Verzinken
Beim Verzinken wird Stahl mit einer dünnen Schicht Zink versehen, um ihn vor Korrosion zu schützen.[1]
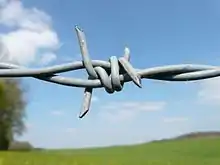
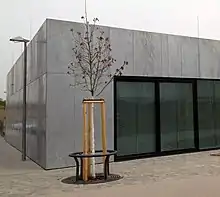
Im Gegensatz zu nichtmetallischen Beschichtungen bewirkt die Zinkschicht einen aktiven Korrosionsschutz, indem sie gegenüber dem edleren Eisen als Opferanode wirkt (siehe: Spannungsreihe). Die kathodische Wirkung des Zinküberzuges verhindert die Korrosion des Eisens bis zu einem Abstand von etwa 5 mm, so dass auch Fehlstellen in der Zinkschicht und bloßliegende Schnittkanten geschützt sind. Die resultierende Bimetallkorrosion bewirkt jedoch einen beschleunigten Abtrag der angrenzenden Zinkschicht.
Verzinkungsverfahren
Verfahren zum Auftrag eines Überzugs aus Zink auf Bauteile auf Stahl:
- Feuerverzinken (Schmelztauchverzinkung)[2]
- Stückverzinken (Tauchfeuerverzinkung) durch Eintauchen in eine Zinkschmelze ergibt Schichtdicken von 50 bis 150 µm[3]
- Bandverzinken (Sendzimirverzinkung) durch kontinuierlichen Durchlauf durch eine Zinkschmelze ergibt Schichtdicken von 5 bis 40 µm, typisch sind 10 bis 20 µm[4]
- Spritzverzinken (Lichtbogenspritzen[5] oder Flammspritzen mit Zinkdraht[6] oder Zinkpulver), Schichtdicken von 80 und 150 µm
- Galvanisch Verzinken (Elektrolytische Verzinkung; in der Schweiz: Promatisieren), Schichtdicke steuerbar von 2,5 bis 25 µm,[3] meist werden jedoch nur 10 µm erreicht[7]
- Sherardisieren (Diffusionsverzinkung), Schichtdicke steuerbar zwischen 10 und 80 µm
- Zinklamellen/Binder-Systeme (Aufsintern einer anorganischen Beschichtung aus chrompassivierten Zinklamellen im Tunnelofen; in der Schweiz: Dacrometisieren), Schichtdicken von 4 bis 5 µm pro Auftrag, typische Gesamtdicke 8 bis 15 µm.
- Mechanisches Verzinken, Schichtdicke bis 50 µm
- Bindemittelhaltige Zinkbeschichtungen – Eine Zinkstaubfarbe wird ohne Wärmeeinwirkung aufgetragen. Die Zinkpartikel werden durch ein Bindemittel zusammengehalten. Der Zinkanteil des Trockenfilms sollte mindestens 90 % betragen. Siehe auch Filmverzinken
Der Bundesgerichtshof urteilte 1969 (BGH, 12.03.1969 – I ZR 79/67): „Der Verkehr verstehe unter einer Verzinkung, daß ein reiner Zinküberzug aufgebracht werde, denn das entspreche dem Sprachgebrauch und sei auch das übereinstimmende Ergebnis aller Verzinkungsverfahren, wenn diese auch in sonstigen Beziehungen abweichend verliefen.“ Jedem Verzinkungsverfahren liegt demnach das Aufbringen eines reinen Zinküberzugs zugrunde. Entsprechend können Beschichtungen wie Zinkstaubfarben nicht als Verzinkung bezeichnet werden. Zinkhaltige Beschichtungen können nur dann einen aktiven Korrosionsschutz gewährleisten, wenn genügend Zinkpartikel enthalten sind, um einen durchgängig leitfähigen Film zu erzeugen. Um dies zu erreichen, muss in der Regel der Bindemittelgehalt des Produkts soweit reduziert werden, dass im Vergleich zu anderen Korrosionsschutz-Anstrichen die Haftung und Widerstandsfähigkeit leidet.[8][9]
Feuerverzinkung/ Schmelztauchverfahren
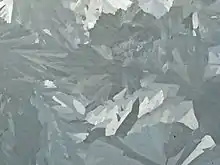
Beim Feuerverzinken wird Stahl in eine Schmelze aus flüssigem Zink getaucht, deren Temperatur bei ca. 450 °C liegt. Unterschieden wird zwischen
- dem Stückverzinken, bei dem unterschiedlich geformte Stahlteile (beispielsweise Treppenelemente oder Geländer) in das Zinkbad getaucht werden und
- dem kontinuierlichen Endlosverfahren für Halbzeuge wie Bleche, das auch Bandverzinken oder Sendzimir-Verzinken genannt wird.
Die Zinkschichtdicke liegt beim Stückverzinken in der Regel zwischen 50 und 150 Mikrometer und beim Bandverzinken zwischen 5 bis 40 Mikrometer. Durch die größere Zinkschichtdicke erreichen stückverzinkte Bauteile eine Nutzungsdauer von zumeist mehr als 50 Jahren.[10]
Beim Feuerverzinken bildet sich an der Grenzfläche zwischen Stahl und Zink eine Legierung. Durch die Wärmeeinwirkung können sich größere (Blech-)Teile beim Feuerverzinken verziehen. Eine Wandstärke von wenigstens 1,5 mm wird empfohlen. Blechfalze können durch die Zinkschicht verklebt werden, wodurch sich die Steifigkeit der Konstruktion erhöht. Gewinde und passgenaue Öffnungen müssen nach dem Feuerverzinken in der Regel nachgeschnitten werden. Die Beschichtung feuerverzinkter Oberflächen bedarf besonderer Maßnahmen, da manche Lacke die Bildung einer Oxidschicht an der Oberfläche des Zinks nicht verhindern können, wodurch die Haftung erschwert wird.[11][12]
Spritzverzinken
Spritzverzinken ist eine Variante des Flammspritzens, bei der Zinkpulver oder ein Zinkdraht durch eine (Sauerstoff-Acetylen-)Flamme oder Lichtbogen aufgeschmolzen und durch Druckluft zerstäubt auf das Werkstück aufgebracht wird. Das noch flüssige Zink bildet auf dem Werkstück eine poröse Schicht, die ähnlich gute Korrosionsschutzeigenschaften aufweist, wie die durch Feuerverzinken erzeugte. Durch die große innere Oberfläche der porösen Schicht erfordert eine anschließende Lackierung ungewöhnlich große Mengen Grundierung oder Füller.
Um eine ausreichende Haftung zu erreichen, wird die Oberfläche des Werkstücks oft durch Sandstrahlen aufgeraut, was zum Verziehen von dünnen Blechen führen kann. Auch ist es schwierig eine gleichmäßige Schichtdicke zu erzielen, insbesondere in schwer zugänglichen Hohlräumen. Der Überzug erreicht oft eine Dicke von einem Millimeter.[13] Im Vergleich zum Feuerverzinken ist die thermische Belastung des Werkstückes gering. Nachteilig ist, dass Hohlräume und schwer zugängliche Stellen (Behälter-Innenräume, Falze etc.) nicht erreicht werden können.
Sherardisieren – Diffusionsverzinken
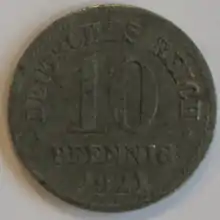
Beim Sherardisieren werden in geschlossenen, rotierenden Trommeln die zu verzinkenden Metallteile chargenweise mit Zinkpulver erhitzt.[14] Bei Temperaturen von 320 °C bis 500 °C verdampft Zink und verbindet sich durch Diffusion mit dem Basismaterial zu einer intermetallischen Phase, welche aus dem Grundmaterial heraus wächst. Es bilden sich gleichmäßige, temperaturbeständige, harte und abriebfeste Zink-Eisen-Legierungsschichten. Das Verfahren eignet sich für Teile mit komplizierten Geometrien und Hohlräumen, wie auch zur preisgünstigen Beschichtung von Massenprodukten. Da der Prozess trocken abläuft und keine wässrige oder ätzende Vorbehandlung erforderlich ist, kann eine Wasserstoffversprödung der zu beschichteten Teile ausgeschlossen werden. Die matt-graue Oberfläche bietet eine gute Lackhaftung und erreicht in Verbindung mit Passivierungs- oder Duplex-Systemen einen hervorragenden Korrosionsschutz.
Zinklamellen/Binder-Systeme
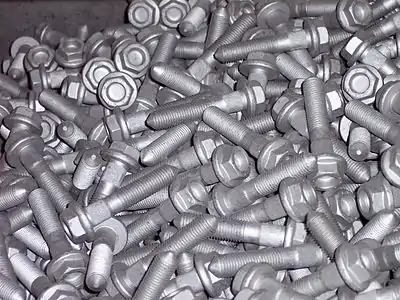
Seit Anfang der 1970er Jahre werden Dispersionen kleiner Zink- und meist auch Aluminiumflocken in einem Tauch-/Schleuder-Verfahren aufgebracht, getrocknet und bei 180–350 °C eingebrannt. Bei der klassischen Zinklamellenbeschichtung wird bei einem Beschichtungsvorgang eine Schichtdicke von etwa 4–5 µm erreicht, außerdem ist die Schicht nicht porendicht. Daher wird üblicherweise zweimal beschichtet und teilweise zusätzlich silikatisch versiegelt bzw. mit organischem Decklack überbeschichtet.
Galvanische Verzinkung
Die Werkstücke werden nicht in eine Zinkschmelze, sondern in einen Zinkelektrolyten eingetaucht; dabei wird das zu verzinkende Werkstück als Kathode in die Lösung gehängt. Als Anode benutzt man eine Elektrode aus möglichst reinem Zink. Beim galvanischen Verzinken ist der Zinkauftrag proportional zu der Stärke und Zeitdauer des Stromflusses, wobei – abhängig von der Werkstück- und Anodengeometrie – eine Schichtdickenverteilung über das gesamte Werkstück entsteht.[14] Sollen Hohlräume verzinkt werden, so müsste die Anode in den Hohlraum eingeführt werden. Im galvanischen Bad besteht die Gefahr der Wasserstoffversprödung, was insbesondere bei gehärteten Stahlbauteilen von Nachteil sein kann.[15]
Durch die unterschiedlichen Schichtstärken ist der Korrosionsschutz meist weniger langlebig als bei anderen Verzinkungsverfahren. Galvanisch verzinkte Werkstücke, die über längere Zeiträume einer direkten Bewitterung ausgesetzt werden, sollten eine zusätzliche Kunstharzbeschichtung erhalten (siehe Duplex-System). Galvanisch verzinkte Bleche eignen sich gut für die anschließende Pulverbeschichtung, da die Oberfläche gleichmäßig ist und so gut wie keine Oberflächenstruktur aufweist (Blumen). Hoch belastete Werkstücke wie Schrauben, bei denen sich eine Kunststoff-Beschichtung ablösen würde, werden zur Verbesserung des Korrosionsschutzes häufig anschließend noch einer Chromatierung unterzogen.[7]
Kleine Flächen können auch ambulant behandelt werden, indem ein Gewebe oder Schwamm mit einem Elektrolyt getränkt und zwischen das Zink und das Werkstück gebracht wird. Das Zink muss dabei am Plus- und das eiserne Werkstück am Minuspol einer Stromquelle angeschlossen sein.[16]
Nach DIN EN ISO 4042 ist der Code für galvanisch verzinkt A2F.
Mechanische Verzinkung
Für gehärtete Teile, die empfindlich gegen Wasserstoffversprödung sind, ist in einigen Spezifikationen die mechanische Beschichtung vorgeschrieben. Hier wird in einem Mischer Zinkstaub mit Glaskugeln ohne Wärmeeinwirkung auf die zu beschichtenden Teile quasi aufgehämmert. Da es sich nicht um ein elektrolytisches Verfahren handelt, entsteht kein Wasserstoff, der in das Stahlteil eindringen könnte. Je nach Teilegeometrie (z. B. Innensechskant) kann die Abriebfestigkeit etwas eingeschränkt sein. Die hochglänzenden Oberflächen der Galvanik können nicht erreicht werden. Es können Schichtdicken bis etwa 50 µm erzeugt werden.
Diese Form der Verzinkung wird bei Bauteilen aus Federstahl wie Tellerfedern oder Befestigungsclips angewendet.
Bearbeitung
Wenn es bei der nachträglichen Bearbeitung verzinkter Objekte zur Verletzung der Zinkschicht kommt, kann die Schutzwirkung beeinträchtigt werden.
Metallische Verbindungen können durch das Metall-Schutzgas-Löten (MSG-Löten), das Laserlöten und bestimmte Schweißverfahren hergestellt werden.[17]
Bei der Nachverzinkung von Schweißnähten sind die DIN EN ISO 1461 (Schichtdicke) und DIN EN 1090-2 (Vorbereitung) zu beachten. Möglich ist das Flammspritzen und die Zinkstaubbeschichtung. Bei geringeren Ansprüchen an die Schutzwirkung werden Zinksprays verwendet[17].
Nachbehandlung verzinkter Oberflächen
Verzinkte Stahlteile sind durch die Zinkschicht sehr gut vor Korrosion (Rotrost) geschützt. Die Zinkschicht selbst ist aber Korrosionsbelastungen ausgesetzt, oftmals durch Kontaktkorrosion. Auch durch den Einfluss von Seeklima kann es schnell zur Zinkkorrosion (Weißrost) kommen.
Zusätzlich aufgebrachte Passivierungsschichten und Versiegelungen verzögern die Korrosion von Zink- oder Zinklegierungsüberzügen und verbessern damit auch die Beständigkeit gegen Grundmaterialkorrosion.
Speziell für galvanisch verzinkte Teile wurden Chromatierungsverfahren entwickelt, die sich im Grad des Korrosionsschutzes und in der Farbe unterscheiden. Einige Chromatierungsschichten enthalten giftiges Chrom(VI). In letzter Zeit wurden Chrom(VI)-freie Verfahren wie die Dickschichtpassivierung entwickelt.
Zusätzliche Kunststoffbeschichtung (Duplex-System)
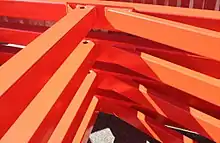
Unter Duplex-Systemen versteht man ein Korrosionsschutz-System, das aus einer Verzinkung in Kombination mit einer oder mehreren nachfolgenden Beschichtungen besteht. Die Beschichtung kann sowohl als Nass- als auch als Pulverbeschichtung ausgeführt werden. Duplex-Systeme mit Nassbeschichtungen sind in DIN EN ISO 12944-5[18], Duplex-Systeme mit Pulverbeschichtungen sind in DIN 55633 geregelt[19]. Verzinkung und Beschichtung ergänzen sich. Die Verzinkung wird durch die darüberliegende Beschichtung vor atmosphärischen und chemischen Einflüssen geschützt. Hierdurch wird die Lebensdauer der Verzinkung erhöht, welche bei direkter Bewitterung einem konstanten Abtrag unterliegt.
Die Beschädigung einer direkt auf Stahl aufgebrachten Beschichtung hat weitaus gravierendere Korrosion zur Folge, da eine dazwischenliegende Verzinkung die Unterwanderung und Ablösung der Beschichtung durch Korrosionsprodukte des Eisens, vulgo Rost, verhindert.
Durch Synergie von Verzinkung und Beschichtung ist die Gesamtschutzdauer eines Duplex-Systems 1,2- bis 2,5-mal so groß wie die Summe aus der jeweiligen Einzelschutzdauer von Verzinkung oder Beschichtung.[20]
Ausbesserung von beschädigten Zinküberzügen
Die galvanische Schutzwirkung eines Zinküberzugs verhindert die Korrosion auch auf unbeschichtetem Stahl, der nur wenige Millimeter von der Zinkschicht entfernt liegt und leitend mit dieser verbunden ist.
Um die Schutzwirkung langfristig zu erhalten, sollten beschädigte oder angearbeitete Stellen ausgebessert werden. Geeignete Ausbesserungsverfahren gemäß DIN EN ISO 1461 sind:
- Thermisches Spritzen mit Zink,
- das Auftragen geeigneter Zinkstaubbeschichtungen sowie
- Lote auf Zinkbasis.
Um die Haltbarkeit von durch Stückverzinken aufgebrachten Zinküberzügen zu erreichen, sollte die Schichtdicke des ausgebesserten Bereiches mindestens 100 µm betragen. Mit gewöhnlichen Zinksprays kann diese Schichtdicke auch bei mehrmaligem Übersprühen in der Regel nicht erreicht werden.[21] Um den galvanischen Effekt durch die Leitfähigkeit der Beschichtung zu erreichen, sollte der Trockenfilm der Beschichtung zudem mindesten 90 % Zink enthalten.[2]
Weblinks
Einzelnachweise
- Brockhaus ABC Chemie. VEB F. A. Brockhaus Verlag Leipzig 1965, S. 1484.
- Drei Verzinkungsverfahren im Vergleich, Niedax Group. Abgerufen im Februar 2021
- Übersicht Verzinkungsverfahren und Tabelle: Verzinken ist nicht Verzinken, Industrieverband Feuerverzinken
- Lexikon - Fachbegriffe aus dem Bausektor: Sendzimirverzinkung (Memento des Originals vom 10. April 2017 im Internet Archive) Info: Der Archivlink wurde automatisch eingesetzt und noch nicht geprüft. Bitte prüfe Original- und Archivlink gemäß Anleitung und entferne dann diesen Hinweis. , LKG - Ingenieurbüro für Bautechnik
- Lichtbogenspritzen. Oerlikon, abgerufen am 12. April 2019.
- Drahtflammspritzen. Oerlikon, abgerufen am 12. April 2019.
- Lexikon - Fachbegriffe aus dem Bausektor: Verzinken (Memento des Originals vom 10. April 2017 im Internet Archive) Info: Der Archivlink wurde automatisch eingesetzt und noch nicht geprüft. Bitte prüfe Original- und Archivlink gemäß Anleitung und entferne dann diesen Hinweis. , LKG - Ingenieurbüro für Bautechnik
- Zeitschrift "Oldtimer Markt", Sonderheft Oldtimer Praxis Nr. 62 - Rostschutz, S. 95, Oktober 2018
- Siehe hierzu auch: Rost#Abbau der Potenzialdifferenz in Lokalelementen
- Tabelle "Nutzungsdauern von Bauteilen zur Lebenzyklusanalyse des Bewertungssystems Nachhaltiges Bauen (BNB)", deutsches Bundesministerium für Verkehr, Bau und Stadtentwicklung
- Zeitschrift "Oldtimer Markt", Sonderheft Oldtimer Praxis Nr. 62 - Rostschutz, S. 92 f., Oktober 2018
- Siehe hierzu auch: Rost#Abbau der Potenzialdifferenz in Lokalelementen
- Zeitschrift "Oldtimer Markt", Sonderheft Oldtimer Praxis Nr. 62 - Rostschutz, S. 94, Oktober 2018
- Gerhard Jokisch, Bruno Schütze, Werner Städtler in: Autorenkollektiv: Das Grundwissen des Ingenieurs. VEB Fachbuchverlag Leipzig, 1968, S. 991–1163, dort S. 1048.
- Zeitschrift "Oldtimer Markt", Sonderheft Oldtimer Praxis Nr. 62 - Rostschutz, S. 94, Oktober 2018
- Mit einem wenige Quadratzentimer großen Stück Zink, einer Spannung von 12 Volt und einem Strom von wenigstens 20 Ampere lassen sich innerhalb einiger Minuten Schichtdicken von mehreren Mikrometern erreichen. Siehe: Zeitschrift "Oldtimer Markt", Sonderheft Oldtimer Praxis Nr. 62 - Rostschutz, S. 95 ff., Oktober 2018
- Stéphane Itasse: Verzinkten Stahl schweißen. Maschinenmarkt. 11. August 2017.
- Arbeitsblatt Feuerverzinken G.2 NASSBESCHICHTEN VON FEUERVERZINKTEM STAHL. In: Arbeitsblatt Feuerverzinken. Abgerufen am 18. Mai 2020.
- Arbeitsblatt Feuerverzinken G.3 PULVERBESCHICHTEN VON FEUERVERZINKTEM STAHL. In: Arbeitsblatt Feuerverzinken. Abgerufen am 18. Mai 2020.
- Informationen zu Duplex-Systemen, Industrieverband Feuerverzinken; abgerufen im Oktober 2016
- E.4 Fachgerechte Ausbesserung. In: Arbeitsblätter Feuerverzinken. Institut Feuerverzinken, abgerufen am 26. Mai 2020.