Linz-Donawitz-Verfahren
Das Linz-Donawitz-Verfahren (LD-Verfahren; englisch basic oxygen process, BOP) ist ein Sauerstoffblasverfahren zum Frischen, also zur Stahlerzeugung durch Umwandlung von kohlenstoffreichem Roheisen in kohlenstoffarmen Stahl.
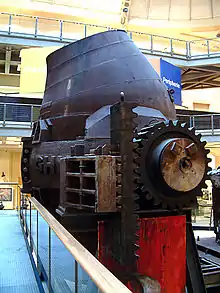
Mit dem LD-Verfahren werden derzeit 72 % der Weltrohstahlproduktion hergestellt (Stand: 2013).[1] Stahlwerke nach diesem Verfahren können lizenzfrei betrieben werden, da alle wichtigen Patente abgelaufen sind. Benannt ist es nach den beiden österreichischen Stahlwerken Linz (Oberösterreich) und Donawitz (Steiermark), deren Ingenieure den Prozess entwickelt haben.
Beschreibung
Das LD-Verfahren ist eine Weiterentwicklung des Thomas-Verfahrens. Statt des Einblasens von atmosphärischer Luft von unten wird Sauerstoff von oben aufgeblasen.
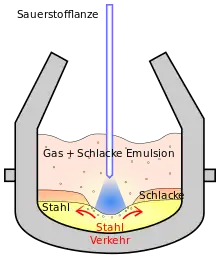
Beim LD-Verfahren wird ein basisch ausgekleideter Konverter, der so genannte LD-Konverter, mit flüssigem Roheisen, einem Kühlmittel (Schrott oder Eisenschwamm, insgesamt ca. 20 %[2]) und Kalk oder Dolomit als Schlackenbildner beschickt. Danach wird durch eine ausfahrbare, wassergekühlte Lanze reiner Sauerstoff von oben auf die Eisenschmelze geblasen. Daher wird das LD-Verfahren auch als Sauerstoffaufblasverfahren bezeichnet.
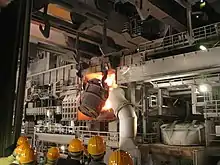
Die heftige Verbrennung (Oxidation) der Eisenbegleiter sorgt für eine Durchwirbelung der Schmelze und eine starke Temperaturzunahme. Zur besseren Durchmischung und Herabsetzung des Wasserstoffpartialdrucks wird Argon durch Düsen im Boden eingeblasen. Die Löslichkeit des Wasserstoffs (ein Stahlschädling) in der Schmelze wird herabgesetzt. Dieser gast aus, was die Bildung sogenannter Wasserstofffallen im späteren Werkstück verhindern soll. Während des Frischprozesses nehmen die Gehalte von Kohlenstoff, Silizium, Mangan, Schwefel und Phosphor stetig ab, da diese mit dem zugegebenen Gesteinsmehl verschlackt werden.
Die Blasdauer beträgt zwischen 10 und 20 Minuten und wird so gewählt, dass die gewünschte Entkohlung und die Verbrennung bzw. Oxidation der unerwünschten Beimengungen erreicht wird. Die verbrannten Eisenbegleiter entweichen als Gase oder werden durch zugesetzten gebrannten Kalk in der flüssigen Schlacke gebunden.
Während des Konverterprozesses entsteht Kohlenstoffmonoxid (CO) durch die Oxidation des Kohlenstoffs, das in Form von Blasen in der Schmelze aufsteigt. Da der Kohlenstoffgehalt der Schmelze zu Beginn des Konverterprozesses noch am höchsten ist, läuft die Entkohlungsreaktion zu diesem Zeitpunkt am stärksten ab. Die CO-Blasen steigen auf und sorgen für ein Aufschäumen der Schlacke[3].
Während des Stahlerzeugungsprozesses im Konverter kann der Abstand der wassergekühlten Sauerstofflanze zur Stahlbad- und Schlackenoberfläche variiert werden. Die Lanzenstellung beeinflusst u. a. die Stärke der Konvektion im Stahlbad, das Aufschäumen der Schlacke und hat außerdem einen Einfluss auf den Verschleiß der feuerfesten Ausmauerung des Konverters. Auch die Sauerstoffmenge, die pro Zeiteinheit auf das Bad geblasen wird (Sauerstoffdurchflussrate), ist einstellbar.
Das während der Entkohlungsphase entstehende Kohlenstoffmonoxid kann zur späteren Energiegewinnung genutzt werden. Um ein Entweichen des Gases und eine Reaktion des Kohlenstoffmonoxids zu Kohlenstoffdioxid zu vermeiden, wird der Konverter möglichst gut zur Umgebungsatmosphäre abgedichtet.
Das Stahlbad wird mit einer Temperatur von mehr als 1600 °C (bis zu heute möglichen 1750 °C) durch das Abstichloch in eine Pfanne abgestochen. Beim Abstich kann die Zugabe von Desoxidationsmitteln und Legierungsstoffen erfolgen. Danach wird die Schlacke über den Konverterrand abgegossen. Der Rohstahl kann anschließend einer sekundärmetallurgischen Behandlung zugeführt werden.
Nach einem Konverterprozess wird häufig ein Schlackenrest im Konverter belassen. Dieser kann als Basis für die Verschlackungsreaktionen der nächsten Konvertercharge verwendet werden. Eine weitere Möglichkeit ist es, die im Konverter verbliebene Restschlacke zum sogenannten Slag-Splashing[4] zu nutzen. Hierbei wird die Schlacke durch das Einblasen von Stickstoff durch die Lanze im Konverterinnenraum verteilt. Ziel dabei ist es, eine Schutzschicht auf der Konverterausmauerung zu bilden und hierdurch eine höhere Lebensdauer zu erreichen.
Die bisher erreichte Konvertergröße ist 380 t (ThyssenKrupp Stahl, Duisburg-Bruckhausen).
Ein wesentliches technisches Problem war anfangs die Beseitigung des braunen Rauchs (Eisen (Fe), das bei der hohen Reaktionstemperatur verdampft und als FeO aus dem Konverter entweicht), der weithin sichtbar war und ein Hindernis für die weltweite Verbreitung des LD-Verfahrens gewesen wäre; das Problem wurde jedoch technisch gelöst.
Entstehung
Vorentwicklungen
Im Jahre 1928 wurde der Schweizer Robert Durrer Professor für Eisenhüttenwesen an der Technischen Hochschule in Berlin-Charlottenburg, wo er seine grundlegenden Forschungen und Versuche über den Ersatz von Luft durch reinen Sauerstoff begann.[5]
Zwischen 1936 und 1940 hatte der aus Estland stammende, inzwischen zum US-amerikanischen Staatsbürger gewordene Otto Lellep (1884–1975) in der Gutehoffnungshütte die Gelegenheit, Versuche im Herdofen und im Konverter unter Verwendung von konzentriertem Sauerstoff zu machen.[6] Dabei wurden vorgeschmolzene Kalkferrite zur Vorverlegung der Entphosphorung sowie von unten angewendete Sauerstoffdüsen erprobt. Beides machte Probleme und ließ keine sichere Reproduzierbarkeit zu.[7] Da das Reichswirtschaftsministerium des „Dritten Reiches“ nach Lelleps im Ausland angelegter Alterssicherung trachtete[8], zog Lellep wieder in die USA und die Versuche wurden nicht fortgeführt.[7]
Durrer kehrte 1943 in die Schweiz zurück, wo ihm die Oberleitung der Metallurgischen Betriebe aller Werke der von Roll’schen Eisenwerke A.G. und die Leitung des Werkes Gerlafingen übertragen wurde und er einen neugeschaffenen Lehrstuhl für Eisenhüttenkunde an der ETH Zürich besetzte.[5] Auf seine Veranlassung wurden 1948 im Werk Gerlafingen Versuche durchgeführt, wobei erstmals in einem basischen 2-t-Kleinkonverter reiner Sauerstoff durch eine wassergekühlte Düse auf Roheisensorten verschiedener Zusammensetzung aufgeblasen wurde. H. Hellbrügge berichtete über die Versuche[7] und Durrer regte an, die Arbeiten in Linz weiterzuführen.[9]
LD-Verfahren
Das LD-Verfahren wurde in Österreich ab Juni 1949 bei der VÖEST in Linz bis zur Betriebsreife entwickelt. Die Versuche in einem 2,5-t-Konverter dauerten vom 3. bis zum 25. Juni, bis sich schließlich unter Beteiligung von Theodor Eduard Suess und Rudolf Rinesch ein Erfolg einstellte. Es wurde dann eine große Versuchsreihe mit einem 5-t-Konverter in Donawitz und einem 15-t-Gefäß in Linz durchgeführt.[10] Die Erfindung Rineschs führte u. a. zu seiner Dissertation über Das LD-Verfahren, die wegen des darin enthaltenen Know-hows lange Zeit unter Verschluss gehalten wurde. Herbert Trenkler wirkte als Hüttendirektor maßgeblich an der Neuentwicklung mit.
Aufgrund der viel niedrigeren Produktionskosten orientierte sich die VÖEST am 9. Dezember 1949 neu zum LD-Verfahren, das durch Tests und Kostenrechnungen überzeugt hatte:
„Dr. Richter-Brohm, der allein verantwortliche Verwalter der VÖEST, entschied aufgrund dieser Fakten, die Stahlerzeugung in Linz auf eine völlig neue Basis zu stellen und ein Sauerstoffaufblas-Konverterstahlwerk zu bauen. […] Im Oktober 1950 erfolgte die Auftragsvergabe für das erste LD-Stahlwerk und am 27. November 1952 wurde die Produktion aufgenommen.“[11]
Am 31. August 1949 wurde die Erfindung angemeldet und am 15. Dezember 1950 dafür das Österreichische Patent AT168589 erteilt. Das LD-Verfahren löste das vorher übliche Siemens-Martin-Verfahren (SM-Verfahren) und das ältere Thomas-Verfahren ab.
Bezeichnung
Die Herkunft der Abkürzung LD ist ungeklärt. Heute wird sie meist von den Produktionsstandorten Linz und Donawitz[9] abgeleitet, an denen das Verfahren zur Produktionsreife gebracht wurde. Eine alte, seltener verwendete Bezeichnung ist auch Linzer Düsenstahl[12][13] da der Sauerstoff über spezielle, hitzeunempfindliche Düsen eingeblasen wird.
Eine andere mögliche Herkunft stellt Linz-Durrer[9] dar, da Durrer entscheidende Vorarbeit geleistet hatte. Er war allerdings der Meinung gewesen, der Sauerstoffstrahl müsse „tief, nach Art eines festen Körpers“, eingeblasen werden, was aber am Ende erfolglos blieb, weil sich keine reaktionsfähige Schlacke bildete. Hingegen führte das „nicht tiefe“ Ein- bzw. Aufblasen des Sauerstoffs rasch zu einer sehr heißen Reaktionszone und flüssigen Schlacke, was letztlich dem LD-Verfahren zum Durchbruch verhalf.
Die Begriffe „nicht tief“ und „tief einblasen“ sind wegen fehlender Maß- oder Bereichsangaben patentrechtlich unklar. Dies war der Grund, weshalb ein US-amerikanisches Gericht zwischen der Patentinhaberin und der US-Klägerin letztlich zu Gunsten der Klägerin entschied und das US-Patent für ungültig erklärte, weil es keine klare Lehre zum technischen Handeln enthalte.
Eine Weiterentwicklung des LD-Verfahrens ist das LD-AC Verfahren (A steht für die ARBED in Luxemburg, C für das Centre National de Metallurgique in Lüttich). Dabei wird Kalkstaub zusammen mit dem Sauerstoff durch die Blaslanze auf das Metallbad geblasen.
Auszeichnung
1959 wurden Otwin Cuscoleca, Felix Grohs, Hubert Hauttmann, Fritz Klepp, Wolfgang Kühnelt, Rudolf Rinesch, Kurt Rösner und Herbert Trenkler als Erfinder des LD-Verfahrens mit dem Karl-Renner-Preis ausgezeichnet.[14][15]
Siehe auch
Weblinks
- Das LD-Verfahren erobert die Welt. In: ooegeschichte.at. Virtuelles Museum Oberösterreich (Bericht zur Entstehung des LD Verfahrens).
- expedition voestalpine: Linz & Donawitz – ein Verfahren schreibt Geschichte
- Die Geschichte des Linz-Donawitz-Verfahrens (PDF; 3,6 MB) voestalpine; 44-seitige Broschüre über Ursprünge, Anfänge und Auswirkungen des LD-Verfahrens
- LD-Stahl. (PDF; 7,5 MB; 51 Seiten) Zeitschrift des Österreichischen Stahlbauvereines, 3. Jahrgang, Heft 2, 1957.
Einzelnachweise
- stahl-online.de
- bdsv.org (Memento des Originals vom 2. April 2015 im Internet Archive) Info: Der Archivlink wurde automatisch eingesetzt und noch nicht geprüft. Bitte prüfe Original- und Archivlink gemäß Anleitung und entferne dann diesen Hinweis. (PDF)
- Helmut Burghardt, Gerd Neuhof: Stahlerzeugung. Hrsg.: Hans-Joachim Eckstein. 1. Auflage. VEB Deutscher Verlag für Grundstoffindustrie, Leipzig 1982, S. 68–75.
- Michael Degner u. a.,: Stahlfibel. Hrsg.: Stahlinstitut VDEh. Verlag Stahleisen GmbH, Düsseldorf 2007, ISBN 978-3-514-00741-3, S. 53–59.
- Schweizerische Bauzeitung: Wochenschrift für Architektur, Ingenieurwesen, Maschinentechnik, Band 83, 1965, S. 858
- Günter Bauhoff: Lellep, Otto. In: Neue Deutsche Biographie (NDB). Band 14, Duncker & Humblot, Berlin 1985, ISBN 3-428-00195-8, S. 179 (Digitalisat).
- Stahl und Eisen, Band 73, Verein Deutscher Eisenhüttenleute, A. Bagel, 1953, S. 7
- Helmut Heiber (Hrsg.): Akten der Partei-Kanzlei der NSDAP: Register, Band. 1, Oldenbourg Verlag, 1983, ISBN 978-3-486-49641-3, S. 472 (Akt 14120, eingeschränkte Vorschau in der Google-Buchsuche)
- Metallurgie und Giessereitechnik, Bände 1–2, Verlag Technik, 1951, S. 173
- Stahl und Eisen. Zeitschrift für das Deutsche Eisenhüttenwesen, Band 72, 1952, S. 993
- Herbert Hiebler, Wilfried Krieger: Prof. Dr. mont. Herbert Trenkler zum 100. Geburtstag. In: Berg- und Hüttenmännische Monatshefte (BHM), Bd. 152, 2007, Heft 11, S. 378–380, hier S. 378 (doi:10.1007/s00501-007-0332-7).
- Österreichische Bauzeitschrift: Organ der Fachgruppen für Bauwesen der österreichischen Ingenieur- und Architekten-Vereines und der städtischen Prüf- und Versuchsanstalt für Bauwesen Wien, Bände 11–12, Springer-Verlag in Wien, 1956, S. 25
- Tätigkeitsbericht des österreichischen Gewerkschaftsbundes, ÖGB, 1956, S. U-46
- Wiener Rathauskorrespondenz, 12. Dezember 1959, Blatt 2461.
- Wiener Rathauskorrespondenz, 23. Jänner 1960, Blatt 114.