Toluol-2,4-diisocyanat
Toluol-2,4-diisocyanat (TDI) ist eines der wichtigsten Isocyanate und ein wichtiges Zwischenprodukt der Kunststoffindustrie. Ende der 1930er Jahre erwies sich die Verbindung neben anderen Isocyanaten als eine ideale Ausgangssubstanz für Polyadditionsreaktionen und wurde von Otto Bayer und seinen Mitarbeitern in Leverkusen als aussichtsreiches Produkt für die Herstellung von Schaumstoffen (Polyurethanen) eingestuft.
Strukturformel | |||||||||||||||||||
---|---|---|---|---|---|---|---|---|---|---|---|---|---|---|---|---|---|---|---|
![]() | |||||||||||||||||||
Allgemeines | |||||||||||||||||||
Name | Toluol-2,4-diisocyanat | ||||||||||||||||||
Andere Namen |
| ||||||||||||||||||
Summenformel | C9H6N2O2 | ||||||||||||||||||
Kurzbeschreibung |
farblose bis gelbliche, stechend riechende Flüssigkeit[1] | ||||||||||||||||||
Externe Identifikatoren/Datenbanken | |||||||||||||||||||
| |||||||||||||||||||
Eigenschaften | |||||||||||||||||||
Molare Masse | 174,16 g·mol−1 | ||||||||||||||||||
Aggregatzustand |
flüssig[1] | ||||||||||||||||||
Dichte |
1,22 g·cm−3[1] | ||||||||||||||||||
Schmelzpunkt |
21 °C[1] | ||||||||||||||||||
Siedepunkt |
251 °C[1] | ||||||||||||||||||
Dampfdruck | |||||||||||||||||||
Löslichkeit | |||||||||||||||||||
Sicherheitshinweise | |||||||||||||||||||
| |||||||||||||||||||
Toxikologische Daten | |||||||||||||||||||
Soweit möglich und gebräuchlich, werden SI-Einheiten verwendet. Wenn nicht anders vermerkt, gelten die angegebenen Daten bei Standardbedingungen. |
Eigenschaften
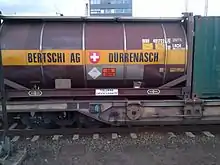
Toluol-2,4-diisocyanat ist eine sehr giftige Flüssigkeit. TDI ist gut in organischen Lösungsmitteln löslich (beispielsweise in Benzol oder in Toluol), es reagiert mit Wasser unter relativ langsamer Zersetzung (Bildung polymerer Harnstoffe und Kohlenstoffdioxid). Deshalb müssen organische Lösungsmittel wasserfrei sein, wenn sie zur Synthese mit TDI verwendet werden sollen.
Die Verbindung bildet bei höheren Temperaturen entzündliche Dampf-Luft-Gemische. Ihr Flammpunkt liegt bei 127 °C,[4] der Explosionsbereich liegt zwischen 0,9 Vol.‑% (64 g/m3) als untere Explosionsgrenze (UEG) und 9,5 Vol.‑% (685 g/m3) als obere Explosionsgrenze (OEG).[4] Die Zündtemperatur beträgt 620 °C.[4] Der Stoff fällt somit in die Temperaturklasse T1.
Den Markt dominieren drei verschiedene Isomerengemische bzw. Produkte: Den weitaus größten Anteil hat hier das Gemisch aus 80 % Toluol-2,4-diisocyanat und 20 % Toluol-2,6-diisocyanat unter Handelsnamen wie „Desmodur T 80“ (Covestro AG) oder „Lupranat T 80“ (BASF AG), ferner T 65 aus 65 % Toluol-2,4-diisocyanat und 35 % Toluol-2,6-diisocyanat. T 100 dagegen besteht aus nahezu 100 % Toluol-2,4-diisocyanat.
Die weltweiten Jahreskapazitäten betragen etwa 1,5 Mio. Tonnen (Stand: 2005) und TDI ist neben MDI das am meisten hergestellte Isocyanat. Es wird heute in Großanlagen um die 100.000 Jahrestonnen und mehr produziert, z. B. in Dormagen, Brunsbüttel, Schwarzheide (D), in Baytown (USA), in Japan und seit 2006 in Caojing (China). Im November 2016 ging in al-Dschubail (Saudi-Arabien) die weltgrößte Produktionsanlage der Fa. Sadara Chemical Company, ein Gemeinschaftsunternehmen von Dow Chemical und Saudi Aramco, in Betrieb. BASF hat am Standort Ludwigshafen im November 2015 eine TDI-Anlage mit einer Kapazität von 300.000 Jahrestonnen in Betrieb genommen (Kosten ca. 1 Mrd. Euro).
Kleinere Anlagen in Leverkusen, Tarragona (E), Antwerpen (B) und New Martinsville (USA) wurden Ende des 20. und Anfang des 21. Jahrhunderts im Rahmen weltweiter Konsolidierungsmaßnahmen geschlossen.
Herstellung
Die Herstellung von TDI kann auf unterschiedlichen Wegen erfolgen:
Der Weg über die Nitrierung von Toluol und darauf folgender katalytischer Hydrierung mit Wasserstoff zu 2,4-Diaminotoluol (2,4-Toluoldiamin, TDA), welches schließlich phosgeniert wird, ist ein technisch ausgereifter Prozess mit hohen Ausbeuten.

Ein Nachteil dieses Verfahrens ist, dass das hochgiftige Phosgen als ein Reaktant eingesetzt werden muss und dass die meisten so produzierenden Chemieanlagen mit leichtem Überdruck arbeiten. Diese Basenphosgenierung ist jedoch immer noch der wirtschaftlichste Herstellungsprozess und der weltweit am häufigsten angewandte. Er wurde seit Inbetriebnahme der ersten Großanlage 1953 in Leverkusen ständig optimiert. Um das Risiko eines Phosgenausbruchs, bzw. die Exposition dieses Gases in die Umwelt so gering wie möglich zu halten, sind die Sicherheitsvorkehrungen einer solchen Chemieanlage sehr streng reglementiert und redundant. Sie unterliegt in Deutschland der Störfall-Verordnung. Das Grundprinzip liegt darin, die während des Prozesses im Umlauf befindliche Phosgenmenge so gering wie möglich zu halten (keine Phosgenlagertanks etc., siehe Bhopalunglück). Die Anlage muss bei Störungen selbsttätig abschalten und das austretende Phosgen durch Ammoniakdampf schnellstmöglich vernichtet werden. Hierzu gibt es in der Industrie spezielle Sicherheitseinrichtungen. Durch Phosgenierung in der Gasphase, also ohne ein Lösemittel als Trägerflüssigkeit, kann eine Chemieanlage drucklos, also mit leichtem Unterdruck betrieben werden. Gasaustritte werden damit schon rein physikalisch extrem erschwert.
Alternativ kann TDI durch die Oxidehydrierung von Formamiden hergestellt werden. So kann auf die Handhabung von Phosgen verzichtet werden. Hierbei handelt es sich jedoch noch nicht um ein ausgereiftes Verfahren.
Basenphosgenierung von TDA
Das Verfahren läuft in mehreren Schritten in einer kontinuierlich arbeitenden Chemieanlage. Diese Schritte sind im Einzelnen:
- Phosgenherstellung
- Phosgenabsorption
- Phosgenierung
- Entphosgenierung
- Lösemitteldestillation
- Rückstandsabtrennung
- Isocyanatreinigung
Träger der Ausgangsstoffe Phosgen und Toluoldiamin (leicht alkalisch, daher Base) sowie der Reaktionsprodukte ist das Lösemittel ortho-Dichlorbenzol (ODB oder ODCB). Die Edukte werden vor der Reaktion beide damit vermischt; das Produkt TDI muss anschließend durch Destillationsprozesse davon getrennt werden. Das wiedergewonnene ODB wird im Kreislaufverfahren erneut eingesetzt.
Für die Herstellung von Phosgen werden die Gase Chlor und Kohlenstoffmonoxid (CO) zunächst vermischt, wobei es hierbei aufgrund der hohen Aktivierungsenergie (95 kJ/mol) noch zu keiner Reaktion kommt. Durch Überleiten des Mischgases über den Katalysator Aktivkohle kann diese auf etwa 30 kJ/mol herabgesetzt werden. Dadurch springt die Reaktion schon bei ca. 40–50 °C an. Hierbei werden bei vollständigem Umsatz 106,7 kJ/mol Energie frei. Die Reaktion ist somit exotherm, die entstehende Wärme des Reaktors muss durch eine Kühleinrichtung abtransportiert werden.
Von diesen drei Stoffen hat das Chlor die größte Affinität zur Aktivkohle und adsorbiert bevorzugt. Gleichzeitig ist gewährleistet, dass gebildetes und adsorbiertes Phosgen sofort durch neu hinzuströmendes Chlor desorbiert wird. Um das Chlor vollständig umsetzen zu können, wird ein geringer Überschuss an Kohlenmonoxid gewährleistet. Die Austrittstemperatur des entstandenen Gasgemisches muss deutlich unter 100 °C liegen, damit noch keine Dissoziation merkbar wird. Phosgen beginnt bei steigender Temperatur erneut in die Ausgangsstoffe zu zerfallen (bei 200 °C sind ca. 5 % Phosgen dissoziiert, bei 800 °C liegen praktisch nur noch CO und Chlor vor).
Das Phosgen wird nun in kaltem ODB gelöst. Die Löslichkeit ist hoch, so dass Massenanteile von 60 % COCl2 und mehr erreicht werden können. Das zuvor bei ca. 140 °C aufgeschmolzene Toluoldiamin (TDA) wird in heißem ODB verdünnt.
Die Phosgenierungsreaktionen setzen sich aus einer kleinen Anzahl Hauptreaktionen und einer Unzahl von Nebenreaktionen zusammen. Sie lassen sich in zwei Unterverfahrensschritte, der Kalt- und Heißphosgenierung zusammenfassen. Vor Beginn ist es wichtig, einen großen Überschuss an Phosgen einzusetzen. Dieser sollte mindestens 300 %, jedoch möglichst nicht höher als 400 % liegen. Maßgeblich ist hierbei der Anteil des 2,4-TDA im Isomerengemisch. Je größer dieser ist, desto höher muss der Phosgenüberschuss liegen, da die sterisch günstige 4er-Stellung der zweiten Aminogruppe einfacher von Phosgenmolekülen erreicht werden kann als die seitlich durch die Methylgruppe abgeschirmte 6er-Aminogruppe des 2,6-TDA. Ein zu hoch gewählter Phosgenüberschuss würde hierbei zu einer unerwünscht schnellen Phosgenierung führen.
Aus den ersten exothermen Hauptreaktionen der Kaltphosgenierung entstehen vereinfacht fünf feste Zwischenprodukte, die eine Suspension in ODB bilden: Carbaminsäurechlorid, Bis-Carbaminsäurechlorid, Aminhydrochlorid, Bis-Aminhydrochlorid sowie Verbindungen mit beiden chemischen Gruppen.
Diese Zwischenprodukte müssen nun durch Zuführung von viel Wärme weiter umgesetzt werden. Aus den Carbaminsäurechloriden wird durch Wärmeeinwirkung Chlorwasserstoff (HCl) endotherm abgespalten, es entsteht TDI. Des Weiteren setzt Phosgen die Aminhydrochloride unter wiederholtem HCl-Ausschluss ebenfalls zu TDI um. Die Löslichkeit von Chlorwasserstoff in ODB ist kaum vorhanden, so dass es sofort zum Ausgasen des Reaktions-Chlorwasserstoffs kommt.
Während der Heißphosgenierung ist das Entstehen von einigen unerwünschten und irreversiblen, rückstandsbildenden Nebenverbindungen (Harnstoffe, Biurete, Isocyanurate u. v. m.) unvermeidlich, jedoch auf ein Minimum zu begrenzen. Die Weichen für eine hohe Ausbeute (95 % und mehr) müssen dabei bereits in der Kaltphosgenierung durch optimale Mischungs-, Strömungs- und Temperaturverhältnisse gestellt werden. Der Aufbau der Heißphosgenierreaktoren ist äußerst wichtig. Damit es nicht zu unerwünschten Nachchlorierungen durch den Chlorwasserstoff oder Überphosgenierungen kommt, sind die Verweilzeiten der Moleküle zu straffen. Im Optimalfall sollten alle Moleküle die annähernd gleiche Verweilzeit haben. Hierzu sind die turmartigen, zylindrischen Reaktoren schlank und hoch ausgeführt, Rückströmungen werden durch viele Lochböden verhindert oder zumindest auf den Raum zwischen zwei Böden begrenzt (Kammerung). Die für die endothermen Reaktionen notwendige Wärme sollte zu einem Großteil unmittelbar beim Eintritt in den Reaktor zugeführt werden um eine schnellstmögliche Umsetzung zum TDI zu erzielen. Der Apparatewerkstoff dieser Heißphosgeniertürme muss aufgrund des stark korrosiven HCl-Dampfes einen hohen Nickel-Anteil aufweisen (z. B. Inconel 600).
Am Austritt der Heißphosgenierreaktoren wird die flüssige Rohware (ca. 15 % TDI, 80 % ODB, 5 % Phosgen und Rückstandsprodukte aus Nebenreaktionen) vom heißen Prozessgas (Phosgenüberschuss, HCl) zwangsläufig getrennt. Die Prozessgase gehen zurück in die Phosgenabsorption wo das Phosgen einerseits zur Phosgenlösung zurückgeführt, andererseits der Chlorwasserstoff ausgeschleust wird. Dieser wird in einer separaten Anlage in ca. 18%iger Salzsäure in einem azeotropen Verfahren absorbiert. Die daraus entstehende ca. 30%ige Salzsäure ist sehr rein und kann mehreren Verwendungszwecken zugeführt werden.
Die Rohware wird parallel durch einen ersten Destillationsschritt entphosgeniert, in dem ein Großteil des noch gelösten Phosgen durch Wärme abgetrennt wird. Anschließend erfolgt die destillative Abtrennung des ODB, des Rückstandes und die Reinigung des TDI von nicht erwünschten Nebenkomponenten wie z. B. hydrolysierbaren Chlorverbindungen oder Tetrachlorkohlenstoff. Diese erfolgt im besten Fall in hintereinander geschalteten Rektifikationskolonnen, kann jedoch auch in einer einzigen, entsprechend ausgelegten Kolonne mit bspw. Glockenböden durchgeführt werden. Aufgrund des hohen Siedepunktes von TDI werden diese Verfahrensschritte als Vakuumdestillationen durchgeführt.
Verwendung
In der chemischen Industrie ist TDI ein wichtiges Zwischenprodukt für die Herstellung von Klebstoffen, Schaumstoffen für Matratzen und Polsterungen, Polyurethane (z. B. für Schuhsohlen), Elastomeren, Beschichtungen und hochwertigen Lacken zur Verwendung in der Automobilindustrie, für Flugzeug- oder Triebwagenlackierungen sowie für die Produktion von Schmierstoffen.
Sicherheitshinweise
Die Dämpfe reizen Augen und Atemwege sehr stark. Nach dauerhafter Einatmung der Dämpfe ist ein Lungenödem möglich, das verzögert auftreten kann. Der Arbeitsplatzgrenzwert liegt mit 0,005 ppm[1] sehr niedrig, da langfristige Einwirkungen auf die Lunge die Sensibilisierung der Atemwege bis hin zu asthmatischen Erkrankungen zur Folge haben können.
Weblinks
Einzelnachweise
- Eintrag zu Toluol-2,4-diisocyanat in der GESTIS-Stoffdatenbank des IFA, abgerufen am 20. Januar 2022. (JavaScript erforderlich)
- Datenblatt Toluene 2,4-diisocyanate bei Sigma-Aldrich, abgerufen am 24. April 2011 (PDF).
- Eintrag zu 4-methyl-m-phenylene diisocyanate im Classification and Labelling Inventory der Europäischen Chemikalienagentur (ECHA), abgerufen am 1. Februar 2016. Hersteller bzw. Inverkehrbringer können die harmonisierte Einstufung und Kennzeichnung erweitern.
- E. Brandes, W. Möller: Sicherheitstechnische Kenngrößen - Band 1: Brennbare Flüssigkeiten und Gase. Wirtschaftsverlag NW – Verlag für neue Wissenschaft GmbH, Bremerhaven 2003.