Innendruck-Spritzgießen
Innendruck-Spritzgießen oder auch Fluidinjektionstechnik (FIT) ist ein spezialisiertes Spritzgussverfahren zur Herstellung hohler Werkstücke. Nach einem Arbeitsschritt des herkömmlichen Spritzgießens bzw. nach einer definierten Teilfüllung der Gussform wird ein vorübergehender Füllstoff (Wasser oder inertes Gas, in der Regel Stickstoff) so in eine teilgefüllte Form injiziert, dass es als inneres Formstück (Kern) wirkt. Durch die Verdrängung der Schmelze aus der Mitte wächst zum einen ein Hohlraum und zum anderen wird die Schmelze an bzw. in die äußere Gussform gedrückt. Nach Erstarren der Schmelze entweicht das Fluid wieder.[1]
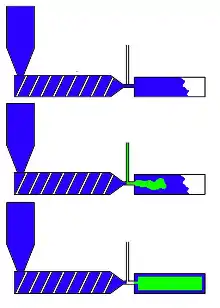
- blau: Formmasse
- grün: Fluid
Es ähnelt damit dem Sandwich-Verfahren beim Mehrkomponenten-Spritzgießen.
Verfahren der Fluidinjektionstechnik
Gasinjektionstechnik
Bei der Gasinjektionstechnik (GIT) – auch: Gasinnendrucktechnik, Gasinnendruck-Spritzgießen (GID) – verdrängt das Gas die Schmelze und übernimmt mit Drücken bis maximal 300 bar die Restfüllung. Das Injizieren kann durch die Maschinendüse und damit durch das Angusssystem oder durch eine separate Injektionsnadel direkt in das Formteil in der Kavität erfolgen. Eine weitere Variante ist die vollständige Füllung der Kavität mit Schmelze und anschließendem Ausblasen von Schmelze in eine Nebenkavität oder das Zurückblasen in den Schneckenzylinder.
Tendenziell bevorzugt man Gas immer dann, wenn Schwindung kompensiert werden soll[1], Masseanhäufungen nicht vermeidbar sind, Kanalquerschnitte sehr klein sind, Wasser nicht aus dem Bauteil entfernt werden kann oder die Baugröße des Injektors ausschlaggebend ist.
Wasserinjektionstechnik
Das Wasserinjektionstechnik (WID), auch Wasserinnendruck-Spritzgießen oder kurz WID genannt, ist prinzipiell gleich dem Gasinnendruck-Spritzgießen mit dem Unterschied, dass statt Gas Wasser über einen sogenannten Injektor in ein Spritzgussbauteil eingeleitet wird. Längere Zeit scheiterte die technische Umsetzung an den anlagen- und betriebstechnischen Schwierigkeiten, die mit dem Medium Wasser verbunden sind (Dichtigkeit, Korrosion). Forschungsvorhaben am Institut für Kunststoffverarbeitung (IKV) an der RWTH Aachen zeigten jedoch Wege für die praxisnahe Realisierung des Verfahrens auf, so dass dieses Verfahren mittlerweile erfolgreich am Markt etabliert ist.
Vorteile, die sich durch die Verwendung von Wasser ergeben, sind die deutliche Reduzierung der Taktzeit (größere Wärmekapazität des Wassers im Vergleich zu Stickstoff bei der GIT) und eine Verbesserung der Oberflächenstruktur, was insbesondere für Medienleitungen interessant ist.
Wasser kommt automatisch zum Zuge, wenn die Querschnitte und die Kanallänge in Abhängigkeit vom Material für die Gasinjektionstechnik zu groß werden und wenn bei unverstärkten Kunststoffen eine glatte, geschlossene Oberfläche gefordert ist, z. B. im Sanitärbereich. Im Allgemeinen spielt aber neben dem geringen Verzug die ebenfalls geringere erzielbare Restwanddicke eine zentrale Rolle.[1] Betriebswirtschaftlich gesehen stehen die wesentlich kürzeren Taktzeiten und die nicht anfallenden Gaskosten bei der Auswahl von Wasser im Vordergrund.[1] Bei großen Stückzahlen kann dies zu einer Reduzierung der Investitionskosten um bis zu 50 % führen (Halbierung der Fertigungslinien aufgrund des Effizienzanstiegs jeder einzelnen Linie).
Auswahl des Verfahrens und kombinierte Gas- und Wasserinjektion
Grundsätzlich haben diese beiden primären Verfahren ihr spezifisches Anwendungsgebiet, wobei dies überwiegend durch die Bauteilanforderung definiert wird. Im Übergangsbereich der Verfahrensauswahl entscheiden im Einzelfall die Gesamtkosten, die zu erwartende Stückzahl oder aber pragmatisch, welche Anlagentechnik bereits vorhanden ist.
Bei manchen Anwendungen reichen die bekannten Standardverfahren der Fluidinjektion nicht mehr aus. Hier steht dann eine wachsende Zahl von Sonderverfahren zur Verfügung, wie beispielsweise die Kombination von Wasser- und Gasinjektion in einem Bauteil. Bereiche mit größeren Querschnitten (z. B. Griffe) werden mit Fluidinjektionstechnik[2] ausgeformt, zur Schwindungskompensation an Rippen aber simultan Gasinjektionstechnik eingesetzt. Typische Anwendungsfälle sind Verkleidungen mit rückseitigen Rippen und Griffbereichen, Türtaschen, Motorrad-, Roller- und Gepäckträger.
Verwendung
Durch das Entfernen nicht benötigten Materials aus dem Bauteilkern und dem nahezu ohne Druckverlust von innen wirkenden Nachdruck durch das Fluid sind neue Designs und eine sonst nicht erreichbare Qualität der Bauteile, insbesondere ihrer Oberfläche, möglich. Die gezielte Hohlraumbildung, die bereits bei der Formteilkonstruktion berücksichtigt werden muss, ermöglicht bei vergleichbarer Steifigkeit der Formteile erhebliche Materialeinsparungen und ergibt dadurch wirtschaftlichere und zugleich leichtere Designvariationen gegenüber dem normalen Spritzgießen. Zusätzlich ergeben sich kürzere Taktzeiten durch die schnellere Abkühlung durch die Wasser- bzw. Gasinjektion.
Die Verwendungsmöglichkeiten des Verfahrens erstrecken sich nicht nur auf herkömmliche thermoplastische Werkstoffe. Es ist für nahezu alle Formmassen mit Quellflussverhalten anwendbar. Dies trifft auf die meisten Thermoplaste, eine große Anzahl Duroplaste und auch viele Elastomere zu.
Besonders geeignete Formteile zur Anwendung des Innendruck-Spritzgießens sind z. B. lange, dickwandige Teile, wie Handgriffe oder auch PKW-Türinnenmodule[1]. Diese Teile zeichnen sich durch sehr große Wandstärken aus. Man ist so in der Lage, Kunststoffteile mit sehr großen Wandstärken ohne Einfallstellen in einem Arbeitsgang herzustellen. Damit ist eine Materialersparnis bis ca. 50 % möglich. Es können sich dabei auch deutlich kürzere Taktzeiten durch kürzere Kühlzeiten aufgrund der geringeren Wandstärken ergeben. Zweiteilige Produkte, die bisher nach dem Spritzvorgang zusammengeklebt oder verschweißt wurden, sind in einem Arbeitsgang herstellbar.
Weitere Vorteile:
- Reduzierung der Schließkraft (nicht unbedingt)
- Realisierung von langen Fließwegen
- Bessere Oberfläche im Vergleich zu geschäumten Teilen
- Zum Teil einfachere Werkzeugkonstruktionen
Nachteile:
- Zusätzliche Kosten
- Empirische Ermittlung der Einstellparameter
- Loch am Injektionspunkt
- Festigkeit/Dichtigkeit beim Versiegeln oft ungenügend
Einzelnachweise
- Walter Michaeli: Einführung in die Kunststoffverarbeitung. 5. Auflage. Hanser Verlag, München/Wien 2006, ISBN 978-3-446-40580-6, Kap. 6.3.3. Verfahrensvarianten, S. 129–132 (eingeschränkte Vorschau in der Google-Buchsuche).
- Anm. Fluid ist hier als Flüssigkeit gemeint