Schweißfehler
Ein Schweißfehler ist ein Fehler, der die Integrität einer Schweißkonstruktion beeinträchtigt. Es gibt eine Vielzahl von Arten von Schweißfehlern. Sie sind nach ISO 6520[1] klassifiziert, während die zulässigen Grenzwerte nach ISO 5817[2] und ISO 10042[3] spezifiziert sind.
Hauptursachen
Nach Aussage der American Society of Mechanical Engineers (ASME), können die Ursachen von Schweißfehlern wie folgt unterteilt werden: 45 % schlechte Verfahrensbedingungen, 32 % Bedienungsfehler, 12 % falsche Technik, 10 % schlechte Schweißzustände und 5 % schlechte Schweißnaht.[4]
Wasserstoffversprödung
Bei der Wasserstoffversprödung handelt es sich um einen Einschluss von Wasserstoff im Inneren des Metalls. Dies kann zu einer von innen beginnenden Korrosion führen, welche unmittelbar nach dem Schweißen auftritt. Daher werden oftmals verschiedene Wärmeverfahren zur Vorbeugung angewandt. Diese leiten den eingeschlossenen Wasserstoff aus dem Metall heraus.[5]
Eigenspannungen
Der Spannungszustand, der durch Schweißen erzeugt wird, kann grob durch folgende Formen berechnet werden:[6]
Wobei das Elastizitätsmodul ist, der Wärmeausdehnungskoeffizient, und die Temperaturänderung. Für Stahl ergibt sich hierdurch annähernd 3.5 GPa (510,000 psi).
Arten
Risse
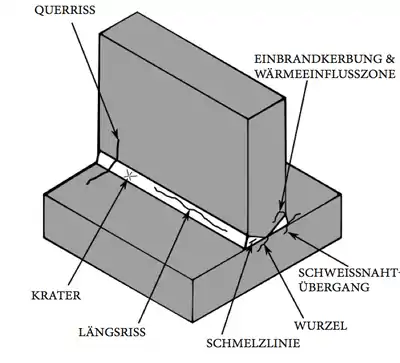
Risse an Zündstellen
Risse an Zündstellen entstehen, wenn der Schweißbogen gezündet wird, aber der Punkt nicht verschweißt. Der Grund hierfür ist, dass das Material über seine obere Temperaturgrenze erhitzt und dann abgeschreckt wird. Dabei entsteht Martensit, welches spröde ist und zu einer höheren Wahrscheinlichkeit von Mikro-Rissen führt. Normalerweise wird der Schweißbogen über der Schweißnaht gezündet, sodass diese Art von Rissen nicht entsteht, aber wenn der Bogen außerhalb der Naht gezündet wird, muss noch mal übergeschweißt werden, damit eine Rissbildung verhindert werden kann. Wenn das nicht möglich ist, kann die Schweißnaht nachträglich durch den Einsatz eines Acetylen-Sauerstoff-Brenners erhitzt und danach wieder langsam abgekühlt werden.[7]
Kaltrissbildung
Eigenspannungen können die Integrität des Grundmaterials vermindern und zu katastrophalen Fehlern durch Kaltrissbildung führen, wie zum Beispiel bei den Hüllen von einigen Liberty-Frachter aus dem Zweiten Weltkrieg. Kaltrissbildung tritt bei Stahl auf und entsteht bei der Formung von Martensit, wenn das Schweißmaterial sich abkühlt. In der kristallinen Struktur von Martensit kann sich Wasserstoff einlagern, der die Eigenspannung des Materials erhöht in der Wärmeeinflusszone. Wenn diese Eigenspannung ein kritisches Level überschreitet, kommt es zur Kaltrissbildung.[8] Um den Schweißverzug und die Eigenspannung zu mindern, sollte die zugeführte Hitze nicht zu groß sein und die Schweißfolge sollte nicht von einem Ende direkt zum anderen sein, sondern besser in Abschnitten.[9]
Kaltrissbildung entsteht wenn diese Umstände zusammentreffen:[8]
- anfällige Mikrostruktur (wie Martensit)
- Wasserstoff im Schweißmaterial oder der Atmosphäre
- mechanische Spannungen (thermische oder Eigenspannung)
Wenn einer dieser Umstände beseitigt wird, tritt keine Kaltrissbildung mehr auf.
Endkraterriss
Endkraterrisse treten auf, wenn ein Krater nicht gefüllt wird, bevor der Schweißbogen bricht. Das führt dazu, dass die äußeren Ränder des Kraters schneller abkühlen, als der Krater, was zu ausreichenden Spannungen führt, um einen Riss hervorzurufen. Längsbrüche, Querrisse oder Radialrisse können entstehen.[10]
Risse an der Schmelzlinie
Der folgende Abschnitt ist ein Ausschnitt aus Forschung an dem Schädigungsverhalten von Schweißverbindungen, mit Mängeln an der Schmelzlinie.
Zwei Modelle für Mängel an Schweißverbindungen, mit Einkerbungen und Rissen auf der Schmelzlinie, wurde angewandt um den Einfluss der Heterogenität der mechanischen Eigenschaften und geometrischen Heterogenität, wie die Anpassung an die Intensität, die Bruchdehnung des Basismetalls, Geschwindigkeit der Kaltverfestigung und die Breite der Schweißstraße auf der Ermüdungsverteilung und die Beziehung zwischen Schädigungsparameter und Bruchspannungs-Parameter zu analysieren. Außerdem wurde, in Bezug auf die gesamte Schadenszone, das Ausdehnungsverhalten von Rissen der Schweißverbindungen, untersucht.
Die mechanischen Eigenschaften des Basismetalls hat große Auswirkungen auf die Schadensverteilung in den Schweißverbindungen. Unter der Bedingungen von gleichen Lasten, erhöhte sich der Schadenswert mit einer Vermindungen der Bruchdehnung und einem erhöhten Kaltverformungsexponenten und Intensitätsanpassung.
Für schlecht abgestimmte Schweißverbindungen, wird die Schadenszone von den Schweißverbindungen nahe der Nut verlagert von der Schweißmaterialseite zu der Grundmaterialseite, wenn die Bruchdehnung sich vermindert und der Kaltverformungsexponent sich erhöht. Für über abgestimmte Schweißverbindungen wird die Schadenszone verlagert von der Grundmaterialseite zu der Schweißmaterialseite, wenn die Bruchdehnung sich erhöht und der Kaltverformungsexponent sich vermindert.
Auf der anderen Seite, hat die Änderung der Schweißlinienbreite geringen Einfluss auf die Schadensverteilung in Schweißverbindungen. Für die Schweißverbindungen mit Rissen auf der Schweißlinie, wenn sie unter Lasten sind und das Rissausmaß ein bestimmtes Level erreicht, erhöht sich der maximale Schadenswert vor dem Riss, solange der Kaltverformungsexponent und die Intensitäts Abstimmung sich erhöhen und vermindert sich solange die Bruchdehnung sich erhöht.
Die Einführung eines Fehler-Prinzips an der geschweißten Struktur sollte die mechanische Eigenschaft der Heterogenität mit in Betracht ziehen. Die numerische Berechnung des Rissausdehnungsverhalten, welche die gesamte Schadenszone als Grundlage hat, zeigt, dass der Rissausdehnungs Pfad parallel zu der Schweißlinie unter der Bedingungen von ebener Spannung aber unter der Bedingung von ebener Belastung ist der Winkel zwischen der Rissausdehnung und der Schweißlinie annähernd 45° ist. Die numerische Berechnung und Analyse deuten darauf hin, dass mikro-Schadensparameter und makro-Bruchparameter beide Spannungs-Dehnungsverhalten beschreiben können und ihre Beziehung zueinander auf der Heterogenität der mechanischen Eigenschaften beruht. Die Untersuchung von mikro-Schadensparametern und makro-Bruchparametern ist ohne Zweifel eine Ergänzung zu der Bewertung der Sicherheit und der erwarteten Lebensspanne von Schweißverbindungen, welche eine große Wichtigkeit in der Theorie hat.
Hutriss
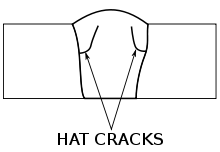
Der Hutriss hat seinen Namen von der Form des Querschnitts der Schweißnaht, da das Schweißmaterial sich ausbeult an der Oberfläche. Der Riss beginnt an der Schweißlinie und dehnt sich durch das Schweißmaterial. Diese Risse werden normalerweise von zu hoher Spannung oder zu geringer Geschwindigkeit erzeugt.[10]
Heiße Rissbildung
Heiße Rissbildung, auch bekannt als Erstarrungsrissbildung kann in allen Metallen auftreten und entsteht in der Schmelzzone der Naht. Um diese Art von Rissbildung zu vermeiden, sollte Überschussmaterial beschränkt werden und passendes Füllmaterial verwendet werden.[9] Andere Ursachen beinhalten einen zu hohen Schweißstrom, schlechtes Verbindungsdesign, welches Hitze nicht ableitet, Verunreinigungen (wie zum Beispiel Sulfat und Phosphor), verheizen, zu hohe Geschwindigkeit oder zu lange Schweißbögen.[11]
Einbrandkerben
Einbrandkerben können zu Rissen in der Wärmeeinflusszone (WEZ) führen.[12] Das sind Risse, die sich in kleinem Abstand zur Schmelzlinie bilden. Diese Risse kommen in niedriglegiertem Stahl und hochlegiertem Stahl vor. Die genauen Ursachen dieser Risse sind noch nicht voll erforscht, aber man weiß, dass gelöster Wasserstoff vorhanden sein muss. Ein anderer Faktor, der diese Art von Riss betrifft, ist die Eigenspannung resultierend aus der ungleichen Kontraktion von Basismetall und Schweißmetall, Rückhaltung des Basismetals, Spannungen durch die Bildung Martensit und Spannungen aus der Präzipitation von Wasserstoff aus dem Metall.[13]
Längsriss
Längsrisse verlaufen entlang der Schweißraupe. Es gibt drei Formen: „Checkrisse“, „Wurzelrisse“ und „volle Mittellinienrisse“. Checkrisse sind auf der Oberfläche sichtbar und gehen teilweise in die Schweißung hinein. Sie werden normalerweise durch großes Schwindungsspannungen verursacht, vor allem in Endphasen, oder in Heißrissmechanismen. Wurzelrisse starten an der Wurzel und dehnen sich teilweise in die Schweißung aus. Sie sind aufgrund der geringen Größe der ersten Schweißraupe die häufigste Art von Längsrissen. Wenn diese Art von Riss nicht in Angriff genommen wird, wird er sich in weiteren Schweißvorgängen fortführen, wodurch volle Risse (Risse von der Wurzel zur Oberfläche) entstehen.[10]
Risse bei Nacherwärmung
Risse bei Nacherwärmung entstehen in hochfesten, niedrig legierten Stählen auf, besonders in Chrom-, Molybdän- und Vanadiumstahl während des Nachwärmens. Dieses Phänomen wurde in austenitischen Edelstählen beobachtet. Es wird hervorgerufen durch schlechte Kriechduktilität der Wärmeeinflusszone. Bereits vorhandene Fehler oder Einkerbungen verstärken die Rissbildung. Um ihr vorzubeugen kann zuerst mit einer niedrigen Temperatureinheit und dann mit schnell steigenden Temperaturen, Schleifen oder Kugelstrahlen der Schweißnahtübergänge, eine zwei Lagenschweißtechnik genutzt werden, um die Wärmeeinflusszone zu verbessern.[14]
Risse an Wurzel und Schweißnaht
Ein Wurzelriss ist ein Riss der durch eine kurze Sicke an der Wurzel (an der Fugenvorbereitung) am Anfang des Schweißens, erzeugt durch niedrigen Schweißstrom am Anfang des Schweißens und durch unzureichender Füllmaterial für das Schweißen. Der Hauptgrund für diese Risse ist Wasserstoffversprödung. Diese Art von Fehler kann eliminiert werden durch starken Schweißstrom am Anfang und passendes Füllmaterial. Nahtbrüche entstehen durch Feuchtigkeit im Schweißbereich, als Teil des Oberflächenrisses können sie schnell entdeckt werden. Durch vorwärmen und angemessene Verbindungsbildung lassen sich diese Fehler vermeiden.
Querriss
Querrisse verlaufen senkrecht zur Schweißrichtung. Sie entstehen allgemein durch längsverlaufende Schrumpfspannung, welche in Schweißmetallen mit geringer Duktilität auftreten. Kraterrisse treten auf in Kratern, wenn der Schweißbogen zu früh beendet wird. Kraterrisse sind meistens oberflächlich, heiße Risse formen dabei meist einzelne oder sternförmige Risse. Diese Risse starten normalerweise in einem Kratertrichter und dehnen sich längslaufend in den Krater aus. Jedoch können sie sich zu Längsrissen im Rest der Schweißung ausdehnen.
Schweißverzug
Schweißmethoden, bei denen das Metall an den Seiten der Verbindungen geschmolzen wird, haben häufig ein Schrumpfen zur Folge, wenn das Metall sich abkühlt. Das Schrumpfen führt dann zu Eigenspannung und Verzug. Verzug kann ein großes Problem darstellen, da das Endprodukt nicht die gewünschte Form hat. Um einige Arten von Verzug zu lindern, können die Werkstücke versetzt werden, so dass sie nach dem Schweißen in der richtigen Form sind.[15] Die folgenden Bilder zeigen verschiedene Typen des Schweißverzugs:[16]
- Querschrumpfung
- Winkelverzug
- Längsschrumpfung
- Kehlnaht- Verzug
- Neutralachsen-Verzug
Gaseinschluss
Gaseinschlüsse können eine Vielzahl von Fehlern hervorrufen, wie „Porosität“ und „Lunker“. Die grundlegende Ursache des Gaseinschlusses ist der Einschluss von Gas in der erhärteten Schweißung. Gasbildung tritt durch folgende Ursachen auf: hoher Schwefel-Anteil im Werkstück oder der Elektrode, große Feuchtigkeit an der Elektrode oder am Werkstück, zu kurzer Schweißbogen, oder falscher Schweißstrom oder falsche elektrische Polarität.[12]
Einschlüsse
Es gibt zwei Arten von Einschlüssen: „Lineare Einschlüsse“ und „Runde Einschlüsse“. Einschlüsse können entweder isoliert oder kumuliert auftreten. Lineare Einschlüsse treten auf, wenn Schlacke oder Flussmittel in der Schweißung auftreten. Schlacke entsteht durch den Gebrauch von Flussmitteln, weshalb solche Fehler normalerweise in Schweißverfahren auftreten, die Flussmittel, wie zum Beispiel Metallschutzgasschweißen, Fülldraht-Schweißen, verwenden und Unterpulverschweißen kann aber auch beim Schutzgasschweißen auftreten. Dieser Fehler tritt normalerweise in Schweißungen auf, die mehrere Schweißvorgänge benötigen, und zwischen den Vorgängen schlechte Überschneidungen bestehen. Die schlechte Überschneidung führt dazu, dass die Schlacke vom vorherigen Vorgang nicht ausschmelzen kann und zur Spitze der neuen Schweißraupe aufsteigen kann. Es kann auch sein, dass der vorherige Vorgang eine Einbrandkerbe oder eine unebene Oberfläche hinterlassen hat. Um zu verhindern, dass die Schlacke eingeschlossen wird, sollte zwischen den Vorgängen geschliffen, mit einer Drahtbürste abgebürstet werden oder abgeschlagen werden.[17]
Isolierte Einschlüsse treten auf, wenn Rost oder Walzzunder im Basismaterial vorhanden sind.[18]
Bindefehler und Wurzeldurchschweißfehler
Ein Bindefehler ist die schlechte Adhäsion (Haftung) der Schweißraupe am Basismaterial; der Wurzeldurchschweißfehler bezeichnet eine Schweißraupe, die nicht an der Wurzel der Schweißfuge beginnt. Wurzeldurchschweißfehler formen einen Kanal und Spalten an der Wurzel der Schweißfuge, die zu großen Problemen führen können, da sich korrosive Substanzen hier ablagern können. Diese Arten von Fehlern können auftreten, wenn Schweißprozesse nicht ordnungsgemäß ausgeführt werden; Ursachen können unter anderem im Ansetzen des Schweißstroms, Schweißbogenlänge, Elektrodenwinkel oder Elektrodenbedienung liegen.[19] Die Fehler können variieren und als kritisch oder nicht kritisch eingestuft werden. Porosität in der Schweißung ist normalerweise bis zu einem gewissen Grad akzeptabel. Einschlüsse von Schlacke, Einkerbungen und Risse sind meistens nicht akzeptabel. Einige Porositäten, Risse und Schlackeneinschlüsse sind sichtbar und müssen nicht näher inspiziert werden, um die Beseitigung anzuordnen. Kleine Fehler können durch Liquid Penetrant Testing (Dye check) festgestellt werden. Einschlüsse von Schlacke und Risse kurz unter der Oberfläche können durch magnetische Inspektion festgestellt werden. Tiefer liegende Fehler können durch radiographische oder Ultraschall Test-Techniken entdeckt werden.
Terrassenbruch
Terrassenbrüche sind eine Form von Schweißfehlern, die in Walzstahlplatten auftreten, die zusammengeschweißt wurden, auf Grund von Schrumpfungskräften senkrecht zu den Enden der Platten.[20] Seit den 1970ern haben Veränderungen in den Herstellungstechniken zur Verminderung von Schwefel stark dazu beigetragen, das Auftreten dieses Problems zu minimieren.[21]
Terrassenbrüche werden meistens durch Schwefeleinschlüsse im Material verursacht. Eine andere Ursache kann ein Überschuss von Wasserstoff in der Legierung sein. Dieser Fehler kann durch eine Obergrenze von 0,005 % an Schwefel in der Legierung vermindert werden.[21] Die Zugabe von seltenen Elementen, Zirkonium oder Calcium zu der Legierung um die Konfiguration von Schwefeleinschlüssen im Metallgitter zu kontrollieren kann das Problem ebenfalls lindern.[22]
Wenn man den Konstruktionsprozess abändert, indem man gegossenes oder geschmiedetes Metall an Stelle von geschweißten Teilen verwendet, kann man dieses Problem beseitigen, denn Terrassenbrüche treten nur in geschweißten Teilen auf.[23]
Einbrandkerben
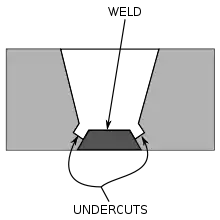
Einbrandkerben entstehen, wenn die Schweißung, die Querschnittsdicke des Basismaterials vermindert, welchen die Integrität der Schweißung und des Werkstückes verkleinert. Ein Grund für diesen Fehler kann zu hoher Schweißstrom sein, welcher die Ecken der Verbindung zum Schmelzen bringt und in die Schweißung abläuft; welches eine kanalartige Prägung an der Länge der Schweißung hinterlässt. Ein anderer Grund ist eine schlechte Technik, die nicht genug Füllmaterial an den Kanten der Schweißung ablegt. Andere Gründe sind ein zu kleiner Elektrodenwinkel, eine angefeuchtete Elektrode, ein zu langer Schweißbogen oder zu geringe Schweißstromgeschwindigkeit.[24]
Literaturverzeichnis
- Howard B. Cary, Scott C. Helzer: Modern Welding Technology. Pearson Education, Upper Saddle River NJ 2005, ISBN 0-13-113029-3.
- Baldev Raj, R. Jayakumar, M. Thavasimuthu: Practical non- destructive testing. 2. Auflage. Woodhead Publishing, 2002, ISBN 1-85573-600-4.
- Hoobasar Rampaul: Pipe welding procedures. 2. Auflage. Industrial Press, 2003, ISBN 0-8311-3141-1.
- Preto Moreno: Welding Defects. 1. Auflage. Aracne, 2013, ISBN 978-88-548-5854-1.
- Klas Weman: Welding processes handbook. CRC Press, New York 2003, ISBN 0-8493-1773-8.
Weblinks
- Understanding Hydrogen Failures (Memento vom 9. Januar 2015 im Internet Archive)
- Radiograph Interpretation – Welds
Einzelnachweise
- BS EN ISO 6520-1: Welding and allied processes – Classification of geometric imperfections in metallic materials – Part 1: Fusion welding (2007)
- BS EN ISO 5817: Welding – Fusion-welded joints in steel, nickel, titanium and their alloys (beam welding excluded) – Quality levels for imperfections (2007)
- BS EN ISO 10042: Welding. Arc-welded joints in aluminium and its alloys. Quality levels for imperfections (2005)
- Clifford Matthews: ASME engineer’s data book. ASME Press, 2001, ISBN 0-7918-0155-1, S. 211.
- Wasserstoffsprödung. Abgerufen am 28. Oktober 2019.
- Magnitude of stresses generated. Archiviert vom Original am 6. Dezember 2009; abgerufen am 16. März 2000.
- Rampaul: Pipe welding procedures. S. 207–208.
- Cold Cracking. Abgerufen am 1. Mai 2015.
- Cary, Helzer: Modern Welding Technology. S. 404–405.
- Raj, Jayakumar, Thavasimuthu: Practical non- destructive testing. S. 128.
- Factors promoting hot cracking. Archiviert vom Original am 6. Dezember 2009; abgerufen am 6. Dezember 2009.
- Raj, Jayakumar, Thavasimuthu: Practical non- destructive testing. S. 126.
- Rampaul: Pipe welding procedures. S. 208.
- Reheat cracking. Archiviert vom Original am 7. Dezember 2009; abgerufen am 6. Dezember 2009. oder Reheat cracking. Archiviert vom Original am 7. Dezember 2009; abgerufen am 6. Dezember 2009.
- Weman: Welding processes handbook. S. 7–8.
- Welding Faults and Defects. Archiviert vom Original am 6. Dezember 2009; abgerufen am 16. März 2000.
- Defects/imperfections in welds – slag inclusions. Archiviert vom Original am 16. Mai 2010; abgerufen am 5. Dezember 2009.
- Welding Faults and Defects. Archiviert vom Original am 5. Dezember 2009; abgerufen am 5. Dezember 2009.
- Rampaul: Pipe welding procedures. S. 216.
- Welding Faults and Defects. Archiviert vom Original am 4. Dezember 2009; abgerufen am 3. Dezember 2009.
- Understanding Hydrogen Failures. Archiviert vom Original am 9. Januar 2015; abgerufen am 3. Dezember 2009.
- Vladimir B. Ginzburg, Robert Ballas: Flat rolling fundamentals. CRC Press, 2000, ISBN 0-8247-8894-X, S. 142.
- Magnitude of stresses generated. Abgerufen am 6. Dezember 2009.
- Rampaul: Pipe welding procedures. S. 211–212.