Kohlenstofffaser
Kohlenstofffasern – im allgemeinen Sprachgebrauch auch verkürzt Kohlefasern[1] oder (aus dem Englischen carbon fibers lehnübersetzt) Carbon- bzw. Karbonfasern genannt – sind industriell gefertigte Fasern aus kohlenstoffhaltigen Ausgangsmaterialien, die durch an den Rohstoff angepasste chemische Reaktionen in graphitartig angeordneten Kohlenstoff umgewandelt werden. Man unterscheidet isotrope und anisotrope Typen: Isotrope Fasern besitzen nur geringe Festigkeiten und geringere technische Bedeutung, anisotrope Fasern zeigen hohe Festigkeiten und Steifigkeiten bei gleichzeitig geringer Bruchdehnung in axialer Richtung.
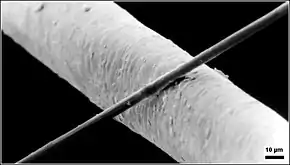
Die wichtigste Eigenschaft von Kohlenstofffasern als Versteifungskomponente für den Leichtbau ist der E-Modul; die E-Modulwerte der besten Fasern liegen nahe bei dem theoretischen E-Modul von Graphit in a-Richtung.[2]
Eine Kohlenstoff-Faser oder auch -Filament hat einen Durchmesser von etwa 5–9 Mikrometer. Üblicherweise werden 1.000 bis 24.000 Filamente zu einem Multifilamentgarn (Roving) zusammengefasst, das aufgespult wird. Die Weiterverarbeitung zu textilen Halbzeugen wie z. B. Geweben, Geflechten oder Multiaxialgelegen erfolgt auf Webmaschinen, Flechtmaschinen oder Multiaxial-Wirkmaschinen bzw. im Bereich der Herstellung von faserverstärkten Kunststoffen direkt auf Prepreganlagen, Strangziehanlagen (Pultrusionsanlagen) oder Wickelmaschinen.
Als Kurzschnittfasern können sie Polymeren beigemischt und über Extruder- und Spritzgussanlagen zu Kunststoffbauteilen verarbeitet werden. Neben diesen Niederfilament-Typen gibt es auch sogenannte HT-Typen mit 120.000 bis 400.000 Einzelfasern, die hauptsächlich zu Kurzschnittfasern, aber auch zu textilen Gelegen verarbeitet werden. Es ist auch möglich, solche Heavy Tows mit Subtows, z. B. in der Form von siebenmal 60.000 Einzelfilamenten, herzustellen.
Die Fasern werden überwiegend zur Herstellung von kohlenstofffaserverstärktem Kunststoff (CFK = C-Faser verstärkter Kunststoff) benutzt. Aus dem Englischen stammend wird auch die Abkürzung CFRP (amerikanisches englisch Carbon Fiber Reinforced Plastic) benutzt.
Eigenschaften
Typische Eigenschaften von HT-Kohlenstofffasern | |
---|---|
Dichte | 1,8 g/cm³ |
Filamentdurchmesser | 6 µm |
Zugfestigkeit | 3530 MPa (N/mm²) |
Zug-E-Modul | 230 GPa |
Bruchdehnung | 1,5 % |
Typische Eigenschaften von UMS-Kohlenstofffasern | |
---|---|
Dichte | 1,8 g/cm³ |
Filamentdurchmesser | 6 µm |
Zugfestigkeit | 4560 MPa (N/mm²) |
Zug-E-Modul | 395 GPa |
Bruchdehnung | 1,1 % |
Elektronegativität (EN) χ | 2,50 |
Kohlenstofffasern sind elektrisch und thermisch sehr gut leitfähig, die Elektronegativität EN hat mit 2,50 einen sehr hohen Wert. Die Differenz zu Eisen (EN=1,64) ist mit 0,86 sehr hoch, was unter Vorhandensein eines Elektrolyten bereits erheblich korrosiv wirkt. Zum Vergleich ist die Differenz bei der Werkstoffpaarung Eisen zu Aluminium (EN=1,47) nur 0,17. Kohlenstofffasern haben zudem bei niedrigeren Temperaturen in Längsrichtung einen negativen Wärmeausdehnungskoeffizienten. Bei Erwärmung werden sie deswegen anfangs kürzer und dicker.
Aus den beiden vorgenannten Eigenschaften ergibt sich die zwingende Notwendigkeit, kohlefaserbasierte Bauteile von anderen metallischen Bauteilen sowohl mechanisch als auch elektrisch zu isolieren, wenn im Einsatzfall Temperaturschwankungen und Kontakt zu Außenluft, Wasser und im Besonderen zu Seewasser sowie anderen Elektrolyten (zum Beispiel Schmelzwasser mit Streusalz im Straßenverkehr) zu erwarten ist. Das Voranschreiten der Elektrokorrosion von Eisen, welches in direktem Kontakt zu Kohlefasern steht, ist unter einem geeigneten Elektrolyt hoch.
- Spezifische Wärmekapazität: 710 J/(kg·K)
- Wärmeleitfähigkeit: 17 W/(m·K)
- Wärmeausdehnungskoeffizient: −0,1·10−6/K
- Spezifischer elektrischer Widerstand: 1,6·10−5 Ohm·m[3] (= 16 Ω · mm2/m)
- HT – hochfest (High Tenacity)
- UHT – sehr hochfest (Ultra High Tenacity)
- LM – Low Modulus
- IM – intermediate (Intermediate Modulus)
- HM – hochsteif (High Modulus)
- UM – (Ultra Modulus)
- UHM – (Ultra High Modulus)
- UMS – (Ultra Modulus Strength)
- HMS – hochsteif/hochfest (High Modulus / High Strain)
Das Spektrum der Eigenschaften ist entsprechend dieser Liste breit: die verfügbaren Zugfestigkeiten liegen im Bereich von etwa 3500 MPa bis 7000 MPa, die Zug-Steifigkeiten zwischen 230 GPa und fast 600 GPa und die Bruchdehnungen liegen bei hohen Steifigkeiten teils unter 1 %, während sie bei niedrigen Steifigkeiten verbunden mit höheren Festigkeiten bis zu 2 % betragen können.[6]
Herstellung
Thomas Alva Edison erhielt bereits 1881 ein Patent für die von ihm entwickelte Kohlenstofffaserglühlampe mit Glühfäden aus pyrolysierten Bambusfasern.[7]
Ein großer Schritt gelang 1963 mit der Herstellung von Fasern mit gerichteten Kristallstrukturen im englischen Royal Aircraft Establishment.[8][9]
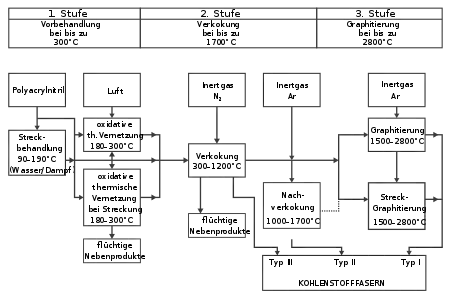
Typ III: IM-Faser und Typ II: HT-Faser
Typ I: HM-Faser
Kohlenstofffasern werden aus organischen Ausgangsmaterialien hergestellt. Es kommen in erster Linie solche Verbindungen in Frage, die sich zunächst in eine unschmelzbare Zwischenstufe umwandeln lassen und anschließend unter Formerhalt in einem Pyrolyseprozess zum Kohlenstoff carbonisiert werden können. Durch Verstreckung (Anlegen einer Zugspannung) bei diesem Temperaturbehandlungsschritt lässt sich die Orientierung der atomaren Struktur in den Fasern so verändern, dass bei der Carbonisierung höhere Festigkeiten und Steifigkeiten der Fasern erreicht werden.
Bei dieser Carbonisierungsbehandlung werden alle Elemente bis auf den Hauptanteil Kohlenstoff gasförmig abgespalten. Der relative Kohlenstoffanteil steigt mit zunehmender Temperatur, die üblicherweise im Bereich von 1300 bis 1500 °C liegt. Damit wird ein Kohlenstoffanteil von 96 bis 98 Gewichtsprozenten erreicht.
Von Graphitierung spricht man oberhalb 1800 °C. Hierbei wird vor allem die Struktur der graphitischen Kohlenstoffschichten mehr und mehr perfektioniert. Der Schichtebenenabstand zwischen diesen Kohlenstoffschichten bleibt jedoch über dem vom eigentlichen Graphit bekannten Wert. Deshalb ist der im englischen Sprachraum übliche Begriff „graphite fiber (fibre)“ streng genommen nicht korrekt. Dies gilt auch für die im deutschen Sprachraum verwendeten Begriffe „Graphitfaser“ und „Kohlefaser“.
Durch die Glühbehandlung steigt der E-Modul wegen der Strukturannäherung an das Graphit-Gitter, die Festigkeit vermindert sich dadurch jedoch.[2]
Die Strukturvielfalt der Fasern mit der großen Bandbreite an Eigenschaften resultiert aus der über die Herstellparameter steuerbaren Anisotropie der graphitischen Schichten. Bei Endlosfasern erreicht man je nach Fasertyp nahezu den theoretischen Steifigkeitswert, jedoch üblicherweise nur 2–4 % der theoretischen Festigkeit. Bei Fasern, die abweichend von der oben beschriebenen Methode aus der Gasphase abgeschieden werden (sogenannte Whisker mit sehr kurzer Länge), sind deutlich höhere Festigkeiten erreichbar.
Es gibt heute drei etablierte Ausgangsmaterialien für Endlosfasern aus Kohlenstoff:[2]
Rayon/Viskose (Cellulose)
Die auf Cellulosebasis über das Viskoseverfahren hergestellten Viskosefasern sind hier das Ausgangsmaterial für die Kohlenstofffasern. Diese zeigen aufgrund des Ausgangsmaterials keine perfekte Kohlenstoffstruktur. Sie haben damit eine vergleichsweise niedrige thermische und elektrische Leitfähigkeit. (In der Verwendung als Glühfaden war der hohe ohmsche Widerstand allerdings günstig.) Sie werden deshalb überwiegend als (unter Luft/Sauerstoffabschluss) thermisch hochbelastbare Isolierwerkstoffe eingesetzt, zum Beispiel im Ofenbau.
Polyacrylnitril (PAN)
Der größte Teil der heute gebräuchlichen Hochleistungsfasern (HT/IM) wird durch Stabilisierungsreaktionen an Luft und anschließende Pyrolyse unter Schutzgas aus Polyacrylnitril gefertigt.[10] Ihr wesentliches Merkmal ist die hohe Zugfestigkeit. Man unterscheidet Niederfilament- und Multifilamentgarne (englisch HeavyTow). Bei letzteren werden die günstigeren Fertigungstechnologien der Textilindustrie genutzt, daher sind sie am kostengünstigsten.
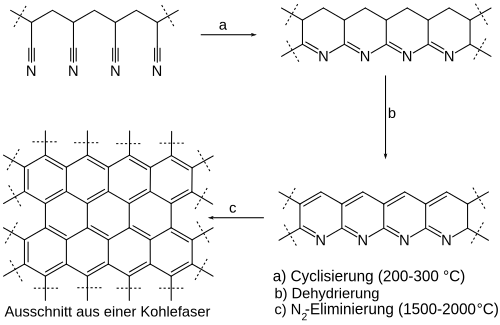
Pech (unterschiedlicher Herkunft)
Pech ist als Ausgangsstoff wesentlich billiger als PAN, aber die Reinigungs- und Aufbereitungskosten sind so hoch, dass Fasern aus PAN nach wie vor preiswerter sind.
Wird das Pech lediglich geschmolzen, versponnen und carbonisiert, erhält man isotrope Kohlenstofffasern mit geringeren Festigkeitswerten. Erst die Überführung in die sogenannte Mesophase durch eine Hydrierungsbehandlung erlaubt eine Orientierung der Kohlenstoff-Netzebenen entlang der Faserachse durch Verstreckung während des Herstellprozesses.
Dies erlaubt dann auch die Herstellung von Fasern mit hoher Steifigkeit (HM). Bei gleichzeitiger hoher Zugfestigkeit (HMS) werden diese Fasern aus Kostengründen nur in Spezialanwendungen eingesetzt.
Weiterverarbeitung
Zur Weiterverarbeitung werden die Fasern zu sogenannten Filamentgarnen zusammengefasst. Gängig sind hier die Typen mit 67 tex (1 K), 200 tex (3 K), 400 tex (6 K), 800 tex (12 K) und 1600 tex (24 K), Rovings mit einer Filamentenzahl von mehr als 24 K, z. B. 50 K, 100 K oder 400 K bezeichnet man als Heavy Tows. Die Angabe 200 tex steht dabei für ein Gewicht von (200 g)/(1000 m) und 1 K bedeutet, dass 1000 Filamente zu einem Garn zusammengefasst sind.[11]
Die gröberen Garne (bei Textilglas „Rovings“ genannt) kommen beispielsweise als Verstärkungsfasern für Flächengebilde zum Einsatz. Im Flugzeugbau werden mit Harz vorimprägnierte Garnscharen oder Gewebe, die sogenannten Prepregs, mit geringem oder mittlerem Flächengewicht verwendet. Das gängigste im Automobilbau verwendete Produkt ist ein multiaxiales Flächengebilde.
Anwendung
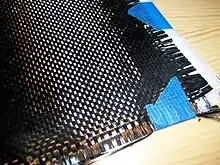
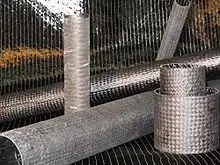
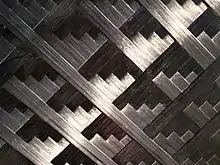
Um die mechanischen Eigenschaften der Fasern nutzen zu können, werden sie bei der Herstellung von Faserverbundwerkstoffen, insbesondere Faser-Kunststoff-Verbunden, und seit einiger Zeit auch bei keramischen Faserverbundwerkstoffen weiterverarbeitet. Dabei nimmt die Bedeutung der kohlenstofffaserverstärkten Kunststoffe im Hochleistungsmaschinenbau seit einigen Jahren deutlich zu, bereits vorher kamen sie im Flugzeugbau zur Anwendung. Im allgemeinen Sprachgebrauch, insbesondere bei Sportgeräten aller Sportarten, stehen Begriffe wie Carbon, Graphit(e) und Kohlenstofffaser typischerweise für Kohlenstofffaser-verstärkte duromere Kunststoffe.
Kohlenstofffasern zeichnen sich im Vergleich zu Glasfasern durch ein geringeres Gewicht und einen höheren Preis aus. Sie werden daher vor allem in der Luft- und Raumfahrt sowie bei Sportgeräten (zum Beispiel Angelruten, Rennrädern, Mountainbikes, Tennisschlägern, Speedskates, Ruderbooten, Windsurfausrüstung) eingesetzt. So sind zum Beispiel auch das sogenannte Monocoque sowie weitere Teile von Formel-1-Rennwagen aus kohlenstofffaserverstärktem Kunststoff hergestellt.
Beispiele aus der Luftfahrt sind das Seitenleitwerk des Airbus A380 oder der Rumpf der Boeing 787.
In England wird eine Brücke aus einem mit Kohlenstofffasern verstärkten Beton gefertigt, die enormen Zug- und Druckkräften standhält.[12][13]
Kohlenstofffaserverstärkter Kohlenstoff wird vor allem in der Raumfahrt als Material für Hitzeschilde oder Boosterdüsen verwendet, jedoch findet er auch Anwendung in der Hohlglasindustrie als Ersatz für Asbest oder als Auskleidung für Fusionsreaktoren.
Weitverbreitet sind kohlenstofffaserverstärkte Kunststoffbauteile inzwischen in einigen Fahrrädern, wie z. B. Rennrädern/Mountainbikes. Hier werden inzwischen nicht nur die Rahmen, sondern zunehmend auch andere Komponenten wie Kurbeln, Laufräder, Lenker, Sattelstützen u. a. aus CFK gefertigt.
Eine weitere Anwendung finden Kohlenstofffasern im Bereich des Bogenschießens. Moderne Sportpfeilschäfte werden mit Kohlenstofffaserverstärkung hergestellt, die sich durch ihr geringes Gewicht hervorragend für weite Distanzen eignen.
In der Wasserski-Fertigung, bei hochwertigen Angelruten und bei Bögen für Streichinstrumente und sogar bei Streichinstrumenten selbst finden Kohlenstofffasern eine weitere Anwendungsmöglichkeit.
In der Zahnheilkunde werden Kohlenstofffasern zur Schienung von Zähnen, aber auch in Stiftform zur Retentionsgewinnung von Aufbauten für zerstörte Zähne in Wurzeln eingeklebt.
Militärisch wird die elektrische Leitfähigkeit sowie die geringe Größe (Durchmesser) von Kohlenstofffasern in Graphitbomben ausgenutzt. Die in einer Bombe eingebrachten kurzen Kohlenstoff-Faserabschnitte werden durch eine Zerlegerladung über dem jeweiligen Objekt verteilt. Die Fasern werden durch Luftströmung, sowie begünstigt durch Ventilatoren oder Lüftungs- und Kühlsysteme, in elektrischen Anlagen und Geräten verteilt und erreichen selbst unzugängliche Stellen im Inneren von Computern. Die hervorgerufenen Kurzschlüsse führen dann zum Versagen auch großer Anlagen, wenn die Steuerungseinrichtungen betroffen sind.
Prüfung von mit Kohlenstofffasern verstärkten Werkstoffen
Zur Prüfung von kohlenstofffaser-verstärkten Werkstoffen werden sowohl zerstörende als auch zerstörungsfreie Prüfverfahren angewendet. Mit zerstörender Prüfung (z. B. Kerbschlagtest) wird beispielsweise die Bruchlast des Materials oder das Bruchverhalten geprüft. Zerstörungsfreie Prüfverfahren, wie zum Beispiel Ultraschall- oder akustische Prüfung, werden vorrangig zur Prüfung von Defekten im Polymeranteil des Komposits (Delaminationen, Lunker, Blasen) verwendet.
Effekte in der Faserstruktur selbst (Gassen, Risse, Ondulationen, Falten, Überlappungen, Faseransammlungen oder Fehlorientierungen) werden mit Hochfrequenz-Wirbelstromverfahren gemessen.[14]
Ähnliche Wirbelstromverfahren werden angewendet zur lokalen Bestimmung des Flächengewichts in CFK-Bauteilen und Textilen.
Hersteller
Die größten Hersteller nach Produktionskapazität in 1000 t (Stand 2018) sind:[15]
Hersteller | Kapazität |
---|---|
Toray (mit Zoltek) | 47,5 |
SGL Carbon | 15 |
MCCFC | 14,3 |
TohoTenax | 12,6 |
Hexcel | 12,5 |
Formosa Plastics | 8,8 |
Solvay (Cytec) | 7,0 |
Zhongfu-Shenying | 6 |
Hengshen Fibre Material | 5 |
DowAksa | 3,6 |
Entsorgung und Recycling
Die Entsorgung und das Recycling von Kohlenstofffaser-haltigen Materialien befinden sich noch in der Entwicklung und sind nicht final gelöst. Es gibt verschiedene Ansätze, die verfolgt werden, von einem Wiedereinsatz der Faser in Faserverstärkten Bauteilen bis hin zu einer thermischen Verwertung.[16] Das Faserinstitut Bremen e. V. hat 2008–2010 mit einer Technik experimentiert, bei der gerichtete Fasern mit einer Faserlänge von etwa 60 mm auf ein thermoplastische Polypropylen-Folie aufgetragen und so zu hochfesten Matten verpresst werden (sog. Organofolie).[17][18] Bei dieser Technik wie bei anderen Methoden des Recycling (z. B. bei der Produktion sogenannter Organobleche) ist der erste Schritt das Zerkleinern der Abfälle. Dafür können übliche mechanische Verfahren eingesetzt werden.[19] Dabei entstehen allerdings in geringen Mengen Stäube aus Fasern und Matrixmaterial. Diese Stäube sind unerwünscht, da sie sich nicht für ein Recycling eignen, die enthaltenen Fasern elektrisch leitfähig sind und zum Ausfall elektrischer Anlagen führen können.[20] Zudem sind Stäube gesundheitsschädlich, so dass entsprechende Schutzkleidung getragen werden muss. Durch die mechanische Bearbeitung von CFK entstehen allerdings keine „WHO-Fasern“ (Fasern die als potentiell krebserregend gelten).[21] Bei der thermischen Verwertung in Müllverbrennungsanlagen für Siedlungsabfälle ist die Verweilzeit der Abfälle in der heißen Zone der Anlagen in der Regel zu kurz, als dass ein vollständiger Abbrand der in einer Matrix eingebundenen Fasern erfolgen kann.[22] Dies kann zu technischen Problemen bei elektrostatischen Abscheidern führen.[20] In Sondermüllverbrennungsanlagen ist die Verweilzeit der Materialien größer, zudem sind die Temperaturen höher, trotzdem wurden in der Schlacke, die deponiert wird, Fasern gefunden, so dass mittels MVA keine vollständige Verwertung stattfindet.
Untersucht werden aktuell eine thermisch-stoffliche Verwertung beim Stahlrecycling und eine rein stoffliche bei der Calcium-Carbidherstellung im Lichtbogenofen und damit bei deutlich höheren Temperaturen.[16] Bei entsprechenden Pilot-Versuchen wurden die Fasern vollständig zersetzt und es konnte kein Faseraustrag nachgewiesen werden.[23]
Beim Recycling werden nach einer Faser-Matrix-Separation z. B. in kommerziellen Pyrolyse-Anlagen aus den Fasern gemahlene Fasern, Kurzfasern oder Vliese hergestellt.[24][25] Da ab Faserlängen von 3–4 cm quasi Endlosfasereigenschaften erreicht werden, können mit Faservliesen und Stapelfasern wieder hochwertige Produkte erzeugt werden.
Bei einer thermoplastischen Matrix können die Bauteile direkt geschreddert und wieder im Spritzguss eingesetzt werden, eine Fasermatrix-Separation ist nicht notwendig.
Weblinks
Einzelnachweise
- Hans-J. Koslowski: Chemiefaser – Lexikon; 12., erweiterte Auflage. Deutscher Fachverlag, Frankfurt am Main 2009, ISBN 978-3-87150-876-9, S. 118.
- Erich Fitzer, Arnold Kurt Fiedler, Dieter Jürgen: Zur Herstellung von Kohlenstoff-Fasern mit hohem Elastizitätsmodul und hoher Festigkeit. In: Chemie Ingenieur Technik. Band 43, Nr. 16, August 1971, S. 923–931, doi:10.1002/cite.330431607.
- wiki.r-g.de Faserverbundwerkstoffe (man beachte: 1 Ohmmeter = 100 Ohmzentimeter)
- Konrad Bergmeister: Kohlenstofffasern im Konstruktiven Ingenieurbau. 2003, Ernst & Sohn, S. 39
- Hauke Lengsfeld, Hendrik Mainka, Volker Altstädt: Carbonfasern – Herstellung, Anwendung, Verarbeitung.Hanser Verlag, München 2019, ISBN 978-3-446-45407-1, S. 54ff.
- Bernd Clauß: Fibers for Ceramic Matrix Composites in Ceramic Matrix Composites, Fiber Reinforced Ceramics and their Applications. Wiley-VCH, Weinheim 2008, ed. Walter Krenkel, ISBN 978-3-527-31361-7, S. 1ff.
- Patent US390462: Process of making carbon filaments. Veröffentlicht am 2. Oktober 1888, Erfinder: Thomas Alva Edison.
- Patent GB1110791: The production of carbon fibres. Angemeldet am 24. April 1964, veröffentlicht am 24. April 1968, Erfinder: William Johnson, Leslie Nathan Phillips, William Watt.
- New Materials make their mark. In: Nature. Band 219, Nr. 5156, 24. August 1968, S. 818–819, doi:10.1038/219818a0.
- How is Carbon Fiber Made? abgerufen am 29. Dezember 2017
- Hauke Lengsfeld, Hendrik Mainka, Volker Altstädt: Carbonfasern – Herstellung, Anwendung, Verarbeitung. Hanser Verlag, München 2019, ISBN 978-3-446-45407-1, S. 52.
- Vorlesungs-Skript zu faserverstärkten Brücken (geöffnet Mai 2018)
- Pressemeldung zu faserverstärkter Brücke (geöffnet Mai 2018)
- Methoden der zerstörungsfreien Carbonfaserprüfung (Englisch) SURAGUS GmbH. Abgerufen am 29. November 2014.
- Composites-Marktbericht 2018
- Tjark von Reden; Warzelhan: Aktuelle Entwicklungen im Bereich des Recyclings und Verwertung von CFK. In: 22. Internationales Dresdner Leichtbausymposium.
- Holger Fischer, Ralf Bäumer: Organofolien aus rezyklierten Kohlenstofffasern — neue Wege für CFK-Halbzeuge in der Serienproduktion. Vortrag, ThermoComp Chemnitz, 30. Juni 2011, online (PDF; 2,3 MB)
- Gerettet? In: VDI-Nachrichten, 10. Mai 2018.
- MAI Recycling - Entwicklung ressourceneffizienter CFK-Recyclingverfahren und Prozessketten für die künftige Bereitstellung qualitativ hochwertiger rC-Halbzeuge : Schlussbericht MAI Recycling
- Marco Limburg, Jan Stockschläder, Peter Quicker: Thermische Behandlung carbonfaserverstärkter Kunststoffe. : Gefahrstoffe – Reinhalt. Luft. 77, Nr. 5, 2017, ISSN 0949-8036, S. 198–208.
- N. Bienkowski, L. Hillermann, T. Streibel, J. Kortmann, F. Kopf, R. Zimmermann, P. Jehle: Bearbeitung von Carbonbeton – eine bauverfahrenstechnische und medizinische Betrachtung: DVI-Bautechnik, Jahresausgabe 2017/2018 s. 110 – 119.
- Marco Limburg, Peter Quicker: Kleine Teile, große Probleme. In: ReSource. 29, Nr. 2, 2016, ISSN 1866-9735, S. 54–58.
- Denny Schüppel, Jan Stockschläder, Tjark von Reden: End Of-Life CFRP as a Raw Material in Steel and of Calcium Carbide Production. In: European Conference on Composite Materials 2018 / Athen.
- Webseite von ELG. Abgerufen am 9. Juli 2018.
- Webseite CarboNXT. Abgerufen am 9. Juli 2018.
Literatur
Hauke Lengsfeld, Hendrik Mainka, Volker Altstädt: Carbonfasern – Herstellung, Anwendung, Verarbeitung.Hanser Verlag, München 2019, ISBN 978-3-446-45407-1.