Feingießen
Feingießen ist ein Gießverfahren, mittels dessen auch kleine und kleinste Gussteile formgetreu und bei minimierter Nachbearbeitung hergestellt werden können. Feingießen ist zum Teil dem Wachsausschmelzverfahren ähnlich, bei dem sowohl das Modell, meist aus Wachs oder Kunststoff bestehend, als auch die Form nach dem Guss nicht mehr vorhanden sind.
Verfahren
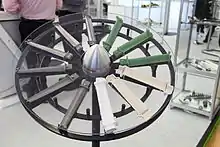
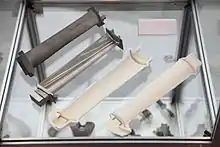
Unter Feinguss versteht man die Herstellung von kleinen bis kleinsten Gussteilen. Die Gussstücke zeichnen sich durch Detailstärke, Maßgenauigkeit und Oberflächenqualität aus. Oftmals kann eine spanende Bearbeitung eingespart werden. Bis zur Mitte des 20. Jahrhunderts wurde zwischen Spritzguss und Feinguss in der Literatur nicht immer sauber unterschieden, Inzwischen ist Spritzguss weitgehend als Bezeichnung für in einer Variante des Druckgießverfahrens hergestellte Kunststoffteile gebräuchlich, wogegen Feinguss vornehmlich im Schwerkraftverfahren – wie bei Kokillenguss üblich – gelegentlich aber auch als Niederdruckguss oder im Schleudergussverfahren aus nahezu jeder Legierung hergestellt werden kann.
Gussfehler können beim Übergang vom flüssigen in den festen Zustand auftreten. Dabei werden zum Teil Gase freigesetzt, die bei unzureichender Diffusion eingeschlossen bleiben.[1]
Der Atmosphärische Guss ist der offene Abguss der Schmelze unter normalen Druck- und Luftverhältnissen. Das Niederdruckgießverfahren eignet sich etwa für das Gießen von Aluminiumlegierungen, Magnesium, Kupfer, Eisen und beim Stahlguss. Durch den Gasdruck gelangt die Schmelze mittels eines Steigrohrs in den Formhohlraum der Feingießform. Hochreaktive Legierungen können unter Vakuum aufgeschmolzen und abgegossen werden. Die Vakuumgussprozesse können sich etwa durch die Anzahl der Vakuumkammern unterscheiden. Beim Vakuumgießen mit einer Vakuumkammer erfolgt das aufzuschmelzen in derselben Kammer wie auch der Abguss. Beim Vakuumguss mit zwei Vakuumkammern wird die Schmelze in der separaten Vakuumkammer vorbereitet. Für das Gießen von speziellen Materialien mit schlechten Fließeigenschaften und hoher Reaktivität kann das Verfahren des Schleudervakuumguss angewandt werden. Dieser ist eine Kombination des Vakuumgusses und des Schleudergusses.
Das Modell wird dabei aus speziell geeigneten Wachsen oder ähnlichen Thermoplasten oder deren Gemischen zum Beispiel im Spritzgussverfahren hergestellt. Die Modelle werden zunächst in Einfach- oder Mehrfachwerkzeugen gespritzt. Je nach Gesamtstückzahl, Gestalt des Gussstückes und Art des Modellwerkstoffes wird das entsprechende Spritzwerkzeug gebaut. Um Hinterschneidungen in der Kontur mit einzubringen, können vorgeformte wasserlösliche oder keramische Kerne erforderlich sein, für welche dann ein Zusatzwerkzeug benötigt wird.
Eine andere Möglichkeit zur Herstellung der physischen Vorlagen bildet der Einsatz von Technologien des Rapid Prototypings. Es handelt sich jeweils um verlorene Modelle aus einem schmelzfähigen, vergasbaren oder in einer Flüssigkeit lösbaren Modellwerkstoff.
Im nächsten Schritt werden die Modelle mit dem Gießsystem zu sogenannten Modelltrauben zusammengefügt. Diese Modelltraube wird dann in einen sogenannten Schlicker getaucht. Der Schlicker ist eine keramische Masse zur Herstellung einer Formschale aus feinem feuerfesten Mehl als Formgrundstoff und zum Beispiel Ethylsilikat als Bindemittel. Die mit Schlicker benetzte Traube wird anschließend mit Sand berieselt oder die Traube wird in ein durch Druckluft fluidisiertes Sandbett getaucht. Das Tauchen und Besanden wird so oft wiederholt, bis die Formschale die notwendige Stabilität zum Abguss erreicht hat. Zum Ausschmelzen der Wachsmodelle bei etwa 150 °C dienen spezielle Ausschmelzöfen (in der Regel sind dies Autoklaven), während das Brennen der Formen bei etwa 750 bis 1200 °C vorgenommen wird. Die gebrannten Formen können nun direkt abgegossen werden. Ist der metallostatische Druck und die Gießtemperatur der Schmelze hoch, können die Formen auch in einen Kasten gegeben, und mit trockenem Sand als Füllstoff hinterfüllt werden. Das Gießen geschieht meistens in heiße Formen, damit auch enge Querschnitte und feine Konturen sauber „auslaufen“, wie es der Gießer bezeichnet. Nach dem Abguss und der vollständigen Erstarrung der Schmelze wird das Gussstück entformt, und die Gussteile werden mittels Trennscheibe, Säge oder Vibration vom Gießsystem getrennt. Anschließend erfolgt die notwendige Nacharbeit durch Putzen, Schleifen, Strahlen sowie die Wärmebehandlung und Richten wie auch die erforderlichen Prüfungen der Gussteile.
Mit diesem Verfahren können Gussstücke mit einer Masse von 1 g bis zu mehreren hundert Kilogramm vergossen werden. Die linearen Toleranzen liegen bei etwa ± 0,4 bis ± 0,7 % vom Nennmaß. Bei Feingussteilen aus Kupfer ist zum Beispiel ein Schwindmaß von 1,8 % bis 2,2 % zu berücksichtigen. Im Feingussverfahren können viele Werkstoffe und Legierungselemente abgebildet werden. Darunter sind unter anderem Aluminiumlegierungen, Kupferlegierungen, Stahl-Legierungen (siehe Cobalt- und Chromlegierungen), Magnesiumlegierungen, Nickellegierungen, Titanlegierungen, Superlegierungen und viele mehr.
Der Vorteil des Verfahrens besteht darin, dass die gegossenen Teile in der Regel einbaufertig sind oder nur sehr wenig Bearbeitung erfordern. Als Faustregel für die Wirtschaftlichkeit gilt, dass das Feingießen besonders günstig ist, wenn das Bauteil komplex gestaltet ist und/oder je schwieriger es bearbeitet werden kann. Darüber hinaus ist das Verfahren besonders dann vorteilhaft, wenn weitere, in anderen Verfahren erforderliche Anbauteile in das Feingussteil integriert werden können. Diese Strukturoptimierung wird auch als Funktionsintegration bezeichnet und beschreibt die Integration von Verbindungselementen wie Hülsen, Gewindeeinsätze oder Bolzen.[2]
Siehe auch
Literatur
- DKI Informationsdruck 1.004: Kupfer – Vorkommen, Gewinnung, Eigenschaften, Verarbeitung, Verwendung. (s. bes. S. 9).
- Guss aus Kupferlegierungen. Fachverlag Schiele & Schoen, 1986, ISBN 978-3-7949-0444-0, S. 96 ff.
- H.J. Müller, Handbuch der Schmelz- und Legierungspraxis für Leichtmetalle, Verlag Schiele& Schön, Berlin 1977, ISBN 3-7949-0247-5, siehe dort S. 110 f.
- Andreas Kalweit, Christof Paul, Sascha Peters, Reiner Wallbaum: Handbuch für Technisches Produktdesign: Material und Fertigung, Entscheidungsgrundlagen für Designer und Ingenieure. Springer-Verlag, 2011. Seite 423f. ISBN 978-3-642-02642-3.
- Stephan Hasse: Taschenbuch der Gießerei-Praxis 2010. Fachverlag Schiele & Schoen. ISBN 978-3-7949-0801-1.
Einzelnachweise
- Fritz Klocke: Fertigungsverfahren 5; Gießen, Pulvermetallurgie, Additive Manufacturing. Hrsg.: VDI-Buch. 4. Auflage. Springer Vieweg, Aachen, ISBN 978-3-540-23453-1, S. 32–34.
- Funktionsintegration – Eingießen von Einlegeteilen. (PDF) In: Giessereitechnologie von der Idee zum Produkt. Fraunhofer-Institut für Fertigungstechnik und Angewandte Materialforschung (IFAM), S. 7, abgerufen am 9. Dezember 2020.