Keramischer Faserverbundwerkstoff
Keramische Faserverbundwerkstoffe sind eine Werkstoffklasse innerhalb der Gruppe der Verbundwerkstoffe oder auch der technischen Keramiken. Sie sind charakterisiert durch eine zwischen Langfasern eingebettete Matrix aus normaler Keramik, die durch keramische Fasern verstärkt wird und so zur faserverstärkten Keramik, Verbundkeramik oder auch einfach Faserkeramik wird. In der deutschen Fachliteratur wird die Werkstoffklasse häufig auch auf Englisch als Ceramic Matrix Composites bezeichnet und mit CMC abgekürzt. Matrix und Fasern können im Prinzip aus allen bekannten keramischen Werkstoffen bestehen, wobei in diesem Zusammenhang auch Kohlenstoff als keramischer Werkstoff behandelt wird.
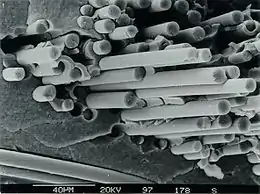
Foto: MT Aerospace, Augsburg
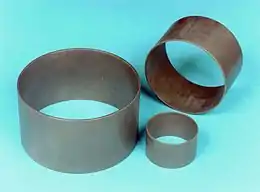
Foto: MT Aerospace AG, Augsburg
Der Artikel beschreibt die zurzeit industriell verfügbaren Verbundkeramiken mit ihren wichtigsten Herstellungsverfahren, wesentlichen Eigenschaften sowie einige Entwicklungs- und erfolgreiche Anwendungsbeispiele dieser relativ jungen Gruppe von Werkstoffen.
Einleitung
In Entwicklung und Anwendung von Verbundkeramik kommen zurzeit im Wesentlichen Kohlenstoff- und sogenannte Siliciumcarbid-Fasern zum Einsatz und in geringerem Umfang auch Fasern, die aus Aluminiumoxid (Al2O3) oder Mischkristallen aus Aluminiumoxid und Siliciumoxid (SiO2), sogenanntem Mullit, bestehen. Als Matrixmaterialien werden bei technischen Anwendungen zurzeit in der Hauptsache Aluminiumoxid, Mullit, Kohlenstoff und Siliciumcarbid eingesetzt (Lit.: W. Krenkel, 2003).
Die Motivation zur Entwicklung dieser Keramiken ist aus den Problemen entstanden, die sich beim Einsatz konventioneller technischer Keramiken wie Aluminiumoxid, Siliciumcarbid, Aluminiumnitrid, Siliciumnitrid oder Zirconium(IV)-oxid gezeigt haben: alle diese Werkstoffe zerbrechen leicht unter mechanischen oder thermomechanischen Belastungen, weil selbst kleine Fertigungsfehler oder Kratzer auf der Oberfläche zum Startpunkt eines Risses werden können. Einer Ausbreitung von Rissen wird, anders als bei Metallen (Stichwort: Duktilität), aber ähnlich wie bei Glas, nur ein sehr geringer Widerstand entgegengesetzt. Charakteristisch ist ein sprödes Bruchverhalten, das viele Anwendungen erschwert oder unmöglich macht. Entwicklungen, diese Eigenschaft durch Einbettung von Fremdpartikeln, einkristallinen Kurzfasern (sogenannten Whiskern) oder Scheibchen (sogenannten Platelets) in die Keramik zu verbessern, haben deren Risswiderstand nur begrenzt verbessern können, aber in einigen keramischen Schneidwerkzeugen Anwendung gefunden. Erst die Verwendung von Langfasern zur Verstärkung von Keramik hat diesen Risswiderstand drastisch erhöhen können und zu verbesserten Eigenschaften wie zum Beispiel erhöhter Dehnbarkeit, Bruchzähigkeit und Thermoschockbeständigkeit geführt, mit denen neue Anwendungsfelder erschlossen werden konnten und können.
Üblicherweise werden die so hergestellten Verbundkeramiken in der Form „Fasertyp/Matrixtyp“ abgekürzt. So steht „C/C“ zum Beispiel für Kohlenstofffaser-verstärkter Kohlenstoff oder „C/SiC“ für Kohlenstofffaser-verstärktes Siliciumcarbid. Soll das Herstellverfahren noch in diese Kurzbezeichnung mit aufgenommen werden, wird häufig (und auch im folgenden Artikel) mit dem Schema „Herstellverfahren-Fasertyp/Matrixtyp“ abgekürzt. So wird zum Beispiel ein mit dem Liquid-Polymer-Infiltration-Verfahren (siehe unten) hergestelltes Kohlenstofffaser-verstärktes Siliciumcarbid einfach als „LPI-C/SiC“ bezeichnet.
Die wichtigsten, zurzeit industriell verfügbaren faserverstärkten Keramiken sind C/C, C/SiC, SiC/SiC und Al2O3/Al2O3. Sie unterscheiden sich von den konventionellen technischen Keramiken im Wesentlichen durch weiter unten ausführlicher vorgestellte Eigenschaften:
- höhere Bruchdehnung von bis zu einem Prozent
- deutlich höherer Risswiderstand
- extreme Thermoschockbeständigkeit
- bessere dynamische Belastbarkeit
- anisotrope, an den Faserausrichtungen orientierte Eigenschaften
Geschichte
Für die Verarbeitung von CMCs unter Verwendung von flüssigen, gasförmigen oder festen Ausgangsstoffen stehen mehrere Ansätze zur Verfügung. Die Technik der Chemische Gasphaseninfiltration (CVI) förderte die Entwicklung von CMCs. Die CVI-Technik wird seit den 1960er Jahren als Erweiterung der Chemical Vapor Deposition (CVD) Technologie untersucht. CVD beinhaltet die Abscheidung eines Feststoffs auf einem erwärmten Substrat aus gasförmigen Vorläufern. Es wird seit vielen Jahren zur Herstellung von verschleißfesten Beschichtungen, Beschichtungen für Kernbrennstoffe, dünnen Schichten für elektronische Schaltungen, Keramikfasern und so weiter verwendet. Wenn die CVD-Technik eingesetzt wird, um relativ große Mengen von Matrixmaterialien in faserigen Preforms zu imprägnieren, wird sie wird als CVI bezeichnet. CVI wurde erstmals für die Herstellung von Kohlenstoff-Kohlenstoff-Verbundwerkstoffen durch Pyrolyse von Methan bei 1000–2000 °C. Kohlenstoff-Kohlenstoff (C/C)-Verbundwerkstoffe weisen mehrere vorteilhafte Eigenschaften auf (z. B. wie niedrige Dichte und gute mechanische Eigenschaften bei hohen Temperaturen). Es wurde jedoch ca. 1973 sichtbar, dass Anwendungen von C/C-Verbundwerkstoffen aufgrund ihrer schlechten Oxidationsbeständigkeit bei Temperaturen über 450 °C begrenzt wären. SiC-Matrix-Verbundwerkstoffe wurden als Lösung betrachtet, um den oben genannten Mangel an C/C-Verbundwerkstoffen zu beheben für lange Lebensdauer bei erhöhten Temperaturen in oxidativer Umgebung. Die faserverstärkten CMCs folgten der Entwicklung von C/C-Verbundwerkstoffen und der CVI-Fertigungstechnik. Die Entwicklung von CVI SiC/SiC-Verbundwerkstoffen begann in den 1980er Jahren, als SEP (heute SNECMA), Amercorm, Refractory Composites und andere begannen, Ausrüstungen und Prozesse zur Herstellung von CMC-Komponenten für Luft- und Raumfahrt, Verteidigung und andere Anwendungen zu entwickeln. SNECMA war an der Spitze dieser Technologie und zeigte verschiedene CVI-SiC/SiC-Komponenten mit zufriedenstellende Leistung bei Turbinentriebwerken. Eine Reihe von CVI-SiC/SiC-Komponenten haben sich erfolgreich in Turbinentriebwerken und anderen Komponenten bewährt. Die Machbarkeit von CVI-SiC-Matrix-Verbundwerkstoffen wurde 1977 untersucht und 1978 unabhängig davon bestätigt. CVI SiC-Matrix-Verbundwerkstoffe, die durch SiC-Fasern verstärkt sind, werden seit Ende der 1980er Jahre hergestellt. Die aktuellen CVI SiC/SiC-Verbundwerkstoffe weisen eine hervorragende Leistung unter extremen Bedingungen auf, wie zum Beispiel bei erhöhten Temperaturen. Inzwischen wurden alternative Herstellungsverfahren wie die Schmelzinfiltration (MI), Polymerinfiltration und Pyrolyse (PIP) und Hybridansätze, die eine Kombination aus CVI und anderen Methoden entwickelt. In den letzten 30 Jahren wurden enorme Fortschritte bei den CMC-Entwicklungen erzielt.[1]
Herstellung allgemein
Die Herstellung von Bauteilen aus faserverstärkter Keramik erfolgt in der Regel in drei Schritten:
- Ablegen und Fixieren der Fasern in der gewünschten Bauteilform
- Einbringen des keramischen Matrixmaterials zwischen die Fasern
- Endbearbeitung und bei Bedarf weitere Nachbehandlungsschritte wie zum Beispiel das Aufbringen von Beschichtungen
Der erste und letzte Schritt ist bei allen Typen von faserverstärkter Keramik nahezu gleich:
Beim ersten Schritt werden die Fasern (technisch auch als Rovings bezeichnet) ähnlich wie bei der Herstellung von faserverstärktem Kunststoff mit verschiedenen Techniken abgelegt und fixiert: Ablegen von Fasergewebe, Wickeln, Flechten oder Stricken von Fasern sind Beispiele hierfür. Im dritten und letzten Schritt sind konventionelle schleifende, bohrende, läppende oder fräsende Bearbeitungstechniken üblich, wie bei allen Keramiken durchweg mit Diamantwerkzeugen. Durch die besonderen Eigenschaften der faserverstärkten Keramik sind zusätzlich noch Bearbeitungstechniken mit dem Wasserstrahl und dem Laser ohne Probleme möglich.
Der zweite Schritt kennt zurzeit im Prinzip fünf unterschiedliche Verfahren, die keramische Matrix zwischen die Fasern zu bringen:
- Abscheidung von Keramik aus einem heißen Gasgemisch
- Erzeugung durch Pyrolyse eines Si- und C-Atome enthaltenden Polymers
- Erzeugung durch chemische Reaktion
- Erzeugung durch Sintern bei niedrigen Temperaturen (1000 bis 1200 °C)
- Erzeugung durch Elektrophorese mit keramischem Pulver
Das fünfte Verfahren wird zurzeit noch nicht industriell eingesetzt. Bei allen genannten Verfahren gibt es noch Untervarianten, die sich in verfahrenstechnischen Details unterscheiden, sowie Kombinationen. Sie können in Büchern, Fachzeitschriften und Kongressliteratur nachvollzogen werden. Im Folgenden sind sie nur vereinfacht beschrieben.
Die ersten drei Verfahren werden praktisch ausschließlich zur Herstellung der nicht-oxidischen, das vierte zur Herstellung der oxidischen Verbundkeramik benutzt.
Allen Verfahren gemeinsam ist, dass der Herstellprozess, wie im Folgenden erläutert, zu einem porösen Werkstoff führt.
Bemerkungen über keramische Fasern
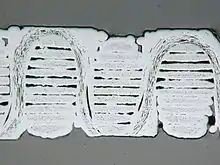
Foto: MT Aerospace AG, Augsburg
Unter keramischen Fasern werden im Zusammenhang mit faserverstärkter Keramik nicht nur Fasern verstanden, die, wie echte Technische Keramik, eine polykristalline Materialstruktur aufweisen, sondern auch solche mit amorpher Anordnung der Atome. Wegen der hohen Temperatur bei der Herstellung von Verbundkeramik ist die Verwendung nicht nur der organischen, sondern auch der anorganischen Metall- und Glasfasern ausgeschlossen. Nur hochtemperaturstabile keramische Fasern aus kristallinem Aluminiumoxid, Mullit (Mischkristallen aus Aluminiumoxid und Siliciumoxid), weitgehend kristallinem Siliciumcarbid sowie Zirkonoxid, Kohlenstofffasern mit den graphitischen Lamellenebenen in Faserrichtung sowie amorphe Fasern aus Siliciumcarbid sind in Anwendungen im Einsatz. Alle diese „keramischen“ Fasern zeichnen sich aus durch eine Dehnbarkeit, die zum Teil mit über 2 % wesentlich über der Dehnbarkeit normaler Keramik (etwa 0,05 bis 0,10 %) liegt. Ursache hierfür ist, dass in den Fasern je nach Hersteller verschiedene Additive (zum Beispiel Sauerstoff, Titan, Aluminium, siehe Keramikfaser) enthalten sind, ohne die zum Beispiel die amorphen SiC-Fasern niemals eine Dehnbarkeit von 2 % und eine Zugfestigkeit von über 3000 MPa erreichen könnten. Mit diesen Eigenschaften können die Fasern auch zu zwei- und dreidimensionaler Faserstrukturen verwoben werden (siehe Bild). Beim Verarbeiten wie zum Beispiel beim Weben müssen die Fasern hohe Zuglasten und kleine Biegeradien überstehen.
Abscheidung der Matrix aus einem Gasgemisch
Dieses Verfahren ist abgeleitet aus Beschichtungsverfahren, bei denen ein bestimmtes Gas oder Gasgemisch an erhitzten Oberflächen Material abscheidet. Es wird CVD-Verfahren genannt; CVD ist die Abkürzung für Chemical Vapor Deposition.
Bei der Anwendung dieses Verfahrens auf ein in Bauteilform fixiertes Fasergebilde scheidet sich auf den Faseroberflächen auch im Inneren des Bauteils das Beschichtungsmaterial ab. Daher wird dieses Verfahren auch als Chemische Gasphaseninfiltration (engl. Chemical Vapour Infiltration oder CVI-Verfahren) bezeichnet.
Ein Beispiel hierfür ist ein Verfahren zur Herstellung von C/C: ein C-Fasergebilde wird unter bestimmten Druck- (in der Regel unter 100 hPa) und Temperaturbedingungen (in der Regel über 1000 °C) mit einem Gemisch aus Argon und Methan (CH4) oder Propan (C3H8) begast. Aus dem Gasgemisch scheidet sich Kohlenstoff auf und zwischen den Fasern ab.
Ein weiteres Beispiel ist die Abscheidung von Siliciumcarbid. Hierzu wird üblicherweise ein Gasgemisch aus Wasserstoff als Katalysator und Methyl-Trichlor-Silan (MTS, chemische Formel CH3SiCl3) verwendet, das auch bei der Herstellung von Silikonen eine Rolle spielt. Das Kohlenstoff- und Siliciumatom des MTS-Moleküls bildet auf jeder über etwa 800 °C heißen Oberfläche Siliciumcarbid, die übrigen H- und Cl-Atome verlassen als HCl-Gas mit dem Wasserstoff den Prozess.
Bei der Abscheidung entstehen zwangsläufig geschlossene Poren, wenn Gaszutrittsöffnungen zugewachsen sind.
Matrixerzeugung durch Pyrolyse C- und Si-haltiger Polymere
Geeignete Polymere aus Kohlenwasserstoffen bilden bei der Pyrolyse unter Volumenschwund und Ausgasung Kohlenstoff. Polymere, bei denen ein Teil der Kohlenstoffatome durch Siliciumatome ersetzt worden ist, zum Beispiel sogenannte Carbosilane, bilden bei der Pyrolyse ebenfalls unter Volumenschwund und Ausgasung in analoger Weise ein amorphes und meist mit Kohlenstoff angereichertes Siliciumcarbid.
Fasern, Fasergewebe oder -gewebestapel und auch dreidimensionale Fasergebilde lassen sich mit diesen Polymeren tränken bzw. infiltrieren. Durch anschließende Härtung und Pyrolyse wird das Gebilde in einer ersten Stufe fixiert. Durch den Volumenschwund hat die Matrix in dieser Stufe noch eine hohe Porosität, die für die meisten Anwendungen nicht akzeptabel ist. Um die Porosität zu senken, sind daher in der Regel fünf bis acht anschließende Zyklen aus Imprägnierung, Härtung und Pyrolyse zur Fertigstellung des Rohbauteiles erforderlich.
Das Verfahren wird meist als Liquid Polymer Infiltration bezeichnet, abgekürzt mit LPI-Verfahren, und manchmal auch als Polymer Infiltration and Pyrolysis, abgekürzt PIP-Verfahren.
Auch hier gibt es eine Restporosität, da jedes Polymer bei der Pyrolyse im Volumen schrumpft. Die Porosität reduziert sich mit jedem Infiltrations- und Pyrolysezyklus.
Matrixerzeugung durch chemische Reaktion
Bei diesem Verfahren ist zwischen den Fasern bereits ein Material vorhanden, das durch chemische Reaktion mit einem weiteren Stoff zur eigentlich gewünschten keramischen Matrix umgewandelt wird. Die Herstellung konventioneller Keramiken benutzt solche Reaktionen ebenfalls: So wird reaktionsgebundenes Siliciumnitrid (RBSN) durch die Reaktion von Siliciumpulver mit Stickstoff hergestellt und poröser Kohlenstoff wird mit Silicium zum siliciumhaltigen Siliciumcarbid, sogenanntem SiSiC, umgesetzt.
Ein Beispiel für die Herstellung von faserverstärkter Keramik mit diesem Verfahren ist die sogenannte gerichtete Schmelzinfiltration: geschmolzenes Aluminium zwischen den Fasern wird durch den Zutritt von Sauerstoff zur Aluminiumoxid-Matrix oxidiert. Legierungsbestandteile in der Schmelze verhindern, dass die durchgängige Oxidation durch Bildung von Aluminiumoxidbarrieren unterbrochen wird. Der fertige Werkstoff enthält immer noch Restbestandteile von nicht abreagiertem Aluminium.
Ein weiteres Beispiel, das bei der Herstellung keramischer Bremsscheiben industriell eingeführt worden ist, ist die Umwandlung des Matrixkohlenstoffes eines porösen C/C-Materials mit flüssigem Silicium. Bei kontrollierter Prozessführung unter Vakuum und oberhalb der Schmelztemperatur des Siliciums (1410 °C) reagiert im Wesentlichen der Matrixkohlenstoff zu Siliciumcarbid und die Fasern bleiben nahezu unberührt und können so ihre Verstärkungsfunktion erfüllen. Dieses Verfahren wird meist mit Liquid Silicon Infiltration, abgekürzt LSI-Verfahren, bezeichnet.
Bei diesen Verfahren liegt die Restporosität bei niedrigen Werten von unter 3 %.
Matrixerzeugung durch Sintern
In oxidischer Verbundkeramik wird das Matrixmaterial zurzeit durch Hochtemperaturbehandlung („Sintern“) aus Vormaterialien erzeugt. Diese Vormaterialien erlauben es, die Temperaturen niedriger zu halten als die üblichen Sintertemperaturen der herkömmlichen Keramik, die bei etwa 1600 °C liegen. Die verfügbaren oxidischen Fasern würden durch so hohe Temperaturen zu stark geschädigt. Die Vormaterialien sind Flüssigkeiten, die mit mehr oder weniger hohen Anteilen von oxidischen Keramikpulvern zu einem sogenannten Schlicker angerührt und in die Fasern eingebracht werden. Bei Temperaturen zwischen 1000 und 1200 °C entsteht (mit starker Volumenschrumpfung verbunden) die oxidkeramische, poröse Matrix. Ein Beispiel für Vormaterialien sind Mischungen aus Al2O3-Pulver mit Tetra-Ethyl-Ortho-Silikat (als Silicium- und Sauerstoff-Spender) und Aluminium-Butylat (als Aluminium-Spender), die in richtiger Mischung Mullit als Matrix erzeugen. An weiteren Möglichkeiten für die Flüssigkeiten sind noch Sol-Gel-Ansätze zu nennen. Stand der Technik sind aber rein wässrige Suspensionen von Pulver mit Nanometer-Korngrößen, in denen auch ein Anteil gröberer oxidkeramischer Pulver verschiedener Qualität (Aluminiumoxid, Zirkoniumoxid) beigemischt wird.
Hier liegt die Porosität bei kommerziell eingesetztem Material um etwa 20 %.
Matrixerzeugung durch Elektrophorese
Bei der Elektrophorese werden dispergierte, elektrisch geladene Teilchen in einer Flüssigkeit im elektrischen Gleichspannungsfeld zweier Elektroden auf die entgegengesetzt geladene Oberfläche transportiert und dort abgesetzt. Wird als Oberfläche ein Fasergebilde benutzt, scheiden sich die Pulverteilchen dort ab und füllen auch die Faserzwischenräume aus. Auf diese Weise hergestellte faserverstärkte Keramik ist zurzeit noch nicht im industriellen Einsatz. Probleme sind unter anderem die relativ komplexe Aufbereitung und Dispergierung der Pulver, die Einstellung der Ladung und die Begrenzung auf recht dünne Bauteilwandstärken.
Bleibende Porosität wird auch hier durch das Zuwachsen von Zutrittskanälen erzeugt.
Eigenschaften
Grundmechanismus der mechanischen Eigenschaften
Die in der Einleitung erwähnte Erhöhung des Risswiderstandes durch die Einbettung keramischer Fasern in die keramische Matrix basiert auf folgendem Grundmechanismus:
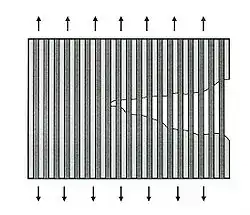
Bei Belastung bildet das Matrixmaterial Risse genau wie in der unverstärkten Form bei Dehnungen über (je nach Matrixtyp) 0,05 % und die eingebetteten Fasern bilden eine Brücke über den Riss. Dieser Mechanismus der Brückenbildung setzt voraus, dass die Matrix längs der Fasern gleiten kann, also nur schwach mechanisch mit den Fasern verbunden ist. Bei fester Verbindung zwischen Matrix und Fasern müssten die Fasern in der Brücke eine extrem hohe Dehnbarkeit oder entsprechend niedrige Steifigkeit besitzen, was aber nicht der Fall ist. Das bedeutet, dass bei fester Verbindung der Matrixriss an der gleichen Stelle auch durch die Fasern ginge und die faserverstärkte Keramik das spröde Bruchverhalten der nicht verstärkten Keramik zeigte.
Das Geheimnis faserverstärkter Keramik mit hohem Risswiderstand besteht demnach darin, bei der Herstellung sicherzustellen, dass die Verbindung zwischen Fasern und Matrix ein Gleiten zulässt. Nur auf diese Weise können die Fasern eine nennenswerte Brücke über Risse bilden und ihre Dehnbarkeit (bei C- und SiC-Fasern über 2 %, bei Al2O3-Fasern knapp 1 %) zur Geltung bringen. Bei der Herstellung von faserverstärkter Keramik wird dieser Gleitmechanismus meist durch eine dünne Beschichtung der Fasern mit Kohlenstoff oder Bornitrid sichergestellt. Diese Beschichtungen haben atomar angeordnete, lamellenartige Gleitebenen und bilden das Schmiermittel zwischen Fasern und Matrix.
Bei oxidischer Verbundkeramik liegt eine Besonderheit vor: die schwache Anbindung wird durch hohe Porosität der Matrix oder durch künstlich erzeugte Lücken zwischen Faser und Matrix hergestellt. Letztere erhält man zum Beispiel durch eine beliebige Beschichtung der Fasern, zum Beispiel mit Kohlenstoff, die beim abschließenden Sinterprozess ausbrennt und eine entsprechende Lücke hinterlässt. Eine zu hohe Matrixporosität führt allerdings zu niedrigen Druck- und Biegefestigkeiten, so dass in der Praxis ein Kompromiss zwischen guten Festigkeitswerten und gutem Bruchverhalten gefunden werden muss.
Eigenschaften bei Zug- und Biegebelastungen, Risswiderstand
Der Einfluss der Faserbeschichtung auf die Eigenschaften solcher Verbundkeramiken wird bei der Bestimmung von Biege-, Zugfestigkeit und Risswiderstand an Materialproben sichtbar.
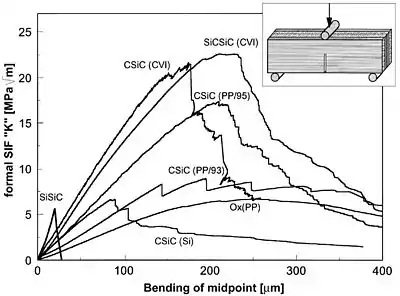
Bildlegende: SiSiC: konventionelles SiSiC, SiCSiC(CVI) und CSiC(CVI): im CVI-Verfahren hergestelltes SiC/SiC bzw. C/SiC, CSiC(95) und CSiC(93): im LPI-Verfahren hergestelltes C/SiC, Ox(PP): oxidische Verbundkeramik, CSiC(Si): im LSI-Verfahren hergestelltes C/SiC.
Die Kurven von Risswiderstandsmessungen an gekerbten Proben sind im Bild rechts beispielhaft gezeigt. Bei diesen Versuchen wird mit zunehmender Kraft eine gekerbte Probe (siehe Bild) bis zum Bruch belastet. Kraft und der Weg des die Kraft einleitenden Stempels werden gemessen. In der Bruchmechanik wird die Kraft auf den Spannungsintensitätsfaktor (SIF, in der Technik K1c-Faktor genannt) normiert, wobei die Größe der entstehenden Bruchfläche berücksichtigt wird. Da sich herausgestellt hat, dass die Größe der Bruchfläche in Verbundkeramiken nicht bestimmt werden kann, ist in den gezeigten Kurven die Normierung nur auf die Größe der Anfangskerbe erfolgt[3] und deshalb im Bild auch als formaler SIF „K“ bezeichnet worden. Da dieser Wert einer Kraft entspricht, kann man die Fläche (das Integral) unter den Kurven im relativen Vergleich der Kurven untereinander als die Energie betrachten, die zur Zerstörung der Probe aufgewendet werden muss. Direkt vergleichbar sind die Ergebnisse nur, wenn die Probengeometrie bei allen Proben identisch ist.
Die Risswiderstandskurven der im Bild gezeigten verschiedenen Verbundkeramiken zeigen, dass der spezifische Energieaufwand, mit dem ein Riss durch Verbundkeramikproben getrieben werden kann, ein Vielfaches von dem der konventionellen SiSiC-Keramik beträgt. Das Maximum der verschiedenen Risswiderstandskurven gibt das Kraftniveau an, das erforderlich ist, um den Riss durch die Probe zu treiben. Unterschiedliche Typen und Herstellverfahren führen zu erkennbaren und deutlichen Unterschieden in den Qualitäten dieser Werkstoffklasse, speziell im Hinblick auf den Risswiderstand.
Materialtyp | Al2O3/Al2O3 | Al2O3 | CVI-C/SiC | LPI-C/SiC | LSI-C/SiC | SSiC |
---|---|---|---|---|---|---|
Porosität (%) | 25 | <1 | 12 | 12 | 3 | <1 |
Dichte (g/cm³) | 2,8 | 3,9 | 2,1 | 1,9 | 1,9 | 3,1 |
Zugfestigkeit (MPa) | 170 | 250 | 310 | 250 | 190 | 200 |
Bruchdehnung (%) | 0,3 | 0,1 | 0,75 | 0,5 | 0,35 | 0,05 |
E-Modul (GPa) | 100 | 400 | 95 | 65 | 60 | 395 |
Biegefestigkeit (MPa) | 350 | 450 | 475 | 500 | 300 | 400 |
Erläuterungen zur Tabelle: Mit dem Vorsatz CVI-, LPI- und LSI- ist das Herstellverfahren der jeweiligen C/SiC-Verbundkeramik gemeint. Die Daten für die Verbundkeramiken stammen aus (Lit.: W. Krenkel, S. 143), die der oxidischen Verbundkeramik Al2O3 von der Firma Pritzkow Spezialkeramik und die Daten für SSiC aus einem Datenblatt der Firma H.C.Starck Ceramics. Die Zugfestigkeit für SSiC und Al2O3 wurde aus Bruchdehnung und E-Modul berechnet, da für konventionelle Keramiken Zugfestigkeiten nicht angegeben werden, sondern üblicherweise nur Biegefestigkeitswerte. Es muss darauf hingewiesen werden, dass es sich um durchschnittliche Werte handelt. Innerhalb der einzelnen Herstellverfahren auch der konventionellen Keramik gibt es zum Teil erhebliche Abweichungen von den angegebenen Werten.
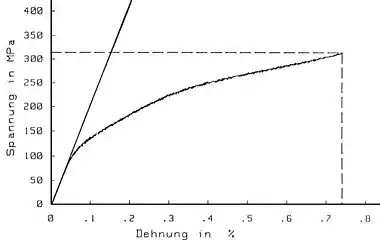
Bild: MT Aerospace AG, Augsburg
Bei Prüfung der Zugfestigkeit von Verbundkeramiken zeigen sich, verursacht durch den Rissüberbrückungsmechanismus, im Unterschied zu konventioneller Keramik quasi-plastische Kurvenverläufe und mögliche Dehnungen bis zu einem Prozent, mehr als dem Zehnfachen der Dehnbarkeit aller technischen Keramiken; quasi-plastisch deshalb, weil das Abbiegen der Kurve nach dem linear-elastischen Bereich nicht auf plastischer Verformung des Werkstoffes beruht, sondern auf die Ausbildung eines Risssystems zurückzuführen ist, das durch die Fasern zusammengehalten wird. Da die lasttragenden Fasern einen kleineren E-Modul besitzen, nimmt die Steigung der Kurve ab und täuscht so ein plastisches Verhalten vor. Die Werte in der Tabelle zeigen auch hier, dass die verschiedenen Verbundkeramiktypen die Faserdehnbarkeit in unterschiedlichem Maße nutzen.
Die Messkurven zur Bestimmung der Biegefestigkeit sehen praktisch genauso aus wie die oben gezeigten Kurven zur Bestimmung des Risswiderstandes. Bei der Bewertung von Zug- und Biegefestigkeiten sind zwei Dinge zu unterscheiden:
- Material mit wenig oder im Extremfall ohne Matrix weist hohe Zug- (nämlich Faserzug-), aber so gut wie keine Biegefestigkeit auf.
- Umgekehrt zeigt Material mit hohem Matrixanteil und geringer Porosität hohe Biegefestigkeiten (wie konventionelle Keramik), die wiederum nichts darüber aussagen, ob die Dehnbarkeit der Fasern genutzt wird.
Beide Werte müssen unabhängig voneinander betrachtet werden.
Sonstige mechanische Eigenschaften
In vielen Bauteilen aus Verbundkeramik liegen die Fasern in zweidimensionaler Form entweder als gestapelte Gewebelagen oder als gekreuzte Lagen eindimensional ausgerichteter Fasern vor. Die Werkstoffe sind damit anisotrop. Eine Rissausbreitung zwischen diesen Lagen wird durch keine Faserbrücke behindert. Die Werte für die interlaminare Scherfestigkeit sind bei diesem Material entsprechend niedrig, ebenso wie die Zugfestigkeit senkrecht zum Gewebe. Wie beim faserverstärkten Kunststoff sind mögliche Delaminationen eine Schwachstelle des Materials. Sie kann durch Einführung dreidimensionaler Faserstrukturen erheblich verbessert werden.
Material | CVI-C/SiC | LPI-C/SiC | LSI-C/SiC | CVI-SiC/SiC |
---|---|---|---|---|
Interlaminare Scherfestigkeit (MPa) | 45 | 30 | 33 | 50 |
Zugfestigkeit senkrecht zur Faserebene (MPa) | 6 | 4 | - | 7 |
Druckfestigkeit senkrecht zur Faserebene (MPa) | 500 | 450 | - | 500 |
Bemerkungen zur Tabelle: Durch die Porosität sind die Druckfestigkeitswerte niedriger als bei konventioneller Keramik, wo für Siliciumcarbid über 2000 MPa angegeben werden. Porosität und fehlende Faserbrücken führen zu den sehr niedrigen Zugfestigkeiten senkrecht zur Faserebene.
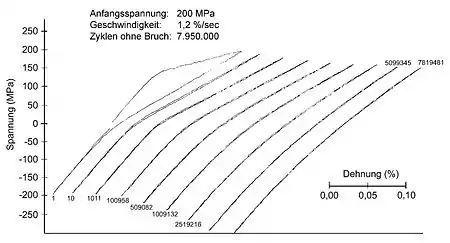
Bild: MT Aerospace AG, Augsburg
Die rissüberbrückende Wirkung der Fasern erlaubt auch eine hohe dynamische Belastung dieser Keramik. Proben werden in Wechsellastversuchen, sogenannten „Low-“ oder „High-Cycle-Fatigue“-Versuchen, zyklischen Druck- und Zugbelastungen bis zum Bruch ausgesetzt. Je höher die Startbelastung gewählt wird, umso weniger Zyklen überlebt die Probe. Verschiedene Startlasten aufgetragen gegen den Logarithmus der jeweils erreichten Zyklenzahl ergeben die sogenannte Wöhler-Linie. Sie zeigt an, wie viele Tausend oder Millionen Lastzyklen das getestete Material bei einer bestimmten dynamischen Belastung überleben kann. Faserverstärkte Keramik kann hier mit ausgezeichneten Ergebnissen aufwarten: bei 80 % der Dehnbarkeit zyklisch belastet überlebt SiC/SiC etwa 8 Millionen Zug-Druck-Zyklen (siehe Bild).
Die Querkontraktionszahl zeigt senkrecht zur zweidimensionalen Faserebene während der Messung eine Anomalie: sie nimmt in der Richtung senkrecht zu den Fasern negative Werte an, wenn durch die Bildung interlaminarer Risse die Probendicke in der Frühphase der Messung kurz ansteigt statt abzunehmen.
Thermische und elektrische Eigenschaften
Die thermischen und elektrischen Eigenschaften von faserverstärkter Keramik ergeben sich aus den Bestandteilen von Fasern, Matrix und Poren und deren Zusammensetzung. Die Faserorientierung erzeugt darüber hinaus noch richtungsabhängige (anisotrope) Kennwerte.
Zu den häufigsten zurzeit verfügbaren Verbundkeramiken lässt sich Folgendes zusammenfassen:
Faserverstärkte Keramiken, die Oxide einsetzen, sind unverändert sehr gute elektrische Isolatoren und wegen der Poren steigt auch die thermische Isolationswirkung deutlich über die von konventionellen Oxidkeramiken.
Die Verwendung von Kohlenstofffasern erhöht die elektrische und die thermische Leitfähigkeit in Richtung der Fasern, sobald direkter elektrischer Kontakt zu ihnen vorliegt.
Siliciumcarbid als Matrix ist ein sehr guter Wärmeleiter. Als elektrischer Halbleiter nimmt sein elektrischer Widerstand mit steigender Temperatur ab. Siliciumcarbid-Fasern leiten Wärme und elektrischen Strom wegen der amorphen Mikrostruktur deutlich schlechter. In Verbundkeramik mit Siliciumcarbid als Matrix sinken sowohl die Wärme- als auch die elektrische Leitfähigkeit wegen der Porosität auf niedrigere Werte. Einige Angaben sind in der folgenden Tabelle aufgelistet.
Material | CVI-C/SiC | LPI-C/SiC | LSI-C/SiC | CVI-SiC/SiC | SSiC |
---|---|---|---|---|---|
Wärmeleitung (p) [W/(m·K)] | 15 | 11 | 21 | 18 | >100 |
Wärmeleitung (s) [W/(m·K)] | 7 | 5 | 15 | 10 | >100 |
Wärmedehnung (p) [10−6·1/K] | 1,3 | 1,2 | 0 | 2,3 | 4 |
Wärmedehnung (s) [10−6·1/K] | 3 | 4 | 3 | 3 | 4 |
spezifischer elektr. Widerstand (p) [Ω·cm] | - | - | - | - | 50 |
spezifischer elektr. Widerstand (s) [Ω·cm] | 0,4 | - | - | 5 | 50 |
Bemerkungen zur Tabelle: Mit (p) und (s) sind die Eigenschaften parallel und senkrecht zu Faserorientierung des anisotropen Materials gemeint. Zu nicht eingetragenen Werten fehlen Literatur- oder Herstellerangaben. Wegen der geringen Porosität zeigt das LSI-Material die höchste Wärmeleitfähigkeit aller Verbundkeramiken – ein Vorteil für den Einsatz dieses Werkstoffes als hochbelastetes Bremsscheibenmaterial. Auch hier gilt, dass die Werte selbst innerhalb der einzelnen Keramiktypen je nach Details beim Herstellprozess erheblich abweichen können.
Normale Keramik und technische Keramik sind empfindlich gegenüber Thermospannungen, die bei Thermoschockbelastungen besonders hoch sind. Die Ursache liegt in der geringen Dehnbarkeit und hohen Steifigkeit (hohem E-Modul) dieser Materialien. Temperaturunterschiede im Material erzeugen unterschiedliche Ausdehnung, die wegen des hohen E- Moduls zu entsprechend hohen Spannungen führt. Durch diese wird das Material überdehnt und bricht. In faserverstärkter Keramik werden solche Risse durch die Fasern überbrückt. Ein Bauteil erleidet keinen makroskopischen Schaden, auch wenn sich in der keramischen Matrix Risse gebildet haben. Der Einsatz dieser Materialklasse in Scheibenbremsen beweist die Leistungsfähigkeit von Verbundkeramik unter extremen Thermoschockverhältnissen.
Korrosionseigenschaften
Breitere Untersuchungen zum Korrosionsverhalten von faserverstärkter Keramik liegen noch nicht vor. Auch hier sind die Eigenschaften bestimmt durch die Eigenschaften der verwendeten Bestandteile, nämlich Fasern und Matrix.
Generell sind keramische Werkstoffe im Vergleich zu den meisten übrigen Werkstoffen sehr korrosionsstabil. Die Vielzahl der Herstellvarianten mit verschiedenen Additiven, zum Beispiel Sinterhilfsmitteln, Mischformen, vor allem bei den Oxiden, Verunreinigungen, Glasphasen an den Korngrenzen und Porositätsunterschiede beeinflussen das Korrosionsverhalten entscheidend (Lit.: J. Kriegesmann).
Über die zurzeit in Anwendungen wichtigen Matrix- und Fasermaterialien lässt sich stichwortartig Folgendes aus der Literatur entnehmen:
- Aluminiumoxid:
Aluminiumoxid ist in sehr reinem Zustand gegen fast alles beständig; amorphe Glasphasen an den Korngrenzen und Siliciumoxid-Gehalt entscheiden die Korrosionsgeschwindigkeit in konzentrierten Säuren und Laugen. Bei hohen Temperaturen führen sie unter Last zu Kriechverhalten. Für Metallschmelzen wird Aluminiumoxid nur bei Edelmetallen wie Gold oder Platin eingesetzt. - Aluminiumoxidfasern:
Verhalten sich ähnlich wie Aluminiumoxid. Die kommerziell verfügbaren Fasern sind nicht von extremer Reinheit und daher anfälliger. Das Kriechverhalten bei Temperaturen über etwa 1000 °C erlaubt zurzeit auch nur wenige Anwendungen oxidischer Verbundkeramik.
- Kohlenstoff:
Kohlenstoff korrodiert, besser verbrennt, mit Sauerstoff bei Temperaturen ab etwa 500 °C. Ebenso oxidiert er in stark oxidierenden Medien (zum Beispiel konzentrierter Salpetersäure). In den meisten Metallschmelzen löst er sich oder bildet Carbide.
- Kohlenstofffasern:
Kohlenstofffasern verhalten sich praktisch so wie Kohlenstoff.
- Siliciumcarbid:
Sehr reine Varianten des Siliciumcarbides gehören zu den korrosionsbeständigsten Werkstoffen. Lediglich starke Laugen, Sauerstoff ab ca. 800 °C und die meisten Metallschmelzen reagieren mit diesem Material. Bei Metallschmelzen bilden sich sowohl Carbide als auch Silicide (Verbindungen von Silicium mit Metall).
Bei der mit Sauerstoff einsetzenden Reaktion von SiC zu SiO2 und CO2 bildet das Siliciumdioxid eine Schutzschicht, die passivierend wirkt („passive Oxidation“). Bei noch höheren Temperaturen (ab ca. 1600 °C) und gleichzeitigem Sauerstoffmangel (Partialdruck unter 50 mbar) bildet sich jedoch neben dem CO2 und CO das gasförmige Siliciummonoxid (SiO), das jede Schutzwirkung verhindert. Diese sogenannte „aktive Oxidation“ führt unter den genannten Bedingungen zu sehr raschem Abbau des Siliciumcarbides.
Im Zusammenhang mit Verbundkeramik gilt diese Charakterisierung nur für SiC-Matrixmaterial, das mit dem CVI-Verfahren hergestellt worden ist. Dort besteht die Matrix aus sehr reinem, feinkristallinen SiC. Mit dem LPI-Verfahren hergestellte Matrix ist wegen der amorphen Struktur und der Porosität deutlich empfindlicher für alle Arten von Korrosion. In der Matrix des LSI-Materials sorgen die immer vorhandenen Reste von Silicium für eine verschlechterte Korrosionsbeständigkeit. - Siliciumcarbidfasern:
Da Siliciumcarbidfasern durch Pyrolyse vernetzter, silicium-organischer Kunstharze (analog zur Herstellung von Kohlenstofffasern) hergestellt werden, gilt für sie das Gleiche wie für die im LPI-Verfahren hergestellte Matrix: deutlich stärkere Korrosionsempfindlichkeit gegen Laugen und oxidierende Medien.
Anwendungen
Mit faserverstärkter Keramik steht ein Werkstoff zur Verfügung,[4] der gewichtige Nachteile konventioneller technischer Keramik, nämlich deren geringe Bruchzähigkeit und hohe Thermoschockempfindlichkeit, nicht mehr besitzt. Anwendungsentwicklungen haben sich folglich auf Gebiete konzentriert, in denen Zuverlässigkeit bei hohen, für Metalle nicht mehr zugänglichen Temperaturen und bei abrasiven (= Verschleiß erzeugenden) Belastungen gefordert sind. Folgende Schwerpunkte haben sich in Entwicklungen und Anwendungen bisher ergeben:
- Hitzeschutzsysteme für Raumflugkörper, die beim Wiedereintritt in die Erdatmosphäre hohen Thermospannungen und Vibrationsbelastungen ausgesetzt sind.
- Komponenten für Gasturbinen im Bereich der heißen Gase, also in der Turbinenbrennkammer, den statischen, den Gasstrom lenkenden Leitschaufeln und den eigentlichen Turbinenschaufeln, die den Verdichter der Gasturbine antreiben.
- Bauteile für die Brennertechnik und Heißgasführungen aus oxidischer Verbundkeramik.
- Bremsscheiben für hoch belastete Scheibenbremsen, die auf der Reibfläche extremen Thermoschockbedingungen ausgesetzt sind (anders als beim Eintauchen eines glühenden Teiles in Wasser entsteht hier keine wärmeisolierende Wasserdampfschicht).
- Komponenten für Gleitlager mit hoher Korrosions- und Verschleißbelastung.
Darüber hinaus sind grundsätzlich alle Bereiche interessant, in denen konventionelle technische Keramik verwendet wird oder in denen metallische Komponenten wegen Korrosion oder hoher Temperaturen keine befriedigenden Lebensdauern erreichen. Die folgende Präsentation einiger Entwicklungs- und Anwendungsbeispiele ist bei weitem nicht vollständig und soll nur die Breite der technischen Möglichkeiten andeuten.
Entwicklungen für Anwendungen in der Raumfahrt
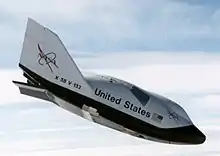
Im Bereich der Raumfahrt ist faserverstärkte Keramik interessant für Komponenten von Hitzeschutzsystemen und für bewegliche Steuerklappen von Raumgleitern. Beim Wiedereintritt in die Erdatmosphäre entstehen für einige Minuten an diesen Elementen Oberflächentemperaturen über 1500 °C, die nur von keramischen Werkstoffen ohne größere Beeinträchtigung ertragen werden. Durch den Einsatz von faserverstärkter Keramik für heiße Strukturen in der Raumfahrt verspricht man sich im Unterschied zu den bisher eingesetzten Materialsystemen unter anderem:
- Gewichtseinsparungen
- Einen Beitrag des Hitzeschutzsystems zur lasttragenden Struktur
- Wiederverwendbarkeit für mehrere Wiedereintritte
Da bei diesen hohen Temperaturen die verfügbaren oxidischen Fasern unter Last kriechen und die amorphen SiC-Fasern durch Rekristallisation ihre Festigkeit verlieren, haben sich die Material- und Komponentenentwicklungen auf die Verbundkeramik C/SiC konzentriert. Die im Rahmen des HERMES-Programmes der ESA in den 1980er Jahren durchgeführten und 1992 abgebrochenen Entwicklungen haben nach mehreren Folgeprogrammen ihren Höhepunkt mit der Entwicklung und Qualifikation von Bugnase, Flügelvorderkanten und Hecksteuerklappen des Raumgleiters X-38 der NASA gefunden.[5][6]
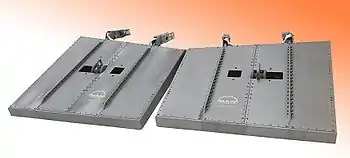
Größe: 1,5×1,5×0,15 m, Masse: je 68 kg, gefügt aus Einzelteilen mit jeweils über 400 Schrauben/Muttern aus CVI-C/SiC.
Foto: MT Aerospace
Eine dieser Entwicklungen diente zum Beispiel der Qualifikation von Schrauben und Muttern aus Verbundkeramik.[7] Schrauben aus technischer Keramik sind zwar verfügbar, auf Grund der Kerben im Gewindegrund aber bruchempfindlich und haben bei weitem nicht die geforderte Zuverlässigkeit. Der Einsatz von Schrauben aus C/C ist auf Grund der Oxidationsempfindlichkeit ebenfalls zu risikoreich.
Eine weitere wichtige Komponente dieser Steuerklappen ist das zentral gelegene Lager, über das die Kraft für die Bewegung eingeleitet wird. Dieses Lager wurde unter realitätsnahen Bedingungen (4 Tonnen Last, 1600 °C auf der Unterseite, Sauerstoffkonzentration auf dem Niveau beim Wiedereintritt in die Erdatmosphäre und gleichzeitige 8°-Lagerbewegungen mit einem Bewegungszyklus in vier Sekunden) erfolgreich beim DLR in Stuttgart getestet; fünf Wiedereintrittsphasen wurden auf diese Weise simuliert.[8]
Die Verwendung von C/SiC hat die Entwicklung und Qualifikation von Beschichtungssystemen erzwungen, die den raschen Ausbrand der C-Fasern unter den Wiedereintrittsbedingungen verhindern. Versuche im Plasmastrom unter simulierten Wiedereintrittsbedingungen haben den Erfolg dieser Entwicklungsarbeiten nachgewiesen.
Ein weiterer Qualifikationsschritt für die Flugtauglichkeit erfolgte durch Verformungstests bei über 1000 °C auf einem Prüfstand der IABG in München. Die Verformung unter 4 Tonnen Last bestätigte die entsprechenden Berechnungen und die Auslegung. Abschließende Bodentests nach der Montage der Klappen an den für den Flugtest vorgesehene X-38-Raumgleiter in Houston, Texas, USA, verliefen ebenfalls erfolgreich. Die NASA hat aus finanzpolitischen Gründen das Ziel des Projektes, nämlich den Transport des X-38 mit einem Space-Shuttle-Flug in die Erdumlaufbahn und den anschließenden (unbemannten) Wiedereintritt in die Erdatmosphäre, nicht mehr realisieren können.
Man muss an dieser Stelle darauf hinweisen, dass diese Qualifikationen dem Einsatz von C/SiC-Verbundkeramik für diesen speziellen Fall gedient haben. Die Hochtemperaturbelastung dauert bei einem Wiedereintritt etwa 20 Minuten. Bei Wiederverwendbarkeit addiert sich die Dauer auf wenige Stunden zyklischer Belastung. Ein Einsatz von oxidationsgeschütztem C/SiC für industrielle Hochtemperaturanwendungen mit mehreren Hundert oder Tausend Stunden geforderter Lebensdauer ist damit noch nicht sichergestellt.
Entwicklungen für den Einsatz in Gasturbinen
Ziel des Verbundkeramikeinsatzes in Gasturbinen ist die Erhöhung der Gastemperatur, die einen Anstieg des Wirkungsgrades zur Folge hat.
Die komplexe Formgebung für Leitschaufeln und Turbinenschaufeln in Gasturbinen sowie die sehr hohe thermische und mechanische Belastung dieser Teile haben dazu geführt, dass zunächst mit Erfolg nur die Entwicklung von Brennkammern aus Verbundkeramik vorangetrieben worden ist. Am weitesten sind hier die Fortschritte in den Vereinigten Staaten gediehen. Eine Brennkammer aus SiC/SiC-Verbundkeramik auf der Basis einer speziellen hochtemperaturfesten SiC-Faser ist über 15.000 Stunden in einer Gasturbine im Einsatz gewesen.[9] Da SiC in solchen Zeiträumen bei Temperaturen von etwa 1100 °C schon nennenswert durch Oxidation angegriffen wird, musste auch hier ein sehr leistungsfähiger Oxidationsschutz entwickelt werden. Er besteht aus einem mehrschichtigen System oxidischer Keramiken.[10]
Einer schnellen Umsetzung der bisherigen Ergebnisse in reale Anwendung steht noch entgegen, dass das getestete Temperaturniveau noch keine Vorteile gegenüber den herkömmlichen, mit einem Luftfilm gekühlten metallischen Brennkammern bietet, dass die der Brennkammer folgenden Komponenten (Leitschaufeln und Turbinenschaufeln) ebenfalls für ein erhöhtes Temperaturniveau entwickelt und qualifiziert werden müssen und dass die Kosten für die Herstellung des Verbundwerkstoffsystems aus speziellen SiC-Fasern, SiC-Matrix und speziellem Beschichtungssystem noch sehr hoch sind.
Anwendung oxidischer Verbundkeramik in Brennern und Heißgasführungen
Sauerstoffhaltige, heiße Gase mit einer Temperatur über 1000 °C führen über kurz oder lang in Brennern mit konventionellen Flammrohren aus hochtemperaturfestem Stahl zu deren Verzunderung, bei Rohren aus Siliciumcarbid zur Schädigung durch Oxidation. Da diese Teile keiner hohen mechanischen Belastung, sondern nur starken Thermoschocks ausgesetzt sind, eignet sich oxidische Verbundkeramik besonders gut für solche Einsätze bis zu 1300 °C. Die Bilderreihe unten zeigt das Flammrohr eines Brenners aus oxidischer Aluminiumoxid-Verbundkeramik, das 15.000 Stunden in einer Backstraße für Knäckebrot genutzt worden ist und inzwischen über 20.000 Betriebsstunden erreicht hat.[11] Eine Lebensdauer bis zum 20fachen von konventionellen Werkstoffen kann bei diesen Einsatzfällen realisiert werden.
- Flammrohr aus oxidischer Verbundkeramik
Bilder: Pritzkow Spezialkeramik, Stuttgart - Ventilator für Heißgase
- Hubtor aus oxidischer Verbundkeramik
- Hubtor im Ofeneinsatz
Klappen oder Ventilatoren zur Regelung oder Förderung von sauerstoffhaltigen Heißgasströmen in verschiedenen Anlagen können aus Oxid-Verbundkeramik in baugleicher Form wie Metalle hergestellt werden. Sie haben den Vorteil, dass sie sich nicht – wie Metalle bei Temperaturen über 650 °C – verformen („verziehen“). Der Einsatz diese Werkstoffes für Hubtore (siehe Bilderreihe) zum Beispiel in Sinteröfen, die bei häufigen Öffnungs- und Schließvorgängen ebenfalls thermisch hoch bis 1300 °C belastet werden, hat sich in einem Fall seit mehr als 12 Monaten mit über 260.000 Öffnungs- und Schließzyklen bewährt.[12]
Anwendung als Bremsscheibe
Nach den Bremsscheiben aus C/C-Material, die schon seit längerem in Rennwagen der Formel 1 und in Bremsen von Flugzeugen eingesetzt werden, sind inzwischen Bremsscheiben aus C/SiC-Material, die mit dem LSI-Verfahren hergestellt werden, kommerziell verfügbar und werden in teuren Sportwagen, teilweise gegen Aufpreis, verbaut. Das LSI-Verfahren bietet Kostenvorteile bei der Herstellung. So werden die Scheiben aus einem Gemisch von Kurzfasern und Harz vergleichsweise schnell und kostengünstig gepresst, gehärtet, zur C/C-Scheibe pyrolysiert und anschließend, wie oben beschrieben, mit geschmolzenem Silicium in eine LSI-C/SiC-Scheibe umgewandelt.
Die Vorteile dieser Bremsscheiben lassen sich wie folgt zusammenfassen:
- Der Scheibenverschleiß ist sehr gering. Die Lebensdauer im Vergleich zu einer herkömmlichen Grauguß-Scheibe ist rund sechs Mal höher. Je nach Fahrweise erlaubt dies auch den Einsatz einer Scheibe über die gesamte Lebensdauer des Fahrzeuges. Bis zu 300.000 km werden bei normaler Belastung angegeben.
- Es gibt auch bei hoher Beanspruchung keine Schwankungen im Reibkoeffizienten, den bei Metallscheiben bekannten sogenannten Fading-Effekt.
- Im Unterschied zu Bremsscheiben aus C/C wird kein Einfluss von Feuchtigkeit auf die Bremsleistung beobachtet.
- Das Scheibenmaterial ist außerordentlich korrosionsbeständig und damit unempfindlich gegenüber Streusalzwirkung im Winter.
- Die Masse kann im Vergleich zur Stahlscheibe auf ca. 40 % reduziert werden. Das bedeutet wegen der deutlich geringeren ungefederten Massen der Räder verbesserten Fahrkomfort und gleichzeitig bessere Haftung, da das Rad der Kontur des Bodens leichter folgen kann.
Da die C-Fasern weitgehend durch die SiC-Matrix vor Oxidation geschützt sind und der Zeitraum, in der Bremsscheiben Temperaturen von über 500 °C nennenswert überschreiten, in der gesamten Lebensdauer eines Fahrzeuges auf wenige Stunden begrenzt ist, spielt die Oxidation des Werkstoffes bei dieser Anwendung keine wesentliche Rolle.
Es bleibt abzuwarten, ob die Herstellkosten für solche Scheiben so weit abgesenkt werden können, dass auch Fahrzeuge der Mittelklasse damit ausgestattet werden. Den aktuellen Stand kann man aus den Internetseiten der Anbieter entnehmen.
Anwendungen in Gleitlagern
In Gleitlagern von Pumpen wird konventionelles SSiC oder auch das kostengünstigere SiSiC schon seit über 20 Jahren mit viel Erfolg verwendet (Lit.: W. J. Bartz, 2003). Das Lager benutzt dabei die von der Pumpe geförderte Flüssigkeit als Schmiermittel. Ursache für den Erfolg dieses Lagerkonzeptes ist die Korrosionsfestigkeit gegenüber fast allen Medien und der durch die große Härte bedingte extrem geringe Verschleiß bei Reibbelastung oder abrasiver Belastung durch Partikel sowie der niedrige Reibkoeffizient bei Flüssigkeitsschmierung. Die SiC-Komponenten des Gleitlagers bestehen aus der sogenannten Wellenschutzhülse, die auf der Welle montiert ist und in der Lagerbuchse rotiert. Die SiC-Lagerbuchse ist in der Regel in ihre metallische Umgebung eingeschrumpft und steht unter Druckspannung. Ein spröder Bruch dieser Komponente ist damit sehr unwahrscheinlich. Die SiC-Wellenschutzhülse hat diesen Vorteil nicht und wird deshalb in der Regel mit einer großen Wandstärke ausgeführt und/oder mit speziellen konstruktiven Vorkehrungen eingebaut. Bei großen Pumpen mit entsprechend großen Wellendurchmessern (100 bis 300 mm) sowie bei Pumpen mit hoher Lagerbelastung hat sich wegen des Ausfallrisikos der Wellenschutzhülse das keramische Lagerkonzept erst mit dem Einsatz von Verbundkeramik realisieren lassen. Auf dem Prüfstand konnte gezeigt werden, dass die Lagerpaarung aus CVI-SiC/SiC und konventionellem SSiC unter Mischreibungsbedingungen nahezu das Dreifache an spezifischer Lagerbelastung ertragen kann wie viele andere geprüfte Paarungen[13]. Mit spezifischer Lagerbelastung ist das Produkt aus Reibkoeffizient (dimensionslos), Laufgeschwindigkeit (m/s) und Lagerbelastung (MPa oder N/mm²) gemeint; es gibt die im Lagerspalt umgesetzte Leistung in W/mm² an und wird oft auch – unter Weglassung des Reibkoeffizienten – als „P mal V-Wert“ angegeben.

Foto: MT Aerospace AG
Kesselspeisewasserpumpen[13] in Kraftwerken, mit denen einige tausend m³/h von 160 °C heißem Wasser auf 20 bar Druck gefördert werden, oder Rohrgehäusepumpen,[14] mit denen einige zehntausend m³/h Schleusenwasser oder Meerwasser für Entsalzungsanlagen gepumpt werden, sind seit 1994 die bisher bevorzugten Einsatzfälle für wassergeschmierte Gleitlager mit Wellenschutzhülsen aus CVI-SiC/SiC-Verbundkeramik (Bild am Anfang dieses Artikels).
In der Entwicklung befindet sich noch die Anwendung dieses Gleitlagertyps in Turbopumpen, mit denen in Triebwerken der Raumfahrt flüssiger Sauerstoff (Liquid Oxygen = LOx, Siedepunkt: −183 °C) gefördert wird. Die bisherigen Tests haben gezeigt:
- SiC und CVI-SiC/SiC sind mit LOx verträglich und reagieren auch unter verschärften Bedingungen nicht mit Sauerstoff (Zur Bestimmung der Selbstzündungstemperatur wird Pulver unter 20 bar reinem Sauerstoffgas nach der französischen Norm NF 29-763 bis auf 525 °C erhitzt.).
- Reib-Verschleißversuche haben im Vergleich zu einer metallischen Standard-Paarung einen halbierten Reibkoeffizienten und einen auf ein Hundertstel reduzierten Verschleiß ergeben.[15]
- Das mit LOx-Schmierung hydrostatisch ausgelegte Gleitlager hat einen Test einige Stunden bei einer Drehzahl von 10.000 min−1 mit unterschiedlichen Lagerlasten sowie 50 Start/Stopp-Übergänge unter Mischreibungsbedingungen praktisch verschleißfrei überstanden.[16]
Der Vorteil dieser keramischen Lager mit Verbundkeramik im Vergleich zu Lagern mit herkömmlicher Keramik liegt in der stark erhöhten Zuverlässigkeit. Eine Beschädigung der Wellenschutzhülse führt nicht zu einer Zersplitterung in mehrere größere und harte Bruchstücke mit großen Folgeschäden für Pumpengehäuse und -rad.
Sonstige Anwendungen und Entwicklungsansätze
Erwähnt werden können noch die folgenden Anwendungs- und Entwicklungsbeispiele:
- Schubsteuerklappen in Strahltriebwerken von Kampfflugzeugen,[17] mit denen der Strahlquerschnitt an die Triebwerksleistung angepasst wird.
- CVI-SiC/SiC-Platten mit dreidimensionaler Faserstruktur als Auskleidung heißer Bereiche von Fusionsreaktoren.[18] Durch die dreidimensionale Faserstruktur wird die Wärmeleitung senkrecht zur Plattenebene erhöht. Da kristallines SiC sich in der mit Neutronenstrahlung belasteten Umgebung als vergleichsweise beständiges Material erwiesen hat, werden hier auch kristalline SiC-Fasern eingesetzt, deren Hochtemperaturstabilität im Vergleich zu den amorphen stark verbessert ist.
- Strahlruder („Fins“), Flammhalter und Heißgasleitrohre in Überschallraketen[19], die extrem heiße Abgase, bei Festbrennstoffen auch mit Partikelanteilen, für kurze Zeit kontrolliert führen und umlenken müssen.
- Bremsklötze zur Schnellbremsung von Schlitten in Simulationsanlagen für Unfälle im Automobilverkehr[19] mit dem Vorteil des geringen Verschleißes und auch bei mehreren Tests sehr stabiler Bremsverzögerungswerte.
- Hochtemperatur-Wärmeübertrager[19] mit den noch ähnlich wie bei Gasturbinen anstehenden Problemen der Heißgaskorrosion und zusätzlich der notwendigen Gasdichtigkeit.
- Steife Strukturen für Präzisionsspiegel.[19]
- Verkleidungselemente im Bereich Abgas führender Rohre von Rennwagen der Formel 1 sowie Scheiben für die stark belasteten Kupplungen dieser Fahrzeuge.
Industrielle Hersteller in Europa
- WPX Faserkeramik: Oxidische Faserkeramik Bauteile und Komponenten für industrielle Wärmebehandlung und Hochtemperaturanwendungen
- KLETKE Advanced Composites: Komponenten aus C/C, C/C mit SiC-Beschichtung mit C-CVI und LSI-Verfahren
- SGL Carbon: Bremsscheiben (LSI-Verfahren)
- Schunk Group: Axiallager, Radiallager, Gleitbeläge, Ofenauskleidungen aus C/C-Material
- BJS Ceramics: Raumfahrtkomponenten, Gleitlagerkomponenten (CVI-Verfahren)
- Snecma: Komponenten für Raumfahrt, Verteidigungstechnik, Bremsscheiben (CVI-Verfahren)
- Brembo: Bremsscheiben (LSI-Verfahren)
- Pritzkow Spezialkeramik: Hochtemperaturbeständige Bauteile für den Industriebedarf aus oxidischer Verbundkeramik
- CERAFIB GmbH: Hochtemperaturbeständige Filamente und Werkstoffe
Forschungseinrichtungen in Deutschland
- Universität Bremen: Fachgebiet Keramische Werkstoffe und Bauteile sowie Biokeramik
- Universität Stuttgart: Institut für Fertigungstechnologie Keramischer Bauteile (IFKB)
- Universität Karlsruhe: Institut für Keramik im Maschinenbau (IKM)
- Dresden: Fraunhofer-Institut für Keramische Technologien und Systeme (IKTS), sowie das Institut für Leichtbau und Kunststofftechnik (ILK) an der TU Dresden
- Universität Bayreuth: Lehrstuhl Keramische Werkstoffe des Instituts für Materialforschung (IMA)
- Institut für Textilchemie und Chemiefasern (ITCF Denkendorf): Faserforschung und -entwicklung
- DLR Institut für Bauweisen und Strukturtechnologie: Entwicklung von maßgeschneiderten CMC-Werkstoffen, z. B. Thermalschutzsysteme
- DLR Institut für Werkstoff-Forschung Köln: Entwicklung von oxidischen Faserverbundkeramiken für den Hochtemperatureinsatz
- Fraunhofer-Zentrum für Hochtemperatur-Leichtbau (HTL): Forschung und Entwicklung von Ceramic Matrix Composites (CMC), Keramikfasern und Hochleistungskeramiken
Literatur
- W. Krenkel (Hrsg.): Keramische Verbundwerkstoffe. Wiley-VCH, Weinheim 2003. ISBN 3-527-30529-7
- J. Kriegesmann (Hrsg.): DKG – Technische Keramische Werkstoffe. HvB-Verlag, Ellerau 2005. ISBN 978-3-938595-00-8
- W. J. Bartz (Hrsg.): Keramiklager, Werkstoffe – Gleit- und Wälzlager – Dichtungen. Handbuch der Tribologie und Schmierungstechnik. Bd. 12. Expert Verlag, Renningen 2003. ISBN 3-8169-2050-0
Quellenangaben
- Narottam P. Bansal, Jacques Lamon: Ceramic Matrix Composites Materials, Modeling and Technology. John Wiley & Sons, 2014, ISBN 978-1-118-83289-9, S. XV (eingeschränkte Vorschau in der Google-Buchsuche).
- M. Kunz, „Ceramic Matrix Composites“, cfi/Bericht der DKG, Band 49, Nr. 1, 1992, S. 18
- M. Kunz: Risswiderstand keramischer Faserverbundwerkstoffe. Dissertation an der Universität Karlsruhe, Shaker Verlag, Aachen, 1996.
- A. Mühlratzer, M. Leuchs: Applications of Non-Oxide CMCs, aus: High Temperature Ceramic Matrix Composites, Hrsg. W. Krenkel et al., Wiley-VCH, Weinheim, 2001, ISBN 3-527-30320-0, S. 288
- H. Pfeiffer: Ceramic Body Flap for X-38 and CRV. 2nd International Symposium on Atmospheric Re-entry Vehicles and Systems, Arcachon, Frankreich, März 2001
- H. Pfeiffer, K. Peetz: All-Ceramic Body Flap Qualified for Space Flight on the X-38. 53rd International Astronautical Congress, Houston, Texas, USA, Oktober 2002, Paper IAF-02-I.6.b.01
- H. Lange, M. Dogigli, M. Bickel: Ceramic Fasteners für High Temperature Applications. 5th International Conference on Joining: Ceramics, Glas and Metal, Jena, Mai 1997, DVS-Berichte Band 184, Deutscher Verlag für Schweißtechnik, S. 55, ISBN 3-87155-489-8
- M. Dogigli, H. Weihs, K. Wildenrotter, H. Lange: New High-Temperature Ceramic Bearing for Space Vehicles. 51st International Astronautical Congress, Rio de Janeiro, Brasilien, Oktober 2000, Paper IAF-00-I.3.04
- N. Miriyala, J. Kimmel, J. Price, H. Eaton, G. Linsey, E. Sun: The evaluation of CFCC Liners After Field Testing in a Gas Turbine – III. ASME Turbo Expo Land, Sea & Air, Amsterdam, June 2002, Paper GT-2002-30585
- K.L. More, P.F. Tortorelli, L.R. Walker, J.B. Kimmel, N. Miriyala, J.R. Price, H.E. Eaton, E. Y. Sun, G.D. Linsey: Evaluating Environmental Barrier Coatings on Ceramic Matrix Composites After Engine and Laboratory Exposures. ASME Turbo Expo Land, Sea & Air, Amsterdam, June 2002, Paper GT-2002-30630
- W.E.C Pritzkow: Keramikblech, ein Werkstoff für höchste Ansprüche. cfi Sonderausgabe zum DKG-DGM Symposium Hochleistungskeramik 2005, W. Krenkel (Hrsg.), ISSN 0173-9913, S. 40
- W.E.C. Pritzkow: Oxide-Fibre-Reinforced Ceramics. cfi/Ber. DKG 85 (2008) No. 12, p.E1
- K. Gaffal, A.-K. Usbeck, W. Prechtl: Neue Werkstoffe ermöglichen innovative Pumpenkonzepte für die Speisewasserförderung in Kesselanlagen. VDI-Berichte Nr. 1331, VDI-Verlag, Düsseldorf, 1997, S. 275
- W. Kochanowski, P. Tillack: Neue Pumpenlagerwerkstoffe verhindern Schäden an Rohrgehäusepumpen. VDI-Berichte Nr. 1421, VDI-Verlag, Düsseldorf, 1998, S. 227
- J.L. Bozet, M. Nelis, M. Leuchs, M. Bickel: Tribology in Liquid Oxygen of SiC/SiC Ceramic Matrix Composites in Connection with the Design of Hydrostatic Bearing. Proceedings of the 9th European Space Mechanisms & Tribology Symposium (ESMAT), Liège, Belgien, September 2001, ESA Dokument SP-480, S. 35
- M. Bickel, M. Leuchs, H. Lange, M. Nelis, J.L. Bozet: Ceramic Journal Bearings in Cryogenic Turbo-Pumps. 4th International Conference on Launcher Technology – Space Launcher Liquid Propulsion, Liège, Belgien, Dezember 2002, Paper #129
- P. Boullon, G. Habarou, P.C. Spriet, J.L. Lecordix, G.C. Ojard, G.D. Linsey, D.T. Feindel: Characterization and Nozzle Test Experience of a Self Sealing Ceramic Matrix Composite for Gas Turbine Applications, ASME Turbo Expo Land, Sea & Air, Amsterdam, June 2002, paper GT-2002-30458
- B. Riccardi, L. Giancarli, A. Hasegawa, Y. Katoh, A. Kohyama, R.H. Jones, L.L Snead: Issues and Advances in SiCf /SiC Composite development for Fusion Reactors. Journal of Nuclear Materials, Band 329–333, 2004, S. 56
- W. Krenkel: Anwendungspotenziale faserverstärkter C/C-SiC-Keramiken, in Lit.: W. Krenkel, 2003, S. 220