Prozessregelung beim Widerstandspunktschweißen
Die Prozessregelung beim Widerstandspunktschweißen hat die Aufgabe, den Schweißprozess bei sich ändernden Einflussgrößen so zu führen, dass eine ausreichende Verbindungsqualität des entstehenden Schweißpunktes gewährleistet wird. Das versucht man durch gezielte Änderung der Schweißparameter mit Parametersteuerung oder in geschlossenem Regelkreis zu erreichen. Mögliche Regelgrößen sind der Schweißstrom Is, die Schweißspannung Us, die Schweißleistung Ps, die Schweißenergie Ws oder die Schweißkraft Fs. Eine Regelung der elektrischen Größen und der Kraft spielt besonders beim Kleinteil- und Aluminiumschweißen eine besondere Rolle, aber auch beim Schweißen von Teilen mit beschichteten Oberflächen, da sich die Widerstandsverhältnisse zwischen Elektrode und Fügeteil und zwischen den Fügeteilen im Prozessverlauf stark ändern.
Ungeregelter Schweißprozess
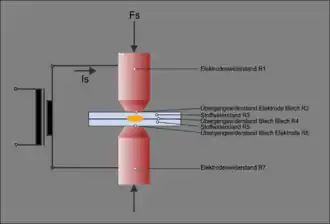
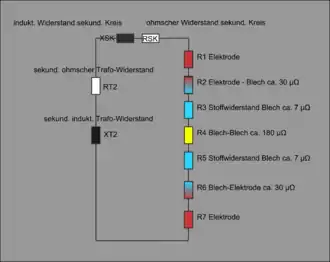
(Widerstandspunktschweißprozess beim Schweißen unlegierter Stahlbleche mit blanker Oberfläche).
Im Verlauf des Schweißprozesses ändern sich die Übergangs- und Stoffwiderstände R2...6, die für die Erwärmung der Schweißstelle maßgeblich sind. Nach dem Aufbau der Elektrodenkraft und dem Einschalten des Schweißstroms Is verringern sich die Übergangswiderstände R2,5,7 durch Einebnen der Oberflächenrauhigkeit. Die beginnende Erwärmung lässt die Stoffwiderstände R3,5 bis zu einem Maximum steigen. Das Material erweicht, die Elektrode dringt teilweise in das Material ein, der Widerstand sinkt. Daraus ergibt sich ein materialtypischer sogenannter dynamischer Widerstandsverlauf.

Wird das Schweißen bei annähernd gleichem Effektivwert der Spannung (konstanter Phasenanschnittswinkel beim Netzfrequenzschweißen, konstante Pulsbreite beim Inverterschweißen) durchgeführt, stellt sich der Stromfluss nach dem ohmschen Gesetz ein. Bei stark schwankenden Widerstandsverhältnissen kommt es zu sehr unterschiedlicher Erwärmung und damit zu Schweißverbindungen verschiedener Größe und Festigkeit.
Stepperfunktion
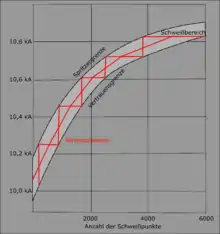
Beim Punktschweißen verschleißen die Elektroden mit zunehmender Anzahl der Schweißungen, wodurch der Widerstand kontinuierlich fällt, die Schweißpunkte werden kleiner. Zur Erzielung gleicher Punktdurchmesser muss der Schweißstrom auf vorgegebene Sollwerte geregelt und gezielt erhöht werden. Das kann die sogenannten Stepperfunktion leisten. Ein Schweißpunktzähler registriert die Anzahl der geschweißten Punkte. Bei vorzugebenden Zählerständen wird der Schweißstrom entweder schrittweise oder kontinuierlich erhöht. Die Stromsollwerte müssen experimentell ermittelt werden. In heutigen automatisierten Anlagen wird die Stepperfunktion mit dem Kappenmanagement (Kappenfräsen und -wechseln) kombiniert.
Voraussetzung für die Wirkung der Stepperfunktion ist eine Konstantstromregelung.
Konstantstromregelung
Den Schweißstrom konstant zu halten ist eine Möglichkeit zur Stabilisierung des Schweißprozesses. Bei der Konstantstromregelung wird der Schweißstrom sekundärseitig mit Hilfe einer Rogowskispule gemessen und mit dem vorgegebenen Sollwert verglichen. Die Stellgröße zur Konstantregelung ist entweder der Zündwinkel der Thyristoren bei der Netzfrequenzschweißung oder die Pulsbreite beim Inverterschweißen. Dadurch können solche Störgrößen wie Netzspannungsschwankungen, Sekundärimpedanzänderungen oder Oberflächenveränderungen teilweise erkannt und kompensiert werden. Bei Netzfrequenzanwendungen arbeitet der Regler periodenbezogen, die Ansprechzeit des Reglers liegt bei 20 ms. Inverter reagieren je nach Frequenz deutlich schneller.
Angebracht ist die Konstantstromregelung für das Schweißen flächiger Verbindungen mit relativ gleichbleibenden Übergangswiderständen. Bei extremen Änderungen der Widerstandsverhältnisse durch Änderung des Stromleitungsquerschnitts innerhalb einer Schweißung (z. B. bei Kleinteil- und Mikroschweißen, Kreuzdrahtschweißen, Buckelschweißen) kann die Konstantstromregelung zu ungenügender Schweißenergie führen, wenn der Widerstand durch Querschnittsverbreiterung während der Prozesszeit sinkt oder zum Überhitzen, wenn der Widerstand steigt.
Beispiel: Beim Buckelschweißen von Schweißmuttern, die nicht ideal gleichmäßig aufsetzen: Einseitiges Aufsetzen führt zu hohem Widerstand bei geringem Stromquerschnitt. Die Konstantstromregelung führt zu einem Schweißstrom, der für den vollen Schweißquerschnitt eingestellt ist. In der Folge wird das Material überhitzt und verspritzt. Die erforderliche Schweißqualität kann nicht erreicht werden.
Konstantkraftregelung
Mit konstanter Schweißkraft wird eine Widerstandsverringerung infolge der mit der thermischen Ausdehnung einhergehenden Krafterhöhung verhindert. Weiterhin wird das Nachsetzverhalten deutlich verbessert, da es mit dem Aufschmelzen der Linsen zu einem Krafteinbruch kommen kann. Durch die Konstantkraftregelung kann grundsätzlich der Schweißstrom reduziert werden, was sich positiv auf den Verschleiß der Kappen auswirkt.
Konstantspannungsregelung
Durch sich schnell ändernde Übergangswiderstände infolge der Änderungen der Oberflächenverhältnisse oder Berührungsflächen (Buckelformen) oder Kraftvariation ändert sich der Wärmeeintrag bei gleichbleibendem Strom. Die Folge können Spritzer oder ungenügende Erwärmung sein. Wird die Spannung konstant gehalten, kann der Strom sich den Verhältnissen innerhalb gewisser Grenzen selbständig anpassen. Dieser Regelungstyp ist bei Kreuzdrahtschweißungen und buckelähnlichen Schweißungen besonders auch beim Kleinteil- und Mikroschweißen bedeutsam.
Konstantleistungsregelung
Diese Regelungsart kann zur Kompensation von Elektrodenverschleiß und -anlegierung nützlich sein. Anwendungen findet man besonders beim Kleinteil- und Mikroschweißen.
„Adaptive“ oder „intelligente“ Regler
Die Stabilisierung des Schweißprozesses und der Qualität wird durch regelnden Eingriff in die elektrischen Größen vorgenommen. Dazu wurden in den vergangenen Jahren unterschiedliche Konzepte für den industriellen Einsatz entwickelt. Schweißstrom oder -zeit werden entsprechend dem aktuellen Prozesszustand mit dem Ziel geändert, die Qualität des Schweißpunktes auf ein gewünschtes Niveau zu bringen.
Eine Größe, die den Prozesszustand widerspiegelt und zur Regelung des Prozesses herangezogen werden kann, ist der dynamische Widerstand Rs(t)[2]. Auf der Basis der Messung von Strom und Spannung wird nach der Bildung der Effektivwerte der Widerstand als deren Quotient berechnet. Daraus wird ein Stellsignal für den Schweißstrom generiert. Wie das Stellsignal gewonnen wird, beschreibt das Patent[2] nicht.
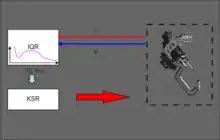
Ein weiteres Konzept ist eine Erweiterung des Konstantstromreglers (KSR)[3]. Es werden Is(t) und Us(t) an der Schweißzange gemessen. Daraus wird der aktuelle Widerstand bzw. die Leistung berechnet. In Abhängigkeit vom Widerstandsverlauf oder der Leistung wird der Stromsollwert des KSR geändert, und notfalls wird zusätzlich die Schweißzeit verlängert.
Ein drittes Konzept basiert auf dem Prinzip der Referenzschweißung. Auch hier wird der Verlauf des dynamischen Widerstandes zur Prozesscharakterisierung herangezogen. Es werden zunächst sogenannte Referenzschweißungen durchgeführt, während der der Schweißstrom auf den eingestellten Wert mit KSR geregelt wird. Bei optimaler Wahl von Schweißzeit, Schweißstrom und Elektrodenkraft wird ohne Störungen eine gute Schweißverbindung erreicht. Die Daten von Schweißstrom und Elektrodenspannung werden abgespeichert. Nach dem Umschalten auf eine Betriebsart „Regeln“ werden alle folgenden Schweißungen so geregelt, dass sie den gespeicherten MASTER-Referenzdaten weitgehend entsprechen[4].
Auf der technischen Grundlage der Erfassung der Prozessspannung direkt zwischen den Kappenoberflächen über virtuelle Messleitungen wurde ein viertes Konzept entwickelt.[5][6]
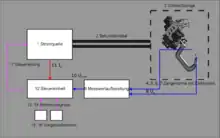
Die innerhalb der Schweißzange liegenden Messpunkte für die Spannung werden über eine „Virtuelle Maschine“ (nach P. Puschner, 1992) auf die Berührungsstellen der Kappen mit dem Bauteil transformiert. Damit können die aktuellen Prozessparameter Impedanz, Leistung und Energie im 50-µs-Zyklus ermittelt werden. Anstelle der bekannten Prozesssteuerungen nach einem Strom-/Zeitprogramm wird die von der Gesamtblechdicke abhängige Energie eingebracht. Für jeden einzelnen Punkt wird hierzu über ein integriertes präzises Messsystem nach dem Schließen der Zange die aktuelle Gesamtblechdicke ermittelt. Dem Verfahren liegt ein kaloriemetrisches Modell zugrunde, welches aufgrund des erforderlichen Linsenvolumens und damit der geometrische Ausdehnung der Linse den erforderlichen Energieeintrag einschließlich der durch Wärmeableitung in die wassergekühlten Elektroden und in das umgebende Bauteil kalkuliert und als Führungsgröße benutzt. Daraus folgt unabhängig von prozessbedingten Impedanzveränderungen während des Fügens aber auch durch die jeweilige Werkstoffkombination der sichere erforderliche Energieeintrag, der wiederum in der Konsequenz einen deutlichen Fortschritt bei der Qualitätssicherung von Punkt zu Punkt darstellt.
Anhand des Bildes Prozessregelung beim Widerstandspunktschweißen mit „Virtueller Maschine“ soll das Verfahren erläutert werden. Eine schnell steuerbare Stromquelle (1) ist über die Leistung führenden Kabel (2) mit einer Schweißzange (3) verbunden. Am Ende der beiden Zangenarme befinden sich die Elektroden, an deren Oberflächen die momentane Prozessspannung erfasst werden soll. Von Messpunkten für die Spannungserfassung an den Einspannvorrichtungen der Arme in der Zange führen Messleitungen über eine Messwertverarbeitungseinheit (9) zur Steuereinheit (12) (Virtuelle Maschine), die die realen Messleitungen auf die Kappenoberflächen transformiert und damit virtuelle Messleitungen (8) erzeugt. Aus dem so erzeugten Spannungssignal (10) (Prozessspannung) und dem Stromsignal (11) wird die momentane Prozessimpedanz berechnet. Die Steuereinheit erhält in Abhängigkeit von der gemessenen Gesamtblechdicke über die Sensorik (13) für die verschiedenen Prozessphasen Führungsgrößen aus einer Datenbank (14) für die einzubringende Energie und das momentan wirkende statische und dynamische Generatorverhalten einer virtuell an den Kappenoberflächen gebildeten elektrischen Quelle. Je nach Anforderung des Prozesses wird die wirkende Quelleneigenschaft im 50-µs-Zeitraster dem Prozessgeschehen angepasst. Durch die Einstellbarkeit der Generatoreigenschaften während unterschiedlicher Prozessphasen lässt sich die Spritzerbildung weitestgehend vermeiden und in der Regel vollständig unterbinden. Über die Steuerungseinheit wird das Leistungsteil beeinflusst.[6]
Referenzen
- M. Krause: Widerstandspreßschweißen. DVS-Verlag, Düsseldorf 1993, ISBN 3-87155-531-2.
- Patent DE4317557C1: Vorrichtung zur Schweißstromregelung beim Punktschweißen mit einem nach dem Effektivwertverfahren arbeitenden Messgeber zur schnellen Erfassung des Istwertes des Widerstandes zwischen den Elektroden. Erfinder: St. Köbler.
- Th. Jansen, J. Eggers, R. Bothfeld: GeniusMFI IQR - a new inverter power supply with adaptive regulation system to assure the quality for resistance spot welding. IIW-Document III-1480-08, 2008.
- Matuschek Messtechnik GmbH: MASTER Regelverfahren
- P. Puschner: Punktschweißen mit „Virtueller Maschine“. In: Schweißen und Schneiden. 57, H. 1–2, 2005.
- Patent DE10334478B4: Verfahren und Vorrichtung zum Widerstandsschweißen. Erfinder: G. Kölzer, P. Puschner, D. Regner, W. Riether.