Katalytisches Reforming
Katalytisches Reforming (von lat. reformare = umgestalten) ist ein Raffinerieprozess, bei dem Alkane und Cycloalkane aus Naphtha (Rohbenzin) verschiedener Herkunft mit dem Ziel der Oktanzahlsteigerung in aromatische Verbindungen und verzweigte Alkane konvertiert werden. Das flüssige Hauptprodukt, das so genannte Reformat, besteht vorwiegend aus Benzol, Toluol, Xylolen, C9- und C10/C11-Aromaten sowie verzweigten und linearen Alkanverbindungen.
Ein wichtiges Nebenprodukt ist Wasserstoff, welcher unter anderem in Entschwefelungs- und Hydrocracking-Prozessen benötigt wird. Durch Cracken werden die gasförmigen Kohlenwasserstoffe Methan, Ethan, Propan und Butan erzeugt.
Geschichte
Der erste katalytische Reforming-Prozess wurde in den 1930er Jahren von der Firma Kellog entwickelt, von denen ab 1939 sieben Anlagen gebaut und betrieben wurden.[1] Das Verfahren verwendete einen molybdänhaltigen Katalysator, der jedoch geringe Selektivität und Standzeit aufwies.
In den 1940er Jahren entwickelte Vladimir Haensel bei Universal Oil Products (UOP) einen stabileren und aktivieren Reforming-Katalysator auf Basis von Platin auf Aluminiumoxid. Schon in den 1940er Jahren wurde der erste kommerzielle Platformer, eine von UOP geschaffene Komposition aus Platin und Reformer, gebaut. Das Verfahren verdrängte auf Grund der höheren Standzeiten des Katalysators das Kellog-Verfahren.
In der Folgezeit wurde der von Haensel entwickelte Katalysator weiterentwickelt. Vor allem der Einsatz von Zinn (Sn) und Rhenium (Re) als Co-Katalysatoren erhöhten die Standzeiten und auch die Aktivität. Der Schwerpunkt der verfahrenstechnischen Weiterentwicklung lag auf dem Gebiet der Katalysatorregenerierung. Der bis Anfang der 1970er Jahre installierte Prozesstyp wird als Semi Regenerative Catalytic Reformer bezeichnet (SRR). Hierbei sind drei Reaktoren mit den jeweiligen Erhitzern hintereinandergeschaltet (siehe Bild 1).
Die heute verbreitete Prozessvariante ist der sogenannte Continuous Catalyst Regenerative Reformer (CCR), bei dem vier Wanderbettreaktoren hintereinander geschaltet werden. Der Katalysator läuft durch alle vier Reaktoren und wird anschließend kontinuierlich regeneriert.
Rohstoffe
Der Feedstock eines Reformers kann aus verschiedenen Quellen stammen. Hauptquelle ist die Rohöldestillation, die sogenanntes „straight-run“-Naphtha liefert, ein unstabilisiertes, das heißt Propan und Butan enthaltendes Kohlenwasserstoffgemisch mit einem Siedebereich von circa 25 bis 135/180 °C. Das Siedeende wird je nach Prozessbedingungen für den Reformer ausgewählt. Weiterhin ist dieses Rohbenzin mit Stickstoff- und Schwefelverbindungen kontaminiert.
Hydrotreating
Schwefel- und Stickstoffverbindungen sind Katalysatorgifte, die entfernt werden müssen. Eine gängige Verfahrensweise ist es daher, das Rohnaphtha direkt über einen Hydrotreater zu entschwefeln beziehungsweise zu entsticken. Der unter den Prozessbedingungen des Reformers gebildete Schwefelwasserstoff (H2S) würde mit den Metallen auf dem Reformer-Katalysator reagieren und dadurch den Katalysator deaktivieren. Ein typisches Reformerfeed erfordert einen Schwefelgehalt von circa 0,5 ppm. Im Reformer gebildetes Ammoniak (NH3) reagiert mit dem Cl− zu Ammoniumchlorid (NH4Cl) und zerstört die saure Funktion. Deshalb müssen Stickstoffverbindungen ebenfalls weitgehend entfernt werden.
Stabilisator
Nach dem Hydrotreater wird das Naphtha stabilisiert, das heißt, das Butan, Propan, Ethan, Methan, der entstandene Schwefelwasserstoff sowie das im Produkt vorhandene Wasser und der restliche Wasserstoff werden in einem Stabilisator abdestilliert. Propan und Butan fallen als noch H2S haltiges Flüssiggas (Liquefied Petroleum Gas, LPG) an. Die leichteren Komponenten werden in das noch unentschwefelte Raffineriegas abgegeben. Wasser sammelt sich in einer Wassertasche des Kopfrefluxbehälters. Auch Wasser ist ein Katalysatorgift, da es das Chlorid auswäscht.
Das Siedeende dieses stabilisierten, entschwefelten Naphthas und damit der Anteil an schweren Reformatkomponenten (C9/C10/C11) wird bereits in der Rohöldestillation festgelegt, sollte aber nicht über etwa 180 °C liegen, da sonst das Siedeende des Reformats wesentlich über 210 °C steigt und damit die Einhaltung der Benzin-Siedeendespezifikation nicht gewährleistet ist. LPG und Leichtbenzin des Rohöls bereits an dieser Stelle zu hydrieren vermeidet die Installation zusätzlicher Entschwefelungsanlagen für LPG beziehungsweise Leichtbenzin.
Reformer-Feed-Vorfraktionierung
Der Siedebeginn des stabilisierten Naphthas muss nach der Stabilisierung durch eine erneute Destillation eingestellt werden, da Pentane (C5) im Naphtha nicht zur Aromaten- und zur Wasserstofferzeugung beitragen. n-Pentan würde zwar zum großen Teil zu i-Pentan isomerisiert, liefert aber nur einen kleinen Beitrag zur Oktanzahlerhöhung. Außerdem führen Pentane zur erhöhten Koksbildung durch Cracken. Aus diesen Gründen werden die Pentane aus dem Reformerfeed entfernt.
Hexane (C6), speziell n-Hexan, Methylcyclopentan und Cyclohexan werden im Reformer vorwiegend zu Benzol umgesetzt (sogenannte benzene precursor). Zusammen mit dem bereits im straight-run-Naphtha vorhandenen Benzol ergäben sich im Reformat Benzolgehalte von ca. 8 Gew.-% bis 12 Gew.%. Raffinerien destillieren normalerweise deshalb auch Hexane ab um Benzolgehalte von circa 2 % bis 4 % zu erreichen. Raffinerien, die eine Benzolextraktion besitzen, verfolgen eine Benzolmaximierungsstrategie. Ungeeignete iso-Hexane werden jedoch auch abdestilliert.
Heptane (C7) erzeugen ausreichend Wasserstoff. Wenn man nicht unbedingt aus blendtechnischen Gründen (Benzin) auf C7-Anteile im Reformat angewiesen ist, vermehrt Xylole produzieren will und genügend Reformerfeed zur Verfügung hat, dann schneidet man auch die Heptane aus dem Reformer-Einsatz.
Man kann damit drei Grundtypen an Reformerfeed unterscheiden:
- Pentan/i-Hexan-reduziertes Naphtha (Benzolproduktion erwünscht, Siedebereich: 70–135/180 °C)
- C6-reduziertes Naphtha (Standardfeed, Siedebereich: 85–135/180 °C)
- C7-reduziertes Naphtha (Xylolproduktion bevorzugt, Siedebereich: 115–135/180 °C).
Das abdestillierte entschwefelte Leichtbenzin kann je nach Qualität als Benzinkomponente oder Steamcrackerfeed verwendet werden.
Andere Naphthaquellen
Neben dem Straight-Run-Naphtha der Rohöldestillation gibt es noch andere Naphthaquellen in der Raffinerie: das non-straight-run-Naphtha. Darunter zählen Hydrocracker-Schwernaphtha, welches gegebenenfalls entschwefelt werden muss, das Coker-Schwernaphtha oder FCC-Schwerbenzin. Diese müssen hydriert werden, um Olefine und Schwefel zu entfernen. Gegebenenfalls wird der Siedebeginn und das Siedeende bereits in den entsprechenden Anlagen eingestellt. Die Hydrierung kann unter Umständen zusammen mit dem straight-run-Naphtha erfolgen.
Die Qualität des Reformerfeeds wird anhand der sogenannten PIONA-Analyse (Paraffine, Isomere, Olefine, Naphthene, Aromaten) bestimmt. Dabei handelt es sich um eine gaschromatographische Bestimmung der Einzelkomponenten in Massenanteil (Gew.-%).[2]
Verfahren
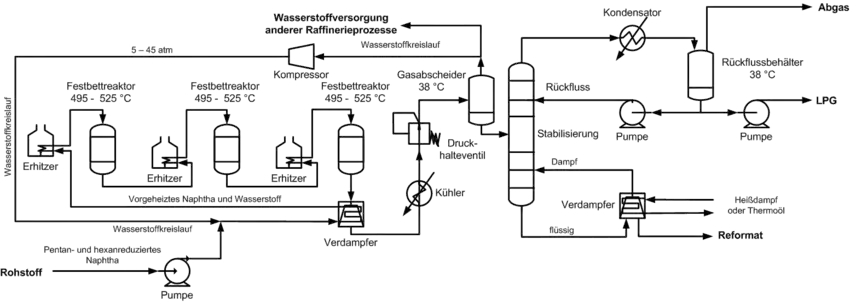
Das Reforming läuft bei Temperaturen von circa 500 °C und je nach Prozesstyp bei Drücken von 30 bar beim semi-regenerativen Verfahren beziehungsweise 3,5 bis etwa 8 bar bei Verfahren mit kontinuierlicher Katalysatorregeneration ab.[3] Eingesetzt werden dabei bifunktionelle Katalysatoren wie Platin-Zinn- oder Platin-Rhenium auf chloriertem Aluminiumoxid oder Zeolithen.
Die ablaufenden Reaktionen sind endotherm. Die Reaktoraustrittstemperatur kann dadurch um 100 K absinken. Deshalb werden mehrere Reaktoren mit Zwischenerhitzer, meist in Form gasbefeuerter Öfen, installiert, um den Temperaturverlust auszugleichen und einen ausreichenden Umsetzungsgrad zu erzielen.
Durch Dehydrierungs- und Polymerisierungsreaktionen entsteht auf dem Katalysator Koks, der durch physikalische Blockade der aktiven Zentren die Aktivität des Katalysators beeinträchtigt. Der Koks wird beim semi-regenerativen Verfahren in Intervallen von 6 bis 24 Monaten abgebrannt, dabei verbleibt der Katalysator im Reaktor. Anschließend erfolgt eine so genannte Oxychlorierung, bei der die saure Funktionalität wiederhergestellt wird. Der Reaktordruck eines semi-regenerativen Reformers liegt bei ungefähr 30 bar. Die Ausbeuten sind schlechter als die eines kontinuierlichen regenerativen Reformers, da der hohe Wasserstoffpartialdruck zur Re-Hydrierung der Aromaten führt.
Beim Verfahren mit kontinuierlicher Regeneration erfolgt auf Grund der niedrigeren Wasserstoffpartialdrücke die Koksbildung wesentlich schneller. Zur Regeneration wird der koksbeladene Katalysator am Boden des letzten Reaktors ausgeschleust und über ein Gas-Liftsystem zum Kopf eines sogenannten Regenerators vom Typ Wanderbettreaktor transportiert. Dort wird dem Katalysator in verschiedenen Zonen erst der Koks schonend abgebrannt und anschließend wird er oxychloriert. Dann erfolgt der Rücktransport durch ein Gas-Liftsystem vom Boden des Regenerators zum Kopf des ersten Reaktors.
Beim UOP-System sind die vier Reaktoren übereinander gestapelt (stacked). Hierdurch läuft der Katalysator allein durch die Schwerkraft vom Kopf des ersten Reaktors zum Boden des vierten Reaktors, Axens verwendet eine horizontale Aufstellung, ähnlich wie beim semi-regenerativen Verfahren. Der Katalysator wird zwischen den Reaktoren durch ein Liftsystem vom Boden des jeweiligen Reaktors zum Kopf des nächsten transportiert.
Ein niedriger Wasserstoffpartialdruck erhöht die Koksbildung, verbessert jedoch Ausbeute und Qualität des Reformats durch verstärkte Dehydrierungsreaktionen mit vermehrter Wasserstoff-Erzeugung und höhere Aromatenausbeute. Die Qualität des Wasserstoffgases verbessert sich ebenfalls, da es weniger Crackprodukte wie Methan oder Ethan enthält. Zur Aufrechterhaltung der Säurefunktion werden kleine Mengen eines chlorierten Kohlenwasserstoffs in den Einsatz dosiert, die unter den herrschenden Prozessbedingungen sofort zu HCl und dem entsprechenden Kohlenwasserstoff hydriert werden. Chloridverluste, hervorgerufen etwa durch Stickstoff- und Wassereintrag werden hierdurch kompensiert.
Die typischen Apparate eines katalytischen Reformers sind
- Einsatzstoffpumpe
- Zuspeisung der Kreislaufgases
- Wärmetauscher (gegen Reaktoraustritt des letzten Reaktors), ein sogenannter Feed-Effluent-Heat-Exchanger.
- Ofen/Reaktorkombination (3- bis 4-mal), dann wieder Wärmetauscher
- Produktkühler
- Hochdruckseparator (SRR), über Kopf Recycle- und Wasserstoffgas
- Wasserstoffreiches Gas wird nach nochmaliger Reinigung ins Wasserstoffnetz der Raffinerie gespeist
- Recyclegas wird mit dem Kreislaufgaskompressor zurück zum Einsatz befördert
- unstabilisiertes Reformat läuft zum Stabilisator (Druckdestillation bei ~ 8–15 bar)
- Stabilisatorkolonne, über Kopf LPG und Raffineriegas, im Sumpf "stabilisiertes" Reformat.
Produkte
Als Produkte des katalytischen Reformers lassen sich folgende Komponenten unterscheiden
- wasserstoffreiches Gas (je nach Prozessvariante:20 Gew-% bis 45 Gew.-% H2 im Gas, der Rest ist Methan, Ethan, eventuell Propan und geringe Mengen an Butan)
- Raffineriegas (schwefelfrei)
- LPG (schwefelfrei)
- Reformat: je nach Prozessführung: Siedebereich ~25–155/210 °C, d. h. C5-C11 Verbindungen der Typen: n- und i-Alkane, Aromaten[C6+ !], etwa 0,1 % bis 0,2 % Olefine, etwa 1 % bis 2 % Cycloalkane.
Im Reformerprozess entstehen durch Cracken und Dealkylierung auch Stoffgruppen, die ursprünglich im Reformerfeed gar nicht oder in nur sehr untergeordnetem Maße enthalten waren. Selbst wenn das Feed nur aus C8-Verbindungen besteht, weist das Reformat einen nicht unbeträchtlichen Anteil an n- und i-Pentan auf, weiterhin Benzol und Toluol, sowie Hexane und Heptane.
Reformat-Fraktionierung
Das direkte Blenden von „full-range-Reformat“ ins Motorenbenzin ist in Europa nicht üblich, da bereits ein Gehalt von 2 % bis 4 % Benzol im Reformat schnell zum Überschreiten der Benzolspezifikation führt. Das Reformat wird meist destillativ aufgearbeitet, um das Benzol zu entfernen. Eine sinnvolle Lösung ist ein sogenannter 3-Cut-Splitter (Destillationskolonne mit Kopf- und Sumpfprodukt, sowie einem Seitenabzug). Über Kopf wird, ähnlich wie bei der Reformerfeed-Destillation, ein Schnitt mit Pentan- und i-Hexanverbindungen sowie geringen Mengen Benzol (ca. 1 Vol.-% bis 1,5 Vol.-% im Produkt) abdestilliert, so genanntes Leichtreformat, das in Motorenbenzin oder im Steamcracker verwendet wird.
Im Seitenabzug wird ein sogenannter Heartcut (Herzschnitt) abgezogen, der die Hauptmenge an Benzol, sowie Hexane und leichtere C7-Alkane enthält. Der heartcut wird verkauft. Das Sumpfprodukt (C7-C11) enthält ebenfalls nur noch wenig Benzol und kann direkt als Benzinkomponente verwendet werden. Einige Raffinerien bereiten das Sumpfprodukt weiter auf und destillieren C7- (Toluol und C7-Nichtaromaten), C8- (Xylole, sehr wenige C8-Nichtaromaten) und C9/C10/C11-Verbindungen (fast ausschließlich Aromaten) auseinander. C7 und C9/C10/C11 laufen ins Motorenbenzin, das Xylolgemisch wird verkauft bzw. einer Xyloltrennung (z. B. PAREX) zugeführt.
Mechanismus
An den Metallzentren des Katalysators laufen bevorzugt die Hydrierungs-/Dehydrierungsreaktionen ab, während die Säurezentren Isomerisierungs- und Ringschlussreaktionen katalysieren. Eine unerwünschte Nebenreaktion ist das Cracken von Alkanen in niedrigkettige Produkte, sowie Dealkylierungsreaktionen.
Typische Reaktionen beim Reforming sind[4]
- Cyclisierung
- Cyclisierung von n-Heptan zu Methylcyclohexan bzw. 1,2-Dimethylcyclopentan (reagiert weiter, siehe Isomerisierung)
- Dehydrierung
- auch als Folgereaktion der Cyclisierung,
- hier Dehydrierung von Methylcyclohexan zu Toluol (auch Dehydrocyclisierung genannt)
- Isomerisierung
- Isomerisierung von n- in iso-Alkane, z. B. n-Octan in 2,5-Methylhexan
- Isomerisierung von 1,2-Dimethylcyclopentan in Methylcyclohexan
- Cracken
- Cracken von Alkanen, z. B. n-Octan in n-Butan und n-Buten. Die Doppelbindung wird anschließend sofort hydriert
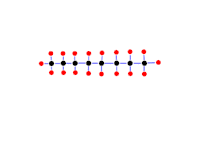
- Dealkylierung
- Dealkylierung von Aromaten, beispielsweise Toluol in Benzol und Methan
Verfahrensvarianten
AROMAX
Aromax[5] ist ein spezieller Reformer zur Verarbeitung eines C6/C7-Naphthaschnittes. Durch hohe Konversionsraten von C6- und C7-Alkanen werden hohe Ausbeuten an Benzol und Toluol erzielt, die H2 Erzeugungsrate ist ebenfalls exzellent.[6]
Fully-Regenerative-Reformer
Funktioniert wie ein SRR, es steht jedoch ein vierter, sogenannter Swing-Reaktor zur Verfügung, der zyklisch die Funktion eines anderen übernimmt, wenn dieser off-line regeneriert wird. Hierdurch muss dieser sogenannte Powerformer (Exxon-Bezeichnung) nicht alle sechs bis 24 Monate abgefahren werden, sondern kann fünf Jahre ohne Zwischenstopp betrieben werden. Diese Prozessführung erfordert jedoch ein kompliziertes System aus Motorschiebern mit entsprechender Schaltlogik.
Ausblick
Die Reduzierung des Aromatengehaltes im Benzin ab 2005 durch das Europäische Auto/Öl-Programm (Auto Oil 2, kurz AOP II) von 42 Vol.-% auf 35 Vol.-% stellte schon in der Vergangenheit eine Herausforderung für das Betreiben eines Reformers dar. Ein Verfahren, das ein Produkt mit einem Aromatengehalt von ca. 65 % erzeugt passt nicht mehr ins Anlagen-Portfolio.
Andererseits ist die Wasserstoffproduktion für viele Raffinerien unverzichtbar. Viele Produzenten haben dann „negative“-Reformer-Margen in Kauf genommen, mehr Benzin erzeugt und die Überschüsse nach Übersee (USA) exportiert. Mit sinkendem Benzinbedarf in Europa und den USA steht dieses „Schlupfloch“ jedoch nicht mehr zur Verfügung. Gleichzeitig steigt der Wasserstoffbedarf weiter an, beispielsweise durch Reduzierung des Schwefelgehaltes im Heizöl EL von 1000 auf 50 ppm.
Die Produzenten reagierten/reagieren mit 3 Strategien
- Installation einer teuren Wasserstofferzeugung (Dampfreformierung), Abstellen des Reformers bzw. Durchsatzreduktion, Verkauf des Naphthas (Steamcrackerfeed).
- Entfernung der Aromaten aus dem Benzin-Pool,
- durch den Verkauf von Rein-Toluol oder Xylol,
- Erzeugung von Benzol und Xylolen aus Toluol (Transalkylierung)
- Stilllegung ganzer Raffinerien, speziell FCC-Raffinerien, die viel Benzin herstellen.
Literatur
- Manfred Baerns, Arno Behr, Axel Brehm: Technische Chemie. 757 Seiten, Wiley-VCH, 2006, ISBN 3-527-31000-2.
- George J. Antos, Abdullah M. Aitani: Catalytic Naphtha Reforming, Marcel Dekker Inc., 2004, ISBN 0-8247-5058-6
Einzelnachweise
- History of Reforming; doi:10.1021/ie51396a028
- Lourdes Ramos: Comprehensive two dimensional gas chromatography. Elsevier, 2009, ISBN 0-08-093269-X, S. 164 (eingeschränkte Vorschau in der Google-Buchsuche).
- Reformer Druck.
- UOP CCR Platforming™ Process. (Nicht mehr online verfügbar.) Archiviert vom Original am 5. Juli 2013; abgerufen am 27. Juni 2013. Info: Der Archivlink wurde automatisch eingesetzt und noch nicht geprüft. Bitte prüfe Original- und Archivlink gemäß Anleitung und entferne dann diesen Hinweis.
- Chevron AROMAX.
- AROMAX-Prozess.