Schlauchfilter
Ein Schlauchfilter ist in der Fluidtechnik ein Filter (Oberflächenfilter), bei dem das Filtermedium zu einem Schlauch geformt ist.[1] Als filternde Abscheider haben Schlauchfilter sich in der Filtertechnik, Gasreinigung und Entstaubung bei zahlreichen industriellen Prozessen durchgesetzt.
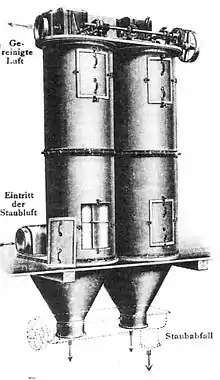
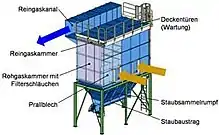
Als ihr Erfinder gilt Wilhelm Beth aus Lübeck.[2]
Wurden die Filter in früheren Jahren durch Klopfen, Rütteln oder in Kombination mit Niederdruckspülung gereinigt, so erfolgt dies heute mit Druckluft.
Ausführung
Schlauchfilter bestehen aus Fasermaterial, das zu Schläuchen gewoben ist. Wurden früher häufig Naturfasern eingesetzt, so haben sich mittlerweile bei industriellen Anwendungen synthetische Fasern weitgehend durchgesetzt.[3] In der Heißgasfiltration finden metallische Drahtgewebe Anwendung.[4]
Die Länge einzelner Filterschläuche liegt in der Regel zwischen 1,5 m und 8 m.[1]
Filtervorgang
Das Rohgas wird idealerweise im Kreuzstrom zu den Filterschläuchen geführt, um eine Aufströmung entgegen der Sedimentationsrichtung der Partikel zu vermeiden. Das Rohgas wird über eine Verteilerplatte gelenkt, an der eine Vorabscheidung stattfindet und der Rohgasstrom im Filtergehäuse vergleichmäßigt wird. Die eigentliche Abscheidung der Partikel findet an der Oberfläche des Filtermediums bzw. des sich darauf abscheidenden Filterkuchens statt. Das gereinigte Gas strömt nach oben aus dem Schlauch ab.
Die entsprechenden Strömungswiderstände resultieren aus den Druckverlusten des Filterkuchens sowie des Filtermediums direkt nach der Jet-Pulse-Abreinigung (Restdruckverlust). Speziell bei langen Schläuchen (z. B. eine Schlauchlänge von 8 m bei einem Schlauchdurchmesser von 160 mm) und hohen Filterflächenbelastungen ist der Druckverlust über den Schlauchboden, d. h. bei Austritt aus dem Schlauch über die Einlaufdüse in den Reingasbereich, ebenfalls von Bedeutung. Dieser und sämtliche weiteren Strömungswiderstände des Filtergehäuses (Rohgaseintritt bis Filterkuchenoberfläche, Reingasströmung ab Schlauchaustritt bis Austritt Reingaskanal) werden im Gehäusedruckverlust zusammengefasst.
Abreinigung
Vibrationsmethode
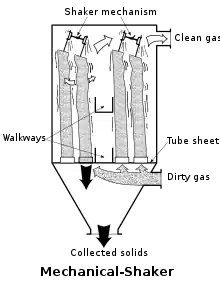
Bei der ältesten Abreinigungsmethode, durch manuell zu betätigende oder motorische Rüttelvorrichtungen (Vibration), wird zeitabhängig oder bei Erreichen eines maximalen Filterwiderstandes ein Motor gestartet, der das Filterelement in Schwingung versetzt. Bei der sich daraus ergebenden Bewegung löst sich der angelagerte Filterkuchen von der Filteroberfläche und fällt nach unten in einen Staubsammelbehälter, der in der Regel durch Staubaustragsorgane geleert wird. Die mechanische Abreinigung wird nach Unterbrechung des Filtrationsbetriebs durchgeführt. Nachteilig an der Abreinigung durch Rütteln ist, dass die Filterschläuche mechanisch beansprucht werden und daher nur relativ kurze Standzeiten aufweisen.
Rückspül-Methode
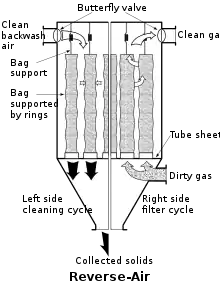
Ein schonenderes Abreinigungsverfahren besteht in der periodischen Umkehrung der Strömungsrichtung durch Spülluft (Rückspülung). Hierbei ist die Filteranlage in mehreren separaten Kammern ausgeführt, die einzeln abgereinigt werden. Vielfach wurde auch die Kombination der Abreinigungsmethoden Vibration und Rückspülung realisiert.
Druckstoß-Methode
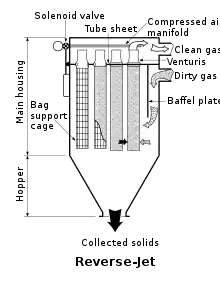
Die in der Filtertechnik am häufigsten, inzwischen weitgehend als Standard angewandte und modernste Form der Abreinigung ist das Druckstoßverfahren (Jet-Pulse-Abreinigung). Bei dieser Methode werden die Filterschläuche, anders als bei den beiden o. g. Methoden, im Filterbetrieb von außen nach innen durchströmt und benötigen daher Stützkörbe, die ihnen die erforderliche Stabilität verleihen. Die Abreinigung erfolgt durch einen zyklischen, intensiven Druckluft-Stoß ins Schlauchinnere, der den Filterschlauch kurzzeitig in Überdruck versetzt. Die Filterschläuche werden kurz aufgebläht, die Strömungsrichtung umgekehrt (nun von innen nach außen) und der Filterkuchen von der Schlauch-Außenseite abgelöst. Nach der Abreinigung der Filterschläuche sedimentieren die Staubpartikel in den Staubsammelraum, und das Material wird von dort zumeist über Förderschnecken und Zellenradschleusen abtransportiert.
Die Abreinigung hat so zu erfolgen, dass sich der Filterkuchen über die gesamte Schlauchlänge vollständig ablöst. Parallel ist das Zurückschlagen des Mediums auf den Stützkorb durch entsprechende Modulation des Druckverlaufs zu minimieren.
Die Abreinigungszyklen hängen u. a. ab von
- der Filterflächenbelastung (Volumenstrom pro Filterfläche und Zeiteinheit)
- der Gasdichte
- der Rohgasbeladung
- den Partikeleigenschaften.
Der Übergang von Verfahren der Spülluftabreinigung zur Jet-Pulse-Abreinigung hat durch die wirksame Entfernung der sich periodisch ablagernden Filterkuchen erheblich zur Steigerung der Energieeffizienz beigetragen.
Betriebsweisen
In der Online-Betriebsweise werden die in der Rohgaskammer befindlichen Partikel kontinuierlich anfiltriert. Direkt nach der Jet-Pulse-Abreinigung ist die Partikelkonzentration in der Nähe des Filterschlauchs sehr hoch. In diesem Zustand kommt es, insbesondere bei feindispersen Stäuben mit geringer Agglomerationsneigung, zum Wiederanfiltrieren abgereinigter Partikel. Diese „innere“ Staubzirkulation kann einen erheblichen Anteil an der Filterkuchenmasse verursachen und trägt damit zum Druckverlust bei.
Zur Steigerung der Energieeffizienz werden daher Filtermodule durch roh- und/oder reingasseitige Absperrorgane während der Abreinigung in einen strömungslosen Zustand versetzt. In diesem Offline-Modus wird die sofortige Wiederanlagerung des Staubes an benachbarten Filterschläuchen unterbunden. Dies kann auch erreicht werden, indem der Filter mit einem Druckluftimpuls von wesentlich niedrigerer Intensität gereinigt wird.
Steuerung
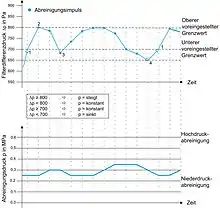
Die Steuerung der Abreinigung erfolgt heute über Mikroprozessortechnik und Feldbussysteme. Neben der Steuerung der Membranventile werden die pneumatisch oder elektrisch betätigten Roh- und Reingasklappen angesteuert und Signale von Feldsensoren, beispielsweise „broken-bag-Wächtern“, verarbeitet.
Bei Taktung der Druckstöße wird unterschieden zwischen
- einer festen Zeitsteuerung und
- der Differenzdrucksteuerung mit variablen Zykluszeiten.
Ein weiterer Steuerungsparameter ist die kontinuierliche Regelung des Tankdrucks des Druckluftspeichers. Dabei wird über die kontinuierliche Anpassung des Abreinigungsdrucks der Druckluftbedarf den jeweiligen Betriebsbedingungen angepasst. So dient der Filterdifferenzdruck als Regelgröße der vordruckgeregelten Abreinigung (s. Abb.). Vorteile dieser Methode: Die Betriebsdaten der Entstaubungsanlage werden bei minimalem Druckluftbedarf im gewünschten Betriebspunkt gehalten, der Staubanfall wird gleichmäßiger, die Kapazität der Staubaustragsorgane wird besser ausgenutzt, und die Filterschläuche werden geringer mechanisch belastet.
Injektor-Technologien
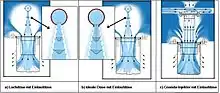
Entscheidend für einen energieeffizienten Betrieb von Schlauchfiltern ist das zweistufige Injektorsystem, das bei der periodischen Regenerierung die Druckluft einbringt.
Injektorsysteme können beispielsweise aus einem Blasrohr mit einfachen Bohrungen bestehen, aus denen die Druckluft ausströmt (linker Teil der Abb.). Durch die nachgeschaltete Venturi-Einlaufdüse wird Sekundärluft angesaugt und eine Erhöhung des statischen Drucks im Filterschlauch erzielt. Die Einlaufdüse stellt eine Optimierung mit verminderten Strömungsverlusten dar.
Durch Aushalsung der Einlassbohrung zu einer „Idealen Düse“ wird eine weitere Effizienzsteigerung bei Umwandlung der Druckluftenergie in einen Abreinigungsimpuls erreicht (mittlerer Teil der Abb.).
Eine sehr effiziente Abreinigungstechnologie stellt der Coanda-Injektor dar (rechter Teil der Abb.). Dieses Abreinigungssystem nutzt den Coanda-Effekt, bei dem die Druckluft aus einem Ringspalt austritt und über eine gewölbte Oberfläche geführt wird. Die Primärluft folgt dabei der Grenzschicht, die durch die Geometrie des Coanda-Injektors nicht ablöst. Dabei entsteht innerhalb der ersten Injektorstufe ein extrem hoher Unterdruck, der weitere Sekundärluft ansaugt und einen Treibstrahl ausbildet, der gegenüber den zuvor beschriebenen Varianten eine deutlich erhöhte Luftmenge aufweist. Dieser Treibstrahl tritt in die Einlaufdüse als zweite Injektorstufe ein, in der weitere Sekundärluft angesaugt wird.
Literatur
- Friedrich Löffler: Staubabscheiden. G. Thieme Verlag, Stuttgart-New York (1988), ISBN 3-13-712201-5
- Intensiv Filter GmbH & Co. KG (Hrsg.): Entstaubungstechnik, Filtermedien. Intensiv-FilterTaschenbuch. 3. Auflage, 1989.
- H. Meyer zu Riemsloh, F. Kordas: Entstaubung großer Abgasvolumenströme mit filternden Abscheidern. Aufbereitungstechnik 33 (1992) Nr. 12, ISSN 1434-9302, S. 673–683.
- Gunnar-Marcel Klein, Tim Neuhaus, Peng Bai, Theo Schrooten, Tobias Daniel: Verminderung der durch die Partikelablagerung verursachten Druckverluste in industriellen Schlauchfiltern. F & S Filtrieren und Separieren 23 (2009) Nr. 3, ISSN 1432-3559, S. 134–139.
- Tim Neuhaus, Peng Bai, Theo Schrooten, Gunnar-Marcel Klein: Steigerung der Energieeffizienz in der industriellen Gasreinigung durch optimierte Oberflächenfiltration. In: Gefahrstoffe - Reinhalt. Luft. 70 (2010), Nr. 6, ISSN 0949-8036, S. 231–236.
- VDI-Richtlinie VDI 3677 Blatt 1:2010-11 Filternde Abscheider – Oberflächenfilter. Beuth Verlag, Berlin.
Einzelnachweise
- VDI 3677 Blatt 1:2010-11 Filternde Abscheider; Oberflächenfilter (Filtering separators; Surface filters). Beuth Verlag, Berlin. S. 28.
- Rüdiger Segenbusch: Zeitenwende – Fabriken in Lübeck. Lübeck 1993, ISBN 3-7950-0114-5, Kapitel: Beth und Dräger – Ohne Idee keine Fabrik.
- VDI 3677 Blatt 1:2010-11 Filternde Abscheider; Oberflächenfilter (Filtering separators; Surface filters). Beuth Verlag, Berlin. S. 13.
- VDI 3677 Blatt 3:2012-11 Filternde Abscheider; Heißgasfiltration (Filtering-separators; High-temperature gas filtration). Beuth Verlag, Berlin, S. 23.