Eindringprüfung
Die Eindringprüfung (nach DIN EN ISO 3452-1, früher DIN EN 571-1: Eindringprüfung, allgemeine Grundlagen) ist eine zerstörungsfreie Werkstoffprüfung, bei der die Kapillarkräfte von feinen Oberflächenrissen und Poren genutzt werden, um diese sichtbar zu machen. Unterschieden wird zwischen der Farbeindringprüfung und der fluoreszierenden Eindringprüfung.
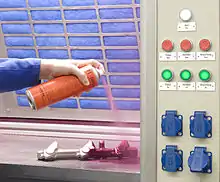
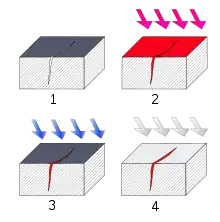
2. Farbe auftragen und eindringen lassen
3. Oberflächliches reinigen
4. Entwickler auftragen
Farbeindringprüfung (bei Tageslicht, > 500 Lux)
Bei der Farbeindringprüfung (PT) wird die Oberfläche des zu prüfenden Bauteils von Fett- und Ölrückständen befreit. Anschließend wird ein Farbeindringmittel (Kontraster) aufgebracht. Dies kann durch Auftragen mit einem Pinsel, durch Tauchen in ein Bad oder, an gut belüfteten Orten, durch Aufsprühen erfolgen. Durch die genannten Aufbringmethoden erfolgt eine „Zwangsbenetzung“. Das Kriechvermögen des Eindringmittels ist hoch, nutzt die Kapillarwirkung feinster Spalte und hat einen starken Farbkontrast zum Entwickler.
Nach Ablauf der vom zu prüfenden Werkstoff abhängigen Einwirkungszeit wird die Oberfläche mit Wasser oder einem speziellen Reiniger gereinigt, getrocknet und der Entwickler wird aufgetragen. Der Entwickler ist ein feinkörniges Pulver, meist auf Kalkbasis – Kreide, in Wasser oder Lösungsmittel suspendiert –, das durch die Kapillarwirkung seiner Hohlräume (Saugwirkung) das in feinen Rissen (Poren) verbliebene Eindringmittel lokal absorbiert. Im Regelfall ist das Eindringmittel eine rote Farbstofflösung und der Entwickler weiß. Der große Farbkontrast ermöglicht es, Fehlerstellen einfach zu lokalisieren und Rissverläufe zu bestimmen.
Fluoreszierende Eindringprüfung (im Dunkeln, < 20 Lux)
Bei niedriger Umgebungshelligkeit kann mit fluoreszierendem Eindringmittel gearbeitet werden, das mithilfe von UV-Bestrahlung sichtbar gemacht wird. Diese Prüfung ist wesentlich empfindlicher als die Farbeindringprüfung, weil die fluoreszierenden Partikel einen Leuchtdichtekontrast durch Umwandlung der UVA-Strahlung in sichtbares Licht erzeugen. Das menschliche Auge reagiert auf Leuchtdichtekontraste wesentlich empfindlicher als auf Farbkontraste. Hauptanwendungsgebiete der fluoreszierenden Eindringprüfung sind die Automobil,Luft- und Raumfahrtindustrie.
Anregungsquellen für die fluoreszierende Prüfung
Nach der EN ISO 3059 muss zu einer normkonformen fluoreszierenden Prüfung eine UV-A-Strahlenquelle oder ein blaues Licht zur Fluoreszenzanregung eingesetzt werden. Während in den letzten Jahrzehnten ausschließlich Entladungslampen (Quecksilberdampf-, Xenon- oder Metall-Halid-Lampen) eingesetzt wurden, werden heute primär UV-A-LED-Leuchten oder Blaulichtlampen verwendet. Blaulicht (450 nm) ist in der DIN CEN/TR 16638 vom Mai 2014 geregelt und zugelassen.
UV-Strahlung kann die Augen gefährden, daher sind u. U. Schutzmaßnahmen notwendig.
Die Eindringprüfung ist auf allen Werkstoffen anwendbar, die eine eindeutige Anzeige von Oberflächenfehlern erlauben (nicht porös sind), vorwiegend auf Metallen, Kunststoffen (mit Einschränkungen, z. B. Teflon), glasierten Keramiken und ähnlichen. Bei Maschinenteilen aus Stahl wird wegen der hohen Korrosionsanfälligkeit gegen Wasser in der Regel ein Entwickler auf Lösemittelbasis verwendet bzw. bei ferromagnetischen (nicht austenitischen) Stählen gleich die Magnetpulverprüfung angewandt.
Die Farbeindringprüfung ist geeignet, Risse (bis zu einem tausendstel Millimeter Breite) in der Oberfläche eines Werkstoffs schnell zu finden. Allerdings kann es bei rauen bzw. spröden Oberflächen zu sog. Scheinanzeigen kommen. Diese Anzeigen sind keine Fehlstellen. Auch lässt das Verfahren keine Aussage über die Fehlstellentiefe (Risstiefe) in Bezug auf die Anzeigenintensität zu: Eine beispielsweise zartrosa gefärbte Anzeige deutet nicht unbedingt auf einen weniger tiefen Riss hin als eine tiefrote Anzeige. Diese teilweise mangelnde Empfindlichkeit hat dazu geführt, dass dieses Verfahren beispielsweise im Rahmen von Prüfungen in der allgemeinen Luftfahrt nicht mehr als Prüfverfahren zugelassen ist.
Anlagen für die Eindringprüfung
In einer Eindringprüfanlage, auch Rissprüfanlage oder Penetrieranlage genannt, werden in verschiedenen Modulen die einzelnen Schritte des Eindringverfahrens umgesetzt. Damit kann die Eindringprüfung in möglichst konstanter Qualität durchgeführt werden, Normen und Standards insbesondere in der Luft- und Raumfahrtindustrie sowie Autoindustrie mit qualifizierten Eindringprüfanlagen eingehalten werden. Die Art und der Aufbau einer solchen Anlage ist abhängig von dem eingesetzten Eindringverfahren, den einzuhaltenden Normen sowie der Art der zu prüfenden Bauteile.
Automatisierungsgrad / Wirtschaftlichkeit
- Manuelle Penetrieranlagen: für Einzelteile und Kleinserien (z.B. klassischer Prüftisch / Prüfstand für die Eindringprüfung)
- teilautomatische Eindringprüfanlagen: üblicherweise bei unterschiedlichen Bauteilen im Einsatz / wechselndes Bauteil-Portfolio (halbautomatische Anlagen z.B. mit manueller Auf-/Abgabe und automatischem Penetriermittelauftrag)
- vollautomatisierte Penetrierlinie: ausgelegt für Massenteile, z.T. mit Transportkörben
Module einer Eindringprüfanlage
Die nachfolgend aufgelisteten Komponenten werden individuell kombiniert und auf den notwendigen Prozess für die Eindringprüfung abgestimmt. Je nach Ausführung der Anlage sind mehr oder weniger der genannten Module integriert.
- Ladestation / Vorreinigung: speziell bei automatischen Eindringprüfanlagen im Einsatz
- Waschstation Zwischenreinigung: bei automatischen Penetrieranlagen in zwei oder mehrere Module wie Vorspülstation/Abwaschen und Nachspülstation/Nachwaschen unterteilt
- Eindringstation (Penetrierstation) bzw. Entwickler Spray Station: Sprühen bzw. Eintauchen der Bauteile (Penetrieren), auch im Tauchverfahren
- Trockenentwicklerstation: für die Auswertung und Inspektion, Überprüfung der Teile auf vollständige Abdeckung durch das Prüfmittel
- Emulgatorstation bzw. Emulgatorbecken: Eintauchbecken, um den Emulgator aufzubringen. Nach dem Emulgator kommt das Stoppbad zur Stabilisierung der Emulsion
- Trocknerstation: Trockenofen für die Eindringprüfung, normalerweise im Bereich von 60-70°C. Teilweise Haftwassertrockner, Trogtockner, Schranktrockner oder Durchlauföfen im Einsatz
- Betrachtungsstation: Prüfstand für die Inspektion. In größeren Eindringprüfanlagen auch mehrere Betrachtungsplätze inklusive Verdunklungskabine mit UV-Beleuchtung (Ultraviolettstrahlung)
- Beladesysteme und Entladesysteme: Automatisiertes Beschicken der Eindringprüfanlage mit Bauteilen sowie Weitergabe der Prüfteile nach der Inspektion in den weiteren Produktionsprozess
Normen für die Eindringprüfung
Allgemeines
Eindringprüfungen, insbesondere in der Luft- und Raumfahrtindustrie, werden nicht nach der ursprünglich deutschen DIN EN ISO 3452 durchgeführt, sondern primär nach der amerikanischen ASTM E 1417, der die ISO 3452-2 mittlerweile sehr stark ähnelt. Zur Prüfung nach dieser Norm dürfen ausschließlich Produkte, die in QPL (qualified products list) der AMS 2644 gelistet und somit zugelassen sind, verwendet werden. Hauptunterschiede sind die in der ISO vorhandene Klassifizierung der Empfindlichkeit bei Farbeindringprüfmitteln und die Berücksichtigung und Zulassung von fluoreszierenden Farbeindringmitteln.
Normen
- DIN 25435-2, Wiederkehrende Prüfungen der Komponenten des Primärkreises von Leichtwasserreaktoren – Teil 2: Magnetpulver- und Eindringprüfung
- DIN EN 1371-1, Gießereiwesen – Eindringprüfung – Teil 1: Sand-, Schwerkraftkokillen- und Niederdruckkokillengußstücke
- DIN EN 1371-2, Gießereiwesen – Eindringprüfung – Teil 2: Feingußstücke
- DIN EN 2002-16, Luft- und Raumfahrt – Metallische Werkstoffe; Prüfverfahren – Teil 16: Zerstörungsfreie Prüfung, Eindringprüfung
- DIN EN 10228-2, Zerstörungsfreie Prüfung von Schmiedestücken aus Stahl – Teil 2: Eindringprüfung
- DIN EN ISO 10893-4 Zerstörungsfreie Prüfung von Stahlrohren – Teil 4: Eindringprüfung nahtloser und geschweißter Stahlrohre zum Nachweis von Oberflächenunvollkommenheiten
- DIN EN ISO 3059, Zerstörungsfreie Prüfung – Eindringprüfung und Magnetpulverprüfung – Betrachtungsbedingungen
- DIN EN ISO 3452-1, Zerstörungsfreie Prüfung – Eindringprüfung – Teil 1: Allgemeine Grundlagen
- DIN EN ISO 3452-2, Zerstörungsfreie Prüfung – Eindringprüfung – Teil 2: Prüfung von Eindringprüfmitteln
- DIN EN ISO 3452-3, Zerstörungsfreie Prüfung – Eindringprüfung – Teil 3: Kontrollkörper
- DIN EN ISO 3452-4, Zerstörungsfreie Prüfung – Eindringprüfung – Teil 4: Geräte
- DIN EN ISO 3452-5, Zerstörungsfreie Prüfung – Eindringprüfung – Teil 5: Eindringprüfung bei Temperaturen über 50 °C
- DIN EN ISO 3452-6, Zerstörungsfreie Prüfung – Eindringprüfung – Teil 6: Eindringprüfung bei Temperaturen unter 10 °C
- DIN EN ISO 12706, Zerstörungsfreie Prüfung – Eindringprüfung – Begriffe
- DIN EN ISO 23277, Zerstörungsfreie Prüfung von Schweißverbindungen – Eindringprüfung von Schweißverbindungen – Zulässigkeitsgrenzen
- DIN CEN/TR 16638, Zerstörungsfreie Prüfung – Eindringprüfung und Magnetpulverprüfung unter Anwendung von blauem Licht
- ASTM International (ASTM)
- ASTM E 165, Standard Practice for Liquid Penetrant Examination for General Industry
- ASTM E 1417, Standard Practice for Liquid Penetrant Testing