Hochofen
Ein Hochofen (veraltet auch Hohofen[1]) ist eine großtechnische Anlage, mit der aus aufbereiteten Eisenerzen (meist Oxiden) in einem kontinuierlichen Reduktions- und Schmelzprozess flüssiges Roheisen erzeugt wird.
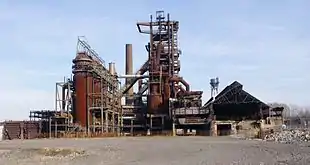
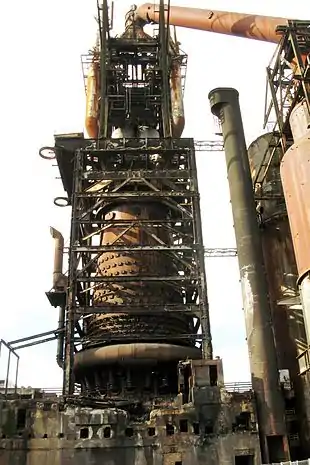
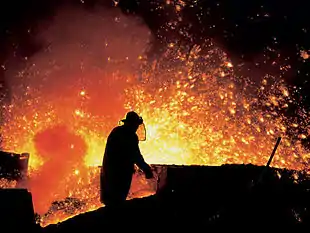
Die komplette Anlage wird auch als Eisenwerk oder Hüttenwerk bezeichnet und besitzt neben dem Hochofen als zentralem Bauteil weitere Einrichtungen, die den kontinuierlichen Betrieb gewährleisten. Dazu zählen der Bunker zur Lagerung der Einsatzstoffe (Möller: Eisenerz und Zuschlagstoffe) und der Heizstoffe (Koks) mit angeschlossenen Transport- und Leitungssystemen, um diese am Ofenkopf in den Hochofen einzubringen. Weitere Einrichtungen dienen zur Abführung des Gichtgases am Ofenkopf, zur Zuführung des von den Winderhitzern vorgewärmten Gebläsewindes im mittleren Teil des Hochofens sowie zur Abführung von Roheisen und Schlacke am Ofengrund.
Die im Möller enthaltenen Zuschlagstoffe wie Siliciumdioxid (Quarzsand), Calciumoxid (Kalk) und andere dienen während des Hochofenprozesses zur Bindung der unerwünschten Bestandteile des Erzes in der Schlacke und senken zudem die Schmelztemperatur des Eisens. Der schichtweise aufgegebene Koks dient als Energieträger und Reduktionsmittel und der über mehrere Windformen eingeblasene Heißwind liefert den nötigen Sauerstoff.
Dem produzierten Roheisen muss anschließend durch Frischen ein Teil des aufgenommenen Kohlenstoffs sowie der größte Teil des aufgenommenen Phosphors und Schwefels entzogen werden, bevor es zu verschiedenen Gusseisen- oder Stahlsorten weiterverarbeitet werden kann. Als Nebenprodukte fallen Schlacke und Gichtgas an. Die Schlacke wird üblicherweise granuliert und als Hüttensand in der Zememtindustrie verwendet. Mit dem Gichtgas wird zunächst der benötigte Heißwind erzeugt, anschließend wird es als Heizgas weitergenutzt.
Der moderne Hochofenprozess entwickelte sich im Laufe von rund 5000 Jahren aus einfachen, mit Holzkohle betriebenen und mit Kaltluft angefachten Renn- bzw. Luppenfeuern weiter in Rennöfen und Stücköfen. Der Prozess unterscheidet sich signifikant vom modernen Hochofen. Die klassischen Öfen erzeugen durch Direktreduktion festes Schmiedeeisen mit niedrigem Kohlenstoffgehalt. Nur die flüssige Schlacke läuft aus dem Ofen. Das Renneisen konnte und musste im Anschluss geschmiedet werden, um die eingeschlossene Schlacke auszutreiben. Im Gegensatz dazu muss das mit dem Floßofen und nachfolgenden Hochofen produzierte Roheisen, der ab Anfang des 18. Jahrhunderts mit Koks beheizt und seit 1828 mit Heißwind betrieben wird, in einem weiteren Arbeitsschritt entkohlt werden.
Bei der Erzeugung von einer Tonne Stahl entstehen etwa 1,37 Tonnen des Treibhausgases CO2, ein großer Teil davon beim Hochofenprozess. In Deutschland entspricht das etwa einem Drittel der Industrieemissionen.[2] Viele große Stahlunternehmen in Europa planen deshalb, den Hochofenprozess durch emissionsarme Verfahren zu ersetzen wie beispielsweise durch Direktreduktion mit Wasserstoff und nähern sich damit wieder dem klassischen Prozess an.
Geschichte
Zur frühesten Nutzung und archäologischen Funden von Eisen siehe
Anfänge der Eisenverhüttung in Europa
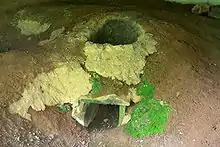
_-_1556.jpg.webp)
Eine erste einfache und lange genutzte Form zur Eisenverhüttung waren die sogenannten Rennfeuer (auch Luppenfeuer genannt). Eine trichterförmige Grube von etwa 30 Zentimeter Durchmesser wurde mit Holzkohle und leicht reduzierbarem Raseneisenerz gefüllt, entzündet und mit einer als Gebläse fungierenden, halbkugelförmigen und fellüberspannten Schale (als frühe Form des Blasebalgs) mit Luftsauerstoff versorgt. Nach etwa zehn Stunden hatte sich am Boden eine etwa faustgroße, schwarze, mit Eisenkörnern und unverändertem Erz sowie Schlacke durchsetzte Luppe (Eisenschwamm) angesammelt.[3] Während der Ofenreise verflüssigt sich das Eisen in einem Rennofen nicht. Das Erreichen der dazu notwendigen Temperaturen ist zwar problemlos möglich, jedoch wäre das so gewonnene Produkt stark aufgekohlt und nicht mehr schmiedbar. Während des Betriebes musste daher die Temperatur dauernd in einem Bereich gehalten werden, der eine Verflüssigung des Metalls nicht zuließ. Der meist aus Lehm oder Steinen errichtete Rennofen war eine Weiterentwicklung des Rennfeuers mit seitlicher Öffnung für die Luftzufuhr und einem kurzen Schacht zur Be- und Nachfüllung von Holzkohle vor und während des Ofenganges. Der Schacht unterstützte zudem den natürlichen Kamineffekt, so dass Temperaturen zwischen 1000 und 1200 °C erreicht werden konnten.[4] Die Luftversorgung wurde zunächst mit einem natürlichen Luftzug realisiert, beispielsweise durch Bau an einer Böschung, und die Öfen wurden entsprechend als Windöfen oder Zugöfen bezeichnet. Bei den Gebläseöfen sorgten dagegen Blasebälge für eine effektivere und kontrolliertere Luftversorgung. Je nach zeitlicher Dauer des Ofengangs (4 bis 20 Stunden) und je nach Größe des Ofens erhielten die frühzeitlichen Hüttenleute eine Luppe mit einem Gewicht von einigen Kilogramm bis zu mehreren Zentnern. Diese wurde anschließend durch mehrmaliges Aufheizen (Anhitzen) und Ausschmieden von Kohle und Schlacke befreit, verdichtet und – meist über Halbzeuge – zu den gewünschten Werkstücken weiterverarbeitet.[5]
Siehe hierzu auch: Eisenerzeugung im Lahn-Dill-Gebiet und Eisenverhüttung bei den Germanen.
Bis ins 18. Jahrhundert waren Rennöfen mit angeschlossenen Schmieden, sogenannte Rennwerke, noch weit verbreitet. Sie beschäftigten etwa fünf bis zehn Mann und produzierten jährlich etwa 60 bis 120 Tonnen Luppe. Pro Kilogramm Eisen wurden 2,7 Kilogramm Holzkohle verfeuert.[6]
Entwicklung des Hochofens
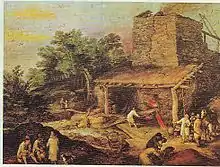
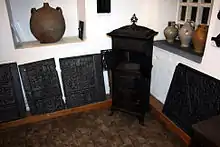
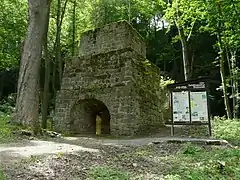
Auch wenn der Rennofen aufgrund seiner einfachen Bauweise lange genutzt wurde, begann man bereits Anfang des 13. Jahrhunderts leistungsfähigere Öfen zu entwickeln.[7] Als ein Bindeglied zur Entwicklung der heutigen Hochöfen kann der Stückofen (auch „Wolfsofen“) angesehen werden, welcher nach dem Eisen-Stück benannt wurde, das man aus dem Ofen herausholte.[8] Der Ofen war ein viereckig gemauerter, oben offener Schachtofen, dessen Größe von etwa vier Meter Höhe im Spätmittelalter bis auf zu zehn Meter Höhe im 17. Jahrhundert anwuchs, wie zum Beispiel die Stücköfen in Vordernberg in der Steiermark, einem damaligen Zentrum der Roheisenerzeugung in Mitteleuropa.[9] Die Blasebälge der Öfen wurden durch Wasserräder angetrieben und die Anlagen wurden daher auch als Radwerk bezeichnet. Sie erreichten Temperaturen von bis zu 1600 °C; das Gemenge aus Eisenerz und Holzkohle wurde dabei teilweise zum Schmelzen gebracht. Eine Weiterentwicklung war der Blauofen, dessen Name aus einer Verballhornung des englischen Wortes blow (= blasen) entstand. Er entspricht im Prinzip dem Stückofen, hat aber eine geschlossene Ofenbrust.[8][10]
In den Schmieden weiterverarbeitet wurde jedoch zunächst nur der über dem Eisenbad angesammelte Eisenschwamm (Luppen), die in den Stücköfen eine solche Größe erreichte, dass sie nicht mehr von Hand, sondern mit ebenfalls durch Wasserkraft angetriebenen Schmiedehämmern weiterbearbeitet wurde.[11] Das durch den Schmelzprozess entstandene flüssige Roheisen erschien den Hüttenleuten zunächst als „verdorbenes Eisen“, das man nicht nutzen konnte, weil es einen so hohen Anteil Kohlenstoff aufgenommenen hatte, dass es zum Schmieden zu spröde war. Man nannte es Saueisen in Deutschland und Graglach, Dreckfluss in der Steiermark und pig-iron im englischsprachigen Raum.[12]
Erst die Erfindung verschiedener Verfahren zum Frischen des Eisens, etwa im 14. Jahrhundert,[8] löste das Problem. Damit war auch der Weg frei, die Leistungsfähigkeit der Öfen weiter zu steigern. Floßöfen mit meterdickem Mauerwerk entstanden, deren Gestell verengt war und bei denen das nach Beendigung des Verhüttungsvorgangs entstandene Roheisen (Flusseisen und Flussstahl) und die Schlacke gemeinsam abgelassen wurden. Floßöfen können als unmittelbare „Vorfahren“ des Hochofens angesehen werden, da sich nach deren Entwicklung am Eisengewinnungsprozess prinzipiell nichts mehr änderte. Der älteste bekannte Floßofen steht im Kerspetal (Bergisches Land). Er wird auf das Jahr 1275 datiert.[13] Im Siegerland gab es um 1450 rund 30 Hochöfen.[14] Mit der steigenden Leistungsfähigkeit der Öfen und der ansteigenden Nachfrage an Eisenwaren entstand allerdings ein neues Problem: Der zur Energieerzeugung nötige Bedarf an Holzkohle konnte nicht mehr gedeckt werden. Steinkohle wurde versuchsweise ebenfalls eingesetzt, konnte aber fast nur durch Kohlengräberei im Tagebau gewonnen werden. 1755 gab es im Ruhrgebiet fast 200 Zechen.[15]
Dem Engländer Abraham Darby I (1676–1717) gelang schließlich 1709 in Coalbrookdale die Produktion von Roheisen mithilfe von Koks, nachdem es zuvor einige erfolglose Versuche mit Steinkohle gegeben hatte.[16] Zusammen mit der von James Watt verbesserten Dampfmaschine als Antrieb für die Gebläse konnte die Leistungsfähigkeit der Hochöfen erheblich gesteigert werden. In Deutschland hingegen blieben ähnliche Versuche zunächst erfolglos. Erst im November 1796 gelang dem Königlichen Hüttenwerk Gleiwitz der Bau eines funktionsfähigen, mit Koks betriebenen Hochofens. Mithilfe des Kokses ließ sich die erzeugte Roheisenmenge bis auf zwei Tonnen täglich steigern, bei einem Verbrauch von dreieinhalb Tonnen Koks pro Tonne Roheisen. Diese Mengen Roheisen konnten die noch kleinen Frischöfen nur teilweise verarbeiten; der Rest wurde als Gusseisen verwendet.[17]
Mit Entwicklung der Kupolöfen gegen Ende des 18. Jahrhunderts erlebte die Gusseisenindustrie eine regelrechte Blütezeit. Kanonen, Kirchenglocken, Kochgeschirr und schließlich auch Kunstgegenstände wie beispielsweise mit Reliefs verzierte Ofen- und Kaminplatten und sogar Schmuck wurden aus Gusseisen gefertigt. Mit zu den größten Gusseisenerzeugnissen zählt unter anderem die 1777/79 erbaute Iron Bridge in England sowie die 1794 über das Striegauer Wasser bei Laasan (heute Łażany) im heutigen Polen erbaute Brücke mit einer Spannweite von 12 Metern.[17]
Eine letzte bedeutende Verbesserung der Leistungsfähigkeit von Hochöfen stellte die Verwendung von Heißluft dar, die zunächst von Röhrenwinderhitzern (Neilson, 1828) und später von den heute noch gebräuchlichen Cowper-Winderhitzern (1857) geliefert wurde.
Die frühesten sicher belegten Hochöfen in Europa standen im Schweden des 13. Jahrhunderts, zum Beispiel in Lapphyttan. Für die folgenden Jahrhunderte sind einzelne Hochöfen in Frankreich, Belgien und vor allem England nachgewiesen. Die älteste, weitgehend komplett erhaltene Hochofenanlage in Deutschland ist die Luisenhütte in Wocklum bei Balve im Sauerland. In Sachsen blieben in Brausenstein (1693), Schmalzgrube (1819) und Morgenröthe (1822) drei Holzkohle-Hochöfen aus dem 17. und 19. Jahrhundert erhalten. Ein Hochofen aus dem Jahre 1783 ist bei der Wilhelmshütte in Bornum am Harz zu besichtigen und im Sauerland wurde die ebenfalls im 18. Jahrhundert erbaute Wendener Hütte zu einem technischen Kulturdenkmal erklärt. In Thüringen steht in Schmalkalden-Weidebrunn das Hochofenmuseum Neue Hütte (Schmalkalden). Die spätklassizistische Hochofenanlage aus dem Jahre 1835 zeigt, wie aus den einheimischen Eisenerzen auf Holzkohlebasis Roheisen produziert wurde. Der Hüttenbetrieb bestand bis 1924.
Eisenverhüttung außerhalb Europas
.jpg.webp)
Spätestens seit dem 7. Jahrhundert kennt man den Tatara-Ofen, eine spezielle Art Rennofen, der in Japan zur Eisenerzeugung benutzt wird. Im Gegensatz zu den in anderen Regionen der Erde verwendeten Öfen ist ein Tatara-Ofen von kastenartiger Form mit einer Höhe von etwa 1,2 bis 2 Metern bei einer oberen Breite von 0,8 bis 1,2 Metern, die sich nach unten auf nur etwa 0,5 Meter verjüngt. Die Länge des Ofens beträgt dagegen etwa 4,5 Meter. Auf beiden Längsseiten sorgen 18 bis 20 keramische Düsen für eine ausreichende Luftzufuhr, die bei „modernen“ Betrieben über ein von mehreren Männern angetriebenes Flügelgebläse eingebracht wird. Der Tatara-Ofen wird abwechselnd mit Holzkohle und Eisenerzsand beschickt und erreicht Temperaturen von 1200 bis 1500 °C. Nach etwa drei Tagen werden die Ofenwände zerschlagen und ein etwa zwei Tonnen schwerer Block aus schmiedbarem Eisen und Stahl entnommen. Die entstandene Schlacke wurde zuvor im laufenden Betrieb abgelassen.[18] Auch heute noch wird der traditionell in Tatara-Öfen hergestellte und für seine Qualität bekannte japanische Stahl (tamahagane) zum Beispiel für hochwertige Küchenmesser (Hōchō) oder für das japanische Langschwert Katana benutzt.
Chinesische Öfen zur Eisenverhüttung des 19. Jahrhunderts glichen einem auf dem Kopf stehenden Kegelstumpf von etwa 2,5 Metern Höhe mit einem oberen Durchmesser von 1,2 Metern, einem unteren von knapp 60 Zentimeter und einer Wandstärke von 30 Zentimetern und wurden aus Lehm gebaut. Zur Sicherung war der Ofen mit einem Korb aus Eisengeflecht umgeben und konnte zur leichteren Entnahme des Roheisens um etwa 30° gekippt werden. Beschickt wurde mit Brauneisenstein, Kohleneisenstein („Blackband“) und je nach Bauart Holzkohle oder Koks. Die zur Reduktion des Erzes nötige Luft wurde mit einem handbetriebenen Zylindergebläse eingebracht. Auf diese Weise konnten pro Tag zwischen 450 und 650 Kilogramm Roheisen bei einem Koksverbrauch von 100 Kilogramm pro 100 Kilogramm Eisen erzeugt werden.[19] Eine ähnliche Hochofenanlage fand sich auch in der Provinz Bulacan auf den Philippinen, die bis um 1900 betrieben wurde. Der Hochofen hatte die Form eines unten geschlossenen, auf dem Kopf stehenden Kegelstumpfes mit einer Außenhöhe von 2,1 Metern, einem Außendurchmesser an der Gicht von 1,5 Metern und einer Wandstärke zwischen 30 und 80 Zentimeter.[20]
In Afrika wurden noch Anfang des 20. Jahrhunderts Völker entdeckt, die mithilfe von ein bis drei Meter hohen Schacht- oder Zugöfen Eisenerze reduzierten. Für den Bau nutzte man entweder Termitenhügel, die man passend aushöhlte, oder der Ofen wurde aus Lehm errichtet. Mehrere am unteren Ende des Ofens eingesetzte Düsen aus Keramik sorgten für ausreichend Luftzufuhr, die aufgrund der Kaminwirkung des hohen Schachts durch die Erz- und Kohlefüllung nach oben gesaugt wurde. Durch die obere Kaminöffnung füllte man mehrmals Erz und Kohle nach, bis nach etwa 20 Stunden eine fußballgroße Luppe entstand, die unten durch die aufgebrochene Ofenbrust entnommen wurde. Das für diese Öfen benötigte, sehr reine Eisenerz kam unter anderem aus Banjéli im Bassariland.[3]
Aufbau
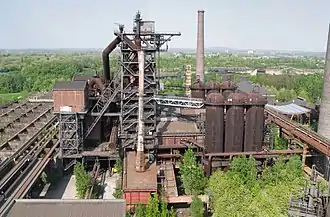
Bauteile von links nach rechts: Bunker, Windenhaus, Gichtgasleitungen mit Staubsack hinter dem Schrägaufzug zur Beschickung, Hochofen, Abstich-Halle, Winderhitzer
Um einen reibungslosen Dauerbetrieb während der sogenannten „Ofenreise“ von 10 bis 20 Jahren[21] bis zum nächsten fälligen Instandhaltungstermin zu gewährleisten, benötigt eine Hochofenanlage neben dem Hochofen selbst noch weitere essenzielle Einrichtungen. Dazu gehört der Bunker für die Einsatzstoffe mit einem angeschlossenen Transportsystem zur kontinuierlichen Beschickung des Hochofens, mit der die Einsatzstoffe über den Gichtverschluss in selbigen eingefüllt werden. Über eine Heißwindringleitung wird die im Winderhitzer vorgewärmte Luft über Düsen in den Hochofen eingeblasen, der im Inneren feuerfest ausgekleidet und außen von einem komplexen Kühlsystem umgeben ist. Angeschlossen an den Hochofen ist eine speziell ausgebaute Abstich- bzw. Gießhalle, in der das entnommene Roheisen während der regelmäßig vorgenommenen Abstiche in entsprechende Pfannen- oder Torpedowaggons geleitet und zur Weiterverarbeitung abtransportiert werden kann.
Der Bau einer modernen Hochofenanlage ist ein umfangreiches Großprojekt eines Hüttenwerkes und dauert von der Planung bis zur Inbetriebnahme zwischen 1,5 und 2,5 Jahre,[22] wovon die Planungsarbeit etwa die Hälfte der Zeit beansprucht. Die Investitionskosten beliefen sich beispielsweise für den Bau des neuen „Hochofens 8“ in Duisburg-Hamborn auf etwa 250 Millionen Euro.[22]
Bunker
Die meist per Bahn oder Schiff angelieferten Einsatzstoffe wie Eisenerze, Koks und Zuschläge (z. B. Kalk, Sand und Dolomit) werden zunächst in eine Bunkeranlage gebracht. Diese besteht aus mehreren Bunkern, die entweder gemauert oder aus Stahlbeton gegossen sind und in denen die ankommenden Rohstoffe gelagert werden. Um die Qualitätsunterschiede in der Zusammensetzung von Möller (Eisenerz, Zuschlagstoffe) und Koks auszugleichen, werden die Materialien vorher häufig auf so genannten Mischbetten vermischt.
Manche Rohstoffe werden bereits von den Zulieferern (unter anderem Bergwerke) vorbereitet. Teilweise muss eine vorgeschaltete Vorbereitung beispielsweise in einer Erzbrech-, Sinter- und Pelletieranlage für eine Aufbereitung sorgen, da die Partikel- bzw. Korngröße der Rohstoffe weder zu klein (Verstopfungsgefahr, schlechte Durchgasung) noch zu groß (keine optimale Rohstoffausnutzung) sein darf.
Beschickung
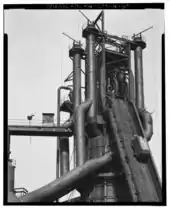
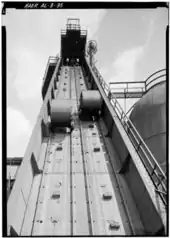
Von der Bunkeranlage aus werden Möller und Koks zum oberen Ende des Schachtes, der so genannten Gicht, transportiert. Die Zuführung des Materials wird auch als Beschickung oder Begichtung bezeichnet und erfolgt je nach Platzangebot entweder über Bandstraßen, Setzkübel oder kleine Schüttwaggons, sogenannte Loren bzw. Hunte (auch Hunde).
Im Falle der Wagenbeschickung oder auch „Skipbegichtung“ erfolgt die Beschickung über einen Schrägaufzug bis zur als „Gichtschleuse“ bezeichneten Einfüllöffnung, die den oberen Abschluss des Hochofens bildet. Für jeden Hochofen sind zwei Aufzugsysteme im Einsatz, die im Wechsel Koks und Möller transportieren. Neben der größeren Versorgungsleistung dient der Einsatz von zwei Aufzügen aber auch der Sicherheit gegen Ausfälle, um die ununterbrochene Versorgung des Hochofens zu gewährleisten. Bei modernen Hochöfen werden zur Beschickung mittlerweile Förderbänder bevorzugt eingesetzt. Diese können zwar nur geringe Steigungen überwinden und haben einen größeren Platzbedarf, besitzen aber eine höhere Leistungsfähigkeit, lassen sich leichter automatisieren und behandeln das Schüttgut schonender.[23][24]
Gichtverschluss
Das am Ofenkopf austretende Gichtgas besteht zum großen Teil aus heißem Stickstoff (N2), Kohlenmonoxid (CO) und Kohlendioxid (CO2) sowie geringen Anteilen weiterer Gase und mitgerissenem Staub (siehe auch unter Hochofenerzeugnisse). Trotz der Gefährlichkeit dieses giftigen und brennbaren Gasgemisches blieb die Gichtöffnung lange Zeit unverschlossen. Erst seit der Entwicklung der gichtgasbeheizten Winderhitzer im 19. Jahrhundert wird diese mit einem Schleusensystem versehen, womit eine Beschickung des Hochofens ohne Verlust des nun wertvoll gewordenen Brenn- und Heizgases möglich wurde. Das Gichtgas wird dabei über große Rohre abgefangen, vom mitgeführten Staub befreit und anschließend unter anderem den Brennern der Winderhitzer zugeführt.
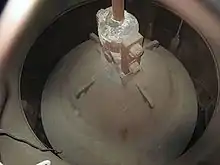
Den ersten Gichtverschluss mit einfacher Trichterschleuse erfand George Parry 1850 in Ebbw Vale, der später als „Parry-Trichter“ bekannt wurde.[25] Die bis in die 1970er-Jahre am weitesten verbreitete Form der Gichtschleuse war jedoch der „Doppelglockenverschluss“ mit einem von McKee entwickelten und zwischengeschalteten Drehtrichter zur Verteilung des Schüttguts. Zur Verringerung der Schütthöhe, die den definierten Durchmesser der Erzpellets gefährden kann, und bei Hochöfen mit höherem Gegendruck der Gicht, kamen aber auch Systeme mit drei oder vier Glocken zum Einsatz. Das große Gewicht dieser Konstruktion und die zunehmenden Probleme beim Erhalt der Dichtigkeit des Glockensystems setzten den Bemühungen einer Leistungserhöhung von Hochöfen mit Glockenverschluss schließlich eine Grenze.
Eine wesentliche Verbesserung des Gichtverschlusses brachte erst die Erfindung des luxemburgischen Unternehmens Paul Wurth S. A., namentlich Édouard Legille, der 1970/1971 den so genannten „glockenlosen Gichtverschluss“ (später auch „Paul-Wurth-Gichtverschluss“) entwickelte.[26] Statt eines komplexen und schweren Glockensystems stehen nun je nach Größe und Bedarf des Hochofens zwei oder mehrere Vorratsbehälter für Koks und Möller auf dem Ofenkopf, die über Bandverteiler oder Aufzugsysteme mit Schüttwaggons befüllt werden. Durch Fallrohre gelangen Koks und Möller in die Mitte des Ofenverschlusses zu einer dreh- und schwenkbaren Schurre, die das ankommende Material präzise und gleichmäßig auf der Schüttoberfläche verteilen kann. Abgedichtet wird das System über Dichtklappen, die sich über und unter den Vorratsbehältern befinden. Eine zusätzliche Materialklappe unter den Behältern sorgt für eine gleichbleibende Auslaufgeschwindigkeit des Schüttguts. Die Bauhöhe des neuen „Glockenlosen Gichtverschlusses“ verringerte sich um rund 1/3, womit auch das Gewicht der Konstruktion entsprechend sank, und die Dichtigkeit des Systems war leichter zu gewährleisten.[27]
Am 9. Januar 1972 wurde der weltweit erste glockenlose Gichtverschluss am Hochofen 4 der August Thyssen-Hütte in Hamborn in Betrieb genommen.[26] Aufgrund der vielen Vorteile gegenüber dem alten System setzte sich der Glockenlose Paul-Wurth-Gichtverschluss erfolgreich durch und kommt bei modernen Hochofenanlagen bevorzugt zum Einsatz.
Design
.jpg.webp)
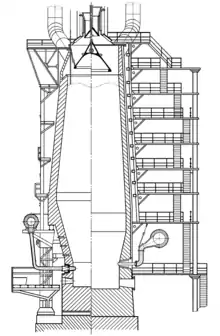
Links: mit Tragring und Stützsäulen
Rechts: „freistehender Hochofen“ mit kompletter Einrüstung
Der Hochofen selbst ähnelt als Schachtofen prinzipiell einem Kamin oder Schornstein, da diese Form aufgrund des entstehenden Kamineffekts eine optimale Durchgasung der Beschickung erleichtert. Die Bauhöhe des Hochofenkerns bestimmt dessen Leistungsfähigkeit und kann zwischen 30 und 75 m betragen. Die oberen 3/5[28] bilden den eigentlichen Schacht, der dabei einem langgezogenen Kegelstumpf entspricht. Daran angeschlossen folgt ein kurzer zylindrischer Zwischenring mit dem am Hochofen größten Innendurchmesser, der als „Kohlensack“ bezeichnet wird. Ein weiterer, auf dem Kopf stehender Kegelstumpf, die sogenannte „Rast“, mündet schließlich in das untere, zylindrisch ausgeführte „Gestell“. Kohlensack und Rast sowie Gestell machen jeweils 1/5 der Gesamthöhe aus. Bei einer Gesamthöhe von 30 m entfallen also auf den Schacht etwa 18 m, auf Kohlensack und Rast etwa 6 m und auf das Gestell ebenfalls 6 m.
Die gesamte Hochofenkonstruktion ist typischerweise umgeben von einem Stahlgerüst mit Arbeits- und Montagebühnen, das einerseits zur Aufnahme der Hilfseinrichtungen wie Materialaufzug und gegebenenfalls der Gichtschleuse dient, aber auch zum Stützen und Stabilisieren des Hochofens verwendet werden kann. Es kann dabei zwischen zwei Arten von Stützkonstruktion unterschieden werden:[29][30]
Ältere und vorwiegend amerikanische Hochöfen erhalten etwa in Höhe der Rast einen Tragring mit Stützsäulen, über den die auf dem Hochofen liegende Last von Ofenkopf und Gichtschleuse ins Fundament geleitet wird. Durch die Stützsäulen kommt es allerdings zu einer Einengung und damit Behinderung des Zugangs zum Abstichbereich sowie zu Problemen im Anschlussbereich zwischen Rast und Tragring. Aufgrund dieser Nachteile wird bei neueren Hochöfen inzwischen die zweite Variante bevorzugt.
Bei diesem in Deutschland entwickelten Design handelt es sich um einen sogenannten „freistehenden Hochofen“. Durch die Stahlpanzerung des Hochofens erhält man eine selbsttragende Ofenkonstruktion, die von einer kompletten Einrüstung für Arbeitsbühnen und zur Aufnahme der Hilfseinrichtungen umgeben ist. Dadurch entfallen die störenden Säulen im Abstichbereich und der Hochofen kann frei allen Wärmeausdehnungen folgen, die ein am Ofenkopf angebrachter Kompensator abfängt.
Die Gesamthöhe einer solchen Anlage beträgt etwa 90 m. Der Hochofen 2 in Duisburg-Schwelgern hat beispielsweise eine Ofenhöhe von nahezu 75 m, einen Gestelldurchmesser von 14,9 m und ein Nutzvolumen von rund 4800 m³,[31] erschmilzt täglich rund 12.000 t Roheisen und gilt zurzeit (Stand 2014) als größter Hochofen Europas.[32] Zwölf Hochöfen auf der Welt überschreiten 5.500 m³ Nutzvolumen (Stand 2013).[33] Der bisher größte bekannte Hochofen der Welt mit einem Nutzvolumen von 6.000 m³ steht in den „Gwangyang Steel Works“ von POSCO in der südkoreanischen Provinz Jeollanam-do.[34]
Am unteren Ende der Rast befindet sich die mit einem keramischen Stopfen verschlossene Abstichöffnung für das Roheisen, über die die entstandenen Hüttenprodukte Roheisen und Schlacke abgelassen werden können. Zur völligen Entleerung („Sauabstich“) bei einer bevorstehenden Neuzustellung des Hochofens ist an der tiefsten Stelle des Gestells sowie in dessen Boden je ein „Sauloch“ (auch Ofensau) angebracht.[35]
Die Düsen der Heißwindringleitung setzen an der Grenze zwischen Rast und Gestell an und werden von Winderhitzern versorgt.
![]() |
Region und Zeitraum | Gestell Ø d in m |
Höhe H in m |
Nutzinhalt in m³ |
Leistung in Tonnen pro Tag |
---|---|---|---|---|---|
1) Hochofen 1861 | 0,9 | 15,3 | 64 | 25 | |
2) Westdeutsche Sonderroheisen-Hochöfen der 1930er Jahre | 4,5 | 20,0 | 425 | 450 | |
3) Westdeutsche Stahl- und Thomasroheisen-Hochöfen 1961 | 6,5 | 24,0 | 900 | 1.200 | |
4) Westdeutsche Hochöfen 1959 | 9,0 | 26,1 | 1.424 | > 2.000 | |
5) Sowjetische Hochöfen 1960 | 9,8 | 29,4 | 1.763 | 4.000 | |
6) Japanische Hochöfen 1968 | 11,2 | 31,5 | 2.255 | 6.000 | |
7) Westdeutsche Großhochöfen 1971/72 | 14,0 | 36,7 | 4.100 | ≈ 10.000 |
Ausmauerung
Ursprünglich bestanden Hochöfen außen aus einem meterdicken, lasttragenden und wärmedämmenden Mauerwerk aus Ziegeln oder Bruchsteinen (Rauchgemäuer) und waren innen mit einer feuerfesten Auskleidung versehen (Kerngemäuer). Bei modernen Hochöfen übernehmen zentimeterdicke Stahlpanzerung und Stützgerüst die Traglast, während das Kerngemäuer allein für die nötige Feuerfestigkeit und Wärmedämmung sorgt.
Um die gewünschte Standzeit (Ofenreise) bis zur fälligen, vollständigen Erneuerung der Hochofenauskleidung[37] zu erreichen, ist der gesamte Hochofenkern vom Schacht bis zum Gestell feuerfest ausgekleidet. Die Ofenauskleidung gibt zudem das endgültige Innenprofil des Ofens vor. Bei einer Gesamtfläche von etwa 2000 m² und einer Dicke von einigen Dezimetern bis über einem Meter können überdimensionierte Ausmauerungen enorme Kosten verursachen, weshalb man sich schon während der Planung bemüht, nur solche Steine zu verwenden, die speziell auf die Anforderungen des jeweiligen Ofenabschnitts abgestimmt sind.
Im oberen Schachtbereich sind die Temperaturen relativ niedrig, die mechanischen Beanspruchungen sind dagegen hoch aufgrund der aufprallenden Beschickung. Entsprechend kommen hier Schamotte mit einem Korundgehalt zwischen 30 und 40 % zum Einsatz. Zusätzlich werden im Eintrittsbereich der Beschickung noch „Schlagpanzer“ aus Stahlplatten angebracht, die die Beschädigung der Ausmauerung durch den Aufprall der Möllerstoffe verhindern sollen.[38]
Im unteren Schachtbereich bis zum Kohlensack nehmen die Temperaturen schnell zu. Die Beanspruchung durch Abrieb sinkt aber nur langsam, da die Beschickung möglichst lange fest bleiben und dem Druck der Möllersäule standhalten soll, um so eine gute Durchgasung zu ermöglichen. Außerdem müssen die Steine in diesem Bereich chemisch stabil sein, da die Reaktionsfähigkeit der umgebenden Stoffe wächst. Entsprechend werden hier hochfeuerfeste Schamotte mit einem Korundanteil zwischen 60 und 86 % oder Halbgraphitsteine verbaut.
In Höhe der Winddüsen und im Rastbereich ist die Ausmauerung höchsten Temperaturen und Drucken ausgesetzt, denen nur Kohlenstoffsteine,[39] Schmelzspinellsteine mit Chromoxid oder Chromkorundsteine standhalten.
Kühlung
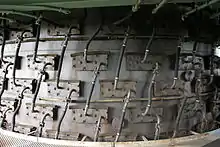
Zum Schutz vor Überhitzung enthält der Hochofen etwa ab dem oberen Drittel des Schachtes bis zum Gestellboden ein System aus Kühlwasserleitungen und -Elementen (Staves), die mit der Panzerung verbunden sind. Da ein Hochofen mit einem Gestelldurchmesser von 8 m einen Wasserumsatz von mehr als 30.000 m³ pro Tag hat, was etwa dem Verbrauch einer mittleren Stadt mit etwa 200.000 Einwohnern entspricht,[38] muss das Kühlsystem entsprechend ausgelegt und zum Schutz gegen Ausfälle mehrfach gesichert sein.
Die früher verbreiteten, offenen Kühlkreisläufe sind bei modernen Hochöfen des 20. Jahrhunderts meist nur noch bei der Ofenkopf- und Gestellberieselung sowie in Notfällen (z. B. bei Ausfall eines geschlossenen Kreislaufs) im Gebrauch. In offenen Kreisläufen wird das benötigte Wasser den nahegelegenen Gewässern (Flüssen, Seen) entnommen und vor der Nutzung im Kühlsystem von Feststoffen gereinigt. Nach Gebrauch übernehmen Kühltürme die Rückkühlung des Wassers, bevor es wieder der Umgebung zugeführt wird. Geschlossene Kreisläufe nutzen dagegen aufbereitetes, entsalztes und entgastes Wasser, das nach Gebrauch über Wärmetauscher wieder abgekühlt und dann erneut dem Kühlsystem zugeführt wird. Neben dem Schutz der Kühlelemente und -leitungen vor Ablagerungen hat aufbereitetes Wasser den Vorteil, dass das Kühlsystem größere Wärmemengen aufnehmen kann.[40][41]
Die Konstruktion der Kühlelemente ist so ausgeführt, dass sie einerseits die Ausmauerung stützen können, sich andererseits bei Beschädigung aber auch schnell auswechseln lassen. Sie bestehen entweder aus Stahlblech, Gusseisen oder Kupfer und sind an der Panzerung entweder angeschraubt, verkeilt oder verschweißt. Bei der Gestaltung der Kühlelemente lassen sich zwei grundsätzliche Bauformen unterscheiden:
- Kühlkästen sind flache, rechteckige Elemente mit labyrinthartig eingezogenen Leitblechen zur Lenkung des Wasserstroms und einem sich zur Ofenmitte hin verjüngenden Profil, das einen schnellen Aus- und Einbau ermöglicht. Die Kühlkästen werden zwischen die Panzerplatten des Schachtes eingeschoben, so dass ein schachbrettartiges Muster aus Panzerplatten und Kühlkästen entsteht.
- Plattenkühler oder auch Staves bestehen aus Spezialguss mit eingegossenen, senkrecht stehenden Kühlrohren. Sie werden an die von der Ofenmitte abgewandte Seite der Panzerung angeschraubt. Die Auflagefläche der Staves ist kammartig mit Nuten durchzogen, die mit Isoliermasse gefüllt werden.
Je nach Anforderung an die Kühlleistung kommen am Hochofen verschiedene Arten der Kühlung zum Einsatz. Der Ofenkopf wird im Bereich der Schlagpanzer mit einer außen liegenden Berieselungsanlage gekühlt. Im Bereich des Schachtes sind überwiegend Kühlkästen eingebaut und im Bereich von Kohlsack und Rast werden Kühlkästen und Plattenkühler eingesetzt. Aufgrund der in diesem Bereich besonders starken Hitzebelastung werden die Kühlelemente in engen Abständen gesetzt, damit möglichst viel Wärme abgeführt werden kann. Die Blasformen erhalten einen eigenen, doppelten Kühlkreislauf. Gestell und Boden werden entweder mit Rieselwasser oder durch Einleiten von Wasser in einen Doppelgestellmantel gekühlt.[42]
Winderhitzer
.png.webp)
James Beaumont Neilson war einer der ersten, der Winderhitzer in rekuperativer Bauform – die benötigte Luft wird durch Wärmetauscher aufgeheizt – entwickelte und patentieren ließ. Zuvor wurden Hochöfen immer mit Kaltluft betrieben, da man im Hüttenwesen seit alters her die Erfahrung gemacht hatte, dass ein Hochofen im Winter besser lief als im Sommer.[43] Deshalb stieß Neilsen zunächst auf großen Widerstand bei dem Versuch, das neue Prinzip einzusetzen. Auch ein 1828 von den Clyde Iron Works gestatteter Versuch mit Gebläsewind, der nur auf 27 °C[44] erwärmt war und dennoch dafür sorgte, dass die anfallende Schlacke eisenärmer und deutlich flüssiger wurde, überzeugte die Arbeiter noch nicht. Neilsons recht einfach konstruierte Winderhitzer bestanden aus einem Stück gewölbeförmig gebogener Zuführungsleitung, die über ein Rostfeuer erhitzt wurde. Ein über dem Rohrgewölbe angebrachter Blechkasten hielt die Wärme eine Weile fest, um die Wärmeübertragung zu verbessern. Weitere konstruktive Verbesserungen durch Einsatz von wärmebeständigeren Gusseisenrohren und -kästen sowie verlängerte und gebogene Heizschlangen zur Aufnahme der Wärmeausdehnung versetzten diese „Röhren-Winderhitzer“ in die Lage, den Gebläsewind bis auf 315 °C aufzuheizen.
Jahr | Windsystem | Brennstoffverbrauch in kg pro t Roheisen |
Roheisenmenge in 24 h in kg |
1829 | Kaltwind | Koks 8060 | 1607 |
1830 | Heißwind | Koks 5160 | 2353 |
1833 | Heißwind | Rohkohle 2280 | 3556 |
Der Widerstand gegenüber der Verwendung von Heißwind legte sich gänzlich, als die erzielten Roheisengewinne immer deutlicher stiegen und gleichzeitig die benötigten Brennstoffmengen erheblich gesenkt werden konnten. Selbst Rohkohle konnte jetzt genutzt werden, was vorher unmöglich war.
Seit Mitte des 18. Jahrhunderts wird nachgewiesenermaßen auch Gichtgas im Hüttenwesen genutzt, anfangs jedoch nur zum Rösten von Erz, Trocknen von Gussformen und Brennen von Kalk und Ziegelsteinen.[46] Erst Wilhelm von Faber du Faur gelang es Anfang 1832 einen effektiven und stabilen Röhren-Winderhitzer, den „Wasseralfinger Winderhitzer“ zu entwickeln, der mit Gichtgas beheizt wurde und die Windtemperatur auf 540 °C erhöhte. Damit war allerdings auch die Leistungsgrenze dieser Bauform erreicht.[47]
.jpg.webp)
Eine entscheidende Verbesserung in der Versorgung der Hochöfen mit Heißwind konnte schließlich Edward Alfred Cowper (1819–1893) für sich verbuchen, indem er die Winderhitzer nicht mehr aus einem System von Röhren, sondern mit feuerfesten, luftdurchlässigen Viellochsteinen konstruierte. Die „Cowper-Winderhitzer“ brachten bereits in der ersten Entwicklungsstufe innerhalb von einer Minute 29 m³ Luft auf eine Temperatur von 650 bis 700 °C. Gemessen werden konnte die Windtemperatur zu dieser Zeit nur mit Schmelzproben verschiedener Metalle. Die bisher verwendeten Proben aus Blei (SP = 327,4 °C) und Zink (SP = 419,5 °C) konnten bei Cowpers Winderhitzern nicht mehr angewendet werden und selbst Antimon (SP = 630,6 °C) schmolz innerhalb von Sekunden.[48] Eine weitere ebenfalls von Cowper entwickelte Neuerung war der regenerative Wechselbetrieb von zwei Winderhitzern, bei dem einer durch Gichtgasbefeuerung aufgeheizt wurde, während der andere die gespeicherte Hitze an die eingeblasene Kaltluft abgab.
Modernere „Cowper-Winderhitzer“ bestehen aus einem senkrecht stehenden Stahlrohr von 20 bis 35 m Höhe bei einem Durchmesser von 6 bis 9 m.[49] Nach innen folgt zunächst eine Schicht wärmedämmender Steine und anschließend eine Schicht aus feuerfesten Schamotte-Steinen. Der Kern besteht vollständig aus übereinander geschichteten Viellochsteinen aus Silika. An einer Seite des Schachtes ist ein ebenfalls feuerfest ausgekleideter Brennschacht bis in Höhe der Kuppel abgeteilt, der etwa ein Drittel[50] des Winderhitzer-Querschnitts einnimmt. Am unteren Brennschacht befinden sich die Brenndüsen und die Anschlüsse für Kaltluft und Heißluft. Eine andere Möglichkeit ist der Bau eines unabhängig vom Winderhitzerschacht außen liegenden Brennschachtes. Diese Bauform hat den Vorteil, dass einerseits Risse, die durch die starken Temperaturschwankungen in der Trennwand zwischen Brenn- und Heizschacht auftreten, vermieden werden und andererseits der Winderhitzer selbst mehr Platz für Viellochsteine hat und damit die Heizleistung nochmals gesteigert werden kann.
Meist sorgen drei, bei größeren Hochöfen auch vier „Cowper“ für eine reibungslose und störungsfreie Versorgung des Hochofens mit Heißluft. Während zwei zeitlich versetzt aufgeheizt werden, drückt ein Axial- oder Radialgebläse Kaltluft (rund 1,4 t pro Tonne Roheisen) mit einem Druck von 2 bis 4,5 bar[51] durch den dritten Winderhitzer. Die zuvor verwendeten Dampf- bzw. Gaskolbengebläse erwiesen sich als nicht wirtschaftlich und schlecht regelbar. Im ständigen Kreislauf erfolgt dann ein Wechsel auf den zuvor länger erhitzten Cowper, während der abgekühlte wieder aufgeheizt wird. Die Aufheizphase beträgt dabei etwa 50 Minuten, die Windphase dagegen nur etwa 30 Minuten, da der Winderhitzer nicht unter eine für Silikasteine kritische Temperatur von 721 °C fallen darf. Silikasteine machen unterhalb dieser Temperatur mehrere Modifikationswechsel durch, was zu einem „Volumensprung“ führt, der die feste Struktur des Viellochstein-Besatzes zerstört und ihn zum Einsturz bringen kann.[52] Der dritte bzw. vierte „Cowper“ dient zudem als Reserve gegen Ausfälle und bei Wartungsarbeiten.
Heißwindringleitung und Düsen
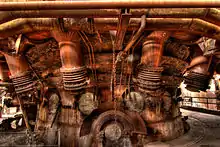

Mit einer maximal erreichbaren Temperatur von 1270 °C (1980) bis 1350 °C (1985) gelangt der Heißwind über die „Heißwindringleitung“ zu den je nach Baugröße des Hochofens zwischen 10 und über 40 Düsen und über die sogenannten Blasformen in den Ofen. Zur Verminderung des Koksverbrauches werden in vielen Werken Ersatzreduktionsmittel über die Formen eingeblasen wie beispielsweise Tierfett oder schweres Heizöl. Da allerdings der Ölpreis im Laufe der Zeit immer weiter anstieg, gab es verschiedene Versuche mit anderen Ersatzstoffen.
Bei Armco in den USA wurde über längere Zeiträume und in chinesischen Betrieben ab 1963 sogar im Dauerbetrieb Kohlenstaub als Brennstoffersatz erfolgreich eingesetzt.[53] Seit 2006[54] werden auch fein pelletierte Altkunststoffe (6 mm × 9 mm) zugesetzt, die neben der im Gegensatz zur Ablagerung auf Deponien umweltfreundlichen Verwertung von Kunststoffabfällen auch die Emission von CO2 und SO2 verringern.[55]
Zum Schutz vor Schäden durch die Wärmebelastung erhalten Ringleitung und Zuführungsstutzen eine feuerfeste Ausmauerung, die gleichzeitig wärmedämmend wirkt, um Wärmeverluste zu vermeiden. Die Blasformen selbst werden intensiv mit Wasser gekühlt, da sie je nach Abnutzungsgrad der Hochofenausmauerung bis zu einem halben Meter in den Ofen hineinragen können und dann höchsten Beanspruchungen durch Temperatur und Druck der Möllersäule ausgesetzt sind. In modernen Hochöfen kommen daher nur noch Hohlformen aus Elektrolytkupfer mit einem Doppelkammer-Kühlwasserkreislauf zum Einsatz. Wenn die Vorderkammer im Verlauf der Ofenreise abbrennt, kann der entsprechende Kühlkreislauf abgeschaltet und mit der Hauptkammer bis zum nächsten Stillstand weitergefahren werden.
Roheisen- und Schlackeabstich
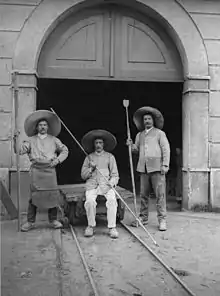
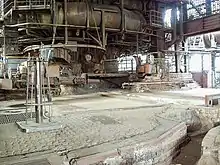
Der Roheisen-Abstich erfolgt in regelmäßigen Abständen von etwa zwei bis drei Stunden.[56] Dabei wird der Keramik-Stopfen an der Abstichöffnung mit einem Druckluft-Bohrer aufgebohrt. In seltenen Fällen, beispielsweise wenn der Bohrer versagen sollte, wird die Öffnung auch mit einer Sauerstofflanze durchstoßen.
Etwa 15 bis 20 Minuten[56] lang fließt dann das Roheisen in einer speziell ausgebauten Abstich- bzw. Gießhalle mit Arbeitsbühne und einem feuerfest gemauerten Rinnensystem, das zusätzlich noch mit feuerfesten Massen ausgestampft bzw. ausgegossen ist.[57] Bei älteren Hochöfen mit höherer Schlackeproduktion wurde zunächst ein Teil der Schlacke als so genannte „Vorschlacke“ in Höhe der Formenbühne abgestochen. Danach erfolgte der weitere gemeinsame Abstich von Roheisen und Schlacke über eine Art Siphon, dem sogenannten „Fuchs“, der die Schlacke vom Roheisen (nach Art des Dekantierens) trennte und über ein entsprechend ausgelegtes Rinnensystem in verschiedene Richtungen ablenkte. Moderne Hochöfen mit geringerer Schlackenproduktion, aber einer Roheisen-Tagesleistung von 3000 Tonnen und mehr brauchen zwar keinen Vorabstich der Schlacke mehr, dafür aber zwischen zwei und vier Stichlöcher. Das System aus Rinnen und Füchsen ist entsprechend komplex und bedarf der sorgfältigen Überwachung.
In der Hauptrinne zwischen Stichloch und Fuchs, die etwa 8 bis 14 Meter lang ist und etwa 20 bis 60 Tonnen Roheisen samt Schlacke fasst, hat die Schlacke Zeit, sich vom Roheisen abzusetzen und an der Oberfläche zu sammeln. Vor dem Fuchs, dessen „Nase“ in die Schmelze eintaucht, staut sich die Schlacke und wird über seitlich abzweigende Rinnen abgeleitet.[58] Das Roheisen fließt dagegen unter dem Fuchs durch bis zu einem Loch, unter dem ein Pfannen- oder Torpedowaggon bereitsteht, der das aufgefangene Eisen zur Weiterverarbeitung ins Stahl- oder Gießwerk transportiert. Auch die Schlacke wird mit speziellen Waggons aufgefangen und zur Weiterverarbeitung abtransportiert.
Nach Beendigung der Abstichphase wird das Stichloch bis zum nächsten Abstich mithilfe einer „Stichlochstopfmaschine“ wieder verschlossen.
Moderne Gießhallen müssen zum Schutz der Mitarbeiter und der Umwelt „raumentstaubt“ werden, das heißt im Bereich der Stichlöcher und an der Übergabestelle zu den Auffangbehältern sind Absaugsysteme installiert und das Rinnensystem mit Stahlplatten abgedeckt. Die abgefangenen Abgase werden in entsprechenden Filteranlagen gereinigt.[59]
Funktion
Anblasen
Bevor ein neuer Hochofen in den Produktionsbetrieb gehen kann, muss er zunächst mit Hilfe von Gasbrennern oder durch Einblasen von Heißluft langsam getrocknet werden. Erst dann erfolgt das eigentliche „Anblasen“ des Ofens. Die Wahl der Anblasmethode hat dabei große Auswirkungen auf seine anschließende Betriebsweise und seine Lebensdauer, kann sich von Werk zu Werk unterscheiden und dauert etwa ein bis zwei Wochen (bei älteren Hochöfen mitunter auch mehrere Monate).[60]
Nach dem Trocknen erfolgt die erste Befüllung des Gestells mit Holz und Koks. Im Schacht darüber werden schichtweise Koks und der aus Eisenerz und schlackebindenden Zuschlägen bestehende Möller eingefüllt, angezündet und durch Einblasen von Heißluft angefacht.[61] Die Zusammensetzung der Anblasschichtung unterscheidet sich stark von der späteren Betriebsschichtung. Sie enthält wesentlich mehr Koks, da das Aufwärmen der Hochofenauskleidung und der kalten Koks-Möller-Säule viel Energie verbraucht. Für eine Aufwärmung und den Schutz des Gestells sorgt der Einsatz einer entsprechend hohen Schlackemenge.[60]
Aufbau und Verhalten der Beschickung während des Ofendurchgangs
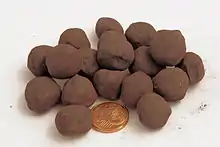
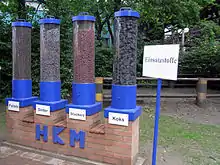
Von entscheidender Wichtigkeit für die Leistungsfähigkeit eines Hochofens sind Form, Zusammensetzung und mechanische Eigenschaften der Beschickung, vor allem der Erze, sowie eine möglichst einheitliche Korngröße. Auch das Reduktionsverhalten bei erhöhter Temperatur spielt eine Rolle, wobei ein möglichst geringer Niedrigtemperaturzerfall und eine hohe Erweichungstemperatur bei gleichzeitig geringem Temperaturbereich der Erweichungsphase angestrebt werden. Nur wenn Sinter und Pellets möglichst lange stückig und im festen Zustand verbleiben, halten sie der Druckbelastung der darüber liegenden Schichten stand und können eine gute Durchgasung gewährleisten.
Die Reduzierbarkeit des Sinters ist abhängig von dessen Zusammensetzung und wird mit der empirischen Größe der Basizität
beschrieben, die das Massenverhältnis von Calciumoxid und Magnesiumoxid zu Siliciumdioxid wiedergibt. Die Reduzierbarkeit ist dabei besser, wenn die Basizität der Zusammensetzung im basischen Bereich liegt (B > 1,0), und erreicht ein Reduzierbarkeitsmaximum im Bereich von 2,0 bis 2,5. Die mechanische Belastbarkeit ist ebenfalls in diesem Bereich am größten. Ab einer Basizität von 2,6 und höher nimmt der Anteil der Schmelzphase im Sinteranteil zu, was die Poren verschließt und die Reduktionsfähigkeit verringert, da die Reduktionsgase nicht mehr direkt an den Erzanteil gelangen. Bei sauren Sintern (B < 1,0) setzt die Erweichungsphase teilweise bereits ein, wenn erst etwa 15 % des Erzes reduziert worden sind.[62]
Im Gegensatz zum Sinter haben Pellets eher eine saure Zusammensetzung, da aufgrund ihrer stabilen Kugelgestalt die Neigung zur Feinkornbildung und Verschlechterung der mechanischen Eigenschaften geringer ist. Pellets bestehen also überwiegend aus Hämatit, verschiedenen Silicaten zur Schlackebindung und Poren. Der Anteil an Hämatit muss allerdings begrenzt bleiben, da sich das Gefüge der Pellets ansonsten im Verlauf der Reduktion zu sehr auflockern und die Pellets schließlich zu konzentriertem Staub zerfallen würden, was einen erheblichen Verlust der Druckfestigkeit zur Folge hätte. Die gleichzeitig übermäßig stattfindende Erhöhung des Pelletvolumens (Schwellen) birgt zusätzlich die Gefahr der Hochofenverstopfung in sich.[63]
Um herauszufinden, wie sich Aufbau und Zustand der Beschickung auf dem Weg von der Gicht bis zur Abstichöffnung verändern und welche Reaktionen im jeweiligen Ofenabschnitt erfolgen, wurden in den 1970er Jahren mehrere Versuche vor allem in Japan durchgeführt, bei denen man Hochöfen mitten in der Produktion stoppte und intensiv mit Wasser herunterkühlte. Alle noch laufenden Reaktionen innerhalb der Möllersäule wurden damit quasi „eingefroren“. Die anschließend erfolgten Analysen der Schichtungszusammensetzung auf verschiedenen Ebenen ergaben zusammenfassend, dass sich die Erweichungs- und Schmelzzone glockenförmig an der Mittelachse nach oben wölbt. Das Zentrum der Glocke besteht aus Koks, der in der 1000 bis 1600 °C heißen Zone immer noch gasdurchlässig ist. Über diese aktive Koksglocke gelangen die schmelzenden Erze und Schlacken nach innen und sinken bis in Rast und Gestell, während der eingeblasene Heißwind gleichmäßig nach außen und oben verteilt wird. Der bisher angenommene so genannte „Tote Mann“ – ein ruhender und reaktionsloser, kegelförmiger Körper aus Koks und verfestigtem Eisen – existiert also nicht.[64]
Lediglich der Fuß dieser „kohäsiven Zone“ ist gasundurchlässig und befindet sich optimalerweise in Höhe der Rast. Er soll von der Durchgasung auch nicht betroffen sein, damit zum einen die Zustellung (feuerfeste Auskleidung) von Kohlensack und Rast weniger angegriffen werden und zum anderen würden die dabei entstehenden Verwirbelungen des Heißwindes eine gleichmäßige Reduktion der Beschickung erschweren oder gar verhindern. Um die Durchgasung in der beschriebenen Form zu optimieren und damit den Energieverbrauch bei gleichzeitiger Steigerung der Roheisenqualität zu senken, ist eine sorgfältige Berechnung der Zonenquerschnitte sowie der eingebrachten Heißwindmenge und Zusammensetzung von großer Wichtigkeit.
Folgende weitere Erkenntnisse wurden bei der Untersuchung an „eingefrorenen“ Hochöfen gewonnen:[65]
- Die sich abwechselnde Beschickung mit Möller und Koks bleibt während des gesamten Ofendurchgangs bis in tiefere Schichten erhalten. Lediglich die Schichtdicken werden im Verlauf der Reduktion geringer.
- In Höhe der Blasebene finden sich statt der festen Erze nur noch Tropfen von metallischem Eisen und mit Schlacke vermischter Koks.
- 3 bis 4 Meter unter der Beschickungsebene beginnt die Reduktion mit der Folge, dass die Korngröße von Sinter, Pellets und Stückerz gleichmäßig abnimmt. Dabei tritt der Sinterzerfall bereits bei einer Temperatur von 200 bis 500 °C ein, der von Stückerz dagegen erst bei etwa 800 bis 900 °C.
- 7 Meter unter der Oberfläche ist die Reduktion so weit fortgeschritten, dass der Sinteranteil nicht weiter zerfällt. Für die anderen Möllerstoffe gilt dies jedoch nicht, da bis in eine Tiefe von 18 Meter ein immer weiter ansteigender Anteil an Feinkorn unter 5 Millimeter festgestellt wurde. Ob und an welcher Stelle im Hochofen sich Feinkorn bildet, hängt jedoch von der Temperatur und Gasstromverteilung, von der Aufheizgeschwindigkeit sowie von der Art der Beschickung ab. Beim Sinter ist der Feinkornanteil grundsätzlich höher.
- Die Reduktion verläuft in der Mitte des Hochofenquerschnitts viel rascher als im Randbereich.
- In Höhe der Gicht nimmt die Festigkeit aller Möllerstoffe zunächst stark ab und in zunehmender Tiefe wieder zu, was mit dem Fortschreiten der Reduktion und der damit verbundenen Zunahme des Eisenanteils zusammenhängt.
Reduktionsschädling Schwefel
Großen Einfluss auf die Reduktionsvorgänge haben die immer in der Beschickung vorhandenen Alkalien und Schwefelverbindungen. Besonders nachteilig auf die ablaufenden Reduktionsvorgänge wirken vor allem die Schwefelverbindungen, die sich trotz aufwändiger Vorbehandlung von Erz und Koks nie ganz austreiben lassen. Bereits geringe Mengen Schwefeldioxid (SO2) von etwa 5 bis 50 ppm im Reduktionsgas beschleunigen zwar zunächst den Sauerstoffabbau erheblich; sobald allerdings das erste metallische Eisen auftritt, kehrt sich der Vorgang um und der Sauerstoffabbau wird stark verlangsamt. Ursache für diese Reaktion ist die Eigenschaft des Schwefels, sich oberflächlich mit dem metallischen Eisen zu verbinden und dadurch die Aufnahme von Kohlenstoff zu verhindern.
Die Reaktion des Wüstits (Eisen(II)-oxid, FeO) mit Kohlenmonoxid (CO) verläuft üblicherweise nicht nur über die Oberfläche des FeO, sondern auch über die Oberfläche des bereits ausgeschiedenen Eisens. Aufgrund des besseren Absorptionsverhaltens von Eisen findet über selbiges ein Großteil des Gastransports von und zur Phasengrenze Eisen-Eisenoxid statt. Dies geschieht jedoch nur, wenn das Eisen ausreichend Kohlenstoff aufnehmen (aufkohlen) konnte. Wird die Aufnahme des Kohlenstoffs vom Schwefel blockiert, kann die Reduktion nur noch an der Oberfläche des Eisenoxids stattfinden.
Der Schwefel als Reduktionsschädling ist auch die Ursache für das bereits beschriebene übermäßige Schwellen der Pellets. Da die Auskristallisation des Eisens nur noch in Richtung des sich abbauenden Eisenoxids stattfinden kann, kommt es zu einer langgestreckten, faserigen Ausbildung der Eisenkristalle. Die bereits aufgrund der ersten Reduktionsstufe aufgelockerte Pelletstruktur verstärkt sich noch einmal und das Pelletvolumen kann insgesamt auf das zwei- bis dreifache seines Ursprungsvolumens anwachsen.[66]
Um den Anteil an Schwefelverbindungen möglichst niedrig zu halten, werden zum einen sulfidische Erze durch sorgfältiges Rösten in Oxide überführt und zum anderen schwefelbindende Zuschläge eingebracht.
Chemische Reaktionen während der Reduktion
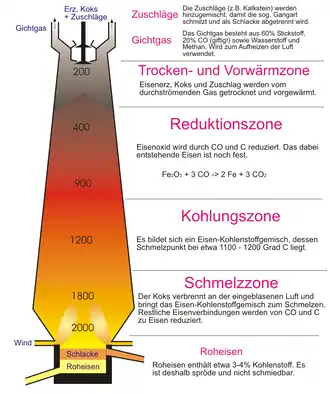
Im Hochofen vollziehen sich verschiedene metallurgische Vorgänge teilweise zeitgleich nebeneinander, bei denen einerseits über mehrere Stufen das Eisenerz zu Roheisen reduziert und die nicht-reduzierbaren Anteile in die Schlacke überführt werden.
Um überhaupt erst eine Reduktion der Eisenerze in Gang zu bringen, müssen allerdings zunächst die dafür nötigen Reduktionsgase erzeugt werden. Dies geschieht im unteren Bereich des Hochofens bei der Verbrennung des im Koks enthaltenen Kohlenstoffs mit Sauerstoff.
Die Reaktion ist stark exotherm, das heißt, es wird Wärme frei, die bei dieser Reaktion 394,4 kJ/mol[67] beträgt und den Hochofen im Bereich der Heißwind-Ringdüsen auf eine Temperatur von 1800 bis 2000 °C, bei Einsatz von zusätzlichem Sauerstoff sogar auf 2200 °C erhitzt. Zwei unmittelbar darauffolgende endotherme, also wärmeverbrauchende Reaktionen senken die Temperatur jedoch wieder auf etwa 1600 bis 1800 °C.
Die so genannte „Boudouard-Reaktion“ , die allerdings eine Mindesttemperatur von 1000 °C benötigt, erfordert 172,45 kJ/mol.
Eine gleichzeitig stattfindende Aufspaltung des im Heißgas befindlichen Wasserdampfs benötigt nochmals 131,4 kJ/mol.[68]
Die beiden reduktionsfähigen Gase Kohlenmonoxid und Wasserstoff steigen entgegen dem Materialstrom im Hochofen nach oben. Aufgrund dieser Eigenschaft – absinkende Möller-Koks-Säule einerseits und aufsteigende, dem wandernden Schüttgut entgegenströmende Reaktionsgase andererseits – wird der Hochofen auch als „Gegenstrom-Reaktor“ sowie als „Wanderbett-Reaktor“ bezeichnet.
In der Temperaturzone zwischen 400 und 900 °C findet die so genannte „Indirekte Reduktion“ statt. Über drei Stufen reagieren die verschiedenen Eisenoxide jeweils mit Kohlenmonoxid bzw. Wasserstoff, bis schließlich metallisches Eisen vorliegt:[69]
Reaktion mit Kohlenmonoxid (CO) | Reaktion mit Wasserstoff (H2) |
---|---|
Aus Hämatit entsteht der stärker eisenhaltige Magnetit. | |
Aus Magnetit entsteht Wüstit. | |
Aus Wüstit entsteht metallisches Eisen, das sich unten im Hochofen ansammelt. |
Solange sich das entstehende Kohlendioxid (CO2) im Temperaturbereich von über 1000 °C aufhält, wird es durch die Boudouard-Reaktion immer wieder zu Kohlenmonoxid (CO) regeneriert und steht dem Reduktionsprozess erneut zur Verfügung. Die Reduktion durch Wasserstoff ist bei etwa 800 °C besonders effektiv. Ein Gehalt von nur 10 % Wasserstoff im Reaktionsgas verdreifacht die Reduktionsgeschwindigkeit, allerdings sinkt diese wieder bei weiterer Erhöhung der Temperatur. Auch darf die Korngröße des Erzes ein gewisses Maß nicht überschreiten, damit die Diffusionswege des Wasserstoffs nicht zu groß werden.
Im Temperaturbereich von 900 bis 1600 °C findet zusätzlich eine „direkte Reduktion“ mit Kohlenstoff statt:[69]
Auch die Eisenbegleiter Mangan, Silicium und Phosphor werden in den Prozess mit einbezogen und reduziert, wobei Wärme verbraucht wird:
Gleichzeitig nimmt das bereits reduzierte Eisen in der Kohlungszone bei etwa 1100 bis 1200 °C Kohlenstoff entweder direkt aus dem glühenden Koks oder aus dem Kohlenmonoxidgas auf.
Die Aufnahme von Kohlenstoff senkt den Schmelzpunkt von 1538 °C (reines Eisen) auf etwa 1300 bis 1400 °C[69] (Schmelzpunkt der eutektischen Mischung, dem Ledeburit, mit 4,3 Gew.-% C: 1147 °C).
Überwachung und Regelung des Hochofenprozesses
Im Zuge von Automatisierung und Qualitätssicherung zum Erhalt der Konkurrenzfähigkeit einerseits, sowie den gestiegenen Sicherheitsanforderungen zum Schutz von Mensch und Maschine andererseits, sind verschiedene Mess- und Regeleinrichtungen unumgänglich. Der Verhüttungsprozess unterliegt naturgemäß mehr oder weniger großen Schwankungen, da auch die Zusammensetzung von Möller, Koks und Heißwind samt den mit eingeblasenen Zusatzstoffen innerhalb der Toleranzgrenzen variieren. Entsprechend schwanken auch Reaktionsverlauf und -geschwindigkeit, was ohne Überwachung und geeignete Maßnahmen zur Gegenregulierung zu schweren Störungen führen würde.
Wichtige Messgrößen sind vor allem:
in Höhe der Gicht |
|
vom Schacht bis zum Kohlensack |
|
in Höhe der Heißwindzuführung |
|
am Gestellboden |
|
Daneben werden unter anderem noch Horizontalsonden zur Messung der Dicke der Möllerschichten sowie von Druck und Geschwindigkeit des durchgehenden Gases in der Möllersäule eingesetzt. Zur Sicherheit gegen Ausfälle sind einige Messeinrichtungen wie beispielsweise zur Teufenmessung der Beschickungsoberfläche redundant ausgeführt.[70][71]
Hängende Beschickung
Aufgrund des Zerfalls von Möller und Koks während der Reduktion kann es zu einer Verdichtung und schließlich zum Aufstauen der Möllersäule im Schacht kommen. Eine in dieser Weise „hängende“ Möllersäule macht sich zunächst dadurch bemerkbar, dass die Teufenmessung keine Sinkbewegung mehr an der Beschickungsoberfläche registriert, aber auch Druck und Temperatur des Gichtgases sinken, weil es nur noch schwer durch die geringer werdenden Lücken in der verdichteten Möllersäule gelangt. Der Winddruck dagegen steigt, da er auf größeren Widerstand trifft.
Unterhalb der Hängezone läuft der Reduktions- und Schmelzprozess jedoch unvermindert weiter, bis sich schließlich ein Hohlraum zwischen hängendem und sinkendem Möller bildet. Da einerseits die Gefahr besteht, dass eine plötzlich in den Hohlraum einbrechende Möllersäule zu schweren Prozessstörungen und Schäden am Hochofen führt und andererseits Roheisen und Schlacke drohen, bis zu den Blasformen aufzusteigen, muss eine Reaktion auf die bereits genannten, charakteristischen Änderungen der Messergebnisse möglichst frühzeitig erfolgen. Dazu zählt zum Beispiel das so genannte „Stauchen“, eine einmalige oder gegebenenfalls mehrmalige starke Drosselung der Windmenge und damit des Gegendrucks auf die Möllersäule, was diese aufgrund ihres Eigengewichtes dazu zwingt nachzurutschen.[72][73]
Ansatzbildung
Das Anbacken von Möller und Koks an die Innenwände des Hochofens kann verschiedene Ursachen haben. Im Laufe der Zeit verändert sich das Profil der Panzerung durch physische und chemische Abrasion, wodurch stellenweise leichtere Ansatzbedingungen entstehen können. Ebenso erleichtern in der Folge auch hervorstehende Kühlelemente die Ansatzbildung. Auch die Möllerzusammensetzung selbst hat Einfluss auf den Anbackvorgang, da unter anderem eine basisch zusammengesetzte Schlacke zur besseren Schwefelbindung einen entsprechend höheren Anteil an verschiedenen Alkalien hat, die als Anbackhilfe wirken. Kleinere Ansätze machen sich zunächst kaum bemerkbar, können jedoch sehr schnell anwachsen und zu Störungen im Hochofenprozess führen; vor allem, wenn diese plötzlich abbrechen und dann für Unregelmäßigkeiten in der Zusammensetzung in der Möllersäule sorgen.
Messbar werden größere Ansätze dadurch, dass sie den Ofenquerschnitt verengen und damit die Strömungsgeschwindigkeit des Windes erhöhen, wodurch mehr Staubteilchen mitgerissen werden. Neben dem erhöhten Staubauswurf kann die Bildung von Ansätzen auch die zuvor genannten Hängeerscheinungen begünstigen. Des Weiteren sind Schwankungen im Ofengang und in der Roheisenqualität durch abbröckelnde Ansätze die Folge. Schließlich kann eine Ansatzbildung auf hereinragenden Kühlelementen auch deren Beschädigung verursachen.
Durch Druck- und Temperaturmessfühler in den Ofenwänden sowie Messsonden, die horizontal in die Möllersäule geschoben werden können, lassen sich Querschnittsänderungen und damit Ansätze inzwischen schneller und genauer lokalisieren. Geeignete Schüttungsänderungen können diese dann meist schon beseitigen. Früher mussten vor allem größere Hochöfen zunächst niedergeblasen und dann die Ansätze entweder angebohrt oder abgesprengt werden.[74][75]
Wassereinbruch
Wassereinbrüche durch beschädigte Kühlelemente können zu erheblichen Störungen im Hochofenprozess führen, da bei größeren Mengen das verdampfende Wasser einen hohen Verlust an Wärmeenergie nach sich zieht und die verschiedenen Reduktionsvorgänge ins Stocken geraten. Messbar ist ein Wassereinbruch einerseits durch einen erhöhten Wasserstoffgehalt im Gichtgas und andererseits durch den erhöhten Verbrauch an Speisewasser, das den Wasserverlust in geschlossenen Kühlkreisläufen ausgleichen soll.
Durch sinnvolle Unterteilung und Verbindung der Kühlelemente und -leitungen untereinander in horizontale Zonen bzw. „Kühlscheiben“ können beschädigte Elemente schneller entdeckt und ersetzt sowie die Wasserverluste gering gehalten werden. In offenen Kühlsystemen ist dagegen eine Druckprüfung an jedem Kühlelement notwendig.[76][77]
Stillsetzung
Je nachdem, ob das Hüttenwerk den Hochofen nur kurzfristig stillsetzen (Dämpfen) oder komplett herunterfahren und stilllegen (Ausblasen) will, sind verschiedene Verfahrensweisen notwendig.
Dämpfen
Soll ein Hochofen nur vorübergehend stillgesetzt werden, beispielsweise bei Versorgungsengpässen oder kleineren Reparaturen, wird er gedämpft. Dabei wird zunächst die Beschickung je nach geplanter Dauer der Betriebspause umgestellt. Sie besteht nun einerseits aus einem „leichten“, das heißt eisenärmeren Dämpfmöller und andererseits aus einer höheren Anzahl Koksschichten. Beim letzten Abstich vor dem Stillsetzen wird darauf geachtet, dass Roheisen und Schlacke möglichst vollständig ablaufen. Soll die Dämpfungsphase länger dauern, kommt zusätzlich die Ofensau zum Einsatz. Steht der Ofen still, werden alle Zu- und Abführleitungen geschlossen, die Heißwinddüsen zugemauert und die Beschickungsoberfläche mit Feinerz oder Schlackensand abgedeckt, damit der Hochofen seine Wärme möglichst lange halten kann und der natürliche Windzug nicht zu unnötigen Koksverbrennungen führt. Um Wassereinbrüche, die zu schweren Störungen des Hochofenprozesses führen würden, zu verhindern, wird das Kühlsystem erst nach einer sorgfältigen Dichtigkeitsprüfung abgestellt.
Das Wiederanblasen nach längeren Dämpfungsphasen erfolgt in umgekehrter Reihenfolge der einzelnen Arbeitsschritte beim Dämpfen, wobei allerdings zunächst nur wenige Winddüsen der Heißwindanlage im Stichlochbereich, dann schrittweise weitere Düsen in Betrieb genommen werden. Falls nötig, wird auch das Stichloch für einige Zeit höher gesetzt.[60]
Ausblasen
Ist ein regelmäßiger Betrieb nicht mehr möglich, unter anderem weil die Ausmauerung soweit abgenutzt ist, dass sie ersetzt werden muss, wird der Hochofen „ausgeblasen“.
Der Hochofenprozess läuft dabei im unteren Bereich zunächst weiter, allerdings wird die Zufuhr der Beschickung abgestellt und die Windzufuhr in der Anfangsphase stark verringert und schließlich ebenfalls abgestellt. In der Tiefblasphase (Absenken der Koks-Möller-Säule) wird an allen Stellen, wo sich „tote“, das heißt leere Räume bilden, durch spezielle Düsen Wasserdampf eingespritzt. Teilweise wird auch Wasser von oben zugegeben. Dies verhindert die Entstehung explosionsgefährlicher Gas-Luft-Gemische. Tote Räume entstehen vor allem über der Beschickungsoberfläche bis zum Gichtabzug, aber auch in den Zwischenräumen der Gichtgasschleuse, je nach Lage der Absperrventile an den Gasabzügen zwischen Ofen und Staubsack oder im Staubsack selbst sowie in den Wirblern und im Ofenventil. Eine andere Methode zur Vermeidung von Gasexplosionen ist der Abbrand der an der Beschickungsoberfläche austretenden Gichtgase mithilfe einer ständig brennenden Koksgas-Zündlanze. Den Abschluss des Ausblasens bildet der Abstich der Ofensau, wobei neben Schlacke je nach Dauer der Hochofenreise und den Kühlbedingungen im Gestell mehrere Tonnen Roheisen anfallen können.[60]
Nach Beendigung der Ofenreise wird zumeist die komplette Auskleidung aus feuerfesten Steinen erneuert und beschädigte Stahlbauteile ersetzt. Oft wird ein solcher Ofenstillstand auch dazu genutzt, um technisch veraltete Einrichtungen wie beispielsweise Mess- und Analysegeräte durch neue zu ersetzen. Neben der Qualitätsverbesserung der Hochofenprodukte trägt dies auch zur Verringerung des Energieverbrauchs und der Umweltbelastungen bei.
Bis alle beschädigten bzw. veralteten Bauteile ersetzt sind, vergehen meist mehrere Monate. Allerdings kann ein Hochofen bei guter Qualität der restlichen Bauteile mehrere Ofenreisen bis zur endgültigen Stillsetzung überstehen. So trat beispielsweise der „Großhochofen 1“ in Duisburg-Schwelgern im März 2008 seine fünfte Ofenreise an.[78]
Hochofenerzeugnisse
Roheisen
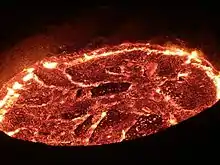
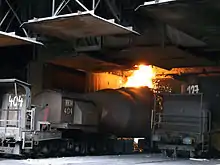
Ziel eines optimal eingestellten Hochofenprozesses ist die Erzeugung von möglichst hochwertigem Roheisen, das möglichst wenig Fremdbeimengungen besitzt und nicht zu viel Kohlenstoff aufgenommen hat.
Nach DIN EN 10001 ist Roheisen definiert als Legierung aus Eisen mit mehr als 2 % Kohlenstoff sowie einigen weiteren Elementen mit folgenden maximalen Anteilen: Mangan ≤ 30 %, Silicium ≤ 8 %, Phosphor ≤ 3 % und Chrom ≤ 10 %. Der Anteil anderer Beimengungen soll höchstens 10 % betragen.[58] Zur Qualitätssicherung wird bei jedem Abstich eine Probe für eine chemische Analyse entnommen.
In 9 von 10[79] Hochofenwerken wird sogenanntes „Weißes Roheisen“ (auch Stahlroheisen) erzeugt, bei dem der enthaltene Kohlenstoff gebunden in Form von Eisencarbid oder Mangancarbid vorliegt und dessen Bruchfläche einen hellen, silberweißen Glanz zeigt. Weißes Roheisen wird meist direkt in flüssiger Form mithilfe geschlossener Torpedowaggons ins nahegelegene Stahlwerk transportiert, kann aber auch zur Vorratshaltung entweder zu handlichen Masseln oder zu Eisengranulat (Korngröße ≈ 2–16 mm[79]) vergossen werden. Weißes Roheisen dient als Ausgangsstoff zur Stahlerzeugung und wird in einem Blasstahlwerk („Stahlkocherei“) durch Einblasen von Sauerstoff von seinen unerwünschten Begleitstoffen und einem Großteil des Kohlenstoffs befreit. Diese verlassen den glutflüssigen, fertigen Stahl entweder als Gase (Schwefeldioxid, Kohlendioxid) oder mit den Zuschlägen als Schlacke (Calcium- und Mangansilicate oder -phosphate).
Der geringe Rest der Eisenhüttenwerke produziert meist „Graues Roheisen“ (auch Gießereieisen), bei dem der Kohlenstoff ungebunden als Graphit auskristallisiert und dessen Bruchfläche entsprechend ein dunkleres Mattgrau zeigt. Graues Roheisen dient als Ausgangsstoff zur Herstellung verschiedener Gusseisensorten wie beispielsweise Grauguss mit Lamellengraphit oder Kugelgraphit, Temperguss und Stahlguss. Einige wenige Betriebe haben sich zudem auf Sonderroheisensorten wie Ferromangan (Spiegeleisen) oder Ferrosilicium spezialisiert.
Schlacke
Die beim Hochofenprozess anfallende Schlacke besteht aus etwa 38–41 % Calciumoxid (CaO), 7–10 % Magnesiumoxid (MgO), 34–36 % Siliciumdioxid (SiO2), 10–12 % Aluminiumoxid (Al2O3), 1,0–1,5 % Schwefel (S), 1,0 % Titandioxid (TiO2), 0,16–0,2 % Eisenoxid (FeO) sowie verschiedenen weiteren Oxiden und Sulfiden.[80]
Erfahrene Hüttenleute sehen oft schon der noch flüssigen Schlacke an, welche ungefähre Zusammensetzung und Eigenschaften sie birgt. Zur Prüfung derselben genügt meist die einfache „Hakenprobe“, bei der ein Eisenhaken in die Schlacke getaucht wird. Bleibt die Schlacke beim Anheben in kurzen, zähen Tropfen am Haken hängen (kurze Schlacke), ist sie „basisch“ mit einem Gewichtsverhältnis von CaO : SiO2 > 1,0. Läuft die Schlacke dagegen in langen Fäden (lange Schlacke) vom Haken, ist sie „sauer“ mit einem Verhältnis von CaO : SiO2 < 1,0.[81]
Hatte die Schlacke im Hochofen noch die Aufgabe, die Gangart der Erze sowie die Asche des Kokses aufzunehmen,[82] das Roheisen zu entschwefeln und als Schutzwall im Gestell gegen die Wärmestrahlung zu dienen, so wird sie nach dem Abstich je nach Zusammensetzung und Eigenschaft als wertvoller Rohstoff für verschiedenste Zwecke weitergenutzt. Neben der Erzeugung von Hüttensand, Hüttensteinen bzw. -bims und Schlackenwolle wird sie auch zu Straßen- und Gleisschotter, Schlackensteinen, Portlandzement und Hochofenzement verarbeitet.
Gichtgas
_-_several_constructions.png.webp)
Das am Hochofenkopf mit einer Temperatur von 150 bis 200 °C austretende Gichtgas besteht aus 22–24 % Kohlenstoffdioxid (CO2), 18–21 % Kohlenstoffmonoxid (CO), 52–59 % Stickstoff (N2), 1–3 % Wasserstoff (H2) sowie aus Wasserdampf und Spuren von Methan.[83] Neben seiner Hauptverwendung als Brennstofflieferant zur Befeuerung der Winderhitzer dient es unter anderem noch als Heizgas in Walzwerken, Dampfkesseln, Kokskammern und bei Fernwärme-Heizungen sowie als Treibstoff für Gasmotoren.
Aufgrund vieler Maßnahmen zur besseren Erz- und Gasausnutzung bei gleichzeitiger Verringerung des Koksverbrauches sank allerdings im Lauf der Zeit die Gesamtmenge des produzierten Gichtgases wie auch dessen Heizwert. Seit den 1990er Jahren fallen pro Tonne Roheisen etwa 1500 bis 2000 m³ i.N. Gichtgas mit einem Heizwert zwischen 3150 und 3570 kJ/m³ an.[80] Durch Zusatz von Koks- oder Erdgas wird dieser Wert auf etwa 4500 kJ/m³ erhöht.[84] Zusätzlich entfallen auf eine Tonne Roheisen etwa 25 kg Gichtstaub an, was einem Staubanteil im Gichtgas von etwa 20–30 g/m³ entspricht.
Um die vom Gichtgas betriebenen Brenner, Gasmotoren und Turbinen vor Schäden durch Abrasion zu bewahren, aber auch aus Gründen des Umweltschutzes, wird das Gichtgas seit Anfang des 20. Jahrhunderts entstaubt und gereinigt. Gichtgas-Turbinen seit den 1970er-Jahren benötigen z. B. hochreines Gas mit einem Staubanteil von höchstens 0,5–1 mg/m³.[85]
Die Reinigung erfolgt über mehrere Stufen von der trockenen Grobreinigung mithilfe von Staubsack und Wirbler über die Nassreinigung in Gaswäschern und Desintegratoren bis zur Feinreinigung mithilfe von Sack- bzw. Schlauchfilteranlagen und Elektrofiltern. Das anschließend nutzbare Reingas enthält dann noch einen Staubanteil von 0,006 bis 0,03 g/m³.[86]
Leistung und Verbrauch
Bis 1914 lieferte ein Hochofen etwa 300 bis 400 Tonnen Roheisen täglich und zwischen 1950 und 1960 konnten bereits 2.500 Tonnen pro Tag erzeugt werden.
In den 1970er-Jahren lieferten die besten Öfen der Welt am Tag 60 Tonnen pro Quadratmeter Gestellfläche und mehr, bei einem durchschnittlichen Verbrauch an Koks sowie Öl von etwa 503 Kilogramm pro Tonne Roheisen.[53] Das entspricht bei mittleren Hochöfen mit einem Gestelldurchmesser von 10 bis 11 Metern einer Tagesleistung von 5000 bis 6000 Tonnen.
In der Bundesrepublik Deutschland lag der spezifische Koksverbrauch eines Hochofens 1980 bei etwa 515 Kilogramm pro Tonne Roheisen. Der spezifische Verbrauch von Heizöl betrug 23 Kilogramm pro Tonne Roheisen. Bis 1994 sank der Koksverbrauch auf etwa 379 Kilogramm, während der Heizölverbrauch auf etwa 45 Kilogramm pro Tonne stieg.[87] Seit 1985 wird zunehmend Kohle statt aufbereitetem Koks als Reduktionsmittel verwendet.[88]
Große Hochöfen wie der „Hochofen 5“ des Hochofenbetriebes Rogesa auf dem Werksgelände der Dillinger Hütte mit einem Gestelldurchmesser von 12 Metern bringen es auf etwa 7000 Tonnen pro Tag. Größere Hochöfen können bis zu 12.000 Tonnen Roheisen täglich produzieren.
1950 lag die Weltjahresproduktion noch bei etwa 189 Millionen Tonnen Roheisen, steigerte sich jedoch bis Ende 2018 auf rund 1808 Millionen Tonnen.[89] Der Ende 1993 angefahrene „Hochofen 2“ der ThyssenKrupp Steel in Schwelgern brachte es bei einem Gestelldurchmesser von 14,9 Metern auf eine Tagesleistung von mehr als 10.000 Tonnen Roheisen.[31]
2007 produzierten große Hochöfen mit einem Gestelldurchmesser von etwa 15 Meter durchschnittlich rund 12.000 Tonnen Roheisen pro Tag, was einer Jahresproduktion von rund 4 Millionen Tonnen entspricht. Um diese Leistung zu vollbringen, braucht es täglich etwa 19.200 Tonnen Eisenerze, 4000 Tonnen Koks, 1750 Tonnen Einblaskohle (Kohlenstaub zum Einblasen über die Heißwinddüsen) sowie 11 Millionen Kubikmeter Luft. Dies entspricht pro Tonne Roheisen einem Verbrauch von etwa 1600 Kilogramm Erz, 330 Kilogramm Koks, 146 Kilogramm Einblaskohle und 917 Kubikmeter Luft. Als Nebenprodukte fielen 3300 Tonnen Schlacke und 17 Millionen Kubikmeter Gichtgas pro Tag an.[37] Zum Schmelzen der Schlacke werden pro 3,2 Tonnen Schlacke etwa eine Tonne Koks verbraucht.[82]
Quellen und Verweise
Literatur
Direkter Hochofenbezug
- Manfred Rasch (Hrsg.): Der Kokshochofen von 1709 bis in die Gegenwart. 2. Auflage. Klartext Verlag, Essen 2015.
- Hans Schoppa: Was der Hochöfner von seiner Arbeit wissen muss. 4. Auflage. Verlag Stahleisen, Düsseldorf 1992, ISBN 3-514-00443-9.
- Gerhard Winzer, Eberhard Reichenstein: Entwicklung der Hochofentechnik. Berichte, gehalten im Kontaktstudium „Metallurgie des Eisens; Teil I: Eisenerzeugung“. In: F. Oeters, R. Steffen (Hrsg.): Metallurgie. Band 2. Verlag Stahleisen, Düsseldorf 1982, ISBN 3-514-00260-6, S. 79–84.
- H. Dickmann: Entwicklung der Hochofen-Winderhitzung bis zur Erfindung E. A. Cowpers. In: Brohltal AG für Stein- und Tonindustrie (Hrsg.): Hundert Jahre Cowper-Winderhitzung. Burgbrohl (Bez. Koblenz) 1958.
- M. A. Pawlow (М. А. Павлов): Konstruktion und Berechnung von Hochöfen. In: Metallurgie des Roheisens. 2. Auflage. Band 3. VEB Verlag Technik, Berlin 1953, DNB 453723004, Lizenznummer Dg.-Nr. 370/39/53 (DDR) – (russisch: Металлургия Чугуна, Часть третья: Доменная печь. Übersetzt von Erich Marquardt).
Hochofenprozess
- K. Grebe: Das Hochofenverhalten von Möller und Koks. Berichte, gehalten im Kontaktstudium „Metallurgie des Eisens; Teil I: Eisenerzeugung“. In: F. Oeters, R. Steffen (Hrsg.): Metallurgie. Band 2. Verlag Stahleisen, Düsseldorf 1982, ISBN 3-514-00260-6, S. 85–145.
- M. A. Pawlow (М. А. Павлов): Der Hochofenprozess. In: Metallurgie des Roheisens. 2. Auflage. Band 2. VEB Verlag Technik, Berlin 1953, DNB 367559374, Lizenznummer Dg.-Nr. 370/40/53 (DDR) – (russisch: Металлургия Чугуна, Часть вторая: Доменный Процесс. Übersetzt von Rudolf Rickert, Walter Philipp, Alexander Junge, Heinz Frahn).
- Verein Deutscher Eisenhüttenleute (Hrsg.): Der Hochofenprozess – Das kinetisch-dynamische Simulationsmodell. Bericht über eine Gemeinschaftsarbeit mit Beiträgen der Vortragstagung „Mathematische Modelle des Hochofenprozesses“ am 2. und 3. Dezember 1971 in Düsseldorf. Verlag Stahleisen, Düsseldorf 1973, ISBN 3-514-00124-3.
- Richard Troska: Die Hochofen-Dimensionen auf Grundlage des Hochofen-Prozesses. Weimar 1867 (online verfügbar in der Google-Buchsuche; zuletzt abgerufen am 27. Mai 2012)
Allgemeines
- Jürgen Ruge, Helmut Wohlfahrt: Technologie der Werkstoffe. 8. Auflage. Springer Verlag, 2007, ISBN 3-8348-0286-7.
- Karl Taube: Stahlerzeugung kompakt: Grundlagen der Eisen- und Stahlmetallurgie. Vieweg Technik, Braunschweig/ Wiesbaden 1998, ISBN 3-528-03863-2, S. 60–159: Hochofen.
- Teil I: Eisenerzeugung. Berichte, gehalten im Kontaktstudium „Metallurgie des Eisens“. In: F. Oeters, R. Steffen (Hrsg.): Metallurgie. Band 2. Verlag Stahleisen, Düsseldorf 1982, ISBN 3-514-00260-6.
- Verein Deutscher Eisenhüttenleute (Hrsg.): Gemeinfassliche Darstellung des Eisenhüttenwesens. 17. Auflage. Verlag Stahleisen, Düsseldorf 1970.
- Fritz Toussaint: Der Weg des Eisens. 6. Auflage. Verlag Stahleisen, Düsseldorf 1969.
- Otto Johannsen (im Auftrag des Vereins Deutscher Eisenhüttenleute): Geschichte des Eisens. 3. Auflage. Verlag Stahleisen, Düsseldorf 1953.
- Robert Durrer: Grundlagen der Eisengewinnung. Verlag Francke, Bern 1947, S. 56–58.
- Johann Christian zu Solms-Baruth, Johann Heinrich Gottlob von Justi: Abhandlung von den Eisenhammern und hohen Oefen in Teutschland. Rüdiger, Berlin/ Stettin/ Leipzig 1764. (E-Book: Becker, Potsdam 2010, ISBN 978-3-941919-73-0)
- A. F. Holleman, E. Wiberg, N. Wiberg: Lehrbuch der Anorganischen Chemie. 102. Auflage. Walter de Gruyter, Berlin 2007, ISBN 978-3-11-017770-1.
- Peter Atkins: Physikalische Chemie. 2. Auflage. Wiley-VCH, Weinheim 1996, ISBN 3-527-31546-2.
Weblinks
Einzelnachweise
- Hohofen. In: Heinrich August Pierer, Julius Löbe (Hrsg.): Universal-Lexikon der Gegenwart und Vergangenheit. 4. Auflage. Band 8. Altenburg 1859, S. 472 (zeno.org).
- Wirtschaftsvereinigung Stahl (Hrsg.): Fakten zur Stahlindustrie in Deutschland 2020. (stahl-online.de [PDF; 3,4 MB; abgerufen am 15. März 2021]).
- Johannsen: Geschichte des Eisens, S. 9–11.
- Matthias Zwissler, Roman Landes: Untersuchungen zu Rennfeuererzeugnissen, Rennfeuersymposium der IGDF Internationale Gesellschaft für Damaszenerstahlforschung e.V. in Polle, 20. August 2005 (Untersuchungen zu Rennfeuererzeugnissen PDF; 3,54 MB).
- Johannsen: Geschichte des Eisens, S. 11, 121.
- Johannsen: Geschichte des Eisens, S. 121–122.
- Albrecht Jockenhövel: Der Weg zum Hochofen – Die Zeit der mittelalterlichen und frühneuzeitlichen Massenhütten. In: Eisenland, zu den Wurzeln der nassauischen Eisenindustrie. Hrsg. Verein für Nassauische Altertumskunde und Geschichtsforschung e. V., Taunusstein 1995, ISBN 3-922027-88-1, S. 83–98.
- Durrer: Grundlagen der Eisengewinnung, S. 56–58.
- Johannsen: Geschichte des Eisens, S. 133.
- Meyers Konversationslexikon – Blauofen
- Gemeinfassliche Darstellung des Eisenhüttenwesens, S. 7.
- Ludwig Beck: Beiträge zur Geschichte der Eisenindustrie in Nassau. In: Nassauische Annalen. Band 33 (1902/03), S. 212.
- Michael Gechter: Montanarchäologie im Bergischen Land. In: gv-roesrath.de. Geschichtsverein Rösrath e.V., abgerufen am 18. April 2019.
- aufbruch ins revier, Hoesch 1871–1961, Seite 34
- aufbruch ins revier, Hoesch 1871–1961, Seite 43
- Johannsen: Geschichte des Eisens, S. 296.
- Gemeinfassliche Darstellung des Eisenhüttenwesens, S. 8–9.
- Harald Pöcher: Kriege und Schlachten in Japan, die Geschichte schrieben: von den Anfängen bis 1853. LIT Verlag, Münster 2009, S. 34 eingeschränkte Vorschau in der Google-Buchsuche
- Johannsen: Geschichte des Eisens, S. 22–23.
- Johannsen: Geschichte des Eisens, S. 35.
- Peter Dahlmann, Gerhard Endemann, Hans Jürgen Kerkhoff, Hans Bodo Lüngen: Wege zur Effizienzsteigerung in der Stahlindustrie, Stahlinstitut VDEh. Wirtschaftsvereinigung Stahl, September 2010 (Wege zur Effizienzsteigerung in der Stahlindustrie PDF 1,7 MB, S. 6 (Memento vom 17. Dezember 2015 im Internet Archive))
- Bau des Hochofens 8 in Duisburg-Hamborn der ThyssenKrupp Steel AG
- Schoppa: Was der Hochöfner …, S. 52–53.
- Taube: Stahlerzeugung kompakt, S. 92.
- Johannsen: Geschichte des Eisens, S. 371–372.
- Roger Kneip: AUS DER GESCHICHTE DER STAHLINDUSTRIE – Über 25 Jahre glockenloser Gichtverschluss
- Schoppa: Was der Hochöfner …, S. 55–56.
- Gemeinfassliche Darstellung des Eisenhüttenwesens, S. 59.
- Schoppa: Was der Hochöfner …, S. 38–39.
- Taube: Stahlerzeugung kompakt, S. 62–63.
- Zehn Jahre Hochofen Schwelgern 2 und 38 Mio. Tonnen Roheisen (Memento vom 29. November 2011 im Internet Archive)
- ThyssenKrupp: Erste Ofenreise nach 21 Jahren beendet: Größter Hochofen Europas wird modernisiert Presse-Mitteilung vom 16. Mai 2014.
- Vaclav Smil: Still the Iron Age. Iron and Steel in the Modern World., Butterworth-Heinemann (Elsevier), Oxford Cambridge 2016, Seite 90. ISBN 978-0-12-804233-5. Leseprobe, abgerufen am 29. September 2016.
- Three of top 10 world melting pots owned by Korea’s POSCO. In: Arirang News. 24. August 2013, mit Video (0:37 Min.)
- Flachstahl – Gestellzustellung in Hochofen B unfallfrei abgeschlossen (Memento vom 19. September 2015 im Internet Archive)
- Gemeinfassliche Darstellung des Eisenhüttenwesens, S. 101.
- stahl-online.de – Roheisen- und Stahlerzeugung (Memento vom 15. Januar 2012 im Internet Archive) (Werte stehen laut Roheisen- und Stahlerzeugung (Memento vom 10. Februar 2011 im Internet Archive) bereits seit Oktober 2007 unverändert auf der Webseite)
- Gemeinfassliche Darstellung des Eisenhüttenwesens, S. 61.
- H. W. Gudenau, H. Kainer, G. Pitzko, M. Scheiwe: Thermisch-mechanisches Verhalten von Hochofen-Gestellzustellungen. In: Stahl und Eisen. 111 (1991)9, S. 71–81, 188.
- Schoppa: Was der Hochöfner …, S. 43–44.
- Taube: Stahlerzeugung kompakt, S. 71–73.
- Taube: Stahlerzeugung kompakt, S. 84–85.
- Dickmann: Entwicklung der Hochofen-Winderhitzung …, S. 1.
- Johannsen: Geschichte des Eisens, S. 325.
- Johannsen: Geschichte des Eisens, S. 327.
- Dickmann: Entwicklung der Hochofen-Winderhitzung …, S. 4.
- Dickmann: Entwicklung der Hochofen-Winderhitzung …, S. 6.
- Dickmann: Entwicklung der Hochofen-Winderhitzung …, S. 9.
- Schoppa: Was der Hochöfner …, S. 58.
- Taube: Stahlerzeugung kompakt, S. 47.
- Taube: Stahlerzeugung kompakt, S. 46.
- Taube: Stahlerzeugung kompakt, S. 59.
- Winzer, Reichenstein: Entwicklung der Hochofentechnik, S. 80–81.
- Innovations-Report: Hochofen: Kunststoff-Pellets statt Koks und Schweröl
- Durch Einsatz von Altkunststoffen reduziert die voestalpine CO2-Emissionen in Linz um mehr als 400.000 Tonnen pro Jahr. (PDF 32 kB) In: voestalpine.com. voestalpine AG, 16. Juni 2007, abgerufen am 17. Juli 2019.
- Ruge, Wohlfahrt: Technologie der Werkstoffe, S. 195.
- Schoppa: Was der Hochöfner …, S. 49.
- Taube: Stahlerzeugung kompakt, S. 152–154.
- Schoppa: Was der Hochöfner …, S. 51.
- Schoppa: Was der Hochöfner …, S. 85–88.
- Toussaint: Der Weg des Eisens, S. 65.
- Grebe: Das Hochofenverhalten von Möller und Koks, S. 95–101.
- Grebe: Das Hochofenverhalten von Möller und Koks, S. 101–109.
- Winzer, Reichenstein: Entwicklung der Hochofentechnik, S. 79.
- Grebe: Das Hochofenverhalten von Möller und Koks, S. 91–92.
- Grebe: Das Hochofenverhalten von Möller und Koks, S. 104–107.
- Atkins: Physikalische Chemie, S. 1108.
- A. F. Holleman, E. Wiberg, N. Wiberg: Lehrbuch der Anorganischen Chemie. 102. Auflage. Walter de Gruyter, Berlin 2007, ISBN 978-3-11-017770-1, S. 897.
- Taube: Stahlerzeugung kompakt, S. 131.
- Schoppa: Was der Hochöfner …, S. 64–66.
- Taube: Stahlerzeugung kompakt, S. 118–124.
- Schoppa: Was der Hochöfner …, S. 88.
- Taube: Stahlerzeugung kompakt, S. 147.
- Schoppa: Was der Hochöfner …, S. 89–90.
- Taube: Stahlerzeugung kompakt, S. 146–147.
- Schoppa: Was der Hochöfner …, S. 90.
- Taube: Stahlerzeugung kompakt, S. 148.
- ThyssenKrupp: Die fünfte Ofenreise kann beginnen: Großhochofen 1 in Duisburg-Schwelgen wird Anfang April nach Modernisierung wieder angeblasen; Presse-Mitteilung vom 19. März 2008, 11:00 Uhr.
- Gemeinfassliche Darstellung des Eisenhüttenwesens, S. 78–79.
- Taube: Stahlerzeugung kompakt, S. 158–159.
- Gemeinfassliche Darstellung des Eisenhüttenwesens, S. 83–84.
- Karl-Heinz Schmidt, Ingo Romey, Fritz Mensch: Kohle, Erdöl, Erdgas: Chemie und Technik. Vogel Verlag, Würzburg 1981, ISBN 3-8023-0684-8.
- Taube: Stahlerzeugung kompakt, S. 159.
- Schoppa: Was der Hochöfner …, S. 102.
- Gemeinfassliche Darstellung des Eisenhüttenwesens, S. 96.
- Schoppa: Was der Hochöfner …, S. 63.
- Bergbau-Lexikon der steinkohle-portal.de – Hochofen (Memento vom 30. März 2012 im Internet Archive)
- Zum Thema Klimaschutz bei stahl-online.de: Stahl ist für eine emissionsarme Welt unverzichtbar.
- World Steel Association: World Steel in Figures 2019. (PDF 1,9 MB) 6. Juni 2019, S. 6, abgerufen am 17. Juli 2019.