Heterogene Katalyse
Heterogene Katalyse ist eine Form der Katalyse, bei der der Katalysator und die reagierenden Stoffe einer chemischen Reaktion in unterschiedlichen Phasen vorliegen, etwa als Gas und Feststoff oder als nicht mischbare Flüssigkeiten. Bei industriellen Prozessen liegt der heterogene Katalysator meist als Feststoff vor, als sogenannter Kontakt, und die Reaktionspartner sind Gase oder Flüssigkeiten. Die Vorteile der heterogenen gegenüber der homogenen Katalyse sind die leichte Trennung des Katalysators von Reaktanten und Produkten sowie die Möglichkeit, deaktivierte Katalysatoren einfach aufzuarbeiten.
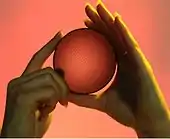
Heterogen-katalytische Verfahren zur Herstellung von Grundchemikalien, etwa das Kontaktverfahren zur Schwefelsäureherstellung, das Haber-Bosch-Verfahren zur Ammoniaksynthese oder die Methanolherstellung, haben einen entscheidenden Anteil am geschäftlichen Erfolg der chemischen Industrie. Durch Fischer-Tropsch-Synthese von Synthesegas aus Biomasse, Kohle oder Erdgas lassen sich synthetische XtL-Kraftstoffe und olefinische Rohstoffe für die chemische Industrie gewinnen.
In Erdölraffinerien liefern heterogen-katalytische Verfahren einen erheblichen Beitrag zur Gewinnung hochoktaniger Ottokraftstoffe und anderer wertvoller Kohlenwasserstoffkomponenten. In der Umwelttechnik dient die heterogene Katalyse der Reinhaltung der Luft durch die Reduktion und Entfernung von Schadstoffen aus Kraftwerksemissionen. Die Entwicklung und der Einsatz des Drei-Wege-Katalysators reduzierten beim Betrieb mit optimalem Verbrennungsluftverhältnis die Schadstoffemissionen von Fahrzeugen mit Ottomotor signifikant.
Geschichte der heterogenen Katalyse
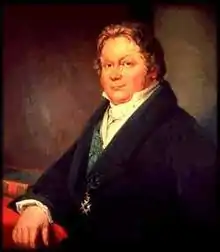
Im Jahr 1783 entdeckte Joseph Priestley den Zerfall von Ethanol zu Ethylen und Wasser an Tonerde – eines der ersten Beispiele der heterogenen Katalyse.[1] Martinus van Marum beschrieb 1796 die katalytische Dehydrierung von Alkoholen zu Aldehyden an glühenden Metallen wie zum Beispiel Kupfer.[1] Nach weiteren Entdeckungen wie dem Ammoniakzerfall zu Stickstoff und Wasserstoff an Eisenkatalysatoren durch Claude-Louis Berthollet und dem Zerfall von Wasserstoffperoxid an Silber, Silberoxid und Mangandioxid durch Louis Jacques Thénard führte die 1823 gefundene Entzündung von Wasserstoff an Platin durch Johann Wolfgang Döbereiner zur Entwicklung des Döbereiner-Feuerzeugs. Dieses in relativ großen Stückzahlen hergestellte Feuerzeug fand bis Mitte des 19. Jahrhunderts Verwendung.[1]
Im Jahr 1835 erkannte Jöns Jakob Berzelius in diesen Reaktionen die Gemeinsamkeit, dass neben den Edukten und Produkten immer ein weiterer Stoff in der Reaktion notwendig war, der sich offenbar nicht verbrauchte. Er prägte dazu den Begriff Katalyse.[2]
Im Jahr 1894 definierte Wilhelm Ostwald den Vorgang der Katalyse:
„Katalyse ist die Beschleunigung eines langsam verlaufenden chemischen Vorgangs durch die Gegenwart eines fremden Stoffes.“
„Ein Katalysator ist ein Stoff, der die Geschwindigkeit einer chemischen Reaktion erhöht, ohne selbst dabei verbraucht zu werden und ohne die endgültige Lage des thermodynamischen Gleichgewichts dieser Reaktion zu verändern.“
Als Anerkennung für seine Arbeiten über die Katalyse zeichnete das Nobelpreiskomitee Ostwald im Jahre 1909 mit dem Nobelpreis für Chemie aus.
In der chemischen Industrie fand die heterogene Katalyse in der Schwefelsäureherstellung nach dem Kontaktverfahren die erste großtechnische Anwendung.[1] Bereits 1901 entwickelte Wilhelm Normann die Fetthärtung durch katalytische Hydrierung von Ölsäure zu Stearinsäure mit Wasserstoff an fein verteiltem Nickel.[4] Sie ist bereits seit 1909 die Grundlage der großindustriellen Margarineherstellung.
Im frühen 20. Jahrhundert begann die Entwicklung einer Reihe von Verfahren, die bis heute zu den wichtigsten der chemischen Industrie zählen. Fritz Haber, Carl Bosch und Alwin Mittasch entwickelten bei der BASF im Jahr 1910 die Ammoniak-Synthese aus den Elementen Stickstoff und Wasserstoff an heterogenen Eisen-Kontakten, das Haber-Bosch-Verfahren. Wilhelm Ostwald entwickelte das Ostwald-Verfahren der Ammoniak-Oxidation an Platin-Netzen zu Salpetersäure, wodurch der zuvor knappe Nitrat-Dünger in großem Maßstab zur Verfügung stand. Ebenfalls bei der BASF im Jahr 1923 entwickelte Matthias Pier ein katalytisches Hochdruckverfahren zur Synthese von Methanol aus Synthesegas an heterogenen Zinkoxid-Chromoxid-Katalysatoren.[5]
Auf dem Gebiet der Raffinerietechnologie entwickelten Chemiker und Ingenieure weitere heterogenkatalytische Verfahren. Durch katalytisches Reforming von niedrigoktanigen Alkanen an heterogenem Platin-Zinn oder Platin-Rhenium auf Aluminiumoxid-Kontakten entstanden hochoktanige, aromaten- und isoalkanreiche Benzine. Nach diesem Verfahren werden pro Tag mehrere Millionen Liter hochoktaniges Benzin hergestellt.[6]
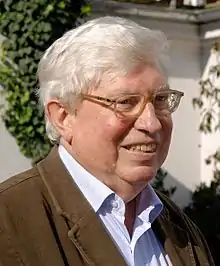
In den 1920er und 1930er Jahren führten die Studien von Irving Langmuir (Nobelpreis 1932) zur Adsorption von Gasen und später die kinetischen Studien von Cyril Norman Hinshelwood (Nobelpreis 1956) zum besseren Verständnis der Mechanismen von heterogen katalysierten Reaktionen von zwei co-adsorbierten Reaktanten (Langmuir-Hinshelwood-Mechanismus).[7] Im Jahre 1943 entwickelten Eley und Rideal einen Mechanismus für Reaktionen, bei denen einer der Reaktanten adsorbiert ist und der zweite aus der Gasphase reagiert.[7]
In der Umwelttechnik entwickelte im Jahr 1957 die Engelhard Corporation für die Entstickung von Kraftwerksemissionen das Verfahren zur selektiven katalytischen Reduktion (SCR) von Stickoxiden mit Ammoniak als Reduktionsmittel. Ein entscheidender Beitrag zur Reinhaltung der Luft war 1973 die Entwicklung des Drei-Wege-Katalysators durch Carl D. Keith und John J. Mooney.[8]
Wissenschaftler wie Gerhard Ertl (Nobelpreis für Chemie 2007) und Gábor A. Somorjai untersuchten seit den 1960er Jahren die Elementarschritte von Oberflächenreaktionen und die Struktur von Adsorbaten an Modellkatalysatoren wie Einkristalloberflächen unter Anwendung moderner oberflächenanalytischer Methoden. So klärte Ertl in den 1970er Jahren den Mechanismus der Ammoniaksynthese.[9]
In den 1970er Jahren entwickelten Forscher eine Reihe neuartiger Zeolithe mit bis dahin völlig unbekannten Eigenschaften. Im Jahr 1972 gelang es Mitarbeitern der Firma Mobil Oil, die Grundlage für eine ganze Reihe neuer, als Pentasile bezeichneter Zeolithe zu schaffen. Wichtigster Vertreter der Pentasile ist der „ZSM-5“, der in petrochemischen Prozessen wie Methanol to Gasoline Verwendung findet.[10]
Aufbau von Feststoffkatalysatoren
Der am häufigsten eingesetzte Aggregatzustand heterogener Katalysatoren ist die feste Form. Hierbei besteht der Katalysator oder Kontakt entweder vollständig aus der aktiven Komponente, sogenannte Vollkatalysatoren, oder die wirksame aktive Komponente wird auf ein Trägermaterial aufgebracht. Die Verfahrensparameter der ablaufenden chemischen Reaktion stellen eine Reihe von Anforderungen an die physikalischen und chemischen Eigenschaften der Kontakte. Die Katalysatorentwicklung muss daher eine zweckmäßige Herstellungsmethode bereitstellen, welche die gewünschten chemischen und physikalischen Eigenschaften der Kontakte liefert.[11] Feststoffkatalysatoren können grob in Pulver-, Formkörper-, Monolith- oder Netzkatalysatoren unterschieden werden.
Formkörperkatalysatoren
Die Formkörperkatalysatoren bestehen meist aus mit aktiver Komponente beschichteten keramischen Teilchen. Typische Dimensionen sind hier zum Beispiel 3×3 mm bis 6×6 mm große Zylinder oder Kugeln mit Durchmessern von 2 bis 6 mm. Die keramischen Materialien sind häufig Aluminiumoxid, Zeolithe und Siliciumdioxid. Eingesetzt werden diese Katalysatoren meist in sogenannten Festbettreaktoren, in denen die Edukte kontinuierlich zu- und die entstehenden Produkte abgeführt werden. Wichtige Kenngrößen sind hier neben der katalytischen Wirksamkeit die Schüttdichte und Druckverlusteigenschaften des Materials.[12]
Monolithkatalysatoren
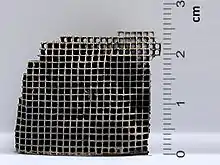
Im Falle der Monolithkatalysatoren wird ein Wabenkörper mit einem sogenannten Washcoat beschichtet. Der Grundkörper besteht hierbei meist aus mineralischer Keramik wie Cordierit oder aus Metall. Der Washcoat ist eine Pulversuspension, zum Beispiel ein Gemisch aus Aluminiumoxid, Siliciumdioxid und anderen Metalloxiden. Diese meist wässrige Pulversuspension wird zum Beispiel bei Drei-Wege-Katalysatoren auf die Wabe aufgebracht und angetrocknet. Danach wird mit einer Metallkomponente, zum Beispiel Platin, Rhodium oder Palladium in Form ihrer wässrigen Säure- oder Salzlösungen, imprägniert und anschließend durch Calcinierung aktiviert.[13] Das sogenannte Washcoaten wird eingesetzt, weil der reine Träger nicht genügend innere Oberfläche aufweist und deshalb nicht genügend aktives Metall aufnehmen kann. Wichtige Kenngrößen sind hier neben der katalytischen Wirksamkeit die Zelldichte, also die Anzahl der Kanäle pro Anströmflächeneinheit, und der Druckverlust des Monolithen.[13]
Pulverkatalysatoren
Pulverkatalysatoren hingegen werden meist in nicht- oder nur semikontinuierlichen Rührkesselreaktoren oder Wirbelschichtreaktoren eingesetzt. Das Katalysatorpulver wird durch Adsorption oder Tränken eines Trägers aus zum Beispiel Aktivkohle, Aluminiumoxid, Siliciumdioxid und anderem mit einer Metallsalzlösung, welche die aktive Komponente enthält, hergestellt.[14] Wichtige Kenngrößen sind hier, neben der katalytischen Wirksamkeit, die Filtrierbarkeit, die Abriebfestigkeit und die Dichte des Materials.
Netzkatalysatoren
Das Ostwaldverfahren für die katalytische Verbrennung von Ammoniak zu Stickoxiden nutzt Netzkatalysatoren aus einer Platin-Rhodium-Legierung.[15] Die Aktivität der Netzkatalysatoren wird durch die Drahtstärke, die Maschenweite und die Oberflächenstruktur bestimmt. Durch Oxidationsverluste und die Verdampfung der aktiven Katalysatorkomponente kommt es zum Verlust der katalytischen Aktivität.[16]
Herstellungsmethoden für heterogene Katalysatoren
Im Zusammenspiel mit den reaktionstechnischen Bedingungen muss versucht werden, die Aktivität, Selektivität und Raum-Zeit-Ausbeute des Kontakts zu optimieren. Neben den chemisch wichtigen Eigenschaften muss der Kontakt den prozesstechnischen Anforderungen entsprechen, das heißt, Eigenschaften wie die Regenerierbarkeit, die Abriebfestigkeit, die Reproduzierbarkeit der Herstellung müssen einstellbar sein und die Herstellung zu so geringen Kosten wie möglich erfolgen.[11]
Fällung
Die Fällung, Präzipitation oder Co-Fällung ist ein gängiges Verfahren zur Herstellung von Vollkatalysatoren. Ein Beispiel ist die Herstellung von Kupfer-Zinkoxid-Alumina-Katalysatoren für die Methanolherstellung. Nach der Fällung folgen die Schritte Waschen, Trocknen, Calcinieren und Aktivieren des Katalysators. Die Aktivität und Selektivität des fertigen Katalysators lässt sich über die chemischen und physikalischen Parameter der Herstellungsschritte beeinflussen.[17]
Schon die Wahl der Metallsalze kann einen Einfluss auf die späteren Eigenschaften des Kontakts haben. Für die Herstellung werden in der industriellen Praxis oft die gängigen anorganischen Metallsalze wie Hydroxide, Nitrate oder Carbonate verwendet. Die Fällung kann durch verschiedene Methoden wie pH-Wert-Einstellung, Übersättigung der Lösung oder durch Zusatz spezieller Fällmittel ausgelöst werden.[18]
Durch das Waschen werden Fremdbestandteile entfernt. Die Trocknung erfolgt oft im Gasstrom bei Temperaturen, die eine Zersetzung der Metallsalze vermeiden. Die Calcinierung wird bei Temperaturen zwischen 300 und 800 °C durchgeführt und überführt die eingesetzten Metallsalze in die Oxide. Außerdem werden gegebenenfalls für die Fällung benötigte organische Additive wie zum Beispiel Citronensäure zur Pufferung entfernt. Die Aktivierung, zum Beispiel durch Reduktion mit Wasserstoff, erfolgt oft unter Reaktionsbedingungen in situ.[18]
Neben der Einstellung der gewünschten chemischen Zusammensetzung wird gegebenenfalls versucht, durch die Herstellungsbedingungen zum Beispiel Gitterfehler zu erzeugen, die eine höhere katalytische Aktivität aufweisen. Dies kann etwa durch die Einfügung von Heteroatomen in die aktive Phase geschehen.
Imprägnierung

Imprägnierung ist eine wichtige Methode zur Herstellung industrieller Trägerkatalysatoren. Bei ihr werden poröse Trägermaterialien mit großer innerer Oberfläche mit einer wässrigen Lösung eines Metallsalzes versetzt. Zu diesen Techniken gehören die diffusionskontrollierte und die trockene Imprägnierung. In nachfolgenden Schritten wird der imprägnierte Katalysator getrocknet und abschließend calciniert, wobei die Aktivkomponente in das Metall oder das Metalloxid überführt werden kann.[19]
Durch geeignete Wahl der Imprägnierungsbedingungen können Profile der Aktivkomponente ausgebildet werden, die vorteilhaft für die Durchführung der chemischen Reaktion sind. Verbreitet sind Katalysatoren mit einem einheitlichen Aktivkomponentenprofil: Schalenkatalysatoren, bei denen die Aktivkomponente nur im äußeren Bereich aufgebracht wurde, oder Katalysatoren, bei denen die Aktivkomponente nur im Inneren des Katalysators liegt. Schalenkatalysatoren finden Einsatz bei Reaktionen, bei denen die Porendiffusion ein limitierender Faktor ist. Unterliegt der Katalysator während des Prozesses mechanischer Abrasion, ist es vorteilhaft, wenn teures Edelmetall nur im Inneren des Kontakts vorliegt.[20]
Diffusionskontrollierte Imprägnierung
Im ersten Schritt wird bei der diffusionskontrollierten Imprägnierung der Kontakt mit reinem Lösungsmittel im Überschuss benetzt. Danach wird der meist wässrigen Lösung ein Metallsalz zugegeben. Die Metallionen wandern durch Diffusion in die Poren des Kontaktes und werden dort adsorbiert. Der Prozess der diffusionskontrollierten Imprägnierung führt häufig zu einer einheitlichen Verteilung der aktiven Komponente über das Katalysatorkorn. Hier ist der Zeitaufwand jedoch größer als bei der trockenen Imprägnierung. Wird das bei der Imprägnierung verwendete Metallsalz nur schwach absorbiert, wird das Metallprofil gegebenenfalls erheblich von den Trocknungsbedingungen beeinflusst.[21]
Trockene Imprägnierung
Bei der trockenen Imprägnierung oder Kapillarimprägnierung wird der Kontakt mit einem Lösungsmittel versetzt, das bereits die gelöste Aktivkomponente enthält. Die Lösungsmittelmenge ist dabei höchstens gleich dem Gesamtporenvolumen der Kontaktmasse, der Kontakt erscheint daher nach der Imprägnierung trocken.[11] Die treibende Kraft der Imprägnierung ist in diesem Fall die Kapillarkraft. Durch sie und die entstehende Adsorptionswärme können im Kontakt eingeschlossene Gase zum Teil nicht entweichen, was zu einem Zerspringen des Katalysatorkorns bei der Imprägnierung führen kann. Um dies zu verhindern, wird der Kontakt zum Teil vor der Imprägnierung unter Vakuum gesetzt.
Schmelzen
Verschiedene heterogene Katalysatoren können durch das Schmelzen geeigneter Vorläuferkomponenten oder Metalle erhalten werden. Beispiele sind Platin-Rhodium-Legierungen, die durch Schmelzen erhalten werden und die für Platin-Rhodium-Netze in der Oxidation von Ammoniak zu Stickoxiden verwendet werden.[15]
Sol-Gel-Prozess
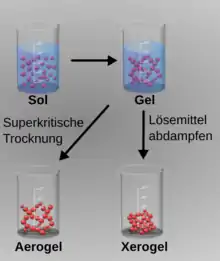
Der Sol-Gel-Prozess kann zur Herstellung anorganischer Katalysatoren aus kolloidalen Dispersionen, den sogenannten Solen, verwendet werden. Als Ausgangsmaterialien oder Precursor werden bevorzugt metallorganische Verbindungen wie Aluminium-(2-propylat), Aluminium-(2-butylat), Zirconiumpropylat, Titanethylat oder Titan-(2-propylat) verwendet, die zunächst hydrolysiert werden. Durch Vernetzung und Trocknung lassen sich Pulver, Fasern, Schichten oder Aerogele hoher Reinheit und mit definierter Porengrößenverteilung erzeugen.[18]
Chemische Gasphasenabscheidung
Neben dem Aufbringen der Aktivkomponente aus der flüssigen Phase kann dies durch die Adsorption von flüchtigen anorganischen oder metallorganischen Verbindungen aus der Gasphase erfolgen. Nach der Adsorption erfolgt die chemische oder thermische Zersetzung des Precursors unter Freisetzung der Liganden und der Fixierung des Metalls am Adsorptionsort.[22]
Der Prozess wird meist bei höheren Temperaturen im Vakuum durchgeführt. Neben den Parametern Temperatur und Druck ist die Auswahl des Precursors, vor allem dessen Flüchtigkeit sowie die thermische Stabilität unter den gewählten Prozessbedingungen, entscheidend für die Durchführung.
Heterogenisierung homogener Katalysatoren
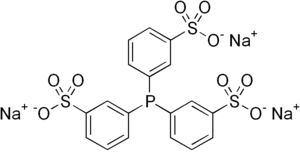
Durch die Heterogenisierung homogener Katalysatoren wird versucht, die Vorteile der homogenen Katalyse, wie hohe Selektivität und vollständige Verfügbarkeit der katalytisch aktiven Spezies mit den Vorteilen der heterogenen Katalyse, wie der leichten Abtrennbarkeit von Katalysator und Reaktanten zu vereinigen.[23]
Die Heterogenisierung homogener Übergangsmetallkomplexe erfolgt meist durch die Fixierung der löslichen Komplexe an einen festen Träger. Die Fixierung kann dabei durch Modifikation der Komplexliganden kovalent erfolgen, aber auch eine ionische oder adsorptive Fixierung ist möglich. Bei porösen Festkörpern ist die physikalische Einlagerung in die Porenstruktur des Festkörpers möglich. Beispiele zeigen, dass eine zu starke Fixierung zum Nachlassen der katalytischen Aktivität führt, während eine zu schwache Fixierung zum „Ausbluten“ oder „leaching“ des Komplexes aus dem Festkörper führt.[23]
Eine weitere Methode ist die Heterogenisierung in flüssig-flüssig-Systemen, wobei der Metallkomplexkatalysator durch Ligandenmodifikation wasserlöslich wird und sich dadurch einfach von der entstehenden organischen Phase trennen lässt. Ein Beispiel ist die Hydroformylierung nach dem Ruhrchemie/Rhône-Poulenc-Verfahren, wobei Rhodium mit Tris(natrium-meta-sulfonatophenyl)phosphan komplexiert wird, das durch die Ligandensubstitution mit Sulfonatgruppen hydrophile Eigenschaften besitzt. Die Reaktion findet in der wässrigen Phase statt. Die organische Produktphase ist wasserunlöslich und wird dabei mittels Phasenabscheidung abgetrennt, die wässrige Katalysatorphase wird wieder dem Reaktor zugeführt.[24] Als Edukte werden Propen sowie Synthesegas, das aus Wasserstoff und Kohlenmonoxid im Verhältnis 1,1:1 besteht, eingesetzt. Das Ruhrchemie/Rhône-Poulenc-Verfahren ist eines der ersten kommerzialisierten Zwei-Phasen-Systeme, in denen der Katalysator in wässriger Phase vorliegt.
Katalysatordesaktivierung und Regeneration
Die Mechanismen der Katalysatordesaktivierung sind vielfältig. Grob kann die Desaktivierung eingeteilt werden in mechanische, etwa durch Abrieb oder Zerfall, thermische wie zum Beispiel durch Sinterung, physikalische wie die Verkokung oder die physikalische Blockade aktiver Zentren sowie die chemische Desaktivierung durch Bildung inaktiver Metallkomponenten wie beispielsweise Sulfiden.[25]
In der heterogenen Katalyse sind zum Beispiel bei Raffinerieprozessen die Verkokung, die Sinterung der aktiven Oberfläche oder der Zerfall des Katalysators durch mechanischen Abrieb, zum Beispiel bei Fluid-Bed-Verfahren, bekannt.[25] Durch Alterungsprozesse kann die katalytisch aktive Oberfläche verkleinert werden oder Poren können verstopfen, zum Beispiel in Zeolithen. Irreversibel ist oft die Desaktivierung durch Phasenumwandlungen. Sie wird beispielsweise bei Zink-Aluminiumoxid-Katalysatoren für die Methanolsynthese beobachtet, die zu hohen Temperaturen ausgesetzt wurden. Durch Bildung einer Spinell-Phase wird der Katalysator desaktiviert und kann nicht regeneriert werden.[26]
Zu den Regenerationsverfahren zählt beispielsweise das Abbrennen von Koks von Kontakten, die in Crack-Prozessen oder dem katalytischen Reforming eingesetzt werden, oder die Oxichlorierung zur Wiederherstellung acider Zentren.[27] Ist der Katalysator so weit desaktiviert, dass eine Regeneration nicht mehr sinnvoll ist, wird der Katalysator aus dem Prozess ausgeschleust. Bei Edelmetallkatalysatoren werden die Träger geschmolzen und das Edelmetall durch Verhüttungs- und elektrochemische Prozesse zurückgewonnen.
Analytische Verfahren zur Charakterisierung heterogener Katalysatoren
Heterogene Katalysatoren können mit den herkömmlichen Methoden zur Analyse von Festkörpern analysiert werden. Mit Methoden wie zum Beispiel der Atomabsorptionsspektroskopie oder der Röntgenfluoreszenzanalyse kann die chemische Zusammensetzung ermittelt werden. Daneben entwickelten Wissenschaftler spezielle Methoden zur Katalysatorcharakterisierung. Die selektive Adsorption von Wasserstoff oder Kohlenstoffmonoxid an Metallzentren etwa dient zur Bestimmung der Dispersion von Metallen. Neben der chemischen Zusammensetzung sind die Art der im Kontakt vorhandenen Phasen, die Porenstruktur, die innere Oberfläche, die Charakterisierung saurer Zentren und die Oberflächenbeschaffenheit von Interesse.[28]
Oberflächensensitive Methoden
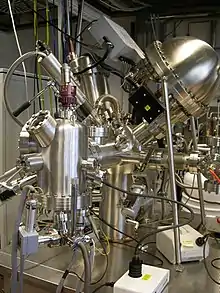
Um Strukturen und Vorgänge an Oberflächen zu untersuchen, werden spezielle Methoden der Oberflächenanalytik verwendet. Sie detektieren nur Prozesse und Strukturen, die sich von denen des Festkörpers unterscheiden. Dazu werden die Wechselwirkungen von Elektronen, Photonen, neutralen Teilchen, Ionen oder Wärme mit den Oberflächen genutzt. Für verschiedene Fragestellungen wurde eine Vielzahl von mikroskopischen, spektroskopischen, thermoanalytischen Adsorptions- und Beugungsmethoden entwickelt.[29]
Eine Voraussetzung für die Oberflächensensitivität einer Methode ist oft, dass das wechselwirkende oder das detektierte Teilchen eine geringe mittlere freie Weglänge in der Materie besitzt. Deshalb ist für viele Methoden ein Ultrahochvakuum nötig. Da viele Reaktionen unter höherem Druck ablaufen, ist die Übertragung der mit oberflächensensitiven Methoden gewonnenen Erkenntnisse in die industrielle Praxis oft schwierig.
Bestimmung der inneren Oberfläche
Die BET-Messung, die nach den Nachnamen der Entwickler des BET-Modells Stephen Brunauer, Paul Hugh Emmett und Edward Teller benannt ist, ist ein Analyseverfahren zur Bestimmung der inneren Oberfläche von porösen Festkörpern mittels Gasadsorption. Durch Ermittlung einer Adsorptions-Desorptions-Isotherme von Stickstoff in bestimmten Druckbereichen ist die gemessene Menge an adsorbiertem beziehungsweise freiwerdendem Stickstoff proportional zur inneren Oberfläche. Die BET-Oberfläche wird in m2·g−1 angegeben.[30]
Bestimmung saurer Zentren
Eine Methode zur Bestimmung der Acidität heterogener Katalysatoren ist die temperaturprogrammierte Desorption von Ammoniak. Dabei können infrarotspektroskopisch oder anhand der Desorptionstemperatur Lewis- und Brønsted-Zentren unterschieden werden.[31]
Zum Nachweis wird die Katalysatorprobe zunächst mit Ammoniak gesättigt und danach zum Beispiel im Inertgasstrom temperaturprogrammiert aufgeheizt und das desorbierte Ammoniak quantitativ erfasst. Physisorbiertes Ammoniak ohne Anlagerung an acide Zentren desorbiert bei Temperaturen zwischen 150 und 200 °C. Ammoniak, das im Bereich zwischen 200 und 400 °C desorbiert, wird Lewis-sauren Zentren zugeschrieben. Bei höheren Temperaturen von 400 bis 600 °C desorbierendes Ammoniak stammt aus der Zersetzung von Ammoniumionen, die sich durch Reaktion von Ammoniak mit Brønsted-Zentren gebildet haben.
Bestimmung der Metalldispersion
Die Aktivität von Trägerkatalysatoren wird durch die Dispersion des Metalls auf dem Trägermaterial bestimmt, da nur die Oberflächenatome des Metalls an der chemischen Reaktion teilnehmen können. Ein oft angewandtes Verfahren zur Messung der Dispersion der Metalle ist die Chemisorption von Wasserstoff oder von Kohlenstoffmonoxid.[32] Dabei wird angenommen, dass das stöchiometrische Verhältnis Metall / Wasserstoff 1:1 beträgt, der Wasserstoff also dissoziativ chemisorbiert wird. Sollte der Wasserstoff im Metall löslich sein wie zum Beispiel bei Palladium-Katalysatoren, kann das Ergebnis der Wasserstoffchemisorptionsmessung fehlerbehaftet sein.
Die Bestimmung der Menge des chemisorbierten Wasserstoffs kann gravimetrisch oder volumetrisch erfolgen. Alternativ kann der chemisorbierte Wasserstoff mit Sauerstoff titriert und das entstandene Wasser detektiert werden.
Bestimmung der Porengrößenverteilung
Nach IUPAC werden drei Größenbereiche bei Poren unterschieden:
- Mikroporen mit einem Durchmesser von weniger als 2 nm
- Mesoporen mit einem Durchmesser von 2 nm bis 50 nm
- Makroporen mit einem Durchmesser von mehr als 50 nm[33]
Die Porengrößenverteilung eines heterogenen Katalysators kann mittels Quecksilberporosimetrie bestimmt werden.[34] Die Eigenschaft von Quecksilber, sich wie eine nichtbenetzende Flüssigkeit zu verhalten, ist die Grundlage dieser Methode. Dazu wird Quecksilber bei Drücken von bis zu 4000 bar in Poren unterschiedlicher Größe gedrückt. Dabei werden anfangs die großen und bei höheren Drücken die kleineren Poren erfasst. Über die Abhängigkeit der Quecksilbermenge vom aufgewendeten Druck können Aussagen über Beschaffenheit, Form, Verteilung und Größe der Poren gemacht werden. Mittels Quecksilberporosimetrie können relativ große Porenbereichverteilungen ermittelt werden.
Bestimmung der Partikelgröße
Zur Bestimmung der Partikelgröße von auf Trägern dispergierten Metallpartikeln können sowohl direkt abbildende Methoden wie die Transmissionselektronenmikroskopie als auch Streumethoden eingesetzt werden. Direkt abbildende Methoden erfordern für eine statistisch gesicherte Aussage über die Partikelgröße einen größeren Probenpräparations- und Auswertungsaufwand.
Zur Bestimmung der Partikelgröße von auf Trägermaterialien dispergierten Metallen im Bereich von circa 1 bis 100 nm kann die Röntgenkleinwinkelstreuung (SAXS) eingesetzt werden. Dazu wird die Katalysatorprobe monoenergetischer Röntgenstrahlung ausgesetzt und die Intensität der gestreuten Röntgenstrahlung bei kleinen Streuwinkeln ermittelt.[35]
Kinetik der heterogenen Katalyse
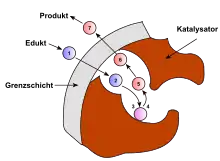
Die heterogene Katalyse in einem porösen Katalysatorkorn kann in sieben Teilschritte unterteilt werden, von denen jeder Schritt geschwindigkeitsbestimmend sein kann. Der erste Schritt ist die Diffusion der Edukte zur Oberfläche des Kontakts durch die stationäre Grenzschicht. Die Dicke der Grenzschicht verändert sich mit der Strömungsgeschwindigkeit. Der zweite Schritt ist die Diffusion der Edukte in den Poren des Kontakts zum katalytisch aktiven Zentrum. Im dritten Schritt erfolgt die Adsorption der Edukte am aktiven Zentrum. Danach folgt als vierter Schritt die Reaktion der Edukte an der Oberfläche.[36] Ein möglicher Teilschritt in der heterogenen Katalyse ist der Spillover. Dabei diffundiert eine aktivierte Spezies von einem katalytisch aktiven Zentrum zu einem anderen Zentrum, das sich chemisch vom ersten Zentrum unterscheidet.[37]
Nun erfolgt der Abtransport der Produkte in umgekehrter Reihenfolge: Im fünften Schritt desorbieren die Produkte vom aktiven Zentrum. Danach erfolgt die Diffusion der Produkte durch das Porensystem des Kontakts als sechster Schritt. Im siebten Schritt diffundieren die Produkte durch die Grenzschicht in den Hauptgasstrom und werden abtransportiert.[36]
Wie bei allen konsekutiven Reaktionen ist nur der langsamste Elementarschritt geschwindigkeitsbestimmend. Hougen und Watson entwickelten einen allgemeinen Ansatz zur Bestimmung der Bruttoreaktionsgeschwindigkeit für heterogen katalysierte Reaktionen:[38]
Der kinetische Term umfasst die Geschwindigkeitskonstanten des geschwindigkeitsbestimmenden Elementarschritts, der Potentialterm umfasst die Konzentrationsterme und die Reaktionsordnung, und der Adsorptions- oder Hemmterm umfasst die Belegung der katalytisch aktiven Zentren. Der Exponent steht für die Anzahl der an der Elementarreaktion beteiligten Zentren.
Langmuir-Hinshelwood-Mechanismus
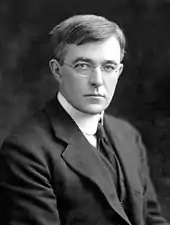
Der Langmuir-Hinshelwood-Mechanismus beschreibt eine Methode für die Darstellung der Reaktionsgeschwindigkeit einer zwei- oder mehrkomponentigen heterogen-katalysierten Reaktion als Funktion von Partialdruck oder Konzentration unter Adsorption aller Reaktanten.
Irving Langmuir untersuchte 1915 die Abnutzung der Wolfram-Glühfäden durch Sauerstoff; sie führte zur Entwicklung einer Theorie über die Adsorption von Gasen als Funktion des Partialdrucks. In Zusammenhang mit der Theorie der aktiven Zentren von Hugh Stott Taylor gelang Langmuir 1927 die Formulierung der Langmuir-Hinshelwood-Kinetik.[7] Bis zur Entwicklung von oberflächensensitiven Analysenmethoden in der zweiten Hälfte des zwanzigsten Jahrhunderts waren kinetische Analysen ein wichtiges Instrument zur Untersuchung heterogen-katalysierter Prozesse.[39]
Die Adsorption eines Moleküls A an der Oberfläche S eines Katalysators kann durch folgende Reaktionsgleichung (1) beschrieben werden:[11]
Das Massenwirkungsgesetz (2) dazu lautet:
mit der Gleichgewichtskonstanten KA. Für eine unimolekulare heterogen-katalysierte Reaktion eines Stoffes A wird angenommen, dass die Reaktionsrate proportional dem Bedeckungsgrad ist. Dieser ist definiert als die Konzentration von chemisorbierten A pro Masseneinheit des Katalysators gemäß Gleichung (3):[11]
Damit ist die Konzentration der freien aktiven Oberflächenplätze definiert durch Gleichung (4):
Durch Einsetzen in die Gleichung (2) und Umstellung nach erhält man
wobei KA die Gleichgewichtskonstante der Adsorption und PA der Partialdruck der Komponente A ist.
Die Reaktionsgeschwindigkeit r ist gleich dem Produkt aus dem Bedeckungsgrad und der Geschwindigkeitskonstanten k:
Für sehr kleine Werte von KAPA (KAPA << 1) ergibt sich
das heißt, die Reaktion ist erster Ordnung in Bezug auf PA. Ist KAPA sehr groß (KAPA ≫ 1), ergibt sich
das heißt, die Reaktion ist nullter Ordnung in Bezug auf PA.
Für Reaktionen zwischen zwei Molekülen basiert der Mechanismus auf der Annahme, dass zwei Reaktanten A und B auf der Oberfläche S eines heterogenen Katalysators adsorbiert werden und im adsorbierten Zustand eine bimolekulare Reaktion abläuft:[7]
Die Geschwindigkeitskonstante für die Reaktion von A und B ist .
Die Konzentration C der durch A und B besetzten Oberflächenplätze AS und BS ist definiert als und , der Bedeckungsgrad als und die Anzahl der aktiven Zentren als . Mit der Definition
der Bedeckungsgrade und lautet das Geschwindigkeitsgesetz:
Wenn zwei Moleküle um denselben Adsorptionsplatz konkurrieren, ist die Reaktionsgeschwindigkeit am größten für
Bei konstantem Partialdruck von B durchläuft die Reaktionsgeschwindigkeit als Funktion des Partialdrucks von A ein Maximum. Bei der Oxidation von Kohlenstoffmonoxid an Palladiumkatalysatoren kommt es zum Beispiel zu dem Phänomen, dass bei Überschreiten eines bestimmten Kohlenstoffmonoxidpartialdrucks die freien Oberflächenplätze des Katalysators ausnahmslos von Kohlenstoffmonoxid besetzt werden, so dass die Oxidationsreaktion zum Erliegen kommt.[40]
Eley-Rideal-Mechanismus
Beim Eley-Rideal-Mechanismus, den im Jahre 1938 D. D. Eley und E. K. Rideal vorschlugen, adsorbiert zunächst Edukt A auf der Katalysatoroberfläche: [41]
Anschließend reagiert das adsorbierte Edukt mit einem weiteren Edukt B aus der Gasphase zum Produkt C:
Im letzten Schritt desorbiert Produkt C:
Der Eley-Rideal-Mechanismus ergibt sich aus dem Langmuir-Hinshelwood-Mechanismus als Grenzfall, wenn der Adsorptionskoeffizient von B gegen Null geht. In diesem Fall ist die Reaktionsgeschwindigkeit proportional dem Bedeckungsgrad von A und dem Partialdruck von B:
Reaktionen, die nach einem reinen Eley-Rideal-Mechanismus ablaufen, sind relativ selten und bislang nur für einige Reaktionen nachgewiesen, etwa für den Wasserstoff-Deuterium-Austausch. Oft sind schwach gebundene Oberflächenspezies in den Mechanismus eingebunden. Der Grund dafür sind die Reaktionszeiten. Eine Gas-Oberflächen-Kollision dauert nur einige Picosekunden,[42] während oberflächengebundene Spezies eine Lebenszeit von einigen Mikrosekunden haben können.[43]
Reaktionskinetische Untersuchungsmethoden
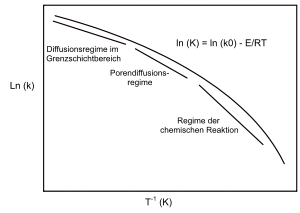
Ziel der kinetischen Untersuchungen ist es unter anderem, den geschwindigkeitsbestimmenden Schritt der heterogen katalysierten Reaktion zu ermitteln. Dabei werden verschiedene Regimes unterschieden. Das Regime bezeichnet den Transport- oder den chemischen Prozess, der die Gesamtkinetik der Reaktion bestimmt.[44] Neben der chemischen Reaktion treten diffusionskontrollierte Schritte wie die Diffusion in der Grenzschicht oder die Porendiffusion als geschwindigkeitsbestimmende Schritte auf.[45]
Kinetische Untersuchungen von Gas-Feststoff-Reaktionen werden experimentell in Apparaten wie dem integralen Zapfstellenreaktor oder dem differenziellen Kreisgasreaktor durchgeführt. Beide Apparatetypen haben verschiedene methodische sowie apparative Vor- und Nachteile und müssen für die jeweilige Untersuchung ausgelegt werden, wobei die einfachste Form der Festbettreaktor mit verschiedenen Zapfstellen ist.
Integralreaktor
Der Intergralreaktor wird oft als einfach zu bauender Festbett-Rohrreaktor mit Zapfstellen ausgeführt. Entlang des Reaktors werden dazu in regelmäßigen Abständen Zapfstellen eingebaut, die eine Probennahme und damit die Bestimmung eines Konzentrationsprofils über die Reaktorlänge erlauben. Das Design entspricht oft einem industriellen Reaktor im Kleinmaßstab. Die Dimensionen sollten so gewählt werden, dass die Verwendung von industriell genutzten Katalysatoren möglich ist und damit Transportvorgänge etwa denen in der industriellen Praxis entsprechen.[46]
Ein bedeutender Nachteil ist das Auftreten von Konzentrations- und eventuell Temperaturgradienten, die eine direkte Messung der Reaktionsgeschwindigkeit verhindern. Die Aufarbeitung der Messdaten führt meist auf Differenzialgleichungen, die nur numerisch gelöst werden können.[46]
Differenzialreaktor
Als Differenzialreaktor werden Berty-Reaktoren eingesetzt. Es handelt sich dabei um einen Kreisgasreaktor, in dem eine Turbine einen Zirkulationsstrom erzeugt, wodurch die Edukte und Produkte vermischt werden. Typische Drehzahlen liegen in der Größenordnung von 4.000 bis 10.000 Umdrehungen pro Minute.[47]
Die eingesetzte Katalysatormenge ist bei diesem Reaktor klein. Ist der Kreislaufvolumenstrom gegenüber dem Eingangsvolumen, das sogenannte Kreis- oder Rücklaufverhältnis, größer als 10, werden Bedingungen erreicht, die dem ideal durchmischten Rührkessel entsprechen. Konzentrations- oder Temperaturgradienten treten nicht auf. Durch die Isothermie wird eine genaue Ermittlung der Temperaturabhängigkeit des Umsatzes möglich. Ein Nachteil sind die relativ großen Wandflächen und Toträume, die zu Blindreaktionen führen können und damit die Messergebnisse verfälschen.[46]
Kenngrößen und -zahlen
Eine wichtige Kenngröße heterogen-katalytischer Prozesse ist die Raumgeschwindigkeit (englisch: gas hourly space velocity; GHSV; bei Flüssigkeiten: liquid hourly space velocity; LHSV). Die GHSV ist der Quotient aus Gasvolumenstrom und Katalysatorvolumen. Die GHSV wird benötigt, wenn die Menge an Katalysator berechnet werden muss, die bei vorgegebener Verweilzeit der Komponenten am Katalysatorvolumen gebraucht wird.
Um die Beziehung zwischen Diffusions- und Reaktionsgeschwindigkeit in porösen Katalysatorpellets, bei denen die Diffusion durch die äußere Grenzschicht nicht geschwindigkeitsbestimmend ist, zu beschreiben, führte E. W. Thiele im Jahr 1939 den Thiele-Modul ein.[48] Zur Vereinfachung wird angenommen, dass die Reaktion in den Poren im Inneren des Pellets stattfindet und der Vereinfachung, dass die Pore durch einen Zylinder mit der Länge L dargestellt wird, an deren Ende die Reaktion beendet ist. Der Thiele-Modul für Reaktionen erster Ordnung ist damit definiert als die Wurzel aus dem Quotienten der Reaktions- und Diffusionsgeschwindigkeit, multipliziert mit der Porenlänge.
Der Thiele-Modul kann für die Bestimmung des Katalysatorwirkungsgrads, des Verhältnisses von effektiver Reaktionsgeschwindigkeit zur Reaktionsgeschwindigkeit ohne Porendiffusionshemmung, verwendet werden.[49]
Um den Einfluss von Porendiffusion auf die Reaktionsgeschwindigkeit in heterogenen katalytischen Reaktionen abzuschätzen, wird das Weisz-Prater-Kriterium oder der Weisz-Modul verwendet.[50] Der Weisz-Modul ist über den Katalysatorwirkungsgrad mit dem Thiele-Modul verknüpft.
Großtechnische Anwendungsbeispiele
Die Tabelle listet eine Auswahl von bedeutenden großtechnischen Anwendungen heterogen-katalysierter Prozesse auf.[51][36]
Prozess | Edukte | Produkte | Katalysator | Anmerkung |
---|---|---|---|---|
Schwefelsäureherstellung (Kontaktverfahren) | SO2 + O2 | SO3, H2SO4 | Vanadiumoxid | |
Ammoniaksynthese (Haber-Bosch-Verfahren) | N2 + H2 | NH3 | Eisenoxide auf Aluminiumoxid | erfordert 1 % des weltweiten Energieverbrauchs |
Salpetersäureherstellung (Ostwaldverfahren) | NH3 + O2 | HNO3 | Pt-Rh-Netze | die direkte Herstellung aus N2 ist ökonomisch nicht sinnvoll |
Wasserstoffgewinnung bei der Dampfreformierung | CH4 + H2O | H2 + CO2 | Nickel auf K2O | andere Herstellungswege direkt aus Wasser werden intensiv untersucht |
Kohlenwasserstoffgemische nach dem Fischer-Tropsch-Verfahren | CO + H2 | CnHm + H2O | Cobalt, Eisen, Nickel, Ruthenium auf Träger mit großen spezifischen Oberflächen | breites Spektrum von Katalysatoren, Drücken und Temperaturen mit verschiedenen Zielprodukten |
Ethylenoxid Synthese | C2H4 + O2 | C2H4O | Silber auf Aluminiumoxid, mit vielen Promotoren | nicht für andere Olefine anwendbar |
Cyanwasserstoffsynthese (Andrussow-Verfahren) | NH3 + O2 + CH4 | HCN | Pt-Rh | das verwandte Verfahren der Ammonoxidation überführt Kohlenwasserstoffe in Nitrile |
Olefinpolymerisation (Ziegler-Natta-Verfahren) | Ethen, Propen | Polyethylen, Polypropylen | TiCl3 auf MgCl2 | es existieren viele Verfahrensvarianten |
Desulfurierung von Petroleum (Hydrodesulfurierung) | H2 + R2S | RH + H2S | Mo-Co auf Aluminiumoxid | produziert schwefelarme Kohlenwasserstoffe, der Schwefel wird im Claus-Prozess wiedergewonnen |
Fetthärtung (Hydrierung) | H2 + ungesättigte Fettsäureester | gesättigte Fettsäureester | Raney-Nickel, Nickel auf Träger | in der Margarineherstellung eingesetzt |
Catcracking (Fluid Catalytic Cracking) | langkettige Kohlenwasserstoffe | kurzkettige Kohlenwasserstoffe | Zeolith Y und andere Zeolithe | produziert kurzkettige Kohlenwasserstoffe |
Literatur
- M. Baerns, H. Hofmann, A. Renken: Chemische Reaktionstechnik. 2. Auflage, Georg-Thieme-Verlag, Stuttgart 1987.
- G. Emig, E. Klemm: Technische Chemie. Einführung in die Chemische Reaktionstechnik. 5. Auflage, Springer Verlag, Berlin 2005.
- B. Cornils, W. A. Herrmann, R. Schlögl, C. H. Wong: Catalysis from A to Z. A Concise Encyclopedia. 863 Seiten, Verlag Wiley-VCH (2003), ISBN 3-527-30373-1, ISBN 978-3-527-30373-1.
- J. M. Thomas, W. J. Thomas: Principles and practice of heterogeneous catalysis. Wiley-VCH, 1997, ISBN 978-3-527-29239-4 (eingeschränkte Vorschau in der Google-Buchsuche).
Weblinks
Einzelnachweise
- Dirk Steinborn: Grundlagen der metallorganischen Komplexkatalyse. Verlag Teubner B.G. GmbH, 2007, ISBN 3-8351-0088-2, S. 2.
- R. Santen, P. Van Leuwen, J. Moulijn: Catalysis: An Integrated Approach. 309 Seiten, Elsevier Science & Technology, ISBN 0-444-50593-8, S. 3.
- Wilhelm Ostwald: Referat zur Arbeit F. Strohmann: „Über den Wärmegehalt der Bestandteile der Nahrungsmittel.“ In: Z. phys. Chem. 15 (1894), S. 705 f.
- Michael Meier: Pflanzenöle für die chemische Industrie. In: Nachrichten aus der Chemie. 56, 2008, S. 738–742, doi:10.1002/nadc.200859277.
- Maria Höring, Ernst E. Donath: Verflüssigung und Vergasung von Kohle. In: Die Naturwissenschaften. 61, 1974, S. 89–96, doi:10.1007/BF00606276.
- G. R. Donaldson, L. F. Pasik, Vladimir Haensel: Dehydrocyclization in Platforming. In: Industrial & Engineering Chemistry. 47.4 (1955), S. 731–735.
- I. Chorkendorff, J. W. Niemantsverdriet: Concepts of Modern Catalysis and Kinetics. 469 Seiten, Verlag John Wiley & Sons (2003), ISBN 3-527-30574-2, S. 57.
- An AIChE Mini History of John Mooney. (Nicht mehr online verfügbar.) Archiviert vom Original am 23. Januar 2009; abgerufen am 20. August 2012.
- Gerhard Ertl: Reactions at Surfaces: From Atoms to Complexity. (PDF; 682 kB) Nobel Foundation, 8. Dezember 2007, abgerufen am 19. August 2012.
- Clarence D. Chang, James C. W. Kuo, William H. Lang, Solomon M. Jacob, John J. Wise, Anthony J. Silvestri: Process Studies on the Conversion of Methanol to Gasoline. In: Industrial & Engineering Chemistry Process Design and Development. 17, 1978, S. 255–260, doi:10.1021/i260067a008.
- Jens Hagen: Technische Katalyse. 445 Seiten, Verlag Wiley-VCH (1996), ISBN 3-527-28723-X, S. 87 ff.
- Jens Hagen: Chemiereaktoren: Auslegung und Simulation. 397 Seiten, Verlag Wiley-VCH Verlag GmbH & Co. KGaA (2004) ISBN 3-527-30827-X, S. 275.
- Jimmie L. Williams: Monolith structures, materials, properties and uses. In: Catalysis Today. 69, 2001, S. 3–9, doi:10.1016/S0920-5861(01)00348-0.
- E. Auer, A. Freund, J. Pietsch, T. Tacke: Carbons as supports for industrial precious metal catalysts. In: Applied Catalysis A: General. 173, 1998, S. 259–271, doi:10.1016/S0926-860X(98)00184-7.
- H. Holzmann: Über die katalytische Oxidation von Ammoniak bei der industriellen Salpetersäure-Herstellung. In: Chemie Ingenieur Technik – CIT. 39, 1967, S. 89–95, doi:10.1002/cite.330390206.
- E. J. Nowak: Catalytic oxidation of ammonia on platinum. In: Chemical Engineering Science. 21, 1966, S. 19–27, doi:10.1016/0009-2509(66)80003-9.
- M. Campanati, G. Fornasari, A. Vaccari: Fundamentals in the preparation of heterogeneous catalysts. In: Catalysis Today. 77, 2003, S. 299–314, doi:10.1016/S0920-5861(02)00375-9.
- J. F. Le Page: Applied Heterogeneous Catalysis. Design, Manufacture, Use of Solid Catalysts. 515 Seiten, Editions Technip (1987), ISBN 2-7108-0531-6, S. 79 ff.
- J. F. Le Page: Applied Heterogeneous Catalysis. Design, Manufacture, Use of Solid Catalysts. 515 Seiten, Editions Technip (1987), ISBN 2-7108-0531-6, S. 117 ff.
- Umit S. Ozkan: Design of Heterogeneous Catalysts: New Approaches based on Synthesis, Characterization and Modeling. 340 Seiten, Wiley-VCH Verlag GmbH & Co. KGaA, ISBN 3-527-32079-2, S. 34 ff.
- Azzeddine Lekhal, Benjamin J. Glasser, Johannes G. Khinast: Impact of drying on the catalyst profile in supported impregnation catalysts. In: Chemical Engineering Science. 56, 2001, S. 4473–4487, doi:10.1016/S0009-2509(01)00120-8.
- Hugh O. Pierson: Handbook of Chemical Vapor Deposition: Principles, Technology and Applications. 458 Seiten, Verlag William Andrew Inc, (1999), ISBN 0-8155-1300-3.
- Boy Cornils, Wolfgang A. Herrmann: Aqueous-Phase Organometallic Catalysis, Concepts and Applications. Wiley-VCH Verlag, 1998, ISBN 3-527-29478-3.
- Ernst Wiebus, Boy Cornils: Die großtechnische Oxosynthese mit immobilisiertem Katalysator. In: Chemie Ingenieur Technik. 66, 1994, S. 916–923, doi:10.1002/cite.330660704.
- J. F. Le Page: Applied Heterogeneous Catalysis. Design, Manufacture, Use of Solid Catalysts. 515 Seiten, Editions Technip (1987), ISBN 2-7108-0531-6, S. 427 ff.
- A. Houteit, H. Mahzoul, P. Ehrburger, P. Bernhardt, P. Legare, F. Garin: Production of hydrogen by steam reforming of methanol over copper-based catalysts: The effect of cesium doping. In: Applied Catalysis A: General. 306, 2006, S. 22–28, doi:10.1016/j.apcata.2006.03.026.
- J. Barbier: Deactivation of reforming catalysts by coking – a review. In: Applied Catalysis. 23, 1986, S. 225–243, doi:10.1016/S0166-9834(00)81294-4.
- Michel Che, Jacques C. Vedrine: Characterization of Solid Materials and Heterogeneous Catalysts: From Structure to Surface Reactivity. 1284 Seiten, Wiley-VCH Verlag GmbH & Co. KGaA (2012) ISBN 3-527-32687-1.
- Wolf Dieter Mroß, Johann Kronenbitter: Untersuchung von Heterogen-Katalysatoren mit modernen Oberflächen-Analysenmethoden. In: Chemie Ingenieur Technik. 54, 1982, S. 33–40, doi:10.1002/cite.330540107.
- Stephen Brunauer, P. H. Emmett, Edward Teller: Adsorption of Gases in Multimolecular Layers. In: Journal of the American Chemical Society. 60, 1938, S. 309–319, doi:10.1021/ja01269a023.
- Naonobu Katada, Hirofumi Igi, Jong-Ho Kim: Determination of the Acidic Properties of Zeolite by Theoretical Analysis of Temperature-Programmed Desorption of Ammonia Based on Adsorption Equilibrium. In: The Journal of Physical Chemistry B. 101, 1997, S. 5969–5977, doi:10.1021/jp9639152.
- Lawrence Spenadel, Michel Boudart: Dispersion of platinum on suppoprted catalysts. In: Journal of Physical Chemistry. 64, 1960, S. 204–207, doi:10.1021/j100831a004.
- Eintrag zu Mesopore in Catalysis. In: IUPAC (Hrsg.): Compendium of Chemical Terminology. The “Gold Book”. doi:10.1351/goldbook.M03853 – Version: 2.3.3.
- L. Moscou, S. Lub: Practical use of mercury porosimetry in the study of porous solids. In: Powder Technology. 29, 1981, S. 45–52, doi:10.1016/0032-5910(81)85003-6.
- O. Kratky: Diffuse Röntgenkleinwinkelstreuung. Bestimmung von Größe und Gestalt von Kolloidteilchen und Makromolekülen. In: Angewandte Chemie. 72, 1960, S. 467–482, doi:10.1002/ange.19600721402.
- Ferdi Schüth: Heterogene Katalyse. Schlüsseltechnologie der chemischen Industrie. In: Chemie in unserer Zeit. 40, 2006, S. 92–103, doi:10.1002/ciuz.200600374.
- Wladimir Reschetilowski: Einführung in die Heterogene Katalyse. Springer-Verlag, 2015, ISBN 978-3-662-46984-2, S. 174 (eingeschränkte Vorschau in der Google-Buchsuche).
- Manfred Baerns, Hanns Hofmann, Albert Renken: Chemische Reaktionstechnik. 428 Seiten, Thieme Georg Verlag, (1999), ISBN 3-13-687502-8.
- R. G. Compton: Kinetic Models of Catalytic Reactions. 406 Seiten, Elsevier Science Ltd. (1991) ISBN 0-444-88802-0, S. 47 ff.
- Gerhard Ertl: Reaktionen an Oberflächen: vom Atomaren zum Komplexen (Nobel-Vortrag). In: Angewandte Chemie. 120, 2008, S. 3578–3590, doi:10.1002/ange.200800480.
- D. D. Eley and E. K. Rideal: Parahydrogen conversion on tungsten. Nature, 1940, 146, 401-2. doi:10.1038/146401d0.
- M. Barbato, V. Belluci, C. Bruno: Effects of Catalytic Boundary Conditions Accounting for Incomplete Chemical Energy Accomodation [sic]. In: AIAA Paper. 1998.
- Bruno Pignataro: New Strategies in Chemical Synthesis and Catalysis. Wiley-VCH Verlag GmbH & Co. KGaA, 2012, ISBN 3-527-33090-9, S. 222.
- H. P. Bonzel: The role of surface science experiments in understanding heterogeneous catalysis. In: Surface Science. 68, 1977, S. 236–258, doi:10.1016/0039-6028(77)90209-6.
- Julian R. H. Ross: Heterogeneous Catalysis: Fundamentals and Applications. 222 Seiten, Elsevier Science & Technology (2011), ISBN 0-444-53363-X.
- Jozsef M. Berty: Experiments in Catalytic Reaction Engineering. 292 Seiten, Elsevier Science (1999), ISBN 0-444-54137-3, S. 31 ff.
- J. M. Berty: Testing Commercial Catalysts in Recycle Reactors. In: Catalysis Reviews. 20, 1979, S. 75–96, doi:10.1080/03602457908065106.
- E. W. Thiele: Relation between Catalytic Activity and Size of Particle. In: Industrial & Engineering Chemistry. 31, 1939, S. 916–920, doi:10.1021/ie50355a027
- D. J. Gunn: Diffusion and chemical reaction in catalysis and absorption. In: Chemical Engineering Science. 22, 1967, S. 1439–1455, doi:10.1016/0009-2509(67)80071-X.
- P. B. Weisz, C. D. Prater: Interpretation of measurements in experimental catalysis. Adv. Catal 6 (1954), S. 143.
- Zhen Ma, Francisco Zaera: Heterogeneous Catalysis by Metals. In: Encyclopedia of Inorganic Chemistry. 2006, John Wiley. doi:10.1002/0470862106.ia084.