Galvanotechnik
Galvanotechnik oder Galvanik bezeichnet die elektrochemische Abscheidung metallischer Niederschläge, also von Überzügen auf Substrate (Werkstücke) in einem elektrolytischen Bad.
.svg.png.webp)
Bei der Galvanik wird elektrischer Strom (Gleichstrom) durch ein elektrolytisches Bad geleitet. Am Pluspol (Anode) befindet sich in der Regel ein Metall wie Kupfer oder Nickel, welches aufgelöst und zum Minuspol (Kathode) transferiert wird. Die im elektrolytischen Bad gelösten Metallionen lagern sich durch Reduktion auf einem Werkstück ab, das mit dem Minuspol elektrisch verbunden ist und so als Kathode dient. Alternativ können die Metallionen auch bereits im Elektrolyt als Lösung enthalten sein. Die Metallionen lagern sich relativ gleichmäßig auf dem Werkstück am Minuspol ab und die Schichtdicke nimmt mit der Zeit zu. Häufig ist vor dem galvanischen Prozess eine Vorbehandlung des Substrats nötig.[1]
Das Elektroplattieren (auch Galvanostegie, engl. electroplating) ist die häufigste Anwendung der Galvanotechnik. Dieses Beschichtungsverfahren dient der Herstellung metallischer Überzüge auf Substratkörpern.
Der zweite Bereich der Galvanotechnik ist die Galvanoplastik (auch Galvanoformung oder Galvanoforming, engl. electroforming). Größere Schichtdicken lassen hierbei solide metallische Körper entstehen. Das Verfahren wurde ab dem 19. Jahrhundert zur Herstellung künstlerischer Skulpturen sowie von Gussformen eingesetzt. Heute wird es im Formenbau zum Spritzgießen von Kunststoffen sowie in jüngster Zeit in der Mikrosystemtechnik als Mikrogalvanoformung angewendet, siehe Lithografisch-galvanische Abformungstechnik (LIGA).
Als Galvano wird einerseits ein Druckverfahren bezeichnet, bei dem der hölzerne Druckstock durch eine galvanisch erzeugte Faksimile-Druckform ersetzt wird. Andererseits bezeichnet Galvano auch die Kopie einer Münze oder Medaille sowie gelegentlich auch Skulpturen, die auf galvanischem Wege hergestellt wurden.
Auch die Anwendung niederfrequenten („galvanischen“) Stroms in der medizinischen Galvanotherapie wird missverständlich als Galvanisation bezeichnet.[2]
Geschichte
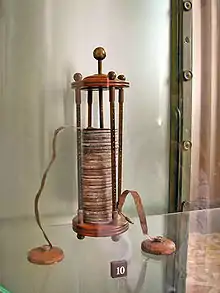
Die Geschichte der Galvanik, wie die Galvanotechnik umgangssprachlich bezeichnet wird, geht zurück auf den italienischen Arzt Luigi Galvani (1737–1798), der Ende des 18. Jahrhunderts den nach ihm benannten Galvanismus entdeckte, als er bei Versuchen mit Froschschenkeln bemerkte, dass diese beim Berühren mit zwei Elektroden aus verschiedenen miteinander verbundenen Metallen zuckten.
Alessandro Volta erkannte, dass der Effekt durch die verschiedenen Metalle verursacht wurde. Diese erzeugen in Kombination mit einem Elektrolyten eine elektrische Spannung, die sich im Tiermuskel entlädt. Er baute daraufhin seine Batterie, die Voltasäule, die eine wichtige Rolle bei der Begründung der Elektrotechnik spielte. Wahrscheinlich war sie die erste Batterie überhaupt, auch wenn es Vermutungen gibt, Menschen hätten schon vor Jahrtausenden Batterien gebaut: Bestimmte Tongefäße, die bei Bagdad gefunden worden sind und in denen ein Kupferzylinder mit Eisenstab eingelassen war, wurden als die ersten Batterien gedeutet. Der verwendete Elektrolyt ist unbekannt. Sie werden auf ca. 2000 v. Chr. datiert und werden gewöhnlich als „Batterie von Bagdad“ bezeichnet. Heute zweifelt man allerdings an, dass es sich wirklich um eine Batterie gehandelt hat.[3] Dementsprechend ist auch fraglich, ob das Galvanisieren schon im Altertum möglich war. Die Vermutung, dass in der Antike die Vergoldung von Gegenständen mithilfe von Galvanotechniken bekannt gewesen sei,[4] ist daher nicht bewiesen.
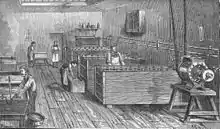
Die erste belegte galvanische Vergoldung fand 1805 durch einen Schüler Voltas statt. 1840 erhielt der englische Unternehmer George Richards Elkington ein Patent auf ein Verfahren zum galvanischen Versilbern mit cyanidhaltigen Lösungen. In der mit seinem Cousin gegründeten Firma nutzte er das Verfahren. Sie beschäftigte 1865, als Elkington starb, fast tausend Arbeiter und galt damals als führender Galvanikbetrieb.[5] Ab der Mitte des 19. Jahrhunderts wurden lebensgroße Statuen wie Reiterstandbilder galvanoplastisch hergestellt, beispielsweise auch die bekannte Statue des Großen Kurfürsten in Berlin, die nach Entwürfen von Andreas Schlüter entstand.[6]
Das relativ ungiftige Aufbringen metallischer Überzüge konnte weitgehend die Technik der Feuervergoldung bzw. -versilberung ablösen, die durch das hierbei verwendete Quecksilber gesundheitsschädlich ist.
Galvanische Anwendungen
Teilweise wird zwischen dekorativer und funktionaler Galvanotechnik unterschieden. Erstere dient vorwiegend der Verschönerung von Gegenständen und muss für diesen Zweck gewisse technische Mindesteigenschaften besitzen. Beispiele für die dekorative Galvanotechnik sind die Kunststoffgalvanisierung, die Verchromung von Stahlrohrmöbeln, Armaturen und Motorrädern sowie die Vergoldung von Schmuck und Essbesteck.
Die funktionelle Galvanotechnik dient dem Korrosionsschutz, dem Verschleißschutz, der Katalyse, der Verbesserung elektrischer Leitfähigkeit und der Reduzierung von Friktionskräften. Auch die Duktilität und Verformbarkeit von Werkstücken kann durch galvanische abgeschiedene Überzüge verbessert werden.[7] Folgend einige Beispiele:
- Verzinkung von Schrauben (Korrosionsschutz)
- Beschichtung von Maschinenteilen mit Hartchrom (Verschleißschutz)
- Beschichtung mit metallischen, meist nickel- oder platinhaltigen Katalysatoren für die chemische Industrie oder Brennstoffzellen (Katalyse)
- Vergoldung und Versilberung elektrischer Kontakte (elektrische Leitfähigkeit)
- Blei-Zinn-Kupfer Schichten für Gleitlager (Reduzierung der Friktion)
- Verkupfern beim Drahtziehen (Verbesserung der Verformbarkeit)
- Rhodinieren von Ringen und Brillengestellen
Hartchromschichten können aufgrund ihrer Verschleißfestigkeit und ihren guten Gleiteigenschaften auch als Beschichtung von Hydraulikzylindern oder für Tauchrohre in Federgabeln genutzt werden. Die Endeigenschaften dieser Bauteile sind nach der Beschichtung erheblich besser als z. B. die ihrer Grundmaterialien.
Galvanotechnik in der Praxis
Allgemeines
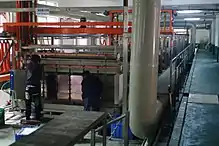
Die Galvanotechnik kann in den Produktionsablauf eines metallverarbeitenden Betriebs integriert sein (Betriebsgalvanik) oder aber als Dienstleister, – also durch Fertigung von Auftragsarbeiten (Lohngalvanik) – fungieren. Im weiteren Sinne werden auch Eloxalanlagen und andere (meist stromgetriebene) Verfahren als Galvanik bezeichnet.
Galvanische Anlagen sind in der Regel eine sehr lange Reihe von Wannen, in denen die verschiedenen Prozessschritte nacheinander erfolgen. Moderne Anlagen sind mehr oder weniger vollständig automatisch gesteuert. Sie werden von Oberflächentechnikern bedient. Die frühere Bezeichnung Galvaniseur wurde durch die Berufsbezeichnung Oberflächenbeschichter ersetzt. Es wird zwischen den Verfahren Stückgalvanisierung (Warenträger mit Waren werden getaktet durch einzelne Becken befördert), Massengalvanisierung (Schüttgut in rotierenden Trommeln wird durch unterschiedliche Becken befördert) und Durchlaufgalvanisierung (Permanentes Durchlaufen von Bauteilen durch eine Anlage ohne einzelne Takte) unterschieden.[8]
Wirtschaftliche Bedeutung der Galvanik
Die Zahl der Galvanikanlagen in der EU wurde 2005 mit ca. 18.000 angegeben.[9] Die Zahl der Beschäftigten liegt nach Angaben des Branchenverbandes im Jahr 2020 europaweit bei rund 440.000.[10] In der Schweiz sind etwa 80 Galvanikbetriebe im Branchenverband Swissgalvanic organisiert.[11] Nach einer Branchenanalyse aus dem Jahr 2006 arbeiteten zu dieser Zeit in Deutschland in ungefähr 2.100 Betrieben etwa 49.000 Menschen in der Galvanotechnik.[12] Zu den Betrieben gehörten etwa 50 Fachlieferanten für Galvanik-Chemikalien, 550 Dienstleistungs-Galvaniken aus dem Bereich Handwerk und 1.500 industrielle Lohn- und inhouse-Galvaniken.[12] Der Gesamtumsatz dieser Betriebe in Deutschland wurde damals auf fast 6 Mrd. Euro geschätzt[12], im Jahr 2020 wurde er bei einer Mitarbeiterzahl von rund 60.000 mit 8,3 Mrd. Euro angegeben.[10] Ferner wurde als Schätzwert angegeben, dass die galvanischen Schutzschichten Korrosionsschäden und damit Kosten von 150 Mrd. € pro Jahr verhindern würden.[12][13]
Grundmaterial
Labortechnisch lassen sich heutzutage alle gängigen Grundwerkstoffe aus Metall sowie die meisten nichtleitenden Polymere (Kunststoffe) und Keramiken beschichten.
Bei der Kunststoffgalvanisierung haben sich großtechnisch nur zwei gängige Verfahren der Polymerbeschichtung etabliert. Direktmetallisieren nach dem sogenannten Futuron-Verfahren, sowie die konventionelle Prozessreihenfolge über die aktivierte stromlose Metallisierung als erste metallische Prozessstufe (Schichtfolge: Vornickel, Glanzkupfer, Glanznickel, Chrom) sind hier speziell im dekorativen Segment anzutreffen. In der Automobilbranche ist man durch hohe Qualitätsmerkmale und Forderungen der Hersteller gezwungen, bis zu vier verschiedene Nickelschichten im Verbund abzuscheiden, um optimale Beständigkeit, Funktion und Aussehen zu erreichen.
Glanz
Die Qualität eines Werkstückes wird oft anhand des Glanzes bestimmt. Dabei ist der physiologische Eindruck des Glanzes metallischer Schichten nicht ohne weiteres mit physikalischen Messmethoden (Reflexionsgrad o. ä.) bestimmbar. Die Wahrnehmung des Menschen kann von diesen physikalisch bestimmten Größen abweichen. Speziell bei dekorativen Anwendungen ist er von hoher Bedeutung. Für einen hohen Glanz werden in den verschiedenen Verfahren spezielle Glanzbildner eingesetzt. Es muss darauf geachtet werden, dass ein hoher Glanz andere physikalische Eigenschaften (z. B. elektrische Leitfähigkeit, Härte, Lötfähigkeit) einer Schicht verändern kann.
Metallüberzüge können Gegenständen Glanz und ein eindrucksvolles Aussehen verleihen. So kann z. B. Besteck, das aus billigem Metall besteht, mit einem teureren Metall überzogen werden. Um beispielsweise einen Löffel aus Nickel zu versilbern, wird der Löffel zuerst gereinigt und dann mit dem negativen Pol einer Spannungsquelle verbunden. Der Löffel ist dann also die Kathode. Als Anode dient ein Silberstab. Beide Elektroden werden in eine Silbernitrat-Lösung getaucht. Nach dem Anlegen der Spannung gehen Silberatome durch Abgabe von Elektronen als Silberionen in die Lösung über. Diese Ionen werden von der Kathode angezogen und scheiden sich auf dem Löffel, unter Elektronenaufnahme, ab. So wird der Löffel aus Nickel mit einer dünnen Silberschicht überzogen. Die Reaktionsgleichungen lauten:
- Anode: Ag → Ag+ + e−
- Kathode: Ag+ + e− → Ag
Einebnung
Ist ein Grundmaterial rau, kann durch die geeignete Auswahl des galvanischen Verfahrens die Oberfläche geebnet werden. Der technisch bessere Ausdruck für Einebnung ist der Begriff Mikrostreufähigkeit. Diese Eigenschaft wird beispielsweise bei Lagern, Walzen oder dekorativen Anwendungen (siehe auch Glanz) genutzt.
Bei der Einebnung muss zwischen geometrischer Einebnung (Mögliche Einebnung durch Geometrie der Unebenheit) sowie zwischen einer echten Einebnung unterschieden werden. Bei einer echten Einebnung wird in tieferen Stellen „Tälern“ mehr Material als an den Erhobenen Stellen „Bergen“ abgeschieden. Die Einebnung kann durch die Zugabe von Additiven, den sogenannten „Einebnern“ verbessert werden.[14]
Galvanogerechtes Konstruieren
Ein Werkstück konstruiert man galvanogerecht, indem man bestimmte Grundsätze berücksichtigt, welche den geplanten Galvanisierprozess begünstigen und mögliche Probleme vermeiden. Die Notwendigkeit für galvanogerechtes Konstruieren beruht beispielsweise auf der Ausbildung von Feldlinien im elektrischen Feld und einer damit verbundenen unterschiedlich schnellen (Inhomogenen) Abscheidung des Materials.
- Durchgangslöcher sind günstiger als Sacklöcher. Letztere können je nach Durchmesser und Tiefe das Eindringen und Auslaufen der Prozessflüssigkeiten erschweren oder verhindern (Luftblasen). Verspätetes Austreten von Flüssigkeiten aus den Sacklöchern erschwert die Spülprozesse und kann zu nachträglicher Korrosion führen.
- Abgerundete Konturen sind günstiger als scharfkantige Außen- und Innenwinkel: Erhöhte Abscheidung (bis hin zu Grat- oder Knospenbildung) an scharfen Außenkanten. Verminderte oder keine Abscheidung an scharfen Innenwinkeln.
- Eine durchgehende V-Naht ist günstiger als ein Überlappungsstoß oder eine punktgeschweißte Verbindung: Werden zwei Flächen nicht dicht verschweißt, dann werden die Flüssigkeiten mittels Kapillarwirkung im Spalt festgehalten. Die Schicht wird beim Trocknen durch diese Flüssigkeiten wieder zerstört. Dasselbe gilt für Bördelungen und Nietverbindungen.
- Faradayscher Käfig: Bei einem rundherum geschlossenen Werkstück mit zu kleinen Öffnungen kann in dem Werkstück kein elektrisches Feld entstehen. In diesem Bereich wirken nur rein chemische Prozesse. Bei einem elektro-chemischen Verfahren ist die Eindringtiefe normalerweise gleichzusetzen mit der Öffnung, d. h., bei einem Rohr mit einem Innendurchmesser von 2 cm wird eine Beschichtung bis zu der Tiefe von 2 cm in das Rohr erreicht.
- Werkstoffauswahl: Stähle mit hohem Kohlenstoffgehalt können die Haftfähigkeit der Schicht verschlechtern. Bei hochfestem Stahl besteht die Gefahr der Versprödung. Kombinationen verschiedener Werkstoffe an einem Werkstück können zu Problemen führen, z. B. wenn es bei der Vorbehandlung verschiedene Indikationen und eine gegenseitige Kontraindikation gibt.
Konstruktion und Werkstoffauswahl haben sehr großen Einfluss auf einen späteren Galvanisierprozess in Bezug auf mögliche Probleme und Wirtschaftlichkeit. Deshalb sollte bei Neukonstruktionen von Beginn an eine interdisziplinäre Arbeitsweise gewählt werden.
Nachbehandlung
Zu den Nachbehandlungsverfahren, beispielsweise bei verzinkten Waren, kann das Aufbringen einer Konversionsschicht (durch Phosphatierung oder Chromatieren) gehören, sowie eine Lackierung.
Bandgalvanik
Bei der Bandgalvanik wird ein Metallband als Vollband oder mit vorher ausgestanzten, jedoch noch aneinanderhängenden Teilen, kontinuierlich durch alle nötigen Bäder gezogen.
Die Vorteile der Bandgalvanik sind:
- die Schichtdicke variiert nur wenig.
- die Teile müssen nicht einzeln kontaktiert oder eingehängt werden.
- mit unlöslichen Anoden ist eine sehr schnelle Beschichtung mit hoher Qualität (z. B. über 1 µm/s bei Silber) möglich
- durch Abdecken mit Riemen ist es möglich, nur einzelne Streifen vom Band zu beschichten (Selektiv-Beschichtung). Dadurch wird weniger Beschichtungsmaterial verbraucht.
Die Bandgalvanik wird unter anderem zur Vergoldung elektrischer Kontakte und zur Beschichtung von Halbleiter-Kontakt-Unterlagen (siehe Chipbonden) verwendet.
Bandgalvanik-Anlagen sind meist weniger gesundheitsschädlich als andere Galvanik-Anlagen, da die Anlagen meist vollständig abgedeckt und mit Luft-Absaugungen versehen sind und keine Handarbeit nötig ist. Dadurch werden giftige Gase und Dämpfe vom umgebenden Raum ferngehalten.
Zahntechnik
Mit der Galvanotechnik kann in der Zahntechnik Zahnersatz hergestellt werden, der aus dünnen Goldkappen besteht und mit Keramik verblendet wird. Durch den elektrochemischen Prozess werden selbsttragende Metallgerüste aus Gold hergestellt. Beim Auro-Galvano-Crown-Verfahren (AGC) wird im zahntechnischen Laboratorium auf die mit Silberpulver vorbereiteten Zahnstümpfe eine Goldschicht von ca. 200 µm abgeschieden. Die Gerüste haben eine Reinheit von 99,99 % Gold. Die Galvanotechnik eignet sich für die Herstellung von Einzelkronen, Prothesenbasis, keramisch verblendete Teilkronen und Einlagefüllungen (Inlays/Onlays), Teleskopkronen, Zahnbrücken für den Ersatz eines Zahnes und Zahnimplantat-Suprastrukturen.[15]
Elektrochemische Vorgänge
Grundlagen
Das Galvanisieren ist eine Elektrolyse, bei der chemische Vorgänge (Redoxreaktionen; siehe chemische Reaktion) unter Einwirkung von elektrischem Strom ablaufen. Die Metallabscheidung, die beim Galvanisieren abläuft, ist eine Umkehrung der Metallauflösung. Beispielsweise kann man die Vorgänge bei der galvanischen Verzinkung als Umkehrung der Auflösung einer Zinkelektrode betrachten, die in vielen galvanischen Zellen stattfindet, z. B. im Daniell-Element oder in der Zink-Kohle-Zelle.
In der Versuchsanordnung und im realen Betrieb der Elektrolyse legt man eine Gleichspannung an zwei Elektroden an, die dadurch polarisiert werden. Es entstehen Kathode und Anode. Befinden sie sich in einer leitenden Flüssigkeit, fließt Strom. Flüssigkeiten, z. B. Säuren, Laugen oder Wasser mit gelösten Salzen, leiten Strom. Diese Substanzen heißen auch Elektrolyte. Legt man eine Spannung an, bewegen sich die positiven Kationen zur Kathode (daher deren Name) und die negativen Anionen zur Anode. Dabei findet an der Anode eine Oxidation statt. Kationen, die nahe genug an die Kathode gelangen, nehmen von der Kathode Elektronen auf. Sie werden also reduziert und lagern sich als Metall an der Kathode an.
Lösliche Anoden
Lösliche Anoden sind nur bei Silber-, Kupfer- oder Nickelbädern üblich. In das Bad wird der entsprechende Elektrolyt gegeben, bei Silber z. B. Silbercyanid und Kaliumcyanid. Die Anode besteht in diesem Fall aus Feinsilberblech. Während der Elektrolyse überzieht sich die Kathode mit einer reinen Silberschicht, wobei sich die Anode auflöst.
Bei allen löslichen Anoden gibt das Metall (vor allem Kupfer, Silber oder Nickel, im Labor auch Zink oder Gold) Elektronen ab und wird oxidiert. Im Idealfall würden an der Anode gleichviele Ionen (z. B. Ag+ beim Silber) in Lösung gehen, wie an der Kathode durch Reduktion verbraucht werden. In diesem Idealfall würde also die Konzentration der Lösung während der Elektrolyse unverändert bleiben, solange das Metall an der Anode noch nicht komplett gelöst ist.
Unlösliche Anoden
An der Kathode erfolgt wie immer bei der Galvanik die Reduktion der Metallionen zum Metall. Es wird jedoch eine unlösliche Anode, beispielsweise aus Edelstahl, verwendet. Die Kationen, die nach der Reaktion das Metall des Überzugs bilden, befinden sich im Bad, z. B. im Vergoldungsbad als Goldchlorid. Legt man eine Spannung an, wird der Stromkreis durch die Oxidation der Anionen im Elektrolyten geschlossen. Bei Chloridlösungen entsteht dabei Chlor, ansonsten entsteht Sauerstoff. Der Vorgang läuft solange, bis die Konzentration der Metallionen (der Goldionen im Beispiel) im Bad zu klein wird. Daher muss zum Aufrechterhalten des Prozesses immer wieder Metallsalz zugegeben werden.
Berechnung der Umsätze
Die Berechnung der umgesetzten Stoffmengen erfolgt wie bei jeder Elektrolyse mit Hilfe der Gleichung, die aus den Faradayschen Gesetzen folgt und dort angegeben ist. In der Regel muss dabei die Stromausbeute berücksichtigt werden.
Qualitätssicherung
Die Qualitätssicherung nimmt in der Galvanotechnik einen sehr hohen Platz ein. Zu ihr gehören die ständige Analyse der Badparameter, wie Säure- und Metallgehalt, Kontrolle des Aussehens und Farbe der Schichten, Schichtdickenmessungen mittels Röntgenfluoreszenz, Ultraschall, Wirbelstromverfahren, Ablöseverfahren, aber auch die Überprüfung des Rohmaterials.
Des Weiteren können noch überprüft werden: Oberflächenrauheit, Härte, Haftfestigkeit und Duktilität der Schicht, Oberflächenfehler (z. B. Poren, Risse) und Prüfung der Korrosionsbeständigkeit mittels Salzsprühtest, Schwitzwasserklima, Corrodkote-Prüfung, CASS-Test (Essigsäure-Salzlösung).
Die elektrochemischen Eigenschaften der Elektrolyte können mittels Praxisversuchen (z. B. Hull-Zelle) oder Vergleichsmessungen (Haring-Blum-Zelle oder Cyclovoltammetrie) beurteilt werden.
Die Qualität sowie die Endeigenschaften einer Beschichtung hängen unter anderem von den folgenden Parametern ab:
- Stromdichte
- pH-Wert
- Badtemperatur
- Menge der Metallionen im Bad
- Verschmutzungsgrad des Bades (Metallpartikel im Bad führen, je stärker der Strom ist, zu mehr Einschlüssen in der Beschichtung)
- Dauer des Galvanisierens
- Abstand zwischen Kathode und Anode
- Entfettung des Werkstückes
- Reinheit des Wassers; es ist demineralisiertes Wasser zum Ansetzen (Mischen) des Bades nötig.
- Größenverhältnis zwischen Anode und Kathode, wobei die Faustregel Anode: mindestens zweimal so große Oberfläche wie die Kathode verwendet wird
Gefährdungen, Umweltproblematik
Weitere wichtige Punkte innerhalb der Galvanotechnik sind die Abwasseraufbereitung und der damit verbundene Umweltschutz, die Belehrung im Umgang mit gefährlichen Chemikalien und das Arbeiten im Labor. Die Dicke des entstehenden Metallüberzug variiert je nach Anwendung: dekorative Schichten (z. B. Gold oder Glanzchrom) haben oft Schichtstärken kleiner 1 Mikrometer (µm), während funktionelle Schichten deutlich dicker sind (Zink oder Nickel als Korrosionsschutz etwa 10 µm, Hartchrom oder Nickel als mechanisch funktionelle Schichten (z. B. in Hydraulikzylindern) meist 100–500 µm).
In der Galvanik können die Beschäftigten gegenüber Gefahrstoffen exponiert sein. Im Rahmen der Gefährdungsbeurteilung müssen die am Arbeitsplatz auftretenden Gefahrstoffe ermittelt und geeignete Schutzmaßnahmen festgelegt werden. Die DGUV Information 213-716 der Deutschen Gesetzlichen Unfallversicherung gibt Verfahrensweisen und Schutzmaßnahmen in der Galvanotechnik an, sodass für Stoffe mit Arbeitsplatzgrenzwert (AGW) dessen Einhaltung sichergestellt ist. Für Stoffe ohne AGW ist der Stand der Technik dokumentiert.[16]
Liste von Galvanisierverfahren (Überblick)
Diese technisch ähnlichen Galvanisierverfahren beschränken sich jeweils auf spezielle Substrate oder Beschichtungsmaterialien und erhielten dadurch ihre spezifischen Namen.
Zu den Verfahren, die zwar in Galvanikbetrieben durchgeführt werden, aber selbst keine galvanischen Prozesse sind, gehören die Erzeugung von Konversionsschichten durch Phosphatierung oder Chromatieren sowie das Brünieren und die stromlose Erzeugung von Metallschichten über chemische Prozesse bzw. Reduktionsmittel, siehe Außenstromlos (insbesondere Chemisch Nickel). Auch das Färben von Metallen und die Anodische Oxidation des Aluminiums beim Eloxieren sind keine galvanischen Prozesse im Sinne einer Metallabscheidung.
Galvanische Elektrolyte
- Aluminiumelektrolyte
- Antimonelektrolyte
- Bleielektrolyte
- Bronzeelektrolyte
- Cadmiumelektrolyte
- Cobaltelektrolyte
- Chromelektrolyte
- Eisenelektrolyte
- Goldelektrolyte
- Indiumelektrolyte
- Kupferelektrolyt
- Manganelektrolyte
- Messingelektrolyte
- Nickelelektrolyte
- Nickel-Eisen-Elektrolyte
- Palladiumelektrolyte
- Platinelektrolyte
- Rheniumelektrolyte
- Rhodiumelektrolyte
- Rutheniumelektrolyte
- Silberelektrolyte
- Bismutelektrolyte
- Wolframelektrolyte
- Zinkelektrolyte
- Zinnelektrolyte
Verwandte Verfahren
Die elektrophoretischen Abscheidung (Tauchlackierung) ist wie die Galvanik ein Verfahren, das mit Hilfe eines Gleichstroms eine Beschichtung erzeugt. Diese Beschichtung ist allerdings nicht metallisch, und sie entsteht durch die pH-Wert-Änderung bei der Zersetzung von Wasser.
Literatur
- Thomas Walter Jelinek: Praktische Galvanotechnik: Ein Lehr- und Handbuch. Leuze, Bad Saulgau 2005, ISBN 3-87480-207-8.
- Bernhard Gaida: Technologie der Galvanotechnik. Leuze, Bad Saulgau/Württ. 1996, ISBN 3-87480-114-4.
- Bernhard Gaida: Einführung in die Galvanotechnik: Grundlagen der chemischen, elektrochemischen, physikalischen und elektrotechnischen Begriffe. Leuze, Bad Saulgau/Württ. 1999, ISBN 3-87480-143-8.
- Wolfgang Autenrieth: Neue und alte Techniken der Radierung und der Edeldruckverfahren – Vom „Hexenmehl und Drachenblut“ zur Fotopolymerschicht – Tipps, Tricks, Anleitungen und Rezepte aus 5 Jahrhunderten. 7. Auflage. 2020, ISBN 978-3-9821765-0-5 (Einige Hinweise zu galvanischen Radierverfahren und Rezepte zum Verstahlen, Vercadmen und Versilbern von Kupfer).
- Gerhard Pinke: Fachkunde Edelmetallgewerbe. 7. Auflage. Rühle-Diebener-Verlag, Stuttgart 1992, ISBN 3-7935-5493-7.
- Hans Rudolf Christen, Gerd Meyer: Grundlagen der allgemeinen und anorganischen Chemie. 9. Auflage. Diesterweg, Frankfurt a. M. 1988, ISBN 3-7935-5394-9.
- DGUV Information 213-716: Galvanotechnik und Eloxieren – Empfehlungen Gefährdungsermittlung der Unfallversicherungsträger (EGU) nach der Gefahrstoffverordnung.
Weblinks
- Animation einer Galvanisierung (Flash; 541 kB)
- Galvanische Beschichtung im Wiki der elektrischen Kontakte
- Praktische Galvanotechnik (abgerufen am 18. Juni 2020)
- VORLESUNG FERTIGUNGSTECHNIK I (abgerufen am 18. Juni 2020)
- Grundlagen Galvanotechnik (abgerufen am 18. Juni 2020)
Einzelnachweise
- Nasser Kasnani: Galvanotechnik – Grundlagen, Verfahren und Praxis einer Schlüsseltechnologie. 2., überarb. u, erw. Auflage. Hanser, München/Wien 2009, ISBN 978-3-446-41738-0, S. 16.
- Wolfgang Miehle: Gelenk- und Wirbelsäulenrheuma. Eular Verlag, Basel 1987, ISBN 3-7177-0133-9, S. 174.
- Harald Eggebrecht: Der Ur-Strom. Dem Geheimnis auf der Spur. In: Süddeutsche Zeitung SZ.de. Süddeutsche Zeitung Digitale Medien GmbH, 29. Juli 2016, abgerufen am 16. April 2020.
- Hans-Gert Bachmann, Günter Bachmann: Oberflächenvergoldung: Alte und neue Techniken. In: Chemie in unserer Zeit. Band 23, Nr. 2, April 1989, S. 46–49, doi:10.1002/ciuz.19890230203.
- British bronze sculpture founders and plaster figure makers, 1800-1980 - E - National Portrait Gallery. In: National Portrait Gallery. National Portrait Gallery, abgerufen am 16. April 2020 (englisch).
- Darstellung der Galvanoplastik mit Nennung konkreter metallisierter Figuren, abgerufen am 26. Dezember 2020.
- Nasser Kanani: Galvanotechnik : Grundlagen, Verfahren, Praxis. 2., überarb. u, erw. Auflage. Hanser, München 2009, ISBN 978-3-446-41738-0, S. 24.
- Nasser Kanani: Galvanotechnik : Grundlagen, Verfahren, Praxis. 2., überarb. u, erw. Auflage. Hanser, München 2009, ISBN 978-3-446-41738-0, S. 12–14.
- Integrierte Vermeidung und Verminderung der Umweltverschmutzung. (PDF) Merkblatt zu den besten verfügbaren Techniken für die Oberflächenbehandlung von Metallen und Kunststoffen. In: BVT-Merkblätter und Durchführungsbeschlüsse. Umweltbundesamt UBA, September 2005, abgerufen am 16. April 2020.
- Zentralverband Oberflächentechnik e.V. Stimme der Galvano- und Oberflächentechnik. Zentralverband Oberflächentechnik e.V. ZVO, abgerufen am 16. April 2020.
- Swissgalvanic – Mitglieder. Abgerufen am 16. April 2020.
- sofia, Ökopool, ZVO: Branchenanalyse der deutschen Galvano- und Oberflächentechnik. (PDF) 2006, abgerufen am 16. April 2020.
- Systemadmin_Umwelt: Galvanische Oberflächenbeschichtung. In: Umweltbundesamt > Themen > Wirtschaft | Konsum > Industriebranchen > Herstellung und Verarbeitung von Metallen. Umweltbundesamt, 29. Januar 2013, abgerufen am 16. April 2020.
- Nasser Kanani: Galvanotechnik : Grundlagen, Verfahren, Praxis. 2., überarb. u, erw. Auflage. Hanser, München 2009, ISBN 978-3-446-41738-0, S. 127–130.
- Gabriele Dietrichs, Paul Rosenhain: Galvanoforming: Bio-Ästhetik in der restaurativen Zahnheilkunde. Verlag Neuer Merkur GmbH, 1995, ISBN 978-3-921280-99-7, S. 25– (eingeschränkte Vorschau in der Google-Buchsuche).
- Deutsche Gesetzliche Unfallversicherung e. V. (DGUV): Galvanotechnik und Eloxieren – Empfehlungen Gefährdungsermittlung der Unfallversicherungsträger (EGU) nach der Gefahrstoffverordnung. Abgerufen am 15. Oktober 2019.