Erdölraffinerie
Eine Erdölraffinerie ist ein Industriebetrieb, der den Rohstoff Erdöl durch Reinigung und Destillation unter Normaldruck und unter Vakuum in Fraktionen mit einem definierten Siedebereich überführt. Die weitere Verfeinerung erfolgt durch Verfahren wie Extraktion oder chemische Reinigungsverfahren. Um die Qualität der Produkte, etwa deren Oktanzahl, zu steigern, werden Konversionsverfahren wie die Isomerisierung oder das katalytische Reforming eingesetzt. Des Weiteren werden den Produkten Additive zugesetzt, die gewisse Eigenschaften entweder verbessern oder unterdrücken.
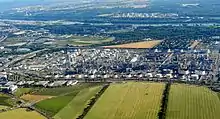
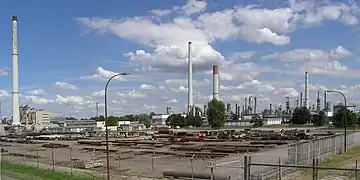
Dabei werden höherwertige Produkte wie Ottokraftstoff, Dieselkraftstoff, Heizöl oder Kerosin gewonnen. Für die chemische Industrie fallen Rohstoffe wie Flüssiggas, Naphtha und Mitteldestillat an. Erdölraffinerien sind üblicherweise große industrielle Komplexe, deren Bild durch ausgedehnte Tanklager, Rektifikationskolonnen, Rohrleitungssysteme sowie Fackelanlagen geprägt ist. Erdölraffinerien gelten als energieintensive Betriebe. Der hohe (bis zu 50 % der Kosten) notwendige Energieeinsatz für die Produktion wird dabei zum Teil aus den primären Energieträgern selbst gewonnen, als auch als elektrische und thermische Energie zugeführt.[1]
Geschichte
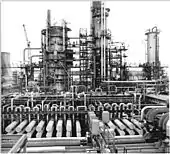
Die ersten Raffinerien entstanden schon zum Beginn der Mineralöl-Ära Mitte des 19. Jahrhunderts. Der erste Raffineriebetrieb wurde 1856 von Ignacy Łukasiewicz, dem Erfinder der Petroleumlampe, in Ulaszowice (Polen) eingerichtet. Nachdem diese von einem Feuer vernichtet wurde, wurde in Chorkówka eine weitere, modernere Raffinerie gebaut. Sehr schnell begannen die aus Erdöl gewonnenen Leuchtöle die bis dahin aus Tierfetten, insbesondere Waltran, gewonnenen Lampenbrennstoffe zu ersetzen, wozu zunächst eine Aufbereitung des Erdöls durch Destillation notwendig war.[2]
Die Destillation des gewonnenen Erdöls fand auf eine sehr einfache Weise statt. In einem Kupferkessel wurden etwa 750 Liter Erdöl zum Sieden gebracht. Die entstehenden Dämpfe wurden durch ein Kühlrohrsystem geleitet, in dem sie kondensierten. Auf diese Weise wurde Petroleum zu Beleuchtungszwecken gewonnen. Der im Kessel verbliebene teerartige Rückstand wurde als Abfall entsorgt.
Die Verwertung weiterer aus dem Erdöl gewonnener Produkte und insbesondere die schnelle Verbreitung der Verbrennungsmotoren nach dem Ersten Weltkrieg erforderte nicht nur den Bau zahlreicher neuer Raffinerien, sondern führte auch zu einer rasanten Weiterentwicklung der in einer Raffinerie verwendeten Verfahren.
Wie in vielen anderen Industriezweigen haben sich die Anforderungen an eine Raffinerie, insbesondere an die Produkte, im Laufe der Jahre geändert. Grundsätzlich ist hier das Anpassen der Produktspezifikation zu nennen, die sich aufgrund der Gesetze (Umwelt und Gesundheit) geändert haben. So sank der erlaubte Schwefelgehalt bei den meisten Kraftstoffen und auch beim Heizöl. Bei den Vergaserkraftstoffen sanken die Benzol- und die Aromatenspezifikationen.
Einsatzstoffe
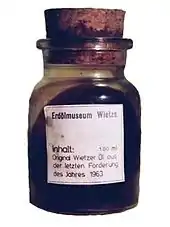
Erdöl besteht aus einem Kohlenwasserstoffgemisch. Am häufigsten vertreten sind lineare oder verzweigte Alkane (Paraffine), Cycloalkane (Naphthene) und Aromaten. Jedes Erdöl hat je nach Fundort eine spezielle chemische Zusammensetzung, die auch die physikalischen Eigenschaften wie Farbe und Viskosität bestimmt. Erdöl enthält in geringerem Maße stickstoff-, sauerstoff- oder schwefelhaltige Kohlenstoffverbindungen wie Amine, Porphyrine, Merkaptane, Thioether, Alkohole und Chinone. Daneben finden sich Verbindungen von Metallen wie Eisen, Kupfer, Vanadium und Nickel. Der Anteil der reinen Kohlenwasserstoffe variiert erheblich. Der Anteil reicht von 97 % bis zu nur 51 % bei Schwerölen und Bitumen. Der Kohlenstoffanteil liegt zwischen 83 und 87 %, der Wasserstoffanteil zwischen 10 und 14 %. Andere Hauptgruppenelemente liegen zwischen 0,1 und 1,4 %, der Gehalt an Metallverbindungen beträgt weniger als 1000 ppm.[3]
Typische Rohöle unterscheiden sich nach der Lagerstätte. Das West Texas Intermediate (WTI) ist ein qualitativ hochwertiges, schwefelarmes und leichtes Rohöl aus Cushing (Oklahoma). Ein europäischer Vertreter ist das Brent Blend, ein Rohöl aus dem aus 15 Ölfeldern bestehenden Brentsystem in der Nordsee. Das Dubai-Oman aus dem Mittleren Osten wird vor allem für den asiatisch-pazifischen Markt gefördert. Das Tapis aus Malaysia ist ein leichtes, Minas aus Indonesien ein schweres fernöstliches Rohöl.
Produkte
Flüssiggase, z. B. Propan, Butan | ~3 % |
Fertigprodukte | Mengenanteil |
---|---|
Rohbenzin (Naphtha, Cycloalkane) | ~9 % |
Benzin (Otto-Kraftstoff) | ~24 % |
Flugturbinenkraftstoff (Kerosin) | ~4 % |
Dieselkraftstoff, leichtes Heizöl (EL, L) | <21 % |
schweres Heizöl (M, S) | ~11 % |
Bitumen, Heizöl schwer (ES) | ~3,5 % |
Schmierstoffe (z. B. Spindelöl) | ~1,5 % |
Sonstige Produkte, Verluste usw. | ~2 % |
Die Fertigprodukte können gasförmig, flüssig oder fest sein. Prozentual ist die Ausbeute einer modernen Raffinerie in etwa 3 % an Flüssiggasen wie Propan und Butan. Etwa 9 % entfallen auf Rohbenzin (Naphtha), 24 % auf Benzin (Otto-Kraftstoff). Höhersiedende Kraftstoffe wie Flugturbinenkraftstoff (Kerosin) machen 4 %, Dieselkraftstoff und leichtes Heizöl bis zu 21 %, schweres Heizöl etwa 11 % aus. Die hochviskosen und festen Anteile wie Bitumen oder Heizöl schwer liegen bei 3,5 %, Schmierstoffe bei 1,5 %. Etwa 2 % entfallen auf sonstige Produkte oder Verluste. Der Eigenverbrauch der Raffinerie liegt je nach Weiterverarbeitungsgrad zwischen 5 und 11 % des eingesetzten Rohöls.[4] Die MiRO hat beispielsweise 16 Mio. t Rohölkapazität, die zu 14,9 Mio. t Endprodukten verarbeitet werden, das heißt, der Eigenverbrauch beträgt circa 7 %.
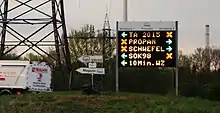
Die Mengenanteile an Fertigprodukten sind einerseits von den eingesetzten Rohölsorten, andererseits von den in der Raffinerie vorhandenen Verarbeitungsanlagen abhängig. So enthalten „leichte“ Rohöle relativ hohe Anteile an leichten Produkten, das heißt solche mit geringer Dichte wie Flüssiggas, Kerosin, Benzin, Diesel. Schwere Rohöle enthalten größere Anteile an schweren Produkten, wie schweres Heizöl und Bitumen. In modernen Raffinerien kann ein Teil dieser schweren Bestandteile in leichtere umgewandelt werden, beispielsweise durch Cracken, so dass eine solche Raffinerie mehr schweres Rohöl verarbeiten kann.
Raffinerieverfahren

Das aus den Lagerstätten gewonnene Erdöl wird vor dem Transport zur Raffinerie vor Ort aufbereitet, im Wesentlichen durch eine grobe Trennung von unerwünschten Bestandteilen, etwa Sedimenten und Wasser. Nach diesen ersten Verarbeitungsschritten wird das jetzt entstandene Rohöl per Schiff oder Pipeline zur Raffinerie geliefert. Hier wird das Flüssigkeitsgemisch in weiteren Schritten mit einem speziellen Destillationsverfahren in unterschiedliche Fraktionen getrennt und zu verkaufsfähigen Produkten aufbereitet. Die Technik ist heute so weit fortgeschritten, dass keine Stoffe des Rohöls ungenutzt bleiben. Selbst das als unerwünschtes Nebenprodukt anfallende Raffineriegas findet Verwendung. Es wird entweder direkt in den Prozessöfen als Energieträger benutzt oder in der chemischen Weiterverarbeitung als Synthesegas eingesetzt.
Erdölreinigung/Entsalzung
Das Erdöl/Rohöl wird bereits an der Lagerstätte von Sand und Wasser befreit. Um Korrosion in den Anlagen vorzubeugen, wird das Rohöl entsalzt (auf Salzgehalte <10 ppm), indem unter Zusatz von Wasser eine Rohöl-Wasser-Emulsion hergestellt wird. Das Salz löst sich in der wässrigen Phase dieser Emulsion. Die Emulsion wird dann in einem elektrostatischen Entsalzer wieder getrennt, wobei das salzhaltige Wasser sich am Boden absetzt und entsprechenden Aufbereitungsanlagen zugeführt wird und das entsalzte Rohöl weiter zur Destillation gepumpt wird. Die Brechung der Emulsion erfolgt bei erhöhten Temperaturen von etwa 130 °C, um die Viskosität des Rohöls zu senken und Spannungen von circa 20 kV. Durch Arbeiten bei erhöhtem Druck wird verhindert, dass leichtflüchtige Komponenten bei diesem Verfahrensschritt ausdampfen. Die Öl-Wasser-Emulsion kann auch durch Zugabe geeigneter Chemikalien, sogenannter Demulgatoren, gebrochen werden.
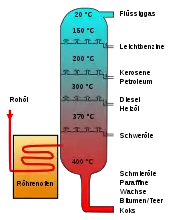
Primärverarbeitung (Rohöldestillation)
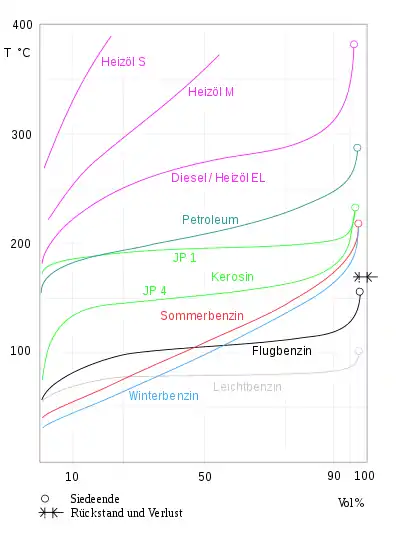
Nach der Entsalzung wird das Rohöl in zwei Stufen erwärmt. Die Vorwärmung geschieht in Wärmetauschern durch Wärmerückgewinnung des ablaufenden Produkts. Die Spitzenvorheizung erfolgt durch Öfen bis auf etwa 400 °C. Das erhitzte Öl wird durch Rektifikation in einer bis zu 50 m hohen Kolonne in seine Bestandteile aufgetrennt. Das Rohöl tritt in einer Zwei-Phasen-Strömung (gasförmig/flüssig) in die Kolonne ein. Das Temperaturprofil fällt nach oben hin ab. Da die Temperatur im Sumpf, also am Boden der Kolonne, am höchsten ist und die leichten Bestandteile somit nicht kondensieren können, steigen sie gasförmig weiter nach oben. Im Kopf der Kolonne fällt Gas und Leichtbenzin, so genanntes Naphtha, an, darunter Kerosin, Zwischenprodukt für Treibstoffe turbinengetriebener Luftfahrzeuge (nicht zu verwechseln mit dem so genannten „Flugbenzin“, dem AVGAS für Flugzeugottomotoren), Dieselkraftstoff und leichtes Heizöl, weiter unten Gasöl (Heizöl- und Diesel-Ausgangsstoffe) und im Sumpf – dem Fuß der Kolonne – der atmosphärische Rückstand (engl.: Long Residue). Diese erste Rektifikation findet bei atmosphärischem Druck statt und wird daher atmosphärische Rektifikation genannt.
Der Rückstand wird in einer weiteren Rektifikationskolonne bei niedrigem Druck (typischerweise ~20 mbar) erneut destilliert, um ihn in weitere Produkte aufzuspalten (siehe Vakuumdestillation). Eine Vakuumrektifikation ist nötig, da die Kettenlänge der schwersiedenden Kohlenwasserstoffe größer ist und diese bei hohen Temperaturen ab circa 400 °C dazu neigen, eher thermisch zu cracken als sich destillativ trennen zu lassen. Die Produkte der Vakuumdestillation sind Vakuumgasöl und der sogenannte Vakuumrückstand (engl.: Short Residue).
Konversionsverfahren und Blending
Nach der Primärverarbeitung wird eine Reihe von Veredlungsverfahren angewendet, um Schadstoffe (Schwefel, Stickstoff) zu entfernen und die Qualität der Zwischenprodukte zu verbessern. Anschließend werden die Endprodukte wie Motorenbenzin, Jet A-1, Dieselkraftstoff oder Heizöle aus verschiedenen Zwischenprodukten/Komponenten zusammengemischt (verschnitten), die bei unten genannten Herstellungsprozessen erzeugt werden.
Hydrotreating
Die bei der fraktionierten Destillation anfallenden Komponenten (Naphtha, Mitteldestillate, Vakuumgasöle) sind noch reich an Schwefelverbindungen. Diese würden bei der Weiterverarbeitung (katalytisches Reforming, s. u.) die Katalysatoren vergiften. Bei direkter Verbrennung unbehandelter Produkte (Heizöl) entstünde umweltschädigendes SO2. Beim Hydrotreating werden die zu entschwefelnden Komponenten mit Wasserstoff vermischt und auf etwa 350 °C erhitzt. Das heiße Gemisch gelangt in einen mit Katalysatoren aus Nickel, Molybdän oder Cobalt auf Aluminiumoxid gefüllten Reaktor, der Wasserstoff reagiert mit den Schwefel-, Stickstoff- und Sauerstoffverbindungen zu Schwefelwasserstoff, Ammoniak und Wasser.
Am Beispiel die Umsetzung von Mercaptanen: ,
die Umsetzung von Alkoholen:
und die Umsetzung von Aminen: .
Katalytisches Reforming
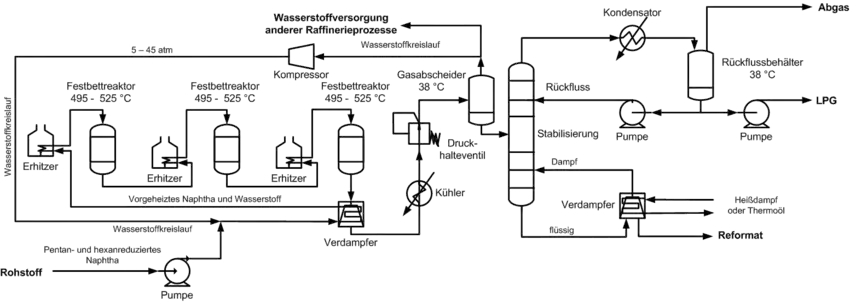
Das katalytische Reforming hat das Ziel, die Oktanzahl des Naphthas (Siedebereich ~70–1820 °C) zu erhöhen und aromatische Kohlenwasserstoffe zu erzeugen. Weiterhin erhält man Wasserstoff als Produkt, der in den Hydrotreating- und in Hydrocracking-Prozessen eingesetzt wird. Das Reforming läuft bei etwa 500 °C und – je nach Prozesstyp – 3,5–40 bar ab. Eingesetzt werden dabei bifunktionelle Katalysatoren (Platin-Zinn oder Platin-Rhenium, auf chloriertem Aluminiumoxid oder Zeolithen).
Typische Reaktionen beim Reforming sind:
- Ringschluss:
- Dehydrierung:
- Isomerisierung:
An den Metallzentren des Katalysators laufen dabei bevorzugt die Hydrierungs-/Dehydrierungsreaktionen ab, während die Säurezentren Isomerisierungs- und Ringschlussreaktionen katalysieren. Eine unerwünschte Nebenreaktion ist die Verkokung des Katalysators durch Polymerisations- und Dehydrierungsreaktionen. Die Verkokung wird durch Abbrennen des Kokses und anschließender Oxychlorierung des Katalysators entfernt.
Isomerisierung
In der Isomerisierung werden n-Alkane in iso-Alkane mit dem Ziel der Oktanzahlverbesserung umgewandelt oder das Substitutionsmuster an Aromaten verändert. So wird meta-Xylol in o- und p-Xylol isomerisiert, da diese zur Herstellung von Phthalsäureanhydrid oder Dimethylterephthalat verwendet werden. Es sind ähnliche Katalysatoren wie beim katalytischen Reforming im Einsatz. Die Reaktion wird bei niedrigeren Temperaturen um 250 °C und – zur Verhinderung der Katalysatordeaktivierung durch Verkokung – bei moderatem Wasserstoffpartialdruck von etwa 15 bar durchgeführt. Durch die im Vergleich zum katalytischen Reforming moderaten Verfahrensbedingungen werden Crack- und Ringschlussreaktionen weitgehend unterdrückt.
Weitere Isomerisationsverfahren beziehen sich auf die Umwandlung von n-Pentan zu iso-Pentan bzw. von n-Hexan zu iso-Hexan (Oktanzahlverbesserung, z. B. Hysomer-Prozess, PENEX-Prozess).
Alkylierung
Bei der Alkylierung werden iso-Alkane (Isobutan) und Alkene (n- und iso-) unter Säurekatalyse zu höhermolekularen hochoktanigen iso-Alkanen (C7-C12) umgesetzt. So reagieren Isobuten und Isobutan u. a. zu 2,2,4-Trimethylpentan (Isooktan). Dabei werden die Reaktanten in der Flüssigphase im Alkanüberschuss mit konzentrierter Schwefelsäure oder wasserfreier Flusssäure umgesetzt. Die typische Verweilzeit beträgt circa 10 bis 15 Minuten. Danach werden die Flüssigphasen durch Absetzen der Phasen getrennt. Im so genannten Iso-Stripper werden die iso-Alkane abgetrennt und in den Prozess zurückgeführt (recycled). Das fertige Endprodukt wird als Alkylat[5] bezeichnet. Das Verfahren bietet sich an, wenn die Raffinerie über einen Steam- oder Catcracker verfügt und damit die Einsatzstoffe für die Alkylierung liefern kann.
Cracken
Es gibt drei Hauptgruppen beim Cracken: thermisches, katalytisches und Hydrocracken.
Beim thermischen Cracken werden keine Katalysatoren eingesetzt. Dadurch können auch Rückstände der Erdöldestillation zugeführt werden, die wegen ihres Gehalts an Schwermetallen und Schwefel den Katalysator beim katalytischen Cracken schädigen würden.
Beim Visbreaking z. B. handelt es sich um das Cracken schwerer Rückstandsöle bei moderaten Verweilzeiten und Temperaturen um 500 °C mit dem Ziel, Gasöl zu erzeugen. Die Ausbeute an Gasöl (und leichter) liegt beim Visbreaker bei circa 30 %. Durch anschließende Destillation werden die leichtflüchtigen Fraktionen abgetrennt.
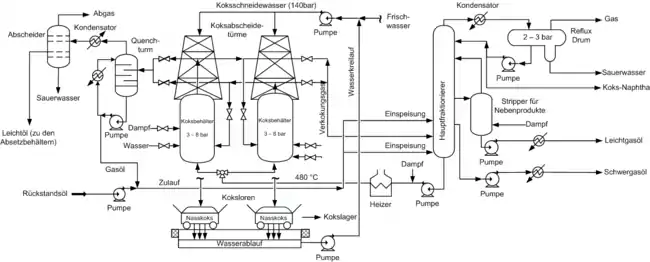
Beim Delayed Coking wird Petrolkoks durch thermisches Cracken von Rückständen der Vakuumdestillation gewonnen. Dazu wird das Rückstandsöl auf circa 500 °C erhitzt und in Kokskammern versprüht, wo es zu Petrolkoks, flüssigen und gasförmigen Kohlenwasserstoffen umgewandelt wird. Nach dem Verkoken wird der Koks mechanisch abgetrennt und ggf. in Calzinieröfen bei Temperaturen von 1200 °C von flüchtigen Bestandteilen befreit.
Es können aber auch Naphtha, Gasöl oder sogar hydrogenierte Vakuumgasöle (Hydrowax, Hydrocracker Bottoms) durch das sogenannte Steamcracken thermisch gecrackt werden, um Ethen, Propen und Aromaten zu erzeugen.
Beim katalytischen Cracken (engl. Fluid Catalytic Cracking, FCC) dienen saure Silikate als Katalysatoren, Edukte sind schwere atmosphärische Gasöle bzw. Vakuumgasöl. Als Produkte fallen überwiegend kurzkettige Olefine und Alkane an.
Beim Hydrocracken werden langkettige Alkane unter Wasserstoffzufuhr in kurzkettige Alkane überführt. Bei höheren Wasserstoffpartialdrücken werden sogar Aromaten hydrogeniert und somit auch Cycloalkane erzeugt. Als Edukt wird vorwiegend Vakuumgasöl verwendet. Die meisten Schwefel- und Stickstoffverbindungen des Edukts werden hydriert, so dass beträchtliche Volumina an H2S und NH3 anfallen.
Claus-Verfahren
Hydrotreating-Prozesse, Hydrocracking und ggf. die Synthesegaserzeugung aus Schweröl produzieren nicht unerhebliche Mengen H2S, welches nicht einfach "abgefackelt" werden kann. Beim Claus-Verfahren wird der anfallende Schwefelwasserstoff mit Luftsauerstoff in einem Reaktor unterstöchiometrisch verbrannt. Das entstandene SO2 komproportioniert mit restlichem H2S zu elementarem Schwefel und Wasser.
Die zunächst unvollständige Reaktion wird über mehrere katalytische Stufen bei tieferen Temperaturen zum vollständigen Umsatz getrieben.
In einem anderen Verfahren (WSA Prozess, engl. wet sulfuric acid) wird aus Schwefelwasserstoff direkt Schwefelsäure hergestellt.
Umweltschutz, Arbeitssicherheit und Anlagensicherheit
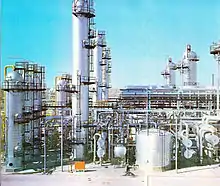
Die prozesstechnischen Anlagen, die Tanklager und die Rohrleitungssysteme sind Gegenstand umfangreicher Sicherheitsmaßnahmen. Ziel der Anlagensicherheit und der Störfallvorsorge ist es, Störungen zu verhindern und die Auswirkungen von Störungen, die dennoch eintreten, für Mensch und Umwelt zu begrenzen.
Anlagen zur Herstellung, Lagerung und Förderung von Erdöl und seinen Folgeprodukten bedürfen in Deutschland einer Genehmigung nach dem Bundes-Immissionsschutzgesetz. Dieses fordert, dass die Anlagen nach dem Stand der Technik errichtet und betrieben werden. Weiterhin sind die anwendbaren technischen Regeln zu befolgen. Die Anforderungen an den Umgang mit wassergefährdenden Stoffen ergeben sich aus dem Wasserhaushaltsgesetz.
Dennoch kann es zu Bränden und Explosionen kommen, wie bei der Raffinerie-Katastrophe in San Juanico, der Raffinerieexplosion in Texas City[6][7] oder der Explosion bei Bayernoil 2018.[8]
Siehe auch
Literatur
- Raimund Fischer: Raffinerien und Petrochemie: Vom schwarzen Gold zum edlen Produkt, in: RWE-DEA-Aktiengesellschaft für Mineralöl und Chemie (Hrsg.):1899-1999 100 Jahre RWE-DEA, Hamburg 1999, S. 133–170, ISBN 3-00-003548-6.
- H. J. Arpe: Industrielle Organische Chemie: Bedeutende Vor- und Zwischenprodukte. 552 Seiten, Verlag Wiley-VCH (2007), ISBN 978-3-527-31540-6
Weblinks
- Weltkarte mit Standorten von Erdölraffinerien und deren CO2-Ausstoß (siehe unter Register CO2-Sources)
- Raffinerie- und Upgradingkapazitäten, weltweit
Einzelnachweise
- Angelika Heinzel, Universität Duisburg-Essen: Energiewandlungstechniken am Beispiel einer Raffinerie (Memento vom 4. März 2016 im Internet Archive), aufgerufen 22. Dezember 2014
- Ignacy Łukasiewicz, Pionier bei der Erforschung der Erdöldestillation
- James G. Speight: The Chemistry and Technology of Petroleum. Marcel Dekker, 1999, ISBN 0-8247-0217-4, S. S. 215–216.
- J. P. Wauquier,J. P. Favennec : Petroleum Refining: Refinery operation and management
- Alkylat
- Katastrophe in Mexiko: Flammenhölle auf Erden. In: einestages. Spiegel Online, abgerufen am 22. November 2011.
- U.S. Chemical Safety and Hazard Investigation Board, Investigation Report, Report No. 2005-04-I-TX, Refinery Explosion and Fire. (PDF; 3,4 MB) Archiviert vom Original am 29. Juli 2013; abgerufen am 4. Juli 2013.
- Zehn Verletzte und grosse Zerstörung nach Explosion in Oberbayern In: srf.ch, 1. September 2018, abgerufen am 1. September 2018.