Drehrohrofen
Ein Drehrohrofen (DRO) ist ein zylindrischer Ofen für kontinuierliche Prozesse in der Verfahrenstechnik, der sich im Normalbetrieb kontinuierlich um die eigene Achse dreht. Verbunden mit einer leichten Neigung der Rotationsachse sorgt die Drehbewegung für den Produkt- oder Brennstofftransport.
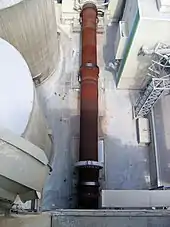
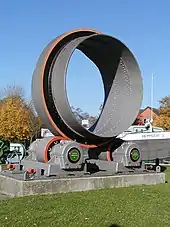
Bauarten
Drehrohröfen können sowohl direkt als auch indirekt beheizt werden. Bei der direkten Beheizung erfolgt die Wärmezufuhr von innerhalb des Ofens, beispielsweise durch einen Brenner. Etwaiges im Drehrohr befindliches Produkt befindet sich dabei im direkten Kontakt mit dem entstehenden Rauchgas. Bei der indirekten Beheizung wird die Wärme von außerhalb in den Reaktionsraum übertragen. Dies kann beispielsweise auch über das Abgas aus dem Prozess erfolgen.[1]
Aufbau direkt beheizter Drehrohröfen
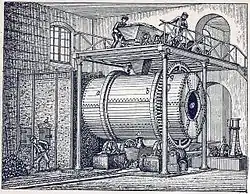
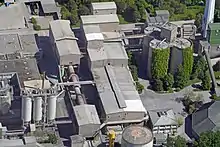
Ein direkt beheizter Drehrohrofen besteht in der Regel aus folgenden Bauteilen:
- ein Einlaufgehäuse zur Aufgabe bzw. zum Einfüllen der kontinuierlich zu behandelnden Materialien
- das Drehrohr
- ein Auslaufgehäuse oder Ofenkopf
- eine Brenner-Ausrüstung, welche am Ofenkopf sitzt.
- die Auskleidung aus feuerfesten Materialien
- die Lagerung auf zwei oder mehreren Stützen, Laufrollen und Achsen
- die Längs-Positionierungsregelung mit einer Axialrolle
- der Antrieb mittels Getriebe und Zahnkranz oder per Reibungsmitnahme auf angetriebenen Laufrollen
- die Dichtungen an Ofen-Einlauf und -Auslauf, um das rotierende Drehrohr gegen die feststehenden Ofenkopf-Teile abzudichten
Bei direkt beheizten Drehrohröfen wird zwischen Gleichstrom- und Gegenstromfeuerung unterschieden, in Abhängigkeit davon, ob sich Abgas und Brenngut in gleicher oder entgegengesetzter Richtung bewegen.
Aufbau indirekt beheizter Drehrohröfen
Ein indirekt beheizter Drehrohrofen besteht in der Regel aus folgenden Bauteilen:
- ein Einlaufgehäuse, meist auch nur eine Eintragschnecke mit Schild
- das Drehrohr
- das Austraggehäuse
- die Dichtungssysteme, die die Produktraumatmosphäre gegenüber der Luft abdichten, häufig mit Einsatz von Sperrgas
- die Lagerung, traditionell mit Laufring und Laufrollen, modern mit Großkugellagern oder Gleitlagerung
- der Antrieb mittels Kompaktgetriebe und Zahnkranz
- die nach außen isolierte Heizmuffel, die die benötigte Wärmemenge bereitstellt, üblicherweise durch Rauchgas oder Heizstäbe
Weiterhin können in Drehrohröfen Einbauten vorhanden sein, die hauptsächlich den Feststofftransport beeinflussen. Hubschaufeln beispielsweise sorgen für ein Abrieseln des Einsatzmaterials durch die heiße Gasatmosphäre und verbessern so den Wärmeübergang. Stauringe am Austrag erhöhen den Füllungsgrad im Ofen. Ketteneinbauten sind besonders bei nassem Einsatzmaterial geeignet, Anbackungen zu vermeiden oder zu beseitigen. Gezielt eingebrachte geometrische Körper, wie beispielsweise Stahlkugeln, verbessern die Durchmischung und erhöhen den Wärmeübergang.[3]
Verfahrenstechnische Besonderheiten
Der Transport des Produkts innerhalb des Drehrohrofens erfolgt durch die Drehbewegung und die Neigung der Ofenachse.[4]
Aufgrund von Länge und Innendurchmesser (jeweils mehrere Meter möglich) sind Drehrohröfen auch für die Behandlung von inhomogenen Materialien geeignet. Die Einsatzstoffe können sehr unterschiedliche Konsistenz und Stückigkeit besitzen. Beispielsweise können Feststoffe, Schlämme und Fässer eingebracht werden.
Ein Drehrohrofen ist ein hochwertiges Investitionsgut mit Kosten von meist mehreren Millionen Euro. In aller Regel werden Drehrohröfen kontinuierlich betrieben. Die zumeist 50-wöchige Betriebszeitspanne („Konti-Betrieb“) vom Anfeuern bis zum Abstellen des Ofens zu Wartungs- und Reparaturarbeiten wird Reisezeit bzw. Ofenreise genannt.
Wegen der zumeist schwierigen thermischen Verhältnisse und der gegenüber schnellen Temperaturschwankungen empfindlich reagierenden Ausmauerung darf der kontinuierliche Betrieb eines Drehrohrofens nicht plötzlich unterbrochen werden. Für den Fall eines Stromausfalles oder eines Schadens am Antrieb müssen Notfall-Einrichtungen bestehen (Hilfsantrieb oder Notlaufeinrichtung), die ein Weiterdrehen des Ofens bis zu seiner Entleerung oder der Absenkung der Temperatur in einen sicheren Bereich ermöglichen. Drehrohröfen, die in voller Beladung mit heißen Materialien plötzlich stehenbleiben, können sich durch die einseitige Hitze- und Gewichtseinwirkung des stehengebliebenen Gutes durchbiegen oder die Ausmauerung kann beschädigt werden, was bis zur Zerstörung des Ofens führen kann.
In der Zementindustrie wird in einigen Anlagen zur Flammenkühlung und damit zur Minderung der Stickoxid-Emissionen den Drehrohröfen Abwasser zugeführt.[5]
Anwendungsfälle von Drehrohröfen
Direkt beheizte DRO
- Zementherstellung[5][6]
- Kalkbrennen[7]
- Müllverbrennung (insbesondere Krankenhaus-[8] und Sonderabfälle[9])
- Schmelzen von keramischen Gläsern / Fritten[10]
- Trocknung von Mineralgestein in Asphaltmischanlagen oder in Betonmischanlagen
- Erschmelzung von Metallen (beispielsweise zur Reduktion von Nickelerz)
- Pigmentherstellung
- Reaktivierung von Aktivkohle zur Wiederherstellung der Adsorptionskapazität[11][12]
- Wälzverfahren zur Aufarbeitung von Stahlwerksflugstäuben und anderen Zinkträgern
- Eisenerzreduktion[13]
- Wärmebehandlung von Eisenwerkstoffen[14]
- Herstellung von Sintermagnesia
- Herstellung von Wasserglas[10]
Indirekt beheizte DRO
- Müllpyrolyse (MPA Burgau, Contherm Hamm-Uentrop)[1]
- thermische Bodenbehandlung (beispielsweise von ölverseuchten Böden, Dioxine, Furane)[15]
- Altreifenpyrolyse (CBp Zypern)
- Entsorgung von Problembiomassen
- Pigmentherstellung
- Flusssäureproduktion
- Tonerdekalzinierung
- Aktivkohleherstellung[16]
- Trocknen von Kupferspänen zur Entfernung des Kühlschmiermittels[17]
Literatur
- VDI 3460 Blatt 1:2014-02 Emissionsminderung; Thermische Abfallbehandlung; Grundlagen (Emission control; Thermal waste treatment; Fundamentals). Beuth Verlag, Berlin. S. 53–57.
Weblinks
Einzelnachweise
- VDI 3460 Blatt 1:2014-02 Emissionsminderung; Thermische Abfallbehandlung; Grundlagen (Emission control; Thermal waste treatment; Fundamentals). Beuth Verlag, Berlin. S. 63–64.
- H. Ost: Lehrbuch der Technischen Chemie, Verlag von Robert Oppenheim, Berlin, 1890, S. 78.
- Trennen, Verwerten und Beseitigen von Abfällen. In: Gefahrstoffe – Reinhalt. Luft. 62, Nr. 10, 2002, ISSN 0949-8036, S. 430–431.
- VDI 2094:2003-03 Emissionsminderung; Zementwerke (Emission control; Cement plants). Beuth Verlag, Berlin, S. 19.
- DIN EN 19694-3:2016-10 Emissionen aus stationären Quellen; Bestimmung von Treibhausgasen (THG) aus energieintensiven Industrien; Teil 3: Zementindustrie; Deutsche Fassung EN 19694-3:2016. Beuth Verlag, Berlin, S. 46.
- VDI 2094:2003-03 Emissionsminderung; Zementwerke (Emission control; Cement plants). Beuth Verlag, Berlin, S. 7.
- DIN EN 19694-5:2016-10 Emissionen aus stationären Quellen; Bestimmung von Treibhausgasen (THG) aus energieintensiven Industrien; Teil 5: Kalkindustrie; Deutsche Fassung EN 19694-5:2016. Beuth Verlag, Berlin, S. 7.
- VDI 2301:1993-01 Emissionsminderung; Verbrennen von Abfällen aus Krankenhäusern und sonstigen Einrichtungen des Gesundheitswesens (Emission control; incineration of solid wastes from hospitals and other public health facilities). Beuth Verlag, Berlin, S. 9.
- VDI 3460 Blatt 1:2014-02 Emissionsminderung; Thermische Abfallbehandlung; Grundlagen (Emission control; Thermal waste treatment; Fundamentals). Beuth Verlag, Berlin. S. 53–54.
- VDI 2578:2017-03 Emissionsminderung; Glashütten (Emission control; Glassworks). Beuth Verlag, Berlin, S. 3–4.
- DIN EN 12915-2 Produkte zur Aufbereitung von Wasser für den menschlichen Gebrauch; Granulierte Aktivkohle; Teil 2: Reaktivierte granulierte Aktivkohle; Deutsche Fassung EN 12915-2:2009. Beuth Verlag, Berlin, S. 10.
- VDI 3897:2007-12 Emissionsminderung; Anlagen zur Bodenluftabsaugung und zum Grundwasserstrippen (Emission control; Soil vapour extraction and groundwater stripping systems). Beuth Verlag, Berlin, S. 32.
- DIN EN 19694-2 Emissionen aus stationären Quellen; Bestimmung von Treibhausgasen (THG) aus energieintensiven Industrien; Teil 2: Stahl- und Eisenindustrie; Deutsche Fassung EN 19694-2:2016. Beuth Verlag, Berlin, S. 50.
- DIN 17022-3:1989-04 Wärmebehandlung von Eisenwerkstoffen; Verfahren der Wärmebehandlung; Einsatzhärten. Beuth Verlag, Berlin, S. 15.
- VDI 3898:2013-01 Emissionsminderung; Trockenmechanische, physikalisch-chemische, thermische und biologische Bodenbehandlungsanlagen (Emission control; Plants for dry mechanical, physio-chemical, thermal and biological soil treatment). Beuth Verlag, Berlin, S. 25.
- VDI 3674:2013-04 Abgasreinigung durch Adsorption; Prozessgas- und Abgasreinigung (Waste gas cleaning by adsorption; Process gas and waste gas cleaning). Beuth Verlag, Berlin, S. 21.
- VDI 2102 Blatt 2:2013-04 Emissionsminderung; Kupfer- und Kupferlegierungsschmelzanlagen (Emission control; Copper and copper alloy melting plants). Beuth Verlag, Berlin, S. 14.