Wood-Plastic-Composite
Als Wood-Plastic-Composites (WPC, englisch für Holz-Kunststoff-Verbundwerkstoffe, auch engl. Wood(-fiber) Polymer Composites ‚Holz(faser)-Polymer-Verbundwerkstoffe‘) werden meist thermoplastisch verarbeitbare Verbundwerkstoffe bezeichnet, die aus unterschiedlichen Anteilen von Holz – typischerweise Holzmehl –, Kunststoffen und Additiven hergestellt werden. Verarbeitet werden sie meist mit modernen Verfahren der Kunststofftechnik wie Extrusion, Spritzgießen, Rotationsguss oder mittels Presstechniken, aber auch im Thermoformverfahren.[1]
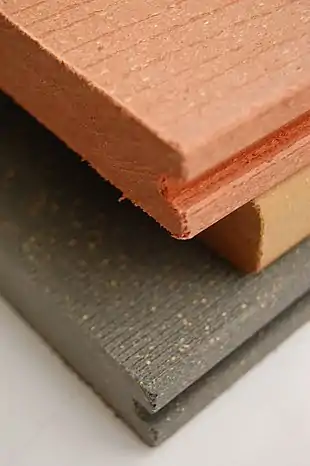
Neben WPC sind auch die Bezeichnungen Holz-Kunststoff-Verbundwerkstoff (HKV), Thermoplastischer Faserstoff (TPF) und Holzkunststoff oder High-Tech-Holz geläufig.[2]
Definition und Abgrenzung
International wird der Begriff WPC unterschiedlich gebraucht, auch im deutschsprachigen Raum.
Holz kann in den Materialien durch andere Pflanzenfasern (z. B. Kenaf, Jute oder Flachs) ersetzt werden, ohne die Materialeigenschaften erheblich zu verändern. Solche Produkte werden teilweise dennoch weiter als WPC bezeichnet.[3][4][5] Zur besseren Abgrenzung sollte in diesem Fall jedoch der Begriff naturfaserverstärkter Kunststoff verwendet werden.
WPC gehören innerhalb der Biowerkstoffe zur Untergruppe der Biokomposite.
Aufbau
Typischerweise bestehen WPC in Deutschland und Mitteleuropa aus einem Holzfaser- oder -mehlanteil von 50 % bis 90 % und einer Kunststoffmatrix aus Polypropylen (PP) oder weniger häufig aus Polyethylen (PE). Auf dem nordamerikanischen Markt dominieren WPC mit einem 50-prozentigen Polyethylen-Anteil. Mischungen mit anderen Kunststoffen und bio-basierten Kunststoffen sind technisch möglich, jedoch wenig verbreitet. Aufgrund der thermischen Empfindlichkeit des Holzes sind Verarbeitungstemperaturen nur von unter 200 °C möglich. Bei höheren Temperaturen kommt es zu thermischen Umwandlungen und Zersetzungen des Holzes.
Die Zugabe von Additiven optimiert spezielle Materialeigenschaften: Bindung zwischen Holz und Kunststoff, Fließfähigkeit, Brandschutz, Farbgestaltung und – besonders für Außenanwendungen – Witterungs- und UV-Schutz sowie Biozide zwecks Schädlingsbeständigkeit.
Eine neue Entwicklung auf diesem Sektor ist ein Gemisch aus Polyvinylchlorid (PVC) und Holzfasern zu je 50 %. WPC auf Basis thermoplastisch verarbeitbarer Duroplaste wie modifiziertes Melaminharz sind in der Entwicklung. Als Bamboo Plastic Composites (BPC) werden Verbundwerkstoffe bezeichnet, bei denen Holzfasern durch Bambusfasern ersetzt sind.
Eigenschaften
Bisherige Langzeitstudien[6] und Schadensfälle aus der Praxis haben gezeigt, dass WPC durch UV-Bestrahlung, Feuchte- und Temperatureinwirkung sowie Pilzbefall geschädigt werden können.
Vorteile
Vorteile des Werkstoffs gegenüber traditionellen Holzwerkstoffen wie Spanplatten oder Sperrholz sind die freie, 3-dimensionale Formbarkeit des Werkstoffs und die größere Feuchteresistenz. Gegenüber Vollkunststoffen bieten WPC eine höhere Steifigkeit und einen deutlich geringeren thermischen Ausdehnungskoeffizienten.
Nachteile
Gegenüber Schnittholz ist die Bruchfestigkeit vermindert. Formstücke können jedoch mit verstärkenden Einlagen versehen werden, um dies auszugleichen.
Die Wasseraufnahme von Formstücken ohne abschließende Beschichtung ist höher als bei massiven Kunststoffteilen oder Formstücken mit Folien- oder Fließbeschichtung.
Normung
Zurzeit wird eine neue Norm für WPC in Europa ausgearbeitet. Die Norm mit der Bezeichnung: „EN 15534 Verbundwerkstoffe aus cellulosehaltigen Materialien und Thermoplasten (üblicherweise Holz-Polymer-Werkstoffe (WPC) oder natürliche Faserverbundwerkstoffe (NFC) genannt)“ enthält mehrere Teile. Einige wurden bereits veröffentlicht:
DIN EN 15534-1:2014-04 Verbundwerkstoffe aus Cellulose haltigen Materialien und Thermoplasten (üblicherweise Holz-Polymer-Werkstoffe (WPC) oder natürliche Faserverbundwerkstoffe (NFC) genannt) - Teil 1: Prüfverfahren zur Beschreibung von Formmassen und Erzeugnissen
DIN EN 15534-4:2014-04 Verbundwerkstoffe aus Cellulose haltigen Materialien und Thermoplasten (üblicherweise Holz-Polymer-Werkstoffe (WPC) oder natürliche Faserverbundwerkstoffe (NFC) genannt) - Teil 4: Anforderungen an Profile und Platten für Bodenbeläge
DIN EN 15534-5:2014-04 Verbundwerkstoffe aus Cellulose haltigen Materialien und Thermoplasten (üblicherweise Holz-Polymer-Werkstoffe (WPC) oder natürliche Faserverbundwerkstoffe (NFC) genannt) - Teil 5: Anforderungen an Profile und Platten für Wandbekleidungen
Weitere Teile befinden sich noch im Aufbau.
Terrassendielen
Seit Ende 2007 gibt es unter dem Qualitätssiegel für Terrassendielen aus Holz-Polymer-Werkstoffen spezifizierte Qualitätskriterien für dieses Produkt. Das von der Qualitätsgemeinschaft Holzwerkstoffe e. V.[7] vergebene Qualitätszeichen berücksichtigt neben bestimmten Materialeigenschaften für Beständigkeit und Stabilität (Biegefestigkeit, Witterungsbeständigkeit, Formstabilität und Rutschfestigkeit) auch die Produktherkunft. Das Produkt ist für den Außenbereich vorgesehen. Für zertifizierte Produkte werden ausschließlich Holzfasern eingesetzt, die zu 100 % aus nachweislich FSC- oder PEFC-zertifizierter Forstwirtschaft stammen. Das eingearbeitete Polymer oder Polymergemisch muss zu 100 Prozent aus erstmals verarbeitetem Kunststoff bestehen.
Herstellung
WPC wird durch Verfahren verarbeitet, die in der Kunststoffproduktion gut eingeführt sind. Der weitaus größte Teil der WPC-Produktion erfolgt dabei mit Profilextrusion. Allerdings werden auch Spritzguss, Plattenpressen und Rotationsguss eingesetzt. In der Automobilindustrie sind Vliesformgebungsverfahren üblich.
Bei der Profilextrusion kann es ein Einstufen- oder Zweistufenprozess sein. Alle anderen Verfahren erfolgen in Zweistufen. Die erste Stufe des Zweistufenprozesses dient der Ermischung des WPC-Grundstoffs (oft als Granulat), in der zweiten Stufe wird die gewünschte Form erzeugt.
Einstufige Verfahren
Beim Einstufenprozess, auch Direktextrusion genannt, werden Holzpartikel und Kunststoffgranulat räumlich getrennt oder am gleichen Ort zur gleichen Zeit dem Extruder zugeführt. Der Kunststoff wird im Extruder vornehmlich durch Reibungswärme geschmolzen. Das Gemenge aus Holz und Kunststoff wird intensiv vermischt und durch das Werkzeug zu einem Profil extrudiert. Die Holzpartikel dürfen dabei eine Feuchtigkeitsobergrenze, die meist nicht über 8 % liegt, nicht überschreiten. Während des Extrusionsprozesses wird die Feuchtigkeit abgesaugt, so dass die WPC-Masse beim Verlassen des Werkzeugs Feuchtigkeiten von unter einem Prozent aufweist. Für Einstufenprozesse werden Planetwalzenextruder, konische, gegenläufige Doppelschneckenextruder eingesetzt, die die Aufgabe des intensiven Mischens und eines erforderlichen Druckaufbaus für das Extrudieren gleichzeitig erfüllen. Der wichtigste Einsatz nach der Menge sind Terrassendielen.
Zweistufige Verfahren
Im zweistufigen Extrusionsprozess wird das Mischen, gegebenenfalls auch das Trocknen, sowie das Kompaktierens in einem Aggregat und das Extrudieren durch ein Werkzeug in einem anderen Aggregat durchgeführt. Beide können direkt gekoppelt oder räumlich und zeitlich getrennt sein.
Zum Mischen und Kompaktieren werden gleichlaufende, parallele Doppelschneckenextruder (Compounder), Heiz-Kühl-Mischer oder Pelletierpressen sowie Mahlverfahren eingesetzt. Die damit erzeugten WPC-Zwischenprodukte können als Rohstoff für die Profilextrusion, für den Spritzguss oder die Plattenpresstechnik eingesetzt werden. Für den Rotationsguss sind nur frei fließende, kunststoffbeschichtete Holzpartikel geeignet.
- Compounder arbeiten kontinuierlich und erzeugen eine sehr homogene Mischung, können aber in der Regel nicht genügend Druck für eine Profilextrusion aufbauen. Der Druck verdichtet bereits die Holzmatrix. Die Verweilzeit im Compounder beträgt wenige Minuten. Die Mischung muss die Schmelztemperatur des Thermoplasten erreichen. Liegt diese Temperatur oberhalb von 160 °C, kann ein thermischer Abbau des Holzes beginnen. Compounder arbeiten kontinuierlich und es können geometrisch weitgehend einheitliche WPC-Pellets als Zwischenprodukt erzeugt werden.
Üblich ist es auch, das WPC-Compound in der Schmelzephase in ein Extrusionsaggregat, wie einen Einschneckenextruder oder eine Schmelzepumpe, zu geben. Die erzeugten Pellets erlauben eine einfache und gleichmäßige Dosierung mit den üblichen Dosiereinrichtungen. Extrudierte Pellets haben Feuchtigkeiten unter 1 % und erleichtern die Weiterverarbeitung.
- Heiz-Kühl-Mischer arbeiten diskontinuierlich. Im Heizmischer werden Holz- und Kunststoffpartikel gemischt und bis zum Schmelzpunkt des Thermoplasts aufgeheizt. Die Verweilzeiten im Heizmischer sind meist länger als im Compounder. Am Schmelzpunkt zieht der Thermoplast auf die Holzfasern auf und die WPC-Mischung wird in einen Kühlmischer überführt. Sie wird abgekühlt und grobe Agglomerate werden in kleinere Stücke aufgebrochen. Das WPC-Zwischenprodukt ist ein trockenes, nicht verdichtetes Granulat mit unregelmäßiger Kornform.
- In Pelletierpressen werden Holzpartikel und Kunststoffpartikel unter Druck miteinander kompaktiert. Beim Pressen durch eine Lochmatrize wird Reibungswärme erzeugt, um den Kunststoffanteil anzuschmelzen. Eine homogene Vermischung wie im Compounder oder Heiz-Kühlmischer findet nicht statt, so dass die so erzeugten Pellets nicht für alle Weiterverarbeitungsprozesse geeignet sind. Der Holzanteil wird durch den hohen Druck beim Pressen verdichtet.
- Bei Mahlverfahren werden Holz- und Kunststoffanteile gleichzeitig vermahlen. Bei einer Mahltemperatur die auf den Kunststoffanteil abgestimmt ist erfolgt eine Verbindung mit den Holzpartikeln. Je nach Mahlverfahren und Prozessführung können verklumpte oder einzelne, frei fließende Holzpartikel erzeugt werden.
Spritzguss
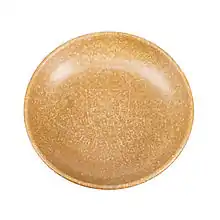
Beim Spritzgießen muss das Material homogen und problemfrei dosierbar sein, damit alle Teile der Schmelze eine gute Fließfähigkeit aufweisen. Eingesetzt werden vornehmlich compoundierte WPC-Pellets mit im Vergleich zu Extrusionsware geringem Holzgehalt. Sie werden in einem Plastifizierer aufgeschmolzen und in einem diskontinuierlichen Verfahren unter hohen Drücken bis zu 2400 bar „schussweise“ in eine Metallform gespritzt. Die WPC-Masse erstarrt beim Abkühlen. Der Spritzguss kann im „Injection Moulding Compounder“ auch in einem Arbeitsschritt erfolgen.
Aufgrund der Holzpartikelgeometrie und der geringen Schlagzähigkeit sind die Wandstärken im Spritzguss dicker ausgelegt als bei reinen Kunststoffgranulaten. Vorteilhaft ist die wesentlich höhere Wärmeformbeständigkeit, die der Masse bei höheren Temperaturen Steifigkeit verleiht. WPC-Formteile können daher bei höheren Temperaturen entformt werden.
Plattenpressen
Beim Plattenpressverfahren sind erste kontinuierlich arbeitende Pressen in der Erprobung. Das WPC-Vorprodukt wird auf ein Band zu einem Kuchen gestreut. Dieser wird ähnlich wie bei etablierten Holzwerkstoffverfahren in eine kontinuierliche Presse gefahren, dort verdichtet und aufgeheizt. Die WPC-Partikel werden angeschmolzen und verbinden sich zu einer Platte. Im folgenden Teil der Presse wird die Platte abgekühlt.
Rotationsguss
Im Rotationsgussverfahren werden Hohlkörper hergestellt. Es wird ein freifließendes Pulver dreidimensional in eine Hohlform getaumelt, während diese von außen erhitzt wird. Das Pulver sintert an der heißen Oberfläche an und bildet eine gleichmäßige Schicht, die der Innenkontur des Werkzeugs entspricht. 2005 wurde erstmals ein Sessel als WPC-Rotationsprodukt vorgestellt.
Geschichte und Marktentwicklung
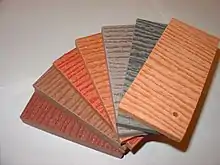
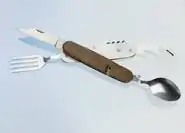
Ein Vorläufer der modernen WPC war Bois Durci, welches aus Holzmehl und verschiedenen tierischen Proteinen bestand. Bois Durci wurde durch die ersten modernen Kunststoffe abgelöst, speziell durch Bakelit, ein Komposit aus Phenol-Formaldehydharz und einem Füllmaterial, für das Holzmehl, Gesteinsmehl oder Textilfasern verwendet wurden. Das erste kommerzielle Produkt aus Bakelit mit Holzmehl war ein Steuerknüppel für Rolls-Royce aus dem Jahr 1916.[8]
Bereits Anfang der 1960er Jahre begannen Technologen in Deutschland und Frankreich auf der Basis von PVC und Cellulose, Altpapier und Holzschliff nach dem VINYPAL-Verfahren WPC zu entwickeln und herzustellen. Die Verfahren und Produkte hatten aber zu dieser Zeit noch keinen Markt in Europa und wurden als „Ersatzprodukte“ und nicht als neue Werkstoffe gewertet.
In den frühen 1970er Jahren entwickelte das italienische Unternehmen G.O.R. Applicazioni Speciali SpA Türinnenverkleidungen, Hutablagen und Dachverkleidungen aus einem Komposit mit 50 % Holz- und 50 % Harzmatrixanteil.[3]
Wood Plastic Composites entwickeln sich seit Anfang der 1990er Jahre rasant. Die USA waren das Ausgangsland für diesen Werkstoff.[9] heute zählen sie auch in Deutschland zu den erfolgreichsten neuen Biowerkstoffen.
Verwendung
Wood Plastic Composites werden vor allem im Baugewerbe, der Automobil- und Möbelindustrie verwendet: im Außenbereich für Bodenbeläge (Terrassen, Schwimmbäder,..) Fassaden und Möbel insbesondere als Ersatz für Tropenhölzer. Es sind bereits mehrere Stuhl- und Regalsysteme aus WPC auf dem Markt. Weitere Anwendungen sind Schreibgeräte, Urnen oder Haushaltsgeräte. Im technischen Bereich finden sie als Profile zur elektrischen Isolation Einsatz. In der europäischen Automobilindustrie werden WPC in Türinnenverkleidungen und Hutablagen eingesetzt. Thermoplastische Spritzguss-Erzeugnisse aus dem Biowerkstoff WPC sind bisher in Deutschland nur als „Nischenprodukte“ zu finden.
Wirtschaftliche Bedeutung
Weltweit wurden 2012 bereits mehr als 2,4 Mio. t WPC produziert, vor allem in Nordamerika (1,1 Mio. t), China (900.000 t) und Europa (260.000 t). In Europa ist Deutschland mit ca. 100.000 t der führende Produzent und zudem der führende Maschinenbauer.[10] Weitere führende WPC-produzierende Länder in Europa sind Österreich, Benelux und Skandinavien. Die wichtigsten Produzenten kommen aus der Holz- und Kunststoffbranche. Die neue WPC Marktstudie von Asta Eder Composites Consulting zeigt, dass die weltweite Verbreitung des Materials WPC sich fortsetzt. Der WPC Markt im südostasiatischen Markt wird in den kommenden Jahren weiteres Wachstum aufzeigen.
Literatur
- Asta Eder, Andreas Haider: Marktchancen für Wood Polymer Composites im deutschsprachigen Raum. In: Holztechnologie. 52 (2011), S. 44–49 (PDF; 1,1 MB)
- Asta Eder Composites Consulting: WPC Publications (Weiterführende Literatur zur WPC-Markt)
- Dominik Vogt, Michael Carus, Sven Ortmann, Christin Schmid, Christian Gahle (nova-Institut GmbH): Studie „Wood-Plastic-Composites“ Holz-Kunststoff-Verbundwerklstoffe. Schriftenreihe „Nachwachsende Rohstoffe“ Bd. 28. Landwirtschaftsverlag, Münster 2006, ISBN 3-7843-3397-4.
- Kristiina Oksman Niska, Mohini Sain (Hrsg.): Wood-polymer composites. Woodhead Publishing, Cambridge 2008, ISBN 978-1-84569-272-8.
- Hans Korte: Aus einem Guss. Technologien zur Herstellung von Holz-Kunststoff-Verbundwerkstoffen. In: HK Holz- und Kunststoffverarbeitung. 4/2006, S. 24–27.
- nova-Institut: Dritter Deutscher WPC-Kongress: Kongress Journal. Hürth 2009 (PDF; 1,8 MB)
Weblinks
Einzelnachweise
- Fachagentur Nachwachsende Rohstoffe e.V. (Hrsg.): Studie „Wood-Plastic-Composites“ Holz-Kunststoff-Verbundwerkstoffe. Band 28, Landwirtschaftsverlag Münster, 2006, ISBN 3-7843-3397-4.
- Merkblatt Terrassendielen von TBHolz (KOHLWEY Handel & Dienst-Leistungen) in Zusammenarbeit mit Gesamtverband Deutscher Holzhandel e.V., Wiesbaden, www.holzhandel.de, abgerufen im Januar 2016
- Geoff Pritchard: Two technologies merge: wood plastic composites. In: Plastics, Additives & Compounding. 6(4), Juli-August 2004, ISSN 1464-391X/04, S. 18–21
- Alireza Ashori: Wood-plastic composites as promising green-composites for automotive industries! Bioresource Technology 99 (11), 2008, ISSN 0960-8524, S. 4661–4667.
- Anatole A. Klyosov: Wood-plastic composites. John Wiley & Sons, 2007, ISBN 978-0-470-14891-4, S. 75.
- Nicole Stark, Laurent Matuana: Ultraviolet Weathering of Photostabilized Wood-Flour-Filled High-Density Polyethylene Composites. Michigan 2003.
- Prüfbestimmungen (Seite nicht mehr abrufbar, Suche in Webarchiven) Info: Der Link wurde automatisch als defekt markiert. Bitte prüfe den Link gemäß Anleitung und entferne dann diesen Hinweis. (PDF; 547 kB)
- Craig M. Clemons, Daniel F. Caulfield: Wood Flour. In: Marino Xanthos (Hrsg.): Functional fillers for plastics. Wiley-VCH, Weinheim 2005, ISBN 3-527-31054-1, S. 249.
- Hans Korte: Aus einem Guss. Technologien zur Herstellung von Holz-Kunststoff-Verbundwerkstoffen. In: HK Holz- und Kunststoffverarbeitung. 4/2006, S. 24–27.
- nova-Institut: Dritter Deutscher WPC-Kongress: Wachstumsmarkt WPC. (Seite nicht mehr abrufbar, Suche in Webarchiven) Info: Der Link wurde automatisch als defekt markiert. Bitte prüfe den Link gemäß Anleitung und entferne dann diesen Hinweis. In: www.nachwachsende-rohstoffe.info vom 4. Dezember 2009.