Gießbarkeit
Gießbarkeit ist die Eignung eines Metalles oder einer Legierung sich durch Gießen verarbeiten zu lassen. Die Gießbarkeit setzt sich aus einer Reihe von sogenannten Gießeigenschaften zusammen, die auf den Gießvorgang oder die Qualität des Gussstückes Einfluss haben. Dazu zählt das Fließ- und Formfüllungsvermögen, das Speisungsvermögen, die Schwindung und Schrumpfung, die Warmrissneigung, die Gasaufnahme, die Penetration und Seigerungen.[1][2][3]
Bei der Gießbarkeit handelt es sich somit um einen Sammelbegriff für verschiedene Werkstoffeigenschaften, die beim Gießen eine Rolle spielen.[3] Sie können jedoch vom eingesetzten Gussverfahren abhängen. Sandgusslegierungen eignen sich beispielsweise nur wenig für den Druckguss.[4] Analog zur Gießbarkeit versteht man unter der Zerspanbarkeit, Umformbarkeit und Schweißeignung die Eignung eines Werkstoffes für das Zerspanen, Umformen oder Schweißen.
Fließvermögen
Das Fließvermögen gibt an, wie weit die Schmelze in die Gussform fließen kann, bevor sie erstarrt. Zu ihrer Messung nutzt man meist waagrechte Rinnen, die spiralförmig aufgerollt sind. Ein gutes Fließvermögen ist vor allem bei dünnwandigen Bauteilen wichtig, um eine vollständige Formfüllung zu gewährleisten und Ausschuss zu vermeiden. Die Schmelze, die sich in der Gießspirale oder der Gussform befindet, erkaltet langsam. Kommt es zu einer glattwandigen, rauwandigen oder schalenbildenden Erstarrung, so verringert dies den Querschnitt, der der Schmelze zum Fließen zur Verfügung steht und die Fließgeschwindigkeit verringert sich, bis sie bei Erreichen der Solidustemperatur erliegt. Bei einer brei- oder schwammartigen Erstarrung steigt dagegen nach Erreichen der Liquidustemperatur die Viskosität der Schmelze sehr stark, sodass der Materialfluss auch vor Erreichen der Solidustemperatur stocken kann. Typische Gussfehler bei zu geringem Fließvermögen sind Kaltschweißstellen und nicht gefüllte Bereiche.
Einen wichtigen Einfluss auf das Fließvermögen hat der Wärmehaushalt. Es ist meist besser, je höher die Temperatur der Schmelze ist. Alternativ ist es auch möglich, Kokillen oder Formen aus einem Werkstoff zu verwenden, der schlecht die Temperatur leitet. Aus diesem Grund ist das Fließvermögen in einer Sandform besser als in einer gut wärmeleitenden Graphitform. Die übereutektischen Aluminium-Silicium-Legierungen mit einem Si-Anteil um 20 % bilden bei der Erstarrung Wärme, die das Fließvermögen verbessert. Auch die Erhöhung der Gießgeschwindigkeit verbessert das Fließvermögen. Eine niedrige Oberflächenspannung oder Viskosität wirkt sich positiv auf das Fließvermögen aus. Beide können über die Temperatur und die Zusammensetzung der Schmelze beeinflusst werden. Oxidschichten auf der Schmelzenoberfläche verschlechtern das Fließvermögen.
Das Fließvermögen reiner Metalle ist meist sehr gut, da sie glattwandig erstarren. Mit steigendem Anteil der Legierungselemente sinkt sie, da es zu einer rauwandigen oder schwammartigen Erstarrung kommt. Im Eutektikum ist es dagegen wieder sehr gut wegen der schalenbildenden Erstarrung.[5]
Formfüllungsvermögen
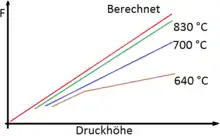
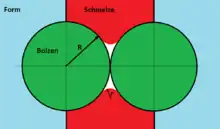
Das Formfüllungsvermögen beschreibt, wie gut die Geometrie der Form auf das Gussstück übertragen wird. Vor allem Ecken und Kanten sind hier von Interesse. Sie hängt bei der ausschließlich flüssigen Schmelze ab von der Oberflächenspannung, dem in der Schmelze herrschenden metallostatischen Druck und der Dichte der Schmelze. Eine teilweise erstarrte Schmelze hat ein schlechteres Formfüllungsvermögen. Bei zu niedrigem Formfüllungsvermögen sind scharfe Konturen der Form im Gussstück nur abgerundet abgebildet. Das Formfüllungsvermögen kann erhöht werden durch eine Erhöhung der Gießtemperatur, erwärmte Formen, Wärmeisolierung der Formen, um die Schmelze bis zum Ende der Formfüllung flüssig zu halten und eine Erhöhung des Druckes entweder durch eine höhere Druckhöhe beim Schwerkraftgießen oder einen höheren Kolbendruck beim Druckguss. Die Oberflächenspannung nimmt meist mit steigender Temperatur ab, was sich günstig auf das Formfüllungsvermögen auswirkt – Ausnahmen sind Kupfer und Gusseisen. Weitere Möglichkeiten sind die Zugabe von Elementen, die die Oberflächenspannung senken oder die Erstarrungsmorphologie beeinflussen. Oxidationen haben negativen Einfluss auf das Formfüllungsvermögen.
Falls eine ausschließlich flüssige Schmelze vorliegt, kann ihr Formfüllungsvermögen berechnet werden aus der Dichte der Schmelze , der metallostatischen Druckhöhe , der Oberflächenspannung , und der Erdbeschleunigung .
In der Praxis weicht das reale Formfüllungsvermögen vom errechneten theoretischen ab. Je höher die Schmelzentemperatur ist und je niedriger die Druckhöhe ist, desto besser stimmen die Ergebnisse überein. Bei höheren Schmelzentemperaturen ist die Wahrscheinlichkeit höher, dass sie auch tatsächlich ausschließlich flüssig vorliegt, was auch die Abweichungen erklären kann. Die Temperatur hat somit nur unterhalb einer bestimmten Übergangstemperatur einen Einfluss. Ab dieser Übergangstemperatur liegt die Schmelze während des gesamten Formfüllungsvorgangs als Flüssigkeit vor. Die Formel zur Berechnung zeigt jedoch die prinzipiellen Einflussmöglichkeiten auf: Das Formfüllungsvermögen ist umso besser, je höher die Dichte und die Druckhöhe ist und je niedriger die Oberflächenspannung ist. Letztere kann über die Zusammensetzung der Schmelze verringert werden und meist durch eine Erhöhung der Temperatur. Eine Temperaturerhöhung führt jedoch auch zu einer stärkeren Oxidationsneigung und Gasaufnahme. Ein besseres Formfüllungsvermögen hat durch die höhere Oberflächenbenetzung eine höhere Kontaktfläche zwischen der Schmelze und der Form zur Folge, was zu einem stärkeren Wärmeverlust führt, der das Fließvermögen reduziert.
Für die Messung des Formfüllungsvermögens hat sich in der Praxis die Bolzenprobe bewährt. Sie besteht aus zwei zylindrischen, aufrecht stehenden Bolzen die sich berühren. Sie werden mit der Schmelze umgossen. Je weiter sie in den Spalt zwischen den Bolzen eingedrungen ist, desto besser ist das Formfüllungsvermögen. Die Schmelze bildet in diesem Spalt eine Rundung, die in Richtung des Spaltes weist. Dieser Rundung kann ein Radius und damit auch ein Durchmesser zugeordnet werden. Das Formfüllungsvermögen entspricht dann dem sogenannten reziproken Durchmesser (1/D). Es hat somit die Einheit 1/mm.[4]
Speisungsvermögen, Schwindung und Schrumpfung
Spätestens nachdem die Form mit der flüssigen Schmelze ausgefüllt ist, erkaltet sie. Bei fast allen Gusswerkstoffen steigt dabei die Dichte und es verringert sich das Werkstückvolumen. Dieser Vorgang wird als Flüssigschwindung bezeichnet. Daher muss flüssige Schmelze in die Form nachfließen können. Dafür sind an das Werkstück in der Form sogenannte Speiser angebracht, aus denen Schmelze nachfließen kann, bis es erstarrt ist. Während der Erstarrung kommt es zur Erstarrungsschwindung. Anschließend erfolgt die Festkörperschrumpfung, die wie auch die Erstarrungsschwindung nicht mehr durch Speißer ausgeglichen werden kann. Das gesamte Volumendefizit beträgt bei den meisten Werkstoffen etwa 11–13 %, bei Gusseisen liegt es bei etwa 3 bis 6 %. Bei besonderen Gusseisenlegierungen mit Silicium kann es sogar zu Ausdehnung kommen.[6]
Warmrissneigung
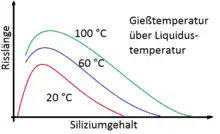
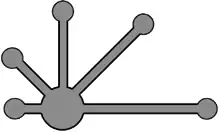
Wegen der Schwindung und Schrumpfung des Werkstücks kann es zu Rissen kommen, falls es dabei behindert wird, etwa durch die Form oder durch das Gussstück selbst. Falls die Schmelze noch nicht vollständig erstarrt ist, kann sie in die entstandenen Risse einfließen und sie so wieder schließen. Warmrisse lassen sich daran erkennen,[7] dass ihre Bruchfläche verzundert und angelaufen ist. Zum Teil sind Dendriten zu erkennen und die Bruchfläche ist interkristallin, sie verläuft also entlang der Korngrenzen. Bei Kaltrissen dagegen ist eine blanke feinkörnige Bruchfläche zu erkennen, die durch die Körner selbst verläuft, also transkristallin ist. Die Warmrissneigung ist stark werkstoffabhängig. Bei Werkstoffen, die zur Ausbildung von Dentriten im Gefüge neigen, können diese die Restschmelze im Inneren des Gussstücks einschließen und sie so daran hindern, in die Risse zu fließen. Die Warmrissneigung kann mit der Ringprobe untersucht werden. Hier wird ein ringförmiges Gussstück gefertigt, dass durch einen Keramikkern in der Mitte der Form an der Schrumpfung gehindert wird. Eine andere Möglichkeit ist die Verwendung von Sternkokillen. Hier gehen vom Einguss mehrere unterschiedlich lange Stäbe ab, die sternförmig angeordnet sind. An ihren Enden weisen sie Verdickungen auf, sodass sie sich nicht zusammenziehen können. Die in den Stäben auftretenden mechanischen Spannungen sind dann proportional zur Länge der Stäbe. Aus dem längsten nicht gerissenen Stab kann dann auf die Warmrissneigung geschlossen werden. Die Warmrissneigung von Stahl und Temperguss ist relativ schlecht, die von Gusseisen und eutektischen Aluminium-Silicium-Legierungen sehr gut.[6]
Gasaufnahme
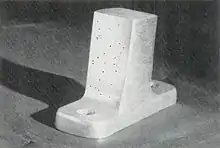
In der flüssigen Schmelze können sich grundsätzlich Gase lösen. Der Zusammenhang zwischen dem Druck und der Löslichkeit bei konstanter Temperatur wird durch das sievertsche Gesetz beschrieben. Wenn die Schmelze erkaltet, sinkt dabei auch die Löslichkeit für Gase, die aus der Schmelze an die Oberfläche wandern. Wenn das Gussstück an den Rändern bereits erstarrt ist, kann das Gas, das aus der im Inneren noch flüssigen Schmelze entweicht, nicht das Gussstück verlassen und bildet Hohlräume, die als Poren oder Lunker erkennbar sind und die Festigkeit mindern. Problematisch ist dabei insbesondere Wasserstoff, der sich wegen der geringen Atomgröße gut löst. In der Schmelze liegt er als einatomige Lösung vor. Wenn er entweicht, setzt er sich zu zweiatomigen Molekülen zusammen, die mehr Volumen benötigen, sodass es zu Dehnungen kommen kann. Diese können jedoch grundsätzlich auch Schwindung und Schrumpfung ausgleichen.[8]
Oxidationsneigung
Die Oxidationsneigung beschreibt die Neigung der heißen Schmelze mit dem Sauerstoff der Luft Oxide zu bilden. Aluminium bildet an seiner Oberfläche eine Oxidschicht, die eine weitere Oxidation verhindert (sogenannte Passivierung). Magnesium dagegen muss unter einer Schutzgasatmosphäre gegossen werden, da es sonst die Oxide ins Innere des Gussstücks ziehen würde. Dort hätten die harten Oxide eine Kerbwirkung die festigkeitsmindernd wirkt. Außerdem beeinträchtigen flüssige Oxide das Fließvermögen und das Formfüllungsvermögen und verringern die Dehnbarkeit, was die Warmrissneigung erhöht. Der Oxidation kann entgegengewirkt werden durch den Einsatz von Schutzgasen wie Schwefeldioxid, die jedoch nicht umweltfreundlich sind. Andere Möglichkeiten sind Filter im Gießlauf oder die Reinigung der Schmelze durch Gasspülungen, Entgasungstablette oder Abdecksalze.[8]
Penetrationsneigung
Als Penetration bezeichnet man beim Sandguss das Eindringen (Penetrieren) der Schmelze in den Formsand. Am Gussstück macht er sich durch anhaftende Sandkörner und schlechte Oberflächenqualitäten (Rauigkeit) bemerkbar. Von Penetration spricht man, falls die Körner des Formstoffes chemisch nicht mit der Schmelze reagiert haben, andernfalls von Vererzung oder Anbrennung.[9] Ein Maß für die Penetrationsneigung ist der Randwinkel, der den Winkel einer Flüssigkeitsoberfläche zu einem Feststoff angibt. Im Idealfall liegt er bei 180°. Für Sand, Quarz, Zirkonium-Sand, Lehm, Ton und Grafit liegt er nahe bei 180°.[10]
Literatur
- Stephan Hasse (Hrsg.): Giesserei-Lexikon 2008. 19. Auflage, Fachverlag Schiele & Schön, Berlin 2007, ISBN 978-3-7949-0753-3.
- Alfred Herbert Fritz (Hrsg.): Fertigungstechnik. 11. Auflage, Springer Fachmedien, Berlin Heidelberg 2015, ISBN 978-3-662-46554-7.
Weblinks
- Gießbarkeit auf Ingenieurkurse.de – mit Abbildung einer Gießspirale, abgerufen am 1. April 2016
- Druckguss In: gta.htw-aalen.de, abgerufen am 1. April 2016
Einzelnachweise
- Stephan Hasse (Hrsg.): Gießerei Lexikon, Schiele & Schön, Berlin, 18. Auflage, 2001, S. 504 (Stichwort „Gießbarkeit“).
- Matthias Bünck: Gießeigenschaften in: Andreas Bührig-Polaczek, Walter Michaeli, Günter Spur (Hrsg.): Handbuch Spanen, Hanser, München, 2014, S. 28.
- Alfred Herbert Fritz (Hrsg.): Fertigungstechnik. 11. Auflage, Springer Fachmedien, Berlin, Heidelberg, 2015, S. 46.
- Matthias Bünck: Gießeigenschaften in: Andreas Bührig-Polaczek, Walter Michaeli, Günter Spur (Hrsg.): Handbuch Spanen, Hanser, München, 2014, S. 28f.
- Matthias Bünck: Gießeigenschaften in: Andreas Bührig-Polaczek, Walter Michaeli, Günter Spur (Hrsg.): Handbuch Spanen, Hanser, München, 2014, S. 30.
- Matthias Bünck: Gießeigenschaften in: Andreas Bührig-Polaczek, Walter Michaeli, Günter Spur (Hrsg.): Handbuch Spanen, Hanser, München, 2014, S. 32–34.
- Alfred Herbert Fritz (Hrsg.): Fertigungstechnik. 11. Auflage, Springer Fachmedien, Berlin, Heidelberg, 2015, S. 51.
- Matthias Bünck: Gießeigenschaften in: Andreas Bührig-Polaczek, Walter Michaeli, Günter Spur (Hrsg.): Handbuch Spanen, Hanser, München, 2014, S. 36.
- Stephan Hasse (Hrsg.): Gießerei Lexikon, Schiele & Schön, Berlin, 18. Auflage, 2001, S. 939 (Stichwort „Penetration“)
- Alfred Herbert Fritz (Hrsg.): Fertigungstechnik. 11. Auflage, Springer Fachmedien, Berlin, Heidelberg, 2015, S. 54.