Wälzprozess
Als Wälzprozess oder Wälzverfahren, kurz Wälzen bezeichnet man ein metallurgisches Verfahren in einem Drehrohrofen. Das Wälzverfahren wird gegenwärtig primär zur Aufarbeitung von zinkhaltigen Reststoffen (hauptsächlich zinkhaltige Stahlwerksstäube) verwendet. Dabei wird grundsätzlich zwischen dem sauren und den basisch betriebenen Wälzprozess unterschieden. Hauptprodukt des Prozesses ist das sogenannte Wälzoxid, das im Wesentlichen aus Zinkoxid (ZnO) besteht und zur Zinkgewinnung verwendet wird.
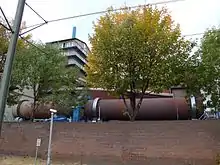
Geschichte des Wälzprozesses
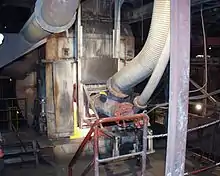
Die Anfänge des heute bekannten Wälzprozesses reichen bis in das 19. Jahrhundert zurück. Bereits 1881 erfolgte von George Drue der Vorschlag Zink zwecks seiner Gewinnung zu verdampfen. Ursprünglich diente der Drehrohrofen primär zur Aufkonzentrierung von Blei- und Zinkerzen, in Deutschland erstmals 1913 patentiert. Er kam aber auch als Röstaggregat (Debuch-Ofen) zum Entschwefeln sulfidischer Erze zum Einsatz. Mit dem kräftigen Ansteigen der Zink- und Bleierzeugung Anfang des letzten Jahrhunderts erhöhte sich zwangsläufig auch die Menge der bei der Primärproduktion anfallenden Rest- und Abfallstoffe. Darunter zum Beispiel zinkhaltige Schlacken und Räumaschen aus Imperial-Smelting- bzw. Muffelöfen oder dem New-Jersey-Prozess. Wurden diese anfänglich beinahe zur Gänze deponiert, erkannte man doch rasch den Wert dieser Stoffe. Hohe Anteile an Kohlenstoff und Metallgehalte, die mitunter über jenen der Primärerze lagen, begründeten das Bestreben diese Stoffe einer Rückgewinnung zu unterziehen. Später gesellten sich mehr und mehr auch umwelttechnologische Aspekte hinzu, die vielerorts zur Aufarbeitung von über Jahrzehnte angehäuften Deponien führten. Einfache Funktion und hoher Durchsatz verhalfen dem Wälzprozess dabei zu einem breiten Einsatzgebiet. Durch laufende Prozessverbesserungen der Zink-Primärhütten verringerten sich jedoch die anfallenden Reststoffmengen bzw. deren Wertstoffgehalte kontinuierlich. Damit war die wirtschaftliche Grundlage des Wälzprozesses vielerorts nicht mehr gegeben, weshalb die Suche nach neuen Einsatzstoffen begann. Parallel zu dieser Entwicklung wurde zu dieser Zeit eine immer größere Zahl von kleinen Blas- und Elektrostahlwerken (EAF = Electric Arc Furnace) in Betrieb genommen. Diese Werke verfügten bereits über Entstaubungsanlagen, in denen bei der zunehmenden Verarbeitung von zinkhaltigen Schrotten Stäube mit teilweise hohen Metallgehalten anfielen. Da im Wälzprozess bereits früher im geringen Maße Stahlwerksflugstäube eingesetzt wurden, bot es sich förmlich an, diese neue Rohstoffquelle zu nutzen. Die erste hauptsächlich EAF-Staub verarbeitende Wälzanlage ging in Deutschland in den siebziger Jahren in Duisburg in Betrieb. Danach entwickelte sich der Wälzprozess schnell zum bedeutendsten Verfahren in der Aufarbeitung von Stahlwerksstaub und blieb dies bis heute. Etwa 80 % der gesamten aufgearbeiteten Stahlwerksflugstaubmenge, das entspricht etwa 1,6 Millionen Tonnen (im Jahr 2006), durchlaufen pro Jahr das Wälzverfahren.
Aufbau und Funktionsweise
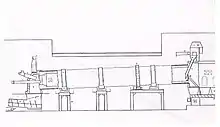
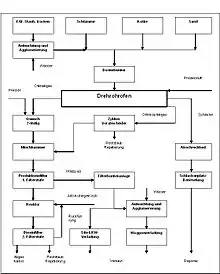
Die Wälzarbeit gehört zu einer Reihe von Verfahren, bei denen die Anreicherung der zu gewinnenden, oxidischen Inhaltsstoffe über die Bildung einer intermediären Metallphase mit anschließender Verflüchtigung und Rückoxidation im Gasstrom erfolgt. Die unerwünschten Reststoffe verbleiben überwiegend in einem hochviskosen Rückstand[1].
Der Stahlwerksstaub wird neben anderen Zinkträgern wie Galvanikschlämmen oder Kupolofenstaub zusammen mit Schlackenbildnern und einem Kohlenstoffträger (meistens Petrolkoks) pelletiert und in das Einlaufende des langsam drehenden Wälzofens aufgegeben. Obwohl es keinen prozesstechnischen Minimalgehalt hinsichtlich des Zinkgehaltes des chargierten Staubes gibt, stellt in der Praxis ein Zinkgehalt im Vorlauf von rund 20 % in den meisten Fällen die wirtschaftliche Untergrenze dar. Nach oben bildet ein Zinkgehalt von rund 50 % die Grenze, da der Ofen sonst zu heiß werden würde. Als Schlackenausgangsstoff dienen hauptsächlich Sand (= Saures Verfahren) oder aber Kalk (= Basisches Verfahren). In den 1980er und 1990er Jahren wurden Versuche mit Räumasche (Zinkhüttenschlacke aus dem Muffelverfahren) als Kohlenstoffträger (20 bis 45 % Restkohlenstoff, sowie Anteile von Zink und Blei in der Summe 5 bis 15 %) unternommen. Dieses hat sich als unwirtschaftlich erwiesen. Das Drehrohr ist bei den heutigen Anlagen 40 bis 50 m lang und hat 2,6 – 5 m Durchmesser. Durch die Rotation von etwa 1/min, sowie einer 2–3 % Neigung gegenüber der Horizontalen wird die feste Beschickung allmählich zum Austragsende entgegen dem Gasstrom bewegt. Die Anlage funktioniert also im sogenannten Gegenstromprinzip. In Abhängigkeit von der Ausmauerung, der Länge und der Umdrehungsgeschwindigkeit des Ofens beträgt die Verweilzeit des Einsatzmaterials im Wälzrohr zwischen 4 und 12 Stunden. Dabei durchläuft das Material folgende vier Zonen:
- Trocknungszone
- Aufheizzone mit Koksverbrennung
- Vorreaktionszone
- Hauptreaktionszone
Trocknungszone
Gleich nach der Beschickung trifft das kühle Aufgabegut auf die heiße Ofenatmosphäre mit 500 bis 1000 °C. Dadurch wird freies wie auch gebundenes Wasser verdampft und die Charge trocknet. Dieser Trocknungsvorgang findet etwa innerhalb der ersten 6 m statt. Das Einsatzmaterial erwärmt sich dabei auf rund 150 °C.
Aufheizzone
Die Temperatur des Einsatzmaterials steigt weiter auf bis zu 500 °C und eine beginnende Koksverbrennung setzt ein. Feinster Kohlenstoff und flüchtige Kohlenwasserstoffanteile im Koks verbrennen dabei in Abhängigkeit vom Restsauerstoffgehalt der Ofenatmosphäre unter Bildung von Kohlenmonoxid CO bzw. Kohlendioxid CO2. Der Verbrennungsprozess findet hier ausschließlich in der Ofenatmosphäre oder an der Kontaktfläche zwischen Ofenatmosphäre und Charge statt.
Vorreaktionszone und Hauptreaktionszone
In diesem Sektor beginnt Sauerstoff in der Ofenatmosphäre verstärkt mit dem Kohlenstoff in der Beschickung unter Bildung von CO2 zu reagieren. Nach der Boudouard Reaktion reagiert CO2 mit weiterem Kohlenstoff zu CO, welches dann zur Reduktion der Metalloxide im Aufgabegut zur Verfügung steht. In der Vor-Reaktionszone erreicht die Beschickung bis zu 900 °C, wobei erste Reduktionsreaktionen einsetzen, wie zum Beispiel jene von Cadmium- und Kupfer(II)-oxid. Auch Eisenoxide mit hohem Sauerstoffanteil werden vorreduziert. Mit steigender Temperatur erhöht sich das Reduktionspotenzial und führt zunehmend zur Zersetzung weiterer Metallverbindungen, wie Zinkoxid und Zinkferrit. Bei einer Höchsttemperatur von rund 1300 °C bis 1400 °C werden neben dem Zink auch Blei, Chlor, Fluor und Alkalien verflüchtigt. Diese folgen dem Zink im Prozessgasstrom aus dem Ofen.
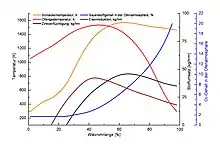
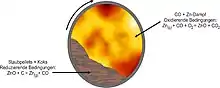
Die Zinkverflüchtigungsrate variiert über die Ofenlänge, erreicht aber etwa zugleich mit der Zone der höchsten Temperatur ihr Maximum (siehe Diagramm). Das Gesamtzinkausbringen einer Wälzanlage liegt heutzutage bei bis zu 96 %.
Blei wird neben Blei(II)-chlorid und Blei(II)-oxid vor allem als Blei(II)-sulfid verflüchtigt, da es eine hohe Schwefelaffinität besitzt. Eine geringe Schwefelaufgabe mit der Beschickung kann daher die Bleiausbeute verbessern. Blei in der Schlacke ist unerwünscht, da es sich negativ auf die Eluatwerte der Schlacke auswirkt. Charakteristisch für den Wälzprozess ist, dass sich in der Beschickung reduzierende, in der Ofenatmosphäre aber oxidierende Bedingungen einstellen (siehe Abbildung). Dadurch wird das reduzierte, dampfförmige Zink in der Ofenatmosphäre spontan rückoxidiert und vorhandenes CO zu CO2 verbrannt.
ZnO-Reduktion in der Beschickung:
Zn-Rückoxidation in der Ofenatmosphäre:
Da die Zink- bzw. Eisenreduktion ein endothermer Prozess ist, richtet sich die zugesetzte Kohlenstoffmenge im Wälzprozess nicht nach der zur Zn-Reduktion stöchiometrisch nötigen Menge, sondern nach dem Wärmebedarf des Verfahrens, weshalb Kohlenstoff deutlich überstöchimetrisch zugegeben wird. Durch das Gegenstromprinzip trifft kalte, sauerstoffreiche Luft auf eine heiße Charge am Ofenende, wodurch die Luft erwärmt wird. Gleichzeitig setzt die Kohlenstoffverbrennung ein. Neben dieser liefert auch die CO-Nachverbrennung und die Rückoxidation des gasförmigen Zinks Wärmeenergie, weshalb sich das Prozessgas weiter erhitzt. Parallel dazu verarmt die Ofenatmosphäre bereits an freiem Sauerstoff. Heißes Abgas trifft schließlich auf die kalte Beschickung am Ofeneintrag und erwärmt diese, ehe die Verbrennungsreaktionen in der Beschickung einsetzen.
Der Koks hat neben seiner Funktion als Energieträger und Reduktionsmittel auch die Aufgabe, die erweichende Schlacke zu durchlüften. Dadurch kann gasförmiges Zn und CO aus der Schlacke besser entweichen. Das Wälzen unterstützt diesen Effekt, indem es ständig die Kontaktzone zwischen Beschickung und Ofenatmosphäre erneuert. Um diesen Vorgang aufrechtzuerhalten, darf die Schlacke nicht aufschmelzen. Aufgrund dessen werden Zuschlagstoffe miteingebracht, die ein Aufschmelzen verhindern sollen. Je nachdem welche Schlackenbildner zugegeben werden, erfolgt eine Unterscheidung zwischen dem sauren und dem basischen Wälzprozess. Der saure Prozess, bei dem Siliciumdioxid SiO2 meist in Form von Quarzsand chargiert wird, liegt bei einer Basizität zwischen 0,2 und 0,5. Das basische Verfahren, mit einer Zugabe von Kalk, Kalkstein oder gebranntem Kalk, wird bei einer Basizität zwischen 1,5 und 4 betrieben. Spricht man vom Schlackenformen, ist damit das teilweise Erweichen der Schlacke im sauren Prozess gemeint. Dieses Erweichen ist bis zu einem gewissen Grad vorteilhaft, da dadurch der Feinanteil der Schlacke (wie z. B. Sand) eingebunden wird. Bei einer basischen Fahrweise erweicht die Schlacke nicht. Ein Schlackenformen ist deshalb nicht möglich aber auch nicht erforderlich, da der Kalk ohnehin miteinpelletiert wird. Die Entscheidung einen Wälzrohrofen basisch oder sauer zu betreiben, wird im Wesentlichen durch die lokale Situation hinsichtlich der verfügbaren Einsatzstoffe und unter Berücksichtigung der Absatzmöglichkeiten für die Wälzschlacke gefällt. Ein Betrieb zwischen den beiden oben genannten Basizitätsbereichen wird in der Praxis vermieden, da er schwierig zu kontrollieren ist und meist zu Problemen wie verstärkter Ansatzbildung an der Ofenfeuerfestausmauerung führt.
Die Wälzschlacke fällt bei der Verarbeitung von Stahlwerksstaub als Nebenprodukt an. Nachdem das Einsatzmaterial den Drehrohrofen durchlaufen hat und die flüchtigen Anteile abgetrennt sind, verlässt die Beschickung als Wälzschlacke den Ofen. Noch heiß, mit über 1000 °C, fällt sie in ein Wasserbad und kühlt dort rasch ab. Durch eine Magnetscheidevorrichtung ist es möglich, einen Teil des in der Schlacke enthalten Kohlenstoffs zurückzugewinnen, ehe man die Restschlacke vom Prozess ausschleust. Abhängig vom gewählten Wälzprozess kann die Schlacke sauer oder basisch sein, wobei sie sich im Wesentlichen nur durch ihre SiO2- und CaO-Gehalte unterscheidet. Während die basische Schlacke CaO-Werte von 15 – 25 % und nur 8 – 9 % SiO2 aufweist, liegen die CaO-Gehalte der sauren Schlacke mit 6 – 12 % niedriger und die SiO2-Gehalte mit 35 – 37 % dementsprechend höher. Die Zink- und Bleigehalte liegen in der Regel bei jeweils bis zu 2 %. Da eine Deponierung der Schlacke mit hohen Kosten verbunden ist, wird versucht, diese als Baumaterial (z. B. für den Straßenbau) abzusetzen. Der Anteil der eluierbaren Anteile (soll möglichst gering sein) in der Schlacke spielt dabei eine zentrale Rolle.
Die Abgasreinigungsanlagen von Wälzanlagen haben deutlich höhere Anforderungen zu erfüllen als jene der übrigen metallurgischen Industrie. Das liegt daran, dass mit dem Abgas auch das eigentliche Produkt, nämlich das Wälzoxid, ausgetragen wird. Grobe Partikel werden gleich nach dem Ofenausgang in einer Staubabsetzkammer aufgefangen und dem Prozess rückgeführt. Im weiteren Verlauf wird das Prozessgas in mehreren Stufen abgekühlt und gereinigt. Das gewonnene Rohzinkoxid wird heutzutage fast ausschließlich hydrometallurgisch in einer Zinkgewinnungselektrolyse weiterverarbeitet. Da in dieser der relativ hohe Alkalien- und Halogenidengehalt (i.a. Fluor und Chlor) Probleme bereiten würde, wird das Rohoxid heutzutage über eine zwei oder dreistufige Laugung von diesen gereinigt. Die dabei anfallenden, festen Rückstände gelangen zur Aufarbeitung zurück in das Wälzrohr. Das doppelt gelaugte Wälzoxid erreicht Halogenwerte von <0,1 % Chlor und <0,15 % Fluor und ist damit meist direkt in der Zinkelektrolyse einsetzbar.
Das SDHL-Verfahren
Das Wälzverfahren gilt auch heute noch als bestverfügbare Technik, um zink- und bleihaltige Stahlwerksstäube zu verwerten. Ein kritisch zu beurteilender Parameter dieses Verfahrens ist aber sein hoher Energieverbrauch. Dieser lässt sich einfach durch die Zusammensetzung der Wälzschlacke erklären, die einen hohen Anteil an Restkoks und metallischem Eisen aufweist. Das SDHL-Verfahren (benannt nach den Erfindern: Saage, Dittrich, Hasche und Langbein) ist eine Weiterentwicklung, die den Energieverbrauch der Wälzanlage drastisch reduziert und gleichzeitig den Durchsatz und das Zinkausbringen verbessert.
Während beim konventionellen Wälzprozess der Koks überstöchiometrisch zugegeben wird, um den Wärmebedarf zu decken, setzt man beim SDHL-Verfahren nur ca. 70 % des zur Metalloxidreduktion nötigen Kohlenstoffes ein. Das ist möglich, da bei diesem Verfahren das zuvor reduzierte Eisen durch gezielte Beaufschlagung mit Frischluft am Ofenende wieder reoxidiert wird und dem Prozess damit die dabei freiwerdende Wärme zur Verfügung steht. Der Restkohlenstoffgehalt der SDHL-Schlacke sinkt dabei bis auf < 1 % und der metallisierte Eisenanteil auf < 10 %. Das freigesetzte energetische Potenzial der Schlacke ist so hoch, dass in weiterer Folge auch auf eine kontinuierliche Zusatzheizung mit Erdgasbrennern verzichtet werden kann. Außerdem steigert sich das Zinkausbringen von rund 90 % auf bis zu 96 %. Trotz einer 20%igen Steigerung des Ofendurchsatzes, reduziert sich der CO2-Ausstoß um rund 40 %.
Sofern keine Eisenrückgewinnung aus der Wälzschlacke erfolgt, stellt das SDHL-Verfahren momentan (2009) die ökonomisch und wirtschaftlich beste Variante des Wälzprozesses dar. Mit relativ geringem technischen Aufwand kann der Prozess auch in bestehende Anlagen integriert werden.
Wälzanlagen in Deutschland
- Harz-Metall GmbH in Goslar/ Oker
- Befesa Zinc Duisburg GmbH (vormals Berzelius Umwelt Service) in Duisburg
- Befesa Zinc Freiberg GmbH in Freiberg (Sachsen)
Literatur
- P. A. Kozlov: The Waelz Process, Ore and metals. publishing house, Moskau 2003.
- U. Meurer: Gewinnung von Zinkoxid aus sekundären Rohstoffen. In: Neue Entwicklungen im Wälzprozess. (= Schriftenreihe der GDMB. Heft 87). 2000, S. 183–196.
- J. Rütten: Application of Pyro-Metallurgical-Processes on Resource Recycling of Steel Mill Dust. In: 55. Tagung des Zinkfachausschusses der GDMB, Balen, Flandern, Belgien. 2007.
- B. Matl: Aufarbeitung zinkhältiger Stäube aus der Sekundärmetallurgie. Diplomarbeit. Montanuniversität Leoben, 2004.
- M. Zechner: Verringerung der Zuschlagstoffe im Wälzprozess unter Vermeidung von Ansatzbildung. Diplomarbeit. Montanuniversität Leoben, 2009.
- V. Tafel, K. Wagenmann: Lehrbuch der Metallhüttenkunde. Band II, 2. Auflage. S. Hirzel Verlagsbuchhandlung, Leipzig 1953.
- J. Czernecki, E. Stós, J. Botor: Technology of EAF Dust Treatment in Rotary Furnaces. In: Proc. of EMC 2003, Hannover, Niedersachsen, Deutschland. 2003, S. 465–479.
- A. D. Zunkel: EAF dust as an electrolytic zinc resource. In: Proc. Third International Symposium on Recycling of Metals and Engineered Materials, Point Clear, Alabama, USA. 1995, ISBN 0-87339-318-X, S. 579–587.
- Franz Pawlek: Metallhüttenkunde. Walter de Gruyter & Co., Berlin 1982, ISBN 3-11-007458-3.
Einzelnachweise
- Matthias Becker: Metallbilanz für die Wälzarbeit im Drehrohrofen der Harz-Metall GmbH – Studienarbeit. Unveröffentlicht, Goslar 1993.