Extrusion (Verfahrenstechnik)
Bei der Extrusion (von lateinisch extrudere ‚hinausstoßen‘, ‚-treiben‘) werden plastisch verformbare bis dickflüssige Massen unter Druck kontinuierlich aus einer formgebenden Öffnung (auch Kalibrierung, Düse, Matrize oder Mundstück genannt) herausgepresst. Die geformte Masse wird als Extrudat bezeichnet und härtet in der Regel beim Austritt aus der Öffnung des Werkzeugs durch Abkühlung oder chemische Reaktion aus. Durch Extrusion können Profile mit komplexen Querschnitten in beliebiger Länge erstellt werden.
Der Querschnitt des so entstandenen Profils mit dem Querschnitt der Öffnung des Werkzeugs in theoretisch beliebiger Länge.
Die Extrusion von keramischen Massen wird auch als Strangpressen bezeichnet. Ein ähnliches Verfahren ist das Strangpressen von Metallen.
Verfahren
Produkte der Extrusionstechnik finden sich in zahlreichen Anwendungsgebieten wieder. Abhängig von den Eigenschaften des zu verarbeitenden Materials, der Druckerzeugung und dem gewünschten Ergebnis lassen sich unterschiedliche Verfahren unterscheiden. Bei der Kaltextrusion wird mit niedrigen Drücken, Temperaturen und Scherkräften, bei der Warmextrusion mit höheren Temperaturen und bei der Heißextrusion sowohl mit hohen Drücken als auch hohen Temperaturen gearbeitet. Das Zusammenführen von artgleichen oder fremdartigen Materialien vor dem Verlassen der Profildüse wird auch Koextrusion genannt.
Extruder
Der Extruder wurde schon vor 1900 für die Kautschukindustrie eingesetzt. Nach einiger Zeit entdeckte auch die Lebensmittelindustrie vielseitige Verwendungsmöglichkeiten. Durch den großen Boom der Kunststoffindustrie Mitte des letzten Jahrhunderts hat sich der Extruder zudem als wichtiges verfahrenstechnisches Element in der kontinuierlichen Produktion von thermoplastischen Kunststoffartikeln etabliert.
Grundsätzlich können Extruder in zwei Prozessprinzipien unterteilt werden: Verarbeitungs- und Aufbereitungsextruder. Verarbeitungsextruder dienen hauptsächlich der Formgebung (in der Regel Kolben- und Einwellenextruder), während Aufbereitungsextruder der chemischen und physikalischen Modifizierung (reagieren, mischen, entgasen etc.) von Stoffen dienen (gleichlaufender dichtkämmender Doppelwellenextruder, Buss-Ko-Kneter etc.).
Je nach Produkt wird mit Drücken von 10 bis zu 1500 bar und Temperaturen von 60 bis 300 °C gearbeitet.
Kolbenextruder
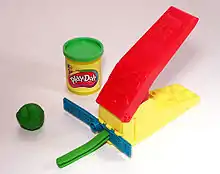
Bei dieser Bauform wird der Druck mittels eines Kolbens erzeugt (engl. ram extrusion). Kolbenextruder werden vor allem eingesetzt, wenn sich das zu verarbeitende Material nicht mittels Schneckenextrudern verarbeiten lässt oder ein häufiger Produktwechsel durchgeführt werden soll, bei dem es im Schneckenextruder zur Vermischung der Rohstoffe käme.
Kolbenextruder werden häufig für keramische Materialien verwendet. Schneckenextruder haben in der Keramikproduktion den Nachteil, dass sich die Schnecken durch die abrasive Keramikmasse schnell abnutzen. Auch Materialien, die empfindlich auf Scherkräfte reagieren, sind in Kolbenextrudern besser zu verarbeiten. Kolbenextruder können schnell gereinigt werden und die Flächen, die in Kontakt mit der Extrusionsmasse treten, sind kleiner als bei Schneckenextrudern.
Durch Verwendung von entsprechend großen Zylindern kann semi-kontinuierlich und durch den parallelen Einsatz von zwei Kolbenextrudern kann ganz kontinuierlich produziert werden.
Schneckenextruder
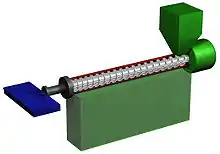
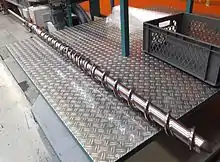
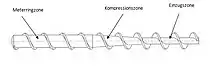
Meteringzone – Kompressionszone – Einzugszone
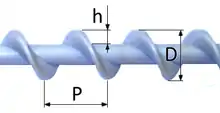
Bei dieser Bauform wird der Druck mittels einer Extruderschnecke, auch Schnecke genannt, erzeugt. Sie steckt in dem sogenannten Schneckenzylinder, dessen Nenndurchmesser nahezu gleich dem Außendurchmesser der Schnecke ist. Am vorderen Ende des Schneckenzylinders befindet sich die formgebende Auslassöffnung. Am hinteren Ende des Zylinders befindet sich der Antrieb, in den meisten Fällen ein Elektromotor mit Getriebeeinheit, der für die Rotation der Schnecke sorgt.
Die Längenbezeichnungen von Schneckenextrudern wird in 25D, 30D, 40D etc. angegeben, was heißt, dass das 25-fache (30-fache, 40-fache etc.) des Schneckendurchmessers die Länge ergibt. Zur Ausstoßsteigerung werden Einschneckenextruder, sogenannte Schnellläufer, mit Drehzahlen von bis zu 1500 Umdrehungen pro Minute hergestellt.
Die zu verarbeitenden Materialien werden der Schnecke meist kontinuierlich über einen Trichter von oben zugeführt. Entscheidend ist bei mehreren Komponenten die exakte und reproduzierbare Dosierung. Man unterscheidet in Abhängigkeit vom Regelungsmechanismus zwischen gravimetrischen und volumetrischen Dosierungen. Weitere Komponenten können über Seitenbeschickung, Nadelventile etc. in den Schneckenzylinder eingebracht werden. In der Kunststoffverarbeitung sind dies z. B. sogenannte Masterbatches oder Flüssigfarben (Färbemittel), Verstärkungsfasern, Alterungsschutzmittel oder Weichmacher. Mit entsprechender Dosiertechnik besteht die Möglichkeit, Flüssigfarben stromabwärts in die Kunststoffschmelze zu injizieren. Somit muss bei Farbwechseln nur noch ein Teilbereich der Produktionslinie gespült werden, was eine erhebliche Material- und Zeitersparnis bedeutet.[1]
Die Extruderschnecke selbst wird im Allgemeinen in drei Zonen aufgeteilt, die unterschiedliche Aufgaben übernehmen. Im hinteren Bereich des Schneckenzylinders befindet sich die sogenannte Einzugszone. In dieser wird das zu extrudierende Material, das z. B. als Feststoff in Form von Granulat oder Pulver vorliegt, über einen Trichter eingespeist („Fütterung“) und gegebenenfalls aufgeschmolzen (bei Thermoplasten). Durch die Drehung der Schnecke wird das Material weiterbefördert. An diese schließt sich die Kompressionszone an, in der das Material durch die verringerte Gangtiefe der Schnecke weiterverdichtet und damit der für den Austrag im Werkzeug notwendige Druck aufgebaut wird. Abschließend sorgt die Austragszone bzw. Meteringzone für einen homogenen Materialstrom zum Werkzeug hin.
Es gibt Extruder mit einer, zwei oder mehreren Schneckenwellen. Die Förderung und der Druckaufbau werden beim Einschnecken- und (gleichläufigen) Doppelschneckenextruder durch die Friktion der mit der Schnecke rotierenden Masse an der stehenden Gehäusewand (Zylinder) bewirkt – man spricht in diesem Zusammenhang von Friktionsförderung. Die so in der Rotation zurückbleibende Masse wird von den wendelförmigen Schneckengängen zur Auslassdüse geschoben. Beim gegenläufigen Doppelschneckenextruder überwiegt das Prinzip der Zwangsförderung.
Die Form bzw. Bauart der Schnecken bestimmt die Eigenschaften.
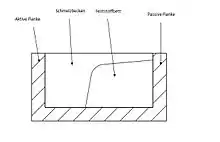
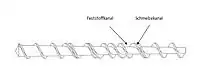
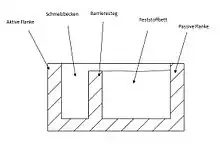
- Einschneckenextruder sind kostengünstig, durchmischen aber nicht so gut. Wichtig bei der Auslegung einer Schnecke ist der voraussichtliche Füllgrad über die Prozesslänge. Er wird maßgeblich durch die Steigung P der Schnecke und die Gangtiefe h beeinflusst. Mit größer werdender Steigung nimmt hierbei der Füllgrad immer weiter zu, so dass der Druck nach Erreichen des vollgefüllten Zustands weiter zunimmt. Auf diese Weise wird der zum Durchströmen des Werkzeugs notwendige Druck aufgebaut.
- Barriereschnecke mit zusätzlichem Steg zu Beginn der Barrierezone, dessen Höhe geringer ist als die des Hauptstegs. Dieser Steg wird als Barrieresteg bezeichnet. Durch den Barrieresteg wird der Schneckenkanal in Schmelze und Feststoffkanal aufgeteilt. Die Spaltweite ist so klein, dass keine Feststoffteilchen über den Steg in den dahinterliegenden Schmelzekanal gelangen können. Durch die Trennung von Schmelze und Festkörper ist ein besserer Aufschmelzvorgang gewährleistet, da keine Feststoffinseln in der Schmelze herumschwimmen können.
In der Austragszone einer Barriereschnecke sind Homogenisierelemente wie Scher- und Mischteile vorhanden.
Gegen Ende der Barrierezone wird der Feststoffkanal kleiner und der Schmelzekanal größer. Dadurch werden die verbleibenden Festkörper durch Dissipation gezwungen, auch in Schmelze zu gehen.
- Barriereschnecke mit zusätzlichem Steg zu Beginn der Barrierezone, dessen Höhe geringer ist als die des Hauptstegs. Dieser Steg wird als Barrieresteg bezeichnet. Durch den Barrieresteg wird der Schneckenkanal in Schmelze und Feststoffkanal aufgeteilt. Die Spaltweite ist so klein, dass keine Feststoffteilchen über den Steg in den dahinterliegenden Schmelzekanal gelangen können. Durch die Trennung von Schmelze und Festkörper ist ein besserer Aufschmelzvorgang gewährleistet, da keine Feststoffinseln in der Schmelze herumschwimmen können.
- Doppelschneckenextruder: Beim gleichläufigen Doppelschneckenextruder rotieren die Schnecken in gleicher Drehrichtung, beim gegenläufigen in entgegengesetzter Drehrichtung. Die Schnecken können parallel oder konisch angeordnet sein. Da das Spiel zwischen den Schnecken besonders eng und die Neigung zu Verschleiß entsprechend höher ist, müssen sie höchste Qualitätskriterien in Bezug auf Festigkeiten und Härten erfüllen.
- Vielwellenextruder
Weitere Bauformen
- Kaskadenextruder
- Planetwalzenextruder
- Ringextruder
- Durch Strangpressen hergestellte Konstruktionsprofile aus Aluminium
- Durch Holzextrusion hergestelltes WPC-Profil
Prozessmesstechnik in der Extrusion
Da in Extrusion und Compoundierung sehr ähnliche Maschinenkonzepte (Extruder) eingesetzt werden, sind hierfür dieselben Verfahren wie in der Prozessmesstechnik in der Compoundierung verfügbar.
Nach der Extrusion kann am Bauteil noch in der Produktionslinie die Ermittlung weiterer Qualitätsparameter erfolgen:
- Vermessung der Dimensionen des Bauteils z. B. mit Lichtvorhängen
- Farbmessung am Extrudat[2]
- Qualitätskontrolle mit Kamerasystemen
Anwendungen und Produkte
Produkte der Extrusionstechnik finden sich in zahlreichen Anwendungsgebieten wieder, z. B. in Bauindustrie (Hoch- und Tiefbau), Automobilindustrie, Luftfahrtindustrie, Medizintechnik, Möbelindustrie (vor allem Küchen- oder Büromöbel), Messebau, Verpackungen, Agrareinsatz, Schlauchanwendungen und Granulierung.
Beispiele für Produkte, die durch Extrusion erzeugt werden, sind:
- Rohre, Stäbe (Halbzeug)
- Profile wie Fensterrahmen, Kabelkanäle oder Dichtungen
- Ummantelungen, wie z. B. für Elektrokabel
- Schläuche
- Platten mittels Breitschlitzdüse, die nach der Fertigung bei Bedarf durch Thermoformung umgeformt werden können.
- Folien (mittels Blaskopf oder Breitschlitzdüse und nachgeschaltetem Kalander)
- Laufflächen von Autoreifen
- Kleinere Autoteile (Innentürverkleidungen, Rückspiegelfassungen)
- Wischgummi beim Scheibenwischer
- Fahrradfelgen
- Keil- und Zahnriemen durch Zuführen von Kupferdraht durch den Extruderkopf
- Türdichtungen
- Extrudierte Polystyrol-Hartschaumplatten (XPS)
- Blei- und Buntstifte aus Holz-Kunststoff-Verbundwerkstoffen
- Keramik, Spaltklinker, Lochziegel und im Gießerei-Formenbau
- Vorprodukte bei der Seifenherstellung
- Stearinkerzen
- Nudel-Teigwaren, Knabbergebäck, Kekse, Formfleisch
- Herstellung von Chemiefasern
- Kühlkörper
- Filament (Recycling für Fused Deposition Modeling)
Kunststoffe
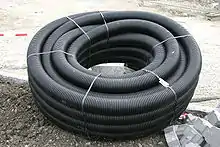
Kunststoff und Kunststoffgranulate, auch Compound-Granulate
Durch Extrusion können beispielsweise nahtlose Platten, Rohre und Profile mit über der Länge konstantem Querschnitt hergestellt werden. Auch Kunststoffbehälter wie Flaschen, Dosen oder Kraftstofftanks werden durch Extrusion hergestellt. Ein extrudierter Schlauch wird von einer Form umschlossen und mittels Druckluft an die Werkzeugwand geblasen. In diesem Fall spricht man von Extrusionsblasformen.
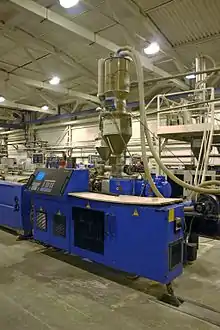
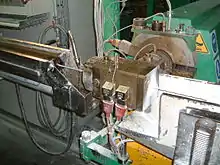
Neben der Lebensmittelindustrie ist die Kunststoffindustrie ein Hauptabnehmer für Extruder. Hier werden zusätzlich zum oben genannten Aufbau Heizbänder am Schneckenzylinder befestigt, die das eingefüllte Kunststoffgranulat oder -pulver aufschmelzen (plastifizieren). Extruder müssen nicht nur beheizt werden. Einige verfahrenstechnische Aufgaben machen auch das Kühlen des plastifizierten Kunststoffes notwendig. Dies erfolgt entweder durch Kühlgebläse oder in den Zylinder des Extruders eingearbeitete Kühlkanäle, die mit einem Kühlmedium, z. B. unter Druck stehendem Wasser, durchströmt werden. Je nach Art des verwendeten Kunststoffes ist weitere Ausrüstung nötig, zum Beispiel zum Abpumpen von Gasen, die Blasen im Endprodukt hinterlassen würden. Das verwendete Material ist auch maßgeblich bestimmend für die Form der Schnecke. So kann die Steigung, die Anzahl der Windungen und die Breite der Schneckengänge je nach Kunststoff vollkommen unterschiedlich sein.
Dazu wird der Kunststoff bzw. das Extrudat zunächst durch einen Extruder (auch Schneckenpresse genannt) mittels Heizung und innerer Reibung aufgeschmolzen und homogenisiert. Weiterhin wird im Extruder der für das Durchfließen der Düse notwendige Druck aufgebaut. Nach dem Austreten aus der Düse erstarrt der Kunststoff meist in einer wassergekühlten Kalibrierung. Das Anlegen von Vakuum bewirkt, dass sich das Profil an die Kaliberwand anpresst und somit die Formgebung abgeschlossen wird. Im Anschluss darauf folgt oft noch eine Kühlstrecke in Form eines gekühlten Wasserbades. Der Querschnitt des so entstehenden geometrischen Körpers entspricht der verwendeten Düse oder Kalibrierung. Die möglichen Fertigungstoleranzen bewegen sich im Bereich von ±0,05 mm. Ähnliche Urformverfahren zur Heißumformung von Metallen sind das Strangpressen und das Stranggießen.
Rohr- und Profilextrusion
Bei der Rohr- oder Profilextrusion muss das extrudierte Material danach in einem Kalibriertisch in Form gehalten werden, bis es abgekühlt ist. Sonst sackt es in sich zusammen und verformt sich. Herzstück des Kalibriertisches ist die Kalibrierhülse, die primär dem Formerhalt des Rohrs oder Profils dient. Sie ist direkt hinter der Düse des Extruders angebracht. Sie besteht aus einem Metallblock, der innen exakt den Querschnitt des Rohrs oder Profils aufweist. Das extrudierte Rohr oder Profil läuft also durch die Kalibrierhülse. Für den Formerhalt des Profils wird im Inneren der Hülse mit Stützluft oder Vakuum gearbeitet. Vakuumöffnungen an unterschiedlichen Stellen in der Hülse entlang des Querschnitts saugen das Profil an die Innenwände, Wasser um- und durchspült dabei das Profil, bis es abgekühlt ist. Die Art und Form des Kalibriertisches richtet sich dabei sehr nach dem zu extrudierenden Kunststoffprodukt. Gerade bei komplizierten Profilen, wie Fensterrahmen, ist hier viel Know-how gefragt, damit das Profil nicht beim Abkühlen in sich selbst zusammensackt und verformt wird.
Ein Abzug hinter dem Kalibriertisch sorgt dabei für den Transport des Rohrs oder Profils. Dabei handelt es sich um zwei oder mehrere Raupenketten, deren Laufflächen gegeneinander gedrückt werden. Zwischen diese Laufflächen wird dann das extrudierte Rohr oder Profil gelegt und durch die Bewegung der Ketten unter Zug gesetzt. Der Abzug zieht also das extrudierte Kunststoffprodukt aus dem Extruder heraus und durch den Kalibriertisch. Die Geschwindigkeit des Abzugs bestimmt dabei zusammen mit der Geschwindigkeit des Extruders maßgeblich die Laufgeschwindigkeit des Profils oder Rohrs.
Hinter dem Abzug befindet sich meist noch eine Schneideanlage, die das bisher endlose Rohr oder Profil entsprechend ablängt. Ein Sammeltisch sammelt die abgelängten Rohre oder Profile. Der Bediener der Maschine kann die fertigen Rohre oder Profile hier bündeln und abpacken.
Die Kombination von Extruder, Kalibriertisch, Abzug, Schneideanlage und Sammeltisch wird „Extrusionslinie“ bezeichnet, weil die einzelnen Maschinen dem Fertigungsablauf entsprechend in einer Achse hintereinanderstehen.
Folienextrusion
Extruder sind auch Bestandteil von Blasfolienanlagen. Hier wird das plastifizierte Material nicht in die Form eines Profils gebracht, sondern zu einer hauchdünnen Folienblase aufgeblasen. Hierfür wird die Schmelze in vertikale Richtung umgelenkt und durch Wendelverteilerwerkzeuge auf die Form eines Schlauchs gebracht. Durch ringförmige Anordnung von bis zu neun Extrudern und Zusammenführung der einzelnen Schmelzströme im Wendelverteilerwerkzeug können auf diese Art und Weise mehrschichtige Folien produziert werden. Um den austretenden Schmelzeschlauch auf die heute üblichen Dicken von mehreren hundertstel Millimeter zu bringen, werden die Schläuche anschließend in Längs- und Querrichtung verstreckt. Dies geschieht durch zentrisches Einblasen von Luft, die den Schlauch nicht nur mechanisch verstreckt, sondern auch abkühlt und damit in seiner Form fixiert. Der Folienschlauch wird durch einen Korb kalibriert, umgelegt und aufgewickelt.
Verwendete Kunststoffe und Verbundwerkstoffe
Die Materialien die auf Extrudern verarbeitet werden können gehören zur Gruppe der Thermoplaste, wie zum Beispiel:
- PVC: Polyvinylchlorid
- PE: Polyethylene wie HDPE und LDPE
- PP: Polypropylen
- PA: Polyamid
- ABS: Acrylnitril-Butadien-Styrol-Copolymerisat
- PC: Polycarbonat
- SB: Styrolbutadien
- PMMA: Polymethylmethacrylat
- PUR: Polyurethan
- PET: Polyethylenterephthalat
- PSU: Polysulfon
und innovative Biowerkstoffe wie
sowie Verbundwerkstoffe wie
- WPC: Wood-Plastic-Composite, siehe auch Holzextrusion
Futtermittel und Lebensmittel
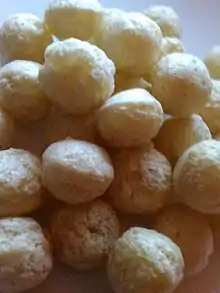
In der Futtermittel- und Lebensmittelindustrie verwendete Rohstoffe können im Rahmen der Extrusion vorkonditioniert werden, etwa durch Erhitzung und Bedampfung, wodurch z. B. Getreidebestandteile aufgeschlossen und damit verdaulicher werden.
Folgende Produkte werden in Extrusion
- Kaugummi und Kaubonbons
- Teigwaren (Nudeln)
- Viele Knabberprodukte:
- Kartoffelerzeugnisse
- Erdnussflips
- Hirsebällchen
- Reiscrispies
- Schokoflocken
- Karamell
- Brot (sog. Knusperbrot)
- Manche Frühstücksflocken
- Textured Vegetable Proteine (TVP) (z. B. Texturiertes Soja, siehe auch: Fleischersatz)
- Trockene und halbtrockene Futterstücke, sog. Kibbles, als Nahrung u. a. für Hunde, Katzen, Fische und Schweine. Durch die Bearbeitung durch den Expander wird das Futter für die Tiere leichter verdaulich und die Futterverwertung erhöht. Außerdem wird das Futter durch die hohen Temperaturen entkeimt.
Beim Heißextrudieren wird ein recht wasserhaltiger Teig (Masse) unter enormem Druck in einer Verdichtungsschnecke (ähnlich einem Fleischwolf) erhitzt. An der Austrittsdüse fällt der Druck ab, so dass das Wasser verdampft und das Produkt stark gelockert wird. Dabei kann die bereits verkleisterte Stärke die Gashaltung (ähnlich wie bei einer Brandmasse) unterstützen und zu festen Poren festhalten. Oft wird noch eine Trocknungs- oder Röststation nachgeschaltet. Typische Produkte sind Erdnussflips, Zwiebelringe und andere Knabberartikel. Aber auch einige Brotsorten (z. B. Flachbrot oder Brotchips) und Gebäck werden in diesem Verfahren produziert.[3][4]
Siehe auch
Literatur
- Hans-Josef Endres, Andrea Siebert-Raths: Technische Biopolymere. Hanser-Verlag, München 2009, ISBN 978-3-446-41683-3
- Helmut Greif, Andreas Limper, Gordon Fattmann, Stefan Seibel: Technologie der Extrusion. Carl Hanser Verlag, München 2004
- Johannes Wortberg, Dirk Kaczmarek: Kunststoff Maschinen Führer. 4. Auflage. Carl Hanser Verlag, München 2004
- T. Hochrein, I. Alig: Prozessmesstechnik in der Kunststoffaufbereitung. Vogel, Würzburg 2011, ISBN 978-3-8343-3117-5
Weblinks
Einzelnachweise
- Flüssigfarben und Additive - Vorteile - ROWASOL. Abgerufen am 18. Januar 2018.
- T. Hochrein, J. Botos, K. Kretschmer, P. Heidemeyer, B. Ulmer, T. Zentgraf, M. Bastian: Schneller und näher am Prozess. In: Kunststoffe, 2012, S. 9.
- Leitsätze für Brot und Kleingebäck, Stand 2021 (PDF; 859 kB) BMEL.
- Videos von Extrudern im Einsatz. Schaaf Technologie GmbH.