Chemiepark Knapsack
Der Chemiepark Knapsack in Hürth-Knapsack (Nordrhein-Westfalen) ist ein in sich geschlossener, zugangsgeschützter Industriepark für die Chemische Industrie. Betreiber des Chemieparks ist seit 1997 die aus der Hoechst AG hervorgegangene YNCORIS GmbH & Co. KG (bis 2019 InfraServ GmbH & Co. Knapsack KG). Die Gesamtfläche des Chemieparks beträgt derzeit 180 ha bzw. 1,8 km².
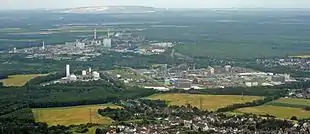
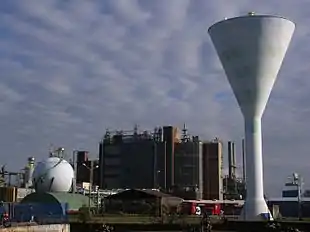
Grund für die Wahl des Standorts war die Nähe zur preiswerten Energie aus Braunkohle im unmittelbar benachbarten Abbaufeld Vereinigte Ville. Den Anfang für den heutigen Chemiepark stellte die 1906 errichtete und 1907 angefahrene Anlage zur Herstellung von Calciumcyanamid (Kalkstickstoff), einem Mineraldünger für die Landwirtschaft, dar. Um sie entwickelte sich eine Reihe weiterer Produktionsstätten mit ständig breiter werdendem Sortiment. Nach dem Zweiten Weltkrieg wurde das Werk auf die Verarbeitung von Phosphor und dessen Folgeprodukten umgestellt; die Phosphorchemie war in dieser Zeit Schwerpunkt des Produktionsprogramms, es umfasste die Herstellung von elementarem Phosphor, Phosphorsäure und ihren Derivaten bis hin zu Produkten für die Waschmittelindustrie sowie Futtermittelzusätzen und Pflanzenschutzmitteln. Seit dem Abbau der Phosphorchemie steht die Chlorchemie und die Kunststoffproduktion (PVC, PE, PP) gemeinsam mit den Pflanzenschutzmitteln im Vordergrund.
Geschichte
Die Keimzelle des heutigen Industriekomplexes entstand durch die Ansiedlung eines Werks zur Herstellung von Calciumcyanamid (Kalkstickstoff), einem Mineraldünger für die Landwirtschaft. Errichtet wurde das Werk durch die am 31. Mai 1906 in Frankfurt am Main von der Metallurgischen Gesellschaft gegründeten Deutschen Carbid Aktiengesellschaft und der Gesellschaft für Stickstoffdünger mbH in Westeregeln, die anfangs auch die Leitung des Werks übernahm. Gründer und erster Aufsichtsratsvorsitzender war der Direktor der Metallurgischen Gesellschaft, Rudolf von Neufville (1867–1937), die Aufbauleitung übernahm Johannes Maruhn, die kaufmännische Leitung Max Bachmann. Obwohl sich die ortsansässige Bevölkerung – vor allem die Landwirte der Region – über das Werk beschwerte, begann im September/Oktober 1906 der Aufbau des Betriebs. Die Anlagen des Unternehmens waren bei Beginn der Produktion 1908[1] weltweit eine der ersten zur industriellen Herstellung von Kalkstickstoff.
Historische Voraussetzungen
Voraussetzung für den Bau einer Fabrik zur Herstellung von Kalkstickstoff war die große Nachfrage nach Düngemitteln zu Beginn des 20. Jahrhunderts. Das bevorzugte Düngemittel war seit etwa 1830 Salpeter, der in großen Mengen in Chile abgebaut und als Chilesalpeter exportiert wurde; bis 1900 ein Drittel davon in das Deutsche Reich.[1] Ende der 1890er Jahre entdeckte der Chemiker Fritz Rothe, dass Calciumcarbid bei etwa 1.100 °C Stickstoff aus der Luft aufnimmt und dabei Calciumcyanamid beziehungsweise Kalkstickstoff entsteht. Das betreffende Patent wurde von Adolph Frank und Nikodem Caro übernommen, die zwar in Berlin die Cyanid-Gesellschaft mbH gründeten, das Verfahren jedoch wegen der dabei benötigten hohen Temperaturen nicht umsetzen konnten. Dies gelang erst durch das 1905 von Ferdinand Eduard Polzeniusz entwickelte Katalysator-Verfahren, das in Knapsack erstmals industriell angewendet wurde.
Vor allem die beabsichtigte Nutzung der in unmittelbarer Nähe anstehenden Braunkohle als preiswertem Energieträger bedingte die Ansiedlung von Industrie in dem im Rheinischen Braunkohlerevier gelegenen Ort Knapsack. Bereits 1901 war die erste Brikettfabrik der Grube Vereinigte Ville zwischen Knapsack und Hürth-Berrenrath errichtet worden, die am 19. Januar 1902 ihren Betrieb aufnahm und der noch vier weitere Fabriken folgten. Jede von ihnen erzeugte nicht nur Prozessdampf für die Kohletrocknung, sondern für den Eigenbedarf auch Strom; dessen Überschuss wurde in das öffentliche Stromnetz abgegeben. Beim Aufbau der Kalkstickstofffabrik schloss die Deutsche Carbid-AG am 3. Oktober 1906 einen Vertrag mit der Betreiberin der Gruben, der Gewerkschaft Roddergrube, um sich die dauerhafte Belieferung mit günstiger Energie zu sichern.
Von der Carbid Aktiengesellschaft zur Aktiengesellschaft für Stickstoffdünger
Der Betrieb des Kalkstickstoffwerkes erfolgte anfangs über drei Retortenöfen, das benötigte Calciumcarbid wurde angekauft und nach einem erst 1905 von Ferdinand Eduard Polzeniusz entwickelten Verfahren in Calciumcyanamid umgewandelt. Das Polzeniusz-Verfahren, später Polzeniusz-Krauss-Verfahren, stellte eine Weiterentwicklung des von Adolph Frank und Nikodem Caro entwickelten Verfahrens zur Umsetzung von Calciumcarbid mit Stickstoff dar, wobei durch den Zusatz von Calciumchlorid als Katalysator die nötige Prozesswärme von etwa 1.100 °C auf 700 bis 800 °C gesenkt werden konnte.

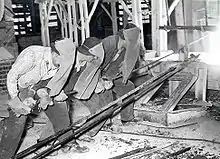
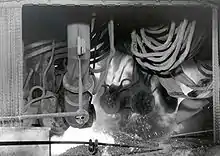
Im Jahr 1908 wurde eine Anlage zur Herstellung von Calciumcarbid sowie ein eigenes Braunkohlekraftwerk aufgebaut, im darauffolgenden Jahr änderte die Deutsche Carbid-AG ihren Namen in Aktiengesellschaft für Stickstoffdünger, Knapsack bei Köln, und übernahm die Leitung des Standorts.[1] Aufgrund der harten Arbeit an den Carbidöfen und des allgemeinen Unmuts über die Ansiedlung des Unternehmens litt es in den Anfangsjahren unter Arbeitskräftemangel und war abhängig von zugewanderten Arbeitskräften aus Bayern, Italien, Kroatien und den Niederlanden. Insbesondere die Bayern schlossen sich zu Vereinen zusammen, sodass sich in Knapsack unter anderem ein Gebirgstrachtenerhaltungsverein Almenrausch gründete.[1]
1910 übernahm Constantin Krauß, der gemeinsam mit Polzeniusz das Polzeniusz-Krauss-Verfahren entwickelte, die Werksleitung in Knapsack. Im Folgejahr 1911 begann das Werk mit der Produktion von Ammoniak und Ammoniumsulfat (ebenfalls als Düngemittel) aus dem Kalkstickstoff, für die es aufgrund von Patentschwierigkeiten mit den Patentinhabern des Frank-Caro-Verfahrens und der Konkurrenz in Westeregeln (bis zur Schließung 1910) massive Absatzschwierigkeiten gab; 1908 konnten von den produzierten 10.000 Jahrestonnen nur 65 Tonnen abgesetzt werden.[1] Bis 1913 verbesserte sich die Situation, und die Produktion für Kalkstickstoff wurde auf ein kontinuierliches Verfahren im ersten selbst entwickelten Kanalofen umgestellt, im selben Jahr wurde das erste eigene Verwaltungsgebäude bezogen. Allerdings kam im selben Jahr auch ernsthafte Konkurrenz für den Kalkstickstoff auf den Markt: Die Chemiker Fritz Haber und Carl Bosch entwickelten für die Badische Anilin- und Sodafabrik (BASF) ein Verfahren zur Herstellung von synthetischem Ammoniak aus Luftstickstoff und Wasserstoff, eine erste großtechnische Anlage zur Herstellung ging 1913 im BASF-Zweigwerk Oppau in Betrieb.
Mit dem Ausbruch des Ersten Weltkriegs 1914 wuchs schlagartig der Bedarf an Düngemitteln und an Schießpulver, das auch aus Kalkstickstoff hergestellt werden konnte, aufgrund einer britischen Blockade der Lieferung von Chilesalpeter – über Ammoniak und Salpetersäure wurden Nitrate produziert, die für die Munitionsherstellung verwendet werden konnten. Die Kriegsrohstoffabteilung des Kaiserreichs wurde zum Großauftraggeber für den Standort, mit einem Darlehen in Höhe von 15 Millionen Goldmark wurde eine neue und moderne Fabrik zur Herstellung von Carbid, Kalkstickstoff und Ammoniak aufgebaut, indem die alte Anlage erweitert und eine neue Anlage mit Kraftwerk und sechs neuen Öfen neu gebaut wurde; die bis dahin nur regional bedeutende Fabrik konnte sich binnen kurzer Zeit auf die fünffache Kapazität vergrößern. In dieser neuen Anlage konnten in 14 Kanalöfen 450 t Kalkstickstoff pro Tag beziehungsweise 150.000 t pro Jahr hergestellt werden. 1915/1916 stellten 40 Autoklaven 55.000 t Ammoniakwasser her und die Stickstoffgewinnung wurde 1916 auf eine neue Anlage zur Luftverflüssigung nach dem Linde-Verfahren umgestellt. Konkurrenz entstand durch den Ausbau von Kapazitäten im BASF-Werk Oppau, die neuen Reichsstickstoffwerke Piesteritz (März 1915), die Oberschlesischen Stickstoffwerke in Königshütte sowie die Inbetriebnahme des BASF-Ammoniakwerks Merseburg (Leuna Werke, April 1917). Die Kriegsführung rechnete 1916 mit einem raschen Ende des Krieges und war an weiterem Kalkstickstoff aus Knapsack nicht mehr interessiert, dem Werk drohte der Konkurs. Die AG für Stickstoffdünger schloss so den Krieg mit einem Verlust von mehreren Millionen Mark ab und litt danach aufgrund der Isolierung durch die Alliierte Rheinlandbesetzung unter Absatzschwierigkeiten.[1]
Entwicklungen von 1918 bis 1945
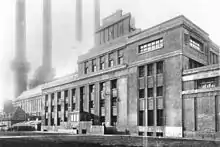
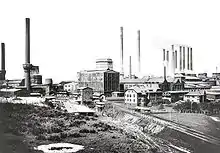
Die Farbwerke vorm. Meister Lucius & Brüning AG, die spätere Hoechst AG, übernahmen die Garantie für den Kredit des Deutschen Reiches und bekamen dafür die Hälfte der Anteile der Aktiengesellschaft für Stickstoffdünger, bis 1919 erwarben sie die Aktienmehrheit und sicherten sich damit die Carbidversorgung für die Produktion von Acetylen, womit der Standort Knapsack als AG für Stickstoffdünger Teil der Farbwerke wurde.
1918 wurden Anlagen zur Produktion von Essigsäure, Aceton und Acetaldehyde in Betrieb genommen, wobei die bereits zur Stickstoffgewinnung genutzte Anlage zur Luftzerlegung auch den für die Essigsäureproduktion notwendigen Sauerstoff lieferte. Im Folgejahr kam es zu ersten Veränderungen im sozialen Bereich: Neben der Werkfeuerwehr wurde eine Beamten- und Arbeiter-Unterstützerkasse gegründet. 1920 wurde die Verwaltung des Unternehmens nach Köln verlegt, eine Reaktion auf das zunehmend schlechter werdende Verhältnis zu den Beschäftigten, das sich nach dem Krieg in Streiks und Arbeiterunruhen äußerte und im Februar 1921 in einem Sympathiestreik für die Chemiearbeiter in Leverkusen entgegen der Zustimmung der Entscheidung des Betriebsrats und der Gewerkschaften eskalierte. Nach einer Vollschließung des Werks für 6 Wochen stellte die Betriebsleitung nur diejenigen ein, „die Ruhe und Ordnung garantierten.“[1]
Am 4. November 1920 schlossen die Braunkohlen- und Brikettwerke Roddergrube AG mit der Rheinisch-Westfälisches Elektrizitätswerk AG einen Betriebsgemeinschaftsvertrag ab, wodurch die Roddergrube zum 1. Januar 1921 in den RWE-Konzern eingegliedert wurde. 1921 wurde durch die Umstellung auf die gemeinsam mit der Elektrokemisk A/S Oslo von Carl Wilhelm Söderberg entwickelte Söderberg-Elektrode die Carbid-Produktion optimiert, 1924 erfolgte die Umstellung auf Dreielektrodenöfen. Über den Kauf des Kalkwerks Gebrüder Wandersleben GmbH in Stromberg im Hunsrück sicherte sich das Werk die Kalkversorgung. 1922 begann das Unternehmen mit der Produktion von Ferrosilicium und baute eine eigene Natrium-Fabrik. Durch die Ruhrbesetzung und die zunehmende Inflation kam es 1923 erneut zu Problemen: Die Rohstoff- und Produktflüsse kamen zum Stillstand, das Werk wurde für sieben Monate stillgelegt und es wurde auf Bestreben der Farbwerke nur mit Notgeld von Bayer in Leverkusen am Leben erhalten. Eine Stabilisierung erfolgte, trotz Verschuldung, erst ab 1924.
Am 2. Dezember 1925 gründete sich die I.G. Farbenindustrie aus den größten Chemieunternehmen Deutschlands, auch Knapsack wurde damit ein Werkstandort des damals größten Chemieunternehmens der Welt. Im selben Jahr wurde die Acetylenherstellung auf eine eigens entwickelte Großtrocknung umgestellt, zudem gründete man am 1. Oktober des Jahres eine von den Angestellten und der Unternehmensleitung gemeinsam finanzierte Pensionskasse. 1926 erfolgte der Beitritt zum Internationalen Carbid-Syndikat, einem Kartell zur internationalen Abstimmung im Bereich der Carbidherstellung, im Folgejahr wurde das Internationale Ferrosilicium-Syndikat mit Beteiligung des Werks Knapsack gegründet. 1928 siedelte sich ein Zweigwerk der Degussa AG im Industriegebiet an,[1] wodurch der Standort Knapsack gemeinsam mit dem Kraftwerk Goldenberg seinen Höhepunkt als Chemieindustrie- und Energiekomplex erreichte.
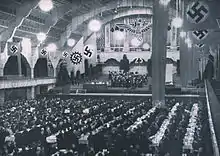
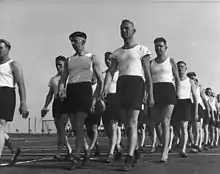
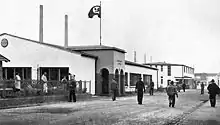
Am 28. Mai 1928 starb der Werksleiter Constantin Krauß nach 18 Jahren Werksleitung. Sein Nachfolger wurde Max Bachmann, der seit der Betriebsgründung die kaufmännische Leitung des Werks und seit 1917 außerordentliches und seit 1922 auch ordentliches Vorstandsmitglied war. 1929 ging der erste Großcarbidofen in Betrieb und steigerte erneut die Produktionskapazität, im selben Jahr wurde eine Anlage zur Herstellung von Aktivkohle gebaut und die 1922 in Betrieb genommene Natriumfabrik wurde geschlossen. Ebenfalls in diesem Jahr übernahm die RWE, die seit 1914 in direkter Nachbarschaft mit dem Kraftwerk Goldenberg das größte Dampfkraftwerk Europas betrieb, die Kraftwerksanlagen des Chemiestandorts, da die Kohlelieferverträge für das Werk ausgelaufen waren. Zur gemeinsamen Abwasserbehandlung gründeten die I.G. Farben, die RWE und die Degussa die Abwasser-Gesellschaft Knapsack GmbH ebenfalls im Jahr 1929. Im Folgejahr begann die Degussa mit der Natriumproduktion in der Nachbarschaft des Chemiewerks.
Mit dem Börsencrash an der New Yorker Börse am 25. Oktober 1929 begann die Weltwirtschaftskrise, in deren Folge der Absatz des Unternehmens auf die Hälfte zurückging und deshalb bis Ende 1932 fast 40 Prozent der Belegschaft entlassen werden musste. 1931 wurde die Essigsäureproduktion durch eine Anlage zur Herstellung von Essigsäureanhydrid ergänzt, das für die Herstellung von Acetatseide gebraucht wurde. Man errichtete im selben Jahr zum einfacheren Transport eine Pipeline für Acetaldehyd zwischen dem Werk Knapsack und dem Rheinhafengelände in Wesseling, wo auch eine Aldehydtankanlage zur Befüllung von Tankschiffen entstand. Zum 25-jährigen Betriebsjubiläum des Standorts wurden eine Branntkalk-Anlage, dank der der bei der Trockenvergasung anfallende Kalk wieder in die Produktion gebracht werden konnte, und ein neuer Kalkstickstoffsilo errichtet.
Nach der Machtergreifung Adolf Hitlers und seiner Ernennung zum Reichskanzler 1933 traten im Mai des Jahres fast alle Führungskräfte des Werks Knapsack geschlossen in die NSDAP ein. Die Oberbeamten unterstellten das Werk vollständig den Vorgaben der nationalsozialistischen Ideologie und passten den Betrieb im Laufe der Folgejahre an die Vorstellungen des Amts für Schönheit der Arbeit an.[1] Im selben Jahr wurde der zweite Großcarbidofen gebaut und in Betrieb genommen. Im Jahr 1934 kam erstmals Kornkalkstickstoff auf den Markt, der in einem Drehofen-Verfahren hergestellt wurde und bessere Eigenschaften für die Ausstreuung hatte. 1935 wurden die Werkszeitung Werks-Nachrichten, eine Sportabteilung, eine Werksbücherei und eine Werksmusikkapelle gegründet, außerdem wurde eine eigene Lehrlingswerkstatt in der 1931 errichteten neuen Hauptwerkstatt eingerichtet. 1936 optimierte man die Produktion von Essigsäureanhydrid und Essigsäure aus Acetaldehyd. 1938 wurden zwei halb gedeckte Carbidöfen in Betrieb genommen, über die als Nebenprodukt Kohlenmonoxid produziert und genutzt werden konnte.
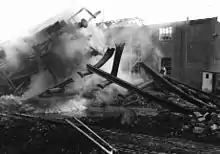
Im Januar 1939 wurde der Betrieb mit dem Leistungsabzeichen für vorbildliche Berufserziehung ausgezeichnet, am 1. Mai erhielt er zudem das Gaudiplom für hervorragende Leistungen. Am 31. Januar des Jahres prallte ein Passagierflugzeug der Air France gegen einen der Schornsteine und stürzte im Werksgelände ab, fünf Flugzeuginsassen starben. Die wirtschaftliche Lage des Unternehmens verbesserte sich in der Zeit des Nationalsozialismus merklich, und zum Zeitpunkt des Kriegsbeginns, Anfang September 1939, beschäftigte die AG für Stickstoffdünger in Knapsack etwa 2000 Mitarbeiter. Im August und Oktober 1940 war das Unternehmen erstmals von Luftangriffen betroffen, und am 12. August 1941 wurden durch einen Tieffliegerangriff mit 24 Sprengbomben eine Reihe von Anlagen beschädigt. Drei Menschen kamen am 23. Juli bei der Explosion der Essigsäure-Anlage infolge eines Angriffs ums Leben, darunter zwei junge Frauen aus der Ukraine, die mit 30 weiteren zur Zwangsarbeit nach Knapsack verschleppt worden waren. Trotz Arbeitskräftemangels und Schwierigkeiten in der Stromversorgung wurde die AG für Stickstoffdünger aufgrund ihrer Leistungen 1943 zum Kriegsmusterbetrieb ernannt. Am 1. Januar 1944 umfasste die Belegschaft insgesamt 2539 Personen, darunter auch 510 Kriegsgefangene. Am 28. Oktober 1944 wurde das Werk Knapsack als Ausweichziel durch einen Luftangriff mit etwa 138 Sprengbomben bei einem Großangriff auf Köln zu etwa 80 Prozent zerstört.
Nachkriegszeit und Aufbau der Phosphorchemie
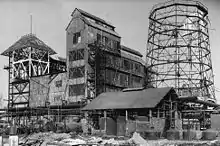
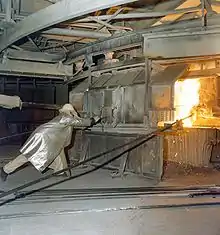
Mit dem Kriegsende 1945 wurde das Werk an die amerikanischen Truppen übergeben, der Wiederaufbau begann noch im selben Jahr. Am 11. Juli 1945 wurde Friedbert Ritter von der britischen Militärregierung als Treuhänder und Geschäftsführer des Werks Knapsack bestellt. Die Produktion von Carbid konnte erst 1945 mit einem Ofen wieder aufgenommen werden und die weiteren Anlagen liefen zum Teil erst einige Jahre später (1946 Essigsäure und Aceton, 1949 Kornkalkstickstoff, 1950 Monochloressigsäure und Ferrosilicium).
1951 kam es zu einer umfassenden Neuordnung der I.G. Farbenindustrie, bei der Aktiengesellschaften für Stickstoffdünger gemeinsam mit der Griesheim-Autogen in Frankfurt, den Nordwestdeutschen Sauerstoffwerken in Düsseldorf, dem Tega Werk, Werk für technische Gase, in Kassel und den Südwestdeutschen Sauerstoffwerken in Stuttgart-Untertürkheim zur Knapsack-Griesheim Aktiengesellschaft für Stickstoffdünger und Autogentechnik zusammengeführt wurden. Dieser Name änderte sich in Knapsack-Griesheim Aktiengesellschaft, Knapsack bei Köln nach der Entlassung aus der alliierten Kontrolle 1952. Durch die im selben Jahr erfolgte Entflechtung der I.G. Farbenindustrie kam die Knapsack-Griesheim AG erneut unter die Führung der Farbwerke Hoechst AG, neuer Aufsichtsratsvorsitzender wurde der Vorstandsvorsitzende der Hoechst AG Karl Winnacker. In der Produktion wurde in diesem Jahr die Herstellung von Essigsäure eingestellt und die Aceton-Anlage auf den Rohstoff Isopropanol umgestellt[2]. Im Rheinhafen Köln-Godorf errichtete das Unternehmen zudem sechs Phosphaterz-Silozellen, die den Einstieg in die Phosphorchemie im Folgejahr einleiteten. Dieser vollzog sich durch den Start der Produktion von elementarem Phosphor in einem Phosphorofen mit einer Maximalleistung von 18 MW, thermischer Phosphorsäure, rotem Phosphor und Acetylenruß, zudem wurde eine neue Brech-, Mahl und Sortier-Anlage für die Carbidaufbereitung in Betrieb genommen. 1954 begann die Produktion von Vinylchlorid durch die Nutzung des am Standort produzierten Acetylen und Ferrosilicium, zudem wurde eine Versuchsanlage zur Herstellung von Magnesium in Betrieb genommen, jedoch im selben Jahr wieder stillgelegt.
1956 begann die Produktion von Pentanatriumtriphosphat (NTPP), das als Wasserenthärter in damaligen Waschmitteln eingesetzt wurde, sowie von Tetranatriumpyrophosphat. Zudem wurde in dem Jahr ein weiterer Phosphorofen in Betrieb genommen sowie das Feierabendhaus des Architekten Karl Hell eingeweiht. 1957 ergänzte man mit der Produktion von Chloropren und Acrylnitril weitere Produkte im Portfolio des Standorts. Hugo Querengässer wurde ständiger Vertreter des zu diesem Zeitpunkt wahrscheinlich als Werksleiter agierenden Georg Janning, er selbst wurde 1961 Werksleiter während Janning zum Vorsitzenden der Knapsack Griesheim AG aufstieg, die seit 1958 in eine Betriebsführungsgesellschaft der Farbwerke Hoechst AG umgewandelt worden war. Im selben Jahr wurde mit dem Carbidofen 20 der weltgrößte Carbidofen mit einer Kapazität von 160.000 Jahrestonnen am Standort in Betrieb genommen; der erste geschlossene Ofen dieser Art lief 1955 an.
Weitere Ausdehnung in Knapsack und Hürth
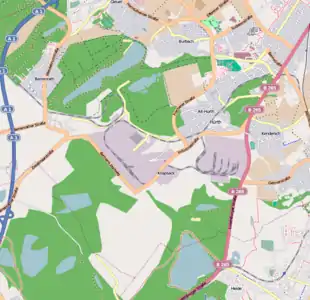
Im Jahr 1960 wurde der Standort Knapsack durch den Werksteil Hürth als zweiter großer Fläche für Industrieanlagen ergänzt. Der Werksteil wurde in einem verfüllten Teil des Braunkohle-Tagebaus Hürtherberg errichtet, der der gleichnamigen Gewerkschaft abgekauft worden war. Dazu waren umfangreiche Gründungsmaßnahmen notwendig. Als erste Anlage auf diesem Gelände startete die Produktion von Chlor durch eine Chloralkalielektrolyse. Das dazu nötige Steinsalz wurde auf einem Werksbahnanschlussgleis von der HGK-Strecke vom Hafen Wesseling herangeführt. Die Acetaldehyproduktion wurde 1961 auf das Wacker-Hoechst-Verfahren umgestellt, das als Rohstoff Ethylen aus Erdöl verwendet. 1963 begann im Werksteil Hürth auch die Produktion von Acetaldehyd, während im selben Jahr ein weiterer Phosphorofen die Mengenleistung in der Phosphorherstellung steigerte und eine neue Anlage für die Produktion von Phosphorpentasulfid in Betrieb genommen wurde. Im Jahr darauf wurde auch die Vinylchloridproduktion auf Ethylenbasis umgestellt, zugleich die Kapazität von NTPP weiter erhöht, dagegen wurde die Herstellung von Aceton und Explosionsruß eingestellt und der Betrieb des letzten offenen Carbidofens eingestellt.
Am 1. Januar 1965 erfolgte die Umfirmierung in die Knapsack Aktiengesellschaft. Die Werksgruppen Sauerstoff und Griesheim Autogen schlossen sich im selben Jahr mit der Adolf Messer GmbH zur Messer Griesheim GmbH zusammen. Diese gründete mit der Krems-Chemie GmbH in Krems an der Donau die Krems-Knapsack Phosphorprodukte GmbH zur Herstellung von Phosphorprodukten für Österreich und Südeuropa. Der Ausbau in den folgenden Jahren führte zu einer Reihe weiterer Produkte und Vergrößerungen der Kapazitäten, vor allem in der Phosphorchemie. So wurde 1965 die Chloropren-Kapazität verdoppelt und mit der Produktion des Zahnpasta-Zusatzstoffes Dicalciumphosphat sowie dem Waschmittelphosphat Thermphos NW begonnen. 1966 wurden im Werksteil Hürth eine Anlage zur Herstellung von Phosphorsäure im Nassverfahren, eine Anlage zur Herstellung des Futterzusatzstoffes Hostaphos, eine Polyvinylchlorid-Anlage (PVC) und eine zentrale Abwasserbehandlungsanlage in Betrieb genommen, während die Phosphorproduktion auf 80.000 Tonnen pro Jahr anstieg und auch die Kapazitäten der Chloralkalielektrolyse erhöht wurde.
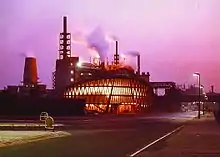
Am 13. November 1967 kam es zu einer großen Explosion in einem Phosphorofen, bei der fünf Arbeiter ums Leben kamen. Die Ursache für diesen Unfall war ein Wassereinbruch in den Ofen. Im selben Jahr wurde eine Anlage zur Herstellung von Elektrolyt-Braunstein in Betrieb genommen, außerdem gründete sich die Benckiser Knapsack GmbH, an der die Johann Anton Benckiser GmbH beteiligt war. In diesem Unternehmen wurde das gesamte Phosphatgeschäft Benckisers mit Ausnahme des Bereichs Reinigungsmittel mit einem Teil der Phosphatbereiche von Hoechst zusammengeführt. 1968 wurde die Produktion von Vinylchlorid auf der Basis von Acetylen aufgenommen, und eine neue Anlage zur Produktion von Phosphorpentasulfid im Werksteil Hürth ersetzte die Anlage in Knapsack. Durch die Fertigstellung und Inbetriebnahme einer eigenen Ethylenpipeline zwischen Wesseling und Kelsterbach konnte das Leitungsnetz Höchst–Knapsack mit Frankfurt-Höchst verbunden werden. Zeitgleich wurde in Vlissingen in den Niederlanden der erste 60 MW-Phosphorofen nach Knapsacker Modell in Betrieb genommen. Ein Jahr später wurde in Hürth eine Anlage zur Herstellung von Dichlorethan aus Chlor und Ethylen angefahren.
1970 übernahm Hellmut Gäbler die Leitung des Werks, dessen Belegschaft inzwischen auf etwa 5.000 Mitarbeiter angewachsen war. Die Produktion von Acrylnitrit und Blausäure am Standort wurde eingestellt, zugleich wurden die Kapazitäten für Monochloressigsäure und Vinylchlorid erhöht und eine Phosphorpentasulfidanlage im Werksteil Hürth gebaut. Mit der Inbetriebnahme einer Anlage zur Herstellung von Polyethylen (HDPE, Niederdruck-Polyethylen) wurden im selben Jahr auch erstmals Polyolefine in Knapsack produziert. Im Folgejahr wurde die Produktion des ältesten Knapsackprodukts, des Kalkstickstoffs, eingestellt und zwei große Carbidöfen stillgelegt; das Düngemittel wurde in der Landwirtschaft durch neue Düngemittel ersetzt. Auch Vinylacetat wurde nicht länger hergestellt, stattdessen wurde eine Anlage zur Gewinnung von Phosphorzwischenprodukten in Betrieb genommen und die PVC-Herstellung durch eine weitere Produktionsstraße erweitert. 1973 folgte eine Anlage von Hostalit H und Chlorhostalen, zudem wurde die Produktion von Gipswandbauplatten begonnen, um den beim Nassaufschluss von Phosphaterzen anfallenden Gips zu nutzen. Mit der schwedischen Boliden Aktiebolag gründeten die Farbwerke Hoechst in Knapsack die Boliden-Knapsack GmbH, um Fällsalze zur Phosphatfällung aus Abwässern zu vertreiben.
1974 wurde die letzte Anlage zur Herstellung von Vinylchlorid aus Acetylen stillgelegt, wodurch der gesamte Bereich der Acetylenchemie geschlossen wurde, während die Produktion von Ethylen durch die Inbetriebnahme einer Anlage zur Oxychlorierung fokussiert wurde. Im selben Jahr wurde die Knapsack Aktiengesellschaft aufgelöst und der Standort rechtlich zum Werk Knapsack der Hoechst AG umgewandelt.
Hoechst Aktiengesellschaft, Werk Knapsack
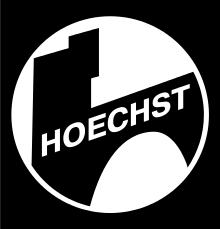
Mit der Umwandlung zum Werk Knapsack wurde der bisherige Werksleiter Hellmut Gäbler Leiter des Geschäftsbereichs Anorganische Chemikalien der Hoechst AG, während Max-Rudolf Buchmann 1975 neuer Werksleiter in Knapsack wurde. Im Folgejahr 1976 wurde die Produktionspalette im Werksteil Hürth durch den Start der Produktion des Flammschutzmittels Ammoniumpolyphosphat und von Azopigment-Farben (Hansa-Gelb) weiter ausgebaut. Zudem wurde die Polyethylen-Anlage auf die Produktion von Polypropylen umgerüstet und ein Entschwefelungsgemisch für Stahlschmelzen auf Carbidbasis entwickelt. 1977 wurde mit der Herstellung des Insektizids Triazophos (Hostathion) das erste Pflanzenschutzmittel in das Portfolio aufgenommen, 1978 wurde die Anlage um das Fungizid Carbendazim (Derosal) erweitert, und 1979 folgte auf einer weiteren Produktionsanlage das Herbizid Diclofop-methyl (Illoxan),[3] das selektiv gegen Flughafer eingesetzt wird. Auch die Azopigment-Palette wurde 1978 erweitert durch die Produktion von Hansa-Rot und Hansa-Scharlach, und mit einer Phoban-Anlage (Phosphabicyclononan) begann die Produktion von Phosphor-Spezialchemikalien auf der Basis von Phosphorwasserstoff. Mit dem Methyldichlorphosphan (MPC), welches aus Methan und Phosphortrichlorid gewonnen wird, wurde 1979 zudem ein neues Basisprodukt entwickelt.
1980 wurde erstmals Pyrazophos (Afugan), ein weiteres Fungizid, hergestellt, gleichzeitig wurde die PE-HD-Herstellung nach einjähriger Unterbrechung wieder aufgenommen. 1981 wurden Vinylmethylacetamin (VIMA) und auf der Basis von Rohphosphorsäure Extraktionsphosphorsäure nach einem in Knapsack entwickelten Verfahren produziert. 1982 konnte das Gelände des Werks durch die Einbeziehung des ehemaligen Bahnhofs Knapsack erweitert werden. Der Phosphorofen 1 sowie die Herstellung von Dithiophosphorsäureester wurden 1981 und die Herstellung von Gipswandbauplatten 1983 aus wirtschaftlichen Gründen eingestellt, während in den Jahren bis 1986 vor allem die Produktion von Hostaphos, Dicalciumphosphat, Illoxan, Polypropylen, Essigsäure, Phosphor-rot und Braunstein teilweise stark ausgebaut wurde. 1985 wurde im kleinen Maßstab mit der Produktion von Phosphonoessigsäureethylester als Hilfsstoff zur Polyesterfaser-Herstellung begonnen, und 1986 wurde die Produktion der Vorprodukte für das Pflanzenschutzmittel Glufosinat (Basta) von Methanphosphonigsäurechlorid (MPC) über Methanphosphoniger Säure (MPS) zu Methanphosphonigsäureester (1987, MPE) gestartet. Die Herstellung des Futtermittels Hostaphos und des Lösemittels Pyranton-A wurden eingestellt.
Am 29. Juni 1987 kam es zu einem Großbrand, der die Phosphorsäureextraktionsanlage zerstörte, bei dem jedoch keine Menschen zu Schaden kamen. Im Juni 1990 wurde mit der Abstellung des letzten Carbidofens (Ofen 10) sowie sämtlicher Anlagen zur Weiterverarbeitung die Herstellung von Carbid nach 82 Jahren eingestellt. 1991 wurde eine Masse-Polypropylen-Anlage mit einer Kapazität von 160.000 Jahrestonnen in Betrieb genommen, im selben Jahr errichtete die Spedition Karl Schmidt GmbH aus Heilbronn eine mit der PP-Anlage verbundene Siloanlage, wodurch erstmals die Herstellung und die Verteilung eines Produktes durch zwei unterschiedliche Unternehmen stattfand. Für die brennbaren Pflanzenschutzmittel wurde zudem ein modernes Pflanzenschutzmittellager eingerichtet, und die Abwasserbehandlungsanlage erhielt einen 6.000 Kubikmeter fassenden Abwasserrückhaltebehälter.
In den folgenden Jahren wurden viele Produktionsanlagen zurückgefahren und abgestellt. So wurden 1995 die seit 25 Jahren laufende Nass-Phosphorsäure-Anlage, die seit über 35 Jahren laufende Produktion des Waschmittelzusatzes Thermphos (NTPP) und die Phoban-Produktion eingestellt, außerdem wurden die stillgelegten Carbidanlagen, der gesamte Kalk- und Koksbetrieb sowie das 1917 aufgebaute Kraftwerk abgerissen. 1992 folgte die Einstellung der Phosphorproduktion mit der Stilllegung des letzten Phosphorofens und der Phosphor-Sinteranlage. Im selben Jahr gingen eine Recycling-Anlage für gebrauchtes, sortenreines Polypropylen mit einer Kapazität von 5000 Jahrestonnen sowie zwei Granulierstrecken zur Herstellung von PP-Compounds in Betrieb. Nachdem Max-Rudolf Buchmann 1993 nach 18 Jahren als Werksleiter in den Ruhestand ging, wurde als sein Nachfolger Horst-Dieter Schüddemage berufen. Die als Joint Venture von Wacker und Hoechst gegründete Vinnolit GmbH übernahm den PVC-Betrieb im Werksteil Hürth. Im Dezember 1993 wurden die Ferrosilizium-Produktion und die werkseigene Luftzerlegungsanlage eingestellt. Am 1. Januar 1994 gingen die Produktionsanlagen für Pflanzenschutzmittel an die Hoechst Schering Agrevo GmbH, die ebenfalls als Joint Venture zu 60 % von der Hoechst AG und zu 40 % von der Schering AG gebildet wurde. Ab dem 1. Februar trat eine über mehrere Jahre diskutierte Neustrukturierung der Hoechst AG ein, die das Unternehmen in verschiedene Geschäftsbereiche (Business Units) aufteilte und damit den Strukturwandel zum offenen Chemiepark einleitete. Noch im selben Jahr wurden die Chlorhostalen-, die Hostaphos und die Braunsteinanlage im Werksteil Hürth demontiert und die Reste der Carbid- und Acetylenanlagen sowie der Kamin des Kraftwerks abgerissen. 1995 wurden auch die Dicalciumphosphat-Anlage und die Phosphorreinigung stillgelegt sowie die bereits stillgelegten Anlagen für Phoban, Ferrosilicium, Elektrodenmasse und Nass-Phosphorsäure abgerissen, 1996 folgte der Abriss der Phosphoröfen und der Phosphatsinteranlage.
1996 wurden vor allem die Polypropylenkapazitäten erhöht und Silafluofen[4] und Formetanat[5] zum Portfolio der Pflanzenschutzmittel der AgrEvo ergänzt.
Umwandlung zum Chemiepark Knapsack
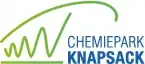
Mit der Umgestaltung der Hoechst AG zur Strategischen Management-Holding 1997 wurde das Werk Knapsack in einen Chemiepark umgewandelt, wobei die verschiedenen operativen Geschäftsbereiche der Hoechst AG in selbstständige Unternehmen überführt wurden. So gingen am 1. Juli des Jahres die Polypropylen-Produktion an die Targor GmbH, einem Joint Venture der Hoechst AG mit der BASF, und die Polyethylen-Produktion an die Hostalen Polyethylen GmbH. Die Spezialchemikalien wurden von der schweizerischen Clariant übernommen, die Chemikalienproduktion gliederte Hoechst in die Celanese GmbH aus. Als Betreibergesellschaft für den Chemiepark wurde die InfraServ GmbH & Co. Knapsack KG (heute YNCORIS) als Servicegesellschaft der Hoechst AG gegründet. Geschäftsführende Gesellschafterin von InfraServ Knapsack wurde die InfraServ Verwaltungs-GmbH in Frankfurt am Main als 100%ige Tochter der Hoechst AG, Kommanditisten in Knapsack waren bei Gründung die Targor GmbH (34 %), die Hoechst AG (22 %), die Celanese GmbH (20 %), die Clariant GmbH (21 %) und die Hostalen Polyethylen GmbH (3 %). Die InfraServ bekam von Hoechst die gesamten Grundstücke sowie die allgemeinen Werksgebäude übertragen. Im Zuge der Fusion von Hoechst und Rhone-Poulenc zur Aventis 1999 übertrug die Hoechst AG ihre Anteile an InfraServ auf die Celanese AG. Die InfraServ Verwaltungs-GmbH wurde damit 100%ige Tochter der Celanese AG, die nach ihrer Abspaltung von Hoechst zudem die Bereiche der industriellen Chemie der Hoechst AG und die Anteile an der Targor GmbH und der Vinnolit Kunststoff GmbH übernahm.[6]
1998 wurde die Pentasulfid-Produktion aus der Celanese GmbH ausgegliedert und in die Thermphos GmbH überführt, die die deutsche Niederlassung der Thermphos International BV darstellt. Die nun zur Targor GmbH gehörende Suspensionspolypropylen-Anlage wurde im selben Jahr stillgelegt, während zugleich die Massepolypropylen-Anlage optimiert und in ihrer Kapazität aufgestockt wurde. 1999 wurde die Hostalen Polyethylen GmbH von der Elenac GmbH, einem Joint Venture von BASF und Shell, übernommen. Diese wiederum verschmolz im Jahr 2000 mit der Targor GmbH und der Montell GmbH (einer Shell-Tochter) zur Basell Polyolefine GmbH, die heute Teil der LyondellBasell Industries AF S.C.A. ist. Die anorganischen Produktionen der Celanese (Salzelektrolyse, Direktchlorierung, Oxichlorierung und Dichlorethan-Spaltung) wurden 1999 als Vintron GmbH in Knapsack ausgegliedert.
Im Jahr 2000 erweiterte Vinnolit die PVC-Produktion am Standort durch eine neue Vinylchlorid-Verflüssigungs-Einheit und neue Großkessel auf 150.000 t PVC/a. Im Juli desselben Jahres wurde die Vinnolit GmbH gemeinsam mit der Vintron GmbH an die Advent International verkauft,[7] 2003 wurde Vintron Teil von Vinnolit.[8] Vinnolit begann 2000 mit dem Bau einer neuen Produktionsanlage für Vinylchlorid mit integrierter Oxichlorierung für eine Kapazität von 330.000 Tonnen Vinylchlorid pro Jahr und einer Erweiterung der Chloralkalielektrolyse auf 250.000 Tonnen pro Jahr.
Im Jahr 2001 wurden die ersten Pläne zum Bau eines neuen Kraftwerks am Standort, des GuD-Kraftwerks, durch die InterGen vorgestellt, außerdem wurde mit dem Bau des neuen Containerterminals im Werksteil Hürth begonnen, das im Januar 2002 seinen Betrieb aufnahm. Weitere Neuerungen wurden eingeführt, darunter die „Abendakademie“ für die betriebliche Weiterbildung, die erste „Hausmesse“ im Feierabendhaus und die Umstellung des Betriebsrestaurants auf ein neues, kundenorientierteres Konzept. In der Nachbarschaft wurde zu diesem Zeitpunkt mit dem Bau einer Papierfabrik der „Rhein Papier GmbH“, einer Tochter der Myllykoski Corporation, begonnen, mit der bis heute enge Kooperationen bestehen.
2002 übernahm die Bayer AG mit der Bayer CropScience weltweit die Pflanzenschutzmittelproduktion der Aventis, darunter auch die Produktionsanlagen am Standort Hürth. Die Essigsäureanhydrid-Anlage wurde abgebaut[9] und für das GuD-Kraftwerk wurde die Baugenehmigung erteilt. Auch technisch kam es zu Neuerungen, so wurde im Oktober 2002 ein neues Server-Zentrum der InfraServ in Betrieb genommen. Im April des Jahres wurde eine neue Vinylchlorid-Anlage der Vinnolit GmbH in Knapsack eingeweiht, die mit 130 Millionen Euro von Advent International finanziert wurde,[10] 2004 erfolgten Erhöhungen der Kapazitäten in der Direktchlorierung und der Vinylchloridproduktion sowie in der Herstellung von PVC im Suspensions-Verfahren.[11]
2003 übernahm die Clariant Acetyl Building Blocks GmbH, heute CABB GmbH, als Tochtergesellschaft der Clariant den Bereich der chlororganischen Chemie. Clariant selber begann mit dem Bau einer Depal-Anlage, in der das Aluminiumsalz der Diethylphosphinsäure, ein Flammschutzmittel für Kunststoffe, hergestellt werden soll. Basell stellte den Betrieb der letzten SPP-Granulierstrecken ein. Die InfraServ gründete in diesem Jahr mit der Personal-Transfair GmbH und der Rhein-Erft-Akademie zwei neue Tochtergesellschaften am Standort, außerdem reichte sie die Genehmigungsunterlagen für ein neues Ersatzbrennstoffkraftwerk ein. Als kleinstes produzierendes Unternehmen stellte die Nexans die bislang weltweit leistungsstärkste Komponente für supraleitende Strombegrenzer vor.
2004 wurde die neue Depal-Anlage von Clariant fertiggestellt und begann im Oktober ihren Produktionsbetrieb, gleichzeitig kündigte das Unternehmen die Schließung der Produktionseinrichtungen für Azo-Farbstoffe für 2005 an. Auch Basell gab bekannt, Produktionseinrichtungen abzustellen, in ihrem Fall die HDPE-Anlage, die ebenfalls 2005 eingemottet, während die APO-Anlage weiter ausgebaut werden sollte. Vinnolit setzte auf den Ausbau der Chlorchemie, der mit einer Investition von 30 Mio. Euro erfolgen sollte. Für eine Produktionshalle für Nexans investierte die InfraServ 300.000 Euro im selben Jahr. InterGen schloss als Investor für das im Bau befindliche GuD-Kraftwerk einen Netznutzungsvertrag mit der RWE ab und sah sich für die weitere Realisierung nach einem Käufer um, den sie 2005 in dem norwegischen Energieunternehmen Statkraft fand. Diese startete den Bau des Kraftwerks offiziell am 30. Juni des Jahres und legte den Grundstein für das am 17. Oktober 2007 in Betrieb genommene und derzeit größte Gas- und Dampf-Kraftwerk (800 Megawatt) in Deutschland am 22. November.
Ebenfalls 2005 verkauften BASF und Shell ihr gemeinsames Tochterunternehmen Basell an ein Konsortium um den amerikanischen Milliardär Leonard Blavatnik. Das Unternehmen stellte wie angekündigt die Produktion von HDPE zum 31. Mai ein, während die Produktion des Katalysators noch einige Wochen weiterlief. Clariant verkaufte die Clariant Acetyl Building Blocks GmbH & Co. KG (CABB) an den Niederländer Gilde Buy-Out Fund und stellte den Azo-Betrieb zum Ende des Jahres ein, 2007 übernahm die AXA Private Equity Group die Mehrheit der Anteile. Mit dem Wasserstoffanwendungszentrum der InteressenGemeinschaft Wasserstoff (IGH2), die am 16. Januar 2007 in den Verein HyCologne – Wasserstoff Region Rheinland e. V. überging,[12] wurde zum ersten Mal im Chemiepark Wasserstoff energetisch genutzt. Ab dem 1. November übernahm Helmut Weihers die Geschäftsführung der InfraServ Knapsack nachdem Horst Dieter Schüddemage in den Ruhestand gegangen war.
In den Folgejahren wurde versucht, neue Unternehmen an den Standort zu binden. So bezog 2006 Sopack die ehemalige Azo-Lagerhalle und vermietete Lagerplätze für Industriemaschinen. Sopack ist Teil der Lintermann-Unternehmensgruppe an, zu der auch die bereits am Standort tätigen Unternehmen Imotech Engineering GmbH (Stahl- und Rohrleitungsbau) und Jägers GmbH & Co. KG (Personaldienstleistungen) gehören. Im Mai des Jahres kam zudem die Spedition Kube & Kubenz nach Knapsack. Im Juli begannen die Planungen für den Bau eines EBS-Kraftwerks der InfraServ gemeinsam mit der Sotec GmbH, für das 105 Millionen Euro investiert werden sollten; die Bauarbeiten begannen im September des Jahres und bereits im Mai 2007 konnte das Richtfest gefeiert werden. Zum Ende des Jahres schloss Clariant die SKS-6-Anlage, da das Produkt (Schichtsilikat als Waschmittelrohstoff) nicht mehr gefragt war. Für das Strukturförderprogramm Regionale-2010-Projekt beteiligte sich die Stadt Hürth gemeinsam mit InfraServ und der RWE unter dem Titel „Energie- und Chemie-Centrum Knapsack“ (ECC) an dem regionalen Strukturförderprogramm in NRW.
Im August 2007 wurde das 100-jährige Jubiläum des Chemieparks begangen. Das EBS-Kraftwerk nahm unter dem Dach der neu gegründeten EBS Kraftwerk GmbH, einem Gemeinschaftsunternehmen der E.ON Energy from Waste AG und der InfraServ Knapsack, am 25. März 2009 offiziell den Betrieb auf; es produziert eine elektrische Leistung von 33 Megawatt und bis zu 1,2 Millionen Tonnen Prozessdampf, die jährlich zur Wärmeversorgung des Chemieparks bereitgestellt werden. Die Jahresverwertungskapazität beträgt 240.000 Tonnen Ersatzbrennstoffe. 2009 legte Statkraft zudem Pläne vor, nach denen der Bau eines weiteren kleineren GuD-Kraftwerks am Standort geprüft wurde. Nach 2 Jahren Bauzeit wurde im Juni 2013 dieses zweite GuD-Kraftwerk "Knapsack II" eröffnet.
Betreiberunternehmen und Werksleitung
Seit der Gründung des heutigen Chemieparks Knapsack als Unternehmen zur Herstellung von Kalkstickstoff änderten sich die Betreiberunternehmen mehrfach. Insbesondere zur Anfangszeit und nach dem Zweiten Weltkrieg wurden dabei die Benennung und die Leitung mehrfach verändert:[13]
Bezeichnung | Ort | Dauer | Werksleiter | Besonderheiten |
---|---|---|---|---|
Gesellschaft für Stickstoffdünger GmbH | Westeregeln | Baubeginn 1906 bis März 1909 | 1908–1909: Johannes Maruhn | Werksleitung wurde parallel mit der Deutschen Carbid-Aktiengesellschaft bis 1909 betrieben. Maruhn war erster Werksleiter während des Aufbaus des Standorts durch die Gesellschaft für Stickstoffdünger GmbH in Westeregeln, deren Direktor er seit 1904 war. |
Deutsche Carbid-Aktiengesellschaft | Frankfurt am Main | 31. Mai 1906 bis März 1909 | 1908–1909: Johannes Maruhn | Werksleitung wurde parallel mit der Gesellschaft für Stickstoffdünger GmbH vom Baubeginn bis 1909 betrieben. |
Aktien-Gesellschaft für Stickstoffdünger in Knapsack | Bezirk Köln am Rhein | 1909 bis 1. Oktober 1951 | 1909–1910: Johannes Maruhn 1910–1928: Constantin Krauß (1864–1928) 1928–1946: Max Bachmann (1881–1954) 1946–1951: Friedbert Ritter (1900–1981) | Ab 1916 gehörten 50 % der Aktien den Farbwerken vorm. Meister Lucius & Brüning AG, der späteren Hoechst AG, bis 1919 erwarben sie die Aktienmehrheit und übernahmen den Betrieb. Ab 1925 wurde die AG Teil der I.G. Farbenindustrie. Krauss wurde Werksleiter der Anlagen zur Herstellung von Kalkstickstoff und war hier maßgeblich an der Verbesserung des Produktionsverfahrens beteiligt (Polzeniusz-Krauß-Verfahren). Sein Nachfolger Bachmann war bereits während des Aufbaus mit Assistenz und kaufmännischer Leitung beauftragt und übernahm 1910 die Gesamtleitung der Unternehmung. Nach der nationalsozialistischen Machtergreifung brachte er Knapsack auf die herrschende ideologische Linie und baute den Betrieb zum „Kriegsmusterbetrieb“ aus. Nach seinem – wahrscheinlich unter Druck der Alliierten – erfolgten Ruhestand blieb er bis 1952 im Vorstand der Knapsack-Griesheim AG. Als Treuhänder wurde Ritter durch die britischen Besatzer eingesetzt; es erfolgte der Ausbau Knapsacks zum Phosphor-Standort sowie die Umstrukturierung des Werks und Gründung der Knapsack-Griesheim AG. |
Knapsack-Griesheim Aktiengesellschaft für Stickstoffdünger und Autogentechnik | U.S.-Administration Knapsack Bezirk Köln | 1. Oktober 1951 bis 26. September 1952 | 1951–1952: Friedbert Ritter (1900–1981) | |
Knapsack-Griesheim Aktiengesellschaft | Knapsack bei Köln | 26. September 1952 bis 1. Januar 1965 | 1951–1961(?): Friedbert Ritter evtl. bis 1961: Georg Janning (1918–1992) 1961–1965: Hugo Querengässer | Nach der Umstrukturierung wurde Ritter wahrscheinlich von Janning ersetzt, aufgrund der Quellenlage ist allerdings unklar, ob er überhaupt Werksleiter war; 1961 wurde er Nachfolger von Ritter als Vorstandsvorsitzender der Knapsack-Griesheim AG, im gleichen Jahr wurde Querengässer Werksleiter in Knapsack. |
Knapsack Aktiengesellschaft | Hürth | 1. Januar 1965 bis 10. Juli 1974 | 1965–1966: Hugo Querengässer 1966–1970: Günther Breil 1970–1974: Hellmut Gäbler (1922–2012) | Als Nachfolger in der Werksleitung wurden 1966 Breil und 1970 Gäbler eingesetzt, der 1953 in die organische Entwicklung der Knapsack-Griesheim AG eingetreten war und unter dessen Leitung 1974 der Standort zum Werk Knapsack der Hoechst AG wurde, er war dann ab 1975 Leiter des Geschäftsbereichs A der Hoechst AG, Frankfurt. |
Hoechst AG, Werk Knapsack | Hürth | 10. Juli 1974 bis 31. Dezember 1997 | 1974–1975: Hellmut Gäbler 1975–1993: Max-Rudolf Buchmann (* 1928) 1993–1997: Horst-Dieter Schüddemage (* 1941) | Buchmann war seit 1974 Direktor im Werk Knapsack, ab 1975 löste er Gäbler als Werksleiter ab. Schüddemage war Werksleiter während der Auflösung der Hoechst AG 1994 und begleitete bis 1997 die Umwandlung des Standorts Knapsack in einen offenen Chemiepark unter der Leitung der InfraServ Knapsack |
Chemiepark Knapsack | Hürth | seit 1. Januar 1998 | 1997–2005: Horst-Dieter Schüddemage 2005 bis 2012: Helmut Weihers seit 2013 Ralf Müller und Clemens Mittelviefhaus | Leitung durch die InfraServ GmbH Knapsack & Co. KG seit 1. Januar 1998, zeitweise bis zu 25 Einzelunternehmen am Standort. Schüddemage war von 1997 bis 2005 Geschäftsführer von InfraServ Knapsack, 2005 wurde er durch Helmut Weihers abgelöst, der seit 2003 Chief Operating Officer (COO) war. Seit dem 1. Januar 2013 übernehmen Ralf Müller (Vorsitzender) und Clemens Mittelviefhaus die Geschäftsleitung. 2019 wurde die InfraServ Knapsack umbenannt in die YNCORIS GmbH & Co. KG. |
Umweltprobleme und Umweltschutz
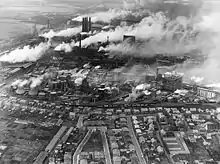
Das Thema Umweltverschmutzung und Umweltschutz spielte in Knapsack von Beginn an eine zentrale Rolle. Bereits vor dem Aufbau der Kalkstickstoff- und Carbidanlagen wurden die Betreiber mit Forderungen und Beschwerden der Anwohner des dörflichen Knapsack konfrontiert, die Schädigungen ihrer Felder durch die Ausdünstungen der Fabrik und einen Wertverfall für ihre Grundstücke befürchteten. Nach einer Besichtigung der Anlage in Westeregeln garantierte der zuständige Gewerbe-Inspektor Maruhn eine Entschädigung für potenzielle Schädigungen durch das neue Werk. Bei der Ausweitung auf die Carbid-Produktion kam zudem die Angst vor Explosionen hinzu, aber auch diese Einwendungen wurden überstimmt. Der Schutz der Umwelt war zu diesem Zeitpunkt zweitrangig, allerdings wurden bereits im Genehmigungsbescheid vom 22. November 1906 dreizehn Bedingungen für den sicheren Betrieb der Anlagen und den Schutz der Arbeiter gestellt. Vor allem vor Explosionen und der Hitze der über 2000 °C mussten die Mitarbeiter geschützt werden.
Als die Ausweitungen des Betriebs zur Munitionsherstellung 1915 anstanden, drängte die Königliche Gewerbeinspektion Cöln-Land auf eine rasche Umsetzung der Ausbaupläne. Der in das Genehmigungsverfahren eingebundene Kreisarzt schrieb in seinem Bericht, dass "bei entsprechender Windrichtung die Luft ein die Schleimhäute der Luftwege stark reizendes Gas enthielt, das heftigen Hustenreiz hervorrief." Er empfahl, "die Concession nur unter dem Vorbehalte zu erteilen, dass, falls notwendig, besondere Maßnahmen auferlegt werden können, um gröbere Belästigungen oder um Gesundheitsbeschädigung der Nachbarschaft zu verhüten." Entgegen den Gutachten wurde am 29. Dezember 1915 die schleunige Fertigstellung der Anlagen durch das Kriegsministerium angeordnet. Der daraufhin ausgestellte Beschluss vom 22. Februar 1916 enthielt die Bedingung, dass Staub und Dünste, Abwässer, Schlamm und Ammoniakgas im Störungsfall unschädlich gemacht werden mussten. Am 22. Juli 1921 wurde der Beschluss wortgleich in eine Genehmigungsurkunde gewandelt.[14]
In den folgenden Jahren wurden Luftreinhaltungsmaßnahmen und Maßnahmen der Abwasserbehandlung in die Weiterentwicklung der Produktion integriert, in der Regel gekoppelt mit Maßnahmen gesteigerter Wirtschaftlichkeit und besserer Nutzung der Ressourcen. Ein wirklicher Umweltschutzgedanke existierte allerdings (weltweit) erst weit nach dem Zweiten Weltkrieg und gipfelte unter anderem in der Veröffentlichung „Grenzen des Wachstums“ des Club of Rome 1972 und in Deutschland 1974 in der Ausarbeitung eines Bundes-Immissionsschutzgesetzes zum Schutz der Umwelt vor schädlichen Umweltwirkungen. Bereits in den 1950er Jahren wurden in Knapsack weitere Überlegungen angestellt, wie man die Umweltbelastung durch die Produktionsstätten durch Verfahrensumstellungen und Staubabscheidung weiter verbessern kann. 1961 forderte Willy Brandt „Der Himmel über Rhein und Ruhr muss wieder blau werden“ und im gleichen Jahr wurde in Knapsack eine eigene Abteilung für die Abwasserreinigung, Luftreinhaltung und Abfallbeseitigung als „Zentralstelle Wasser/Luft“ (ZWL), ab 1968 „Abteilung Wasser/Luft“ (AWL) eingerichtet und bis heute unter wechselnden Namen beibehalten. Während bis in die 1990er Jahre jedoch sogenannte „End-of-pipe“-Maßnahmen wie Verbrennungsanlagen, Kamine, Kläranlagen und Deponien zur Minimierung der negativen Auswirkungen im Vordergrund standen und damit auch die Produktionskosten belasteten, stehen heute vor allem integrierte Maßnahmen und ein nachhaltiges Umweltmanagement im Fokus, die den Umweltschutz bereits in der Produktionsplanung berücksichtigen und so auch Kosten sparen sollen.[14]
Abwasserbehandlung
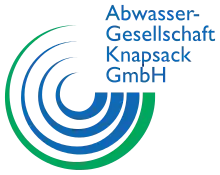
Durch die Zunahme der Abwässer aus dem Chemiepark in den Anfangsjahren, vor allem durch die Acetylenherstellung und die darauf aufbauenden Produktionsstätten, sowie in dem angrenzenden Kraftwerk Goldenberg und den Produktionsstätten der Degussa AG kam es zu einer zunehmenden Verschmutzung des Duffesbachs, der neben den Abwässern der Industrie auch die kommunalen Abwässer der Stadt Hürth und des südlichen Köln aufnahm bevor er in den Rhein mündete. Im Chemiewerk Knapsack fiel dabei vor allem die trübe Kalkmilch ab, die bei der Hydrolyse von Carbid zu Acetylen als ungenutztes Nebenprodukt entstand. Der Geruch beziehungsweise Duft des Gewässers, der bis in die 1960er Jahre bestand, brachte dem Bach seinen Spottnamen „Duftesbach“ ein.
Um die Abwasserbelastung zu entlasten, gründeten die Industrieunternehmen in Knapsack 1929 gemeinsam die Abwasser-Gesellschaft Knapsack GmbH, die ab 1931 die Reinigung der Abwässer übernahm und die gereinigten Abwässer in den Duffesbach einleitete. Entsprechend dem Stand der Technik bestand die Kläranlage der Gesellschaft anfangs aus drei Erdbecken als Absetzbecken für die Schlammbestandteile des Abwassers, darunter auch die festen Bestandteile der Kalkmilch (10 % Kalkhydrat). Der Schlamm wurde auf die benachbarten Schlammtrockenbeete gepumpt, wodurch allmählich eine Hochhalde wuchs. Nach einem Abrutsch der Halde 1937 wurde der Schlamm von 1938 bis 1958 in die ausgekohlten Gruben der Roddergrube gepumpt. Zwei der Erdbecken ersetzte man 1937/38 durch Betonbecken, das dritte Becken diente der Karpfenzucht.
Mit der Umstellung der Acetylenherstellung auf ein Trockenverfahren, das ab 1925 in Knapsack entwickelt wurde, konnte das Kalkhydrat wirtschaftlich und nutzbar produziert werden und wurde nach 1929 über eine Branntkalk-Anlage in die Carbidproduktion zurückgeführt; die Abwasserbelastung durch Kalkmilch ging entsprechend stark zurück, zugleich nahm jedoch die Belastung mit Schwefel-, Stickstoff- und Phosphoranteilen durch die notwendige Nassreinigung des Acetylen zu und machte eine betriebliche Vorreinigung des Abwassers durch eine Chloroxidation notwendig.[14]
Erst in den späten 1950er Jahren wurden in kommunalen Kläranlagen neben der mechanischen Abwasserbehandlung auch biologische Reinigungsverfahren wie Rieselfelder oder bakterienbesiedelter Tropfkörper zum Abbau organischer Bestandteile des Abwassers in Belebtschlamm eingeführt. Bis in die 1960er Jahre wurde angenommen, dass entsprechende Maßnahmen bei industriellen Anlagen nicht nutzbar sind. Nach ersten Versuchen gemeinsam mit dem Institut für Wasser-, Boden- und Lufthygiene in Berlin konnten jedoch in Knapsack 1964 erste Versuche mit vorbehandeltem Abwasser begonnen werden, die in den späteren 1960er Jahren im Einsatz von beiden Kläranlagen (die Kläranlage im Werksteil Hürth wurde 1965 in Betrieb genommen) mit tiefen bodenbelüfteten Belebtschlammbecken mündeten. Die erste biologische Reinigungsstufe konnte 1967/68 in Betrieb genommen werden. Anfang der 1990er Jahre wurde zudem eine Nachfällung des biologisch gereinigten Abwassers zur Fällung von Phosphaten eingeführt, die die Eutrophierung vermeiden sollte. Seit 1997 wurde diese Nachfällung durch einen biologischen Prozess ergänzt, bei dem über eine Bakterienkaskade Ammonium aus ammoniumhaltigen Abwässern in Luftstickstoff abgebaut werden.
Für die Hydroxid-Ausfällung von Schwermetallen wurde durch eine Kalkeintragsanlage ein Vorklärbecken mit einem pH-Wert von 9 bis 10 eingesetzt, im gleichen Becken wurden Phosphate als Calciumphosphat ausgefällt. Zugleich wurden in den Einzelbetrieben immer mehr Vorreinigungsstufen wie die Neutralisierung von Säuren, die Vorfällung von Cyaniden mit Eisensalzen, die Entfernung von Chlorkohlenwasserstoffen, die Lösemittelrückgewinnung und die Verseifung von Abwässern, die Pflanzenschutzmittel enthalten konnten, integriert. Durch regelmäßige Kontrollen beispielsweise auf die Fischgiftigkeit und auf die Anteile verschiedener Inhaltsstoffe wird die Abwasserqualität bis heute festgestellt und effektiv unterhalb der geforderten Grenzwerte des Wasserhaushaltsgesetzes und des Abwasserabgabengesetzes gehalten. Um die Funktionsfähigkeit auch bei großem Wasseraufkommen, beispielsweise bei sogenannten „Jahrhundertregenfällen“, zu gewährleisten, wurden große Staubecken mit einer Kapazität von 26.000 m³ als Rückhaltebecken angelegt.[14]
Luftreinigung
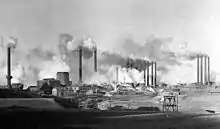
Der Hauptteil der Luftverunreinigungen zu Beginn der Produktion im Chemiepark entstand durch die offenen Carbidöfen, bei denen Kohlenstoffmonoxid entstand und abgebrannt werden musste. Dies resultierte in einer starken Staub- und Abgasbelastung, die durch die Umstellung auf halbgeschlossene Öfen 1938 reduziert werden konnte. Auch in der Kalkstickstoffproduktion wurden die Öfen durch die Umstellung der Retorten- auf Kanalöfen und später auf die Drehöfen zunehmend wirtschaftlich aber auch ökologisch optimiert. Nach der beinahe vollständigen Zerstörung im Zweiten Weltkrieg stellte die Wiederaufnahme der Düngemittelproduktion die höchste Priorität dar. Durch Wissenschaftler und Techniker aus Piesteritz kam die Kenntnis, geschlossene Carbidöfen zu bauen, nach Knapsack, sodass 1955 der erste und 1958 der zweite vollgeschlossene Ofen konstruiert werden konnte. Das Ofengas wurde aufgefangen und anderen Produktionsstätten als Brennstoff zugeführt, wodurch der Ausbrandgrad zu Wasser und Kohlendioxid verbessert und der Kohlenmonoxidanteil reduziert werden konnte. Durch die Nassreinigung wurden die Gasbestandteile zudem zunehmend der Abwasserreinigung zugeführt.
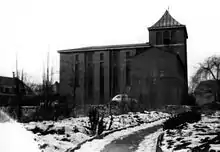
Das Hauptproblem der Produktionsanlagen in Knapsack stellte die hohe Staubentwicklung dar, die sowohl im Chemiewerk wie auch in den benachbarten Anlagen wie der Brikettieranlage und dem Kraftwerk entstanden. Alle angelieferten Feststoffe, vor allem Braunkohle, Erze, Koks und Kalk, mussten geschüttet, transportiert und zerkleinert werden und während Rauch und Verbrennungsgase durch hohe Kamine abgeleitet und abgefackelt werden konnten, blieb der Staub immer in Industrienähe. So bedeckten weißer Kalk und schwarzer Ruß die Umgebung und beeinträchtigten das Leben der Anwohner. Durch die enorme Luftverschmutzung durch die Chemieanlagen und die Kohlekraftwerke gelangte der Ort Knapsack zwischen 1940 und 1960 zunehmend in den Ruf, einer der schmutzigsten Orte Deutschlands zu sein. Bei einem Besuch des nordrhein-westfälischen Ministerpräsidenten Franz Meyers im Jahr 1966 beschloss dieser, den Ort Knapsack aufzugeben und die Menschen umzusiedeln, und dieser Plan wurde trotz seiner Wahlniederlage gegen Heinz Kühn im gleichen Jahr nicht aufgegeben. Entsprechend begann 1970 die Umsiedlung des Ortes, die 1982 mit dem Abriss des letzten Hauses abgeschlossen wurde.[14]
Im Nachgang der Verabschiedung des Bundesimmissionsschutzgesetzes von 1974 wurden in Nordrhein-Westfalen fünf Belastungsgebiete festgelegt, in denen die Luftqualität intensiv überwacht wurde und Maßnahmen zur Verbesserung angeordnet wurden. Knapsack zählte zum Belastungsgebiet „Rheinschiene Süd“. 1975 wurden zwei zentrale Rückstandsverbrennungsanlagen (RVAs) gebaut, die die vielen dezentralen Verbrennungsanlagen ersetzten und in die alle wesentlichen Abgasströme mit organischen Gasen und Dämpfen eingebunden wurden. Es erfolgten zudem Einbauten von verbesserten Entstaubungsfiltern und Abgaswäschern, die die Emissionssituation weiter verbesserten. Als die TA Luft 1986 in Kraft trat und neue Standards festlegte, mussten nur noch wenige Emissionsquellen beseitigt werden, was in den Folgejahren geschah. Besonders intensive Abgasquellen wurden mit Messsystemen ausgestattet, und alle Emissionsquellen sind heute in einem Emissionskataster erfasst und werden regelmäßig überwacht. Zur flächendeckenden Messung wurden Messstationen durch das Landesamt für Immissionsschutz in Essen aufgebaut. Die Belastungsgebiete konnten 1989 wieder aufgehoben werden, die Einstellung des Tagebaus im Hürther Gebiet (1988) und das Abstellen der Carbid- und Phosphoröfen führten zu weiteren Absenkungen der Immissionen, sodass Knapsack heute keine besonders erhöhten Werte mehr aufweist.
Abfallwirtschaft und Sondermüllentsorgung
Durch die Ablagerung des Klärschlamms auf eine eigene Trockenhalde begann in Knapsack auch die integrierte Abfallwirtschaft. Die Trockenhalde wurde nach den Abrutschen verlegt in die ausgekohlte Grube Vereinigte Ville, wodurch die ausgekohlten Braunkohleabbaugruben erstmals in das Konzept der Abfallwirtschaft integriert wurden. Auch die Luftreinigung und natürlich die Produktion selber ergaben den Bedarf zur Entsorgung von Feststoffen und Abfällen. Die reine Lagerung des Klärschlamms in der Grube wurde durch eine Nutzung des Kalkhydrats zur Flugstaubabbindung im benachbarten Kohlekraftwerk Goldenberg ersetzt, das entstehende Granulat wurde über Förderbänder in das Tagebaugelände Vereinigte Ville transportiert. Im Jahr 1964 wurde eine erste Kammerfilterpresse gebaut, in der der Schlamm komprimiert werden konnte, eine zweite folgte 1969 und eine dritte 1977. Bis heute werden alle Klärschlammabfälle einschließlich des Belebtschlamms in diesen Anlagen eingedickt, mit Kalk abgebunden und anschließend gepresst, der Presskuchen wird in der Deponie eingelagert.
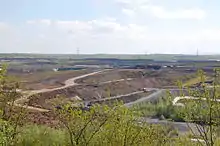
Durch die Produktion von bis zu 300.000 Tonnen Gips pro Jahr als Nebenprodukt bei der Herstellung von Phosphorsäure entstand ein weiterer Grund für eine Optimierung der Abfallwirtschaft nach 1960. 1972 wurde mit dem Bundes-Abfallbeseitigungsgesetz der Stand der Technik festgelegt und die Genehmigung geregelt, 1982 wurden die Deponie des Chemiewerks Knapsack gemeinsam mit der Hausmülldeponie der Stadt Köln und der Aschedeponie von Rheinbraun genehmigt. Mit der zunehmenden Produktion von Phosphor kam als Nebenprodukt der Produktion in den Phosphoröfen granulierte Silikatschlacke (Calciummetasilikat) als Nebenprodukt hinzu, die aus dem Calcium-Bestandteil des Phosphaterzes und Kies entstand. Das Material konnte aufgrund der Eigenschaften als Deponiebaustoff verwendet werden, zwischen den die Gipsmassen in Polyethylenfolien verpackt gelagert wurden. Der dadurch entstehende feste Deponiekörper konnte über ein Drainagesystem entwässert werden. In eigenen Feldern wurden Bariumsulfat aus der Elektrolyseanlage und Klärschlamm, Bodenaushub und Abrissmassen gelagert. Das Sickerwasser konnte aufgrund der guten Qualität bis 1987 unbehandelt in die Erft geleitet werden, aufgrund des enthaltenen Sulfats wird es jedoch seit 1987 über eine Druckleitung in die Kläranlage des Werks Hürth geleitet. Seit 1997 wird auch das unbehandelte Sickerwasser aus der Kölner Hausmülldeponie in die Kläranlage geleitet und dort nachbehandelt.
1984 wurde durch das Austreten von schadstoffbelasteten Sickerwässern am Ortsrand von Kierdorf eine Altlastverfüllung aus kommunalen, gewerblichen und industriellen Abwässern im Deponiegelände Concordia entdeckt, für das kein alleiniger Verursacher feststellbar war. Das Wasser wird seit 1990 in die Kläranlage der Stadt Erftstadt eingeleitet und gereinigt. In den 1990er Jahren wurden durch Novellierungen des Abfallgesetzes zusätzliche Maßnahmen zum Grundwasserschutz notwendig. Seitdem dürfen Sonderabfälle des Chemiewerks nur noch oberhalb der maximalen Grundwasserlinie gelagert werden, eine Schlitzwand schützt zudem seit 1998 die Deponie gegen seitliches Eindringen von Grundwasser.[14]
Produkte des Chemieparks Knapsack
Im Laufe der Entwicklung des Chemieparks Knapsack wurde die Produktpalette ständig erweitert und modifiziert, wobei sich die jeweiligen Betreiber den Marktsituationen angepasst haben. Während der Betrieb in der Anfangszeit auf die Produktion von Kalkstickstoff und Calciumcarbid ausgerichtet war und sich beim Ausbau entsprechend an diesen Produkten ausrichtete, wurde später erst die Acetylenchemie und nach dem Zweiten Weltkrieg die Phosphor- und Chlorchemie in den Fokus gerückt.
Die folgende Tabelle gibt einen vollständigen Überblick über die Produkte, die am Standort hergestellt wurden,[15] heute noch produzierte Stoffe sind grau unterlegt.
Produkt | Produktionsstart | Produktionsstopp | Betreiber |
---|---|---|---|
Kalkstickstoff | 1908 | 1971 | Gesellschaft für Stickstoffdünger GmbH, AG für Stickstoffdünger, Knapsack-Griesheim AG, Knapsack AG |
Calciumcarbid | 1908 | 1990 | Gesellschaft für Stickstoffdünger GmbH, AG für Stickstoffdünger, Knapsack-Griesheim AG, Knapsack AG, Hoechst AG (Werk Knapsack) |
Ammoniumsulfat | 1909 | 1919 | AG für Stickstoffdünger |
Ammoniak | 1909 | 1919 | AG für Stickstoffdünger |
Ammoniumhydroxid (Ammoniakwasser) | 1911 | 1919 | AG für Stickstoffdünger |
Essigsäure | 1918 | 2000 | AG für Stickstoffdünger, Knapsack-Griesheim AG, Knapsack AG, Hoechst AG (Werk Knapsack), Celanese Europe GmbH |
Aceton | 1918 | 1964 | AG für Stickstoffdünger, Knapsack-Griesheim AG, Knapsack AG, Hoechst AG (Werk Knapsack) |
Acetaldehyd (aus Acetylen) | 1919 | 1964 | AG für Stickstoffdünger, Knapsack-Griesheim AG, Knapsack AG, Hoechst AG (Werk Knapsack) |
Acetylen (Naßvergaser) | 1919 | 1990 | AG für Stickstoffdünger |
Natrium (metallisch) | 1922 | 1929 | AG für Stickstoffdünger |
Ferrosilicium | 1922 | 1968 | AG für Stickstoffdünger, Knapsack-Griesheim AG, Knapsack AG, Hoechst AG (Werk Knapsack) |
Acetylen (Großtrockenvergaser) | 1926 | 1991 | AG für Stickstoffdünger, Knapsack-Griesheim AG, Knapsack AG, Hoechst AG (Werk Knapsack) |
Aktivkohle (aus Kraftwerksasche) | 1930 | 1948 | AG für Stickstoffdünger |
Essigsäureanhydrid (aus Essigsäure) | 1931 | 1943 | AG für Stickstoffdünger |
Chlorcalcium | 1931 | AG für Stickstoffdünger | |
Branntkalk | 1932 | 1944 | AG für Stickstoffdünger |
Kornkalkstickstoff | 1934 | ? | AG für Stickstoffdünger, Knapsack-Griesheim AG, Knapsack AG, Hoechst AG (Werk Knapsack) |
Essigsäureanhydrid (aus Acetaldehyd) | 1939 | 2000 | AG für Stickstoffdünger, Knapsack-Griesheim AG, Knapsack AG, Hoechst AG (Werk Knapsack), Celanese Europe GmbH |
Diacetonalkohol | 1949 | 1986 | AG für Stickstoffdünger, Knapsack-Griesheim AG, Knapsack AG, Hoechst AG (Werk Knapsack) |
Monochloressigsäure | 1952 | heute | Knapsack-Griesheim AG, Knapsack AG, Hoechst AG (Werk Knapsack), Clariant, CABB GmbH |
Phosphor (gelb) | 1953 | 1992 | Knapsack-Griesheim AG, Knapsack AG, Hoechst AG (Werk Knapsack) |
Thermische Phosphorsäure | 1953 | 1992 | Knapsack-Griesheim AG, Knapsack AG, Hoechst AG (Werk Knapsack) |
Acetylenruß (Explosionsruß) | 1953 | 1964 | Knapsack-Griesheim AG, Knapsack AG |
Ferrosilicium (pulverförmig) | 1953 | 1993 | Knapsack-Griesheim AG, Knapsack AG, Hoechst AG (Werk Knapsack) |
Chlorwasserstoff | 1953 | 1976 | Knapsack-Griesheim AG, Knapsack AG, Hoechst AG (Werk Knapsack) |
Vinylchlorid (auf Acetylenbasis) | 1954 | 1975 | Knapsack-Griesheim AG, Knapsack AG, Hoechst AG (Werk Knapsack) |
Magnesium | 1954 | 1966 | Knapsack-Griesheim AG, Knapsack AG |
Pentanatriumtriphosphat | 1956 | 1991 | Knapsack-Griesheim AG, Knapsack AG, Hoechst AG (Werk Knapsack) |
Tetranatriumdiphosphat | 1956 | Knapsack-Griesheim AG | |
Monovinylacetylen (Moval, Chloropren) | 1957 | 1975 | Knapsack-Griesheim AG, Knapsack AG, Hoechst AG (Werk Knapsack) |
Blausäure | 1957 | 1970 | Knapsack-Griesheim AG, Knapsack AG |
Acrylnitril | 1958 | 1970 | Knapsack-Griesheim AG, Knapsack AG |
Acetaldehyd (auf Ethylenbasis) | 1961 | 2000 | Knapsack-Griesheim AG, Knapsack AG, Hoechst AG (Werk Knapsack), Celanese GmbH |
Chlor (Chloralkali-Elektrolyse) | 1962 | heute | Knapsack-Griesheim AG, Knapsack AG, Hoechst AG (Werk Knapsack), Vintron GmbH, Vinnolit GmbH & Co. KG |
Natronlauge | 1962 | heute | Knapsack-Griesheim AG, Knapsack AG, Hoechst AG (Werk Knapsack), Vintron GmbH, Vinnolit GmbH & Co. KG |
Acetogenruß (Spaltruß) | 1962 | 1990 | Knapsack-Griesheim AG, Knapsack AG, Hoechst AG (Werk Knapsack) |
Diacetylcyanid | 1962 | Knapsack-Griesheim AG, | |
Phosphorpentasulfid | 1963 | heute | Knapsack-Griesheim AG, Knapsack AG, Hoechst AG (Werk Knapsack), Celanese GmbH, ThermPhos GmbH, BK Giulini/ICL |
Vinylchlorid (aus Dichlorethan) | 1964 | heute | Knapsack-Griesheim AG, Knapsack AG, Hoechst AG (Werk Knapsack), Vintron GmbH, Vinnolit GmbH & Co. KG |
Dicalciumphosphat | 1965 | 1995 | Knapsack AG, Hoechst AG (Werk Knapsack) |
Natriumtripolyphosphat (Thermphos NW) | 1965 | 1991 | Knapsack AG, Hoechst AG (Werk Knapsack) |
Nassphosphorsäure | 1966 | 1991 | Knapsack AG, Hoechst AG (Werk Knapsack) |
Polyvinylchlorid (PVC) | 1966 | heute | Knapsack AG, Hoechst AG (Werk Knapsack), Vintron GmbH, Vinnolit GmbH & Co. KG |
Natrium-Calcium-Magnesiumphosphat (Futtermittelzusatz Hostaphos) | 1966 | 1986 | Knapsack AG, Hoechst AG (Werk Knapsack) |
Elektrolytisches Mangandioxid (Braunstein) | 1967 | 1987 | Knapsack AG, Hoechst AG (Werk Knapsack) |
Vinylacetat (auf Acetylenbasis) | 1968 | 1971 | Knapsack AG |
1,2-Dichlorethan | 1969 | heute | Knapsack AG, Hoechst AG (Werk Knapsack), Vintron GmbH, Vinnolit GmbH & Co. KG |
Phosphorpentoxid | 1969 | heute | Knapsack AG, Hoechst AG (Werk Knapsack), Clariant GmbH |
Polyphosphorsäure | 1969 | heute | Knapsack AG, Hoechst AG (Werk Knapsack), Clariant GmbH |
Niederdruck-Polyethylen (HDPE) | 1970 | 2005 | Knapsack AG, Hoechst AG (Werk Knapsack), Hostalen Polyethylen GmbH, Elenac GmbH, Basell Polyolefins |
Phosphorsäurealkylester | 1971 | Knapsack AG | |
Dialkyldithiophosphorsäureester (ADTP) | 1971 | 1982 | Knapsack AG, Hoechst AG (Werk Knapsack) |
Thiophosphorsäureester | 1971 | 1996 | Knapsack AG, Hoechst AG (Werk Knapsack) |
Phosphorige Säure | 1971 | 1996 | Knapsack AG, Hoechst AG (Werk Knapsack) |
Nachchloriertes PVC (Chlorhostalen) | 1973 | 1992 | Knapsack AG, Hoechst AG (Werk Knapsack) |
PVC (Hostalit H) | 1973 | 1992 | Knapsack AG, Hoechst AG (Werk Knapsack) |
Gipswandbauplatten | 1973 | 1983 | Knapsack AG, Hoechst AG (Werk Knapsack) |
Suspensions-Polypropylen | 1976 | 1998 | Hoechst AG (Werk Knapsack), Targor GmbH |
Ammoniumpolyphosphat | 1976 | heute | Hoechst AG (Werk Knapsack), Clariant GmbH |
Azo-Pigmentfarben | 1976 | 2005 | Hoechst AG (Werk Knapsack), Clariant GmbH |
Triazophos (Hostathion) | 1977 | 2002 | Hoechst AG (Werk Knapsack), Hoechst-Schering AgrEvo GmbH, Aventis CropScience AG, Bayer CropScience AG |
Phoban | 1978 | 1991 | Hoechst AG (Werk Knapsack) |
Carbendazim (Derosan, Derosal) | 1978 | 2005 | Hoechst AG (Werk Knapsack), Hoechst-Schering AgrEvo GmbH, Aventis CropScience, Bayer CropScience |
Diclofop-methyl (Illoxan) | 1979 | 2007 | Hoechst AG (Werk Knapsack), Hoechst-Schering AgrEvo GmbH |
Pyrazophos (Afugan) | 1980 | 1999 | Hoechst AG (Werk Knapsack) |
Vinylmethylacetamid | 1980 | 1981 | Hoechst AG (Werk Knapsack) |
Extraktionsphosphorsäure | 1981 | 1987 | Hoechst AG (Werk Knapsack) |
Phosphonoessigsäuretriethylester (PEE) | 1985 | 1996 | Hoechst AG (Werk Knapsack) |
Methanphosphonigsäuredichlorid | 1986 | heute | Hoechst AG (Werk Knapsack), Hoechst-Schering AgrEvo GmbH, Aventis CropScience, Bayer CropScience |
Methanphosphonige Säure | 1986 | heute | Hoechst AG (Werk Knapsack), Hoechst-Schering AgrEvo GmbH, Aventis CropScience, Bayer CropScience |
Methanphosphonigsäureester | 1987 | heute | Hoechst AG (Werk Knapsack), Hoechst-Schering AgrEvo GmbH, Aventis CropScience, Bayer CropScience |
Oxaphospholan | 1987 | 2008[16] | Hoechst AG (Werk Knapsack), Clariant GmbH |
Massepolypropylen | 1991 | heute | Hoechst AG (Werk Knapsack), Hostalen Polyethylen GmbH, Elenac GmbH, basell Polyolefins |
Kaliumacetat (Landebahnenteiser Safeway KA) | 1991 | heute | Hoechst AG (Werk Knapsack), Clariant GmbH |
Schichtsilikat (SKS-6) | 1994 | 2006 | Hoechst AG (Werk Knapsack), Clariant GmbH |
Formetanat | 1995 | 2001 | Hoechst-Schering AgrEvo GmbH, Aventis CropScience |
Silafluofen | 1995 | 1998 | Hoechst-Schering AgrEvo GmbH |
Isoxadifen | 2002 | heute | Aventis CropScience, Bayer CropScience |
Aluminiumdiethylphosphinat / Depal (Flammschutzmittel Exolit OP) | 2004 | heute | Clariant GmbH |
Propamocarb | 2005 | heute | Bayer CropScience |
Trifluormethylacetophenon | 2006 | heute | Bayer CropScience |
Fluquinconazole | 2004 | heute | Bayer CropScience |
Aktuelle Ausgestaltung
Aus dem ehemaligen Hoechst-Standort wurde ein Verbund von weiterhin durch eine Reihe von Leistungsbeziehungen vielfältig verbundenen, aber unternehmerisch selbständigen und unabhängigen Standortteilnehmern. Die größten Unternehmen sind heute Bayer AG, Division CropScience (Pflanzenschutz), Clariant, (Spezialchemikalien, Flammschutzmittel), LyondellBasell (Polyolefine), CABB (Monochloressigsäure), Vinnolit (Polyvinylchlorid, Natronlauge, Chlor, Wasserstoff), Israel Chemicals Ltd. (ICL) (Phosphor) und Statkraft (GuD-Kraftwerke). Die Gesamtfläche des Chemieparks beträgt derzeit 180 ha bzw. 1,8 km², von denen etwa 20 ha als erschlossene Freifläche für weitere Ansiedlungen sofort nutzbar sind.
Rechnet man die Neuansiedlung der benachbarten Papierfabrik Rheinpapier des finnischen Papierkonzerns Myllykoski Corporation (jetzt UPM-Kymmene) hinzu, wurden beziehungsweise werden seit Gründung des Chemiepark Knapsack 1998 rund zwei Milliarden Euro in Neuanlagen beziehungsweise Anlagenerneuerungen investiert. Gemeinsam mit dem benachbarten Kraftwerk Goldenberg und der Papierfabrik bildet der Chemiepark das Energie- und Chemie-Centrum Knapsack (ECC Knapsack).
Infrastruktur
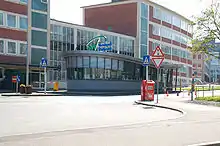
Die YNCORIS bietet als Chemieparkbetreiber und -dienstleister den Unternehmen am Standort eine breite Palette von verschiedenen industrie- und chemienahen Dienstleistungen an, zum Beispiel Anlagenplanung und -bau, Instandhaltung, Reparaturen aller Art, Sicherheitsdienstleistungen wie Werksschutz und Feuerwehr, Umweltschutz, Logistik, eine gemeinsame Standort- und Umfeldkommunikation, eine werksärztliche Abteilung, Betriebsrestaurants, eine Autowerkstatt und das Kultur und Veranstaltungszentrum Feierabendhaus Knapsack, ein 1956 errichtetes denkmalgeschütztes Gebäude des Kölner Architekten Karl Hell.
Für die Produktion am Standort stellt YNCORIS neben Strom verschiedene Gase und Flüssigkeiten über ein Rohrleitungssystem zur Verfügung. Dabei handelt es sich um Frischwasser, Vollentsalztes Wasser, Dampf, Erdgas, Druckluft, Mess- und Regelluft sowie Sauerstoff und Stickstoff von der benachbarten Anlage von Praxair. Hinzu kommen die Gase im Stoffverbund innerhalb des Chemieparks, die von den ansässigen Unternehmen bereitgestellt werden. Dazu gehören Chlor, Natronlauge und Wasserstoff von Vinnolit sowie Chlorwasserstoff von CABB. Der Chemiepark ist über eine Rohrfernleitungstrasse mit den Werken der LyondellBasell sowie der Shell Deutschland in Wesseling verbunden. Über diese Trasse wird der Standort von LyondellBasell mit Propylen und von YNCORIS Höchst mit Ethylen versorgt.
Der Strom für den Chemiepark Knapsack wird hauptsächlich vom benachbarten Kraftwerk Goldenberg und dem standorteigenen Ersatzbrennstoff-Kraftwerk produziert. Die beiden Gas- und Dampfkraftwerke von Statkraft, die am Chemiepark Knapsack ansässig sind, gleichen dagegen die Stromspitzen des allgemeinen Stromnetzes aus. Gegen Stromausfälle und Störungen ist der Chemiepark über mehrere parallele Netze abgesichert.
Wichtig für die angesiedelte Industrie ist zudem die Abwasser-Entsorgung, die durch die bereits 1929 durch die Unternehmen Hoechst, Degussa und RWE gegründete Abwasser-Gesellschaft Knapsack GmbH gewährleistet wird. Das Unternehmen betreibt zwei dreistufige mechanisch-biologisch-chemische Kläranlagen mit einem ausgedehnten Kanalsystem, über die die gesamten Industrie-, Sanitär- und Oberflächenwässer gereinigt werden. Aufgrund der besonderen Ansprüche am Standort werden als zusätzliche Reinigungsverfahren eine Entstickung, eine Phosphatnachfällung und eine Sauerstoffanreicherung genutzt.
Transportdienstleistungen erfolgen über die KCG Knapsack Cargo GmbH, die die öffentlichen Container-Terminals mit Bahnanschluss am Standort betreiben und eine Kapazität von bis zu 50.000 Containern pro Jahr haben. Vernetzt ist das System mit dem Rheinhafen Köln-Niehl und dem Umschlagbahnhof Köln Eifeltor. Transportmöglichkeit bietet am Standort die auf Schüttgut fokussierte Spedition Schmidt mit einer Lagerkapazität von 40.000 m³ in mehr als 100 Silos, die vor allem für Polypropylen- und Polyvinylchlorid-Granulate genutzt wird.
Produzierendes Gewerbe
Im Chemiepark Knapsack sind aktuell verschiedene Unternehmen angesiedelt, die eine breite Palette von Produkten der chemischen Industrie produzieren. Das Spektrum reicht dabei von Grundchemikalien wie Natronlauge, Chlor und Phosphorsäure über Pflanzenschutzmittel und Landebahnenteiser (Safeway KA) bis zu verschiedenen Kunststoffen wie Polyvinylchlorid und Polypropylen. Verschiedene Produktionsanteile werden dabei im Stoffverbund des Chemieparks verwendet.[17]
Der Schweizer Konzern Clariant stellt mit 220 Mitarbeitern eines der größten Produktionsunternehmen im Chemiepark dar. Es produziert in fünf Betrieben eine große Palette verschiedener Spezialchemikalien, darunter etwa den Landebahnenteiser auf der Basis von Kaliumacetat Safeway KA und halogenfreie Flammschutzmittel (Exolit OP). Zudem unterhält Clariant ein Forschungszentrum für umweltfreundliche Flammschutzmittel, die hier zur Marktreife gebracht werden. Ein großer Teil der Produkte des Unternehmens Clariant basiert auf Phosphor, darunter Phosphorpentoxid, Phosphorsäureester, Polyphosphorsäure sowie Ammoniumpolyphosphat (Exolit AP 422 und Exolit AP 462 (modifiziert)).[17] Ebenfalls auf Phosphorchemie basiert die Phosphorpentasulfid-Produktion der BK Giulini. Etwa 20 Mitarbeiter sind hier mit der Produktion des Stoffes beschäftigt, der zur Herstellung von Additiven für Schmierstoffe genutzt wird.[17]
Polypropylen ist die größte Produktgruppe im Chemiepark Knapsack.[17] Der Hersteller LyondellBasell produziert den Kunststoff in zwei Anlagen in Pulver- und Granulatform. Gemeinsam mit dem Standort Wesseling handelt es sich um den größten Standort des Unternehmens in Europa mit rund 2.550 Mitarbeitern und Kontraktoren[18] und 8 Anlagen zur Herstellung von Polyethylen und Polypropylen;[19] Am 20. September 2019 gab LyondellBasell die Erweiterung der Produktion von Polypropylen Compounds bzw. Verbundwerkstoffen in Knapsack um 25.000 t auf 200.000 t Spezialkunststoff pro Jahr bekannt.[20]
Vinnolit ist mit etwa 280 Mitarbeitern das größte Chemie-Unternehmen am Standort und produziert als zweites Unternehmen Kunststoffe. Der Betrieb hat sich dabei auf die Produktion von Polyvinylchlorid sowie auf das Monomer Vinylchlorid aus Steinsalz spezialisiert und gehört damit zu den größten PVC-Produzenten der Welt. Die PVC-Kapazität von Vinnolit am Standort Knapsack beträgt 170.000 t/a (die Gesamtkapazität des Unternehmens beträgt 780.000 t/a[21]), die Kapazität für das Vorprodukt Vinylchlorid 350.000 t/a (Gesamtkapazität 665.000 t/a[21]). Neben diesen Produkten gehören weitere Zwischenprodukte wie Natronlauge, Dichlorethan und Wasserstoff zum Portfolio des Unternehmens. Es stellt diese im Rahmen des Stoffverbundes anderen Unternehmen wie etwa die CABB GmbH zur Verfügung, von denen Vinnolit Chlorwasserstoff erhält.[17] CABB produziert in einer der weltweit größten und effektivsten Anlage[22] mit etwa 90 Mitarbeitern Monochloressigsäure und Natriummonochloracetat sowie Acetylchlorid und Chlorwasserstoff auf der Basis von Essigsäure und Essigsäureanhydrid sowie Chlor und Wasserstoff aus dem Stoffverbund.[17]
Die Pflanzenschutzsparte der Bayer AG stellt in Knapsack eine Reihe von Pflanzenschutzmitteln und Vorprodukten her, die weltweit zum Einsatz kommen. Sie profitieren dabei vom Chlor und der Natronlauge im Stoffverbund, die vor allem von Vinnolit bereitgestellt werden. Zum Portfolio der in Knapsack produzierten Stoffe gehören Triazophos, Carbendazim, Isoxadifen[23], Fluquinconazol[24], Diclofop und Mefenpyr.[17]
Nicht auf dem direkten Chemieparkgelände, sondern auf einem Nachbargrundstück befindet sich die Niederlassung des amerikanischen Unternehmens Praxair, das am Standort Knapsack eine Luftzerlegungsanlage sowie ein Abfüllwerk betreibt. Der Betrieb mit etwa 70 Mitarbeitern füllt hier die Gase Argon, Sauerstoff und Stickstoff als Flüssiggase ab, zudem wird Stickstoff und Sauerstoff in ein Pipelinenetz eingespeist und auf diese Weise zu Verbrauchern im Chemiepark sowie in der Region verteilt.[17]
Siehe auch
Literatur
- Helmut Neßeler: 100 Jahre Chemiestandort Knapsack, herausgegeben von der InfraServ GmbH & Co. Knapsack KG, 2007.
- Helmut Neßeler, Hans-Josef Blatt, Manfred Faust: Knapsack Chemie – Bilder aus 95 Jahren Industriegeschichte im Rheinland. Klartext-Verlag, Essen 2002, ISBN 3-89861-121-3.
- Helmut Neßeler: 100 Jahre Chemiestandort Knapsack – Ein geschichtlicher Überblick. In: Hürther Beiträge zur Geschichte, Kultur und Regionalkunde Band 87, 2008; S. 81–102. ISSN 1864-5348
- Horst-Dieter Schüddemage, Werner Pieper: Knapsack Chemie – Von der Carbidfabrik zu Chemiepark. Klartext-Verlag, Essen 2002, ISBN 3-89861-097-7.
Einzelnachweise
Der Abschnitt „Geschichte“ basiert weitestgehend auf Helmut Neßeler: 100 Jahre Chemiestandort Knapsack und Die Geschichte der Chemie in Knapsack.
- Nach Helmut Neßeler: 100 Jahre Chemiestandort Knapsack – Ein geschichtlicher Überblick. In: Hürther Beiträge zur Geschichte, Kultur und Regionalkunde Band 87, 2008; S. 81–102.
- InfraServ GmbH & Co. Knapsack KG: 1950 – 1959. www.infraserv-knapsack.de. Abgerufen am 14. Juli 2009.
- Erfolgreich zweigleisig. (PDF) Knapsack Spiegel vom 9. August 2002, Seite 4
- silafluofen data sheet. www.alanwood.net. Abgerufen am 18. Mai 2009.
- formetanate data sheet. www.alanwood.net. Abgerufen am 18. Mai 2009.
- Spaltungsbericht der Hoechst AG und der Celanese AG (Memento des Originals vom 8. Mai 2005 im Internet Archive) Info: Der Archivlink wurde automatisch eingesetzt und noch nicht geprüft. Bitte prüfe Original- und Archivlink gemäß Anleitung und entferne dann diesen Hinweis. (PDF)
- rückdatiert auf 1. Januar 2000; Wacker und Celanese schließen Verkauf ihres PVC-Geschäfts an Advent International ab (Seite nicht mehr abrufbar, Suche in Webarchiven) Info: Der Link wurde automatisch als defekt markiert. Bitte prüfe den Link gemäß Anleitung und entferne dann diesen Hinweis. . Pressemitteilung der Vinnolit GmbH vom 20. Juli 2000.
- Integration von Vintron in die Vinnolit GmbH & Co. KG beschlossen, Chemie.de vom 5. August 2003.
- Abschied von einem Oldie. (PDF) Knapsack Spiegel, 5. April 2002, S. 1–2.
- Dr. Michael Winhold neuer Geschäftsführer bei Vintron. Chemie.de, 23. Januar 2003.
- Vinnolit investiert am Standort Knapsack, Chemie.de vom 16. Dezember 2004.
- Aus IGH2 wird HyCologne. Energieportal24 vom 23. Januar 2007.
- Wenn nicht anders angegeben, Angaben nach Helmut Neßeler: 100 Jahre Chemiestandort Knapsack, herausgegeben von der InfraServ GmbH & Co. Knapsack KG, 2007; S. 91.
- Abschnitt basiert auf: Werner Pieper: Umweltschutz und Chemie in Knapsack. Die Geschichte des Umweltschutzes im Werk Knapsack der Hoechst AG. In: Schüddemage & Pieper 2002; S. 299–331.
- Nach Helmut Neßeler: 100 Jahre Chemiestandort Knapsack, herausgegeben von der InfraServ GmbH & Co. Knapsack KG, 2007; S. 91.; Ergänzt durch Angaben der Website und andere Quellen.
- Birgit Lehmann: Clariant legt Anlage in Knapsack still. Kölner Stadtanzeiger vom 25. November 2008.
- InfraServ GmbH & Co. Knapsack KG: Chemiepark Knapsack – Innovativer Chemie- und Industriestandort mit Zukunft. Informationsbroschüre, 3. Auflage 2007.
- Datenblatt des Standorts Wesseling/Knapsack. Abgerufen am 9. April 2021.
- Standortbroschüre. Abgerufen am 9. April 2021.
- Andreas Engels: Weltweit größte Anlage Lyondellbasell erweitert Produktion in Knapsack. In: Kölner Stadtanzeiger. 21. September 2019, abgerufen am 9. April 2021.
- Vinnolit auf einen Blick. Angaben der Vinnolit GmbH & Co. KG.
- Knapsack – most efficient large plant (Memento des Originals vom 15. April 2009 im Internet Archive) Info: Der Archivlink wurde automatisch eingesetzt und noch nicht geprüft. Bitte prüfe Original- und Archivlink gemäß Anleitung und entferne dann diesen Hinweis. . Angaben der CABB GmbH.
- isoxadifen data sheet. www.alanwood.net. Abgerufen am 18. Mai 2009.
- fluquinconazole data sheet. www.alanwood.net. Abgerufen am 18. Mai 2009.