Spektraldensitometrie
Die Spektraldensitometrie ist ein elektrooptisches Messverfahren, das die ursprünglich getrennt entwickelten und angewendeten Verfahren der Farbmessung und der Farbdichtemessung in sich vereint. Die dafür geschaffene Messgeräteklasse, das Spektraldensitometer, vereint geräte- und anwendungstechnisch die bisherigen Messgeräteklassen Spektralfotometer und Farbdensitometer.
Spektraldensitometer kommen in der Druckindustrie einschließlich Verpackungsdruck sowie Papier- und Druckfarbenindustrie zum Einsatz, um prozesstypische Kenngrößen im Rahmen der Qualitätssicherung in den entsprechenden Produktionsprozessen zu ermitteln.
Verfahrensbeschreibung
Spektralmessprinzip
Die Spektraldensitometrie bedient sich des Messprinzips der Erfassung des spektralen Remissionsgrads, aus dem sich alle anderen farbmetrischen und densitometrischen Größen berechnen lassen. Das bedeutet, dass der Sensor für den kompletten sichtbaren Bereich des elektromagnetischen Spektrums, also alle Wellenlängen des Lichts empfindlich sein muss. Der Empfindlichkeitsbereich beginnt etwa bei 400 nm (Nanometer) im Violett und reicht über die Farbnuancen Blaugrün, Grün und Gelb bis zum Rot bei 700 nm. Die Empfindlichkeit des Sensors muss nicht physikalisch kontinuierlich realisiert werden, das heißt, es können kleine Lücken zwischen den Banden auftreten, zwischen denen Messwerte interpoliert werden.
Das Gewinnen der spektralen Remissionswerte erfolgt für alle Wellenlängenabschnitte (Banden) gleichzeitig mittels eines Polychromators. Diese Vorrichtung fächert – je nach Hersteller durch ein Beugungsgitter oder durch viele Schmalbandfilter – den gemessenen Lichtstrom in seine spektralen Anteile auf, deren Signalstärken gemessen und in ihrer Gesamtheit als Spektralwertkurve ausgegeben werden.
Gemeinsamkeiten mit und Unterschiede zu Spektralfotometern und Densitometern
Allen drei Geräteklassen gemeinsam ist die glanzfreie Messgeometrie von Lichtquelle (gasgefüllte Lampe oder LEDs) via Probe auf Sensor. Sie beträgt 45°/0° oder 0°/45°. Nur bei Spektralfotometern mit diffuser Messgeometrie (Ulbricht-Kugel) für Messungen auf gewölbten oder stark reflektierenden Oberflächen und mit schwenkbarem Probenhalter für die Messung winkelabhängiger Farbveränderungen (Goniospektralfotometer) weichen die Messgeometrien ab; diese Geräte sind für die üblichen Anwendungen in der Druckindustrie jedoch nicht relevant und werden nachfolgend nicht weiter diskutiert.
Um den spektralen Remissionsgrad erfassen zu können, muss ein Spektraldensitometer über einen Spektralmesskopf verfügen, wie er auch in Spektralfotometern zur Anwendung kommt. Damit lässt sich ein Spektraldensitometer grundsätzlich auch als Farbmessgerät einsetzen, sofern es die Funktionsfreischaltung des Herstellers erlaubt.
Doch anders als Spektralfotometer sind Spektraldensitometer genau wie klassische Densitometer zusätzlich mit einem Polarisationsfilter ausgestattet, der ISO-konform für die Messung densitometrischer Größen in den Strahlengang eingeschwenkt werden muss. Erst aus den auf diese Weise gewonnenen spektralen Messdaten können densitometrische Größen berechnet und ausgeben werden. Die spektrale Basismessung führt zu einem weiteren Unterschied der Spektraldensitometer gegenüber klassischen Densitometern. Dieser Unterschied besteht in der exakten Messbarkeit von Sonderfarben – also Druckfarben, die nicht der ISO-Skala 2846-1:2006 (Bogenoffsetdruck und Heatset-Rollenoffsetdruck), 2:2007 (Coldset-Zeitungsoffsetdruck), 3:2002 (Illustrationstiefdruck), 4:2000 (Siebdruck) oder 5:2005 (Flexodruck) entsprechen und somit meistens als Volltonfarben und nicht als Prozessfarben verdruckt werden. Bisherige Densitometer konnten die Volltondichten von Sonderfarben eher „schätzen“ als messen.
Anwendung
Spektrale Messgrößen
Mit spektralen Messgrößen sind im Anwendungsfall Druck- und Verpackungsindustrie alle die Größen gemeint, die sich – wie oben beschrieben – auf den sichtbaren Bereich des elektromagnetischen Spektrums (Licht) beziehen. Sie dienen der Beschreibung farbmetrischer Phänomene, also der mathematischen Beschreibung des Farbensehens und der Farbwiedergabe in Verbindung mit dem Mehrfarbendruck auf den verschiedenen Bedruckstoffen.
Grundlage aller dieser spektralen Messungen ist das messtechnische Erfassen des spektralen Remissionsgrads (siehe 1.1). Im entsprechenden Messmodus „Farbmetrik“ verhält sich ein Spektraldensitometer wie die früheren Spektralfotometer. Das bedeutet, dass der im Spektraldensitometer vorhandene Polarisationsfilter nicht in den Strahlengang geschwenkt wird.
Aus dem gemessenen spektralen Remissionsgrad lassen sich alle anderen farbmetrischen Größen berechnen, das heißt, sie werden nicht als Messgrößen direkt erfasst, sondern indirekt aus dem spektralen Remissionsgrad über bekannte Formeln berechnet und dann vom Messgerät-Display oder der damit verbundenen Software auf einem PC ausgegeben. Sowohl beim Messvorgang als auch bei den anschließenden Berechnungen werden die standardisierten Rahmenbedingungen der CIE im Messgerät simuliert. Diese Rahmenbedingungen sind
- die „beleuchtende Lichtart“ – in der Druckindustrie wird die Normlichtart D50 (künstliches Tageslicht mit einer ähnlichsten Farbtemperatur von 5000 Kelvin) gefordert;
- der „Normalbeobachter“ – in der Druckindustrie gilt der 2°-Gesichtsfeldwinkel.
Die prozesstypischen farbmetrischen Kenngrößen der genannten Branchen sind
- die CIE-Farbmaßzahlen 1931 (XYZ und xyY),
- die CIE-Farbmaßzahlen 1976 (L*a*b* und L*u*v*, Farbkreis, Farbabstände ΔE, LCh),
- weitere CIE- und DIN-Farbabstandsformeln (zum Beispiel Lab99, ΔE94, ΔE2000, ΔE99, ΔEcmc),
- der Metamerie-Index (bedingt gleiche Farben bei Lichtartwechsel)
- sowie optische Papierkenngrößen (Weiß- und Gelbgrad).
Farbmessungen an Auflagendruckexemplaren werden an den Volltonfeldern des mitgedruckten Druckkontrollstreifens, an größeren Volltonflächen oder an beliebiger aussagekräftiger Stelle in den gedruckten Fotos und Grafiken durchgeführt. Farbmetrische Messungen verlangen vor Messbeginn die Kalibrierung auf Absolutweiß. Das dafür erforderliche Weißnormal in Form einer Keramikkachel mit bekanntem CIELAB-Farbort gehört zum Lieferumfang eines Spektraldensitometers.
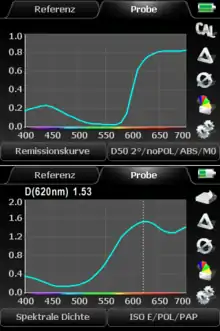
Densitometrische Messgrößen
Densitometrische Messgrößen, auch als dichtebasierte Messgrößen bezeichnet, werden ausschließlich in Verbindung mit drucktechnischen Prozessen erfasst. Denn die im Auflicht gemessene Farbdichte ist ein indirektes Maß für die Schichtdicke von Druckfarben auf dem Bedruckstoff. In der früheren Farbdensitometer-Geräteklasse wurde die Luther-Bedingung ausschließlich durch die selektiven Empfindlichkeiten der Sensoren in Abstimmung auf die Filter erfüllt: Rot-, Grün- und Blaufilter für die Buntfarben Cyan, Magenta und Yellow sowie der „Vis“-Filter (Charakteristik entspricht der Hellempfindlichkeitskurve) für die unbunte Zeichnungsfarbe Key (Schwarz).
Heute wird in den Spektraldensitometern von denselben Sensoren, die den spektralen Remissionsgrad bei der Farbmessung erfassen, auch bei der Bestimmung der densitometrischen Größen der gesamte sichtbare Bereich des elektromagnetischen Spektrums abgetastet. Herstellerabhängig können dabei sowohl physikalische Filter in den Strahlengang eingeschwenkt als auch virtuelle, das heißt mathematisch simulierte Filter gesetzt werden. Zusätzlich verlangt die standardkonforme Dichtemessung die Verwendung eines Polarisationsfilters, der die Glanzunterschiede zwischen noch nassen und bereits getrockneten Druckfarbenschichten unterdrückt. Auf diese Weise werden unabhängig von der Zeitnähe zum Druckvorgang die Messungen vergleichbar gemacht.
Im Messmodus „Densitometrie“ wird also der spektrale Remissionsgrad mit eingeschwenktem Polarisationsfilter erfasst. Wie schon im Farbmetrik-Messmodus schließt sich die rein mathematische Ermittelung der verwandten Kenngrößen an – hier allerdings der dichtebasierten:
- die Farbdichten, wahlweise nach Status E (Europa) oder T (Amerika),
- der Tonwert, wahlweise nach Murray-Davies oder Yule-Nielsen sowie die entsprechenden Differenzen (Tonwertzunahme),
- der Druckkontrast,
- die Buntfarbenbalance (Grau-, Farbbalance),
- die Farbannahme (nach Preucil, Ritz und/oder Brunner),
- die Werte für das Schieben und Dublieren,
- das „Dichtespektrum“ und somit die tatsächlichen Volltondichten von Sonderfarben.
Die Messbarkeit des Dichtespektrums ist ein Alleinstellungsmerkmal der Spektraldensitometer. Weil Dichten durch dekadisches Logarithmieren des Verhältnisses von remittiertem zu eingestrahltem Lichtstrom berechnet werden, wird im Spektraldensitometer der spektrale Remissionsgrad dieser Rechenoperation unterzogen. Denn der spektrale Remissionsgrad ist nichts anderes als die Verteilung der Lichtstromverhältnisse über der Wellenlänge, und das Dichtespektrum erscheint als gespiegelte Kurve des spektralen Remissionsgrades. Auf diese Weise wird hier eine Kurve berechnet, die der Dichtewerteverteilung im sichtbaren Spektrum entspricht. Diese spektrale Dichtekurve ist in der Praxis besonders bei der Messung von Sonderfarben unverzichtbar. Dabei entspricht das Kurvenmaximum in dem gemessenen Dichtespektrum der tatsächlichen Volltondichte der Sonderfarbe. An diesem Kurvenpunkt, der einer bestimmten Wellenlänge zugeordnet ist, setzt das Messgerät einen virtuellen Filter.
Dieses Funktionsmerkmal unterscheidet die Spektraldensitometer von den früheren Farbdensitometern. Bei der Messung an Sonderfarben schwenkten diese Geräte denjenigen Farbfilter in den Strahlengang ein, der der Komplementärfarbe der zu messenden Sonderfarbe am nächsten kam. Beispiel: Für die Messung an einem Grün wurde der Rotfilter benutzt. Da der Rotfilter in seiner spektralen Charakteristik normalerweise auf die Messung des Cyan (Blaugrün) abgestimmt ist, muss die damit gemessene Grün-Dichte logischerweise stark fehlerbehaftet sein. Dieses Manko kann nunmehr durch den Einsatz eines Spektraldensitometers überwunden werden. Sonderfarben werden vorrangig im Verpackungsdruck gedruckt, aber auch in Form der „Hausfarben“ an Werbedrucksachen.
Densitometrische Messungen an Auflagendruckexemplaren werden in den dafür vorgesehenen Feldern des mitgedruckten Druckkontrollstreifens sowie an aussagekräftigen Stellen im Sujet durchgeführt. Neben Volltonfeldern vorhanden sind Rasterfelder für Vierteltöne (zum Beispiel 40 %) und Dreivierteltöne (zum Beispiel 70 % oder 80 %), Zusammendruck-Volltonfelder für die Farbannahme der nacheinander gedruckten Farben, Zusammendruck-Rasterfelder für die Graubalance sowie Vertikal- und Horizontal-Linienfelder für das Detektieren von Schiebe- und Dubliererscheinungen. Densitometrische Messungen verlangen vor Messbeginn eine Kalibrierung auf das Weiß des Bedruckstoffs.
Handmessgeräte für Einzelmessungen
Die am weitesten verbreitete Messgeräteform ist das Handmessgerät. Es sollte gegen die äußeren Einflüsse im Drucksaal (Papierstaub, Puder, Herunterfallen) robust genug sein. Vor Messbeginn muss die Messaufgabe (das heißt die auszugebende Kenngröße) menügeführt ausgewählt werden. Je nachdem, ob es sich dabei um eine farbmetrische oder densitometrische Größe handelt, muss das Aus- und Einschwenken des Polarisationsfilters berücksichtigt werden. Hierbei verhalten sich die Geräte der verschiedenen Anbieter unterschiedlich; so kann zum Beispiel beim SpectroDens diese erforderliche Prozedur automatisch ausgelöst werden, sodass diesbezüglich Anwendungsfehler ausgeschlossen sind. Danach erfolgt gegebenenfalls die Kalibrierung auf das Weißnormal oder das Bedruckstoffweiß.
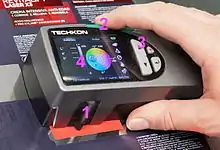
Die eigentliche Messung – als häufigster Praxisfall sei hier als Beispiel die Messung an der Druckmaschine erläutert – wird in folgenden Schritten durchgeführt:
- Ziehen der Probe (also des Druckexemplars) an der Druckmaschine;
- Ablegen der Probe auf dem Ansichtspult gemäß der Ausrichtung der Farbzonen;
- Platzieren des Spektraldensitometers an der gewünschten Messstelle (hochwertige Geräte sind so konstruiert, dass dies schnell und zielgenau möglich ist);
- Auslösen des Messvorgangs (entweder per Funktionstaste am Gerät oder, wenn das Gerät an einen PC angeschlossen ist, alternativ per Klick im Software-Dialog), wobei die Messdauer im Bereich einer Sekunde liegt;
- manuelles Weiterrücken des Messgeräts zur nächsten Messstelle auf dem Druckexemplar.
Weil Handmessgeräte den Messvorgang am ruhenden Druckexemplar durchführen, kann je nach Anforderung eine standardkonforme Messunterlage verwendet werden.[1]
Je nach Hersteller, Funktionsfreischaltung und optionaler PC-Software-Anbindung verfügen als Handmessgeräte ausgeführte Spektraldensitometer über folgende Funktionen:
- CMYK-Dichten (mit Polarisationsfilter), Sonderfarbdichten (mit Polarisationsfilter) oder Farbmaßzahlen (ohne Polarisationsfilter) nacheinander und gegenüber Referenzwerten messen;
- Farbbibliotheken generieren, ex- und importieren;
- auf spektralen Größen basierende Differenz-, Statistik- und Toleranzbewertungen (Pass/Fail, Mittelwert) durchführen;
- Druckkennlinie erstellen;
- an Rasterstufenkeilen auf dem Druckbogen oder an Druckplatten den Flächendeckungsgrad nach Yule-Nielsen messen und aus der Messreihe eine Kennlinie berechnen.
Handgeführte Scangeräte
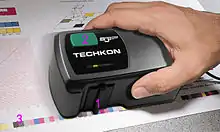
Gegenüber den Geräten ausschließlich für Einzelmessungen besitzen Handscan-Spektraldensitometer zusätzlich die Fähigkeit, zweckmäßig in Linie angeordnete Messfelder in einer durchgängigen Bewegung zu erfassen. Die Geräte erkennen automatisch den Übergang von einem Messfeld zum nächsten und erfassen in Sekundenbruchteilen den spektralen Remissionsgrad jedes Feldes – je nach Messmodus mit aus- bzw. eingeschwenktem Polarisationsfilter.
Aus typischen Messfeldanordnungen besteht zum Beispiel die Fogra-Druckkontrollleiste DKL, mit der während des Einrichte- und des Auflagendruck-Prozesses die farbmetrischen und/oder densitometrischen Größen für jede Farbzone der Druckwerke von Mehrfarben-Druckmaschinen aussagekräftig dargestellt werden.[2] Geeignet sind diese Messgeräte aber auch für das Auswerten des Ugra/Fogra-Medienkeils oder zum Ausmessen von Kalibrierungs- und Linearisierungs-Streifengruppen („Targets“) für digitale Prüfdrucksysteme.
Im Gegensatz zu den Spektraldensitometern für Einzelmessungen verfügen Handscan-Spektraldensitometer nicht über ein Display, weil die Fülle der aufgenommenen Daten (eine Druckkontrollleiste kann weit über 100 Messfelder aufweisen) zu groß ist. Deshalb werden diese Geräte ausschließlich in Verbindung mit einer PC-Software betrieben. An Druckmaschinen wird diese Software oft auf dem Leitstandrechner mit installiert. Innerhalb von einer bis zwei Sekunden nach Beendigung einer handgeführten Scanmessung, das heißt nach Erfassen des letzten Messfeldes, liegt die Auswertung sämtlicher Messfelder vor. Wichtigste Analysemöglichkeiten von kompletten Druckkontrollleisten sind die Darstellung der Volltondichten oder der Dichtedifferenzen, auch im Bezug zu definierten Toleranzgrenzenwerten, sowie deren Protokollierung über die gesamte Druckauflage.
Ein Messvorgang – wiederum anhand eines Beispiels an der Druckmaschine erläutert – wird in folgenden Schritten durchgeführt:
- Ziehen der Probe an der Druckmaschine;
- Ablegen der Probe auf dem Ansichtspult gemäß der Ausrichtung der Farbzonen;
- Platzieren des Spektraldensitometers vor dem ersten Messfeld der Druckkontrollleiste;
- Starten des Messvorgangs per Funktionstaste am Gerät bei gleichzeitigem Beginn der Handführung des Geräts;
- Handführung des Geräts vom ersten bis zum letzten Messfeld, wobei für die exakte Führung die Verwendung einer Metallschiene, die über dem Druckbogenformat fixiert wird, oder das Ausnutzen der Bogenanschlagleiste am Ansichtspult hilfreich ist.
In den Druckereien sind handgeführte Scan-Spektraldensitometer besonders in den Bogendruckmaschinen-Formatklassen 00 bis 1 zu finden, seltener bis 3b. Häufig werden sie von Druckmaschinenherstellern als optionales OEM-Zubehör mit vertrieben.
Elektromotorisch angetriebene Scanmessgeräte
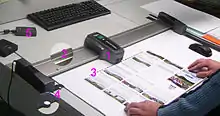
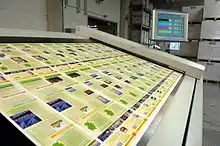
Bei mittel- und großformatigen Bogenoffset-Druckmaschinen, also ab der Formatklasse 3b bis zur derzeit größten (9), empfiehlt sich ein elektromotorischer Antrieb des Scan-Spectraldensitometers, denn die sichere Bedienbarkeit per Hand stößt hier einfach an ihre ergonomischen Grenzen. Derartige Lösungen sind aber auch für kleinere Formate verfügbar. Auch elektromotorisch angetriebene Scan-Spektraldensitometer sind bei einigen Druckmaschinenherstellern als Option erhältlich, darunter manche OEM-Lösungen sogar ausschließlich unter dem Namen des Druckmaschinenherstellers.
Je nach Messgerätehersteller werden unterschiedliche Konstruktionsprinzipien angeboten, die sich im technischen Aufwand und somit im Preis erheblich unterscheiden können, wobei die Messgeschwindigkeit bei allen Lösungen allerdings nahezu gleich ist. Folgende Lösungen, beginnend beim geringsten Aufwand, sind auf dem Markt:
- Das Spektraldensitometer wird auf einer horizontalen, das heißt in Scanrichtung (X-Richtung) angeordneten Zahn- oder Gleitschiene bewegt und dabei entweder mittels Kleingetriebe im Messgerät oder mittels Seilzug in der seitlichen Schienenhalterung elektromotorisch angetrieben. Je nachdem, wo sich die Druckkontrollleiste auf dem Druckbogen befindet, wird die Schiene in entsprechendem Abstand zur Pultkante fixiert. Dieses Konstruktionsprinzip lässt sich direkt auf dem Farbsteuerpult des Druckmaschinenleitstands anordnen. Das Messgerät kann bei Bedarf aus der Vorrichtung herausgenommen und für Einzelmessungen an beliebiger Stelle des Druckexemplars verwendet werden.
- Das Spektraldensitometer ist auf einer vertikalen, das heißt im rechten Winkel zur Scanrichtung angeordneten Schienenvorrichtung befestigt und kann je nachdem, wo sich die Druckkontrollleiste auf dem Druckbogen befindet, in dieser Vorrichtung nach oben oder unten (Y-Richtung) verschoben werden. In der gewählten Position wird das Messgerät samt Vertikalschiene in einer zweiten, und zwar horizontalen Schienenvorrichtung in Scanrichtung elektromotorisch bewegt. Dieses Konstruktionsprinzip benötigt ein separates Pult als Aufstellungsfläche neben dem Druckmaschinenleitstand. Auch hier lässt sich das Messgerät aus der Vorrichtung für Einzelmessungen herausnehmen.
- Das zweitgenannte Konstruktionsprinzip lässt sich erweitern, indem das Spektraldensitometer in der vertikalen Schienenvorrichtung ebenfalls elektromotorisch nach oben oder unten verschiebbar ist. Durch diese elektromotorische X-Y-Steuerung lässt sich außer das Scannen der Druckkontrollleiste auch das sequentielle Anfahren beliebiger Messpunkte auf dem Druckexemplar programmieren und dann während des Auflagendrucks abrufen. Je nach Hersteller benötigt dieses Konstruktionsprinzip zum Aufstellen ein separates Pult oder kann auf dem Farbsteuerpult installiert werden. Nur bei einem Hersteller ist das Spektraldensitometer nicht als Messkopf, sondern als herausnehmbares Messgerät konzipiert.
- Das aufwändigste Konstruktionsprinzip wird von eigenständigen Messpulten verkörpert, die die gesamte Fläche des Druckbogens scannen. Sie werden wegen ihres hohen Preises meistens zentral im Drucksaal installiert und mit dem Leitstandrechner mehrerer Druckmaschinen vernetzt. Im Innern der elektromotorischen Scanvorrichtung, die den Druckbogen in X-Richtung überfährt, befinden sich nebeneinander mehrere Spektralmessköpfe, die Druckexemplare bis zur Formatgröße 3b lückenlos erfassen. In den Messköpfen sind keine Polarisationsfilter einschwenkbar, sodass für die Berechnung der Farbdichten die Polarisationsfilterwirkung entweder simuliert werden muss – auf Grund der unterschiedlichen Trocknungsgeschwindigkeit von Druckfarbenserien ein fehlerbehaftetes Verfahren – oder einfach die Unvergleichbarkeit zwischen nassen und trockenen Drucken in Kauf genommen wird.
Vorwiegend von den deutschen Druckmaschinenherstellern werden darüber hinaus Hybridsysteme angeboten, die zwei Messköpfe in einem Gehäuse integrieren: Der eine arbeitet als reines Spektralfotometer für die Bestimmung der Farbmaßzahlen, der andere als klassisches Filterdensitometer. Der vermeintliche Vorteil besteht in einem Zeitgewinn, der darin besteht, dass farbmetrische und densitometrische Größen zeitgleich gemessen werden können. Spätestens aber dann, wenn Sonderfarbdichten zu bestimmen sind, geht dieses Konzept nicht mehr auf. In diesem Punkt der bessere Kompromiss ist beim Spektraldensitometer zu finden: Beide Messmodi können automatisch hintereinander aufgerufen werden: bei der Hinbewegung auf der Schiene eine spektrale Messung ohne Polfilter (farbmetrischer Modus) und bei der Rückbewegung eine spektrale Messung mit Polfilter (densitometrischer Modus), bei der auch Sonderfarbdichten korrekt ermittelt werden.
Inline-Messsysteme
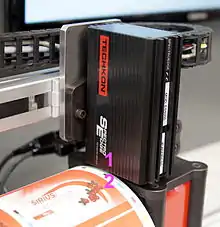
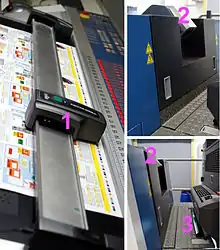
Während Handmessgeräte für Einzelmessungen, handgeführte und elektromotorisch angetriebene Scanmessgeräte am ruhenden Druckexemplar messen (statische Messung), erfassen Inline-Spektraldensitometer mehrere Messfelder am bewegten Druckexemplar (dynamische Messung). Dieses Messkonzept wurde zuerst an Rollendruckmaschinen (Offset-, Tief-, Flexo- und Digitaldruck) verwirklicht, wo die Messung an der laufenden bedruckten Papierbahn erfolgt. Seit ca. 2004 existieren auch Lösungen für den Bogenoffsetdruck.
Indem die Messköpfe „inline“, das heißt in der Druckmaschine, genauer gesagt unmittelbar nach dem letzten Druckwerk installiert werden, verstreicht keine Zeit für ein Entnehmen und Positionieren der Probe auf einem Pult sowie für das Positionieren des Messgeräts. Somit verkürzt sich die Reaktionszeit des gesamten Messsystems gegenüber statischen Messungen.
Der Reaktionszeitvorteil kommt zumindest im Auflagendruckprozess zum Tragen. Beim Einrichteprozess eines Druckauftrages insbesondere an einer Bogenoffsetdruckmaschine wird der Vorteil jedoch oftmals kompensiert, weil dieser Messablauf zu einer zu hohen Druckgeschwindigkeit vor dem eigentlichen Produktionsbeginn verleitet. Dadurch fällt wirtschaftlich unvertretbar viel Makulatur an. Insofern bringen Inline-Spektraldensitometer zurzeit vorwiegend an Rollendruckmaschinen den erwünschten Wirtschaftlichkeitsgewinn.
Die besonderen technischen Herausforderungen bei Inline-Spektraldensitometern bestehen darin, dass
- der Messzeitpunkt mit dem Maschinentakt synchronisiert werden muss und
- sich aufgrund der hohen Bewegungsgeschwindigkeit des Messobjekts die Messdauer extrem verkürzt.
Die Taktsynchronisierung ist relativ einfach vorzunehmen, indem sich die Messfelder an einer vorbestimmten Position befinden und die Optik des Messkopfes auf die eng nebeneinander angeordneten Messfelder fokussiert wird. Um eine kurze Messdauer zu realisieren, ist ein hochenergetisches Messlicht sicherzustellen – entweder in permanenter Einstrahlung oder als synchronisierter Blitz.
Inline-Spektraldensitometer für Rollendruckmaschinen besitzen in der Regel unbeweglich eingebaute Polarisationsfilter und können CMYK-Dichten oder Sonderfarbdichten messen. Nur bei wenigen Fabrikaten ist der Polarisationsfilter ausschwenkbar, um auch farbmetrische Größen messen zu können. In der Praxis wird meistens nur an einer ausgewählten Stelle der Papierbahn gemessen, indem der Messkopf elektromotorisch auf einer Schiene in die gewünschte Position gefahren wird. Selten sind mehrere Messköpfe auf separaten Schienen versetzt positioniert. Über die gesamte Bahnbreite traversierende Messköpfe wenden zurzeit nur nichtspektrale Messverfahren an.[3]
Die bisher für den Bogenoffsetdruck verfügbaren Inline-Messlösungen sind keine Spektraldensitometer, sondern entweder mehrere über die Formatbreite angeordnete Spektralfotometer (bei denen die Polarisationsfilterwirkung bestenfalls simuliert wird und die auf die Verwendung einer speziellen Druckkontrollleiste angewiesen sind) oder Rot-/Grün-/Blau-LED-basierende Densitometerköpfe mit Polfilter.
Allen Inline-Lösungen, die entweder nicht spektral oder zwar spektral, aber geometriebedingt nicht völlig ISO-konform messen können, ist die Notwendigkeit einer Referenzierung gemeinsam. Darunter zu verstehen ist hier die Benutzung eines spektralen Hand-, Handscan- oder Motorscan-Messgeräts, mit dem der Drucker außerhalb der Druckmaschine die erforderlichen Bezugswerte ISO-konform misst und die Resultate in den Computer, auf dem das Inline-System installiert ist (in der Regel der Leitstandrechner), übernimmt. Die Sollwerte für die spätere Inline-Messung werden also mittels eines externen Messverfahrens vorgegeben. Diese Prozedur ist auch schon deshalb unumgänglich, weil Vergleichsvorlagen, zum Beispiel farbverbindliche Digitalproofs, nur außerhalb der Druckmaschine ausgemessen werden können und ohnehin nicht mit einer Druckkontrollleiste ausgestattet sind.
Implementierung von Branchenstandards
Druckindustrie inkl. Verpackungsdruck auf gering reflektierenden Oberflächen
Unter dieser Branchenangabe sind alle Druckverfahren zusammengefasst, deren Prozess- und Farbwiedergabe-Standardisierung in der ISO 12647 verankert sind: Bogenoffsetdruck, Endlos-, Heatset- und Coldset-Rollenoffsetdruck, Illustrationstiefdruck, Siebdruck, Flexodruck und digitaler Prüfdruck. Verpackungsdruck meint hier den Druck von Faltschachteln und Etiketten auf gering reflektierenden Materialoberflächen, also auf Papier, Karton und Wellpappe sowie auf einigen Kunststofffolien, auf denen die Messgeometrie 45°/0° noch zuverlässige Ergebnisse liefert.
Obligatorische Standardumsetzung
In den Gerätefunktionen der Spektraldensitometer müssen folgende grundlegende Standards implementiert sein, um den Mindestanforderungen in dieser Branche zu genügen:
- ISO 5-3 „Dichtemessung“,[4]
- Simulation der ISO 5631-3 „Beobachtungsbedingungen D50/2°“,[5]
- ISO 11664-4 „CIELAB(1976)-Farbraum“;[6]
- ISO 13655 „spektrale Farbmessung“.[7]
Bei der technischen Realisierung der ISO 13655 wurden vor 2009 gasgefüllte Glühlampen mit Wolframwendel eingesetzt, deren Emissionsspektrum weitgehend der Normlichtart A entspricht, also nur einen geringen UV-Anteil, dafür aber einen hohen Infrarot-Anteil aufweist. Die in der Druckindustrie festgelegte Normlichtart D50 besitzt jedoch einen UV-Anteil, der in den Messgeräten nicht in der erforderlichen Höhe vorhanden war, d. h. die Beleuchtung mit Normlicht D50 wurde rein rechnerisch simuliert: aus der spektralen Strahlungsverteilung des Glühlampen-Messlichts und der spektralen Empfindlichkeit der Sensoren.
Da in den zu bedruckenden Papieren aber immer häufiger optische Aufheller eingesetzt werden, die den UV-Anteil aus dem realen Normlicht D50 in sichtbares bläuliches Licht umwandeln und somit den Weißgrad des Papiers auf über 100 % anheben, besteht eine wachsende Notwendigkeit, diesen visuellen Effekt auch in den Spektraldensitometern physikalisch-messtechnisch darzustellen. U.a. aus diesem Grund wurde 2009 die ISO 13655 neu gefasst. Sie definiert in einem Spektralbereich von 340 nm bis 780 nm die vier Messmodus-Einstellungen neu:
- M0, „A-Modus“: für die konventionelle Farbmessung vor 2009, d. h. spektraler Remissionsgrad ohne Polfilter unter einer gasgefüllten Wolframglühlampe mit annähernd Normlichtart A, wobei der UV-Anteil bei Bedarf mathematisch ergänzt werden kann;
- M1, „D50-Modus“: für die physikalisch korrekte Farbmessung ab 2009, d. h. spektraler Remissionsgrad ohne Polfilter unter einer LED-Lichtquelle, die bestmöglich die Normlichtart D50 mit korrektem UV-Anteil physikalisch simuliert, wobei eine UV-Quelle erforderlich zuschaltbar sein muss;
- M2, „UV-Cut-Modus“: für die Farbmessung unter Ausblenden des UV-Anteils im Messlicht, d. h. spektraler Remissionsgrad ohne Polfilter unter einer Lichtquelle, die eine beliebige Normlichtart ohne UV-Anteil erzeugt bzw. gegebenenfalls den UV-Anteil mit einem UV-Sperrfilter ausschließt;
- M3, „Polfilter-Modus“: für die Densitometrie, d. h. die Messung der optischen Dichte (Schwärzung), Farbdichte (Prozessdruckfarben) und spektralen Dichte (Sonderfarben) unter Verwendung eines selektiven Filtersatzes oder eines Spektralmesskopfes.
Weitere Details zu den Messmodi:
Die Forderung im Modus M1 nach physikalisch korrekter Simulation der Normlichtart D50 führte in den Jahren 2011 und 2012 zu einem Innovationsschub. Da eine theoretisch erforderliche F8-Fluoreszenzlampe nicht in ein kleines Messgerät passt, wird praktisch die Normlichtart D50 mit mehreren, insgesamt spektral repräsentativen LEDs (inkl. UV-LEDs für den UV-Anteil) simuliert; eventuelle Intensitätsdefizite in der spektralen Strahlungsverteilungsfunktion werden im Zusammenwirken mit der Spektralempfindlichkeit der Sensoren (Luther-Bedingung) wie bisher mathematisch kompensiert.
Die physikalische Simulation von D50 in M1 mittels LED-Messlicht wurde erstmals 2011 in einem Handmessgerät von Konica Minolta realisiert. Das Spektraldensitometer wurde vor allem für das Erstellen von ICC-Profilen entwickelt. Dem gleichen Zweck folgte als zweiter Hersteller Barbieri electronic im großformatigen Inkjet-Druck (LFP).[8]
Als dritter Hersteller implementierte Techkon 2012 den M1-Modus durch ebenfalls komplette LED-Abdeckung des sichtbaren Spektrums plus UV-Anteil, wobei Techkons Spektraldensitometer vorrangig an Offset- und Flexodruckmaschinen, also unter robusten Produktionsbedingungen eingesetzt werden. Somit ermöglicht Techkon erstmals im Drucksaal eine Bewertung optischer Aufheller in den Auflagenpapieren und einen messtechnischen Vergleich zu Digitalproofs, die optische Aufheller beinhalten oder in ihren ICC-Profilen berücksichtigen. Als bislang einzige Geräte am Markt schwenken die Drucksaal-Spektraldensitometer von Techkon bei Moduswechsel automatisch die Polfilter ein (M3) oder aus (M0, M1, M2).[9]
Fakultative Standardunterstützung
Die Fixierung der Spektraldensitometer auf die Druckindustrie hat die führenden Messgeräteanbieter dazu bewogen, in der Software, die in Verbindung mit der Hardware erworben werden kann, die standardkonforme Qualitätssicherung in den Druckverfahren sowie in der Anfertigung farbverbindlicher Proofs zu unterstützen. Dies geschieht im Allgemeinen durch die Anwendung folgender Standards:
- die siebenteilige ISO 12647, in der die farbmetrischen Daten der Papiertypen und der Prozessfarben-Skalen genannt sowie deren Handhabung vorgeschrieben sind;[10]
- in den deutschsprachigen und einigen europäischen Ländern als Ergänzung zur ISO12647-2 der ProzessStandard Offsetdruck, in dem u. a. die Farbreihenfolge in der Druckmaschine, die Auswahl der Druckfarben, die Tonwertsteuerung in der Druckvorstufe, die Verwendung des Polarisationsfilters beim Messen und andere Abläufe als detaillierte Arbeitsanleitungen beschrieben sind;
- die Prozessdruckfarben-Skala ISO 2846 mit ihren farbmetrischen Sollwerten;
- für den europäischen Markt die Analyse des Ugra/fogra-Medienkeils als standardisiertes Kontrollmittel der Druckindustrie (Medienstandard Druck);
- für den amerikanischen Markt der GRACoL-Standard mit seinen G7-Kontrollmitteln.[11]
Verwandte Industrien
Spektraldensitometer – und zwar Handgeräte für Einzelmessungen – werden auch in anderen Industriebereichen vertrieben, in denen Farben gemessen werden müssen:
- Herstellung von Druck-, Anstrich- und Künstlerfarben,
- Herstellung von Papier, Karton und Packstoffen,
- Textilindustrie.
Dort sind in erster Linie die farbmetrischen Gerätefunktionen gefragt. Obligatorisch müssen daher folgende Standards umgesetzt sein:
Weblinks
Einzelnachweise
- Fogra Forschungsgesellschaft Druck e.V.: FograCert-Prüfprogramm, Messunterlagen, abgerufen am 27. April 2014
- Forschungsgesellschaft Druck e.V.: Kontrollmittel, Digital-Druckkontrollstreifen, abgerufen am 27. April 2014
- Q.I. Press Controls: Intelligent Density System IDS (Memento des Originals vom 27. April 2014 im Internet Archive) Info: Der Archivlink wurde automatisch eingesetzt und noch nicht geprüft. Bitte prüfe Original- und Archivlink gemäß Anleitung und entferne dann diesen Hinweis. (CCD-Sensor-basiertes Inline-Dichtemesssystem; PDF; 244 kB), abgerufen am 27. April 2014
- ISO 5-3:1995 Photography – Density measurements – Part 3: Spectral conditions (International Organization for Standardization), abgerufen am 25. April 2014
- ISO 5631-3:2008 Paper and board – Determination of colour by diffuse reflectance – Part 3: Indoor illumination conditions (D50/2 degrees) (International Organization for Standardization), abgerufen am 26. Oktober 2009
- ISO 11664-4:2008 Colorimetry – Part 4: CIE 1976 L*a*b* Colour space (International Organization for Standardization), abgerufen am 25. April 2014
- ISO 13655:2009 (Revised 2013) Graphic technology – Spectral measurement and colorimetric computation for graphic arts images (International Organization for Standardization), abgerufen am 18. Januar 2016
- Fogra Forschungsgesellschaft Druck e.V.: Methodenentwicklung zur Überwindung fluoreszenzbedingter Abweichungen zwischen Prüf- und Auflagendrucken. (AiF-Nr.: 16607 N), Zwischenergebnisse, DfwG-Tagung Aachen 2012, zuletzt abgerufen am 18. Januar 2016
- Techkon: Spektral-Densitometer SpectroDens, Software SpectroConnect. Handbuch 2015 (Memento des Originals vom 27. April 2014 im Internet Archive) Info: Der Archivlink wurde automatisch eingesetzt und noch nicht geprüft. Bitte prüfe Original- und Archivlink gemäß Anleitung und entferne dann diesen Hinweis. , zuletzt abgerufen am 18. Januar 2016
- ISO 12647-2:2013: Graphic technology – Process control for the production of half-tone colour separations, proof and production prints – Part 2: Offset lithographic processes (International Organization for Standardization), abgerufen am 18. Januar 2016
- GRACoL 2013 Introduction (New Requirements and Applications for Commercial Offset Lithography) (Memento des Originals vom 24. Januar 2016 im Internet Archive) Info: Der Archivlink wurde automatisch eingesetzt und noch nicht geprüft. Bitte prüfe Original- und Archivlink gemäß Anleitung und entferne dann diesen Hinweis. IDEAlliance.org, abgerufen am 27. April 2014
- ISO 11475:2004 Paper and board – Determination of CIE whiteness, D65/10 degrees (outdoor daylight) (International Organization for Standardization), abgerufen am 27. April 2014