Schweißen
Das Schweißen ist eine Gruppe von Fügeverfahren zum dauerhaften Fügen (Verbinden) von zwei oder mehr Werkstücken. Das Schweißen gilt als wichtigste Gruppe der Fügeverfahren. Nach DIN 8580 Hauptgruppe 4 Teil 6 wird es als Fügen durch Schweißen definiert. Die meisten Schweißverfahren eignen sich auch zum Beschichten, was in der Praxis und Fachliteratur als Auftragschweißen bezeichnet wird – definiert in der DIN 8580 Hauptgruppe 5 Teil 6 als Beschichten durch Schweißen.
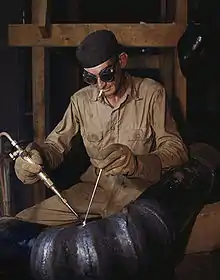
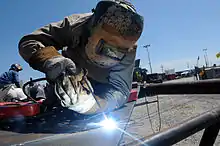
Unter Schweißen versteht man gemäß EN 14610[1] und DIN 1910-100[2] „das unlösbare Verbinden von Bauteilen unter Anwendung von Wärme und/oder Druck, mit oder ohne Schweißzusatzwerkstoffe“. Die Zusatzwerkstoffe werden üblicherweise in Form von Stäben oder Drähten zugeführt, abgeschmolzen und erstarren in der Fuge zwischen den Fügepartnern, um so die Verbindung zu erzeugen. Sie entsprechen somit dem Lot beim Löten oder dem Klebstoff beim Kleben. Die nötige Schweißwärme wird von außen zugeführt oder entsteht beim Reibschweißen durch Reibung an der Fuge im Material selbst. Schweißhilfsstoffe, wie Schutzgase, Schweißpulver, Flussmittel, Vakuum (beim Elektronenstrahlschweißen) oder Pasten, können das Schweißen erleichtern oder auch erst möglich machen. Schweißen kann durch Wärmezufuhr bis zum Schmelzen des Werkstoffs oder durch Wärmezufuhr und zusätzliche Krafteinwirkung (Druck) auf das Werkstück erfolgen.
Das Schweißen zählt zu den stoffschlüssigen Verbindungsmethoden zusammen mit dem Löten und Kleben. Beim Schweißen werden Verbindungen mit hoher Festigkeit erzeugt; beim Schmelzschweißen durch das lokale Schmelzen der zu verbindenden Bauteile. Beim verwandten Löten wird dagegen nur das Lot flüssig, während die Bauteile zwar erwärmt, aber nicht geschmolzen werden. Lötverbindungen weisen daher eine geringere Festigkeit auf, eignen sich aber auch für Verbindungen von Werkstoffen mit stark unterschiedlichem Schmelzpunkt. Solche Werkstoffpaarungen können jedoch auch mit dem Pressschweißen hergestellt werden.
Das Schweißen ist eines der wichtigsten und am weitesten verbreiteten Fügeverfahren, da es deutlich kostengünstiger ist als das Schrauben oder Nieten und deutlich festere Verbindungen ermöglicht als das Löten oder Kleben.
Geschichte des Schweißens
Gliederung der Schweißverfahren
Die Einteilung der Schweißverfahren kann vorgenommen werden nach
- Art der auf das Werkstück einwirkenden Energie
- thermische Energie, etwa beim Schmelzschweißen
- thermische Energie mit gleichzeitigem oder anschließendem Zusammenpressen der Werkstücke, etwa bei vielen Widerstandsschweißverfahren
- mechanische Energie, etwa beim Kaltpressschweißen
- mechanische Energie, die in thermische Energie umgewandelt wird, etwa beim Reibschweißen
- Art des Grundwerkstoffs
- Metallen
- Thermoplasten
- andere Werkstoffe und Kombinationen von Werkstoffen, wie beispielsweise Glas
- Zweck des Schweißens
- Verbindungsschweißen dient dem Zusammenfügen von Werkstücken
- Auftragschweißen dient dem Beschichten eines Werkstückes; sind Grund- und der Auftragwerkstoff unterschiedlich, wird weiter unterschieden in das Auftragschweißen von
- Panzerungen
- Plattierungen
- Pufferschichten
- physikalischem Ablauf des Schweißens
- Schmelzschweißen ist Schweißen bei örtlich begrenztem Schmelzfluss, ohne Anwendung von Kraft mit oder ohne gleichartigem Schweißzusatz (ISO 857-1). Im Gegensatz zum Löten wird dabei die Liquidustemperatur der Grundwerkstoffe überschritten. Prinzipiell können alle Materialien, die in die schmelzflüssige Phase überführbar sind, durch Schmelzschweißen verbunden werden. Bei vielen Verfahren wird zusätzliches Material etwa in Form eines Schweißdrahtes zugeführt.
- Pressschweißen bringt die zu verbindenden Werkstoffe durch unterschiedliche Energieformen auf die erforderliche Schweißtemperatur, worauf die Verbindung unter Einwirkung einer Kraft hergestellt wird. Das Pressschweißen kommt ohne das Zuführen von zusätzlichem Material wie Schweißdraht aus.[4]
- Grad der Mechanisierung
- Handschweißen
- als rein manuelles Schweißen
- als teilmechanisiertes Schweißen, bei dem der Zusatzwerkstoff und die Hilfsstoffe (Schutzgase) mechanisiert zugeführt werden, aber der Brenner von Hand bewegt wird,
- vollmechanisches Schweißen
- (voll-)automatisiertes Schweißen[2]
Schweißbarkeit eines Bauteils
Um ein Bauteil schweißen zu können, muss es schweißbar sein. Darunter versteht man, dass durch das Zusammenwirken der Eignung des Werkstoffs zum Schweißen (Schweißeignung), einer schweißgeeigneten Konstruktion (Schweißsicherheit) und einer geeigneten Fertigungsorganisation (Schweißmöglichkeit) Einzelteile zu Bauteilen mit gewünschter Qualität zusammengeschweißt werden können. Wird dies nicht beachtet, kann das zur Unbrauchbarkeit des Bauteils führen.
Schweißeignung eines Werkstoffs
Infolge der thermischen Einwirkung auf die Schweißteile während des Schweißens ändern sich deren metallurgische Eigenschaften. Je nach Materialzusammensetzung und Art des Temperaturzyklus können Gefüge entstehen, die negative Qualitätseinflüsse haben. Die Schweißeignung beschreibt, inwieweit ein Werkstoff unter jeweils bestimmten Bedingungen qualitativ befriedigend durch Schweißen verbunden werden kann.
Auswahl eines Schweißverfahrens
Für das Fügen von Einzelteilen zum Werkstück stehen zahlreiche Schweißverfahren zur Verfügung, von denen im konkreten Falle eins gewählt werden muss. Bei der Auswahl sollten folgende Gesichtspunkte in Betracht gezogen werden: Aus verfahrenstechnologischer Sicht spielen der Werkstoff, die Bauteilgeometrie, die Zugänglichkeit zur Schweißstelle und die mögliche Schweißposition eine Rolle, ebenso die Qualitätsanforderungen an das geschweißte Produkt. Aus wirtschaftlicher Sicht sind die Stückzahl der herzustellenden Werkstücke, die Kosten für die erforderlichen Schweißeinrichtungen und diejenigen für die Durchführung der Fertigungsarbeiten bei der Verfahrenswahl zu berücksichtigen.
Einteilung der Schweißprozesse in Prozessnummern
| |||
Bereich | Schweißen | ||
Titel | Schweißen und verwandte Prozesse - Liste der Prozesse und Ordnungsnummern | ||
Kurzbeschreibung: | In dieser Norm wird eine numerische Einteilung für Schweiß-, Schneid-, Ausfug-, Hartlöt-, Weichlöt- und Fugenlötverfahren festgelegt. | ||
Letzte Ausgabe | März 2011 |
Die Festlegung umfasst die Hauptgruppen der Prozesse (eine Ziffer), Gruppen (zwei Ziffern) und Untergruppen (drei Ziffern). Die Referenznummer besteht aus maximal drei Ziffern.
Die Referenznummern der Schweißprozesse | ||
---|---|---|
Hauptgruppennummer | Gruppennummer | Untergruppennummer |
1 Lichtbogenschweißen | 11 Metall-Lichtbogenschweißen ohne Gasschutz | 111 Lichtbogenhandschweißen |
112 Schwerkraft-Lichtbogen-schweißen | ||
114 Metall-Lichtbogenschweißen mit Fülldrahtelektrode ohne Schutzgas | ||
12 Unterpulverschweißen | 121 Unterpulverschweißen mit Massivdrahtelektrode | |
122 Unterpulverschweißen mit Massivbandelektrode | ||
124 Unterpulverschweißen mit Metallpulverzusatz | ||
125 Unterpulverschweißen mit Fülldrahtelektrode | ||
126 Unterpulverschweißen mit Füllbandelektrode | ||
13 Metall-Schutzgasschweißen | 131 Metall-Inertgasschweißen mit Massivdrahtelektrode | |
132 Metall-Inertgasschweißen mit schweißpulvergefüllter Drahtelektrode | ||
133 Metall-Inertgasschweißen mit metallpulvergefüllter Drahtelektrode | ||
135 Metall-Aktivgasschweißen mit Massivdrahtelektrode | ||
136 Metall-Aktivgasschweißen mit schweißpulvergefüllter Drahtelektrode | ||
138 Metall-Aktivgasschweißen mit metallpulvergefüllter Drahtelektrode | ||
14 Wolfram-Schutzgasschweißen | 141 Wolfram-Inertgasschweißen mit Massivdraht- oder Massivstabzusatz; WIG-Schweißen | |
142 Wolfram-Inertgasschweißen ohne Schweißzusatz | ||
143 Wolfram-Inertgasschweißen mit Fülldraht- oder Füllstabzusatz | ||
145 Wolfram-Schutzgasschweißen mit reduzierenden Gasanteilen im ansonsten inerten Schutzgas und Massivdraht- oder Massivstabzusatz | ||
146 Wolfram-Schutzgasschweißen mit reduzierenden Gasanteilen im ansonsten inerten Schutzgas und Fülldraht- oder Füllstabzusatz | ||
147 Wolfram-Schutzgasschweißen mit aktiven Gasanteilen im ansonsten inerten Schutzgas | ||
15 Plasmaschweißen | 151 Plasma-Metall-Inertgasschweißen | |
152 Pulver-PlasmaLichtbogenschweißen | ||
153 Plasma-Stichlochschweißen | ||
154 Plasmastrahlschweißen | ||
155 Plasmastrahl-Plasmalichtbogen-Schweißen | ||
185 Lichtbogenschweißen mit magnetisch bewegtem Lichtbogen | ||
2 Widerstandsschweißen | 21 Widerstandspunktschweißen | 211 indirektes Widerstandspunktschweißen |
212 direktes Widerstands-punktschweißen | ||
22 Rollennahtschweißen | 221 Überlapp-Rollennahtschweißen | |
222 Quetschnahtschweißen | ||
223 Rollennahtschweißen mit Kantenvorbereitung | ||
224 Rollennahtschweißen mit Drahtelektrode | ||
225 Folien-Stumpfnahtschweißen | ||
226 Folien-Überlappnahtschweißen | ||
23 Buckelschweißen | 231 einseitiges Buckelschweißen | |
232 zweiseitiges Buckelschweißen | ||
24 Abbrennstumpfschweißen | 241 Abbrennstumpfschweißen mit Vorwärmung | |
242 Abbrennstumpfschweißen ohne Vorwärmung | ||
25 Pressstumpfschweißen | ||
26 Widerstandsbolzenschweißen | ||
27 Widerstandspressschweißen mit Hochfrequenz | ||
29 andere Widerstands-schweißverfahren | ||
3 Gasschmelzschweißen | 31 Gasschweißen mit Sauerstoff-Brenngas-Flamme | 311 Gasschweißen mit Sauerstoff-Acetylen-Flamme |
312 Gasschweißen mit Sauerstoff-Propan-Flamme | ||
313 Gasschweißen mit Sauerstoff-Wasserstoff-Flamme | ||
4 Pressschweißen | 41 Ultraschallschweißen | |
42 Reibschweißen | 421 Reibschweißen mit kontinuierlichem Antrieb | |
422 Reibschweißen mit Schwungradantrieb | ||
423 Reibbolzenschweißen | ||
43 Rührreibschweißen | ||
44 Schweißen mit hoher mechanischer Energie | 441 Sprengschweißen | |
442 Magnetpulsschweißen | ||
45 Diffusionsschweißen | ||
47 Gaspressschweißen | ||
48 Kaltpressschweißen | ||
49 Heißpressschweißen | ||
5 Strahlschweißen | 51 Elektronenstrahlschweißen | 511 Elektronenstrahlschweißen unter Vakuum |
512 Elektronenstrahlschweißen in Atmosphäre | ||
513 Elektronenstrahlschweißen unter Schutzgas | ||
52 Laserstrahlschweißen | 521 Festkörper-Laserstrahlschweißen | |
522 Gas-Laserstrahlschweißen | ||
523 Dioden-Laserstrahlschweißen, Halbleiter-Laserschweißen | ||
7 andere Schweißverfahren | 71 aluminothermisches Schweißen | |
72 Elektroschlackeschweißen | 721 Elektroschlackeschweißen mit Bandelektrode | |
722 Elektroschlackeschweißen mit Drahtelektrode | ||
73 Elektrogasschweißen | ||
74 Induktionsschweißen | 741 induktives Stumpfschweißen | |
742 induktives Rollennahtschweißen | ||
743 induktives Hochfrequenzschweißen | ||
75 Lichtstrahlschweißen | 753 Infrarotschweißen | |
78 Bolzenschweißen | 783 Hubzündungs-Bolzenschweißen mit Keramikring oder Schutzgas | |
784 Kurzzeit-Bolzenschweißen mit Hubzündung | ||
785 Kondensatorentladungs-Bolzenschweißen mit Hubzündung | ||
786 Kondensatorentladungs-Bolzenschweißen mit Spitzenzündung | ||
787 Bolzenschweißen mit Ringzündung |
Schweißverbindungsqualität
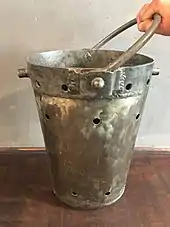
Durch Schweißen sollen Bauteile so miteinander verbunden werden, dass diese die an sie gestellten Anforderungen über eine erwartete Lebensdauer erfüllen können. Dazu müssen die Verbindungen anforderungsgerechte Qualitätskriterien oder Gütemerkmale erfüllen. Generelle Festlegungen zu den Gütemerkmalen können nicht getroffen werden, denn diese sind immer eng an die jeweiligen Bauteilanforderungen im Einsatz gebunden.
Ausreichende Qualität ist dann zu erwarten, wenn auftretende Unregelmäßigkeiten der Schweißnaht, die während oder nach dem Schweißen entstehen, für die Nutzung des geschweißten Bauteils toleriert werden können. Sind sie nicht mehr akzeptabel, werden die Unregelmäßigkeiten als Verbindungsfehler bezeichnet.[5]
Schweißfehler
Schweißnahtfehler
Qualität des Pressschweißens
Qualität des Schmelzschweißens
Qualitätssicherung beim Schweißen
Schmelzschweißverfahren
Vorbereitung – Schweißstoß
Schweißteile werden durch sogenannte Schweißstöße verbunden, die oftmals eine spezielle Fugenvorbereitung benötigen. Der Bereich, in dem Schweißteile miteinander vereinigt werden, wird Schweißstoß genannt. Die Stoßarten unterscheiden sich je nach konstruktiver Anordnung der Teile und der Fugenvorbereitung, die eine fachgerechte Ausführung und Prüfung der Schweißnaht ermöglicht.[6]
- Stumpfstoß
- Überlappstoß
- T-Stoß
Durchführung – Schweißposition
Je nach Anordnung der Schweißteile und der Zugänglichkeit des Brenners und der Schweißelektrode zur Naht ergeben sich beim Schweißen in der Norm DIN EN ISO 6947:2011-08 definierte Schweißpositionen.[7]
Gasschmelzschweißen
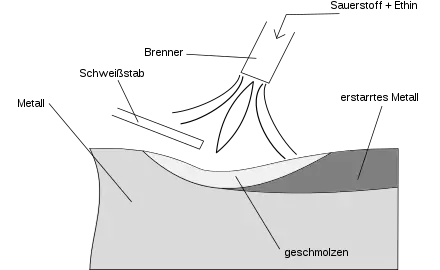
Beim Gasschmelzschweißen oder Autogenschweißen wird das Metall durch die Verbrennung von Brenngasen erhitzt. Das in der Regel verwendete Brenngas ist Acetylen (Ethin), welches mit Sauerstoff in einem Acetylen-Sauerstoff-Gemisch die Schweißflamme erzeugt. Die Temperatur der Flamme beträgt dabei etwa 3200 °C. In der Regel wird ein Schweißdraht als Zusatzwerkstoff verwendet.
Das Gasschmelzverfahren eignet sich sowohl für Schweißarbeiten im Werk als auch auf der Baustelle. Das langsame Verfahren eignet sich in erster Linie zum Schweißen dünner Bleche und einiger NE-Metalle sowie für Reparatur- und Auftragsschweißung. Besonders im Heizungs-, Installations- und Rohrleitungsbau kommt dieses Verfahren zur Anwendung, hat aber nur noch geringe Bedeutung.[8]
Lichtbogenschweißen
Beim Lichtbogenschweißen brennt ein elektrischer Lichtbogen (Schweißlichtbogen) zwischen Werkstück und einer Elektrode, die je nach Verfahren abschmelzen kann und dann gleichzeitig als Zusatzwerkstoff dient oder nicht-abschmelzend ist.
Die wichtigsten Verfahren sind
- das Lichtbogenhandschweißen
- das Schutzgasschweißen mit zahlreichen Untervarianten
- und das Unterpulver-Schweißen.
Durch den Elektronenbeschuss heizt sich die Anode (Pluspol) stärker auf. Bei den meisten Schweißverfahren betreibt man verzehrende Elektroden als Anoden, das Werkstück also als Kathode (Minuspol). Bei umhüllten Stabelektroden hängt die Polarität von der Elektrodenumhüllung ab. Besteht die Umhüllung aus schlecht ionisierbaren Bestandteilen, wie dies bei basischen Elektroden der Fall ist, wird die Elektrode am heißeren Pluspol geschweißt, anderenfalls wegen der geringeren Strombelastung am Minuspol.
Siehe auch: Sensoren für das Lichtbogenschweißen
Lichtbogenhandschweißen
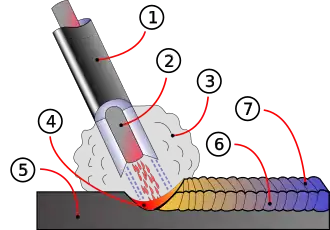
Das Lichtbogenhandschweißen oder Elektrodenschweißen ist ein rein manuelles Verfahren (Handschweißen) mit abschmelzender Elektrode. Diese Stabelektroden besitzen eine Umhüllung, die ebenfalls abschmilzt und teils verdampft und dabei Schutzgase und Schlacke bildet, die beide die Schmelze vor ungewollten Einflüssen der Umgebung schützen. Die Schlacke kann außerdem die metallurgische Zusammensetzung der Schmelze ändern, sodass das Verfahren an viele Anwendungsfälle angepasst werden kann. Es ist sehr einfach und mit geringen Investitionen in die Anlagen verbunden, aber nicht besonders produktiv, sodass es vor allem bei Reparaturarbeiten, in Werkstätten und auf Baustellen genutzt wird.
Schutzgasschweißen (SG)
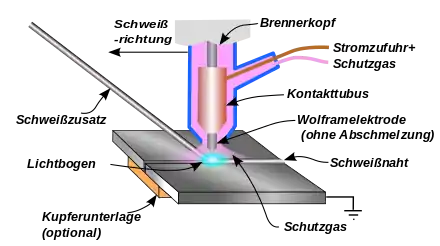
Beim Schutzgasschweißen werden Schutzgase verwendet, die die Elektrode und die Schmelze umströmen. Die Zufuhr der Schutzgase ist im Brenner integriert. Die Verfahren des Schutzgasschweißens sind produktiver als das Elektrohandschweißen und lassen sich auch mechanisieren, manche sogar vollständig automatisieren. Die Kosten sind noch gering und die Flexibilität in der Anwendung deutlich besser als die produktiveren Strahlverfahren (Laser-/Elektronenstrahlschweißen). Das Schutzgasschweißen ist daher bezüglich der Anwendungshäufigkeit die wichtigste Gruppe der Schweißverfahren.
- Metallschutzgasschweißen (MSG): Hier schmilzt die Elektrode ab und besteht aus demselben oder ähnlichem Werkstoff wie das Werkstück (wie beim Elektrohandschweißen)
- Metall-Inertgas-Schweißen (MIG): Hier werden inerte Gase verwendet, also solche, die keine chemischen Reaktionen mit der Schmelze eingehen. Es wird vor allem für Nichteisenmetalle und hochlegierte Stähle genutzt.
- Metall-Aktivgas-Schweißen (MAG): Hier werden reaktionsfreudige Gase verwendet, um die Zusammensetzung der Schmelze bewusst zu verändern. Es wird für un- und niedriglegierte Stähle genutzt.
- Wolfram-Inertgasschweißen (WIG): Nutzt eine nicht-abschmelzende Elektrode aus Wolfram. Es sind hohe Nahtqualitäten erreichbar, es ist aber langsamer als das MSG-Schweißen.
- Plasmaschweißen: Mit dem WIG verwandt. Der Lichtbogen erzeugt hierbei ein Plasma, das eine höhere Leistungsdichte aufweist als der bloße Lichtbogen. Es ist sehr produktiv, aber auch weniger flexibel als die anderen Schutzgasverfahren und stellt in dieser Hinsicht den Übergang zu den Strahlverfahren dar.
Unterpulverschweißen
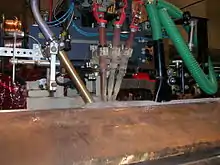
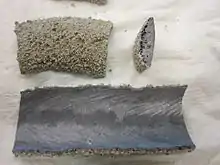
Das Unterpulverschweißen (UP-Schweißen, EN ISO 4063: Prozess 12) ist ein Lichtbogenschweißverfahren mit abschmelzender Draht- (Prozess 121) oder Bandelektrode (Prozess 122), bei dem hohe Abschmelzleistungen erzielt werden können.[9] Es wird industriell vor allem zum Schweißen langer Nähte eingesetzt und eignet sich nicht zur manuellen Ausführung.
Beim Unterpulverschweißen wird das Schweißbad von einer Schicht aus grobkörnigem mineralischem Schweißpulver bedeckt. Dieses schmilzt durch die vom Lichtbogen emittierte Wärme und bildet eine flüssige Schlacke, die aufgrund ihrer geringeren Dichte auf dem metallischen Schmelzbad schwimmt. Durch die Schlackeschicht wird das flüssige Metall vor Zutritt der Atmosphäre geschützt. Der Lichtbogen brennt in einer gasgefüllten Kaverne unter Schlacke und Pulver. Nach dem Schweißvorgang löst sich die Schlackeschicht oft von selbst ab; das nicht aufgeschmolzene Pulver kann wiederverwendet werden.
Besonders hervorzuheben ist die weitgehende Emissionsfreiheit dieses Verfahrens, da der Lichtbogen unter der Pulverschicht brennt und nur geringe Mengen Rauch freigesetzt werden. Es ist kein Sichtschutz notwendig. Wegen der Abdeckung des Prozesses hat das Verfahren einen hohen thermischen Wirkungsgrad, was jedoch den Einsatz auf große Blechdicken beschränkt. Gleichzeitig ist hierdurch keine unmittelbare Sichtkontrolle des Prozesses möglich. Jedoch werden im Allgemeinen spritzerfreie Nähte sehr hoher Qualität erzielt, sofern geeignete Schweißparameter verwendet werden.
Durch die Auswahl einer bestimmten Kombination aus Draht und Pulver kann die chemische Zusammensetzung des Schweißgutes beeinflusst werden, da durch die Reaktionen von metallischer Schmelze und Schlacke in der Kaverne ein Abbrand oder Zubrand von Legierungselementen erfolgen kann.
Wegen der großen Schmelzbäder kann das UP-Verfahren nur in Wannenlage oder mit Pulverabstützung auch in Querposition angewandt werden.[10]
Laserschweißen
Das Laserschweißen (EN ISO 4063: Prozess 52) wird vor allem zum Verschweißen von Bauteilen eingesetzt, die mit hoher Schweißgeschwindigkeit, schmaler und schlanker Schweißnahtform und mit geringem thermischem Verzug gefügt werden müssen. Das Laserschweißen oder Laserstrahlschweißen wird in der Regel ohne Zuführung eines Zusatzwerkstoffes ausgeführt. Die Laserstrahlung wird mittels einer Optik fokussiert. Die Werkstückoberfläche der Stoßkante, also der Fügestoß der zu verschweißenden Bauteile, befindet sich in der unmittelbaren Nähe des Fokus der Optik (im Brennfleck). Die Lage des Fokus relativ zur Werkstückoberfläche (oberhalb oder unterhalb) ist ein wichtiger Schweißparameter und legt auch die Einschweißtiefe fest. Der Brennfleck besitzt typische Durchmesser von einigen Zehntel Millimetern, wodurch sehr hohe Energiekonzentrationen entstehen, wenn der eingesetzte Laser die typischen Leistungen von einigen Kilowatt Laserleistung besitzt. Durch Absorption der Laserleistung erfolgt auf der Werkstückoberfläche ein extrem schneller Anstieg der Temperatur über die Schmelztemperatur des Metalls hinaus, so dass sich eine Schmelze bildet. Durch die hohe Abkühlgeschwindigkeit der Schweißnaht wird diese je nach Werkstoff sehr hart und verliert in der Regel an Zähigkeit.[11]
Elektronenstrahlschweißen
Beim Elektronenstrahlschweißen (EN ISO 4063: Prozess 51) wird die benötigte Energie von durch Hochspannung (60–150 kV) beschleunigten Elektronen in die Prozesszone eingebracht. Die Strahlbildung erfolgt im Hochvakuum (< 10−4 mbar). Der Schweißvorgang erfolgt meistens im Vakuum, kann aber auch unter Normaldruck durchgeführt werden. Hier wird dann mit einer Strahlleistung von bis zu 30 kW gearbeitet, wobei der Arbeitsabstand zwischen Strahlaustritt und Werkstück zwischen 6 und 30 mm liegen sollte.
Das Elektronenstrahlschweißen bietet eine etwa gleich große Leistungsflussdichte wie das Laserstrahlschweißen bei höherem Wirkungsgrad der Strahlerzeugung (Laser: 3 bis 40 %, Elektronenstrahl: etwa 70 %). Darüber hinaus entfällt beim Elektronenstrahlschweißen im Vakuum die Verwendung von Schutzgasen. Beides wirkt sich direkt auf die Betriebskosten aus, sodass eine Elektronenstrahlanlage in der Summe und über die Lebensdauer preiswerter sein kann als ein vergleichbares Lasersystem.
Das Elektronenstrahlschweißen erlaubt hohe Schweißgeschwindigkeiten mit extrem tiefen, schmalen und parallelen Nähten. Durch die geringen Nahtbreiten und die hohe Parallelität kann der Verzug extrem klein gehalten werden. Daher kann dieses Verfahren auch am Ende der Fertigungskette eingesetzt werden. Das Verfahren eignet sich auch für kleine, kompliziert geformte Schweißnähte, da der Elektronenstrahl durch elektrische oder magnetische Felder exakt und schnell abgelenkt werden kann. Damit kann auf die Bewegung des Bauteils verzichtet werden, der Elektronenstrahl führt die Bewegung selbst aus. Das Spektrum möglicher Nahttiefen liegt zwischen 0,1 mm und 300 mm (Aluminium), (Stahl) 150 mm, (Kupfer) 100 mm, (Titan): 100 mm.
Elektronenstrahlschweißanlagen werden häufig in der Massenfertigung von Getriebebauteilen in der Automobilindustrie eingesetzt (vor allem Japan und Deutschland). Neben einfachen und preisgünstigen Lohnaufträgen werden auch Bauteile für die Luft- und Raumfahrt, den Schienenverkehr, die Medizintechnik und die Nahrungsmittelindustrie elektronenstrahlgeschweißt.[12]
Aluminothermisches Schweißen
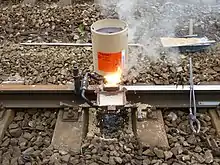
Aluminothermisches Schweißen ist auch unter dem Namen Thermit-Schweißen bekannt und wird vor allem beim Verschweißen von Bahnschienen angewendet. In einem Tiegel mit einem Loch an der Unterseite, der auf der Verbindungsstelle steht, wird (mit Hilfe eines Magnesiumspanes) eine Mischung aus Eisenoxidpulver und Aluminiumpulver entzündet, woraus sich bei einer Temperatur von circa 2450 °C flüssiges Eisen und darauf schwimmende Aluminiumoxid-Schlacke bilden.
Spleißen von Glasfasern
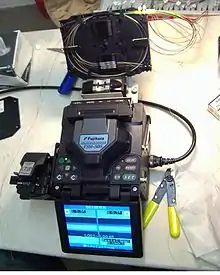
Zur Datenübertragung genutzte Lichtwellenleiter werden mittels Lichtbogenschweißen ohne Zusatzwerkstoff miteinander verbunden. Der Vorgang wird als Spleißen bezeichnet. Die Kerndurchmesser der zu verbindenden Glasfasern liegen zwischen 3,5 und 1500 µm, die Manteldurchmesser zwischen 125 und 1550 µm. Zur Schweißverbindung genutzte Geräte positionieren die Glasfasern vor der Verbindung entweder automatisch oder manuell mittels Mikroskop und Mikrometerschraube, anschließend erfolgt durch einen Lichtbogen eine Erwärmung bis auf die Schmelztemperatur des Glases und eine Verschmelzung der beiden Fasern. An der Verbindungsstelle werden Signaldämpfungen unter 0,1 dB erreicht.
Schmelzschweißen von Kunststoffen
Thermoplastische Kunststoffe können mit folgenden Schmelzschweißverfahren verbunden werden:
Pressschweißverfahren
Feuerschweißen

Beim Feuerschweißen werden die zu verbindenden Metalle im Feuer unter Luftabschluss in einen teigigen Zustand gebracht und anschließend durch großen Druck, zum Beispiel durch Hammerschläge, miteinander verbunden. Diese dürfen anfangs nicht zu stark sein, da sonst die zu verbindenden Teile wieder auseinandergeprellt werden. Im Gegensatz zu den meisten anderen Schweißmethoden wird der Stahl hierbei nicht aufgeschmolzen, sondern bei Schweißtemperatur (1200 bis 1300 °C) gefügt. Zur Vorbereitung des Schweißvorgangs im Schmiedefeuer muss bei den zu verbindenden Werkstücken auf Luftabschluss geachtet werden, damit die Oberflächen nicht oxidieren. Ursprünglich wurde Luftabschluss durch eine stark reduzierende Flamme und feinkörnigen Flusssand erreicht, wobei es schwierig war, einen solchen Sand mit dem richtigen Schmelzpunkt zu finden. Heutzutage benutzt man meist Borax, welches sich ähnlich wie beim Sand als eine flüssige, glasige Haut über die Stahlteile legt und versiegelt. Diese werden dadurch vor Oxidangriff geschützt.
Widerstandsschweißen
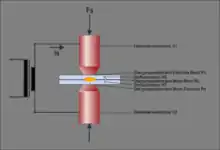
Beim Widerstandsschweißen wird der elektrische Widerstand der Fügepartner genutzt. Sie werden zusammengepresst und von Strom durchflossen. An den Berührstellen ist der Widerstand am größten, sodass dort die meiste Wärme frei wird und die Werkstoffe am stärksten erhitzt werden.
- Beim Widerstandspunktschweißen (auch kurz Punktschweißen) werden vor allem Bleche geschweißt. Sie werden dabei durch zwei gegenüberliegende Elektroden an einem Punkt zusammengepresst. Durch die Elektroden wird ein Schweißstrom in das Blech eingeleitet. Das Punktschweißen wird besonders häufig zum Schweißen von Karosserien in der Automobilindustrie genutzt
- Beim Rollennahtschweißen sind die Elektroden scheibenförmig ausgeführt und rollen auf den zwischen den Scheiben hindurchgeförderten Fügepartnern ab. Somit lassen sich kontinuierliche Nähte erzeugen.[13] Ein Anwendungsbeispiel des Verfahrens ist die Herstellung des zylindrischen Teiles von Konservendosen.
- Widerstandsbuckelschweißen entspricht im Prinzip dem Punktschweißen, wobei aber in einem der zu verbindenden Bauteile eine oder mehrere Erhöhungen (Schweißbuckel) eingebracht werden. Nur diese Buckel liegen nun auf dem anderen zu verschweißenden Bauteil auf. Durch die Geometrie des Buckels ist der Bereich des Stromüberganges genau definiert, als Elektroden werden (im Unterschied zum Punktschweißen) flächenhafte Kupferelektroden verwendet. Während des Stromflusses schmilzt der Buckel teilweise auf, drückt das Material des Buckels teilweise in das andere Bauteil und geht mit diesem eine Verbindung ein.
- Die Pressstumpfschweißverfahren und das Abbrennstumpfschweißen lassen sich leicht automatisieren und werden verwendet, um tubulare Strukturen, Rollen, Ringe, Kettenglieder, Schienen-, Beton-Armierungsstähle, Fensterrahmen, Folien und Schläuche zu verbinden. Die Bauteile werden mit zwei Spannbacken gegeneinandergepresst, die mit einer elektrischen Spannung beaufschlagt werden. Dabei fließt ein hoher Strom durch die Bauteile, so dass die Fügestelle kurzzeitig aufschmilzt.
Kaltpressschweißen
Verbindungen mittels Kaltpressschweißen (EN ISO 4063: Prozess 48) erfolgen unter hohem Druck und unterhalb der Rekristallisationstemperatur der Einzelteile. Hierbei bleiben die Partner im festen Zustand, allerdings ist eine plastische Verformung mit einer starken Annäherung der Kontaktflächen notwendig. Durch die extrem enge Berührung der beiden Kontaktflächen erfolgt die Zerstörung störender Oberflächenschichten und auf Grund von nun wirkenden zwischenatomaren Bindekräften eine stabile Verbindung der Werkstücke. Um eine gute Verbindung zu erhalten, sind Mindestverformungen von Materialien mit ausreichender Kaltverformbarkeit notwendig (Beispiel: Kupfer sowie Aluminium miteinander und untereinander). Kaltpressschweißen ist wie andere Schweißverfahren auch für stromleitende Verbindungen geeignet. Bei Aluminium ist eine vorherige Entfettung und ein Aufreißen der oberflächlichen Oxidschicht hilfreich (Beispiel: Aluminium-Kontaktfahnen in Elektrolytkondensatoren). Unter Hochvakuum können Metalle unter anderem auch mit Keramik kaltpressverschweißt werden.
Reibschweißen
Beim Reibschweißen (EN ISO 4063: Prozess 42) werden zwei Teile unter Druck relativ zueinander bewegt, wobei sich die Teile an den Kontaktflächen berühren. Durch die entstehende Reibung kommt es zur Erwärmung und Plastifizierung des Materials. Am Ende des Reibvorganges ist es von entscheidender Bedeutung, die Teile richtig zueinander zu positionieren und einen hohen Druck auszuüben. Die Vorteile dieses Verfahrens sind, dass die sogenannte Wärmeeinflusszone deutlich kleiner ist als bei anderen Schweißverfahren und dass es nicht zur Bildung von Schmelze in der Fügezone kommt. Es können eine Vielzahl von Werkstoffen, wie beispielsweise Aluminium mit Stahl, miteinander verschweißt werden. Auch die Verbindung von metallischen Werkstoffen, die keine Legierungen miteinander eingehen, ist vielfach möglich.[14]
Verfahrensvarianten sind:
- das Rotationsreibschweißen
- das Orbitalreibschweißen und
- das Rührreibschweißen.
Ultraschallschweißen
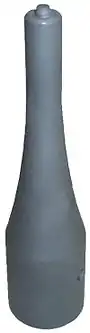
Das Ultraschallschweißen (EN ISO 4063: Prozess 41) ist ein Verfahren zum Fügen von thermoplastischen Kunststoffen und metallischen Werkstoffen. Das Verfahren findet in vielen Bereichen der Industrie Verwendung. So werden z. B. in der Verpackungsindustrie Kunststoffverpackungen oder in der Automobilindustrie Kabelbäume mittels Ultraschall geschweißt. Bei den metallischen Werkstoffen kommt es vor allem bei Aluminium, Kupfer und deren Legierungen zum Einsatz. Die Verschweißung wird durch eine hochfrequente mechanische Schwingung im Bereich von i. d. R. 20 bis 35 kHz erreicht, welche zwischen den Bauteilen zu Erwärmung durch Molekular- und Grenzflächenreibung, bei Metallen auch zur Verzahnung und Verhakung der Fügepartner führt.[15][16] Somit gehört das Ultraschallschweißen zur Gruppe der Reibschweißungen.
Mit Hilfe eines Generators wird hochfrequenter Wechselstrom erzeugt und über ein Koaxialkabel zu einem Ultraschallwandler, dem sogenannten Konverter, übertragen, der daraus mit Hilfe des piezoelektrischen oder des magnetostriktiven Effekts eine mechanische Ultraschallschwingung erzeugt. Diese Schwingungen werden über ein Amplitudentransformationsstück auf die Sonotrode übertragen. Unterschiedliche Anwendungen erfordern unterschiedliche Bauformen von Sonotroden, die meist aus Stahl, Aluminium oder Titan hergestellt werden. Die Amplitude der Schwingung und die Impedanzanpassung wird durch die Form und Masse des Amplitudentransformationsstückes beeinflusst. Die Schwingungen werden unter Druck über die strukturierte, oft geriffelte Arbeitsfläche der Sonotrode auf die zu verbindenden Werkstücke übertragen.
Beim Schweißen von Kunststoff wird die Schwingung meist vertikal zu den Fügepartnern eingeleitet. Diese erhitzen sich und beginnen zu erweichen, wodurch der Dämpfungskoeffizient ansteigt. Die Zunahme des Dämpfungskoeffizienten führt zu höherer innerer Reibung, was die Temperaturerhöhung weiter beschleunigt. Die aufgeschmolzenen Werkstoffe verbinden sich und sind nach dem Abkühlen und Erstarren miteinander verschweißt.
Beim Ultraschallschweißen von Metallen wird die Schwingung horizontal zu den Fügepartnern eingeleitet, so dass diese aneinanderreiben. Die Verbindung entsteht nach dem Abscheren von Rauhigkeitsspitzen und dem Aufbrechen der Oxidschicht im Wesentlichen durch ein Ineinanderverzahnen und -verhaken der Fügepartner. Dies geschieht durch plastisches Fließen, ohne dass die Materialien schmelzen, was insbesondere bei Folien, dünnen Blechen oder Drähten, wie zum Beispiel beim Drahtbonden, vorteilhaft ist.
Neben punktförmigen Schweißungen sind mit abrollenden Sonotroden auch Nahtschweißungen möglich, so z. B. bei der Fertigung von Solarkollektoren.[16]
Das Verfahren ist weiterhin durch sehr geringe Schweißzeiten und hohe Wirtschaftlichkeit gekennzeichnet.[17] Es lassen sich unterschiedliche Materialien miteinander verbinden, die Werkstücke werden nur im Schweißbereich geringfügig erwärmt, das umliegende Material somit nicht geschädigt.
Sprengschweißen
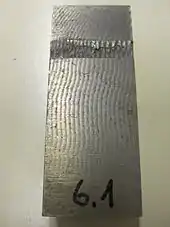
Mit Hilfe des Sprengschweißverfahrens ist es möglich, zwei nicht schmelzschweißbare Materialien dauerhaft und fest miteinander zu verbinden. Dabei prallen die beiden Schweißflächen unter Zuhilfenahme von Sprengstoff mit mindestens 100 m/s[18] unter einem Winkel von 2° bis 30° aufeinander. Die Kollisionsenergie bringt die Schweißpartner bis zur atomaren Ebene zusammen, so dass auch die Gitterkräfte (bei Metallen) wirken. Da die Schmelztemperatur nicht erreicht wird, können sich keine intermetallischen Phasen bilden. In der industriellen Anwendung werden auf diese Art meist zwei auf konventionelle Weise nicht schweißbare Metallpartner miteinander verbunden, beispielsweise Titan und Kupfer. Als Sprengstoffe kommen vorwiegend hochbrisante plastische PETN-, RDX- und HMX-Sprengstoffe, wie Semtex mit Detonationsgeschwindigkeiten von mehr als 5000 m/s zum Einsatz. Durch den Aufprall der Schweißpartner entstehen an den Grenzflächen wellenartige Verwerfungen, die eine stoffschlüssige Verbindung herstellen.
Elektromagnetisches Pulsschweißen
Das elektromagnetische Pulsschweißen, kurz EMP-Schweißen oder EMPW kann ohne Wärme mithilfe des Verfahrens des Magnetumformens (auch Elektromagnetische Pulstechnik, kurz EMPT) Werkstoffmischverbindungen, aber auch artgleiche Werkstoffe, binnen etwa 25 μs miteinander verbinden, indem einer der Fügepartner mittels eines Magnetfeldes berührungslos einen Impuls erfährt und gegen den anderen Partner prallt. Das Verfahren ist daher mit dem Sprengschweißen und -plattieren verwandt. Es können Rohre, Bleche und Zylinder verschweißt werden. Bei dem Verfahren befinden sich die Bauteile in der Nähe einer Spule, durch die ein sehr hoher Stromimpuls fließt welcher aus einem Impulsgenerator gewonnen wird. Es können zumindest als einer der Fügepartner nur gut leitfähige Materialien wie Aluminium verarbeitet werden. Durch die hohe Geschwindigkeit des Zusammenpralls der Fügepartner kommt es wie beim Sprengschweißen zu einer stoffschlüssigen Verbindung in der festen Phase.[19]
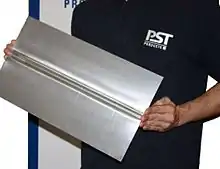
Beim Verbinden von Blechen (Plattieren) beschleunigt der Impuls eines der beiden zu fügenden Bleche über eine Distanz von 0,3–2 mm auf Geschwindigkeiten über 200 m/s. Beim Aufprall dieses Blechs auf ein stationäres Gegenblech werden im Aufschlagbereich die auf beiden Oberflächen haftenden Oxidschichten gelöst und die sich zwischen den Blechen befindliche Luft ausgeblasen. Die so erzeugten reinen Oberflächen sind nun hoch reaktiv und werden mit hohem Druck aufeinandergepresst. Dies bewirkt eine ggf. heliumdichte metallische Bindung durch Elektronenaustausch.[20]
Die Methode bringt kaum Wärme in die Bauteile ein. Daher ist es möglich, metallische Werkstoffe mit stark unterschiedlichen Schmelzpunkten zu verschweißen. Zudem tritt keine Gefügebeeinflussung durch Wärme auf. Daher können beispielsweise auch Verbindungen zwischen Blechen aus Aluminiumlegierungen und hochfesten Stählen hergestellt werden, ohne deren festigkeitsbestimmendes Gefüge zu ändern.
Diffusionsschweißen
Das Diffusionsschweißen (EN ISO 4063: Prozess 45) ist eine etwa 50 Jahre alte Schweißtechnik, um vorwiegend metallische Werkstücke miteinander zu verbinden. Die Qualität der Schweißverbindungen ist außerordentlich hoch und kann im Bereich des verwendeten Materials liegen.
Diffusionsschweißen erfolgt bei hohem Druck (typische Größenordnung: Fließgrenze) und etwas unterhalb der Solidustemperatur. Aber auch unter Raumtemperatur können Metalle zu Diffusionsverschweißen neigen, sofern ihre Flächen außerordentlich eben und glatt ausgebildet sind. Endmaße beispielsweise können schon nach kurzer Zeit miteinander kaltverschweißen, wenn sie angesprengt sind, also sehr nah beieinander liegen.
- Bei dem vorwiegend in der Pulvermetallurgie eingesetzten Verfahren Heißisostatisches Pressen (HIP) werden die Werkstücke in einem Stahlblechkanister eingeschweißt und anschließend evakuiert oder offen in eine Druckkammer gelegt. Ein Schutzgas mit entsprechendem Druck und Temperatur presst die Bauteile zusammen. Die Kraft wirkt so von allen Seiten, also isostatisch.
- Die zweite Variante wird auch als Uniaxial Diffusion Weld (UDW) bezeichnet. Hierbei wird eine einachsige Kraft meist mittels einer hydraulischen Presse senkrecht zur verbindenden Fläche ausgeübt. Die Presse verfügt entweder über einen Vakuumbehälter oder es wird ein zum HIP-Verfahren analoger Kanister benutzt.
MBP-Schweißen
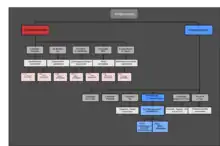
Das MBP-Schweißen (Pressschweißen mit magnetisch bewegtem Lichtbogen)[21] ist ein Lichtbogenpressschweißverfahren nach DIN 1910-100:2008-02[2] und hat die Ordnungsnummer 185 nach EN ISO 4063.[3] Das Verfahren wird auch als MBL- oder Magnetarc-Schweißen bezeichnet. In der englischsprachigen Literatur ist es bekannt als MIAB Welding – magnetically impelled arc butt welding. Mit dem Verfahren werden Profile mit geschlossenem Querschnitt stumpf miteinander verbunden.
Lichtbogenbolzenschweißen
Lichtbogenbolzenschweißen (Kurzform: Bolzenschweißen, engl.: stud welding, Ordnungsnummer 78 EN ISO 4063[3]) gehört zu den Lichtbogenpressschweißverfahren. Mit dem Verfahren werden bolzenförmigen Elemente (z. B. Gewindebolzen, Stifte, Buchsen, Haken, Ösen) mit größeren Bauteilen (z. B. Karosseriebleche, Gehäuse, Heizkörper) dauerhaft verbunden.
Pressschweißen von Kunststoffen
Thermoplastische Kunststoffe können mit folgenden Pressschweißverfahren verbunden werden:
- Hochfrequenzschweißen
- Zirkularschweißen
- Rotationsreibschweißen
- Ultraschallschweißen
- Vibrationsschweißen
Schweißsimulation
Die Schweißsimulation ist ein Werkzeug zur Klärung schweißtechnischer Fragestellungen, die auf der numerischen Lösung eines mathematischen Modells beruht. Ziel ist es, einerseits durch das Ersetzen zahlreicher praktischer Versuche Kosten in den Unternehmen zu senken und andererseits Informationen zu gewinnen, die über Messungen nicht oder nur mit einem sehr hohen Aufwand zu erreichen wären.
Zur schweißtechnischen Ausbildung werden durch einige Schweißtechnik-Hersteller Schweißsimulatoren angeboten. Diese können WIG-, MAG- und Lichtbogenhandschweißen simulieren. Mit dem Simulator können in Echtzeit und unter realitätsnahem Bedingungen verschiedene Schweiß-Aufgaben trainiert werden. Gegenüber dem normalen Schweißen bieten derartige Geräte zum virtuellen Schweißtraining einige Vorteile. Unter anderem wird kein Material verbraucht, es müssen keine Arbeitsschutzmaßnahmen beachtet werden, auch seltene Arbeitsaufgaben bzw. Kombinationen von Materialien und Werkstoffen können genutzt werden, durch die Variation von Parametern kann ein Verständnis für die Abhängigkeiten der Schweißergebnisse erreicht und je nach Brennerhaltung und -Führung die Ergebnisse sofort analysiert und Fehler korrigiert werden. Einzelne Simulatoren nutzen auch reale Lichtbögen.[22]
Lebensdauerverlängerung durch Nachbehandlungsmethoden
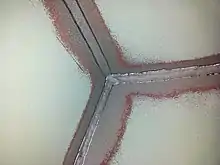
Die Betriebsfestigkeit und Lebensdauer dynamisch belasteter geschweißter Metallkonstruktionen wird in vielen Fällen durch die Schweißnähte – insbesondere die Schweißnahtübergänge – bestimmt. Durch gezielte Nachbehandlung der Übergänge durch Schleifen, Strahlen, Kugelstrahlen, hochfrequentes Hämmern etc. kann die Lebensdauer mit einfachen Mitteln bei vielen Konstruktionen erheblich gesteigert werden. Beim hochfrequenten Hämmern basiert die Steigerung der Lebensdauer im Wesentlichen auf einer Reduzierung der Kerbwirkung, Verfestigung der Randschicht und dem Einbringen von Druckeigenspannungen zur Erhöhung des Widerstandes gegen Rissbildung und Rissausbreitung durch Überlagerung der Kerbspannungen mit Druckeigenspannungen. Nach der Behandlung sind die Schweißnähte durch geeignete Maßnahmen wie beispielsweise durch Beschichtung mit einem korrosionsbeständigen, langlebigen Material (passiver Korrosionsschutz) zu schützen. Eine solche Beschichtung kann jedoch im Reparaturfall problematisch sein.[23]
Arbeitsschutz
Gefahren durch Schweißrauche und Schweißgase
Schweißen ist mit Gefährdungen verbunden, die sich aus der Verwendung von elektrischem Strom, durch unter Druck stehende Gase, Wärme sowie aus dem Freiwerden von optischer Strahlung und Gefahrstoffen ergeben können. Die Gefährdungen sind davon abhängig, welches Schweißverfahren angewendet wird.
Gefahrstoffe in Form von Schweißrauch und Schweißgasen werden aus der Schmelze – insbesondere aus abschmelzenden Schweißzusätzen – freigesetzt. Durch Überhitzen der Schmelze bzw. des Schweißzusatzes verdampft Metall. Der Dampf steigt über der Schmelze auf, kühlt ab und bildet durch Kondensation Metallpartikel. Luftgetragene Metallpartikel werden als Schweißrauch bezeichnet. Die Zusammensetzung des Rauches ist abhängig von der Zusammensetzung der zu schweißenden Werkstoffe. Rauche, die beim Schweißen von un- und niedriglegierten Stählen frei werden, bestehen überwiegend aus Eisen und Mangan oder deren Oxiden. Beim Schweißen von Aluminiumwerkstoffen besteht der Rauch vorrangig aus Aluminium bzw. Aluminiumoxiden, das Schweißen von korrosionsbeständigen Chrom-Nickel-Stählen setzt Nickel- und Chromverbindungen frei. Eingeatmete Eisen- und Aluminiumverbindungen können die Atemwege belasten und die Lungenfunktion beeinträchtigen. Eine akute Vergiftung durch Einatmen von Stäuben mit einem sehr hohen Mangangehalt kann zu entzündlichen Reaktionen in der Lunge führen. Diese Toxizität manifestiert sich als Bronchitis und kann sich zu einer fibrösen Lungenerkrankung entwickeln. Manganhaltige Rauche können auch neurologische Störungen, ähnlich einer Parkinson-Krankheit, verursachen[24], sechswertige Chromverbindungen und Nickeloxid sind als krebserzeugend eingestuft. Die Internationale Agentur für Krebsforschung (IARC) stuft sogar Schweißrauche generell als krebserzeugend ein.[25]
Schweißgase wie Kohlenstoffmonoxid, Kohlenstoffdioxid, Stickstoffmonoxid, Stickstoffdioxid und Ozon können ebenfalls die Atemwege schädigen. MSG-Schweißen setzt diese Gase nur in geringen Mengen frei, sodass die damit verbundenen Gesundheitsgefahren im Allgemeinen als gering eingeschätzt werden. Wird jedoch in engen, schlecht belüfteten Räumen geschweißt, können die Gase den Luftsauerstoff verdrängen, sodass Erstickungsgefahr besteht.
Die deutsche Gesetzgebung hat zum Schutz der Beschäftigten Grenzwerte für die Luftqualität an Arbeitsplätzen festgelegt, die für die Verfahren der Schweißtechnik z. B. in der Technischen Regel für Gefahrstoffe (TRGS) 528 „Schweißtechnische Arbeiten“ aufgeführt sind. Die TRGS 528 beschreibt auch die Vorgehensweise zur Ermittlung der prozessbedingten Gefährdungen und gibt Hinweise zu Schutzmaßnahmen und arbeitsmedizinischer Vorsorge.[26]
Als technische Schutzmaßnahme sollten üblicherweise Filteranlagen und -geräte zum Absaugen und Abscheiden von Schweißrauch eingesetzt werden. Wird die so gereinigte Luft in den Arbeitsbereich zurückgeführt, werden besondere Anforderungen u. a. an die filtertechnischen Eigenschaften der Geräte gestellt. Dies betrifft insbesondere Geräte zur Abscheidung krebserzeugender Rauche, die z. B. beim Schweißen von Chrom-Nickel-Stählen frei werden. In diesen Fällen ist eine Luftrückführung nur für Geräte zulässig, die nach DIN EN ISO 15012-1 und -4 (zukünftig DIN EN ISO 21904) positiv geprüft wurden.[27] Das Institut für Arbeitsschutz der Deutschen Gesetzlichen Unfallversicherung (IFA) bietet für die Gerätehersteller und Inverkehrbringer Prüfungen nach diesen Normen auf freiwilliger Basis an.[28] Die Herstellerfirmen von positiv geprüften Filteranlagen und -geräten erhalten eine DGUV Test-Prüfbescheinigung. Filteranlagen und -geräte, die die sicherheitstechnischen Anforderungen der Norm erfüllen, sind in einer Positivliste aufgeführt.[29]
Maßnahmen
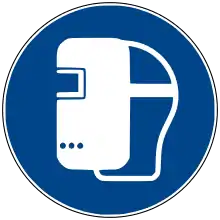
Es ist für Schweißarbeitsplätze eine Gefährdungsbeurteilung zu erstellen. Hier sind alle Inhaltsstoffe des Schweißrauches zu berücksichtigen, unter anderem Titandioxid, Fluoride, Magnesiumoxid, Calciumoxid, Eisenoxide und dessen Legierungsbestandteile wie Nickel, Cobalt, Chrom und Mangan. Bei hochlegierten Stählen ist, wenn möglich, auf Elektrodenschweißungen zu verzichten und auf Schutzgasschweißen oder automatisierte Verfahren auszuweichen, denn durch die fehlende Ummantelung der Elektrode werden weniger Chromate freigesetzt.
- Information
Eine entsprechend fachkundige Einweisung ist für alle abhängig Beschäftigte nach dem Arbeitsschutzgesetz (ArbSchG) zwingend erforderlich; weiterhin ist ein Ausbildungsnachweis (Facharbeiterbrief oder Lehrgangsprüfung einer Handwerkskammer) üblich. In vielen Industriebereichen, bei Bahnanwendungen, ist eine Schweißaufsicht erforderlich.
- Augenschutz
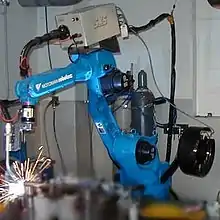
Beim Autogenschweißen benötigt man Schutzgläser, damit keine glühenden Teile oder Funken in die Augen gelangen. Die Gläser sind eingefärbt, damit man blendfrei die Schweißumgebung beobachten kann.
- Strahlungsschutz
Beim Lichtbogenschweißen entsteht Ultraviolettstrahlung, welche die Haut, insbesondere jedoch die Augen schädigt. Weiterhin entsteht Infrarotstrahlung (Wärmestrahlung), die nicht nur auf ungeschützten Körperteilen Verbrennungen erzeugen, sondern auch die Netzhaut schädigen kann. Deshalb müssen Schutzgläser verwendet werden, die diese beiden Strahlungsarten abschirmen. Die Schutzklassen für derartige Gläser sind in der Europäischen Norm EN 169 festgelegt. So sind zum Autogenschweißen die Schutzklassen 2 bis 8, für offenes Lichtbogenschweißen dagegen die Klassen 9 bis 16 vorgesehen. Die Schutzgläser tragen eine Beschriftung, welche die Eigenschaften des Glases charakterisiert. Die Angabe ist wie folgt: Schutzklasse, Herstellerkürzel, optische Klasse 98, DIN-Norm. Der moderne Ersatz für Schutzgläser sind automatische Schweißerschutzfilter.
Da die UV-Strahlung auch die Haut schädigt, wird ein Schirm verwendet, der das ganze Gesicht abdeckt. Vor dem eigentlichen fast schwarzen Glas ist meist ein normales Glas, das die Funken abhält und billiger auszutauschen ist. Um beide Hände frei zu haben, kann der Schirm an einem Schutzhelm oder einer auf dem Kopf getragenen Vorrichtung klappbar angebracht werden. Zusätzlich ist spezielle schwer entflammbare Schweißerkleidung zu tragen, die alle Hautflächen sicher abdeckt. Viele Schweißverfahren sind sehr laut, ein angemessener Gehörschutz ist daher vonnöten.
Eine weitere Gefahrenquelle stellen in diesem Zusammenhang auch thoriumhaltige Wolframelektroden zum WIG-Schweißen dar. So heißt es in der DGUV Information 209-049 (Deutsche Gesetzliche Unfallversicherung e.V. DGUV)
„Werden thoriumoxidhaltige Schweißelektroden angeschliffen oder wird damit WIG-Schweißen mit Wechselstrom durchgeführt, müssen Unternehmerinnen und Unternehmer innerhalb von sechs Monaten nach Beginn der Arbeiten eine auf den Arbeitsplatz bezogene Abschätzung der Körperdosis durchführen (§ 95 Abs. 1 Strahlenschutzverordnung). Werden die zuvor genannten Arbeitsplätze so verändert, dass höhere Strahlenexpositionen auftreten können, ist eine Abschätzung erneut unverzüglich durchzuführen.“
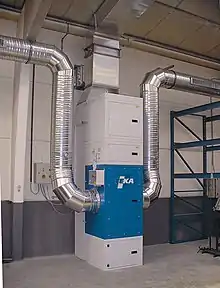
- Stäubeschutz
Beim Schweißen entstehen auch feinste Staubpartikel, die abgesaugt werden müssen, damit sie nicht in die Lunge des Schweißers gelangen und von dort in die Blutbahn diffundieren können. Zu diesem Zweck werden mobile oder stationäre Schweißrauchfilter eingesetzt, die diesen Feinstaub absaugen und filtern. Stand der heutigen Technik sind so genannte ePTFE-Filter (Oberflächenfiltration). Wenn keine effektive Absaugung des Schweißrauchs sichergestellt werden kann, muss der Schweißer durch eine persönliche Schutzausrüstung in Form eines Gebläsefiltergerätes (PAPR) geschützt werden. Vor Sauerstoffmangel oder schädlichen Gasen in Schächten und Behältern schützen diese Geräte nicht. Wenn keine ausreichende Belüftung möglich ist, müssen umluftunabhängige Atemschutzgeräte getragen werden. Besondere Vorsicht ist beim Flammrichten und Vorwärmen mit Gasbrennern, in unzureichend belüfteten engen Räumen geboten, da die Flamme einen Teil des Atemsauerstoffs verbraucht.
- Umgebungsschutz
Beim Schweißen müssen auch die Personen in der Umgebung vor der Strahlung und Lärm geschützt werden. Dazu gibt es Schweißlamellen- und Schweißervorhänge sowie Schallschutztrennwandsysteme. Bei Lichtbogenhandschweißungen ist die elektrische Gefährdung des Schweißers besonders zu beachten. Die Lichtbogenspannung liegt zwar unter dem – im Allgemeinen – gefährdenden Bereich, jedoch ist vor allem bei Arbeiten unter besonderer elektrischer Gefährdung, also beispielsweise bei Arbeiten in engen elektrisch leitenden Räumen (Kessel, Röhren etc.) eine Reihe von Vorsichtsmaßnahmen zu beachten, die unter anderem im Merkblatt BGI 553 der Metallberufsgenossenschaft vorgeschlagen werden.[31]
- Maßnahmen beim Laserschweißen
Beim Laserschweißen ist der Laserstrahl selbst eine zusätzliche Gefahrenquelle. Er ist in der Regel unsichtbar. Während Strahlung im Nahen Infrarotbereich (Festkörperlaser, Faserlaser, Diodenlaser) in die Haut und das Auge eindringt und auch bei geringen Intensitäten (Streustrahlung) Netzhautschäden verursacht, wird die Strahlung des CO2-Lasers (Mittleres Infrarot) auf der Oberfläche (Haut und Hornhaut des Auges) absorbiert und verursacht oberflächliche Verbrennungen. Hautverbrennungen durch Laser im Nahen Infrarot sind unter anderem auch deshalb gefährlich, da die Strahlung in tiefen Gebieten unter der Haut absorbiert wird, wo sich keine temperaturempfindlichen Nerven befinden. Laser-Schweißgeräte sind in der Regel sicher gehaust (verriegelte Schutztüren, Laserschutzfenster), sie fallen dann unter die Laserklasse I und können gefahrlos ohne Laserschutzbrille bedient werden.
- Bekleidung
Gegen abspritzende Schlacken- und Schweißgutpartikel wird der Schweißer durch geeignete Bekleidung geschützt, die gegen heiße Partikel widerstandsfähig sein muss, z. B. eine Lederschürze, und die keine Falten bilden darf, in denen sich diese Partikel festsetzen können.
Verbände
Die nationale und internationale Zusammenarbeit bei der Ausbildung, Zertifizierung, Normung und technisch-wissenschaftliche Weiterentwicklung im Bereich Schweiß- und Fügetechnik wird in Deutschland durch den DVS, in Europa durch die EWF und weltweit durch das IIW koordiniert.
Siehe auch
- Schweißgerät
- Pneumatic Impact Treatment – Beispiel für ein höherfrequentes Hämmern (HFMI) – Verfahren zur Verlängerung der Ermüdungslebensdauer bzw. Schwingfestigkeit von Schweißnähten
Literatur
- Fachgruppe für die schweißtechnische Ingenieurausbildung: Fügetechnik Schweißtechnik. 6., überarb. Auflage. DVS Verlag, Düsseldorf 2004, ISBN 3-87155-786-2.
- U. Dilthey, A. Brandenburg: Schweißtechnische Fertigungsverfahren. Band 3: Gestaltung und Festigkeit von Schweißkonstruktionen. 2. Auflage. Springer Verlag, 2001, ISBN 3-540-62661-1.
- H. Hügel: Strahlwerkzeug Laser. (= Teubner Studienbücher Maschinenbau). Stuttgart 1992, ISBN 3-519-06134-1.
- U. Dilthey (Hrsg.): Laserstrahlschweißen – Prozesse, Werkstoffe, Fertigung, Prüfung. DVS-Verlag, Düsseldorf 2000, ISBN 3-87155-906-7.
- H. Schultz: Elektronenstrahlschweißen. (= Fachbuchreihe Schweißtechnik. Band 93). DVS-Verlag, Düsseldorf 2000, ISBN 3-87155-192-9.
- K.-J. Matthes, E. Richter: Schweißtechnik. Fachbuchverlag Leipzig im Carl Hanser Verlag, 2002, ISBN 3-446-40568-2.
Weblinks
Einzelnachweise
- DIN EN 14610:2005-02 Schweißen und verwandte Prozesse – Begriffe für Metallschweißprozesse.
- DIN 1910-100:2008-02: Schweißen und verwandte Prozesse – Begriffe – Teil 100: Metallschweißprozesse mit Ergänzungen zu DIN EN 14610:2005.
- DIN EN ISO4063:2011-03 Schweißen und verwandte Prozesse – Liste der Prozesse und Ordnungsnummern
- Pressschweißverfahren. Abgerufen am 9. Oktober 2017.
- DIN EN ISO 6520-1:2007-11 Schweißen und verwandte Prozesse – Einteilung von geometrischen Unregelmäßigkeiten an metallischen Werkstoffen – Teil 1: Schmelzschweißen, 2007.
- DIN EN ISO 17659:2005-09 Schweißen – Mehrsprachige Benennungen für Schweißverbindungen mit bildlichen Darstellungen
- DIN EN ISO 6947:2011-08 Schweißen und verwandte Prozesse – Schweißpositionen
- Gasschweißen. In: Klaus-Jürgen Matthes, Erhardt Richter: Schweißtechnik: Schweißen von metallischen Konstruktionswerkstoffen. Carl Hanser Verlag, 2008, ISBN 978-3-446-41422-8, S. 290 (eingeschränkte Vorschau in der Google-Buchsuche).
- Stephan Kallee: Unterpulverschweißen – UP-Schweißen (EN ISO 4063: Prozess 12), ein Lichtbogenschweißverfahren mit abschmelzender Draht- (Prozess 121) oder Bandelektrode (Prozess 122).
- Hans J. Fahrenwaldt, Volkmar Schuler: Praxiswissen Schweißtechnik. Friedrich Vieweg & Sohn Verlag/DVS Verlag, 2007, ISBN 978-3-87155-970-9, S. 42 (Abschnitt: Unterpulverschweißen. eingeschränkte Vorschau in der Google-Buchsuche).
- technolix.net (Memento vom 15. Januar 2008 im Internet Archive) (8. Juli 2007)
- Webseite der RWTH Aachen, Institut für Schweiß- und Fügetechnik
- Ulrich Dilthey: Schweißtechnische Fertigungsverfahren 1: Schweiß- und Schneidtechnologien. Springer Verlag, 2006, ISBN 3-540-21673-1 (Abschnitt: Metallschutzgasschweissen (MSG). eingeschränkte Vorschau in der Google-Buchsuche).
- Gerd Witt u. a.: Taschenbuch der Fertigungstechnik. Carl Hanser Verlag, München 2006, ISBN 3-446-22540-4 (eingeschränkte Vorschau in der Google-Buchsuche).
- Grundlagen und Schweißen. Ultrasonics Steckmann GmbH, abgerufen am 29. Oktober 2014.
- Metallschweißen. Ultrasonics Steckmann GmbH, abgerufen am 29. Oktober 2014.
- Christian Bonten: Produktentwicklung: Technologiemanagement für Kunststoffprodukte. Carl Hanser-Verlag, München, ISBN 3-446-21696-0 (eingeschränkte Vorschau in der Google-Buchsuche).
- dynaplat.de (Memento vom 10. November 2013 im Internet Archive)
- Ralph Schäfer, Pablo Pasquale: Die Elektromagnetische Puls Technologie im industriellen Einsatz. (PDF; 949 kB).
- Blechschweissen mal wirklich ganz anders. Kundenmagazin der PSTproducts GmbH (PDF; 4,09 MB).
- DVS: Preßschweißen mit magnetisch bewegtem Lichtbogen (MBP-Schweißen) DVS Merkblatt 2934, 2001.
- Schweißtrainersysteme – eine „Revolution“ in der fügetechnischen Ausbildung? In: DVS-Magazin 01/2012 S. 5–8. (PDF; 1,6 MB)
- Stéphane Itasse: Verzinkten Stahl schweißen. Maschinenmarkt. 11. August 2017.
- Arbeitsschutz Schweißen: Mangan im Schweißrauch verursacht parkinsonähnliche Symptome. Abgerufen am 21. April 2020.
- Leibniz-Institut für Präventionsforschung und Epidemiologie: IARC verschärft Risikoeinschätzung: Schweißrauche sind krebserregend bei Menschen. Abgerufen am 21. April 2020.
- Technische Regel für Gefahrstoffe 528 (TRGS 528). Bundesanstalt für Arbeitsschutz und Arbeitsmedizin
- IFA-Handbuch: Filteranlagen zum Abscheiden von Schweißrauch. Abgerufen am 20. April 2020.
- Institut für Arbeitsschutz der Deutschen Gesetzlichen Unfallversicherung (IFA): Grundsätze für die Prüfung und Zertifizierung von Einrichtungen zum Erfassen und Abscheiden von Schweißrauch. Abgerufen am 20. April 2020.
- IFA-Handbuch: Schweißrauchabsauggeräte – Positivliste –. Abgerufen am 20. April 2020.
- Abschnitt 2.2 Umgang mit thoriumoxidhaltigen Wolframelektroden beim Wolfram-Inertgasschweißen (WIG) (DGUV Information 209-049), auf arbeitssicherheit.de
- Merkblatt BGI 553. (Seite nicht mehr abrufbar, Suche in Webarchiven) Info: Der Link wurde automatisch als defekt markiert. Bitte prüfe den Link gemäß Anleitung und entferne dann diesen Hinweis. Berufsgenossenschaft Metall: Lichtbogenschweißer