Bohren
Bohren ist ein spanendes Fertigungsverfahren, das der Fertigung von Bohrungen dient. Da die Geometrie der Schneiden eines Bohrers bekannt ist, zählt es in der Einteilung der Fertigungsverfahren zum Spanen mit geometrisch bestimmter Schneide, zu dem auch das Drehen und Fräsen zählen. Definiert ist es in der DIN 8589 gemeinsam mit dem Senken und Reiben, die alle über dieselbe Kinematik verfügen, also dieselbe lineare, rotierende Relativbewegung zwischen Werkzeug und Werkstück aufweisen. Das Senken und Reiben wird als präzisere Variante des Bohrens eingesetzt. Diese können jedoch nur eine bereits vorhandene Bohrung verbessern, während mit dem Bohren auch ins Volle gebohrt werden kann. Bei allen drei Verfahren werden immer innenliegende Flächen erzeugt, die häufig zylindrisch sind, jedoch immer rotationssymmetrisch. Sowohl die Handwerkzeuge als auch die Werkzeugmaschinen werden als Bohrmaschinen bezeichnet.
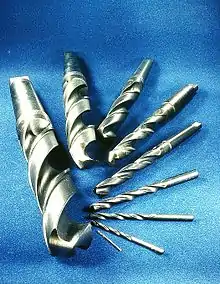
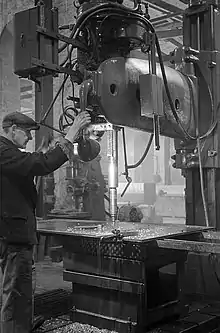
Das Bohren ist bereits seit der Steinzeit bekannt. Die heute weit verbreiteten Spiralbohrer gibt es jedoch erst seit etwa 1840. Zuvor wurde der Löffelbohrer genutzt. Beim Bohren ist die Schnittgeschwindigkeit am Umfang des Werkzeuges am größten und fällt zur Mitte hin auf Null ab. Dort wird der Werkstoff nicht geschnitten, sondern von der Spitze nach außen gedrückt. Das Bohren ist eines der wichtigsten spanenden Fertigungsverfahren. Schätzungen zufolge macht es etwa die Hälfte der gesamten Bearbeitungszeit aus, was jedoch auch daran liegt, dass es vergleichsweise unproduktiv ist.
Beim Bohren entsteht viel Wärme an der Spitze des Bohrers. Da die Bearbeitungsstelle schlecht zugänglich ist, kann die dort entstehende Wärme ebenso schlecht abgeführt werden wie die dort entstehenden Späne. Die Wendel der verbreiteten Wendelbohrer dienen dazu, einerseits Kühlschmiermittel zuzuführen und andererseits die Späne abzutransportieren. Die meisten Bohrungen sind etwa zwei- bis fünfmal so tief wie breit. Bei tieferen Bohrungen spricht man vom Tiefbohren, für das spezielle Tiefbohrwerkzeuge existieren, da sich bei Wendelbohrern Späne und Kühlschmiermittel gegenseitig blockieren würden.
Beim Bohren rotiert üblicherweise das Werkzeug um seine eigene Achse und vollführt so die Schnittbewegung. Die Vorschubbewegung kann durch die Bewegung des Bohrers oder des Werkstücks erfolgen. Auf Säulen- und Ständerbohrmaschinen wird statt des Werkzeuges das Werkstück bewegt. Auf Drehmaschinen kann ebenfalls gebohrt werden, falls die Bohrachse mit der Drehachse zusammenfällt. Dort rotiert jedoch meist das Werkstück um seine Achse und das Werkzeug vollführt nur die Vorschubbewegung. Zur Fertigung größerer, rotationssymmetrischer Innenflächen eignet sich das Innendrehen, das im Englischen als boring bezeichnet wird.
Geschichte der Bohrtechnik
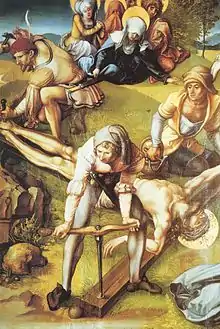
Bereits Ende des Paläolithikums (im Magdalenien) wurden durchbohrte Muscheln und Tierzähne als Schmuck getragen. Im Mesolithikum (8300–4000 v. Chr.) werden Knochen und Geweihe, Kleinschmuckstücke aus Stein, vereinzelt auch Steinscheiben durchbohrt. Die Steinbohrung wird das charakteristische Merkmal der Jungsteinzeit. Bei der Bohrtechnik in Gestein lassen sich zwei Arten unterscheiden:
- Die „unechte Bohrung“: durch beidseitiges Picken werden sanduhrförmige Vertiefungen erzeugt, die ein doppelkonisches Bohrloch hinterlassen.
- Die „echte Bohrung“ lässt sich in die Voll- und die Hohlbohrung unterteilen.
Die Vollbohrung erfolgt mit einem rotierenden Bohrkopf aus Elfenbein, Hartholz, Stein oder Tierzähnen. Merkmal ist das V-förmige Bohrloch, das durch die Abnutzung des Bohrers entsteht.
Beide Techniken schleifen mit Wasser und einem Abrasionsmittel wie Quarzsand eine mehr oder weniger zylindrische Vertiefung ein. Wie Experimente ergaben, lassen sich je nach Rohmaterial und Bohrtechnik Tiefen zwischen 0,4 mm und 0,7 mm pro Stunde erreichen.
Linsenbohrer
Im vorderasiatischen Natufien (12.000–9700 v. Chr. zeitweise zeitgleich mit dem europäischen Magdalenien) wurden Linsenbohrer eingesetzt, um Steingefäße auszuhöhlen (es gab anfangs keine Keramikherstellung). Ein flacher, gewölbter oder konisch zulaufender rotierender Dioritstein ergab entsprechende flache oder tiefere Ausbohrungen mit mehr oder weniger steiler Wandung. Der Bohrkopf war mittels zweier Vertiefungen mit einem unten gegabelten Schaft verbunden. Mit der Bogensehne wurde der Bohrkopf in Drehung versetzt, bis der gewünschte Hohlraum erreicht war. Charakteristisches Merkmal sind die konzentrischen Ringe, die der Bohrvorgang hinterlässt. Die äußere Gestaltung des Gefäßes erfolgte in einem weiteren Arbeitsgang durch Schleifen.
Hohlbohrung
Die Hohlbohrung (auch Zapfenbohrung): erfolgt mit hohlem Holz wie Holunder oder hohlen Halmen wie Schilfrohr, mit Hohlknochen (die mit Sand als Schleifmittel gefüllt werden konnten) und schnell rotierender Bohrstange. Pflanzliche Bohrer können benutzt werden, weil die eigentliche Schleifarbeit durch Quarzsand erfolgt, der um den Bohrer angehäuft wird. Erfolgt die Bohrung von einer Seite, fällt ein konischer Zapfen (Bohrkern) heraus. Typisch ist ein doppelkonisches Bohrloch, wenn von beiden Seiten gebohrt wird. Gegenüber der Vollbohrung wird ca. 1/3 der Zeit gespart.
Bohrantriebe
Der Bohrkopf aus Knochen, Elfenbein oder Stein sitzt an der Spitze eines Holzstabes. Der Stab rotiert zwischen den Handflächen, wobei der Bohrer jedes Mal mehrere Umdrehungen macht. Um den Bohrstab mit Gegenlager (mit der Hand gehaltener, ausgehöhlter Stein) wird ein Riemen geschlungen und von zwei Personen hin und her gezogen, wobei der Bohrer schnell rotiert. Größere Wirksamkeit hat der Antrieb des Bohrstabs mittels Bogen (Bogenbohrer), der eine höhere Umdrehungszahl und -geschwindigkeit erreicht. Der Holzschaft mit dem Bohrkopf dreht sich in einem Gegenlager, das mit der Hand gehalten wird; mit der anderen Hand wird der Bogen hin und her bewegt, dessen einfach um den Holzschaft gelegte Schnur die Rotation erzeugt. Vermutlich gab es auch den Drillbohrer (Rennspindel, Dreule). Ein an einer Schnur befestigter, beim Drehen auf und ab gleitender Quergriff machte den Bohrer zum Drillbohrer. Die Bohrmaschine arbeitete wie der Bogenbohrer, nur wurde statt des etwa handgroßen Widerlagers ein Bohrgestell errichtet, wobei ein waagerechter Querbalken mit seinem Gewicht ständig auf den Bohrschaft drückt, der wie beim Fiedelbohrer von der Schnur des Bogens angetrieben wird.
Bohr- oder Schleifmittel
Bohr- oder Schleifmittel waren Mischungen aus Harz und feinem Quarzsand oder Quarzsand mit Wasserzugabe bzw. der beim Bohren anfallende Gesteinsabrieb mit Wasser (Steinschliff).
Werkstückspektrum und wirtschaftliche Bedeutung
Das Bohren macht einen großen Teil der Bearbeitungszeit[1] im Maschinenbau aus. Dies liegt aber auch daran, dass es vergleichsweise unproduktiv ist, also wenig Material pro Zeit entfernen kann (Siehe Zeitspanvolumen). Der Spiralbohrer ist das am häufigsten[2] genutzte Werkzeug in der gesamten Zerspantechnik.
Bohrungen kommen an zahlreichen Werkstücken vor. Dazu zählen Durchgangsbohrungen, die auf beiden Seiten offen sind und Sacklochbohrungen, die einseitig offen sind, sowie Gewindebohrungen und Profilbohrungen, die von der zylindrischen Form abweichen. Zentrierbohrungen dienen dazu, die Mitte von Werkstücken zu markieren, um die Maßabweichungen beim Umspannen auf andere Maschinen zu minimieren. Die meisten durch Bohren hergestellten Bohrungen haben eine Tiefe von maximal dem Fünffachen des Durchmessers. Bei tieferen Bohrungen biegen sich die Werkzeuge, was zu schlechten Genauigkeiten führt. Mit speziellen Tiefbohrverfahren und Werkzeugen sind auch Tiefen bis zum 200-fachen des Durchmessers möglich. Werkstücke mit Bohrungen sind beispielsweise Motorblöcke, Schließzylinder an Türschlössern, Bremszylinder, Deckel und Gehäuse an Maschinen und Pumpen.[3]
- Durchgangsbohrung (Links) und Sackloch (rechts, unteres Bauteil)
- Sackloch
- Gewindebohrung
Bewegungen von Werkzeugen und Werkstücken
In der Zerspantechnik werden allgemein zwei Spanungsbewegungen unterschieden: Die Schnittbewegung oder Hauptbewegung, die zum Abtrennen des Spans führt und die Vorschubbewegung, die für eine kontinuierliche Spanabnahme zuständig ist. Beim Bohren dreht sich üblicherweise das Werkzeug um seine Achse und dringt gleichzeitig entlang dieser Achse in das Werkstück ein. Die drehende Bewegung ist die Schnittbewegung, die andere die Vorschubbewegung. Die entsprechenden Geschwindigkeiten sind die Schnittgeschwindigkeit und die Vorschubgeschwindigkeit. Zwischen den jeweiligen Vektoren liegt beim Bohren immer ein rechter Winkel; beim verwandten Fräsen ändert sich dieser Winkel dagegen ständig.
Es gibt auch Varianten des Bohrens, bei denen die Bewegungen ganz oder teilweise durch das Werkstück übernommen werden:[4][5]
- Bei Ständerbohrmaschinen befindet sich das Werkstück auf einem höhenverstellbaren Tisch, über dem das Bohrwerkzeug um eine senkrechte Achse rotiert. Das Werkstück wird von unten in den Bohrer hineingeschoben; die Vorschubbewegung ist somit dem Werkstück zugeordnet.
- Auf Drehmaschinen rotieren die Werkstücke. Viele verfügen über eine Vorrichtung, mit der ein nicht rotierendes Bohrwerkzeug in das Werkstück hineingeschoben werden kann. Hier wird also die Schnittbewegung vom Werkstück übernommen.
- Auf Drehautomaten und Drehzentren mit Gegenspindel wird das Werkstück in Rotation versetzt und an ein gänzlich stehendes Bohrwerkzeug herangeführt. Die gesamte Spanungsbewegung wird damit vom Werkstück übernommen. Auf diesen Maschinen gibt es auch eine Variante ähnlich der auf gewöhnlichen Drehmaschinen. Um die Bearbeitungszeit zu verringern, drehen sich zusätzlich die Werkzeuge entgegen der Werkstückrotation, um so die Schnittgeschwindigkeit zu erhöhen. Für die Präzisionsbearbeitung (Reiben) läuft das Werkzeug gleichsinnig mit dem Werkstück aber mit geringerer Drehzahl. Damit wird die effektive Schnittgeschwindigkeit verringert ohne das Werkstück abzubremsen, was für die gleichzeitig stattfindende Drehbearbeitung nachteilig wäre.[6]
Definition nach DIN 8589 und Unterschiede zum Fräsen
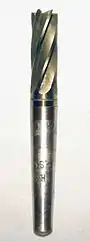
Das Bohren wird häufig definiert als (spanende) Herstellung von Löchern oder Bohrungen, was jedoch auf viele Fertigungsverfahren zutreffen kann darunter das Innendrehen und Zirkularfräsen.[7] In der DIN 8589 gibt es für alle spanenden Fertigungsverfahren eine exakte Definition, die auf den Begriffen der Schnitt- und Vorschubbewegung aufbaut und in der Fachliteratur bevorzugt wird. Das Bohren wird hier mit dem Senken und Reiben wegen der identischen Bewegung zusammengefasst:
- Bohren, Senken, Reiben ist Spanen mit geschlossener kreisförmiger Schnittbewegung, bei dem das Werkzeug eine Vorschubbewegung nur in Richtung der Drehachse erlaubt. Die Drehachse der Schnittbewegung behält ihre Lage zum Werkzeug und Werkstück unabhängig von der Vorschubbewegung bei.[8]
Diese Formulierung lässt offen, ob sich die Werkzeuge oder Werkstücke bewegen. Die "geschlossene" Schnittbewegung bezieht sich darauf, dass eine Schneide des Bohrers sich nach einer vollständigen Umdrehung wieder an der gleichen Stelle in der Bohrung befindet – nur etwas tiefer.
Das verwandte Fräsen ist dagegen folgendermaßen definiert:
- Fräsen ist Spanen mit kreisförmiger, [nicht geschlossener] dem Werkzeug zugeordneter Schnittbewegung und beliebiger Vorschubbewegung. Die Drehachse der Schnittbewegung behält ihre Lage zum Werkzeug [aber nicht zum Werkstück] unabhängig von der Vorschubbewegung bei.[8]
Beim Fräsen rotieren also immer die Werkzeuge und nie die Werkstücke. Außerdem bewegen sich die Werkzeuge seitlich in das Werkstück hinein. Ein Fräswerkzeug hat folglich immer am Umfang seine Hauptschneiden und manchmal noch auf der Stirnseite Nebenschneiden, während ein Bohrwerkzeug immer auf der Stirnseite die Hauptschneiden hat und auf dem Umfang nie Schneiden besitzt (Bis auf die sehr kurzen Nebenschneiden in der Nähe des Kopfes).
Spanbildung und Schneidengeometrie
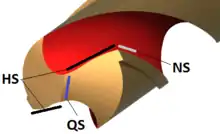
HS:Hauptschneide
QS:Querschneide
NS:Nebenschneide
Da beim Bohren die Werkzeuge um ihre eigene Achse rotieren, verändert sich die Schnittgeschwindigkeit über den Radius: Am Umfang ist sie am größten und zur Mitte hin fällt sie auf null ab. Daher ist die Spanbildung über den Querschnitt unterschiedlich, was sich in der relativ komplizierten Form der Bohrer widerspiegelt.[9][10][11]
- In der Mitte der Bohrung wird der Werkstoff des Werkstücks durch die Querschneide des Bohrers seitlich abgedrängt. Die Spanbildung entspricht hier der beim Schaben, sie wird oft als "Quetschen" bezeichnet. Die Querschneide ist in Richtung der Schnittbewegung hin geneigt, der Spanwinkel ist somit negativ.
- Der größte Teil des Bohrungsquerschnittes wird durch die Hauptschneiden abgespant. Sie sind bei Spiralbohrern entgegen der Schnittbewegung geneigt, der Spanwinkel ist somit positiv, die Schneiden selbst sind gerade. Bei Wendeplattenbohrern und einigen anderen Bohrern ist der Winkel dagegen etwa null. Die Spanbildung entspricht hier einem Schneiden, wie es beim Drehen üblich ist.
- Die Oberfläche der Bohrung wird durch die Nebenschneiden am Umfang des Bohrers erzeugt. Die Stelle an der die Haupt- mit der Nebenschneide zusammenstoßen, ist die Schneidenecke. Hier ist die Schnittgeschwindigkeit am größten und die mechanischen und thermischen Belastungen somit am höchsten. Gleichzeitig ist die Schneidenecke aber von zwei Seiten belastet (von der Haupt- und Nebenschneide). Sie verschleißt somit am schnellsten, was unter anderem ein Grund für die beim Bohren im Vergleich zu anderen spanenden Verfahren schlechte Oberflächenqualität ist.
Die Spanbildung beim Bohren wird auch wissenschaftlich untersucht. Eine Methode besteht in der sogenannten Schnittunterbrechung[12][13] bei der der Prozess plötzlich abgebrochen wird, beispielsweise durch Sollbruchstellen im Werkzeug. Anschließend kann ein Querschnitt durch die Bohrung mitsamt Werkzeug durch Schleifen hergestellt werden und unter dem Mikroskop untersucht werden. Die Form der Spanwurzel, dem Übergang vom Werkstück-Werkstoff zum Span, gibt Aufschluss über die Spanbildungsmechanismen. Andere Methoden sind die FEM-Simulation,[13][14] die in der modernen Konstruktion genutzt wird, um von verschiedenen Werkzeugkonzepten die vielversprechenden zu ermitteln, die Mikrokinematographie[13] bei der der Bohrprozess mit Hochgeschwindigkeitskameras gefilmt wird und die Ringspanuntersuchung[13].
Besonderheiten des Bohrens in der Zerspantechnik
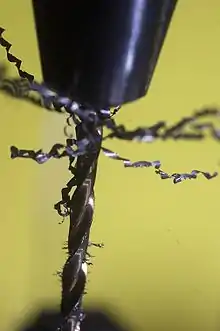
Grundsätzlich weisen die verschiedenen Verfahren der Zerspantechnik viele Gemeinsamkeiten auf. Die folgenden Eigenschaften gelten als charakteristisch für das Bohren:[9][15][16]
- Es dient ausschließlich der Herstellung von innen liegenden Flächen.
- Der Durchmesser der herzustellenden Bohrung ist im Werkzeug enthalten, lediglich die Tiefe wird über die Bewegung des Werkzeuges beeinflusst. Somit ist für jeden zu fertigenden Durchmesser ein anderes Werkzeug nötig.
- Der Abtransport der Späne ist erschwert. Bei kurzen Bohrungen genügen dazu die Nuten der Werkzeuge, bei größeren müssen sie mit Kühlschmiermittel herausgespült werden.
- Die Wärme entsteht an der Spitze des Bohrers und kann von dort nur schwer abgeführt werden. (Siehe auch Energieumwandlung und Wärme beim Spanen)
- Die Zuführung von Kühlschmiermittel ist problematisch. Bei gewöhnlichen Spiralbohrern erfolgt sie entgegen den abtransportierten Spänen, sodass es zu Blockaden kommen kann. Andere Bohrer verfügen in ihrem Inneren über Kanäle für das Kühlschmiermittel, dass direkt an der Spitze austritt.
- Der Schaft des Bohrers bewegt sich über die bereits erzeugte Oberfläche und zerkratzt sie.
- Der hohe Verschleiß der Schneidenecken gilt als typisch für das Bohren. (Siehe auch Verschleiß (Spanen))
- Die über den Querschnitt des Werkzeugs veränderliche Schnittgeschwindigkeit. Dies führt dazu, dass fast immer an einer Stelle des Bohrers eine Aufbauschneide gebildet wird, die zu schlechten Oberflächen und Standzeiten führt. Bei anderen Verfahren kann durch eine veränderte Schnittgeschwindigkeit dieses Phänomen vermieden werden.
Erreichbare Genauigkeiten und Oberflächenqualitäten
Mit dem normalen Bohren sind nur sehr schlechte Form-, Lage- und Maßgenauigkeiten und Oberflächen erreichbar, weshalb es prinzipiell zum Schruppen (Grobbearbeitung) zählt. Innerhalb der Zerspantechnik ist das Bohren mit erreichbaren ISO-Toleranzen von nur IT15 bis IT12 (Mit Sondermaßnahmen auch IT11) das ungenaueste Verfahren. Mit dem verwandten Senken und Reiben sind die in der Zerspantechnik üblichen Genauigkeiten bis IT6 erreichbar. Mit Bohrwerkzeugen aus Vollhartmetall sind auch Toleranzen erreichbar wie beim Senken; ebenso mit dem Ausdrehen und Spindeln, zwei weitere Bohrvarianten.
Die Oberflächenqualitäten werden üblicherweise als Rauheit angegeben. Beim Bohren ins Volle mit Spiralbohrern aus Schnellarbeitsstahl – Standardwerkzeuge und -verfahren – liegt die mittlere Rautiefe Rz bei etwa 80 µm. Beim Aufbohren mit Wendelsenkern dagegen bei 20 µm und beim Reiben bei 8 µm. Mit dem Ausdrehen sind bis zu 4 µm erreichbar.[17][18][19]
Einteilung der Bohrverfahren nach erzeugter Form und verwendeten Werkzeugen (DIN 8589)
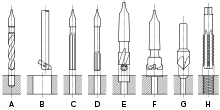
In der DIN 8589 werden sämtliche spanenden Verfahren definiert und eingeteilt. Das Bohren, Senken und Reiben wird dort wegen der identischen Kinematik gemeinsam abgehandelt. Eingeteilt werden die Bohrverfahren auf der ersten Gliederungsebene nach der erzeugten Form. Sie tragen eine eindeutige Nummer, die bei allen Bohrverfahren mit 3.2.2 beginnt (3. Hauptgruppe: Trennen, 2. Gruppe: Spanen mit geometrisch bestimmter Schneide, 2. Fertigungsverfahren: Bohren).[20][21]
- 3.2.2.1 Plansenken: Dient zur Erzeugung planer (ebener) Formen, was nur durch Senken, aber nicht durch Bohren möglich ist.
- 3.2.2.2 Rundbohren: Zur Herstellung runder Formen. Es wird weiter eingeteilt in Bohren ins Volle, Kernbohren und Aufbohren, welche nach den verwendeten Werkzeugen weiter unterteilt werden.
- 3.2.2.3 Schraubbohren zur Herstellung von schraubenförmigen Flächen. Das einzige Verfahren dazu ist das Gewindebohren.
- 3.2.2.4 nicht belegt. (Sämtliche spanenden Verfahren werden einheitlich eingeteilt. Der vierte Unterpunkt ist dem Wälzspanen vorbehalten (z. B. Wälzdrehen, Wälzfräsen oder Wälzstoßen) und dient zur Herstellung von Verzahnungen. Mit dem Bohren ist dies prinzipbedingt nicht möglich, die Ordnungsnummer entfällt daher.)
- 3.2.2.5 Profilbohren dient zur Herstellung rotationssymmetrischer Profile. Wichtig ist vor allem das Zentrierbohren.
- 3.2.2.6 Formbohren. Hier wird die Schnitt- und Vorschubbewegung gesteuert, um auch nicht kreisrunde Formen herzustellen.
Rundbohren
Das Rundbohren dient zur Herstellung zylindrischer Innenflächen, die koaxial zur Drehachse des Werkzeuges liegen. Es trägt die Ordnungsnummer 3.2.2.2 und wird eingeteilt in die vier Verfahren Bohren ins Volle, Kernbohren, Aufbohren und Rundreiben. Die letzten beiden Verfahren vergrößern oder verbessern eine bereits vorhandene Bohrung.[22]
Bohren ins Volle
Das Bohren ins Volle (ON 3.2.2.2.1) wird definiert als Rundbohren in den vollen Werkstoff, also ohne bereits vorhandene Bohrung. Dabei wird der Werkstoff über den gesamten Querschnitt entfernt, während beim Kernbohren in der Mitte der Bohrung ein Kern verbleibt. Es wird weiter eingeteilt nach den verwendeten Werkzeugen. Werkzeuge mit symmetrischen oder unsymmetrischen Schneiden werden standardmäßig verwendet. Einlippenbohrer und Bohrköpfe werden für besonders tiefe (Tiefbohren) oder präzise Bohrungen verwendet.[23]
- 3.2.2.2.1.1 Bohren mit symmetrisch angeordneten Hauptschneiden, dazu zählen die Wendelbohrer, die zu den häufigsten Zerspanungswerkzeugen gehören.
- 3.2.2.2.1.2 Bohren mit unsymmetrisch angeordneten Hauptschneiden, dazu zählen Wendeplattenbohrer mit Schneiden aus Wendeplatten.
- 3.2.2.2.1.3 Bohren mit Einlippenbohrer
- 3.2.2.2.1.4 Bohren mit Bohrkopf nach dem Einrohrverfahren, besser bekannt als BTA-Bohren. Die Bezeichnung des Herstellers wird in der DIN vermieden.
- 3.2.2.2.1.5 Bohren mit Bohrkopf nach dem Doppelrohrsystem, besser bekannt als Ejektor-Tiefbohren.
- BTA-Bohren
- Ejektor-Bohren
- Bohren mit Einlippenbohrer
Kernbohren
Kernbohren (ON 3.2.2.2.2) ist ein Bohren mit einem ringförmigen Querschnitt. In der Mitte der Bohrung verbleibt ein Zylinder, der weiterverarbeitet werden kann. In der industriellen Fertigung wird das Kernbohren eingesetzt, um das zu zerspanende Volumen bei Bohrungen mit großem Durchmesser zu verringern. In der Bautechnik und Geologie wird es genutzt, um Gesteinsproben zu entnehmen, die später analysiert werden können.
- 3.2.2.2.2.1 Bohren mit symmetrisch angeordneten Hauptschneiden
- 3.2.2.2.2.2 Bohren mit Einlippenbohrer
- 3.2.2.2.2.3 Bohren mit Bohrkopf nach dem Einrohrsystem
Aufbohren
Aufbohren (ON 3.2.2.2.3) wird angewendet, um den Durchmesser einer bereits vorhandenen Bohrung zu vergrößern. Bei Gussstücken können Bohrungen enthalten sein, die durch Kerne erzeugt wurden. Diese sind jedoch nicht besonders präzise, sodass sie ihre endgültige Form durch Aufbohren erhalten. Weitere Gründe für das Aufbohren sind die begrenzte Leistung der zur Verfügung stehenden Maschinen und die erreichbare Genauigkeit. Beim Bohren ins Volle beträgt die Schnittgeschwindigkeit an der Spitze des Bohrers Null. Dort wird der Werkstoff nicht geschnitten, sondern zur Seite weggedrückt. Daraus resultieren große Vorschubkräfte. Beim Aufbohren fallen diese weg. Außerdem neigen Bohrer mit großem Durchmesser zum Verlaufen beim Bohren ins Volle. Deswegen werden solche Bohrungen meist mit einem kleineren Bohrer vorgebohrt. Für das Aufbohren gibt es spezielle Aufbohrer mit fehlender Querschneide, einem größeren Kern und meist mehr als den üblichen zwei Schneiden.[24]
- 3.2.2.2.3.1 Aufbohren mit symmetrisch angeordneten Hauptschneiden
- 3.2.2.2.3.2 Aufbohren mit unsymmetrisch angeordneten Hauptschneiden
- 3.2.2.2.3.3 Aufbohren mit Einlippenbohrer
- 3.2.2.2.3.4 Aufbohren mit Bohrkopf nach dem Einrohrsystem
- 3.2.2.2.3.5 Aufbohren mit Bohrkopf nach dem Doppelrohrsystem
Rundreiben
Rundreiben (ON 3.2.2.2.4) Dient zur Verbesserung von Form- und Maßgenauigkeit zylindrischer Bohrungen. Die Lagegenauigkeit kann nicht mehr verbessert werden. Es wird eingeteilt in mehr- und einschneidiges Rundreiben.
Schraubbohren
Das Schraubbohren dient zur Herstellung schraubenförmiger Werkstücke. Die einzige Variante ist das Gewindebohren. Dabei wird mit einem speziellen Gewindebohrer in eine Bohrung, deren Durchmesser dem Kerndurchmesser des Gewindes entspricht, ein Gewinde eingeschnitten.[25][26] Größere Innengewinde können auch durch Zirkularfräsen (eine Variante des Schraubfräsens) oder Gewindedrehen hergestellt werden.
Profilbohren
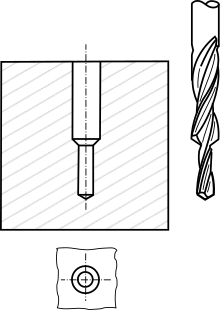
Beim Profilbohren werden rotationsymmetrische Flächen erzeugt, die nicht zylindrisch sind wie beim Rundbohren. Das Profil der Bohrung ist in der Form der Hauptschneiden des Profilbohrers enthalten. Es gibt genormte Profilbohrer wie die Zentrierbohrer und NC-Anbohrer für Zentrierbohrungen. Die meisten anderen Werkzeuge sind Spezialanfertigungen. Wichtige Profile sind Senkungen für Schraubenköpfe und kegelförmige Bohrungen, die für die Werkzeugaufnahmen an verschiedenen Maschinen dienen. Deren Maschinenschnittstelle ist häufig als Morsekegel, Steilkegel oder Hohlschaftkegel ausgeführt. Das Profilbohren trägt die Ordnungsnummer 3.2.2.5.[26][27]
- 3.2.2.5.1 Profilbohren ins Volle: Hier wird ein Profilwerkzeug genutzt, um ins Volle zu bohren. Dazu zählen die Zentrierbohrer.
- 3.2.2.5.2 Profilaufbohren: Dient zum Erweitern einer Bohrung mit einem Profilwerkzeug. Wird beispielsweise für Werkzeugaufnahmen genutzt oder zur Aufnahme von Kegelstiften.[28]
- 3.2.2.5.3 Profilsenken: Für die Auflagefläche von kegeligen Schraubenköpfen genutzt.[28]
- 3.2.2.5.4 Profilreiben: Zum Verbessern von Maßgenauigkeit und Oberflächenqualität. Wird für Werkzeugaufnahmen genutzt.[28]
Sonderverfahren
Hartbohren
Das Hartbohren ist eine Variante des Hartzerspanens und wurde in den 1980ern entwickelt, gemeinsam mit dem Hartdrehen und Hartfräsen. Bei der Hartbearbeitung werden Werkstücke mit einer Härte von etwa 54 HRC aufwärts bearbeitet. Zuvor waren solche Werkstücke nur durch Schleifen oder Läppen zu bearbeiten. Das Hartzerspanen weist allgemein höhere Zeitspanvolumina auf, ist also deutlich produktiver. Da die Schleifbearbeitung wegfallen kann, da das Hartzerspanen ausreichend präzise ist, können die Prozessketten verkürzt werden, was zu reduzierten Kosten führt.
Das Hartbohren wird eingesetzt für Bohrungen an gehärteten Zahnrädern, Flanschen, Matrizen oder Werkzeugen. Für das Hartbohren gibt es besondere Bohrer mit einer speziellen Spitze: Die Querschneide ist deutlich kleiner, häufig ist sie S-förmig mit einem Spiralpointanschliff oder Kreuzanschliff. Der Keilwinkel ist deutlich größer.[30]
Die Werkstücke können direkt im gehärteten Zustand bearbeitet werden. Damit entfällt sowohl das Weichglühen als auch das Schleifen, was auch in kürzeren Durchlaufzeiten resultiert. Außerdem kann auf die teuren Schleifmaschinen verzichtet werden, da die Bearbeitung stattdessen auf den günstigeren Drehmaschinen stattfindet. Des Weiteren ist Hartdrehen wirtschaftlicher, da pro Zeit ein größeres Werkstoffvolumen entfernt werden kann (größeres Zeitspanvolumen). Da beim Hartdrehen die Werkstückform durch die Bewegung des Werkzeuges gesteuert wird, ist es auch flexibler als das Schleifen, bei dem die Werkstückform meist teilweise im Werkzeug enthalten ist. Wegen der größeren Spanungsdicke benötigt das Hartdrehen weniger Energie und lässt sich auch ohne oder mit nur wenig umweltschädlichem Kühlschmierstoff einsetzen, was als Trockenbearbeitung beziehungsweise Minimalmengenkühlschmierung bezeichnet wird.[31]
Hochgeschwindigkeitsbohren
Das Hochgeschwindigkeitsbohren ist eine Variante des Hochgeschwindigkeitsspanens (eng. High Speed Cutting). Es wird auch als HSC-Bohren oder High Speed Drilling (HSD) bezeichnet und ermöglicht kürzere Bearbeitungszeiten, bessere Oberflächen und verringerte Schnittkräfte. Nachteilig ist der höhere Verschleiß und die höheren Anforderungen an die Maschinen (HSC-Bohrmaschinen).[32][33]
Kühlschmierstoffe
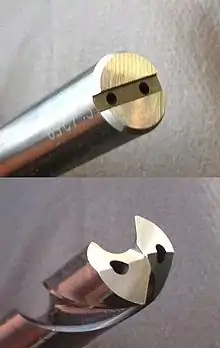
Kühlschmierstoff (KSS) soll die Reibung verringern und die beim Bohren entstehende Wärme und anfallende Späne abführen. Das hält den Bohrer länger schneidhaltig, bis er verschleißbedingt wieder angeschliffen werden muss, und erhöht die Oberflächengüte der Bohrung. KSS hat also beim Bohren drei Aufgaben:
- Ausspülen des Bohrgutes (Späne, Bohrschlamm, Schmant)
- Abfuhr der Reibungswärme
- Verringerung der Reibung zwischen Bohrer und Werkstück
Für die unterschiedlich zu bohrenden Werkstoffe werden unterschiedliche Kühlschmierstoffe eingesetzt:
- Bei Stahl wird oft Schneidöl oder eine Kühlschmierstoffemulsion (mit Wasser) eingesetzt.
- Grauguss wird wegen des im Material enthaltenen Graphits, der ein Festschmierstoff ist, meist ohne zusätzlichen KSS gebohrt.
- Bei Aluminium hat sich auch Spiritus bewährt. Petroleum ist eine weniger brennbare Alternative bei vergleichbaren Ergebnissen.
- Holz und Kunststoff werden meist trocken gebohrt.
- Für Gestein wird ein Gemisch aus Wasser und den sogenannten Compounds verwendet. Dies sind Kunststoffe, denen zusätzliche Füll- oder Verstärkungsstoffe beigemischt worden sind.
Häufig werden Kühlschmierstoffe durch Minimalmengenschmierung eingebracht oder gänzlich durch Trockenbearbeitung ersetzt. Spiralbohrer und Wendeplattenbohrer verfügen oft über eine innere Kühlschmiermittelzufuhr; d. h. der Kühlschmierstoff wird durch kleine Bohrungen im Bohrerschaft auf die eigentliche Werkzeugschneide geführt. Das erhöht gerade bei größeren Bohrtiefen die Werkzeugstandzeit.
Bohrwerkzeuge
Für das Bohren gibt es zahlreiche verschiedene Werkzeuge. Es gibt sie massiv aus einem einzigen Material – meist Schnellarbeitsstahl oder Hartmetall – oder mit eingesetzten Wendeschneidplatten. Manche verfügen über auswechselbare Spitzen – die Wechselkronen. Die meisten verfügen über zwei symmetrische Schneiden, es gibt aber auch einschneidige, mehrschneidige und welche mit asymmetrischen Schneiden.
Das mit Abstand wichtigste Bohrwerkzeug ist der Spiralbohrer. Er hat einen Anteil[2] von 20 bis 30 % an allen Zerspanungswerkzeugen und verfügt über zwei symmetrische Schneiden sowie spiralförmige Nuten die der Zuführung von Kühlschmiermittel und Abführung der Späne dienen. Es gibt ihn aus Schnellarbeitsstahl oder Hartmetall und mit Wechselköpfen. Verschiedene Schneidenformen erlauben die Anpassung an den Werkstückwerkstoff.
Außerdem gibt es noch Spezialwerkzeuge zum Tiefbohren, Bohrstangen mit nur einer Schneide zum Spindeln, Aufbohrer, Anbohrer, Gewindebohrer sowie Profilbohrer zu denen auch die Zentrierbohrer zählen. Im weiteren Sinne zählen auch Senkbohrer und Reibahlen zu den Bohrwerkzeugen.[34][35]
Maschinen
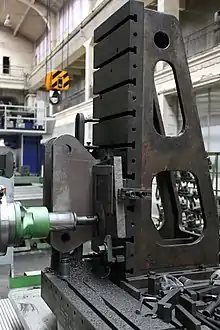
Als Bohrmaschinen werden sowohl die mechanisch angetriebenen Handwerkzeuge bezeichnet als auch die Werkzeugmaschinen. Die Handbohrmaschinen verfügen meist über einen Elektromotor als Antrieb und werden in der Hand gehalten. Auf den Werkzeugmaschinen wird die Relativbewegung zwischen Werkzeug und Werkstück durch die Maschine selbst erzeugt. Die wichtigsten Bauarten sind die Ständerbohrmaschine mit bewegtem Werkzeug und die Säulenbohrmaschine mit bewegtem Werkstück. Beide verfügen über eine senkrecht hängende Spindel in der sich das Werkzeug befindet. Das Werkstück liegt darunter. An Radialbohrmaschinen befindet sich die Spindel auf einem Ausleger der sich um eine Säule drehen kann. Die Spindel kann radial verschoben werden und somit schnell positioniert werden. Bei Koordinatenbohrmaschinen kann die Spindel entlang von drei unabhängigen linearen Achsen verschoben werden. Bei Horizontalbohrwerken bewegt sich das Werkzeug horizontal und das Werkstück ist vertikal aufgespannt. Außerdem gibt es noch Spezialmaschinen zum Tiefbohren, HSC-Bohren und Feinbohren.
Das Bohren kann auch auf Maschinen durchgeführt werden, die eigentlich für andere Verfahren gedacht sind, sofern sie über Zusatzeinrichtungen für das Bohren verfügen. Dies betrifft insbesondere Bearbeitungszentren, Drehzellen und Drehautomaten.[36][37]
Normen
In der Fachliteratur werden folgende Normen als wichtig für das Bohren bezeichnet. Diese enthalten Richtwerte und Anmerkungen zum Bohren und die zu berücksichtigenden Bedingungen.[29]
- VDI 3210 Blatt 1: Tiefbohrverfahren
- VDI 3208: Richtwerte für das Tiefbohren mit Einlippenbohrer
- VDI 3209 Blatt 1: Tiefbohren mit außerer Zustellung
- VDI 3334 Blatt 1: Maschinelle Innengewindefertigung – Allgemeines, Grundlagen, Verfahren
- VDI 3388: Werkstoffe für Schneid- und Umformwerkezeuge
- VDI/VDE 3906: Werkstoffe der Feintechnik; Werkzeugstähle
- VDI 3035: Gestaltung von Werkzeugmaschinen, Fertigungsanlagen und peripheren Einrichtungen für den Einsatz von Kühlschmiermitteln
- VDI 3397 Blatt 1: Kühlschmierstoffe für spanende und umformende Fertigungsverfahren
- VDI 3397 Blatt 2: Pflege von Kühlschmierstoffen für die Be- und Verarbeitung von Metallen – Maßnahmen zur Qualitätserhaltung, Abfall- und Abwasserverminderung
- VDI 3397 Blatt 3: Entsorgung von Kühlschmierstoffen
Andere Verfahren zur Herstellung von Bohrungen
Es gibt eine Reihe von nicht-spanenden Fertigungsverfahren, mit denen sich für spezielle Anwendungsfälle ebenfalls Bohrungen herstellen lassen. Dabei handelt es sich entweder um abtragende oder um zerteilende Verfahren, die gemäß DIN 8589 eigenständige Gruppen trennender Fertigungsverfahren bilden. Formal werden diese Verfahren nicht der Gruppe der Bohrverfahren nach DIN 8589 zugeordnet. Beispiele dafür sind das Bohrerodieren, als spezielle Form des Funkenerodierens ein thermisch abtragendes Fertigungsverfahren, das Laserbohren und Laserschneiden, ebenfalls thermisch abtragende Verfahren, bei denen Werkstücke mit Laserstrahlen bearbeitet werden, sowie das Wasserstrahlschneiden.
Siehe auch
Weblinks
Einzelnachweise
- Dirk Biermann: Allgemeines [zum Bohren] in: Uwe Heisel, Fritz Klocke, Eckart Uhlmann, Günter Spur: Handbuch Spanen. 2. Auflage, Hanser, München 2014, S. 311.
- Wilfried König, Fritz Klocke: Fertigungsverfahren 1 : Drehen, Fräsen, Bohren. 8. Auflage. Springer, Berlin 2008, S. 454.
- Herbert Schönherr: Spanende Fertigung. Oldenbourg, Berlin 2002, S. 151f.
- Heinz Tschätsch: Praxis der Zerspantechnik. Verfahren, Werkzeuge, Berechnung. 11. Auflage, Springer Vieweg, Wiesbaden 2014, S. 82.
- Uwe Heisel, Fritz Klocke, Eckart Uhlmann, Günter Spur: Handbuch Spanen. 2. Auflage, Hanser, München 2014, S. .
- Albert Herscher: Ein- und Mehrspindeldrehautomaten in: Uwe Heisel, Fritz Klocke, Eckart Uhlmann, Günter Spur: Handbuch Spanen. 2. Auflage, Hanser, München 2014, S. 133.
- Heinz Tschätsch: Praxis der Zerspantechnik. Verfahren, Werkzeuge, Berechnung. 11. Auflage, Springer Vieweg, Wiesbaden 2014, S. 92.
- Heisel, Klocke, Uhlmann, Spur: Handbuch Spanen. Hanser, 2014, S. 23 f.
- Dirk Biermann: Allgemeines [zum Bohren] in: Uwe Heisel, Fritz Klocke, Eckart Uhlmann, Günter Spur: Handbuch Spanen. 2. Auflage, Hanser, München 2014, S. 311 f.
- Herbert Schönherr: Spanende Fertigung. Oldenbourg, Berlin 2002, S. 152–155.
- Wilfried König, Fritz Klocke: Fertigungsverfahren 1 : Drehen, Fräsen, Bohren. 8. Auflage. Springer, Berlin 2008, S. 454–457.
- Berend Denkena, Hans Kurt Tönshoff: Spanen, 3. Auflage, Springer, 2011, S. 12.
- Dirk Biermann: Allgemeines [zum Bohren] in: Uwe Heisel, Fritz Klocke, Eckart Uhlmann, Günter Spur: Handbuch Spanen. 2. Auflage, Hanser, München 2014, S. 312.
- Thomas Bruchhaus: Hochleistungs-Bohrwerkzeuge - Der Unterschied liegt im Detail in: D. Biermann (Hrsg.): Spanende Fertigung - Prozesse, Innovationen, Werkstoffe, 6. Ausgabe, Vulkan, 2012, S. 121 f.
- Herbert Schönherr: Spanende Fertigung. Oldenbourg, Berlin 2002, S. 154.
- Berend Denkena, Hans Kurt Tönshoff: Spanen, 3. Auflage, Springer, 2011, S. 9 f.
- Heinz Tschätsch: Praxis der Zerspantechnik. Verfahren, Werkzeuge, Berechnung. 11. Auflage, Springer Vieweg, Wiesbaden 2014, S. 96.
- Herbert Schönherr: Spanende Fertigung. Oldenbourg, Berlin 2002, S. 188–191.
- Uwe Heisel, Thomas Stehle: Bedeutung der Zerspantechnik in: Uwe Heisel, Fritz Klocke, Eckart Uhlmann, Günter Spur: Handbuch Spanen. 2. Auflage, Hanser, München 2014, S. 311 f.
- Uwe Heisel, Fritz Klocke, Eckart Uhlmann, Günter Spur (Hrsg.): Handbuch Spanen. 2. Auflage, Hanser, München 2014, S. 313–315.
- Alfred Herbert Fritz, Günter Schulze (Hrsg.): Fertigungstechnik. 11. Auflage. Springer Vieweg, Berlin/Heidelberg 2015, S. 317 f.
- Alfred Herbert Fritz, Günter Schulze (Hrsg.): Fertigungstechnik. 11. Auflage. Springer Vieweg, Berlin/Heidelberg 2015, S. 318 f.
- Dirk Biermann: Übersicht der Bohrverfahren in: Uwe Heisel, Fritz Klocke, Eckart Uhlmann, Günter Spur (Hrsg.): Handbuch Spanen. 2. Auflage, Hanser, München 2014, S. 313 f.
- Eberhardt Paucksch, Sven Holsten, Marco Linß, Franz Tikal: Zerspantechnik - Prozesse, Werkzeuge, Technologien, Vieweg Teubner, 12. Auflage, 2008, S. 153.
- Alfred Herbert Fritz, Günter Schulze (Hrsg.): Fertigungstechnik, Springer, 9. Auflage, 2010, S. 313 f.
- Alfred Herbert Fritz, Günter Schulze (Hrsg.): Fertigungstechnik. 11. Auflage. Springer Vieweg, Berlin/Heidelberg 2015, S. 319.
- Uwe Heisel, Fritz Klocke, Eckart Uhlmann, Günter Spur (Hrsg.): Handbuch Spanen. 2. Auflage, Hanser, München 2014, S. 315 f.
- Herbert Schönherr: Spanende Fertigung, Oldenbourg, 2002, S. 148 f.
- Uwe Heisel, Fritz Klocke, Eckart Uhlmann, Günter Spur (Hrsg.): Handbuch Spanen. 2. Auflage, Hanser, München 2014, S. 315.
- Herbert Schönherr: Spanende Fertigung, Oldenbourg, 2002, S. 200 f.
- Herbert Schönherr: Spanende Fertigung, Oldenbourg, 2002, S. 127.
- Herbert Schönherr: Spanende Fertigung. Oldenbourg, Berlin 2002, S. 197–200.
- Manfred Berger: HSC-Maschinen (Kapitel I.6.7.6) in: Uwe Heisel, Fritz Klocke, Eckart Uhlmann, Günter Spur: Handbuch Spanen. 2. Auflage, Hanser, München 2014, S. 382–384.
- Jürgen Fronius: Werkzeuge und Werkzeugaufnahmen in: Uwe Heisel, Fritz Klocke, Eckart Uhlmann, Günter Spur: Handbuch Spanen. 2. Auflage, Hanser, München 2014, S. 322–333.
- Herbert Schönherr: Spanende Fertigung. Oldenbourg, Berlin 2002, S. 159–177.
- Uwe Heisel, Fritz Klocke, Eckart Uhlmann, Günter Spur (Hrsg.): Handbuch Spanen. 2. Auflage, Hanser, München 2014:
- Dirk Biermann: Maschinen und Systeme, S. 315–317.
- Rocco Eisseler: Ständerbohrmaschinen, S. 344–346, Radialbohrmaschinen, S. 346–350, Koordinatenbohrmaschinen, S. 360f.
- Ulrich Straub, Ralf Müller: Feinbohrmaschinen, S. 350–359.
- Andreas Hirsch: Werkzeugmaschinen - Grundlagen, Auslegung, Ausführungsbeispiele, Springer, 2. Auflage, 2012, S. 232–240.