Geschichte der Keramik
Die Geschichte keramischer Werkstoffe reicht mehrere tausend Jahre zurück.
Anfang bzw. Herkunft
Paläolithikum
Die ältesten Figuren aus Keramik, die jungpaläolithische Venus von Dolní Věstonice und mehrere Tierfiguren (25.000 bis 29.000 Jahre alt, Gravettien), fand man an einem Lagerfeuer der Mammutjäger in Mähren, „neben einer Anzahl roh geformter Klumpen“ aus Ton.[1] Die Tonklumpen sind mit pulverisiertem, verkohltem Elfenbein und Knochen gemischt,[2] was eine feuchte Aufbereitung erfordert. Diese magernden Zusätze können zur Arbeitserleichterung beim Schnitzen gedient haben, sie können aber auch aus kultischen Gründen erfolgt sein; die feuchte Aufbereitung braucht aber nicht zwingend zum plastischen Modellieren geführt zu haben. Diese Venus aus Ton fand sich an einem Brandplatz mit einer 80 Zentimeter hohen Aschenlage.
Tierfiguren sind aus Dolní Věstonice, Pavlov und Krems-Wachtberg bekannt.[3]
Die Entdeckung von Keramik als Töpferware aus Ton ist wahrscheinlich unabhängig voneinander in mehreren Regionen erfolgt.
Nordasien
Die ältesten Keramikgefäße des russischen Fernen Ostens stammen aus dem östlichen Sibirien Amur-Gebiet und sind durch Beschleuniger-Daten der vegetabilen Magerung auf 15.000 BP datiert.[4] Keramikgefäße sind auch aus der mesolithischen Jomon-Kultur Japans nachgewiesen, 12.350 ± 700 BC wurden die ersten niedrig gebrannten Zeremonialgefäße mit reichen plastischen Verzierungen hergestellt. Auch in Korea, China und der Mandschurei war frühe Keramik verbreitet, ohne dass dies mit einer neolithischen Wirtschaftsweise einherging[5][6] Das Alter von Funden aus der Höhle von Xianrendong in der Provinz Jiangxi wird auf Grund ihrer stratigraphischen Position auf bis zu 20.000 Jahren geschätzt.[7][8]
Spitzbödige Töpfe wurden von Jägern und Sammlern in weiten Teilen Nordasiens hergestellt. In Europa finden sie sich im östlichen Ostseegebiet, der südlichen Ukraine, in Finnland und Karelien (Sperrings-Kultur), Skandinavien (Grübchenkeramik), Dänemark (Ertebölle-Kultur) und den nördlichen Niederlanden (Swifterbant-Kultur).
Afrika
Im Sudan wurde Töpferware (Wavy line) von semisesshaften Jägern und Sammlern hergestellt. Keramik wurde von Jäger- und Sammlergruppen im heutigen westafrikanischen Mali im 10. Jahrtausend v. Chr. hergestellt (Fundplatz Ounjougou).[9] Im Nildelta trat Keramik erstmals im 9.–8. Jahrtausend v. Chr. auf.
Neolithikum
Lange Zeit sah die Forschung die Gefäßkeramik als ein charakteristisches Merkmal der neolithischen Revolution, Teil der "Neolithic package". Inzwischen ist jedoch deutlich geworden, dass es im Vorderen Orient eine akeramische Phase gab, die durch Sesshaftigkeit und Viehzucht charakterisiert wurde (PPNA, PPNB). Im Gegensatz dazu wurde Keramik in manchen Gegenden auch von Jägern und Sammlern hergestellt.[10]
Vorderer Orient
Die frühesten, noch ungebrannten Tongefäße fand man aus der Zeit um 7600–6300 v. Chr. in El-Khiam in der Wüste Juda in Westjordanland. Sie hatten wegen ihrer hohen Trockenbiegefestigkeit die Jahrtausende überstanden. Die ersten schwach gebrannten modellierten einfachen Formen fand man aus 7000 bis 6000 in Karim Schahir bei Jarmo im Zagros. Höher gebrannte und mit einem farbigen Streifen aus fein geschlämmtem Ton (Engobe) bemalte archaic painted ware gab es zwischen 6000 und 5600 in Tell Hassuna in Nord-Mesopotamien.[11]
In Tappe Sialk im Iran wurde im 4. Jahrtausend ein kuppelförmiger Ofen mit Lochtenne zu einem liegenden Ofen umkonstruiert, indem die Feuergase zum Absteigen gezwungen und durch einen Schornstein ins Freie gezogen wurden.[12]
3400 bis 2900 begann man Gefäße auf einem Stück Scherben zu drehen; das war die langsam laufende Töpferscheibe (Tournette). In der Halaf-Kultur findet sich eine dreifarbige Bemalung der Keramik, zum Beispiel in Tell Halaf und Arpachiya in Nord-Syrien. Schließlich kam es 3250 ±250 v. Chr.[13] (Uruk-Zeit) in Südmesopotamien zur Erfindung der Töpferscheibe.
Welches hohe Niveau die Töpferei zu dieser Zeit erreicht hatte, beweisen die nordmesopotamischen Kochtöpfe aus Stoneware oder metallic ware der frühdynastischen- und Akkadzeit, wie sie zum Beispiel in Tell Brak und Tell Chuera gefunden wurden. Sie sind stark versintert. Sie waren mit grobkörnigem Kalk gemagert und so flammfest, dass man sie in das offene Feuer stellen konnte. Nach Ansicht von G. Schneider ahmen sie metallische Formen nach.[14]
China
In der Yangshao-Kultur am Gelben Fluss im 8. Jahrtausend v. Chr. wurden meist Gefäße aus rotem, selten aus weißem Ton hergestellt, häufig mit eingedrückten Schnurmustern und Ritzlinien verziert, auch schwarz in geometrischen Mustern und sogar mit Tierdarstellungen und menschlichen Köpfen auf den Gefäßhälsen bemalt. Sie wurden im Hammer-und-Amboss-Verfahren oder aus Tonwülsten hergestellt. Daneben gab es eine Schwarz-Keramik, das heißt, das reduzierende Brennen war bekannt. Es wurden Erdöfen mit vorgelagerter Brenngrube und Lochtenne verwendet (Lung-Shan-Ofen seit dem 8. Jahrtausend v. Chr.).
Europa
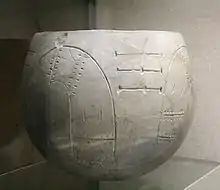
In Europa war die Töpferei schon seit dem 7. Jahrtausend v. Chr., seit dem frühen Neolithikum bekannt. Die Technik wurde vermutlich von Einwanderern aus Anatolien eingeführt. Viele neolithischen Kulturen sind nach den charakteristischen Keramiken benannt (z. B. Linearbandkeramik, Cardial-Kultur, Trichterbecher-Kultur, Glockenbecher-Kultur, Schnurkeramik). Auf dem Balkan war bemalte Keramik schon im Früh-Neolithikum gebräuchlich (Karanovo I/II). Weiter im Westen sind bemalte Gefäße nur sporadisch bekannt, dies mag an den schlechteren Überlieferungsbedingungen liegen. Die frühneolithische Cardial-Keramik des Mittelmeerraums war vor allem durch Muschelabdrücke verziert. Auch die Keramik der La-Hoguette-Gruppe ist abdruckverziert. In Teile von Nordeuropa waren spitzbodige Gefäße in der Tradition des Waldneolithikums in Gebrauch (s. o.).
Antike
Auf Kreta war die Töpferscheibe seit minoischer Zeit in Gebrauch.[15]
In der frühen Eisenzeit kamen schwarzfigurige und etruskische Gefäße in den Norden und beeinflussten die heimische Töpferei der Latènezeit. Die Töpferscheibe war in Mitteleuropa seit der Lt-Zeit bekannt, nun finden sich auch die ersten mehrkammrigen Keramikbrennöfen.
Die Herstellung von Terrakotten (terra cotta, italienisch für gebrannte Erde) begann im Paläolithikum. Aus neolithischer Zeit sind aus Südost- und Mitteleuropa zahlreiche Menschen- und Tierfiguren überliefert, meist zwischen 10 und 20 cm groß. Auch im minoischen Kreta wurden Menschen- und Tierstatuetten hergestellt.
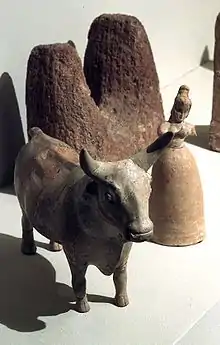
Mit zierlichen und reich bemalten Mädchenstatuetten der Werkstatt von Tanagra in Böotien kam es im 4. Jahrhundert v. Chr., ausgehend von Attika, zur Blütezeit der griechischen Terrakotta. Auch die römische Kaiserzeit kannte eine reiche Terrakotta-Produktion; zum Teil von hoher Qualität, wie die architektonisch verwendeten Campana-Reliefs (vom 1. Jahrhundert v. Chr. bis gegen Mitte des 2. Jahrhunderts n. Chr.), die ebenfalls farbig bemalt waren.
Griechische Töpfer bemalten ihre Tonvasen mit schwarzen Figuren. Sie benutzten dazu einen eisengefärbten illitischen Feintonschlicker. Das war eine Technik, bei der durch verschiedene Auftragsdicken der Malfarbe und durch oxidierenden (luftreichen) und reduzierenden (luftarmen) Brand Schwarz und Rot erhalten wurden. Die Athener brachten die um 700 v. Chr. in Korinth erfundene schwarzfigurige Malerei zur höchsten Blüte. Es folgte um 530 die rotfigurige (mit rotbrennendem Ton bei Reoxidation, rot „ausgesparten“ Figuren und schwarz abgedecktem Hintergrund) und um 480 die weißgrundige Malerei (mit reduzierter kupferroter Malerei auf einem weißbrennenden kaolinitischen Ton, dem Pottasche hinzugefügt wurde). Zum ersten Mal wurde die Keramik signiert.
In den griechischen Kolonien Unteritaliens und auch in Etrurien wurde in großem Umfang Feinkeramik produziert, die technisch wie ikonographisch an Vorbilder aus Korinth, Athen und Ostgriechenland anknüpft. Die im 4. Jahrhundert v. Chr. in Apulien hergestellten Gnathiavasen stellen einen letzten Höhepunkt dar.
Terra Sigillata wurde seit etwa 30 v. Chr. an dem Hauptfabrikationsort Arretium in Italien hergestellt, in späterer Zeit auch in vielen römischen Provinzen. In West-Kleinasien hielt sie sich noch bis ins 7. Jahrhundert. Die besondere Technik bestand darin, dass sie auf der Töpferscheibe in eine Formschüssel aus Ton eingedreht wurde, wobei sich die in die Formschüssel eingedrückten Vertiefungen als erhabene Reliefs abformten. Der überstehende Ton wurde als glatter Rand frei gedreht. Durch die Trockenschwindung löste sich die Keramik von selbst aus der Form. Nach dem Trocknen auf Lederhärte wurde sie mit einem Feinschlamm übergossen, der aus illitischem Ton, in Regenwasser aufgeschlämmt, gewonnen wurde. Dabei kam nach dem Absitzen der Aufschlämmung nur das Feinste als Beguss zur Verwendung. Die Ware wurde bei etwa 950 °C in korinthischen Öfen oxidierend gebrannt, wobei der Ofen immer so angelegt wurde, dass der Westwind in den Ofenhals blies. Dieser in Korinth erfundene Ofen mit Lochtenne war überall in Europa verbreitet und wurden erst in der Völkerwanderungszeit von den liegenden Öfen abgelöst, die die Slawen benutzten. In ihnen konnte man in reduzierendem Brand auch die schwarze Terra Nigra herstellen. Die rote Terra sigillata wurde in – für derartige Feinkeramik – großer Menge produziert. Die Manufaktur in Rheinzabern (Tabernae) etwa besaß im 2. Jahrhundert fünf Öfen, 100 bis 150 Beschäftigte und hatte eine Jahresproduktion von 35.000 bis 70.000 Gefäßen.
Glasuren
1922 bis 1925 fand der Ausgräber Guy Brunton in El Badari am östlichen Rand des Niltals „reichlich Perlen“, darunter glasierte Steatitperlen.[16] Sie stammten von nomadisierenden Rinderhirten aus der Zeit um 4000 v. Chr. Man erklärt sich die Herstellung dieser Perlen durch Brennen in einer Grube, in der sie mit dem Salz aus der Verdunstung des Grundwassers in Berührung kamen. Das durch das verdampfende Chlor auf den quarzhaltigen Stein (Steatit ist ein Magnesiumsilikat) transportierte Natrium kann mit diesem schon bei 867 °C eine Glasur bilden. Das war hundert Jahre früher als die erste Erzverhüttung. Mit diesem Verfahren, das man Zementation nennt, werden heute noch in Ghom, südlich von Teheran, Eselsperlen hergestellt. Das Natriumsalz[17] ist wasserlöslich und wird, wenn man es einer Masse aus Sand zusetzt, beim Trocknen mit dem verdunstenden Wasser an die Oberfläche transportiert, wie es die Natur mit dem salzigen Grundwasser tut. In diesem Ausblüh-(Effloreszenz-)Verfahren entstand im 3. Jahrtausend am oberen Nil die ägyptische Fayence. Sie beherrschte das Neue Reich in Ägypten (1552–1070). Blau, gelb, grün, rot, orange gefärbt, fand sie sogar neben Gold auf den Insignien der Pharaonen Platz. 700 Jahre später, um 1700 v. Chr., mischte man den lockeren Sandscherben nicht mehr mit Soda, sondern mit einer Sodafritte (sie wurde durch Schmelzen einer Mischung aus Soda und Sand hergestellt und nach dem Abkühlen zerkleinert; als Natriumsilikat war sie nicht mehr wasserlöslich). Jetzt konnte nichts mehr ausblühen, sondern die Glasur musste außen aufgetragen werden. Aus dieser jetzt festeren glasigen Fayence (glassy faience) entstand das Frittenporzellan, dessen Arkanum (alchemistisches Herstellungsgeheimnis) als „Persisches Porzellan“ 1752 von den Persern an Ludwig XIV. verkauft wurde und das seit 1766 heute noch in Marieberg und Rörstrand in Schweden hergestellt wird. Eine solche Frittenporzellan-Masse wird heute aus Lyon angeboten.
Für die Natrium-Silikat-Glasur tat sich im 1. Jahrtausend v. Chr. ein neuer Entwicklungsstrang auf, der mit der Glastechnologie verbunden war. Aus den Keilschrifttexten von Ninive geht hervor, dass das Glas aus einer Mischung von Sand und Pflanzenasche (aus der Verbrennung der salzhaltigen Pflanzen, der Halophyten) in zwei Stufen geschmolzen wurde. Dieses Glas wurde mit Pflanzengummi auf einen quarzreichen Scherben aufgeklebt und aufgeschmolzen. Im ganzen Vorderen Orient verbreitete sich diese Glasur nicht unter Verwendung der Soda aus den Salzseen, sondern aus der Asche der Salzpflanzen. In Europa werden diese Pflanzen als Schlickfänger zur Landgewinnung im Wattenmeer an der Nordseeküste eingesetzt und heißen Queller oder Glasschmalz. Die Asche dieser Salzpflanze war auch das Geheimnis der venezianischen Glasmacher. Sie pflanzten sie an verschiedenen Stellen des Mittelmeeres an. Das venezianische Glas war also ein Natronglas und ihr Geheimnis nichts anderes als das Rezept der Assyrer.
Die Glasur aus Sand und Soda oder Pflanzenasche war also auf den quarzhaltigen Untergrund angewiesen, und sie musste in zwei Stufen gebrannt werden, weil sonst der saugende Scherben die im Wasser gelöste Natriumverbindung weggesaugt hätte. Auf einem Ton hielt die Glasur nicht, denn sie hatte eine größere Wärmeausdehnung als ein Tonscherben. Mit vermindertem Alkali- und erhöhtem Erdalkaligehalt konnte sie zwar bei etwa 900 bis 1000 °C auf einen Tongrund aufgebrannt werden, der aber musste kalkreich sein, was im Vorderen Orient von Natur aus gegeben ist, nicht aber in Europa. Eine solche Glasur blieb mit engen Grenzwerten im Irak und Iran über Jahrtausende unverändert. Auf Quarzfrittescherben erreichte die Alkaliglasur ein technisches und künstlerisches Niveau, das weit über dem landläufiger Töpfereierzeugnisse stand.
Der Assyrerkönig Assurbanipal (669 bis etwa 627 v. Chr.) in seiner Bibliothek in Ninive schon ein Glasrezept auf eine Tontafel schreiben ließ und dieses Rezept auch zu einer Glasur führte.
Im 9. Jahrhundert erhielt Hārūn ar-Raschīd in Bagdad von dem Gouverneur von Chorasan „zwanzig Stück kaiserliches Porzellan“ aus China, das er nachahmen lassen wollte. Die irakischen Töpfer sahen wohl ein, dass ihnen die Natur nicht die gleichen Möglichkeiten bot wie den Chinesen. Mit ihren Erfahrungen mit Erdalkaliglasuren aus parthischer Zeit (250 v. Chr. bis 226 n. Chr.) schufen sie eine weiße Glasur, auf die sie mit Kobalt wie „mit Tinte auf Schnee“ malten. Die Weißtrübung erzielten sie durch Zinnoxid in der Glasur, deren Weißtrübung auf dem hohen Brechungsindex beruht. Die blaue Bemalung wurde von den Chinesen als „Hui-ch´ing = Mohammedanerblau“ übernommen (Kobalterz wurde aus dem sächsischen Erzgebirge importiert). Das kobaltbemalte Porzellan wurde zum überlegenen Exportprodukt der Ming-Zeit (1368–1644). Die Unmöglichkeit, das chinesische Porzellan nachzuahmen, führte zu einer neuen Erfindung, der Fayence, und in osmanischer Zeit wurde das Steingut à la porcellana erfunden. Die Fayence bestand aus einem naturfarbenen Scherben, der mit einer undurchsichtigen Glasur bedeckt ist, in die im rohen Zustand gemalt wurde („Inglasurmalerei“). Das Steingut hingegen bestand aus einem weißbrennenden Scherben, auf den gemalt wurde. Darüber kam eine durchsichtige Alkali-Blei-Glasur, wobei das Blei die Lichtbrechung erhöht und die Farben zum Leuchten bringt. Der Alkaligehalt beseitigt den Gelbstich der reinen Bleiglasur. Im Gegensatz zum europäischen Steingut enthielt die osmanische Steingutglasur kein Bor, obwohl es südlich von İznik, wo das Steingut erfunden wurde, große Colemanit-Lagerstätten gibt.
In China war die Glasur aus der Beobachtung erstanden, dass sich im Holzfeuer die Flugasche auf der Keramik absetzte und mit dem Tongrund eine Glasur bildete. Da die Holzaschen sehr kalkreich sind, waren es Calcium-Aluminium-Silikate, die schon bei 1170 °C schmelzen können. Die Chinesen erfanden diese Glasuren in der Zeit der West-Chou-Kulturen, 1122 bis 770 v. Chr. Das waren, wie im Vorderen Orient, die Glasuren vor dem Aufkommen des Auftragverfahrens. Etwa gleichzeitig mit dem Westen kamen in der dem Römischen Reich entsprechenden Han-Dynastie die Bleiglasuren auf, die mit Kupfer für Grün, mit Ocker für Honiggelb, mit Kobalt für Blau und mit Mangan für Violett gefärbt waren. Sie hörten erst mit den Buddhistenverfolgungen (9.–14. Jahrhundert) auf. Während die Bleiglasuren auf den vorgebrannten Scherben aufgetragen wurden, brannten die Chinesen fortan alles im Einbrandverfahren. Das Steinzeug war in der Han-Zeit aufgekommen und setzte sich in der Tang-Zeit mit einer Feldspat-Glasur bei 1260 °C fort, die die weitere Entwicklung beherrschte. Das mit eisengefärbten Glasuren versehenen Steinzeug erhielt in Frankreich die Bezeichnung „Seladon“, weil es der Farbe der Kleidung des Hirten Celadon in dem Theaterstück von Honoré d’Urfé nach dessen Schäferroman „L’Astrée“ im 17. Jahrhundert entsprach. Dem Porzellan ging ein weißes Steinzeug in der Tang-Periode voran, dem im späten 8. und frühen 9. Jahrhundert das Porzellan folgte. Einige Stücke kamen bald danach als Diplomatengeschenke nach Bagdad.
Als das Blei aufkam, weil es bei der Silbergewinnung in großen Mengen als Abfallprodukt anfiel, taugte die jetzt bleihaltige Glasur auch zum Glasieren der europäischen Tone. In römischer Zeit hatten die Betreiber der Terra-sigillata-Manufakturen offenbar keine Motivation, sich auf die Glasur einzulassen. Glasierte Keramik blieb relativ unbedeutend. Nach dem Zerfall des Römischen Reiches geriet die Technik wohl weitestgehend in Vergessenheit. Eine Ausnahme bildete die maurische Keramik in Spanien seit 711, als die Mauren nach Granada kamen, und im 13. Jahrhundert, als die Keramik unter den Nasriden mit persischen Töpfern, die vor den Mongolen geflohen waren, eine Blütezeit erlebte. Die Mudejar (= Steuerpflichtigen) stellten vom 11. bis zum 16. Jahrhundert in Andalusien Metalllüster (metallisch schillernde Glasuren) und blaubemalte Keramik im Mudejar-Stil her und exportierten sie von Málaga aus nach Italien, Sizilien und in den Nahen Osten.
Brennöfen
Keramikbrennöfen sind in Südosteuropa seit dem mittleren Neolithikum archäologisch belegt. In der Uruk-Zeit wurden in Mesopotamien Brenntemperaturen um 1000–1100°, manchmal auch noch darüber erreicht.[18] Schon im 4. Jahrtausend v. Chr. gab es im Vorderen Orient Zweikammer-Öfen, in denen Brennstoff und Brenngut getrennt waren. Die Öfen waren erst stehend (mit aufsteigender Flamme), dann – um 100 n. Chr. in Nordchina, in Europa im späten Mittelalter – liegend, um die Flammen besser auszunutzen, indem man sie durch den Zug eines Schornsteins durch den Ofen zog. Mit den liegenden Öfen tauchte erst das harte Steinzeug auf. Bis dahin brannten alle Öfen nur „periodisch“ (zeitweise). In China kannte man Kuppelofen mit der Feuerung unter der Tenne und Feuerzügen in den Wänden (Shang-Ofen seit dem 18. Jahrhundert v. Chr.), in denen man bei 1050 bis 1150 °C brannte. Der liegende Ofen mit Schornstein kam in China schon 100 n. Chr. auf (in Japan wurde er in die Bergwand gegraben). In der Song-Zeit (960–1279) wurde er mit einer Feuerwand („Ständer“) zwischen Heiz- und Brennraum versehen. Er war dann genauso konstruiert wie bei uns der Kasseler Ofen im 19./20. Jahrhundert. Moderne Industrieöfen, ob für Ziegel oder Porzellan, sind kontinuierlich brennende lange Tunnelöfen mit Temperaturregelung. Vor der Temperaturmessung und -regelung durch Thermoelemente wurde die Temperatur in ältesten Zeiten nach dem Niederschlag der Rauchgase, an der Farbe des Feuers, dann durch Ziehproben, mit optischen Pyrometern und seit 1886 mit den von Hermann August Seger (1839–1893) entwickelten Segerkegeln gemessen, die so zusammengesetzt waren, dass sie bei einer bestimmten Temperatur umsanken. Ähnliche schmelzende Pyrometer: Orton- und Staffordshire-Kegel (von Wedgwood) sowie schrumpfende (Bullers Ringe) wurden in England entwickelt. Als Brennstoffe dienten Rinder- und Schafsmist, Öl (heute noch in primitiven Öfen im Irak und in Mexiko), Holz, Kohle, Gas und Elektrizität.
Bis in die Gegenwart lag die übliche Brenntemperatur in der Töpferei der westlichen Hemisphäre bei 900 bis 1000 °C, der Steinzeugtöpfer mit liegenden Öfen seit etwa 1300 n. Chr. bei 1250 °C, während die Chinesen diese Temperatur schon in der Tang-Zeit (618–906) erreichten. Die großen Unterschiede lagen daran, dass im Vorderen Orient, von dem Europa abhing, keine höheren Temperaturen aufkamen, weil dort alle Tone schon über 1150 °C zu Klumpen zusammenschmelzen. Eine vermutlich höhere Temperatur erreichte Tschirnhaus 1687 in Dresden mit Brennspiegeln. Und das Porzellan Böttgers 1708 in Dresden war ein Hartporzellan, das höher gebrannt war als das Weichporzellan der Chinesen. Böttger brannte in einem liegenden Ofen, dem „Wiener Ofen“, den er verbesserte.
Mittelalter und Neuzeit
Die europäische Keramik außerhalb des griechisch-römischen Kulturkreises erreichte nicht dessen technische Perfektion. Nach dem Untergang des Römischen Reichs dauerte es lange, bis wieder in vergleichbarer Qualität produziert wurde. In den ehemals römischen Gebieten hielt sich die Tradition der Drehscheibe. Vielerorts überwog aber handgemachte oder nachgedrehte Keramik. Erst im Spätmittelalter, als die Töpferei zunehmend ein städtisches Handwerk wurde, wurde Scheibenware wieder dominierend. Die Kreuzritter staunten über das hohe Niveau der Keramik im Orient. Erst in der Frührenaissance trat die Werkstatt der Familie Della Robbia in Florenz hervor und wurde sogar von Leonardo da Vinci gerühmt. Luca della Robbia verwendete unter anderem die Zinnglasur, und man hielt ihn lange Zeit für deren Erfinder. Er galt trotzdem nicht als Keramiker, sondern als Bildhauer. Eine Keramik gab es als Kunst gar nicht, und selbst die Malerei wurde erst im Laufe der Renaissance als Kunst anerkannt. Die Keramik war an der von Religion und Geist bestimmten Kultur nicht beteiligt. Obwohl schon 1429 in Siegburg die Salzglasur (bei der man Kochsalz in die Feuerung warf) auf Steinzeug aufkam, herrschte der Niedrigbrand vor, denn die für den hohen Steinzeugbrand geeigneten Tone kommen nur um den 50. Breitengrad vor, und die Entwicklung wurde vom vorderen Orient beeinflusst, der nur über niedrig brennbare Tone verfügt. Dazu war nun die Bleiglasur wie geschaffen. Die ersten hervortretenden Persönlichkeiten waren Bernard Palissy in Frankreich, der Bunthafner Paul Preuning in Nürnberg und Cipriano Piccolpasso in Casteldurante, alle im 16. Jahrhundert. Schon im 14. Jahrhundert war die Zinnglasur nach Italien gekommen, und die Pest brachte einen großen Bedarf an Apothekergefäßen mit sich. Die zinnglasierte Keramik hieß noch nicht Fayence. Erst als die Guelfen unter Astorgio Manfredi 1313 in Faenza eine Stadtherrschaft (Signoria) errichteten, stieg Faenza zu einer Metropole der Keramik auf, und von hier verbreitete sich die nach der Stadt benannte Fayence nach dem Sturz der Manfredis 1501 und durch Flucht aus der Inquisition in ganz Europa. Hervorragend unter den schier unzählbaren Fayencemanufakturen waren Delft und die Provence (Moustiers, Marseille, Toulon) im 17. und 18. Jahrhundert. Mit Ausnahme der muslimischen Majolika in Spanien, die über Mallorca nach Florenz und andere Städte gelangt und als Majolika bezeichnet wurde, waren die europäischen Fayencen, die auf die türkischen Vorbilder zurückgingen, immer weiß glasiert und in die rohe Glasur bemalt („Inglasurmalerei“).
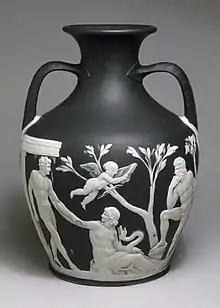
1748 desertierte der Maler Christian Wilhelm von Löwenfinck „in voller Montur“ und auf einem gestohlenen Pferd aus Meißen, von wo er Aufglasurfarben mitnahm. In Fulda bemalte er damit Fayencen und schuf damit die Aufglasurfayencen (faience à grand feu), die von da an die Fayencekunst beherrschte. Im 19. Jahrhundert wurde die Fayence in Europa durch Steingut abgelöst. Es besteht aus einem weißbrennenden Ton mit einer durchsichtigen Glasur über der Bemalung. Die Glasur ist eine Bleiglasur, die infolge ihrer hohen Lichtbrechung die Farben glänzen lässt. Zur Verbreitung des Steinguts in Europa haben die klassizistischen Erzeugnisse Wedgwoods beigetragen, die dem Zeitgeschmack entsprachen.
Hartporzellan
Die Erfindung des Hartporzellans durch Johann Friedrich Böttger und Ehrenfried Walther von Tschirnhaus am 15. Januar 1708 in Dresden (nach dem Brandprotokoll um 5 Uhr Nachmittag) wie auch des chinesischen Porzellans war der Beginn einer synthetischen Keramik, die nicht (wie das Steinzeug) vom Vorkommen eines bestimmten Tones abhängig war. Das Arkanum (das alchemistische Geheimnis der Herstellung) wurde streng gehütet und verbreitete sich erst 1720 in Wien, 1740 in Höchst, 1743 in Fürstenberg, 1850 in Berlin und Sankt Petersburg, 1755 in Frankenthal, 1758 in Nymphenburg, 1764 in Wallendorf und 1772 in Sèvres und Kopenhagen. Seit der Renaissance war Europa von Wissensdurst erfasst. Noch in der Barockzeit hatten fast alle europäischen Herrscher einen Hofalchimisten. Im siebzehnten Jahrhundert kam aber mit Newton, Leibniz, Descartes auch die Naturwissenschaft auf.
Weitere Erfindungen
Im Wettlauf um die Porzellanerfindung hatten die Italiener mit ihrer Führungsrolle in Fayence- und Glaskunst einen weiten Vorsprung. Die Ergebnisse waren aber nur Pseudoporzellane (z. B. das Medici-Porzellan in Florenz um 1575–1620). Einen großen Anteil an der technischen Entwicklung hatten Franzosen und Engländer. In England erfand 1748 Thomas Frye das Knochenporzellan, und Josiah Wedgwood (1730–1795) experimentierte an der Nachbildung von Achat. Er ließ die Konturen seiner chinoisen Malerei in Liverpool aufdrucken und zu Hause ausmalen. Das für ihn typische farbige, meist blaue Steingut mit aufgarnierten Reliefs von klassischen weißen Figuren, das er Jasperware nannte, erfand er 1774. Er machte Stoke-on-Trent zum Zentrum der englischen Keramikherstellung. Hier gelang auch Copeland & Garrett 1844 das dem parischen Marmor gleichende Biskuitporzellan (auch „Parian“), das bereits 1753 von Jean-Jacques Bachelier in der Manufaktur Vincennes erfunden worden sein soll.
Das industrielle Zeitalter
Wedgwood war nicht nur der erfolgreichste Keramiker des Klassizismus (er beschäftigte seit 1775 John Flaxmann, den Hauptmeister des englischen Klassizismus, als Modelleur), sondern er stellte auch eine der ersten Dampfmaschinen von James Watt und eine Drehbank in seinem Werk auf. Auch in Berlin installierte man nach dem Tod Friedrichs II. (1786) eine Dampfmaschine und baute 1797 den ersten Etagen-Rundofen. Der Klassizismus setzte hier schon 1767 mit dem „Antikzierat“ ein. In Sèvres führte man 1809 das Pressverfahren und 1816 das Gießverfahren ein. 1912 folgte das Pressluft-Gießverfahren. Maschinen, Öfen und Herstellungsverfahren waren voll von neuen Erfindungen. 1898 gab es das erste Patent für Tunnelöfen in Montereau, und 1906 ging der erste Porzellantunnelofen in Altwasser, Schlesien, in Betrieb. 1922 erhielt R. H. Staley in den Vereinigten Staaten das Patent auf eine Vakuumstrangpresse, 1946 Smith & Johnson in England auf eine Teller-Rollmaschine, 1964 wurde in Selb eine vollautomatische Gießanlage installiert.
Was Handwerk und Kunst betrifft, versuchten William Morris (1834–1896) und die 1888 von Charles-Robert Ashbee (1863–1942) gegründete Arts and Crafts Society, später, 1907, auch der Deutsche Werkbund, das Kunsthandwerk vor dem Ansturm der Maschine zu retten. Die Einflüsse des Vorderen Orients, die zur Fayencekunst geführt hatten, dauerten auf das europäische Kunsthandwerk noch so lange an, wie die hohen Brenntemperaturen noch eine Seltenheit waren. Noch 1919 galten für Max Laeuger (1864–1952) die Sultan-Abad-Fayencen des 12. bis 14. Jahrhunderts, die er 1910 auf der Ausstellung mohammedanischer Kunst in München kennenlernte, als Vorbilder. Mit der Weiterentwicklung der elektrisch beheizten Brennöfen und dem Aufkommen der Gasfeuerung nahm der Wunsch nach höheren Brenntemperaturen zu. So schwenkte das Vorbild auf die chinesischen Porzellane der Song-Zeit um, die auf der großen China-Ausstellung 1936 in London zu sehen waren. Die japanische Keramik wurde erst in der zweiten Hälfte des 20. Jahrhunderts, gefördert durch Bernard Leachs „Potters Book“, durch die aufkommende Reisetätigkeit und durch das Raku, das sich einer zunehmenden Popularität erfreute, als Vorbild aufgefasst, obwohl sie schon 1867 in das Blickfeld Europas geraten war, als der letzte Shogun der Tokugawa-Familie seine Familienschätze in Paris ausstellte. 1919 spaltete sich in dem von Walter Gropius (1883–1969) gegründeten Bauhaus das Industriedesign vom Kunsthandwerk ab. Und 1952 trennte sich in einer globalen Entscheidung in Kalifornien, angeführt von Peter Voulkos, die Kunst vom Kunsthandwerk und von jeglicher Tradition und folgte dem abstrakten Expressionismus. Das Kunsthandwerk blieb unter dem Einfluss der japanischen, von Bernard Leach verfochtenen Keramik. In der allgemeinen Massenbewegungen verbreitete sich die Freizeitkeramik, die nicht auf den finanziellen Erfolg bedacht war, sondern einen sozialreformerischen Ausgleich zur industriellen Welt suchte. Sie fand ihn weitgehend im Raku, das kein Gebrauchsprodukt hervorbringt, sondern ein Surrogat für Naturnähe mit Erde und Feuer darstellt.
In der Industrie-Epoche ging die Vorherrschaft der auf Ton beruhenden Keramik zu Ende. Das Gebrauchsgeschirr war am Ziel seiner Entwicklung angekommen. Wie in der Kunst, so hat sich auch in der Technik ein traditionsloser Strang abgespalten, dem eine größere Bedeutung zukommt.
Die traditionelle Keramik, das sind die silikatkeramischen Werkstoffe von der Töpferware bis zum Porzellan, aber auch Erzeugnisse für den technischen Gebrauch: Ziegel, Fliesen und Bauteile, Silikate mit geringer Wärmedehnung (Cordierit und Lithiumaluminiumsilikate) oder mit einer bestimmten Porosität, Steatit und schließlich Porzellane für die Elektrotechnik, die Sanitärtechnik und die Zahnmedizin.
In der Anwendung zählen auch die feuerfesten Werkstoffe zur keramischen Tradition. Dazu kommen aber auch neue Werkstoffe wie keramische Fasertypen für die Wärmedämmung und Zirkonsilikate für die Auskleidung von Schmelzwannen in der Glasindustrie und im Stahlgießbereich.
Indem sich die Technik in immer neue Gebiete ausbreitete, wuchs auch die Vielfalt der Werkstoffe, die keine Silikate sind und nicht mehr der keramischen Tradition, aber ihrer Definition entsprechen. Diese lassen sich in fünf Gruppen gliedern: Oxidkeramik, Elektro- und Magnetokeramik, nichtoxidische Keramik, Glaskeramik und spezielle Sonderwerkstoffe.
Im deutschen Sprachgebrauch hat sich die Bezeichnung Oxidkeramik für Werkstoffe eingebürgert, die in der Mehrzahl nur aus einem Oxid bestehen und durch Sinterung hergestellt werden: Aluminiumoxid dient als verschleißfester Werkstoff im Maschinen- und Anlagenbau, als korrosionsfestes Material in der chemischen Industrie, als Isoliermaterial in der Elektrotechnik und Elektronik oder als Hochtemperaturwerkstoff in der Wärmetechnik. Berylliumoxid wird in der elektronischen Industrie verwendet. Magnesiumoxid ist ein Hochtemperaturwerkstoff und wird als feuerfestes Material und in der Elektrotechnik eingesetzt. Yttriumoxid kann porenfrei gesintert werden und ist deshalb transparent. Seine Verwendung unterliegt zur Zeit der Forschung. Zirkonoxid wird in der Textilindustrie als Fadenführer, in der Metallherstellung als Strangpressmatrize, zum Erschmelzen bestimmter Metalle und zu Messinstrumenten in Industrieöfen und Motoren verwendet. Thoriumoxid spielt in der Nukleartechnik eine sehr wichtige Rolle. Es ist das höchstschmelzende Oxid mit einem Schmelzpunkt bei 3220 °C.
Elektro- und Magnetokeramik hat ein vielseitiges Anwendungsfeld. Hierher gehört die Bariumtitanatkeramik als dielektrischer Werkstoff für Kondensatoren und als Kaltleiter für PTC-Widerstände, das Bleizirkonat-Titanat als piezoelektrischer Werkstoff für elektrooptische Anwendung, Zink-Varistoren mit einem spannungsabhängigen Widerstand zum Schutz von Geräten vor Überspannungen und Heißleiter auf der Basis Aluminiumoxid/KupferIoxid für Fühler zur Temperaturmessung. Zur Magnetokeramik gehören weich- und dauermagnetische Ferrite (aus Eisenoxid mit Mn, Ni, Zn, Co, Cu, Mg beziehungsweise mit Ba, Sr, Pb) für die drahtgebundene Nachrichtentechnik beziehungsweise in elektromagnetischen Wandlern, Relais, Separatoren, Haftsystemen und Transporteinrichtungen.
Zur nichtoxidischen Keramik gehören Carbide, Nitride, Boride, Silicide, Sulfide und Fluoride. Unter den Carbiden ist das Siliciumkarbid am bekanntesten. Es besitzt eine hohe Härte, eine gute Wärmeleitfähigkeit und gute Temperaturfestigkeit. Kohlenstoff-Fasern werden aus Cellulose, Polyacrylnitril und anderen langkettigen organischen Verbindungen hergestellt und besitzen eine hohe Elastizität. Sie dienen zur Herstellung von Verbundwerkstoffen. Unter den Nitriden besitzt das Bornitrid „Borazon“ die größte Härte hinter dem Diamanten.
Als Glaskeramik bezeichnet man Werkstoffe, die aus Lithium- und Bariumsilikatgläsern hergestellt werden. Die erschmolzenen und erkalteten Glasformen werden mit UV-Strahlen belichtet, wobei sie kristallisieren. Die belichtete kristalline Phase wird mit verdünnter Flusssäure herausgelöst, wodurch maßhaltige Durchbrüche entstehen, die als Raster und Siebe mit bis zu 50.000 Löchern je Quadratzentimeter enthalten („Fotoform“-Verfahren). In diesem Verfahren lassen sich durch erneute Sinterung auch „Pyroceram“-Produkte herstellen, die für Raketenspitzen, Kochgeschirr, Astrospiegel und Herdplatten dienen. Im „Fotoceram“-Verfahren kristallisiert das zumeist lithiumhaltige Glas mit Titandioxid als Keimbildner, indem das Glasformstück einer zweiten Temperung unterworfen wird, wodurch es kristallisiert. Man erhält feinstkristalline Miniaturbauteile höchster Präzision für die Elektronik und Elektrotechnik.
Spezielle Sonderwerkstoffe spielen in der Nukleartechnik als Kernbrennstoffe, als Hüll- und Strukturmaterial und andere Verwendungen eine bedeutende Rolle. Für Brennelemente wird der keramische Brennstoff (Urandioxid) in Form zylindrischer Sinterkörper („Pellets“) in metallische Hüllrohre eingefüllt. Das Urandioxidpulver wird bei 1700 °C unter Wasserstoff gesintert. Keramische Werkstoffe für die Medizin werden als „Biokeramik“ bezeichnet. Sie werden in drei Gruppen eingeteilt:
- die inerten keramischen Werkstoffe für Implantate, vor allem Aluminiumoxid für Hüftgelenke, pyrolytischer Kohlenstoff für Herzklappen,
- bioaktive Keramik für die Verträglichkeit mit dem Gewebe. Dazu dienen Silikat-Phosphat-Gläser,
- resorbierbare Calciumphosphatkeramik.
Eine weitere Gruppe von Sonderwerkstoffen bilden keramische Überzüge auf Metallen, die im Flammspritzen (mit einem Brenngas) oder im Plasmaspritzen (im elektrischen Lichtbogen) aufgebracht werden. Die hohen Temperaturen im Plasma können bis zu 40.000 °C betragen. Als Beschichtungsstoffe dienen Oxide des Aluminiums, Titans, Chroms, Zirkons, jedoch auch Spinelle, Carbide, Nitride, Boride und Silicide. Andererseits werden zum Anbringen von Metallen auf Keramik Suspensionen von Metallpulvern in ätherischen Ölen verwendet, die eingebrannt, manchmal auch noch galvanisiert werden. Verbundwerkstoffe aus Keramik und Metall werden als Cermets bezeichnet. Die Herstellung erfolgt durch Sintern oder durch Infiltration einer porösen Keramik durch eine Metallschmelze oder durch Flammspritzen. Anwendung finden Cermets in der Hochtemperaturtechnologie und als Kontaktwerkstoffe in der Elektrotechnik.
Literatur
- Bryan Sentance: Atlas der Keramik. Haupt, Bern 2004, ISBN 3-258-06803-8.
- Rainer Schreg: Keramik aus Südwestdeutschland. Eine Hilfe zur Beschreibung, Bestimmung und Datierung archäologischer Funde vom Neolithikum bis zur Neuzeit. Lehr- und Arbeitsmaterialien zur Archäologie des Mittelalters und der Neuzeit (Tübingen 1998. 3. Aufl. 2007)
- Hochmittelalterliche Keramik am Rhein. Eine Quelle für Produktion und Alltag des 9. bis 12. Jahrhunderts, 13. Tagungsband des RGZM, Mainz 2012.
Einzelnachweise
- Karol Absolon: „Die Erforschung der diluvialen Mammutjägerstation“ von Unter-Wisternitz. 1924 (Arbeitsbericht).
- Miroslav Králík: Ancient ceramics and imprints on their surfaces. In: Jiři Svoboda: Pavlov – Excavations 2007–2011 (= Dolní Věstonice Studies, Band 18). Academy of Sciences of the Czech Republic, Brno 2011, ISBN 978-80-86023-85-4, S. 207–244 (Kapitel III.10.)
- Thomas Einwögerer: Die jungpaläolithische Station auf dem Wachtberg in Krems, Niederösterreich. Eine Rekonstruktion und wissenschaftliche Darlegung der Grabung von J. Bayer aus dem Jahre 1930. In: Mitteilungen der Prähistorischen Kommission Band 34. Wien 2000.
- Y. V. Kuzmin: The earliest centres of pottery origin in the Russian Far East and Siberia: review of chronology for the oldest Neolithic cultures. In: Documenta Praehistorica. 29, 2002, S. 37–46.
- Jeanette Werning: Früheste Scherben, frühester Reis, früheste Hirse. Zur Neolithisierung in China. In: Jörg Eckert, Ursula Eisenhauer, Andreas Zimmermann (Hrsg.): Archäologische Perspektiven. Analysen und Interpretationen im Wandel. FS Lüning Leidorf, Rahden/Westfalen 2003, S. 103–129.
- Elisabetta Boarettoa u. a.: Radiocarbon dating of charcoal and bone collagen associated with early pottery at Yuchanyan Cave, Hunan Province, China. In: PNAS. 2009, doi:10.1073/pnas.0900539106
Die ersten Töpfer lebten in China. In: wissenschaft.de. 2. Juni 2009, abgerufen am 9. September 2019. - Pottery 20,000 years old found in a Chinese cave. In: USA Today. 28. Juni 2012.
- Bruce Bower: Chinese pottery is oldest known. In: Science News 182/2, 2012, 15. JSTOR 41697713.
- Eric Huysecom: Wann begann Afrikas Jungsteinzeit? In: Spektrum der Wissenschaft. 8/2008, S. 62–67.
- Peter Hommel: Ceramic Technology. In: Vicki Cummings, Peter Jordan, Marek Zvelebil (Hrsg.): The Oxford Handbook of the Archaeology and Anthropology of Hunter-Gatherers. Oxford University Press, Oxford Online Publication, Oct 2013, doi:10.1093/oxfordhb/9780199551224.013.008
- Seton Lloyd, Fuad Safar, Robert J. Braidwood: Tell Hassuna Excavations by the Iraq Government Directorate General of Antiquities in 1943 and 1944. In: Journal of Near Eastern Studies, 4/4, 1945, fig. 7.I, JSTOR 542914
- Lindsay Scott: A History of Technology. Band 1. Oxford 1956
- Fundort? Kalibriert oder unkalibriert?
- Gerwulf Schneider: A technological Study of North-Mesopotamian Stone Ware. In: World Archaeology, 21, Nr. 1, 1989, S. 30–50, JSTOR 124483
- Tim Darvill: Potter’s wheel. The Concise Oxford Dictionary of Archaeology. Oxford, Oxford University Press 2008, ISBN 978-0-19-172713-9
- Guy Brunton, Gertrude Caton-Thompson: The Badarian civilisation and predynastic remains near Badari. 1928.
- Sabine Wenigwieser untersuchte in ihrer Dissertation 1992 die Salzseen im nordägyptischen Wadi Natrun. Danach sind es Na-Cl-Sole mit wechselnden Karbonat- und Sulfat-Anteilen. Die Chloridkonzentrationen betragen 10 bis über 50 Prozent in den einzelnen Seen. Mineralogische Untersuchungen an den Evaporiten und Tonen des Wadi el-Natrun. Universität Fridericiana zu Karlsruhe, 1992.
- Gerwulf Schneider: A technological Study of North-Mesopotamian Stone Ware. In: World Archaeology, 21/1989, S. 42, JSTOR 124483