Druckguss
Druckguss (englisch High Pressure Die Casting (HPDC)) ist ein Gießverfahren für die Serien- oder Massenproduktion. Hierfür kommen in der Regel Gusslegierungen mit niedrigem Schmelzpunkt zum Einsatz.
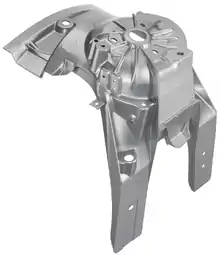
Beim Druckguss wird die flüssige Schmelze unter hohem Druck von ca. 10 bis 200 MPa und mit einer sehr hohen Formfüllgeschwindigkeit von bis zu 12 m/s in eine Druckgussform (Gussform, Kavität) gedrückt, wo sie dann erstarrt. Das Besondere am Druckgussverfahren ist, dass mit einer Dauerform, d. h. ohne Modell, gearbeitet wird. Dadurch fällt bei einer Serie gleicher Bauteile die Formherstellung nur einmal an, allerdings bei wesentlich höherem Herstellungsaufwand. Damit wird eine hohe Mengenleistung erzielt, insbesondere bei einer Warmkammer-Druckgießmaschine, bei der sich der Gießbehälter und der Gießkolben ständig in der Schmelze befinden. Bei Legierungen, deren Schmelzpunkt höher ist, wird das Kaltkammer-Druckgussverfahren angewendet, die Gießgarnitur befindet sich hierbei außerhalb der metallischen Schmelze.
Das Druckgießen steht in Konkurrenz zum Spritzgießen mit Kunststoffen. Metallische Werkstoffe haben im Einzelfall Vorteile, die den Markt für Druckgussartikel sichern.
Die am häufigsten verwendeten Werkstoffe sind
Eigenschaften
Druckgießteile besitzen glatte, saubere Flächen und Kanten. Des Weiteren erlaubt dieses Verfahren geringere Wandstärken als andere Verfahren. Bei Zink zum Beispiel können die Teile eine Wandstärke von 1 mm und bei Aluminium von 1,4 mm, in Ausnahmefällen sogar unter 1 mm haben.
Die erreichbaren Toleranzen liegen bei ±0,05 bis ±0,15 mm, so dass auch von einem Genau- oder Fertigguss gesprochen wird. Bei großen Gussteilen benötigt man jedoch etwas größere Toleranzen.
Dabei ist es möglich, Teile aus anderen Werkstoffen, wie z. B. Buchsen, Gewindebolzen oder Stifte mit einzugießen. Innengewinde werden unmittelbar mit drehbaren Stahlkernen hergestellt, die dann später wieder entfernt werden können. Im Gegensatz zu anderen Verfahren nennt man den Abguss hier „Schuss“. Es ist möglich, bis zu 1000 Schüsse pro Stunde durchzuführen (je nach Maschinengröße). Je nach Gießwerkstoff beträgt die Standmenge der Formen bis 2.000.000 Schüsse (Zinklegierungen).
Bei Aluminium werden Standzeiten von ca. 80.000 bis 200.000 Schuss erreicht. Lange galt Aluminium-Druckguss als nicht geeignet zum Schmelzschweißen und zur Wärmebehandlung. Inzwischen ist es in aufwändigen Untersuchungen gelungen, Aluminium-Druckguss schmelzschweißgeeignet und wärmebehandelbar herzustellen. Hier sind – für optimale Festigkeitseigenschaften – die besonders verzugsarmen Strahlschweißverfahren (Elektronenstrahl- und Laserstrahlschweißen) hervorzuheben. Jedoch ist es für optimale Ergebnisse notwendig und empfehlenswert, bei der Konstruktion die Anforderungen des Verfahrens zu berücksichtigen. Darüber hinaus kann Aluminium-Druckguss jedoch auch sehr gut mittels Reibschweißverfahren wie etwa dem Rührreibschweißen verschweißt werden.
Druckgießmaschine
Druckgießmaschinen bestehen üblicherweise aus einer Formschließeinheit, die dem Öffnen und Schließen der Druckgießform dient. Bestandteile der Formschließeinheit (auch Schließteil genannt) sind:
- eine feste Maschinenplatte (auch feste Platte genannt) zur Aufnahme der feststehenden Eingießformhälfte und im Kaltkammerverfahren der Gießgarnitur
- eine bewegliche Maschinenplatte (auch mobile Platte) zur Aufnahme des hydraulischen Auswerfers und der beweglichen Formhälfte
- die vier Führungssäulen auf denen die bewegliche Maschinenplatte geführt wird
- das Kniehebelsystem (bestehend aus Zylinderplatte (auch Querhaupt genannt), kurzem und langem Hebel sowie Kreuzkopf)
- der Schließzylinder
Das flüssige Metall wird aus der Gießkammer mit einem Gießkolben in die Form gepresst. Nach der Art der eingesetzten Maschine unterscheidet man das Warm- und das Kaltkammerverfahren. Der Antrieb des Gießkolbens erfolgt durch den Antrieb der Gießeinheit. Die Beaufschlagung des Antriebskolben erfolgt meist durch einen hydraulischen Druckspeicher. In einzelnen Fällen wird der Gießkolben elektrisch angetrieben (Stand 2006).
Peripherie
Im Umfeld der Druckgießmaschine arbeiten die Peripherieeinheiten. Dabei handelt es sich um prozesstechnische Vorrichtungen, die zum Ablauf des automatischen Prozesses notwendig sind.
- Formsprühmaschine oder Manipulator zu Formsprühung bzw. feste Düsen
- Heiz- und Kühlgeräte
- Entnahmevorrichtungen
- Dosierofen oder Schöpflöffel
Vakuumunterstütztes Druckgießverfahren
Das vakuumunterstützte Druckgießverfahren mit Zwangsentlüftung ermöglicht Werkstücke mit geringen oder keinen Gaseinschlüssen. Dabei wird die Kavität und die Füllkammer bei Gießbeginn evakuiert, so dass die sich darin befindliche Luft und entstehende Gase beim Gießen abgesaugt werden und sich so weniger bis gar keine Lufteinschlüsse in der Schmelze bilden können.
Nachverdichtung
Hier wird durch hohe Verdichtung in der Phase vor der endgültigen Erstarrung des Werkstücks ein ähnlicher Effekt erreicht. Poren und Lufteinschlüsse werden deutlich reduziert. Da während der Erstarrung der Schmelze, d. h., beim Übergang von flüssig nach fest ein Volumensprung stattfindet, kommt es zwangsläufig zu Volumendefiziten im Inneren von dickwandigen Bauteilen. Um diesen Effekt der flüssigen Schwindung zu kompensieren kann bei den sogenannten Squeeze-Verfahren eine Nachverdichtung der erstarrenden Schmelze erreicht werden. Dazu wird in der Druckgussform in Bereichen, in denen ein Volumendefizit erwartet wird, mittels eines „Squeeze Pins“ die breiige Schmelze komprimiert.
Druckgussform und -werkzeug
Die im Druckgussverfahren benötigten Druckgusswerkzeuge werden im Werkzeugbau respektive im Formenbau hergestellt. Als Werkstoff für die Gussformen verwendet man meistens Sonderwerkstoffe oder hochfeste Warmarbeitsstähle nach DIN EN ISO 4957. Eine Auswahl ist in der folgenden Tabelle dargestellt.
Werkstoffkurzname | Werkstoffnummer |
---|---|
32CrMoV 12-28 | 1.2365 |
X37CrMoV 5-1 | 1.2343 |
X40CrMoV 5-1 | 1.2344 |
Phasenfolge
Beim Druckgießen wird eine zuvor temperierte (100 bis 300 Grad Celsius) Dauerform (zwei- oder mehrteilig) unter Druck mit hoher Geschwindigkeit mit Metallschmelze befüllt. Der eigentliche Gießprozess kann in drei Phasen gegliedert werden.
Die Vorfüllphase dient dazu, die Schmelze in der Gießkammer bis zum Anschnitt zu fördern. Die bei der ersten Phase im Anguss-system komprimierte Luft kann aufgrund der relativ geringen Geschwindigkeit des Kolbens (0,05–0,7 m/s) über Entlüftungskanäle und durch die Formteilungsebene entweichen.
Bei der Formfüllphase presst der Gießkolben mit sehr hoher Geschwindigkeit (0,4–6 m/s) die Schmelze in die Form. Die Formfüllzeit ist mit 5–60 ms außerordentlich kurz. Eine Entlüftung der Form ist deshalb praktisch nicht möglich.
In der Nachdruckphase am Ende der Formfüllung wird ein sehr hoher statischer Enddruck aufgebaut. Dabei wird die bei der Formfüllung eingeschlossene Luft komprimiert und die Nachspeisung des Gussteils gewährleistet.
Gießdruck
Verschiedene Gusswerkstoffe erfordern jeweils einen anderen Gießdruck. Aluminium- und Magnesiumlegierungen werden mit 300–1200 bar, Zink mit 130–250 bar und Messing mit 300–1000 bar vergossen. Die Festigkeit eines Werkstückes ist bei hohem Gießdruck größer.
Der Querschnitt des Antriebskolbens und der Betriebsdruck des Druckspeichers sind nicht veränderbar. Um einen bestimmten Gießdruck zu erreichen, variiert man also den Querschnitt des Gießkolbens. Dabei gilt
- (Kräftegleichgewicht)
Bei kreisförmigem Kolbenquerschnitt gilt zudem für Antriebskolbendurchmesser und Gießkolbendurchmesser
Durch Umstellen dieser Gleichung erhält man für den gewünschten Gießdruck den erforderlichen Gießkolbendurchmesser
Schwindungsverhalten von Aluminium-Silicium-Schmelzen
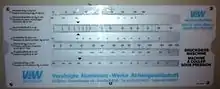
Wenn man flüssiges Aluminium von etwa 700 °C so in einen Formhohlraum gießt, dass die Form genau ausgefüllt ist, dann verringert sich das Volumen des Metalls bis auf Raumtemperatur aufgrund seiner Kontraktion um insgesamt etwa 1,3 %. Von diesem Gesamtwert entfallen 0,05 % auf die Flüssigkeits-, 0,75 % auf die Erstarrungs- und 0,5 % auf die Festkörperkontraktion.
Dieses Volumendefizit von 1,3 %, das bei Aluminium-Legierungen nicht viel geringer ist als bei Reinst-Metall, macht sich am erstarrenden Gussteil in Form vom Volumenfehlern bemerkbar. Diese Fehler treten neben der normalen Schwindung teils als Einfallstellen, teils als Makro-Lunker oder als Schwindungsporen auf.
Die Schwindung kann sich in einer Druckgießform nicht so ungehindert vollziehen wie beispielsweise in einer Sandgussform. Der Ausdruck „Schwindung“ bedeutet in der Gießereitechnik außer einem Vorgang eine Maßgröße und zwar die prozentuale Maßabweichung des erkalteten Gussteils von den Abmessungen der Formfasson bei Betriebstemperatur. Ob nun eine Schwindung frei oder behindert erfolgen kann, hängt fast ausschließlich von der geometrischen Gestalt des Gussteiles ab. Es ist also möglich, dass man an ein und demselben Gussteil für viele Maße das heute allgemein übliche Schwindmaß von 0,5 % anwenden kann, während für andere Bereiche 0,4 % noch zu viel sein könnte. Die Formabmessungen sind unter Berücksichtigung anhand einer Schwindmaßzeichnung der betreffenden Druckgießlegierungen festzulegen.
Druckgusslegierung | Schwindmaß in % |
---|---|
Aluminiumlegierungen | 0,5–0,7 |
Magnesiumlegierungen | 0,5–0,8 |
Zinklegierungen | 0,4–0,6 |
Einfluss der Legierungselemente in Aluminium-Gusslegierungen
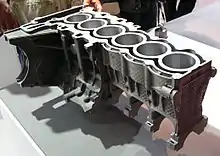
Gefüge
Aluminium bildet mit 12,5 % Silicium ein Eutektikum1, das bei 577 °C schmilzt. Im Zweistoffsystem gibt es keine Verbindung zwischen Aluminium und Silicium. Die Löslichkeit von Silicium im festen Aluminium beträgt im Gleichgewicht bei 577 °C 1,65 %, fällt bei 300 °C auf 0,22 % und bei tieferen Temperaturen noch weiter ab. Hat eine Legierung mehr Silicium als der Löslichkeit entspricht, so enthält das Gefüge neben Aluminium-Mischkristallen auch Silicium-Kristalle. Wenn die Abkühlungsgeschwindigkeit nicht besonders groß ist, erstarrt das Silicium im eutektischen Gemisch in Form von kantigen Kristallen, Nadeln und Platten. Diese Ausbildungsformen werden durch kleine Beimengungen von z. B. Natrium, Strontium, Antimon oder Phosphor beeinflusst. Ähnliche Effekte bewirkt das Druckgießen aufgrund der schnellen Erstarrung.
Eutektikum1 ist ein Gemisch von Legierungselementen, welches von allen möglichen Zusammensetzungen den niedrigsten Schmelzpunkt besitzt. Der eutektische Punkt, z. B.: einer Al-Si-Legierung, liegt bei 12,5 % und 577 °C.
Gießeigenschaften
Je höher der Si-Gehalt, desto vorteilhafter wirkt er sich auf das Fließ- und Formfüllungsvermögen aus. Mit sinkendem Si-Gehalt wird das Fließvermögen schlechter.
Einfluss von Silicium auf das Speisungsverhalten
Mit steigendem Si-Gehalt, über 11 %, nimmt das Makro-Lunkervolumen stark zu. Das Einfallvolumen verläuft zum Makro-Lunkervolumen entgegengesetzt. Unter 9 % Si kommt es bei starkwandigen Teilen bevorzugt zu Sauglunkern. Die Speisungsmöglichkeiten von Makro-Lunkern sind bei Druckguss beschränkt (Vom Anschnitt liegende, dickwandige Gussteilbereiche bereiten einige Probleme, da Materialanhäufungen beim Schuss zuletzt gefüllt und zuletzt erstarren). Bei untereutektischen Legierungen macht sich Grobkorn infolge von Überhitzung durch Saugstellen bemerkbar.
Eine naheutektische Schmelze (um ca. 11 % Si) verursacht stärkere Makro-Lunker. Eutektische und naheutektische Al-Si-Schmelzen, die zu einem „körnigen“ oder „veredelten“ Gefüge führen, erstarren unter Bildung einer Randschale (exogene Erstarrung), so dass diese Schmelzen nicht für Sauglunker anfällig sind.
Eisen
Bei Druckguss wirkt sich ein höherer Eisengehalt positiv aus (z. B., Leg. EN AC-AlSi9Cu3(Fe) max. 1,2 %), da es die Klebeneigung des Metalls an der Formoberfläche vermindert. Innerhalb der Toleranzgrenzen hat Eisen normalerweise keinen Einfluss auf die Gießeigenschaften. Unbeabsichtigte Erhöhung durch unsachgemäße Schmelz- oder Arbeitsweise in der Gießerei können zu Versprödung der Gussteile sowie zu unerwünschter Lunker-, Warmriss- oder Einfallstellenbildung führen. Bei niedrigen Warmhalte- und Gießtemperaturen treten oftmals Schwereseigerungen auf, die sich auf dem Boden des Ofens sammeln. Die Seigerungsprodukte bestehen aus Eisen, Mangan und Silicium. Die Härte von Seigerungsprodukten beträgt 500–1000 Vickers.
Kupfer
Kupferzusätze vermindern die Erstarrungsschrumpfung. Dies hat zur Folge, dass kupferhaltige Al-Legierungen leichter druckdichte Gussstücke erlauben. Positiven Einfluss haben Cu-Zusätze auf Festigkeit und Bearbeitbarkeit. Kupfer vermindert die Korrosionsbeständigkeit.
Mangan
Mangan-Zusatz von einigen zehntel % vermindert den nachteiligen Einfluss des Eisens auf Dehnung und Schlagfestigkeit. Treten jedoch Eisen und Mangan in höherem Gehalt auf, so können diese bei ungünstigen Schmelzbedingungen, z. B. durch niedrige Warmhaltetemperaturen, zu harten Ausseigerungen führen.
Magnesium
Bei gleichzeitiger Anwesenheit von Silicium, Kupfer oder Zink führt Magnesium zu einer Verbesserung der Bearbeitbarkeit infolge von Härtesteigerung. Magnesium hat keinen nachteiligen Einfluss auf das Korrosionsverhalten. Magnesium wird auch immer interessanter in der Automobilbranche, besonders wegen seines geringeren Gewichts.
Nickel
Wichtigster Vorteil der Nickelzusätze ist die Erhöhung der Warmfestigkeit. Insbesondere Kolben und Zylinderköpfe sind die Haupteinsatzgebiete der nickelhaltigen Al-Legierungen.
Zink
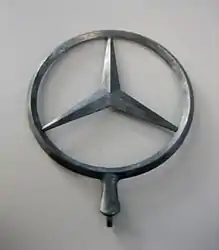
Unterschiedlicher Gehalt an Zink im Rahmen der Toleranzgrenzen sind im Allgemeinen ohne Einfluss. Im Druckguss wird der Zn-Gehalt zusammen mit Magnesium bei warmrissanfälligen Teilen gelegentlich eingeengt.
Titan
Titan wird den Al-Legierungen hauptsächlich als Kornfeinungsmittel bis max. 0,15 % zugesetzt. Bei Sand- und Kokillengusslegierungen ist es kornfeinender Legierungsbestandteil.
Blei
Blei liegt im festen Zustand ungelöst in Form feiner Tropfen vor. Innerhalb der Toleranzgrenzen (< 0,1 %) beeinflusst Pb die Legierungseigenschaften nicht merklich.
Zinn
Zinn scheidet sich bei einem Gehalt über 0,02 % entlang der Korngrenzen aus und hat bei Überschreitung der Normaltoleranz eine sehr nachteilige Auswirkung auf das Warmrissverhalten – vor allem bei Druckguss.
Vergleich Druckguss und Spritzguss
Die Investitionskosten für Gießmaschinen und die hohen Fertigungskosten für die Form sind in etwa vergleichbar. Bei beiden Verfahren müssen hohe Stückzahlen diese hohen Investitionskosten rechtfertigen. Danach sind die Rohmaterialkosten vorrangig.
Druckgegossene Metallbauteile besitzen eine wesentlich höhere Biegefestigkeit (-steifigkeit) als spritzgegossene; sie kann bis zu 20-mal höher sein. Die im Druckguss hergestellten Werkstücke sind auch bei höheren Temperaturen (Aluminium bis ca. 450 °C) noch belastbar. Bei spritzgegossenen Materialien nimmt die Festigkeit und Steifigkeit bei höheren Temperaturen (ab 100 °C) stark ab; eine Ausnahme bilden nur teure Spezialkunststoffe. Ein weiterer Vorteil ist, dass bei Belastung der Bauteile (mit Ausnahme von Zink) kein Kriechen auftritt, wie es bei vielen spritzgegossenen Werkstücken der Fall ist. Druckgegossene Teile besitzen eine wesentlich bessere Gestaltsfestigkeit, das heißt eine mechanisch bearbeitete Fläche bleibt eine Fläche, wobei sich die Fläche eines Kunststoffteiles wesentlich leichter verformt. Des Weiteren verändern einige spritzgegossene Kunststoffe die Form unter klimatischen Bedingungen. Druckgegossene Werkstoffe besitzen eine elektromagnetische Abschirmung und eine Beständigkeit gegen organische Lösungen. Außerdem ist ein Recycling ohne Qualitätsverlust möglich.
Spritzgegossene Bauteile sind bei der Verwendung von Standardmaterialien preiswerter. Außerdem kann beim Spritzgießen farbig gegossen werden. Ein weiterer Vorteil ist das geringere Gewicht gegenüber druckgegossenen Werkstücken. Letztere besitzen außerdem schlechtere Korrosionseigenschaften. Des Weiteren ist die Herstellung druckgegossener Metallbauteile aufwändiger und „komplizierte“ Geometrien sind teilweise nicht realisierbar.
Siehe auch
- Spritzguss
- Squeeze Casting (Pressgießen)
- Thixoforming