Ruß
Ruß (von ahd. ruos, dunkel-, schmutzfarben) ist ein schwarzer, pulverförmiger Feststoff, der je nach Qualität und Verwendung zu 80 % bis 99,5 % aus Kohlenstoff besteht. Ruß bezeichnet umgangssprachlich sowohl industrielle Produkte als auch unerwünschte, schädliche Nebenprodukte von Verbrennungsprozessen.
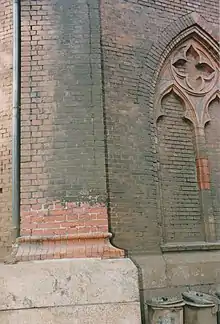
Industrieruß (englisch Carbon Black, CAS-Nr.: 1333-86-4) ist gezielt als Industrie-Grundstoff hergestellter Ruß. Industrieruß ist zweckbedingt eine Modifikation des Kohlenstoffs mit hohem Oberfläche-zu-Volumen-Verhältnis und wird vor allem als Füllstoff und als Schwarzpigment verwendet.
Der sich bei unvollständiger Verbrennung an Rauchgasleitungen wie Schornsteinen absetzende Ruß wird als Glanzruß bezeichnet. Aus Kienspänen hergestellter Ruß heißt Kienruß.
Geschichte
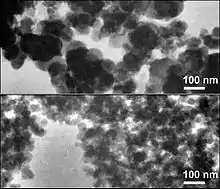
Die Herstellung von Rußen als Schwarzpigment für Tinten → Rußtinte und Tuschen geht bis in die frühen Hochkulturen der Menschheit zurück. Zur Zeit der alten Hochkulturen der Chinesen und Ägypter stieg der Bedarf an kleinen und kleinsten Rußpartikeln beständig an, um daraus große Mengen an Tuschen und Tinten herstellen zu können. Der dafür benötigte Ruß wurde durch gezielte Verbrennung von Harzen, Pflanzenölen oder Asphalt in speziellen Öfen oder flachen Wannen gewonnen. So schreibt der römische Bauherr Marcus Vitruvius Pollio (1. Jhdt. v. Chr.) in seinem Standardwerk der Antike De Architectura über die Kunst der Herstellung von Schwarzpigment: „In den Ofen wird nun Kiefernharz eingebracht, daraus entsteht beim Verbrennen Ruß, der gesammelt wird.“ Ein besonders edles Schwarz, das „Beinschwarz“, entstand aus der Verkohlung von Elfenbein. Die Herstellung von „Beinschwarz“ soll vom griechischen Maler und Gelehrten Apelles (um 325 v. Chr.) erfunden worden sein.[1]
Im Mittelalter war die Rußgewinnung Sache der Rußbrenner, die in ihren Waldhütten – meist mit Teerschwelern und Pechsiedern – stark qualmendes harzhaltiges Holz und den bei der Herstellung von Pech anfallenden Rückstand (Pechkuchen) verbrannten. Der mit dem Rauch entweichende Ruß schlug sich in der Rußkammer des Abzugs nieder, wo er abgeschabt werden konnte.[2][3] Ruß von feinster Qualität war der Lampenruß (auch Lampenschwarz), der in der „Rußlampe“ mit Hilfe eines dicken Baumwolldochts (in China wurde der Docht mit Saft vom echten Steinsamen getränkt) aus Ölen, Fetten, Tranen, Pech und Teeröl (in China auch Kampferöl und Tungöl)[4][5] bei geminderter Luftzufuhr gebrannt wurde.[6] Ruß wurde benötigt zur Herstellung von Lederfarbe, Malfarben, Druckerschwärze, Tinten und Wagenschmiere. Eine Anleitung zur Rußherstellung findet sich im Codex latinus Monacensis 4, einer um 1470 im Kloster Tegernsee entstandenen Handschrift. Um besonders feinen Ruß für spezielle Anwendungen herzustellen, wurden vor allem Baumharze unter begrenzter Luftzufuhr verbrannt → Pecherei. Bis in das 16. Jahrhundert war dies das einzige bekannte Verfahren zur Rußherstellung mit kleinsten Partikelgrößen, die mit Carbon Black vergleichbar sind. Dieses Verfahren kommt noch unter dem Namen Flammrußverfahren zum Einsatz. Ab dem 19. Jahrhundert wurde Ruß vermehrt aus Erdgas und Steinkohlenteer gewonnen.[7][8]
Der Begriff „Carbon Black“ verbreitete sich in den 1870er Jahren, als die aus Erdgas hergestellten Produkte unter diesem Namen verkauft wurden. 1882 wurde durch Godfrey Lowell Cabot die erste Produktionsstätte für Industrieruß gegründet, welche mit dem Channelrußverfahren zu „Channel Black“ betrieben wurde. Verwendung fand der Ruß hauptsächlich als Bestandteil von Druckerschwärze. Da Erdgas in Deutschland nur in unbedeutenden Mengen zur Verfügung stand, wurde intensiv nach Alternativen unter Verwendung einheimischer Rohstoffe gesucht. Steinkohlenteer fällt in Gaswerken bei der Kondensation von Gas in bedeutenden Mengen an. 1889 entwickelte Otto Thalwitzer auf Basis von Teeröl aus Steinkohlenteer das Furnaceverfahren. Obwohl „geschlossene Reaktoren“ entwickelt waren und die Furnaceverfahren wesentlich höhere Ausbeuten ergeben, setzte sich das Oil-Furnaceverfahren aufgrund der Verknappung der Primärenergieträger erst 1943 durch.
Die Massenfertigung von Rußen setzte in Folge der expandierenden Reifenindustrie ein in der ersten Hälfte des 20. Jahrhunderts. Als Verstärkerfüllstoff optimieren Ruße die physikalischen Eigenschaften der Reifen und fördern ihre Langlebigkeit. Die ersten größeren Anlagen wurden als Channel-Black-Anlagen auf den Ölfeldern in den USA gebaut, um einen Teil des bei der Ölförderung austretenden Erdgases zu verwerten. Die Ausbeuten waren gering (5 %), was wegen des Überschusses an Erdgas keine Rolle spielte. Ab 1920 wurden in den USA das Thermalrußverfahren, zuerst zur Gewinnung von Wasserstoff für Luftschiffe, und das Gas-Furnaceverfahren entwickelt, diese haben eine größere Ausbeute und produzieren weniger Emissionen. 1922 wurde das Oil-Furnaceverfahren patentiert, es wurde aber erst später genutzt.
In Deutschland wurde 1934 das Degussa-Gasrußverfahren („Gas-Black“ auf Basis von Teerölen) entwickelt. Unter den Nationalsozialisten war Industrieruß ein kriegswichtiger Rohstoff; in den neu gegründeten Gemeinschaftsunternehmen von Degussa und Reifenherstellern wurde nach dem Gasrußverfahren produziert. So erfolgte 1936 die Gründung der „Deutschen Gasrußwerke GmbH & Co. KG“ in Dortmund.[9] Der stark steigende Bedarf der Reifenindustrie sorgte ab 1937 in den USA für die weitere Entwicklung des Oil-Furnacerußverfahrens, das eine Ausbeute je nach Produkteigenschaft von 10 % bis 70 % erreicht, es wurde 1943 erstmals kommerziell genutzt.[10]
Technisch verlief die Entwicklung der „Furnaceruße“ in vier Wellen: Eine erste Generation von Produkten unterschied sich hauptsächlich in der Größe der Primärpartikel und damit der spezifischen Oberfläche (N110, N220, … N990), in einer zweiten Generation wurde das Aggregierungsverhalten, also der „Verwachsungsgrad“ der Primärpartikel, die „Struktur“, variiert. In den 1970er und 1980er Jahren wurden beispielsweise über die Verweilzeit direkt anwendungstechnische Eigenschaften des Gummis beeinflusst. In den 1990er Jahren schließlich kamen andere Füllstoffe auf den Markt, so das Kieselsäure-Silan-System in dem von Michelin patentierten Grünen Reifen, mit dem der Rollwiderstand und damit der Benzinverbrauch gesenkt wurde. So wurden die nanostrukturierten Industrieruße als vierte Innovationsgeneration von Reifenrußen entwickelt.
Hersteller
Zu den größten Herstellern von Industrierußen (Carbon Black) zählen unter anderem:
- Birla Carbon (ein Unternehmen des indischen Mischkonzerns Aditya Birla)
- Cabot Corporation (Spezialchemieunternehmen und einer der größten Rußhersteller)
- Orion Engineered Carbons (das ehemalige globale Carbon Black-Geschäft von Evonik Industries, seit 2011 eigenständig und seit 2014 gelistet an der New York Stock Exchange)
- Phillips Carbon Black (größter nationaler Rußhersteller Indiens)
Eigenschaften
Zwei fundamentale Eigenschaften des Industrierußes bestimmen die zwei Hauptanwendungsgebiete:
- die Verstärkungswirkung in Gummi (Natur- und Synthesekautschuk)
- die Farbe des Industrierußes als meistverbreitetes Schwarzpigment
- die Wärmeleitfähigkeit und die elektrische Leitfähigkeit
- die Beständigkeit gegen UV-Strahlung
Industrieruß besteht aus kleinen, meist kugelförmigen Teilchen (Primärpartikel oder auch Nodule). Diese haben meist eine Größe von 10 bis 300 Nanometern. Diese Primärpartikel sind zu kettenförmigen, teilweise klumpenartigen Aggregaten zusammengewachsen. Viele dieser Aggregate lagern sich zusammen und bilden so die Agglomerate. Bei diesen Dimensionen bestimmen weniger die chemische Zusammensetzung allein, sondern vorrangig Größe und Form der Partikel die Eigenschaften. Die Schüttdichte von Rußpulver beträgt etwa 80 kg/m3.
Optische, elektrische und magnetische Eigenschaften, sowie Härte, Zähigkeit und Schmelzpunkt von Nanomaterialien unterscheiden sich deutlich von denen der jeweiligen makroskopischen Festkörper. Daraus erklären sich die besonderen Eigenschaften von Ruß.
Die spezifische Oberfläche von Industrieruß beträgt etwa BET 10 bis 1500 m2/g.[11] Industrieruß kann gezielt mit speziellen Eigenschaften erzeugt werden, Einflussgrößen dafür sind: die Art des Herstellverfahrens, Änderungen von Prozessparametern wie Druck, Temperatur, Reaktionszeit, Eindüsung, Rohstoff. Es können die Größe der Primärteilchen und deren Aggregierung gezielt beeinflusst werden.
Die folgende Liste gibt eine Übersicht der Eigenschaften von Rußqualitäten.[12][13][14][15]
Rußart | Type of Carbon Black | Korndurchmesser nm | BET Oberfläche m2/g | pH-Wert | Zusammensetzung | Ausbeute % |
---|---|---|---|---|---|---|
Channel Black | 0–30 | 110–120 | 3 | –5,5C 95,6; H 0,6; S 0,2 | ; O 3,53-6 | |
Gasruß | Gas Black | 8–30 | 90–500 | 3 | –5,5C 96 | ; H 1 ; S 0,2 ; O 2,510–60 |
Ofenruß | Furnace Black | 10–110 | [16] bis 1500 (PEMFCS) | 24–6002,1–9[16] | C 97,9; H 0,4; S 0,6 | ; O 0,710–70 |
Flammruß | Lamp Black | 60–110 | 16–24 | 6 | –9C 98 | ; H 0,2; S 0,8 ; O 0,850[17] |
Spaltruß | Thermal Black | 100–500 | 10–50 | 7 | –9C 99,3; H 0,4; S 0,01; O 0,2 | 35–40 |
Acetylenruß | Acetylene Black | 30–50 | 20–80 | 4,8–7 | C 99,7; H 0,1; S 0,02; O 0,2 | 35–40 |
Herstellung
Industrieruß ist ein technisches Produkt, das durch unvollständige Verbrennung oder Pyrolyse von Kohlenwasserstoffen hergestellt wird.[18] Im Jahr 2006 wurden weltweit 8,1 Millionen Tonnen, im Jahr 2011 wurden 10,8 Millionen Tonnen produziert.[19][20]
Herstellungsverfahren

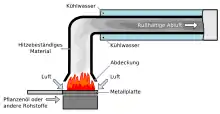
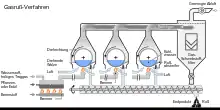
Industrieruß wird nach seiner Herstellung in Verbrennungsruß (entsteht durch unvollständige Verbrennung) und Spaltruß (entsteht durch thermische Zersetzung bzw. Pyrolyse) unterteilt.
- Acetylenruß (Acetylen-Black): durch unvollständige Verbrennung von Acetylen gewonnener Ruß, Acetylenruße sind Ruße hoher Reinheit.
- Thermalruß (Thermal-Black): Thermalruße entstehen in einem diskontinuierlichen oder zyklischen Prozess in speziellen Öfen, bei dem Erdgas oder Methan als am häufigsten verwendeter Rohstoff eingesetzt wird. Es können jedoch auch Mineralöle als Ausgangsmaterial verwendet werden. Das Erdgas wird in die innere Atmosphäre des Ofens injiziert, wo es in Ruß und Wasserstoff zersetzt wird (thermische Spaltung, Pyrolyse). Thermalruße haben die größte Primärteilchengrößen (größer als beim Flammrußverfahren) und gehören zu den Rußtypen mit der niedrigsten Oberfläche und Struktur. Da sie aus Erdgas hergestellt werden, sind sie sehr rein.[21]
- Channelruß (Channel-Black): Erdgas wird in vielen kleinen leuchtenden Flammen gegen wassergekühlte Eisenrinnen (Channels) verbrannt. Wegen der geringen Ausbeute (3 % – 6 %) wird dieses Verfahren nicht mehr angewandt.
- Flammruß (Lamp-Black): es ist die industrielle Variante zur Gewinnung von „Lampenschwarz“, Öl, Teer, Pech: harzreiche Hölzer werden verbrannt, dies ergibt grobe, dichte Ruße[22]
- Gasruß (Gas-Black): er wurde in den 1930er Jahren in Konkurrenz zu den Herstellern aus den USA von der Firma Degussa mit Unterstützung durch das nationalsozialistische Deutschland entwickelt.[23] In diesem Verfahren wird ein wasserstoffhaltiges Gas über erhitztes aromatenreiches Öl (meist Steinkohlen-Teeröle) geführt und das so mit Öldämpfen gesättigte Traggas (Trägergas) wird mit einem vor einer wassergekühlten Walze sitzenden Brenner verbrannt. Der dabei entstehende Ruß wird zu einen Teil direkt an der Walze abgeschieden, zum anderen Teil über einen Schwebstofffilter aus den Rauchgasen dem Endprodukt zugefügt. Das Gasruß-Verfahren arbeitet im Gegensatz zum Furnaceruß-Verfahren in einem für die Außenluft offenen System. Der Prozess kann daher lediglich über die Rohstoffzufuhr über das Traggas reguliert werden. Dennoch ist das Verfahren hinsichtlich der Partikelgröße sehr anpassungsfähig. Die Struktur dieses Rußes ist herstellungsbedingt locker und leicht dispergierbar.[24] Das Gasruß-Verfahren besitzt nur noch eine geringe Bedeutung (ca. 5 %). Es wird nahezu ausschließlich für Pigmente (Farbruß) verwendet, kaum als Zuschlagstoff für Reifen-Laufflächen.
- Furnaceruß (Furnace Black): das Furnacerußverfahren ist mit weltweit etwa 95 % das am meisten genutzte Verfahren. Dabei wird Industrieruß durch unvollständige Verbrennung der schweren Fraktionen der Erdöldestillation, meist Rückstände aus Fluid Catalytic Cracking- oder Steamcracken oder auch aus der Destillation von Steinkohlenteer, hergestellt.[25] Bei diesem Verfahren wird in einer Brennkammer (englisch furnace) ein Heißgas von 1200 bis 1800 °C durch Erdgas- oder Öl-Verbrennung erzeugt. In dieses Heißgas werden die Rußrohstoffe (aromatenreiche kohle- und erdölstämmige Ruß-Öle) eingedüst. Durch unvollkommene Verbrennung und thermische Spaltung (Pyrolyse) entsteht dabei Ruß, wobei die konkurrierenden Reaktionen von Keimbildung und Keimwachstum in der Reaktionszone durch die Ölbeladung und die Verweilzeit so gesteuert werden, dass Industrieruß mit den gewünschten Eigenschaften entsteht. Nach einer bestimmten Verweilzeit wird das Prozessgasgemisch durch Wassereindüsung schlagartig abgekühlt (gequencht) und der dabei entstehende Ruß wird nachfolgend in Schlauchfiltern abgetrennt. Die Anlagen werden kontinuierlich gefahren.
Für manche Anwendungen werden die Ruße nachbehandelt. Beispielsweise werden Ruße für hochfarbtiefe Lacke durch eine nachträgliche Oxidation hergestellt. Durch oxidischen Gruppen wird eine bessere Benetzung mit Bindemitteln und Harzen erreicht.
Füllstoffruß
In der Menge wird Industrieruß zu über 90 % als Füllstoff in der Gummiindustrie verwendet, davon etwa 70 % für Autoreifen und etwa 20 % für technische Gummiartikel wie Förderbänder, Keilriemen, Schläuche, Dämpfungselemente. Die Fahrzeugindustrie ist der mit Abstand größte Abnehmer von Industrieruß: Für Reifen verbrauchte sie im Jahr 2011 mehr als 7,8 Millionen Tonnen.[26] Für Autoreifen gibt es nahezu 40 verschiedene Industrierußtypen, die dem Gummi jeweils spezifische Eigenschaften vermitteln. International üblich ist die Klassifizierung von „Standardrußen“ nach der US-amerikanischen ASTM-Norm. Im Bereich der GUS-Staaten ist die abweichende GOST-Norm gebräuchlich. Industrieruße mit großer Oberfläche und entsprechender Verstärkungsaktivität (N1xx bis N3xx gemäß folgender Tabelle) werden in der Lauffläche von Reifen verarbeitet, um ihr die notwendige Härte und Abriebfestigkeit zu geben. Diese Gruppe von Industrierußen wird daher auch Tread Blacks, Hard Blacks oder Aktivruß genannt. Die Gruppe der halbaktiven Industrieruße (N5xx bis N7xx) wird für die Seitenwände (Karkasse) des Reifens verwendet, um die notwendige Federung und Dämpfung einzustellen. Sie machen den Gummi elastischer. Sie werden Carcass Blacks, Soft Blacks oder Halbaktivruße genannt. Typischerweise werden die Produktionsanlagen so ausgelegt, dass entweder die eine oder die andere Gruppe optimal produziert wird. Neben den weiteren Rohstoffen und insbesondere der Reifentechnologie selbst bestimmen die Eigenschaftsprofile der verwendeten Industrieruße im Reifen seine drei Kenngrößen: Rollwiderstand, Nassrutschfestigkeit und Abrieb.
Bezeichnung | Abkürzung | ASTM-Code | Anmerkung |
---|---|---|---|
Super Abrasion Furnace | SAF | N 110 | sehr abriebfester Typ |
Intermediate S.A.F. | ISAF | N 220 | Ruß für Reifenlaufflächen |
ISAF - Low Modulus | ISAF-LM | N 234 | ISAF Variante mit besseren Verarbeitungseigenschaften |
Super Conductive Furnace | SCF | N 294 | elektrisch leitfähiger Typ |
High Abrasion Furnace | HAF | N 330 | |
HAF - Low Structure | HAF-LS | N 326 | für Haftmischungen verwendeter Typ und Verbrauchmaximierung |
HAF - High Structure | HAF-HS | N 347 | ähnlich wie N 220 |
Fine Furnace | FF | N 440 | US-Typ (in Europa nicht gebräuchlich) |
Extra Conductive Furnace | XCF | N 472 | nicht mehr gebräuchlicher Typ |
FEF - Low Structure | FEF-LS | N 539 | |
Fast Extrusion Furnace | FEF | N 550 | Einsatz z. B. in Profilen |
FEF - High Structure | FEF-HS | N 568 | |
High Modulus Furnace | HMF | N 601 | US-Typ (in Europa nicht gebräuchlich) |
General Purpose Furnace | GPF | N 660 | Karkassenruß |
SRF - Low Modulus, non staining | SRF-LM-NS | N 762 | Typ für nicht verfärbende technische Artikel |
Semi Reinforcing Furnace | SRF | N 770 | |
Multi Processing Furnace | MPF | N 785 | selten eingesetzter Typ |
Fine Thermal | FT | N 880 | US-Typ (in Europa eher nicht gebräuchlich) |
Medium Thermal | MT | N 990 | inaktivster Typ |
Leitfähigkeitsruß
Besitzt der Ruß kleine „Primärteilchen“ und hat weitverzweigte Aggregate, so besitzt er eine elektrische Leitfähigkeit für unterschiedliche Anwendungen. Diese Sorten und Produktqualitäten werden als Leitfähigkeitsruß geführt. Er wird in der Elektroindustrie und als Rohstoff für Ingenieurkeramiken genutzt, sowie für Elektrodenmaterial. Eine spezielle Anwendung besteht in der Herstellung elektrisch leitfähiger Druckfarben, die besonders als Sicherheitsmerkmal für Dokumente geeignet sind. Eine andere Anwendung ist der Druck von Leiterbahnen mit schwarzen leitenden Druckfarben.
Acetylenruß wird als Zusatz bei der Herstellung von Kathoden für Zink-Kohle-Batterien verwendet. Die Zugabe von Acetylenruß erhöht die elektrische Leitfähigkeit des elektrochemisch aktiven Mangandioxids (Braunstein) und erlaubt eine bessere Aufnahme von Elektrolytlösung in der Kathode.
Farbruß
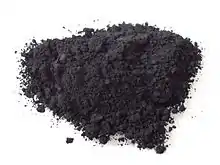
Ruß wird als Schwarzpigment (C. I. Pigment Black 7 und 6 Lamp Black)[27] für Druckfarben, Tuschen, Lacke und zur Einfärbung von Kunststoffen (insbesondere als UV-Schutz) genutzt. In Spezialprodukten wie Maskara, Graberde, Dekorpapier und Fasern dient er gleichfalls als Schwarzpigment.
Farbruße sind nanoteilige Ruße, die durch ihre Feinheit zunehmend den braunen Grundton verlieren. Ihre Verwendung erfolgt bei der Herstellung schwarzer Druckfarben der unterschiedlichsten Druckverfahren. Da die gedruckten Schichten sehr dünn und teilweise transparent sind, ist eine besondere Qualität der Ruße erforderlich. Für eine ausreichende Farbtiefe (Schwarzton) von preiswerteren Rußqualitäten, insbesondere bei Zeitungsdruckfarben, wird oft mit Blaupigmenten geschönt, um einen Rot-/ Braunstich zu unterdrücken. Ruße für hochfarbtiefe Lacke werden durch nachträgliche Oxidation des Basisrußes hergestellt. Die oxidischen Gruppen ergeben eine bessere Einarbeitung zu den Bindemitteln und Harzen. Ruß wird als farbgebendendes Pigment bei den meisten Tätowierfarben, nicht nur bei Schwarz, verwendet.
Ökologie und Toxikologie
Industrieruß wird so breit angewendet, dass er überall vorkommt, zunächst jedoch meist eingebettet in die jeweilige Grundsubstanz. Er gelangt durch Abrieb von Reifen oder aus Druckfarben recycelter Zeitungen in die Umwelt. Die Partikelgröße bedingt eine Einordnung als Feinstaub.
Relevanz ist auch aufgrund der Herstellverfahren oder Nanomaterial denkbar. Bei der Herstellung wird teilweise PAK-haltiges und somit krebserregendes Ausgangsmaterial eingesetzt. Es können je nach den Prozessbedingungen Rückstände des Ausgangsmaterials im Industrieruß verbleiben. Diese Rückstände werden durch die hohe Oberflächenaktivität (Van-der-Waals-Kräfte) des Industrierußes fest adsorbiert. Die International Agency for Research on Cancer (IARC) bewertet die Toxizität von Carbon Black: „Carbon black is possibly carcinogenic to humans (Group 2B)“.[28]
Kurzzeitige Exposition mit hohen Konzentrationen von Carbon Black (Staub) kann möglicherweise durch eine mechanische Irritation die Beeinträchtigung der oberen Atemwege auslösen. Industrieruß wird als für Menschen möglicherweise karzinogen angesehen. Zwar gibt es ausreichend aussagekräftige Untersuchungen mit Tieren, aber keine entsprechenden Studien mit Menschen.[28] Die wesentlichen Aussagen zur Karzinogenität in Tierstudien rühren von Studien an Ratten, zwei davon zur chronischen Inhalation und zwei zum direkten Einflößen in die Luftröhre. Diese Studien zeigten signifikant erhöhtes Auftreten von Lungenkrebs an den untersuchten Ratten.[28] Eine weitere Inhalationsstudie, diesmal an Mäusen, zeigte keine Zunahme des Lungenkrebses.[28] Epidemiologische Daten gibt es über drei verschiedene Kohorten von Produktionsarbeitern. Zwei Studien, eine aus Großbritannien und eine aus Deutschland (Produktionswerk Kalscheuren bei Köln), mit jeweils mehr als 1000 Arbeitern in jeder untersuchten Gruppe zeigten eine erhöhte Mortalität an Lungenkrebs.[28] Eine weitere Studie an über 5000 Industrierußarbeitern aus den USA zeigte diese erhöhte Mortalität nicht.[28]
Industrieruß (Carbon Black) wurde 2016 von der Europäischen Union gemäß der Verordnung (EG) Nr. 1907/2006 (REACH) im Rahmen der Stoffbewertung in den fortlaufenden Aktionsplan der Gemeinschaft (CoRAP) aufgenommen. Hierbei werden die Auswirkungen chemischer Stoffe auf die menschliche Gesundheit bzw. die Umwelt neu bewertet und ggf. Folgemaßnahmen eingeleitet. Ursächlich für die Aufnahme von Industrieruß in die Bewertung waren die Besorgnisse der Verbraucher, kumulative Exposition, Exposition empfindlicher Bevölkerungsgruppen, Exposition von Arbeitnehmern, hoher (aggregierter) Tonnage und weit verbreiteter Verwendung sowie der vermuteten Gefahren durch krebserregende Eigenschaften und der möglichen Gefahr durch reproduktionstoxische Eigenschaften. Die Neubewertung soll ab 2022 von Frankreich durchgeführt werden.[29]
Unerwünschter Ruß
Ruß tritt bei Verbrennungsvorgängen oft als unerwünschtes Produkt auf. Bei unvollständiger Verbrennung entstehen ölige Ruße und Aerosole. Solcher Ruß (englisch soot) hat im Tierversuch das Potential gezeigt, Krebs auszulösen. Die Krebsgefährdung verursachen hierbei jedoch die bei unvollständiger Verbrennung entstehenden polycyclischen aromatischen Kohlenwasserstoffe (PAK).
In Ofen-Heizungen setzt sich als Produkt der unvollständigen Verbrennung Ruß im Kaminrohr ab und kann zusammen mit dort kondensiertem Teer zum Kaminbrand führen. Um das zu verhindern, fegt der Schornsteinfeger (Rauchfangkehrer) regelmäßig die Kamin-Innenwände mit einer harten Metallbürste.
Der Dieselruß in Abgasen von Kraftfahrzeugen mit Dieselmotor hat eine ähnliche Zusammensetzung, enthält abhängig vom Aromatengehalt des Diesels PAK und ist daher ein Luftschadstoff. Je besser die Zerstäubung des Diesels beim Einspritzen, desto kleiner und lungengängiger (und damit riskanter) sind die Rußpartikel.
Eine 2020 veröffentlichte Studie gelangt durch Klimasimulationen zum Schluss, dass die durch Rußpartikel veränderte Wolkenbildung zur Erderwärmung beiträgt.[30][31]
Messtechnischer Nachweis
Die Emissionsmessung von Ruß aus Feuerungsanlagen kann mittels Bacharach-Methode erfolgen.[32] Mit ihr wird halbquantitativ die Rußzahl bestimmt. Ein vergleichbares Verfahren zur Bestimmung der Rußzahl basiert auf der Änderung des Reflexionsvermögens eines beaufschlagten Messfilters.[33]
Bei der gezielten Immissionsmessung von Ruß wird auf einem Filter abgeschiedener Kohlenstoff erhitzt und die optische Transmission des Filters gemessen.[34] Bei einem anderen Verfahren wird der auf einem Filter abgeschiedene elementare Kohlenstoff vom organischen Kohlenstoff durch Flüssigextraktion und Thermodesorption getrennt, um anschließend verbrannt zu werden, damit das gebildete Kohlenstoffdioxid coulometrisch ermittelt werden kann.[35] In der Regel erfolgt im Rahmen von Immissionserhebungen keine separate Messung von Ruß.[36]
Literatur
- Roop C. Bansal, Meng-Jiao Wang, Jean-Baptiste Donnet: Carbon Black: Science and Technology. 2. Auflage. Marcel Dekker, 1993, ISBN 0-8247-8975-X.
Weblinks
- Carbon Black: A users guide der International Carbon Black Association. (PDF; 1,03 MB), auf cancarb.com, abgerufen am 26. August 2016.
- Carbon Black – Struktur und Eigenschaften. (PDF; 555 kB), auf duepublico.uni-duisburg-essen.de, abgerufen am 26. August 2016.
Einzelnachweise
- Elfenbeinschwarz. Auf materialarchiv.ch, abgerufen am 16. August 2016.
- Johann Carl Leuchs (Hrsg.): Vollständige Farben und Färberkunde. 3. Band, 2. Auflage, Verlag C. Leuchs, Nürnberg 1846.
- Ferdinand Schubert: Handbuch der Forstchemie. Brockhaus, Leipzig 1848, S. 658 ff.
- Yingxing Song, E-tu Zen Sun, Shiou-chuan Sun: Chinese Technology in the Seventeenth Century. Dover Publications, 1997, ISBN 0-486-29593-1, S. 285.
- Kurt Arndt, J. Zellner: Die künstlichen Kohlen. 2. Auflage. Springer, 1932, S. 50. (Reprint: ISBN 978-3-642-89488-6)
- Hellmut Gnamm, K. Grafe, L. Jablonski u. a.: Handbuch der Gerberei und Lederfabrikation. 3. Band, 1. Teil, Springer, 1936, S. 544. (Reprint: ISBN 978-3-7091-2211-2)
- Was ist Carbon Black. (Memento des Originals vom 16. August 2016 im Internet Archive) Info: Der Archivlink wurde automatisch eingesetzt und noch nicht geprüft. Bitte prüfe Original- und Archivlink gemäß Anleitung und entferne dann diesen Hinweis. (PDF; 306 kB), auf riskcart.wzu.uni-augsburg.de, abgerufen 16. August 2016.
- Rußbrenner. (Memento des Originals vom 16. August 2016 im Internet Archive) Info: Der Archivlink wurde automatisch eingesetzt und noch nicht geprüft. Bitte prüfe Original- und Archivlink gemäß Anleitung und entferne dann diesen Hinweis. Auf user.hosting-agency.de, abgerufen am 16. August 2016.
- Kalscheuren – Stammsitz der Industrierußaktivitäten. Auf geschichte.evonik.de, abgerufen am 18. März 2013.
- John J. McKetta Jr.: Encyclopedia of Chemical Processing and Design: Volume 6, Marcel Dekker, 1978, ISBN 0-8247-2456-9, S. 189.
- Alessandro Lavacchi, Hamish Miller, Francesco Vizza: Nanotechnology in Electrocatalysis for Energy. Springer, 2013, ISBN 978-1-4899-8058-8, S. 121 f.
- Hans G. Hirschberg: Handbuch Verfahrenstechnik und Anlagenbau: Springer, 1999, S. 222. (Reprint: 2014, ISBN 978-3-642-63550-2)
- Joachim Voigt: Die Stabilisierung der Kunststoffe gegen Licht und Wärme. Springer, 1966, S. 188. (Reprint: ISBN 978-3-642-52098-3)
- Carbon Black. (PDF; 856 kB), auf monographs.iarc.fr, abgerufen am 26. August 2016.
- J. V. Koleske: Paint and Coating Testing Manual. Fourteenth Edition of the Gardner-Sward Handbook, ASTM Int., 1995, ISBN 0-8031-2060-5, S. 181.
- H. S. Katz, J. V. Mileski: Handbook Of Fillers For Plastics. Van Nostrand Reinhold, 1987, ISBN 0-442-26024-5, S. 393 f.
- Martin Bertau, Armin Müller, Peter Fröhlich, Michael Katzberg: Industrielle Anorganische Chemie. 4. Auflage. Wiley, 2013, ISBN 978-3-527-33019-5, S. 654.
- Brockhaus ABC Chemie. F. A. Brockhaus Verlag, Leipzig 1965, S. 1219.
- What is Carbon Black ? Auf carbon-black.org, abgerufen am 18. März 2013.
- Carbon Black World Data Book 2012. Auf researchandmarkets.com, abgerufen am 18. März 2013.
- Unsere Spezial Carbon Blacks - PentaCarbon GmbH. In: pentacarbon.de. Abgerufen am 10. April 2018.
- Nicholas Eastaugh, Valentine Walsh, Tracey Chaplin, Ruth Siddall: Pigment Compendium. Routledge, 2008, ISBN 978-0-7506-8980-9, S. 222.
- Peter Hayes: Die Degussa im Dritten Reich.
- Deutsche Gasrußwerke GmbH & Co.
- Fritz Röthemeyer, Franz Sommer: Kautschuktechnologie. 2. Auflage. Carl Hanser Verlag, München/ Wien 2006, ISBN 3-446-40480-5, S. 246–247.
- Marktstudie Carbon Black (Ruß). Auf ceresana.com, abgerufen am 26. April 2013.
- Robert Leach: The Printing Ink Manual. Fourth Edition, Van Nostrand Reinhold, 1988, ISBN 978-94-011-7099-4, S. 154.
- Eileen D. Kuempel, Tom Sorahan: Identification of Research Needs to Resolve the Carcinogenicity of High-priority IARC Carcinogens: Views and Expert Opinions of an IARC/NORA Expert Group Meeting. Lyon, France, 30. Juni–2. Juli 2009. In: IARC Technical Publication. Band 42. International Agency for Research on Cancer, 2010, ISBN 978-92-832-2449-5, S. 61–72 (iarc.fr [PDF; 1,5 MB; abgerufen am 30. August 2012]).
- Community rolling action plan (CoRAP) der Europäischen Chemikalienagentur (ECHA): Carbon black, abgerufen am 11. September 2021.
- Simone Ulmer: Russpartikel beeinflussen Erderwärmung. In: ETH Zürich. 3. November 2020, abgerufen am 1. Dezember 2020.
- Ulrike Lohmann, Franz Friebel, Zamin A. Kanji et al.: Future warming exacerbated by aged-soot effect on cloud formation. In: Nat. Geosci. Band 13, 29. September 2020, S. 674–680, doi:10.1038/s41561-020-0631-0.
- Franz Joseph Dreyhaupt (Hrsg.): VDI-Lexikon Umwelttechnik. VDI-Verlag Düsseldorf, 1994, ISBN 3-18-400891-6, S. 182.
- VDI 2066 Blatt 8:1995-09 Messen von Partikeln; Staubmessung in strömenden Gasen; Messung der Rußzahl an Feuerungsanlagen für Heizöl EL (Measurement of particles; Dust measurement in flowing gases; Measurement of smoke number in furnaces designed for EL-type fuel oil). Beuth Verlag, Berlin, S. 3.
- DIN EN 16909:2017-06 Außenluft; Messung von auf Filtern gesammeltem elementarem Kohlenstoff (EC) und organisch gebundenem Kohlenstoff (OC); Deutsche Fassung EN 16909:2017. Beuth Verlag, Berlin, S. 11.
- VDI 2465 Blatt 1:1996-12 Messen von Ruß (Immission); Chemisch-analytische Bestimmung des elementaren Kohlenstoffes nach Extraktion und Thermodesorption des organischen Kohlenstoffes (Measurement of soot (immission); Chemical analysis of elemental carbon by extraction and thermal desorption of organic carbon). Beuth Verlag, Berlin, S. 2–3.
- Franz Joseph Dreyhaupt (Hrsg.): VDI-Lexikon Umwelttechnik. VDI-Verlag Düsseldorf, 1994, ISBN 3-18-400891-6, S. 1001.