Holzextrusion
Die Holzextrusion ist ein kunststofftechnisches Verfahren (Extrusion), mit dem unter Verwendung von Holz und Kunststoffen in einem kontinuierlichen Verfahren Wood-Plastic-Composites hergestellt werden. Dazu werden die eingesetzten Compound-Materialien zunächst in einem Extruder gemischt, aufgeschmolzen und homogenisiert. Weiterhin wird im Extruder der für das Durchfließen der Spritzdüse notwendige Druck aufgebaut. Nach dem Austreten aus der Düse erstarrt das Material in der gewünschten Form und kann weiterbearbeitet werden.
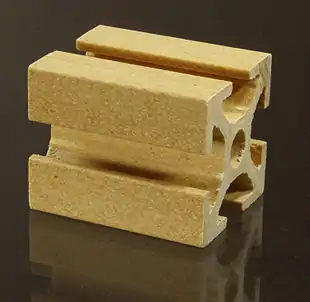
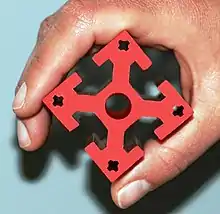
Compounds
Es lassen sich Compoundmischungen aus Holz und unterschiedlichen Thermoplasten extrudieren. Insbesondere eingesetzt werden derzeit Polyethylen und Polypropylen; für spezifische Anwendungsbereiche finden als Kunststoffe auch weiterhin Polyvinylchlorid, aber auch Polystyrol Verwendung. Wichtig ist, dass die eingesetzten Polymere einen relativ niedrigen Schmelzbereich haben, damit es während der Extrusion zu keiner thermischen Schädigung des Holzes kommt. Je nach Anwendung im Innen- oder Außenbereich wird heute in der Regel ein Holzanteil zwischen 25 und 85 % gewählt. Zunehmend ist Holz der tragende Werkstoff mit geringen Anteilen an Kunststoffen als Bindemittel.
Holz wird bei der Holzextrusion in sehr unterschiedlichen Formen eingesetzt: Von Holzmehl über Holzfasern mit unterschiedlichen Geometrien bis hin zu Pellets. Pellets sind zwar leicht förder- und dosierbar, werden aber wegen des nicht konstanten Kompaktierungsgrades im Extruder unterschiedlich gut „aufgeschlossen“, so dass schwankende Endproduktqualitäten die Folge sind. Auch Holzmehle können trotz der ebenfalls guten Dosierbarkeit für bestimmte Anwendungen technologisch nachteilig sein, da sie kaum Matrix verstärkende Eigenschaften aufweisen. Bei der Holzextrusion können unterschiedliche Holzarten (z. B. Fichte, Kiefer, Buche) verwendet werden.
Als Zusatzstoffe werden bei der Holzextrusion – je nach Anwendungsfall – fast alle in der Kunststoffindustrie bekannten Additive wie UV-Stabilisatoren, Antioxidantien, Gleitmittel, Schlagzähmodifizierer, Flammschutzmittel oder Hitzestabilisatoren eingesetzt. Einen Spezialfall stellen die sogenannten Coupling Agents dar, mit denen die Holzfaser-Kunststoffmatrix-Haftung verbessert werden soll. Diese bestehen im Regelfall aus einer polaren Gruppe und aus einem langen, unpolaren Kettenrest (z. B. Maleinsäureanhydrid gepfropft auf Polypropylen).
Extruder-Typen
Vier verschiedene Extruder-Typen werden für die Holzextrusion eingesetzt: der Planetwalzenextruder, der konische Doppelschneckenextruder, der parallele Doppelschneckenextruder und der Einschneckenextruder. Die Größe der extrudierten Holzpartikel wird vorwiegend durch den Extruder (z. B. Zylindergröße, Schneckengeometrie) bestimmt. In einem gegebenen Extruder wird die Partikelgröße im Endprodukt ein bestimmtes kritisches Maß nicht übersteigen; werden längere Fasern und Späne eingesetzt, werden diese im Extruder zermahlen.
Die Temperaturempfindlichkeit der Holzkomponente stellt eine große Herausforderung dar, wenn Standard-Extrusions- und Spritzgießmaschinen verwendet werden. Zum Beispiel haben die Verfahrensteile des Planetwalzenextruders eine mindestens fünfmal größere Abtauschfläche als ein konventioneller Doppelschneckenextruder, was ein schonendes Mischen des Materials erlaubt. Dieses trägt zum einen auch zu der genauesten Temperaturführung bei, verglichen mit anderen Compoundiersystemen. Zum anderen bietet das System ein großes Verarbeitungsfenster von verschiedenen Thermoplastmaterialien und erlaubt einen fast problemlosen Materialwechsel. Es handelt sich um ein modulares System mit bis zu acht Modulen, abhängig vom Ausstoß und Anwendung.
Der konische Doppelschneckenextruder mit seinem großen Durchmesser im Einzugsbereich und der kontinuierlichen Kompression durch die konischen Schnecken wird für hochgefüllte Systeme bevorzugt, weil sich damit sehr hohe Materialverdichtungen im Extruder bewerkstelligen lassen. Die relativ kurze Bauweise garantiert eine kurze Verweilzeit der Schmelze im Extruder und reduziert somit die thermische Belastung der Holzzusätze. In den letzten Jahren sind diese Werkzeuge an die Besonderheiten in der Holzextrusion angepasst wurden.
Einschneckenextruder finden überwiegend dort Verwendung, wo als Rohstoff fertige Granulate eingesetzt werden. Zwar ist die Mischwirkung im Vergleich zu den Doppelschneckenextrudern wesentlich schlechter; das kann aber durch die deutlich niedrigeren Kosten unter bestimmten Rahmenbedingungen kompensiert werden.
Verfahrensschritte
Die Holzextrusion umfasst mit der Vorbehandlung und der Nachbehandlung des Produktes die folgenden Prozessschritte:
- Eventuell Vortrocknen der Holzfasern
- Komprimieren und Plastifizieren im Extruder
- Entspannen und Entgasen (entweder atmosphärisch oder mit Hilfe von Vakuum)
- Weiteres Plastifizieren und Mischen
- Formgebung durch die Extrusionsdüse bei 100 bis 300 bar
- Kalibrieren, Kühlen, Ablängen
- Oberflächenbehandlung
Bei der Direktextrusion finden die Schritte 2 bis 5 im Extruder statt. Alternativ dazu wird das compoundierte Material zunächst granuliert und erst in einem Weiteren Schritt erneut erhitzt und zur Formgebung extrudiert. Damit wird die zeitliche und räumliche Trennung der Produktionsschritte Compoundierung und Formgebung ermöglicht, für die temperaturempfindlichen Holzfasern ist die zweimalige Erhitzung jedoch von Nachteil.
Vorteile
Wenn eine sehr gute Formbarkeit der Artikel gefordert ist und die außerordentlichen Gestaltungsmöglichkeiten der Kunststoffverarbeitung benötigt werden, nutzt man das Verfahren der Holzextrusion. Ebenso, wenn das Produkt eine hohe Steifigkeit und besondere Festigkeit aufweisen muss bzw. eine hohe Solidität zu günstigen Kosten erreicht werden soll.
Alternativen
Die Holzextrusion ist das vorherrschende Verfahren bei der Produktion von WPC-Produkten. Mit diesem Verfahren können jedoch lediglich lineare Profile hergestellt werden. Erweiterte Möglichkeiten der Formgebung bietet unter anderem der Naturfaser-Spritzguss.
Literatur
- Stadlbauer u. a. Wood Plastic Composites Berichte aus Energie- und Umweltforschung 68/2006 (pdf)
- Dominik Vogt, Michael Karus, Sven Ortmann, Christin Schmidt, Christian Gahle, 2006: Studie "Wood-Plastic-Composites" Holz-Kunststoff-Verbundwerkstoffe. Schriftenreihe "Nachwachsende Rohstoffe", Band 28. Landwirtschaftsverlag, Münster. ISBN 3-7843-3397-4