Gießprozess-Simulation
Unter Gießprozess-Simulation versteht man die „Modellierung“, also das Abbilden von Gießprozessen in einer Simulations-Software. Dabei wird der Prozessablauf des Gießens und Erstarrens durch die Software möglichst detailgetreu als Randbedingung für die Berechnung vorgegeben. Als Ergebnis erhält man die Darstellung über den Ablauf der Formfüllung, der Erstarrung, der Gefüge- und Eigenschaftsbildung sowie der Bildung von Eigenspannungen und Verzug der Gussteile. „Aus einem Guss“ heißt für die Modellierung die Berücksichtigung von zahlreichen, sich gegenseitig beeinflussenden technischen, physikalischen und chemischen Einflussgrößen.
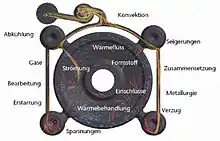
Grundlagen der Gießprozess-Simulation
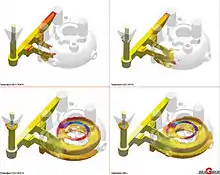
Die Grundlage für die Gießprozess-Simulation liefern die bekannten Gleichungen zur Beschreibung der Dynamik von Strömungen, Temperaturfluss, Spannungsentwicklung und anderer zu berücksichtigenden mechanischen, chemischen und thermischen Vorgänge. Der spezifische Gießprozess wird durch die Randbedingungen modelliert, unter denen die Software die Gleichungen löst.
Die Ergebnisse der Simulationsrechnungen können am Bildschirm, ausgedruckt als Farbgrafik oder in dreidimensionalen Räumen (holografisch) dargestellt werden. Sie stellen eine qualitative und quantitative, leicht zu erfassende Dokumentation der Phänomene des Gießprozesses dar. Sie illustrieren den Ablauf der Formfüllung und der Erstarrung. Berechnete Qualitätskriterien zeigen potenzielle Fehler auf und ermöglichen die Vorhersage von zu erwartenden Gussteil-Gefügen und -Eigenschaften. Die Bildung von Eigenspannungen und Verzug im Gussteil kann ebenfalls vorhergesagt werden. Dynamische Prozesse wie das Einströmen der Schmelze in den Formhohlraum können als Animationen visualisiert werden.
Genutzt werden können diese Ergebnisse über den gesamten Lebenszyklus eines Gussteils hinweg. Simulation unterstützt gleichzeitig die spezifikations- und gussgerechte Konstruktion eines Gussteils, den Werkzeugbau, die Auslegung einer stabilen, wirtschaftlichen Fertigung bis zur Qualitätssicherung und der optimierenden Weiterentwicklung eines Gussteils. Die Gießprozess-Simulation gestattet zu jeder Zeit einen Blick in die Zukunft des nächsten Prozessschritts. Vor der Entwicklung der Gießprozess-Simulation war dies nur auf der Basis von Erfahrung und durch „Versuch und Irrtum“ möglich – was bei kürzeren Entwicklungszeiten, den stetig steigenden Qualitätsanforderungen und dem Zwang zu kostengünstiger Fertigung nicht mehr zu befriedigenden Ergebnissen führt.
Ziele der Gießprozess-Simulation
Mit der Simulation von Gießprozessen werden die folgenden Aufgabenstellungen unterstützt:
Die Prüfung und Verbesserung des Gussteildesigns in Richtung stabiler, robuster Gießprozesse (gießgerechte Konstruktionen) sowie die Beurteilung von Fehlerrisiken beim Gießen (Vermeidung von Gussfehlern). Hier geht es um Phänomene der Formfüllung wie Turbulenzen bzw. Verwirbelungen, Formerosion, Oxidbildung sowie Phänomene der Erstarrung wie Lunker-, Gefüge- und Eigenspannungsbildung.
Ebenso geht es um die Beurteilung und Minimierung von Gussteilverzug, der in großem Maße von den Wandstärkenverteilungen im Gussteil – also vom Design abhängt (Maßhaltigkeit) und um die Optimierung von Gieß- und Wärmebehandlungsprozessen (Wirtschaftlichkeit). Ein weiteres Ziel ist die Auslegung von Gießtechnik mit minimalem Rohstoff- und Energieeinsatz (Energie- und Materialeffizienz) sowie die Schaffung von Informationen, Ergänzung von Erfahrungen (Wissensmanagement).
Stationen eines Simulationsprojekts
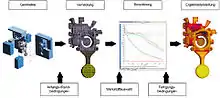
Simulationsprojekte bestehen grundsätzlich aus fünf Schritten: 3D-Geometrie-Modellierung, Vernetzung, Festlegung der Prozess-Parameter, Berechnung und Ergebnisauswertung.
Ausgangspunkt der Simulation ist ein 3D-CAD-Modell des zu simulierenden Teils und des in die Betrachtung einbezogenen Gießsystems (Angusssystem, Form etc.). In der Automobilindustrie liegen digitale 3D-CAD-Modelle der Gussteile in der Regel vor. In anderen Branchen müssen sie häufig noch auf der Basis von Konstruktionszeichnungen angefertigt werden.
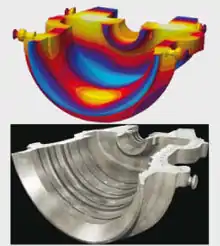
Die Vernetzung teilt die zu betrachtende Geometrie für die mathematische Behandlung in infinitesimale (Volumen-)Segmente. Bei der Berechnung nach der Finite-Volumen-Methode geschieht die Vernetzung vollautomatisch. Kommt die Finite-Elemente-Methode zur Anwendung, wird ebenfalls automatisch vernetzt, jedoch bleibt eine Bearbeitung von Hand notwendig. Mit der Festlegung der Prozess-Parameter (Gießleistung, Schusskurve, Legierung und Gießtemperatur, Temperiermedium, Formtemperatur etc.) komplettiert der Nutzer die notwendigen Voraussetzungen, um die Berechnung zu starten. Heute sind die PC-Plattformen so leistungsfähig geworden, dass Simulationsberechnungen für ein Projekt mehrmals täglich durchgeführt werden können. Mehrkernprozessoren ermöglichen auch bei größeren, komplexen Verhältnissen kurze Berechnungszeiten.
Um die Ergebnisse auszuwerten, werden Berechnungsresultate als farbcodierte Grafiken oder Filme ausgegeben, die etwa das Füllen der Gießform und die Erstarrung der Schmelze dynamisch darstellen. Je nachdem, welche entstehenden Eigenschaften betrachtet werden sollen, beispielsweise die Bildung von Eigenspannungen oder Porositäten, werden ihnen verschiedene Farbtöne zugeordnet, die der Anwender interpretieren kann.
Die Gesamtdauer eines Simulationsprojekts variiert mit der Komplexität und der Ganzheitlichkeit des zu betrachtenden Modells. So kann z. B. eine thermische Analyse eines Gießprozesses in einem Zeitraum von Minuten, in aller Regel weniger als einer Stunde, durchgeführt werden – vom Vorliegen des 3D-CAD-Modells des Gussteils bis zum ausgewerteten, dokumentierten Ergebnis. Für die Berechnung des Formfüllens, der Erstarrung und der Eigenspannungsbildung über mehrere Zyklen hinweg benötigt man natürlich länger.
Informationen aus der Gießprozess-Simulation
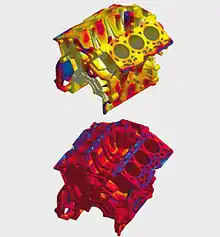
Konkret zeigt die Simulation die folgenden Informationen über den Gießprozess auf: Formfüllung des Gussteils, Verlauf und Temperaturen der Schmelzströmung, zuletzt gefüllte Bereiche, Entlüftung der Form, Ansammlung von Trennmittelrückständen (nur bei Druckguss), Totgebiete im Fließlauf, Verwirbelungen der Schmelze, Desintegration der Schmelze, Aufeinandertreffen von Schmelzfronten, Kaltschweißstellen und Fließfiguren.
Gussteilerstarrung:
- Lunker und Poren
- Warmrisse
- Gefügeausbildung
- Nachspeisungsverhalten
- Bildung von Eigenspannungen und resultierendem Verzug
Informationen über das Werkzeug:
- Unterstützung der vollständigen Formfüllung
- Zykluszeiten
- Kernverschleiß
- Klebeneigung
- Wärmeverlust beim Sprühen
- Lebensdauer der Form
Simulation der Prozesskette
Gussteile erhalten ihre letztendlichen Eigenschaften häufig aus nachgelagerten Prozessschritten, wie z. B. aus der Wärmebehandlung oder durch Bearbeitung. Daher ist es für die Gießprozess-Simulation unverzichtbar, sich auch mit diesen Prozessschritten zu beschäftigen, um so aussagefähig bezüglich der tatsächlichen Eigenschaften eines Gussteils im Lieferzustand zu werden.
Nachgelagerte Prozessschritte verändern aber auch die Eigenschaften des Gefüges und des Gussteils. So kann heute mit Hilfe der Wärmebehandlungssimulation durch Kopplung von Diffusionsrechnungen und Phasenumwandlungen bei der Abkühlung Gefüge und Eigenschaften nach der Wärmebehandlung vorhergesagt werden. Dies hilft dem Stahlgießer, mögliche Durchhärtungsprobleme frühzeitig zu erkennen oder dem Aluminiumgießer, die Parameter für eine optimale Auslagerung bezüglich Festigkeit oder Dehnung festzulegen.
Integration der Simulation in Gussteil-Lebenszyklus und Gießerei-Prozesse
Je tiefer und umfassender die Simulation in den Lebenszyklus eines Gussteils integriert ist, desto höher ist ihr technischer und damit auch ihr wirtschaftlicher Nutzen. Da der Lebenszyklus in der Regel unternehmensübergreifend ist, sollte die Gießprozess-Simulation nicht nur in die Prozesse der Gießereien, sondern auch in die der Gussteil-Konstruktion und beim Gussteil-Abnehmer integriert werden.
In der Design- und Konstruktionsphase hilft die Gießprozess-Simulation, Teile zu entwickeln, die den Spezifikationen der Abnehmer genügen und gleichzeitig gussgerecht ausgelegt sind. Potenzielle Probleme beim Gießen lassen sich so bereits früh erkennen und konstruktiv eliminieren. Dies reduziert und verkürzt Überarbeitungsschleifen und beschleunigt damit die Entwicklungsprojekte.
Nach der Konstruktionsphase ermöglicht die Simulation das Aufsetzen eines stabilen und wirtschaftlichen Gießprozesses. Der Werkzeugbau erhält durch die Simulationsergebnisse fundierte Informationen für die Anfertigung der Formen, die Fertigung erhält verlässliche Parameter, um Füllkurven, Gießlöffelsteuerung, Zykluszeiten etc. so einzustellen, dass sie zuverlässig ein spezifikationsgerechtes Gussteil liefern. Bevor die Simulationsmethode zur Verfügung stand, mussten sich Gießereien in dieser Phase auf das individuelle Wissen des Gießers und die Versuch-und-Irrtum-Ergebnisse aus zahlreichen, teuren Probeabgüssen verlassen. Jetzt steckt dieses Wissen in der Software und die theoretisch beliebig oft zu wiederholende Berechnung ersetzt den realen Probeguss.
Die Qualitätssicherung profitiert bereits ohne eigenen Einsatz von Simulationswerkzeugen insofern, dass durch die simulationunterstützte Konstruktion und Fertigung die Produktion fehlerhafter Teile minimiert wird und durch die Simulation alle relevanten Prozessschritte in der Software dokumentiert sind. Die Dokumentation für Qualitätsaudits von Kunden oder Zertifizierungsstellen ist damit quasi automatisch erstellt. Der direkte Einsatz der Gießprozess-Simulation empfiehlt sich für die kontinuierliche Qualitätssicherung. Sie erlaubt z. B. die einfache Überprüfung, ob sich die Belastbarkeit eines Gussteiles durch die Änderung eines Prozessparameters steigern lässt.
Gießprozess-Simulation als Kommunikationswerkzeug
Neben dem direkten Einfluss, den die Gießprozess-Simulation auf die Entwicklungs- und Fertigungsprozesse von Gussteilen hat, spielt sie auch eine verbindende Rolle in den fach- und unternehmensübergreifenden Prozessen: Sie dient als verbindliche „Sprache“, über die sich alle beteiligen Personen verständigen können. Über objektive Ergebnisse einer Simulation können etwa Konstruktion und Fertigung fundiert diskutieren und entscheiden, ob Gussteil oder Gießsystem modifiziert werden müssen oder direkt in die Fertigung gehen können. Ohne das Simulationsergebnis fehlt diese Verständigungsbasis. Der Gießer kann allenfalls, und für den Konstrukteur nicht überprüfbar, auf der Basis seines Wissens und seiner Erfahrung die Gussgerechtigkeit eines Teils beurteilen. Ob er recht hat oder nicht, erweist sich erst, wenn überhaupt, nach den ersten gefertigten Gussteilen.
Kopplung von Gießprozess-Simulation und autonomen Optimierungsverfahren
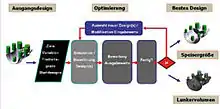
Gießprozesse konnten bis zur Entwicklung der Gießprozess-Optimierung nur durch ein mehrmaliges Durchlaufen der Schrittsequenz „Versuch, Prüfung und Modifikation“ optimiert werden, um die Qualität der Gussteile oder die Wirtschaftlichkeit der Fertigung zu verbessern. Bei „physischen“ Versuchen mit realen Modellen, Formen und Guss-Prototypen basieren die optimierenden Modifikationen von Fertigungsparametern und Gießsystem-Design ausschließlich auf der Interpretation der Prüfungsergebnisse durch den Gießer. Das Gießsystem bleibt eine „Black Box“, die Füll- und Erstarrungsprozesse in ihrem Inneren unsichtbar und nur durch Rückschlüsse vom Gießergebnis aus analysierbar.
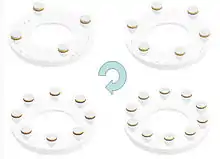
Die Gießprozess-Simulation verlagert die Optimierungsschritte in eine Software, die die Füll- und Erstarrungsprozesse sicht-, analysier- und messbar macht (und gleichzeitig die mit den physischen Versuchen verbundenen Kosten eliminiert). Die optimierenden Modifikationen basieren damit nicht mehr nur auf den Erfahrungen eines Gießers, sondern auf reproduzierbaren, belastbaren Daten und allgemein gültigen physikalisch-technischen Prinzipien.
Der Fortschritt in der Rechnertechnik und der Software-Entwicklung gestattet es heute, noch einen Schritt weiter zu gehen und Simulationsmethoden mit Optimierungsverfahren zu koppeln, um die Optimierung zu automatisieren. Statt physisch oder virtuell Versuch auf Versuch folgen zu lassen, berechnet eine autonom optimierende Software nach der Definition der Optimierungsziele und der Variationsbandbreiten für die Modifikationen so lange verschiedene Szenarien mit variierenden Prozessparametern und Formenlayouts, bis die ideale Parameter-Gießsystem-Kombination für die Verwirklichung der Optimierungsziele gefunden ist. Die Parameter-Variationen können z. B. Fertigungsgrößen wie Gießbedingungen, Werkstoffe, Formtemperierung, Schusskurven oder Sprühbedingungen betreffen. Um ideale Formenlayouts zu ermitteln, werden in den Simulationen Gießlaufdesign, Anschnitt- und Speiserdimensionierung oder Kühlkanalpositionierung modifiziert. Auch generelle Fertigungsrestriktionen lassen sich dabei berücksichtigen.
Die autonome Optimierung kann auf verschiedene, auch miteinander in Konflikt stehende Kriterien zielen, etwa auf die Verbesserung von Qualitätseigenschaften auf der einen und die Reduzierung des Materialverbrauchs auf der anderen Seite. Als Ergebnis liefert der Optimierungsalgorithmus dann die Parameter-Gießsystem-Kombination, die den besten Kompromiss beider Ziele liefert.
Die Geschichte der Gießprozess-Simulation
Die Gießsimulation etablierte sich als die wichtigste Innovation der Gießerei-Branche in der Zeit von 1960 bis 2010. Sie hat die Entwicklung und Produktion von Gussteilen revolutioniert und auf eine ganz neue Grundlage gestellt.
Bereits in den 1950er Jahren nutzte V. Paschkis analoge Computer, um die Bewegung der Erstarrungsfront in einer und zwei Dimensionen (1D und 2D) vorherzusagen. 1962 war K. Fursund der Erste, der digitale Computer nutzte, um gießrelevante Probleme zu lösen (Penetration von Stahl in die Sandform). 1965 veröffentlichten Hentzel und Keverian ihre bahnbrechende Arbeit zur zweidimensionalen Simulation der Erstarrung in Stahlgussteilen. Sie nutzten dabei ein bei General Electric entwickeltes Programm zur Simulation des Wärmetransports. Ole Vestby programmierte 1968 ein 2D-Modell, um Temperaturverteilungen beim Schweißen zu untersuchen. Er nutzte hierzu erstmals die Finite-Differenz-Methode. Um 1970 nutzte Viktor de Lange Davies, Ole Vestbys 2D-Programm, um Speisungslängen in plattenförmigen Gussteilen zu simulieren. 1975 wurde Preben N. Hansen mit einer Arbeit zur Simulation des Warmrissverhaltens in Stahlgussteilen promoviert. In dieser Arbeit wurde auch erstmals ein 3D-Modell programmiert. Mit Beginn der 1980er Jahre nahmen die Forschungsarbeiten rund um das Thema „Gießprozess-Simulation“ an vielen Stellen substanziell zu. Neben den Aktivitäten an der Technischen Hochschule Dänemark rund um Preben N. Hansen gab es Arbeitsgruppen in Amerika (Berry und Pelke), Japan (Niyama) und Lausanne (Kurz) sowie Grenoble (Durand) und insbesondere in Aachen am dortigen Gießerei-Institut mit der Arbeitsgruppe von Peter R. Sahm.
Wichtige Meilensteine waren die Einführung des Begriffs „Kriteriumsfunktion“ von Hansen und Berry 1980, die Einführung eines Kriteriums zur Mittellinienlunkerung von Stahlgussteilen durch Niyama 1982 sowie die Vorstellung einer Kriteriumsfunktion zur Warmrissneigung in Stahlgussteilen durch E. Flender und P. N. Hansen 1984. Ende der 1980er Jahre wurden erste Software-Lösungen zur Simulation der Formfüllung vorgestellt.
In den 1990er Jahren fokussierten sich die Entwicklungen auf die Spannungssimulation in Gussteilen (Hattel und Hansen, 1990) sowie erste Schritte zur Vorhersage von Gefügen und Eigenschaften insbesondere durch Ingvar Svensson und Magnus Wessén in Schweden.[1]
Literatur
- J. C. Sturm, E. Flender: 30 Jahre Gießtechnische Simulation. In: Giesserei. 96, Nr. 5, 2009, S. 94–109.
- C. Rogers: A Virtual Tool for the Manufacture and Use of Foundry Cores and Molds. MCWASP 2006 (Opio)
- J. Hattel (Hrsg.): Fundamentals of Numerical Modelling of Casting Processes. Polyteknisk Forlag, Lyngby 2005, ISBN 87-502-0969-8.
- V. Kokot, P. Bernbeck: Integration and application of optimization algorithms with casting process simulation. In: Modeling of Casting, Welding and Advanced Solidification Processes X. Destin, Florida, 25.–30. Mai 2003 (Konferenzbeitrag).
- P. R. Sahm, P. N. Hansen: Towards Integrated Modeling for “Intelligent Castings”. In: Peter R. Sahm (Hrsg.): Modeling of Casting, Welding and Advanced Solidification Processes. Bd. IX, Shaker, Aachen 2000, ISBN 3-8265-7230-0, S. LXXXI–XCIII.
- P. R. Sahm, P. N. Hansen: Numerical Simulation and Modelling of Casting and Solidification Processes for Foundry and Cast-House. CIATF 1984.
- S. Findeisen: Untersuchungen zum Wärmetransport bei der Erstarrung. VDM Verlag Dr. Müller 2010, ISBN 978-3-639-29263-3.