Zellstoff
Als Zellstoff (englisch chemical pulp oder kurz pulp) bezeichnet man die beim chemischen Aufschluss von Pflanzenfasern entstehende faserige Masse, die vorwiegend aus Cellulose besteht. Zellstoff ist, neben Holzschliff, ein wichtiger Rohstoff der Papierherstellung. 90 % des weltweit erzeugten Zellstoffs wird aus Holz hergestellt.[1] Die Verwendung von Stroh, Bagasse, Kenaf oder Bambus als Rohstoff geht weltweit deutlich zurück.
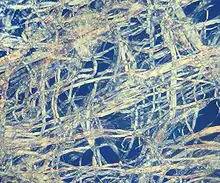
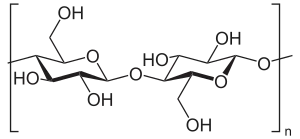
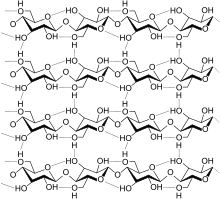
Die Herstellung von Zellstoff erfolgt regional unterschiedlich aus Industrierestholz oder Plantagenholz. In Europa und Nordamerika wird beispielsweise Sägerestholz (meist Nadelholz) verwendet. In Südamerika, Südafrika und Australien wird oft Laubholz aus Waldplantagen (schnellwachsender Eukalyptus) eingesetzt. Das Holz wird zunächst entrindet und dann zu geschnitzeltem Holz (Hackschnitzel) verarbeitet. Anschließend wird das Holz chemisch aufgeschlossen:
- Vorherrschend ist das alkalische Sulfat-Verfahren, mit dem über 95 % der Weltproduktion hergestellt werden. Sowohl Laub- als auch Nadelholz kann verwendet werden.
- Daneben gibt es das saure Sulfit-Verfahren. Nur noch 2 % bis 3 % werden nach diesem Verfahren hergestellt. Der Aufschluss von stark harzhaltigem Holz, wie Kiefernholz, ist hierbei selten. Meist wird Fichten-, Buchen- oder Eukalyptusholz verwendet. Das Sulfitverfahren hat eine stabile Marktnische bei der Herstellung von Viskosezellstoff.
Es wird qualitativ zwischen Nadelholz- und Laubholzzellstoff unterschieden. Nadelholz-Sulfatzellstoff hat lange, feste Fasern von durchschnittlich 3,3 mm Länge und gibt Papier dadurch eine Armierung. Laubholz-Zellstoff hat kürzere Fasern von etwa 1 mm Länge. Er eignet sich für die Herstellung von glatten Papieren (Schreib-, Kopierpapier) oder Tissue (Hygienepapier).[1]
Geschichte
Papier wurde anfangs ausschließlich aus Lumpen hergestellt. Im 19. Jahrhundert führte der steigende Papierbedarf zur Entwicklung des Holzschliffs und des Zellstoffs.
Der Aufschluss von Holz mit Natronlauge (NaOH) wurde 1851 von H. Burgess und C. Watt in England entwickelt und 1854 in den USA eingeführt. Der hohe Natronlaugebedarf machte das Eindampfen, Verbrennen und die erneute Kaustifizierung zu teuer. C. Dahl in Danzig versuchte Natriumsulfat (Na2SO4) direkt in das Rückgewinnungssystem einzufügen. Das durch Reduktion entstandene Natriumsulfit (Na2SO3) verbesserte die Faserqualität deutlich. 1884 erhielt Dahl ein Patent für die Verfahrensmodifikation. Die alkalischen Bedingungen führten zu sehr festen Fasern, die allerdings dunkelbraun gefärbt waren. Sie wurden daher lange nur für die Herstellung von ungebleichten Papierprodukten (Papiersäcke, Kartonagen) eingesetzt.[1]
1867 wurde der Sulfitaufschluss für B. C. Tilghman in den USA patentiert (USP 70.485). Dieses Verfahren verwendet eine Lösung von Calciumbisulfit (Ca(HSO3)2) und freiem Schwefeldioxid (SO2). Die erste großtechnische Anlage entstand 1874 in Schweden unter C. D. Ekman, sie nutzte kleine, rotierende Kocher und Magnesiumbisulfit [Mg(HSO3)2]. In Deutschland wurde das Sulfitverfahren nach Tilghman von Mitscherlich 1875 eingeführt. Mitscherlich benutzte liegende Kocher, niedrige Temperaturen von 110 °C und sehr lange Umtriebszeiten.[1] Die saure Sulfitkochung nach Mitscherlich führt zu vergleichsweise hellen Fasern. Bei der Verwendung von Hackschnitzeln aus gut entrindetem Holz ist ein Weißgrad von nahezu 70 % ISO erreichbar. Zur weiteren Aufhellung der Fasern war die Chlorbleiche mit Chlorkalk im Einsatz.
Rohstoff
Quelle:[2]
Holzart | Eucalyptus globulus | Eucalyptus grandis | Birke | Kiefern | Fichten | Buche | Acacia | Pappeln |
---|---|---|---|---|---|---|---|---|
Verbreitungsgebiet | Iberische Halbinsel | Südamerika | Nordhalbkugel | Nordhalbkugel | Nordhalbkugel | Nordhalbkugel | Indien, Indonesien | |
Ertrag [m³/ha/Jahr] | 15–30 | 3–8 | 2–10 | 4–10 | 2–9 | 15–25 | ||
Standzeit [Jahre] | 9–14 | 25–45 | 75–110 | 60–80 | 100–140 | 6–12 | ||
Ergiebigkeit [m³ Holz/t Zellstoff][3] |
2,8–2,9 | 3,8–4,0 | 4,5 | 5 | 3 | 4,9 |
Herstellung
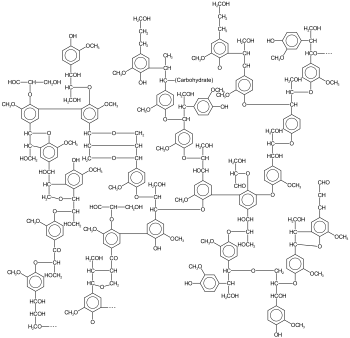
Zur Zellstofferzeugung werden möglichst gleichmäßig geformte Hackschnitzel benötigt. Die mechanische Zerkleinerung verbessert die gleichmäßige Imprägnierung des Holzes mit der Aufschlusslösung. Sehr grobe Hackschnitzel werden nicht vollständig imprägniert, was zu unaufgeschlossenen Rückständen führt. Zu feine Hackschnitzel haben den Nachteil einer starken mechanischen Kürzung der Fasern. Sägewerksabfall (Spreißel) oder zerspantes Holz sind kaum geeignet. Holz besteht vor allem aus Lignocellulose. Beim Aufschluss werden die Inkrusten des Lignins innerhalb der Cellulosematrix aufgespalten und gelöst, während die Struktur der Cellulose weitgehend erhalten bleibt.
Sulfatverfahren
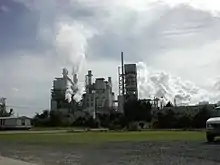
- (siehe Hauptartikel Sulfatverfahren)
Das Sulfatverfahren (auch Sulfataufschluss oder -prozess) wird wegen der festeren Fasern auch Kraft-Verfahren genannt. Es ist nach der „Make-up-Chemikalie“ des Prozesses, dem Glaubersalz (Natriumsulfat, Na2SO4), benannt. Die aktiven Substanzen sind Natronlauge und Natriumsulfid. Der Aufschluss findet überwiegend in kontinuierlichen Kochern statt. Auch Modifikationen des ursprünglichen Batch-Prozesses werden angewandt. Die Hackschnitzel werden mit der Kochlauge imprägniert und von oben den stehenden Reaktoren zugeführt. Bei einer Temperatur bis zu 170 °C werden Holzbestandteile, wie Hemicellulosen und Lignine, alkalisch gelöst. Das Lignin wird durch nukleophile Etherspaltung der Sulfitionen (SO32−) depolymerisiert. Ein Abbau der Cellulosefasern ist unerwünscht, weshalb der Aufschlussprozess abgebrochen wird, bevor das gesamte Lignin in Lösung gegangen ist. In ungebleichtem Zellstoff sind daher noch etwa 2 % bis 3 % Lignin enthalten.[1] In einer Produktionslinie einer Anlage zur Zellstoffherstellung werden jährlich bis zu 1,3 Millionen t Zellstoff produziert.
In Deutschland arbeiten 2 Zellstofffabriken nach dem Sulfatverfahren: Die Zellstoff- und Papierfabrik Rosenthal GmbH in Blankenstein/ Thüringen mit einer Kapazität von 360.000 Tonnen jährlich, und die Zellstoff Stendal GmbH bei Arneburg/ Sachsen-Anhalt, die über eine Jahreskapazität von 660.000 Tonnen verfügt.
Sulfitverfahren
- (siehe Hauptartikel Sulfitverfahren)
Das zum Sulfitverfahren (auch Sulfitaufschluss oder -prozess) benötigte Schwefeldioxid wurde früher durch direktes Verbrennen von Schwefel oder Rösten von sulfidischem Erz erzeugt und durch einen hölzernen Turm mit Kalksteinen geleitet. Durch Berieselung mit kaltem Wasser, bildete sich die benötigte Calciumbisulfitlösung mit zusätzlichem freien Schwefeldioxid. Heute wird flüssiges Schwefeldioxid verwendet. Der saure Sulfitprozess löst den Verbund zwischen Lignin und Cellulose durch Sulfonierung und Etherspaltung des Lignins. Der niedrige pH-Wert schädigt die Struktur der Celluloseketten an den Acetalbrücken zwischen den Zuckermolekülen. Der kristalline Bereich der Cellulose bleibt dabei stabil.[1] Die Faserfestigkeit des Sulfitzellstoffes ist schlechter als bei Sulfatzellstoff. Das hydrophile, sulfonierte Lignin ist gut wasserlöslich und kann zu Lignosulfonaten weiterverarbeitet werden. Diese kommen bei Dispersionsfarbstoffen als Hilfsmittel zum Einsatz.
Zur Herstellung von Papier ist fast immer eine Zellstoffbleiche erforderlich, die Ligninreste durch Oxidation löst. Beim Sulfitprozess werden durch die alkalische Bleiche zusätzlich Hemicellulosen gelöst.
Die Ausbeuten pro Trockenmasse Holz betragen beim Sulfatverfahren 40 % bis 45 % und beim Sulfitverfahren 45 % bis 50 %. Die Abwasserbelastung korreliert direkt mit der Menge an gelöster Substanz.
Andere Verfahren
Andere Verfahren, wie das Soda- (Na2CO3·10H2O) und das Soda/Anthrachinon-Verfahren (Soda/AQ-Verfahren), bei dem das Anthrachinon als Katalysator für eine bessere Delignifizierung dient, spielen technisch keine Rolle.
Auch der alkalische Sulfitaufschluss unter Zusatz von Anthrachinon und Methanol (ASAM-Verfahren)[4] oder das Acetocell-Verfahren mit einem Peroxyessigsäure-Aufschluss[5] sind zu nennen. Diese Verfahren wurden in Pilotanlagen erprobt, sind aber nicht wirtschaftlich. Auch das Organocell-Verfahren mit Natronlauge und Methanol (CH3OH) erwies sich als nicht konkurrenzfähig. Eine großtechnische Anlage nach diesem Prinzip in Kelheim wurde mit erheblicher staatlicher Förderung 1992 in Betrieb genommen, aber 1993 wegen Qualitätsproblemen stillgelegt.[6]
Einen umweltfreundlichen Ansatz stellt der versuchsweise durchgeführte Aufschluss mittels Ameisen- und Essigsäure dar.[7]
Chemikalienrückgewinnung
Beim klassischen Mitscherlich-Verfahren wurde die Ablauge des Calciumsulfit-Aufschlusses über den Vorfluter entsorgt. Somit belastete die Hälfte der eingesetzten Holzmasse das Abwasser und die Gewässer. Moderne Zellstoffanlagen gewinnen die Aufschlusschemikalien zurück. Wegen der Bildung von Calciumsulfat-Ablagerungen (Gips) wird in Mitteleuropa – mit wenigen Ausnahmen – nur noch das saure Magnesiumsulfit-Verfahren durchgeführt. Nach der „Kochung“ wird der Zellstoff gewaschen und das Abwasser eingedampft. Man erhält die saure „Schwarzlauge“. Bei deren „Verbrennung“ wird Magnesiumsulfit thermisch in Magnesiumoxid (MgO) und Schwefeldioxid gespaltet. An elektrostatischen Filtern wird MgO abgeschieden und in Venturireaktoren mit dem im Rauchgas enthaltenen SO2 wieder zu Magnesiumbisulfit [Mg(HSO3)2] umgesetzt.
Bei der Verbrennung der „Schwarzlauge“ (schwarz bezieht sich nicht auf die Farbe, sondern die geringe Reinheit) unter vermindertem Luftzutritt entsteht eine Schmelze aus Natriumcarbonat (Na2CO3) und Natriumsulfid (Na2S). Durch Auflösen in Wasser erhält man „Grünlauge“. Das Natriumcarbonat wird mit Calciumhydroxid [gelöschter Kalk, Ca(OH)2] zu Natronlauge kaustifiziert. Durch Filtration entsteht die „Weißlauge“. Diese wird erneut in den Prozess eingesetzt. Das abfiltrierte Calciumcarbonat wird in einem Drehrohrofen wieder zu Calciumoxid (gebrannter Kalk, CaO) gebrannt.
Diese Rückgewinnung entlastet nicht nur den Vorfluter, sondern aus der Ablauge wird auch die benötigte Prozessenergie gewonnen. Moderne Anlagen erzeugen einen Überschuss an elektrischer Energie. Der Dampfüberschuss kann bei einer integrierten Zellstoff- und Papierproduktion zur Papiertrocknung dienen.
Kleine Zellstoffanlagen haben üblicherweise keine Rückgewinnungsanlage. Die starke Umweltbelastung durch den hohen Gehalt an Lignin und Hemicellulosen im Abwasser führt zunehmend zur Stilllegung. Allein in China wurden durch die Regierung in den vergangenen zehn Jahren über 10.000 Strohzellstofffabriken mit einer Jahresproduktion unter 5.000 Tonnen wegen der Verschmutzung von Flüssen und Seen geschlossen. Der Aufwand für die Rückgewinnung der Chemikalien ist bei kleinen Anlagen zu hoch.
Zellstoffqualität
Die Festigkeit der Zellstofffaser ist für die Herstellung einiger Papiersorten von entscheidender Bedeutung. Zellstoff zur Verbesserung der Papierfestigkeit wird als Armierungszellstoff bezeichnet. Er hat lange und dünne Fasern. Nadelholz aus Regionen mit kühlem Winter, aber warmem Sommer besitzt diese Eigenschaften. Dieser Zellstoff wird bei der Herstellung von holzhaltigem Papier (Magazin-, Katalogpapier) verwendet. In Regionen mit langer Vegetationsperiode entstehen Nadelholzfasern, die sowohl lang als auch relativ dick sind. Diese groben Fasern eignen sich hervorragend zur Herstellung fester Papiersäcke oder für Kaffeefilter.
Die kurzen Fasern der Laubhölzer ermöglichen eine glatte, gleichmäßige Papieroberfläche. Auf Papiermaschinen kann hochwertiges Papier ausschließlich aus Laubholzzellstoff gefertigt werden. Für ältere Maschinen sind Mischungen von langen und kürzeren Fasern nötig.[8]
Der Zellstoff-Herstellungsprozess hat erheblichen Einfluss auf die Faserqualität. Qualitätsverluste entstehen durch Faserkürzung der Hackschnitzel, zu intensiven Aufschluss oder bei der Zellstoffbleiche. Qualitätswerte der mechanischen Prüfung der Festigkeit sind Reißlänge oder Durchreißfestigkeit. Hinzu kommt der Zusammenhang zwischen dem Polymerisationsgrad der Cellulose und der Faserfestigkeit. Die Analyse der Viskosität einer gelösten Faserprobe gibt Hinweise auf den Grad der Faserschädigung.
Zellstoff wird in verschiedenen Qualitäten hergestellt. Nördlicher gebleichter Langfaser-Sulfatzellstoff, meist NBSK-Zellstoff oder NBSK genannt (Abkürzung für engl. Northern bleached softwood kraft), wird bei der Herstellung verschiedener Papiersorten verwendet. Zellstoffwatte (engl. fluff pulp) wird aus Weichhölzern hergestellt, besitzt ein hohes Wasserbindungsvermögen und wird überwiegend für Hygieneprodukte wie Windeln verwendet. Chemiezellstoff (engl. dissolving pulp) besitzt eine geringe Färbung, eine gleichmäßige Molmassenverteilung[9] und wird nicht für die Papierherstellung, sondern für eine chemische Weiterverarbeitung verwendet; zur Erhöhung der Qualität des Endprodukts werden Harthölzer mit hohem Anteil an Cellulose verwendet.[10]
Zellstoffhandel
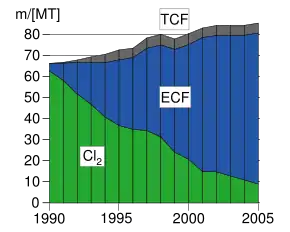
Grün: mit elementarem Chlor (Cl2) gebleicht
Blau: ECF (elemental chlorine free), d. h. mit Chlordioxid oder Chlorit gebleicht
Grau: TCF (totally chlorine free), d. h. mit Ozon oder Wasserstoffperoxid gebleicht
Zellstoff wird überwiegend gebleicht gehandelt. Für 2004 wurde die Weltproduktion an gebleichtem Zellstoff auf 80 Millionen Tonnen geschätzt.[11] Führend sind heute ECF-(Elementar-Chlor-Frei) gebleichte Qualitäten mit einem Weißgrad von 88 % bis 90 % ISO bei Nadelholzzellstoff und über 90 % ISO bei Laubholzzellstoff. Zur Herstellung von Fotopapier werden hochweiße Laubholzzellstoffe mit einem Weißgrad von über 92 % ISO verwendet.
Ein weiteres Qualitätsmerkmal ist die Stabilität gegen Vergilbung. Diese kann bei TCF-(Total-Chlor-Frei)gebleichtem Laubholzzellstoff gering sein.
Verwendung
- Papier
- Karton
- Papierfilter (im Haushalt zumeist Filtertüten)
- Watte und Verbandstoffe
- Papiertaschentücher
- Hygiene-Produkte wie Tampons, Damenbinden, Höschenwindeln und Hilfsmittel bei Harn- oder Stuhlinkontinenz
- Armierung von Gips oder Zement als Verbundwerkstoff
- Zellstoffverbundelemente
Produkte aus Chemiezellstoff:
- Cellulosederivate wie Cellulose-Ester oder -Ether
- Celluloseregenerate wie Viskose, Lyocell, Modal, Kupferseide, Folien
Umweltaspekte
Siehe auch
Weblinks
Einzelnachweise
- H. Sixta: Handbook of Pulp. 2006, ISBN 3-527-30999-3.
- Sustainable Forest management and Eucalyptus. (PDF; 12 MB) ENCE, 2009, S. 32.
- Bedarf an trockenem Holz in m³ zur Produktion von 1 Tonne lufftrockenem Zellstoff
- Hans-Ludwig Schubert: Probleme der Umsetzung neuer Technologien in die industrielle Praxis, dargestellt am Beispiel des Alkalischen Sulfitverfahrens mit AQ und Methanol – ASAM. In: Lenzinger Berichte. Nr. 86, 2006, S. 24–31 (archive.org [PDF; abgerufen am 26. April 2018]).
- Papier Lexikon, Deutscher Betriebswirte-Verlag, Gernsbach 1999, Bd. 1, 41, ISBN 3-88640-080-8.
- Papier Lexikon, Deutscher Betriebswirte-Verlag, Gernsbach 1999, Bd. 2, 379, ISBN 3-88640-080-8.
- Jan Beringer: Zellstoff aus Weizenstroh: Gewinnung durch Aufschlussverfahren mit Ameisen- und Essigsäure sowie Untersuchungen zur Zellstoffstruktur und Eignung als Papier- und Chemiezellstoff. Im: Logos Verlag Berlin, 2005, ISBN 978-3-8325-0797-8.
- H. Holik: Handbook of Paper and Board. VCH-Wiley, Weinheim 2006 ISBN 3-527-30997-7.
- Christopher J. Biermann: 3. In: Handbook of Pulping and Papermaking, 2. Auflage 1996, ISBN 978-0-12-097362-0, S. 72–73.
- F.C. Aldred: Pulping Quality in Plantation Grown Species. In: The Commonwealth Forestry Review. 46, Nr. 4, Dezember 1967, S. 270–277.
- Bleaching. In: Ullmann’s Encyclopedia of Industrial Chemistry. 7th Edition. Wiley-VCH Verlag, 2007, online edition.