Exjection
Das Exjection-Verfahren (auch: Extrusionsspritzguss) zählt zu den Spritzgusssonderverfahren. Das Verfahren ist eine Kombination aus Extrusion und Spritzgießen und dient zur Herstellung langer, dünnwandiger und strukturierter Bauteile, auch aus zähfließenden Thermoplasten auf verhältnismäßig kleinen Spritzgussmaschinen mit geringer Schließkraft.
Der Grundgedanke von Exjection besteht darin, die beim Spritzguss normalerweise feststehende Formkavität durch den Formaufbau im Verhältnis zum Anspritzpunkt zu verschieben und dadurch die Bauteillänge vom erzielbaren Fließweg zu entkoppeln. Damit wird es möglich aus den üblichen, hochviskosen Formmassen Bauteile und Komponenten ohne eine prozesstechnische Beschränkung der Bauteillänge zu fertigen.
Der Exjectionprozess
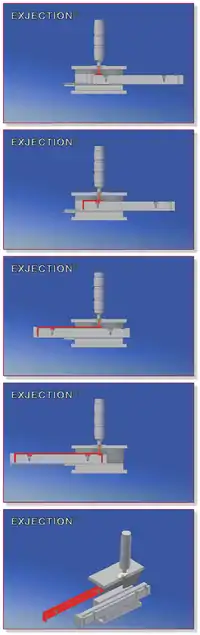
Nach dem Schließen der Form auf der Spritzgießmaschine beginnt der Exjectionprozess analog zum konventionellen Spritzgießen mit dem Einspritzen in die Kavität aus dem voll aufdosierten Zylinder. Der Schlitten der Exjectionform steht in der Ausgangsposition. Im Schlitten ist die gesamte Bauteilgeometrie eingeformt, wobei das Formnest über die gesamte Länge des Anschnitts offen ist. Ein entsprechender Teil der Form auf der feststehenden Düsenseite der Form dichtet das Formnest partiell ab und wirkt als Extrusionswerkzeug mit Kalibriereinheit.
Über eine Düse und einen beheizten Düseneinsatz wird die Schmelze in die Kavität eingespritzt, füllt den Endbereich und fließt vom Anschnitt weg in die offene Kavität. Es baut sich dabei ein Fülldruck von mehreren 100 bar an der Düse auf. Noch bevor die Schmelze den entsprechenden, teilweise variotherm beheizten, Bereich der Kavität verlässt und ins Freie tritt, beginnt sich der Schlitten entgegen der Spritzrichtung zu bewegen.
Der nachfolgende Einspritzvorgang läuft primär druckgeregelt ab, wobei die Fließfrontgeschwindigkeit und Schlittenbewegung harmonisiert werden. Damit eilt der Anschnitt der Fließfront hinterher und es bildet sich auf Basis der Quellströmung und der Viskosität der Schmelze ein gleichmäßiges Druckprofil mit niedrigen Scherraten aus. Dieser Zustand ist quasistationär und daher bei konstantem Querschnitt unabhängig von der nachfolgenden Länge des herzustellenden Bauteiles. Der Füllvorgang mit konstanten Prozessparametern vermeidet Bindenähte und hat eine gleichmäßige Pigment- und Füllstoffverteilung im Bauteil zur Folge.
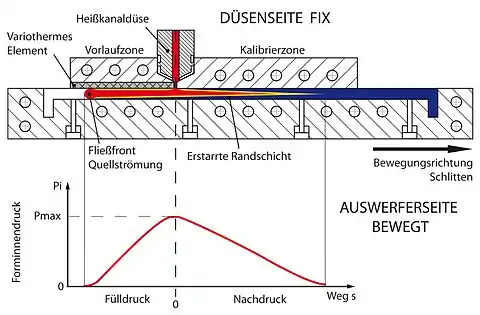
Schlittengeschwindigkeit und Einspritzprofil werden über die Bauteillänge durch Vorgabewerte und Geschwindigkeitsprofile gesteuert. Regelgröße ist dabei der Profilquerschnitt und die Bauteildicke, die in Abhängigkeit vom Spritzmaterial und den Prozesstemperaturen die Abkühlgeschwindigkeit und damit die Schlittengeschwindigkeit bestimmen. Im gefüllten Querschnitt wird der, gleichzeitig auch als Nachdruck wirkende, Fülldruck mit seinem Maximum am Anschnitt aufgebaut. Je nach Viskosität der Schmelze, Füllgeschwindigkeit und Bauteilwandstärke können Fülldrücke, und damit auch Nachdrücke, im Bereich von etwa 50 bar bis 200 bar gewählt werden. Eine gute Strukturabformung und das Vermeiden von Einfallstellen sind die direkte Folge dieses Zustandes. Der Druck ist im Formnest noch so lange wirksam, bis die Schmelze über die gesamte Wandstärke erstarrt ist. Jedes Volumenelement im Bauteil unterliegt so einem zeitabhängigen Nachdruckverlauf. Nach der Erstarrung verlässt die extrudierte Oberfläche die Kalibrierzone des Düseneinsatzes und tritt ins Freie.
Kurz bevor der Anschnitt das Ende der Kavität erreicht, wird die Geschwindigkeit des Schlittens reduziert und dieser zum Stillstand gebracht. Durch einen konventionellen Spritzzyklus mit Einspritzen, Nachdrücken und Abkühlen wird der Endbereich des Bauteils gefüllt, ausgeprägt und zum Erstarren gebracht. Nach dem Aufdosieren der Plastifiziereinheit kann die Form geöffnet werden. Die Rückfahrbewegung des Schlittens in die Ausgangsposition wird noch für die Abkühlung genutzt, nachfolgend kann das Bauteil entformt, ausgeworfen und entnommen werden. Die Gesamtzykluszeit für den Exjectionprozess entspricht jener eines Spritzgussprozesses mit Kaskadensteuerung bei Füllung von einem Bauteilende.
Umsetzbare Bauteilgeometrien
Das Exjectionverfahren ist primär zur Fertigung von profilartigen Komponenten und Leisten gedacht. Kennzeichnend für Exjectionbauteile ist dabei ein großes Verhältnis der Bauteillänge zu den Abmessungen des Bauteilquerschnitts. Typische Produktbeispiele für Exjection sind etwa Lichtbandabdeckungen, Kabelführungskanäle, Hochleistungskabelbinder, Zier- und Dekorleisten, Zahnstangen oder Gleitleisten.
- Exjection Beispiel: Kabelführungskanal mit echten 3D Geometrieelementen
- Exjection Beispiel: Zierleiste mit Echtholzdekor für automotive Interior Anwendung
- Exjection Beispiel: Hochleistungskabelbinder aus Victrex PEEK
- Exjection Beispiel: In-Mold dekorierte Zierleiste mit Versteifungsrippen
Materialien
Von der Materialseite ist Exjection geeignet für die Verarbeitung sämtlicher Formmassen die auf konventionelle Spritzgussmaschinen verarbeitbar sind. Im thermoplastischen Bereich reicht diese Palette von Standardkunststoffen (PS, ABS, SAN, PP) über technische Kunststoffe (u. a. Ionomer, POM, PBT, PC, PMMA, PA6, PA66) bis zu thermoplastischen Elastomeren und thermoplastischen Polyurethanen. Infolge des schonenden Prozessablaufs weist Exjection eine besondere Eignung für die Verarbeitung von Hochleistungskunststoffen wie Polyetherimid (Typ: Ultem; Hersteller: Sabic Innovative Plastics), Polyphenylensulfon (PPSU, Typ: Radel R; Hersteller: Solvay) oder PEEK (Typ: Victrex PEEK; Hersteller: Victrex) auf.
Kombination mit Sonderverfahren des Spritzgießens
Sonderverfahren des Spritzgießens wie das In-Mold-Labeling, die Hybridtechnik und die Mehrkomponententechnik sind in Kombination mit Exjection realisierbar. Die grundsätzlichen Prozessverhältnisse (geringer Prozessdruck, schonende Füllung des Bauteils) bei Exjection können dabei entsprechende Vorteile für die Kombination von Exjection mit einem Sonderverfahren bieten. Beispielsweise erlaubt das geringe Schergeschwindigkeitsniveau in Verbindung mit dem nicht ortsfesten Anspritzpunkt bei der Herstellung von In-Mold dekorierten Bauteilen die Verwendung von empfindlichen Dekoren wie etwa Echtholzfurnieren.
Entwickler des Exjectionverfahrens
Das Exjectionverfahren wurde 2005 vom IB Steiner, einem österreichischen Ingenieurbüro mit den Schwerpunkten Bauteil- und Prozessentwicklung im Bereich der Kunststoffe, mit Sitz in Spielberg in der Steiermark, als Eigenentwicklung zum Patent angemeldet. Seit der Anmeldung wurde das Verfahren vom IB STEINER in enger Zusammenarbeit mit einer weiteren österreichischen Firma, der Hybrid Composite Products, bis zur Marktreife weiter entwickelt. Weitere Projektpartner mit Anteil an der Entwicklung des Verfahrens sind die Firmen Arburg und Engel Austria, beide weltweit tätige Hersteller von Spritzgießmaschinen, sowie weitere Unternehmen aus der Kunststoffbranche wie der Anbieter von Normalien Hasco, die Firma Oerlikon Balzers als Spezialist im Bereich Oberflächenbeschichtung, Böhler Edelstahl als Anbieter von Werkzeugstählen sowie die Formenbauer CAD-Plast und Dema Engineering.
Das erste Mal wurde das Verfahren im Oktober 2007 auf der K2007, der weltweit größten Kunststoffmesse, in Düsseldorf einem breiteren Publikum präsentiert und erregte in der Fachwelt großes Interesse.
Verfügbare Maschinenplattformen
Derzeit werden von 2 Herstellern entsprechende Spritzgießmaschinen mit Hardwareplattformen für den Exjectionprozess angeboten. Es handelt sich dabei um zwei große europäische Anbieter von Spritzgießmaschinen, die österreichische Firma Engel Austria sowie den deutschen Maschinenhersteller Arburg. Beide Hersteller bieten serienreife Lösungen zur Umsetzung von Exjection-Fertigungszellen, wobei hier als Basis sowohl vollelektrische als auch hydraulische Spritzgussmaschinen zur Anwendung kommen.
Literatur
- H. Sambale: Spritzgießen profilähnlicher Kunststoffteile. In: Kunststoffe Technik-Trends. auf www.kunststoffe.de, 08/2007.
- Exjection kombiniert Extrusion und Spritzguss – Weltneuheit: Lange, profilierte Kunststoffteile aus der Spritzgießmaschine. In: Kunststoff-Berater. 10/2007, S. 57–59.
- Die Kavität kommt zum Anschnitt - Exjection: Reif für die Serie. In: Plastverarbeiter. 9/2009, S. 76–78.
- G. Steiner, T. Krivec: Exjection: Spritzguss und Extrusion als Einheit erfolgreich. In: Österreichische Kunststoffzeitschrift. Nr. 3 und 4/2009, S. 49 bis S. 52.
- G. Steiner: Spuitgieten en extruderen tegelijk: Exjection, voordeel over de volle lengte. In: Kunststof en Rubber. Nr. 6 - Juni 2008, S. 26–29.
- G. Steiner, H. Eichler: Spritzgießen um Längen voraus. In: Kunststoffe international. 98, 4, 2008, S. 24–28.
- G. Steiner, T. Krivec: Exjection: Serienumsetzung läuft. In: Kunststoff-Berater. 3/2008, S. 30–35.
- M. Knights: Close-Up On Technology: Injection Molding. New Low-Pressure Process Molds Long Profiles On Small Presses. In: Plastics Technology. July 2008, S. 45–47.