Methanolherstellung
Die Methanolherstellung ist ein großtechnisches Verfahren, das in mehreren Varianten zur Herstellung von Methanol aus Synthesegas durchgeführt wird. Dem Chemiker Matthias Pier gelang 1923 die großtechnische Herstellung von Methanol aus Synthesegas im Hochdruckverfahren an Zinkoxid-Chromoxid-Katalysatoren. Bis zu diesem Zeitpunkt wurde Methanol nur durch trockene Destillation von Holz gewonnen. Damit war neben Ammoniak ein weiteres Grundprodukt der industriellen Chemie durch Hochdruckverfahren zugänglich. Das von Winkler entwickelte Wirbelschichtverfahren zur Vergasung feinkörniger Braunkohle stellte das benötigte Synthesegas im großen Maßstab zur Verfügung.
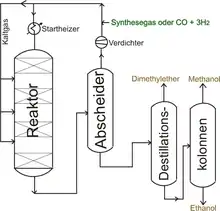
Geschichte
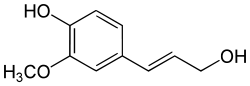
Die Methanolgewinnung erfolgte zunächst durch die trockene Destillation von Holz. Noch im Jahr 1930 wurde in den USA 50 % des Methanols nach diesem Verfahren gewonnen. Dazu wird Holz auf circa 500 °C in eisernen Behältern erhitzt. Die im Lignin vorhandenen Methyl-Phenyl-Etherguppen der Coniferyl- und Sinapylalkoholeinheiten spalten sich dabei unter Aufnahme von Wasser in Methanol und den phenolischen Rest. Als fester Rückstand wird Holzkohle gewonnen, die gasförmigen und flüssigen Produkte werden abgezogen und teilweise kondensiert.[1] Das entstehende wässrige Destillat enthält neben Methanol hauptsächlich Aceton, Essigsäure und Essigsäuremethylester.[2] Die Abtrennung dieser Komponenten sowie die abschließende Trocknung erforderte mehrere Neutralisations-, Destillations- sowie Trocknungsschritte. Die Ausbeute an Methanol bei der trockenen Destillation betrug etwa 10 % der Masse des Ausgangsprodukts.
Die Chemiker der BASF experimentierten ab 1913 mit der Hydrierung von Kohlenstoffmonoxid bei Drücken von etwa 100 bar und Temperaturen von 350 °C. Als Produkte erhielten sie ein Gemisch von reinen Kohlenwasserstoffen und Oxidationsprodukten wie Alkoholen, Aldehyden und Ketonen.[3] Mittasch, Pier und Winkler nahmen diese Arbeiten 1923 wieder auf und entwickelten daraus ein Verfahren, das bei Drücken von 200 bis 300 bar und Temperaturen von 350 bis 400 °C reines Methanol lieferte.[3]
Rohmaterial
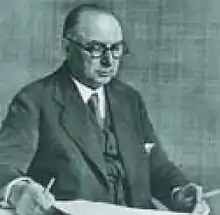
Die Herstellung von Synthesegas für die Methanolherstellung geschieht heute überwiegend durch das Steamreforming oder die partielle Oxidation von Erdgas und die Vergasung von Kohle. In Nordamerika und Europa wird meist Erdgas als Rohmaterial genutzt, in China und Südafrika basiert die Synthesegasherstellung auf Kohle oder Braunkohle. Je nach Kohlenstoffmonoxid zu Wasserstoffverhältnis werden die Produkte Wassergas (CO + H2), Synthesegas (CO + 2 H2) oder Spaltgas (CO + 3 H2) genannt.
Dampfreformierung von Erdgas
Der Prozess der allothermen katalytischen Umwandlung von Erdgas, das überwiegend aus Methan besteht, mit Wasserdampf zu Kohlenstoffmonoxid und Wasserstoff heißt Dampfreformierung. Die Reaktion (1) von Methan und Wasser zu Kohlenstoffmonoxid und Wasserstoff ist endotherm, das heißt, es muss Energie zugeführt werden, damit der Prozess in Richtung Kohlenstoffmonoxidbildung abläuft. Vor der Reaktion müssen alle Katalysatorgifte wie Schwefelwasserstoff entfernt werden, zum Beispiel durch das Rectisolverfahren.[4] Das Methangas wird auf etwa 420 bis 550 °C vorgeheizt und durch mit Nickel imprägnierte Röhren geleitet.
Da nach Gleichung (1) aus zwei Molekülen vier Moleküle entstehen, begünstigt ein niedriger Druck diese Reaktion nach dem Prinzip von Le Chatelier, eine Druckerhöhung begünstigt die Rückreaktion. Das Kohlenstoffmonoxid reagiert nach Gleichung (2), der Wassergas-Shift-Reaktion, weiter mit Wasserdampf, so dass sich neben Kohlenstoffmonoxid zusätzlich Kohlenstoffdioxid bildet.
Hohe Temperaturen begünstigen die Verschiebung des sogenannten Boudouard-Gleichgewichts nach links, welches sich zwischen Kohlenstoffmonoxid auf der linken, Kohlenstoffdioxid und Kohlenstoff auf der rechten Seite einstellt:
Partielle Oxidation von Erdgas
Bei der partiellen Oxidation wird ein unterstöchiometrisches Erdgas-Sauerstoff-Gemisch in einem Reformer gemäß Gleichung (4) teilweise oxidiert, wobei Synthesegas entsteht.
Das Verfahren kann rein thermisch bei Temperaturen zwischen 1200 und 1800 °C und Drücken von 30 bis 80 bar oder katalytisch unter Einsatz von Platin oder Rhodium auf Alumina-Katalysatoren durchgeführt werden. Der Temperaturbereich des katalytischen Verfahrens liegt zwischen 800 und 900 °C bei Normaldruck. Ein Nachteil des Verfahrens ist der Bedarf an reinem Sauerstoff, der eine vorherige Luftzerlegung notwendig macht und damit entscheidend die Energiekosten beeinflusst. Außerdem ist der gewonnene Wasserstoff im Gegensatz zum Dampfreforming rein fossilen Ursprungs, die preiswerte Wasserstoffquelle Wasser wird nicht genutzt.
Autotherme Reformierung von Erdgas
Durch Kombination der Dampfreformierung und der partiellen Oxidation lässt sich der Wirkungsgrad des Gesamtverfahrens optimieren. Durch genaue Dosierung von Sauerstoff und Wasser lässt sich die Ausbeute an Synthesegas bei Senkung der Fremdenergiekosten maximieren. Das Verfahren wird großtechnisch zum Beispiel als Lurgi-Combined Reforming Process durchgeführt, mit dem 2004 die weltgrößte Methanolanlage der Atlas Methanol Company in Trinidad mit einer Anlagenkapazität von 5000 Tagestonnen betrieben wird.[5]
Kohlevergasung
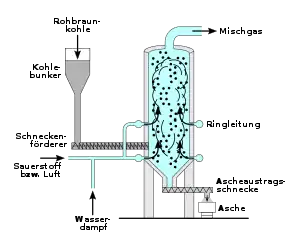
Die Kohlevergasung wird als autothermer Prozess mit Wasserdampf und Luft durchgeführt. Die Energie für die endotherme Wassergasreaktion wird durch die Verbrennung eines Teils der Kohle zugeführt. Der Kohle werden zur Reduktion des Schwefelgehaltes im Gas Kalk oder basische Alkalisalze zugegeben.
Die Einstellung des gewünschten Kohlenstoffmonoxid zu Wasserstoffverhältnisse erfolgt durch die Wassergas-Shift-Reaktion gemäß Gleichung (2). Die Abtrennung des dabei entstehenden Kohlenstoffdioxids geschieht zum Beispiel mit Ethanolamin.
Je nach Art der zu verarbeitenden Kohle haben sich verschiedene Kohlevergasungstechniken etabliert. Eines der ältesten Verfahren ist die Wirbelschichtvergasung im von Fritz Winkler entwickelten Winkler-Generator. Das Verfahren ist geeignet für Braunkohle und wird im Temperaturbereich von 850 bis 1100 °C durchgeführt.
Beim Lurgi-Druckgasverfahren wird Kohle oder Braunkohle bei erhöhtem Druck im Gegenstrom vergast. Die Temperaturen müssen hierbei unter 1000 °C liegen, um eine Verflüssigung der Asche zu vermeiden. Als wertvolle Nebenprodukte fallen bei diesem Verfahren große Mengen an Kohlenwasserstoffen wie Naphtha, Öle, Teer und Phenole an.
Beim Koppers-Totzek-Verfahren, das für alle Kohlesorten geeignet ist, wird die Kohle im Gleichstrom bei hohen Temperaturen von 1500 bis 1600 °C vergast. Die Kohle muss dafür sehr fein gemahlen sein. Durch die hohen Temperaturen fällt kein Methan oder höhere Kohlenwasserstoffe an.
Verfahren
Die Methanolherstellung lässt sich in die Schritte Synthesegasherstellung, Roh-Methanolherstellung und Aufarbeitung des Roh-Methanols unterteilen. Das Synthesegas kann aus einer Reihe verschiedener fossiler und nachwachsender Rohstoffe wie Kohle, Braunkohle, schweren Erdölfraktionen, Müll, Torf, Holz, Biogas oder Klärschlamm gewonnen werden. Biomasse kann im Biomass-to-Liquid-Verfahren (BTL) vergast werden. Die Vergasung von Riesen-Chinaschilf hat nach heutigem Erkenntnisstand eine positive Netto-Energiebilanz pro Hektar Anbaufläche, die gegenüber der Gewinnung von Biodiesel aus Rapsöl circa 4,4 Mal so hoch ist.[6] Bei Verfahren, die einen überschüssigen Wasserstoffanteil liefern, ist der zusätzliche Einsatz von Kohlenstoffdioxid als Kohlenstoffquelle möglich. Die Dampfreformierung und die partielle Oxidation von Erdgas, nach aktuellen Schätzungen die größte ökonomisch nutzbare Kohlenwasserstoffquelle, ist neben der Kohle der Hauptlieferant für Synthesegas.
Entscheidend für die Auswahl des Verfahrens sind neben den Investitionskosten der Wirkungsgrad, der Energiebedarf und die Kohlenstoffdioxid-Emissionen sowohl für die Bereitstellung des Rohstoffes als auch für den eigentlichen Prozess. Der Wirkungsgrad für die Methanolherstellung liegt zwischen circa 40 % für die Flugstromvergasung von Kohle bis 70 % für Verfahren auf Erdgasbasis.
Die Verfahren zur Methanolherstellung aus Synthesegas werden nach dem Reaktionsdruck klassifiziert. Dabei werden drei Druckbereiche unterschieden. Das Hochdruckverfahren, das heute nicht mehr verwendet wird, arbeitet bei Drücken von 250 bis 350 bar und Temperaturen von 360 bis 380 °C. Das Mitteldruckverfahren verwendet einen Druck von 100 bis 250 bar bei einem Temperaturbereich von 220 bis 300 °C und das Niederdruckverfahren wird bei einem Druck von 50 bis 100 bar und Temperaturen zwischen 200 und 300 °C durchgeführt. Jedes Verfahren arbeitet mit speziellen Katalysatoren und Kohlenstoffmonoxid zu Wasserstoffverhältnissen.
Das ursprüngliche Hochdruckverfahren beruhte auf einem Zinkoxid-Chromoxid-Mischkatalysator. Die Katalysatorkomponenten lagen im Molverhältnis von circa 2,3 zu 1 vor. Der Katalysator war nicht besonders aktiv und benötigte hohe Temperaturen und Drücke, reagierte jedoch relativ unempfindlich auf Katalysatorgifte wie Schwefelverbindungen. Diese konnten zur Zeit der Entwicklung des Hochdruckverfahrens Anfang der zwanziger Jahre noch nicht im großtechnischen Maßstab abgetrennt werden. Die Temperatur im Katalysatorbett musste daher in engen Grenzen kontrolliert werden, da oberhalb einer Temperatur von circa 380 °C die Katalysatorkomponenten eine Spinell-Phase bilden und dadurch an Aktivität verlieren. Der Katalysator wurde in durch Einbauten unterstützte Festbett-Schüttungen eingesetzt. Zwischen den Schüttungen konnte zur Temperaturkontrolle Kaltgas eingespeist werden. Der Umsatz betrug etwa 10 bis 15 % pro Durchgang. Zur weiteren Verarbeitung wurde das Methanol abgetrennt und das Gas nach Abtrennung der inerten Anteile teilweise in den Prozess zurückgeführt.
Methanol wird heute großtechnisch aus Synthesegas im Nieder- oder Mitteldruckverfahren hergestellt. Das dabei entstehende Rohmethanol ist zum Teil mit Nebenprodukten verunreinigt. Wird das Rohmethanol im Energiesektor zur Verbrennung eingesetzt, ist die Reinheit des Rohmethanols ausreichend. Für die Weiterverarbeitung in der Chemischen Industrie muss das Methanol destillativ aufgearbeitet werden. Leicht siedende Komponenten wie Dimethylether werden in einer Leichtsiederkolonne abgetrennt. Die höher siedenden Fraktionen werden als Sumpf in einer weiteren Destillationsstufe in einer Schwersiederkolonne abgetrennt, wobei Methanol über Kopf abgezogen wird.
Für die Herstellung von Methanol aus Synthesegas werden hauptsächlich Kupfer-Zinkoxid-Aluminiumoxid Katalysatoren verwendet, wobei neuere Generationen des Katalysators mit Cäsium dotiert sind.[7] Die Katalysatoren haben eine relativ lange Standzeit, die im Normalfall mehrere Jahre beträgt. Nachlassende Aktivität, die meist durch Katalysatorgifte wie Schwefel, Halogene oder durch Eisenpentacarbonyl verursacht wird, kann eine Zeit lang durch Erhöhung des Reaktionsdrucks ausgeglichen werden. Erhöhte Temperaturen führen ebenfalls zu einer irreversiblen Schädigung des Katalysators durch Sinterung der aktiven Kupfer-Spezies.
Katalyse
Für die Bildung von Methanol aus Kohlenstoffmonoxid, Kohlenstoffdioxid und Wasserstoff können die folgenden Gleichungen formuliert werden:
Diese beiden Reaktionen sind exotherm. Nach dem Prinzip von Le Chatelier führen niedrige Temperaturen und eine Druckerhöhung zu einer Verschiebung des Gleichgewichtes nach rechts.
Zur Methanolsynthese werden Kupfer-Zinkoxid-Aluminiumoxid-Katalysatoren eingesetzt. Diese werden durch Co-Präzipitation ausgehend von Kupfer-, Zink- und Aluminiumhydroxycarbonaten hergestellt. Weitere Schritte sind die Waschung, Alterung, Trocknung, Kalzinierung und Aktivierung durch Reduktion im Wasserstoff/Stickstoffstrom, wobei das bei der Kalzinierung entstandene Kupferoxid zum Metall reduziert wird. Das Zinkoxid liegt in der Wurtzit-Struktur vor. Als getrennte Einzelkomponenten sind die Verbindungen katalytisch nicht aktiv.[8]
Die Methanolsynthese an Kupfer-Zinkoxid-Aluminiumoxid-Katalysatoren läuft kinetischen Daten zufolge nach einem Langmuir-Hinshelwood-Mechanismus ab. Sowohl Kohlenstoffmonoxid als auch Wasserstoff adsorbieren an der Katalysatoroberfläche und reagieren schnell zu einer oberflächengebundenen Formyl-Spezies. Als geschwindigkeitsbestimmender Schritt wurde die Reaktion der durch weitere Hydrierung entstehenden Methoxy-Spezies mit adsorbiertem Wasserstoff zum Methanol bestimmt.[9] Die Bildung einer oberflächengebundene Formyl-Spezies wurde infrarotspektroskpisch nachgewiesen.[10] Ein gewisser Prozentsatz von Kohlenstoffdioxid im Einsatzgas ist vorteilhaft für die Reaktion und bei einer Konzentration von etwa 1 % Kohlenstoffdioxid ist die Aktivität am höchsten. Die genaue Funktion des Kohlenstoffdioxids ist nicht abschließend geklärt.
Kinetischen Untersuchungen führten zur Formulierung einer Geschwindigkeitsgleichung der Art:
r = k pCO0,2 – 0,6 pH20,7 ΦCO2
wobei das optimale Partialdruckverhältnis von CO2 : CO bei 0,01 bis 0,03 liegt.
Niederdruckverfahren
Nachdem Verfahren bekannt waren, den Schwefelgehalt im Synthesegas zu minimieren, wurde von den Firmen ICI und Lurgi die Entwicklung von Niederdruckverfahren auf Basis von Kupfer-Zinkoxid-Aluminiumoxid-Katalysatoren vorangetrieben. Der Kontakt wird durch Imprägnierung mit den Metallsalzen hergestellt und anschließend reduziert. Das Kupfer liegt im Kontakt als metallisches Kupfer vor. Das Kupfer rekristallisiert bei höheren Temperaturen und wird dadurch katalytisch inaktiv. Eine genaue Einhaltung der Reaktionstemperaturen ist daher für die Standzeit des Katalysators von großer Bedeutung.[11] Als Nebenprodukt der Reaktion fallen im ppm Bereich Dimethylether, Ameisensäuremethylester und Ethanol an, die abdestilliert werden. Dabei wird der durch die Reaktorkühlung beim Prozess entstehende Dampf verwendet.
Die im Niederdruckverfahren eingesetzten Reaktortypen müssen eine effektive Wärmeabfuhr erlauben, um die Katalysatoraktivität zu erhalten. Von Lurgi wurde ein Festbett-Rohrbündelreaktor eingesetzt, in denen das Katalysatorbett sich in von siedendem Wasser umspülten Röhren befindet. Der Röhrendurchmesser wurde so ausgelegt, dass die Temperatur im Katalysatorbett auf etwa 5 bis 10 °C konstant gehalten werden kann.[12] Der entstehende Dampf wird zum Antrieb der Kompressoren oder zur Destillation des Roh-Methanols eingesetzt.
Mitteldruckverfahren
Die Mitteldruckverfahren nutzen sowohl Kupfer-Zinkoxid-Alumina-Katalysatoren wie das Niederdruckverfahren als auch Katalysatoren auf Basis oxidischer Kupfer-Chrom-Zink- oder Chrom-Zink-Katalysatoren. Der Nachteil der höheren Drücke wird ausgeglichen durch höhere Raum-Zeit-Ausbeuten. Ein entsprechendes Verfahren wurde beispielsweise von der Firma Vulcan entwickelt, das bei einem Druck von 150 bis 250 bar und einem Temperaturbereich von 220 bis 300 °C mit einem Cu-Zn-Al-Katalysator arbeitet oder von der Firma Haldor-Topsoe.[13]
Hochdruckverfahren
In einer Methanolanlage müssen pro Kubikmeter Katalysator zwischen sechs und acht Millionen Kilojoule Wärme abgeführt werden. Die hohen Ansprüche an die Temperaturführung im Katalysatorbett haben zu einer Reihe von Prozessvarianten geführt. Die Wärmeabfuhr wird durch verschiedene reaktionstechnische Prozesse realisiert. Möglich ist die direkte Einspeisung von kaltem Quenchgas, die Zwischenkühlung der Produkte nach Teilumsatz oder die direkte Kühlung des Katalysatorbettes mittels im Bett eingebauter Kühlschlangen.
Des Weiteren wurde versucht, die Methanolherstellung mit Prozessen zur Energiegewinnung zu kombinieren. Eines dieser Verfahren ist das Liquid-Phase-Methanol-Verfahren (LPMeOH-Verfahren). Es basiert auf einer Katalysator-Öl-Slurry, durch die direkt aus der Kohlevergasung stammendes Synthesegas geleitet wird. Bei etwa 235 °C bildet sich im Reaktor Methanol, das in Dampfform zusammen mit dem nicht umgesetzten Synthesegas den Reaktor wieder verlässt. Durch das Vorliegen des Katalysators in Öl-suspendierter Form kann die Temperatur der Katalysatorslurry in engen Grenzen kontrolliert werden. Der Prozess wurde auf Initiative des Energieministerium der Vereinigten Staaten untersucht mit dem Ziel, das bei Kraftwerksprozessen anfallende Synthesegas außerhalb der Spitzenbedarfszeiten in Methanol umzuwandeln. Das Methanol kann gespeichert werden und später wieder zur Energiegewinnung verwendet werden. Der Prozess wurde bislang nur in einer Versuchsanlage realisiert.
Produkte
Methanol ist ein weit verbreitetes Lösungsmittel, Energieträger und Rohstoff für die chemische Industrie. Es ist eine farblose, neutrale, polare Flüssigkeit, die mit Wasser und vielen organischen Lösungsmitteln in beliebigem Verhältnis gemischt werden kann. Auch anorganische Salze lösen sich in Methanol. Methanol ist brennbar und giftig.
Varianten
Intensiv werden Prozesse untersucht, bei dem Methan direkt zu Methanol ohne den Umweg über das Synthesegas oxidiert wird.[14] Ein solcher Prozess würde den kostenintensiven Schritt der Dampf-Reformierung eliminieren. Da die Methylgruppe im Methanol leichter zu oxidieren ist als im Methan, ist eine selektive Oxidation bei hohen Umsätzen schwierig. Untersucht wurden gemischte Metalloxid-Katalysatoren, etwa auf Molybdän und Bismut-Basis. Zur Vermeidung der Weiteroxidation wird im hohen Methanüberschuss mit reinem Sauerstoff gearbeitet. Die bisherigen Versuche deuten darauf hin, dass die direkte Oxidation von Methan zu Methanol nach einem Mars-van-Krevelen-Mechanismus über Gittersauerstoff abläuft.[15] Die erreichten Selektivitäten und Umsätze sind jedoch noch zu gering für eine wirtschaftliche Umsetzung des Verfahrens.
Ein weiterer möglicher Weg ist die direkte Veresterung des entstehenden Methanols mit starken Säuren.[16] Die Ester sind unempfindlicher gegen die Weiteroxidation. Das Methanol wird in einem weiteren Schritt durch Verseifung freigesetzt. Versuche mit Platin-, Kobalt-, Palladium-, Kupfer und Quecksilbersalzen als Katalysatoren in Schwefel- oder Trifluoressigsäure waren erfolgreich, jedoch bei geringen Umsätzen. Die Aufarbeitung der Ester erwies sich als unwirtschaftlich, bislang ist kein Verfahren bis zum kommerziellen Einsatz entwickelt worden.
Enzymkatalytisch kann Methanol aus Methan mit Hilfe von Methan-Monooxygenase erzeugt werden. Methanotrophe Bakterien, zum Beispiel Methylococcus capsulatus, nutzen diese Reaktion als Energiequelle, wenn Methan als einzige Nahrungsquelle angeboten wird. Eine großtechnische Umsetzung dieses Reaktionsweges wird zurzeit nicht untersucht.
Erfolgversprechend scheint die Weiterentwicklung der bekannten Synthesgas- und Methanolverfahren zu sein. Japanische Wissenschaftler haben einen Katalysator mit einem zwei- bis dreifach höheren Umsatz gegenüber herkömmlichen Katalysatoren bei der Umsetzung von Kohlenstoffdioxid und Wasserstoff zu Methanol entwickelt.[17] Das Verfahren erfordert billigen Wasserstoff, der z. B. durch Elektrolyse von Wasser mit idealerweise klimaneutral aus erneuerbaren Energien, streitbar Kernkraft, oder langfristig möglicherweise Fusionsenergie gewonnenem Strom hergestellt werden kann. Auch biotechnische oder photokatalytische Verfahren zur Wasserstoffherstellung, sowie der Schwefelsäure-Iod-Zyklus in Verbindung mit Prozesswärme (z. B. aus Hochtemperatur-Atomreaktoren wie dem Dual Fluid Reaktor) sind als Zukunftsperspektive denkbar.
Der Chemiker und Nobelpreisträger George Olah entwickelte ein Verfahren, nachdem Methanol aus Kohlenstoffdioxid und Wasser unter Zuführung von elektrischem Strom hergestellt wird als Umkehrung der in Brennstoffzellen ablaufenden Reaktion; so sei ein „Recycling“ von CO2 möglich.[18] (Siehe Artikel Methanolwirtschaft)
Regeneratives Methanol wird derzeit vor allem aus vergärten Abfällen sowie Hausmüll (Bio-Methanol) und erneuerbarem Strom (e-Methanol) hergestellt.[19]
Siehe auch
Literatur
- F. Asinger: Methanol, Chemie- und Energierohstoff. Akademie-Verlag, Berlin, 1987, ISBN 3-05-500341-1.
- E. Supp: How to Produce Methanol from Coal. Springer-Verlag, 1990, ISBN 0-387-51923-8.
- J. G. Speight: Synthetic Fuels Handbook: Properties, Process, and Performance. Verlag Mcgraw-Hill Professional, 2008, ISBN 0-07-149023-X, ISBN 978-0-07-149023-8.
- Martin Bertau, Heribert Offermanns, Ludolf Plass, Friedrich Schmidt, Hans-Jürgen Wernicke: Methanol: The Basic Chemical and Energy Feedstock of the Future: Asinger’s Vision Today, 750 Seiten, Verlag Springer; 2014, ISBN 978-3-642-39709-7
Weblinks
- Methanol Institut, Arlington (englisch)
Einzelnachweise
- Peter Klason, Gust. V. Heidenstam, Evert Norlin: Untersuchungen zur Holzverkohlung. In: Zeitschrift für Angewandte Chemie. 23, 1910, S. 1252, doi:10.1002/ange.19100232702.
- Walter Fuchs: Die Chemie des Lignins, Springer Verlag, ISBN 978-3-642-89726-9, S. 151–162.
- Friedrich Asinger: Chemie und Technologie der Paraffinkohlenwasserstoffe. Akademie Verlag, 1956, S. 71–75.
- Rectisol-Wäsche. (Nicht mehr online verfügbar.) In: linde-le.com. Ehemals im Original; abgerufen am 8. Januar 2010. (Seite nicht mehr abrufbar, Suche in Webarchiven)
- Reforming. In: lurgi.com. Archiviert vom Original am 18. Oktober 2006. Abgerufen am 8. Januar 2010.
- Die Ökobilanz des Biosprits: Energie versus Biotope (PDF; 103 kB) Ministerium für Umwelt, Klima und Energiewirtschaft Baden-Württemberg. Archiviert vom Original am 10. Januar 2014. Abgerufen am 9. Januar 2010.
- L. Guczi (Hrsg.): New Trends in CO Activation. Elsevier, Amsterdam 1991, ISBN 978-0-08-088715-9, S. 268 (eingeschränkte Vorschau in der Google-Buchsuche).
- K. Klier: Methanol Synthesis. In: D. D. Eley, Herman Pines, Paul B. Weisz (Hrsg.): Advances in Catalysis. Band 31, ISBN 978-0-08-056535-4, S. 243 (eingeschränkte Vorschau in der Google-Buchsuche).
- Rajesh M. Agny, Christos G. Takoudis: Synthesis of methanol from carbon monoxide and hydrogen over a copper-zinc oxide-alumina catalyst. In: Industrial & Engineering Chemistry Product Research and Development. Band 24, Nr. 1, 1985, S. 50–55, doi:10.1021/i300017a010 (PDF).
- J.C. Lavalleya, J. Sausseya and T. Raïsa: Infrared study of the interaction between CO and H2 on ZnO: Mechanism and sites of formation of formyl species, in: Journal of Molecular Catalysis, 1982, 17 (2–3), S. 289–298 (doi:10.1016/0304-5102(82)85040-2).
- Methanol. In: linde-process-engineering.com. Archiviert vom Original am 15. Oktober 2006. Abgerufen am 8. Januar 2010.
- Michael Felleisen: Prozeßleittechnik für die Verfahrensindustrie. Oldenbourg Industrieverlag, 2001, ISBN 3-486-27012-5, S. 112 (eingeschränkte Vorschau in der Google-Buchsuche).
- Haldor Topsoe – Processes. www.topsoe.com. Abgerufen am 8. Januar 2010.
- Evalyn Mae C. Alayon, Maarten Nachtegaal, Marco Ranocchiari, Jeroen A. van Bokhoven: Catalytic conversion of methane to methanol using Cu-zeolites. In: Chimia. Band 66, Nr. 9, 2012, S. 668–674, doi:10.2533/chimia.2012.668, PMID 23211724.
- W. Choi, J. Park, M. Kim. H. Park und H. Hahm: Catalytic Partial Oxidation of Methane to Methanol, in: Journal of Industrial and Engineering Chemistry, 2008, 7 (4), S. 187–192.
- Martin Bertau, Heribert Offermanns, Ludolf Plass, Friedrich Schmidt, Hans-Jürgen Wernicke: Methanol: The Basic Chemical and Energy Feedstock of the Future: Asinger’s Vision Today, 750 Seiten, Verlag Springer; 2014, ISBN 978-3-642-39709-7, S. 52.
- Patent DE69808983: Methanolsynthese- und Reformierungskatalysator bestehend aus Kupfer, Zink und Aluminium. Veröffentlicht am 7. August 2003, Erfinder: Hideo Fukui, Masayuki Kobayashi, Tadashi Yamaguchi, Hironori Arakawa, Kiyomi Okabe, Kazuhiro Sayama, Hitoshi Kusama.
- Kevin Bullis: Methanol statt Wasserstoff. In: Technology Review. Juli 2006.
- Innovation Outlook Renewable Methanol. IRENA, abgerufen am 25. Juli 2021.