ,
- Schweißstrom ,
- Widerstand an der Schweißstelle ,
- Schweißzeit .
Sie unterscheiden sich durch die Art der Stromzufuhr und durch den ausgenutzten physikalischen Verbindungsmechanismus.
DIN 1910/ ISO 857 | EN ISO 4063 | |
---|---|---|
Widerstandsschweißen | R | 2 |
Widerstandspunktschweißen | RP | 21 |
Rollennahtschweißen | RR | 22 |
Widerstandsbuckelschweißen | RB | 23 |
Abbrennstumpfschweißen | RA | 24 |
Pressstumpfschweißen | RPS | 25 |
Widerstandsbolzenschweißen | RBO | 782 |
Die DIN 1910–100[1] unterteilt das Metallschweißen und damit auch die Widerstandsschweißverfahren in Preß- und Schmelzschweißverfahren. Für die Schweißverfahren werden nach der EN ISO 4063[2] Ordnungsnummern vergeben. Das Bild zeigt Beispiele der Untergliederung mit den Ordnungsnummern für einige Verfahrensvarianten des Widerstandsschweißens:
- Widerstandspressschweißen: im Allgemeinen ohne Zufuhr eines Zusatzwerkstoffes, jedoch mit einer Anpresskraft auf die Schweißpartner:
- Widerstandspunktschweißen
- Widerstandsbuckelschweißen
- Widerstandsbolzenschweißen
- Widerstandsrollennahtschweißen
- Widerstandsstumpfschweißen
- Abbrennstumpfschweißen
- Kondensator-Impulsschweißen (sowohl Punkt- als auch Buckelschweißen)
- Widerstandsschmelzschweißen: ohne Presskraft, Zusatzwerkstoff möglich:
- Kammerschweißen
Stromarten beim Widerstandsschweißen
Wechselstrom
Die klassische Widerstandsschweißtechnik verwendet Wechselstrom (AC) mit einer Frequenz von 50 Hz (oder 60 Hz). Dieser kann einfach mittels entsprechend leistungsstarker Transformatoren aus dem Netz erzeugt werden. Für die meisten Anwendungen ist diese Stromart zwar geeignet, Strom und Schweißzeit werden jedoch durch Phasenanschnittsteuerung mit einem Thyristorsteller gesteuert, weshalb die Zeit- und Stromregelinkremente minimal 10 ms (bzw. 8,3 ms) betragen, was für präzise Steuerung oft zu lang ist.
Gleichstrom
Um eine rasche und gleichmäßige Einbringung der Energie zu gewährleisten, wird auch Gleichstrom (DC) verwendet. Dessen Erzeugung ist jedoch aufwändiger und damit teurer. An DC-Quellen unterscheidet man hauptsächlich:
- Einphasengleichrichter (selten, schlechte Qualität des Gleichstroms)
- Frequenzwandler (heute kaum noch üblich, können je nach Einstellung DC-Impulse oder Niederfrequenz erzeugen → dann AC)
- Dreiphasengleichrichtermaschinen, mit einem dreiphasigen Schweißtransformator und dreiphasigem Gleichrichter
- Inverteranlagen (MFDC = Mittelfrequenz-Anlagen, üblicherweise mit Gleichspannungszwischenkreis und 1000–4000 Hz Taktfrequenz des Wechselrichters, mit höheren Frequenzen, bis 20 kHz – dann HFDC = Hochfrequenz-Anlagen genannt) und Gleichrichtung (DC) am Ausgang des entsprechenden Transformators.
Bei MFDC und HFDC eingesetzte Inverter werden in der Regel mit Dreiphasen-Wechselstrom (z. B. 400 V) versorgt. Die Spannung wird gleichgerichtet und IGBT erzeugen daraus eine Rechteckspannung von 1 bis 20 kHz.[3] Diese Spannung (im Allgemeinen 400 V) gelangt anschließend in einen geeigneten Transformator. Aufgrund der höheren Frequenz ist er leichter und effizienter als ein netzfrequenter Transformator. Ausgangsseitig muss gleichgerichtet werden, da ansonsten die Induktivität der Stromzuführungen zu den Schweißelektroden den Strom zu sehr begrenzen würde.
Kondensatorentladung
Die Gleichstromversorgung beim Widerstandsschweißen kann auch durch Kondensatorentladung vorgenommen werden. Aufgeladene Kondensatorbatterien geben dabei impulsförmig ihre Energie ab. Es sind aber auch Schaltungen zur Umpolung der Stromrichtung entwickelt worden, die eine Wechselstromschweißung ermöglichen.[4]
Widerstandspunkt- und Buckelschweißen
Widerstandspunktschweißen
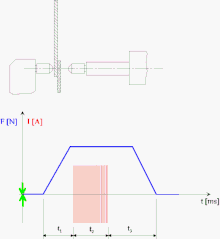
Widerstandspunktschweißen (Kurzform: Punktschweißen, RP, EN ISO 4063 [2]: Prozess 21) ist ein Widerstandspressschweißverfahren zum Verschweißen von Blechen unterschiedlichster Abmessungen und Materialien.
Das Widerstandspunktschweißen wird zur Verbindung von Blechen im Karosserie- und Fahrzeugbau und allgemein in der blechverarbeitenden Fertigung angewendet. Es wird auch zum Verschweißen unterschiedlichster Metalle und Metallkombinationen in der Elektroindustrie und der Elektronikfertigung verwendet, z. B. bei der Herstellung von Kondensatoren, Kontaktsätzen für Relais und Leitungsschutzschalter oder Anschlüssen von Spulen und Motorwicklungen. Mit gewissen Einschränkungen können auch ansonsten nicht verschweißbare Materialien miteinander verbunden werden.
Das Prinzip besteht darin, dass den zu verschweißenden Metallteilen über Elektroden unter der Wirkung von Kraft Strom zugeführt wird. Durch die Widerstandserwärmung werden die Verbindungspartner bis zum Erreichen der erforderlichen Schweißtemperatur erhitzt. Die Teile werden an ihrer Berührungsstelle zwischen den Elektroden unter der Wirkung einer Elektrodenkraft punktförmig durch Erstarren von Schmelze, durch Diffusion oder in fester Phase verschweißt. Innerhalb relativ kurzer Zeit wird eine hohe Energie in Form von joulescher Stromwärme auf eine kleine Fläche der Werkstücke konzentriert, wobei unter Zuführung von hohem Druck die unlösbare Verbindung entsteht.
Widerstandsbuckelschweißen
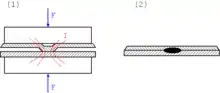
Widerstandsbuckelschweißen (Kurzform: Buckelschweißen, RB, EN ISO 4063 [2]: Prozess 23) ist ein Widerstandspressschweißverfahren zum Verschweißen von Blechen miteinander oder mit Schweißmuttern und von Drähten unterschiedlichster Abmessungen und Materialien.
Im Unterschied zum Widerstandspunktschweißen wird beim Widerstandsbuckelschweißen die zum Schweißen notwendige Stromdichte nicht durch die Elektroden, sondern durch die Bauteilform generiert. Die Elektroden dienen beim Widerstandsbuckelschweißen nur der Stromzuführung und der Krafteinbringung. Der prinzipielle Aufbau von Buckelschweißmaschinen entspricht dem von Widerstandspunktschweißgeräten. Varianten des Widerstandsbuckelschweißens sind unter anderem die Kreuzdrahtschweißung, bei der Drahtgeflechte zusammengeschweißt werden, und die Ringkantenschweißung.
Kondensatorimpulsschweißen
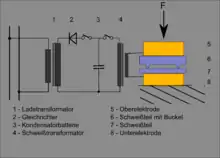
Das Kondensatorimpulsschweißen, als CD-Schweißen (engl. capacitor discharge) oder KE-Schweißen (Kondensatorentladungsschweißen) und in spezieller Anwendung auch Perkussionsschweißen bezeichnet, unterscheidet sich vom konventionellen Widerstandsschweißen durch die Art der Energieerzeugung. Es findet vor allem beim Buckel- oder Stumpfschweißen Anwendung. Nicht verwechselt werden darf das Kondensator-Impulsschweißen mit dem gleichfalls auf Kondensatorentladung beruhenden Lichtbogenbolzenschweißen, das ein Lichtbogenschweißverfahren ist, oder mit dem Schweißen mit elektromagnetischer Puls Technologie.
Zum Schweißen wird ein impulsförmiger Gleichstrom benutzt, der durch die Entladung eines Kondensators entsteht. Die im Kondensator gespeicherte Energie kann berechnet werden als:
mit
- W … Energie
- C … Kondensatorkapazität
- U0 … Ladespannung des Kondensators.
Die Energie wird von aufgeladenen Kondensatoren über einen Schweißtransformator auf das Werkstück abgegeben. Der Ladestrom kann hierbei um etliche Größenordnungen kleiner sein als der spätere Entladestrom, so dass eine Impulsbelastung des Stromnetzes und ggf. eine Überlastung vermieden werden können. In der Netzleitung entstehen keine hohen Stromspitzen, weil der Kondensator relativ langsam in den Schweißpausen geladen wird (1–2 s, je nach Bauart). Die Netzbelastung ist gering. Berücksichtigung sollte die Alterung der Kondensatoren finden, was nach einigen Jahren zu Kapazitätsverlust führt.
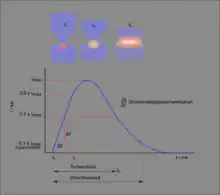
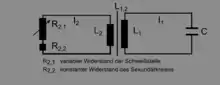
Der Schweißprozess hat zwei Prozessschritte:
- Laden des Kondensators
- Schweißen
Der Kondensator wird über den Ladespannungstransformator vor dem Schweißen aufgeladen. Mit der Ladespannung UL ist bei vorgegebener Kapazität C die für den Schweißprozess zu speichernde Energie festgelegt. Nach dem Aufladen wird die Schweißmaschine vom Ladungstransformator elektrisch getrennt.
Für das Schweißen wird zunächst die Elektrodenkraft F aufgebracht. Wird nun der Primärstromkreis zwischen dem Kondensator und Schweißformator geschlossen, fließt im Sekundärstromkreis durch die Kontaktfläche der Fügeteile der Strom Is(t), während die Elektrodenkraft F konstant bleibt.
Elektrisch betrachtet handelt es sich bei der Anordnung der elektrischen Baugruppen um einen gedämpften elektrischer Schwingkreis mit induktiver Kopplung in dem in relativ kurzer Zeit die im Kondensator gespeicherte elektrische Energie an der Schweißstelle in Wärme umgewandelt wird. Beim Buckelschweißen findet die größte Erwärmung an der Buckelspitze statt, da dort der größte Widerstand vorliegt. Der Wirkungsgrad beim KES-Schweißen ist hoch, da es kaum zu Energieabfuhr durch Wärmeleitung kommt. Wärmeeinflusszonen bleiben auf ein Minimum beschränkt.
Mit steigender Temperatur nimmt die Warmfestigkeit des Materials ab, die Buckeldeformation zu. Die Temperaturerhöhung wird verstärkt, da der spezifische elektrische Widerstand des Schweißgutes mit der Temperatur steigt. Bei Erreichen der Schmelztemperatur kommt es zum Verschweißen. Die zunehmende Buckeldeformation führt zu wachsender elektrischer Kontaktfläche der Fügeteile, damit zu sinkendem Widerstand und sinkender Temperatur. Diese Tendenz wird durch die Zunahme der spezifischen Wärmekapazität bei steigender Temperatur verstärkt. Wärmeleitung und abfallender Entladestrom bewirken ein rasches Abkühlen der verschweißten Fügeteile.
Während der Entladung kommt zu einem sehr steilen Stromanstieg und kurzen Schweißzeiten. Die kürzeste Schweißzeit ist etwa 1 ms. Der Schweißvorgang ist abgeschlossen, sobald die Kondensatoren entladen sind. Die Schweißzeit wird vom Beginn des Stromflusses an und bis zum Abfall des Stromes auf einen Wert von 50 % des Spitzenstromes gerechnet.[5] Die kurze Schweißzeit verursacht eine lokale Energiekonzentration bei einer kleinen Wärmeeinflusszone im Bauteil. Das ermöglicht das sichere Schweißen von hochfesten Stählen und verschiedensten Materialkombinationen, auch gut leitfähiger Schweißpartner unterschiedlichster Abmessungen.
Das Schweißen mittels eines Hochstromimpulses wird durch zwei Parameter gekennzeichnet:
- die Schweißkraft,
- die Schweißenergie
Die Schweißparameter werden auf die zu verschweißende Teile abgestimmt und entsprechend eingestellt. Die maximale Energie und der Höchstschweißstrom der Maschinen werden durch die Baugröße der Maschine bestimmt und sind unabhängig vom Netzanschluss.
Mit dem KE-Schweißen können Werkstücke unterschiedlicher Materialdicke aus verschiedenen Werkstoffen geschweißt werden (z. B. Stahl mit Messing). Auch legierte Edelstähle, hochkohlenstoffhaltige oder gehärtete Werkstücke lassen sich mit dem Verfahren verbinden.
Schweißausrüstung
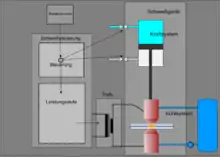
Zur Schweißausrüstung für das Widerstandsschweißen gehören ein mechanischer Maschinenkörper und ein elektrisches System, bestehend aus einem Leistungsteil und einer Steuerung.
Schweißgeräte
Schweißgeräte können stationäre Schweißmaschinen oder Schweißzangen unterschiedlichster Baugröße und verschiedenster Bauausführung sein. Stationäre Schweißmaschinen werden zum Punkt-, Buckel- und Rollennahtschweißen oder Stumpfschweißen in der Werkstattfertigung genutzt. Das jeweilige Schweißverfahren bestimmt die Bauart und die elektrischen und mechanischen Anforderungen an die Maschinen EN ISO 669.[6] Schweißzangen sind mobile Schweißgeräte zum Punktschweißen, die von Hand oder durch Manipulatoren – wie Industrieroboter – zum Schweißort geführt werden.
Steuerungen und Leistungsteile
Das Leistungsteil ist eine Einrichtung zur elektrischen Versorgung eines angepassten Schweißtransformators, der aus der hohen Netzspannung bei vergleichsweise niedrigem Netzstrom einen hohen Schweißstrom bei niedriger Schweißspannung erzeugt. Die Kraft und der Schweißstrom werden nach einem von der Schweißaufgabe vorgegebenen zeitlichen Ablauf von der Steuerung eingestellt.[7] Die Stromquellen können je nach Stromart und Anwendungsbedingungen sehr verschieden ausgeführt sein. Die Elektrodenkraft und der Schweißstrom müssen beim Punkt-, Buckel und Rollennahtschweißen nach einem von der Schweißaufgabe vorgegebenen zeitlichen Ablauf von einer Steuerung eingestellt werden. Das Leistungsteil und ein angepasster Schweißtransformator erzeugen aus der hohen Netzspannung bei vergleichsweise niedrigem Netzstrom einen hohen Schweißstrom bei niedriger Schweißspannung. Schweißsteuerung, Leistungsteil und ggf. Transformator sind oftmals in einem Gehäuse zusammengefasst, können aber auch als eigenständige Komponenten ausgebildet sein.
Netzfrequenzstromquellen
In Netzfrequenzstromquellen werden Thyristoren als Wechselstromsteller genutzt. Damit lässt sich die Spannung über eine Zündpunktverzögerung stufenlos ändern, so dass nur ein Teil jeder Spannungshalbwelle zum Schweißtransformator gelangt. Durch diesen Phasenanschnitt wird der Effektivwert der Sekundärspannung variabel und der Schweißstrom einstellbar. Der Stromfluss wird durch Antiparallelschaltung der Thyristoren gesteuert. Nach dem Nulldurchgang des Stromes wird der weitere Stromfluss gesperrt, bis der entsprechende Thyristor einen Zündimpuls erhält. Von diesem Zeitpunkt an wird der Verbraucher bis zum nächsten Nulldurchgang mit Energie versorgt. Je später der jeweilige Thyristor gezündet wird, desto geringer ist die mittlere Leistung.
Gleichstromquellen
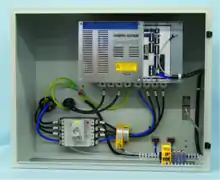
Es gibt verschiedene Ausführungen von Gleichstromquellen (s.[7]), von denen hier nur die Inverterstromquelle (Mittelfrequenz = MF, Hochfrequenz = HF) genannt wird. Bei Inverterstromquellen, die sich in den vergangenen Jahren mehr und mehr durchgesetzt haben, wird der Schweißtransformator mit einer Wechselspannung (1 kHz bis 4 kHz (MF) oder bis 20 kHz (HF)) eingespeist, die von einem Wechselrichter erzeugt wird. Die dreiphasige Wechselspannung wird zunächst in eine Gleichspannung und danach in eine einphasige Rechteckwechselspannung umgewandelt. Diese wird in den Schweißtransformator primärseitig eingespeist. Die Stromstärke wird durch Änderung der Pulsbreite eingestellt, wodurch sich der Effektivwert der Spannung und damit die Stromstärke im Sekundärkreis ändert. Unmittelbar nach dem Transformator wird gleichgerichtet, um induktive Spannungsabfälle in Kabel und/oder Zange zu vermeiden.
Vorteilhaft ist die wesentlich höhere Regelgeschwindigkeit (bei 1-kHz-Invertern wird eine Reaktionszeit des Leistungsstellers 0,5 ms gegenüber 10 ms bei 50-Hz-Schweißstromstellern erreicht). Ein weiterer technologischer Vorteil des Inverterschweißens ist die geringere Masse der Transformatoren, so dass es möglich ist, diese in die Schweißzangen zu integrieren, wodurch u. a. ein kleiner Sekundärkreis geringen induktiven Widerstand verursacht und keine schweren Sekundärkabel manipuliert werden müssen.
Stromquellen für das Kondensator-Impulsschweißen
Im Grundsatz handelt es sich um Gleichstromquellen, die für das Kondensator-Impulsschweißen genutzt werden. Das Prinzip besteht darin, dass eine Kondensatorbatterie zunächst aufgeladen und zum Schweißen über den Schweißtransformator und die Schweißstelle stoßartig entladen wird. Es ergibt sich ein hoher Energieeintrag zu Beginn der Schweißung bis zu einem Spitzenwert und nachfolgendes Abklingen des Stroms.
Die Stromquellen bestehen aus einer Komponente zur Gleichstromerzeugung, einer Kondensatorbatterie als elektrischen Energiespeicher, einem Thyristorschalter und einem speziellen Transformator.
Schweißpunktqualität und Gütesicherung beim Punkt- und Buckelschweißen
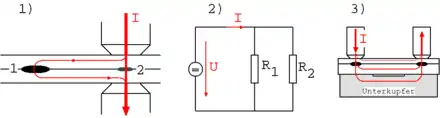
Ausschlaggebend für die Schweißpunktqualität sind neben vielen anderen Einflussgrößen die über die Schweißsteuerung eingegebenen Schweißparameter, die von der Art und Dicke der zu verschweißenden Bauteile, deren Anzahl, deren Passung zueinander, sowie von deren Oberfläche abhängig sind (beschichtet, galvanisiert, verzinkt).
Eine Rolle spielt auch die Kühlung der Punktschweißelektrode, die Temperatur des Kühlwassers und dessen Durchflussmenge.
Bei der Anordnung der Schweißpunkte auf dem Bauteil sollte die Möglichkeit eines Nebenschlusses berücksichtigt werden. Ein Teil des anliegenden Stroms kann dadurch unwirksam werden. Der Strom fließt nicht nur durch die aufzuschmelzende Schweißlinse, sondern auch daran vorbei. Ein typisches Beispiel sind Nebenschlusseffekte über bereits fertiggestellte Schweißpunkte (Abb. Nebenschluss 1) und 2)). Der über die Schweißpunkte i fließende Strom ist . Durch geeignete Wahl der Schweißpunktabstände kann der Nebenschlusseffekt hierbei verschwindend gering gehalten werden. Ist dies nicht möglich, so muss der anliegende Strom entsprechend erhöht werden, damit der erforderliche Schweißpunktmindestdurchmesser erreicht wird. Auch beim einseitigen Widerstandspunktschweißen (Abb. Nebenschluss 3)) tritt Nebenschluss auf. Verringern lässt sich bei dieser Schweißart der Nebenschlusseinfluss mittels einer Schweißanordnung „Bauteil mit geringer Wandstärke – Bauteil mit größerer Wandstärke – Unterkupfer“.
Auch muss der Verschleiß der Elektrode bei der Verfahrensdurchführung berücksichtigt werden: Mit zunehmender Anzahl von Schweißungen wird die Elektrode abgenutzt, wodurch sie ihren Querschnitt durch thermische und mechanische Einflüsse vergrößert, ihre Rauhigkeit zunimmt und durch "Anlegieren" ihre metallurgischen Oberflächeneigenschaften sich ändern. Dadurch werden die Stromdichte verringert und die Übergangswiderstände zwischen den Elektroden und der Blechoberfläche geändert, was zu sich änderndem thermischen Energieumsatz führt. Dieses Verhalten muss bei der Parametrierung der Steuerung berücksichtigt werden (Stepperfunktion[8]). Gegebenenfalls müssen die Elektrodenkappen nachgearbeitet werden, um den ursprünglichen Querschnitt zu erhalten und den Oberflächenzustand wiederherzustellen.[9] Dies geschieht in der Regel nach circa 300 gesetzten Schweißpunkten, hängt jedoch sehr von der Dicke des zu verschweißenden Materials, dessen Oberfläche und der thermischen Belastung ab. Die Abnutzung kann durch die richtige Wahl des Elektrodenmaterials verringert werden.
Je nach den zu verbindenden Materialien ist ihre Schweißeignung und Verbindungsqualität von den gewählten Elektrodenmaterialien abhängig.[10] Für das Kleinteil- und Mikroschweißen haben sich spezielle Elektrodenwerkstoffkombinationen als wirksam erwiesen.[11]
Schweißpunkte unterliegen angepasst an die Einsatzbedingungen der zu schweißenden Bauteile spezifischen Gütesicherungsnaßnahmen. Zu ihnen zählen die Verfahren der Werkstoffprüfung und der Online-Prozessüberwachung. Werkstoffprüfverfahren können zerstörend oder zerstörungsfrei durchgeführt werden. Zu den zerstörenden Prüfungen gehören die Meißelprüfung als Werkstattprüfung, verschiedene Formen des Zugversuches, Abroll- oder Torsionsversuche, metallurgische Schliffe. Auch sind dynamische Werkstoffprüfverfahren wie der Dauerschwingversuch gebräuchlich. Angewendete zerstörungsfreie Prüfverfahren sind die Ultraschallprüfung oder die aktive Thermografie. Bei der Schweißprozessüberwachung werden einige für die Qualität wesentliche physikalische Prozessgrößen wie Strom, Spannung, Widerstand, Elektrodenkraft, Elektrodenweg während des Schweißprozesses aufgezeichnet und hinsichtlich der erwartbaren Schweißpunktqualität bewertet.[12][13] Letztere Verfahren sind sehr viel kostengünstiger, können jedoch auch je nach Verfahren und seiner Anwendung falsch positive Resultate liefern.
Widerstandsrollennahtschweißen
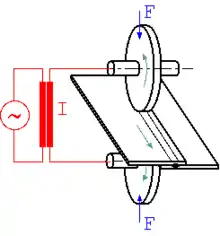
Das Widerstandsrollennahtschweißen (Kurzform: Rollennahtschweißen RR, Ordnungsnummer 22 nach der EN ISO 4063.[2]) ist ein Widerstandsnahtschweißen, das zu den Widerstandspressschweißverfahren zählt und aus dem Widerstandspunktschweißen abgeleitet wurde.[14] Die zum Schweißen erforderliche Kraft und der Strom werden durch Rollenelektrodenpaare, oder eine Rolle und einen Dorn oder eine Rollen- und eine Flachelektrode übertragen. Die als Rollen ausgebildeten Elektroden pressen die Bleche zusammen und leiten den Schweißstrom konzentriert in die Werkstücke. Dazu werden entsprechend ausgerüstete stationäre Schweißmaschinen verwendet.
Widerstandsstumpfschweißen
Auch die Widerstandsstumpfschweißmethoden basieren auf dem Prinzip der Widerstandserwärmung.
Pressstumpfschweißen
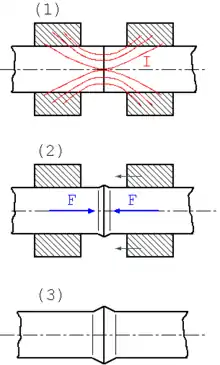
Das Pressstumpfschweißen (Ordnungsnummer 25 nach EN ISO 4063 [2]) dient zur Verbindung von begrenzten Querschnitten, etwa den Stirnseiten von Rundstäben, Drähten, Bolzen und den Enden der umgebogenen Drahtstücke zur Herstellung von Kettengliedern.[15]
Die zu verbindenden Bauteile werden fest in die Spannbacken des Schweißgeräts eingeklemmt, welche sowohl als Elektroden der Stromübertragung als auch dem Zusammenpressen der Teile dienen.
Indem die Bauteile aneinandergepresst werden, bildet sich ein guter Kontakt über die gesamte Querschnittsfläche aus. Durch den fließenden Strom werden die gesamten Kontaktstellen zugleich auf Schweißtemperatur (Aufschmelzen) erhitzt. Bei Erreichen der erforderlichen Temperatur über die gesamte Schweißquerschnittsfläche wird der Stromfluss unterbrochen und die Bauteile mittels Vorschubbewegung der Elektroden fest aufeinander gestaucht.
Die Pressstumpfschweißung zeichnet sich im Ergebnis durch einen gratfreien dicken Wulst aus. Die zu verschweißenden Bauteile müssen für ein optimales Schweißergebnis an der Stoßstelle sauber sein.
Abbrennstumpfschweißen
Eine Variation des Pressstumpfschweißens ist das Abbrennstumpfschweißen. Bei dieser Schweißmethode besteht während der Aufheizphase immer nur punktuell Kontakt zwischen den Bauteilen. Durch die daraus resultierende hohe Stromdichte wird an diesen Kontaktstellen das Material verflüssigt, verdampft, bzw. spritzerartig weggeschleudert. Die Bauteile brennen an der Schweißstelle also teilweise ab. Als Folge der laufenden Bildung und Zerstörung der Kontaktbrücken muss zwecks Kontakterhaltung auch während der Aufheizphase eine Vorschubbewegung der mit den Elektroden verbundenen Bauteile erfolgen. Nach Erreichen der erforderlichen Temperatur wird der Stromfluss unterbrochen und die Bauteile werden schlagartig aufeinander gepresst, so dass sie an der Verbindungsstelle aufeinander gestaucht werden. Vorteil dieser Methode ist, dass der Abbrand an der Kontaktstelle zugleich Verunreinigungen an der Schweißstelle beseitigt und das verdampfende Metall eine Schutzgasatmosphäre um die Schweißstelle bildet. Jedoch bildet das verflüssigte Material an der Stauchstelle zumeist einen Grat aus, der gegebenenfalls in einem gesonderten Arbeitsgang entfernt werden muss.
Kammerschweißen
Das Kammerschweißen ist ähnlich den genannten Widerstandsstumpfschweißmethoden. Die Bauteilenden werden in ein keramisches Rohr (Kammer) eingebracht, berühren sich, werden durch den fließenden Strom geschmolzen und unter stetigem Vorschub zusammengeschweißt. Anwendungsmöglichkeiten dieses Verfahrens sind z. B. das Verschweißen von Drahtseilenden oder Kabellitzen.
Im Gegensatz zu allen anderen hier beschriebenen Verfahren wird das Kammerschweißen laut Norm nicht zu den Widerstandspressschweißverfahren, sondern den Widerstandsschmelzschweißverfahren gezählt.
Arbeitsschutz
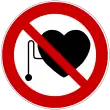
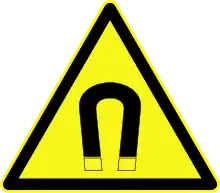
Alle Widerstandsschweißverfahren arbeiten mit geringen Spannungen (unterhalb der maximal zulässigen Berührungsspannung) und hohen Strömen. Deshalb ist ein direktes Berühren der schweißstromführenden Teile und der Werkstücke während der Schweißung grundsätzlich ungefährlich.
Gefahren beim Widerstandsschweißen können entstehen durch
- Schweißspritzer: aus der Schweißstelle herausgespritztes schmelzflüssiges Schweißgut (dabei handelt es sich nicht um elektrische Funken)
- Kraftwirkung: Möglichkeit der Quetschung der Hände im Bereich der Elektroden und Elektrodenarme
- Lärmemission durch Aufsetzen der Elektroden auf das Schweißgut und durch Ausblasen von Druckluft beim Betätigen druckluftbetriebener Krafterzeugungssysteme
- Dämpfe von organischen Beschichtungen auf dem Schweißgut. Aus diesen Gründen sind in der Regel Atemschutz (Absaugvorrichtungen oder Atemschutzmaske), Augenschutz (Schutzbrille oder Schutzschirm), Gehörschutz und ggf. Handschutz vorgeschrieben.
- Nach Trennung eines Schweißinverters vom Netz besitzt der Zwischenkreis noch eine berührungsgefährliche Spannung. Je nach Typ und Ausführungsform kann die Entladezeit bis zu mehreren Minuten betragen[7].
- Bei Öffnen der Schweißanlagen für das Kondensator-Impulsschweißen besteht die Gefahr eines lebensgefährlichen elektrischen Schlages, wenn die Kondensatoren nicht oder nur teilweise durch den Schweißvorgang entladen wurden. Sofern nicht geeignete Schutzmechanismen integriert wurden, besteht diese Gefahr auch bei abgeschaltetem Schweißgerät.
In unmittelbarer Nähe zu Widerstandsschweißeinrichtungen treten während der Schweißung starke Magnetfelder auf. In der Regel sind Arbeitsplätze an Widerstandsschweißeinrichtungen mit dem Verbotszeichen „Verbot für Personen mit Herzschrittmacher“ und den Warnzeichen „Warnung vor magnetischem Feld“ bzw. (fälschlicherweise) „Warnung vor elektromagnetischem Feld“ gekennzeichnet. Dies geschieht oft aus Vorsorgegründen und ist nicht zwingend Zeichen einer tatsächlichen Gefährdung. Ob für Träger aktiver Implantate wirklich eine Gefahr besteht oder eine Weiterbeschäftigung möglich ist, ist im Einzelfall zu prüfen.
Literatur
- M. Krause: Widerstandspreßschweißen. DVS-Verlag, Düsseldorf 1993, ISBN 3-87155-531-2.
- A. Kirchheim, A. Lehmann, R. Staub, G. Schaffner, N. Jeck: Kraftmessung beim Widerstandsschweißen. (pdf, 11,94 MB) In: 19. DVS Sondertagung, Sonderdruck. DVS, 27. Mai 2004, archiviert vom Original am 28. September 2007; abgerufen am 5. Juni 2020.
- N.N.: Taschenbuch DVS-Merkblätter und -Richtlinien, Widerstandsschweißtechnik. DVS-Verlag, Düsseldorf 2002, ISBN 3-87155-201-1.
- Manfred Beckert: Grundlagen der Schweißtechnik. Schweißverfahren. Verlag Technik, Berlin 1993, ISBN 3-341-00812-8.
- Ulrich Dilthey: Schweißtechnische Fertigungsverfahren. Band 1 Schweiß- und Schneidtechnologien. Springer Verlag, Berlin 2003, ISBN 3-540-21673-1.
- Hans-Jürgen Rusch: Reparaturschweißen. Vogel Buchverlag, Würzburg 2005, ISBN 3-8343-3019-1.
- Thoralf Winkler: Magnetfeldemission von Widerstandsschweißeinrichtungen. docupoint Verlag, Magdeburg 2007, ISBN 978-3-939665-09-0.
- BGI 5011. Beurteilung magnetischer Felder von Widerstandsschweißeinrichtungen. (pdf, 3,15 MB) Berufsgenossenschaft Energie Textil Elektro Medienerzeugnisse, November 2006, abgerufen am 5. Juni 2020..
- Lorenz Pfeiffer: Fachkunde des Widerstandsschweißens. Verlag W. Girardet, Essen 1969.
- Patent US451345: Method of Electric Welding. Veröffentlicht am 20. Juli 1909, Erfinder: Elihu Thomson (pat2pdf.org).
- Patent US928701: Uniting the Component Parts of Composite Sheet Metal Structures. Veröffentlicht am 20. Juli 1909, Erfinder: Adolph F. Rietzel (pat2pdf.org).
- Wolfgang Piersig: Geschichtlicher Überblick zur Entwicklung der Metallbearbeitung: Beitrag zur Technikgeschichte (8), GRIN Verlag, 2010 (eingeschränkte Vorschau in der Google-Buchsuche).
Weblinks
Einzelnachweise
- DIN 1910-100:2008-02: Schweißen und verwandte Prozesse - Begriffe - Teil 100: Metallschweißprozesse mit Ergänzungen zu DIN EN 14610:2005
- DIN EN ISO 4063:2011-03Schweißen und verwandte Prozesse - Liste der Prozesse und Ordnungsnummern
- http://www.matuschek.de/html/de/gleichstrom_hochfrequenz.htm
- Patent US6321167: RESISTANCE-WELDING POWER SUPPLY APPARATUS. Veröffentlicht am 1998, Erfinder: Takashi Jochi, Mikio Watanabe.
- DVS: Messen beim Punkt-, Buckel- und Rollennahtschweißen. DVS-Merkblatt 2908, 2006.
- DIN ISO 669:2001-06: "Widerstandsschweißeinrichtungen - Mechanische und elektrische Anforderungen"
- DVS: "Steuerungen und Leistungsteile für das Widerstandsschweißen", DVS-Merkblatt 2904, 2010
- Kleines Lexikon. (Memento vom 22. März 2014 im Internet Archive) Harms & Wende GmbH & Co. KG.
- GSI, IMWF: Standmengenerhöhung beim Widerstandsschweißen durch Elektrodenfräsen, FORSCHUNGSVORHABEN AiF-Nr. 13.134 N / DVS-Nr. 4.031
- DVS,Elektroden für das Widerstandsschweißen, Merkblatt, DVS 2903
- DVS, Widerstandsschweißen in der Elektronik und Feinwerkstechnik - Übersicht und Grundlagen, Merkblatt, DVS 2950
- D. Steinmeier: Resistance Welding - Weld Monitoring Basics-1. (PDF) microJoining Solutions – microTips™.
- Yi Ming Zhang: Real-time weld process monitoring. (= Woodhead Publishing Series in Welding and Other Joining Technologies. Nr. 62) 2008, ISBN 1-84569-268-3.
- DVS "Widerstands-Rollennahtschweißen - Verfahren und Grundlagen", DVS-Merkblatt 2906-1, 2006
- DVS: Pressstumpfschweißen von Stahl, DVS-Merkblatt 2931, 2008