Siemens-Martin-Verfahren
Das Siemens-Martin-Verfahren dient der Aufbereitung von Roheisen für die Gewinnung von Stahl und gehört zu den sogenannten Herdfrischverfahren. Benannt wurde das Verfahren nach den drei Brüdern des berühmten Werner von Siemens, Friedrich, Otto und Wilhelm sowie dem französischen Eisenhüttenmann Pierre Martin. Das Siemens-Martin-Verfahren war das bevorzugte Stahlherstellungsverfahren von seiner Erfindung im Jahr 1864 bis in die erste Hälfte des 20. Jahrhunderts.
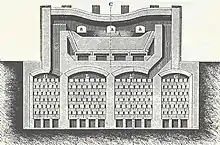
Siemens-Martin-Ofen
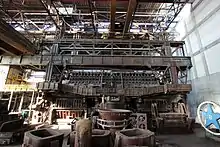
Vor dem Siemens-Martin-Verfahren wurde Stahl in Tiegelöfen erzeugt, es stellt eine Weiterentwicklung dieser Verfahren dar. Um höhere Temperaturen von 1800 Grad Celsius zu erreichen, wurden Generatorgase und Öle verwendet als Katalysatoren bzw. Brennstoffe. Das Verfahren beruhte auf einem speziellen Ofenaufbau, einem Oberofen, vom Gewölbe überspanntem Schmelzraum und dem Unterofen. Im Oberofen wird flüssiges Roheisen, Roheisenmasseln oder Schrott chargiert. Im Oberofen wird mit öl- oder gasbetriebenen Brennern der Schmelzraum beheizt. Im Unterofen sind die sogenannten Regenerativkammern zur Luft- und auch zur Gasvorwärmung untergebracht. Die Ausmauerung des Ofens besteht aus basischem Feuerfestmaterial (Magnesia, Sinterdolomit).[1]
Die zur Verbrennung notwendige Luftmenge wird in Regenerativkammern auf ca. 1200 °C erhitzt. Das Gas wird, getrennt davon in einer anderen Kammer, allerdings auf ein geringeres Temperaturniveau, ebenfalls erwärmt. Dies geschieht für beide Medien durch ein Gitterwerk aus aufgeheizten, feuerfesten Steinen in den Regenerativkammern. Die erhitzte Luft sowie das vorgewärmte Gas werden durch jeweils getrennte Kanäle einem von zwei Ofenköpfen zugeführt, vermischen sich dort und die Verbrennung findet statt. Die heißen Abgase werden dann über den gegenüberliegenden Ofenkopf in das zweite Regenarativkammersystem geleitet. Dabei wird das Gitterwerk der Kammern durch die Abgase aufgeheizt. Ist ein dann bestimmtes Temperaturniveau erreicht, wird durch eine Wechselklappe der kalte Luft- und Gasstrom umgelenkt und durch diese aufgeheizten Kammern dem zweiten Ofenkopf zur Verbrennung zugeführt – die Strömungsrichtung also umgekehrt. So wird das zuvor durch die kalten Medien abgekühlte erste Gitterwerk nun mit den Abgasen, welche bei der Verbrennung jetzt am zweiten Ofenkopf erzeugt werden, wieder aufgeheizt. Bei Erreichen eines bestimmten Temperaturniveaus wird dann die Durchströmungsrichtung in den Kammern erneut umgekehrt. Dieser Wechsel findet in regelmäßigen Zeitintervallen statt. Auf diese Weise konnten erhebliche Energieeinsparungen erzielt und dauerhaft Temperaturen gehalten werden, die über der Schmelztemperatur von Stahl lagen.
Verfahrensweisen
Nach den verwendeten Ausgangsmaterialien für das Schmelzverfahren kann unterschieden werden in:
- Schrott-Roheisen-Verfahren – Zugabe von 25 % festem oder flüssigem Roheisen zu 75 % Schrott
- Roheisen-Erz-Verfahren – Gemisch aus etwa 75 % flüssigem Roheisen und 25 % Eisenerz oder Walzzunder
- Schrott-Kohlungs-Verfahren – Aufkohlung von Schrott durch Holzkohle, Koks oder Elektrodenkohle
An das Einschmelzen schließt sich das Frischen an. Damit werden unerwünschte Anteile wie vor allem Kohlenstoff, aber auch Phosphor und Schwefel verringert. Der notwendige Sauerstoffeintrag erfolgt durch den Sauerstoffüberschuss der Brennerflamme oder aus dem Erz.
Im Prinzip spielt sich der gleiche Vorgang wie beim Puddelverfahren ab, jedoch friert die Schmelze mit zunehmender Entkohlung durch den Anstieg der Liquidustemperatur nicht ein. Die hohen Ofentemperaturen gewährleisten ein Flüssigbleiben bis zum Ende des Frischprozesses, sodass auch das beim Puddeln erforderliche Rühren entfällt.[2]
Ablauf
Der Schmelzprozess gliedert sich in mehrere Abschnitte, die nicht streng zu trennen sind und deren Gesamtzeit ca. 8 Stunden bedurfte:
- Ofenpflege: Torkretieren des Oberofens, Ofenberäumung, Sauberhalten der Gewölbe und Vorderwände, Kontrolle der Messtechnik (ca. 0,5 h)
- Einsetzen: Chargieren der metallischen Einsätze und Zusätze für die Schlackebildung (ca. 2 h)
- Einschmelzen: Verflüssigen des Einsatzes (ca. 3,5 h)
- Fertigmachen: Arbeit zur Einstellung der Abstichanalyse und Abstichtemperatur (ca. 1,5 h)
- Desoxydieren und Legieren
- Abstich bei Erreichen der erforderlichen Temperatur und Analyse (ca. 6–17 min)
Unmittelbar nach dem Abstich erfolgt das Vergießen des flüssigen Stahls in Kokillen. Nach dem Erstarren werden die Blöcke/Brammen zur Weiterverarbeitung ins Walzwerk transportiert.
Durch diesen hier langsam ablaufenden Prozess, mehrere Stunden, konnte der gewünschte Kohlenstoffgehalt sehr genau eingestellt werden. Das Verfahren eignet sich v. a. für die Erzeugung unlegierter Stähle. Der sogenannte Siemens-Martin-Stahl wird im Anschluss aus dem Ofen chargiert ("abgestochen").
Trotz Massentauglichkeit der Stahlerzeugung handelte es sich mit 8 Stunden um eine langsame Methode, im Vergleich zu den etablierten Verfahren nach Bessemer und Thomas. Der Ofen bedurfte einer zeitintensiven Pflege währenddessen keine Produktion stattfinden konnte. Nach der Pflege wurden zwei Stunden lang Einsätze und Zusätze für die Schlackebildung eingesetzt. Anschließend wurde der Einsatz für 3,5 Stunden verflüssigt durch das Verfahren des Einschmelzens. Weitere 1,5 Stunden wurden verwendet, um den Ofen vorzubereiten. Die Abstichtemperatur und die Abstichstichprobe wurden in diesem Zuge überprüft und ermittelt. Die letzten Minuten des Verfahrens dienten der Entziehung des Sauerstoffs, der Legierung von Elementen und der Durchführung eines Abstiches nach Erreichen der erforderlichen Temperatur.[1]
Bedeutung und Entwicklung
Jahr | USA | Frankreich | Deutschland |
---|---|---|---|
1880 | 102 | 0 | 35 |
1885 | 135 | 0 | 275 |
1890 | 521 | 251 | 387 |
1895 | 1155 | 376 | 1189 |
1900 | 3272 | 645 | 2145 |
1905 | 8579 | 756 | 3252 |
1907 | 10976 | 1001 | 4252 |
Das Siemens-Martin-Verfahren lieferte einen qualitativ höherwertigen Stahl, der jedoch wegen des aufwendigeren Prozesses etwas teurer war. Einst waren die Siemens-Martin-Öfen mit einer Abstichmasse, d. h. für die Herstellung von 10 Tonnen Stahl konzipiert worden. Durch die wirtschaftliche Massennutzung des Siemens-Martin-Verfahrens wurde die Abstichmasse in vereinzelten Ländern, wie z. B. den USA, auf 600 Tonnen ausgeweitet.
1867 auf der Pariser Weltausstellung erhielten die Martins für ihren hervorragenden Stahl und die Gebrüder Siemens für den Ofen höchste Auszeichnungen.
Das Verfahren wurde nach der Erfindung, in den späteren Jahren des 19. Jahrhunderts für das kontinuierliche Erschmelzen von Glas, insbesondere für die Massenproduktion, adaptiert, konstruktiv sowie in Hinsicht auf energetische Effizienz weiterentwickelt und ist noch heute Stand der Technik.
75 % der Stahl-Erzeugnisse weltweit sind in den 40er Jahren des 20. Jahrhunderts aus dem Siemens-Martin-Stahl erzeugt worden. Der Großteil des Stahls wurde bis 1960 mit diesem Verfahren hergestellt, da man damit auch ausgezeichnet Schrott verwerten konnte. 1993 wurde in Brandenburg an der Havel der letzte deutsche Siemens-Martin-Ofen aus wirtschaftlichen Gründen stillgelegt. Er ist heute als technisches Denkmal erhalten.[3][4]
Literatur
- Ernst Cotel: Der Siemens-Martin-Ofen. Hrsg.: Springer, Berlin, Heidelberg. 1927, ISBN 978-3-662-29140-5.
Einzelnachweise
- Christoph Löbbing: 100 Jahre bedeutend für die Stahlgewinnung: Das Siemens-Martin-Verfahren. In: Technikmuseen in Deutschland. 20. Mai 2020, abgerufen am 19. Dezember 2021.
- Siemens-Martin-Verfahren. In: www.giesserei-praxis.de. Abgerufen am 19. Dezember 2021.
- Technologie Siemens-Martin-Verfahren in Brandenburg. 2002 .
- Industriemuseum Brandenburg Siemens-Martin Stahlherstellung. Abgerufen am 13. Dezember 2021 (deutsch, Video).