Kalibrierung (Extrusion)
Die Kalibrierung ist eine dem Extruder nachgeschaltete Einheit, um das extrudierte Material auf die späteren Produktmaße zu fixieren. Dabei wird das noch schmelzeflüssige Material auf eine Temperatur abgekühlt, bei der eine nachträgliche Verformung nicht mehr möglich ist. Die vollständige Abkühlung erfolgt in der nachgehenden Kühlstrecke.
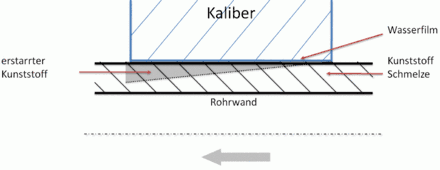
Unterscheidung Trocken- und Nasskalibrierung:
Die Nasskalibrierung kommt in erster Linie wegen der Reduzierung der Reibkräfte zum Einsatz, ist jedoch nur bei drehsymmetrischen Teilen (z. B. Rohre) möglich, da sich der Wasserfilm nur bei solchen Teilen gleichmäßig bilden kann. Die Trockenkalibrierung wird vorwiegend für Profile bzw. Teile mit rechteckigem Querschnitt verwendet.
Allgemein
Der Kaliber ist meist flüssigtemperiert. Tritt das Profil in den Kaliber ein, so wird dieses von der äußeren Profilfläche aus gekühlt. Um den Kontakt mit der Kaliberinnenwand zu gewährleisten, wird meist ein Vakuum eingesetzt, welches das Material an die Wand pressen soll. Zu diesem Zweck befinden sich im Kaliber Vakuumschlitze, damit das Vakuum wirksam werden kann. Eine weitere Möglichkeit wird unter dem Punkt Vollprofile behandelt. Da der Kaliber wesentlich die Oberflächenqualität beeinflusst (sind mehrere Kaliber hintereinander geschaltet, beeinflusst der erste Kaliber die Oberfläche am meisten), muss bei der Fertigung besonders auf die Oberflächenqualität des Kalibers geachtet werden. Außerdem ist der Einlaufbereich des Kalibers erhöhtem Verschleiß ausgesetzt. Empfohlen werden hier besondere Materialien bzw. gehärtete oder anderweitig behandelte Oberflächen. Besonders bei der Trockenkalibrierung müssen die Reibkräfte im Kaliber beachtet werden, da hier das Material durch das angelegte Vakuum direkt mit der gehärteten Oberfläche in Kontakt kommt. Daran angepasst werden müssen einerseits die Abzugsvorrichtung als auch der Kalibriertisch. Man unterscheidet zwischen verschiedenen Kalibriermethoden:
Rohrkalibrierung
Bei der Rohrkalibrierung kann prinzipiell zwischen Innen- und Außenkalibrierung unterschieden werden. Die Außenkalibrierung unterteilt sich weiter in die Vakuumwasserbadkalibrierung und die Vakuumkalibrierung mit geschlossenem Kalibriergehäuse.
Vakuumwasserbadkalibrierung
Die viskoelastische Schmelze wird aus dem Extruder in eine Folge aus wassergefüllten Tanks geleitet, welche luftdicht abgeschlossen werden können. Beim Anfahren des Extruders wird das Rohr durch eine Folge von Kalibrier-Lamellenpakete geführt. Danach wird ein Vakuum von 0,3 bis 0,8 bar um das Rohr angelegt und die Becken geflutet. Durch das Vakuum wird das Rohr in die Kalibrier-Einheiten gepresst. Das Wasser kühlt einerseits die Formmasse und schmiert andererseits durch die Kapillarwirkung die Kontaktflächen zwischen Kunststoff und Metall, was eine Reduktion der Reibkräfte zur Folge hat. Analog zu den Lamellenpaketen können auch sogenannte Schlitzhülsen verwendet werden, welche entweder radial gebohrt oder geschlitzt sind. Die Vakuumwasserbadkalibrierung findet Anwendung bei Rohrdurchmessern von 2 bis 160 mm.
Vakuumkalibrierung mit geschlossenem Kalibriergehäuse
Hier sind im Kaliber die Vakuum- und die Kühlkammern getrennt. Dies bedeutet, dass das Wasser nicht direkt auf das Material trifft. Durch die erste Kühlkammer wird ein Ankleben des Kunststoffes durch Erkalten der äußersten Randschicht des Rohres verhindert. Durch die schlechte Wärmeleitfähigkeit erstarrt jedoch nicht die gesamte Wand und bleibt daher noch flexibel. Das angelegte Vakuum verhindert Einfallstellen und gewährleistet die Einhaltung der Formkontur.
Druckluftkalibrierung
Im Gegensatz zu den bisherigen Methoden wird bei der Druckluftkalibrierung die Kalibriereinheit unmittelbar mit an die Düse des Extruders angeflanscht. Der Kaliber besteht aus einer gekühlten Hülse mit Doppelmantel und Zwangsumlauf, um mit Wasser temperieren zu können, und einem Schleppstopfen. Der Überdruck von 0,3 bis 0,8 bar gegenüber Umgebungsdruck wird über eine Bohrung im Rohrkopf erzeugt. Der Überdruck wird durch den Schleppstopfen, welche über ein Schleppseil oder eine -kette, welche an der Düse befestigt ist, in einem festgelegten Bereich des Rohres aufrechterhalten. Der Überdruck im Bereich nach der Düse presst das Material an die Kaliberinnenwand, wo das Material abkühlt. Druckluftkalibrierungen finden hauptsächlich bei Rohren mit Durchmessern größer 160 mm Einsatz.
Profilkalibrierung
Vollprofilkalibrierung
Bei der Vollprofilkalibrierung ist besonders darauf zu achten, dass nur einseitig kalibriert wird. Das bedeutet, dass die gegenüberliegende Profilseite die Kaliberwand nicht berühren darf, da sich sonst das noch verformbare Material verkeilen könnte und zerstört werden würde. Die Kaliberschlitze sollten deshalb mit einem Übermaß von ca. 15 bis 20 % dimensioniert werden. Ein weiterer Grund für das Übermaß ist, dass das Druckgefälle zur Vakuumseite nur existiert, wenn auf der nicht kalibrierten Seite atmosphärischer Luftdruck wirken kann. Eine weitere Möglichkeit zur Vollprofilkalibrierung ist, den oberen Teil der Vorrichtung durch sein Eigengewicht oder mit Federkraft auf das zu kalibrierende Band wirken zu lassen.
Hohlprofilkalibrierung
Der erforderliche Differenzdruck zum Anlegen der zu kühlenden Profilflächen wird bei Hohlkammerprofilen durch Vakuum erreicht. Die Kalibrierung wird in kurzem Abstand zur Düse fixiert. Durch das Relaxationsverhalten des Kunststoffes weitet sich der in die Kalibrierung einlaufende Profilstrang auf. Dies wird zum Abdichten der Unterdruckzonen genutzt. Dickwandige Profile, sowie jene mit tragenden Stegen, erfordern lange Kaliberstrecken. Um dies zu gewährleisten, werden einzelne Kaliberwerkzeuge in Serie geschaltet. Deren Abmessungen müssen von Stufe zu Stufe proportional reduziert werden, um der Schwindung des Profils Rechnung tragen zu können. Auf die exakte Auslegung der Kaliberwerkzeuge ist zudem besonders zu achten.
Kalibriertisch
Nachdem bei großen Profilen Abzugskräfte von bis zu 30 kN wirksam werden können, ist es erforderlich, sehr robuste Konstruktionen des Aufspanntisches sowie die Lagefixierung der Profilwerkzeuge zu gewährleisten. Der Kalibertisch muss folgende Verstellmöglichkeiten zulassen:
- Axialverstellung, um den Abstand zwischen Profildüse und Kalibrierungseinlauf entsprechend der Arbeitsgeschwindigkeit zu optimieren.
- Höhenverstellung, um Kalibrierungen mit unterschiedlichen Querschnitten aufspannen zu können.
- Seitenverstellung, um die Kalibrierung in der Werkzeugachse ausrichten zu können.
Um eine optimale Profiloberfläche gewährleisten zu können, müssen alle verwendeten Spindeln, Führungsstangen oder Schlittenführungen, welche durch Vibrationen „Rattermarken“ verursachen, annähernd spielfrei ausgeführt werden.
Quellen
- Schaab, Herbert/Stoeckhert, Klaus: Kunststoffmaschinenführer, Verlag: Hanser, 1979
- Greif, Helmut/Seibel, Stefan: Technologie der Extrusion: Lern- und Arbeitsbuch für die Aus- und Weiterbildung, Verlag: Hanser, 2004