Spritzgießen
Das Spritzgießen (oft auch als Spritzguss oder Spritzgussverfahren bezeichnet) ist ein Urformverfahren, das hauptsächlich in der Kunststoffverarbeitung eingesetzt wird. Dabei wird mit einer Spritzgießmaschine der jeweilige Werkstoff verflüssigt (plastifiziert) und in eine Form, dem Spritzgießwerkzeug, unter Druck eingespritzt. Im Werkzeug geht der Werkstoff durch Abkühlung oder eine Vernetzungsreaktion wieder in den festen Zustand über und wird nach dem Öffnen des Werkzeuges als Fertigteil entnommen. Der Hohlraum, die Kavität, des Werkzeuges bestimmt dabei die Form und die Oberflächenstruktur des fertigen Teiles. Es sind heute Teile im Gewichtsbereich von wenigen Zehntel Gramm bis zu einer Größenordnung von 150 kg herstellbar.
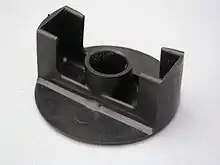
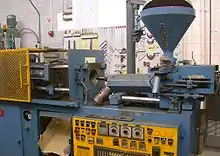
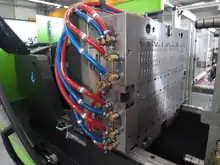
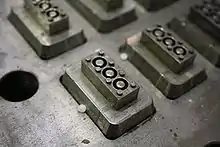
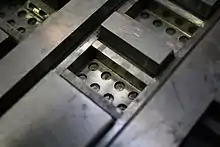
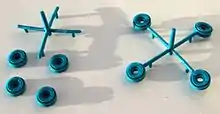
Mit diesem Verfahren lassen sich direkt verwendbare Formteile in großer Stückzahl kostengünstig herstellen. Die Kosten für das Werkzeug machen einen großen Teil der notwendigen Investitionen aus. Dadurch ist selbst bei einfachen Werkzeugen die Schwelle der Wirtschaftlichkeit erst bei einigen tausend Teilen erreicht. Andererseits können die Werkzeuge für die Herstellung von bis zu einigen Millionen Teilen verwendet werden.
Das Spritzgießen, insbesondere erweiterte spezielle Verfahren, erlaubt eine nahezu freie Wahl von Form und Oberflächenstruktur wie z. B. glatte Oberflächen, Narbungen für berührungsfreundliche Bereiche, Muster, Gravuren und Farbeffekte. Zusammen mit der Wirtschaftlichkeit macht dies das Spritzgießen zum weitestverbreiteten Verfahren zur Massenherstellung von Kunststoffteilen in praktisch allen Bereichen.
Die Formteile, die mit Spritzgießen hergestellt werden, lassen sich wie folgt kategorisieren: A-Teile – Präzisionsteile mit höchsten Anforderungen, B-Teile – technische Teile mit hohen Anforderungen und C-Teile – geometrisch einfache Formteile aus Standardkunststoffen mit geringen Anforderungen. Alle Kategorien besitzen unter anderem folgende wesentliche Qualitätsmerkmale: Formteilmaße und -gewicht, Festigkeit, Verzugserscheinungen und Oberflächenbeschaffenheit.[1]
Unterteilung der Spritzgießverfahren
Beim Spritzgießen werden fast ausschließlich Kunststoffe verarbeitet. Diese lassen sich in Thermoplaste, Duroplaste und Elastomere unterteilen. Alle drei Materialarten können im Spritzgussverfahren verwendet werden, wobei das Thermoplast-Spritzgießen die größte wirtschaftliche Bedeutung hat. Es ist das am häufigsten verwendete Kunststoffverarbeitungsverfahren überhaupt.
Deswegen soll im Folgenden das Verfahren zunächst für Thermoplaste erklärt werden. Das Spritzgießen von Duroplasten und Elastomeren funktioniert prinzipiell gleich und unterscheidet sich in erster Linie nur in den Betriebsparametern (z. B. Temperaturen).
Die unten beschriebenen speziellen Verfahren stellen Erweiterungen bzw. Modifikationen des Grundprozesses für bestimmte Anwendungen dar.
Thermoplast-Spritzgießen
Grundsätzlicher Aufbau einer Spritzgießmaschine
Die heute übliche Schneckenkolbenspritzgießmaschine besteht aus zwei Einheiten: der Spritzeinheit oder auch Plastifiziereinheit, welche den Kunststoff plastifiziert, aufbereitet und dosiert, und der Schließeinheit, die das Formwerkzeug schließt, zuhält und wieder öffnet.
Die Spritzeinheit setzt sich im Wesentlichen aus einem waagerechten Zylinder, dem Plastifizierzylinder und einer darin befindlichen Schnecke zusammen. Die Schnecke rotiert und ist auch axial im Zylinder beweglich. An einem Ende des Plastifizierzylinders befindet sich der Einfülltrichter zum Beschicken mit dem Rohmaterial, am anderen befindet sich die Düse, welche entweder verschließbar oder nicht verschließbar sein kann, sie stellt den Übergang zur Schließeinheit dar.
Die Schließeinheit besteht aus dem Formwerkzeug selbst, das in zwei Hälften trennbar ist (Formtrennebene). Die Hälften sind auf zwei Aufspannplatten montiert, von denen die eine, die Düsenseite, starr und der Düse der Spritzeinheit zugewandt ist. Die andere, die Auswerferseite, ist beweglich. Sie kann hydraulisch oder elektromechanisch (Kniehebelmechanismus) von der Düsenseite wegbewegt oder mit Kraft auf sie gepresst werden. Sie enthält den namensgebenden Mechanismus, welcher das Spritzgußteil entformt (auswirft).
Spritz- und Schließeinheit müssen entsprechend dem Werkstoff, Bauteil und Prozess temperiert werden (die Spritzgußform ist ggf. temperaturgeführt). Da die beiden Einheiten unterschiedliche Temperaturen aufweisen, können sie, außer bei Heißkanalsystemen, zur thermischen Trennung voneinander wegbewegt werden.
Bis 1956 verwendete man Kolbenspritzgießmaschinen.
Verfahrensablauf
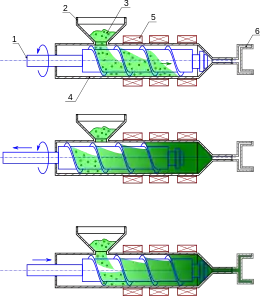
Plastifizieren und Dosieren
Der thermoplastische Kunststoff rieselt in Form eines Granulats in die Gänge der rotierenden Schnecke ein. Das Granulat wird Richtung Schneckenspitze gefördert und durch die Wärme des Zylinders und die Friktionswärme, die beim Zerteilen und Scheren des Materials entsteht, erwärmt und aufgeschmolzen. Die Schmelze sammelt sich vor der Schneckenspitze, da die Düse zu diesem Zeitpunkt geschlossen ist. Da die Schnecke axial beweglich ist, weicht sie durch den Druck zurück, auch schraubt sie sich ähnlich einem Korkenzieher aus der Masse heraus. Die Rückwärtsbewegung wird durch einen Hydraulikzylinder oder elektrisch gebremst, so dass sich in der Schmelze ein Staudruck aufbaut. Dieser Staudruck in Verbindung mit der Schneckenrotation verdichtet und homogenisiert das Material.
Die Schneckenposition wird gemessen und sobald sich eine für das Werkstückvolumen ausreichende Materialmenge angesammelt hat, ist der Dosiervorgang beendet und die Schneckenrotation wird eingestellt. Ebenso wird die Schnecke aktiv oder passiv entlastet, so dass die Schmelze dekomprimiert wird.
Einspritzen
In der Einspritzphase wird die Spritzeinheit an die Schließeinheit gefahren, mit der Düse angedrückt und die Schnecke rückseitig unter Druck gesetzt. Dabei wird die Schmelze unter hohem Druck (meist zwischen 500 und 2000 bar) durch die geöffnete Düse und den Anguss bzw. das Angusssystem des Spritzgießwerkzeugs in den formgebenden Hohlraum gedrückt. Die Rückstromsperre verhindert dabei ein Zurückströmen der Schmelze Richtung Einfülltrichter.
Während des Einspritzens wird versucht, ein möglichst laminares Fließverhalten der Schmelze zu erreichen. Das heißt, die Schmelze wird im Werkzeug dort, wo sie die gekühlte Werkzeugwand berührt, sofort abgekühlt und bleibt erstarrt „kleben“. Die nachrückende Schmelze wird durch den dadurch verjüngten Schmelzkanal mit noch höherer Geschwindigkeit und noch mehr Scherdeformation gedrückt und vorne an der Schmelzfront zum Rand hin dehndeformiert. Es überlagert sich Wärmeabfuhr über die Werkzeugwand und Wärmezufuhr durch Schererwärmung. Die hohe Einspritzgeschwindigkeit erzeugt in der Schmelze eine Schergeschwindigkeit, welche die Schmelze leichter fließen lässt. Dennoch ist ein stets schnelles Einspritzen nicht anzustreben, denn durch die hohe Schergeschwindigkeit wird auch der Molekülabbau verstärkt. Auch die Oberfläche, das Aussehen und der Orientierungszustand werden durch die Einspritzphase beeinflusst.[2]
Nachdrücken und Abkühlen
Da das Werkzeug (mit typischerweise 20 bis 120 °C) kälter als die Kunststoffmasse (mit typischerweise 200 bis 300 °C) ist, kühlt die Schmelze in der Form ab und erstarrt bei Erreichen des Gefrierpunktes. Das Abkühlen geht einher mit einer Volumenschwindung, die sich nachteilig auf Maßhaltigkeit und Oberflächenqualität des Werkstückes auswirkt. Um diese Schwindung teilweise zu kompensieren, wird auch nach Füllung der Form ein reduzierter Druck aufrechterhalten, damit Material nachfließen und die Schwindung ausgleichen kann. Dieses Nachdrücken kann so lange erfolgen, bis der Siegelpunkt erreicht ist, also der Anguss erstarrt ist.
Nach Beendigung des Nachdrückens kann die Düse geschlossen werden und in der Spritzeinheit bereits der Plastifizier- und Dosiervorgang für das nächste Formteil beginnen. Das Material in der Form kühlt in der Restkühlzeit weiter ab, bis auch die Seele, der flüssige Kern des Werkstückes, erstarrt ist und eine zum Entformen hinreichende Steifigkeit erreicht ist.
Die Spritzeinheit wird dann von der Schließeinheit wegbewegt (abgehoben), da kein Kunststoff mehr aus dem Anguss austreten kann. Dies dient dazu, einen zu starken Wärmeübergang von der wärmeren Düse auf das kältere Werkzeug zu unterbinden und vermeidet so ein zu starkes Abkühlen der Düse (Einfrieren).
Entformen
Zum Entformen öffnet sich die Auswerferseite der Schließeinheit und wird das Werkstück durch in die Kavität hineindringende Stifte ausgeworfen. Es fällt dann entweder herunter (Schüttgut) oder wird durch Handlinggeräte aus dem Werkzeug entnommen und geordnet abgelegt oder gleich einer Weiterverarbeitung zugeführt.
Der Anguss muss entweder durch separate Bearbeitung entfernt werden oder wird beim Entformen automatisch abgetrennt. Auch angussloses Spritzgießen ist mit Heißkanalsystemen möglich, bei denen das Angusssystem ständig über der Erstarrungstemperatur bleibt und das enthaltene Material somit für den nächsten Schuss verwendet werden kann.
Nach dem Entformen schließt sich das Werkzeug wieder und der Zyklus beginnt von neuem.
Schritte | 1 s | 2 s | 3 s | 4 s | 5 s | 6 s | 7 s | 8 s | 9 s | 10 s | 11 s | 12 s | 13 s | 14 s | 15 s | 16 s | 17 s | 18 s | 19 s | 20 s | 21 s | 22 s |
---|---|---|---|---|---|---|---|---|---|---|---|---|---|---|---|---|---|---|---|---|---|---|
Werkzeug schließen | ||||||||||||||||||||||
Spritzeinheit vor | ||||||||||||||||||||||
Plastifizieren | ||||||||||||||||||||||
Einspritzen | ||||||||||||||||||||||
Nachdrücken | ||||||||||||||||||||||
Dekomprimieren | ||||||||||||||||||||||
Spritzeinheit zurück | ||||||||||||||||||||||
Restkühlen | ||||||||||||||||||||||
Entformen | ||||||||||||||||||||||
Pause | ||||||||||||||||||||||
Physikalische Kühlzeit |
Verwendete Kunststoffarten und Produkte
Spritzgussteile können mit Massen zwischen einigen Milligramm und ca. 150 kg hergestellt werden. Die verarbeiteten thermoplastischen Kunststoffe werden durch Additive und Füllstoffe für die Spritzgießverarbeitung und die spätere Verwendung modifiziert. Darunter sind auch sehr harte anorganische Füllstoffe wie Glaskugeln oder sehr oft Glasfasern.
Im Fahrzeugbau werden Polyolefine, hauptsächlich Polypropylen für Armaturenbretter und Stoßstangen im Spritzguss verwendet. Plexiglas (PMMA) und Polycarbonat (PC) werden für transparente Gegenstände (KFZ-Scheinwerfer, Rückleuchten) verwendet. Polystyrol (PS) und dessen Copolymere (ABS = Acrylnitril-Butadien-Styrol) werden größtenteils für Spielzeug (z. B. Lego) und Haushaltsgeräte benutzt. Polyamid (PA), Polyoxymethylen (POM) und viele weitere technische Kunststoffe werden ebenfalls im Maschinenbau und der Elektrotechnik eingesetzt, allerdings in wesentlich geringeren Mengen für meist hochpreisige Teile.
Beim Naturfaser-Spritzguss werden mit Naturfasern gefüllte Thermoplaste verwendet.
Duroplast-Spritzgießen
Verfahren
Das Duroplast-Spritzgießen unterscheidet sich vom Thermoplast-Spritzgießen in seinen Betriebsparametern. Duroplaste härten meistens durch Einwirken von Wärme aus. Nach dem Aushärten ist ein erneutes Aufschmelzen nicht mehr möglich, nur ein Recycling. Die noch nicht ausgehärtete Masse muss deshalb mit einer vergleichsweise niedrigen Temperatur (je nach Material ca. 30 bis 110 °C) in die Form eingespritzt und dort durch eine höhere Temperatur (je nach Duroplast zwischen 130 °C und 250 °C) ausgehärtet werden.
Die aufbereitete Formmasse fließt u. a. wegen der hohen Füllstoffanteile schlechter als Thermoplastschmelzen. Auf diese Besonderheiten muss der Spritzgießvorgang abgestimmt werden.
Die Spritzgießmaschine arbeitet mit einer Förderschnecke, die wenig Scherwärme erzeugt. Die erzielbaren Drücke betragen bis zu 2500 bar. Das Formteil wird heiß entformt. Angussloses Spritzgießen ist mit Kaltkanalsystemen, dem Pendant zum Heißkanalsystem, bei dem der Anguss gekühlt und so eine Vernetzung verhindert wird, möglich.
Mit dem Duroplast-Spritzgießen können sehr große Wanddicken der Teile von bis zu 50 mm realisiert werden.
Anwendung
Ein typisches Anwendungsgebiet für Duroplaste (BMC) sind Fahrzeugscheinwerfer, genauer deren Reflektoren, bei denen die gute Maßhaltigkeit und Temperaturbeständigkeit von Duroplasten zum Tragen kommt. Bei Wanddicken bis ca. 4 mm allerdings sind die Zykluszeiten der Duroplastverarbeitung meist länger als die bei Thermoplasten, so dass Duroplaste, wenn auf ihre besonderen elektrischen und mechanischen Qualitäten verzichtet werden kann, im Wirtschaftlichkeitsvergleich trotz ihres im Allgemeinen günstigeren Materialpreises meist gegenüber den Thermoplasten verlieren.
Elastomer-Spritzgießen
Elastomere – wie Naturkautschuk – vulkanisieren analog zu den Duroplasten durch den Einfluss von Wärme. Das Werkzeug muss also auch hier heißer als die Formmasse beim Einspritzvorgang sein. Eine Ausnahme bilden die thermoplastischen Elastomere.
Das Spritzgießen von Elastomeren erfolgt auf Schneckenspritzgießmaschinen. Elastomere können in Form von rieselfähigen Pulvern oder bandförmig von einer speziellen Förderschnecke, die wenig Scherung in die plastifizierte Masse einbringt, eingezogen werden. Der Zylinder wird meist mit einer Flüssigkeit auf ca. 80 °C temperiert (Wassertemperierung), um Überhitzung zu vermeiden, was ein vorzeitiges ausvulkanisieren des Elastomers zufolge hätte. Weiters stellt auch das gratfreie Spritzgießen von Elastomeren eine besondere Herausforderung dar, da Elastomere im Fließbereich (genau so wie Duroplaste) sehr dünnflüssig sind, so ist auch der Aufwand bei der Werkzeuggestaltung etwas höher als bei Thermoplastwerkzeugen.
Von den genannten Besonderheiten abgesehen, verläuft der Spritzgießvorgang prinzipiell auch hier ähnlich wie beim Thermoplast-Spritzgießen ab. Die Schnecke knetet und mischt die Formmasse, die dadurch homogen aufbereitet wird. Dadurch lässt sich z. B. gegenüber dem Pressen, bei dem durch die Wärmezufuhr von außen eine inhomogene Temperaturverteilung entsteht, eine Qualitätsverbesserung der hergestellten Formteile erzielen. Einige mechanische Eigenschaften können bis zu 30 % höher liegen als bei gepressten Elastomeren.
Beim Strömen in der Düse und in den Angusskanälen entsteht Reibungswärme. Dies verkürzt die Vulkanisierzeit. Dadurch wird der Spritzgießprozess besonders wirtschaftlich. Die hohe Materialviskosität macht relativ große Angussquerschnitte erforderlich. Auch bei Elastomeren sind Kaltkanalsysteme einsetzbar.
Man verwendet beim Elastomerspritzgießen oft Spritzgießmaschinen mit mehreren Schließeinheiten für mehrere Werkzeuge und unterschiedlicher Teile, da die Vulkanisierzeit erheblich größer ist als die Aufbereitungszeit in der Spritzeinheit.
Spezielle Verfahren
Das oben beschriebene Grundverfahren lässt sich für spezielle Anwendungszwecke modifizieren bzw. erweitern.
So erlaubt das Mehrkomponenten-Spritzgießen die Herstellung von Teilen aus unterschiedlichen Kunststoffen in einem Arbeitsgang. Beim In-Mold-Verfahren werden in das Spritzgießwerkzeug eingelegte Materialien hinterspritzt, z. B. der Hartschaum eines Sporthelmes oder beschriftete Folien (In-Mould-Labeling, IML). Alternativ kann bei der In-Mould Decoration (IMD) auch nur eine bedruckte Folie, die später entfernt wird, eingelegt werden, so dass nur die Farbe auf dem Teil verbleibt. Das Metallfolienhinterspritzen dient der Herstellung von Kunststoffteilen mit Metallfolienüberzug.
Wird der Werkstoff in eine nicht ganz geschlossene Form eingespritzt und die Form erst danach vollends geschlossen, so spricht man vom Spritzprägen. Dieses kann zum Quellflussprägen erweitert werden, indem dabei Materialien hinterspritzt werden, analog zum In-Mold-Verfahren.
Beim Innendruck-Spritzgießen (auch Fluidinjektionstechnik (FIT) genannt, aufteilbar in Gasinnendruck-Spritzgießen (GID) und Wasserinnendruck-Spritzgießen (WID)) wird zusätzlich ein Gas oder Wasser injiziert, welches nach dem Erstarren oder Aushärten entweicht, so dass ein Hohlraum entsteht. Dagegen dient beim Gashinterdruck-Verfahren (GHD) das zwischen Werkzeugwand und Formteil eingebrachte Gas dem festen Anpressen an die gegenüberliegende Wand, um u. a. eine hohe Oberflächenqualität zu erreichen. Gase können auch mit Treibmitteln verteilt im Kunststoff erzeugt werden, was einen Schaumstoff ergibt (Thermoplast-Schaumgießen, TSG).
Beim Schmelzkern-Spritzgießen wird ein niedrigschmelzendes Metall eingegossen, das nachher im Heizbad ausgeschmolzen wird, um ebenfalls einen Hohlraum zu schaffen.
Das Pulverspritzgießen (Powder Injection Molding (PIM)) erlaubt die Herstellung von Metall- und Keramikteilen, indem Metall- und Keramikpulver mit einem Bindemittel spritzgegossen, das Bindemittel danach entfernt und das verbleibende Pulver schließlich gesintert wird.
Die Exjection oder Extrusionsspritzgießen stellt eine Kombination aus Spritzgießen und Extrusion dar. Beim Spritzstreckblasen wird ein spritzgegossener Rohling, z. B. ein PET-Rohling für Flaschen einem anschließenden Streck- und Blasformprozess unterzogen.
Die Tandem-Werkzeuge ähneln einem klassischen Werkzeug. Es befindet sich jeweils eine Kavität an jeder der zwei Trennebenen. Die Angüsse können je nach Belieben heiß oder kalt ausgeführt sein. Durch die Dopplung ist es möglich, die erste Kavität zu spritzen; während diese abkühlt, wird die andere Kavität gefüllt. So ist es möglich die nicht genutzte Zeit der ersten Erkaltung produktiv zu nutzen.
Probleme
Durch die vielfältigen Möglichkeiten bei der Wahl der Bauteilgeometrie, des genauen Spritzverfahrens und des Werkstoffes können beim Spritzprozess bzw. beim fertigen Bauteil verschiedene, meist unerwünschte, Effekte auftreten. Angusshöfe, bei denen die Oberflächenstruktur und -Form vom restlichen Bauteil abweicht, entstehen an der Schnittstelle zwischen Anguss und eigentlichem Bauteil. Gründe hierfür können eine lokale Umorientierung der Moleküle des Werkstoffs, zu hohe Einspritzgeschwindigkeit oder zu geringe Prozesstemperaturen sein. Lufteinschlüsse entstehen bei schlecht gewählter Bauteilgeometrie, zu niedrigen Prozesstemperaturen, zu hoher Einspritzgeschwindigkeit oder mangelhafter Entlüftung. Werden solche Lufteinschlüsse durch den Prozess stark verdichtet, so kann es zu lokal sehr hohen Temperaturen und in deren Folge zu Verkohlungen im Bauteil kommen. Hierbei spricht man auch vom Dieseleffekt. Einfallstellen und generell Verzug, also die Abweichung der Bauteilform von der eigentlich gewünschten, entstehen nach dem Ausformen, beim Abkühlen. Hierfür sind vielfältige Faktoren zu berücksichtigen. Bei der Wahl der Bauteilgeometrie können etwa Massenanhäufungen durch lokal unterschiedliche Wandstärken des Bauteils dazu führen, dass die einzelnen Bereiche beim Abkühlen verschieden stark schrumpfen oder auch unterschiedlich schnell abkühlen. Auch eine nicht optimale Prozesstemperatur oder seltener ein nicht genügend homogener Ausgangsstoff können diese Probleme verursachen.[3]
Arbeitsschutz
Bei Kunststoffspritzgießmaschinen handelt es sich um gekapselte Anlagen, an denen in der Regel eine Exposition gegenüber Gefahrstoffen nur bei bestimmten Tätigkeiten, insbesondere bei Umrüst- und Instandhaltungsarbeiten sowie ggf. bei der Probenahme und beim Auftreten von Leckagen möglich ist. Trotzdem können Zersetzungsprodukte bei der Verarbeitung thermoplastischer Kunststoffe in Spritzgießmaschinen in der Luft für Beschäftigte eine Gefahr darstellen.[4]
Die Empfehlungen Gefährdungsermittlung der Unfallversicherungsträger (EGU) basieren auf Messungen möglicher Zersetzungsprodukte thermoplastischer Kunststoffe in Spritzgießmaschinen in der Luft an Arbeitsplätzen. Sie stellen ein geeignetes Beurteilungsverfahren für die Exposition bei der Verarbeitung von Kunststoffen in Spritzgießmaschinen dar und bieten praktische Unterstützung bei der Durchführung der Gefährdungsbeurteilung – inklusive Schutzmaßnahmen – gemäß der Gefahrstoffverordnung. Dermale Gefährdungen, z. B. durch heiße Oberflächen und erhitzte Kunststoffe müssen in der Gefährdungsbeurteilung gesondert berücksichtigt werden.[4]
Literatur
- F. Johannaber, W. Michaeli: Handbuch Spritzgießen. Hanser Verlag, 2002, ISBN 3-446-15632-1.
- T. Munch, B. Lantz: Konsequente Optimierung des Spritzgiessverfahrens. Ein SGP-Handbuch. 2009, ISBN 978-3-8370-7081-1.
- S. Stitz, W. Keller: Spritzgießtechnik. Hanser, 2001, ISBN 3-446-21401-1.
Weblinks
- Literatur von und über Spritzgießen im Katalog der Deutschen Nationalbibliothek
- Themenseite „Basiswissen Spritzgießen“ der Zeitschrift Kunststoffe
- Whitepaper "Qualität erhöhen, Energieverbrauch senken – ein Leitfaden" des Instituts für Integrierte Produktion Hannover
- Formelsammlung zum Thema Spritzgießen für den Praktiker (stammt aus einer Vorlesung einer Hochschule mit renommiertem Kunststoffinstitut)
Einzelnachweise
- IPH Whitepaper-Energiesparen. Abgerufen am 15. Januar 2018.
- Christian Bonten: Kunststofftechnik Einführung und Grundlagen, Hanser Verlag, 2014.
- http://kunststoff.bearx.de/ausbildung/spritzfehler/spritzfehler.htm abgerufen am 9. Juli 2015.
- Deutsche Gesetzliche Unfallversicherung e. V. (DGUV): DGUV Information 213-728 – Empfehlungen Gefährdungsermittlung der Unfallversicherungsträger (EGU) nach der Gefahrstoffverordnung - Verarbeitung thermoplastischer Kunststoffe in Spritzgießmaschinen. Abgerufen am 11. November 2019.