Stahlerzeugung
Ziel der Stahlerzeugung ist es, aus Eisenerz und Roheisen eine Eisenlegierung mit bestimmtem Kohlenstoffgehalt (Stahl) mit innerer und oberflächlicher Reinheit herzustellen. Das Verfahren und der Kohlenstoffgehalt werden für die gewünschten Werkstoffeigenschaften, z. B. Umformbarkeit, Härte oder auch Rostbeständigkeit, nach dem Gießen oder Schmieden angepasst. Den Wirtschaftszweig der Stahlerzeugung nennt man Stahlindustrie.
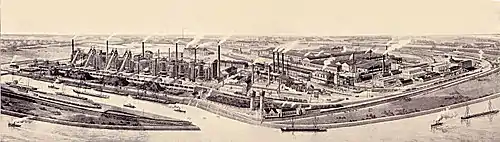
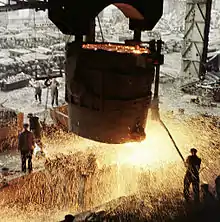
Ein Stahlwerk ist eine Fabrik in der Metallindustrie, die Stahl zumeist in Hochöfen oder Lichtbogenöfen produziert. Die Mitarbeiter eines Stahlwerks werden Stahlwerker oder Stahlkocher genannt. Die eingesetzten Verfahren zählen zur Metallurgie.
Stahl wird zunehmend in integrierten Stahlwerken hergestellt, die die Roheisen- und Rohstahlherstellung (Primärmetallurgie), die Stahlproduktion (Sekundärmetallurgie) und die Halbzeug-Fabrikation in einem Werk integrieren, um Transporte, Energie und damit Kosten zu sparen.
Die Stahlerzeugung ist für ca. 25 % der CO2–Emissionen im Industriesektor und ca. 8 % insgesamt verantwortlich.[1][2] Um die globale Erwärmung abzuschwächen, verwendet bzw. erprobt die Stahlindustrie eine Reihe von Technologien zur Dekarbonisierung. Dazu gehören die Nutzung von Wasserstoff, die Kohlenstoffabscheidung und -wiederverwendung sowie der breitere Einsatz von Lichtbogenöfen, die mit erneuerbarer Energie betrieben werden können.[3]
Geschichte
Die frühe Verhüttung von Eisenerz ist bereits für das 2. Jahrtausend v. Chr. im damaligen Hethiter-Reich belegt, wo auch um die Mitte des 1. Jahrtausends v. Chr. einfache schmiedbare Eisenwerkstoffe und erstmals ein einfacher härtbarer Stahl hergestellt wurde.[4] Eisen verdrängte allmählich die zuvor genutzten Kupferwerkstoffe (Bronze), da es als Stahl härtbar und gleichzeitig zäher ist. Eisenerze waren nahezu überall zu finden, während die zur Bronze-Herstellung benötigten Metalle Kupfer und Zinn selten waren und nicht an denselben Orten vorkamen. Zur Eisengewinnung wurde Holzkohle benötigt, die aus Holz gewonnen werden konnte. Genutzt wurde Eisen vor allem für Waffen sowie für Werkzeuge, weniger in der Landwirtschaft oder als Schmuck.
Antike
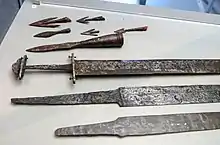
In der Antike und im Mittelalter wurde das Erz in mit Holzkohle beheizten Rennöfen bei Temperaturen von etwa 1250 °C verhüttet. Die ersten Typen wurden ungefähr 1500 v. Chr. gebaut. Diese waren Lehmöfen, in die Holzkohle und Eisenerz schichtweise eingebracht wurden. Im Rennofen entstehen Temperaturen zwischen etwa 1200 und 1300 °C, die das taube Gestein aufschmelzen und als Schlacke ablaufen lassen. Die Schmelztemperatur von reinem Eisen (1539 °C) wird nicht erreicht. Das Eisenerz wandelt sich im Rennofen in halbfestes Eisen sowie in flüssige Schlacke um, die verschiedene unerwünschte Bestandteile der Erze enthält. Der Ofen wurde bodennah angestochen, sodass die Schlacke herausrinnen konnte. Daher stammt die Bezeichnung Rennofen, von rinnen.
Das Produkt (Eisenschwamm oder Luppe genannt) war poröses, festes Roheisen, das noch Schlackereste enthielt, die durch Schmieden entfernt wurden. Danach wurde es als Schmiedeeisen bezeichnet, das beinahe keinen Kohlenstoff enthielt und dem heutigen Stahl recht nahekam, aber auf einem anderen Weg gewonnen wurde und daher stärker mit Begleitelementen verunreinigt war. Aristoteles unterschied jedenfalls bereits in der Meteorologica das Roheisen vom Schmiedeeisen, das keine Schlackereste mehr enthält.[5] Da das kohlenstoffarme Eisen für Werkzeuge und Waffen zu weich ist, wurde es auf Holzkohlen geglüht, wodurch es das Element Kohlenstoff vor allem in den Randschichten aufnahm und reduziert wurde. Auch das Härten durch Abschrecken in Wasser oder Öl war bekannt und wird von Plutarch (45–125 n. Chr.) korrekt durch das schnelle Abkühlen erklärt. Zuvor war Plinius der Ältere (23/24–79 n. Chr.) noch der Meinung, die Wasserqualität habe den entscheidenden Einfluss.[6] Der Name des gehärteten Eisens bzw. des Stahls war altgriechisch χάλυψ chalybs, deutsch ‚Schmiedeeisen‘; die Chalybes (Stahl-Leute) waren danach benannt.
Als neue Berufe entstanden Grob- und Feinschmiede, die nun Eisen nutzten, im Gegensatz zu den Kupferschmieden. Andere Schmiede spezialisierten sich auf bestimmte Produkte oder Produktgruppen. Dazu zählen der Werkzeug-, Messer-, Sichel-, Nagel-, Schwert-, Helm-, Lanzen- oder Pfeilschmied und Schlosser.[7] In der Antike wurden die notwendigen Arbeiten häufig von Sklaven verrichtet.[8]
Mittelalter
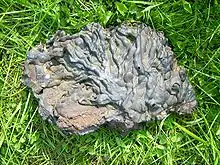
Zu Beginn des Mittelalters war die Arbeitsteilung noch wenig ausgeprägt. Grob- und Feinschmiede arbeiteten häufig in derselben Schmiede. Für die Landwirtschaft produzierte im Frühmittelalter das dörfliche Handwerk Sensen, Sicheln und Pflüge.[9] Ab etwa dem 12. Jahrhundert wurden die Öfen nicht mehr in die Erde, sondern oberirdisch gebaut (Vorläufer der Hochöfen) und zusätzlich durch wassergetriebene Blasebälge mit Luft versorgt. Für die Stahlbearbeitung wurden Hammerwerke, die durch Wind- oder Wassermühlen angetrieben wurden, entwickelt.
Der Benediktinermönch Theophilus Presbyter beschrieb im 11. Jahrhundert das Härten von Feilen: Zunächst wurde Ochsenhorn verbrannt und mit Salz vermischt und über die Feilen gestreut, die dann im Ofen geglüht wurden. Anschließend wurden sie in Wasser abgeschreckt und im Ofen angelassen.[10] Draht wurde ursprünglich wie in der Antike gedreht und geschmiedet. Im Mittelalter ging man zum Drahtziehen mit Zieheisen über, um die großen Drahtmengen herzustellen, die vor allem für Ringpanzer („Kettenhemden“) benötigt wurden.[11]
Im 14. Jahrhundert n. Chr. wurde in Europa der Holzkohle-Hochofen (Stückofen oder Wolfsofen) entwickelt. Er erreichte höhere Temperaturen und benötigte weniger Holzkohle. Das Eisenerz reagierte darin mit dem Kohlenstoff der Holzkohle. Die Hochofentemperatur lag dank des Kohlenstoffgehalts nun über der Schmelztemperatur, sodass erstmals flüssiges Roheisen entstand, das jedoch wegen des hohen Kohlenstoffgehalts von etwa 4 % nicht schmiedbar war. Es ähnelte dem heutigen Gusseisen und wurde auch in Formen gegossen. Um schmiedbares Eisen zu erhalten, wurde das Roheisen aus dem Hochofen nochmals im Frischfeuer geschmolzen. Die Eigenschaften des Eisens konnten gezielt durch Anlassen, Aufkohlen, Abschrecken und Glühen beeinflusst werden.
Frühe Neuzeit
Später war die Arbeitsteilung ähnlich wie in der Antike, wozu neue Berufe wie Huf-, Pfannen-, Pflug- und Zangenschmiede sowie Feilenhauer beitrugen.[12] Neben der beruflichen Arbeitsteilung gab es auch regionale Unterschiede. In der Gegend um Solingen lagen an Nebenläufen der Wupper zahlreiche durch Wassermühlen getriebene Hammerwerke, auf denen Klingen geschmiedet wurden. Die Schleifmühlen für die Klingen benötigten für die Fertigbearbeitung mehr Energie und lagen daher direkt an der Wupper. Diese getrennten Fertigungsstufen erforderten jedoch den Transport der geschmiedeten Klingen von den Nebenläufen bis zur Wupper, wodurch bis zu einer Wegstunde für den Transport aufgebracht werden musste.[13]
- Panzerhemdmacher
- Messerer
- Hufschmied
- Plattner
- Pfannenschmied
Industrialisierung
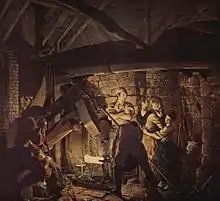
Die Herstellung gebrauchsfähigen Eisens aus Erzen geschah in mehreren Schritten:[14]
- Verhütten der Erze im Hochofen zu Roheisen,
- Frischen des Roheisens, um den Kohlenstoffgehalt zu reduzieren, und anschließend
- Ausschmieden und Walzen zu Stangen, Schienen oder Blechen.
Neu war die technische Umsetzung dieser Prozesse, die ab dem 18. Jahrhundert von Großbritannien ausgehend zunehmend auf Steinkohlebasis beruhte und daher Eisenwerkstoffe günstiger werden ließ und die Produktionsmengen erhöhte. Innerhalb der Produktionstechnik konnten Eisen oder Stahl nun als Konstruktionswerkstoff für Werkzeugmaschinen[15] genutzt werden, die dadurch präziser und leistungsfähiger wurden.
Für die Verhüttung der Erze im Hochofen war es notwendig, dass das Erz mit Kohle in Berührung kam, da der Kohlenstoff für chemische Reaktionen benötigt wurde. Bei Holzkohle, die fast ausschließlich aus Kohlenstoff besteht, war dies kein Problem, die günstigere Steinkohle jedoch war stark mit Schwefel und anderen Elementen verunreinigt, die das Produkt schlechter werden ließen.[16] Abraham Darby kam auf die Idee, Steinkohle zu verkoken. Als Hauptprodukt entstand dabei Koks, der für die Verhüttung der Erze genutzt werden konnte, als Nebenprodukt Teer. Als sich die Teergruben in der Nähe der Eisenhütten immer weiter füllten, wurden Chemiker darauf aufmerksam und fanden Methoden, daraus Teerfarben und Medikamente herzustellen.[17] Ein deutlich niedrigerer Kohle-/Koksverbrauch war mit dem Heißluftblasen von James Beaumont Neilson möglich. Hierbei wurde die dem Hochofen zugeführte Luft erhitzt, was höhere Temperaturen zur Folge hatte und besseren Stahl lieferte.[18]
Für das Frischen mit Steinkohle gab es zwei verschiedene Methoden, um das Eisen vor dem Schwefel der Steinkohle abzuschirmen. Ab 1740 entwickelte Benjamin Huntsman den Tiegelgussstahl,[19] bei dem Stahl unter Einhaltung einer genauen chemischen Zusammensetzung in einen Tiegel gegeben und mehrere Tage lang im Kohlefeuer erhitzt wurde. Im Tiegelofen entstand ein homogener Stahl ausgezeichneter Qualität vergleichbar dem Wootz. Wegen seiner relativ hohen Härte wurde er bevorzugt für Schneidwerkzeuge, aber auch für Ambosse, Hämmer und andere Werkzeuge genutzt. Er war jedoch sehr teuer und konnte nur in geringen Mengen erzeugt werden. Das Roheisen wird im seit 1742 angewendeten Gussstahlverfahren zusammen mit Schrott geschmolzen. Der Sauerstoffanteil im Schrott frischt das Roheisen und verbessert somit die Qualität des Stahls.
Puddelverfahren
.jpg.webp)
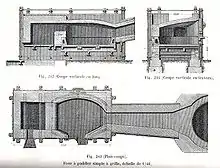
Das bedeutendere Verfahren war das Puddeln, das 1784 von Henry Cort in England erfunden wurde. Beim Puddeln wurde das Roheisen in großen Tiegeln auf einen Herd gegeben, unter dem Steinkohle verbrannt wurde. Das flüssige Roheisen wurde manuell mit Eisenstangen gerührt (= Puddeln), kam dabei mit dem Sauerstoff der Luft in Kontakt und verbrannte den im Eisen enthaltenen Kohlenstoff. Da das kohlenstoffarme Eisen einen höheren Schmelzpunkt hat, bildeten sich Klumpen, die schließlich zu Luppen anwuchsen und aus dem Herd geholt wurden. Um sicherzustellen, dass alle Teile der Schmelze gleichmäßig mit Sauerstoff in Kontakt kamen, mussten Arbeiter die Schmelze ständig kräftig umrühren, was viel Erfahrung erforderte. Von den Puddlern hing somit entscheidend die Qualität des erzeugten Stahls ab. Das Puddeln ermöglichte zwar größere Produktionsmengen als zuvor, war jedoch ein manuelles Verfahren, das sich nicht mechanisieren ließ, und bildete den Engpass in der gesamten Prozesskette vom Erz bis zum fertigen Produkt.[20]
Das durch Puddeln gefrischte Eisen wurde anschließend unter dem Schmiedehammer bearbeitet, um die Schlackereste zu entfernen und den Werkstoff homogener zu machen. Dieser Schmiedeprozess hatte ebenfalls großen Einfluss auf die Qualität des Stahls. Erst danach wurde er zu Blechen oder Schienen gewalzt.[21][22]
Die erste deutsche Gussstahlfabrik gründete Friedrich Krupp 1811 in Essen. Der Impuls für die sprunghafte Zunahme der Stahlproduktion erfolgte etwa in der Mitte des 19. Jahrhunderts durch die gleichzeitige Anwendung mehrerer technischer Erfindungen: Die Dampfmaschine stellte der Industrie eine leistungsstarke und flexible Arbeitskraft zur Verfügung, in den Kokereien wurde die Steinkohle zu Koks verarbeitet und die Entwicklung des Eisenbahnwesens sowie der Dampfschifffahrt förderten die Erreichbarkeit neuer, großer Absatzmärkte für Stahl. Neue Anwendungen des Eisens im 19. Jahrhundert waren Dampflokomotiven und Schienen sowie Brücken.[23]
Die Stahlindustrie hatte in allen Ländern, unabhängig von ökonomischen Erwägungen, eine enorme politische Bedeutung, da sie neben einem Indikator für die technisch-wirtschaftliche Entwicklung und der Bedeutung für die Rüstungsindustrie auch eine nationale Prestigefrage war. Die Bedeutung des Stahls für die damalige Zeit symbolisiert der Eiffelturm (allerdings wegen der hohen Anforderung an Bruchsicherheit noch aus Puddeleisen), der anlässlich der Pariser Weltausstellung von 1889 als ein Monument des technischen Fortschritts aus Stahl erbaut wurde.
Hochindustrialisierung und Massenstahlverfahren
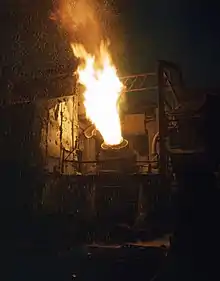
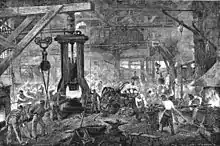
Die wichtigsten Neuerungen betreffen die Entwicklung von Verfahren zur Massenproduktion von günstigem und gleichzeitig hochqualitativem Stahl und die Rationalisierungsbewegung, die mit einer wirtschaftlicheren Produktion einherging.
Engpass der Stahlproduktion war nach wie vor das Frischen im Puddelofen. Roheisen konnte in guter Qualität und in ausreichenden Mengen in den stetig größer werdenden Hochöfen geschmolzen werden. Die Weiterverarbeitung des Puddeleisens in mechanisierten Walzwerken geschah ebenfalls zügig. Um die große Nachfrage aus dem Eisenbahnwesen zu befriedigen, unternahm man einige Versuche, das Puddeln ebenfalls zu mechanisieren, was jedoch nicht erfolgreich war. Die Erfahrung der Puddler konnte nicht einfach in Maschinen übertragen werden. Abhilfe kam durch drei konkurrierende Verfahren: Die beiden bodenblasenden oder windfrischenden Verfahren von Bessemer und Thomas sowie das Herdfrischen von Siemens und Martin.[24][25][26]
Bessemer-Verfahren
Henry Bessemer kam in den 1850er Jahren auf die Idee, das flüssige Roheisen in einen Konverter zu geben und durch Düsen im Boden Luft zu blasen. Der in der Luft enthaltene Sauerstoff verbrannte den Kohlenstoff und andere unerwünschte Begleitelemente in nur 20 Minuten und erhitzte gleichzeitig auch das Roheisen, sodass der gefrischte Stahl nun erstmals flüssig entstand und gegossen werden konnte. Der Vorgang, Luft durch Roheisen zu blasen, wird auch als Windfrischen bezeichnet. Nur mit Luft konnte man nun mit dem Bessemer-Verfahren die bis dahin höchsten Temperaturen im Hüttenwesen erzeugen und halten und hatte dabei nicht etwa wie früher Brennstoffe verbraucht, sondern auch noch Wärme erzeugt. Das Verfahren war daher deutlich günstiger. Außerdem war der Bessemer-Stahl von sehr guter Qualität: Er war sehr rein und homogen und hielt durch seine große Härte den Belastungen stand, denen er als Schienenmaterial ausgesetzt war. Schienen aus Puddeleisen mussten dagegen meist nach bereits 10 Jahren ausgetauscht werden. Vor allem in den USA entstanden in den späten 1860er und frühen 1870er Jahren zahlreiche Bessemeranlagen. Das Verfahren hatte allerdings zwei Nachteile. Es eignete sich nur für phosphorarme Erze, die vor allem in Deutschland selten waren, und der chemisch neutrale Stickstoff in der Luft löste sich im Gefüge des Stahls und führte dazu, dass er hart, aber auch spröde war. Außerdem verbrannte beim Frischen fast der gesamte Kohlenstoff, sodass Bessemer-Stahl nicht besonders fest war.
Thomas-Verfahren
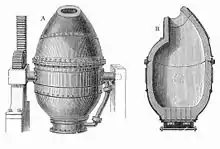
Das Thomas-Verfahren von Sidney Thomas und Percy Gilchrist war seit 1878 eine Variante des Bessemer-Verfahrens, die auch „basisches Windfrischverfahren“ genannt und durch die Konverterform, die Thomasbirne, bekannt wurde. Sie eignet sich für phosphorreiche Erze und wurde daher vor allem in Regionen an Rhein und Ruhr, in Belgien, Luxemburg und Lothringen bevorzugt genutzt. Im Thomasverfahren wurde eine Dolomit-Teer-Mischung für die Ausmauerung des Ofens verwendet, welche basisch wirkt. Es benötigte allerdings auch einen gewissen Mindestgehalt an Phosphor, sodass man in England und Amerika wenig Interesse daran zeigte, da hier entsprechende Erze nicht vorkamen. Thomas-Stahl war sogar noch etwas härter und spröder als Bessemer-Stahl und eignete sich eher für wenig belastete Fälle wie Draht oder Rohre und weniger für den Brücken- oder Schiffsbau.
Siemens-Martin-Verfahren
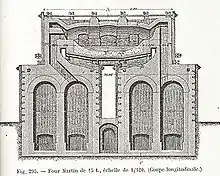
Eine Alternative zu den beiden bodenblasenden oder windfrischenden Verfahren war das Siemens-Martin-Verfahren, das zum Herdfrischen gezählt wird und nach den drei Brüdern des berühmten Werner von Siemens, Friedrich, Otto und Wilhelm sowie dem französischen Eisenhüttenmann Pierre Martin benannt ist. Das Siemens-Martin-Verfahren war die bevorzugte Stahlherstellungsmethode von seiner Erfindung im Jahr 1864 bis in die erste Hälfte des 20. Jahrhunderts.
Das Verfahren beruhte auf einem speziellen Ofenaufbau, einem Oberofen, vom Gewölbe überspanntem Schmelzraum und dem Unterofen. Im Oberofen wird flüssiges Roheisen, Roheisenmasseln oder Schrott chargiert. Im Oberofen wird mit öl- oder gasbetriebenen Brennern der Schmelzraum beheizt. Im Unterofen sind die sogenannten Regenerativkammern zur Luft- und auch zur Gasvorwärmung untergebracht.
Die zur Verbrennung notwendige Luftmenge wird in Regenerativkammern auf ca. 1200 °C erhitzt. Das Gas wird, getrennt davon in einer anderen Kammer, allerdings auf ein geringeres Temperaturniveau, ebenfalls erwärmt. Dies geschieht für beide Medien durch ein Gitterwerk aus aufgeheizten, feuerfesten Steinen in den Regenerativkammern. Die erhitzte Luft sowie das vorgewärmte Gas werden durch jeweils getrennte Kanäle einem von zwei Ofenköpfen zugeführt, vermischen sich dort und die Verbrennung findet statt. Die heißen Abgase werden dann über den gegenüberliegenden Ofenkopf in das zweite Regenarativkammersystem geleitet. Dabei wird das Gitterwerk der Kammern durch die Abgase aufgeheizt. Ist ein dann bestimmtes Temperaturniveau erreicht, wird durch eine Wechselklappe der kalte Luft- und Gasstrom umgelenkt und durch diese aufgeheizten Kammern dem zweiten Ofenkopf zur Verbrennung zugeführt – die Strömungsrichtung also umgekehrt. So wird das zuvor durch die kalten Medien abgekühlte erste Gitterwerk nun mit den Abgasen, welche bei der Verbrennung jetzt am zweiten Ofenkopf erzeugt werden, wieder aufgeheizt. Bei Erreichen eines bestimmten Temperaturniveaus wird dann die Durchströmungsrichtung in den Kammern erneut umgekehrt. Dieser Wechsel findet in regelmäßigen Zeitintervallen statt. Auf diese Weise konnten erhebliche Energieeinsparungen erzielt und dauerhaft Temperaturen gehalten werden, die über der Schmelztemperatur von Stahl lagen.
Man unterscheidet je nach dem verwendeten Einsatz das Schrott-Roheisen-Verfahren (Zugabe von festem oder flüssigem Roheisen und Schrott), das Roheisen-Erz-Verfahren (Zugabe von Erz oder Walzzunder zu dem hier meist flüssigen Roheisen) und das Schrott-Kohlungs-Verfahren (Aufkohlung von Schrott durch Holzkohle, Koks, Elektrodenkohle). An das Einschmelzen schließt sich das Frischen an. Damit werden unerwünschte Anteile wie vor allem Kohlenstoff, aber auch Phosphor und Schwefel verringert. Der notwendige Sauerstoffeintrag erfolgt durch den Sauerstoffüberschuss der Brennerflamme oder aus dem Erz.
Durch diesen hier langsam ablaufenden Prozess, mehrere Stunden, konnte der gewünschte Kohlenstoffgehalt sehr genau eingestellt werden. Das Verfahren eignet sich v. a. für die Erzeugung unlegierter Stähle. Der sogenannte Siemens-Martin-Stahl wird im Anschluss aus dem Ofen chargiert ("abgestochen").
Einst waren die Siemens-Martin-Öfen mit einer Abstichmasse, d. h. für die Herstellung von 10 Tonnen Stahl konzipiert worden. Durch die wirtschaftliche Massennutzung des Siemens-Martin-Verfahrens wurde die Abstichmasse in vereinzelten Ländern, wie z. B. den USA, auf 600 Tonnen ausgeweitet.
Trotz Massentauglichkeit der Stahlerzeugung handelte es sich nicht um eine Methode, die schnell ging. Insgesamt dauerte der technologische Ablauf bzw. der Schmelzprozess des Siemens-Martin-Verfahrens jeweils acht Stunden.
Der Ofen bedurfte zudem einer zeitintensiven Pflege währenddessen keine Produktion stattfinden konnte. Nach der Pflege wurden zwei Stunden lang Einsätze und Zusätze für die Schlackebildung eingesetzt. Anschließend wurde der Einsatz für 3,5 Stunden verflüssigt durch das Verfahren des Einschmelzens. Weitere 1,5 Stunden wurden verwendet, um den Ofen vorzubereiten. Die Abstichtemperatur und die Abstichstichprobe wurden in diesem Zuge überprüft und ermittelt. Die letzten Minuten des technologischen Ablaufs dienten der Entziehung des Sauerstoffs, der Legierung von Elementen und der Durchführung eines Abstiches nach Erreichen der erforderlichen Temperatur.[27] Das Siemens-Martin-Verfahren lieferte einen qualitativ höherwertigen Stahl, der jedoch wegen des aufwendigeren Prozesses etwas teurer war.
Der Großteil des Stahls wurde bis 1960 mit diesem Verfahren hergestellt, da man damit auch ausgezeichnet Schrott verwerten konnte. 1993 wurde in Brandenburg an der Havel der letzte deutsche Siemens-Martin-Ofen aus wirtschaftlichen Gründen stillgelegt. Er ist heute als technisches Denkmal erhalten.[28][29][30]
Das Verfahren wurde nach der Erfindung, in den späteren Jahren des 19. Jahrhunderts für das kontinuierliche Erschmelzen von Glas, insbesondere für die Massenproduktion, adaptiert, konstruktiv sowie in Hinsicht auf energetische Effizienz weiterentwickelt und ist noch heute Stand der Technik.
Wegfall des Schmiedens
Das nach dem Puddeln notwendige Schmieden der Luppen, um den Werkstoff zu homogenisieren, konnte mit den neuen Verfahren entfallen, da sie alle flüssigen Stahl erzeugten, der schon sehr viel homogener war, als Puddeleisen je werden konnte. Dennoch zögerten die Stahlproduzenten damit, das Schmieden aufzugeben, da ein gründlicher Schmiedeprozess bis dahin Kennzeichen eines guten Stahls war. Vor allem die Kunden konnten lange nicht glauben, dass mit weniger Aufwand ein besseres Produkt möglich war. Krupp war in Deutschland der letzte Industrielle, der das Schmieden aufgab, verbot seinen Verkäufern aber, zu verraten, dass sein Stahl, der für seine hohe Qualität bekannt war, nur noch gewalzt wurde.
Schnellbetrieb
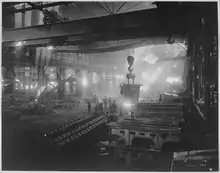
In Amerika etablierte sich Ende des 19. Jahrhunderts allmählich eine Rationalisierungsbewegung, die im frühen 20. Jahrhundert ihren Höhepunkt fand. Unter Rationalisierung verstand man damals vor allem die Erhöhung der wirtschaftlichen Effizienz der Produktion. Man wollte also mit den vorhandenen Arbeitern und Anlagen möglichst viel produzieren oder eine bestimmte Produktionsmenge zu möglichst geringen Kosten herstellen. Erst mit den daraus entstandenen Organisationsprinzipien wurde das wahre Leistungspotential der neuen Technologien vollständig ausgeschöpft – nicht nur im Bereich der Stahlindustrie, sondern in allen Gewerben.
Obwohl in den Bessemer-Werken in einem Konverter der Stahl nach nur 20 Minuten gefrischt war, konnte man nur fünf bis sechs Chargen pro Tag ausbringen. Die restliche Zeit stand der Konverter still. Dies lag vor allem an der hohen Reparaturbedürftigkeit der Konverterböden, die nach spätestens sechs Chargen verschlissen waren und etwa 10 Stunden lang repariert werden mussten. In Europa versuchte man daher neue hitzebeständigere Materialien zu verwenden. In Amerika, wo ein sehr großer Bedarf an Stahl herrschte, hielt man sich damit nicht lange auf. Man wechselte einfach den gesamten Boden in wenigen Minuten aus und produzierte dann weiter. Die Kosten für die Böden spielten dagegen keine große Rolle. In amerikanischen Stahlwerken wurde nun rund um die Uhr produziert und damit auch zum ersten Mal sowohl schnell als auch gut, was Beobachter aus Europa besonders beeindruckte. Denn bisher hieß gut produzieren vor allem langsam und gründlich produzieren. Diese Produktionsweise in der Stahlindustrie wurde in Amerika als englisch hard driving und in Deutschland als Schnellbetrieb bezeichnet.[31][32][33][34]
20. Jahrhundert
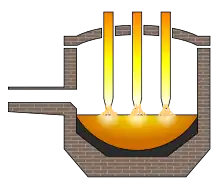
Elektrischer Strom ermöglichte mit den damals neuartigen Lichtbogenöfen die Herstellung von sogenanntem Elektrostahl. Diese Stahlwerke waren ausgezeichnete Schrottverwerter, spielten aber auf dem Gesamtmarkt nur eine untergeordnete Rolle. Hier konkurrierten nach wie vor drei verschiedene Verfahren: Das Bessemer- und das Thomasverfahren mit dem etwas günstigeren Stahl und das Siemens-Martin-Verfahren mit dem qualitativ besseren Stahl. In den Bessemer- und Thomashütten bemühte man sich daher die Qualität zu verbessern und damit die ersehnte „Siemens-Martin-Gleichheit“ zu erreichen, was jedoch nicht gelang. Alle Verfahren waren jedoch ausgesprochen produktiv, sodass es erstmals zu Überkapazitäten kam. Bisher hatte man versucht die Kosten einzelner Anlagen zu optimieren; die Produktionsmenge war eine daraus resultierende Größe. Nun war sie ebenso wie der Marktpreis vorgegeben durch Kartellierung, Konzernbildung, Schutzzölle und weitere wirtschaftliche Einflüsse. In den vertikal integrierten Stahlkonzernen, mit ihren Erzgruben, Hochöfen, Bessemer- oder Siemens-Martin-Hütten und den Walzwerken ging es nun darum, die Kosten für das gesamte Unternehmen zu minimieren.[35]
- OBM-Verfahren
- Im OBM-Verfahren (Oxygen-Bottom-Maxhütte oder Oxygen-Bodenblas-Metallurgie-Verfahren) werden Sauerstoff und Methan oder Propan durch gasgekühlte Ringspaltdüsen im Boden des Konverters in die Schmelze eingeblasen. Das Verfahren wurde Mitte der 1970er Jahre von der Maxhütte in Zusammenarbeit mit der damaligen Vöest-Alpine („Division“ Industrieanlagenbau) entwickelt. Die Elemente Silicium, Mangan, Kohlenstoff und Phosphor verbrennen dabei. Der Schwefel wird mit Calcium und den gebildeten Oxiden in der Schlacke gebunden. Ausgangsstoffe sind Roheisen, Kühlschrott, Zuschläge, Propan bzw. Methan. Reaktionsprodukte sind Rohstahl und Schlacke (Stahlgewinnung). Mit der Stilllegung der Maxhütte im Jahr 2002 ist der letzte deutsche OBM-Konverter außer Betrieb gegangen. Die Technologie der Bodeneindüsung wird aber erfolgreich bei Konvertern für rostfreie Stähle angewendet (CLU = Creusot-Loire Uddeholm process und AOD).Stahl-/Sauerstoff-Konverter nach dem OBM-Verfahren (Sauerstoffbodeneinblasung) – verwendet von 1974 bis 1992 in Maxhütte (Unterwellenborn)
Integrierte Hüttenwerke
.jpg.webp)
Zur Effizienzsteigerung entstanden bald integrierte Hüttenwerke, um Nebenprodukte zu verwerten. Im Hochofen entsteht beispielsweise Gichtgas, das schon lange genutzt wurde, um den Hochofenwind zu erwärmen. Dabei wurde jedoch nur etwa 20 % des Gases verbraucht. Nun versuchte man es weitergehend zu nutzen: Zunächst wurde es in den Dampfmaschinen der Walzwerksantriebe verbrannt. Dadurch entstand eine starre technische Kopplung zwischen der Anzahl der Hochöfen und der Anzahl der Walzwerke. Als man zu elektrischen Antrieben überging, trieb man stattdessen Generatoren damit an: Das Gas wurde „verstromt“.[36] Außerdem begann man das flüssige Roheisen aus dem Hochofen direkt in die Konverter (Bessemer- und Thomas-Verfahren) oder Siemens-Martin-Öfen zu geben ohne es erneut einzuschmelzen, was energiesparender ist. Das gefrischte Eisen ließ man gerade soweit abkühlen, dass es fest wurde und walzte es dann. Im Idealfall genügte die im Hochofen erzeugte Hitze für den gesamten Prozess, was als „Walzen in einer Hitze“ bezeichnet wurde. Die schon immer abfallende Schlacke wurde nun zu Sand, Stein und Zement weiterverarbeitet. Besonders begehrt war die Schlacke der Thomas-Werke, da sie einen hohen Anteil von Phosphaten aufweist und daher zu Dünger weiterverarbeitet werden kann. Die Thomas-Werke zählten sogar zu den größten Düngemittelherstellern. Diese Thomasgutschrift trug wesentlich zu den Kostenvorteilen des Verfahrens bei, da der Thomasstahl um diese Gutschrift günstiger wurde.[37]
Chrom-Nickel-Stahl
In der chemischen Industrie wurden bei einigen Prozessen wie dem damals neuen Haber-Bosch-Verfahren zur Herstellung von Ammoniak sehr hohe Drücke und Temperaturen von bis zu 330 bar und 550 °C benötigt. Der am Prozess beteiligte Wasserstoff diffundierte in den Stahl der Reaktorwände, löste den darin enthaltenen Kohlenstoff und verringerte dadurch die Festigkeit des Stahls, was zu Reaktorexplosionen führte. In der Folge entwickelte man hochlegierte Stähle, die ihre Festigkeit nicht über den Kohlenstoff, sondern über andere Legierungselemente erhalten und daher chemisch beständiger sind. Der wichtigste Vertreter ist der austenitische, rostfreie Chrom-Nickel-Stahl. Die neuen Stähle und chemischen Verfahren verhalfen sich somit gegenseitig zum großtechnischen Durchbruch.[38]
Wirtschaftliche Bedeutung
In beiden Weltkriegen des 20. Jahrhunderts war Stahl ein kriegswichtiger Werkstoff. So galt der deutsche Norwegenfeldzug 1940 unter anderem der Sicherung des Nachschubs von schwedischem Eisenerz, das für die deutsche Stahlerzeugung ein unverzichtbarer Rohstoff war. Die Alliierten bombardierten das Ruhrgebiet, die größte stahlproduzierende Region Europas. Am Ende des Kriegs hatten die Luftangriffe ca. 20 % der Produktionskapazitäten zerstört.
Die auf der Potsdamer Konferenz beschlossene Demilitarisierung des Deutschen Reichs beinhaltete auch eine Demontage der Stahlindustrie. Ein Teil der demontierten Betriebe ging an die Sowjetunion, die diese zum Wiederaufbau des durch den Krieg zerstörten Landes benötigte. Eine weitere Maßnahme der alliierten Kontrollbehörde war die sogenannte „Entflechtung“ der Stahlindustrie. Damit sollte das neuerliche Aufkommen von marktbeherrschenden Unternehmenszusammenschlüssen wie den Vereinigten Stahlwerken verhindert werden.
Um eine gemeinsame Kontrolle der Kohle- und Stahlproduktion sicherzustellen, wurde 1952 auf französische Initiative hin die Montanunion gegründet. Aus der Montanunion entwickelte sich dann schrittweise die Europäische Union. In der Folge erlebte die Stahlindustrie in der Bundesrepublik Deutschland einen großen Aufschwung. 1961 produzierten 420.568 Beschäftigte 33 Millionen Tonnen Rohstahl, was einen Höchststand bei der Mitarbeiterzahl bedeutete. Einen Produktionsrekord stellte die westdeutsche Stahlindustrie 1974 auf, als sie über 53 Millionen Tonnen Stahl fertigte. Heutzutage benötigt die Stahlindustrie im wiedervereinigten Deutschland etwa 94.000 Mitarbeiter[39], um rund 35,7 Millionen Tonnen Stahl (Stand 2020)[40] herzustellen. Diese enorme Produktivitätssteigerung war nur durch bedeutende technische Innovationen möglich.
Primärmetallurgie
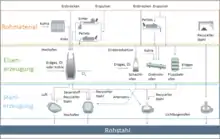
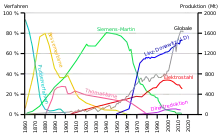
In der Primärmetallurgie wird unlegierter Stahl in einfachster Form hergestellt. Die beiden wichtigsten Routen sind dabei die Hochofen-Konverter sowie die Elektrostahlroute. Andere Produktionswege wie offene Herdöfen, Schmelzreduktion oder Direktreduktion tragen weltweit einem Anteil von weniger als 1 % bei.[41]
Hochofen | Elektroofen | |||
---|---|---|---|---|
[t] | [%] | [t] | [%] | |
Deutschland | 29 732 | 70,1 | 2 703 | 29,9 |
EU | 97 652 | 58,4 | 69 471 | 41,6 |
Weltweit | 1 291 27 | 70,8 | 524 30 | 28,7 |
Hochofen-Konverter Route
Die Route Hochofen-Konverter besteht aus der Reduktion von Eisenerz zu Roheisen im Hochofen sowie der nachgeschalteten Weiterverarbeitung des Roheisens im Konverter zu Rohstahl.
Erzeugung von Roheisen im Hochofen
Beim Hochofenverfahren wird zuerst Roheisen aus Eisenerz mit Hilfe von Koks hergestellt. Danach wird durch weitere Verfahren aus dem Roheisen der Stahl hergestellt. Das Eisenerz wird als Stückerz, Pellets oder Sinter zusammen mit dem Reduktionsmittel (Koks) und weiteren Bestandteilen (Kalkstein, Dolomit, Schlackenbildner usw.) zum sogenannten Möller vermischt und anschließend chargiert. Der Hochofen ist ein metallurgischer Reaktor, in dem im Gegenstrom die Möllersäule mit heißer Luft, dem sogenannten Wind, reagiert. Durch Verbrennen des Kohlenstoffs aus dem Koks entstehen die für die Reaktion nötige Wärme und Kohlenstoffmonoxid, das die Möllersäule durchströmt und das Eisenerz reduziert. Die wichtigsten Reduktionsgleichungen sind:
Es entstehen Roheisen und Schlacke, die regelmäßig abgestochen wird. Das Roheisen enthält nicht nur Kohlenstoff, sondern auch Eisenbegleiter die durch Erze, Zuschläge, Brennstoff und feuerfeste Auskleidungen der Gefäße und Öfen in die Schmelze gelangt sind. Phosphor, Schwefel, Sauerstoff, Stickstoff und Wasserstoff wirken sich qualitätsmindernd aus, während sich kleine Mengen an Silicium und Mangan positiv auswirken können.[42] Die Schlacke wird zu Hüttensand weiterverarbeitet. Das anfallende Gichtgas hat eine Zusammensetzung von circa 51 Volumenprozent (vol%) Stickstoff, 22 vol% Kohlendioxid, 22 vol% Kohlenmonoxid und 5 vol% Wasserstoffgas.[43] In diesem Gichtgas ist noch Heizwert durch die Anwesenheit von Kohlenmonoxid und Wasserstoffgas. Der Anteil an Kohlenmonoxid macht Gichtgas tödlich giftig.
Erzeugung von Stahl aus Roheisen
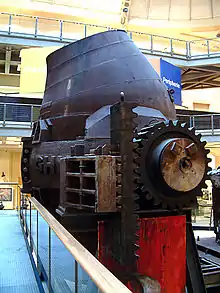
Roheisen aus dem Hochofen, aber häufig auch Schrott, enthält sehr viel Kohlenstoff und meist noch zu viel Schwefel, weshalb es weiter aufbereitet werden muss. Eine Entschwefelung findet meist bereits während des Transports der Schmelze im Stahlwerk statt und geschieht durch Zugabe von Calciumoxid (Kalkentschwefelung).[44] Der Kohlenstoffgehalt wird durch das sogenannte Frischen reduziert. Dabei wird der flüssige Stahl mit Sauerstoff behandelt, der Kohlenstoff oxidiert und als CO und CO2 entweicht. Hierbei kann zwischen so genannten Blasverfahren und Herdfrischverfahren unterschieden werden:
- Bei den Blasverfahren wird das Roheisen mit Sauerstoff oder Luft gefrischt. Der Oxidationsprozess, der den Kohlenstoffanteil senkt (das Frischen), liefert in diesen Verfahren genug Wärme, um den Stahl flüssig zu halten, eine externe Wärmezufuhr ist in den Konvertern deshalb nicht notwendig. Die Blasverfahren kann man zusätzlich in Aufblasverfahren und Bodenblasverfahren unterteilen. Zu den Bodenblasverfahren gehören das Bessemerverfahren und das Thomasverfahren. Das am weitesten verbreitete Aufblasverfahren ist das Linz-Donawitz-Verfahren (LD)- oder Sauerstoffaufblas-Verfahren. In den LD-Konverter werden flüssiges Roheisen und bis zu 30 % (durchschnittlich etwa 20 %)[45] Stahlschrott eingefüllt und Schlackenbildner hinzugegeben. Über eine Lanze wird Sauerstoff auf die Schmelze geblasen. Dabei verbrennen im Stahl unerwünschte Begleitelemente wie Schwefel, Phosphor, Kohlenstoff usw. und gehen in das Rauchgas oder die Schlacke über. Die Vollständigkeit der Entfernung lässt sich mit dem Baumannabdruck ermitteln. Durch die mit der Verbrennung verbundene enorme Wärmeentwicklung wird der beigegebene Schrott aufgeschmolzen. Eine Variante des LD-Verfahrens ist das Sauerstoff-Durchblasverfahren oder eine Kombination von Aufblas- und Durchblasverfahren (LWS-Verfahren nach Loire-Wendel-Sprunch oder TBM-Verfahren nach Thyssen-Blas-Metallurgie), bei dem Sauerstoff durch Düsen im Boden in den Konverter, gegebenenfalls zusätzlich zur Sauerstofflanze, eingeblasen wird.
- Bei den Herdfrischverfahren wird der zur Oxidation notwendige Sauerstoff dem dem Roheisen zugesetzten Schrott und Erz entnommen. Außerdem muss den Herdfrischkonvertern extern Wärme zugeführt werden. Das bekannteste Herdfrischverfahren ist das Siemens-Martin-Verfahren. Frischwirkung und Heizwirkung gehen von einem oxidierenden Brenngas-Luft-Gemisch aus, das über den flachen Schmelzherd geleitet wird.
Direktreduktion
Die Nachteile des Hochofens sind die Anforderungen an die Einsatzmaterialien und der hohe Ausstoß an CO2. Der eingesetzte Eisenträger und der Koks müssen stückig und hart sein, sodass genügend Hohlräume in der Möllersäule bestehen bleiben, die das Durchströmen durch den eingeblasenen Wind gewährleisten. Zu den etablierten Hochofen-Verfahren zählen die Eisenschwamm- und Pelletherstellung in Drehrohröfen sowie die Corex-, Midrex- und Finex-Verfahren. Der Eisenschwamm wird in der Elektrostahlroute oder direkt für Gusseisen eingesetzt.
Am weitesten verbreitet sind bisher das Midrex- bzw. HYL-Direktreduktionsverfahren, die Eisenschwamm bzw. HBI (engl. Hot Briquetted Iron) als festes Einsatzmaterial erzeugen.[46][47] Dieses ist immer noch mit einer gewissen Menge von Gangart des Ausgangserzes belastet, aber der Kohlenstoffgehalt ist normalerweise nicht höher als 1 %.
Das Corex-Verfahren ist neueren Datums und erzeugt ein flüssiges, roheisenähnliches Vormaterial, dessen Kohlenstoffgehalt bei ca. 3,5 bis 4 % liegt. Der Corex-Prozess ist ein zweistufiges Schmelzreduktionsverfahren (engl.: smelting-reduction), in dem Roheisen auf Basis nicht verkokter Kohle und Eisenerzen hergestellt werden kann. Ziel des Schmelzreduktionsverfahrens ist es, durch die Kombination von Schmelzprozess, Kohlevergasung und Direktreduktion flüssiges Eisen zu erzeugen, dessen Qualität dem Hochofenroheisen entspricht. Die Schmelzreduktion kombiniert den Prozess der Direktreduktion (Vorreduktion von Eisenoxid zu Eisenschwamm) mit einem Schmelzprozess (Hauptreduktion). Der Prozess läuft also zweistufig in getrennten Aggregaten ab. Zuerst werden die Erze zu Eisenschwamm reduziert, im zweiten Schritt erfolgt die Endreduktion und das Aufschmelzen zu Roheisen. Die für den Schmelzvorgang nötige Energie liefert die Verbrennung von Kohle (nicht verkokt). Dabei entstehen große Mengen Kohlenmonoxid als Abgas, das als Reduktionsgas genutzt wird.
Eine Variante der Direktreduktion wird seit 2010 mit einer Pilotanlage in IJmuiden unter dem Namen HIsarna-Prozess erprobt.[48][49]
Direktreduktion mit Wasserstoff
Der CO2-Ausstoß stellt eine starke Belastung an Treibhausgasen dar. Deshalb gibt es Bestrebungen, die Hochofenroute abzulösen und Koks durch Wasserstoff als Reduktionsmittel zu ersetzen (H-DR). Wasserstoff reagiert im Prozess mit Eisenoxiden zu Wasserdampf.[2][50] Die Reduktionsgleichung ist:
Das Eisenerz wird im Prozess meist durch Erdgas oder auch elektrisch auf bis zu 900 °C erhitzt. Das Produkt ist ein fester Eisenschwamm in Form von Briketts oder Feingut mit einer Metallisierung von ca. 95 %, das der Elektrostahlroute zugeführt werden kann.[3]
Die Stahlerzeugung kann so mithilfe von Wasserstoff auf lange Sicht CO2–neutral gemacht werden.[51] Entscheidend für die Bilanz sind ein hoher Anteil erneuerbarer Energien im Strom und der Syntheseweg des Wasserstoffes. SSAB, LKAB und Vattenfall arbeiten zusammen an dem Projekt "HYBRIT", bei dem mit diesem Wasserstoff-Verfahren Stahl erzeugt werden soll. Wenn das Projekt wie geplant im Jahr 2035 im kommerziell-industriellen Maßstab einsatzbereit ist, soll es laut Unternehmen den CO2-Ausstoß von Schweden um 10 % und den CO2-Ausstoß von Finnland um 7 % senken können.[52][53] Im Jahre 2018 wurde dazu mit dem Bau einer Pilotanlage begonnen.[54] 2021 erfolgte die erste Probelieferung an Volvo.[55]
Eine Studie von Fraunhofer-Instituten legt nahe, dass in Deutschland bis 2030 die Wasserstoffnachfrage für die Stahlproduktion auf 6 TWh und bis 2050 auf 38–56 TWh steigen wird. Die Zahlen basieren auf der Annahme, dass die Stahlerzeugung aus Eisenerz sinkt und das Stahlschrottaufkommen wächst, für eine Tonne Rohstahl werden ca. 1900 kWh H2 benötigt.[56] Dass die Industrie bereit ist, in diesen Umbau zu investieren, begründen die Wissenschaftler mit dem Einhalten der Ziele des Pariser Klimaabkommens.
Elektrostahlroute
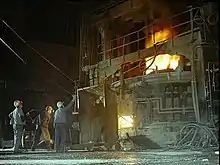
Bei den Elektrostahlverfahren wird die zum Schmelzen erforderliche Wärme direkt aus elektrischer Energie erzeugt. Die Entladung durch einen Lichtbogen von den Graphitelektroden zum Schmelzgut erzeugt Temperaturen bis zu 3500 °C direkt im Material. Weit verbreitet ist der Lichtbogenofen mit drei Elektroden bei Drehstrom, seltener zwei bei Gleichstrom. Gegenüber der Hochofenroute wird bei der Elektrostahlroute bis zu 55 % Energie eingespart.
Der Lichtbogenofen wird mit Schrott, Eisenschwamm und/oder Roheisen "beschickt".[57] Außerdem werden noch Kalk zur Schlackenbildung und Reduktionsmittel zugegeben. Zusätzliches Einblasen von Sauerstoff oder anderer Brennstoff-Gasgemische beschleunigen den Schmelzprozess.
Lichtbogenöfen werden zur Herstellung von hochlegierten Qualitäts- und Edelstählen genutzt. Aufgrund der höheren Temperaturen, im Vergleich zur Hochofen-Konverter Route, können auch schwer schmelzbare Legierungselemente wie Wolfram und Molybdän als Ferrolegierungen eingeschmolzen werden.
Ein Schmelzprozess dauert ca. 30 Minuten. Danach wird der Rohstahl über Stahlgießpfannen oder eine Stranggussanlage abgegossen. Das Fassungsvermögen der kippbaren Elektroöfen beträgt 100 bis 300 t. Mit einem Elektroofen können ca. 0,9 bis 2,8 Mio. t/Jahr erschmolzen werden.[47][57][58]
Sekundärmetallurgie und Gießen
In der Sekundärmetallurgie wird der Rohstahl für das Gießen fertig behandelt (Tiefentkohlung in Vakuumanlage, Legieren in Pfannenofen). Für legierte Stähle werden Metalle wie z. B. Chrom, Nickel, Cobalt, Molybdän, Wolfram oder Mangan zugesetzt. Nach dem Zulegieren der gewünschten Elemente wird der Stahl im Strang oder in der Kokille zu Halbzeug vergossen. Das Vergießen bedarf besonderer Techniken, man unterscheidet zwischen unberuhigtem und qualitativ höherwertigen beruhigtem vergossenen Stahl.
Das Beruhigen (auch Desoxidation) bezeichnet das Binden des in der Schmelze gelösten Sauerstoffs in FeO durch Zulegieren von Aluminium, Calcium, Magnesium, Silicium oder Titan bzw. einer Kombination.[42] Durch Redox-Reaktionen entstehen nichtmetallische Teilchen, die nur teilweise über die Schlacke entfernt werden können. Hingegen wandern teure Elemente wie Chrom aus der Schlacke wieder zurück in die Stahlschmelze. Dies hat Einfluss auf im erkaltenden Stahl entstehende Seigerungen (Materialentmischungen, z. B. Schwefelablagerungen) oder Lunker (durch das Schwinden des Materials bedingte Hohlräume). Beide sind mit Qualitätsverlusten verbunden. Auskochen verhindert hingegen Oxideinschlüsse und erhöht damit die Zähigkeit und den Reinheitsgrad des Stahls.
Der flüssige Stahl wird dann in die sogenannte Kokille abgegossen, wo die Erstarrung stattfindet:
- Beim Strangguss ist die wassergekühlte Kokille so gestaltet, dass durchlaufend unten einer bzw. mehrere Guss-Stränge abgezogen werden. Der Strangguss ist weltweit mit über 90 % das am häufigsten eingesetzte Gussverfahren.[57]
- Im Blockguss wird für die einseitig offene Kokille eine einfache Geometrie verwendet und der hieraus entstehende Block wird in der Regel weiter verarbeitet.
- Ist die Kokille so gestaltet, dass der Stahl nahezu die Endkontur für einen Einsatzzweck erreicht, handelt es sich um Formguss.
Zur Erzeugung von Spezialstählen können Umschmelzverfahren eingesetzt werden, z. B. das Elektroschlacke-Umschmelzverfahren (ESU).
Es folgen i. d. R. Umformverfahren wie Walzen, Strangpressen oder Schmieden.
Die größten Stahlproduzenten
Das bedeutendste Herstellerland für Stahl ist die Volksrepublik China, gefolgt von Indien und Japan. Alleine China ist hierbei verantwortlich für etwas mehr als die Hälfte der Weltproduktion – Indien und Japan für 5,9 % bzw. 5,7 % des weltweiten Produktionsvolumens.[59] In Europa sind Russland, Deutschland und Italien die drei wichtigsten Produzenten.
Siehe auch
Literatur
- Dieter Janke: Moderne Stahlerzeugung. In: Chemie in unserer Zeit. 15, Nr. 1, 1981, S. 10–20 (doi:10.1002/ciuz.19810150104).
- Karl Taube: Stahlerzeugung kompakt. Grundlagen der Eisen- und Stahlmetallurgie. Friedrich Vieweg & Sohn Verlag, 1998, ISBN 3-528-03863-2.
Weblinks
- Fotografien zu fast allen Verfahren der Stahlerzeugung und Stahlverarbeitung, Stahlseite.de, abgerufen am 2. November 2012
- Das Quarks-Stahlwerk, abgerufen am 2. November 2012
- Viktor Macha:Fotografien zu fast allen Verfahren der Stahlerzeugung und Stahlverarbeitung (Tschechische Fotografie)
Einzelnachweise
- Energy Use and CO2 EmissionsIn the Steel Industry. (PDF) IEA, 2019, abgerufen am 15. Mai 2021 (englisch).
- Frank Wunderlich-Pfeiffer: Stahlherstellung mit Wasserstoff geht in den Testbetrieb. In: www.golem.de. 7. Oktober 2020, abgerufen am 15. Mai 2021.
- Alexander Otto, Martin Robinius, Thomas Grube, Sebastian Schiebahn, Aaron Praktiknjo: Power-to-Steel: Reducing CO2 through the Integration of Renewable Energy and Hydrogen into the German Steel Industry. In: Energies. Band 10, Nr. 4, 2017, S. 451, doi:10.3390/en10040451.
- Friedrich Cornelius: Geistesgeschichte der Frühzeit. Band 1, Verlag Brill Archive, 1960, S. 132.
- Wolfgang König (Hrsg.): Propyläen Technikgeschichte. Band 3, Propyläen, Berlin 1997, S. 98 f. Günter Spur: Vom Wandel der industriellen Welt durch Werkzeugmaschinen. Carl Hanser Verlag, München/ Wien 1991, S. 49–51.
- Wolfgang König (Hrsg.): Propyläen Technikgeschichte. Band 3, Propyläen, Berlin 1997, S. 99 f.
- Günter Spur: Vom Wandel der industriellen Welt durch Werkzeugmaschinen. Carl Hanser Verlag, München/ Wien 1991, S. 57 f.
- Alex R. Furger: Antike Stahlerzeugung. Ein Nachweis der Aufkohlung von Eisen aus Augusta Raurica. LIBRUM Publishers & Editors, Basel/Frankfurt am Main 2019, ISBN 978-3-906897-28-8
- Günter Spur: Vom Wandel der industriellen Welt durch Werkzeugmaschinen. Carl Hanser Verlag, München/ Wien 1991, S. 67, 70 f., 77.
Wolfgang König (Hrsg.): Propyläen Technikgeschichte. Propyläen, Berlin 1997:
- Band 1, S. 346–408, 419–435.
- Band 2, S. 76–107.
- Günter Spur: Vom Wandel der industriellen Welt durch Werkzeugmaschinen. Carl Hanser Verlag, München/ Wien 1991, S. 68, 79–81. Wolfgang König (Hrsg.): Propyläen Technikgeschichte. Propyläen, Berlin 1997, Band I, S. 423–425 (Damast), Band II 390 (Gusseisen).
- Günter Spur: Vom Wandel der industriellen Welt durch Werkzeugmaschinen. Carl Hanser Verlag, München/ Wien 1991, S. 69 f., 79–81. Wolfgang König (Hrsg.): Propyläen Technikgeschichte. Band 2, Propyläen, Berlin 1997, S. 377, 391.
- Günter Spur: Vom Wandel der industriellen Welt durch Werkzeugmaschinen. Carl Hanser Verlag, München/ Wien 1991, S. 69, 85–88.
- Beispiel Solingen: Günter Spur: Vom Wandel der industriellen Welt durch Werkzeugmaschinen. Carl Hanser Verlag, München/ Wien 1991, S. 76. Regionale Verteilung allgemein: Wolfgang König (Hrsg.): Propyläen Technikgeschichte. Band 1, Propyläen, Berlin 1997, S. 426.
- Wolfgang König (Hrsg.): Propyläen Technikgeschichte. Band 3, Propyläen, Berlin 1997, S. 383.
- Wolfgang König (Hrsg.): Propyläen Technikgeschichte. Band 3, Propyläen, Berlin 1997, S. 330.
- Wolfgang König (Hrsg.): Propyläen Technikgeschichte. Band 3, Propyläen, Berlin 1997, S. 383 f., 397.
- Gottfried Pumpe: Chemische Industrie. In: Ulrich Wengenroth (Hrsg.): Technik und Wirtschaft. (= Technik und Kultur. Band 8). VDI-Verlag, Düsseldorf 1993, S. 161–163.
- Günter Spur: Vom Wandel der industriellen Welt durch Werkzeugmaschinen. Carl Hanser Verlag, München/ Wien 1991, S. 127–129. Wolfgang König (Hrsg.): Propyläen Technikgeschichte. Band 3, Propyläen, Berlin 1997, S. 390–393, 395.
- Günter Spur: Vom Wandel der industriellen Welt durch Werkzeugmaschinen. Carl Hanser Verlag, München/ Wien 1991, S. 129. Wolfgang König (Hrsg.): Propyläen Technikgeschichte. Band 3, Propyläen, Berlin 1997, S. 397.
- Günter Spur: Vom Wandel der industriellen Welt durch Werkzeugmaschinen. Carl Hanser Verlag, München/ Wien 1991, S. 130. Wolfgang König (Hrsg.): Propyläen Technikgeschichte. Band 3, Propyläen, Berlin 1997, S. 399 f., 406 f. Ulrich Wengenroth: Eisen, Stahl und Buntmetalle. In: Ulrich Wengenroth (Hrsg.): Technik und Wirtschaft. (= Technik und Kultur. Band 8). VDI-Verlag, Düsseldorf 1993, S. 101–103.
- Wolfgang König (Hrsg.): Propyläen Technikgeschichte. Band 3, Propyläen, Berlin 1997, S. 402 f.
Ulrich Wengenroth: Eisen, Stahl und Buntmetalle. In: Ulrich Wengenroth (Hrsg.): Technik und Wirtschaft. (= Technik und Kultur. Band 8). VDI-Verlag, Düsseldorf 1993, S. 100–103. - R. Sonnemann, S. Richter, H. Wolffgramm, G. Buchheim, H. Eschwege: Allgemeine Geschichte der Technik von den Anfängen bis 1870. VEB Fachbuchverlag, 1981.
- Ulrich Wengenroth: Eisen, Stahl und Buntmetalle. In: Ulrich Wengenroth (Hrsg.): Technik und Wirtschaft. (= Technik und Kultur. Band 8). VDI-Verlag, Düsseldorf 1993, S. 103.
- Ulrich Wengenroth: Eisen, Stahl und Buntmetalle. In: Ulrich Wengenroth (Hrsg.): Technik und Wirtschaft. (= Technik und Kultur. Band 8). VDI-Verlag, Düsseldorf 1993, S. 103–109.
- Lothar Gall (Hrsg.): Enzyklopädie Deutscher Geschichte. Band 79, Christian Kleinschmidt: Technik und Wirtschaft im 19. und 20. Jahrhundert S. 17f.
- Wolfgang König (Hrsg.): Propyläen Technikgeschichte. Band IV, Propyläen, Berlin 1997, S. 71–78, 286f.
- Christoph Löbbing: 100 Jahre bedeutend für die Stahlgewinnung: Das Siemens-Martin-Verfahren. 20. Mai 2020 .
- Technologie Siemens-Martin-Verfahren in Brandenburg. 2002 .
- Industriemuseum Brandenburg - Homepage.
- Industriemuseum Brandenburg Siemens-Martin Stahlherstellung. Abgerufen am 13. Dezember 2021 (deutsch, Video).
- Martina Heßler: Kulturgeschichte der Technik. Campus Verlag, Frankfurt/ New York, S. 47 f.
- Wolfgang König (Hrsg.): Propyläen Technikgeschichte. Band 4, Propyläen, Berlin 1997, S. 288 f., 427–431.
- Ulrich Wengenroth: Eisen, Stahl und Buntmetalle. In: Ulrich Wengenroth (Hrsg.): Technik und Wirtschaft. (= Technik und Kultur. Band 8). VDI-Verlag, Düsseldorf 1993, S. 111 f.
- Lothar Gall (Hrsg.): Enzyklopädie Deutscher Geschichte – Band 79. Christian Kleinschmidt: Technik und Wirtschaft im 19. und 20. Jahrhundert. Oldenbourg, 2007, S. 18, 23.
- Ulrich Wengenroth: Eisen, Stahl und Buntmetalle. In: Ulrich Wengenroth (Hrsg.): Technik und Wirtschaft. (= Technik und Kultur. Band 8). VDI-Verlag, Düsseldorf 1993, S. 115–119.
- Ulrich Wengenroth: Elektroenergie. In: Ulrich Wengenroth (Hrsg.): Technik und Wirtschaft. (= Technik und Kultur. Band 8). VDI-Verlag, Düsseldorf 1993, S. 342.
- Ulrich Wengenroth: Eisen, Stahl und Buntmetalle. In: Ulrich Wengenroth (Hrsg.): Technik und Wirtschaft. (= Technik und Kultur. Band 8). VDI-Verlag, Düsseldorf 1993, S. 118.
- Wolfgang König (Hrsg.): Propyläen Technikgeschichte. Band 5, Propyläen, Berlin, 1997, S. 46.
- Beschäftigtenzahl in der Stahlindustrie in Deutschland bis 2020. .
- Rohstahlproduktion in Deutschland. In: stahl-online.de |. 18. August 2020 .
- Steel Statistical Yearbook2020 concise version. In: www.worldsteel.org. Abgerufen am 14. Mai 2021 (englisch).
- Wolfgang Weißbach: Werkstoffkunde : Strukturen, Eigenschaften, Prüfung. 16., überarbeitete Auflage. Friedr. Vieweg & Sohn Verlag GWV Fachverlage GmbH, Wiesbaden, Wiesbaden 2007, ISBN 978-3-8348-0295-8, S. 100.
- Carbon capture and utilization in the steel industry: challenges and opportunities for chemical engineering. In: Current Opinion in Chemical Engineering. Band 26, 1. Dezember 2019, ISSN 2211-3398, S. 81–87, doi:10.1016/j.coche.2019.09.001.
- tec-science: Vom Roheisen zum Rohstahl. In: tec-science. 21. Juni 2018, abgerufen am 2. November 2019 (deutsch).
- Stahlschrottbilanz 2014: Stahlrecyclingwirtschaft musste Rückgang des Gesamtversands um 1,7 Prozent verkraften. (Memento vom 2. April 2015 im Internet Archive) Bei: bdsv.org. Pressemitteilung, 23. März 2015.
- Abhilasha Gulhane, Gaurav Kumar: TECHNICAL DEVELOPMENTS IN THE MIDDREX PROCESS. (PDF) In: International Journal of Scientific & Engineering Research. Abgerufen am 14. Mai 2021 (englisch).
- midrex.com
- HISARNA: BAHNBRECHENDFÜR DIE STAHLINDUSTRIE. (PDF) TATA Steel, abgerufen am 14. Mai 2021.
- Emissionsarme Stahlproduktion in Testphase. In: www.blechonline.de. 11. Januar 2018, abgerufen am 14. Mai 2021.
- Hochöfen ohne Koks. In: Technology Review. 23. August 2016. Abgerufen am 24. August 2016.
- H2Future Green Energy. In: https://www.h2future-project.eu/. Abgerufen am 27. Oktober 2021 (englisch).
- HYBRIT toward fossil-free steel. Abgerufen am 18. November 2018 (englisch).
- HYBRIT-Website. Abgerufen am 4. September 2020.
- HYBRIT: Baubeginn für weltweit erste Pilotanlage zur fossilfreien Stahlproduktion. In: www.vattenfall.com. 20. Juni 2018, abgerufen am 9. Mai 2020.
- Weltweit erster fossilfreier Stahl hergestellt: Explodieren jetzt die Preise? - ingenieur.de. 20. August 2021, abgerufen am 27. Oktober 2021 (deutsch).
- C. Hebling et al.: Eine Wasserstoff-Roadmap für Deutschland. (PDF) Fraunhofer-Institut, Oktober 2019, abgerufen am 19. November 2021.
- Stahlerzeugung. Stahlinstitut VDEh, abgerufen am 14. Mai 2021.
- Hubert Trenkler: Energiesparender Gleichstrom-Doppel-Lichtbogenofen für Schrott minderer Qualität. (PDF) ABB Technik, 1996, abgerufen am 19. November 2021.
- worldsteel | Steel Statistical Yearbook. Abgerufen am 7. Februar 2020 (englisch).