Keramik
Der Begriff Keramik, auch keramische Massen, bezeichnet in der Fachsprache eine Vielzahl anorganischer nichtmetallischer Werkstoffe, die grob in die Typen Irdengut, Steingut, Steinzeug, Porzellan und Sondermassen unterteilt werden können (siehe auch Klassifikation keramischer Massen). Allgemeinsprachlich dient Keramik auch als Oberbegriff für die geformten und gebrannten Produkte, die als Gebrauchs- und Ziergegenstände, Bauteile oder Werkzeuge verwendet werden. Außerdem können die Herstellungstechnik, das Handwerk (bzw. Kunsthandwerk) und die keramische Produktion damit gemeint sein.[1]
Man unterscheidet unter anderem Tonkeramik und Glaskeramik. In der Gegenwart spielt die technische Keramik eine bedeutende Rolle, zu der auch die Verbundkeramik zählt. In kulturhistorischen und archäologischen Studien wird vor allem nach der Verwendung im Alltag unterschieden: Gefäßkeramik (Tischgeschirr, Trinkgeschirr, Kochgeschirr, Sonderformen), Baukeramik (Dachziegel, Backsteine, Bodenfliesen und Wandfliesen), Ofenkeramik (Ofenkacheln, Kachelofenfüße, Abdeckplatten) und Sanitärkeramik (Waschbecken, WC-Schüsseln, Badewannen).
Das Wort Keramik stammt aus dem Altgriechischen: κέραμος keramos war die Bezeichnung für Tonminerale und die aus ihm durch Brennen hergestellten formbeständigen Erzeugnisse, wie sie etwa im antiken Athener Bezirk Kerameikos produziert wurden. Das Töpferhandwerk wurde als κεραμικὴ (τέχνη) keramikḗ (téchnē) bezeichnet; später ging die Bezeichnung auch auf die Produkte über.
Vorgeschichtliche Verbreitung
Während der jungpaläolithischen Kultur des Gravettien wurden erste Kleinplastiken aus gebranntem Lösslehm hergestellt. Der Lösslehm wurde mit Knochenmehl gemagert und in einer Feuerstelle gebrannt.[2] Das berühmteste Beispiel ist die circa 30.000 Jahre alte Venus von Dolní Věstonice, dazu kommen eine Reihe von Tierfiguren aus Dolní Věstonice, Pavlov und Krems-Wachtberg.[3]
Die Entdeckung von Keramik als Töpferware aus Ton ist wahrscheinlich unabhängig voneinander in mehreren Regionen erfolgt.
Nordasien
Die ältesten Tongefäße der Welt stammen aus dem östlichen Sibirien Amur-Gebiet und ist durch Beschleuniger-Daten der vegetabilen Magerung auf 15.000 BP datiert.[4] Keramikgefäße sind auch aus der mesolithischen Jomon-Kultur Japans nachgewiesen und datieren um 13.000 v. Chr.
Die Kenntnis der Töpferei verbreitete sich durch Wildbeuter-Kulturen weiter nach Korea sowie in die Mandschurei, ohne dass dies mit einer neolithischen Wirtschaftsweise einherging. Auch in China ist sehr alte Keramik belegt.[5][6][7] Funde aus einem Höhlengrab bei Xianrendong in der Provinz Jiangxi werden sogar auf ein Alter von bis zu 20.000 Jahren geschätzt.[8] Keramik wird um 6000 v. Chr. auch am Südlichen Bug in der Ukraine nachgewiesen.
Afrika
Im Sudan wurde Töpferware (Wavy line) von semi-sesshaften Jägern und Sammlern hergestellt und unabhängig von Asien erfunden. Erste Keramik aus dem 10. Jahrtausend v. Chr. wurde von Jäger- und Sammlergruppen im heutigen westafrikanischen Mali hergestellt (Fundplatz Ounjougou).[9]
Im Nildelta trat Keramik erstmals im 9.–8. Jahrtausend v. Chr. auf.
Herstellung
Frühe Töpferware wurde nach heutigem Wissen überall im „offenen Feldbrand“ hergestellt. Im 5. Jahrtausend sind in China erste Töpferöfen nachgewiesen, im Vorderen Orient im 4. Jahrtausend. In Mitteleuropa gibt es zeitgleiche Nachweise für Töpferöfen aus Triwalk, Mecklenburg-Vorpommern, aus der Trichterbecherkultur.
Ihre Verbreitung in den Kulturen der Jungsteinzeit verdanken Keramikgefäße den verbesserten Möglichkeiten zum Kochen und zur Vorratshaltung, die sich bei gleichzeitiger Sesshaftwerdung durchsetzt, da sie zuvor als zu schwerer und zerbrechlicher Transportbehälter zunächst ungeeignet war. Keramik spielt eine ganz wesentliche Rolle im Rahmen der Identifizierung und Datierung archäologischer Kulturen.
Begriff und Unterteilung
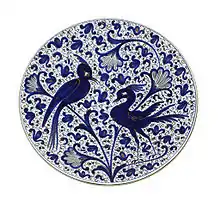
Heute ist der Begriff Keramik breiter gefasst.
So kann der Begriff „Keramik“ einerseits einem Werkstoff zugeordnet werden, genauer gesagt, einer Stoffklasse, die gegenüber den Metallen oder den Kunststoffen oder anderen abgegrenzt werden kann, oder einer ganzen Technologie die sich im weitesten Sinne mit der Keramik befasst. Der Nomenklaturausschuss der Deutschen Keramischen Gesellschaft definiert „Keramik“ als einen „Zweig der chemischen Technologie oder Hüttenkunde, der sich mit der Herstellung keramischer Werkstoffe und Weiterverarbeitung bis zum keramischen Erzeugnis befaßt“. Keramische Werkstoffe wiederum werden definiert als „sind anorganisch, nichtmetallisch, in Wasser schwer löslich und zu wenigstens 30 % kristallin. In der Regel werden sie bei Raumtemperatur aus einer Rohmasse geformt und erhalten ihre typischen Werkstoffeigenschaften durch eine Temperaturbehandlung meist über 800 °C. Gelegentlich geschieht die Formgebung auch bei erhöhter Temperatur oder gar über den Schmelzfluß mit anschließender Kristallisation.“.[10][11] Es existieren jedoch noch weitere Definitionen. So wird der Begriff im anglo-amerikanischen Sprachraum für alle festen Werkstoffe aus anorganischen Verbindungen mit nichtmetallischen Eigenschaften verwendet, was auch Halbleiter wie Silizium oder Galliumarsenid oder Edelsteine wie Saphir mit einschließt.[12]
Aus chemischer Sicht ist es bei diesen Definitionen nicht korrekt bei Keramik von „metallfreien“ oder „nichtmetallischen“ Restaurationen zu sprechen. Neben Sauerstoff und Silizium sind Metalle oft die Hauptbestandteile von Keramik. Sie liegen jedoch nicht in metallischer Form, sondern vorwiegend als Oxide vor. Werden diese (zum Beispiel bei Dentalkeramik) im Mund gelöst, entstehen Metallionen, die sich prinzipiell nicht von denen unterscheiden, die durch Korrosionvorgänge aus Metallen gebildet werden.[13] Der Begriff „nicht-metallisch“ bezieht sich hier auf die Eigenschaften des Werkstoffes wie elektrische Leitfähigkeit, Wärmeleitfähigkeit oder Duktilität, wobei einige der heutigen Spezialkeramiken durchaus teilweise Eigenschaften von Metallen aufweisen können.[14]
Keramiken sind also weitgehend aus anorganischen, feinkörnigen Rohstoffen unter Wasserzugabe bei Raumtemperatur geformte und danach getrocknete Gegenstände (sogenannte Grünkörper), die in einem anschließenden Brennprozess oberhalb 700 °C zu härteren, dauerhafteren Gegenständen gebrannt werden. Einen härteren Scherben bekommt man durch höhere Brenntemperatur, wobei es ab etwa 1200 °C (je nach Tonmasse) zu einer Sinterung kommt, die die Porosität des Scherbens aufhebt. Man erhält also dauerhaft flüssigkeitsdichte Gefäße. Keramik wird heute im zunehmenden Maße für technische Einsatzzwecke genutzt (technische Keramik) und in ähnlichen Prozessen, allerdings meist wesentlich höheren Sintertemperaturen, hergestellt. Im Bereich der faserverstärkten Keramik sind auch siliciumhaltige organische Polymere (Polycarbosilane) als Ausgangsstoffe zur Herstellung von amorpher Siliciumcarbid-Keramik in Verwendung. Sie wandeln sich in einem Pyrolyseprozess vom Polymer zur amorphen Keramik um.

Eine klare Systematik der keramischen Werkstoffe – wie beispielsweise bei Metall-Legierungen – ist schwierig, weil es hinsichtlich der Rohstoff-Zusammensetzung, des Brennvorgangs und des Gestaltungsprozesses fließende Übergänge gibt. Keramische Produkte werden deshalb häufig nach den jeweils im Vordergrund der Betrachtung stehenden Aspekten unterschieden, zum Beispiel nach regionalen Keramiktypen wie Westerwälder Steinzeug, Bunzlauer Keramik oder auch Majolika und Fayence, bei technischer Keramik nach der chemischen Zusammensetzung in Silikatkeramik, Oxidkeramik und Nichtoxidkeramik oder auch nach dem Verwendungszweck (Funktionskeramik, Gebrauchskeramik, Baukeramik, Sanitärkeramik und Strukturkeramik).
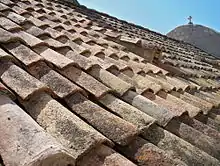
Gebräuchlich ist auch die Unterteilung in Grob- und Feinkeramik. Zur erstgenannten gehört die große Gruppe der Baukeramik (zum Beispiel Bau- und Dachziegel, Kanalisationsrohre); diese Produkte sind dickwandig, häufig inhomogen, von oft zufälliger Färbung. Feinkeramik ist dagegen feinkörnig (Korngröße unter 0,05 mm), von definierter Färbung (zum Beispiel weiß für Haushaltskeramik, Tischgeschirr und Sanitärkeramik); hierher gehören auch die künstlerischen Erzeugnisse. Feinkeramik erfordert bezüglich der Aufbereitung der Rohmasse, der Formgebung und des Trocknens sowie Brennens eine erheblich größere Sorgfalt, als sie bei der Herstellung von Grobkeramik nötig ist. Die Eigenschaften keramischer Produkte werden bestimmt durch Art und Menge der in ihnen enthaltenen Kristalle und die als Bindung funktionierenden Verglasungen (sogenannte Glasphasen). Keramiken sind formbeständig, im Allgemeinen hart (es gibt Ausnahmen:beispielsweise pyrolytisches Bornitrid (hexagonal) ist flexibel durch seine Schichtstruktur) und hitzebeständig.
Zur Klassifikation keramischer Massen:
Die Einteilung keramischer Massen kann in drei Klassen, verschiedenen Unterklassen, Gruppen, Untergruppen, weiterführende Aufteilungen, beispielsweise in Grobkeramik und Feinkeramik sowie durch weitere Spezifikationen erfolgen.
Grobkeramik (englisch coarse ware) ist die beschreibende Bezeichnung für vorzeitliche alltägliche keramische Gebrauchsware der unterschiedlichsten Kulturen, die mehr als zwei Drittel aller Funde ausmacht. Die Gefäße waren für den Transport und die Lagerung von Gütern, die Zubereitung von Speisen und als Kochgefäße in Gebrauch. Grobkeramik steht sowohl in der Art der Herstellung, als auch im allgemein unverzierten Aussehen, qualitativ im Kontrast zur speziellen Ausführung von zeremoniellen Gefäßen.
Keramische Rohstoffe
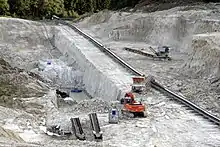
Silikat-Rohstoffe
Dieser Bereich umfasst generell alle Rohstoffe, die [SiO4]4−-Tetraeder in der Kristallstruktur eingebaut haben.
Tonminerale und deren Gemische
Tone sind wasserhaltige Alumosilicate. Siehe auch Tonmineral. Man unterscheidet zwischen Primärton und Sekundärton. Tone und Lehme entstehen durch die Verwitterung von Feldspäten und verwandten Mineralien. Die Hauptbestandteile sind Illit, Montmorillonit und Kaolinit. Die Korngrößen liegen hierbei im µm-Bereich. Je nach Verwendungszweck unterteilt man diese Rohstoffe in Steinzeugtone, Steinguttone, Irdenwaretone und -lehme. Mergeltone haben einen hohen Gehalt an Kalk, der stark verflüssigend wirkt. Da an solchen Scherben die früher viel verwendeten Blei- und Zinnglasuren sehr gut haften, werden sie häufig für Ofenkacheln und Fliesen eingesetzt. Bentonite sind ein Verwitterungsprodukt vulkanischen Ursprungs, sie wirken bereits bei geringen Zugaben sehr stark plastifizierend, verbessern die Formbarkeit und die Standfestigkeit während des Trocknungsprozesses. Aus der hohen Wasseraufnahme der Bentonite im Formgebungsprozess resultiert eine enorme Schwindung schon während des Trocknens. Durch die Trockenschwindung kann es zu Rissen und Verformungen in der Grünware kommen.
Die Auswahl und Mischung der Rohstoffe muss folgenden Forderungen genügen: Gute Formbarkeit der Masse, geringe Schwindung beim Trocknen und Brennen, hohe Standfestigkeit beim Brennen, geringe oder keine Verfärbung des Endprodukts.
Kaoline
Kaolin, auch Porzellanerde genannt, ist ein Verwitterungsprodukt von Feldspat. Es besteht weitgehend aus Kaolinit, einem hydratisierten Alumosilikat, begleitet von Quarzsand, Feldspat und Glimmer. Die letztgenannten Bestandteile werden durch Schlämmen und Sieben entfernt, das Endprodukt muss möglichst plastisch, beim Trocknen formstabil und nach dem Brennen weiß sein. Zur Erzielung der gewünschten Eigenschaften werden Kaoline unterschiedlicher Herkunft gemischt (Mineral Dressing); um ein gutes Gießverhalten zu erreichen, gibt man noch Plastifizierungsmittel wie Wasserglas und/oder Soda zu.
Kaolin ist zur Porzellanherstellung zwingend. Ist kein Kaolin in der Tonerde enthalten, entsteht automatisch immer nur Keramik. Manche Länder konnten in der Vergangenheit kein Porzellan herstellen, weil es dort kein Kaolin gab. Belgien und die Niederlande gehören dazu.
Nichtplastische Rohstoffe
Feldspäte sind im Vergleich zum Kalk ebenfalls gute Flussmittel, die aber mit steigender Brenntemperatur eine stärkere Verglasung und damit Verdichtung der Erzeugnisse bewirken. Der Trocknungsschwund wird zwar reduziert, der Schwund beim Brennen steigt jedoch. Quarz senkt als Magerungsmittel den Trocknungs- und Brennschwund, verschlechtert jedoch die Plastizität. Quarz wird als feinstkörniger Sand oder als gemahlenes Ganggestein eingesetzt, er muss möglichst rein sein, um unerwünschte Verfärbungen zu vermeiden. Kalk wird als geschlämmte Kreide oder als gemahlener Kalkstein eingesetzt. Als Magerungsmittel unterstützt er die Formstabilität beim Trocknen, beim Brennen wirkt er als Flussmittel. Allerdings liegen sein Sinter- und sein Schmelzpunkt nahe beieinander, bei zu hohen Brenntemperaturen besteht mithin die Gefahr von Deformationen durch Ausgasen. Schamotte, als gemahlener gebrannter Ton oder Tonschiefer, ist ein Magerungsmittel, das die Porosität bei niedrigen Brenntemperaturen erhöht und die Trocknungs- und Brennschwindung reduziert. Magnesiummineralien (Talkum, Magnesit) verleihen den Erzeugnissen eine hohe Temperaturwechselbeständigkeit; sie werden bevorzugt für elektrotechnische Produkte eingesetzt.
Oxidische Rohstoffe
Mit den im Folgenden aufgeführten oxidischen Rohstoffen werden Oxidkeramiken hergestellt, die sich in vielen Anwendungen der technischen Keramik finden. Bei einem Teil davon handelt es sich um synthetische Rohstoffe.
Aluminiumoxid
Aluminiumoxidkeramiken basieren auf α-Al2O3, dem Korund. Sie dienen zum Beispiel als Schleif- und Poliermittel und werden auch als Trägermaterial für integrierte Schaltkreise eingesetzt. Aus gesintertem Korund oder Schmelzkorund lassen sich feuerfeste Erzeugnisse herstellen. Aluminiumoxiderzeugnisse können Glasphase enthalten, ein hoher Glasphaseanteil setzt die Sintertemperatur herab, jedoch auch die Festigkeit und Temperaturbeständigkeit.
Um die Festigkeit weiter zu erhöhen, kann Zirkoniumoxid zugesetzt werden. Diese besonders zähe Keramik wird als ZTA (Zirconia toughened alumina) bezeichnet.
Berylliumoxid
Aus gesintertem Berylliumoxid (BeO) werden Tiegel für chemische Reaktionen bei sehr hohen Temperaturen hergestellt. Des Weiteren wurden aus BeO elektrisch isolierende, aber hoch wärmeleitfähige Chip-Träger produziert, um die entstehende Wärmeenergie an einen Kühlkörper abzuleiten. Wegen des hohen Preises und der Giftigkeit ist BeO zunehmend durch andere Materialien ersetzt worden, z. B. Aluminiumoxid oder das teurere Aluminiumnitrid zur Wärmeableitung und Graphit für Hochtemperatur-Laborgefäße.
Weitere oxidische Rohstoffe
Weitere oxidische Rohstoffe, die bei der Keramikherstellung verwendet werden, sind z. B. Zirconium(IV)-oxid, Titan(IV)-oxid.
Nichtoxidische Rohstoffe
Die im Folgenden aufgeführten nichtoxidischen Rohstoffe werden zur Herstellung von Nichtoxidkeramiken verwendet, die sich in vielen technischen Anwendungen (siehe technische Keramik) durchgesetzt haben. In der Praxis werden alle diese Rohstoffe künstlich erzeugt.
Siliciumcarbid
Siliciumcarbid (SiC) gehört wegen seiner besonderen Eigenschaften zu den wichtigsten Industriekeramiken für Hochleistungsanwendungen. Es wird als Schleifmittel, in Gleitlagern von Chemiepumpen, als Dieselrußpartikelfilter, Gleitringdichtungen und für Hochtemperaturanwendungen als temperaturstabiles Formbauteil (zum Beispiel Receiver bei Solarturm-Kraftwerken) verwendet. Es eignet sich für diese Anwendungen, da es sehr hart sowie resistent gegen Wärme und Chemikalien ist. Zudem bestehen die Kupplungsscheiben und Bremsscheiben in Renn- und Luxuswagen aus kohlenstofffaserverstärktem Siliciumcarbid (C/SiC).
Die wichtigste Herstellungsart ist das Acheson-Verfahren. Quarzsand wird mit Koks bei 2200 °C zu Siliciumcarbid reduziert, wobei Kohlenmonoxid entsteht:
Das ist vergleichbar der Reduktion von Quarz zu Rohsilicium; es wird allerdings ein Überschuss von Kohlenstoff verwendet. Für bessere Formgebung ist die Herstellung aus geschmolzenem Silicium und Kohlenstoff geeignet. Hier hat sich Holzkohle bewährt, die vorher auf die richtige Form gebracht wurde. Durch die Poren kann Silicium aufgenommen werden und dann zu SiC reagieren. Dabei entsteht eine Sonderform des Siliciumcarbid, das sogenannte SiSiC (siliciuminfiltriertes SiC), in dem sich immer noch einige Prozent nicht umgesetztes Silicium befinden, was die Korrosionsbeständigkeit verringert.
In der Natur wird SiC nur selten gefunden. Es wird dann als Moissanit bezeichnet.
Bornitrid
Da Bornitrid (BN) bei Normalbedingungen analog zu Graphit aufgebaut ist und darüber hinaus sehr temperaturbeständig ist (es reagiert erst bei 750 °C mit Luft), ist es als Hochtemperatur-Schmiermittel geeignet. Die diamantähnliche Modifikation des kubischen Bornitrids ist nach Diamant das härteste Material.
Die hexagonale Kristallstruktur kann man ableiten, wenn man bei Graphit abwechselnd die Kohlenstoffe durch Bor und Stickstoff ersetzt. Anders ausgedrückt, besteht sie aus Ebenen von an allen Seiten kondensierten Borazin-Ringen. Bornitrid ist nicht elektrisch leitfähig wie Graphit, da die Elektronen stärker an den Stickstoffatomen lokalisiert sind.
Bei 60–90 kbar und 1500–2200 °C wandelt sich BN in die kubisches Form um, das in einer zum Diamant analogen Zinkblendestruktur auskristallisiert. Kubisches Bornitrid ist ähnlich hart wie Diamant, aber oxidationsbeständiger und wird daher als Schleifmittel eingesetzt.
Ab und an wird auch der Begriff Borazon verwendet, welcher einst als Schutzmarke von General Electric eingeführt wurde. Dieser Begriff ist allerdings gleichbedeutend mit kubischem Bornitrid[15].
Borcarbid
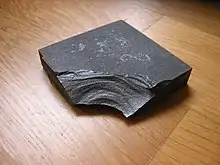
Borcarbid (B4C) ist ein weiterer sehr harter Werkstoff (an dritter Stelle nach Diamant und Bornitrid). Es wird als Schleifmittel und für Panzerplatten und Sandstrahldüsen verwendet. Die Herstellung erfolgt bei 2400 °C aus B2O3 und Kohlenstoff.
Weitere nichtoxidische Rohstoffe
Weitere nichtoxidische Rohstoffe, die bei der Keramikherstellung verwendet werden, sind Siliciumnitrid, Aluminiumnitrid, Molybdändisilicid und Wolframcarbid.
Manipulierte keramische Rohstoffe
Ursprünglich hier „metallisch-keramische Rohstoffe“ genannt. Die Keramik hat in der Regel nichts mit metallischen Werkstoffen zu tun. Da man Metalle ähnlichen Formgebungsprozessen zuführen kann wie keramische Rohstoffe, wurde diese Rubrik wohl irreführend so genannt. Es handelt sich um Trockenpressen, Schlickergießen oder plastische Formgebung mittels Bindemitteln. Man bezeichnet diesen Teil der Herstellung metallischer Werkstoffe als Pulvermetallurgie. Dabei wird mit feinsten Körnungen gearbeitet.
- Trockenpressen
- Das Keramikpulver wird trocken in einer Stahlmatrix durch Druck von einem Unter- und einem Oberstempel mit Drücken von über 1 t/cm² verpresst. Es ist auch kaltisostatisches Pressen möglich. Dabei wird das Keramikpulver in eine Gummiform gefüllt und mittels Flüssigkeitsdruck (meist Öl) von allen Seiten gleichmäßig gepresst. Nach der Formgebung wird das Werkstück gebrannt bzw. gesintert. Bei dem Formgebungsverfahren des kaltisostatischen Pressens sind gegenüber dem Trockenpressen gleichmäßige Eigenschaften im gesamten Werkstück möglich.
- Schlickergießen
- Das keramische Pulver wird mit Wasser und einem geeigneten Verflüssiger (Elektrolyt) bei geringer Viskosität in Suspension gebracht. Dabei ist es möglich, die Viskosität der Suspension durch den Einsatz von Peptisationshilfsmitteln herabzusetzen, so dass möglichst viel Feststoff/Volumen in die Suspension / den Schlicker eingebracht werden kann. Durch Gießen des Schlickers in Gips-Gießformen, wobei die Gipsform das Wasser aus dem Schlicker absorbiert, bildet sich am Formenrand eine plastische Haut. Wenn die überflüssige Schlickermasse abgegossen wird, verbleibt in der Form das eigentliche Produkt. Nach der anschließenden Trocknung und Sinterung wird das Endprodukt hergestellt.
- Plastische Formgebung
- Durch Versetzen des keramischen Pulvers mit sogenannten Plastifizierungsmitteln wird eine Formbarkeit des Materials erreicht. Diese Plastifizierungsmittel sind häufig organischen Ursprungs. Sie härten durch Polykondensation bzw. durch Polymerisation aus, so dass sie durch die vollständige Reaktion des Plastifizierers aushärten und eine ausreichende Festigkeit erhalten. Die Formgebung selbst geschieht entweder durch Strangpressen oder durch das Pressen in Formen. Die organischen Zusätze verbrennen später im Brand. Diese Materialkombination wird in flüssigerer Form mittlerweile auch beim Rapid Prototyping (3D-Druck) angewendet.
Andere Zusatzstoffe
Weitere Zusatzstoffe sind Flussmittel in der Glasindustrie. Plastifizierer oder Flockungsmittel verbessern die Formbarkeit und verbrennen beim Brennprozess. Organische Plastifikatoren sind zum Beispiel Leim, Wachse, Gelatine, Dextrin, Gummiarabikum, Paraffinöl. Weiterhin verwendet werden Verflüssiger oder Peptisatoren, die zur Verhinderung von Flockung des Rohmaterials eingesetzt werden.
Sonstige Hilfsmittel sind fein gemahlene Ausbrennmittel wie Säge- und Korkmehl, Stärke, Kohlestaub und Styroporkugeln. Sie machen den Scherben porös und leicht und können interessante Oberflächeneffekte erzeugen; sie verbrennen ebenfalls beim Brand. Sogenannte Porosierungsmittel haben den Haupteinsatzzweck in der Ziegelindustrie, wobei sie die Dichte und die Wärmeleitfähigkeit der Ziegel reduzieren.
Herstellungsschritte
Aufbereitung der Rohstoffe
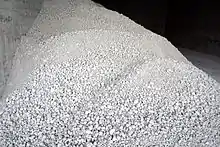
In der industriellen Keramikproduktion werden die Komponenten, nachdem sie teilweise vorgebrannt wurden, entsprechend der Rezeptur gemeinsam in Trommelmühlen fein gemahlen. Nach dem Schlämmen unter Zugabe von Wasser wird dieses in Filterpressen wieder weitgehend entfernt. Der zurückbleibende Filterkuchen wird getrocknet und nochmals gemahlen. In dieser Form wird die Rohmasse entweder gelagert oder sofort unter Zugabe von Wasser und verflüssigenden Hilfsstoffen in Maschinen geknetet und ggf. entlüftet. Daneben hat in jüngerer Zeit die halbnasse und die trockene Aufbereitung bei der industriellen Herstellung Bedeutung gewonnen. In der Töpferwerkstatt wird zum Teil noch heute dieser Prozess in aufwändiger Handarbeit durchgeführt. Da Mahlwerke oft nicht zur Verfügung stehen, kommt dem Schlämmen große Bedeutung zu. Die Homogenisierung der Masse wurde in mühsamer Knetarbeit erreicht. Heute stehen dafür meist Maschinen zur Verfügung. Ziel ist es, eine möglichst homogene, geschmeidige und blasenfreie Arbeitsmasse zu erzeugen.
Formgebung
Die Formgebung der Grünkörper oder Rohlinge zur Herstellung feinkeramischer Erzeugnisse kann nach historisch-traditionellen Verfahren oder modernen Methoden erfolgen. Zu diesen Verfahren gehören unter anderem:
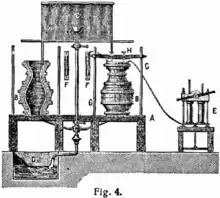
- Schlickerguss durch Einbringen der flüssigen Keramikmasse (auch Schlicker) in Gipshohlformen oder Gefrierguss
- Spritzguss und temperaturinverser Spritzguss
- Foliengießen
- Modellieren
- Extrudieren
- Aufbauarbeit aus einzelnen Strängen (z. B. bei Hohlgefäßen)
- Plattentechnik
- Drehen rotationssymmetrischer Hohlgefäße auf der Töpferscheibe
- Eindrehen oder Überdrehen rotationssymmetrischer Körper in Hohlformen mit Hilfe von Schablonen auf der Drehscheibenmaschine
- Pressen
- uniaxiales Pressen
- kaltisostatisches Pressen
- heißisostatisches Pressen (HIP)
- Trennende Nachbearbeitung mit Funkenerodieren, Stanzen oder Fräsen
In der Formgebung zur Herstellung grobkeramischer Erzeugnisse können zudem das Strangpresseverfahren und das Formpressverfahren, vor allem zur Fertigung von Rohren und Stangen, Anwendung finden. In der industriellen Großserienfertigung haben die halbtrockene und die trockene Formgebung Bedeutung erlangt, da hierbei wesentlich geringere Trocknungszeit der Grünkörper bei gleichzeitig besserer Maßhaltigkeit erreichbar sind. Da jedoch Verunreinigungen, beispielsweise lösliche Salze nicht abgetrennt werden können, sind diese Verfahren für die Herstellung von Porzellan und anderen feinkeramischen Erzeugnissen vorerst ungeeignet.
Neben der Herstellung von Keramikteilen durch additive Fertigungsverfahren[16], ist zukünftig auch eine finalisierende Formgebung durch hermetisch-stoffschlüssiges Fügen mittels Keramiklaserschweißen mit Ultrakurzpulslasern denkbar geworden[17].
Beschichtungen und Infiltration
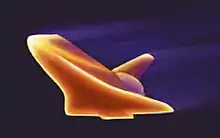
In der technischen Keramik werden auch folgende Sonderverfahren angewandt:
- Chemische Gasphasenabscheidung (englisch chemical vapor deposition, CVD): Bei diesem Verfahren reagieren mehrere Gase unter einem bestimmten Druck und hohen Temperaturen und scheiden auf Oberflächen den keramischen Stoff ab. So lassen sich zum Beispiel Bornitridschichten durch ein Gasgemisch aus Bortrichlorid und Ammoniak, Siliciumcarbidschichten durch ein Gemisch aus Methyltrichlorsilan und Wasserstoff, Kohlenstoffschichten durch ein Gemisch aus Methan und Argon oder Propan und Argon herstellen. Wird die Schicht vom formgebenden Untergrund (zum Beispiel Graphit) getrennt, hat man das fertige keramische Bauteil.
- Chemische Gasphaseninfiltration (englisch chemical vapor infiltration, CVI): Hier ist die Form durch ein zu infiltrierendes Teil vorgegeben, zum Beispiel durch eine fixierte Gewebestruktur aus Kohlenstofffasern oder eine andere offenporige, schwammähnliche Struktur. Gasgemische und Abscheideprodukt entsprechen denen des CVD-Verfahrens (siehe auch keramischer Faserverbundwerkstoff).
- Physikalische Gasphasenabscheidung (englisch physical vapor deposition, PVD): Anders als beim CVD wird mithilfe physikalischer Verfahren das Ausgangsmaterial in die Gasphase überführt. Das gasförmige Material wird anschließend zum zu beschichtenden Substrat geführt, wo es kondensiert und die Zielschicht bildet. Anwendung besonders für dünne Schichten.
Das Trocknen
Nach der Formgebung ist der Rohling feucht durch
- mechanisch eingeschlossenes Wasser in den Hohlräumen,
- physikochemisch gebundenes Wasser (Adhäsion, Kapillarwasser) und
- chemisch gebundenes Wasser (Kristallwasser).
Die Trocknungsgeschwindigkeit hängt außer von dem umgebenden „Klima“ stark von der Rezeptur der Rohmasse ab. Um die Trocknungsgeschwindigkeit zur Vermeidung von Rissen niedrig zu halten, können die Rohlinge abgedeckt werden. Industriell erfolgt das Trocknen in klimatisierten Räumen. Das physikochemisch gebundene und insbesondere das chemisch gebundene Wasser werden allerdings erst durch den Brand vertrieben.
Unterschieden werden drei Stadien des Trocknens:
- Lederhart: Der Scherben lässt sich nicht mehr verformen, besitzt aber noch soviel Feuchtigkeit, dass man ihn dekorieren kann.
- Lufttrocken: Der Scherben gibt bei Raumtemperatur keine Feuchtigkeit mehr ab und fühlt sich kühl an.
- Brennreif: Der Scherben fühlt sich nicht mehr kühl an, sondern erweist sich als bedingt saugfähig (Versuch: Zunge bleibt an Scherben kleben).
Der Brennprozess
Der Brennprozess (Roh- oder Schrühbrand) überführt den getrockneten Formkörper in ein hartes, wasserbeständiges Produkt. In der technischen Keramik wird dieser Prozess auch als Sintern bezeichnet. Bei niedrigen Temperaturen (< 1000 °C) werden flüchtige Bestandteile ausgetrieben (Wasser, Kohlenstoffdioxid, organische Hilfsstoffe). Dabei zersetzen sich die tonigen Bestandteile und bilden neue Minerale. In dem entstehenden „Scherben“ schließen sich Kristalle an den Korngrenzen zusammen (Kristallwachstum) und werden (falls enthalten) durch glasige Anteile verkittet. Anteil und Art (Korngrößenverteilung, Texturen etc.) der Kristall- und Glasphase sowie der Poren bestimmen die Eigenschaften des gebrannten Guts. Sehr wichtig ist vor dem Brennen das sehr langsame Hochheizen der Keramik, damit das Wasser vollständig ausgetrieben wird und nach dem Brennen das sehr langsame Abkühlen, um die Bildung von Rissen zu vermeiden.
Die angewandten Temperaturen reichen bis etwa 1400 °C; bei Sonderkeramiken liegen sie auch erheblich höher. In Abhängigkeit von den Rohstoffen und dem gewünschten Produkt wird die Brenntemperatur häufig während des Brennprozesses variiert (Temperaturprofil). Überdies muss der Prozess in vielen Fällen zeitweilig unter reduzierender Atmosphäre verlaufen, um etwa bei weißem Geschirr oder bei Sanitärkeramik eine Gelbfärbung durch Eisenverunreinigungen zu vermeiden. Bei Brenntemperaturen von 1400 °C und mehr werden Tragegestelle aus besonders hitzebeständigen Materialien wie Siliciumcarbid verwendet.
Bei der Massenproduktion wird zwischen periodischen und kontinuierlichen Öfen unterschieden. Eingesetzt werden Kammer- und Ringöfen sowie Tunnelöfen (Herstellung von Ziegeln, Produkten aus feuerfesten Werkstoffen und Porzellan) und Rollenöfen (für flache Erzeugnisse wie Fliesen). Überwiegend kommen Öfen mit fossilen Brennstoffen zum Einsatz. In Handwerksbetrieben werden oft elektrische Öfen verwendet. Bei Brennöfen für kleine Stückzahlen ist zu unterscheiden zwischen offenen Systemen, bei denen die Brenngase (mit unterschiedlicher Flammführung) in unmittelbaren Kontakt mit der Ware treten, und Muffelöfen, bei denen die Brenngase das Brenngut indirekt erhitzen.
Für die nachträgliche Ermittlung von Brenntemperaturen, wie es bei antiken Keramiken üblich ist, gibt es zwei methodische Ansätze. Entweder wird das angenommene Ausgangsmaterial experimentell solange kontinuierlich erhitzt, bis annähernd die gleichen Eigenschaften erzielt sind, oder es werden temperatur-indizierende Minerale (etwa Gehlenit), die ein begrenztes Temperatur-Stabilitätsfeld haben, genau untersucht und auf diese Weise die Brenntemperatur abgeschätzt.[18]
Die für das Brennen von Massenprodukten der Keramik verwendeten Durchlauföfen sind sehr energieintensiv. Es ist eine verfahrenstechnische Herausforderung, die Qualität und Menge der gebrannten Produkte mit möglichst geringem Energieverbrauch herzustellen.[19]
Glasuren
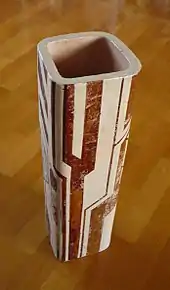
Glasuren sind dünne Glasüberzüge. Zum einen machen sie den porösen Keramikkörper nahezu wasserdicht und geben ihm eine leicht zu reinigende Oberfläche. Zum anderen ermöglichen sie eine abwechslungsreiche, dekorative Gestaltung der Keramiken. Glasuren können farbig, transparent oder deckend (opak), glänzend, halbmatt oder matt sein. Sie können weich und niedrig schmelzend (ab etwa 800 °C bei Raku-Keramik bis etwa 1000 °C) oder hart und hoch schmelzend (ab 1000 °C bis etwa 1400 °C bei Porzellan) sein. Nach ihrer chemischen Zusammensetzung kann man z. B. zwischen Borosilikat-, Feldspat-, Salz-, Gold- und bleihaltigen Glasuren unterscheiden. In jedem Fall ist aber der glasbildende Hauptbestandteil SiO2 wie beim Flaschen- oder Fensterglas. Die Glasuren werden häufig in der Keramikherstellung erst nach dem Schrühbrand der Ware aufgebracht (Tauchen, Spritzen, Pinseln, Stempeln) und in einem erneuten Brennprozess (Glattbrand) verglast. Dieser Brand wird auch Glasurbrand genannt und benötigt höhere Temperaturen als der Schrühbrand. Hierbei sintert der Scherben und wird dicht.
Bei Aufglasurmalerei benötigt man in der Regel für jede Farbe einen weiteren Brand. Dieser liegt unterhalb der Sintertemperatur. Auch beim Einsatz von Siebdrucktechnik lässt sich ein weiterer Brand nicht vermeiden: Hier müssen die Temperaturen sogar unterhalb der Schrüh-Temperatur liegen.
Bei der traditionellen Salzglasur wird beim Brand Steinsalz in das Feuer gegeben, dessen Gase das Brenngut überstreichen. Dabei senkt das sich niederschlagende Natriumoxid oberflächlich die Schmelztemperatur und erzeugt auf dem Scherben eine Glasur.
Institutionen
Wissenschaft
Die Deutsche Keramische Gesellschaft e. V. (DKG) versteht sich als technisch-wissenschaftlicher Verein für die gesamte Keramik. Sie ist die Diskussionsplattform dieses Industriebereichs zu allen technisch-wissenschaftlichen Fragestellungen (Ausbildung, Fortbildung, Forschung, Lehre und Umweltschutz) sowie zentrale Kontaktstelle zwischen Wissenschaft und keramischer Industrie.
Keramikkunst
Die künstlerische Seite einer Modernen Keramik als Teil der Modernen Kunst wird nicht durch eine einzige Institution vertreten, sondern in einer Vielzahl von Einrichtungen der Keramikkunst, wie Museen, Symposien, Galerien etc. vermittelt.
Museen
- Hetjens – Deutsches Keramikmuseum, Düsseldorf
- Stiftung Keramion, Frechen
- Museum Schloss Fürstenberg, Fürstenberg
- Keramikmuseum Westerwald, Höhr-Grenzhausen
- Töpfereimuseum Langerwehe, Langerwehe
- Museum Schloss Glücksburg – Sammlung zeitgenössischer internationaler Keramikkunst (seit 1975), Römhild
- Keramikmuseum Scheibbs, Scheibbs
- Porzellanikon – Museumskomplex in Selb und Hohenberg an der Eger
Weitere Museen: siehe Weblinks
Siehe auch
Literatur
Technik
- Kleine Enzyklopädie Technik. Bibliographisches Institut, Leipzig 1972.
- Keramik. In: Hans-Herbert Möller (Hrsg.): Restaurierung von Kulturdenkmalen. Beispiele aus der niedersächsischen Denkmalpflege (= Berichte zur Denkmalpflege. Beiheft 2). Niedersächsisches Landesverwaltungsamt – Institut für Denkmalpflege. Niemeyer, Hameln 1989, ISBN 3-87585-152-8, S. 117–138.
- Werkstoffe und Werkstoffprüfung – Grundlagen. In: Lueger Lexikon der Technik. (vier Bände), Rowohlt Taschenbuch-Verlag, Reinbek 2003, ISBN 3-499-19008-7.
- P. Rada: Die Technik der Keramik. Dausien, 1989, ISBN 3-7684-1868-5.
- Sven Frotscher: dtv-Atlas Keramik und Porzellan. München 2003, ISBN 3-423-03258-8.
- Verband der Keramischen Industrie e. V. (Hrsg.): Brevier Technische Keramik. 4. Auflage. Fahner Verlag, Lauf a.d. Pegnitz 2003, ISBN 3-924158-36-3.
Geschichte
- Peter Hommel: Ceramic Technology. In: Vicki Cummings, Peter Jordan, Marek Zvelebil (Hrsg.): The Oxford Handbook of the Archaeology and Anthropology of Hunter-Gatherers. Oxford University Press, Oxford Online Publication Date: Oct 2013 doi:10.1093/oxfordhb/9780199551224.013.008
- Detlev Jantzen: Töpferei und Feuerkult – Vom Leben auf der Anhöhe bei Triwalk, Lkr. Nordwestmecklenburg. In: Die Autobahn A 20 – Norddeutschlands längste Ausgrabung. Archäologische Forschungen auf der Trasse zwischen Lübeck und Stettin. Schwerin 2006, ISBN 3-935770-11-1, S. 33–36.
- Peter Jordan, Marek Zvelebil (Hrsg.): Ceramics before farming, the dispersal of pottery among prehistoric Eurasian hunter-gatherers. Left Coast Press, Walnut Creek 2009.
- R. Schreg: Keramik aus Südwestdeutschland. Eine Hilfe zur Beschreibung, Bestimmung und Datierung archäologischer Funde vom Neolithikum bis zur Neuzeit. Lehr- und Arbeitsmaterialien zur Archäologie des Mittelalters und der Neuzeit. Tübingen 1998, ISBN 3-9806533-0-7.
Weblinks
- Literatur von und über Keramik im Katalog der Deutschen Nationalbibliothek
- Auswahl von Videos aus der Fernsehsendung Kunst und Krempel des Bayerischen Rundfunks mit ausführlichen Beschreibungen von Keramik-Objekten
Weitere Museen:
- Keramik-Museum Berlin
- Keramik-Museum Bürgel
- Töpfereimuseum Langerwehe
- Töpfereimuseum Raeren (Belgien)
- Keramik- und Glasmuseum Ariana, Genf (Schweiz)
Bildungsorganisationen:
- Bildungs- und Forschungszentrum Keramik in Höhr-Grenzhausen
- Staatliche Fachschulen für Keramik in Höhr-Grenzhausen
- Staatliche Fachschule für Keramik in Landshut
- Landesfachschule für Keramik und Ofenbau in Stoob (Österreich)
- Keramikdesign Fachklasse, Schule für Gestaltung Bern und Biel in Bern (Schweiz)
Berufsverband und technisch-wissenschaftlicher Verband:
Wirtschaftsverbände:
- Bundesverband Keramische Rohstoffe und Industrieminerale, Neuwied
- Informationszentrum der Fachgruppe Technische Keramik Verband der Keramischen Industrie, Selb
- Bundesverband Keramische Industrie, Selb
Einzelnachweise
- Vgl. Keramik bei Duden online.
- Miroslav Králík: Ancient ceramics and imprints on their surfaces. In: Jiři Svoboda: Pavlov – Excavations 2007–2011. (= The Dolní Věstonice Studies. Band 18). 1. Auflage. Academy of Sciences of the Czech Republic, Brno 2011, ISBN 978-80-86023-85-4, S. 207–244 (Kapitel III.10.)
- Thomas Einwögerer: Die jungpaläolithische Station auf dem Wachtberg in Krems, Niederösterreich. Eine Rekonstruktion und wissenschaftliche Darlegung der Grabung von J. Bayer aus dem Jahre 1930. (= Mitteilungen der Prähistorischen Kommission. Band 34). Wien 2000.
- Y. V. Kuzmin: The earliest centres of pottery origin in the Russian Far East and Siberia: review of chronology for the oldest Neolithic cultures. In: Documenta Praehistorica. 29, 2002, S. 37–46.
- Jeanette Werning: Früheste Scherben, frühester Reis, früheste Hirse. Zur Neolithisierung in China. In: Jörg Eckert (Hrsg.): Archäologische Perspektiven. Analysen und Interpretationen im Wandel. Leidorf, Rahden/Westfalen 2003, S. 103–129.
- Elisabetta Boarettoa u. a.: Radiocarbon dating of charcoal and bone collagen associated with early pottery at Yuchanyan Cave, Hunan Province, China. In: PNAS. 2009, doi:10.1073/pnas.0900539106
- Die ersten Töpfer lebten in China. In: wissenschaft.de. 2. Juni 2009, abgerufen am 9. September 2019. (deutsche Zusammenfassung des Artikels der PNAS)
- Pottery 20,000 years old found in a Chinese cave. In: USA Today. 28. Juni 2012.
- Eric Huysecom: Wann begann Afrikas Jungsteinzeit? In: Spektrum der Wissenschaft. 8/2008, S. 62–67.
- Hermann Salmang, Horst Scholze: Keramik. Springer Science & Business Media, 2006, ISBN 978-3-540-63273-3, S. 2 (eingeschränkte Vorschau in der Google-Buchsuche).
- Hennicke, H.W.: Zum Begriff Keramik und zur Einteilung keramischer Werkstoffe. Ber. Dtsch. Keram Ges. 44 (1967) 209–211
- Hanno Schaumburg: Keramik. Springer-Verlag, 2013, ISBN 978-3-663-05976-9, S. 1 (eingeschränkte Vorschau in der Google-Buchsuche).
- Roland Strietzel: Die Werkstoffkunde der Metall-Keramik-Systeme. Verlag Neuer Merkur GmbH, 2005, ISBN 978-3-937346-14-4, S. 101 (eingeschränkte Vorschau in der Google-Buchsuche).
- Wolfgang Kollenberg: Technische Keramik Grundlagen, Werkstoffe, Verfahrenstechnik. Vulkan-Verlag GmbH, 2004, ISBN 978-3-8027-2927-0, S. 2 (eingeschränkte Vorschau in der Google-Buchsuche).
- Dr. Robert Wentorf and Borazon, 1957 - General Electric Company. Abgerufen am 21. Oktober 2021 (englisch).
- Zhangwei Chen et al.: 3D printing of ceramics. A review. In: ScienceDirect. Elsevier, 6. November 2018, abgerufen am 15. September 2019 (englisch).
- E. H. Penilla et al.: Ultrafast laser welding of ceramics. In: Science. American Association for the Advancement of Science (AAAS), 23. August 2019, abgerufen am 15. September 2019 (englisch).
- C. Tschegg, Th. Ntaflos, I. Hein: Thermally triggered two-stage reaction of carbonates and clay during ceramic firing – a case study on Bronze Age Cypriot ceramics. In: Applied Clay Science. 43, 1, 2009, S. 69–78, doi:10.1016/j.clay.2008.07.029.
- Hajo Hagens, Rudolf Jeschar, Peter Jeschke, Hartmut Kainer: Veränderung der Prozessführung und der Energiebilanz von Tunnelöfen bei der Verbesserung vo Tunnelwagenaufbauten In: cfi/Ber. DKG. 64, 6/7, 1987, S. 205–210.