Verschleiß (Spanen)
Verschleiß von Zerspanungswerkzeugen tritt aufgrund der hohen thermischen und mechanischen Belastung des Schneidkeils auf. Verschleiß bewirkt steigende Zerspankräfte und Geometrieabweichungen am herzustellenden Werkstück. Dies kann die Rauheit, Formfehler oder Maßfehler betreffen.[1]
Der Verschleiß wird beim Spanen durch mehrere Verschleißmechanismen verursacht. Dazu zählen mechanischer Abrieb (Abrasion) infolge von Reibung zwischen Span und Werkzeug, Adhäsion (Ankleben von Teilen des Spanes als Pressschweißung), Oxidation und Diffusion. Bei letzterem wandern bei hohen Temperaturen erwünschte Legierungselemente des Werkzeuges in den Span und unerwünschte Bestandteile des Spanes in das Werkzeug.
Am Werkzeug selbst macht sich Verschleiß in verschiedenen Formen oder Erscheinungen bemerkbar. Die wichtigsten beiden sind der Freiflächenverschleiß und der Kolkverschleiß. Der erste tritt auf der Freifläche des Werkzeuges auf, der zweite auf der Spanfläche. Als Maß dient oft die Verschleißmarkenbreite für ersteren und die Kolktiefe für letzteren. Sie werden als Standzeitkriterien herangezogen. Bei überschreiten dieser Kriterien müssen dann die Werkzeuge getauscht oder nachgeschliffen werden.[2]
In der Literatur wird häufig in Ursachen, Formen und Mechanismen des Werkzeugverschleißes unterschieden, die Begriffe sind jedoch nicht immer eindeutig.
Ursachen
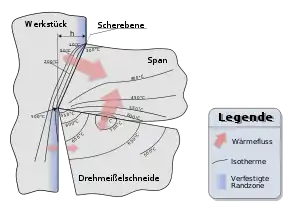
Die Ursachen des Verschleißes liegen bei den hohen thermischen und mechanischen Belastungen des Werkzeuges.[3][4] Zum Teil werden auch chemische Beanspruchungen dazugezählt.[5][6] Sie sind jeweils abhängig vom Werkstoff des Werkstücks, vom Werkstoff des Werkzeugs (Schneidstoff) und von den sonstigen Parametern wie Schnittgeschwindigkeit, Schnittkraft oder den Eingriffsgrößen.[1] (Zu den thermischen Belastungen siehe Energieumwandlung und Wärme beim Spanen)
Die mechanische Beanspruchung resultiert aus der Zerspankraft, die auf das Werkzeug wirkt und der daraus resultierenden Reibung auf der Span- und Freifläche. Zusammen mit den hohen Schnittgeschwindigkeiten resultieren daraus thermische Beanspruchungen. Wärme entsteht auch innerhalb der Späne durch das Abscheren infolge innerer Reibung. Über den Span wird ein Großteil der Wärme abgeführt, über das Werkzeug nur etwa 5 % bis 20 %. Da das Werkzeug jedoch ständig im Kontakt mit dem Span ist, entsteht eine große Wärmebelastung. Die Temperaturen führen zu Wärmeausdehnungen und Wärmespannungen, die den mechanischen Spannungen aufgrund der Zerspankraft überlagert sind. Bei Verfahren, bei denen einzelne Schneiden nicht ständig im Eingriff sind, wie beim Fräsen ergibt sich eine wechselnde thermische Beanspruchung. Die Temperaturen können dabei innerhalb einiger Millisekunden um 600 °C wechseln. Die absoluten Werte sind von den Schnittwerten und den Schneidstoffen abhängig: Während Schnellarbeitsstahl schon bei 600 °C seine Härte verliert, lassen sich andere Schneidstoffe auch noch bei über 1000 °C bei hohen Schnittgeschwindigkeiten einsetzten.[7]
Mechanismen
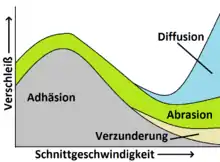
Der Verschleiß wird durch verschieden physikalisch-chemische Mechanismen[1][4] verursacht. Sie werden daher teilweise auch als Ursachen[8] oder Vorgänge[9] bezeichnet. Zu ihnen zählen Abrasion, Adhäsion, Diffusion, Oxidation (Verzunderung) und verschiedene mechanische Erscheinungen wie plastische Verformung, Oberflächenzerrüttung oder Risse.
Adhäsion
Als Adhäsion bezeichnet man allgemein das Festkleben von Teilchen aufgrund atomarer Bindungen. Da die Neigung Bindungen einzugehen von den beteiligten Elementen abhängt, ist der Adhäsionsverschleiß von der verwendeten Schneidstoff-Werkstoff-Paarung abhängig. Durch die hohen Temperaturen und Drücke kommt es zu Pressschweißungen im Mikrobereich zwischen der Spanfläche und der Spanunterseite. Wenn sich immer mehr Material auf der Spanfläche sammelt, wird dies als Aufbauschneide bezeichnet, da diese Ansammlungen nun ihrerseits als eigentliche Schneide fungieren. Wenn die Aufbauschneide oder festgeklebte Partikel durch den ablaufenden Span mitgenommen werden, werden kleine Teile der Werkzeugoberfläche mit herausgerissen. Die Größe des Adhäsionsverschleißes und der Aufbauschneide hängen von der Schnittgeschwindigkeit ab. Zunächst wachsen sie mit zunehmender Geschwindigkeit, um dann wieder zu fallen. Bei hohen Geschwindigkeiten treten sie kaum noch auf. Die Oberflächen vieler Körper bestehen aus einer sehr dünnen Oxidschicht, die sich in Folge der sogenannten Passivierung bildet. Beim Spanen können sich diese Schutzschichten jedoch nicht ausbilden. Die Oberflächen des Spanes und der Werkzeuge entsprechen während des Prozesses den Eigenschaften, wie sie normalerweise im inneren von Werkstücken auftreten. Sie sind daher chemisch sehr reaktionsfreudig was die Adhäsion begünstigt. Besonders weicher und zäher Stahl neigt zur Adhäsion insbesondere wenn das Gitter des Werkzeuges dem des Werkstoffes entspricht.[3][10][11]
Abrasion
Unter Abrasion versteht man mechanischen Abrieb durch mikroskopische, harte Teilchen. Er tritt meist gemeinsam mit anderen Verschleißmechanismen auf. Es lassen sich drei Varianten unterscheiden: Das Mikropflügen, das Mikrospanen und das Mikrobrechen. Die ersten beiden kommen bei duktilen (weichen, zähen) Schneidstoffen vor, der letzte bei harten. Bei allen Varianten gleitet ein harter Partikel auf und zumindest teilweise in der Oberfläche des Werkzeuges.
- Beim Mikropflügen verursacht der Partikel eine Furche und drängt das Material des Werkzeuges durch plastische Verformung an die Ränder der Furche. Es kommt beim reinen Mikropflügen zu keinem Materialabtrag, durch Beanspruchung kann es bei nachfolgenden Teilchen zu Abtrag kommen.
- Beim Mikrospanen wird Material der Werkzeugoberfläche in Form eines Spanes abgetragen. Beim reinen Mikrospanen entspricht das Volumen des Spanes dem Volumen des abgetrennten Materials.
- Beim Mikrobrechen verursacht der harte Partikel Risse auf der Oberfläche des Werkzeuges, die sich ausbreiten und so Teile der Oberfläche abtrennen. Beim Brechen sind die Verschleißteilchen meist deutlich größer als die Verschleißfurche.
Abrasion tritt bei allen Schnittgeschwindigkeiten auf. Die harten Teilchen können aus dem Werkstoff des Werkstücks stammen, etwa Oxide, Carbide und Nitride. Es kann sich jedoch auch um Partikel handeln, die durch Adhäsion aus der Werkzeugoberfläche abgetrennt wurden. Auch durch Oxidation können im Werkzeug harte Partikel entstehen, die sich beim Zerspanen ablösen und zur Abrasion führen. In diesem Sinne spricht man auch von "Selbstverschleiß", der insbesondere auf der Freifläche auftritt.[12][13]
Diffusion
Bei der Diffusion handelt es sich um eine thermisch aktivierte Vermischung der Bestandteile von Werkzeug und Werkstück. Bei hohen Temperaturen können einzelne Atome ihren Gitterplatz verlassen und in den jeweiligen Partner eindringen. Hierbei wird unterschieden zwischen dem Ausdiffundieren von Atomen aus dem Werkzeug in den Span und dem Eindiffundieren von Atomen aus dem Span in das Werkzeug. Das Ausdiffundieren führt in der Regel nur zu geringem Materialverlust, wichtiger ist jedoch, dass durch Ein- und Ausdiffundieren das Werkzeug seine Zusammensetzung verändert und dadurch seine Härte und Verschleißbeständigkeit verliert. Diffusion tritt insbesondere bei Hartmetallen auf. Schnellarbeitsstahl verliert seine Härte bereits bei Temperaturen von etwa 600 °C, bei denen noch keine Diffusion auftritt. Schneidkeramiken dagegen unterliegen nur sehr geringem Diffusionsverschleiß. Bei unbeschichteten Hartmetall-Werkzeugen liegen jedoch bei den bei der Zerspanung von Stahl typischen Drücken und Temperaturen ideale Bedingungen für Diffusion vor. Aus dem Hartmetall diffundieren Cobalt und Wolfram, die ihm seine Härte verleihen, in den Span. Eisen aus dem Span dagegen diffundiert in die Cobalt-Bindephase des Hartmetalls. Dort löst sich auch das Wolframcarbid auf und bildet Misch- und Doppelkarbide in Form von Fe3W3C, (FeW)6 und (FeW)23C6. Um den Diffusionsverschleiß zu vermeiden, kann man Hartmetall-Werkzeuge beschichten. Diffusionsverschleiß macht sich insbesondere auf der Spanfläche als Kolkverschleiß bemerkbar, da hier die größten Drücke und Temperaturen herrschen.[14]
Bei der Verwendung von Diamantwerkzeugen bei der Zerspanung von Stahl, diffundiert der Kohlenstoff des Diamanten sehr schnell in den Stahl. Ein ähnlicher Effekt tritt bei Verwendung von Siliciumnitrid-Schleifscheiben auf, sodass sich beide Stoffe nicht für die Zerspanung von Stahl eignen.[15]
Oxidation
Unter Oxidation versteht man die chemische Veränderung des Werkzeuges. Da der Vorgang durch die Reibung aktiviert wird, spricht man auch von Tribooxidation. Sie macht sich meist in Form von Verzunderung bemerkbar. Oxidationsverschleiß kann den Verschleiß erhöhen oder senken. Letzteres ist vor allem dann der Fall, wenn die Oxidschicht härter ist als der eigentliche Schneidstoff oder wenn die Schicht gegen Adhäsion schützt. Oxidation tritt in Zusammenhang mit der Umgebungsluft oder dem Werkstückwerkstoff auf.[16] Bei Schnellarbeitsstahl tritt er nicht auf, da er bei den für eine spanende Bearbeitung erforderlichen Temperaturen schon zu weich ist. Keramiken dagegen oxidieren auch bei hohen Schnittgeschwindigkeiten kaum. Hartmetalle oxidieren etwa bei Temperaturen von 700 °C bis 800 °C. Die Verzunderung macht sich vor allem auf der Nebenfreifläche bemerkbar und kann zu Ausbrüchen der Schneidenecken führen.[17]
Oberflächenzerrüttung, plastische Verformung und Risse
Oberflächenzerrüttung ist eine Folge von thermischen und mechanischen Wechselbelastungen. Nach einer längeren Zeit, während derer kein Verschleiß messbar ist, macht sich die Oberflächenzerrüttung in Form von Rissen bemerkbar die sich ausbreiten, sowie durch Gefügeveränderungen und Ermüdungserscheinungen die zum Abtrennen von Partikeln führen können.[18] Bei hohen Temperaturen verlieren die Schneidstoffe ihre Härte, wodurch es zu plastischen Verformungen kommen kann.[1] Besonders bei neuen Werkzeugen aus Schnellarbeitsstahl und Hartmetall und solchen die neu nachgeschliffen wurden wird die Schneidkante plastisch verformt.[15]
Formen
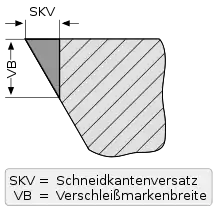
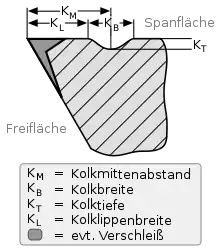
Die wichtigsten Verschleißformen (auch Erscheinungen[3]) sind der Kolkverschleiß auf der Spanfläche und der Freiflächenverschleiß. Außerdem zählen dazu Verzunderung, verschiedene Ausbrüche und Risse.[3]
Über die Haupt- und Nebenfreifläche reiben die neu erzeugten Werkstückoberflächen und hinterlassen hier Markierungen, die als Verschleißmarke VB bezeichnet werden. Ihre Breite ist ein Kriterium dafür, wie stark ein Werkzeug verschlissen ist.
Auf der Spanfläche bildet sich hinter der Hauptschneide der sogenannte Kolk aus. Es handelt sich um eine Mulde, die durch den ablaufenden Span erzeugt wird. Die Kolktiefe wird auch als Verschleißkriterium herangezogen.[19]
Ausbrüche sind makroskopische Fehlstellen im Werkzeug. Sie können auf der Haupt- oder Nebenschneide oder auf der Span- und Freifläche auftreten.[20][3]
Querrisse resultieren aus der wechselnden mechanischen Beanspruchung, Kammrisse dagegen aus der wechselnden thermischen Beanspruchung.[20]
Einzelnachweise
- Alfred Herbert Fritz, Günter Schulze: Fertigungstechnik. 11. Auflage. Springer, 2015, S. 303.
- A. H. Fritz, G. Schulze: Fertigungstechnik. 11. Auflage. Springer, 2015, S. 306.
- A. H. Fritz, G. Schulze: Fertigungstechnik. 11. Auflage. Springer, 2015, S. 302.
- Fritz Klocke, Wilfried König: Fertigungsverfahren 1 – Drehen, Fräsen Bohren. 8. Auflage. Springer, 2008, S. 75.
- Berend Denkena, Hans Kurt Tönshoff: Spanen – Grundlagen. 3. Auflage. Springer, 2011, S. 138f.
- Eberhard Paucksch: Zerspantechnik. 12. Auflage. Vieweg, 2008, ISBN 978-3-8348-0279-8, S. 45.
- B. Denkena, H. K. Tönshoff: Spanen – Grundlagen. 3. Auflage. Springer, 2011, S. 138–143.
- B. Denkena, H. K. Tönshoff: Spanen – Grundlagen. 3. Auflage. Springer, 2011, S. 144.
- Eberhard Paucksch: Zerspantechnik. 12. Auflage. Vieweg, 2008, ISBN 978-3-8348-0279-8, S. 46.
- B. Denkena, H. K. Tönshoff: Spanen – Grundlagen. 3. Auflage. Springer, 2011, S. 146.
- Fritz Klocke, Wilfried König: Fertigungsverfahren 1 – Drehen, Fräsen Bohren. 8. Auflage. Springer, 2008, S. 77.
- Fritz Klocke, Wilfried König: Fertigungsverfahren 1 – Drehen, Fräsen Bohren. 8. Auflage. Springer, 2008, S. 76, 80.
- B. Denkena, H. K. Tönshoff: Spanen – Grundlagen. 3. Auflage. Springer, 2011, S. 145.
- Fritz Klocke, Wilfried König: Fertigungsverfahren 1 – Drehen, Fräsen Bohren. 8. Auflage. Springer, 2008, S. 78, 85–87.
- Eberhard Paucksch: Zerspantechnik. 12. Auflage. Vieweg, 2008, ISBN 978-3-8348-0279-8, S. 47.
- Fritz Klocke, Wilfried König: Fertigungsverfahren 1 – Drehen, Fräsen Bohren. 8. Auflage. Springer, 2008, S. 78.
- Fritz Klocke, Wilfried König: Fertigungsverfahren 1 – Drehen, Fräsen Bohren. 8. Auflage. Springer, 2008, S. 76, 89–91.
- Fritz Klocke, Wilfried König: Fertigungsverfahren 1 – Drehen, Fräsen Bohren. 8. Auflage. Springer, 2008, S. 78f., 85.
- Fritz Klocke, Wilfried König: Fertigungsverfahren 1 – Drehen, Fräsen Bohren. 8. Auflage. Springer, 2008, S. 91f.
- Fritz Klocke, Wilfried König: Fertigungsverfahren 1 – Drehen, Fräsen Bohren. 8. Auflage. Springer, 2008, S. 83.