Punktschweißelektrode
Punktschweißelektroden übertragen den Schweißstrom und die Elektrodenkraft auf die Werkstücke beim Widerstandspunkt- und Buckelschweißen. Ein vom Punktschweißen abgeleitetes Verfahren ist das Rollennahtschweißen, das sich drehende Rollen als Elektroden nutzt.[1] Elektroden sind damit das unmittelbare Schweißwerkzeug, das den Stromübergang von der Stromquelle in das Werkstück übernimmt, den Stromfluss in den Fügeteilen konzentriert und die Schweißteile fixiert. Sie bestehen aus leitfähigen Werkstoffen und müssen an die spezielle Schweißaufgabe abgepasst werden.
Form und Aufbau von Widerstandspunktschweißelektroden
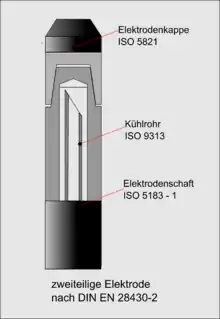
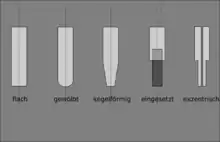
Die Form und die geometrischen Abmessungen der Elektroden beeinflussen die Wärmebilanz des Schweißprozesses, die Zugänglichkeit des Schweißgerätes zum Werkstück und das Verhalten des Eindringens in das Material während des Erwärmungsprozesses. Die Materialwiderstände der Elektroden sollten möglichst klein gehalten werden. Ihre Querschnitte sollten möglichst groß, ihre Längen kurz und ihre spezifischen elektrischen Widerstände niedrig sein, denn für die Stoffwiderstände gilt:[6]
mit
- … Elektrodenlänge,
- … spezifischer Widerstand,
- … Elektrodenquerschnitt.
Die Elektroden können ein- oder zweiteilig aufgebaut sein. Zweiteilige Elektroden bestehen aus einem gekühlten Elektrodenschaft und aufgesetzten Elektrodenkappen unterschiedlicher Form. Von der Wahl der Kappenform hängt der Schweißbereich und die Prozesssicherheit (Prozessfähigkeit und -beherrschung), letztlich die Schweißbarkeit des Bauteils ab. Die EN ISO 5821[4] und das DVS Merkblatt 2903[7] unterscheiden sieben Kappenformen. Davon abweichend werden in der Praxis verschiedenste Sonderformen eingesetzt. In der Feinwerk- und Elektrotechnik finden einteilige Elektroden verschiedener Form Verwendung.[3]
Form und Aufbau von Rollennahtelektroden
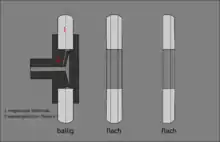
Die Rollenelektroden haben die zusätzliche Aufgabe den Werkstücktransport zu übernehmen. In fast allen Fällen bestehen die Elektroden aus einem Rollenpaar. Für gerade Nähte, zum Beispiel bei Längsnähten von Hohlkörpern, wird eine der beiden Rollenelektroden durch einen zylindrischen oder profilierten Dorn ersetzt.[8]
Die Stromdichte wird durch die Breite der Elektrodenkontaktfläche bestimmt. Die Rollendurchmesser müssen den konstruktiven Gegebenheiten des Werkstücks angepasst sein. der Je Zugänglichkeit zur Schweißstelle werden Rollenschweißelektroden zum Nahtschweißen gerade oder mit einseitiger bzw. beidseitiger Flanke ausgeführt. Das Rollenprofil wird dem zu schweißenden Werkstoff angepasst und kann ballig oder flach sein. Flache Profile werden zum Schweißen blanker Stahlbleche angewendet. Bei metallisch beschichteten Stahlblechen und Leichtmetallen kommen ballige Elektroden zum Einsatz.
Die Elektroden werden oft als Ringe ausgeführt, die in einen wassergekühlten Flansch eingespannt sind.
Elektrodenwerkstoffe
Auch die Wahl des Elektrodenmaterials beeinflusst den erreichbaren Schweißbereich und die Prozesssicherheit (Prozessfähigkeit und -beherrschung).
Erwünschte Materialeigenschaften ist eine hohe elektrische Leitfähigkeit (oftmals angegeben in %IACS – International Annealed Copper Standard – elektrische Leitfähigkeit im Vergleich zu Kupfer) zur Verringerung von elektrischen Leistungsverlusten. Bei Anwendung an niedrigleitenden Fügeteilen wird eine hohe thermische Leitfähigkeit und bei hochleitenden Fügeteilen eine niedrige thermische Leitfähigkeit gewünscht. Elektroden sollen eine hohe Härte bei Raum- und Schweißtemperatur zur Formbeständigkeit und Vermeidung von Mikrorissen aufweisen. Die Neigung zur Anlegierung an Werkstück oder Elektrode sollte gering sein.[9]
Die Werkstoffe werden in der EN ISO 5182[10] nach Werkstoffgruppe, -typ und -nummer bezeichnet:
- Gruppe A – Kupfer- und Kupferlegierungen (drei Werkstofftypen)
- Gruppe B – Gesinterte Werkstoffe (sechs Werkstofftypen)
- Gruppe C – Dispersionsgehärtete Kupferlegierungen (DSC) (zwei Werkstofftypen)
International gebräuchlich sind Elektrodenwerkstoffe nach AWS-RWMA.[11] Es werden zwei Materialgruppen (Kupferwerkstoffe, Sinterwerkstoffe) mit unterschiedlichen Materialklassen unterschieden, die ihre Entsprechungen in den Werkstoffen nach EN ISO 5182[10] finden.
Die Eignung von Materialien für das Widerstandspunktschweißen ist in hohem Maße von der Wahl günstiger Elektrodenwerkstoffe abhängig. Das DVS-Merkblatt 2903[7] enthält eine Tabelle: "Schweißeignung und Auswahl der Elektroden nach dem Werkstoff der zu verbindenden Metalle".
Elektrodenverschleiß und Standmenge
Elektroden unterliegen während ihres Gebrauchs durch die thermische, mechanische und chemische Beanspruchung einem Verschleiß. Die Elektrodenoberflächen vergrößern sich durch das stete Aufschlagen und Pressen der Elektroden auf die Werkstücke. Außerdem kommt es besonders bei beschichteten Materialien zu Anlegierungen an der Elektrodenoberfläche. Durch die größere Fläche wird die Stromdichte geringer und durch die Anlegierungen der Übergangswiderstand größer. Der Elektrodenverschleiß wird beim Punkt- und Buckelschweißen durch den Begriff Standmenge beschrieben. Die Standmenge ist gemäß EN ISO 8166:
„Die Elektrodenstandmenge ist […] für alle Werkstoffe definiert, als die Anzahl der Schweißungen, welche die vorgegebene Schweißqualität erfüllen, bevor eine Nacharbeit der Elektrodenkontaktfläche notwendig wird. Eine Elektrode hat ihre Standmenge erreicht, wenn die damit hergestellten Schweißungen einen Punktdurchmesser (festgestellt im Schälversuch) unter 3*√t haben (bei drei von fünf aufeinander folgenden Schweißungen in einem Prüfstück, dabei ist t die Blechdicke in mm) […].“[12]
Die Elektrodenstandmenge wird von verschiedenen Faktoren beeinflusst. Die Form, Masse, der Werkstoff und die Anlegierungsneigung der Elektrodenkappe sind wesentlich. Während des Schweißens wirken die Kühlung und die Wahl der Schweißparameter auf die erreichbare Standmenge ein. Diese ist auch abhängig von den Eigenschaften des verschweißten Materials, dessen Dicke und Beschichtung. Das Auf- und Nachsetzverhalten der Schweißgeräte spielt ebenfalls eine Rolle. Die Elektrodenstandmenge kann durch regelmäßige mechanische Bearbeitung der Elektrodenoberflächen durch Fräsen oder Umformen wesentlich erhöht werden.[13]
Elektrodenkühlung
Die Elektroden beim Widerstandspunktschweißen werden im Allgemeinen von Innen durch Wasser gekühlt. Es sollte der Wasserdurchfluss mindestens 4 l/min betragen, beim Schweißen von beschichtetem Stahl werden jedoch höhere Durchflussgeschwindigkeiten empfohlen. Das Kühlwasserzuflussrohr sollte so angeordnet werden, dass das Wasser auf die Rückseite der Elektrode einwirkt. Die Einlasswassertemperatur sollte kleiner als 20 °C sein, die Auslasstemperatur 30 °C nicht übersteigen.[14]
Auch Rollenelektroden beim Rollennahtschweißen müssen ausreichend gekühlt werden, besonders dann, wenn Stahlbleche mit metallischen Überzügen sowie Aluminium- und Magnesiumlegierungen geschweißt werden, da diese zu einer Legierungsbildung mit dem Werkstoff der Rollenelektrode neigen. Bei großen Elektrodendurchmessern wird über die Welle (Bild „Elektrodenrollen mit balligem und flachem Profil“), bei kleinen auch über ein Wasserbad gekühlt. Im erstgenannten Fall wird das Kühlwasser in der Regel dem Hohlraum der Elektrode oder dem Flansch der Elektrodenwelle zugeführt.[1]
Einzelnachweise
- DVS Widerstands-Rollennahtschweißen – Verfahren und Grundlagen, DVS-Merkblatt 2901-1, 2006
- DIN EN 28430-2:1992: Elektrodenhalter – Teil 2: Morsekegelbefestigung
- MiyachiUnitek: Fundamentals of Small Parts Resistance Welding
- DIN EN ISO 5821:2009: Widerstandsschweißen – Punktschweiß-Elektrodenkappen
- DIN ISO 669:2001-06: Widerstandsschweißeinrichtungen – Mechanische und elektrische Anforderungen
- DVS: Widerstandspunktschweißen von Stählen bis 3 mm Einzeldicke, DVS-Merkblatt 2902-4, 2001
- Elektroden für das Widerstandsschweißen, Merkblatt DVS 2903, 1998
- DVS Widerstands-Rollennahtschweißen – Verfahren und Grundlagen, DVS-Merkblatt 2906-1, 2006
- DVS: Widerstandsschweißen in der Elektronik und Feinwerkstechnik – Übersicht und Grundlagen, DVS-Merkblatt 2950
- DIN EN ISO 5182:2009-08: Widerstandsschweißen – Werkstoffe für Elektroden und Hilfseinrichtungen
- Resistance Welding Manufacturing Alliance (RWMA)
- DIN – Deutsches Institut für Normung: Verfahren für das Bewerten der Standmenge von Punktschweißelektroden bei konstanter Maschinen-Einstellung EN ISO 8166
- Standmengenerhöhung beim Widerstandsschweißen durch Elektrodenfräsen. (PDF) GSI, IMWF; Forschungsvorhaben AiF-Nr. 13.134 N / DVS-Nr. 4.031
- DIN EN ISO 14327:2004: Widerstandsschweißen. Verfahren für das Bestimmen des Schweißbereichsdiagramms für das Widerstandspunk-, Buckel- und Rollennahtschweißen