Gießen (Metall)
Das Gießen (auch der Guss oder das Werk) von Metallen und Legierungen ist ein Fertigungsverfahren, bei dem Werkstücke (Gussstücke) aus flüssigem Metall – der Schmelze – hergestellt werden. Beim häufigsten Verfahren – dem in Gießereien vorgenommenen Formguss – wird die Schmelze in eine Hohlform gefüllt, in der sie anschließend erstarrt. Die Innenfläche der Hohlform ist das Negativ der Außenfläche des Gussstücks.
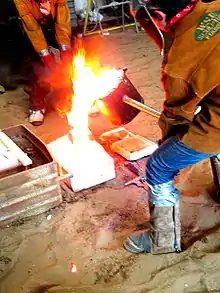
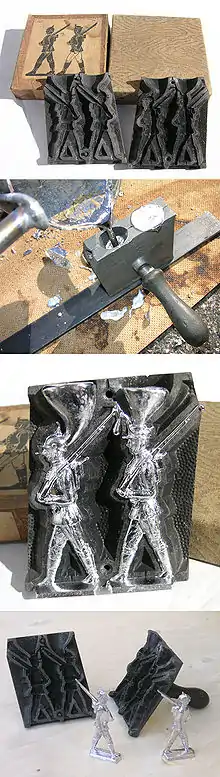
Das Gießen zählt zur Hauptgruppe des Urformens und ist innerhalb dieser die bedeutendste Verfahrensgruppe. Für das Gießen nicht-metallischer Werkstoffe siehe Gießen (Urformen).
Das Einfüllen der Schmelze in die Formen wird als Abguss bezeichnet. Zur gesamten Prozesskette des Formgusses vom Rohmaterial bis zum Gussstück zählt auch der Formenbau, die Fertigung der Modelle, das Schmelzen der Werkstoffe und die Schmelzebehandlung, sowie die Nachbehandlung: Entformen, Wärmebehandeln und das Gussputzen. Zu letzterem zählt die Entfernung von Anschnitt und Speisern, die nur zur Zuführung von Schmelze dienen, aber nicht Bestandteil des Gussteils sind, das Entsanden, Entgraten, Entzundern und das Ausbessern von Gussfehlern.
Bei der Eisengewinnung aus Erz wird das flüssige Metall zu Barren oder Masseln (Blockguss) oder zu endlosen Strängen (Strangguss) gegossen. Die Weiterverarbeitung der Masseln erfolgt in den Gießereien, wobei das Eisen wieder eingeschmolzen wird. Von den dort angewendeten Gießverfahren sind die wichtigsten der Sandguss, wobei Formen aus Sand genutzt werden, und der Druckguss, bei dem die Schmelze von einem Kolben in eine mehrfach genutzte Dauerform gepresst wird.
Die wichtigsten Gießwerkstoffe für Formguss sind Gusseisen mit einem Massenanteil an der Gesamtproduktion in Gießereien von etwa 75 % und Aluminiumlegierungen. Die für das Gießen wichtigen Werkstoffeigenschaften werden zur Gießbarkeit zusammengefasst.
Die gießenden sowie die zuliefernden Betriebe werden unter dem Begriff „Gießerei-Industrie“ zusammengefasst, die wiederum in Deutschland im Bundesverband der Deutschen Gießerei-Industrie gebündelt ist.
Geschichte
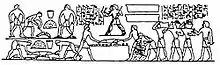
Ur- und Frühgeschichte
Das Gießen stammt aus der Kupferzeit, der Übergangszeit von der Jungsteinzeit zur Bronzezeit. Erste Metalle waren schon in der Steinzeit bekannt. In gediegener, also metallischer Form kamen in der Natur Gold, Silber und Kupfer vor. Kupfer wurde anfangs durch Hämmern bearbeitet, wodurch es sehr spröde und brüchig wurde. Daher wurde es zunächst nur als Schmuck genutzt; für Werkzeuge waren alle bekannten Metalle wegen der geringen Härte und Festigkeit nicht brauchbar. Mit der Entwicklung von Schmelzöfen (sogenannte Tiegelöfen) um 3000 v. Chr. – zuerst in China und Indien – wurde es möglich, Metalle zu gießen und auch aus Kupfererz Kupfer zu gewinnen. Kupfer bereitete jedoch beim Gießen Probleme, da es dazu neigt, Blasen zu bilden. Außerdem weist es einen hohen Schmelzpunkt auf und ist relativ zähflüssig. Seit 1500 v. Chr. wurden in Ägypten daher Blasebälge statt Blasrohre eingesetzt. Der entscheidende Durchbruch gelang mit der Technik des Legierens: Durch Zulegieren von Zinn entstand Bronze, die sich ausgezeichnet vergießen lässt, deutlich härter und fester ist als Kupfer und sich daher auch für Werkzeuge eignet. Damit löste Bronze den Stein als wichtigsten Werkzeugwerkstoff ab. Bronze, Silber und Gold wurden für den Kunstguss genutzt, Bronze zusätzlich für die Herstellung von Waffen und Werkzeugen. Diese Metalle wurden zwar auch durch Schmieden und Treiben bearbeitet, das wichtigste Verfahren aber war das Gießen.[1] Da sich der Schmelzofen aus dem Keramikofen entwickelte, waren die frühen Metallverarbeiter auch mit dem Bau keramischer Formen vertraut.
Antike
In der Antike wurde Bronze durch Eisen als wichtigster Werkstoff abgelöst, das sich in Europa bis ins Mittelalter nicht gießen ließ, während die Chinesen die Technik seit etwa 500 v. Chr. beherrschten. Im Kunsthandwerk wurde nach wie vor der Bronzeguss genutzt und weiterentwickelt. Die Bronzestandbilder wurden im Laufe der Antike immer größer und komplexer. Anfangs wurden nur massive Figuren von etwa 30 cm Höhe hergestellt. Später gelang der Guss von hohlen Gussstücken (Hohlguss), was viel Material einsparte und so bedeutend größere Werkstücke ermöglichte, darunter lebensgroße Reiterstandbilder. Angewandt wurde das Wachsausschmelzverfahren: Über eine Grundmasse aus Ton wurde ein Mantel aus Wachs gelegt, in den die zu fertigende Form eingearbeitet wurde. Danach wurde diese Schicht mit einer weiteren Lage aus Ton umgeben. Die Schmelze wurde in die Zwischenlage aus Wachs gegossen, wodurch dieses verbrannte. Bei einer Weiterentwicklung des Verfahrens wurden die Standbilder in einzelnen Teilen wie Armen oder Köpfen vergossen und zusammengelötet. Wenn die einzelnen Teile misslangen, musste nicht die gesamte Form erneut gefertigt werden.[2]
Mittelalter
Im Hochmittelalter gelang dank der neuen Schachtöfen, den Vorläufern der Kupolöfen, erstmals die Herstellung von Gusseisen (gießbares, aber nicht schmiedbares Eisen), das nun im Kunstguss genutzt wurde. Außerdem wurden die Blasebälge immer häufiger durch Wasserkraft angetrieben. Teils wurde in den gleichen Schachtöfen auch Gusseisen und schmiedbares Eisen hergestellt.[3] Teilweise wurden die Formen in der Gießerei gebaut und zu den Öfen transportiert, teils wurde das Gusseisen in den Gießereien erneut eingeschmolzen. Besondere Bedeutung erlangte der Glockenguss.
Frühe Neuzeit
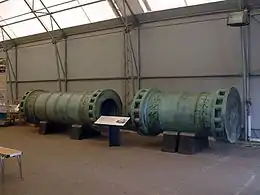
Die ersten Kanonen der frühen Neuzeit wurden noch aus schmiedeeisernen Blechstreifen geschmiedet, was jedoch aufwendig war. Danach gewann der Bronzeguss an Bedeutung. Die Bronzekanonen wurden zunächst im Vollguss hergestellt und dann gebohrt, später wurden sie über einem Kern gegossen und die vorhandene Bohrung nur noch ausgebohrt, was Gussmasse und Bearbeitungszeit einsparte. Kurz vor der Industrialisierung wurden auch Kanonen aus Gusseisen über einem Kern gegossen und danach ausgebohrt.
Barock
Industriezeitalter
Während der Industrialisierung wurde Gusseisen zum wichtigen Konstruktionswerkstoff. Zum Teil wurden ganze Brücken daraus gefertigt. Gegen Ende des 19. Jahrhunderts wurden mit Aluminium und Magnesium neue Gusswerkstoffe entdeckt. Bereits um 1900 wurden Serienteile für die Automobilindustrie aus Aluminium vergossen, größere Anwendungen gab es aber erst Mitte des 20. Jahrhunderts.
In den 1970er Jahren wurde es durch die Entwicklung moderner FEM-Simulation möglich, den Gießprozess zu simulieren und zu optimieren.[4]
Konkurrierende Verfahren
Viele Fertigungsverfahren lassen sich alternativ anwenden. Das Gießen konkurriert vor allem mit dem Umformen (Schmieden) und dem Zerspanen (Drehen, Bohren, Fräsen, Schleifen). Diese benötigen allerdings Rohmaterial in fester Form, das üblicherweise durch Gießen hergestellt wurde. Beim Gießen sind auch sehr komplexe Formen herstellbar und es eignet sich für große Serien. Kleine und mittelgroße Werkstücke werden eher geschmiedet oder zerspant.
Werkstoffe mit sehr hohem Schmelzpunkt werden häufig pulvermetallurgisch hergestellt. Statt einer Schmelze wird dabei Metallpulver genutzt. Bei Einzelstücken ist das 3D-Drucken eine Alternative.[5][6]
Wirtschaftliche Bedeutung
Das Gießen komplexer Werkstücke hat gegenüber anderen Produktionsmethoden den Vorteil, dass es nur relativ wenige Prozessschritte umfasst und den Materialverbrauch reduziert, der z. B. beim Fräsen entsteht. Auch bei gewichtsoptimierter Bauteilgeometrie, wie sie im Flugzeugbau oder in der Medizintechnik beim Titanguss erforderlich ist, erlangt das Gießen gegenüber der Zerspanung eine immer größere Bedeutung. Der Anteil der Produktion der Gießereien an der Gesamtproduktion des produzierenden Gewerbes in Deutschland macht zwar nur etwa ein Prozent aus, es gibt jedoch zahlreiche Branchen, die die Gießereien als Zulieferer benötigen. Hauptabnehmer sind mit über 50 % die Fahrzeugindustrie (mit stark steigender Tendenz in den letzten Jahrzehnten) und der Maschinenbau. Hingegen ging der Bedarf der Montanindustrie an Gussteilen stark zurück.
Die Anzahl der Beschäftigten lag 2011 bei 78.000 in Deutschland, die in etwa 500 Gießereien arbeiteten. Die Produktionsmenge wird in der Gießerei als Gesamtmasse der Werkstücke angegeben. 2011 lag sie für Deutschland bei 5,8 Millionen Tonnen.[7] Die weltweite Jahresproduktion an Gussteilen betrug 2013 über 100 Millionen Tonnen. 2013 war China der wichtigste Produzent mit 42,5 Millionen Tonnen, gefolgt von den USA (12,8 Millionen Tonnen) und Indien (9,3 Millionen Tonnen). Danach folgen Japan, Deutschland und Russland mit 5,3 bis 4,3 Millionen Tonnen.[8]
- Entwicklungsperspektiven
Allein die deutschen Fahrzeugbauer beziehen etwa 3 Millionen Tonnen aus der Produktion der deutschen Gießereien. Das zeigt, dass die Branche von der Durchsetzung der Elektromobilität, die zum Wegfall schwerer mechanischer Komponenten (Motor, Getriebe usw.) führen wird, stark betroffen sein dürfte. Auch verschiebt sich der Schwerpunkt der Automobilproduktion nach Asien. Ein weiterer wichtiger Trend ist die Entwicklung von Leichtbaugussteilen. Der Handformguss von großen Einzelstücken und Kleinserien ist in Deutschland aus Effizienzgründen weitgehend eingestellt worden, was dazu führt, dass große, von Hand gegossene Einzelstücke heute oft aus dem Ausland (z. B. Brasilien) bezogen werden müssen.
Erreichbare Genauigkeiten und Produktivität
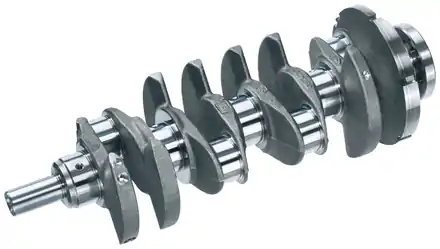
Die erreichbaren Genauigkeiten sind im Allgemeinen gering. Die ISO-Toleranzen liegen zwischen IT16 bis IT11 (kleine sind genauer), mit Sondermaßnahmen auch IT10. Die Genauigkeiten beim Schmieden sind vergleichbar (Präzisionsschmieden bis IT8) beim Zerspanen deutlich besser mit IT7 bis IT6, weshalb Gussteile häufig spanend nachbearbeitet werden. Weiterentwicklungen in der Gießereitechnik versuchen diese Nacharbeit möglichst gering zu halten. Die Oberflächenrauheit ist wie auch beim Schmieden relativ hoch mit mittleren Rautiefen von 63 µm bis 1000 µm, bei Zerspanen liegen sie zwischen 10 µm und 0,25 µm.
Die Seriengussverfahren wie das Druckgießen sind sehr produktiv.[9] Demgegenüber ist das Vakuumgießen ein Verfahren für den Präzisionsguss von Einzelstücken, Kleinserien oder Prototypen aus Kunststoff.
Energiebilanz und Materialausnutzung
Die Materialausnutzung ist beim Gießen wie auch beim Schmieden sehr gut. Nur etwa 10 % des Materials geht verloren, beim Zerspanen wird teilweise über die Hälfte des Rohteils in Form von Spänen entfernt. Trotz der großen Energiemengen zum Schmelzen ist das Gießen daher wie auch das Schmieden sehr energieeffizient, wenn die gesamte Prozesskette zum fertigen Bauteil betrachtet wird, während beim Zerspanen etwa die dreifache Energie benötigt wird.[10]
Werkstückspektrum und Anwendungsgebiete
Mit dem Gießen ist eine große Bandbreite an Werkstücken herstellbar. Manche Kleinteile wiegen nur wenige Gramm, die größten über 200 Tonnen. Die Vielfalt der herstellbaren Formen ist kaum begrenzt, vor allem Freiformflächen, also dreidimensionale gekrümmte Flächen sind möglich. Wichtige Produkte sind Glocken (hergestellt durch Glockenguss), Implantate und Prothesen, Bronzestandbilder (per Bronzeguss gefertigt) und sonstiger Kunstguss, Gehäuse für Pumpen, Getriebe und Elektromotoren, Impeller, Schiffspropeller und Turbinenschaufeln für die Luft- und Raumfahrtindustrie aus Titan oder Nickel. Für die wichtigste Abnehmerbranche der Gießerei, die Automobilbranche, werden Räder, Fahrwerksteile wie Bremsscheiben, Naben und Lenker der Radaufhängungen, Motorblöcke, Kurbelwellen, Zylinderköpfe, Abgaskrümmer und viele weitere Teile gefertigt, häufig per Sandguss (mit Gusseisen) oder Druckguss (mit Aluminium).[11]
- Glocke, noch mit teilweise erhaltener Form und Anschnitt
- Teil eines Turboladers.
- Turbinenschaufel (links) und Wachsmodell
- Aluminiumdruckgussteil (Teil eines Staubsaugergebläses)
- Motorblock
- Autoteil aus Aluminium (Federbeinstütze)
Werkstoffspektrum – Gusswerkstoffe und Gießbarkeit
Werkstoffe, die in der Gießerei genutzt werden, werden als Gusswerkstoff oder Gusslegierung bezeichnet, ihre Eignung zum Gießen als Gießbarkeit.
Der mit Abstand wichtigste Gusswerkstoff mit einem Anteil von 75 % ist das Gusseisen, eine Eisenlegierung mit mindestens 2 % Kohlenstoff (meist um 4,3 %). Es hat mit 1200 °C einen deutlich geringeren Schmelzpunkt als Stahl (1500 °C), der unter 2 % Kohlenstoff enthält. Außerdem weist Gusseisen eine sehr gute Gießbarkeit auf: Die Schmelze ist sehr dünnflüssig und weist ein gutes Formfüllungsvermögen auf. Die Schwindung und Schrumpfung beim Abkühlen und Erstarren sind gering. Außerdem weist Gusseisen sehr gute Gebrauchseigenschaften auf, darunter die Verschleißbeständigkeit, und die Schwingungsdämpfung. Die meisten Gusseisensorten enthalten noch um 2 % Silicium, das die Gießbarkeit verbessert. Gusseisen wird bevorzugt in Formen aus Sand vergossen (Sandguss).
Der zweitwichtigste Gusswerkstoff gemessen als Massenanteil der Gesamtproduktion in Gießereien ist Aluminiumguss, eine Aluminiumlegierung die noch Silicium, Magnesium oder Kupfer enthält. Sie schmelzen bei etwa 570 °C und lassen sich auch sehr gut vergießen. Aluminiumgusslegierungen können auch für filigrane Bauteile genutzt werden, deren Formen von anderen Werkstoffen nicht vollständig gefüllt werden würden. Aluminiumlegierungen werden bevorzugt für den Druckguss eingesetzt.
Einstellige prozentuale Anteile haben noch der Stahlguss und die verschiedenen Kupferlegierungen (Messing, Bronze, Rotguss).[12] Medizinische Implantate, aber auch Flugzeugteile werden teils aus Titan gegossen, jedoch läuft der Titangussanteil in der Gießereistatistik unter „Sonstige“ und andererseits wird nur etwa 2 %[13] des Titans durch Gießen verarbeitet da es einen sehr hohen Schmelzpunkt aufweist und seine Schmelze zur Aufnahme von Sauerstoff neigt, die im festen Zustand zu Versprödungen führt.
Gießverfahren
Es gibt zahlreiche verschiedene Gießverfahren, die nach mehreren Kriterien eingeteilt werden können.
-2_NT.PNG.webp)
Das Gießen in Formen, die der Form des Fertigteils weitgehend entsprechen, ist das Formgießen, das am häufigsten eingesetzt wird. Daneben gibt es noch das Vergießen zu Barren oder Brammen, den Blockguss und das Gießen von kontinuierlichen, theoretisch endlosen Strängen, dem Strangguss.
Nach der Art der Formfüllung unterscheidet man das Schwerkraftgießen, das Standardverfahren, bei dem die Schmelze durch die Wirkung der Schwerkraft in die Form fällt, sowie das Schleudergießen mit Zentrifugalkräften (für rotationssymmetrische Teile) und das Druckgießen, bei dem die Schmelze durch Kolbendruck in die Form gepresst wird.
Eine besonders wichtige[14] Einteilung unterscheidet zwischen Verfahren mit Formen, die nur einmalig genutzt werden und beim Entnehmen der Gussstücke zerstört werden (verlorene Form) und den Dauerformen, die mehrfach genutzt werden:
- Gießen mit verlorenen Formen. Für die Herstellung der Formen werden Modelle genutzt. Es wird weiter unterschieden, ob die Modelle einmalig (verlorenes Modell) oder mehrfach (Dauermodell) genutzt werden können.
- Gießen mit verlorenen Formen und Dauermodellen: Es wird auch als Sandguss bezeichnet, da die Formen aus Sand gefertigt werden. Je nach Art der Formherstellung eignet es sich für Einzelteile und Serienstücke sowie beliebige Werkstückmassen und hat daher große wirtschaftliche Bedeutung. Zahlreiche Fahrzeugkomponenten werden so hergestellt. Da Sand sehr temperaturbeständig ist, wird es vor allem zum Vergießen von Gusseisen und Stahlguss genutzt.
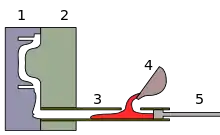
- Gießen mit verlorenen Formen und verlorenen Modellen: Dazu zählen das Wachsausschmelzverfahren (Feingießen) und das Vollformgießen. Beim Feingießen werden die Modelle aus Wachs gefertigt und mit Ton oder Keramik umhüllt. Danach wird das Wachs ausgeschmolzen und die Form mit Schmelze befüllt. Es eignet sich nur für kleinere Stückzahlen und kleine Werkstückmassen, erreicht aber hohe Qualitäten. Beim Vollformgießen werden die Formen aus Styropor gebaut, mit beliebigem Formstoff umgeben und dann, ohne die Modelle zu entfernen, mit Schmelze übergossen, die die Modelle verbrennt. Es eignet sich für kleine Stückzahlen und auch sehr große Gussstücke.
- Gießen mit Dauerformen. Sie bestehen meistens aus Stahl. Durch den Kontakt mit der Schmelze verschleißen sie, wodurch die Werkstücke eine schlechtere Oberflächenqualität und Formgenauigkeit aufweisen als bei verlorenen Formen. Bei niedrigschmelzenden Werkstoffen wie Aluminium können sie sehr häufig abgegossen werden, bei hochschmelzenden wie Kupfer seltener. Da die Dauerformen sehr teuer sind, wirkt sich die Stückzahl stark auf den Stückpreis aus.[15]
- Kokillenguss: Schwerkraftgießen mit DauerformenVarianten des Schleudergießens
- Druckguss: Hier wird die Schmelze mittels eines Kolbens in die Form gepresst. Die Zeit zum Füllen der Form ist reduziert, weshalb er für Großserien kleiner Werkstücke gut geeignet ist. Besonders häufig wird er zum Vergießen von Aluminium genutzt, dem Aluminiumdruckguss.
- Schleuderguss
- Strangguss
- Niederdruckguss: Hier wird der Luftdruck in der Umgebung der Schmelze erhöht, um sie in ein Steigrohr zu drücken, das zur Form führt.
- Kokillenguss: Schwerkraftgießen mit Dauerformen
Außerdem gibt es noch eine Reihe von Spezialverfahren wie das Thixogießen, Vacuralgießen und Squeeze Casting.
Prozesskette beim Gießen
Die Prozesskette beim Gießen besteht aus
- der Vorbereitung mit der Herstellung der Formen und dem Schmelzen der Werkstoffe,
- dem Abguss, wozu das Füllen der Form und das Erstarren der Schmelze zählt, sowie
- der Nachbehandlung: dem Entformen, dem Gussputzen und der Wärmebehandlung.
Vorbereitung
Zur Vorbereitung des eigentlichen Gießvorgangs, des Abgusses, werden die Formen gebaut, für die zuvor Modelle gefertigt werden. Um Hohlräume in den Werkstücken fertigen zu können, werden Kerne hergestellt und in die Formen gelegt. Parallel zu diesen Aufgaben wird die Schmelze vorbereitet.[16]
Modellbau
Die Wachsmodelle beim Feingießen werden entweder manuell aus einem Wachsmodell geschnitzt oder mittels eines Urmodells selbst durch Gießen hergestellt. Beim Vollformgießen werden die Styropormodelle aus Blöcken geschnitten und teilweise auch aus Einzelteilen zusammengebaut und verklebt. Dauermodelle für das Sandgießen können aus Holz, Keramik oder Metall bestehen, die verschieden oft genutzt werden können. Billige Holzmodelle können teilweise nur fünfmal genutzt werden, Metallmodelle deutlich öfter.[17]
Formenbau und Formstoffaufbereitung
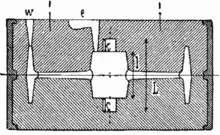
Dauerformen werden aus Stahl geschmiedet oder gefräst und können mehrere 100.000 Euro kosten.[18] Verlorene Formen bestehen aus Formstoff, für den meist Sand genutzt wird, der mit geringen Mengen von Ton und Wasser zusammengehalten wird. Die Formen können aus verfestigtem Sand gefräst werden (direktes Formstofffräsen). Teilweise werden sie durch 3D-Drucken[19] gefertigt. Üblicherweise werden zum Formenbau aber Modelle genutzt, über die der Formstoff gelegt wird. Der noch lose Formstoff muss dann verfestigt werden, wofür zahlreiche verschiedene Verfahren zum Einsatz kommen können. Dazu zählt einfaches Schütteln und Pressen, was in der Serienfertigung genutzt wird, da es sich automatisieren lässt (Maschinenformen). Beim Maskenformen wird eine relativ dünne Schicht aus Formstoff über das Modell gelegt und mit Harzen durchtränkt. Diese härten im Ofen aus.
Die Formen müssen nicht nur die Form der zu fertigenden Werkstücke enthalten, sondern weitere Öffnungen zum Zuführen der Schmelze. Der Hohlraum, in die die Schmelze gegossen wird, wird als Anschnitt bezeichnet. Nach der Formfüllung verringert sich das Volumen der flüssigen, abkühlenden Schmelze, weshalb weiteres Material in die Form fließen muss. Ein einzelner Anschnitt reicht häufig nicht dafür aus, weshalb sogenannte Speiser angebaut werden, die nach dem Erstarren mit dem Anschnitt wieder entfernt werden. Der Anschnitt besteht im einfachsten Fall aus einer Öffnung direkt über dem Hohlraum für das Werkstück. Bessere Werkstückqualitäten lassen sich erreichen, wenn die Schmelze in einem separaten Schacht auf den Boden fällt und seitlich in das Werkstück fließt. Für die Form, Größe und Anzahl der Speiser und Anschnitte gibt es zahlreiche Varianten, da sie einen großen Einfluss auf die Bauteilqualität haben.[20][21]
Kernherstellung und Kernformstoffaufbereitung
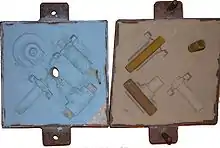
Kerne sind nötig, um Gussteile mit Hohlräumen fertigen zu können. Die Kerne werden in die Formen gelegt und nach dem Erstarren entnommen. Bei Dauerformen bestehen die Kerne meistens ebenfalls aus Metall, bei Sandformen aus Sand. Sie werden ebenfalls nach dem Gießen zerstört. Außerdem werden Kerne für Hinterschneidungen benötigt.[22]
Schmelzevorbereitung
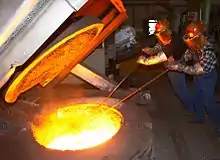
Zur Vorbereitung der Schmelze zählt die Zusammenstellung der Rohstoffe, das Schmelzen in Öfen und die Schmelzebehandlung.
Als Rohstoffe können Metalle direkt von den Hüttenwerken genutzt werden, in der Gießerei werden aber größere Mengen Schrott verarbeitet. Die Branche ist durch eine hohe Recyclingquote geprägt. Ein Teil des Schrotts entsteht in der Gießerei selbst; dazu zählen fehlerhafte Gussstücke sowie die entfernten Speiser und Anschnittsysteme, die als Kreislaufmaterial fungieren. Verarbeitet wird aber auch Altschrott aus gebrauchten und zerkleinerten Bauteilen.
Um eine Legierung mit der gewünschten Zusammensetzung zu erhalten, müssen verschiedene Ausgangsmaterialien gemischt werden. Diese Mischung wird als Gattierung bezeichnet. Mittels spezieller Software kann berechnet werden, welche Mengen in welchen Verhältnissen benötigt werden für die günstigste Gattierung.
Zum Schmelzen der Metalle werden verschiedene Industrieöfen verwendet. Besondere Bedeutung haben der Kupolofen, der Lichtbogenofen und der Induktionsofen. Sie eignen sich für verschiedene Werkstoffe unterschiedlich gut. Kupolöfen werden für Eisenwerkstoffe genutzt, Lichtbogenöfen für Stahl und Nichteisenmetalle, beide aber nur zum Schmelzen. Induktionsöfen und Widerstandsöfen eignen sich auch zum Warmhalten der Schmelze. Etwa 60 bis 70 % des Energiebedarfs einer Gießerei geht auf das Schmelzen zurück.[23]
Danach erfolgt die Schmelzebehandlung. Der Schmelze werden verschiedene Stoffe zugesetzt, die verhindern, dass sie mit dem Sauerstoff der Luft reagiert und sich in sonstiger Weise ungewollt verändert. Bei der Impfung der Schmelzen werden Fremdstoffe zugesetzt, die die Erstarrung beeinflussen und damit die Härte und Festigkeit des fertigen Gussstücks.[24]
Meistens werden die Metalle in der Gießerei geschmolzen, manchmal auch in den Stahl- oder Hüttenwerken und dann per Flüssigmetalltransport zur Gießerei verbracht.
Abguss
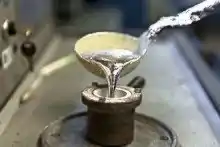
Das Einfüllen der Schmelze in die Form wird als Abguss bezeichnet. Danach und teilweise parallel dazu erstarrt die Schmelze. Diese Vorgänge haben entscheidenden Einfluss auf die Qualität der Gussteile.[25] Die Schmelze kann direkt aus dem Ofen in die Form gefüllt werden, sie kann aber auch in Gießpfannen oder Gießlöffel gefüllt werden und erst anschließend in die Formen.[26]
Formfüllung
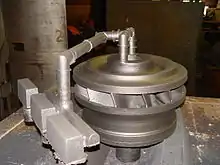
Die Schmelze kann direkt in die Formen gegossen werden, was vor allem bei nach oben offenen Formen praktiziert wird. Üblich ist das Vergießen in ein spezielles Eingusssystem. Die Schmelze kann von oben in die Form fallen oder seitlich oder von unten in sie hineinfließen. Fallende Schmelzen führen zu Verwirbelungen und turbulenten Strömungen. Die Schmelze vermengt sich dabei mit Luft und nimmt unerwünschte Gase auf, die später als Poren im Gussstück zurückbleiben. Die Formen werden aber relativ schnell befüllt. Bei steigender Formfüllung kommt es zu keinen oder nur geringen Verwirbelungen, was zu laminaren Strömungen führt. Die Gussstücke enthalten dann nur wenige Poren. Beim Kippgießen werden beide Varianten kombiniert.
Die Schmelze erkaltet beim Kontakt mit der Form. Die Erstarrung soll erst beginnen, wenn die Form vollständig gefüllt ist, da es sonst zu Fehlstellen kommen kann. Manche Schmelzen werden beim Erkalten zähflüssig, was Fehlstellen begünstigt. Die entsprechende Gießeigenschaft ist das Formfüllungsvermögen. Manche Formen werden beheizt, um die Differenztemperatur so gering wie möglich zu halten oder es werden Formen mit geringer Wärmeleitfähigkeit verwendet. Dies verlängert allerdings die anschließende Erstarrung. Andere Formen vor allem Dauerformen werden gekühlt, um den Prozess zu beschleunigen und die Temperaturbelastung zu verringern.[27]
Abkühlen und Erstarren der Schmelze
Spätestens nach der vollständigen Formfüllung erkaltet die Schmelze und verringert dabei ihr Volumen, was als (Flüssig-)Schwindung bezeichnet wird. Aus dem Anschnitt und den Speisern muss Schmelze nachfließen, bis sie erstarrt. Während der Erstarrung kommt es infolge des Schrumpfens ebenfalls zu Volumenänderungen. Diese kann nicht mehr durch Speiser ausgeglichen werden. Danach verringert sich das Volumen weiter, bis das Gussstück Raumtemperatur erreicht hat (Festkörperschwindung).
Der genaue Ablauf der Erstarrung und anschließenden Abkühlung hat entscheidenden Einfluss auf die Mikrostruktur und damit auf die Härte und Festigkeit der Gussteile. In der Schmelze sind verschiedene Stoffe gelöst. Da sich die Löslichkeit beim Abkühlen verringert, werden diese Stoffe ausgeschieden. Bei Gusseisen wird beispielsweise Grafit (Kohlenstoff) ausgeschieden. Die Einteilung der Gusseisensorten erfolgt nach der (mikroskopischen) Form des Grafits in Gusseisen mit Lamellengraphit, Gusseisen mit Vermiculargraphit (Würmchengrafit) und Gusseisen mit Kugelgraphit, die sich in ihrer Härte und Festigkeit unterscheiden. Auch gelöste Gase können aus der Schmelze ausgeschieden werden. Wenn sie nicht aus der Form entweichen können, bleiben sie als Poren oder Lunker zurück. Auch die Abkühlgeschwindigkeit hat Einfluss auf die Härte und Festigkeit der Gussteile. Bei langsamem Abkühlen entsteht beispielsweise das gut zu bearbeitende graue Gusseisen, bei schneller Hartguss.[28]
Nachbehandlung
Zur Nachbehandlung zählt das Entformen, bei dem die Gussstücke aus den Formen entnommen werden. Dies kann geschehen, nachdem sie auf Raumtemperatur abgekühlt sind, oder direkt nach dem Erstarren. Vor allem in der Serienfertigung werden die Gussstücke möglichst früh aus den Formen entnommen, da dadurch einerseits die weitere Schrumpfung nicht durch die Form behindert wird und andererseits die Formen für ein erneutes Abgießen schnell wieder zur Verfügung stehen. Bei Dauerformen werden die Gussstücke mit Ausstoßern entfernt, bei verlorenen Formen wird die Form zerstört.[29]
Die weitere Nachbehandlung beinhaltet vor allem das Putzen sowie manchmal noch eine Wärmebehandlung.
Putzen
Das Gussputzen beinhaltet das Abtrennen von Anschnitt und Speißern, Entfernen von Kernen, Entzundern (Brandstellen), Entsanden (Entfernen von Formstoffresten), Ausbessern von Gussfehlern und das Reinigen der Oberfläche. Teilweise werden auch noch Bearbeitungszugaben entfernt. Auf die Putzarbeiten entfällt ein großer Teil der Gesamtkosten in der Gießerei, da es sich nur teilweise automatisieren lässt. Eine putzgerechte Konstruktion des Gussstücks ist daher für die Stückkosten entscheidend.[30]
Wärmebehandlung
Die Wärmebehandlung soll die mechanischen Eigenschaften des Gussteils verbessern. Bei Temperguss (eine Gusseisensorte) zählt sie zum festen Bestandteil (Tempern ist eine Form der Wärmebehandlung). Auch Stahlguss wird üblicherweise geglüht, da das Gussgefüge sehr grobkörnig ist. Bei anderen Werkstoffen kann die Wärmebehandlung auch entfallen.[31]
Gießprozess-Simulation
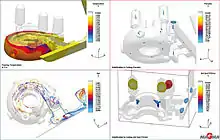
Die Gießprozess-Simulation nutzt numerische Methoden, um den gesamten Gießprozess inklusive Formfüllung, Erstarrung und Abkühlung von Gussteilen vorauszusagen und erlaubt auch die quantitative Vorhersage von mechanischen Eigenschaften, thermischen Spannungen und Verzug der Gussteile. Durch Simulation wird die Qualität eines Gussteils bereits vor dem Produktionsbeginn exakt beschreibbar und die Gießtechnik kann auf die gewünschten Teileeigenschaften ausgerichtet werden. Damit lassen sich nicht nur teure Probeabgüsse in der Entwicklung eliminieren. Die genaue Auslegung des gesamten Gießsystems spart darüber hinaus Energie, Material und Werkzeugkosten.
Software zur Simulation von Gießprozessen unterstützt den Anwender von der Auslegung des Bauteils, der Festlegung der Schmelzpraxis und der Gießtechnik über den Modellbau und die Formherstellung bis hin zur Wärmebehandlung und Nachbearbeitung. Damit können Kosten in der gesamten Fertigungskette konsequent eingespart werden.
Die Gießprozess-Simulation wurde seit den 1970er Jahren zunächst an Hochschulen, insbesondere in Europa und den USA, entwickelt und gilt als bedeutendste Innovation in der Gießereitechnik der letzten 50 Jahre. Seit den späten 1980er Jahren stehen kommerzielle Programme zur Verfügung, die den Gießereien erstmals Einblicke in die Gießtechnik möglich machen, die zuvor eine Blackbox war. Allerdings sind die Optimierung der Geometrie der Gussform und die Ermittlung der richtigen Gusskonfiguration (Material, Temperatur, Zeitdauer des Gießens usw.) relativ komplexe Prozesse, für die nicht durchweg exakte mathematische Modelle zur Verfügung stehen. Daher ist für die Entwicklung von Simulationsmethoden immer noch der Einsatz experimenteller Methoden notwendig.
Ausbildung
Der Arbeitsort heißt Gießerei, der Arbeiter Gießer. Die offiziellen Berufsbezeichnungen[32] sind:
- Gießereimechaniker/in (Ausbildungszeit 3,5 Jahre) in den Spezialisierungen Handformguss, Druck-, Kokillen- und Maschinenformguss.
- Metall- und Glockengießer/in (Ausbildungszeit 3 Jahre) in den Spezialisierungen Kunst-, Glocken-, Metall- und Zinngusstechnik
Trotz maschineller Hilfsmittel werden relativ hohe körperliche Anforderungen an die Gießer und ihre Helfer gestellt.
In Österreich existiert seit dem 1. Juli 2010 der Lehrberuf Gießereitechnik. Dieser ersetzt die Vorgängerlehrberufe Gießereimechaniker, Former und Gießer. Der Lehrberuf Gießereitechnik unterscheidet Eisen- und Stahlguss von Nichteisenmetallguss. Beide Ausbildungen haben eine duale Ausbildungsdauer von vier Jahren. Gießereitechniker mit Schwerpunkt Eisen- und Stahlguss arbeiten in Betrieben des Gießereigewerbes und der Eisen-, Stahl- und Maschinenbauindustrie. Sie stellen Gussteile aus Eisen und Stahl her.[33] Gießereitechniker mit Schwerpunkt Nichteisenmetallguss arbeiten in Betrieben des Gießereigewerbes und der Leichtmetall-, Buntmetallgießereiindustrie und Maschinenbauindustrie. Sie stellen Gussteile aus Nichteisenmetallen und Legierungen, wie z. B. Aluminium, Messing, Bronze, Kupfer her.[34]
Siehe auch
- Gießerei (Zeitschrift)
- Konstruieren + Gießen – Fachzeitschrift
Literatur
- Andreas Bühring-Polaczek, Walter Michaeli, Günter Spur (Hrsg.): Handbuch Urformen, Edition Handbuch der Fertigungstechnik, Hanser, München 2014, ISBN 978-3-446-42035-9.
- Paul Schimpke: Technologie der Maschinenbaustoffe. 17. Auflage. Hirzel, Stuttgart 1968, DNB 458836591.
- Karl Stölzel: Gießerei über Jahrtausende. Deutscher Verlag für Grundstoffindustrie, Leipzig 1978, DNB 800185536.
- Günter Spur, Theodor Stöferle: Handbuch der Fertigungstechnik. Band 1: Urformen. Hanser, München / Wien 1981, ISBN 3-446-12532-9.
- A. Herbert Fritz, Günter Schulze: Fertigungstechnik. Springer, Berlin / Heidelberg 2012, ISBN 978-3-642-29786-1.
- Rolf Roller (Hrsg.): Fachkunde für gießereitechnische Berufe, Technologie des Formens und Gießens. 5., überarbeitete und erweiterte Auflage. Verlag Europa-Lehrmittel Nourney, Vollmer Haan-Gruiten 2007, ISBN 978-3-8085-1795-6.
Weblinks
- Literatur von und über Gießen im Katalog der Deutschen Nationalbibliothek
- Videodokumentation des Gießvorganges von Grauguss (GJL), Sphäroguss (GJS) und Ni-Resist
- „Konstruieren und Gießen“ – Technisches Online-Portal des Bundesverbandes der Deutschen Gießerei-Industrie
- Bundesverband der Deutschen Gießerei-Industrie
- Verein Deutscher Gießereifachleute
- Fachverband der Gießereiindustrie der Wirtschaftskammer Österreich
- Berufs- und Brancheninfos Gießereitechnik – Eisen- und Stahlguss der Wirtschaftskammer Österreich
- Berufs- und Brancheninfos Gießereitechnik – Nichteisenmetallguss der Wirtschaftskammer Österreich
- Wissensfloater: Kaiser-Wilhelm-Standbild - Wissensfloater 42 / Technik-Floater, Bergische Universität Wuppertal auf YouTube, abgerufen am 3. Februar 2021.Anwendung im Bereich der Bildhauerei
Einzelnachweise
- Günter Spur: Vom Wandel der industriellen Welt durch Werkzeugmaschinen. Carl Hanser Verlag, München, Wien 1991, S. 38, 42, 44 f.
-
- Günter Spur: Vom Wandel der industriellen Welt durch Werkzeugmaschinen. Carl Hanser Verlag, München, Wien 1991, S. 51.
- Wolfgang König (Hrsg.): Propyläen Technikgeschichte – Band 3. Propyläen, Berlin 1997, S. 104 f.
- Johann Mehrtens: Der Gießerei-Schachtofen im Aufbau und Betrieb. Berlin 1942, S. 4. Digitales Archiv Springer Books, siehe Google Books.
- Fritz Klocke: Fertigungsverfahren 5 – Gießen, Pulvermetallurgie, Additive Manufacturing, 4. Auflage, Springer, 2015, S. 5 f.
- Alfred Herbert Fritz, Günter Schulze: Fertigungstechnik. 11. Auflage. Springer, 2015, S. 2, 8.
- Andreas Bühring-Polaczek, Walter Michaeli, Günter Spur (Hrsg.): Handbuch Urformen, Hanser, 2014, S. V, 7.
- Heiko Lickfett: Wirtschaftliche Bedeutung der Gießereiindustrie, in: Andreas Bühring-Polaczek, Walter Michaeli, Günter Spur (Hrsg.): Handbuch Urformen, Hanser, 2014, S.
- Die weltweiter Gießerei-Industrie. (PDF; 709 KB) In: get-in-form.de. Hüttenes-Albertus Chemische Werke GmbH, abgerufen am 7. Februar 2017.
- Alfred Herbert Fritz, Günter Schulze: Fertigungstechnik. 11. Auflage. Springer, 2015, S. 4
- Alfred Herbert Fritz, Günter Schulze: Fertigungstechnik. 11. Auflage. Springer, 2015, S. 5.
- Andreal Bühring Polaczek: Technologische und wirtschaftliche Bedeutung in: Andreas Bühring-Polaczek, Walter Michaeli, Günter Spur (Hrsg.): Handbuch Urformen, Hanser, 2014, S. 7–9, 85, 91, 96, 101, 216, 224.
- Fritz Klocke: Fertigungsverfahren 5 – Gießen, Pulvermetallurgie, Additive Manufacturing, 4. Auflage, Springer, 2015, S. 6 f, 9 f.
- Ilschner, Singer: Werkstoffwissenschaften und Fertigungstechnik 5. Auflage, Springer, 2010, S. 455.
- Fritz Klocke: Fertigungsverfahren 5 – Gießen, Pulvermetallurgie, Additive Manufacturing, 4. Auflage, Springer, 2015, S. 4.
- Fritz Klocke: Fertigungsverfahren 5 – Gießen, Pulvermetallurgie, Additive Manufacturing, 4. Auflage, Springer, 2015, S. 20.
- Fritz Klocke: Fertigungsverfahren 5 – Gießen, Pulvermetallurgie, Additive Manufacturing, 4. Auflage, Springer, 2015, S. 13.
- Böge: Handbuch Maschinenbau, Springer, 21. Auflage, S. M1 f.
- Matthias Blünkin: Andreas Bühring-Polaczek, Walter Michaeli, Günter Spur (Hrsg.): Handbuch Urformen, Hanser, 2014, S. 252, 272.
- Hartmut Polzin: Rapit Prototyping mit Formstoffen in: Andreas Bühring-Polaczek, Walter Michaeli, Günter Spur (Hrsg.): Handbuch Urformen, Hanser, 2014, S. 237.
- Böge: Handbuch Maschinenbau, Springer, 21. Auflage, S. M3f.
- in: Andreas Bühring-Polaczek, Walter Michaeli, Günter Spur (Hrsg.): Handbuch Urformen, Hanser, 2014, S. 112.
- Fritz Klocke: Fertigungsverfahren 5 – Gießen, Pulvermetallurgie, Additive Manufacturing, 4. Auflage, Springer, 2015, S. 15.
- Veronika Groten: Technologie des Schmelzens und Gießens in: Andreal Bühring Polaczek: Technologische und wirtschaftliche Bedeutung in: Andreas Bühring-Polaczek, Walter Michaeli, Günter Spur (Hrsg.): Handbuch Urformen, Hanser, 2014, S. 112.
- Eike Wüller, Bin Lao, Benjamin Schelnberger: Schmelzebehandlung in: Andreal Bühring Polaczek: Technologische und wirtschaftliche Bedeutung in: Andreas Bühring-Polaczek, Walter Michaeli, Günter Spur (Hrsg.): Handbuch Urformen, Hanser, 2014, S. 21.
- Fritz Klocke: Fertigungsverfahren 5 – Gießen, Pulvermetallurgie, Additive Manufacturing, 4. Auflage, Springer, 2015, S. 2.
- Roland Kahn: Schmelzetransport und Gießeinrichtung und Dosiertechnik beide in: Andreal Bühring Polaczek: Technologische und wirtschaftliche Bedeutung in: Andreas Bühring-Polaczek, Walter Michaeli, Günter Spur (Hrsg.): Handbuch Urformen, Hanser, 2014, S. 171, 175.
- Veronika Groten: Technologie des Schmelzens und Gießens in: Andreal Bühring Polaczek: Technologische und wirtschaftliche Bedeutung in: Andreas Bühring-Polaczek, Walter Michaeli, Günter Spur (Hrsg.): Handbuch Urformen, Hanser, 2014, S. 13.
- Alfred Herbert Fritz, Günter Schulze: Fertigungstechnik. 11. Auflage. Springer, 2015, S. 18 f.
- Alfred Herbert Fritz, Günter Schulze: Fertigungstechnik. 11. Auflage. Springer, 2015, S. 15.
- Rüdiger Bähr, Stefan Scharf: Gussnachbehandlung und Fertigstellung der Gussteile zum Versnad in: Andreas Bühring-Polaczek, Walter Michaeli, Günter Spur (Hrsg.): Handbuch Urformen, Hanser, 2014, S. 348.
- Andreas Bühring-Polaczek, Walter Michaeli, Günter Spur (Hrsg.): Handbuch Urformen, Hanser, 2014, S. 358.
- Bundesagentur für Arbeit, Berufsbeschreibungen bei BERUFENET
- Berufs- und Brancheninfo: Gießereitechnik – Eisen- und Stahlguss auf der Webseite der Wirtschaftskammer Österreich.
- Berufs- und Brancheninfo: Gießereitechnik – Nichteisenmetallguss auf der Webseite der Wirtschaftskammer Österreich.