Linoleum
Linoleum (Deutschland: [liˈnoːleʊm]; Österreich und Schweiz: [linoˈleːʊm]; Englisch [lɪˈnəʊliəm]) ist ein von dem englischen Chemiker Frederick Walton 1860 entwickelter faserverstärkter Bodenbelag, der im Wesentlichen aus Leinöl, Korkmehl und Jutegewebe besteht. Der Name kommt von dem lateinischen Begriff oleum lini für Leinöl und verweist auf das Leinöl als wichtigsten Grundstoff für Linoleum.
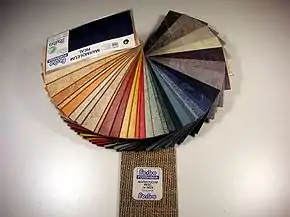
.jpg.webp)
Verwendung
Linoleum dient zur Fertigung elastischer Bodenbeläge sowie als Druckplatte beim Linolschnittverfahren in der bildenden Kunst.[1] Weitgehend historisch ist seine Verwendung für Tapeten (Lincrusta). Vereinzelt wird es auch als Belag für Möbelstücke (Tische, Schränke, Pinnwände) gebraucht.
Geschichte
Linoleum setzte sich in der zweiten Hälfte des 19. Jahrhunderts als elastischer Bodenbelag durch. Lange Zeit galt es aber gegenüber traditionellen Fußbodenbelägen – etwa Dielen – als gehobene Ausstattung.[2] Bis weit in die Mitte des 20. Jahrhunderts war es im Bereich elastischer Bodenbeläge vorherrschend. Mit der Einführung von Bodenbelägen aus PVC in den 1960er Jahren brach der Markt zusammen und erholte sich erst ab Mitte der 1980er Jahre wieder. Weltweit gab es 2008 nur noch vier Werke (alle in Europa) von drei Eigentümern, die Linoleum herstellten.
Herstellung
Rohstoffe
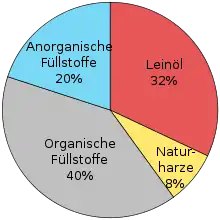
Linoleum besteht hauptsächlich aus oxidativ polymerisiertem Leinöl (Linoxin), Naturharzen (Kolophonium, Copal und ersatzweise Dammar), Kork- oder Holzmehl, Kalksteinpulver, Titan(IV)-oxid als Weißpigment, Farbstoffen und einem Jutegewebe als Trägerschicht. Alternativ zum Leinöl wird heute auch Sojaöl verwendet, zudem können je nach Hersteller und Zeitpunkt der Herstellung auch Anteile von Kautschuk oder Kunststoffen enthalten sein. Die Festigkeit wird allein durch das oxidierte Öl erreicht, die Zusatzstoffe dienen nur der Veränderung der spezifischen Eigenschaften.
Linoleum wird in einem mehrstufigen, zeit- und arbeitsaufwendigen Verfahren hergestellt. Das Linoxin und die Harze sind die Bindemittel und machen als Linoleumzement etwa 40 % der Gesamtmasse aus, 60 % entfallen auf organische (Holz-, Korkmehl) und anorganische (Kalksteinpulver, Pigmente) Füllmittel. Das Trägermaterial, im Regelfall Jutegewebe (früher Segeltuch), bildet mit nur etwa einem Prozent den geringsten Teil der Gesamtmasse.[3]
Firnis- und Linoxinherstellung
Ausgangsprodukt der Linoleumproduktion ist das Leinöl aus den Samen des Ölleins. Es wird per Warmpressung oder Extraktion gewonnen und vor der Weiterverarbeitung zu Leinölfirnis umgewandelt, indem es unter Zugabe von Trockenstoffen (früher oft Blei- und Kobalt-, heute nur Manganverbindungen in Mengen von etwa 20 ppm)[3] bei höheren Temperaturen eingekocht wird. Dabei verliert es rund die Hälfte an Gewicht und wird zäher. Das Einkochen verkürzt die spätere Trocknungszeit.[4] Der Leinölfirnis wird nun zu Linoxin oxidiert, dabei lassen sich drei Verfahren unterscheiden.
Historische Verfahren
Das älteste Oxidationsverfahren ist das auf Frederick Walton zurückgehende Tücher-Linoxinverfahren (auch Walton- oder Alt-Walton-Verfahren), bei dem in auf 30 bis 40 °C geheizten sogenannten Oxydationsschuppen feine Stoffbahnen aus Baumwolle oder Nesseltuch herabhingen. Sie wurden regelmäßig mit Leinölfirnis berieselt, der mit dem Luftsauerstoff zu Linoxin reagierte. Erst nach vier bis fünf Monaten wurden die auf eine Stärke von 1 bis 1,5 Zentimeter angewachsenen Bahnen abgenommen und das gewonnene Linoxin weiterverarbeitet. Die Methode war langsam und aufwendig, das Linoxin jedoch von hoher Qualität. Das Verfahren war zumindest noch bis in die 1950er Jahre in Gebrauch.[5][6]
Das 1871 von William Parnacott entwickelte und nach dem Fabrikanten Caleb Taylor benannte Taylor-Verfahren war ein künstliches Oxidationsverfahren, bei dem das Leinöl mit Oxidationsbeschleunigern versehen und unter Rühren und Einblasen von Sauerstoff auf gut 300 °C erhitzt wurde. Der gesamte Oxidationsprozess dauerte nur einen Tag, was die Kosten für das Endprodukt erheblich reduzierte. Das gewonnene Linoxin galt als von minderer Qualität und war sehr dunkel, weshalb es sich nur für spezielle Anwendungen eignete, etwa für die Produktion von Korklinoleum, dunkler einfarbiger Ware oder von bedrucktem Linoleum.[6]
1894 ließ Frederick Walton das sogenannte Schnelloxidationsverfahren (auch Bedford- oder Neu-Walton-Verfahren) zur Produktion des Linoxins patentieren. Das Verfahren gliederte sich in zwei Teile, nämlich die Firnisbereitung in großen Oxidationstürmen, wo das Leinöl ‚herabregnete‘, sowie die abschließende Bereitung des Linoxins in großen, liegenden Trommeln, sogenannten Bedford-Trommeln. Darin wurde der Firnis bei 55 °C unter Rühren zu einer zähen, teigartigen gelbroten Masse verdickt.[6]
Später wurde das zwischenzeitlich zwecks Reifung gelagerte Linoxin wieder eingeschmolzen und durch Zugabe verschiedener Harze der sogenannte Linoleumzement hergestellt. Dieser lagerte dann für zwei Monate bis zur endgültigen Weiterverarbeitung.
Heutiges Oxidationsverfahren
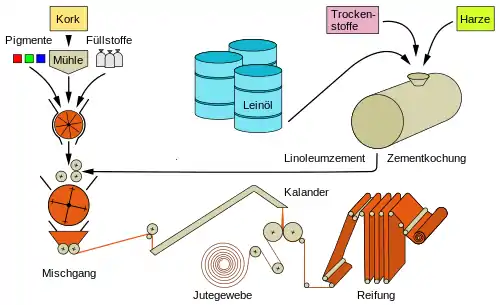
Heutige Verfahren basieren auf dem Schnelloxidationsverfahren, die einzelnen Schritte sind aber weitgehend zusammengefasst worden. Das Leinöl in den Bedford-Trommeln wird mit Trocknungsstoffen versetzt, bei einer Temperatur von etwa 80 °C und unter ständigem Rühren erfolgen dann Firnisbereitung und Oxidation. Sobald die Masse eine bestimmte Zähigkeit (Viskosität) erreicht hat, erfolgt die Zugabe der eingeschmolzenen Harze in die Trommeln. Durch computergesteuerte Verfahren können diese Trommeln aufgeheizt und abgekühlt werden, um die richtige Konsistenz und das optimale Mischungsverhältnis zu erreichen.[3]
Bis zu diesem Punkt nimmt die Zubereitung heute nicht mehr als einen Tag in Anspruch. Der Masse wird während der Oxidation zudem Linoleummehl zugegeben, das durch Schreddern und Mahlen von Produktionsresten entsteht. Dies dient zum einen der Verringerung der Abfallmenge, zum anderen wird durch das bereits oxidierte Material der Reifeprozess des neuen Linoleumzements beschleunigt.[3]
Der fertige Linoleumzement wird durch eine Schneckenpresse in einen Strang gepresst und in definierte Längen gekürzt. Er wird in mit Kreide oder Holzmehl eingestäubten Eisenkästen abgekühlt und anschließend zur Nachreife und Abkühlung bis zur Verwendung gelagert.[3]
Mischmassenbereitung, Kalandern und Nachreife
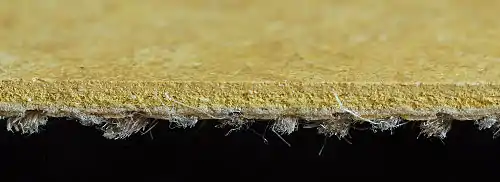
Der so produzierte Linoleumzement wird mit Kork- und Holzmehl, Kalksteinpulver als Bindemittel sowie Weißpigmenten (Titandioxid) und Farbstoffen vermischt und verknetet. Dabei werden anteilig etwa 40 % Linoleumzement, 40 % Kork- und Holzmehl und 20 % Kalksteinstaub und Pigmente gemischt, wobei die trockenen Bestandteile in einem Vormischer vermengt und erst dann mit dem dünn ausgewalzten Linoleumzement verknetet werden. Die gründliche Verknetung entsteht durch einen mehrstufigen Mischgang, in dem das Material durch mehrere Ein- und Zweischneckenmischer geführt wird. So ergibt sich eine homogene Mischung des Materials.[3]
Zum Kalandern schütten Dosieranlagen das Material als feinkörnige Masse vor den Kalanderwalzen auf das Trägergewebe auf. Diese großen, gegenläufig arbeitenden Walzenpaare können je nach Bedarf in der Drehgeschwindigkeit reguliert und aufgeheizt werden. Die Mischmasse wird durch die Kalander auf das Trägermaterial aufgewalzt, wodurch sich beide fest miteinander verbinden.[3]
Nach dem Kalandern werden die langen, ungeschnittenen Linoleumbahnen zum Nachreifen in Reifekammern gebracht. Durch eine zwei- bis vierwöchige regulierte Wärmebehandlung erhält das Linoleum hier die gewünschten Eigenschaften. Die Kammern beherbergen bis zu 20.000 Meter Linoleum und sind im Regelfall 15 Meter hoch, durch mittiges Hängen der Bahnen können die Einzelbahnen bis 30 Meter lang sein.[3]
Verlegen
.JPG.webp)
Linoleum wird im Regelfall von qualifizierten Bodenlegern verlegt. Als Hilfsmittel werden Klebstoffe sowie Spachtelmasse und spezielle Werkzeuge zur Fußbodenvorbereitung benötigt.[3] Wichtig bei der Verlegung ist die Beachtung des Raumklimas in Bezug auf Luftfeuchtigkeit, Raum- und vor allem die Bodentemperatur. Das bereits mindestens zwei Tage vor Arbeitsbeginn am Einbauort gelagerte Linoleum sollte bei Zimmertemperatur, nicht jedoch unter 15 °C verlegt werden, da es in nicht beheizten Räumen beim Ausrollen brechen sowie der verwendete Klebstoff keine stabile Verbindung zum Unterboden aufbauen kann. Sollte man die produktionsbedingten „Hängebeulen“ aufgrund der Raummaße nicht ausschneiden können, ist in diesem Bereich auch die Rückseite mit Klebstoff einzustreichen sowie eine mindestens 24-stündige, voll abdeckende und beschwerte Auflage während der Klebstoffhärtung aufzulegen.
Das Linoleum nimmt normalerweise Feuchtigkeit vom Kleber und vom Untergrund auf, die es vorübergehend erweichen. Moderne Dispersionskleber enthalten bis zu 30 % Wasser, das in den Unterboden oder das Linoleum abgegeben wird. Durch die erhöhte Feuchtigkeit kann es bis zu sechs Wochen dauern, bis das Linoleum vollständig getrocknet und voll beanspruchbar ist; in dieser Zeit ist es vor allem für Kerbschlagbelastungen anfälliger, die z. B. durch Stuhlbeine eingeschlagen werden können. Wird unter dem Linoleum zur Schallisolierung eine Korkschicht verlegt, kann der Trocknungsprozess durch die doppelte Feuchtigkeit nochmals deutlich verlängert werden.[3]
Um Räume vollständig und fugenlos an den Wänden abzuschließen, gibt es spezielle Wandanschlusssysteme, die ebenfalls aus Linoleum bestehen und in verschiedenen Ausführungen mit Stützprofil oder mit einfachen Sockelstreifen einen sauberen Abschluss ermöglichen. Ebenfalls zum Zubehör gehört Linoleumschmelzdraht zum Abdichten der Nähte, der aus einem Schmelzklebstoff besteht und transparent oder in den gleichen Farben wie das Linoleum angeboten wird. Zum Abdichten der Nähte nach dem Abbinden des Klebstoffes dient ein Handschweißgerät oder ein Schweißautomat.[3]
Oberflächenbehandlung
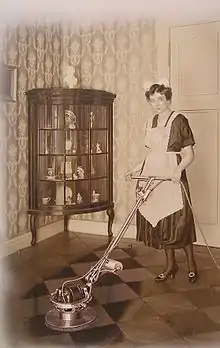
Ein Nachteil des Linoleums gegenüber Bodenbelägen aus PVC ist seine relativ große Pflegebedürftigkeit. Linoleum musste bis in die 1950er Jahre neben der normalen Reinigung regelmäßig mit wachsbasierten Pflegemitteln gebohnert werden, um die Oberfläche vor Verschmutzung und mechanischen Schäden zu schützen.
Heutzutage wird nach der Reifung eine Schutzschicht auf die Oberfläche des Linoleums aufgetragen und anschließend getrocknet. Bis Mitte der 1990er Jahre war Acrylharz gebräuchlich,[3] heute verwenden die großen Anbieter dazu entweder Polyurethan (DLW Armstrong) oder spezielle, hauseigene Beschichtungen wie TopShield (Forbo Holding) oder xf – Extreme Finish (Tarkett). Diese versiegeln das Linoleum und machen es ab Werk unempfindlich gegen Verschmutzungen. Der von den Herstellern häufig angeführte Zusatznutzen, dass bisher notwendige Pflegeschritte so entfielen, wird aber von Fachleuten durchaus skeptisch gesehen. Auch werde durch diese vollständigen Versiegelungen Wasser im Material zurückgehalten, was Stippnähte begünstigt.[7]
Unversiegelt wird Sportlinoleum für Turnhallen ausgeliefert, da es erst nach der Verlegung mit speziellen rutschfesten Pflegemitteln behandelt werden kann, um vor allem die Aufbringung der jeweils individuellen Sportboden-Linierungen und Markierungen vor Ort zu ermöglichen. Als „Ökoprodukt“ bezeichnet der Handel Linoleum, das unbehandelt vertrieben und erst nach dem Verlegen mit Naturwachsen versiegelt wird.[3] Auch Linoleum für den Linoldruck ist nicht behandelt, da die Oberfläche mit Schnittwerkzeugen bearbeitbar bleiben muss.
Reinigung und Pflege
Man kann beschichtetes und unbeschichtetes Linoleum durch feuchtes Wischen mit pH-neutralen Reinigungsmitteln reinigen. Anschließend lassen sich zur Versiegelung und Glanzerhöhung Emulsionen von Wachsen auftragen und wischen.
Eigenschaften
Linoleum besitzt viele Eigenschaften, die es als Bodenbelag auszeichnen. Seine Basiszusammensetzung und technischen Eigenschaften sind national und international genormt. Die wichtigste Norm für Europa stellt EN 548 (Elastische Bodenbeläge – Spezifikation für Linoleum mit und ohne Muster) in der letzten Fassung vom 20. September 2004 dar, die mit zahlreichen weiteren Normen zur Qualität von Sonderformen, Verlegetechniken und anderem verknüpft ist.[8] Nach dieser Norm ist Linoleum nach Art des Bindemittels definiert: Es muss aus Leinöl oder anderen trocknenden Pflanzenölen und Harzen bestehen, und der Mindestanteil an Füllmitteln (Kork-, Holzmehl) muss 30 % betragen.
Technische Eigenschaften
Hauptvorteil des Linoleums ist seine Widerstandsfähigkeit gegen mechanische und chemische Beanspruchungen. Verformungen (Druckstellen) die durch hohe Belastungen entstehen, bilden sich nach einiger Zeit fast vollständig zurück. Entsprechende Testverfahren und Grenzwerte sind als Qualitätsspezifikation in nationalen Vorschriften enthalten oder werden vom Hersteller angegeben. In Deutschland darf unter genormten Bedingungen (23 °C, 50 % relative Luftfeuchtigkeit) nach 150 Minuten Belastung und weiteren 150 Minuten Entlastung eine Eindrucktiefe von 0,15 Millimeter bzw. bei Materialien über 3,2 mm von 0,2 mm nicht überschritten werden.
Linoleum kann als schwer entflammbar (früher B1) bzw. normal entflammbar (früher B2) eingestuft werden. Dies entspricht den europäischen Brandschutzklassen Cfl-s1 bzw. Efl. Die nach der EN 1399 geforderten Eigenschaften zur Beständigkeit gegenüber brennenden Zigaretten, die vor allem bei Bodenbelägen im Publikumsbereich wichtig ist, sieht vor, dass das Material beim Ausdrücken keine und beim Abbrennen einer Zigarette nur leichte Farbveränderungen aufweisen darf.
Des Weiteren ist Linoleum beständig gegenüber einer ganzen Reihe von Säuren und Lösungsmitteln sowie anderen Chemikalien. Dazu gehören zum Beispiel Benzin, Ethanol, Öle, sowie die meisten waschaktiven Substanzen. Sehr empfindlich ist das Material allerdings gegen Alkalien mit einem pH-Wert über 9 wie zum Beispiel Seife oder Ammoniak.
Hygienische Eigenschaften
Linoleum ist antistatisch, leicht fungizid und bakteriostatisch (hemmt also Bakterien-Wachstum). Ursache ist die permanente Emission geringer Mengen verschiedener Aldehyde (Hexanal, Acrolein, Acetaldehyd usw.), die aus der praktisch nie endenden Leinölautoxidation an der Luft stammen oder Reste der Oxidationsreaktion im Herstellungsprozess (‚Reifeprozess‘) sind. Dieser Effekt hat dazu geführt, dass Linoleum bevorzugt als Bodenbelag in Gebäuden mit erhöhten Hygieneanforderungen verwendet wurde und auch heute noch wird.
Reifeschleier
Linoleum entwickelt durch Dunkelvergilbung aufgrund der enthaltenen natürlichen Öle einen typischen „Reifeschleier“, eine Farbverschiebung, die bei dunkel gelagertem Material vorkommen kann. Der Reifeschleier und die Farbverschiebung sind abhängig von der Linoleumfarbe, so bildet sich der Reifeschleier bei helleren Farben schneller zurück als bei dunklen Farben.[9] Zudem verschieben sich Blau und Grau eher in Richtung Grün und Beige in Richtung Gelb.
Dieser Reifeschleier wird durch Licht abgebaut. Eine einstündige Beleuchtung im Freien durch helle Mittagssonne reicht bereits aus, um ihn vollständig abzubauen, dunklere Lichtverhältnisse verzögern den Prozess, in vergleichsweise dunklen Wohnungen kann er teilweise auf Wochen verlangsamt sein. Bei ungleichen Lichtverhältnissen kann es zu Farb- und Helligkeitsunterschieden bei verlegtem Linoleum kommen, sogenannten Belichtungsvorsprüngen. Eine vollständige Anpassung kann Wochen in Anspruch nehmen.
Linoleum mit speziellen Eigenschaften
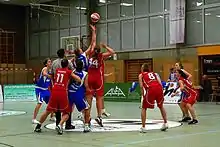
Linoleum wird auch für verschiedene Spezialanwendungen produziert. Für Bereiche, in denen mit elektrosensiblen Bauteilen gearbeitet wird, wird ein Bodenbelag verlangt, der keine elektrostatische Aufladung ermöglicht. Er muss entsprechend leitfähig sein und häufig zudem eine Standortisolierung durch einen hohen Oberflächenwiderstand aufweisen. Solche Beläge werden vor allem in Bereichen eingesetzt, in denen elektronische Bauteile gebaut oder fernmeldetechnische Anlagen oder Rechenzentren betrieben werden. Auch Räume mit hoher Explosionsgefahr wie für die Feuerwerksherstellung erfordern elektrisch leitfähige Fußböden, um keine Zündung durch elektrostatische Aufladungen zu provozieren. Das Linoleum wird hier auf einem Ableitsystem mit Kupferbändern verlegt.
Eine weitere Spezialanforderung ist verstärkte Schall- und Trittschallreduzierung. Diese wird durch Zusatzstoffe im Bodenbelag (weichfedernder Bodenbelag) oder einen speziellen Untergrund (schwimmender Estrich) erreicht.
Hochstrapazierfähiges Linoleum ist insbesondere in Turnhallen zu finden. Mit einer Dicke von 4 mm ist es besonders dick und wird vor allem auf flächenelastischen Böden aufgebracht. Es wurde bereits vor dem Ersten Weltkrieg entwickelt und auf Kriegsschiffen eingesetzt, wodurch es den Beinamen battle ship linoleum erhielt.
Geschichte
Vorgeschichte: Öltücher und Kamptulikon
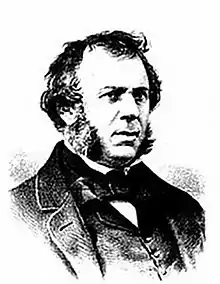
Bodenbeläge zum Schutz von Fußböden wurden schon mehrere Jahrhunderte vor dem Linoleum verwendet. Vor allem Wachs- oder Öltücher stellten einen direkten Vorgänger der späteren elastischen Bodenbeläge dar. Wachstuch in Form von bemaltem Gewebe wurde wahrscheinlich bereits im 15. oder 16. Jahrhundert entwickelt, als Fußbodenbelag ist es allerdings erst aus dem frühen 18. Jahrhundert belegt. Es setzte sich zu dieser Zeit vor allem in England durch zum Schutz von Holzböden oder wertvollen Teppichen unter Tischen, von Treppenstufen und in Durchgängen. Im Regelfall quadratische Stücke von etwa zwei Quadratmetern (zwei bis drei square yards) aus Leinen, Hanftuch oder Baumwolle wurden auf die gewünschte Größe vernäht und anschließend mit einer Farbschicht wasserdicht bemalt.[10]
Das englische Patent für Wachstuch als Fußbodenbelag wurde 1763 durch Nathan Smith eingereicht. Es bestand aus einem Gewebe, das einem mit einem Gemisch aus Harz, Teer, Spanischbraun, Bienenwachs und Leinöl überzogen war.[6] Smith eröffnete im selben Jahr eine erfolgreich laufende Manufaktur für Bodenöltuch in London und am Ende des 18. Jahrhunderts gab es in England bereits 20 Öltuchfabriken. Auch in den USA etablierte sich das Produkt und eine Reihe von Unternehmen wurden gegründet. Eine der bedeutendsten Fabriken Großbritanniens war die Tuchfabrik von Michael Nairn in Kirkcaldy, die ab 1848 auch Öltücher produzierte.[10][11]
1844 patentierte der Engländer Elijah Galloway einen elastischen Bodenbelag namens Kamptulikon. Es handelte sich um ein kautschukartiges Material, das auch in großen Gebäuden wie Kirchen verwendet wurde und gegenüber dem Öltuch wärme- und schalldämmender war.[12] Hergestellt wurde Kamptulikon aus Kautschuk, Guttapercha, Abfällen aus der Korkindustrie, Schellack und Leinöl. In den 1860er Jahren gab es in England zehn Fabriken, die Kamptulikon herstellten. Aufgrund des relativ hohen Preises konnte es sich allerdings in weniger wohlhabenden Haushalten nicht durchsetzen.[10]
Entdeckung und Entwicklung des Linoleums
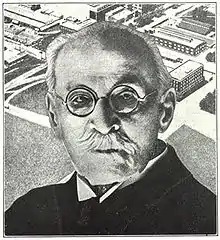
Zahlreichen Quellen zufolge entdeckte Frederick Walton das Linoleum durch einen Zufall: Bei Arbeiten zur Entwicklung schnelltrocknender Farben sah er auf einer Dose mit Farbe auf Leinölbasis eine feste gummiartige Schicht oxidierten Leinöls.[10] 1860 ließ er einen Prozess zur Herstellung des Linoxins patentieren, bei dem Leinöl der Luft ausgesetzt wurde und sich durch Oxidation verdichtete. Walton versuchte, das von ihm neu entwickelte Linoxin auf Gewebebahnen aufzutragen und so einen Ersatz für Kautschuk zu bekommen. 1863 stellte er sein erstes Stück Linoleum her und ließ das Verfahren im Jahr darauf patentieren.[13]
Bei seiner Einführung wurde Linoleum ein breites Verwendungsspektrum zugetraut, dem in dieser Form jedoch erst erdölbasierte Kunststoffe des 20. Jahrhunderts wirklich gerecht werden konnten. Zeitgenössische Quellen formulieren hohe Erwartungen an das Material: Es sollte Verwendung finden als Schutzanstrich für Eisen, Holz und Kutschwagen, als wasserfester Klebstoff sowie – nach Vulkanisierung und weiterer Härtung – als Holz-, Elfenbein- und Marmorersatz, im Alltag für Bilderrahmen, Tischdecken oder Besteckgriffe, im technischen Bereich für Prägestöcke und Gasrohre. Im Verbund mit Korund sollten selbst Schleifräder daraus hergestellt werden. Zur Umsetzung solcher Anwendungen, die Walton weitgehend Lizenznehmern überlassen wollte, kam es jedoch nicht. Sein bereits marktreifes Verfahren zur Herstellung von Bodenbelägen hingegen setzte er selbst mit der Gründung der Linoleum Manufacturing Company in Staines um, die er unter anderem durch eine Partnerschaft[10] mit William J. Turner und anderen Investoren finanzierte.[14]
Nach schleppender Einführung konnte sich das neue Material aufgrund seiner Dämmwirkung, Haltbarkeit und Elastizität schnell gegenüber den Öltüchern und dem Kamptulikon durchsetzen. Linoleum wurde aufgrund der leichten Reinigungsmöglichkeit vor allem für öffentliche Gebäude wie Krankenhäuser oder Büros genutzt. 1877 lief der Patentschutz des Linoleums aus, andere Hersteller begannen ebenfalls mit der Produktion und traten in direkte Konkurrenz zu Walton. Walton hatte es versäumt, den Namen Linoleum schützen zu lassen und verlor eine Klage gegen die mittlerweile von Michael Barker Nairn geleitete Michael Nairn & Co. mit der Begründung, dass der Begriff Linoleum durch seine Bekanntheit bereits ein etablierter Begriff für das Material und nicht mehr nur für das Unternehmensprodukt sei.[10] Innerhalb von nur 14 Jahren hatte sich Linoleum in Großbritannien als allseits bekannte Bezeichnung durchgesetzt.
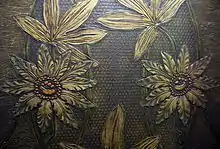
1877 entwickelte und patentierte Frederick Walton ein Verfahren, Linoxin auch als Wandverkleidung nutzbar zu machen, er nannte das neue Produkt Lincrusta.[13] Es bestand aus einem starken Papier, auf das mit einer plastischen Masse erhabene Muster aufgewalzt wurden. Diese Masse war eine Mischung aus Holzmehl, Kreide, Farbe und einem Harz-Linoxin-Gemisch. Die Produktion begann 1878 in Sunbury-on-Thames, später auch in Paris und Hannover.
1890 gelang es Walton, mit dem Straight-line-inlaid-Verfahren eine Einlegetechnik marktreif zu machen. Zwar hatte es bereits vorher Möglichkeiten gegeben, Linoleum auch zu gestalten, diese waren aber entweder nur wenig vielfältig (z. B. bei granitiertem oder marmoriertem Linoleum) oder technisch nicht überzeugend (wie das nicht verschleißfeste Bedrucken oder ein unpräzises Verfahren nach C. F. Leake). Walton gründete 1894 die Greenwich Inlaid Linoleum Company in Greenwich, die sich auf dieses Verfahren spezialisierte.
Michael Nairn bot ab 1881 große nahtlose Linoleumbahnen an und produzierte ab 1895 ebenso wie Walton Linoleum mit einer Einlegetechnik, die mehrfarbige Designs ermöglichte. 1922 übernahm Michael Nairn Ltd. das Unternehmen von Walton und firmierte seither als Michael Nairn and Greenwich Ltd.
Internationale Entwicklung
Mit dem Erfolg des Linoleums entstanden zum Ende des 19. Jahrhunderts erste Werke außerhalb Englands. Walton hatte zwar bereits vorher einzelne Lizenzen zur Herstellung von Linoleum nach Frankreich und Deutschland verkauft, der entscheidende Impuls war aber das Auslaufen des Patents von Walton im Jahr 1877. Nairn eröffnete 1888 seine erste Linoleumfabrik in Kearny, New Jersey sowie in den 1890er Jahren in Choisy-le-Roi nahe Paris und in Bietigheim (1899, ab 1900 "Germania") bei Stuttgart.[11] 1886 gründete sich zudem Tarkett in Ronneby, Schweden, als einer der wenigen bis heute existierenden Linoleumhersteller.
Ab den 1870er Jahren entstand eine Linoleum-Industrie in den USA, ab den 1880er Jahren auch in Deutschland. Die erste Linoleumfabrik in Deutschland wurde 1882 als "German Linoleum Manufacturing Comp." in Delmenhorst gegründet. Die zweite Delmenhorster Linoleumfabrik "Anker-Marke" wurde zehn Jahre später im Jahre 1892 gegründet, und die Linoleumfabrik "Adler-Marke" 1893 in Maximiliansau. Vor allem um die Jahrhundertwende sowie zwischen 1920 und 1930 entstanden Werke in vielen Ländern Kontinentaleuropas, aber auch in Kanada[15] oder Japan,[16] seit 1927 auch in Australien.[11]
1928 skizzierte die Continentale Linoleum-Union die Verhältnisse auf dem Weltmarkt mit den Worten: „England erzeugt ungefähr ebenso viel Linoleum wie der europäische Kontinent. Amerikas Produktion ist ca. fünfmal so groß wie die englische. Daneben ist in Japan eine sehr starke Linoleumindustrie erstanden, die den japanischen und den chinesischen Markt vollkommen abdeckt.“[16]
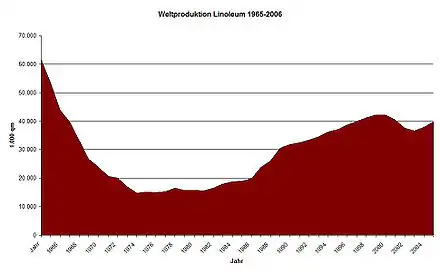
Bereits vor dem Ersten Weltkrieg existierten Abkommen zwischen Herstellern verschiedener europäischer Länder, die sowohl Preise wie auch Verkaufsbedingungen festlegten. Dieses Kartell wurde zunehmend stärker, so existierten 1934 Absprachen zwischen fast allen englischen, deutschen und italienischen Herstellern, die sicherstellten, dass man nicht in die Heimatmärkte des jeweils anderen Vertragspartners exportieren werde. 1939 galt, dass sowohl zahlreiche britische Hersteller wie auch „alle wichtigen Linoleumhersteller des Kontinents Teil förmlicher Übereinkünfte bezüglich der Verkäufe von Linoleum und Bodenbelägen in allen Märkten außer den Vereinigten Staaten“[18] seien. Der Zweite Weltkrieg inaktivierte diese Verträge. Obwohl sie nach 1945 aufgrund von Anti-Kartell-Gesetzen verschiedener europäischer Staaten nicht erneuert werden konnten, galten die Absprachen informell noch mindestens bis in die Mitte der 1950er Jahre.[19]
Nachdem sich die Linoleummärkte in den 1950er Jahren allmählich erholt hatten, begannen sich Mitte der 1960er Jahre synthetische Bodenbeläge insbesondere aus PVC durchzusetzen und der Markt für Linoleum brach zusammen. Zahlreiche Werke mussten schließen oder auf andere Produkte umstellen. Im Gefolge dieser Krise, die bis in die Mitte der 1970er Jahre anhielt, konzentrierte sich der Markt zunehmend.
Die letzten noch verbliebenen Hersteller von Linoleum sind heute die aus der Continentalen Linoleum-Union hervorgegangene Forbo Holding, die 1998 von Armstrong Industries übernommenen Deutschen Linoleum-Werke (DLW) und das französische Unternehmen Tarkett. Weltweit werden jährlich rund 38 Millionen Quadratmeter Linoleum verkauft, mit knapp 9 Millionen Quadratmetern ist dabei Deutschland der größte Einzelmarkt,[20] gefolgt von Nordamerika mit 4,5 Millionen Quadratmetern.[21] International besitzt Forbo mit einem Marktanteil von rund 65 % die Marktführerschaft,[20] gefolgt von Armstrong DLW mit 26 % und Tarkett mit 9 %.[21]
Großbritannien
Bereits ab 1906 begann die britische Linoleum-Industrie sich in einem anfangs lockeren und informellen Rahmen zu organisieren.[22] Aufgrund der Depression Anfang der 1930er Jahre gründeten sieben der neun damaligen Linoleum-Hersteller 1934 die sogenannte Linoleum and Floorcloth Manufacturers’ Association (L.M.A.), die vor allem Formate, Qualitäten und Preise vereinheitlichen und den Absatz des Linoleums fördern sollte.[22] Zeitgleich erwuchs dem Linoleum Konkurrenz durch alternative Bodenbeläge, im unteren Preissegment dem bedruckten Linoleum durch das neue Balatum, im oberen durch Bodenbeläge aus Gummi sowie Teppichböden.[23] Betrug die Jahresproduktion der britischen Linoleum-Industrie 1933 noch nur 47 Millionen m² (56 Millionen square yards), stieg sie bis 1937 auf rund 55 Millionen m² (66 Millionen square yards).[24]
Mit Beginn des Zweiten Weltkrieges verringerte sich die Versorgung mit Rohstoffen schlagartig bei gleichzeitig stark steigenden Preisen. Bereits im September 1939 stellte die Regierung den wichtigsten Grundstoff, das Leinöl, unter Kontrolle. Harze, Jute und Farbstoffe folgten bald. Ab 1940 gab es dann erste Abgabebeschränkungen und ab 1942 durfte Linoleum nur noch an staatliche Stellen abgegeben werden, die Zivilbevölkerung konnte nur Linoleum ohne Juterücken und ohne Korkgehalt erwerben. Im Kriegsjahr 1944 wurden so nur 18 Millionen m² Linoleum erzeugt.[24] All diese Beschränkungen blieben bis 1947 in Kraft, nur eine Preiskontrolle hielt sich noch bis 1953.[23]
Unmittelbar nach dem Krieg sah sich die britische Linoleum-Industrie gestiegenen Preisen, Rohstoffmangel (Leinöl, Jute) und einem lückenhaften Maschinenpark gegenüber, Schwierigkeiten, die erst um 1954 gelöst waren. In diesem Jahr produzierte die britische Linoleum-Industrie rund 50 Millionen m² (59 Millionen square yards) und knüpfte damit wieder an die Vorkriegszahlen an.[24]
Der Verfall des Linoleummarktes führte Mitte der 1960er Jahre dazu, dass viele Werke schlossen (Barry, Ostlere and Shepherd Ltd. in Kirkcaldy 1967,[25] The Linoleum Manufacturing Co. Ltd. 1973,[26] James Williamson & Son Ltd. 1963.[26]) Manche Unternehmen fusionierten (Nairn und Williamson 1963)[26] oder passten sich dem Marktgeschehen an, indem sie von der Produktion von Linoleum auf die der nun erfolgreichen neuen Bodenbeläge auswichen. Gegen die sich bis zur Mitte der 1970er Jahre hin fortsetzende Krise jedoch fand die britische Industrie kein Gegenmittel, 1975 wurde der letzte britische Hersteller, Nairn and Williamson Ltd., von Unilever und 1985 wiederum von Forbo übernommen. Forbo betreibt in Kirkcaldy heute das letzte britische Linoleum-Werk, Forbo Nairn.[27]
Nordamerika
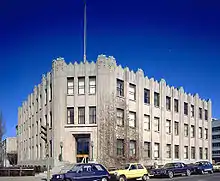
1872 wurde Frederick Walton nach New York eingeladen, um gemeinsam mit Joseph Wild die American Linoleum Manufacturing Company in Staten Island aufzubauen. Bereits 1879 konnte von der dortigen Popularität des Linoleums berichtet werden, die amerikanischen Öltuchhersteller bekamen durch Wilds Fabrik spürbare Konkurrenz.[28]
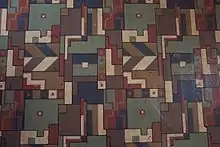
Neben Michael Nairn & Co und Joseph Wilds American Linoleum Manufacturing Company entstanden um die Jahrhundertwende insgesamt sechs Linoleumunternehmen in den USA. Während die Unternehmen von George Blabon und Thomas Potter, beide in Philadelphia, sowie Cook in New Jersey jedoch nur kurzzeitig bedeutend waren, dominierte die Armstrong Cork and Tile Company in Lancaster, Pennsylvania bald den amerikanischen Linoleummarkt. Armstrong wurde 1860 von Charles D. Armstrong gegründet und belieferte ab den 1880er Jahren vor allem Joseph Wild mit Korkmehl für die Linoleumproduktion. 1907 beschloss die Geschäftsführung, eine eigene Linoleumproduktion aufzubauen, was 1908 realisiert wurde. Im Gegensatz zu anderen Unternehmen bot Armstrong sein Linoleum direkt dem Privatverbraucher an und startete mehrere Kampagnen, um die Endbenutzer für das Programm Linoleum für jedes Zimmer des Hauses zu gewinnen. Zu Armstrongs Innovationen gehörte die dauerhafte Verlegetechnik: Während Linoleum vorher wie Teppich ausgelegt wurde und so leicht beschädigt werden konnte, wurde Armstrong-Linoleum auf den Boden geklebt. Armstrong entwickelte sich sehr schnell und war in den 1920er Jahren Marktführer im amerikanischen Raum.[10]
Der mittlerweile in Armstrong World Industries umbenannte Marktführer konnte in der Krise der 1960er Jahre zwar seine bedeutende Stellung im Bereich der elastischen Fußbodenbeläge bis in die Gegenwart aufrechterhalten, produzierte aber lange kein Linoleum mehr. Erst durch die Übernahme der Deutschen Linoleum-Werke AG 1998 wurde Armstrong wieder im Linoleum-Markt aktiv.
Der erste[29] kanadische Linoleumproduzent war die 1872 von einer elfköpfigen Investorengruppe gegründete Dominion Oil Cloth Co., später Dominion Oilcloth & Linoleum Co. Das Unternehmen, das anfangs nur Öltuch herstellte, begann um die Jahrhundertwende, auch Linoleum zu produzieren und war in den 1920er Jahren bekannt für die Qualität seiner Waren. 1934 übernahm Dominion mit der Barry & Staines Canada Ltd. den kanadischen Ableger des britischen Unternehmens, das ebenso wie Michael Nairn Ltd. einen Anteil am Unternehmen hielt.[30] 1940 übernahm Dominion auch Congoleum Canada Ltd. 1967 fusionierten die Unternehmen und firmierten als Domco Industries Ltd., nach weiteren Übernahmen 1991 und 1994 in den USA reorganisierte sich das Unternehmen 1996 zur Domco Inc. 1999 erwarb Domco die Unternehmen Tarkett und Harris Tarkett und firmierte kurz als Domco Tarkett, bevor der Konzern seit 2003 nach weiteren Fusionen global als Tarkett auftrat.[31][32]
Kontinentaleuropa
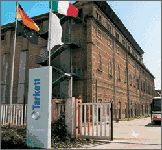
In zahlreichen Ländern Kontinentaleuropas gab es linoleumproduzierende Unternehmen (Skandinavien, Italien, Schweiz, Frankreich, Niederlande, Österreich), meist beschränkte sich dies aber auf einzelne Werke, nur selten kam es zu regelrechten Industrien mit mehreren Herstellern wie in Deutschland.
Deutschland
_Die_Kohlm%C3%BChle.jpg.webp)
In Deutschland konnte sich Linoleum anfangs nur schwer durchsetzen. Der importierte neue Bodenbelag war teuer und unterschied sich deutlich vom vertrauten Dielenboden, die Akzeptanz beim Verbraucher war entsprechend gering.[4] Erst Ende der 1870er und Anfang der 1880er Jahre änderte sich dies, und so wurden 1882 mit der Delmenhorster Linoleumfabrik (Marke „Hansa“) und der Deutschen Linoleum- und Wachstuch-Compagnie in Rixdorf bei Berlin die ersten Linoleumfabriken gegründet. 1883 folgte die Erste Deutsche Patent-Linoleumfabrik in Cöpenick bei Berlin, ab 1907 Teil der Bremer Linoleum-Werke AG Delmenhorst („Schlüssel“-Marke). Viele weitere Werke folgten bis 1899, als letzte wurde die Continental Linoleum Company 1911 gegründet.[33]
In Delmenhorst siedelte sich 1892 zusätzlich die Delmenhorster Linoleum-Fabrik AG („Anker“-Marke) an, so wurde die Stadt zum Schwerpunkt der deutschen Linoleumproduktion. Ausschlaggebende Standortvorteile Delmenhorsts waren die dort bereits ansässige Kork- und Juteindustrie, die Nähe zu England, was insbesondere in der Gründungsphase den Personal-, Technik- und Wissenstransfer vereinfachte, und die Nähe Bremens als Seehafen, was kurze Wege für Rohstofflieferungen und Export der Produktion bedeutete.[4]
Weitere Schwerpunkte der Linoleumindustrie waren die Region Berlin und Südwestdeutschland. In der Region Berlin gab es neben Rixdorf und Köpenick Werke in Velten (Continental Linoleum Company, ab 1911) und Eberswalde (Eberswalder Linoleumwerke Frentzel & Söhne). In Maximiliansau bei Karlsruhe wurde 1893 die Linoleumfabrik Maximiliansau („Adler“-Marke) gegründet, und im württembergischen Bietigheim entstand 1899 ein Ableger der schottischen Nairn Ltd., die Linoleumwerke Nairn AG.[33]
Mit dem Beginn des Ersten Weltkriegs 1914 brach die deutsche Linoleumproduktion zusammen, denn fast alle Rohstoffe kamen aus dem Ausland. Nach Kriegsende 1918 dauerte es bis zum Anfang der 1920er Jahre, bis die Branche sich erholt hatte und an die Produktionszahlen der Vorkriegszeit anknüpfen konnte.[33]
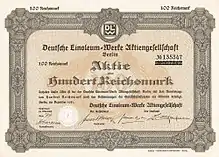
Mit dem Ende der Gründungsphase um 1900 begann eine Phase der Unternehmenskonzentration. Bis 1922 waren alle Werke der Region Berlin in Delmenhorster Unternehmen aufgegangen, 1926 kam es dann zum Zusammenschluss der Delmenhorster und süddeutschen Unternehmen zur Deutsche Linoleum Werke Aktiengesellschaft, anfangs mit Sitz in Berlin, ab 1938 dann in Bietigheim. Die Konzentration setzte sich auch auf europäischer Ebene fort: 1928 war die Deutsche Linoleum-Werke AG Berlin Mitgründer der Continentale Linoleum Union, schied aber aus politischen Gründen gegen Ende der 1930er Jahre wieder aus ihr aus.[6][33]
Im Zweiten Weltkrieg kollabierte die deutsche Linoleumproduktion aufgrund fehlender Rohstoffe erneut.[33] Erst nach 1949 erholte sie sich wieder. Von 1951 bis 1955 verdoppelte sich die Jahresproduktion von 2,8 Mio. auf 5,6 Mio. Quadratmeter.[34]
Eine Außenseiterposition nahmen die Rheinischen Linoleumwerke Bedburg (RLB) ein. Das 1897 gegründete und zeit seines Bestehens im Familienbesitz stehende Unternehmen blieb stets unabhängig von der restlichen Industrie. Im Dritten Reich übernahm die RLB mehrere Unternehmen aus jüdischem Besitz, darunter mit der Österreichischen Linoleum-, Wachstuch- und Kunstlederfabriken AG und dem Prager Unternehmen Linoleum-Industrie Leopold Blum auch zwei Linoleum-Werke. In der Nachkriegszeit wurde das Unternehmen zum zweitgrößten deutschen Hersteller nach der DLW AG und beschäftigte bis zu 1100 Mitarbeiter.[35]
Die Krise der 1960er Jahre führte zu einem drastischen Produktionsrückgang. Hatten 1960 Linoleum und ähnliche Bodenbeläge wie Stragula und Balatum noch einen Marktanteil von über 50 %, so fiel er bis 1969 auf rund 10 %. Als Folge mussten alle deutschen Werke bis auf das Werk in Delmenhorst schließen oder die Produktion von Linoleum einstellen. In den 1970er Jahren betrug die Produktion der DLW AG nur noch 150.000 Quadratmeter jährlich,[36] die RLB stellten 1973 die Linoleumproduktion ein und mussten 1978 Konkurs anmelden. Erst ab Ende der 1970er, Anfang der 1980er Jahre wuchs die Nachfrage im Zuge wachsenden Umweltbewusstseins bis zur Jahrtausendwende wieder, und der vorwiegend aus natürlichen Rohstoffen bestehende Baustoff erlangte neue Bedeutung.[33]
In Deutschland ist die DLW AG traditionell Marktführer, ihr Marktanteil lag um die Jahrtausendwende stabil bei rund 54 Prozent (Forbo 36 %, Tarkett 10 %).[20] Die Gesamtverkaufszahlen stagnierten zwischen 2003 und 2007 bei 9 bis 10 Millionen verkauften Quadratmetern, davon entfielen rund 8 bis 8,5 Millionen Quadratmeter auf den sogenannten Objektbereich. An der Warengruppe der elastischen Bodenbeläge hat Linoleum in Deutschland damit einen Anteil von rund 7 %.[37]
Schweden
Die schwedische Linoleum AB Forshaga wurde 1896 von Karl Ekström in Forshaga gegründet, zog aber nach einigen Jahren nach Göteborg, um über dessen Hafen besseren Zugang zu Rohstoffen und kürzere Exportwege zu haben. Über ein halbes Jahrhundert beherrschte das Unternehmen den schwedischen Markt für Bodenbeläge. In den 1960er Jahren verbreiterte das Werk sein Produktionsspektrum auf PVC- und Textilböden. Das Gründungsmitglied der Continentalen Linoleum Union ging dann 1968 im Forbo-Konzern auf. Heute wird Linoleum in Schweden nicht mehr hergestellt.
Italien
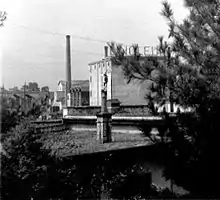
In Italien begann die Produktion 1898 mit der Gründung der Società Italiana del Linoleum mit Sitz in Mailand durch den Industriellen Giovanni Battista Pirelli, der seine Kautschukfabrik in Narni zur einzigen italienischen Produktionsstätte für Linoleum umwidmete. Die Società Italiana del Linoleum war Teil des europäischen Linoleumkartells und so gegen Importe weitgehend geschützt. Gestützt auf ihren Heimatmarkt steigerte das Monopolunternehmen den Exportanteil seiner Produktion auf bis zu 30 % in den 1930er Jahren. Auch dieses Werk geriet jedoch zum Ende der 1960er Jahre in die Krise der Branche und musste 1985 schließen.[38] Das Werk wurde von Sommer Allibert übernommen, nach deren Fusion 1997 mit Tarkett[39] in den Folgejahren umfangreich modernisiert[21] und ist heute eines der letzten vier noch aktiven Linoleumwerke.
Schweiz
Das italienische Unternehmen wurde auch zur Mutter des einzigen Schweizer Linoleumwerkes, das Pirelli 1905 in Giubiasco im Tessin gründete. Nach einigen Anfangsschwierigkeiten konnte sich das Werk erfolgreich am Markt etablieren, musste aber die Produktion im Ersten Weltkrieg unterbrechen. Zwei Jahre nach der Wiederaufnahme der Produktion 1919 wurde aus dem Filialwerk 1921 ein eigenständiger Betrieb, die Linoleum AG Giubiasco, die 1928 Mitgründer der CLU wurde. Das Werk arbeitete weiterhin erfolgreich und beschäftigte vor der Krise zwischen 1930 und 1940 bis zu 225 Angestellte. Nach dem Zweiten Weltkrieg expandierte das Unternehmen und baute sein Angebot weiter aus. Die Linoleumproduktion stellte das Werk 1965 ein und verlegte sich auf die Produktion synthetischer Bodenbeläge. 1974 ging das Werk dann im Forbo-Konzern auf, dem sie bis heute angehört, heutzutage werden dort Pressplatten für antistatische Bodenbeläge[40] hergestellt.[41]
Niederlande
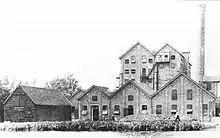
Das erste niederländische Linoleumwerk wurde 1898/1899 in Zaanstad errichtet, brannte aber bereits 1903 bis auf die Grundmauern nieder.[42] Zeitgleich wurde von der Nederlandse Linoleum Fabriek ein Werk in Krommenie errichtet, das 1922 um ein weiteres Werk in unmittelbarer Nachbarschaft erweitert wurde. Sowohl das Werk in Zaanstad wie jenes in Krommenie wurden unter Lizenz von Frederick Walton betrieben, der auch sachkundiges Personal bereitstellte. Die NLF schloss sich 1929 der CLU an. 1968 erweiterte die NLF ihre Produktpalette um Vinylböden, um der Krise zu begegnen. Im selben Jahr folgte die Fusion der Betriebe in der CLU zum Forbo-Konzern. Im Rahmen der Reorganisation des Konzerns war es das Werk in Krommenie, das neben dem in Kirkcaldy für die weitere Produktion von Linoleum ausgewählt wurde. Bis heute wird der niederländische Markt von Forbo dominiert, die 2006 einen Marktanteil von über 90 % hatten.[20][43] 2016 hat eine holländische Firma zum ersten Mal einen flüssigen Linoleum entwickelt. Diese Variante wird nicht in der Fabrik vorproduziert, sondern vor Ort verlegt. Der flüssige Linoleum hat nahezu die gleichen Inhaltsstoffe wie die herkömmliche Bahnenware. Ein großer Vorteil des flüssigen Linoleum ist, dass keine Schnittverluste mehr entstehen und das Produkt dadurch nachhaltiger und umweltverträglicher ist.
Österreich
Die Erste österreichische Linoleumfabrik (Prima Fabbrica Austriaca di Linoleum) wurde am 28. Mai 1895 in Triest gegründet; Ihr Zentralbüro und Verwaltungsrat befand sich in Wien. Sie war zunächst die erste und einzige Produktionsstätte in Österreich-Ungarn. 1904 führte sie die Herstellung nach dem Walton-System ein. 1905 wurde die Produktion von Taylor-Ware eingestellt, 1910 die von Linkrusta. 1907 wurde die Produktion von Inlaid-Ware begonnen. 1916 wurde die Linoleum-Herstellung in Triest eingestellt. Erst in den 1920er-Jahren gründete die Österreichische Linoleum-, Wachstuch- u. Kunstlederfabriken-Aktiengesellschaft mit einem Werk in Brunn am Gebirge wieder eine Produktionsstätte für Linoleum in Österreich.[44]
1922 gründete das Unternehmen Blum Haas in Traiskirchen die Österreichische Linoleum-, Wachstuch- und Kunstlederfabriken AG. Das Unternehmen wurde 1938 „arisiert“, von den Rheinischen Linoleumwerken Bedburg gekauft und in Wiener Linoleum Wachstuchwerke umbenannt.[35] 1945 wurde das Unternehmen enteignet und als USIA-Betrieb geführt, 1955 wurde es an den aus den USA zurückgekehrten Gründer zurückgegeben, 1958 übernahm es der halbstaatliche Semperit-Konzern. Wann die Linoleumproduktion eingestellt wurde, ist nicht bekannt. Die ÖLW AG produziert heute Kunstleder und Beschichtungen.[45]
Kartellbildung
1928 gründete die Deutsche Linoleum-Werke A.G. gemeinsam mit der schwedischen Linoleum Aktiebolaget Forshaga und der Schweizer Linoleum AG Giubiasco die Continentale Linoleum Union (CLU) mit Sitz in Zürich, die nach eigenen Angaben zu diesem Zeitpunkt „ungefähr 80 % der kontinentaleuropäischen Linoleumproduktion“[16] repräsentierte. Im Folgejahr kam die Nederlandsche Linoleumfabriek (Niederlande) dazu, später auch Unternehmen aus Österreich, Frankreich und Lettland. Die DLW schieden aus politischen Gründen gegen Ende der 1930er Jahre wieder aus der Union aus.[6] Aus der Continentalen Linoleum Union ging dann in den 1970er Jahren die Forbo Holding AG hervor.
Konkurrenzprodukte
Linoleum war bereits kurze Zeit nach seiner Etablierung das marktbeherrschende Produkt unter den elastischen Bodenbelägen und konnte diese Stellung fast ein Jahrhundert lang behaupten. In dieser Zeit wurden allerdings immer wieder Alternativen entwickelt, die mehr oder weniger stark mit Linoleum konkurrierten. In der Anfangszeit war dies vor allem das bereits erwähnte ältere Kamptulikon, es war allerdings weniger fußwarm und verschleißfest als Linoleum. Durch den Ausgangsstoff Gummi, der zum Ende des 19. Jahrhunderts immer teurer wurde, war es auch preislich immer weniger konkurrenzfähig. Um die Jahrhundertwende verschwand es so endgültig vom Markt.
1871 und damit etwa zehn Jahre nach der Entdeckung des Linoleums wurde das Corticin, später einfach Korkteppich genannt, entwickelt. Dieses bestand aus Korkmehl und polymerisiertem Öl. 1875 patentierte der Designer William Morris ein afrikanisches Design dieses Materials, das bis etwa 1900 erhältlich war. Corticin konnte sich allerdings gegen Linoleum nicht durchsetzen.[10]
Ursprünglich als Ersatzstoffe wurden in der ersten Hälfte des 20. Jahrhunderts Stragula, Balatum, Bedola und Triolin entwickelt. Alle existierten zeitweise parallel und konkurrierten mit Linoleum nur im untersten Preissegment. Ein weiteres, bis in die 1970er häufig verbautes Konkurrenzprodukt waren Fußböden aus Vinyl-Asbest-Platten – optisch kaum von den damaligen Linoleum-Ausführungen zu unterscheiden. Erst in der zweiten Hälfte des 20. Jahrhunderts setzte sich zunehmend PVC als Fußbodenbelag durch und verdrängte neben den verschiedenen Alternativen auch das Linoleum fast vollständig vom Markt.
Kulturgeschichte
Technische Voraussetzungen
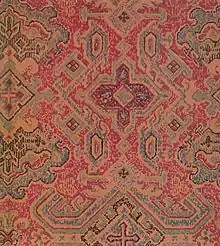
Ursprünglich gab es nur einfarbig pigmentiertes Linoleum. Zwar konnte man es mit Dekoren bedrucken, eine vermutlich schon seit der Erfindung des Linoleums gängige Praxis, solche Aufdrucke waren aber nicht verschleißfest und nutzten sich durch Gebrauch ab. Die wohl früheste Methode einer Gestaltung des Materials selbst war ein bereits 1863 existierendes und 1879 noch einmal verbessertes Verfahren, das dem Linoleum ein granitartiges Erscheinungsbild verlieh.[6] Charles Frederick Leake, einem Mitarbeiter von Walton,[13] gelang es dann 1880 erstmals, eine Methode zur Produktion nicht-granitierten, mehrfarbigen Linoleums zu entwickeln, dem Verfahren mangelte es aber noch an Präzision. Die Kunsthistorikern Pamela Watson sprach 1997 von „etwas verschwommen aussehenden Mustern, die aber die Präzision einer Gestaltung durch Kacheln nicht nachahmen konnten“.[46] 1882 dann erfand Walton das sogenannte Straight-Line-Inlaid-Verfahren, eine Einlegetechnik, die endlich ein dauerhaftes Design ermöglichte. Musterungen wurden hierbei aus verschiedenfarbigen Bahnen ausgeschnitten, mosaikähnlich zusammengelegt und mittels Druck und Hitze zusammengefügt. Anfangs war das so erzeugte Linoleum sehr teuer und entsprechend wenig erfolgreich, da das Schneiden und Zusammenlegen noch von Hand erfolgen musste. Erst als Walton 1890 einen Weg zur maschinellen Erzeugung von Inlaid-Linoleum fand, stand dessen Erfolg nichts mehr im Weg. Walton gründete 1894 die Greenwich Inlaid Linoleum Company, die sich auf diese Linoleumform spezialisierte.[13][47]
Frühes Design
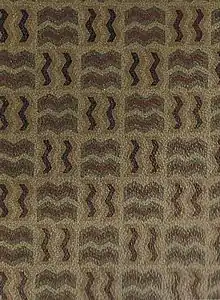
Wenn in den ersten Jahrzehnten Linoleum überhaupt gestaltet wurde, orientierten sich die zu dieser Zeit federführenden englischen Hersteller in der Regel am Publikumsgeschmack ihrer konservativen Heimatmärkte, die wenigen Produzenten in anderen Ländern wie den USA oder Frankreich wiederum schauten meist nach England. Mit der Absicht, das Linoleum zur Erhöhung der Akzeptanz optisch aufzuwerten, wurden besonders hochwertige oder wertvolle Materialien wie Orientteppiche, Steinböden oder Parkett imitiert. Diese Gestaltungsprinzipien blieben noch bis weit ins 20. Jahrhundert maßgeblich. 1912 konstatierte Gustav Gericke: „Frankreich pflegt in seinem Geschmack noch konservativer zu sein als England und den in der Entwicklung befindlichen neuen deutschen Stil gegenüber den historischen französischen Stilen als minderwertig, mindestens aber dem französischen Geschmack absolut nicht zusagend anzusehen. Auch die in Schweden, Norwegen, Italien, Österreich und der Schweiz bestehenden Fabriken, welche für den Wettbewerb mit Deutschland in Frage kommen, haben sich bislang darauf beschränkt, es England in der Musterung nachzutun.“[15][6]
Modernes Design ab 1900
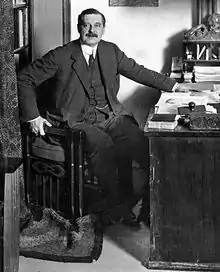
In Deutschland konnte sich ab der Jahrhundertwende ein modernerer Ansatz der Linoleumgestaltung durchsetzen, der Einflüsse aus Jugendstil, Art Déco und Neuer Sachlichkeit integrierte. Der erste Hersteller, der hier den Schulterschluss mit progressiven Künstlern für eine zeitgemäße Gestaltung des Linoleums suchte, waren die in Delmenhorst ansässigen Hansa-Werke. Bereits seit 1892 gab es hier einen künstlerischen Beirat, dem es allerdings lange nicht gelang, adäquate Vorlagen zu liefern. 1903 dann starteten die Hansa-Werke ein Preisausschreiben und setzten im Anschluss vier der Entwürfe um, darunter auch einen des Münchner Jugendstil-Künstlers Richard Riemerschmid.[48]
Hauptsächlich zurückzuführen ist der Durchbruch des modernen Designs in der deutschen Linoleumherstellung jedoch auf Gustav Gericke, der seit 1903 Direktor der 1892 gegründeten Anker-Werke Delmenhorst war. Gericke war nicht nur ein erfolgreicher Geschäftsmann, sondern war auch einem reformistischen, kunstverbundenen Ideal verbunden. Wahrscheinlich bereits direkt nach seinem Amtsantritt kontaktierte er den Industriedesigner Peter Behrens, der in den Folgejahren stark vom Jugendstil beeinflusst nicht nur Entwürfe für das Linoleum selbst vorlegte, sondern das gesamte Erscheinungsbild des Unternehmens vom Briefpapier an über Plakate, Broschüren bis hin zu Ausstellungspavillons überarbeitete. Ab 1906 dann verbreiterte sich die auf den sogenannten Künstlermustern basierende Produktpalette der Anker-Werke, neben Behrens entwarfen bedeutende Künstler wie Richard Riemerschmid, Bruno Paul, Albin Müller, Rudolf Alexander Schröder, Josef Hoffmann, Henry van de Velde, Willi Baumeister,[49] Lucian Bernhard, Johann Vincenz Cissarz sowie zahlreiche andere für die Anker-Werke.[48]
Das Engagement der Anker-Werke unter Gericke ging weit über das Erschließen einer Marktlücke hinaus. 1907 trat das Unternehmen dem neu gegründeten Deutschen Werkbund bei, dem einige seiner Gestalter angehörten, Gericke war dort zeitweise auch Vorstandsmitglied. Neubauten für das Werk zwischen 1910 und 1912 ließen sie von dem Bremer Architekten Heinz Stoffregen ausführen, seine neusachlichen Bauten fanden insbesondere bei modernen Architekten ebenso viel Beachtung wie die Künstlermuster der Kollektion. Die sehr grafischen und stark geometrischen Entwürfe sorgten dafür, dass die Anker-Werke nicht nur nach Marktanteilen, sondern auch künstlerisch als führend galten. Auch die anderen Werke in Delmenhorst konnten sich dieser Entwicklung nicht entziehen. Die Hansa-Werke veranstalteten 1911 ein weiteres Preisausschreiben und selbst die kleineren Schlüssel-Werke vertrieben unter anderem Entwürfe von Heinrich Vogeler.[48]
Wenngleich diese künstlerische Orientierung sich in Deutschland durchaus am Markt erfolgreich zeigte, sollte sie sich international als ein Hindernis erweisen. Gericke musste erkennen, dass „die moderne deutsche Mustergebung im Wettbewerb auf dem Auslandsmarkte bislang verhältnismäßig wenig Boden gewinnen konnte“, allein in der Schweiz, Österreich, Holland, Belgien und den skandinavischen Länder ließen sich „einige Erfolge […] erkennen“.[15]
Zu den wenigen Beispielen für gehobenes Design außerhalb Deutschlands gehörten einige Muster von Josef Hoffmann und weiteren Künstlern der Wiener Werkstätte, die von dem nordamerikanischen Unternehmen Armstrong Industries um 1915 in sein Programm aufgenommen wurden, sowie Arbeiten von Christopher Dresser für Frederick Walton.[47]
Werkstoff in der Architektur der Moderne
Mit dem Ausbruch des Ersten Weltkriegs 1914 und dem Kollaps der deutschen Linoleumindustrie endete diese intensive Phase der Zusammenarbeit zwischen den Linoleumwerken und zeitgenössischen Künstlern,[48] sie sollte sich erst Mitte der 1920er Jahre nach dem Zusammenschluss fast aller deutschen Werke zu den Deutschen Linoleum-Werken 1926 neu ergeben, dann aber vor allem unter architektonischen Vorzeichen.
Architekten wie Walter Gropius, Ludwig Mies van der Rohe oder Bruno Taut schätzten den Belag zwar als modern und hygienisch, gebrauchten aber ihren Konzepten gemäß einfarbiges und ungemustertes Linoleum in klaren Farben.[50] So gestaltete Mies van der Rohe zwischen 1928 und 1930 einen speziellen, rein elfenbeinweißen Linoleumbelag für den Bau der Villa Tugendhat in Brünn.[51] In großem Maßstab wurde dieser Belag in der Stuttgarter Weißenhofsiedlung eingesetzt, wo man 20 der 21 Bauten mit Linoleum auslegte.[52]
Häufig wurden verschiedene einfarbige Beläge verwendet, um den Raum zu strukturieren. Ideal dafür waren Linoleumfliesen. So benutzte Gropius in der Karlsruher Siedlung Dammerstock, wo es auch für die Wände und das Mobiliar verwendet wurde, den Belag als Raumteiler[53] und Bruno Taut legte in seinem zweiten Wohnhaus (Haus Taut II) 1927 in fast allen Räumen große, einfache Muster aus Linoleumfliesen.[54]
Mit der Machtergreifung der Nationalsozialisten 1933 sollte auch diese kurze Phase ihr Ende finden. Als die Produktion in der Nachkriegszeit wiederaufgenommen wurde, spielten gestalterische Fragen zunächst keine Rolle, zumeist wurde einfarbiges Linoleum verlangt. Erst 1957 wurde die Tradition der Künstlermuster mit der von Hertha Maria Witzemann gestalteten Kollektion Inlaid ’57 wiederaufgenommen. In Zusammenarbeit mit Architekten erschienen bei der DLW die beiden Muster Mikado und Konfetti. Aus Kostengründen wurde das Programm 1959 aber wieder eingestellt. Heutzutage gibt es keine Inlaid-Kollektionen mehr, Inlaid wird nur noch für Sonderaufträge hergestellt.[50]
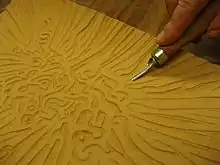
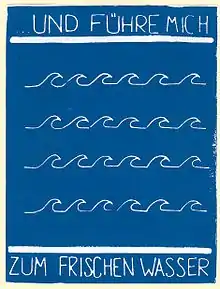
Linolschnitt
In der bildenden Kunst wird Linoleum für das Hochdruckverfahren des Linolschnitts verwendet, dabei wird ein Negativ in das später als Druckplatte dienende Linoleum geschnitten. Dieses weist, anders als das ähnlich gebrauchte Holz, keine Maserung auf, wodurch die Druckflächen klar und gleichmäßig sind, und die Linienführung ist weich, da es leicht schneidbar ist. Durch diese Eigenschaften begünstigt das Verfahren großflächige Bildelemente. Zur Einfärbung der Druckplatte dienen spezielle Farben, der Druck erfolgt meist auf Papier, aber auch auf Stoff.[55]
Wann zum ersten Mal mit Linoleum gedruckt wurde, ist nicht genau zu datieren. Häufig angeführt wird ein Drucker in Stettin, der 1890 auf diese Weise Tapeten bedruckt habe, die Behauptung ist jedoch unbelegt. Ab 1895 etablierte sich der Linolschnitt in Deutschland als Technik im schulischen Kunst- und Werkunterricht und wurde in den ersten Jahren des 20. Jahrhunderts auch von Künstlern genutzt. Der erste bekannte Kunst-Linoldruck stammt von Erich Heckel aus dem Jahre 1903, schnell folgten weitere Künstler, die von der neuen Technik teilweise intensiv Gebrauch machten, so Maurice de Vlaminck, Henri Matisse, Wassili Kandinsky, Gabriele Münter oder Christian Rohlfs. In den 1920er Jahren arbeiteten Konstruktivisten wie Heinrich Hoerle oder Gerd Arntz mit dem Linoldruck stark grafisch und formelhaft.[56]
In der Nachkriegszeit begannen Künstler dann den Linoldruck abseits der bisherigen Techniken zu erkunden. Wilhelm Lachnit ätzte Linoleum, Pablo Picasso löste sich vom klassischen Verfahren separater Arbeitsgänge und entwickelte den Einplatten-Farbdruck, bei dem er unter Einsatz zunehmend dunklerer Farben abwechselnd druckte und schnitt und im letzten Gang Konturen nachdruckte.[55] Den größten Teil des Spätwerks von Karl Rössing bilden Linolarbeiten, oft auch in Kombination mit der Offset-Technik. HAP Grieshaber nahm den Linolschnitt als eine zentrale Technik in sein Repertoire auf und schuf damit Großwerke wie die Josefslegende, eine 7 × 9 Meter große Altarwand. In der Kunst der Gegenwart sind vor allem Per Kirkeby und Markus Lüpertz, die Linoldruck und Kupferstich kombinierten, sowie Georg Baselitz, Jörg Immendorff, Norbert Prangenberg und Jess Walter zu nennen.[56]
Großflächigkeit und klare Farben machten den Linoldruck insbesondere bei volksnah orientierten Künstlern populär. Lateinamerikanische Kunstgruppen wie Taller de Gráfica Popular (Mexiko) oder der Club de la Estampa (Argentinien) nutzten ihn ebenso wie Künstler der Ostblock-Staaten. In der DDR spezialisierte sich Ingrid Goltzsche-Schwarz auf seine Anwendung.[55]
Andere, sehr selten eingesetzte Verfahren auf Linoleumbasis sind das sogenannte Cerataryt[57] sowie die Bronzo-Lino-Technik von Bruce Onobrakpeya,[58] bei dem Linoleum bronziert wird und so Reliefcharakter erhält.
Weiterführende Literatur
- Günther Förster, Josef Eiffler, Uwe Buchholz: Linoleum: Der Bodenbelag aus nachwachsenden Rohstoffen. (= Die Bibliothek der Technik, Band 107). Verlag Moderne Industrie, Landsberg am Lech 1995, ISBN 3-478-93123-1.
- Gerhard Kaldewei (Hrsg.): Linoleum – Geschichte, Design, Architektur 1882–2000. Hatje Cantz, Ostfildern-Ruit 2000, ISBN 3-7757-0962-2.
- Robert Würth: Linoldruck – Motivwahl, Schneiden, Drucken. Englisch Verlag/Christophorus Verlag Freiburg 2012, ISBN 978-3-86230-216-1.
- Silvia Tauss: Problematik der Erhaltung von Linoleumbelägen in situ – Am Beispiel Warenhaus „Cheesmeyer“ in Sissach. Diplomarbeit, HKB Bern 2007[6]
- Pamela H. Simpson: Comfortable, Durable, and Decorative: Linoleum’s Rise and Fall from Grace, in: APT Bulletin 30 (2/3), 1999, ISSN 0848-8525
- The Monopolies and Restrictive Practices Commission (Hrsg.): Report on the Supply of Linoleum (= HC 366, 1955–56). London 1956 (Online (Memento vom 27. September 2011 im Internet Archive))
Weblinks
- MATERIAL ARCHIV: Linoleum – Umfangreiche Materialinformationen und Bilder
- Video: Herstellung von Linoleum
- Vox: Linoleum flooring is cool, actually auf YouTube
Einzelnachweise
- Harald Olbrich (Hrsg.): Lexikon der Kunst, Band IV. E. A. Seemann Verlag, Leipzig 1992, S. 349–350
- Eisenbahndirektion Mainz (Hrsg.): Amtsblatt der Königlich Preußischen und Großherzoglich Hessischen Eisenbahndirektion in Mainz, 9. April 1904, Nr. 19. Bekanntmachung Nr. 171, S. 279: Linoleum darf als Fußbodenbelag in Eisenbahner-Dienstwohnungen nur mit höherer Genehmigung verlegt werden.
- Günther Förster, Josef Eiffler, Uwe Buchholz: Linoleum: Der Bodenbelag aus nachwachsenden Rohstoffen. Die Bibliothek der Technik, Band 107. Verlag Moderne Industrie, Landsberg/Lech 1995, ISBN 3-478-93123-1.
- Torsten Ziegler: Wachstuch, Fußtapete, Kamptulikon, Korkteppich: Linoleum – Der Beginn des idealen Bodenbelags. In: Gerhard Kaldewei (Hrsg.): Linoleum – Geschichte, Design, Architektur 1882–2000, 2000, ISBN 3-7757-0962-2, S. 32–47.
- Hi.: Unser Jute-Gewebe in der Linoleum-Herstellung. In: Die Brücke. Werkzeitung der Jute-Spinnerei und Weberei Bremen/Delmenhorst, 10. Jg., Nr. 6, 1953, Reprint in: Gerhard Kaldewei (Hrsg.): Linoleum – Geschichte, Design, Architektur 1882–2000, 2000, ISBN 3-7757-0962-2, S. 54–57.
- Silvia Tauss: Problematik der Erhaltung von Linoleumbelägen in situ – Am Beispiel Warenhaus „Cheesmeyer“ in Sissach. (PDF) Diplomarbeit, Bern. (Nicht mehr online verfügbar.) In: hkb.bfh.ch. 2007, ehemals im Original; abgerufen am 2. Januar 2022. (Seite nicht mehr abrufbar, Suche in Webarchiven)
- Sachverständigenseminar des ZVPF in Kassel – PU-Beschichtung im Fokus. In: FussbodenTechnik, 05/06, raumausstattung.de abgerufen am 30. September 2008
- Darstellung bei Standards Direct mit assoziierten Normen; standardsdirect.org abgerufen am 30. September 2008
- Linoleum Böden
- Pamela H. Simpson: Comfortable, Durable, and Decorative: Linoleum’s Rise and Fall from Grace. APT Bulletin 30 (2/3), 1999; Seiten 17–24.
- Anne Pimlott Baker: Nairn, Sir Michael Barker, first baronet (1838–1915). In: Henry Colin Gray Matthew, Brian Harrison (Hrsg.): Oxford Dictionary of National Biography, from the earliest times to the year 2000 (ODNB). Oxford University Press, Oxford 2004, ISBN 0-19-861411-X, (oxforddnb.com Lizenz erforderlich), Stand: 2004, abgerufen am 30. September 2008.
- Kamptulĭkon. In: Heinrich August Pierer, Julius Löbe (Hrsg.): Universal-Lexikon der Gegenwart und Vergangenheit. 4. Auflage. Band 19. Altenburg 1865, S. 858 (zeno.org).
- Anne Pimlott Baker: Frederick Edward Walton. In: Henry Colin Gray Matthew, Brian Harrison (Hrsg.): Oxford Dictionary of National Biography, from the earliest times to the year 2000 (ODNB). Oxford University Press, Oxford 2004, ISBN 0-19-861411-X, (oxforddnb.com Lizenz erforderlich), Stand: 2004, abgerufen am 30. September 2008.
- Linoleum Manufacture In: The Mechanics Magazine, 7. April 1865, S. 216/217
- Gustav Gericke: Das Deutsche Linoleum auf dem Weltmarkte. In: Die Durchgeistigung der deutschen Arbeit – Jahrbuch des Deutschen Werkbundes 1912, Jena, 1912, Reprint in: Gerhard Kaldewei (Hrsg.): Linoleum – Geschichte, Design, Architektur 1882–2000, 2000, ISBN 3-7757-0962-2, S. 116–119.
- Continentale Linoleum Union (Hrsg.): Der europäische Linoleum-Konzern, Basel, Wever & Co, 1928, S. 5, zitiert nach: Silvia Tauss: Problematik der Erhaltung von Linoleumbelägen in situ – Am Beispiel Warenhaus „Cheesmeyer“ in Sissach, Diplomarbeit, Bern, 2007, S. 22
- Daten nach Karlheinz Müller, B2B Industriemarktforschung GmbH; Offizielle Datenaufnahme für die Linoleumindustrie, abgesichert durch Daten des Statistischen Bundesamtes Deutschland.
- „By 1939 the L.M.A, and all the important Continental linoleum manufacturers were parties to formal Convention Agreements covering sales of linoleum and floorcloth in all markets except the United States.“ Report on the Supply of Linoleum. HC 366. (Memento vom 23. Oktober 2008 im Internet Archive; PDF; 73 kB) Competition Commission London, 1955–1956, S. 35; abgerufen am 30. September 2008
- Report on the Supply of Linoleum. HC 366. (Memento vom 23. Oktober 2008 im Internet Archive; PDF; 73 kB) Competition Commission London, 1955–1956, S. 35; abgerufen am 30. September 2008
- Birgit Geiger: Zielgerichtet den Großhandel unterstützen – Marktanteile bei Linoleum gewinnen im wichtigsten Markt Deutschland. In: eurodecor, 12-05/01-06, S. 22–23; eurodecor.de (Memento vom 9. Mai 2013 im Internet Archive; PDF; 2,0 MB) abgerufen am 30. September 2008
- Tarkett Sommer investiert in Linoleum In: BTH Heimtex, 06/03
- Report on the Supply of Linoleum. HC 366, 1955–56 competition-commission.org.uk (Memento vom 24. Oktober 2007 im Internet Archive; PDF; 345 kB) Competition Commission London, S. 12; abgerufen am 30. September 2008
- Report on the Supply of Linoleum. HC 366. (Memento vom 20. September 2008 im Internet Archive; PDF; 310 kB) Competition Commission London, 1955–1956, S. 2–3; abgerufen am 30. September 2008
- Report on the Supply of Linoleum. HC 366. (Memento vom 23. Oktober 2008 im Internet Archive; PDF; 1,8 MB) Competition Commission London, 1955–1956, S. 104; abgerufen am 30. September 2008
- All Change In The Town Centre (1960–1969). (Memento vom 15. Juni 2009 im Internet Archive) fifetoday.co.uk; abgerufen am 25. September 2008
- Makers Biography des Historic Houses Trust. (Nicht mehr online verfügbar.) In: hht.net.au. Ehemals im Original; abgerufen am 2. Januar 2022. (Seite nicht mehr abrufbar, Suche in Webarchiven)
- Siehe auf der Website des Unternehmens (Memento vom 24. August 2007 im Internet Archive) dort auch das herunterladbare Dokument The History of Forbo Nairn; abgerufen am 30. September 2008
- Floorcloth. In: The Carpet Trade, 10, Oktober 1879. Nach: Pamela H. Simpson: Comfortable, Durable, and Decorative: Linoleum’s Rise and Fall from Grace. In: APT Bulletin, 30 (2/3), 1999, S. 17–24.
- W. H. Morton Cameron: Canadian register of commerce and industry. 1959; Auszug zu Dominion Oilcloth & Linoleum Co. Online. (Memento vom 2. Dezember 2008 im Internet Archive) abgerufen am 28. September 2008
- Report on the Supply of Linoleum. HC 366. (Memento vom 20. September 2008 im Internet Archive; PDF; 244 kB) Competition Commission London, 1955–1956, S. 4–5; abgerufen am 30. September 2008
- Die Geschichte von Tarkett. Unternehmens-Website der FieldTurf Tarkett; abgerufen am 28. September 2008
- Anonymus: Domco. Company Profile. In: Flooring, Januar 2001, allbusiness.com (Memento vom 1. Dezember 2008 im Internet Archive) abgerufen am 28. September 2008
- Roland A. Hellmann: Aufstieg, Fall und Renaissance eines Fußbodenklassikers. Die Geschichte des Linoleums in Deutschland. In: Gerhard Kaldewei (Hrsg.): Linoleum. Geschichte, Design, Architektur 1882–2000. 2000, ISBN 3-7757-0962-2, S. 48–53.
- Statistisches Bundesamt (Hrsg.): Die industrielle Produktion 1951–1955. (= Die Industrie der Bundesrepublik Deutschland, Sonderheft 11.) Stuttgart, S. 61.
- Bestandsbeschreibung Abteilung 58 Rheinische Linoleumwerke Bedburg. (PDF) Stiftung Rheinisch-Westfälisches Wirtschaftsarchiv zu Köln; abgerufen am 11. Mai 2014
- DDP: Linoleum ist wieder im Kommen. In: Die Welt, 28. Oktober 2003.
- Die Verbrauchsentwicklung diverser Bodenbeläge in der BRD. Website des Bundesverbands Großhandel Heim & Farbe e. V.; abgerufen am 30. September 2008
- Silvia Bombara: Il peso della storia. Narni e l’industria. (PDF) (Nicht mehr online verfügbar.) In: provincia.terni.it. Ehemals im Original; abgerufen am 2. Januar 2022. (Seite nicht mehr abrufbar, Suche in Webarchiven) . In: Comune di Narni (Hrsg.): Lavoro e formazione - Le aziende narnesi parlano, o. J. (2007/2008), S. 20–26
- Michael Wortmann: Ausländische Direktinvestitionen und Arbeitsplatzexport? Eine Untersuchung des externen und internen Auslandswachstums deutscher Unternehmen. (PDF) (Nicht mehr online verfügbar.) In: wzb.eu. Ehemals im Original; abgerufen am 2. Januar 2022. (Seite nicht mehr abrufbar, Suche in Webarchiven) . FAST-Studie, Nr. 32, Berlin 2002, S. 60
- Ein Jahrhundert Tätigkeit. (Memento vom 9. Oktober 2011 im Internet Archive) Unternehmens-Website der Forbo-Giubiasco SA; abgerufen am 5. Oktober 2011
- Pasquale Genasci: Forbo. In: Historisches Lexikon der Schweiz. 2. Februar 2005, abgerufen am 30. September 2008.
- Maura Huig: Kaars Sijpesteijns eerste linoleumfabriek (1898–1903). In: Met Stoom, Nr. 34, Dezember 1999, zaans-industrieel-erfgoed.nl abgerufen am 29. September 2008
- Jan Schoen: Honderd jaar linoleum in Nederland. In: Met Stoom, Nr. 34, Dezember 1999; aans-industrieel-erfgoed.nl abgerufen am 29. September 2008
- Jahrbuch der österreichischen Industrie. Compassverlag, 1912; S. 541; Christian Benesch: Die "Erste österreichische Linoleumfabrik" in Triest. Zentraleuropäisches digitales wirtschafts- und gesellschaftshistorisches interaktives Archiv.
- ÖLW: Unternehmenschronik. (Nicht mehr online verfügbar.) In: oelw.at. Ehemals im Original; abgerufen am 2. Januar 2022. (Seite nicht mehr abrufbar, Suche in Webarchiven)
- “… inlay in somewhat fuzzy-looking patterns, but it could not imitate the precision of a tile design”. Pamela H. Simpson: Linoleum and Lincrusta: The Democratic Coverings for Floors and Walls. In: Perspectives in Vernacular Architecture, Vol. 7: Exploring Everyday Landscapes, 1997, S. 283
- Pamela H. Simpson: Linoleum and Lincrusta: The Democratic Coverings for Floors and Walls. In: Perspectives in Vernacular Architecture, Vol. 7, Exploring Everyday Landscapes, 1997
- Nils Aschenbeck: Im Zeitalter der Hygiene. In: Gerhard Kaldewei (Hrsg.): Linoleum – Geschichte, Design, Architektur 1882–2000, 2000, ISBN 3-7757-0962-2, S. 140–161.
- Anhang In: Armstrong DLW (Hrsg.): DLW Referenzen, 2008, S. 248
- Gerhard Kaldewei: Linoleum – Kunst und Industrie 1882–2000 – Eine Einführung. In: Gerhard Kaldewei (Hrsg.): Linoleum – Geschichte, Design, Architektur 1882–2000, 2000, ISBN 3-7757-0962-2
- Julia Franke: Linoleum zum historischen Design des Bodenbelags um 1900 In: Gerhard Kaldewei (Hrsg.): Linoleum – Geschichte, Design, Architektur 1882–2000, 2000, ISBN 3-7757-0962-2, S. 130–137.
- Karin Schulte: Linoleum und der Ausstellungsraum der DLW auf der Werkbund-Ausstellung „Die Wohnung“ 1927 in Stuttgart. In: Gerhard Kaldewei (Hrsg.): Linoleum – Geschichte, Design, Architektur 1882–2000, 2000, ISBN 3-7757-0962-2, S. 198–207.
- Anonymus: Die Dammerstock-Siedlung in Karlsruhe. In: Nachrichten der Deutschen Linoleum-Werke AG Nr. 12/1930, Reprint in: Gerhard Kaldewei (Hrsg.): Linoleum – Geschichte, Design, Architektur 1882–2000, 2000, ISBN 3-7757-0962-2, S. 168–170.
- Bettina Zöller-Stock: Zu Innenraumentwürfen des Architekten Bruno Taut In: Gerhard Kaldewei (Hrsg.): Linoleum – Geschichte, Design, Architektur 1882–2000, 2000, ISBN 3-7757-0962-2, S. 130–137.
- Harald Olbrich (Hrsg.): Lexikon der Kunst – Architektur, Bildende Kunst, Angewandte Kunst, Industrieformgestaltung, Kunsttheorie: Linol(eum)schnitt. Band 4. ISBN 3-363-00286-6, S. 349–350.
- Andrea Tietze: Der Linolschnitt in der Geschichte und Kunst der Moderne. In: Gerhard Kaldewei (Hrsg.): Linoleum – Geschichte, Design, Architektur 1882–2000, 2000, ISBN 3-7757-0962-2, S. 68–93.
- Harald Olbrich (Hrsg.): Lexikon der Kunst – Architektur, Bildende Kunst, Angewandte Kunst, Industrieformgestaltung, Kunsttheorie: Cerataryt, Band 1, ISBN 3-363-00286-6, S. 789.
- Harald Olbrich (Hrsg.): Lexikon der Kunst – Architektur, Bildende Kunst, Angewandte Kunst, Industrieformgestaltung, Kunsttheorie: Onobrakpeya, Band 5, ISBN 3-363-00286-6, S. 287.