Schweißprozessüberwachung
Durch Prozessüberwachung soll die Güte eines Produktes während laufender Fertigung überwacht und damit sichergestellt werden, dass die Qualitätsvorgaben eingehalten werden. Im Gegensatz dazu kontrolliert die Zustandsüberwachung von Fertigungsanlagen permanent den Anlagenzustand durch Messung physikalischer Größen und überzeugt sich von der störungsfreien Anlagenfunktionalität.
Prozessüberwachung in industrieller Fertigung erfasst wesentliche, die Fertigungsqualität charakterisierende physikalische Messgrößen oder daraus abgeleitete Merkmale während des ablaufenden Prozesses und bewertet den Prozess. Das Ergebnis ist eine Aussage zur erwartbaren Qualität des gefertigten Produktes. Auf diese Weise wird eine Vollprüfung aller hergestellten Produkte angestrebt. Die Online-Prozessüberwachung koppelt die Qualitätsbewertung zeitlich eng an den Herstellungsprozess, so dass zwischen seinem Abschluss, der Qualitätsaussage und einer möglichen Reaktion der Fertigungsanlage auf das Qualitätsergebnis möglichst kein Zeitverlust auftritt.
Bei der Online-Schweißprozessüberwachung handelt es sich um die Qualitätsbewertung von Schweißverbindungen während oder unmittelbar nach Abschluss des Schweißvorgangs. Einrichtungen der Online-Schweißprozessüberwachung kombinieren oft Funktionen der Qualitätsüberwachung mit denen der Zustandsüberwachung von Fertigungsanlagen.
Grundlagen und Begriffe der Online-Prozessüberwachung
Die Gütewerte von Schweißverbindungen (Qualitätsmerkmale) können mit Hilfe der Prozessüberwachung nicht direkt gemessen werden. Stattdessen wird mittels korrelierender Qualitätsersatzgrößen (Überwachungsmerkmale) auf die Qualität geschlossen. Dazu werden Objekte, die bewertet werden sollen, mit einer Gruppe (einer Klasse) von Objekten verglichen, von denen bekannt ist, dass sie die Qualitätsforderungen erfüllen. Das Vergleichsergebnis ist eine Bewertung der Ähnlichkeit des Objektes mit der Menge aller bekannter Objekte. Die theoretische Grundlage dafür bieten Verfahren der Klassifizierung, d. h. des Zusammenfassens von Objekten zu Klassen und der Zuordnung unbekannter Objekte in ein existierendes Klassensystem (Klassierung) mit Hilfe eines Klassifikators.
Objekt
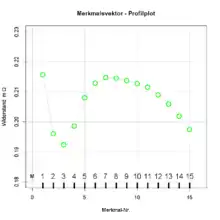
Objekte werden in gegebenem Zusammenhang durch aus Messwerten gewonnene Merkmale eines Schweißprozesses repräsentiert. Im Falle eines einzelnen Merkmals ist das Objekt eine skalare Größe. Werden mehrere Merkmale zur Objektbeschreibung herangezogen, kann das Objekt als Merkmalsvektor im mehrdimensionalen Merkmalsraum aufgefasst und grafisch durch einen Punkt im kartesischen Koordinatensystem dargestellt werden. Bei Merkmalsvektoren mit Dimensionen größer als drei bietet sich die Profildarstellung (Profilplot) oder die Darstellung in Polarkoordinaten (Polarplot, Netzdiagramm) an (s. Grafische Darstellung von Objekten und Klassen).
Beispiel: Eine Widerstandspunktschweißung wird durch die Messgrößen Spannung und Schweißstrom charakterisiert. Die Erwärmung der Bleche und damit die Größe des entstehenden Schweißpunktes spiegelt der Widerstand wider. Da sich beide Größen während der Verbindungsbildung ändern (dynamischer Widerstand), soll der Widerstandsmittelwert aus den Effektivwerten beider Größen berechnet werden. Diese skalare Größe repräsentiert in diesem Falle das Objekt „Widerstandsschweißpunkt“. Für eine genauere Betrachtung kann man die Auflösung der Messung erhöhen und mittlere Messwerte der elektrischen Größen über ein Zeitfenster (z. B. alle 20 ms) nutzen, aus denen jeweils der Quotient gebildet wird. Es ergibt sich eine Folge von Messwerten, deren Komponenten als Merkmalsvektor aufgefasst werden kann. Er ist grafisch durch eine Profildarstellung visualisierbar.
Signale und Merkmale
Die Überwachungsmerkmale werden aus messbaren physikalischen Prozessgrößen extrahiert. Die Prozesssignale und die daraus abgeleiteten Merkmale müssen eine hohe Korrelation mit der Qualität aufweisen, wenn sie zur Qualitätsbewertung herangezogen werden sollen. Die Frage, welche Prozesssignale und Merkmale für eine spezielle Überwachungsaufgabe genutzt werden sollten, kann formal nicht beantwortet werden. Nur in Prozessanalysen kann geklärt werden, welche Signale und abgeleitete Merkmale genügende Korrelation mit der Produktqualität zeigen.
Forderungen an Merkmale
Generell sollten Merkmale folgende Forderungen erfüllen:[1]
- sie müssen eindeutige funktionale Zusammenhänge mit mindestens einem oder mehreren Qualitätsmerkmalen zeigen und auf diese Weise eine möglichst eindeutige Zuordnung der Qualität ermöglichen,
- eine Prozessänderung ohne Qualitätsänderung darf den Merkmalsvektor nicht relevant beeinflussen,
- der Störpegel der Prozesssignale muss signifikant geringer sein als die Signaländerung durch relevante Prozessstörungen,
- bei Anwendung mehrerer Merkmale sollte die Korrelation zwischen den Merkmalen möglichst gering sein.
Merkmalskorrelation
Korrelierende Merkmale haben für die Klassifikation keine zusätzliche Information. Korrelation zwischen Merkmalen führt zu gedreht liegenden Klassen im Merkmalsraum. Die Drehung wirkt sich auf die Klassierung ungünstig aus. Wenn die Klasse z. B. durch scharfe, achsparallele Grenzen beschrieben wird, führt das dazu, dass sich der Gültigkeitsbereich auch in die Ecken des umschriebenen Rechtecks erstreckt (rote Flächen in nebenstehendem Bild). Diese Bereiche liegen jedoch tatsächlich außerhalb der Klasse, denn die Klasse wird nur durch die grün dargestellten Objekte repräsentiert. Objekte mit Merkmalswerten innerhalb des roten Bereiches (blaue Objekte) werden fälschlicherweise als zur Klasse gehörend angesehen. Das kann durch Klassenbeschreibungen, die diese Klassendrehung berücksichtigen (z. B. Kerndichteschätzung oder Fuzzy-Pattern-Klassenbeschreibung) vermieden werden. Möglich ist auch eine Merkmalsvorbehandlung, die eine Transformation der Merkmale in der Weise vornimmt, dass Korrelation vermieden wird (Hauptkomponentenanalyse, Diskriminanzanalyse oder Unabhängigkeitsanalyse).
Klasse
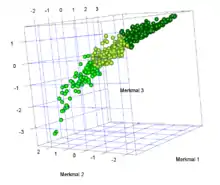
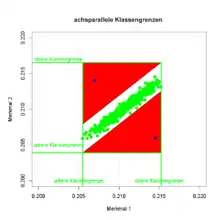
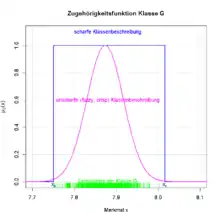
Klassen sind Mengen von Objekten mit ähnlichen Merkmalswerten, z. B. alle Widerstandsschweißungen mit einem Widerstandsmittelwert innerhalb bestimmter Minimal- und Maximalgrenzen oder solche, die der Qualität „in Ordnung – iO“ zuzuordnen sind. Die Ähnlichkeit kann nach inhaltlichen (semantischen) oder formalen Kriterien bestimmt werden. So lassen sich semantische und natürliche Klassen unterscheiden. Semantische Klassen fassen Objekte zusammen, die im inhaltlichen Sinne (z. B. der Qualität) ähnlich sind. Natürliche Klassen bestehen aus formal ähnlichen Objekten.[2] Diese Unterscheidung ist für die Prozessüberwachung sinnvoll. Es ist Ziel der Überwachung, eine weitgehende Übereinstimmung zwischen Qualitätsklassen (semantisch) und den natürlichen Klassen (formal) herzustellen. Im automatisierten Überwachungsprozess kann nur mit natürlichen Klassen umgegangen werden, wobei die semantische Klasse „in Ordnung – iO“ oftmals nur durch mehrere natürliche Klassen abgebildet werden kann, um die nötige Güte der Klassierung zu erreichen. Dann wird eine semantische Klasse durch mehrere natürliche Klassen abgebildet.
Disjunkte, nichtdisjunkte, scharfe und unscharfe Klassen
Klassen können disjunkt sein, d. h. sie sind durch scharfe Ränder begrenzt. Alle Objekte mit Merkmalswerten innerhalb der scharfen Grenzen gehören nur in diese Klasse, alle anderen Objekte nicht. Solche Klassen sind in der realen Welt selten. Objekte gehören dort eher mehr oder weniger stark einer Klasse an, oftmals haben sie auch mehr oder weniger ausgeprägte Eigenschaften und damit Merkmalswerte anderer Klassen. Die Klassen sind nicht disjunkt, die Grenzen fließend. Da keine Klassengrenzen beschrieben werden können, werden diese Klassen durch Verteilungsfunktionen abgebildet, die sich als Zugehörigkeitsfunktionen auffassen lassen. Die Zugehörigkeitsfunktion weist jedem Objekt der Merkmalsmenge eine Zahl aus dem reellwertigen Intervall zu, welche den Zugehörigkeitsgrad des Objekts zur so definierten unscharfen Menge angibt. Statt des Begriffes Zugehörigkeitsgrad wird auch Zugehörigkeitswert oder Sympathiewert[2] benutzt.
Grafische Darstellung von Objekten und Klassen
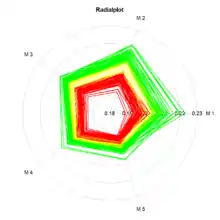
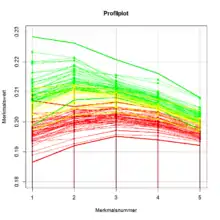
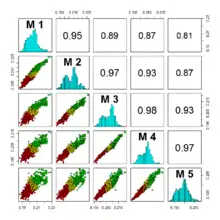
Klassen aus Objekten im höherdimensionalen Merkmalsraum können ebenso wie die Objekte durch Radial – oder Profilplots grafisch dargestellt werden. Eine besondere Form der grafischen Darstellung der Objekte einer Klasse sind eingefärbte mehrdimensionale Streudiagramme. Es werden jeweils zwei Merkmale in einer Matrix von 2D-Darstellungen visualisiert. Da eine Seite der Matrixdiagonalen dafür ausreicht, können auf der Diagonalen die Häufigkeitsverteilungen der Objekte über einem Merkmal dargestellt werden und auf der anderen Seite die Korrelationskoeffizienten zwischen den Merkmalen.
Objekt- und Klassengleichheit oder -ähnlichkeit
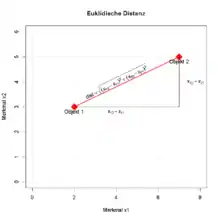
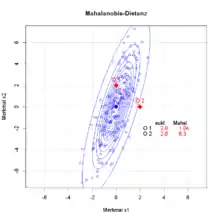
Die automatische Überwachung durch Computer kann nur mit formaler Gleichheit oder Ähnlichkeit arbeiten. Dabei wird Gleichheit oder Ähnlichkeit durch Distanzen im Merkmalsraum ausgedrückt. Befindet sich ein Objekt (oder eine Klasse) zum anderen innerhalb eines definierten Abstandes kann es als gleich angesehen werden. Da die Merkmale bei der Online-Prozessüberwachung mehrheitlich auf metrischen Skalen erklärt sind, wird häufig die Euklidische Distanz zur Bestimmung der Ähnlichkeit herangezogen. Sie ist die direkte Entfernung zwischen zwei Objekten im Euklidischen Merkmalsraum.
Korrelieren Merkmale untereinander, drückt die Euklidische Distanz in Richtung der Korrelationsachse einen scheinbaren Unterschied der Objekte aus. Soll die Korrelation bei der Distanzberechnung berücksichtigt werden, bietet sich die Mahalanobis-Distanz zur Berechnung der Objektähnlichkeit an. Das sei an folgendem Beispiel erläutert. Die euklidischen Distanzen der Objekte O1 und O2 zum Schwerpunkt aller Objekte M[0,0] sind gleich und betragen jeweils 2. Die Ellipsen in nebenstehendem Bild sind die Schätzungen (0,1 % … 99,9 %) der Gaußverteilung für die gegebenen Objekte. Die beiden Merkmale M1 und M2 liegen auf der Ellipse 1 (0,1 %) und 6 (50 %), haben also hinsichtlich ihrer Varianzen zum Mittelpunkt sehr unterschiedliche Distanzen, während die Euklidische Distanz beider Objekte zum Mittelpunkt ist gleich ist. Diese Differenz wird durch die Mahalanobisdistanz abgebildet.
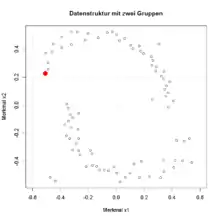
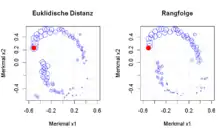
Zusätzlich zu geometrischen Abständen kann Ähnlichkeit zwischen Objekten auch durch die Berücksichtigung der inneren Verteilungsstruktur der Objekte im Merkmalsraum definiert werden. Beispiel: Nebenstehendes Bild zeigt Objekte, die im zweidimensionalen Merkmalsraum für einen menschlichen Betrachter deutlich in zwei Gruppen angeordnet sind. Sie haben jeweils untereinander eine Ähnlichkeit, die durch ihre gemeinsame Nähe, durch ihren Rang innerhalb einer Gruppe, gestützt wird. Wird die Ähnlichkeit eines Objektes zu allen anderen Objekten allein durch die Distanz bestimmt, haben einige Objekte beider Gruppen eine größere Ähnlichkeit zu diesem Objekt als Objekte der eigenen Gruppe. Wird die Rang der Objekte innerhalb der Gruppe mit berücksichtigt, ergibt sich ein deutlich anders Bild. Für die Berücksichtigung des Ranges für die Distanzberechnung wurde durch Zhou u. a. ein Algorithmus entwickelt (Ranking on Data Manifolds).[3]
Die Wahl des Distanzmaßes hat auf die Zuordnung einzelner Objekte zu einer Klasse große Bedeutung.
Prozessüberwachung
Klassifikationsverfahren
Für die Qualitätsüberwachung werden statistische Mustererkennungsverfahren auf der Basis überwachter Klassifikation (überwachtes Lernen, supervised learning) eingesetzt. Die Klassifizierungsverfahren müssen im automatisierten Herstellungsprozess in Echtzeit handhabbar sein. Der gesamte Überwachungsvorgang hat zwei Phasen:
- Lern- (Trainings-) und Validierungsphase
- Anwendungsphase
Trainingsphase
Der Fertigungsprozess wird in der Trainingsphase über einen bestimmten Zeitraum messend beobachtet. Dabei werden Werte von Überwachungsmerkmalen (Merkmalsvektoren) gewonnen und abgespeichert. Es wird die Qualität der einzelnen Verbindungen gemessen und zusammen mit den Merkmalsvektoren gespeichert. Der Grad der Prozessstabilität und der Prozessfähigkeit während dieses Fertigungszeitraumes wird bestimmt. Liegt ein beherrschter und fähiger Prozess vor, bildet die Menge aller abgespeicherter Merkmalsvektoren (Lernobjekte) die Basis für die semantische iO-Klasse. Daraus wird durch eine mathematische Beschreibung ein Klassifikator berechnet (Klassenbeschreibung). Dieser Vorgang wird als überwachtes Lernen bezeichnet. Der Klassifikator wird gespeichert und dient in der Anwendungsphase der Bewertung unbekannter Merkmalsvektoren.
Vor jeder Klassenbeschreibung aus vorhandenen Beispielobjekten wird eine Festlegung getroffen, welche Objekte zur iO-Klasse gehören. Diese Bewertung wird durch einen Experten (Lehrer) vorgenommen. Aus pragmatischen Gründen wird für die Prozessüberwachung nur eine semantische Klasse – die i.O.-Klasse – gebildet, denn aus Kosten- und Aufwandsgründen kann eine technologische Absicherung nur für die aufgetretenen i.O.-Prozesse vorgenommen werden. Es ist unmöglich, alle denkbaren Prozesssituationen und damit auch Prozesse ungenügender Qualität durch Beispieldaten zu stützen.
Die i.O.-Klasse kann Objekte aus verschiedenen technologischen Prozesssituationen enthalten. Die Merkmalswerte innerhalb der semantischen i.O.-Klasse unterscheiden sich in diesem Falle mehr oder weniger stark und sie kann dann aus mehreren natürlichen Untergruppen bestehen, die jeweils einem technologisch ähnlichen Zustand entsprechen. Die Struktur formal ähnlicher Subklassen kann durch Anwendung von Clusterverfahren gefunden werden.
Beschreibungsverfahren für Klassen
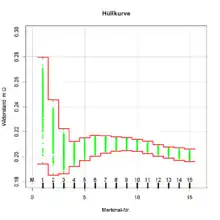
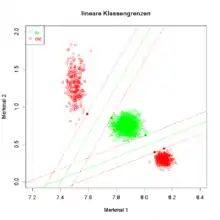
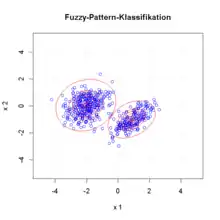
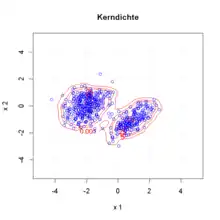
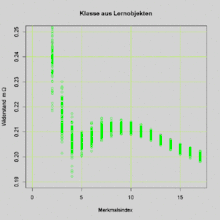
Vor der Klassenbeschreibung liegen Datensätze von Merkmalsvektoren mit Klassenzuordnung vor, die durch einen Experten (Lehrer) nach möglicherweise formaler Trennung in natürliche kompakte Subklassen bereitgestellt werden.
Eine natürliche Klasse hat eine Lage und Streuung im Merkmalsraum, deren Ort im Merkmalsraum mit mathematischen Mitteln beschrieben werden muss. Nur so lassen sich unbekannte Objekte maschinell zuordnen. Dieser Prozess wird Klassenbeschreibung genannt. Dafür wurden die unterschiedlichsten Konzepte entwickelt:
- Beschreibung durch scharfe Klassengrenzen (z. B. Trennfunktionen oder Hüllkurven),
- Beschreibung durch Verteilungsfunktionen (z. B. mittels Kerndichteschätzung, EM-Algorithmus mit Gaussian Mixture Models[4] oder Fuzzy- Pattern- Klassenbeschreibung[2]).
Das Resultat einer Klassenbeschreibung ist ein Klassifikator als Instanz für die Klassenzuordnung (Klassierung) unbekannter Objekte zu einer oder mehreren definierten Klassen.
Nachlernen und Klassentrennung
Die Schweißverfahren sind im Allgemeinen zeitvariant, d. h., sie ändern über eine gewisse Zeit durch Verschleiß und Änderung der technologischen Situation ihr Verhalten, ohne dass sich unbedingt die Qualitätsergebnisse signifikant ändern müssen. Um dem Rechnung zu tragen, muss ein Nachlernen in der sich anschließenden Arbeitsphase (Nutzung des Klassifikators) möglich sein.
Das Nachlernen kann zu einer übermäßigen lokalen Dehnung der Klasse führen, die je nach Beschreibungsverfahren zu einer Verschlechterung der Klassierung führt. Das kann durch eine Aufspaltung der Klasse in einzelne kompakte Subklassen verhindert werden. Dazu werden Verfahren des unüberwachten Lernens, z. B. Clusterverfahren, angewendet.
Nebenstehendes Bild zeigt ein Beispiel der Klassenbildung beim Widerstandspunktschweißen. Die Merkmale sind Abtastwerte des dynamischen Widerstandes. Die Klassen werden aus Beispielobjekten gebildet. Nach weiterem Schweißen zeigen sich neue, außerhalb der Klasse liegende Objekte, die nach einer Prüfung für gut befunden werden. Die Objekte werden zur Klasse hinzugefügt. Die Klasse wird breiter. Bei Anwendung der Klassenbeschreibung durch Hüllkurven verschlechtert sich die Klassifizierung. Die Klasse wird durch k-means-Clusterung in zwei Subklassen aufgespalten, die getrennt durch Hüllkurven beschrieben und zur Klassifizierung genutzt werden.
Anwendungsphase
In der Anwendungs- oder Überwachungsphase werden in Echtzeit die Merkmalsvektoren des aktuellen Prozesses berechnet. Sie werden mit Hilfe des Klassifikators mit den gegebenen I.O.-Klassen verglichen. Alle Merkmalsvektoren außerhalb dieses Bereiches oder unterhalb einer Zugehörigkeitswertschwelle werden als nicht in Ordnung (niO) bewertet. In diesem Falle kann ein Eingriff in die Fertigungssteuerung vorgenommen werden. Die Bewertungsergebnisse werden gespeichert, statistisch ausgewertet und zur Visualisierung bereitgestellt.
Komponenten eines Systems zur Schweißprozessüberwachung
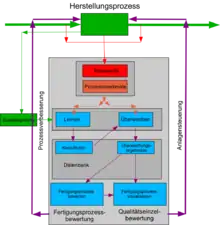
Ein Überwachungssystem ist ein Hardware-Softwaresystem. Es verfügt über technische Mittel zur Durchführung aller Teilaufgaben einschließlich der Mensch-Maschine-Kommunikation. Es ist technisch in den Fertigungsarbeitsplatz eingebunden, der im einfachsten Fall aus einem Schweißwerkzeug besteht (Schweißmaschine, Schweißzange, Schweißbrenner), das durch einen Menschen bedient wird. Im komplexen Fall müssen gleichzeitig mehrere Roboter, Schweißzangen, Bauteile und Schweißverbindungen überwacht werden. Außer der gewachsenen Komplexität ändert sich dabei nichts am grundsätzlichen technischen Konzept. Nebenstehendes Bild zeigt das grundsätzliche Schema eines solchen Systems.
Die Hardware besteht aus Komponenten für die Messwertverarbeitung einschließlich der Sensoren und Messwertübertragung, der Signalverarbeitung, der Datenspeicherung, Bedienung und Visualisierung.
Softwaremodule steuern das Messen der Prozessgrößen und Berechnen der Merkmale. In der Lern- oder Trainingsphase werden aus den Merkmalsdaten geprüfter Lernobjekte Klassifikatoren berechnet und gespeichert (Klassifizierung). Dazu müssen die Prüfergebnisse der Lernobjekte vorliegen und archiviert worden sein, um jederzeit die geprüfte Qualität der Lernobjekte nachweisen zu können. Nach dem Vorliegen gültiger Klassifikatoren werden die Prozessmerkmale in der Anwendungsphase für den Vergleich der aktuellen Merkmalsvektoren mit den Klassen (Klassierung) genutzt. Das Ergebnis Vergleichs ist eine Qualitätsbewertung jeder einzelnen Schweißverbindung. Daraus kann eine Rückmeldung an die Anlagensteuerung generiert werden. Die Überwachungsergebnisse werden in Datenbanken archiviert und stehen für statistische Auswertungen zur Verfügung. Die komprimierten Auswertungsergebnisse werden in Echtzeit visualisiert. Daraus ergeben sich Hinweise für die Prozessverbesserung.
Prozessüberwachung durch Beobachtung und Bewertung der Prozessstabilität
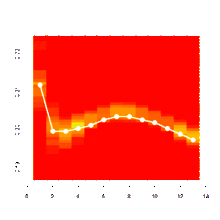
Online-Überwachungssysteme können auch zur Bewertung der Prozessstabilität eingesetzt werden. So wird rechtzeitig das Verlassen des technologisch gewünschten Prozessfensters signalisiert und Abstellmaßnahmen können eingeleitet werden. Auf diese Weise werden Funktionen der Anlagenzustandsüberwachung in Online-Überwachungssysteme integriert, um Fehlfunktionen des Schweißprozesses durch Anlagenstörungen wie mangelhafter Elektrodenzustand, Störungen des Kraft- oder Kühlsystems, Änderungen der Werkstückoberflächen u. ä. zu erkennen und frühzeitig abzustellen. Diese Verfahrensweise wird in der VW-Norm PV 6702[6] als Adaptive Prozessvisualisierung[5] bezeichnet. Dabei werden gemessene Daten gespeichert und durch eine besondere Form einer Profildarstellung visualisiert. Die Merkmalswerte jeder Einzelschweißung (Objekt) werden sequenziell über einer Laufvariablen aufgetragen, z. B. jede Schweißung wird durch ihren zeitlichen Merkmalsverlauf repräsentiert. Aus der Menge aller von einem Startwert bis zum aktuellen Zeitpunkt gespeicherten Objekte werden über jedem Merkmal (Stützwert der Laufvariablen) Häufigkeitsverteilungen berechnet. Die aktuelle Häufigkeit wird durch einen Farbwert visualisiert. Während eines laufenden Prozesses verändern die Häufigkeitsverteilungen dynamisch ihre Form und Lage. So entsteht ein dynamisches statistisches Abbild des Prozesses. Die Varianz ist unmittelbar durch die Farbgebung zu erkennen. Ein statistisch weitgehend invarianter Prozess ist durch ein scharfes Farbband gekennzeichnet, ein stark variierender Prozess wird sowohl seine Form und Lage als auch die Schärfe seiner farblichen Kontur ändern.
Struktur
Für die Rückverfolgung der Schweißverbindungsgüte muss jede einzelne Verbindung durch eine eindeutige Signatur gekennzeichnet sein. Aus ihr muss sich entnehmen lassen, an welchem Schweißarbeitsplatz das Bauteil und die spezielle Verbindung wann geschweißt worden ist. Jede Schweißeinrichtung hat eine eigene Kennzeichnung, die mit einer Bauteil- und Verbindungsnummer und einem Zeitstempel zur eindeutigen Identifikationsnummer nach Abschluss der Schweißung zusammengefasst wird. Diese Signatur wird zusammen mit dem Ergebnis der Gütebewertung und den Istwerten der Schweißparameter archiviert.
Für die permanente Prozessverbesserung ist vorteilhaft, für jede Verbindung die Lage auf dem Bauteil, die Materialgüte und Oberflächenbeschaffenheit, die Materialabmessungen und die eingestellten Schweißparameter im System verfügbar zu haben.
Ein Überwachungssystem sollte in der Lage sein, die Schweißverbindungsnummern zu generieren und zusammen mit den genannten Informationen komfortabel zu archivieren und über eine visuelle Mensch-Maschine-Schnittstelle zu verfügbar zu machen.
Einbindung von Überwachungssystemen in einen Handarbeitsplatz
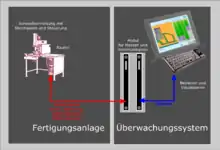
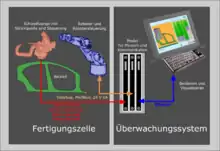
Der Arbeitsplatz besteht je nach Schweißverfahren aus einer Schweißmaschine oder Schweißzange beim Widerstandsschweißen oder einer Schweißstromquelle und einem Schweißbrenner beim Lichtbogenschweißen mit einer eindeutigen Gerätekennzeichnung. Er ist mit Sensoren für die Messung der Überwachungsgrößen ausgestattet. Das Werkstück wird durch eine Vorrichtung gehalten und gegebenenfalls manipuliert. Ein Bediener führt das Werkstück zum Schweißwerkzeug (beim Widerstandsschweißen) oder das Schweißwerkzeug zum Werkstück (beim Lichtbogenschweißen). Der Schweißprozess wird durch den Bediener über die Schweißsteuerung ausgelöst.
Die Sensorsignale werden einem Modul zur Merkmalsberechnung und Prozessüberwachung über Messleitungen zugeführt. Diese sind der einzige Kommunikationskanal zwischen dem Überwachungssystem und der Anlage. Überwachungsbeginn und -ende werden durch den beginnenden Stromfluss signalisiert (Trigger). Ein interner Zähler erzeugt eine Verbindungsnummer und zählt die Anzahl der Verbindungen. Ist eine voreingestellte Verbindungsanzahl erreicht, wird das Bauteilende signalisiert und eine Bauteilnummer generiert. Sollte diese einfache Lösung zu unsicher sein, müssen durch Steuerungsmaßnahmen Bauteilbeginn und -ende (Tigger) und die jeweilige Verbindungsnummer generiert werden. Daten werden für jede Bauteil- und Verbindungsnummer archiviert.
Einbindung von Überwachungssystemen in komplexe Fertigung
Komplexe Bauteile, wie z. B. eine Karosserie, werden in komplexen Schweißanlagen gefertigt, die aus mehreren Schweißstationen mit zahlreichen Schweißrobotern bestehen. Jeder Roboter kann beim Widerstandsschweißen mehrere Wechselzangen bedienen.
Das Werkstück wird durch Vorrichtungen gehalten und manipuliert. Roboter führen das Schweißwerkzeug mit eigener Kennung zum Werkstück (oder das Werkstück zum Schweißwerkzeug). Die Robotersteuerungen sorgen für den richtigen Fertigungsablauf, möglicherweise übernehmen sie auch die Aufgaben der Manipulator-, Zangen- und Schweißsteuerungen. Die Steuerungen stellen die Informationen über den aktuellen Schweißprozess bereit. Stations-, Roboter-, Zangen-, Brenner-, Bauteil- und Schweißverbindungsnummer bereit. Auch die Ein- und Ausschaltsignale für die Prozessüberwachung werden durch die Steuerung ausgelöst und vom Überwachungssystem übernommen.
Visualisierung eines Überwachungssystems
Eine wesentliche Funktion von Online-Überwachungssystemen besteht über die Überwachungsfunktion hinaus in der Bereitstellung von Informationen über den gesamten Schweißprozess. Nur so kann die Prozessqualität permanent verbessert werden. Es sind verschiedenste Konzepte für die Darstellung von Prozessinformationen entwickelt worden. Letztlich gründen sie alle auf mehr oder weniger komplexen Visualisierungen. Der nebenstehende Film zeigt die strukturellen Möglichkeiten solcher Visualisierung auf.
Online-Prozessüberwachung beim Widerstandsschweißen
Überwachungsgrößen und -merkmale
Die Schweißverfahren stellen wegen ihrer unterschiedlichen physikalischen Wirkmechanismen jeweils spezifische Anforderungen an die Wahl der Überwachungsgrößen und -merkmale, an die angewendeten Verfahren der Prozessbewertung, den Zeitpunkt und die Art der Prozessauswertung im Fertigungsprozess.
Allgemein akzeptierte Qualitätsmerkmale beim Widerstandspunktschweißen sind der Punktdurchmesser dP (ermittelt durch eine Werkstattprüfung) oder der Linsendurchmesser dL (gemessen an einem Makroquerschliff). Auch diese Größen können im Überwachungsprozess nicht direkt gemessen werden, sondern es müssen aus messbaren physikalischen Größen Merkmale für die Überwachung gewonnen werden.
Überwachungsgrößen
Der Punktdurchmesser ist abhängig vom zeitlichen Verlauf der elektrischen Erwärmung. Daraus ergeben sich als potenzielle Überwachungsgrößen:
- der Schweißstrom,
- die Schweißspannung,
- die Schweißleistung und der dynamische Widerstand als kombinierte Größen aus Strom und Spannung
- die Schweißstromzeit.
Die Krafteinwirkung auf die Schweißstelle beeinflusst den Übergangswiderstand und damit den Erwärmungsprozess. Infolge der Erwärmung des Materials vergrößert sich das dessen Volumen, wodurch eine Kraftwirkung auf die Elektrode entsteht. Diese Kraft ist proportional zur Erwärmung. Aus diesen Überlegungen folgt, dass auch die Elektrodenkraft und der Elektrodenrückhub (Elektrodenweg) und daraus abgeleitete Größen wie Elektrodengeschwindigkeit und Elektrodenbeschleunigung Informationen über die Verbindungsbildung liefern können.
Die Bildung der Verbindung geht mit einer Schallemission einher, so dass auch im Schall Informationen über die Verbindung gesucht werden könnten.
Einen Überblick über die in der Vergangenheit untersuchten Überwachungsgrößen vermittelt.[7]
Überwachungsmerkmale
Aus den gemessenen Prozesssignalen werden Merkmale generiert, die mit der Punktschweißqualität korrelieren.[8]
Wechselstromschweißen
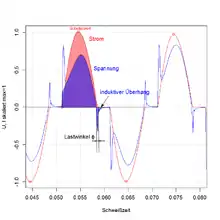
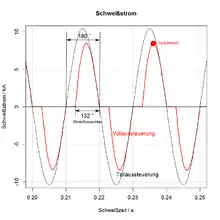
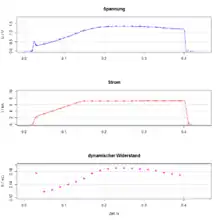
Merkmale, die aus dem Strom beim Wechselstromschweißen gewonnen werden können, sind der Spitzen- oder Scheitelwert und der Effektivwert. Beim Wechselstromschweißen wird der Strom durch Phasenanschnitt verändert. Die Zeitdauer des tatsächlichen Stromflusses pro Halbwelle wird als Stromflusszeit in ms oder bezogen auf die ganze Halbwelle von bei bzw. bei als Stromflusswinkel in ° (Grad) bezeichnet.[9] Durch die Induktivität des Sekundärkreises ergibt sich zwischen Spannung und Strom eine Phasenverschiebung mit einem Lastwinkel . Daraus berechnet sich die Wirkleistung zu . Die Größe des Leistungsfaktors wird im Wesentlichen durch die Fensteröffnung des Sekundärkreises der Schweißzange bestimmt. Alle genannten Größen kommen für die Überwachung des Wechselstromschweißens in Betracht.
Dynamischer Widerstand
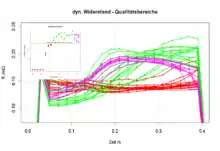
Beim Schweißen mit allen Stromarten ist die Erwärmung und Verbindungsbildung und letztlich die Größe der Schweißlinse von der zeitlichen Entwicklung der Widerstandsverhältnisse während der ablaufenden physikalischen Prozesse an der Schweißstelle abhängig. Die Linsenbildung spiegelt sich deutlich im sogenannten dynamischen Widerstand wider.[10] Er hängt außer von der Werkstofftemperatur auch von der Material- und Oberflächeneigenschaften der Fügepartner ab.
Ein ähnlicher Widerstandsverlauf bei verschiedenen Schweißungen mit gleichen physikalischen Eigenschaften der Fügepartner (Material) deutet auf ähnliche Linsenbildung hin. Beim Schweißen unlegierter Stahlbleche mit blanker Oberfläche durchläuft der Gesamtwiderstand drei zeitliche Abschnitte:
- Im ersten Abschnitt ist der Widerstand stark fallend und wird vom Oberflächenzustand der Werkstücke und der Elektroden bestimmt. Durch das Zusammenpressen der Bleche sinkt er innerhalb kurzer Zeit.
- Der Stoffwiderstand wächst auf Grund der Temperaturerhöhung an der Kontaktstelle, gleichzeitig dringen die Elektroden mit zunehmender Materialerweichung in das Werkstück ein. Der Stromweg und damit der Widerstand fallen.
- In der Schlussphase verringert sich der Stoffwiderstand infolge des starken Elektrodeneindringens in das Werkstück.
Diese Vorgänge überlagern sich, so dass der dynamische Widerstand seinen charakteristischen Verlauf bekommt.
Zusammenhang zwischen dynamischem Widerstand und Punktdurchmesser
Die Änderung des Punktdurchmessers und der Form und Lage des dynamischen Widerstandes infolge von verändertem Energieeintrag zeigen die Bilder (2 × 1,5 mm Stahlblech H320 mit beschichteter Oberfläche). Die Energie wurde durch Stromvariation verändert. Bei zu geringem Energieeintrag verläuft der Widerstand flach, die Punktdurchmesser sind kleiner als erforderlich (rot). Mit gesteigerter Energie wächst der Punktdurchmesser und überschreitet die erforderliche Spezifikationsgrenze. Der dynamische Widerstand steigt an und es bildet sich ein ausgeprägtes relatives Maximum aus (grün). Bei weiterer Energiesteigerung verschiebt sich das Maximum auf einen früheren Zeitpunkt. Der Widerstandsabfall nach dem Durchlaufen des relativen Maximums wird mit steigender Energie steiler. Nach Überschreiten der Spritzergrenze schwanken die Schweißpunktgrößen wegen des Materialverlustes durch Spritzer. Spritzer sind als Steilabfall des dynamischen Widerstandes erkennbar (magenta).
Merkmale aus dem dynamischen Widerstand
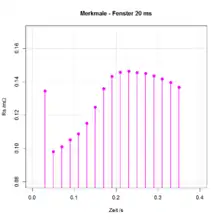
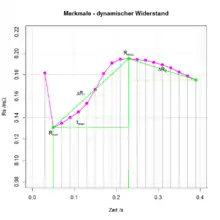
Zur Prozessüberwachung mit Hilfe des dynamischen Widerstandes, müssen Merkmale gefunden werden, die ein Abbild von Form und Lage darstellen. Im einfachsten Falle lassen sich über ein Zeitfenster gemittelte Abtastwerte rs(t) nutzen. Vorteilhaft bei dieser Vorgehensweise ist, dass jede Kurvenform problemlos nachgebildet werden kann. Die Merkmalsanzahl hängt dann von der Schweißzeit ab, was sich nachteilig auf die praktischen Handhabung auswirkt. Außerdem korrelieren diese Merkmale in hohem Maße im Bereich steigenden oder fallenden Verlaufs. Die Anwendung zusätzlicher Achstransformationen zur Merkmalsvorbehandlung ist in diesem Falle sinnvoll.
Günstiger als eine direkte Abbildung des dynamischen Widerstands durch Stützwerte sind Merkmale, die von der Schweißzeit unabhängig und weitgehend frei von Korrelation sind. Für den dynamischen Widerstand mit ausgeprägtem relativen Widerstandsmaximum, wie er sich beim Schweißen unlegierter Stahlbleche ausformt, bieten sich folgende geometrische Größen an:
- die Höhe des relativen Maximums : Rmax
- der Zeitpunkt minimalen Widerstandes Rmin nach der Kraftaufbringung tmin
- der Zeitpunkt des Erreichens von Rmax tmax
- die Steigung R vom Minimum Rmin bis zum Erreichen von Rmax dR1
- die Steigung von Rmax bis zum Schweißende: dR2
Auch damit kann die Form und Lage des Verlaufes eindeutig nachgebildet werden.
Merkmale aus mechanischen Größen
In Folge der ohmschen Erwärmung der Fügepartner an der Schweißstelle dehnt sich das Material lokal aus. Es besteht ein proportionaler Zusammenhang zwischen der Wärmeentwicklung, der daraus resultierenden Temperaturerhöhung und der Materialvolumenausdehnung:
mit:
- Volumenänderung
- Ausgangsvolumen
- Temperaturänderung
- linearer Ausdehnungskoeffizient.
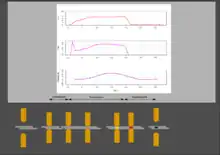
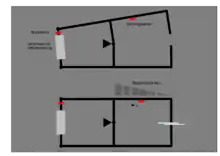
Das umgebende kalte Material behindert die Volumenausdehnung, so dass die Ausdehnungsrichtung auf die Materialoberfläche zeigt. Solange die Flächenpressung der Elektroden unterhalb der Fließgrenze des Werkstoffs ist, verdicken sich die Bleche. Die Elektrodenkraft wirkt dem entgegen. Mit steigender Temperatur sinkt die Fließgrenze des Materials. Die Folge ist ein Eindringen der Elektroden in das Material. Während der Stromflusszeit überlagern sich die thermische Ausdehnung und die Materialerweichung mit dem Einsinken der Elektrode. Bestimmende Größe für den Prozess ist die Materialtemperatur, die vom Stromfluss und dem Widerstand an der Wirkstelle abhängt. Der beschriebene Vorgang verursacht eine Wegänderung an den Elektroden (engl: thermal expansion TE), bzw. eine Änderung der Elektrodenkraft, sofern das mechanische System sich elastisch verformen kann. Die Kraft- bzw. die Wegänderung während des Schweißvorgangs ist ein indirektes Maß für die Temperatur in der Schweißzone.
Nebenstehendes Bild zeigt schematisch den Kraftaufbau während der lokalen Materialerwärmung durch eine servomotorisch betätigte X-Schweißzange und die Anordnung von Kraftsensoren. Nachdem der Servomotor die eingestellte Elektrodenkraft erreicht hat, wirkt die Selbsthemmung der Antriebsspindel während der Schweißzeit. Die Zange kann als mechanisch elastisch verformbares System betrachtet werden, bei dem die Zangenarme als elastisches Federglied wirken. Am Drucksensor wird die Elektrodenkraft gemessen, am Dehnungssensor ein Moment, das einer Kraft proportional ist. Mit beginnender Materialdehnung wächst die Kraft. Diese zusätzliche Kraft ist ein Maß der Materialdehnung und damit der Erwärmung.
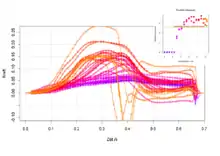
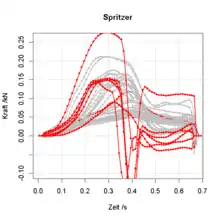
Bei variiertem Energieeintrag durch Stromänderung zwischen der Kleb- und Spritzergrenze ändert sich die Ausdehnungskraft infolge der Materialerwärmung. Bei kleinem Strom ist nur eine geringe Materialausdehnung beobachtbar. Diese steigt mit zunehmender Erwärmung an und durchläuft nach steiler werdendem Anstieg ein Maximum. Es kommt zu einem Kraftabfall, sobald das Fließen des Materials beginnt. Bei einsetzenden Spritzern im Bereich oberhalb der Spritzergrenze bricht die Kraft ein.
Das Signal der Elektrodenkraftänderung liefert ein sehr gutes Abbild der Schweißpunktgröße. In nebenstehendem Bild sind die Schweißpunktgrößen in Abhängigkeit vom Schweißstrom und die zugehörigen Kraftverläufe dargestellt. Unterhalb der erforderlichen Erwärmung für das Erreichen eines genügenden Punktdurchmessers verläuft die zeitliche Kraftänderung relativ flach. Ausreichende Verbindungsbildung ist gekennzeichnet durch einen zügigen Anstieg mit ausgeprägtem Maximum. Spritzer bewirken eine größere Streuung des Punktdurchmessers und einen Steilabfall der Elektrodenkraft durch den Materialverlust infolge des Materialspritzens.
Während die Verlaufsform des dynamischen Widerstandes durch verschiedene Umgebungsbedingungen wie die Zusammensetzung des Werkstoffs (z. B. Stahlfeinbleche mit höherer und höchster Festigkeit wie DP, TRIP, Mangan-Bor-Stahl zum Warmumformen oder austenitischer rostfreier Stahl, Aluminiumlegierungen), unterschiedliche Oberflächenbeschichtungen, dem Einsatz von Klebstoff, den zu verschweißenden Blechdicken, Nebenschluss und Passung der Bleche stark beeinflusst wird, ist der dynamische Kraftverlauf nur von der Materialerwärmung und dem Ausdehnungskoeffizienten des Materials abhängig. Die Vorteile des beschriebenen physikalischen Mechanismus gegenüber der Nutzung des dynamischen Widerstandes als Überwachungsgröße scheinen daher groß zu sein. So sind in der Vergangenheit verschiedene Verfahren zur Prozessüberwachung unter Nutzung der thermischen Ausdehnung entwickelt und teilweise durch Patentanmeldungen geschützt worden.[11][12][13] H. Heinz, W. Rennau:[14] Eine ausführliche Literaturzusammenstellung zur Beschreibung und zur Nutzung dieses physikalischen Effektes findet man bei Janota.[15]
Praktische Probleme haben jedoch bisher den industriellen Einsatz unterbunden. Ein Problem ist das Schieben der Zangen (besonders der X-Zangen). Dabei treten durch slip-stick-Effekte vermehrt Kraftsprünge auf, die das Signal verfälschen. Ein anders Problem besteht darin, dass eine Kraftkonstantregelung bei servomotorischen Schweißzangen diese Überwachungsgröße hinfällig macht. Der Regler bei elektromotorischen Zangen ist ein aktives Glied im Masse-Feder-System der Zange und überlagert den qualitativen Verlauf der Kraft und vermindert deren Aussagefähigkeit. Diese Überlagerung ist vom dynamischen Verhalten der gesamten Regelstrecke abhängig.
Für die Nutzung des beschriebenen Effektes bei der Prozessüberwachung muss die Kraftkurve durch geeignete Merkmale repräsentiert werden. Es können dafür die gleichen Methoden wie bei der Nutzung des dynamischen Widerstandes angewandt werden.
Funktionsweise eines Überwachungssystems
Im Folgenden wird eine mögliche Funktionsstruktur eines Überwachungssystems beschrieben. Dabei soll auf die Verarbeitung der Prozessdaten von der Merkmalsbildung bis zum Überwachungsergebnis eingegangen werden. Fragen der Gerätetechnik bleiben dabei unberührt. Es gibt verständlicherweise eine sehr große Zahl möglicher Realisierungen. Eine davon wird schematisch dargestellt.
In einem konkreten Überwachungssystem sind die gemessenen Prozesssignale und die daraus gebildeten Merkmale festgelegt, ebenso die implementierten Algorithmen für die Bildung der Klassifikatoren und für die Berechnung des Überwachungsergebnisses.
Merkmalsbildung
- Merkmale einer Menge von Schweißungen gebildet aus dem dynamischen Widerstand durch Bildung von Mittelwerten über ein Zeitfenster des Signalverlaufes. Genutzt werden nur die grün dargestellten Merkmale, die die Signalform genügend genau abbilden.
- Merkmale der Lernschweißungen, aus denen die Klassen gebildet werden. Für eine genauere Klassenbeschreibung wurde die Lernobjektgruppe durch Clustern in drei Subgruppen geteilt, die als Basis für die Klassenbeschreibung dienen.
- Merkmale der Lernschweißungen als Streudiagramm über jeweils zwei Merkmale
- Beschreibung der drei Subklassen durch EM-Algorithmus
Basis für die Merkmalsbildung ist der dynamische Widerstand. Dazu werden der Schweißstrom und die Spannung an den Elektroden gemessen. Die Signale liegen als digitalisierte Messwertfolgen vor. Durch geeignete Division wird daraus der dynamische Widerstand berechnet. Als Merkmale werden die Mittelwerte des Widerstandsverlaufes über ein Zeitfenster von jeweils 20 ms berechnet. Zur Reduktion der Merkmalsanzahl sollen nur vier der Merkmale herangezogen werden, die sicherstellen, dass die Verlaufsform des dynamischen Widerstandes genügend genau nachgebildet wird.
Klassenbildung in der Trainingsphase
Für die Überwachung müssen Sollklassen aus den Merkmalen von Lernschweißungen gebildet werden. Als Lernschweißungen dienen die Merkmale einer Gruppe geprüfter Schweißverbindungen. Nebenstehende Abbildungen zeigen die Gruppen von Lernobjekten sequenziell als Profilplot und im Streudiagramm über jeweils zwei Merkmale mit einem Einzelobjekt als blauen Punkt.
Die Klassenmodelle werden in der Trainingsphase mittels des EM-Algorithmus berechnet und die Modellparameter (Mittelwerte und Kovarianzmatrizen) als Klassifikator abgespeichert.
Wegen der unterschiedlichen Lage auf dem Bauteil, der anders gearteten Position der Schweißzange und ähnlichen Einflussfaktoren ist der Sollverlauf der Merkmale auch bei gleichen Schweißbedingungen verschieden. So muss der Klassifikator für jede einzelne Verbindung eines Bauteils gesondert trainiert werden.
Arbeitsphase
Nach dem Vorliegen von Klassifikatoren können unbekannte Schweißprozesse überwacht werden. Dazu wird der richtige Klassifikator ausgewählt und die Parameter des korrekten Modells werden geladen. Kurz vor dem Einschalten des Schweißprozesses wird der Messvorgang gestartet und nach Abschluss des Prozesses beendet. Die Merkmale werden berechnet und die Klassenzugehörigkeiten zu allen i . O - Prozessklassen werden berechnet. Im Falle der Anwendung unscharfer Klassifikation[16] wird die Zugehörigkeit zur am besten passenden Klasse bestimmt. Liegt die Zugehörigkeit oberhalb einer festgelegten Schwelle, wird die Qualität als i . O . bewertet. Es wird der Zugehörigkeitswert gespeichert. Dieser drückt aus, wie gut der aktuelle Prozess zu einer der angelernten Klassen gehört. Damit können statistische Prozesskennwerte über eine längere Fertigungszeit (wie Prozessstreuung und - stabilität, Trends) berechnet und visualisiert werden.
Visualisierung
- Visualisierung des Sollbereiches vom dynamischen Widerstand nach der Trainingsphase (grüner Bereich) mit vier Subklassen (Profilplot), Lernobjekten für jede Subklasse (farbige durchgezogene Linien) und einer Beispielschweißung (blaue Linie) mit dem System PQS-RES der HWH-QST GmbH[17]
- Visualisierung der Überwachung: Auswahl von Schweißpunkten (PQS-RES)[17]
- Anwendung der unscharfen Klassifikation bei der Prozessüberwachung des Widerstandspunktschweißens.
- Beispiel für die Visualisierung der Überwachung einer Widerstandspunktschweißung
Es ist sinnvoll, das Ergebnis der Klassenbildung für den Nutzer zu visualisieren. Er muss die gewünschte Verbindung auswählen können, um sich ein Bild vom Prozess machen zu können. Dafür ist ein Profilplot geeignet, in dem z. B. die Subklassen der gesamten dynamischen Widerstandsverläufe angezeigt werden, da diese durch den Nutzer direkt interpretiert werden können (s. Bild des Systems PQS-RES). Andere Diagrammformen sind denkbar (Streudiagramme oder Radialplots), wenn sie den Nutzer bei seiner Interpretation der Form und Lage der Klassen und damit des Schweißprozesses unterstützen (die Visualisierung der Klassen merkmalsweise im Streudiagramm, wie oben gezeigt, leistet das nicht, wurde hier jedoch gewählt, um den Klassenbildungsprozess zu erläutern).
Online-Prozessüberwachung beim Lichtbogenschmelzschweißen (MIG/MAG)
Bei der Online-Überwachung eines Schweißprozesses wird der laufende Schweißprozess in Echtzeit überwacht, um die Einhaltung der vorgegebenen technologischen Bedingungen zu ermitteln und auftretende Störungen sofort zu erkennen. Es wird davon ausgegangen, dass bei Einhaltung der gewünschten technologischen Vorgaben wesentliche Anforderungen an die Qualität der entstehenden Schweißnaht erfüllt werden. Ein quantitativer Nachweis einzelner Gütekriterien ist auf diese Weise nicht möglich.
Überwachungsprinzip beim Lichtbogenschmelzschweißen
Die Online-Überwachung vergleicht aktuelle Merkmalsmuster physikalischer Überwachungsgrößen in kontinuierlicher Folge mit vorgegebenen Sollmustern. Die Überwachungsgrößen sollten das Prozessverhalten widerspiegeln und damit Rückschlüsse auf die erwartbare Schweißnahtqualität möglich machen. Das können solche Größen sein, die mit dem Energieumsatz korrelieren oder Ausdruck der Prozessstabilität sind.
Die Ist- und Sollmuster werden innerhalb eines gleichbleibend langen Zeitfensters gebildet. Die ständige Wiederholung ist erforderlich, da mit dem Lichtbogenschweißverfahren theoretisch unendlich lange Schweißverbindungen in unendlich langer Zeit hergestellt werden können. Der Schweißprozess wird in abgeschlossene Zeitintervalle (ähnlich der Frames eines Films) unterteilt, die als Einheit einzeln bewertet werden (s. Bild „Schweißstrom eines MAG-Lichtbogens mit Histogrammen von Signalausschnitten“). Haben die Istmuster genügende Ähnlichkeit mit den Sollmustern, wird ausreichende Qualität angenommen und der aktuelle Schweißnahtabschnitt akzeptiert, anderenfalls zurückgewiesen. Die Zurückweisung kann durch unterschiedliche Maßnahmen ausgedrückt werden, z. B. durch Signalisierung nach Ende des gesamten Prozesses, durch Prozessunterbrechung oder Markierung des entsprechenden Nahtabschnittes.
Die Sollmuster werden durch Referenzschweißungen gewonnen, deren Prozessstabilität und Qualität durch eine Prüfung bestätigt wird.
Elektrische Überwachungsgrößen und -merkmale
- Schweißstrom eines MAG-Lichtbogens mit Histogrammen von Signalausschnitten
- Anteile des ohmschen Spannungsabfalls an der gemessenen Spannung beim MIG/MAG-Schweißen nach [18]
- Gemessene und korrigierte Schweißspannung beim Kurzlichtbogenschweißen
- Gemessene und korrigierte Schweißspannung, Schweißstrom beim Kurzlichtbogenschweißen
Überwachungsgrößen Lichtbogenspannung und -strom
Die folgenden Ausführungen beschreiben eine unter verschiedenen Möglichkeiten, aus Prozessdaten von MIG/MAG-Schweißungen Merkmale zu bilden und für die Prozessüberwachung zu nutzen.
Die Signale der elektrischen Größen drücken sowohl die Lichtbogenenergie als auch die Reproduzierbarkeit des Prozesses aus.
Der Spannungsabfall über dem Lichtbogen und der Spannungsabfall über der freien Drahtlänge liefern unterschiedliche Informationen über den Schweißprozess. Im technologischen Umfeld kann nur der gesamte Spannungsabfall über den Lichtbogen und die freien Drahtlänge , über das Kontaktrohr , über das Werkstück und über das Schweißkabel innerhalb des Spannungsabgriffs gemeinsam gemessen werden (s. Bild „Anteile des ohmschen Spannungsabfalls an der gemessenen Spannung beim MIG/MAG-Schweißen“). Die Induktivität des Schweißkreises und der daraus resultierende induktive Anteil des gemessenen Spannungsabfalls kann für Zwecke der Prozessüberwachung vernachlässigt werden, da er gering und für stationäre Anlagen konstant ist. Das gemessene Spannungssignal kann als Summe aus der Lichtbogenspannung und einer Summe der verschiedenen ohmschen Widerstände multipliziert mit dem Schweißstromsignal aufgefasst werden:
- mit
- .
ist durch Änderungen der Temperaturverhältnisse der freien Drahtlänge, des Zustandes der Stromkontaktdüse, der Drahtoberfläche und der Übergangswiderstände des Werkstücks und Schweißtisches variabel.
Beim Schweißen unter Kurzschlussbildung (Kurzlichtbogen) zeigen die Strom-Spannungs-Kennlinien während der Kurzschluss- und Brennphase unterschiedliche Steigung. Die Steigung in der Kurzschlussphase bildet den Spannungsabfall ab. Ist dieser bekannt, kann aus der gemessenen Spannung eine korrigierte Schweißspannung berechnet werden, die von der Lichtbogenspannung allein bestimmt wird (s. Bilder „Gemessene und korrigierte Schweißspannung beim Kurzlichtbogenschweißen“ und „Gemessene und korrigierte Schweißspannung, Schweißstrom beim Kurzlichtbogenschweißen“).
Während sich in der korrigierten Schweißspannung die Vorgänge im Lichtbogen widerspiegeln, drückt sich in der Kurzschlussspannung die Änderung der freien Drahtlänge und damit der Abstand des Schweißbrenners zur Werkstückoberfläche aus. Daraus folgt, dass es für die Prozessüberwachung beim Schweißen mit Kurzlichtbogen sinnvoll sein kann, die Spannung der Lichtbogen- und Brennphase gesondert zu beobachten. Die Trennung ist durch eine Spannungsschwelle unterhalb einer Mindestbrennspannung von 14 V möglich.
Merkmale aus elektrischen Größen
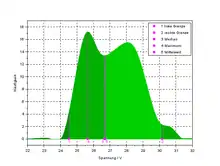
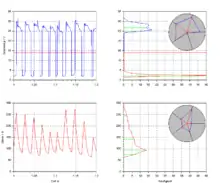
Der zeitliche Verlauf der digitalisierten elektrischen Signale Strom und Spannung lassen sich durch empirische Häufigkeitsverteilungen (Histogramme) charakterisieren [19]. Die deskriptive Statistik benutzt Parameter, um die Lage, Streuung, Konzentration und Gestalt solcher Verteilungen zu beschreiben. Solche Parameter werden als Merkmale für die Überwachung genutzt. Ein Datensatz bestehend aus Merkmalswerten charakterisiert den aktuellen Signalverlauf und kann als Merkmalsistmuster aufgefasst werden. Die Bilder „Bildung von Merkmalen aus den elektrischen Signalen beim MAG-Schweißen mit Kurzlichtbogen“ und „Beschreibende Merkmale eines Histogramms…“verdeutlichen einen möglichen Merkmalsbildungsprozess:
Es wird ein Zeitabschnitt der beiden Spannungssignale betrachtet (linke Teilbilder). Zur Charakterisierung der Form und Lage der Dichteverteilung des Stroms werden die Parameter „linke Grenze“, „rechte Grenze“, „Median“, „Lage des Maximums“ und „Mittelwert“ berechnet (Bild „Beschreibende Merkmale eines Histogramms…“). Die Grenzen links und rechts beschreiben die Lage eines vorgegebenen Prozentsatzes der Fläche unter der Verteilung. Die Spannung wird durch eine Schwelle bei 14 V in eine „Brennphase“ und „Kurzschlussphase“ unterteilt. Für jeden Teilbereich ober- und unterhalb der Spannungsschwelle wird eine empirische Dichte berechnet. Als Merkmale werden aus der „Kurzschlussphase“ nur der „Median“ benutzt, aus der „Brennphase“ die „Grenzen“, der „Median“ und der „Effektivwert“. Zur Illustration eines Merkmalsmusters sind die Merkmalswerte in einem Radialplot dargestellt.
Trainingsphase beim Schmelzschweißen
In der Trainingsphase werden die Sollmuster für die Prozessüberwachung ähnlich wie beim Widerstandspunktschweißen gewonnen (s. Klassenbildung in der Trainingsphase). Da innerhalb einer Schweißnaht mit verschiedenen Schweißparametern und unterschiedlichen Schweißpositionen gearbeitet werden kann, ist das Auftreten verschiedener Prozessklassen wahrscheinlich. Jede Prozessklasse hat ein jeweils eigenes Sollmuster. Ein Überwachungssystem sollte die unterschiedlichen Prozessklassen während der Trainingsphase automatisch erkennen und getrennte Merkmalsdatensätze zum Anlernen der spezifischen Sollmuster zur Verfügung stellen.
Optische Signale
Aus optischen Lichtbogeninformationen kann auf Lichtbogentemperatur und -dynamik geschlossen werden. Es lässt sich daraus auch das Bild der Wechselwirkung zwischen Schweißbad und Zusatzwerkstoff und dem Ort des Schweißbades gewinnen.
Akustische Signale
Das Geräusch des Lichtbogens liefert dem Lichtbogenschweißer Informationen über die Prozessstabilität und die Art des Tropfenübergangs.
Bedeutung der Online-Prozessüberwachung in der Qualitätssicherung
Die Online-Prozessüberwachung ist Teil des Qualitätsregelkreises 1 (QRK1) beim Qualitätsregelkreiskonzept nach Haepp und Hopf.[20] Sie ermöglicht eine Vollprüfung, macht den Qualitätsregelkreis 2 weitgehend überflüssig und liefert Daten für die Statistische Qualitätslenkung. Sie ist somit ein wesentliches Instrument der Qualitätssicherung und der permanenten Prozess- und Qualitätsoptimierung nach dem PDCA-Konzept. Es werden Informationen zur Verfügung gestellt, über:
- die aktuelle Verbindungsqualität,
- die aktuelle und vergangene Prozessfähigkeit und -beherrschung,
- die Stabilität des Fertigungsprozesses über einen beliebigen zurückliegenden Fertigungszeitraum
und es werden
- die Notwendigkeiten eines Prozesseingriffs,
- das Erfordernis einer Prozessverbesserung,
- die Wirksamkeit durchgeführter Verbesserungsmaßnahmen
angezeigt.
Literatur
- Yi Ming Zhang: Real-time weld process monitoring. Woodhead Publishing Series in Welding and Other Joining Technologies No. 62, 2008.
- R. O. Duda, P. E. Hart, D. G. Stork: Pattern Classification. 2. Auflage. John Wiley & Sons, 2000, ISBN 0-471-05669-3.
Einzelnachweise
- W. Wiesemann: Process monitoring and closed-loop control. Landolt-Börnstein, New Series VIII/1C (2001)
- S. F. Bocklisch: Prozessanalyse mit unscharfen Verfahren. Verlag Technik, Berlin 1987, ISBN 3-341-00211-1.
- D. Zhou, J. Weston, A. Gretton, O. Bousquet, B. Schölkopf: Ranking on Data Manifolds. 17th Annual Conference on Neural Information Processing Systems (NIPS 2003), MIT Press, Cambridge, MA, S. 169–176.
- D. Reynold: Gaussian Mixture Models. (Memento des Originals vom 9. August 2017 im Internet Archive) Info: Der Archivlink wurde automatisch eingesetzt und noch nicht geprüft. Bitte prüfe Original- und Archivlink gemäß Anleitung und entferne dann diesen Hinweis. MIT Lincoln Laboratory.
- F. Müller, J. Holweg: Verfahren und Vorrichtung zur Erfassung und Auswertung von Prozessdaten; Patent EP 1 455 983 B1. 2004.
- Spot Welding Joints on Steel Materials – Testing of Body Assemblies Volkswagen AG, PV 6702, 2010.
- Kin-ichi Matsuyama: Quality Management of Resistance Welds. IIW-Doc. III-1496-08, 2008.
- D. Steinmeier: Resistance Welding – Weld Monitoring Basics-1. microJoining Solutions – microTips
- DVS: „Messen beim Punkt-, Buckel- und Rollennahtschweißen“, DVS-Merkblatt 2908, 2006.
- M. Uran: Qualitätsüberwachung beim Widerstandspunktschweißen mittels mehrparametrischer Analyse Qualitätsüberwachung beim Widerstandspunktschweißen mittels mehrparametrischer Analyse. Dissertation. TU Berlin 2004, DNB 973319054
- A. Stiebel: Solution – Thermal Force Feedback (TFF®) System
- Apparatus and method for monitoring and controlling resistance spot welding. Patent US4419558.
- U. Niedergesäß, M. Kraska, M. Berg: Verfahren zur Sicherung der Schweißqualität von Schweißpunkten beim Widerstandspunktschweißen einer bestimmten Materialkombination. Patent DE102008005113.
- Schweißzange sowie Verfahren zur Beurteilung der Qualität einer Schweißverbindung. Patent EP1291113 A1.
- M. Janota: Thermal expansion and quality of resistance spot welds. IIW-Doc. III-1479-08, 2008.
- S.F. Bocklisch, J. Burmeister: Verfahren zur Gütesicherung des Fügens. Patent DD265098A1.
- Überwachungssystem für das Widerstandspunktschweißen, HARMS+WENDE QST GmbH
- Igor, W. Merfert: Dynamikverbesserungen an Inverterstromquellen für das Lichtbogenschweißen mit pulsierendem Gleichstrom, Diss., TU Magdeburg 1998, DNB 955255724
- Erdmann-Jesnitzer, F.; Rehfeldt, D.: Verfahren und Vorrichtung zur Überwachung des Schweissablaufes bei Elektroschweissverfahren, insbesondere Lichtbogen- und Elektroschlackeschweissverfahren, Patent der Schweizerischen Eidgenossenschaft, 1971.
- H. J. Haepp, B. Hopf: Anforderungen an ein zukünftiges Qualitätssicherungssystem beim Laserschweißen mit dem Remote-Welding-Verfahren. In: Laser Magazin. 23(2006), H. 4